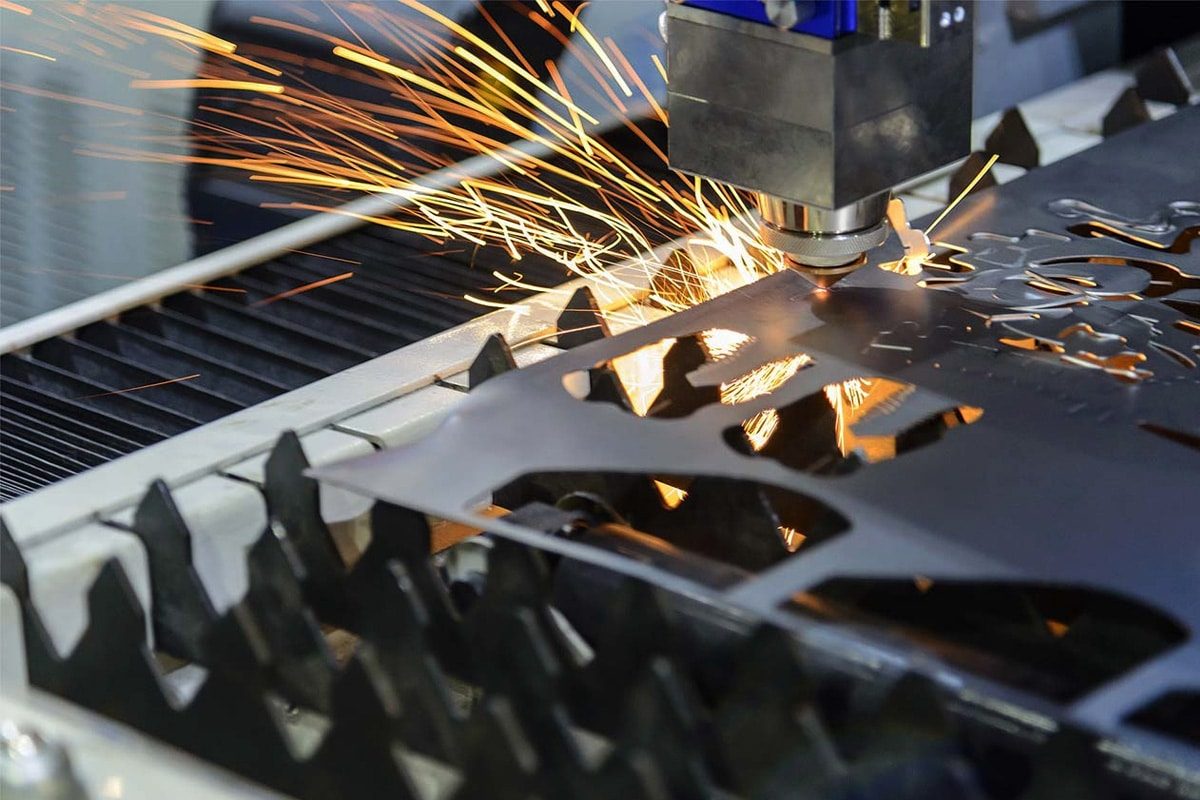
A influência do sistema de controle na máquina de corte a laser de fibra
Na fabricação moderna, máquinas de corte a laser de fibra são amplamente utilizados em processamento de metais, fabricação de automóveis, aeroespacial e outras indústrias com sua excelente eficiência de corte e capacidades de processamento de alta precisão. Com o avanço contínuo da tecnologia, as máquinas de corte a laser de fibra têm mostrado grandes vantagens em vários ambientes de produção complexos, especialmente nas áreas de precisão de corte de alta exigência e processamento de alta velocidade. Como um dos principais componentes deste equipamento de alto desempenho, o sistema de controle desempenha um papel vital em garantir a operação estável da máquina de corte a laser e melhorar a eficiência da produção.
O design e o desempenho do sistema de controle da máquina de corte a laser de fibra determinam diretamente sua qualidade de corte, eficiência de produção e facilidade de operação. Um sistema de controle eficiente e preciso pode otimizar o caminho de corte a laser e controlar com precisão a potência do laser e a velocidade de movimento, alcançando assim maior precisão de corte e menores custos de produção. Ao mesmo tempo, o design inteligente e automatizado do sistema de controle melhora muito a conveniência da operação, permitindo que o operador conclua tarefas de corte complexas sem muita intervenção. Portanto, entender as funções e o impacto do sistema de controle é a chave para melhorar o desempenho e a amplitude da aplicação das máquinas de corte a laser de fibra.
