Maszyna do cięcia laserowego metalu
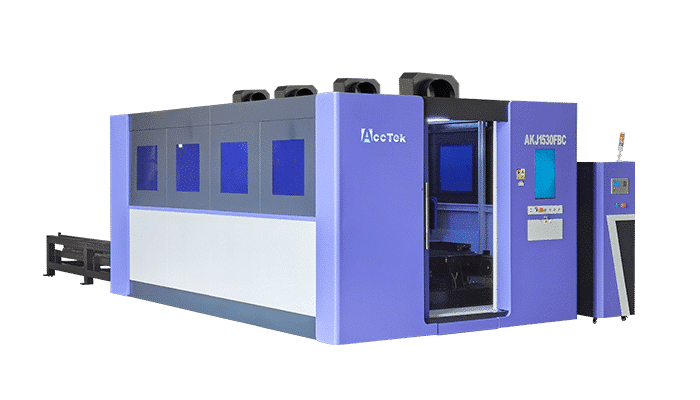
Asortyment produktów
-
Maszyna do cięcia laserem ze stali nierdzewnej
Oceniono 4.75 na 5$13,300.00 – $168,000.00 Wybierz opcje Ten produkt ma wiele wariantów. Opcje można wybrać na stronie produktu -
Maszyna do cięcia laserem stali węglowej
Oceniono 4.75 na 5$13,300.00 – $168,000.00 Wybierz opcje Ten produkt ma wiele wariantów. Opcje można wybrać na stronie produktu -
Laserowa maszyna do cięcia aluminium
Oceniono 4.75 na 5$13,300.00 – $168,000.00 Wybierz opcje Ten produkt ma wiele wariantów. Opcje można wybrać na stronie produktu -
Maszyna do cięcia laserem miedzi
Oceniono 5.00 na 5$13,300.00 – $168,000.00 Wybierz opcje Ten produkt ma wiele wariantów. Opcje można wybrać na stronie produktu -
Mosiężna maszyna do cięcia laserowego
Oceniono 4.75 na 5$13,300.00 – $168,000.00 Wybierz opcje Ten produkt ma wiele wariantów. Opcje można wybrać na stronie produktu -
Maszyna do cięcia laserowego tytanu
Oceniono 4.75 na 5$13,300.00 – $168,000.00 Wybierz opcje Ten produkt ma wiele wariantów. Opcje można wybrać na stronie produktu -
Maszyna do cięcia laserowego stopów niklu
Oceniono 4.75 na 5$13,300.00 – $168,000.00 Wybierz opcje Ten produkt ma wiele wariantów. Opcje można wybrać na stronie produktu -
Maszyna do cięcia laserowego stali ocynkowanej
Oceniono 4.75 na 5$13,300.00 – $168,000.00 Wybierz opcje Ten produkt ma wiele wariantów. Opcje można wybrać na stronie produktu
Cięcie laserowe Przeciwko. Inne metody
Cięcie laserowe kontra cięcie plazmowe
Cięcie laserowe zapewnia wyższą precyzję i czystsze cięcia w porównaniu z cięciem plazmowym. Tworzy mniej stref wpływu ciepła, minimalizując zniekształcenia materiału. Podczas gdy cięcie plazmowe jest szybsze w przypadku grubszych materiałów, cięcie laserowe wyróżnia się dokładnością i drobnymi szczegółami, co czyni je idealnym do skomplikowanych projektów i cieńszych metali.
Cięcie laserowe kontra cięcie strumieniem wody
Cięcie strumieniem wody jest skuteczne w przypadku grubych materiałów i zapewnia czyste krawędzie bez ciepła. Jednak cięcie laserowe jest szybsze, bardziej energooszczędne i umożliwia cięcie cieńszych metali z większą precyzją. Cięcie strumieniem wody może również mieć problemy z materiałami silnie odbijającymi światło, podczas gdy cięcie laserowe radzi sobie z nimi bez wysiłku.
Cięcie laserowe kontra cięcie mechaniczne
Mechaniczne metody cięcia, takie jak piłowanie lub ścinanie, obejmują siłę fizyczną, która może powodować naprężenia materiału i wymaga częstej konserwacji narzędzi. Natomiast cięcie laserowe nie wymaga kontaktu, co zmniejsza zużycie narzędzi i zapewnia większą precyzję. Jest również szybsze i bardziej odpowiednie do złożonych, szczegółowych cięć.
Dlaczego warto wybrać laser AccTek
Najnowocześniejsza technologia
Maszyny AccTek Laser wykorzystują najnowszą technologię lasera światłowodowego, zapewniając wysoką precyzję i szybkie prędkości cięcia. Nasze systemy zapewniają niezrównaną dokładność i wydajność, zapewniając najlepszą jakość cięcia różnych materiałów przy minimalnym zniekształceniu.
Rozwiązania niestandardowe
Rozumiemy, że każda firma ma wyjątkowe wymagania. Dlatego oferujemy opcje dostosowywalne, w tym zakresy mocy, rozmiary obszaru roboczego i prędkości cięcia, co pozwala dostosować nasze maszyny do konkretnych potrzeb produkcyjnych i rodzajów materiałów.
