CO2 Laser Cutting Machine
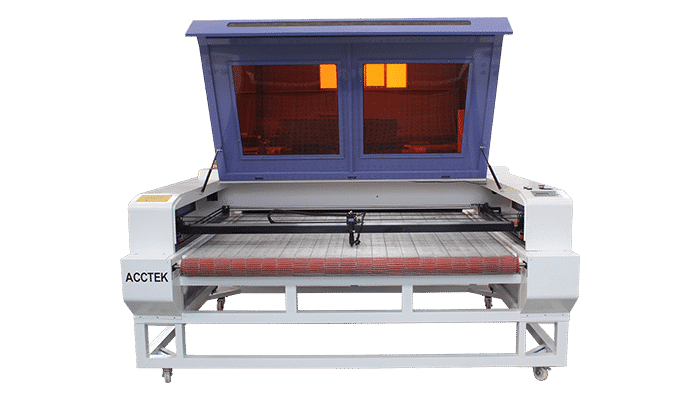
Product Range
-
High Configuration CO2 Laser Cutting Machine
Rated 5.00 out of 5$2,700.00 – $8,000.00 Select options This product has multiple variants. The options may be chosen on the product page -
CO2 Laser Cutting Machine With CCD Camera
Rated 5.00 out of 5$3,900.00 – $10,800.00 Select options This product has multiple variants. The options may be chosen on the product page -
CO2 Laser Cutting Machine With Electric Lift Table
Rated 5.00 out of 5$2,850.00 – $8,200.00 Select options This product has multiple variants. The options may be chosen on the product page -
Fully Enclosed CO2 Laser Cutting Machine
Rated 5.00 out of 5$2,700.00 – $8,000.00 Select options This product has multiple variants. The options may be chosen on the product page -
Double Head CO2 Laser Cutting Machine
Rated 5.00 out of 5$3,200.00 – $8,500.00 Select options This product has multiple variants. The options may be chosen on the product page -
CO2 Laser Cutting Machine With Automatic Feeding Device
Rated 4.75 out of 5$6,300.00 – $11,100.00 Select options This product has multiple variants. The options may be chosen on the product page -
Large-Size CO2 Laser Cutting Machine
Rated 4.75 out of 5$4,600.00 – $9,000.00 Select options This product has multiple variants. The options may be chosen on the product page -
Double Head Large Size CO2 Laser Cutting Machine
Rated 4.75 out of 5$5,100.00 – $9,500.00 Select options This product has multiple variants. The options may be chosen on the product page
Optional CO2 Laser Cutting Machine Power
Materials That Can Be Cut
CO2 Laser Cutting VS. Other Methods
CO2 Laser Cutting vs. Mechanical Cutting
CO2 laser cutting uses a focused laser beam to produce fast, precise cuts with minimal material waste. Unlike mechanical cutting, which requires physical contact with the material, laser cutting ensures smoother edges, fewer imperfections, and no tool wear, making it more suitable for delicate and intricate designs.
CO2 Laser Cutting vs. Oscillating Knife Cutting
CO2 laser cutting is a non-contact process that produces clean, precise cuts with minimal heat distortion, suitable for a wide range of materials. In contrast, oscillating knife cutting uses a moving blade, which is slower and less accurate, especially for harder materials, and can result in more wear and tear on tools.
CO2 Laser Cutting vs. Waterjet Cutting
CO2 laser cutting delivers higher precision and faster cutting speeds, particularly on thin materials, with minimal heat-affected zones. While waterjet cutting is ideal for thicker materials and heat-sensitive applications, it is generally slower and requires more maintenance, especially due to the abrasives used for cutting.
Why Choose AccTek Laser
Cutting-Edge Technology
AccTek Laser machines utilize the latest CO2 laser technology, ensuring high precision and fast cutting speeds. Our systems provide unmatched accuracy and efficiency, ensuring the best quality cuts across various materials with minimal distortion.
Custom Solutions
We understand that every business has unique requirements. That's why we offer customizable options, including power ranges, work area sizes, and cutting speeds, allowing you to tailor our machines to fit your specific production needs and material types.