Índice
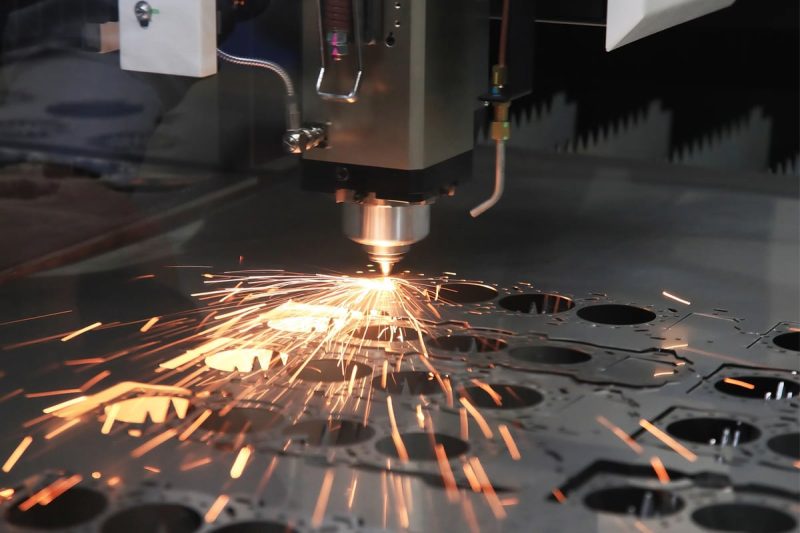
Compreendendo os sistemas de controle
Definição
O sistema de controle é o “cérebro” da máquina de corte a laser de fibra. Ele gerencia e coordena de forma abrangente o trabalho de cada componente-chave da máquina por meio de algoritmos precisos e programas de controle, garantindo assim a precisão e a alta eficiência de todo o processo de corte. O sistema de controle não apenas regula os parâmetros principais, como emissão de laser, controle de movimento e ajuste de distância focal, mas também é responsável por otimizar o caminho de corte, realizar a operação automatizada e coordenar perfeitamente outros links de produção. É uma tecnologia-chave para garantir a operação estável e a operação eficiente do máquina de corte a laser em um ambiente de trabalho complexo.
Componentes
Um sistema de controle típico de máquina de corte a laser de fibra consiste em vários componentes principais, e a sinergia de cada componente em todo o processo de corte é a base para garantir seu desempenho eficiente:
- Unidade de controle de movimento: Esta unidade é responsável por controlar o movimento da cabeça do laser. Ela pode ajustar com precisão a posição, velocidade, aceleração e desaceleração da cabeça do laser para garantir a execução precisa de cada caminho de corte. A precisão do controle de movimento afeta diretamente a qualidade e a eficiência do efeito de corte.
- Unidade de controle da fonte de laser: Controla a potência, frequência e largura de pulso do gerador de laser para garantir a estabilidade do feixe de laser e o efeito de corte. Por meio de ajuste fino, a unidade de controle da fonte de laser pode se adaptar aos requisitos de corte de diferentes materiais, como espessura, material, etc., para garantir o melhor efeito de corte.
- Interface de operação: A interface de operação é a ponte para o usuário interagir com o dispositivo, geralmente por meio de uma tela sensível ao toque ou monitor de computador. Ela pode exibir o status de trabalho da máquina de corte e os parâmetros do equipamento, e permitir que o operador ajuste facilmente as configurações, inicie ou pare a máquina, etc. Um bom design de interface de usuário ajuda a melhorar a conveniência da operação e a reduzir erros humanos.
- Sensor e sistema de feedback: O sensor monitora vários dados no processo de corte a laser (como potência do laser, temperatura do material, velocidade de corte, etc.) em tempo real, e o sistema de feedback ajusta os parâmetros no processo de corte de acordo com esses dados. Sensores e mecanismos de feedback podem efetivamente reduzir o acúmulo de erros e garantir a precisão do corte, o que é particularmente importante em materiais complexos ou processamento de precisão.
Função
O sistema de controle não se limita às tarefas básicas de controle, ele também possui uma série de funções importantes para melhorar o desempenho geral da máquina de corte a laser de fibra:
- Planejamento do caminho de corte: O sistema de controle pode gerar o caminho de corte ideal com base nos desenhos de projeto ou arquivos CAD. Por meio do planejamento eficiente do caminho, o sistema pode reduzir o tempo ocioso e movimentos de corte desnecessários para maximizar a eficiência da produção.
- Controle preciso da saída do laser: O sistema de controle ajustará com precisão a potência de saída e a frequência do laser de acordo com as características do material de corte. Por exemplo, para chapas metálicas grossas, o sistema aumentará a potência do laser; para materiais finos, ele pode reduzir a potência para garantir que o efeito de corte seja limpo e preciso.