Wyjątkowa efektywność energetyczna
Nasze maszyny do cięcia laserowego są zaprojektowane tak, aby zapewnić maksymalną wydajność energetyczną. Dzięki niższemu zużyciu energii i zoptymalizowanej wydajności maszyny AccTek Laser pomagają obniżyć koszty operacyjne, co czyni je opłacalnym rozwiązaniem zarówno dla produkcji na małą, jak i dużą skalę.
Trwałość i niezawodność
Maszyny do cięcia laserowego AccTek są zaprojektowane z myślą o długoterminowej trwałości, z wysokiej jakości komponentami i precyzją wykonania. Nasze maszyny są zaprojektowane tak, aby zapewniać stałą, niezawodną wydajność, zmniejszając potrzeby konserwacyjne i wydłużając żywotność Twojego sprzętu.
Wsparcie posprzedażowe
Wierzymy w budowanie długoterminowych relacji z naszymi klientami. AccTek Laser zapewnia wyjątkowe wsparcie posprzedażowe, w tym instalację, szkolenia i stałą pomoc techniczną. Nasz zespół jest zawsze gotowy pomóc Ci zoptymalizować wydajność maszyny i szybko rozwiązać wszelkie problemy.
Konkurencyjne ceny i wartość
W AccTek Laser oferujemy wydajne maszyny do cięcia laserowego w konkurencyjnych cenach, zapewniając najlepszą wartość inwestycji. Nasze maszyny zapewniają wyjątkową jakość przy przystępnej cenie, co czyni nas zaufanym partnerem w zakresie potrzeb produkcyjnych.
Często Zadawane Pytania
Ile kosztują maszyny do laserowego cięcia metalu?
Koszt maszyny do cięcia laserowego metalu może się znacznie różnić w zależności od wielu czynników, w tym specyfikacji maszyny, mocy, rozmiaru i marki. Oto ogólne przedziały cenowe maszyn do cięcia laserowego metalu:
- Laserowa maszyna do cięcia metalu o małej mocy (1000–3000 W): Ten typ maszyny to kompaktowa maszyna odpowiednia dla małych firm i warsztatów. Zwykle ma niższą moc znamionową i mniejszą powierzchnię cięcia. Cena wycinarki laserowej o mocy 1000 W waha się od $12 500 do $30 000, natomiast cena wycinarki laserowej o mocy 3000 W waha się od $20 000 do $45 000.
- Laserowa maszyna do cięcia metalu średniej mocy (6000 w-12000 w): Ta maszyna jest przeznaczona do średnich operacji produkcyjnych i zapewnia większą moc i większy obszar cięcia. Ceny maszyn do cięcia laserowego średniej klasy wahają się od $35 000 do $180 000.
- Laserowa maszyna do cięcia metalu o dużej mocy (20 000–30 000 w): Koszt dużych maszyn do cięcia laserowego metalu o dużej mocy, zaprojektowanych do intensywnego i szybkiego cięcia, mieści się w zakresie od $160 000 do $320 000. Tego typu maszyny są stosowane w branżach takich jak przemysł lotniczy, motoryzacyjny i produkcja ciężkich maszyn.
Należy zauważyć, że są to ogólne przedziały cenowe, a rzeczywisty koszt maszyny do cięcia laserowego metalu może się znacznie różnić w zależności od takich czynników, jak moc lasera, obszar cięcia, funkcje automatyzacji (takie jak automatyczne urządzenia do załadunku i rozładunku) i inne. Jeśli chcesz uzyskać jak najdokładniejsze i aktualne informacje o cenach, możesz w każdej chwili skontaktować się z nami. Inżynierowie AccTek Laser dostarczą kompletne rozwiązania i oferty w oparciu o Twoje specyficzne potrzeby. Możemy również podać szczegółowe informacje na temat wszelkich dodatkowych kosztów związanych z instalacją, szkoleniem i konserwacją.
Jaki rodzaj lasera może ciąć metal?
Do cięcia metalu można używać wielu typów generatorów laserowych, ale najczęściej używanymi typami do cięcia metalu są generatory lasera światłowodowego, generatory lasera CO2 i generatory lasera Nd:YAG. Każdy generator laserowy ma swoje zalety i ograniczenia, dzięki czemu nadaje się do różnych scenariuszy cięcia metalu.
- Generator lasera światłowodowego: Generatory lasera światłowodowego są popularne w zastosowaniach związanych z cięciem metalu ze względu na ich wysoką wydajność i precyzję. Ten generator laserowy wykorzystuje światłowód do dostarczania skoncentrowanej wiązki laserowej do głowicy lasera. Generatory lasera światłowodowego zazwyczaj działają w zakresie bliskiej podczerwieni (około 1,06 mikrona) i szczególnie nadają się do cięcia metali, takich jak stal nierdzewna, aluminium, mosiądz i miedź. Generatory lasera światłowodowego znane są z dużej mocy i doskonałej jakości wiązki, dzięki czemu mogą dokładnie i szybko ciąć materiały metalowe o różnej grubości.
