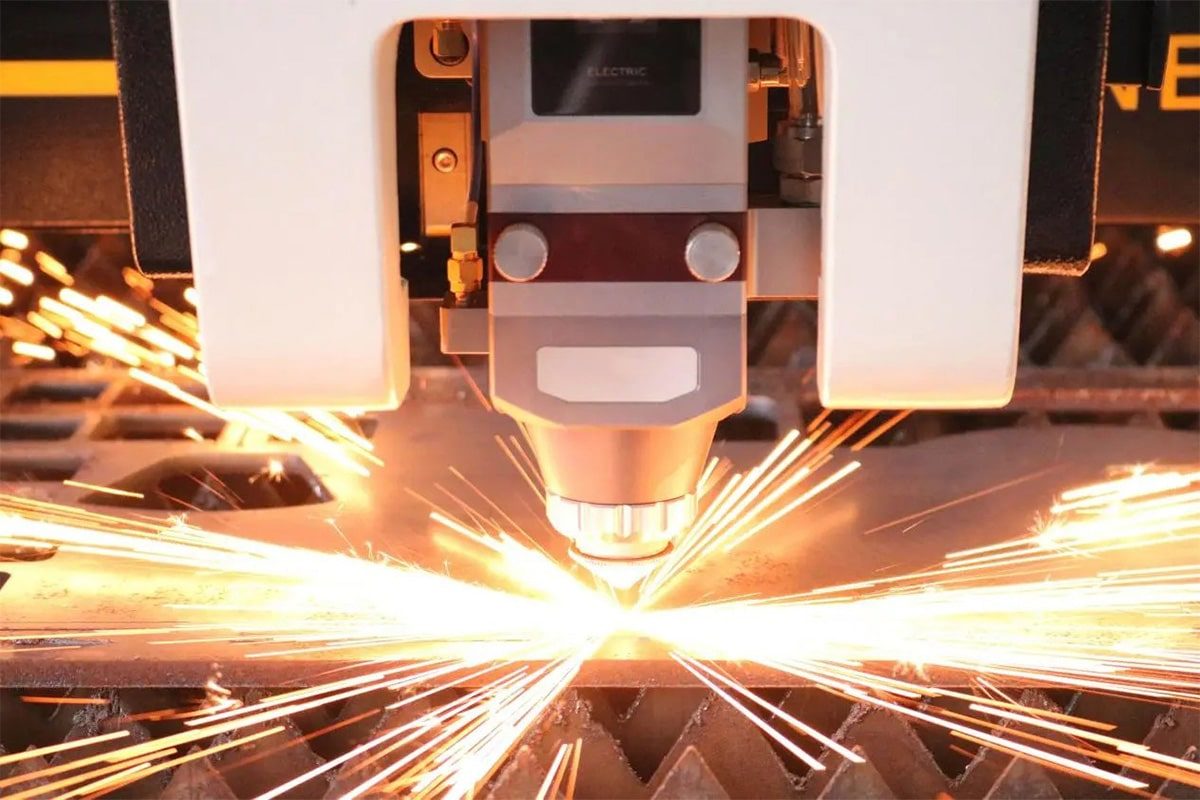
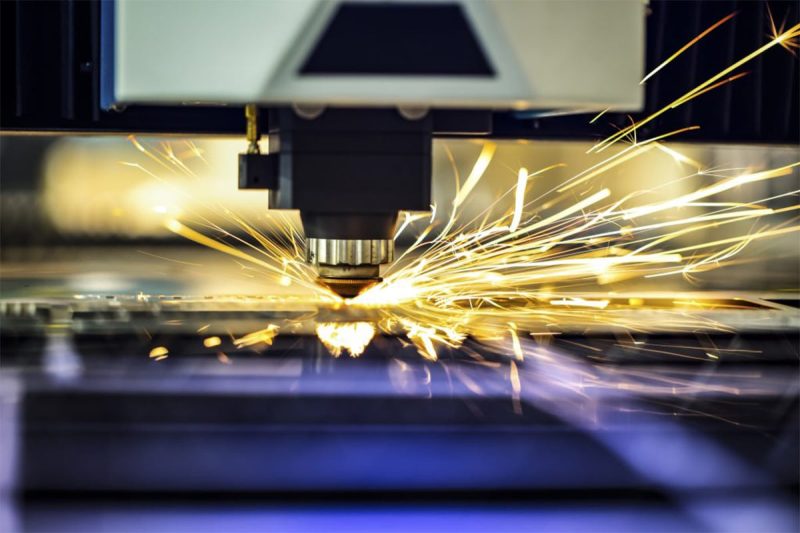
Laser Cutting Basics
Working Principle
Laser cutting is a non-contact, heat-based manufacturing process that uses a focused laser beam to melt, burn, or vaporize material, resulting in precise cuts with high precision. The basic working principle includes the following steps:
- Laser Generation: The laser cutter uses a laser source to generate a high-intensity laser beam. The beam is generated by stimulating a laser medium (e.g., gas, solid material) to emit light.