Exceptional Energy Efficiency
Our CO2 laser cutting machines are designed for maximum energy efficiency. With lower power consumption and optimized performance, AccTek Laser machines help reduce operational costs, making them a cost-effective solution for both small and large-scale manufacturing.
Durability and Reliability
AccTek Laser cutting machines are engineered for long-term durability, with high-quality components and precision manufacturing. Our machines are designed to provide consistent, reliable performance, reducing maintenance needs and extending the lifespan of your equipment.
After-Sales Support
We believe in building long-term relationships with our customers. AccTek Laser provides exceptional after-sales support, including installation, training, and ongoing technical assistance. Our team is always ready to help you optimize machine performance and resolve any issues quickly.
Competitive Pricing and Value
At AccTek Laser, we offer high-performance CO2 laser cutting machines at competitive prices, ensuring that you get the best value for your investment. Our machines deliver outstanding quality at an affordable cost, making us a trusted partner for your manufacturing needs.
Frequently Asked Questions
What Are CO2 Laser-Cutting Machines?
What Materials Can CO2 Laser-Cutting Machines Cut?
- Wood: CO2 laser can cut various types of wood, including plywood, MDF (Medium-Density Fiberboard), hardwood, and veneer.
- Plastic: They can cut acrylic, polycarbonate, ABS (acrylonitrile butadiene styrene), PVC (polyvinyl chloride), PET (polyethylene terephthalate), and many other types of plastic materials.
- Fabric: CO2 laser is commonly used for cutting textiles such as cotton, polyester, nylon, silk, and synthetic fabrics.
- Leather: They can cut natural and synthetic leather materials, including suede, full-grain leather, and PU (polyurethane) leather.
- Paper and Cardboard: CO2 laser is effective for cutting paper, cardboard, cardstock, and other similar materials used in packaging, crafting, and printing industries.
- Foam: They can cut various types of foam, including polyethylene foam, polystyrene foam (Styrofoam), and foam rubber.
- Rubber: CO2 laser can cut rubber materials, such as silicone rubber, neoprene, and EPDM (ethylene propylene diene monomer) rubber.
- Glass: While CO2 lasers are not typically used for cutting glass due to its high melting point, they can be used for engraving and marking glass surfaces.
- Ceramics: CO2 laser is also not commonly used for cutting ceramics due to its hardness and brittleness, but it can be used for marking and engraving ceramic surfaces.
- Metals (With Limitations): While CO2 laser is primarily used for cutting non-metallic materials, they can also cut thin metal sheets (e.g., stainless steel, mild steel, aluminum) with limitations. However, fiber lasers are typically preferred for cutting metals due to their higher power and efficiency.
How Much Do CO2 Laser-Cutting Machines Cost?
- Entry-Level Desktop Models: Entry-level CO2 laser-cutting machines, typically smaller desktop models with lower power (e.g., 40 watts to 60 watts), can range from $2,000 to $5,000. These are suitable for hobbyists, small businesses, or educational purposes.
- Mid-Range Models: Mid-range CO2 laser-cutting machines, with higher power and larger cutting areas (e.g., 80 watts to 150 watts), can range from $5,000 to $15,000. These are suitable for small to medium-sized businesses with higher production needs.
- Industrial Grade: Industrial-grade CO2 laser-cutting machines, with even higher power and larger cutting areas (e.g., 150 watts to 400 watts or more), can range from $15,000 to $100,000 or more. These machines are suitable for large-scale manufacturing operations and businesses with high production volumes.
What Are The Disadvantages of CO2 Laser Cutting?
- Limited Thickness for Metal Cutting: CO2 lasers are not as effective for cutting thick metal materials compared to fiber lasers or other cutting methods. While they can cut thin metal sheets, typically up to around 1/12 inch (2 mm) or less depending on the material, their effectiveness decreases with thicker metals.