- Generator lasera CO2: Generator lasera CO2 jest jednym z najczęściej używanych typów generatorów lasera używanych do cięcia metalu. Działa w zakresie podczerwieni (długość fali około 10,6 mikrona) i idealnie nadaje się do cięcia metali (np. stali, stali nierdzewnej, aluminium itp.) i materiałów niemetalowych (np. tworzyw sztucznych, drewna itp.). Zasada działania generatora lasera CO2 polega na rzutowaniu wiązki lasera CO2 o dużej mocy na powierzchnię metalu przez szereg luster i soczewek skupiających w celu dokończenia cięcia cienkich blach.
- Generator lasera Nd:YAG: Generator lasera Nd:YAG (neodymowo-ytrowo-aluminiowy granat) to kolejny rodzaj lasera używanego do cięcia metali. Działają w zakresie bliskiej podczerwieni i nadają się do cięcia różnych metali, w tym stali, stali nierdzewnej i niektórych materiałów nieżelaznych. Lasery Nd:YAG są zazwyczaj używane do precyzyjnego cięcia i są w stanie ciąć grubsze materiały niż generatory laserów CO2, ale mają mniejsze możliwości cięcia niż lasery światłowodowe.
Wybór typu lasera do cięcia metalu zależy od wielu czynników, w tym od grubości i rodzaju ciętego metalu, wymaganej prędkości cięcia, wymaganej dokładności i względów kosztowych. Ponadto postęp w technologii laserowej stale poprawia wydajność i możliwości tych generatorów laserowych w zastosowaniach związanych z cięciem metalu. Należy wybrać odpowiedni typ i konfigurację generatora laserowego w oparciu o specyficzne wymagania projektu cięcia metalu.
Jakie są wady cięcia laserowego metalu?
Cięcie laserowe metalu ma wiele zalet, ale ma też pewne wady i ograniczenia, które należy wziąć pod uwagę przy wyborze tej metody do swojego zastosowania. Oto główne wady cięcia laserowego metalu:
- Wysoki początkowy koszt inwestycji: Zakup maszyny do cięcia laserowego, zwłaszcza wysokiej jakości, może być kosztowny. Początkowe koszty kapitałowe obejmują system cięcia laserowego, powiązany sprzęt (taki jak układy chłodzenia i wydechowe) oraz instalację. Dla małych firm lub tych z ograniczonym budżetem wyższy początkowy koszt inwestycji może być przeszkodą.
- Zużycie energii: Cięcie laserowe jest energochłonne, szczególnie w przypadku stosowania laserów o dużej mocy do cięcia grubych metali. Powoduje to wyższe koszty energii, ale warto zauważyć, że generatory lasera światłowodowego są bardziej energooszczędne niż generatory lasera CO2.
- Wymagania dotyczące konserwacji: Maszyny do cięcia laserowego wymagają regularnej konserwacji, aby zapewnić ich wydajne i dokładne działanie. Z biegiem czasu elementy takie jak soczewki, lusterka i systemy przepływu powietrza wymagają czyszczenia i wymiany. Konserwacja zwiększa koszty operacyjne i przestoje.
- Wykończenie powierzchni: Podczas gdy cięcie laserowe zazwyczaj zapewnia czyste krawędzie, w procesie tym może czasami pozostawić strefę wpływu ciepła (HAZ) i niewielkie odbarwienie powierzchni, szczególnie w przypadku grubszych materiałów. Aby rozwiązać te problemy, mogą być wymagane dodatkowe procesy.
- Ograniczona grubość materiału: Cięcie laserowe może nie być najskuteczniejszą metodą cięcia wyjątkowo grubych materiałów. Grubsze blachy wymagają większej mocy lasera, co spowalnia proces cięcia i zwiększa koszty eksploatacji. W przypadku bardzo grubych materiałów bardziej odpowiednie mogą być inne metody, takie jak cięcie plazmowe lub cięcie strumieniem wody.
- Ograniczenia materiałowe: Chociaż cięcie laserowe umożliwia obróbkę różnych metali, może nie być odpowiednie dla wszystkich typów. Cięcie niektórych specjalności lub stopów specjalnych może być trudne lub proces ten może niekorzystnie wpływać na właściwości materiału.
- Wypaczenia i deformacje: Ciepło wytwarzane podczas procesu cięcia laserowego może powodować wypaczenie lub deformację niektórych materiałów, szczególnie podczas cięcia cienkich arkuszy lub skomplikowanych wzorów, co może mieć wpływ na dokładność i płaskość wycinanych części.
- Kwestie środowiskowe: Chociaż cięcie laserowe jest ogólnie bardziej przyjazne dla środowiska niż inne metody cięcia, nie jest całkowicie wolne od wpływu na środowisko. Stosowanie generatorów laserowych dużej mocy i usuwanie odpadów w dalszym ciągu mają wpływ na środowisko.
- Hałas i dym: Cięcie laserowe może powodować hałas i dym, w zależności od ciętego materiału i parametrów cięcia. Aby zapewnić bezpieczne i wygodne środowisko pracy, może być konieczna odpowiednia wentylacja i środki kontroli hałasu.
