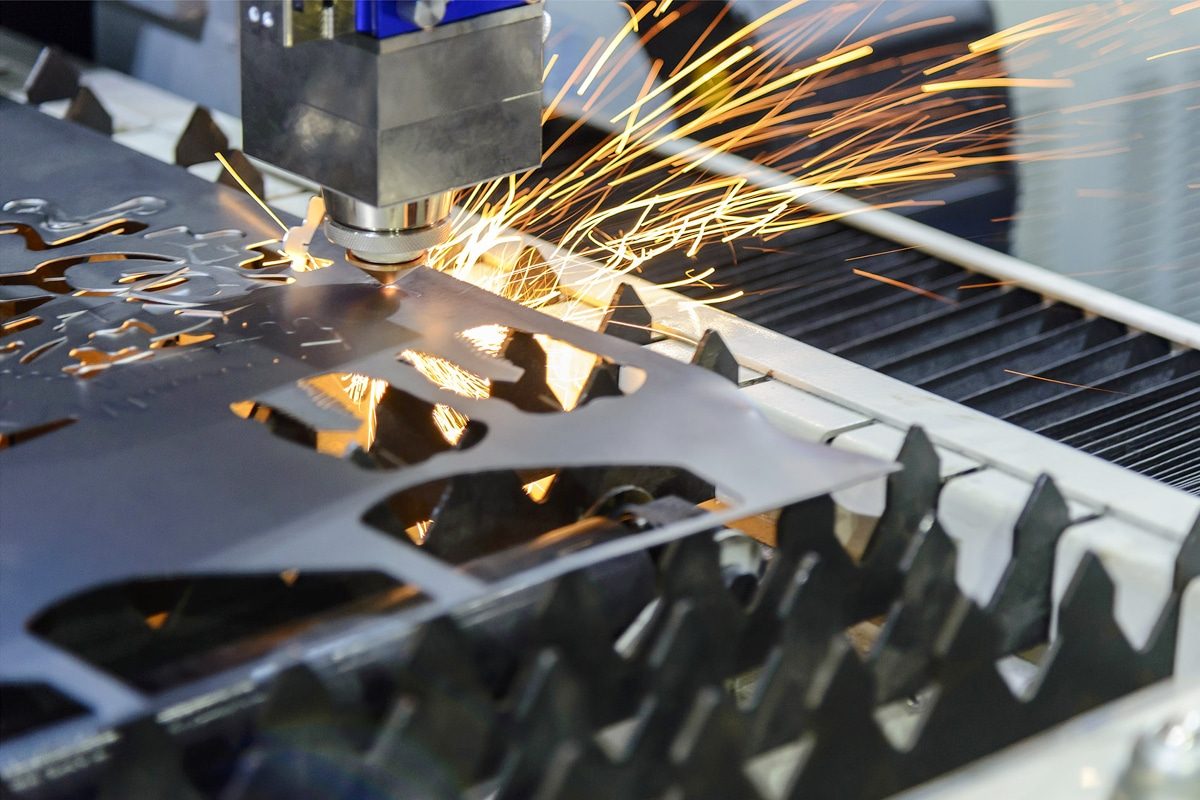
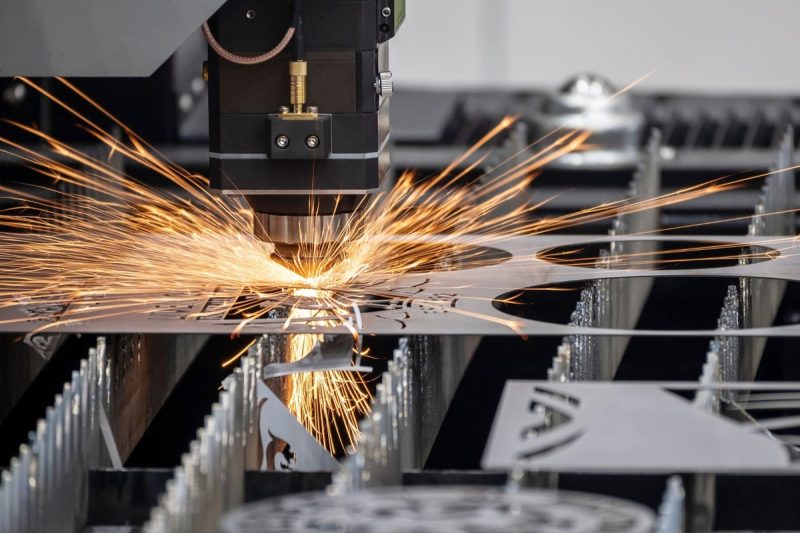
Dowiedz się o cięciu laserowym
Opis cięcia laserowego
Rodzaje laserów stosowanych w zastosowaniach związanych z cięciem
Laser światłowodowy
Laser CO2
Elementy systemu cięcia laserowego
Typowy system cięcia laserowego składa się z kilku kluczowych elementów, które współpracują ze sobą, aby zapewnić precyzyjne i wydajne cięcie:
- Źródło lasera: Jest to główny element wytwarzający wiązkę lasera. W zależności od zastosowania źródłem lasera może być generator lasera światłowodowego, generator lasera CO2 lub generator lasera innego typu.
