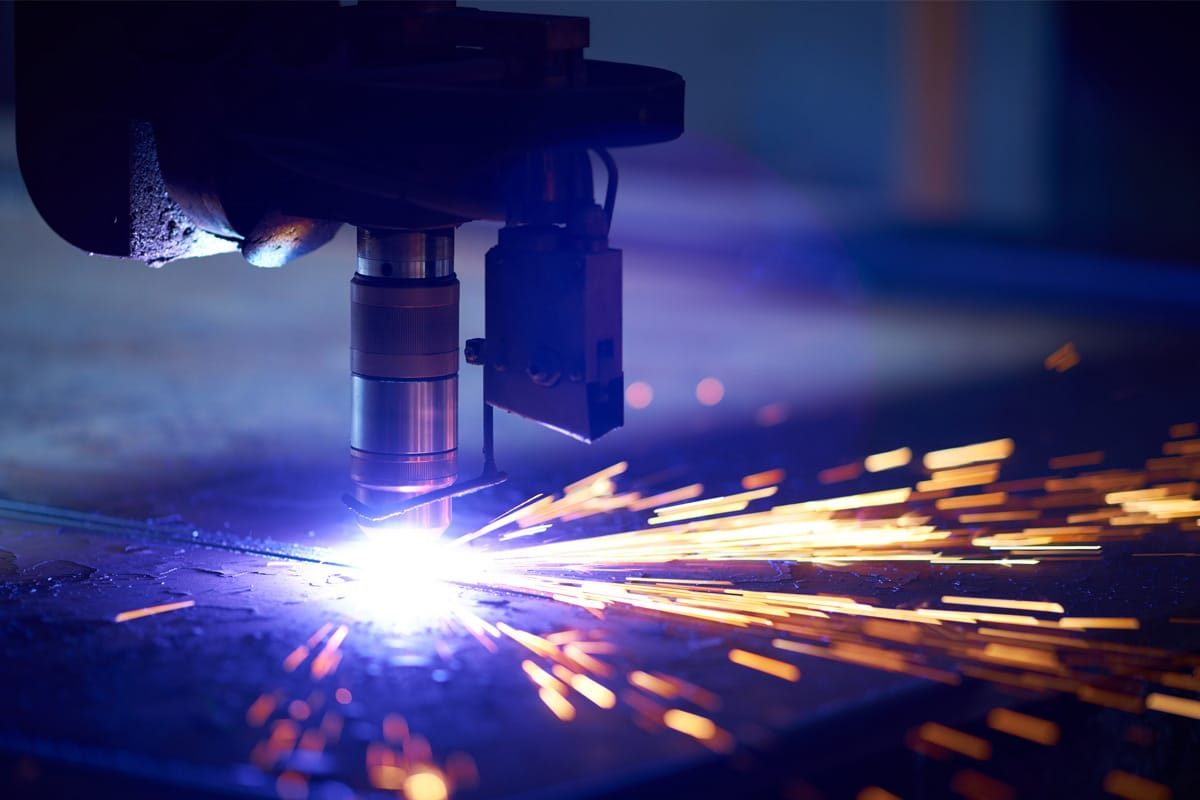
Typowe problemy i rozwiązania dla cięcia laserem światłowodowym
Technologia cięcia laserem światłowodowym jest szeroko stosowana w cięciu i obróbce różnych materiałów metalowych i niemetalowych ze względu na wysoką wydajność, wysoką precyzję i elastyczną pracę. Wykorzystuje wiązkę lasera o dużej mocy do napromieniowania powierzchni przedmiotu obrabianego w celu jego stopienia lub odparowania, co pozwala na precyzyjne cięcie przedmiotu obrabianego. Jednak w praktycznych zastosowaniach cięcie laserem światłowodowym napotyka również na pewne typowe problemy i wyzwania, takie jak obniżona jakość cięcia, niska wydajność cięcia i szybka utrata sprzętu. Zrozumienie i radzenie sobie z tymi problemami może nie tylko wydłużyć żywotność sprzętu, ale także poprawić wydajność produkcji i jakość przetwarzania.
Spis treści
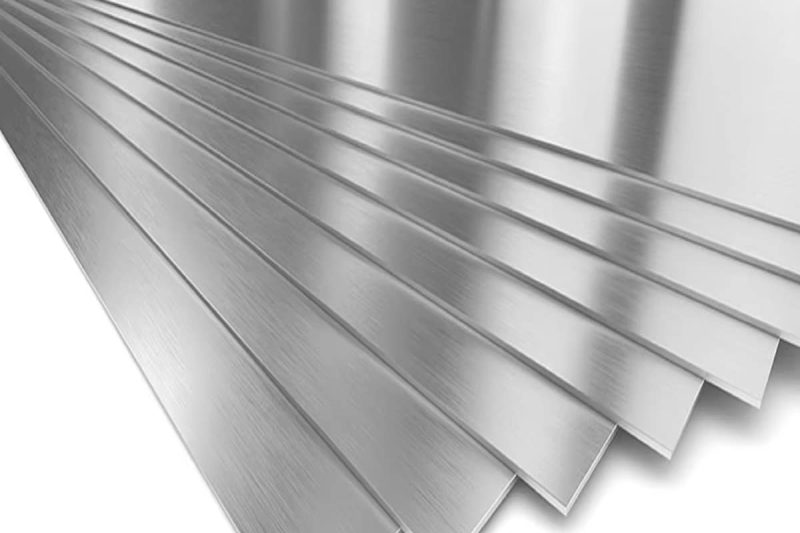
Wyzwania związane z materiałami
Odbicie i przewodność
Im lepsza przewodność materiału, tym niższa szybkość absorpcji energii lasera. Na przykład złoto, srebro, miedź, aluminium i inne materiały mają dobrą przewodność i słabą absorpcję energii, co można również uznać za odbijanie długości fali lasera. Dlatego im wyższa przewodność metalu, tym wyższa jego refleksyjność.
Wyzwanie
- Wysoka refleksyjność: Metale takie jak aluminium i miedź mają wysoką refleksyjność. Zwłaszcza gdy wiązka lasera pada pod kątem zbliżonym do normalnej powierzchni materiału, większość energii lasera zostanie odbita do generatora laserowego lub układu transmisji laserowej, co nie tylko zmniejsza wydajność przetwarzania, ale może również spowodować uszkodzenie sprzętu laserowego, takie jak spalenie soczewki lub włókna optycznego.
- Niewystarczająca absorpcja energii: Ze względu na wysoki współczynnik odbicia efektywna energia lasera pochłaniana przez powierzchnię materiału ulega zmniejszeniu, co skutkuje niewystarczającą głębokością obróbki, niską prędkością cięcia lub niską jakością obróbki.
Rozwiązanie
- Użyj laserów o dużej mocy: Zwiększenie mocy generatora laserowego może bezpośrednio zwiększyć energię lasera napromieniowaną na powierzchnię materiału. Nawet jeśli część energii zostanie odbita, pozostała energia jest wystarczająca do wydajnego przetwarzania. Wybierz generator laserowy o szerokości impulsu i częstotliwości odpowiedniej dla określonych materiałów, aby zoptymalizować transfer energii i efekty przetwarzania.
- Technologia antyrefleksyjna: Poprzez dostosowanie kształtu i kąta rozbieżności wiązki laserowej, energia lasera jest bardziej równomiernie rozłożona na powierzchni materiału, co zmniejsza problem nadmiernego lokalnego odbicia. Użyj dynamicznie regulowanych elementów optycznych (takich jak odkształcalne lustra lub ciekłokrystaliczne przestrzenne modulatory światła), aby korygować zniekształcenie frontu fali wiązki laserowej w czasie rzeczywistym, poprawić jakość ogniskowania wiązki laserowej i zmniejszyć odbicie i rozpraszanie. Niektóre metale mają różne charakterystyki odbicia dla laserów o różnych stanach polaryzacji. Poprzez dostosowanie kierunku polaryzacji lasera, można zmniejszyć utratę odbicia.
