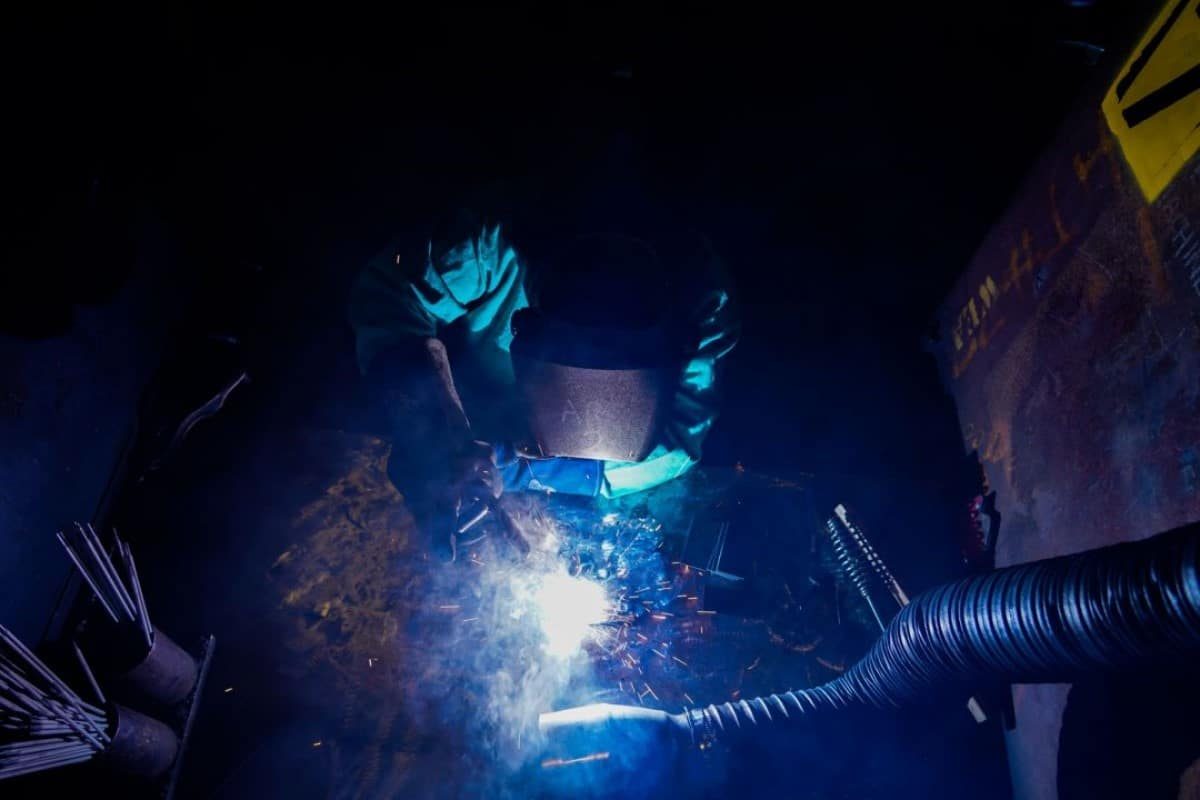
Power Requirements And Electrical Safety Precautions For Laser Welding Machines
In modern industrial manufacturing, laser welding technology has become an indispensable process, known for its high efficiency, high precision, and wide applicability. As the core device of this technology, laser welding machines play a vital role in production lines in various fields, from automobile manufacturing to electronic equipment manufacturing to the aerospace field. However, the stability and safety of the laser welding process depend on multiple factors, one of the most important of which are the power supply and related electrical safety measures.
To minimize potential electrical risks, this article will discuss the power requirements and electrical safety precautions of laser welding machines, including understanding how laser welding machines work, the power and voltage requirements of laser welding machines, and what electrical safety precautions are required for laser welding machines Risks and how to avoid them, etc.