- Optyka: Lustra i soczewki służą do kierowania i skupiania wiązki lasera na ciętym materiale. Jakość optyki wpływa na dokładność i efektywność procesu cięcia.
- Głowica tnąca: Głowica tnąca zawiera soczewkę skupiającą i dyszę, przez którą kierowana jest wiązka lasera i gaz wspomagający. Odpowiada za utrzymanie prawidłowej ogniskowej i zapewnienie optymalnych warunków cięcia.
- Stół roboczy: podtrzymuje cięty materiał i zwykle zawiera mechanizm przesuwający materiał pod głowicą tnącą.
- Kontroler CNC: Kontroler CNC zarządza ruchem głowicy do cięcia laserowego i przedmiotu obrabianego, podążając za zaprogramowaną ścieżką cięcia, aby uzyskać pożądany kształt i wzór.
- Dopływ gazu wspomagającego: Gaz wspomagający wspomaga proces cięcia, wydmuchując stopiony materiał, chłodząc strefę cięcia i zapobiegając utlenianiu. Typowe gazy wspomagające obejmują tlen, azot i sprężone powietrze.
- Układ wydechowy: Usuwa opary i zanieczyszczenia powstające podczas procesu cięcia, aby utrzymać czyste środowisko pracy i chronić optykę i elementy lasera.
- Układ chłodzenia: Cięcie laserowe generuje dużo ciepła, które należy odprowadzić, aby zapobiec uszkodzeniu źródła lasera i innych komponentów. Aby utrzymać optymalną temperaturę roboczą, stosuje się systemy chłodzenia, takie jak agregaty wody lodowej.
Kluczowe parametry wpływające na wydajność cięcia laserowego
Kilka parametrów może mieć wpływ na wydajność i jakość procesu cięcia laserowego. Zrozumienie i optymalizacja tych parametrów może pomóc w osiągnięciu pożądanych wyników:
- Moc lasera: Moc wyjściowa źródła lasera określa grubość i rodzaj materiału, który można wyciąć. Większe moce umożliwiają cięcie grubszych materiałów, ale w celu utrzymania jakości cięcia konieczne może być dostosowanie innych parametrów.
- Prędkość skrawania: Prędkość, z jaką głowica tnąca porusza się po przedmiocie obrabianym. Optymalna prędkość cięcia zapewnia równowagę pomiędzy produktywnością a jakością cięcia. Zbyt duża prędkość może spowodować niekompletne cięcie, natomiast zbyt mała prędkość może spowodować nadmierne nagrzewanie się i uszkodzenie materiału.
- Położenie ogniskowe: Położenie punktu ogniskowego wiązki laserowej względem powierzchni materiału. Prawidłowe skupienie zapewnia maksymalną gęstość energii w punkcie cięcia, co skutkuje czystymi i precyzyjnymi cięciami. Nieprawidłowe ustawienie może skutkować gorszą jakością cięcia i zmniejszoną wydajnością.
- Rodzaj i ciśnienie gazu wspomagającego: Rodzaj i ciśnienie stosowanego gazu wspomagającego (tlen, azot lub sprężone powietrze) mają znaczący wpływ na proces cięcia. Prawidłowy dobór gazu i ciśnienia optymalizuje usuwanie stopionego materiału, zapobiega utlenianiu i poprawia jakość cięcia.
- Rodzaj i grubość materiału: Różne materiały i grubości różnie reagują na cięcie laserowe. Podczas ustawiania parametrów cięcia należy wziąć pod uwagę właściwości materiału, takie jak współczynnik odbicia światła, przewodność cieplna i temperatura topnienia.
- Jakość wiązki: Jakość wiązki laserowej, charakteryzująca się skupieniem i strukturą trybów, wpływa na precyzję i jakość cięcia. Wysokiej jakości wiązka o małym rozmiarze ogniskowej pozwala uzyskać drobniejsze cięcia przy minimalnej szerokości cięcia.
- Konstrukcja dyszy: Konstrukcja dyszy, w tym jej średnica i kształt, wpływa na przepływ gazu wspomagającego i usuwanie stopionego materiału. Zoptymalizowana konstrukcja dyszy poprawia wydajność i jakość cięcia.
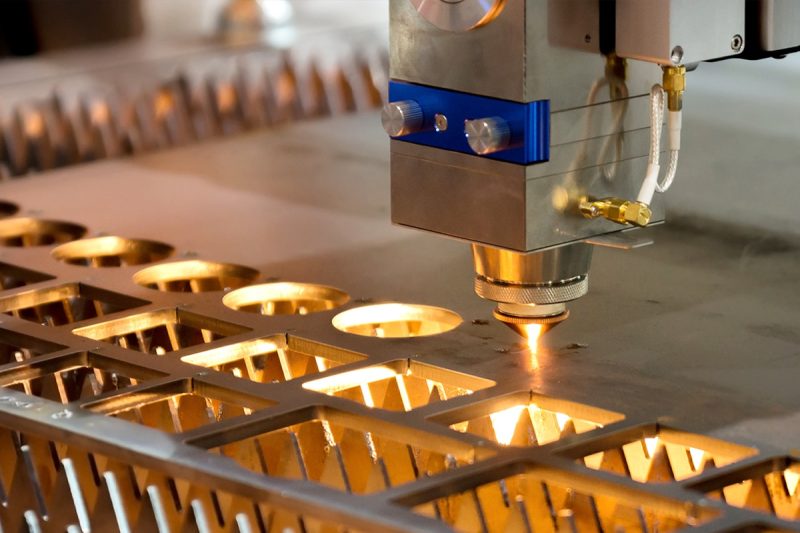
Rola gazów wspomagających w cięciu laserowym
Usuwanie stopionego materiału
Podczas procesu cięcia laserowego wiązka lasera o dużej intensywności topi materiał w miejscu cięcia. Gaz wspomagający kierowany jest przez dyszę do obszaru cięcia, gdzie pomaga usunąć stopiony materiał z nacięcia (szczeliny utworzonej przez laser). Skuteczne usuwanie stopionego materiału utrzymuje jakość cięcia i zapobiega defektom.