- Beam Focusing: The generated laser beam is guided through a series of mirrors or optical fibers and focused onto a small spot on the surface of the material using a lens. The focusing lens concentrates the laser energy into a very narrow, high-density spot.
- Material Interaction: When the focused laser beam strikes the material, it rapidly heats the area, causing it to melt, burn, or vaporize. This localized heating enables the laser to cut the material with minimal impact on the surrounding area.
- Material Removal: High-pressure assist gases (such as oxygen, nitrogen, or air) are typically used to blow away molten material, clear the cutting path and increase cutting speed. The type of assist gas used can also affect the quality of the cut.
- Motion Control: The laser head is guided along the desired cutting path by a computer-controlled motion system that precisely follows the programmed design, ensuring accuracy and repeatability.
Different Types of Laser Cutting Machines
Fiber Laser Cutting Machines
Fiber laser generators are solid-state laser generators that produce a laser beam through a process called “fiber amplification.” Light is generated in an active optical fiber doped with rare earth elements and then directed and focused onto the cutting surface. Fiber lasers are known for their efficiency and effectiveness in cutting metals.
- Pros: Fiber laser generators are extremely efficient at converting electrical energy into laser energy, resulting in lower power consumption and faster cutting speeds, especially for thin and reflective materials such as stainless steel, aluminum, and brass.
- Cons: While fiber lasers are well suited for metal cutting, they are less effective on non-metallic materials, which limits their versatility compared to CO2 lasers.
CO2 Laser Cutting Machines
CO2 lasers are one of the most widely used laser-cutting technologies. They produce a laser beam by exciting a gas mixture (primarily carbon dioxide) with an electrical discharge. CO2 lasers are particularly well suited for cutting non-metallic materials and some metals.
- Pros: CO2 lasers are extremely efficient at cutting organic materials such as wood, acrylic, leather, and plastic. They also provide smooth, clean cuts with minimal post-processing requirements.
- Cons: CO2 lasers are generally less efficient at cutting metals than fiber lasers and require extensive cooling, resulting in higher power consumption.
Common Applications of Laser Cutting
Laser cutting is used in a wide range of industries for its precision, speed, and versatility. Here are some common applications:
- Metalworking: Laser cutting is widely used in the metalworking industry to cut a variety of metals, including steel, aluminum, brass, and copper. It is often used to make parts for automotive, aerospace, and industrial machinery.
- Electronics: In the electronics industry, laser cutting is used to precisely cut circuit boards, microchips, and other parts. Cutting these parts requires high precision and strict requirements for thermal deformation.
- Signage and Advertising: CO2 lasers are often used to cut and engrave acrylics, plastics, and other materials for signage, displays, and decorative applications.
- Medical Devices: Laser cutting is used in the medical field to make precision parts such as stents, surgical instruments, and implants. These parts require high precision and clean edges.
- Textile and Fashion: The textile industry uses lasers to cut cloth and leather, and can quickly and accurately cut intricate designs and patterns.
- Jewelry: The jewelry industry uses laser cutting to cut and engrave precious metals and gemstones, allowing for intricate and delicate designs.
- Aerospace: In the aerospace sector, laser cutting is used to manufacture lightweight, high-strength components from advanced materials, ensuring precision and structural integrity.