- Zoptymalizuj obróbkę powierzchni materiału: Nałóż powłokę lub folię, która pochłania energię lasera na powierzchnię materiału, aby zwiększyć szybkość absorpcji energii lasera i zmniejszyć współczynnik odbicia. Zwiększ chropowatość powierzchni materiału poprzez wstępną obróbkę mechaniczną, chemiczną lub laserową, popraw rozpraszanie i absorpcję energii lasera i zmniejsz bezpośrednie odbicie. Utwórz warstwę absorpcyjną na powierzchni materiału lub zmień jego właściwości chemiczne powierzchni, aby zwiększyć szybkość absorpcji lasera.
- Dostosuj parametry przetwarzania: Zoptymalizuj kąt padania wiązki laserowej, aby uniknąć padania wiązki laserowej bezpośrednio prostopadle do powierzchni materiału, co zmniejszy odbicie lustrzane. Dostosuj prędkość, moc, ogniskową i inne parametry przetwarzania laserowego, aby znaleźć najlepsze warunki przetwarzania, aby zapewnić jakość i wydajność przetwarzania.
Deformacja i odkształcenie materiału
Odkształcenie materiału powstaje w wyniku odkształceń, które powstają wskutek naprężeń szczątkowych wewnątrz materiału i są nierównomiernie rozłożone na całej szerokości i długości materiału.
Wyzwanie
Podczas procesu cięcia laserowego lokalne nagrzewanie może powodować deformację materiału, zwłaszcza w przypadku cienkich płyt. Dzieje się tak, ponieważ laser koncentruje dużą ilość energii cieplnej na małym obszarze podczas cięcia, powodując szybki wzrost temperatury obszaru, co powoduje rozszerzalność cieplną i kurczenie się materiału, a ostatecznie powoduje jego deformację i odkształcenie.
Rozwiązanie
- Dostosuj moc lasera: Zmniejszenie mocy lasera może zmniejszyć koncentrację ciepła, a tym samym ograniczyć odkształcenia termiczne materiału.
- Optymalizacja prędkości cięcia: Odpowiednie zwiększenie prędkości cięcia może skrócić czas oddziaływania lasera na materiał i ograniczyć gromadzenie się ciepła.
- Użyj gazu pomocniczego: Wybór odpowiedniego gazu pomocniczego (np. azotu lub tlenu) i dostosowanie jego natężenia przepływu może skutecznie odprowadzać ciepło wytwarzane w trakcie procesu cięcia i zmniejszać odkształcenia materiału.
Grubość materiału
W procesie cięcia laserem światłowodowym grubość materiału ma bezpośredni wpływ na jakość cięcia, wydajność i wydajność maszyny. Cieńsze materiały są łatwiejsze do cięcia, z większą prędkością i większą precyzją, ale grubsze materiały mogą powodować szorstkie krawędzie cięcia lub wymagać większej mocy i gazu pomocniczego.
Wyzwanie
Podczas cięcia grubszych materiałów laser potrzebuje więcej czasu, aby przeniknąć przez materiał, co może łatwo prowadzić do nierównomiernego cięcia. Grube materiały mają słabą przewodność cieplną, a ciepło nie jest łatwo rozpraszane, co powoduje powstawanie żużlu i nierównych powierzchni cięcia na krawędzi tnącej.
Rozwiązanie
- Wybierz odpowiednią moc lasera: Wybierz odpowiednią moc lasera w zależności od grubości materiału, aby mieć pewność, że energia wiązki zostanie skoncentrowana w obszarze cięcia, co pozwoli uzyskać najlepszy efekt cięcia.
- Dostosuj parametry cięcia: uwzględnij takie parametry, jak prędkość cięcia, położenie ogniskowe i ciśnienie gazu pomocniczego, aby zapewnić stabilność i jednorodność procesu cięcia.
- Cięcie wielokrotne: W przypadku szczególnie grubych materiałów można stosować różne metody cięcia, tnąc za każdym razem tylko część grubości, cięcie warstwa po warstwie, co pozwala ograniczyć gromadzenie się ciepła i problemy z nierównomiernym cięciem.
Dzięki powyższym metodom możliwe jest skuteczne rozwiązanie problemów silnego odbicia materiału, odkształceń, deformacji i nierównomiernego cięcia grubych materiałów podczas cięcia laserowego, a także poprawa jakości i wydajności cięcia.
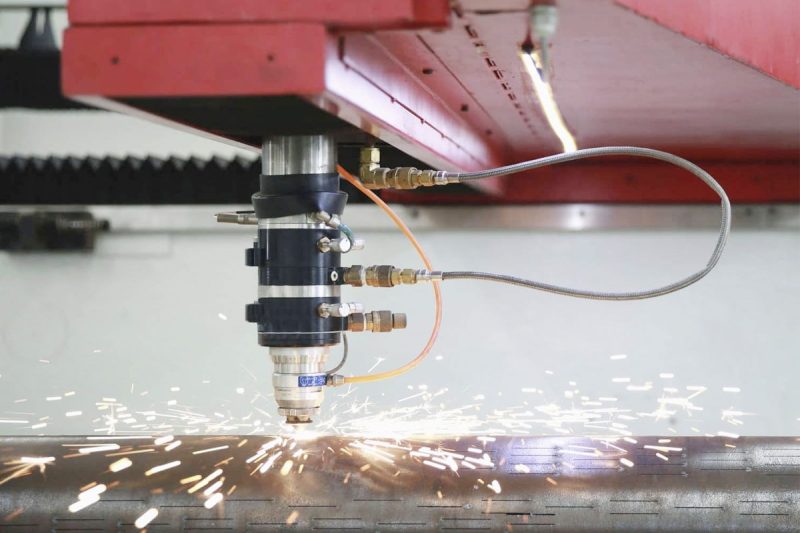
Jakość krawędzi i szerokość nacięcia
Gładkość krawędzi cięcia i ilość zadziorów są kluczowe dla oceny dokładności cięcia. Jeśli energia lasera jest nierównomiernie rozłożona lub prędkość cięcia nie jest odpowiednia, krawędź może wydawać się szorstka lub zadziorna. Szerokość szczeliny zależy od stabilności ogniska lasera. Jeśli ognisko jest niestabilne lub moc lasera ulega wahaniom, szerokość szczeliny może się zmieniać w sposób niespójny, co wpływa na dokładność cięcia.
Szorstkie krawędzie i zadziory
Wyzwanie
- Podczas cięcia laserowego, jeśli energia jest nierównomierna lub prędkość cięcia jest zbyt duża lub zbyt mała, krawędź tnąca często będzie miała zadziory i nierówności. Zwłaszcza gdy moc wyjściowa wiązki laserowej jest niestabilna, powierzchnia ciętego materiału może być lokalnie przegrzana lub stopiona nierównomiernie, co skutkuje szorstkimi krawędziami.
- W przypadku niektórych materiałów metalowych (np. aluminium, stal nierdzewna itp.) nierównomierne rozprowadzanie ciepła powoduje naprężenia cieplne, co z kolei prowadzi do powstawania zadziorów.
- Ponadto niewłaściwe użycie gazu pomocniczego (niewystarczający przepływ powietrza lub nieodpowiednie ciśnienie) także wpływa na wydajność odprowadzania stopionego materiału i zwiększa liczbę zadziorów.
Rozwiązanie
- Ważne jest zoptymalizowanie ustawień mocy lasera i prędkości cięcia. Upewnij się, że moc lasera jest wystarczająco wysoka, a wyjście jest stabilne, aby utrzymać równomierny rozkład ciepła na powierzchni materiału. Jednocześnie prędkość cięcia musi być dostosowana do grubości i charakterystyki materiału, ani za szybka (aby uniknąć niewystarczającego cięcia materiału), ani za wolna (aby zapobiec nadmiernemu stopieniu).
