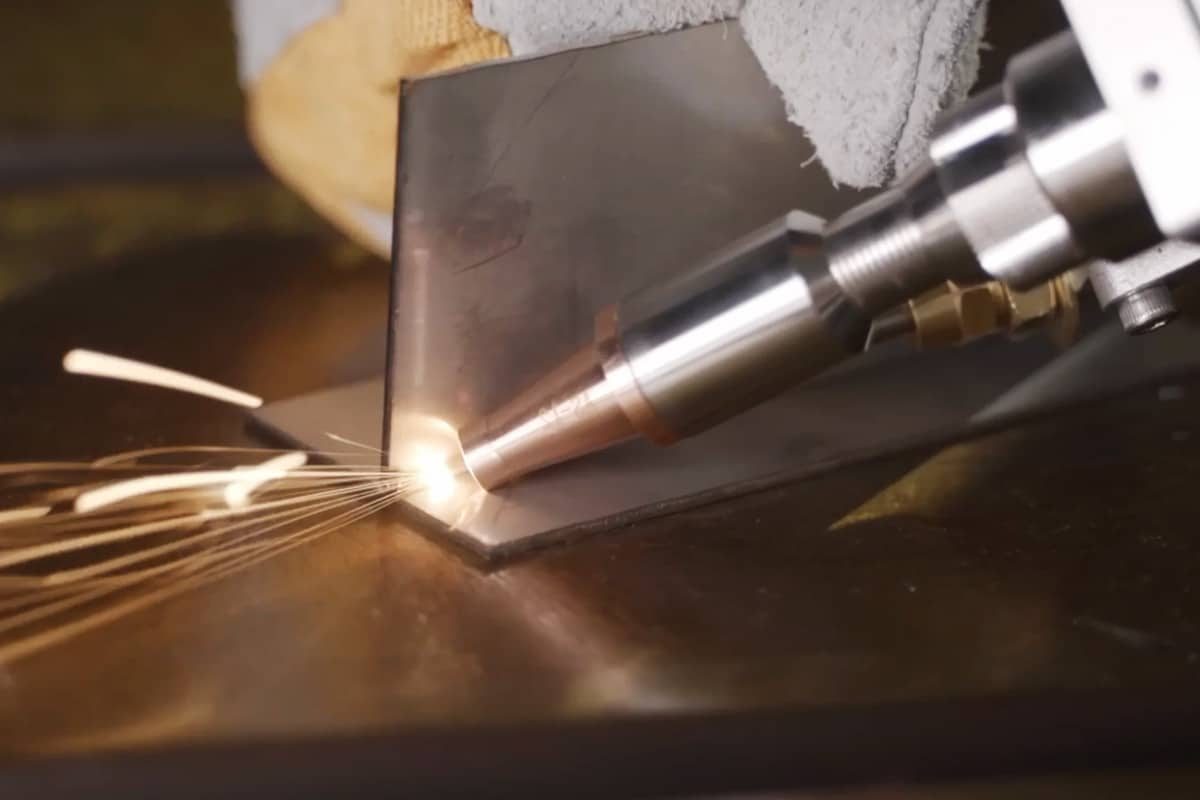
Projektowanie połączeń spawanych laserowo
Spawanie laserowe jest szeroko stosowane w przemyśle lotniczym, samochodowym, elektronicznym, medycznym i innych gałęziach przemysłu ze względu na wysoką precyzję, niskie ciepło dopływowe i wysoką wydajność. W porównaniu z tradycyjnymi metodami spawania, spawanie laserowe ma zalety wąskich spoin, dużej prędkości spawania, małej strefy wpływu ciepła i niskiego odkształcenia, co czyni je idealnym wyborem dla obszarów produkcyjnych o dużym zapotrzebowaniu. Jednak pomimo wielu zalet spawania laserowego, stabilność jakości spawania i niezawodność produktu końcowego nadal w dużym stopniu zależą od konstrukcji spoiny. Rozsądna konstrukcja spoiny może zapewnić integralność i wytrzymałość mechaniczną spoiny oraz zmniejszyć wady, takie jak pęknięcia, pory i penetrację spoiny, które mogą wystąpić podczas procesu spawania, jednocześnie optymalizując energię dopływową, poprawiając wydajność produkcji i zmniejszając szybkość przeróbek i koszty produkcji.