- Feedback em tempo real: Durante o processo de corte, o sistema de controle coleta continuamente dados em tempo real por meio de sensores e ajusta automaticamente os parâmetros de corte com base no mecanismo de feedback. Este feedback de circuito fechado garante que os erros no processo de corte sejam minimizados. Seja enfrentando flutuações de material ou mudanças no desempenho da máquina-ferramenta, o sistema pode corrigir desvios em tempo real para garantir a alta qualidade do efeito de corte final.
Essas funções não apenas melhoram a precisão de corte da máquina de corte a laser de fibra, mas também otimizam o processo de produção e melhoram a eficiência geral da produção. Especialmente em indústrias que exigem processamento de alta precisão e alta eficiência, a importância do sistema de controle é particularmente proeminente.
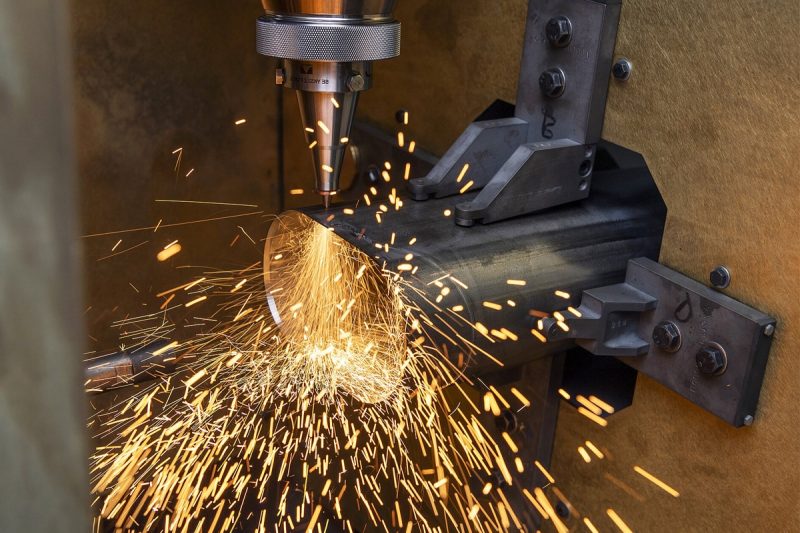
Fácil de usar
Design da interface do usuário: O sistema de controle das modernas máquinas de corte a laser de fibra dá grande atenção ao design da interface do usuário, enfatizando uma interface simples, intuitiva e fácil de operar. Esses sistemas geralmente são equipados com um painel de operação touchscreen de grande tamanho ou conectados a um computador externo para fornecer opções de controle e monitoramento mais abundantes. Os usuários podem facilmente definir parâmetros de corte, como potência do laser, velocidade, distância focal, etc. por meio da tela sensível ao toque, enquanto conseguem monitorar o processo de corte em tempo real e fazer os ajustes necessários. A interface gráfica torna as operações complexas mais intuitivas. Os usuários não precisam entender profundamente a complexidade do programa, mas apenas selecionar o modo de operação apropriado de acordo com suas necessidades. Este design permite que os operadores comecem rapidamente e concluam seu trabalho com eficiência, reduzindo a curva de aprendizado da operação.
Simplicidade de programação: Comparados com as máquinas de corte a laser tradicionais, os sistemas de controle das modernas máquinas de corte a laser de fibra suportam principalmente integração profunda com software CAD/CAM, o que simplifica a programação. Os programadores ou operadores só precisam importar desenhos de projeto por meio do software, e o sistema gerará automaticamente caminhos de corte e ajustará os parâmetros de corte a laser de acordo com os arquivos de projeto, melhorando muito a eficiência da programação. Muitos sistemas também suportam otimização de caminho inteligente, que pode ajustar automaticamente a sequência de corte, velocidade e potência de acordo com as características de diferentes materiais, alcançando assim maior precisão de corte e ciclos de produção mais curtos. Os programadores não precisam executar programação manual tediosa, mas apenas definir parâmetros e ajustar caminhos por meio de uma interface gráfica simples, o que reduz muito a ocorrência de erros humanos e melhora a eficiência da produção.