- Pytanie zabezpieczające: Cięcie laserowe wymaga użycia wiązek laserowych o dużej intensywności, które w przypadku nieprawidłowego obchodzenia się z nimi mogą stanowić zagrożenie dla bezpieczeństwa operatorów. Odpowiednie przeszkolenie i środki bezpieczeństwa mogą pomóc w zapobieganiu wypadkom, takim jak urazy oczu w wyniku bezpośredniego narażenia na wiązkę lasera.
Pomimo tych niedociągnięć cięcie laserowe pozostaje bardzo wszechstronną i wydajną metodą cięcia metali, szczególnie w zastosowaniach wymagających precyzji, skomplikowanych projektów i minimalnych strat materiału. Oceniając, czy cięcie laserowe jest odpowiednie dla Twojego konkretnego projektu, musisz porównać te wady z wieloma zaletami i wziąć pod uwagę swoje unikalne wymagania i ograniczenia budżetowe.
Jak dokładne jest cięcie laserowe metalu?
Cięcie laserowe charakteryzuje się wyjątkową dokładnością i precyzją, co czyni je jedną z najbardziej precyzyjnych metod cięcia metalu. Dokładność laserowego cięcia metalu może się różnić w zależności od różnych czynników, w tym rodzaju lasera, jakości systemu laserowego, ciętego materiału i wiedzy operatora. Oto kilka ogólnych wskazówek dotyczących dokładności cięcia laserowego:
- Jakość ostrości i wiązki: Właściwe skupienie wiązki lasera i utrzymanie dobrej jakości wiązki przyczynia się do uzyskania wysokiej precyzji cięcia. Mniejsza średnica belki pozwala na dokładniejsze cięcie i większą dokładność. Wycinarki laserowe z zaawansowaną optyką i systemami kontroli wiązki zwykle zapewniają bardziej precyzyjne cięcia.
- Grubość materiału: Grubość ciętego materiału wpływa na dokładność. Cieńsze materiały mają zwykle wyższy poziom dokładności, podczas gdy grubsze materiały mogą mieć nieco większe tolerancje ze względu na takie czynniki, jak rozbieżność wiązki i rozpraszanie ciepła.
- Moc lasera: Moc użytego lasera ma również wpływ na dokładność. Generatory laserowe o większej mocy mogą ciąć grubsze materiały, ale mogą wytwarzać szerszą szczelinę (szerokość cięcia) i większą strefę wpływu ciepła, co może mieć wpływ na dokładność.
- Stabilność stołu do cięcia: Stabilność stołu do cięcia i części mechanicznych maszyny pomaga poprawić dokładność. Solidna i dobrze utrzymana maszyna pomaga uzyskać precyzyjne cięcie.
- Planowanie ścieżki cięcia: Ścieżka, po której podąża laser podczas procesu cięcia, będzie miała wpływ na dokładność cięcia. Zoptymalizowane ścieżki cięcia minimalizują błędy i zwiększają dokładność cięcia.
- Właściwości materiału: Na dokładność cięcia laserowego może mieć wpływ cięty materiał. Niektóre metale, takie jak stal nierdzewna i aluminium, ze względu na swoje właściwości tną dokładniej niż inne, natomiast materiały silnie odblaskowe, takie jak miedź, mogą stanowić wyzwanie w osiągnięciu wysokiej dokładności.
- Kalibracja i konserwacja maszyny: Regularna kalibracja i konserwacja maszyny do cięcia laserowego mają kluczowe znaczenie dla osiągnięcia i utrzymania dokładności. Właściwe ustawienie i rutynowa konserwacja optyki pomagają zapewnić dokładne cięcia.
- Umiejętności operatora: Wiedza operatora odgrywa ważną rolę w uzyskiwaniu precyzyjnych cięć. Wykwalifikowani operatorzy rozumieją, jak zoptymalizować parametry cięcia, wybrać odpowiedni punkt skupienia i zarządzać takimi czynnikami, jak jakość wiązki i strefa wpływu ciepła, aby zachować dokładność.
- Złożoność cięcia: Złożoność wzoru lub projektu cięcia wpływa na dokładność. Proste geometrie często tną dokładniej niż złożone lub bardzo szczegółowe projekty, podczas gdy bardziej złożone i szczegółowe cięcia mogą wymagać dodatkowej uwagi, aby osiągnąć precyzyjne wyniki.
Cięcie laserowe to bardzo precyzyjna metoda cięcia metalu, która umożliwia osiągnięcie wąskich tolerancji, ale wysoka dokładność może się różnić w zależności od różnych czynników. Aby osiągnąć najwyższy poziom dokładności, istotne jest korzystanie z dobrze utrzymanej, wysokiej jakości wycinarki laserowej i dobór odpowiedniego rodzaju lasera do danego materiału. Ponadto ważne jest zatrudnienie wykwalifikowanych operatorów, którzy mogą zoptymalizować parametry cięcia zgodnie z Twoimi konkretnymi wymaganiami, aby osiągnąć wymaganą dokładność cięcia.
Czy maszyny do laserowego cięcia metalu zużywają dużo energii?