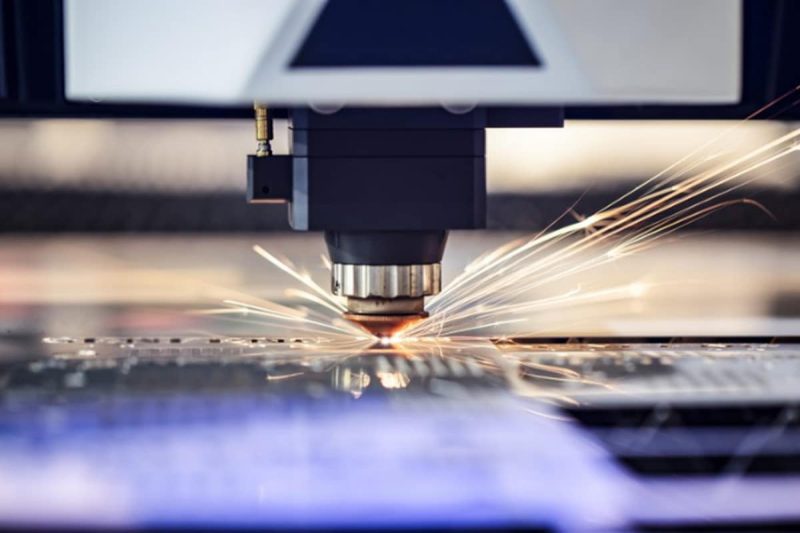
Power Consumption Components of Laser Cutting Machines
Laser Generator
The laser generator, or laser source, is the heart of any laser cutting machine. It produces the laser beam used to cut the material. The power consumption of the laser generator depends on the type of laser (CO2, fiber), the power output of the laser, and the efficiency of the system.
- CO2 Laser Generators: They are generally less efficient than fiber lasers, typically around 10-20%. For example, a CO2 laser with a power output of 200W might consume about 1-2kW of electricity. The inefficiency is due to the discharge required to excite the CO2 gas mixture, as well as energy lost in the generation of heat.
- Fiber Laser Generators: Fiber laser generators are more efficient, converting up to 25-30% of the electrical energy into laser light. This means that a fiber laser generator with an output power of 4 kW might only consume about 13.5-16 kW of electrical energy. This higher efficiency means lower power consumption for the same cutting performance, making fiber laser generators more energy-efficient and cost-effective.
Cooling Systems
Air Cooling
Water Cooling
Motion Control System
Motor
Drive
Controller
Control System
Art and Sculpture
Security Features
CNC Control
User Interface and Software
Auxiliary Systems
Air Supply System
Exhaust and Filtration System
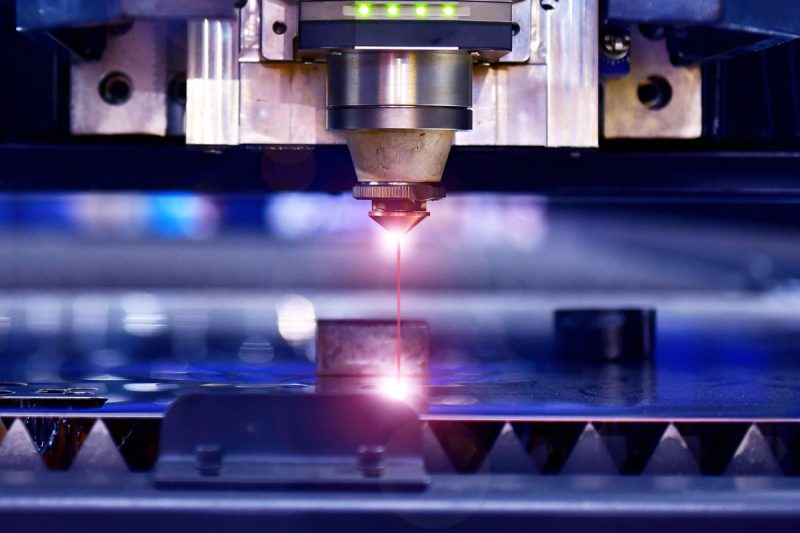
Factors Affecting Power Consumption
Laser Power (Wattage)
Laser power, measured in watts (W), is one of the most important factors affecting power consumption. The wattage of a laser determines the energy intensity of the beam, which directly affects the machine’s ability to cut different materials.
- Higher Wattage: Machines with higher wattage can cut thicker, harder materials faster. However, they also consume more electricity. For example, a 6kW laser generator consumes much more energy than a 3kW laser generator, especially when running at full capacity.