Table of contents
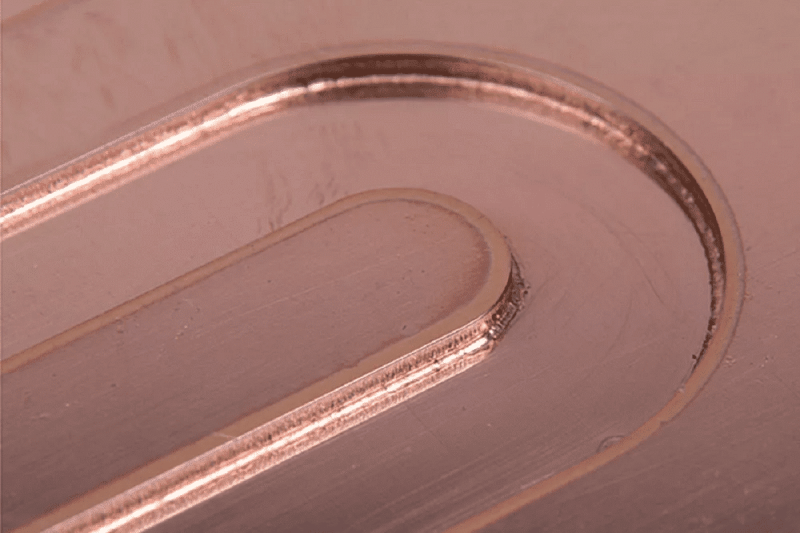
Working principle of laser welding machine
The laser welding machine is a high-precision welding equipment that uses laser beams to heat, melt, and connect workpieces. Its working principle is based on the high-energy characteristics of the laser and the absorption and conduction of the laser by materials.
- Laser generation: The laser welding machine contains a laser generator inside, usually a gas laser generator or a solid laser generator. In a laser generator, energy is converted into laser beams, which are highly focused and capable of delivering high energy density in a very short time.
- Beam focusing: The laser beam is focused through a lens or mirror so that it can be accurately focused on the welding area. The focused laser beam has extremely high energy density and can quickly heat the workpiece surface.
- Material heating and melting: When the laser beam irradiates the surface of the workpiece, the irradiated material absorbs the laser energy and heats up rapidly. As the temperature increases, the material begins to melt and form a molten pool. The high energy density of the laser beam allows the temperature of the molten pool to reach a temperature high enough to melt the material, while also creating a molten pool in a short time.
- Joining and solidification: When the surfaces of two workpieces are heated to a high enough temperature, their molten pools fuse and form a join. Under the control of the laser welding machine, the moving speed and focus position of the laser beam are precisely adjusted to ensure the formation of the molten pool and the quality of the connection. Once welding is complete, the molten pool cools and solidifies, forming a strong welded joint.
Therefore, the welding method has the characteristics of high efficiency, high precision, and adaptability to various materials, and has been widely used in the modern manufacturing industry.
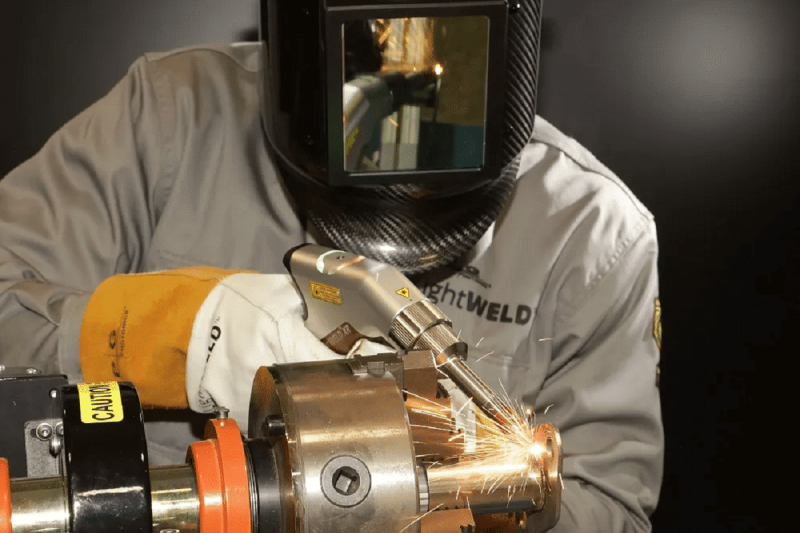
Power supply and voltage requirements of laser welding machine
As a high-precision and high-efficiency welding equipment, laser welding machine has strict requirements for a stable and reliable power supply. While ensuring the normal operation of the laser welding machine, appropriate voltage and power configuration are also key factors to ensure welding quality and operational safety. The following are the main contents of the power supply and voltage requirements of the laser welding machine:
Stable power supply
Laser welding machines have high requirements for the stability of the power supply. A stable power supply can ensure that the laser welding machine can provide sufficient power during operation and maintain the stability of the laser beam. The instability of the power supply will cause power fluctuations during the welding process, thus affecting the welding quality and efficiency.
Suitable voltage frequency
Generally speaking, laser welding machines are suitable for 50Hz or 60Hz AC power supply. A mismatch in voltage and frequency may cause the laser welding machine to fail to start normally or work unstable, so it is necessary to ensure that the power supply provided has a suitable frequency.