- Wydajne natryskiwanie: Wysokie ciśnienie gazu wspomagającego wydmuchuje stopiony materiał z dala od szczeliny, zapobiegając jego ponownemu zestaleniu na obrabianym przedmiocie i zapewniając czyste cięcie.
- Zapobieganie tworzeniu się żużla: Dzięki szybkiemu odprowadzaniu stopionego materiału gaz pomocniczy minimalizuje tworzenie się żużla (resztek materiału przylegających do dolnej powierzchni cięcia), zmniejszając potrzebę obróbki końcowej.
- Utrzymanie szerokości nacięcia: Ciągłe usuwanie stopionego materiału pomaga utrzymać pożądaną szerokość nacięcia, zapewniając dokładność wymiarową i precyzję końcowego cięcia.
Chłodzenie strefy cięcia
Intensywne ciepło generowane przez wiązkę lasera może powodować znaczne skutki termiczne na obrabianym przedmiocie, w tym wypaczenie, deformację i zmiany właściwości materiału. Gaz wspomagający pomaga kontrolować te efekty termiczne poprzez chłodzenie strefy cięcia.
- Rozpraszanie ciepła: Przepływ gazu wspomagającego pochłania i rozprasza nadmiar ciepła w obszarze cięcia, zapobiegając przegrzaniu i minimalizując odkształcenie termiczne materiału.
- Zmniejszanie strefy wpływu ciepła (HAZ): Chłodzenie strefy cięcia pomaga ograniczyć wielkość strefy wpływu ciepła, utrzymując właściwości mechaniczne materiału i zmniejszając ryzyko wypaczenia lub innych uszkodzeń termicznych.
- Zwiększanie prędkości skrawania: Wydajne chłodzenie zwiększa prędkość skrawania, ponieważ w materiale jest mniej prawdopodobne, że wystąpią defekty termiczne, co skutkuje szybszą i bardziej wydajną produkcją.
Ochrona obiektywu
Soczewka w głowicy tnącej skupia wiązkę lasera na obrabianym przedmiocie. Zanieczyszczenia takie jak dym, kurz i inne zanieczyszczenia powstające podczas procesu cięcia mogą uszkodzić soczewkę lub pogorszyć jej działanie. Gaz wspomagający chroni obiektyw przed zanieczyszczeniami.
- Osłona soczewki: Gaz wspomagający tworzy barierę pomiędzy soczewką a obszarem cięcia, zapobiegając przedostawaniu się zanieczyszczeń i osadzaniu się na powierzchni soczewki.
- Utrzymanie jakości optycznej: Utrzymując soczewkę w czystości i wolną od zanieczyszczeń, gaz wspomagający zapewnia optymalne skupienie wiązki i stałą wydajność cięcia.
- Wydłużanie żywotności soczewki: zapobieganie zanieczyszczeniom zmniejsza zużycie soczewki, wydłużając jej żywotność i zmniejszając koszty konserwacji.
Popraw reakcję cięcia
Gazy wspomagające mogą wpływać na reakcje chemiczne zachodzące podczas cięcia laserowego, poprawiając w ten sposób wydajność cięcia różnych materiałów. Rodzaj użytego gazu może sprzyjać lub hamować pewne reakcje, które mogą mieć wpływ na jakość i wydajność cięcia.
- Tlen (O₂): Tlen jest powszechnie używany do cięcia stali węglowej. Sprzyja reakcji egzotermicznej ze stopionym metalem, wytwarzając dodatkowe ciepło, co zwiększa prędkość skrawania. Ta reakcja pomaga uzyskać czyste cięcie z mniejszą ilością żużla, ale może powodować utlenianie na krawędzi cięcia.
- Azot (N₂): Azot to gaz obojętny powszechnie stosowany do cięcia stali nierdzewnej, aluminium i innych metali nieżelaznych. Zapobiega utlenianiu, tworząc obojętną atmosferę wokół strefy cięcia. Pozwala to uzyskać czystą, pozbawioną tlenków krawędź, dzięki czemu idealnie nadaje się do zastosowań wymagających wysokiej jakości wykończenia powierzchni.
- Sprężone powietrze: Sprężone powietrze jest opłacalną alternatywą, którą można stosować do cięcia różnych materiałów. Łączy właściwości tlenu i azotu, aby zapewnić odpowiednią wydajność cięcia przy niższych kosztach. Może jednak wprowadzić zanieczyszczenia, które wpływają na jakość cięcia.