Acessibilidade e ergonomia: O sistema de controle da máquina de corte a laser de fibra é projetado com total consideração ao conforto do operador e à necessidade de operação de longo prazo. O layout de interface amigável, ícones intuitivos e botões de controle estão todos alinhados com os princípios ergonômicos para evitar fadiga causada por operação de longo prazo. A altura, o ângulo do painel de operação e a correspondência de cores da interface são cuidadosamente projetados para garantir que o operador possa manter uma postura confortável durante a operação de longo prazo, reduzindo a fadiga visual e o desconforto físico. Além disso, alguns sistemas de controle avançados também suportam funções de monitoramento e controle remoto. O operador pode monitorar o status operacional da máquina de corte a laser de qualquer lugar por meio de um dispositivo inteligente ou um computador externo e visualizar os parâmetros de trabalho do equipamento em tempo real, evitando a limitação da localização física.
Automação e predefinições: A maioria dos sistemas de controle de máquinas de corte a laser de fibra modernas são equipados com funções de automação poderosas. Esses sistemas podem ajustar automaticamente os parâmetros de acordo com diferentes requisitos de processamento, reduzir a intervenção manual e otimizar a eficiência da produção. Por exemplo, muitos sistemas de controle fornecem programas de processamento predefinidos que podem selecionar automaticamente as configurações de corte mais adequadas de acordo com o tipo, espessura ou requisitos de corte de diferentes materiais. A função de automação não apenas reduz a carga do operador, mas também ajusta dinamicamente parâmetros como velocidade de corte e potência do laser de acordo com as mudanças nas tarefas de produção, garantindo assim a consistência da qualidade de corte para cada lote. Além disso, o sistema também pode otimizar o caminho de corte com base em dados históricos para evitar desperdícios desnecessários, melhorar a eficiência do corte e reduzir ainda mais os custos de produção.
Esses designs humanizados e funções inteligentes não apenas tornam a operação mais conveniente, mas também melhoram efetivamente a capacidade de produção e a precisão do processamento das máquinas de corte a laser de fibra, ajudando as empresas a manter sua posição de liderança no ambiente de mercado cada vez mais competitivo.
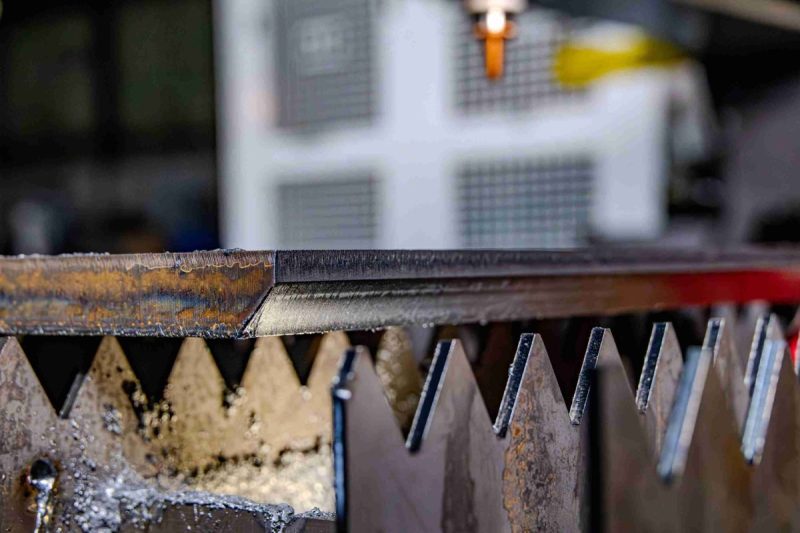
Exatidão e precisão
Algoritmo de controle: O algoritmo de controle é o núcleo da máquina de corte a laser de fibra para obter corte preciso. Algoritmos de controle avançados podem reduzir erros de corte e garantir efeitos de corte de alta precisão, otimizando caminhos de corte e calculando com precisão a distribuição de energia do laser. Por meio do planejamento inteligente de caminho, o sistema de controle ajusta automaticamente os parâmetros do laser de acordo com o tipo de material e os requisitos de corte para minimizar erros e garantir a precisão de cada ponto de corte.
Mecanismo de feedback: As máquinas de corte a laser de fibra são geralmente equipadas com um sistema de feedback de circuito fechado, que detecta a posição e o status de corte do cabeçote do laser em tempo real e faz ajustes oportunos para evitar o acúmulo de erros. O papel do mecanismo de feedback é garantir que cada detalhe no processo de corte seja mantido no melhor estado, evitar flutuações de qualidade causadas por erros e garantir a estabilidade e a precisão do corte.
Ferramentas de calibração e alinhamento: O corte a laser preciso depende das ferramentas de calibração e alinhamento do equipamento. O sistema de controle é equipado com funções de alinhamento e calibração automáticas para garantir que o cabeçote do laser esteja posicionado com precisão antes de iniciar o corte. Esta função de calibração automática pode minimizar o desvio do feixe de laser, melhorar a qualidade do corte e garantir a consistência de cada corte.