- Reflective Materials: CO2 lasers are less effective on highly reflective materials such as metals like aluminum, copper, and brass. The laser beam can reflect off these materials, causing damage to the optics and reducing cutting efficiency. Specialized techniques or coatings may be required to cut reflective materials with CO2 lasers.
- Higher Operating Costs: CO2 lasers require consumables such as laser tubes, lenses, and mirrors, which need periodic replacement. These consumables can contribute to higher operating costs over time compared to other cutting methods. Additionally, CO2 lasers consume more electricity compared to fiber lasers for the same cutting tasks.
- Slower Cutting Speed for Some Materials: While CO2 lasers are capable of high precision, they may have slower cutting speeds compared to other cutting methods, especially for thicker or denser materials. This can impact productivity in high-volume manufacturing environments.
- Maintenance Requirements: CO2 laser-cutting machines require regular maintenance to ensure optimal performance and reliability. This includes cleaning and aligning optics, replacing consumables, and monitoring the condition of the laser tube. Failure to perform regular maintenance can lead to decreased cutting quality and increased downtime.
- Environmental Concerns: CO2 lasers produce fumes and smoke when cutting certain materials, particularly plastics and organic materials. Proper ventilation and filtration systems help maintain a safe work environment and comply with regulations regarding air quality and emissions.
- Initial Investment: While entry-level CO2 laser-cutting machines are relatively affordable, higher-powered industrial-grade models can be quite expensive. The initial investment required to purchase and set up a CO2 laser-cutting machine may be prohibitive for some small businesses or hobbyists.
How Long Is The Service Life of CO2 Laser Cutting Machines?
- Quality of Components: High-quality CO2 laser cutting machines with robust construction and durable components tend to have longer service lives. Machines built with reliable laser sources, precision optics, and sturdy mechanical structures are likely to last longer than cheaper, lower-quality alternatives.
- Usage Intensity: The service life of a CO2 laser cutting machine can be influenced by how frequently it’s used and the types of materials it processes. Machines used for heavy-duty industrial production with long operating hours may experience more wear and tear compared to machines used intermittently for lighter tasks.
- Maintenance: Proper maintenance and regular servicing can significantly extend the service life of CO2 laser-cutting machines. Routine maintenance tasks such as cleaning optics, aligning mirrors, replacing consumables (e.g., laser tubes, lenses), and lubricating mechanical components can help prevent premature wear and ensure consistent performance.
- Technological Advancements: As technology evolves, newer generations of CO2 laser cutting machines may offer improved performance, efficiency, and reliability compared to older models. Upgrading to newer equipment with enhanced features and capabilities may be advantageous for maintaining competitiveness and productivity in the long term.
- Environmental Conditions: The operating environment can impact the service life of CO2 laser-cutting machines. Factors such as temperature, humidity, dust levels, and exposure to corrosive substances can affect machine performance and longevity. Proper environmental controls and maintenance of ideal operating conditions can help prolong the machine’s service life.
- Manufacturer Support: Choosing a reputable manufacturer or supplier that offers comprehensive technical support, spare parts availability, and servicing options can be beneficial for maximizing the service life of CO2 laser cutting machines. Access to timely assistance and genuine replacement parts can help address issues and prolong the machine’s operational lifespan.
How To Determine The Cutting Speed of CO2 Laser Cutting Machines?
- Material Type and Thickness: Different materials have varying cutting characteristics, including their melting point, thermal conductivity, and reaction to laser energy. Thinner materials generally require higher cutting speeds, while thicker materials may necessitate slower speeds to achieve clean cuts.
- Laser Power: The power output of the CO2 laser affects the cutting speed. Higher laser power allows for faster cutting speeds, particularly when cutting through thicker or denser materials. However, excessively high power settings may result in excessive melting or burning, affecting cut quality.
- Focal Length: The focal length of the laser lens affects the spot size and intensity of the laser beam. Longer focal lengths create a narrower beam width, which can improve cutting precision but may require slower cutting speeds. Shorter focal lengths produce wider beams suitable for higher cutting speeds.
