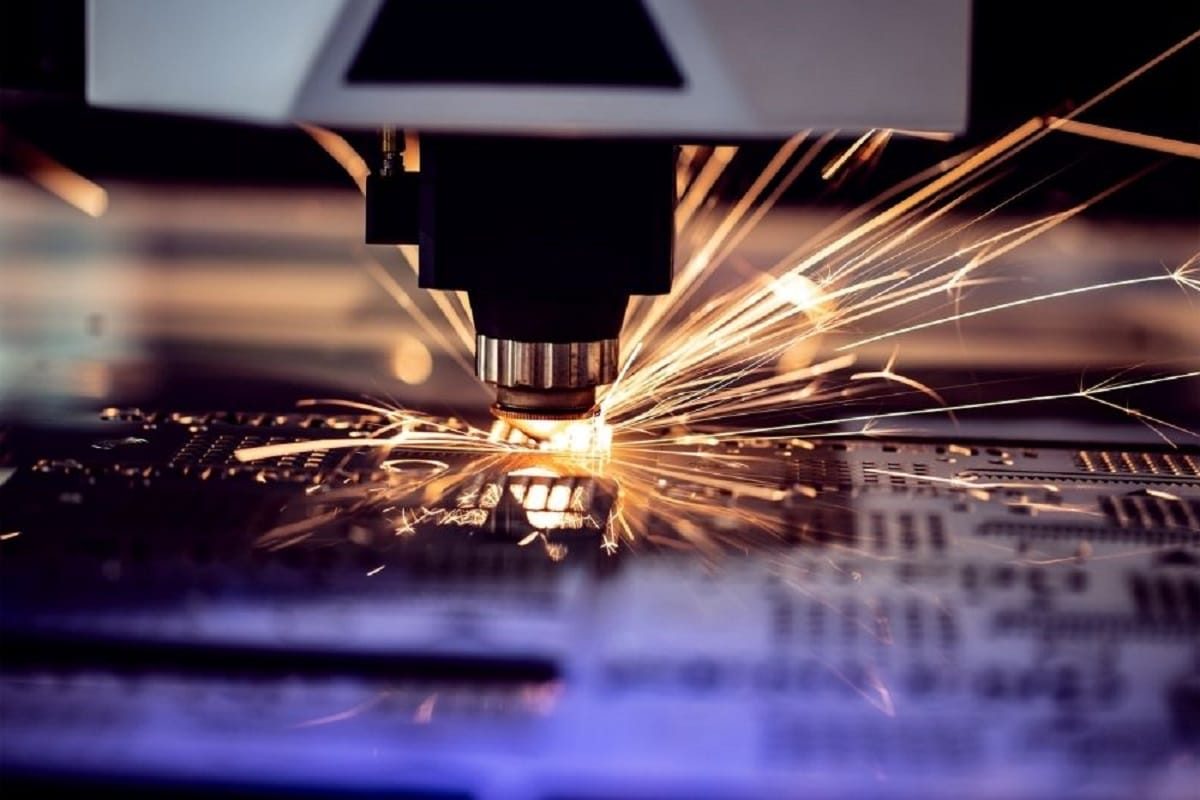
Rozważania projektowe dotyczące cięcia laserowego
Cięcie laserowe stała się wszechstronną i precyzyjną technologią mającą zastosowanie w różnych gałęziach przemysłu, od produkcji po sztukę i projektowanie. Jednocześnie jego zdolność do tworzenia skomplikowanych wzorów, szczegółowych cięć i czystych krawędzi sprawia, że jest to pierwszy wybór w przypadku wielu projektów. Jednakże, jak każdy proces, cięcie laserowe ma swój własny zestaw zagadnień projektowych i ograniczeń, które projektanci i inżynierowie muszą pokonać, aby osiągnąć pożądane wyniki cięcia. W tym artykule szczegółowo zbadamy te czynniki projektowe.