Capacidade de controle dinâmico: Durante o processo de corte a laser, as mudanças em diferentes materiais e espessuras exigem que o sistema tenha a capacidade de ajustar dinamicamente os parâmetros de corte. Os sistemas de controle modernos podem ajustar a potência do laser, a velocidade e outros parâmetros em tempo real para atender aos requisitos de corte de diferentes materiais, garantindo que cada detalhe no processo de corte seja preciso e correto, e garantindo o melhor efeito e eficiência de corte.
Esses algoritmos de controle avançados, mecanismos de feedback, ferramentas de calibração e recursos de controle dinâmico trabalham juntos para garantir que as máquinas de corte a laser de fibra possam continuar a fornecer serviços de corte de alta precisão e alta eficiência em ambientes de produção complexos. Seja enfrentando materiais metálicos convencionais ou peças de trabalho complexas com formatos especiais, as máquinas de corte a laser de fibra podem atingir metas de processamento precisas por meio de sistemas de controle inteligentes.
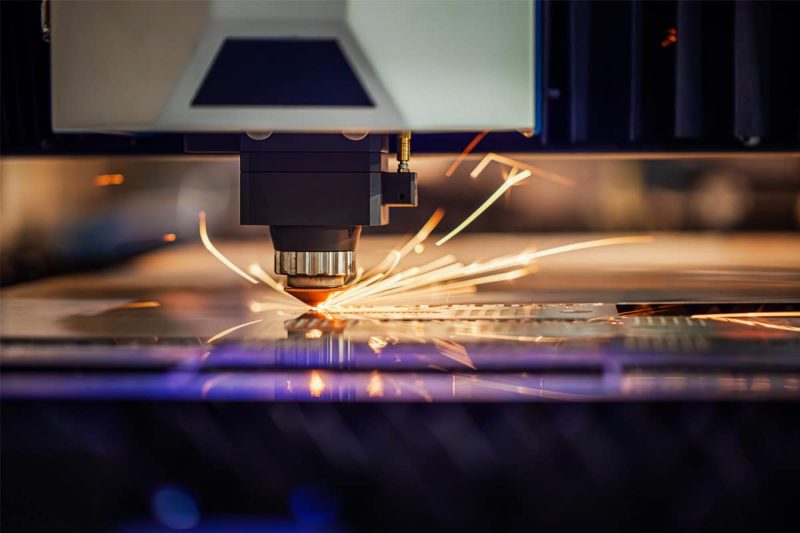
Integrar com fluxo de trabalho e processos de produção
Compatibilidade com software CAD/CAM
O design do sistema de controle das modernas máquinas de corte a laser de fibra enfatiza a alta compatibilidade com vários softwares CAD/CAM. Por meio dessa compatibilidade, os arquivos de design podem ser importados perfeitamente para o sistema de controle, e os caminhos de corte podem ser gerados automaticamente, reduzindo a necessidade de intervenção manual. Por meio da integração com sistemas CAD/CAM, os operadores podem usar diretamente os desenhos de design para gerar planos de corte precisos, otimizar os caminhos de corte e ajustar os parâmetros de acordo com as necessidades reais. Este fluxo de trabalho altamente integrado não apenas melhora a eficiência da produção, mas também garante a precisão do corte e reduz erros potenciais no processo de conversão do design para a produção real. Além disso, o design integrado permite que a máquina de corte a laser de fibra colabore eficientemente com outros equipamentos de produção e sistemas de software, como ERP, MES, etc., formando assim um ecossistema de produção inteligente e melhorando o nível geral de automação e digitalização da fábrica.
Conectividade e Rede
No contexto da Indústria 4.0, o sistema de controle de máquinas de corte a laser de fibra presta cada vez mais atenção à conectividade e aos recursos de compartilhamento de dados com outros equipamentos. Por meio de interfaces de rede integradas ou módulos de comunicação sem fio, as máquinas de corte a laser podem se conectar com eficiência a outros equipamentos de produção, sistemas de computador, sensores e plataformas de nuvem. Essa conexão de rede permite que as máquinas de corte a laser de fibra obtenham monitoramento remoto, diagnóstico remoto de falhas e atualizações de software. A equipe de produção pode visualizar o status do equipamento e os parâmetros de trabalho em tempo real por meio da rede e até mesmo ajustar as configurações de corte remotamente, obtendo assim gerenciamento inteligente e manutenção eficiente. Ao mesmo tempo, a interconexão entre os equipamentos torna todo o processo de produção mais transparente, e a coleta de dados de produção em tempo real pode fornecer aos gerentes uma visão abrangente da produção e ajudar a tomar decisões mais precisas.