- Użycie odpowiedniego gazu wspomagającego, takiego jak azot lub tlen, może poprawić wyniki cięcia i zapewnić czystą i gładką powierzchnię cięcia. Azot jest często używany w celu zapobiegania utlenianiu i redukcji zadziorów na krawędziach, podczas gdy tlen pomaga zwiększyć wydajność cięcia i prędkość topienia.
Zmiana szerokości szczeliny
Wyzwanie
- Głównym powodem niespójnej szerokości szczeliny jest zwykle niestabilność ogniska lasera lub wahania mocy lasera. Gdy ognisko lasera jest przesunięte, koncentracja energii odpowiednio się zmieni, co spowoduje wahania szerokości szczeliny. Jeśli moc lasera jest niestabilna, wahania energii wyjściowej będą miały bezpośredni wpływ na dokładność cięcia i spowodują zmiany szerokości szczeliny.
- Ponadto zanieczyszczenie lub uszkodzenie elementów optycznych może również powodować zmiany w jakości wiązki, wpływając tym samym na jednorodność linii cięcia. Zużycie części mechanicznych urządzenia, takich jak szyny prowadzące i łożyska, również wpłynie na dokładność ruchu głowicy lasera, powodując niespójne szczeliny.
Rozwiązanie
- Regularnie sprawdzaj i konserwuj układ optyczny, aby zapewnić stabilną ostrość i energię lasera.
- Wyczyść lub wymień zanieczyszczone soczewki optyczne, aby zapobiec niepotrzebnemu załamaniu lub rozproszeniu światła podczas transmisji wiązki.
- Regularnie kalibruj ostrość i moc wyjściową sprzętu laserowego, aby zapewnić jego dokładność w czasie pracy.
- Konserwuj części mechaniczne sprzętu, aby zapewnić płynny i niezakłócony ruch głowicy laserowej i ograniczyć błędy cięcia spowodowane zużyciem mechanicznym.
Podsumowując, dzięki prawidłowemu ustawieniu parametrów i regularnej konserwacji układu optycznego można skutecznie poprawić jakość krawędzi i kontrolować szerokość szczeliny.
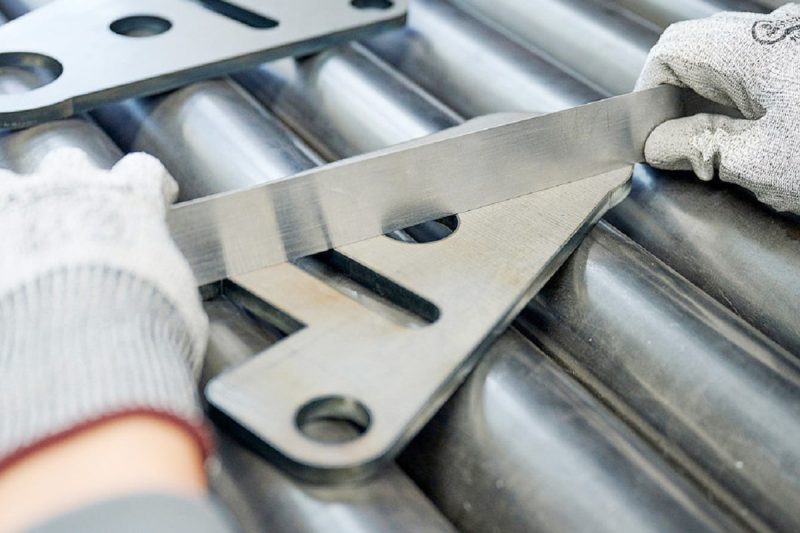
Wyzwania związane z procesami
Wyzwania związane z procesem obejmują głównie problemy techniczne, które mogą wystąpić podczas procesu cięcia laserem światłowodowym. Typowe wyzwania związane z procesem obejmują gromadzenie się żużlu, co jest częstym wyzwaniem w procesie cięcia laserem światłowodowym, szczególnie podczas cięcia grubszych lub trudnych do cięcia materiałów. Zazwyczaj gromadzenie się żużlu jest spowodowane brakiem całkowitego stopienia lub odparowania materiału lub niewystarczającą ilością gazu pomocniczego, aby wydmuchać stopiony materiał z obszaru cięcia na czas.
Nagromadzenie żużla
Wyzwanie
- Gdy energia lasera jest niewystarczająca lub ogniskowanie wiązki lasera jest przesunięte, powierzchnia materiału nie może osiągnąć temperatury umożliwiającej stopienie lub odparowanie, co powoduje, że część materiału pozostaje na krawędzi tnącej. Szczególnie w przypadku obróbki grubych płyt energia lasera musi być wystarczająco silna, aby przeniknąć całą grubość materiału.
- Gazy pomocnicze, takie jak tlen lub azot, są często używane do wydmuchiwania stopionego materiału z obszaru cięcia. Jeśli ciśnienie gazu jest zbyt niskie i stopionego materiału nie można skutecznie usunąć, żużel będzie się gromadził na krawędzi tnącej.
- Zbyt duża prędkość cięcia spowoduje, że wiązka lasera nie będzie oddziaływać na ten sam obszar, materiał nie zostanie całkowicie stopiony lub gaz nie będzie mógł wydalić pozostałości na czas, co doprowadzi do gromadzenia się żużlu.
Rozwiązanie
- Upewnij się, że zapewnione jest wystarczające ciśnienie gazu, aby pomóc skutecznie usunąć stopiony materiał i uniknąć gromadzenia się żużlu. Azot nadaje się do materiałów nieutleniających, podczas gdy tlen może przyspieszyć prędkość cięcia, ale wymaga wyższego ciśnienia gazu.
- Zoptymalizuj prędkość cięcia zgodnie z grubością i charakterystyką materiału, aby zapewnić, że energia lasera może w pełni oddziaływać na obszar cięcia. Odpowiednie połączenie mocy lasera i prędkości cięcia może zmniejszyć niepotrzebne strefy wpływu ciepła, unikając w ten sposób problemu niepełnego stopienia materiałów.
- Upewnij się, że komponenty optyczne generatora laserowego są w najlepszym stanie i mogą stabilnie wytwarzać wymaganą moc lasera, gwarantując spójność procesu cięcia.
Kompleksowa regulacja tych parametrów pozwala znacząco zredukować problemy związane z gromadzeniem się żużlu, poprawić jakość cięcia i ograniczyć późniejsze prace związane ze szlifowaniem i czyszczeniem.
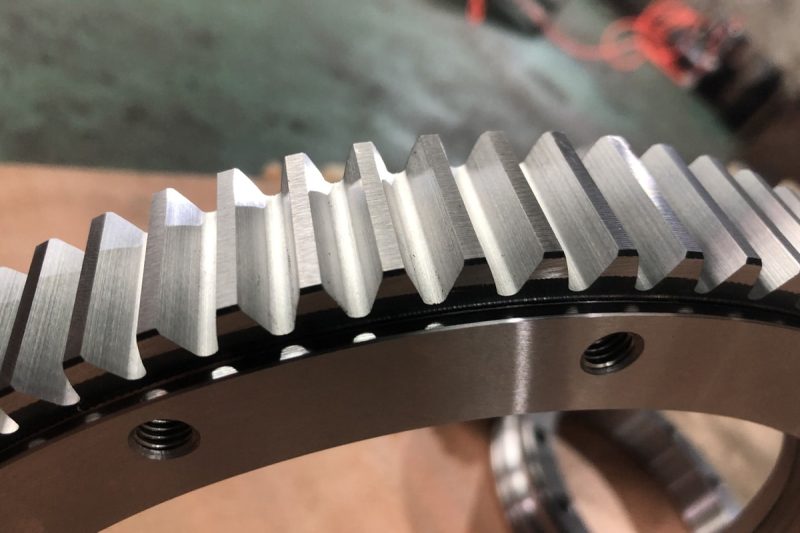
Problemy z przebiciem i uruchomieniem
Podczas procesu cięcia laserem światłowodowym problemy z perforacją i uruchomieniem są powszechnymi wyzwaniami, szczególnie w przypadku grubszych lub silnie odbijających materiałów. Proces perforacji jest punktem wyjścia cięcia laserowego, a jego stabilność i wydajność bezpośrednio wpływają na efekt całego procesu cięcia. Jeśli czas perforacji jest zbyt długi lub nie powiedzie się, może to prowadzić do marnowania materiału i zużycia sprzętu, a nawet wpłynąć na jakość cięcia. Niestabilność procesu uruchamiania doprowadzi do nierównych szczelin i słabej jakości krawędzi tnącej, co wpłynie na dokładność i wygląd gotowego produktu.