W zastosowaniach spawania laserowego, projekt połączenia musi uwzględniać wiele czynników, w tym właściwości metalurgiczne podłoża, metodę spawania, moc lasera, kształt spoiny, dokładność montażu i późniejsze wymagania dotyczące przetwarzania. Doskonały projekt połączenia może w pełni wykorzystać zalety spawania laserowego, aby uzyskać wysokiej jakości, niedrogie wyniki spawania. W tym artykule szczegółowo zbadamy podstawowe zasady, czynniki wpływające i strategie optymalizacji projektowania połączeń spawania laserowego, aby pomóc firmom i inżynierom poprawić jakość spawania, zoptymalizować procesy produkcyjne i wydłużyć żywotność konstrukcji spawanych w praktycznych zastosowaniach.
Spis treści
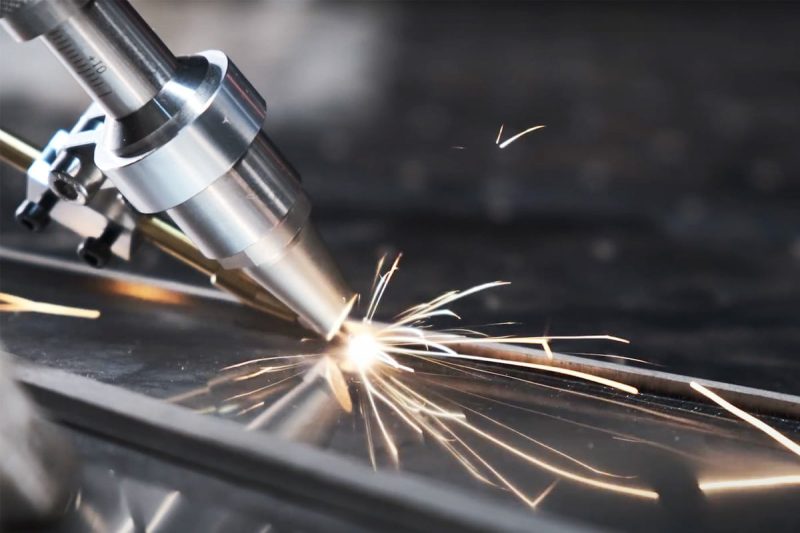
Podstawowe zasady projektowania połączeń spawanych laserowo
Jako wysoce precyzyjny i wydajny proces spawania, spawanie laserowe jest szeroko stosowane w takich branżach jak produkcja samochodów, lotnictwo, sprzęt elektroniczny i urządzenia medyczne. Rozsądna konstrukcja złącza spawanego ma kluczowe znaczenie dla integralności, wytrzymałości i wydajności produkcji spoiny. Zoptymalizowana konstrukcja złącza może nie tylko zmniejszyć wady spawania i poprawić jakość spawania, ale także obniżyć koszty produkcji i poprawić ogólną wydajność produkcji. W tym artykule omówiono kluczowe elementy złączy spawania laserowego i ich rolę w optymalizacji jakości spawania, a także przeanalizowano, jak osiągnąć wydajne i stabilne wyniki spawania dzięki naukowemu projektowaniu.
Kluczowe elementy połączeń spawanych laserowo
Podłoże
Wybór materiału bazowego bezpośrednio wpływa na jakość spawania i wydajność produktu końcowego. Przy wyborze materiałów spawalniczych należy wziąć pod uwagę kilka kluczowych czynników:
- Właściwości mechaniczne: Wytrzymałość, twardość, ciągliwość i inne właściwości materiału wpływają na stabilność połączenia spawanego.
- Właściwości metalurgiczne: obejmują skład stopu, kompatybilność i zmiany mikrostruktury materiału po spawaniu, aby zapewnić niezawodność spoiny.