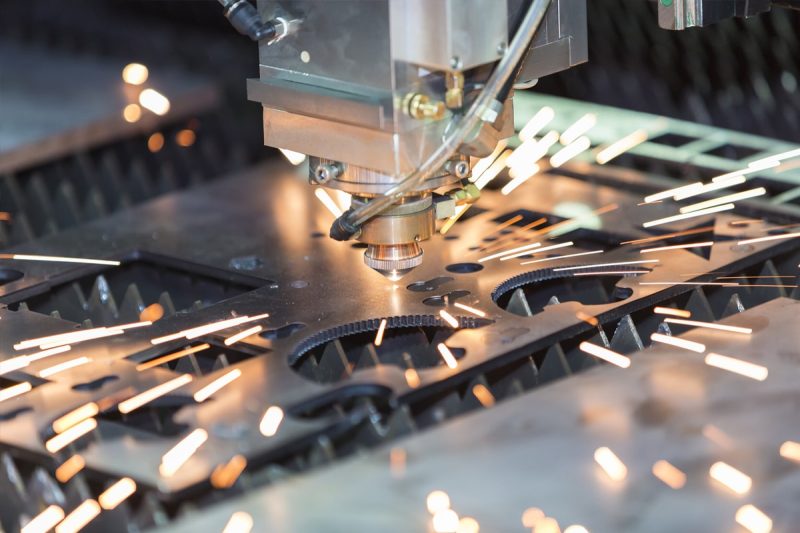
Rodzaje gazów wspomagających
Tlen (O₂)
Zalety
- Zwiększona prędkość cięcia: Tlen reaguje z materiałem w reakcji egzotermicznej, uwalniając dodatkowe ciepło. To dodatkowe ciepło zwiększa prędkość cięcia, dzięki czemu cięcie wspomagane tlenem jest znacznie szybsze, szczególnie w przypadku grubszych materiałów.
- Zwiększona wydajność: Reakcja egzotermiczna zmniejsza moc lasera wymaganą do cięcia materiału, poprawiając ogólną efektywność energetyczną procesu cięcia.
- Czystsze cięcia grubych materiałów: Tlen pomaga uzyskać czystsze cięcia grubszych materiałów, redukując żużel i żużel, co zmniejsza potrzebę intensywnej obróbki końcowej.
Niedogodności
- Utlenianie: Reakcja pomiędzy tlenem a materiałem może powodować utlenianie krawędzi cięcia, co skutkuje bardziej szorstkim wykończeniem powierzchni i możliwymi problemami związanymi z korozją.
- Strefa wpływu ciepła (HAZ): Dodatkowe ciepło wytwarzane w reakcji egzotermicznej zwiększa rozmiar SWC, co może zmienić właściwości mechaniczne materiału w pobliżu krawędzi cięcia i spowodować problemy, takie jak wypaczenie lub zmniejszona integralność strukturalna.
- Ograniczenia dotyczące metali nieżelaznych: Tlen nie jest tak skuteczny jak metale nieżelazne, takie jak aluminium i miedź, które nie reagują tak łatwo z tlenem.
Azot (N₂)
Zalety
- Cięcie bez utleniania: Azot to gaz obojętny, który nie reaguje z materiałem podczas procesu cięcia. Ta właściwość zapobiega utlenianiu, dając czystą, jasną i pozbawioną tlenków krawędź, która idealnie nadaje się do zastosowań wymagających wysokiej jakości wykończenia powierzchni.
- Wysokiej jakości wykończenie powierzchni: Brak utleniania skutkuje gładszą krawędzią i gładszym wykończeniem powierzchni, co zmniejsza lub eliminuje potrzebę obróbki końcowej.
- Zminimalizowana strefa wpływu ciepła (HAZ): Azot pomaga utrzymać małą strefę wpływu ciepła, zachowując właściwości mechaniczne materiału i minimalizując odkształcenie termiczne. Można to wykorzystać do uzyskania precyzyjnych cięć i zastosowań wymagających wąskich tolerancji.
Niedogodności
- Niższe prędkości skrawania: Bez reakcji egzotermicznej zapewnianej przez tlen, cięcie wspomagane azotem zazwyczaj skutkuje niższymi prędkościami skrawania, szczególnie w przypadku grubszych materiałów. Ta mniejsza prędkość wpływa na ogólną produktywność.
- Wyższe wymagania dotyczące mocy lasera: Ponieważ azot nie zapewnia dodatkowego ciepła w procesie cięcia, laser musi zapewnić całą energię potrzebną do cięcia materiału. Wymóg ten może skutkować wyższym zużyciem energii i kosztami operacyjnymi.
- Względy kosztów: Azot może być droższy niż inne gazy, a zwiększone zużycie spowodowane wyższym zapotrzebowaniem na moc lasera może jeszcze bardziej zwiększyć koszty operacyjne.
Skompresowane powietrze
Zalety
- Opłacalność: Sprężone powietrze jest łatwiej dostępne i tańsze niż czyste gazy, takie jak azot i tlen. To sprawia, że jest to ekonomiczny wybór w przypadku wielu zastosowań cięcia laserowego, szczególnie tych obejmujących cieńsze materiały.