Zużycie energii przez maszynę do cięcia laserowego metalu może się znacznie różnić w zależności od wielu czynników, w tym mocy znamionowej maszyny, określonych parametrów cięcia i przetwarzanego materiału. Oto przybliżone szacunki zużycia energii jako ogólne wytyczne:
- Maszyna do cięcia laserowego o mocy 12 kW może zużywać 58,8 kWh (kilowatogodzin) energii elektrycznej na godzinę pracy.
- Maszyna do cięcia laserowego o mocy 15 kW może zużywać 63,8 kWh energii elektrycznej na godzinę pracy.
- Maszyna do cięcia laserowego o mocy 20 kW może zużywać 82,8 kWh energii elektrycznej na godzinę pracy.
Należy pamiętać, że szacunki te są bardzo przybliżone i mogą się różnić w zależności od konstrukcji maszyny, jej wydajności i konfiguracji pod kątem konkretnego zadania cięcia. Ponadto zużycie energii może się zmieniać podczas procesu cięcia, zwłaszcza gdy maszyna pracuje z różnymi prędkościami i poziomami mocy w zależności od części zadania.
Jeśli chcesz uzyskać dokładne informacje o poborze mocy konkretnej maszyny do cięcia laserem światłowodowym, zaleca się zapoznanie się ze specyfikacjami producenta i instrukcją obsługi. Producenci maszyn do cięcia laserowego często podają szczegółowe informacje o wymaganiach dotyczących mocy i efektywności energetycznej maszyny.
Jak konserwować maszyny do cięcia laserowego metalu?
Konserwacja maszyny do cięcia laserowego metalu zapewnia jej trwałość, wydajność i bezpieczeństwo. Oto kilka ogólnych wskazówek dotyczących konserwacji takiej maszyny:
- Regularne czyszczenie: Regularnie czyść maszynę, aby zapobiec gromadzeniu się kurzu, zanieczyszczeń i wiórów metalowych. Użyj miękkiej szczotki, sprężonego powietrza lub odkurzacza, aby usunąć cząsteczki z obszaru cięcia, soczewek, lusterek i innych elementów.
- Sprawdzaj optykę: Często sprawdzaj stan optyki lasera (soczewek i zwierciadeł). Delikatnie czyść je odpowiednimi roztworami do czyszczenia soczewek i niestrzępiącymi się chusteczkami, aby usunąć wszelkie pozostałości lub zabrudzenia, które mogą mieć wpływ na jakość wiązki lasera.
- Sprawdź wyrównanie: Upewnij się, że wiązka lasera jest prawidłowo wyrównana. Niewłaściwe wyrównanie może prowadzić do słabej jakości cięcia i przedwczesnego zużycia podzespołów. Postępuj zgodnie z wytycznymi producenta dotyczącymi procedur wyrównania lub w razie potrzeby skonsultuj się z technikiem.
- Monitoruj dopływ gazu: Upewnij się, że dopływ gazu (zwykle tlenu, azotu lub sprężonego powietrza) jest wystarczający i wolny od zanieczyszczeń. Aby zachować jakość cięcia laserowego, wymieniaj filtry gazu zgodnie z zaleceniami producenta.
- Sprawdzaj i wymieniaj materiały eksploatacyjne: Regularnie sprawdzaj części eksploatacyjne, takie jak dysze, soczewki i okienka ochronne, pod kątem oznak zużycia lub uszkodzeń. Wymień je w razie potrzeby, aby utrzymać jakość cięcia i chronić wrażliwe komponenty.
- Smarowanie: Smaruj ruchome części zgodnie z zaleceniami producenta. Dotyczy to prowadnic liniowych, łożysk i układów napędowych. Używaj odpowiednich środków smarnych, aby zapobiec nadmiernemu zużyciu i zapewnić płynną pracę.
- Aktualizacje oprogramowania: Utrzymuj oprogramowanie sterujące maszyny na bieżąco, aby zapewnić optymalną wydajność i zgodność z nowszymi systemami operacyjnymi. Okresowo sprawdzaj aktualizacje od producenta
- Kalibracja: Okresowo kalibruj maszynę, aby zapewnić dokładność i powtarzalność wymiarów cięcia. Może to obejmować sprawdzenie dokładności układu pozycjonowania głowicy tnącej i w razie potrzeby dostosowanie parametrów.
- Kontrole bezpieczeństwa: Regularnie sprawdzaj funkcje bezpieczeństwa, takie jak przyciski zatrzymania awaryjnego, blokady i osłony zabezpieczające, aby upewnić się, że działają prawidłowo. Natychmiast wymień uszkodzone lub nieprawidłowo działające elementy zabezpieczające.
- Szkolenia i dokumentacja: Upewnij się, że operatorzy zostali odpowiednio przeszkoleni w zakresie bezpiecznej obsługi i konserwacji maszyny do cięcia laserowego. Zapewnij dostęp do dokumentacji, takiej jak instrukcje obsługi, harmonogramy konserwacji i instrukcje rozwiązywania problemów.