- Przewodność cieplna i temperatura topnienia: wpływają na absorpcję i transfer energii lasera. Materiały o wysokiej przewodności cieplnej (takie jak miedź) mogą wymagać generatora laserowego o większej mocy, podczas gdy materiały o niskiej przewodności cieplnej (takie jak tytan) powinny unikać uszkodzeń strukturalnych spowodowanych przegrzaniem.
Konfiguracja złącza
Różne typy konfiguracji połączeń są odpowiednie dla różnych potrzeb spawalniczych. Typowe typy połączeń obejmują:
- Złącze doczołowe: Nadaje się do zastosowań spawalniczych wymagających dużej wytrzymałości, charakteryzuje się doskonałą wydajnością spoiny, ale wymaga wysokiej dokładności obróbki.
- Złącze zakładkowe: Nadaje się do spawania cienkich blach; prosty proces i duża prędkość spawania, należy jednak zwrócić uwagę na ograniczenie koncentracji naprężeń.
- Złącze T: powszechnie stosowane w spawaniu konstrukcyjnym, charakteryzujące się dużą nośnością spoiny, ale konieczne jest zapewnienie odpowiedniego wtopienia, aby uniknąć wad spawalniczych.
Ponadto podczas procesu spawania rozmiar szczeliny, dokładność montażu i wyrównanie połączenia będą miały bezpośredni wpływ na jakość spoiny. Optymalizacja tych parametrów może zmniejszyć odkształcenie spawania i poprawić wytrzymałość połączenia.
Materiał wypełniający
W niektórych zastosowaniach spawania laserowego materiały wypełniające mogą być używane do optymalizacji jakości spoiny. Główne efekty obejmują:
- Zwiększa wytrzymałość spoiny, zapobiega pęknięciom spoiny i poprawia właściwości mechaniczne spoiny.
- Dostosowanie właściwości metalurgicznych i poprawa struktury spoiny poprzez optymalizację składu stopu.
- Zmniejszenie liczby wad spawalniczych, takich jak pory i braki wtopu, oraz poprawa stabilności spawania.
Wybór materiału dodatkowego powinien odpowiadać charakterystyce materiału bazowego i być odpowiednio dostosowany do procesu spawania.
Kluczowe elementy połączeń spawanych laserowo
Zoptymalizowany projekt złącza spawanego musi jednocześnie spełniać następujące cele:
- Zapewnij integralność i wytrzymałość spoiny: Zaprojektuj racjonalnie strukturę połączenia, aby zapewnić dobre zespolenie i wystarczającą wytrzymałość mechaniczną w obszarze spawania.
- Zmniejsz liczbę wad spawalniczych: Zredukuj typowe problemy, takie jak pory, pęknięcia i braki w łączeniu, poprzez optymalizację doboru materiałów, struktury połączeń i procesu spawania.
- Optymalizacja wydajności i produktywności procesu: zaprojektuj rozsądną konfigurację połączeń, aby zwiększyć prędkość spawania, zmniejszyć ilość odpadów materiałowych i obniżyć koszty przetwarzania, co przełoży się na poprawę ogólnej wydajności produkcji.
Projektowanie połączeń spawanych laserowo ma kluczowe znaczenie dla jakości spawania i wydajności produkcji. Poprzez racjonalny wybór materiału bazowego, optymalizację struktury połączenia i materiałów wypełniających oraz precyzyjne dostrojenie procesu spawania, jakość spawania może zostać skutecznie poprawiona, wady mogą zostać zredukowane, a wydajność produkcji może zostać poprawiona. Naukowe projektowanie połączeń może nie tylko zapewnić wytrzymałość i stabilność spoiny, ale także zoptymalizować proces produkcyjny, pomagając firmom utrzymać konkurencyjność w dziedzinie produkcji o wysokiej precyzji.