Spis treści
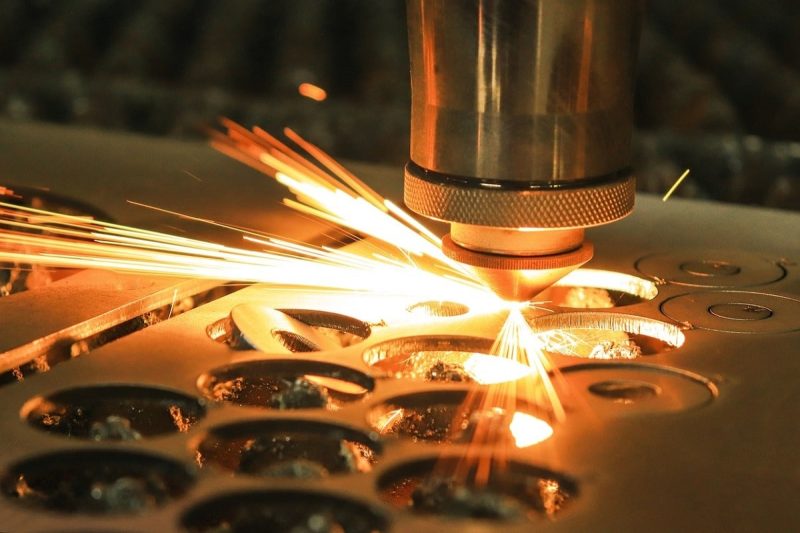
Zagadnienia dotyczące projektowania wnętrz
Rozważania dotyczące projektowania wnętrz z wykorzystaniem technologii cięcia laserowego skupiają się na specyficznych cechach, kształtach i cechach samego projektu. Czynności te pomogą zapewnić, że Twój projekt będzie dobrze dostosowany do technologii cięcia laserowego i mogą mieć wpływ na powodzenie procesu cięcia i jakość produktu końcowego. Poniżej przedstawiono kluczowe kwestie związane z projektowaniem wnętrz w przypadku stosowania cięcia laserowego:
Zamknięte kształty i perforacje
- Cięcie laserowe jest najskuteczniejsze podczas pracy z zamkniętymi kształtami lub konturami. Ponieważ te kształty utrzymują materiał stabilny podczas procesu cięcia i ułatwiają dokładne śledzenie lasera.
- Jeżeli w projekcie uwzględnione są perforacje (otwory), należy zadbać o to, aby były one rozmieszczone w odpowiednich odstępach i były na tyle duże, aby uniknąć deformacji materiału lub trudności w cięciu. Weź pod uwagę grubość materiału i możliwości generatora laserowego.
Wymiary i tolerancje elementów
Cechy konstrukcyjne powinny być zgodne z funkcjonalnością generatora laserowego i grubością użytego materiału. Należy skupić się na następujących aspektach:
- Wymiary elementów: Zwróć szczególną uwagę na elementy projektu, takie jak otwory, szczeliny i nacięcia. Upewnij się, że mają one odpowiedni rozmiar do grubości materiału i możliwości lasera. Charakterystyki wydajności mogą nie być osiągalne lub mogą wymagać specjalistycznego sprzętu laserowego.
- Tolerancje: Uwzględnij w projekcie odpowiednie tolerancje, aby uwzględnić szerokość wiązki lasera (rzaz) i wszelkie potencjalne różnice materiałowe. Właściwe tolerancje pomagają zapewnić dokładne dopasowanie części po cięciu.
Ostre narożniki i promienie wewnętrzne
- Niezwykle ostre narożniki projektu mogą stanowić wyzwanie dla cięcia laserowego. Ponieważ wiązka lasera ma ograniczoną średnicę, ma tendencję do wytwarzania lekkiego zaokrąglenia.
- Aby poprawić dokładność cięcia, rozważ dodanie do projektu małych zaokrągleń lub zaokrąglonych narożników. Upewnij się, że promień wewnętrzny jest zaprojektowany tak, aby pasował do średnicy wiązki lasera, aby uniknąć niezamierzonych cięć lub usuwania materiału.
Kompatybilność materiałowa
- Upewnij się, że materiały wybrane do Twojego projektu są kompatybilne z procesem cięcia laserowego. Różne materiały mają różne właściwości chłonne i możliwości cięcia.
- Dowiedz się, jak wybrane materiały zachowują się w warunkach cięcia laserowego, aby móc odpowiednio zoptymalizować swoje projekty.
Złożoność projektu
- Cięcie laserowe doskonale nadaje się do skomplikowanych projektów i możesz skorzystać z tej funkcji, projektując szczegółowe i precyzyjne wzory.
- Jednak uzyskanie niezwykle drobnych szczegółów za pomocą cięcia laserowego, szczególnie tych mniejszych niż średnica wiązki lasera (rzazu), może być wyzwaniem.
Kompensacja cięcia
- Aby dostosować projekt, należy wziąć pod uwagę szerokość wiązki lasera (nacięcia), co może obejmować lekkie przecięcie linii do wewnątrz, aby uzyskać pożądany rozmiar części.
Zagnieżdżanie
- Jeśli planujesz zagnieżdżać wiele części lub wzorów na jednym arkuszu materiału, zaprojektuj w sposób optymalizujący wykorzystanie materiału, zapewniając jednocześnie wystarczające odstępy między częściami, aby uniknąć kolizji podczas cięcia.