Opóźnienia i awarie przebijania
Wyzwanie
Opóźnienia w przebijaniu są zwykle spowodowane tym, że wiązka lasera nie skupia wystarczająco dużo energii, aby przebić materiał, co skutkuje długim czasem przebijania. Opóźnienia w przebijaniu są szczególnie zauważalne w przypadku grubszych materiałów lub materiałów odblaskowych (takich jak aluminium i miedź) i mogą nawet powodować niepowodzenia w przebijaniu. Przyczynami niepowodzeń w przebijaniu mogą być niewystarczająca moc lasera, niedokładne skupienie lasera, niewystarczający gaz pomocniczy lub niewłaściwy wybór gazu. Może to powodować nierównomierne lub nieudane rozpoczęcie cięcia, marnotrawstwo materiału i potencjalne uszkodzenie sprzętu laserowego.
Rozwiązanie
- Upewnij się, że moc lasera może być szybko skoncentrowana, szczególnie w przypadku grubych materiałów płytowych, gdzie do perforacji wymagana jest większa energia. Dostosuj ogniskowanie lasera, aby upewnić się, że jest skoncentrowane na powierzchni materiału, zmniejszając rozproszenie energii i skracając czas perforacji.
- Dzięki przebijaniu w trybie krótkich impulsów można zmniejszyć przegrzanie i odkształcenie materiału, a jednocześnie zmniejszyć ryzyko awarii przebijania. Ta technika jest szczególnie odpowiednia dla grubszych materiałów i materiałów silnie odbijających światło.
- Zastosowanie azotu i tlenu ma znaczący wpływ na proces przekłuwania. Tlen może przyspieszyć proces perforacji, ale może powodować utlenianie materiału, dlatego odpowiedni gaz i ciśnienie należy wybrać na podstawie charakterystyki materiału.
- W przypadku bardzo grubych materiałów można stosować techniki perforacji wieloetapowej, które penetrują materiał warstwa po warstwie, a nie wszystkie naraz. Ta metoda może skutecznie zapobiegać uszkodzeniom spowodowanym przebiciem i nadmiernym efektom termicznym.
Niestabilny rozruch
Wyzwanie
Niestabilny rozruch objawia się głównie nierówną szerokością szczeliny i słabą jakością krawędzi na początku cięcia laserowego, a nawet może prowadzić do niepowodzenia procesu cięcia. Jest to zwykle spowodowane niestabilną energią lasera, zmianami w szybkości przepływu gazu, niespójnymi cechami powierzchni materiału (takimi jak utlenianie lub powlekanie) itp. Niestabilny rozruch może prowadzić do słabej jakości cięcia w początkowej części, szczególnie w zastosowaniach precyzyjnego cięcia, ta niestabilność wpłynie na dokładność i spójność gotowego produktu.
Rozwiązanie
- Przed rozpoczęciem powierzchnia materiału może zostać podgrzana, zwłaszcza w przypadku materiałów silnie odbijających światło. Pomaga to zmniejszyć odbicia lasera i sprawia, że proces cięcia jest płynniejszy.
- Upewnij się, że generator laserowy szybko osiągnie stabilny stan podczas rozruchu, dostosowując szybkość wzrostu mocy lasera i natężenie przepływu gazu pomocniczego. To może skutecznie zapobiec wahaniom energii podczas rozruchu.
- W przypadku materiałów z warstwami tlenków lub innymi zanieczyszczeniami na powierzchni, przed uruchomieniem można wykonać proste czyszczenie powierzchni lub usunięcie powłoki, aby zmniejszyć odbicia lasera i niestabilność podczas procesu uruchamiania.
- Użyj systemu monitorowania w czasie rzeczywistym, aby kontrolować proces cięcia, zwłaszcza w fazie rozruchu, i zapewnij stabilność i spójność procesu cięcia poprzez dostosowanie parametrów.
Ogólnie rzecz biorąc, optymalizując parametry lasera, wybierając odpowiedni gaz pomocniczy, stosując technologię perforacji impulsowej i wstępnie przetwarzając przed uruchomieniem, można znacznie zmniejszyć problemy opóźnienia perforacji, awarii i niestabilnego startu, a także poprawić wydajność i jakość cięcia. Te rozwiązania nie tylko poprawiają wydajność operacyjną, ale także zapewniają długoterminową stabilną pracę sprzętu.
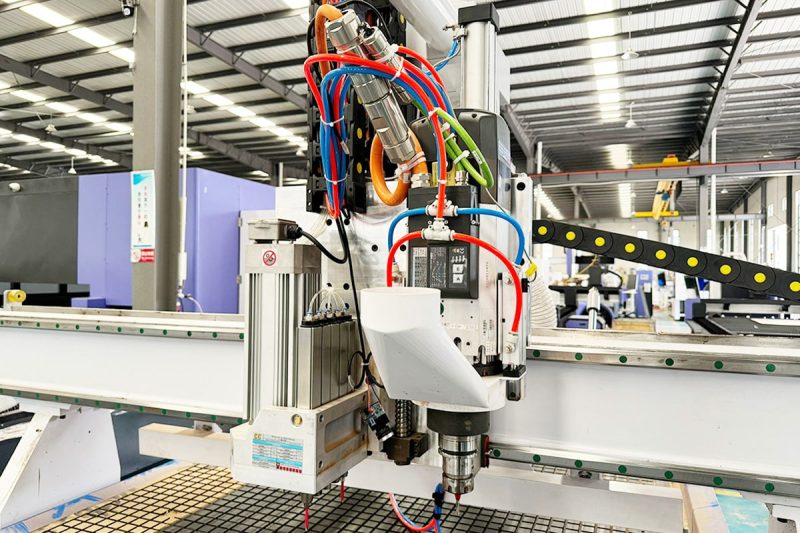
Wyzwania związane z maszynami
W cięciu laserem światłowodowym wydajność maszyny bezpośrednio wpływa na jakość i wydajność cięcia. System transmisji wiązki i komponenty mechaniczne samej maszyny mogą mieć różne problemy po długotrwałym użytkowaniu, co wpłynie na dokładność i stabilność cięcia laserowego.
Problemy z systemem dostarczania wiązki
Wyzwanie
System transmisji wiązki jest systemem rdzeniowym, który przekazuje energię źródła laserowego do głowicy tnącej. Jego wydajność bezpośrednio determinuje stabilność energetyczną wiązki laserowej i jakość cięcia. Jeśli system transmisji wiązki nie jest regularnie sprawdzany i konserwowany, kurz, zanieczyszczenia lub zużycie mechaniczne mogą również uszkodzić elementy optyczne, co dodatkowo obniży wydajność systemu.
Rozwiązanie
- Soczewki optyczne i soczewki w systemach cięcia laserem światłowodowym są podatne na gromadzenie się kurzu i oleju. Regularne czyszczenie może zapobiec spadkowi wydajności transmisji wiązki laserowej i zapewnić stabilność wiązki.