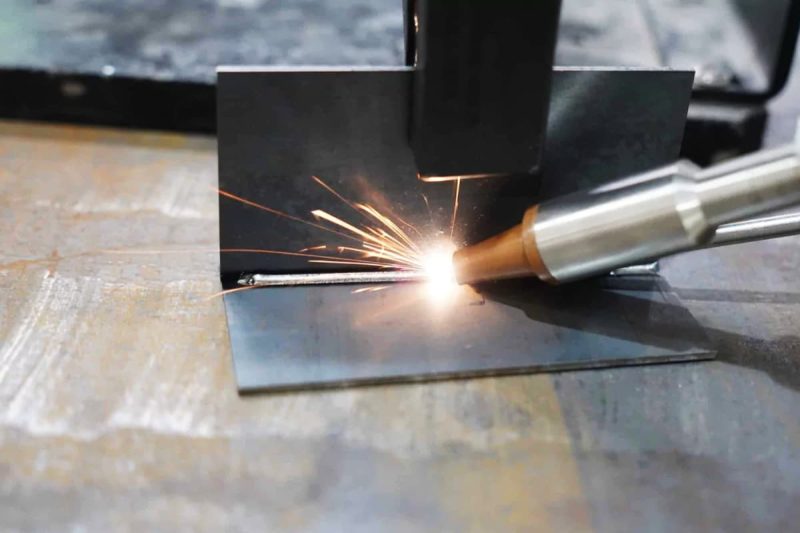
Czynniki wpływające na projekt złącza spawanego laserowo
Projektowanie połączeń spawanych laserowo nie tylko obejmuje wybór podstawowych struktur, ale jest również uwarunkowane wieloma czynnikami, w tym właściwościami materiału, konfiguracją połączenia, parametrami spawania i wymaganiami aplikacji. Właściwe uwzględnienie tych czynników może pomóc zoptymalizować jakość spawania, poprawić wytrzymałość spoiny, zmniejszyć liczbę defektów i poprawić wydajność produkcji.
Właściwości materiału
Właściwości fizyczne i chemiczne podłoża odgrywają kluczową rolę w wydajności połączeń spawanych laserowo. Podczas projektowania połączeń spawanych ważne jest skupienie się na następujących kluczowych aspektach:
- Zgodność podłoża: Zgodność spawalnicza różnych materiałów metalowych decyduje o jakości spoiny. Na przykład stopy o podobnym składzie zwykle mają dobre właściwości topienia, podczas gdy spawanie różnych metali może powodować pęknięcia lub wady spawalnicze z powodu różnych współczynników rozszerzalności cieplnej lub tworzenia kruchych związków międzymetalicznych.
- Właściwości mechaniczne i metalurgiczne: Właściwości mechaniczne (takie jak twardość, ciągliwość i wytrzymałość na rozciąganie) wpływają na niezawodność spoiny. Właściwości metalurgiczne określają zmiany w elementach stopowych podczas spawania. Na przykład niektóre stale wysokowęglowe mogą wytwarzać utwardzone struktury podczas spawania, zwiększając ryzyko pęknięć. Dlatego parametry procesu spawania muszą być dostosowane do różnych właściwości materiału, aby zapewnić jakość spawania.
- Przewodność cieplna i temperatura topnienia: Przewodność cieplna i temperatura topnienia materiału wpływają na transmisję i absorpcję energii lasera. Na przykład metale o wysokiej przewodności cieplnej (takie jak miedź I aluminium) szybko rozpraszają ciepło i wymagają większej mocy lasera lub bardziej skoncentrowanego wkładu energii. Materiały o wyższych temperaturach topnienia mogą wymagać zwiększonej energii spawania, aby zapewnić wystarczające topienie i wytrzymałość połączenia.
Konfiguracja złącza
Rodzaj, dokładność montażu i wyrównanie połączenia mają bezpośredni wpływ na stabilność procesu spawania i jakość spoiny. Typowe typy połączeń obejmują:
- Złącze doczołowe: Nadaje się do scenariuszy spawania wymagających wysokiej wytrzymałości i niskiego odkształcenia. Szczelina złącza doczołowego musi być ściśle kontrolowana, aby zapewnić całkowite zespolenie i uniknąć wad, takich jak niepełne zespolenie lub wtrącenia żużla.