- Matching Power to Application: Laser power needs to be matched to the specific cutting application. Using a high-power laser to cut thin materials can result in unnecessary power consumption and can also affect cutting accuracy.
- Variable Power Settings: Some machines allow for variable power settings, enabling operators to adjust the power based on the material and cutting requirements. This flexibility helps reduce power consumption when full-power lasers are not needed.
Material Type and Thickness
- Material Type: Different materials absorb and respond to laser energy in different ways. Metals such as steel, aluminum, and copper require more power to cut than non-metals such as acrylic, wood, or plastic. Reflective metals, in particular, can present challenges and often require higher power levels or specialized laser types (such as fiber lasers) to cut effectively.
- Material Thickness: Thicker materials require more energy to cut because the laser must penetrate deeper into the material. For example, cutting 20 mm thick stainless steel will require more power and time than cutting 5 mm thick sheet metal. Thicker materials may also require slower cutting speeds, further increasing power consumption.
- Material Quality: The quality of the material, such as its purity and surface finish, can also affect the efficiency of the laser. Materials that contain impurities or have a rough surface may require more power to achieve a clean cut.
Cutting Speed and Precision
Cutting speed and precision are closely related to power consumption, as both affect the duration and intensity of laser operation.
- Cutting Speed: Faster cutting speeds generally require higher power levels to maintain the energy density required for effective cutting. However, operating at very high speeds results in increased power consumption. Conversely, slower speeds can reduce power consumption but may require the laser to operate longer, balancing overall energy costs.
- Precision Requirement: High-precision cutting generally requires slower cutting speeds to achieve detailed and accurate results. This slower operation increases the active time of the laser generator, resulting in higher energy consumption. In applications where precision is critical, such as in medical device manufacturing or complex metal processing, power consumption may be higher due to the need for precise control and stable operation.
- Optimization: Balancing cutting speed and precision is key to optimizing power consumption. Advanced control systems can help by dynamically adjusting speed and power settings based on the specific cutting task.
Assist Gas Use
The use of assist gas, such as oxygen, nitrogen, or air, plays a critical role in the laser cutting process, affecting both cut quality and total power consumption.
- Gas Type: The choice of assist gas affects the power required for cutting. For example, oxygen can increase the cutting speed of steel by promoting an exothermic reaction, which may reduce the required laser power. However, it can also lead to increased energy consumption in the gas supply system. Nitrogen, used for cutting stainless steel and aluminum, prevents oxidation but requires more laser power to achieve the same cutting speed.
- Gas Pressure: The pressure of the gas supply also affects power consumption. Higher gas pressures can improve cut quality and speed, but increase the energy required by the gas supply system, which increases total power consumption.
- Optimizing Gas Use: Effectively managing gas flow and pressure can help minimize power consumption. Automated systems that adjust gas use based on cutting parameters can save energy.
Duty Cycle and Operating Conditions
The duty cycle and operating conditions of a laser-cutting machine have a significant impact on power consumption. The duty cycle refers to the percentage of time that the machine is running at full power in a given period.
- High-Duty Cycle: Machines with high-duty cycles consume more power due to long periods of high-intensity operation. This is common in industrial environments, as laser-cutting machines need to run continuously to meet production needs. Ensuring that the machine is well maintained and running efficiently can help manage power consumption in such situations.
- Intermittent Use: Machines that are used intermittently may have lower overall power consumption, but the energy cost per unit of output may be higher and efficiency may be reduced due to frequent startups and shutdowns.
- Environmental Conditions: The operating environment, including temperature, humidity, and ventilation, can affect the power consumption of the machine. For example, in a hot environment, the cooling system needs to work harder and consume more power. Dusty or poorly ventilated environments can also lead to more frequent maintenance and cleaning, indirectly affecting energy use.
- Maintenance: Regular maintenance of the laser cutting machine (including the laser generator, cooling system, and optics) ensures that the machine operates at optimal efficiency and reduces unnecessary power consumption.