- Zapewnienie stabilności złączy światłowodowych i precyzyjnego wyrównania wiązek laserowych może zmniejszyć utratę energii. Regularnie sprawdzaj połączenia światłowodowe, aby upewnić się, że nie ma luzu ani zużycia.
- Jeżeli często występują problemy z niestabilnością wiązki, należy rozważyć zastosowanie technologii optyki adaptacyjnej w celu regulacji układu transmisji wiązki w czasie rzeczywistym, co zapewni najlepszą jakość wiązki.
- Akumulacja ciepła podczas transmisji wiązki wpływa na jakość wiązki, dlatego kluczowe jest, aby układ chłodzenia działał skutecznie. Regularnie sprawdzaj układ chłodzenia, aby upewnić się, że może on normalnie odprowadzać ciepło i zmniejszać wpływ termiczny podczas transmisji wiązki.
Zużycie mechaniczne
Wyzwanie
Elementy mechaniczne w maszynach do cięcia laserem światłowodowym, w tym szyny prowadzące, serwosilniki i układy napędowe, będą się stopniowo zużywać z czasem podczas intensywnego użytkowania. Zużycie mechaniczne nie tylko spowoduje niestabilny ruch głowicy tnącej, ale może również wpłynąć na dokładność ścieżki cięcia i ostatecznie na jakość gotowego produktu. Zwłaszcza w przypadku wymagań dotyczących cięcia o dużej prędkości i wysokiej precyzji zużycie mechaniczne przyspieszy starzenie się sprzętu oraz zwiększy koszty konserwacji i przestoje. Ponadto zwiększone wibracje i hałas są również powszechnymi objawami zużycia mechanicznego.
Rozwiązanie
- Szyny prowadzące i układy przeniesienia napędu muszą być regularnie smarowane, aby zmniejszyć tarcie i wydłużyć żywotność części mechanicznych. Jednocześnie należy sprawdzić układ smarowania, aby zapewnić jego normalne działanie i uniknąć nadmiernego zużycia części z powodu niewystarczającego smarowania.
- Jeżeli okaże się, że prowadnice, koła zębate lub inne części są zużyte lub przesunięte, uszkodzone części należy wymienić na czas, aby zapewnić dokładność i stabilność maszyny.
- W przypadku operacji wymagających wysokiej precyzji wibracje mogą negatywnie wpłynąć na dokładność cięcia. Poprzez instalację urządzeń antywibracyjnych lub optymalizację pozycji instalacji maszyny można zmniejszyć wpływ wibracji na części mechaniczne, opóźniając w ten sposób zużycie.
- Nowoczesny maszyny do cięcia laserem światłowodowym może zostać wyposażony w system monitorujący, który kontroluje stan części mechanicznych w czasie rzeczywistym, przewiduje z wyprzedzeniem możliwe awarie poprzez analizę danych i zapobiega nagłym przestojom spowodowanym zużyciem mechanicznym.
Dzięki regularnej konserwacji i optymalizacji układu transmisji wiązki oraz podzespołów mechanicznych można znacznie poprawić wydajność i stabilność pracy urządzenia do cięcia laserem światłowodowym, zapewniając jednocześnie ciągłość i wysoką jakość efektu cięcia.
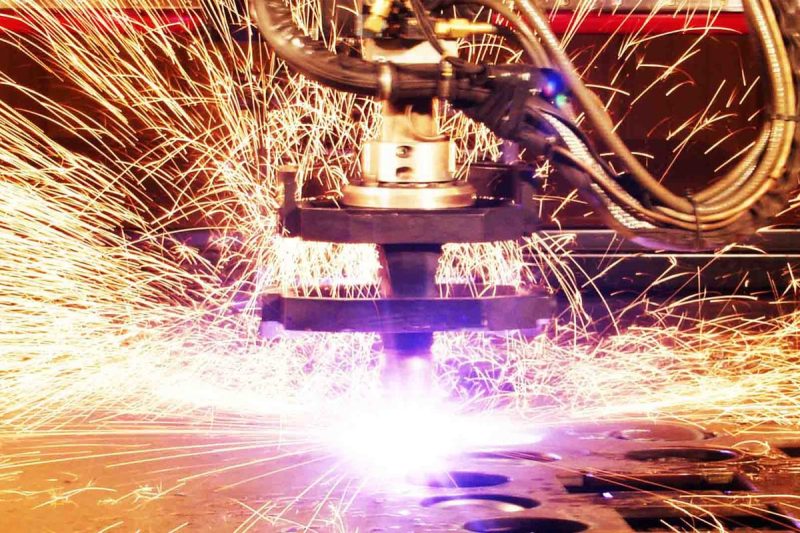
Stożek i odchylenie kątowe
Odchylenie stożka i kąta to dwa powszechne wyzwania dotyczące precyzji w procesie cięcia laserem światłowodowym. Problemy ze stożkiem zwykle objawiają się niespójną górną i dolną szerokością krawędzi cięcia, podczas gdy odchylenie kąta odnosi się do braku prostopadłości między wiązką lasera a materiałem, co skutkuje przechyloną powierzchnią cięcia. Problemy te wpływają na jakość i wygląd końcowego przedmiotu obrabianego, szczególnie w przypadku zadań cięcia o wysokiej precyzji.
Stożek
Wyzwanie
Zjawisko stożka występuje zazwyczaj podczas cięcia grubych materiałów i objawia się tym, że krawędź tnąca jest wąska u góry i szeroka u dołu lub szeroka u góry i wąska u dołu. Dzieje się tak, ponieważ rozkład energii wiązki laserowej jest nierównomierny podczas przechodzenia przez materiał. Im większa głębokość cięcia, tym bardziej widoczne jest tłumienie energii lasera, co skutkuje różnicą w górnej i dolnej szerokości krawędzi tnącej. Stożek wpłynie na dokładność przedmiotu obrabianego, szczególnie w przypadku montażu o wysokiej precyzji. Stożek spowoduje trudności w montażu, a nawet zezłomowanie przedmiotu obrabianego. Ponadto niewłaściwe ciśnienie gazu pomocniczego i niestabilna moc lasera również pogorszą zjawisko stożka.
Rozwiązanie
- Problemy ze stożkiem można skutecznie zmniejszyć, optymalizując głębokość i położenie ogniska lasera. Umieszczenie ogniska w środku materiału, a nie na powierzchni, pomaga utrzymać równomierny rozkład energii lasera na całej grubości cięcia.
- W przypadku grubszych materiałów użycie generatora laserowego o większej mocy pozwala uzyskać bardziej stabilną energię wyjściową w trakcie procesu cięcia i zredukować problemy ze stożkowością spowodowane tłumieniem lasera.
- Stożek można zmniejszyć, odpowiednio regulując ciśnienie gazu pomocniczego, utrzymując obszar cięcia w czystości i skutecznie chłodząc krawędź tnącą. Szczególnie w przypadku cięcia grubych materiałów rola gazu pomocniczego jest kluczowa.
- Każdy niewielki problem z układem optycznym spowoduje nierównomierny rozkład energii wiązki laserowej. Dlatego regularna konserwacja i czyszczenie elementów optycznych w celu zapewnienia jakości wiązki laserowej może skutecznie zmniejszyć stożek.
Odchylenie kątowe
Wyzwanie
Odchylenie kątowe odnosi się do braku pionowości wiązki lasera względem materiału, co skutkuje pochyłą krawędzią tnącą. Może to być spowodowane niestabilną instalacją głowicy laserowej, nieprawidłowym ustawieniem wiązki lub niewystarczającą precyzją układu mechanicznego. Odchylenie kątowe spowoduje, że powierzchnia cięcia przedmiotu obrabianego będzie nierówna, co wpłynie na dokładność i wygląd, zwłaszcza gdy przedmiot obrabiany musi być cięty pod kątem prostym.