- Złącze zakładkowe: Nadaje się do spawania cienkich płyt, zachodząca na siebie część spoiny może zapewnić lepszą wytrzymałość. Jednak ze względu na efekt układania w stos gaz może pozostać w szczelinie, a parametry spawania muszą zostać zoptymalizowane w celu zmniejszenia porowatości.
- Złącze T: Zwykle stosowane w przypadku elementów konstrukcyjnych, które wytrzymują większe naprężenia. Spawanie złączy T musi zapewnić wystarczającą penetrację, aby uniknąć pęknięć spowodowanych koncentracją naprężeń.
Ponadto przy projektowaniu połączeń spawanych należy uwzględnić również:
- Montaż i wielkość szczeliny: Zbyt duża szczelina może skutkować niewystarczającym wypełnieniem spoiny, natomiast zbyt mała szczelina może skutkować niepełnym połączeniem lub odkształceniem spoiny. Dlatego dokładny montaż i kontrola szczeliny są kluczowe dla jakości spawania.
- Transmisja wiązki laserowej i kanał obróbki części: Upewnij się, że wiązka laserowa może płynnie dotrzeć do obszaru spawania, aby uniknąć wpływu na efekt spawania z powodu przeszkód lub odbić wiązki. Jednocześnie w zautomatyzowanej linii produkcyjnej należy zoptymalizować metodę mocowania części i konstrukcję kanału spawalniczego, aby zapewnić stabilność i spójność spawania.
Parametry spawania
Rozsądne dostosowanie parametrów spawania może zoptymalizować jakość spoiny i zmniejszyć wady spawania. Typowe kluczowe parametry obejmują:
- Moc lasera: wpływa na głębokość spawania i formowanie się jeziorka stopionego. Wysoka moc nadaje się do spawania z głębokim wtopieniem, podczas gdy niska moc nadaje się do spawania precyzyjnego.
- Pozycja ogniska i średnica wiązki: Dokładna kontrola ogniska wpływa na gęstość energii i głębokość spawania. Mniejsze średnice wiązki nadają się do spawania o wysokiej precyzji, podczas gdy większe wiązki można stosować do szerokich wymagań spawalniczych.
- Prędkość spawania i kierunek ruchu: Zbyt duża prędkość spawania może prowadzić do niewystarczającej penetracji i wpłynąć na wytrzymałość spoiny, natomiast zbyt mała może powodować odkształcenie spawania lub rozszerzenie strefy wpływu ciepła (HAZ). Dlatego prędkość spawania należy dostosować w połączeniu z materiałem i strukturą złącza.
- Kontrola gazu osłonowego i atmosfery: Odpowiedni gaz osłonowy (taki jak argon, azot lub gaz mieszany) może zmniejszyć utlenianie podczas spawania i zoptymalizować jakość spoiny. Różne materiały mają różne wymagania dotyczące gazu. Na przykład stopy tytanu muszą być całkowicie odizolowane od tlenu, podczas gdy Stal nierdzewna można zabezpieczyć argonem w celu zmniejszenia przebarwień i utleniania podczas spawania.
Wymagania aplikacyjne
Oprócz czynników związanych z materiałem i procesem, projekt złącza spawanego musi także spełniać wymagania konkretnych scenariuszy zastosowań, w tym:
- Wymagania funkcjonalne i strukturalne: Wybierz odpowiedni typ połączenia i strukturę spoiny w oparciu o końcowe zastosowanie produktu. Na przykład spawanie laserowe w przemyśle motoryzacyjnym zwykle wymaga wysokiej wytrzymałości i lekkości, podczas gdy spawanie urządzeń elektronicznych kładzie nacisk na udoskonalenie i kontrolę strefy wpływu ciepła.
- Wykończenie powierzchni i wygląd: W niektórych zastosowaniach, takich jak elektronika użytkowa lub urządzenia medyczne, estetyka spoiny ma kluczowe znaczenie. Wymaga to optymalizacji parametrów spawania, zmniejszenia odprysków i żużla spawalniczego oraz poprawy wykończenia powierzchni.