- Wszechstronność: Sprężonego powietrza można używać do cięcia szerokiej gamy materiałów, w tym stali miękkiej, stali nierdzewnej i aluminium. Jego wszechstronność sprawia, że jest to praktyczny wybór do cięcia ogólnego.
- Obniżone koszty operacyjne: Ponieważ sprężone powietrze jest niedrogie i powszechnie dostępne, użycie sprężonego powietrza może obniżyć całkowite koszty operacyjne, dzięki czemu nadaje się do operacji na małą skalę lub projektów oszczędnych.
- Korzyści dla środowiska: Stosowanie sprężonego powietrza zmniejsza zależność od gazu w butlach, co z kolei zmniejsza ślad węglowy związany z produkcją i transportem gazu, zapewniając korzyści dla środowiska.
Niedogodności
- Niższa jakość cięcia: Tlen i zanieczyszczenia w sprężonym powietrzu mogą wpływać na jakość cięcia, powodując bardziej szorstkie krawędzie, większą ilość żużla i potencjalne zanieczyszczenie powierzchni cięcia. Problem ten jest szczególnie zauważalny w zastosowaniach wymagających wysokiej jakości powierzchni lub precyzji.
- Ograniczone prędkości cięcia: Sprężone powietrze zazwyczaj tnie z mniejszą prędkością niż cięcie wspomagane tlenem, szczególnie w przypadku grubszych materiałów. To ograniczenie wpływa na produktywność i może nie być odpowiednie w przypadku produkcji na dużą skalę.
- Niespójne wyniki: Jakość i wydajność cięcia sprężonym powietrzem może być niespójna ze względu na różnice w składzie i ciśnieniu dostarczanego powietrza. Ta niespójność sprawia, że osiągnięcie jednolitych wyników w różnych zadaniach cięcia jest trudne.
- Utlenianie i powstawanie żużli: Sprężone powietrze zawiera różnorodne gazy, w tym tlen, które mogą powodować utlenianie i tworzenie się żużli na krawędzi cięcia, co wymaga dodatkowej obróbki końcowej w celu osiągnięcia pożądanych rezultatów.
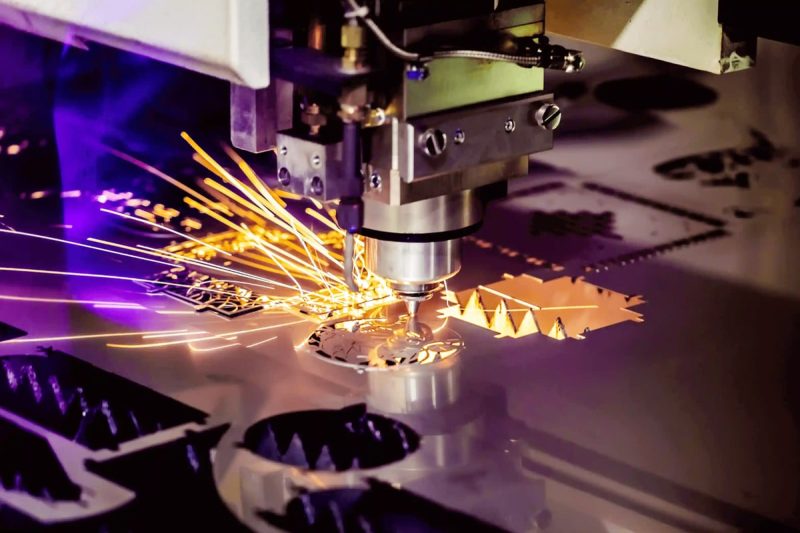
Wpływ na różne materiały
Stal węglowa
Tlen
- Zalety: Do cięcia stali węglowej często stosuje się tlen, ponieważ reaguje on egzotermicznie z materiałem. Reakcja ta generuje dodatkowe ciepło, co znacznie zwiększa prędkość i wydajność cięcia. Powstałe cięcia są zazwyczaj czyste i zawierają minimalną ilość żużla, a zwiększone ciepło pomaga ciąć grubsze sekcje stali węglowej.
- Wady: Reakcja egzotermiczna z tlenem powoduje utlenianie, które, jeśli nie zostanie poddane obróbce, może skutkować bardziej szorstkim wykończeniem powierzchni i możliwą korozją. Strefa wpływu ciepła (HAZ) jest również większa, co może wpływać na właściwości mechaniczne materiału w pobliżu krawędzi cięcia.
Azot
- Zalety: Azot nie reaguje ze stalą węglową, zapobiegając utlenianiu i zapewniając czyste, wolne od tlenków cięcie. Skutkuje to wysokiej jakości wykończeniem powierzchni i mniejszą HAZ, co pozwala zachować właściwości mechaniczne materiału.
- Wady: Brak reakcji egzotermicznej powoduje, że cięcie wspomagane azotem jest wolniejsze niż cięcie tlenem. Aby osiągnąć tę samą prędkość cięcia, wymagana jest większa moc lasera, co zwiększa koszty eksploatacji.
Skompresowane powietrze
- Zalety: Sprężone powietrze jest opłacalną alternatywą do cięcia stali węglowej. Zapewnia równowagę pomiędzy kosztem a wydajnością i nadaje się do cięcia cieńszych profili ze stali węglowej.