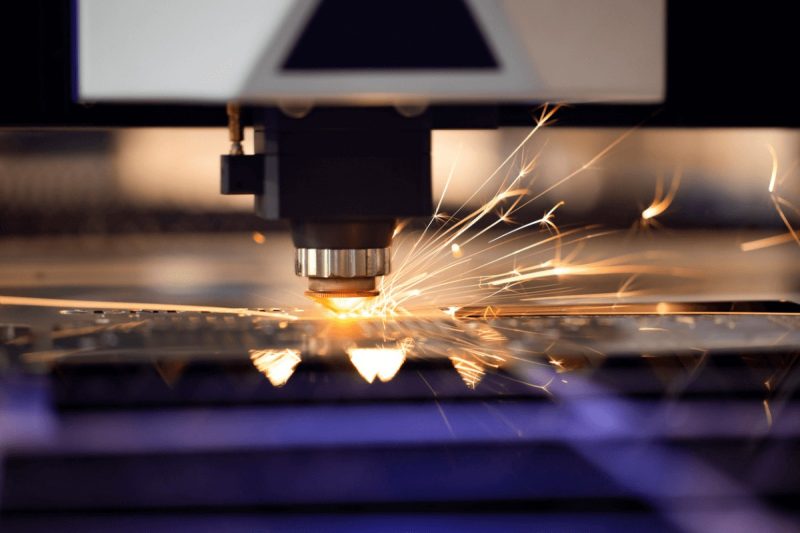
Energy-Saving Measures for Laser-Cutting Machines
Regular Maintenance and Calibration
Regular maintenance and calibration can ensure that your laser-cutting machine is operating at peak efficiency. Over time, wear and tear can cause components to become less efficient, which can lead to increased power consumption.
- Maintenance: Routine maintenance includes inspecting and replacing worn parts, such as mirrors, lenses, and motors, which can degrade over time. Ensuring these components are clean and in good condition helps maintain the efficiency of the machine and reduces unnecessary energy use.
- Calibration: Regular calibration ensures that the laser is accurately aligned and the motion control system is operating precisely. A misaligned laser or a poorly calibrated system can result in inefficient cutting, requiring more power and time to achieve the desired results.
Advanced Cooling Technologies
Cooling systems can maintain the optimal operating temperature of a laser cutting machine, but they can also be a significant source of energy consumption. Implementing advanced cooling technologies can reduce this energy demand.
- Water Cooling with Chillers: High-power laser cutting machines often require a water-cooling system that uses a chiller to keep the temperature low. Modern chillers are designed with energy efficiency in mind, using advanced refrigeration cycles and variable-speed compressors to minimize power consumption.
- Air Cooling for Low-Power Lasers: For low-power laser cutting machines, air cooling can be an energy-efficient alternative. These systems use ambient air to cool the laser generator, eliminating the need for energy-consuming water-cooling systems. Ensuring that the air-cooling system is well-ventilated and free of obstructions can further improve its efficiency.
- Hybrid Cooling Systems: Some advanced laser cutting machines use hybrid cooling systems that combine air and water cooling. These systems dynamically adjust the cooling method based on the laser generator’s power output and operating conditions, optimizing energy use.
Energy Management Software
- Real-time Monitoring: Energy management systems track power usage of various components, such as the laser generator, cooling system, and motion control system. Real-time data enables operators to identify inefficiencies and adjust settings to minimize energy consumption.
- Automatic Control: Advanced energy management software can automatically adjust machine settings based on cutting requirements and operating conditions. For example, it can reduce laser power during idle times or optimize the duty cycle to balance cutting speed and energy usage.
- Reporting and Analysis: Detailed reporting and analysis help businesses understand their energy consumption patterns and identify opportunities for improvement. By analyzing trends and performance data, businesses can implement targeted energy-saving measures.
Invest in Energy-Efficient Equipment
Selecting energy-efficient equipment can significantly reduce the power consumption of your laser-cutting machine. Investing in modern energy-efficient technology can achieve long-term cost savings and reduce your environmental footprint.
- High-Efficiency Laser Generators: Modern fiber laser generators are more energy-efficient than traditional CO2 laser generators, converting a higher percentage of electrical energy into laser light. Upgrading to high-efficiency laser generators can significantly reduce power consumption, especially in high-volume cutting operations.
- High-Efficiency Motors and Drives: Selecting energy-efficient motors and drives for motion control systems can also reduce power consumption. Servo motors with advanced drive technology provide precise control while minimizing energy waste, while newer drive systems can optimize power transmission to reduce consumption.