Grubość materiału
- Cechy konstrukcyjne powinny być zgodne z grubością użytego materiału. Jeśli Twój projekt uwzględnia różne grubości materiału, upewnij się, że Twoja maszyna do cięcia laserowego jest odpowiednio skonfigurowana, aby wytrzymać te różnice.
Kierunek usłojenia materiału
- Weź pod uwagę kierunek słojów materiału, zwłaszcza materiałów takich jak drewno lub niektóre metale. Dostosuj swój projekt, aby dopasować go do kierunku słojów lub dostosować do niego, aby uzyskać lepsze rezultaty.
Cechy wewnętrzne i wnęki
- Maszyny do cięcia laserowego mogą nie mieć dostępu do wewnętrznych elementów lub wgłębień w materiałach, dlatego należy odpowiednio zaplanować projekt i rozważyć alternatywne metody produkcji, jeśli wymagane są wewnętrzne cięcia.
Uwzględniając te wewnętrzne kwestie projektowe, można zoptymalizować projekt cięcia laserowego, zwiększyć wydajność i dokładność procesu cięcia oraz zapewnić, że ostateczna wycięta część spełnia wymagania projektu. Współpraca z doświadczonym dostawcą usług cięcia laserowego lub inżynierem może dostarczyć cennych wskazówek dotyczących projektu i doboru materiałów.

Zewnętrzne uwagi dotyczące projektu
Zewnętrzne rozważania dotyczące cięcia laserowego skupiają się na czynnikach spoza samego projektu, ale mają kluczowe znaczenie dla powodzenia procesu cięcia i ogólnej jakości wyniku. Rozważania te obejmują czynniki związane z całym procesem, obsługą materiałów i działaniem maszyny. Poniżej przedstawiono kluczowe kwestie związane z projektowaniem zewnętrznym podczas stosowania cięcia laserowego:
Wsparcie materialne
- Prawidłowo podpieraj materiały na stole do cięcia, aby zapobiec wypaczeniu, wibracjom lub deformacji materiału podczas cięcia. Niewystarczające podparcie może powodować niedokładne cięcie i pogorszenie jakości cięcia.
Obsługa i wyrównywanie materiałów
- Prawidłowo załaduj i wyrównaj materiał na stole do cięcia, aby upewnić się, że podczas procesu cięcia pozostaje on płaski, stabilny i bezpiecznie ustawiony.
- Nieprawidłowo ustawione lub niestabilne materiały mogą powodować niedokładne cięcie i pogarszać jakość cięcia.
Wentylacja i przepływ powietrza
- W zależności od ciętego materiału, cięcie laserowe może powodować powstawanie dymu i gazów. Upewnij się, że projekt umożliwia odpowiednią wentylację i harmonogram w celu wyeliminowania produktów ubocznych w obszarze cięcia.
- Odpowiedni przepływ powietrza pomaga usunąć zanieczyszczenia z obszaru cięcia i utrzymuje czystą ścieżkę cięcia. Zaleca się skonsultowanie się z producentem maszyny do cięcia laserowego w celu ustalenia odpowiedniego natężenia przepływu i rodzaju gazu dla Twoich materiałów.
Przewody wejściowe i wyjściowe
- Uwzględnij ścieżki wejściowe i wyjściowe w swoim projekcie. Ścieżki te stanowią punkty wejścia i wyjścia wiązki lasera, pomagając zapewnić płynne rozpoczęcie i zakończenie procesu cięcia.
- Linie wejściowe i wyjściowe mogą zapobiegać niepotrzebnym śladom lub defektom na początku i na końcu cięcia, poprawiając w ten sposób jakość cięcia.
Unikaj nadcięć i podcięć
- Przecięcie występuje, gdy wiązka lasera wykracza nieco poza zamierzoną ścieżkę cięcia, co powoduje nadmierne usuwanie materiału.
- Podcięcie występuje, gdy wiązka lasera nie dociera do zamierzonej ścieżki cięcia, potencjalnie pozostawiając nieobcięty materiał.
- Problemy te można zminimalizować poprzez dopracowanie projektu, optymalizację parametrów cięcia i zapewnienie dobrej konserwacji maszyny do cięcia laserowego.
Zewnętrzna konstrukcja nośna
- Jeśli projekt zawiera delikatne lub cienkie części, które mogą łatwo poruszać się podczas procesu cięcia, rozważ dodanie zewnętrznych konstrukcji wsporczych lub zakładek, które utrzymają części na miejscu do czasu zakończenia procesu cięcia.
- Te konstrukcje wsporcze można usunąć po zakończeniu cięcia.