Suitable voltage level
Different models of laser welding machines may have different voltage level requirements. Normally, the voltage requirements of laser welding machines are between 200V and 400V. Ensuring that the power supply voltage provided to the laser welding machine meets the equipment specifications is an important step to ensure its normal operation.
Protection against voltage fluctuations
To sum up, choosing a laser cutting machine suitable for specific applications is of great significance to an enterprise’s production efficiency, product quality, cost control, and market competitiveness. Therefore, when choosing a laser cutting machine, companies should fully consider their own production needs and product characteristics, and choose the most suitable model and specifications.
Power cord and socket standards
To provide a stable power supply, you must ensure that the power lines and sockets comply with the safety standards of the corresponding country or region. Correct power line and socket standards can effectively reduce power failures and safety risks and ensure the normal operation of the laser welding machine.
The power and voltage requirements of laser welding machines are important factors in ensuring the normal operation of the equipment and welding quality. Only in this way can the advantages of laser welding technology be fully utilized, production efficiency improved, welding quality ensured, and the safety of operators and equipment guaranteed.
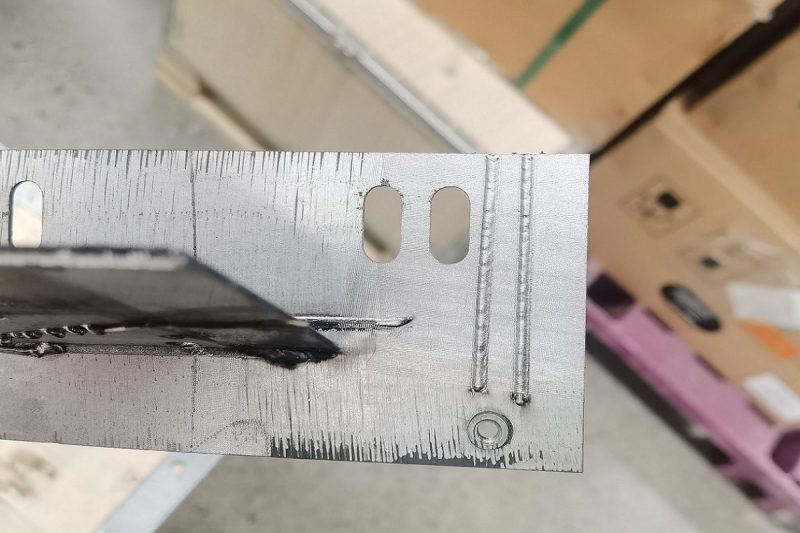
Electrical safety risks of laser welding machines
The laser welding machine is a high-energy electrical equipment, and there are many potential electrical safety risks during its operation. The following are some of the main risks:
- Electric shock risk: Because the working principle of laser welding machines involves high-energy laser beams and high-voltage power supplies. If operators come into contact with live parts or equipment that is not properly grounded, they may be injured by electric shock or even life-threatening.
- Fire risk: The laser welding machine generates a large amount of heat when working. If the equipment has poor heat dissipation or an electrical fault, it may cause the equipment to overheat and cause a fire. In addition, short circuits or overloads in electrical lines can also cause fires.
- Risk of leakage: The laser welding machine generates a lot of heat when working. If the equipment has poor heat dissipation or an electrical fault, it may cause the equipment to overheat, which may lead to a fire. In addition, short circuits or overloads in electrical lines can also cause fires.
- Overload risk: The laser welding machine generates a lot of heat when working. If the equipment has poor heat dissipation or an electrical fault, it may cause the equipment to overheat, which may lead to a fire. In addition, short circuits or overloads in electrical lines can also cause fires.
- High-temperature risk: The laser welding machine will generate high temperatures when working, and the temperature in the welding area is very high, which can easily cause burn accidents. In addition, the high temperature of the equipment may cause surrounding materials to catch fire or burn the operator.
- Electromagnetic radiation risks: Laser welding machines will produce electromagnetic radiation when working. Long-term exposure to electromagnetic radiation may have effects on human health, such as eye damage, skin burns, etc.
- Risk of equipment failure: The electrical equipment of the laser welding machine may have design defects, manufacturing defects, or aging problems. These problems may cause equipment failure or failure, increasing the safety risks of operators and equipment.
To reduce these risks, safe operating procedures must be strictly followed, and equipment must be inspected and maintained regularly to ensure the stable operation of electrical equipment and the safety of operators.