- Assist Gas: Assist gas, such as compressed air, nitrogen, or oxygen, is often used to improve cutting efficiency and quality. The choice of assist gas and its pressure can impact cutting speed by affecting material removal and thermal processes. Oxygen is commonly used for cutting metals, while nitrogen or compressed air is preferred for non-metallic materials.
- Cut Quality Requirements: The desired quality of the cut also influences cutting speed. Higher-quality cuts may require slower speeds to achieve smoother edges, minimal burrs, and precise contours. Conversely, rougher cuts or parts with less stringent quality requirements may allow for higher cutting speeds.
How To Maintain CO2 Laser Cutting Machines?
- Fume Extraction: CO2 laser cutting generates fumes and smoke, especially when cutting materials like plastics, wood, and fabrics. These fumes can contain particulates, gases, and potentially hazardous compounds, depending on the materials being processed. The proper fume extraction system can remove these contaminants from the air and prevent them from accumulating in the workspace.
- Exhaust System: A dedicated exhaust system with sufficient airflow capacity is necessary to capture and remove fumes generated during laser cutting. The exhaust system should include ducting connected to the laser cutting machine’s enclosure or cutting area, leading to an external exhaust outlet or filtration system. The exhaust airflow rate should be adequate to effectively capture and remove fumes without causing air turbulence or recirculation within the workspace.
- Filtration: In addition to exhaust ventilation, some laser-cutting setups may incorporate filtration systems to further purify the air before it’s released into the environment. Filtration systems can help remove particulates, odors, and volatile organic compounds (VOCs) from the exhaust air, enhancing air quality and reducing environmental impact.
- Ventilation Design: Proper ventilation design ensures effective capture and removal of fumes from the cutting area. This may involve positioning exhaust ducts and vents strategically to capture fumes at the source and minimize the dispersion of contaminants throughout the workspace. Enclosures or hoods around the cutting area can help contain fumes and direct them toward the exhaust system.
- Outdoor Exhaust: Whenever possible, exhaust vents should discharge fumes and filtered air to the outdoors, away from building entrances, air intakes, and areas where people may be present. Outdoor exhaust helps prevent fumes from re-entering the workspace and minimizes the risk of exposure to harmful pollutants.
- Regulatory Compliance: When designing and operating ventilation systems for CO2 laser cutting machines, strict compliance with relevant occupational health and safety regulations and environmental standards is required. These regulations may specify requirements for air quality, ventilation rates, exhaust emissions, and workplace exposure limits for hazardous substances.
Are There Specific Ventilation Requirements For CO2 Laser-Cutting Machines?
- Fume Extraction: CO2 laser cutting generates fumes and smoke, especially when cutting materials such as plastics, wood, and fabrics. These fumes can contain particulates, gases, and potentially hazardous compounds, depending on the materials being processed. Proper fume extraction systems are necessary to remove these contaminants from the air and prevent their accumulation in the workspace.
- Exhaust System: A dedicated exhaust system with adequate airflow capabilities can capture and remove fumes generated during laser cutting. The exhaust system typically includes ducting connected to the laser cutting machine’s enclosure or cutting area, leading to an external exhaust outlet or filtration system. The exhaust airflow rate should be sufficient to effectively capture and remove fumes without causing air turbulence or recirculation within the workspace.
- Filtration: Some laser cutting setups may incorporate filtration systems to further purify the air before it’s released into the environment. Filtration systems can help remove particulates, odors, and volatile organic compounds (VOCs) from the exhaust air, improving air quality and reducing environmental impact.
- Ventilation Design: Proper ventilation design ensures effective capture and removal of fumes from the cutting area. This may involve positioning exhaust ducts and vents strategically to capture fumes at the source and minimize the dispersion of contaminants throughout the workspace. Enclosures or hoods around the cutting area can help contain fumes and direct them toward the exhaust system.
- Outdoor Exhaust: Whenever possible, exhaust vents should discharge fumes and filtered air to the outdoors, away from building entrances, air intakes, and areas where people may be present. Outdoor exhaust helps prevent fumes from re-entering the workspace and minimizes the risk of exposure to harmful pollutants.