Pozycjonowanie dyszy i ostrość
- Upewnij się, że dysza do cięcia laserowego jest prawidłowo ustawiona i skupiona na ciętym materiale. Prawidłowe ustawienie i skupienie dyszy mają kluczowe znaczenie dla uzyskania precyzyjnych cięć.
Środki bezpieczeństwa maszyn
- Wdrażaj środki bezpieczeństwa podczas obchodzenia się z materiałami i obsługi sprzętu do cięcia laserowego. Postępuj zgodnie ze wskazówkami bezpieczeństwa, używaj odpowiednich środków ochrony osobistej (PPE) i zapewnij odpowiednią wentylację, aby chronić operatora i utrzymać bezpieczne środowisko pracy.
Konserwacja maszyn
- Regularnie konserwuj i kalibruj swoją maszynę do cięcia laserowego, aby zapewnić optymalną wydajność. Właściwa konserwacja może pomóc w zapobieganiu problemom, takim jak niewspółosiowość wiązki lub wahania mocy, które mogą mieć wpływ na jakość cięcia.
Ogniskowanie wiązki laserowej i regulacja mocy
- W zależności od materiału i grubości dostosuj ustawienia skupienia i mocy wiązki lasera, aby zoptymalizować proces cięcia. Znalezienie idealnych ustawień może wymagać pewnych eksperymentów i testów.
Czyszczenie i konserwacja dysz
- Regularnie czyść i konserwuj dyszę do cięcia laserowego, aby zapewnić optymalną wydajność. Czyste dysze pomagają utrzymać stałą jakość i dokładność cięcia.
Gospodarowanie odpadami
- Opracuj plan gospodarki odpadami uwzględniający złom i odpady powstałe w procesie cięcia. Właściwa utylizacja odpadów pomaga w utrzymaniu czystego i bezpiecznego miejsca pracy.
Uwzględniając te zewnętrzne względy projektowe, możesz przyczynić się do pomyślnej realizacji procesu cięcia laserowego, zminimalizować potencjalne problemy lub wady oraz pomóc zapewnić, że ostateczna wycięta część spełnia wymagane standardy jakości. Współpraca z doświadczonym dostawcą usług lub operatorem cięcia laserowego może również dostarczyć cennych wskazówek dotyczących optymalizacji czynników zewnętrznych w projekcie cięcia laserowego.
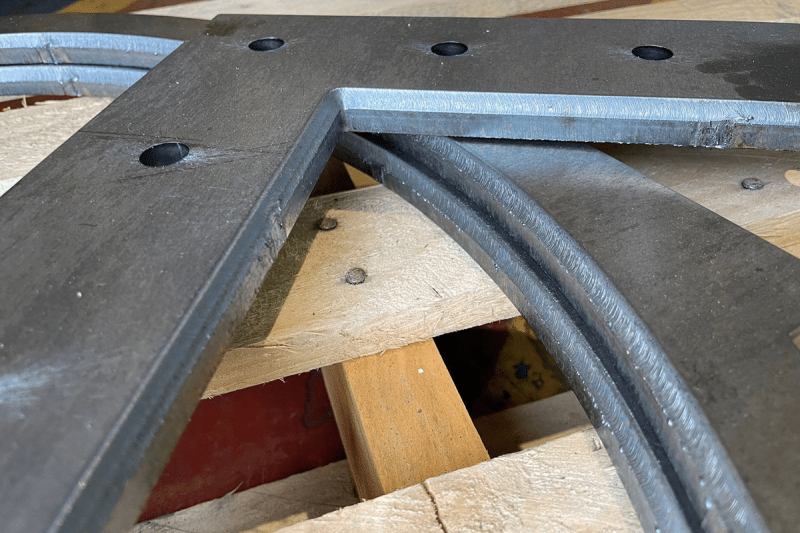
Optymalizacja zagnieżdżona
Projekt optymalizacji zagnieżdżania w cięciu laserowym układa części lub wzory na arkuszu materiału w najbardziej efektywny sposób, aby zminimalizować straty i zmaksymalizować wykorzystanie materiału. Prawidłowe zagnieżdżanie może skutkować znacznymi oszczędnościami, redukcją strat materiałów i zwiększoną wydajnością produkcji. Aby uzyskać najlepsze wyniki optymalizacji zagnieżdżonej dla cięcia laserowego, należy wziąć pod uwagę następujące kluczowe kwestie:
Geometria i orientacja części
- Przeanalizuj geometrię części i wybierz odpowiednie zagnieżdżenie, aby zmaksymalizować wykorzystanie przestrzeni i zminimalizować straty materiału.