Rozwiązanie
- Pierwszym krokiem do rozwiązania problemu odchylenia kąta jest upewnienie się, że głowica lasera jest solidnie zamocowana i prostopadła do materiału. Regularna kalibracja głowicy lasera i układu mechanicznego zapewnia, że wiązka lasera zawsze utrzymuje prawidłowy kąt podczas cięcia.
- Prędkość cięcia, moc wyjściowa i ustawienia gazu pomocniczego wpływają na odchylenie kąta. Optymalizacja tych parametrów umożliwia utrzymanie stabilności wiązki laserowej podczas cięcia, co zmniejsza odchylenie kąta.
- Optyka adaptacyjna umożliwia regulację ścieżki propagacji i ostrości wiązki laserowej w czasie rzeczywistym, co gwarantuje, że podczas cięcia zawsze zachowany jest właściwy kąt względem materiału, redukując w ten sposób odchylenia kątowe.
- Czynniki zewnętrzne, takie jak zmiany temperatury i wilgotności oraz wibracje, mogą wpływać na dokładność kąta cięcia laserowego. Odchylenie kąta można dodatkowo zmniejszyć, utrzymując stabilność środowiska cięcia, np. zmniejszając wibracje, kontrolując temperaturę i wilgotność itp.
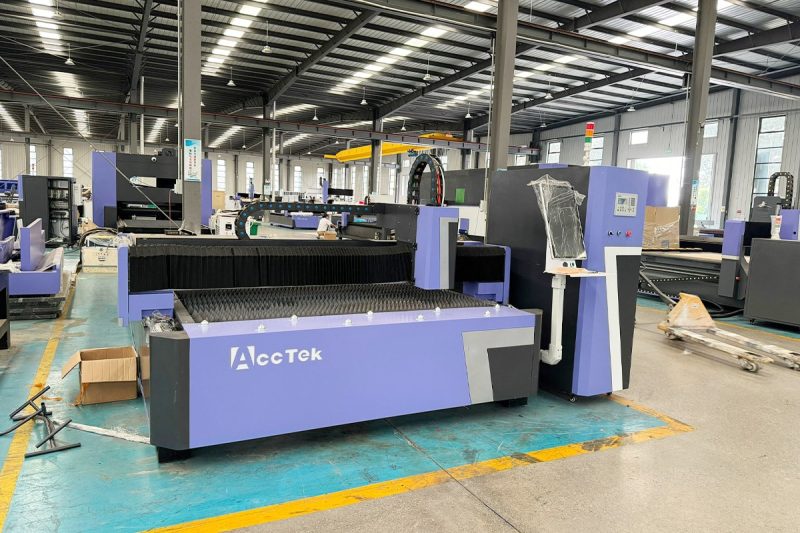
Czynniki środowiskowe
Czynniki środowiskowe mają bezpośredni wpływ na stabilność i jakość procesu cięcia laserem światłowodowym. Wahania temperatury i wilgotności, a także zmiany jakości powietrza mogą negatywnie wpłynąć na wydajność systemu laserowego, jakość cięcia i żywotność maszyny. Zrozumienie i kontrolowanie tych czynników środowiskowych może zapewnić, że sprzęt będzie działał najlepiej, redukując niepotrzebne awarie i wymagania konserwacyjne.
Wahania temperatury i wilgotności
Wyzwanie
Wahania temperatury i wilgotności stanowią poważne wyzwanie w procesie cięcia laserowego. Generator laserowy i układ optyczny są bardzo wrażliwe na zmiany temperatury i wilgotności. Na przykład zbyt wysoka temperatura może spowodować przegrzanie generatora laserowego, co wpłynie na jakość i stabilność wiązki laserowej; podczas gdy zbyt niska temperatura może spowodować, że generator laserowy nie osiągnie wymaganej temperatury roboczej, co wpłynie na moc wyjściową. Zbyt wysoka wilgotność może spowodować kondensację na elementach optycznych, co wpłynie na wydajność transmisji wiązki laserowej, a nawet uszkodzi urządzenia optyczne. Zbyt niska wilgotność może zwiększyć ryzyko elektryczności statycznej, która może zakłócić normalne działanie elementów elektronicznych.
Rozwiązanie
- Aby poradzić sobie z wahaniami temperatury i wilgotności, zaleca się zainstalowanie specjalistycznych systemów kontroli środowiska, takich jak klimatyzacja i urządzenia osuszające w warsztacie cięcia. Systemy te mogą utrzymywać stałą temperaturę i wilgotność w warsztacie, aby zapewnić, że sprzęt laserowy działa w optymalnych warunkach.
- Zainstaluj czujniki temperatury i wilgotności wokół sprzętu tnącego, aby monitorować warunki środowiskowe w czasie rzeczywistym. Po wykryciu nieprawidłowości system kontroli środowiska może zostać automatycznie dostosowany lub proces cięcia może zostać zawieszony, jeśli jest to konieczne, aby uniknąć uszkodzenia sprzętu.
- W suchym środowisku zwiększ wilgotność powietrza, aby ograniczyć ryzyko wystąpienia elektryczności statycznej, a także stosuj podłogi antystatyczne i środki uziemiające sprzęt, aby zapewnić bezpieczną pracę.
Jakość powietrza
Wyzwanie
Nie można ignorować wpływu jakości powietrza na proces cięcia laserowego. Pył, mgła olejowa i inne zanieczyszczenia zawieszone w powietrzu mogą przedostać się do układu optycznego lub obszaru cięcia generatora laserowego, wpływając na transmisję i ogniskowanie wiązki laserowej. Zanieczyszczenia w powietrzu mogą również reagować z wiązką laserową podczas procesu cięcia, co skutkuje słabymi wynikami cięcia lub nawet uszkodzeniem powierzchni przedmiotu obrabianego. Ponadto długotrwałe narażenie na powietrze złej jakości zwiększy częstotliwość konserwacji maszyny i skróci żywotność sprzętu.
Rozwiązanie
- Zainstaluj system oczyszczania powietrza w warsztacie cięcia laserowego, aby odfiltrować cząstki stałe i zanieczyszczenia w powietrzu, zapewniając czyste powietrze. Szczególnie podczas cięcia niektórych materiałów (takich jak tworzywa sztuczne i drewno) materiały te mogą uwalniać szkodliwe gazy podczas procesu cięcia laserowego, dlatego skuteczny system oczyszczania powietrza jest szczególnie ważny.
- Nawet przy systemie oczyszczania powietrza nadal konieczne jest regularne czyszczenie układu optycznego generatora laserowego. Usuń kurz i zanieczyszczenia, które mogą się gromadzić, aby zapewnić jakość wiązki laserowej i efekt cięcia.
- W niektórych kluczowych urządzeniach lub obszarach można zastosować środki ochrony przed nadciśnieniem, tzn. wprowadzić przefiltrowane powietrze, dzięki czemu ciśnienie powietrza w obszarze będzie utrzymywane na wyższym poziomie niż na zewnątrz, aby zapobiec przedostawaniu się zanieczyszczeń.