- Regulatory Compliance: When designing and operating ventilation systems for CO2 laser cutting machines, relevant occupational health and safety regulations and environmental standards need to be adhered to. These regulations may specify requirements for air quality, ventilation rates, exhaust emissions, and workplace exposure limits for hazardous substances.
Related Resources
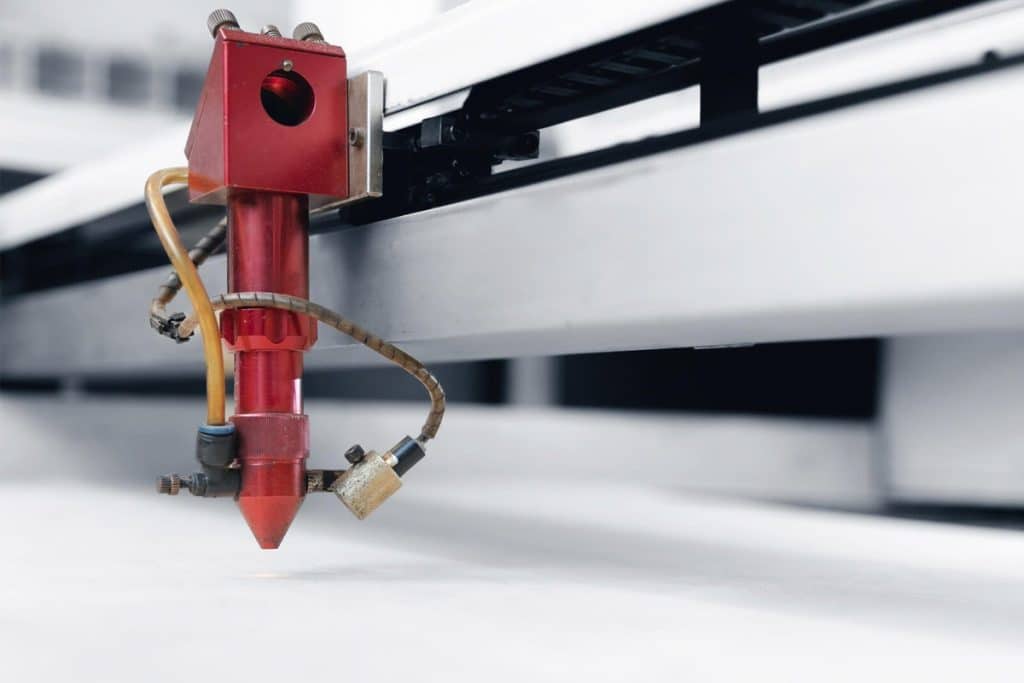
Can a CO2 Laser Cutting Machine Perform Cutting and Engraving Tasks at the Same Time?
Can CO2 laser cutting machines achieve “multi-purpose use” of precise cutting and fine engraving? This article combines the principle with the functional characteristics of AccTek’s CO2 laser cutting machines to