- Obróbka po spawaniu i obróbka wtórna: Niektóre procesy spawalnicze mogą wymagać dodatkowej obróbki końcowej, takiej jak szlifowanie, obróbka cieplna lub powlekanie, aby spełnić standardy jakościowe produktu końcowego. Dlatego przy projektowaniu połączeń spawanych należy również wziąć pod uwagę wykonalność i koszt późniejszej obróbki.
Na projekt połączeń spawanych laserowo wpływa wiele czynników, w tym charakterystyka podłoża, konfiguracja połączenia, parametry spawania i wymagania końcowej aplikacji. Poprzez racjonalny dobór materiałów, optymalizację struktury połączenia, dokładne kontrolowanie parametrów procesu spawania i dostosowywanie do konkretnych wymagań aplikacji, jakość spawania może zostać skutecznie poprawiona, wady mogą zostać zredukowane, a wydajność produkcji może zostać poprawiona. Naukowy i rozsądny projekt połączenia może nie tylko zapewnić wytrzymałość i stabilność spoiny, ale także zoptymalizować proces produkcyjny, poprawiając konkurencyjność produkcji przy jednoczesnym zapewnieniu jakości produktu.
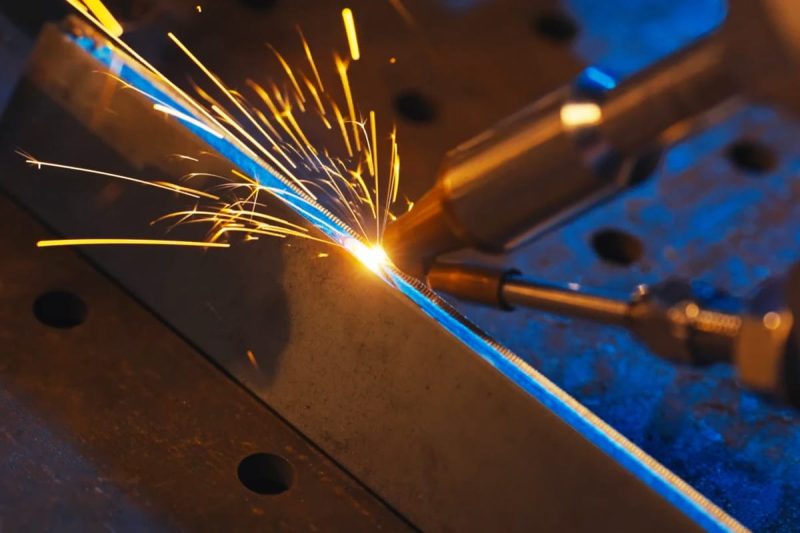
Strategia optymalizacji dla projektowania połączeń spawanych laserowo
Celem optymalizacji projektu złącza spawanego laserowo jest poprawa jakości spawania, zapewnienie integralności i wytrzymałości spoiny, zmniejszenie liczby defektów i poprawa wydajności produkcji. Główne strategie optymalizacji obejmują następujące aspekty:
Zminimalizuj strefę wpływu ciepła (HAZ)
Duża strefa wpływu ciepła (HAZ) może wpływać na właściwości materiału, a nawet powodować kruchość spoiny. Poprzez optymalizację mocy lasera, prędkości spawania i skupienia wiązki, można skutecznie kontrolować dopływ ciepła, aby zmniejszyć strefę wpływu ciepła. Ponadto rozsądny wybór typów połączeń, takich jak połączenia czołowe lub zakładkowe, może również pomóc zmniejszyć gromadzenie się ciepła i poprawić stabilność spawania.