- Wady: Tlen zawarty w sprężonym powietrzu może powodować utlenianie i tworzenie się żużlu, co wpływa na jakość cięcia. Prędkości i jakość cięcia są na ogół niższe niż w przypadku stosowania czystego tlenu lub azotu.
Stal nierdzewna
Tlen
- Zalety: Tlen można stosować do cięcia stali nierdzewnej, zapewniając duże prędkości cięcia dzięki reakcji egzotermicznej. Ta reakcja może również pomóc w uzyskaniu czystych cięć przy minimalnej ilości żużlu.
- Wady: Użycie tlenu może powodować utlenianie, co może prowadzić do odbarwień krawędzi i potencjalnych problemów z korozją. Warstwa tlenku może wymagać dodatkowej obróbki końcowej w celu uzyskania pożądanej jakości powierzchni.
Azot
- Zalety: Azot to gaz preferowany do cięcia stali nierdzewnej, ponieważ zapobiega utlenianiu, co pozwala uzyskać czystą, błyszczącą i pozbawioną tlenków krawędź. Obojętny charakter azotu pozwala uzyskać wysokiej jakości kawałki przy minimalnej konieczności obróbki końcowej. Azot pomaga również zachować właściwości mechaniczne materiału, minimalizując strefę wpływu ciepła.
- Wady: Azot ma mniejszą prędkość cięcia i wymaga większej mocy lasera niż tlen, co powoduje zwiększone zużycie energii i koszty operacyjne.
Skompresowane powietrze
- Zalety: Sprężone powietrze umożliwia cięcie cieńszych odcinków stali nierdzewnej. Jest bardziej opłacalny niż czysty gaz i stanowi realną opcję w zastosowaniach, które nie wymagają dużej precyzji.
- Wady: Tlen w sprężonym powietrzu może powodować utlenianie i tworzenie się żużla, wpływając na jakość cięcia. Krawędź może wymagać dodatkowego oczyszczenia i wykończenia po cięciu.
Aluminium i metale nieżelazne
Tlen
- Zalety: Tlen nie jest generalnie zalecany do cięcia aluminium i innych metali nieżelaznych ze względu na ich wysoki współczynnik odbicia i niską absorpcję wiązki lasera. Jednakże w niektórych przypadkach tlen może pomóc w cięciu grubszych skrawków, sprzyjając reakcji egzotermicznej.
- Wady: Tlen może powodować poważne utlenianie, w wyniku czego powierzchnia cięcia jest szorstka i porowata. Utlenianie to może negatywnie wpłynąć na właściwości i wygląd materiału, wymagając rozległej obróbki końcowej.
Azot
- Zalety: Azot jest bardzo skuteczny przy cięciu aluminium i innych metali nieżelaznych. Zapobiega utlenianiu, zapewniając czystą, jasną i wysokiej jakości krawędź. Azot pomaga również zminimalizować strefę wpływu ciepła, zachowując właściwości mechaniczne materiału.
- Wady: Cięcie azotem jest wolniejsze niż przy użyciu tlenu i wymaga większej mocy lasera do cięcia materiału, co zwiększa koszty operacyjne.
Skompresowane powietrze
- Zalety: Sprężone powietrze jest opłacalną opcją do cięcia cieńszych przekrojów aluminium i metali nieżelaznych. Może zapewnić zadowalającą wydajność cięcia w zastosowaniach, w których precyzja nie jest krytyczna.
- Wady: Tlen w sprężonym powietrzu może powodować utlenianie i tworzenie się żużla, wpływając na jakość cięcia. Krawędzie mogą wymagać dodatkowej obróbki końcowej w celu uzyskania pożądanego wykończenia.
Materiały niemetalowe
Tlen
- Zalety: Tlenu można używać do cięcia materiałów niemetalowych, takich jak drewno, akryl i plastik. Reakcja egzotermiczna z tlenem może zwiększyć prędkość i wydajność cięcia niektórych materiałów.
- Wady: Użycie tlenu może powodować przypalenie i przypalenie materiałów takich jak drewno i akryl, co negatywnie wpływa na jakość powierzchni. Może to skutkować koniecznością przeprowadzenia dodatkowych procesów wykończeniowych w celu uzyskania pożądanego wyglądu.
Azot
- Zalety: Azot doskonale nadaje się do cięcia materiałów niemetalowych, takich jak tworzywa sztuczne i ceramika, które należy chronić przed utlenianiem. Zapobiega przebarwieniom i zapewnia czyste, wysokiej jakości krawędzie, minimalizując jednocześnie uszkodzenia termiczne.
- Wady: Cięcie wspomagane azotem może być wolniejsze niż tlenem i wymaga większej mocy lasera, aby osiągnąć pożądaną prędkość cięcia.
Skompresowane powietrze
- Zalety: Sprężone powietrze jest ekonomicznym rozwiązaniem do cięcia materiałów niemetalowych i zapewnia odpowiednią wydajność cięcia w różnych zastosowaniach. Nadaje się do zastosowań, w których precyzja i jakość nie są krytyczne.
- Wady: Zanieczyszczenia w sprężonym powietrzu mogą wpływać na jakość cięcia, powodując ostre krawędzie i potencjalne zanieczyszczenie. Jakość i prędkość cięcia mogą nie być porównywalne z jakością i szybkością cięcia czystych gazów, takich jak tlen czy azot.