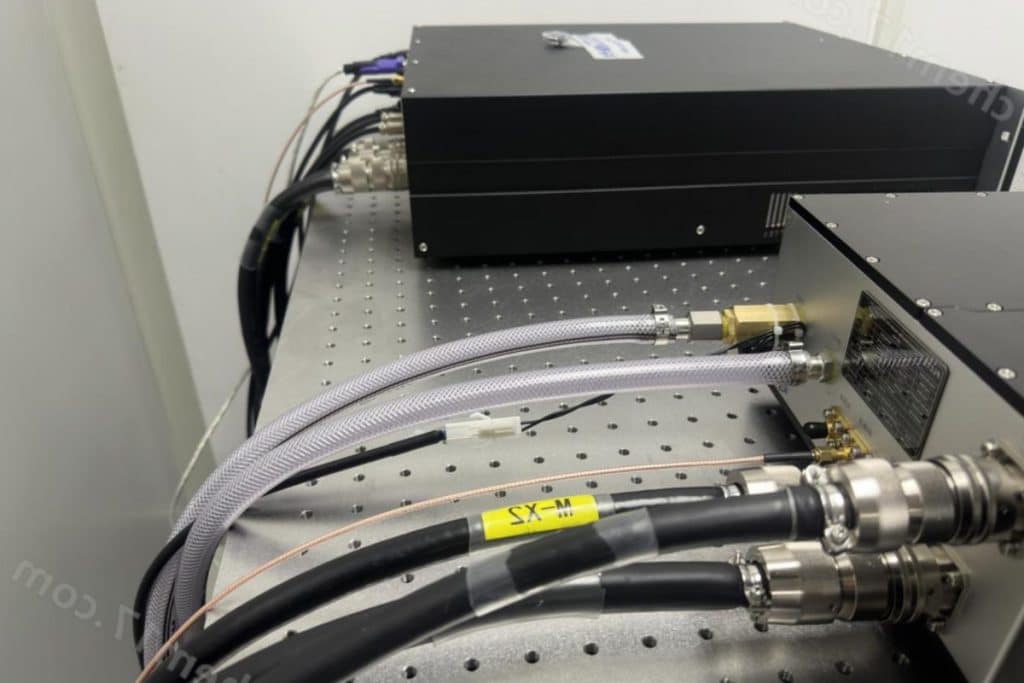
Do Fiber Laser Generators Lose Power over Time?
This article focuses on the reasons why fiber laser generator power decreases over time and proposes effective strategies to mitigate power loss through high-quality equipment, regular maintenance, and an optimized
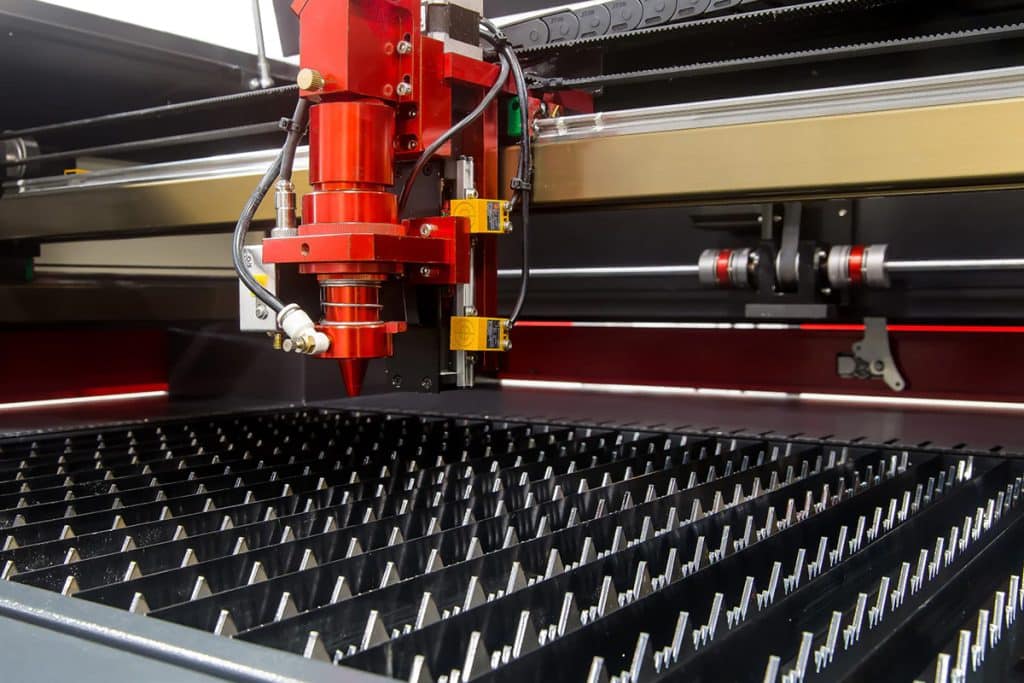
How Does a CO2 Laser Cutting Machine Achieve High-Precision Cutting?
This article mainly introduces the principles and key technologies behind the high-precision cutting capabilities of CO2 laser cutting machines, and analyzes their core structural components and advantages.