Poprawa wytrzymałości spoiny
Kluczem do zapewnienia wytrzymałości spoin jest optymalizacja rozprowadzania ciepła, kontrolowanie wielkości szczeliny i dokładne ustawienie obrabianych elementów. Prawidłowy proces spawania może zmniejszyć koncentrację naprężeń i uniknąć problemów, takich jak brak fuzji. W niektórych zastosowaniach użycie dopasowanych materiałów wypełniających może poprawić wiązanie spoiny i poprawić ogólną wytrzymałość i trwałość połączenia.
Zapewnij jakość spawania
Na jakość spawania wpływa wiele czynników, w tym moc lasera, pozycja ogniskowania, prędkość spawania i użycie gazu osłonowego. Rozsądne dostosowanie tych parametrów może zmniejszyć wady, takie jak pory i pęknięcia. Ponadto wykorzystanie technologii monitorowania online do kontroli jakości może zapewnić spójność spoiny i poprawić wskaźnik kwalifikacji produktu.
Optymalizacja konstrukcji połączeń spawanych laserowo jest ważnym sposobem na poprawę jakości spawania i wydajności produkcji. Zmniejszając strefę wpływu ciepła, zwiększając wytrzymałość spoiny i ściśle kontrolując jakość spawania, można skutecznie poprawić efekt spawania, aby spełnić wysokie standardy produkcji przemysłowej.
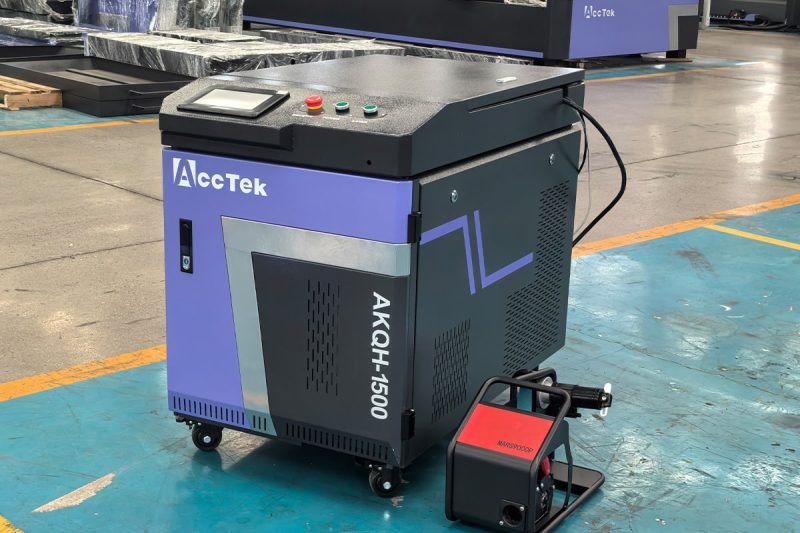
Podsumować
Projekt złącza spawanego laserowo jest kluczowym czynnikiem decydującym o jakości spawania i wydajności produkcji. Głębokie zrozumienie podstawowych zasad, czynników wpływających i strategii optymalizacji projektowania złącza pozwala producentom zapewnić integralność spoiny, zmniejszyć liczbę defektów i poprawić ogólną jakość spawania. Rozsądny projekt złącza może nie tylko poprawić wytrzymałość spawania, ale także zoptymalizować proces produkcji, aby sprostać potrzebom różnych scenariuszy zastosowań.
Jeżeli poszukują Państwo wydajnych i precyzyjnych rozwiązań w zakresie spawania laserowego, Laser AccTek oferuje zaawansowane spawarka laserowas, które spełniają najwyższe standardy jakości i wydajności. Nasz sprzęt wykorzystuje zaawansowaną technologię laserową, aby zapewnić stabilność i spójność spawania, co pomoże Ci osiągnąć cele produkcyjne. Skontaktuj się z nami aby dowiedzieć się więcej o tym, jak nasze produkty mogą pomóc Ci zoptymalizować proces spawania!
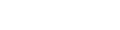
Informacje kontaktowe
- [email protected]
- [email protected]
- +86-19963414011
- Nr 3 Strefa A, strefa przemysłowa Lunzhen, miasto Yucheng, prowincja Shandong.
Uzyskaj rozwiązania laserowe