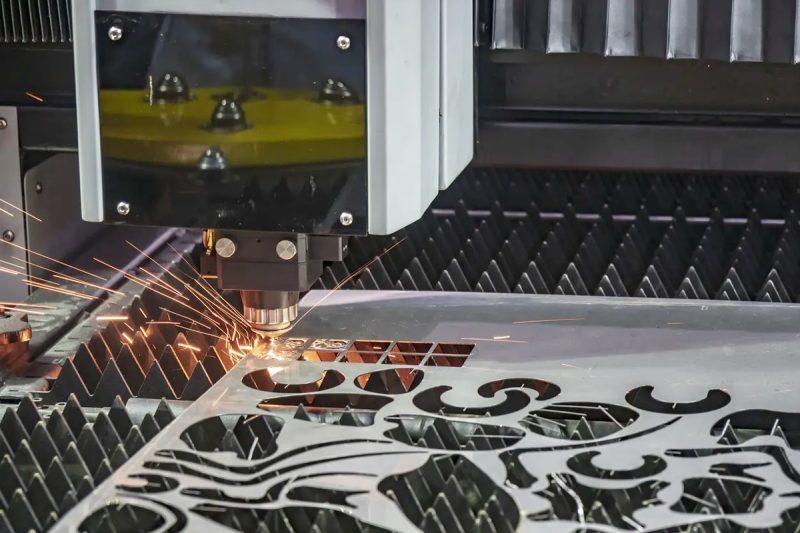
Optymalizacja doboru gazu wspomagającego
Rodzaj i grubość materiału
Rodzaj i grubość ciętego materiału są głównymi czynnikami branymi pod uwagę przy wyborze gazu wspomagającego. Różne materiały różnie reagują na różne gazy, wpływając na jakość i wydajność cięcia.
- Stal węglowa: Tlen jest często pierwszym wyborem do cięcia stali węglowej, ponieważ reaguje egzotermicznie, zwiększając prędkość i wydajność cięcia. W przypadku grubszych stali węglowych tlen może zapewnić ciepło potrzebne do skutecznego cięcia materiału. W przypadku cieńszych stali węglowych można zastosować azot, aby uzyskać czyste, wolne od utleniania cięcie, aczkolwiek w wolniejszym tempie.
- Stal nierdzewna: Azot jest idealny do cięcia stali nierdzewnej, ponieważ zapobiega utlenianiu i zapewnia wysokiej jakości gładką krawędź. W przypadku bardzo grubej stali nierdzewnej można użyć tlenu w celu zwiększenia prędkości skrawania, ale spowoduje to utlenianie i wymaga dodatkowej obróbki.
- Aluminium i metale nieżelazne: Azot jest pierwszym wyborem do cięcia aluminium i metali nieżelaznych, aby uniknąć utleniania i uzyskać czyste cięcie. W przypadku mniej krytycznych zastosowań sprężone powietrze może być opłacalną alternatywą, chociaż może powodować pewne utlenianie.
- Materiały niemetaliczne: Do cięcia niemetali, takich jak tworzywa sztuczne, ceramika i drewno, często stosuje się azot, aby zapobiec przebarwieniom i uzyskać wysoką jakość krawędzi. Tlenu można użyć do szybszego cięcia niektórych niemetali, ale może on spowodować przypalenie lub przypalenie.
Wymagana jakość cięcia
Wymagana jakość cięcia jest kluczowym czynnikiem przy wyborze odpowiedniego gazu wspomagającego. Zastosowania precyzyjne zazwyczaj wymagają wysokiej jakości cięcia przy minimalnym utlenieniu i gładkich krawędziach.
- Wysokiej jakości wykończenie powierzchni: Azot jest często najlepszym wyborem do zastosowań wymagających precyzyjnego, czystego i wolnego od utleniania cięcia. Zapobiega utlenianiu, zapewniając gładkie krawędzie i wysokiej jakości wykończenie powierzchni.
- Ogólna jakość: Tlen może zapewnić wysokiej jakości cięcie przy minimalnej ilości żużlu, ale krawędzie mogą wymagać dodatkowego czyszczenia ze względu na utlenianie. Sprężone powietrze może być odpowiednie do mniej krytycznych zastosowań, w których nie jest konieczna najwyższa jakość wykończenia powierzchni.
Szybkość cięcia i wydajność
Na prędkość i wydajność cięcia wpływa rodzaj użytego gazu wspomagającego. Celem jest osiągnięcie najwyższej możliwej prędkości bez utraty jakości cięcia.
- Maksymalna prędkość: Zapewnia najszybsze prędkości cięcia stali węglowej i grubszych materiałów dzięki egzotermicznej reakcji tlenu, która dodaje dodatkowe ciepło do procesu cięcia.
- Zrównoważona prędkość i jakość: Azot zapewnia równowagę pomiędzy szybkością a wysokiej jakości cięciami, chociaż może wymagać większej mocy lasera i cięcia z mniejszą prędkością w porównaniu z tlenem.
- Ekonomiczna prędkość: Sprężone powietrze stanowi kompromis między szybkością a kosztami i jest odpowiednie do zastosowań, w których dopuszczalne są umiarkowane prędkości skrawania i rozsądna jakość.