- Profesjonalna obsługa: Zaplanuj regularne kontrole konserwacyjne przez wykwalifikowanych techników lub personel serwisowy zgodnie z zaleceniami producenta. Mogą oni wykonywać bardziej szczegółowe inspekcje, regulacje i naprawy, aby utrzymać maszynę w optymalnym stanie.
Przestrzegając tych praktyk konserwacji, możesz mieć pewność, że Twoja maszyna do cięcia laserowego metalu będzie działać wydajnie, niezawodnie i bezpiecznie przez wiele lat.
Jakie środki bezpieczeństwa posiadają maszyny do cięcia laserowego metalu?
W maszynach do cięcia laserowego metalu zastosowano różne środki bezpieczeństwa, aby chronić operatorów, osoby postronne i sam sprzęt. Oto kilka typowych zabezpieczeń występujących w maszynach do cięcia laserowego metalu:
- Obudowy: Maszyny do cięcia laserowego są zwykle obudowane, aby zatrzymać wiązkę lasera i zapobiec narażeniu na promieniowanie. Obudowy mogą mieć zamykające się drzwiczki, które automatycznie wyłączają laser po otwarciu.
- Blokady bezpieczeństwa: Blokady to mechanizmy uniemożliwiające działanie lasera, jeśli nie zostaną spełnione określone warunki, takie jak otwarcie drzwi obudowy lub zdjęcie pokryw maszyny. Pomaga to zapobiec przypadkowemu narażeniu na wiązkę lasera.
- Przycisk zatrzymania awaryjnego: Maszyny do cięcia laserowego są wyposażone w przyciski zatrzymania awaryjnego, które natychmiast wyłączają maszynę w przypadku sytuacji awaryjnej lub gdy pojawią się zagrożenia związane z bezpieczeństwem. Przyciski te są łatwo dostępne dla operatorów.
- Powstrzymywanie wiązki: Maszyny do cięcia laserowego wykorzystują systemy powstrzymywania wiązki, aby zapobiec ucieczce wiązki lasera z obszaru cięcia. Może to obejmować pułapki wiązki, bloki wiązki lub inne środki pochłaniające lub przekierowujące energię lasera.
- Odciąganie oparów: Cięcie laserowe generuje opary i dym, które mogą być niebezpieczne dla zdrowia. Maszyny są wyposażone w systemy odciągu oparów, które usuwają te zanieczyszczenia z obszaru cięcia i bezpiecznie odprowadzają je na zewnątrz maszyny.
- Automatyczne wyłączanie: Niektóre maszyny do cięcia laserowego są wyposażone w czujniki wykrywające nieprawidłowości, takie jak przegrzanie, nadmierne wibracje lub wahania mocy. Czujniki te mogą wywołać automatyczne wyłączenie, aby zapobiec uszkodzeniu maszyny lub potencjalnym zagrożeniom bezpieczeństwa.
- Okulary ochronne: Operatorzy i personel pracujący w pobliżu maszyny do cięcia laserowego powinni nosić odpowiednie okulary lub gogle ochronne, aby chronić oczy przed bezpośrednim lub odbitym promieniowaniem laserowym.
- Szkolenia i certyfikacja: Operatorzy powinni przejść odpowiednie szkolenie w zakresie bezpiecznej obsługi maszyn do cięcia laserowego. Programy szkoleniowe obejmują takie tematy, jak obsługa maszyn, konserwacja, protokoły bezpieczeństwa i procedury awaryjne. Do obsługi urządzenia może być wymagana certyfikacja.
- Znaki i etykiety ostrzegawcze: Maszyny do cięcia laserowego są wyposażone w znaki ostrzegawcze i etykiety wskazujące potencjalne zagrożenia i środki ostrożności. Pomagają one operatorom i osobom postronnym w zrozumieniu zagrożeń związanych z maszyną i sposobie jej bezpiecznej obsługi.
- Zdalne monitorowanie: Niektóre maszyny do cięcia laserowego mają funkcje zdalnego monitorowania, które pozwalają operatorom monitorować działanie i wydajność maszyny z odległości. Może to pomóc we wczesnym identyfikowaniu potencjalnych problemów bezpieczeństwa lub awarii.
Dzięki zastosowaniu tych środków bezpieczeństwa laserowe maszyny do cięcia metalu zapewniają bezpieczną pracę i minimalizują ryzyko wypadków lub obrażeń w środowisku przemysłowym.
Czy istnieje ryzyko deformacji podczas cięcia laserowego metalu?
Tak, istnieje ryzyko odkształcenia podczas cięcia laserowego metalu, szczególnie w przypadku niektórych metali i pod pewnymi warunkami. Odkształcenie może wystąpić z powodu kilku czynników:
- Strefa wpływu ciepła (HAZ): Cięcie laserowe generuje intensywne ciepło, które może spowodować powstanie strefy wpływu ciepła (HAZ) w metalu otaczającym cięcie. W niektórych przypadkach ciepło to może prowadzić do miejscowego stopienia lub wypaczenia, powodując deformację wzdłuż krawędzi cięcia.