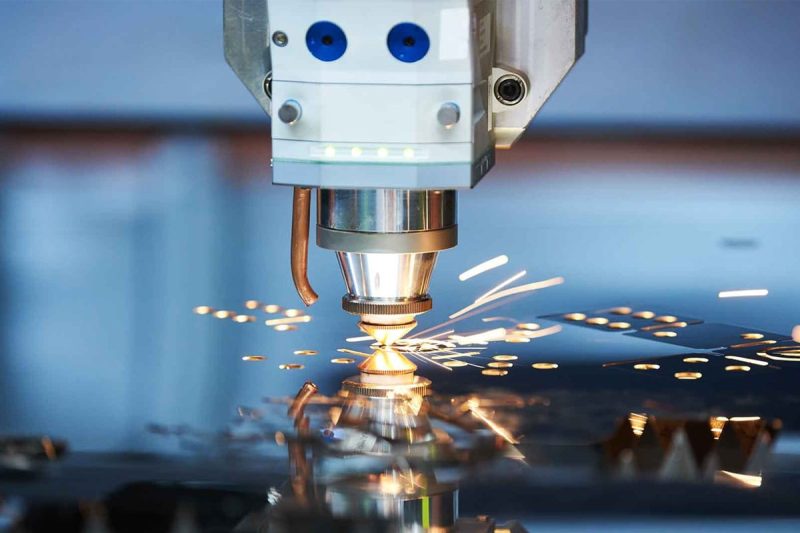
Wyzwania związane z operatorem
Oprócz czynników środowiskowych, poziom umiejętności operatora i wydajność pracy również bezpośrednio wpływają na jakość i wydajność cięcia laserem światłowodowym. Brak przeszkolenia i doświadczenia lub nieefektywny przepływ pracy może prowadzić do niewłaściwej obsługi, zwiększonej liczby błędów, a nawet uszkodzenia sprzętu lub wypadków związanych z bezpieczeństwem. Dlatego poprawa profesjonalizmu operatora i optymalizacja przepływu pracy są ważnymi ogniwami zapewniającymi jakość cięcia i wydajność produkcji.
Brak szkoleń i wiedzy specjalistycznej
Wyzwanie
Cięcie laserem światłowodowym to technologia o wysokiej precyzji, która wymaga od operatorów wysokiej wiedzy i umiejętności zawodowych. Jednak w niektórych firmach operatorzy mogą nie mieć wystarczającego przeszkolenia i nie mogą w pełni zrozumieć i opanować złożoności cięcia laserowego. Taka sytuacja może spowodować, że operatorzy nie będą w stanie skutecznie reagować w przypadku problemów technicznych lub skomplikowanych elementów obrabianych, co może wpłynąć na jakość cięcia, zwiększyć zużycie sprzętu, a nawet spowodować zagrożenia bezpieczeństwa. Ponadto konserwacja i pielęgnacja sprzętu wymaga określonych umiejętności i wiedzy. Brak wiedzy operatora może spowodować, że sprzęt nie będzie konserwowany i pielęgnowany na czas, co skróci jego żywotność.
Rozwiązanie
- Przedsiębiorstwa powinny zapewnić systematyczne szkolenia operatorów, obejmujące podstawowe zasady cięcia laserowego, instrukcję obsługi sprzętu, rozwiązywanie problemów i rozwiązania typowych problemów itp. Poprzez regularne szkolenia należy upewnić się, że operatorzy zawsze opanują najnowszą technologię i specyfikacje operacyjne.
- Ustanowić system certyfikacji operacyjnej dla operatorów, a tylko certyfikowany personel może obsługiwać sprzęt do cięcia laserowego. To nie tylko poprawia poczucie odpowiedzialności operatora, ale także zapewnia jakość i bezpieczeństwo operacji.
- Zapewnij operatorom solidne wsparcie techniczne, np. poprzez utworzenie specjalnego działu doradztwa technicznego lub zatrudnienie ekspertów technicznych, którzy będą regularnie udzielać operatorom wskazówek i pomagać im rozwiązywać problemy związane z codziennymi operacjami.
Nieefektywny przepływ pracy
Wyzwanie
Wydajność przepływu pracy bezpośrednio wpływa na ogólną wydajność produkcji i jakość cięcia laserowego. W niektórych firmach, z powodu nierozsądnego projektu przepływu pracy lub niewystarczającej koordynacji, operatorzy mogą spędzać zbyt dużo czasu na przełączaniu zadań, debugowaniu sprzętu lub obsłudze materiałów. Ten nieefektywny przepływ pracy nie tylko marnuje czas i zasoby, ale może również powodować zmęczenie operatora i zwiększać prawdopodobieństwo błędów. Ponadto, jeśli firma nie zoptymalizuje przepływu pracy na czas, wraz ze wzrostem wolumenu zamówień, nieefektywny proces stanie się bardziej widoczny, poważnie wpływając na zdolność produkcyjną i konkurencyjność przedsiębiorstwa.
Rozwiązanie
- Analizując i oceniając bieżący przepływ pracy, możemy zidentyfikować wąskie gardła i nieefektywne połączenia oraz dokonać ukierunkowanych optymalizacji. Na przykład możemy rozsądnie ustalić kolejność zadań, skrócić czas uruchamiania sprzętu i obsługi materiałów oraz poprawić wydajność pracy.
- Wprowadzenie technologii automatyzacji, takich jak automatyczne systemy załadunku i rozładunku oraz inteligentne oprogramowanie do składu tekstu, może znacznie skrócić czas i zmniejszyć błędy związane z pracą ręczną, a także poprawić wydajność całego przepływu pracy.
- Zastosuj zasady produkcji lean, aby zmniejszyć ilość odpadów i zoptymalizować alokację zasobów. Poprzez ciągłe doskonalenie i udział pracowników możemy ustanowić wydajny i elastyczny przepływ pracy, aby zapewnić wydajność i wysoką jakość procesu cięcia laserowego.
Rozwiązując te problemy związane z ochroną środowiska i operatorem, przedsiębiorstwa mogą znacznie zwiększyć wydajność i jakość cięcia laserem światłowodowym, zyskując tym samym przewagę konkurencyjną na rynku.
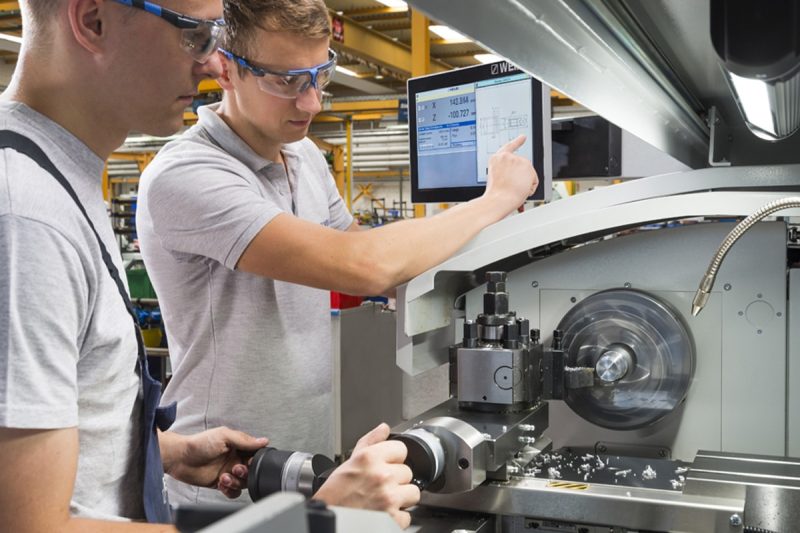
Środki ostrożności i najlepsze praktyki
Aby zapewnić ciągłą, wydajną pracę cięcia laserem światłowodowym, kluczowe jest podjęcie środków zapobiegawczych i najlepszych praktyk. Poprzez regularną konserwację maszyn, optymalizację parametrów, szkolenie operatorów i ciągłe doskonalenie firmy mogą skutecznie zmniejszyć wskaźniki awaryjności, poprawić jakość cięcia i wydłużyć żywotność sprzętu.
Regularna konserwacja maszyny
Wyzwanie
Długotrwała eksploatacja sprzętu do cięcia laserowego może prowadzić do zanieczyszczenia elementów optycznych, zużycia głowicy laserowej i awarii układu chłodzenia. Jeśli brakuje regularnej konserwacji, problemy te mogą wpłynąć na wydajność generatora laserowego, wydłużyć przestoje w produkcji, a nawet spowodować awarię sprzętu.
Rozwiązanie
- Regularnie czyść układ optyczny, aby zapewnić wydajność transmisji wiązki laserowej.