Rozważania dotyczące kosztów
Koszt jest ważnym czynnikiem wpływającym na wybór gazu, wpływającym na koszty operacyjne i ogólną opłacalność.
- Obniżone koszty operacyjne: Sprężone powietrze jest najbardziej ekonomicznym wyborem, ponieważ jest łatwo dostępne i tańsze niż czyste gazy, takie jak tlen i azot. Idealnie nadaje się do cięcia mniej krytycznych materiałów lub gdy priorytetem są ograniczenia budżetowe.
- Wyższa jakość i wyższy koszt: Azot, choć droższy, zapewnia lepszą jakość cięcia. Dodatkowy koszt jest uzasadniony lepszą jakością i zmniejszoną potrzebą późniejszej obróbki.
- Równowaga kosztów i wydajności: Tlen oferuje rozwiązanie pośrednie, zapewniając duże prędkości cięcia i rozsądną jakość przy umiarkowanych kosztach. Nadaje się do wielu zastosowań przemysłowych, gdzie ważna jest zarówno szybkość, jak i jakość.
Wymagania dotyczące przetwarzania końcowego
Potrzeby związane z obróbką końcową mogą mieć wpływ na wybór gazu wspomagającego, ponieważ niektóre gazy zapewniają czystsze cięcie, co może ograniczyć prace wykończeniowe.
- Minimalna obróbka końcowa: Azot zapewnia czyste, wolne od utleniania cięcia, zmniejszając potrzebę rozległej obróbki końcowej oraz oszczędzając czas i koszty operacji wykańczających.
- Umiarkowana obróbka końcowa: Cięcie tlenowe może wymagać dodatkowych etapów w celu usunięcia tlenków i uzyskania pożądanego wykończenia powierzchni. Jednakże większe prędkości skrawania mogą zrekompensować część dodatkowych kosztów.
- Zwiększona obróbka końcowa: Sprężone powietrze może powodować więcej żużlu i utleniania, co wymaga szerszej obróbki końcowej w celu oczyszczenia i wykończenia krawędzi. Może to wydłużyć całkowity czas i koszt produkcji.
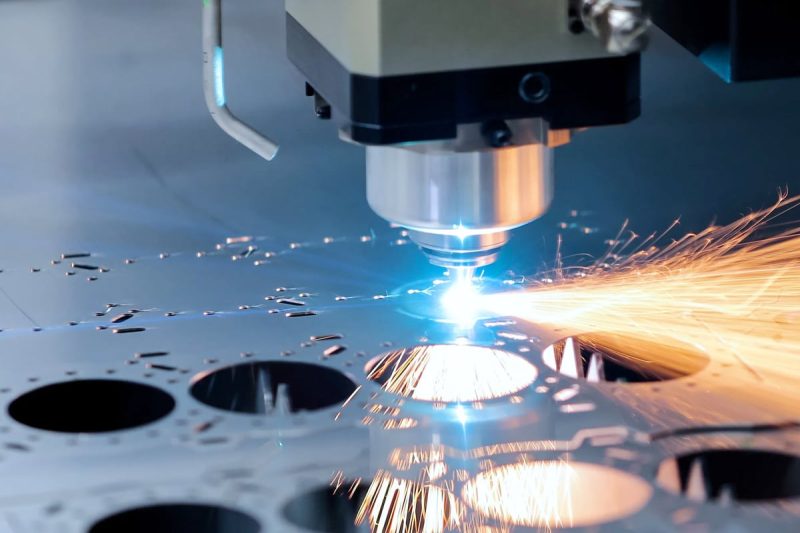
Streszczenie
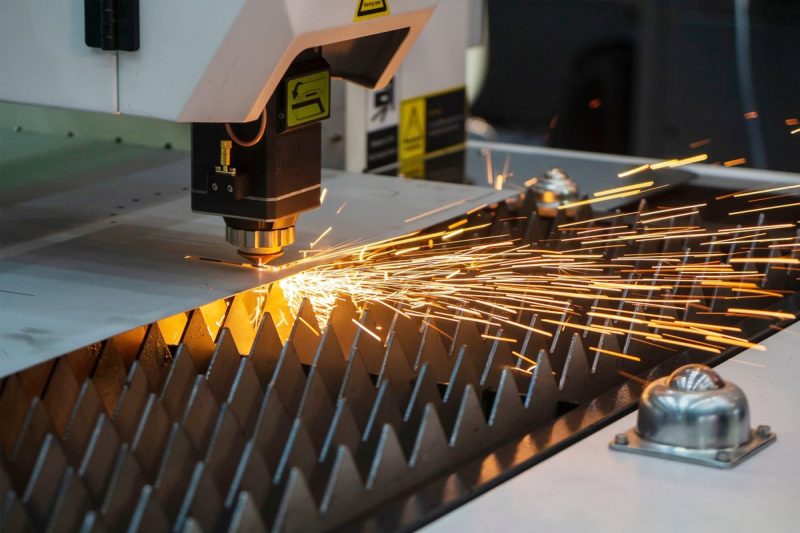
Uzyskaj rozwiązania w zakresie cięcia laserowego
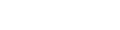
- [email protected]
- [email protected]
- +86-19963414011
- Nr 3 Strefa A, strefa przemysłowa Lunzhen, miasto Yucheng, prowincja Shandong.