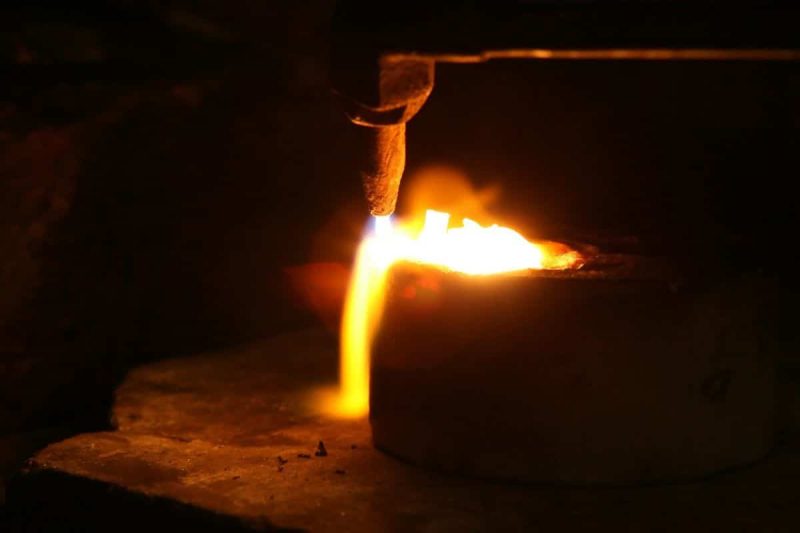
Electrical safety precautions for laser welding machines
The operation of laser welding machines involves high-energy lasers and electrical systems, so strict compliance with electrical safety standards is required to ensure the safety of operators and equipment. The following are electrical safety precautions for laser welding machines:
Power supply and stability
Laser welding machines have high requirements for power supply and must ensure stable voltage and current output. Therefore, you first need to ensure that the power line connected to the laser welding machine meets standards, has stable voltage, and can provide sufficient power. During operation, other high-power equipment should avoid sharing the same power line with the laser welding machine to prevent voltage fluctuations or power overload.
Ground connection and grounding requirements
Good ground connection and grounding are important measures to ensure the electrical safety of laser welding machines. Laser welding machines must be properly grounded to ensure that current can be quickly discharged through the ground wire in the event of a fault, reducing the risk of electric shock. The ground wire connection must be firm and reliable, and the ground resistance of the ground wire should be within the specified range.
Electrical Equipment Insulation and Protection
All electrical equipment of laser welding machines must have good insulation properties to prevent leakage and electric shock accidents. The insulation condition of electrical equipment should be checked regularly. Once the insulation is found to be aged or damaged, it should be stopped immediately and repaired or replaced.
Overload and short circuit protection
To prevent equipment damage and fire risks caused by overcurrent and short circuits, the electrical system of the laser welding machine should be equipped with overload and short-circuit protection devices. These protection devices can cut off the power supply in time to protect the safety of equipment and operators.
Regular inspection and maintenance of electrical equipment
Regular inspection and maintenance of electrical equipment is key to ensuring the safe operation of your laser welding machine. Regular inspections can identify potential faults and problems, allowing them to be repaired and replaced promptly. In addition, a sound maintenance record should be established to record the results of each inspection and maintenance measure to trace and analyze the operating status of the equipment.
Operating procedures and safety training
Operators must receive professional laser welding machine operation training and be familiar with the safety procedures in the operating manual. Operators should strictly follow the operating procedures to avoid unnecessary electrical risks. At the same time, emergency fault handling and emergency evacuation training should also be provided to deal with emergencies.
During the use of laser welding machines, these safety measures need to be strictly observed to effectively prevent electrical accidents and ensure the safety of operators and equipment.
Summarize
In the operation of laser welding machines, power requirements, and electrical safety issues are crucial. Strict electrical safety measures must be followed when using laser welding machines to reduce potential electrical risks and ensure the safety of operators and equipment. Only through appropriate power supply and strict electrical safety measures can we give full play to the advantages of laser welding technology, improve production efficiency, and ensure the safety and reliability of the production environment.
AccTek Laser can meet all your specific needs. With our advanced equipment and experienced technicians, we can provide high-quality and precise welding solutions for your machine tool parts. Just contact us to get started on a new project!
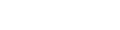
Contact information
- [email protected]
- [email protected]
- +86-19963414011
- No. 3 Zone A, Lunzhen Industrial Zone,Yucheng City , Shandong Province.
Get Laser Solutions