Análise de dados e relatórios
O sistema de controle das modernas máquinas de corte a laser de fibra integra funções poderosas de análise de dados e relatórios, que podem coletar vários dados no processo de produção em tempo real, como tempo de corte, consumo de energia, consumo de material, eficiência de produção, status do equipamento, etc. Esses dados não apenas ajudam a entender o progresso da produção, mas também ajudam os gerentes a identificar potenciais problemas e gargalos de produção. Por exemplo, por meio da análise de dados, os gerentes podem descobrir as flutuações de desempenho do equipamento em determinados períodos e, em seguida, otimizar o equipamento ou ajustar o plano de produção. Além disso, o sistema de controle também pode gerar automaticamente relatórios de produção detalhados para registrar os detalhes de corte de cada lote, o que fornece forte suporte para controle de qualidade, manutenção de equipamentos e análise de produção. Esses relatórios também podem fornecer uma referência para processos de produção subsequentes, ajudando as empresas a otimizar a alocação de recursos e o agendamento da produção.
Otimização do caminho da ferramenta
O sistema de controle da máquina de corte a laser de fibra pode otimizar inteligentemente o caminho de corte, minimizar o tempo ocioso e o tempo não produtivo durante o processo de corte e, assim, melhorar a eficiência geral do processamento. Por meio de uma análise aprofundada das propriedades do material, o sistema pode selecionar automaticamente o melhor caminho e método de corte de acordo com a espessura, dureza e outras propriedades de diferentes materiais. Por exemplo, para peças de trabalho complexas, o sistema de controle pode determinar automaticamente a sequência de corte ideal para evitar duplicação desnecessária do caminho, reduzindo assim o tempo de corte. Ao mesmo tempo, a otimização do caminho pode efetivamente reduzir o desperdício de material e maximizar a utilização do material. Além disso, o sistema também pode ajustar o planejamento do caminho por meio de feedback em tempo real para garantir que o melhor efeito de corte seja sempre alcançado em diferentes condições de trabalho, melhorando assim a eficiência da produção e reduzindo custos.
Essa otimização de caminho altamente inteligente não apenas melhora a eficiência da produção, mas também melhora muito a capacidade de aplicação das máquinas de corte a laser de fibra em tarefas de corte complexas, garantindo que cada tarefa possa ser concluída no menor tempo possível e com a melhor qualidade.
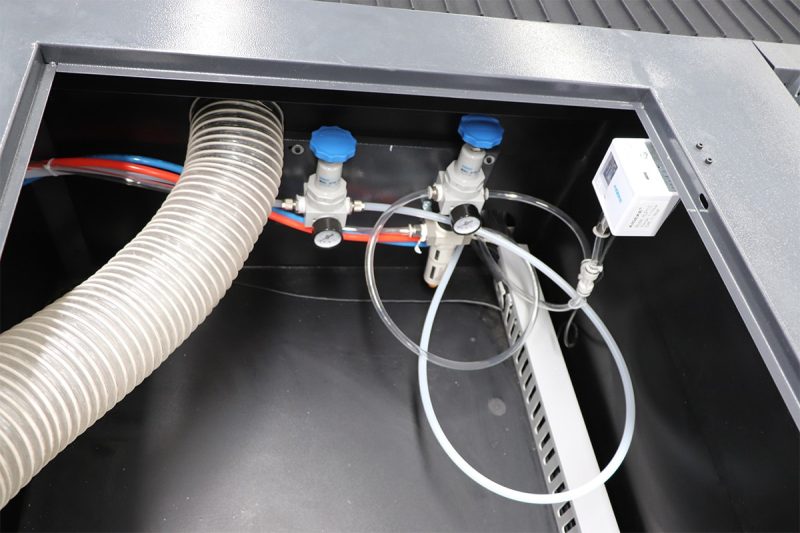
Manutenção e solução de problemas
Ferramentas de diagnóstico
Para garantir a operação contínua e estável da máquina de corte a laser de fibra, os sistemas de controle modernos geralmente são equipados com ferramentas de diagnóstico automático inteligentes. Por meio do monitoramento em tempo real do status de cada componente e sistema do equipamento, a ferramenta de diagnóstico pode detectar falhas potenciais precocemente e identificar automaticamente condições anormais. Por exemplo, o sistema de controle monitorará continuamente o status de trabalho de componentes-chave, como o gerador de laser, sistema de movimento, sensor, sistema de resfriamento, etc. Quando houver um desvio ou anormalidade, o sistema emitirá um aviso prévio para notificar o operador ou técnico para verificar e reparar. Por meio desse mecanismo de aviso prévio, os técnicos podem tomar medidas antes que o problema ocorra para evitar tempo de inatividade do equipamento ou danos mais sérios devido à falha. Além disso, a ferramenta de diagnóstico também pode registrar os dados operacionais do equipamento e informações históricas de falhas, fornecer relatórios detalhados de análise de falhas, ajudar os técnicos a entender a causa raiz da falha e fornecer uma referência para manutenção subsequente.