- Sprawdź i wymień podatne na uszkodzenia części, takie jak dysze tnące, soczewki laserowe i systemy filtrów.
- Regularnie sprawdzaj układ chłodzenia, aby mieć pewność, że działa prawidłowo i zapobiegać przegrzaniu generatora laserowego.
Optymalizacja parametrów
Wyzwanie
Różne materiały i grubości wymagają różnych mocy lasera, prędkości cięcia i ciśnień gazu. Nieprawidłowe ustawienia parametrów mogą skutkować obniżoną jakością cięcia, np. zwiększoną liczbą zadziorów lub zbyt szerokimi lub zbyt wąskimi nacięciami.
Rozwiązanie
- Opracuj szczegółowe tabele parametrów cięcia dla różnych materiałów, aby zapewnić dokładne dopasowanie mocy i prędkości.
- Regularnie testuj moc lasera urządzenia, aby zapewnić stabilną moc i ostrość.
- Użyj oprogramowania pomocniczego do automatycznej optymalizacji parametrów w celu zwiększenia wydajności i jakości cięcia.
Szkolenie operatorów
Wyzwanie
Brak doświadczenia lub umiejętności operatora może prowadzić do błędów operacyjnych, zwiększyć awaryjność i wpłynąć na skuteczność cięcia.
Rozwiązanie
- Regularnie zapewniaj operatorom szkolenia techniczne, aby mieć pewność, że znają specyfikacje operacyjne sprzętu laserowego.
- Przygotuj szczegółowe instrukcje obsługi sprzętu i utwórz zespół wsparcia technicznego, który będzie rozwiązywał codzienne problemy.
- Wprowadź system certyfikacji operatorów, aby mieć pewność, że sprzęt będą obsługiwać wyłącznie osoby wykwalifikowane.
Ciągłe doskonalenie
Wyzwanie
Gwałtowne zmiany w technologii i na rynkach wymagają od firm ciągłej optymalizacji procesów produkcyjnych i technologii, aby mogły utrzymać swoją konkurencyjność.
Rozwiązanie
- Wprowadzanie koncepcji produkcji szczupłej, ciągła analiza i optymalizacja procesów produkcyjnych, redukcja odpadów i poprawa wydajności.
- Śledź trendy rozwojowe technologii cięcia laserowego i na bieżąco aktualizuj sprzęt oraz oprogramowanie.
- Zbieraj dane produkcyjne, analizuj wskaźniki wydajności i nieustannie udoskonalaj parametry cięcia oraz procedury operacyjne.
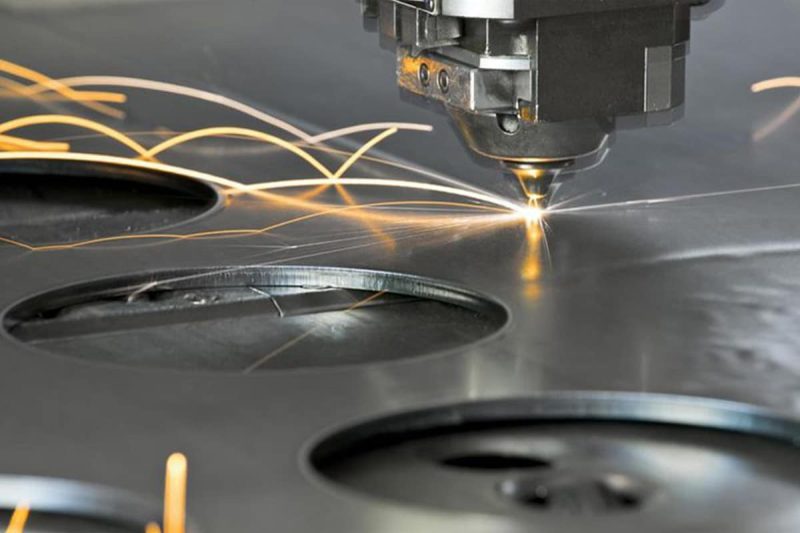
Podsumować
Wyzwania związane z cięciem laserem światłowodowym obejmują wiele aspektów, w tym właściwości materiałów, wydajność sprzętu, warunki środowiskowe itp. Dzięki regularnej konserwacji, zoptymalizowanym parametrom, ulepszonemu szkoleniu i wykorzystaniu zaawansowanej technologii jakość i wydajność cięcia można znacznie poprawić. Rozwiązania należy wdrażać indywidualnie w celu poprawy stabilności procesu cięcia i zmniejszenia przestojów maszyn oraz kosztów konserwacji.
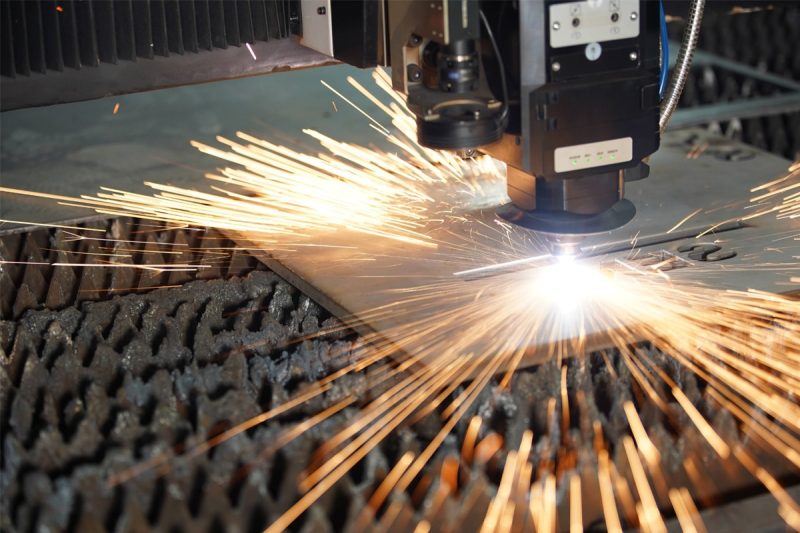
Uzyskaj rozwiązania laserowe
Wybór odpowiedniej maszyny do cięcia laserem światłowodowym może pomóc zoptymalizować zużycie energii i osiągnąć wysoką wydajność operacyjną. Współpraca z zaufanym dostawcą zapewnia dostęp do zaawansowanej technologii, dostosowanych porad i stałego wsparcia. W AccTek Laser oferujemy kompleksową gamę maszyn do cięcia laserem światłowodowym zaprojektowanych tak, aby sprostać różnorodnym potrzebom przemysłowym. Nasi eksperci pomogą Ci wybrać najbardziej energooszczędny model i konfigurację, biorąc pod uwagę takie czynniki, jak rodzaj materiału, grubość i wolumen produkcji. Oferujemy również najnowocześniejsze funkcje, takie jak wysokowydajne generatory laserowe, inteligentne systemy chłodzenia i oprogramowanie do zarządzania energią, aby zmaksymalizować wydajność i zminimalizować zużycie energii. Ponadto nasz zespół zapewnia regularne usługi konserwacyjne i wsparcie techniczne, aby utrzymać Twój sprzęt na najwyższym poziomie wydajności. Współpracując z nami, możesz osiągnąć znaczne oszczędności energii, obniżyć koszty operacyjne i zwiększyć swoje wysiłki na rzecz zrównoważonego rozwoju. Jeśli masz jakiekolwiek pytania, skontaktuj się z nami na czas, AccTek Laser zobowiązuje się do dostarczania doskonałych rozwiązań laserowych dla każdego klienta!
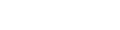
Informacje kontaktowe
- [email protected]
- [email protected]
- +86-19963414011
- Nr 3 Strefa A, strefa przemysłowa Lunzhen, miasto Yucheng, prowincja Shandong.
Uzyskaj rozwiązania laserowe