- Energy-Efficient Auxiliary Systems: Auxiliary systems, such as air supply and exhaust systems, can also be optimized for energy efficiency. Investing in low-power, high-efficiency air compressors, and advanced filtration systems can reduce the energy requirements of these support systems.
Process Optimization
Optimizing the laser-cutting process itself is a key strategy for reducing power consumption. Process optimization includes adjusting cutting parameters, improving material handling, and streamlining workflows to minimize energy use.
- Cutting Parameters: Adjusting cutting speed, laser power, and assist gas flow can optimize energy use. For example, reducing laser power for thinner materials or adjusting cutting speed to match material thickness can reduce overall power consumption without sacrificing cut quality.
- Material Handling: Efficient material handling reduces idle time and increases the overall throughput of the laser cutting process. Automated loading and unloading systems can minimize downtime and ensure that the laser-cutting machine is operating at peak efficiency.
- Workflow Simplification: Streamlining workflows to reduce bottlenecks and optimize machine utilization can also save energy. Efficient scheduling and job sequencing can minimize machine idle time and ensure efficient use of energy.
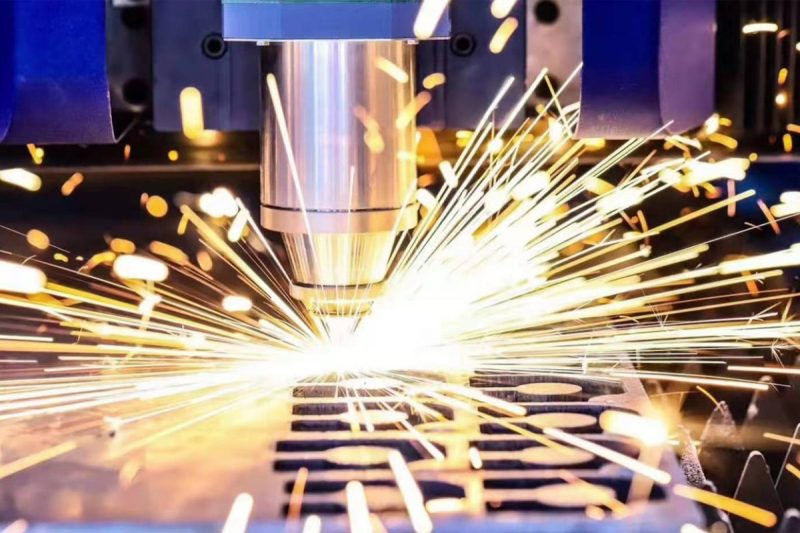
Summary
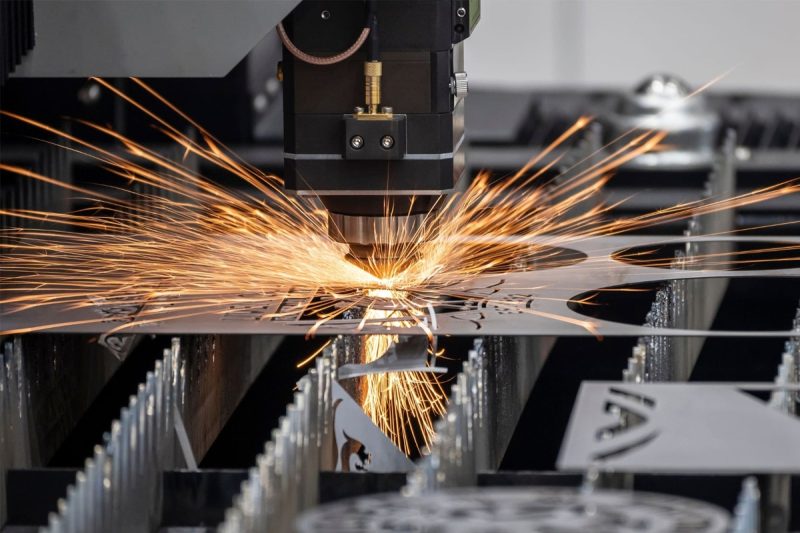
Get Laser Cutting Solutions
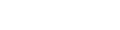
- [email protected]
- [email protected]
- +86-19963414011
- No. 3 Zone A, Lunzhen Industrial Zone,Yucheng City , Shandong Province.