Capacidades de suporte remoto
Com o desenvolvimento contínuo da tecnologia, alguns sistemas avançados de controle de máquinas de corte a laser de fibra integraram funções de suporte remoto, permitindo que os técnicos acessem e diagnostiquem remotamente o equipamento por meio de conexões de rede. Esta função de suporte remoto permite que operadores ou técnicos diagnostiquem, depurem e reparem remotamente o equipamento pela Internet em vez de ter que ir pessoalmente ao local quando ocorrerem problemas. Por meio do acesso remoto, os técnicos podem visualizar os dados operacionais do equipamento em tempo real, diagnosticar falhas, implementar planos de reparo e até mesmo fazer ajustes por meio da interface de controle remoto para resolver os problemas mais comuns. Este suporte remoto pode não apenas encurtar muito o tempo de solução de problemas e reduzir o tempo de inatividade do equipamento, mas também reduzir o custo e a sobrecarga de mão de obra da manutenção no local. Especialmente no caso de vários locais de produção, o suporte remoto pode fornecer suporte técnico unificado e rápido para várias fábricas, melhorando muito a eficiência geral do gerenciamento do equipamento.
O suporte remoto também pode ser usado em conjunto com ferramentas de diagnóstico para fornecer serviços de manutenção mais abrangentes. Os técnicos podem monitorar o status em tempo real do equipamento por meio da plataforma remota e visualizar o relatório de diagnóstico do sistema para determinar com mais precisão a causa da falha e desenvolver um plano de manutenção. Para alguns problemas que não podem ser tratados remotamente, os técnicos também podem orientar o pessoal no local para conduzir inspeções preliminares ou solucionar problemas para garantir que o equipamento retorne à operação normal o mais rápido possível.
A manutenção de máquinas de corte a laser de fibra modernas não é mais simplesmente inspeção e reparo manual, mas manutenção eficiente e precisa é obtida por meio de ferramentas inteligentes integradas e suporte remoto. A combinação de ferramentas de diagnóstico automático e funções de suporte remoto não apenas melhora a disponibilidade do equipamento, mas também ajuda as empresas a reduzir significativamente os custos de manutenção e o tempo de inatividade do equipamento. Ao mesmo tempo, as funções de aviso de falha e diagnóstico remoto do equipamento tornam o trabalho de manutenção mais previsível, ajudando a equipe técnica a realizar manutenção planejada e otimização, e melhorando a eficiência operacional geral e a vida útil do equipamento.
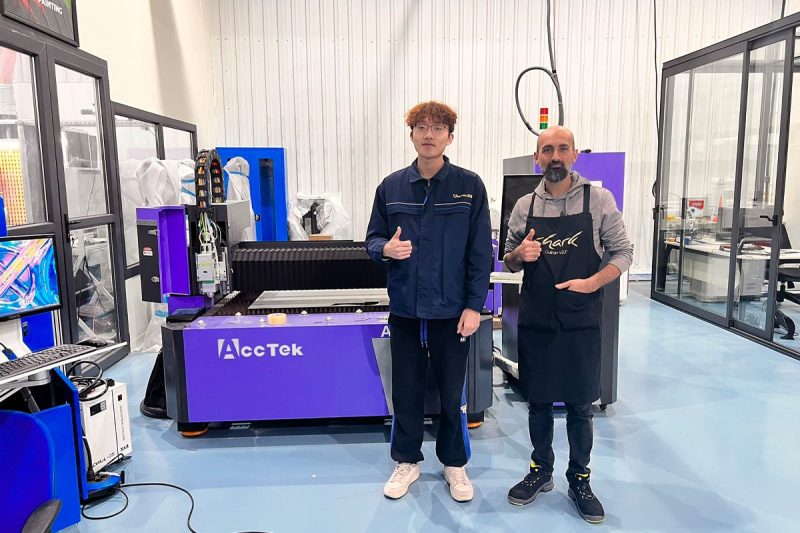
Treinamento e Suporte
Treinamento do operador: Para garantir que os operadores possam usar máquinas de corte a laser de fibra de forma eficiente, os fabricantes geralmente fornecem treinamento abrangente, incluindo operação do equipamento, programação, manutenção diária e solução de problemas. O treinamento ajuda os operadores a dominar as funções da máquina de corte, melhorar a eficiência da produção e reduzir erros operacionais. Os fabricantes geralmente também fornecem treinamento em camadas com base em diferentes níveis técnicos para garantir que todos os operadores possam usar o equipamento de forma eficaz.