- Grubość materiału: Grubsze materiały metalowe są bardziej podatne na odkształcenia podczas cięcia laserowego, szczególnie jeśli moc lasera i prędkość cięcia nie są zoptymalizowane pod kątem grubości materiału. Większa moc lasera i mniejsza prędkość cięcia mogą zwiększyć ilość ciepła przekazywanego do materiału, zwiększając ryzyko odkształcenia.
- Skład materiału: Skład ciętego metalu może wpływać na jego podatność na odkształcenia. Na przykład metale o wysokiej przewodności cieplnej, takie jak miedź czy aluminium, mogą szybciej odprowadzać ciepło, zmniejszając ryzyko odkształcenia w porównaniu z materiałami o niższej przewodności cieplnej, takimi jak stal nierdzewna.
- Mocowanie i zaciskanie: Prawidłowe mocowanie i zaciskanie blachy podczas cięcia laserowego jest niezbędne, aby zminimalizować ryzyko deformacji. Bezpieczne trzymanie materiału na miejscu pomaga zapobiegać ruchom i wibracjom podczas cięcia, które mogą przyczynić się do zniekształceń lub wypaczeń.
- Podgrzewanie wstępne i chłodzenie po cięciu: W niektórych przypadkach wstępne podgrzewanie blachy przed cięciem laserowym lub zastosowanie technik chłodzenia po cięciu może pomóc zmniejszyć ryzyko odkształcenia. Podgrzewanie wstępne może zminimalizować szok termiczny, a kontrolowane chłodzenie może pomóc złagodzić naprężenia szczątkowe w metalu.
- Kalibracja i ustawienia maszyny: Właściwa kalibracja maszyny do cięcia laserowego i optymalizacja parametrów cięcia, takich jak moc lasera, prędkość cięcia i ciśnienie powietrza pomocniczego, mogą pomóc w uzyskaniu czystych, precyzyjnych cięć przy minimalnych zniekształceniach.
Aby zmniejszyć ryzyko deformacji podczas cięcia laserowego metalu, należy dokładnie rozważyć te czynniki i odpowiednio dostosować parametry cięcia. Ponadto wybranie odpowiedniej metody cięcia laserowego i sprzętu do konkretnego metalu i zastosowania może pomóc zminimalizować deformację i zapewnić wysokiej jakości rezultaty.
Powiązane zasoby
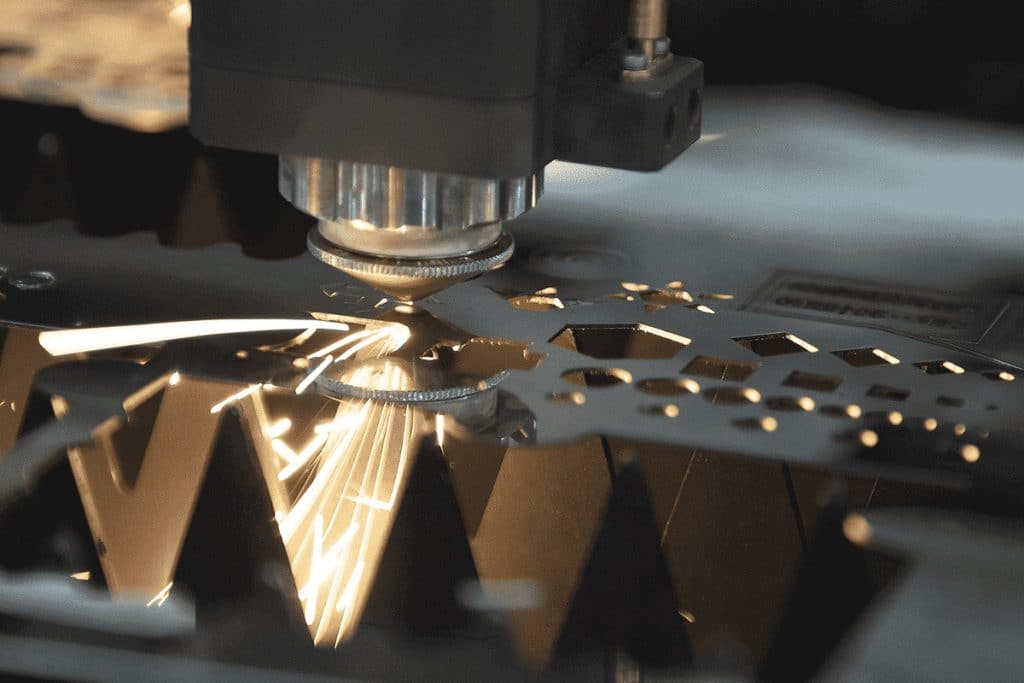
Wpływ autofokusa na dokładność cięcia maszyny do cięcia laserem światłowodowym
W artykule omówiono definicję i rodzaje technologii autofokusa oraz jej wpływ na dokładność cięcia laserem światłowodowym, a także przeanalizowano wyzwania i rozwiązania optymalizacyjne, z którymi musi się zmierzyć, aby usprawnić produkcję.