- Zoptymalizuj orientację części, aby ograniczyć ruchy materiału podczas cięcia i zminimalizować czas przemieszczania się głowicy laserowej.
Optymalny dobór rozmiaru panelu
- Wybierz rozmiar arkusza materiału, który ściśle odpowiada wymiarom części lub wzoru. Stosowanie desek o odpowiednich wymiarach minimalizuje ilość odpadów i maksymalizuje wykorzystanie materiału. Unikaj używania desek, które są znacznie większe niż to konieczne.
Oprogramowanie do zagnieżdżania
- Skorzystaj z funkcji specjalistycznego oprogramowania do zagnieżdżania lub oprogramowania do projektowania, aby zautomatyzować proces zagnieżdżania. Narzędzia te analizują projekt, wymiary arkusza materiału i parametry cięcia, aby automatycznie optymalizować zagnieżdżanie.
Efektywność materiałowa
- Nadaj priorytet efektywnemu wykorzystaniu materiału, umieszczając części blisko siebie, bez nakładania się. Unikanie nadmiernych odstępów między częściami pomaga zmniejszyć ilość odpadów i obniżyć koszty produkcji.
Unikaj nakładających się cięć
- Upewnij się, że ścieżki cięcia różnych części nie nakładają się na siebie. Nakładające się nacięcia mogą powodować nieregularne krawędzie i odpady materiału. Oprogramowanie do zagnieżdżania może służyć do automatycznego rozmieszczania części w celu uniknięcia nakładania się.
Stała grubość materiału
- Upewnij się, że grubość materiału jest jednakowa na całym arkuszu, aby zachować jednolitą jakość cięcia i uniknąć różnic, które mogłyby mieć wpływ na zagnieżdżanie. Ponadto różnice w grubości materiału mogą prowadzić do niespójnych wyników cięcia.
Zoptymalizuj wykorzystanie panelu
- Korzystając z oprogramowania do zagnieżdżania, możesz obliczyć najbardziej efektywny sposób ułożenia części na arkuszu materiału, biorąc pod uwagę nieregularne kształty i właściwości materiału. Niektóre programy mogą nawet obracać części, aby zminimalizować ilość odpadów.
- W niektórych przypadkach ręczne rozmieszczenie części zgodnie z konkretnymi wymaganiami może dać lepsze wyniki niż poleganie wyłącznie na oprogramowaniu do automatycznego zagnieżdżania. Eksperymentuj z różnymi rozwiązaniami, aby znaleźć ten, który działa najlepiej.
Priorytet kolejności cięcia części
- Rozważ kolejność wycinania części, aby zminimalizować ryzyko deformacji materiału lub kolizji pomiędzy częściami. Najpierw wycinanie mniejszych lub wewnętrznych elementów pomaga zachować stabilność materiału.
Zagnieżdżanie konturowe
- Użyj technologii zagnieżdżania konturowego, aby blisko siebie zagnieździć części o podobnych kształtach, jeszcze bardziej ograniczając ilość odpadów i optymalizując wykorzystanie materiału.
Zagnieżdżanie dynamiczne
- Niektóre zaawansowane programy do zagnieżdżania mogą dynamicznie dostosowywać rozmieszczenie części w czasie rzeczywistym w oparciu o zmiany w projekcie lub dostępnych materiałach. Ta elastyczność optymalizuje wykorzystanie materiałów w przypadku produkcji niestandardowej lub na żądanie.
Gospodarowanie odpadami
- Opracuj strategie zarządzania odpadami i ich ponownego wykorzystania, jeśli to możliwe. Mniejsze pozostałości z poprzednich cięć mogą nadal zawierać sekcje nadające się do wykorzystania na mniejsze części.
Podsumować
Cięcie laserowe oferuje niezrównaną precyzję i elastyczność, ale wykorzystanie jego pełnego potencjału wymaga głębokiego zrozumienia względów projektowych i ograniczeń. Wybierając odpowiednie materiały, optymalizując projekty i respektując możliwości technologii cięcia laserowego, projektanci i inżynierowie mogą uwolnić moc tego rewolucyjnego procesu produkcyjnego, unikając jednocześnie potencjalnych pułapek. Współpraca z doświadczonym producentem maszyn do cięcia laserowego lub profesjonalistą może dostarczyć cennych spostrzeżeń dostosowanych do konkretnych wymagań projektu, zapewniając pomyślne zadanie cięcia laserowego.
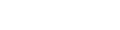
Informacje kontaktowe
- [email protected]
- [email protected]
- +86-19963414011
- Nr 3 Strefa A, strefa przemysłowa Lunzhen, miasto Yucheng, prowincja Shandong.
Uzyskaj rozwiązania laserowe