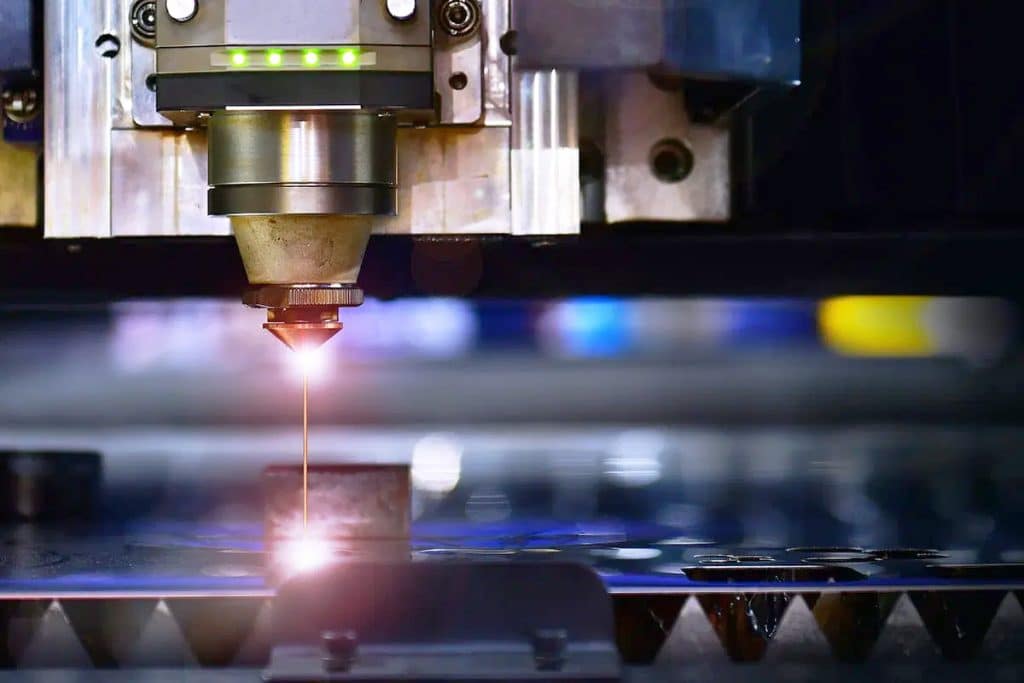
Wpływ jakości wiązki lasera światłowodowego na dokładność i jakość cięcia
Jakość wiązki lasera światłowodowego ma istotny wpływ na dokładność, wydajność i jakość powierzchni cięcia laserowego. Optymalizacja jakości wiązki może znacznie poprawić efekt cięcia
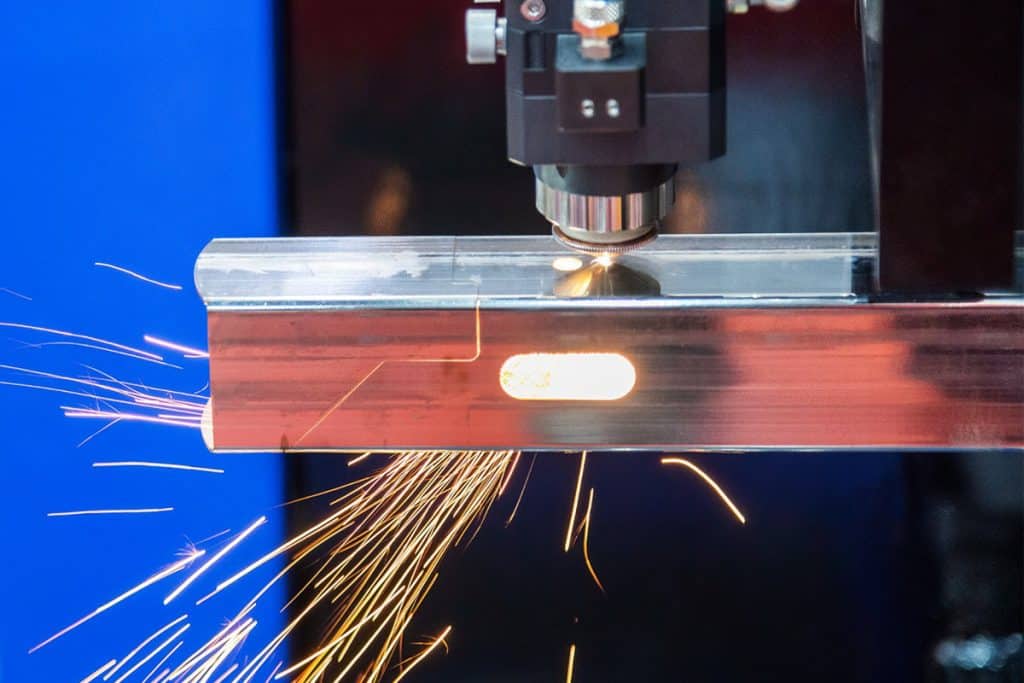
Zrozumienie kosztów operacyjnych: czynniki wpływające na koszty maszyn do cięcia laserem światłowodowym
W tym artykule szczegółowo przeanalizowano kluczowe czynniki wpływające na koszty eksploatacji maszyn do cięcia laserem światłowodowym i przedstawiono strategie optymalizacji, które pomogą firmom obniżyć koszty i zwiększyć wydajność.