Disponibilidade de recursos de treinamento: Além do treinamento no local, muitos fabricantes também fornecem uma riqueza de recursos de treinamento online, incluindo tutoriais em vídeo, manuais de operação e FAQs. Esses recursos são convenientes para os operadores consultarem a qualquer momento em seu trabalho diário e resolverem problemas que encontrarem. Ao mesmo tempo, plataformas online e fóruns de usuários também fornecem aos operadores canais para comunicação mútua e resolução de problemas, melhorando ainda mais a eficiência do uso do equipamento.
Suporte do fabricante: Quando o sistema de controle da máquina de corte a laser de fibra falha ou precisa ser atualizado, o fabricante geralmente fornece suporte técnico abrangente. O suporte técnico do fabricante não cobre apenas reparos de hardware, mas também atualizações de software e otimização de funções para garantir que o equipamento esteja sempre no melhor estado operacional. A equipe técnica do fabricante pode ajudar os clientes a resolver problemas prontamente e reduzir o tempo de inatividade do equipamento por meio de suporte remoto ou serviços no local.
Atualizações e manutenção de software: Conforme a tecnologia avança, os fabricantes lançam regularmente atualizações de software para melhorar o desempenho e a estabilidade do sistema. As atualizações de software podem incluir novos recursos, otimizações de desempenho ou correções de sistema para garantir que o dispositivo permaneça na vanguarda do setor. Os fabricantes geralmente notificam os clientes sobre atualizações e fornecem o suporte técnico necessário para garantir que o processo de atualização ocorra sem problemas.
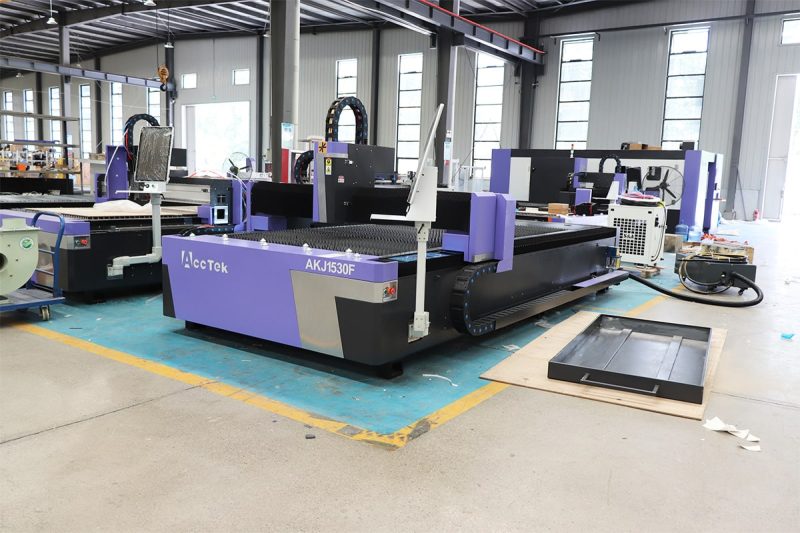
Treinamento e Suporte
O sistema de controle é o componente central da máquina de corte a laser de fibra, que determina diretamente a qualidade do corte, a eficiência da produção e a experiência operacional. O sistema de controle avançado equipado com modernas máquinas de corte a laser de fibra pode atingir maior precisão e maior eficiência no trabalho de corte por meio de algoritmos de controle otimizados, mecanismos de feedback em tempo real e integração próxima com os processos de produção. Ao mesmo tempo, a interface amigável e o suporte de treinamento abrangente do sistema de controle permitem que os operadores dominem facilmente o uso do equipamento, garantindo a estabilidade e a eficiência do equipamento em operação de longo prazo.
Como uma empresa líder na indústria de laser, a AccTek Laser sempre aderiu aos princípios de inovação tecnológica e cliente em primeiro lugar na pesquisa, desenvolvimento e produção de máquinas de corte a laser de fibra. Nossas máquinas de corte a laser de fibra são equipadas com sistemas de controle avançados na indústria, que podem não apenas garantir resultados de corte precisos, mas também melhorar muito a eficiência da produção. Seja em termos de qualidade do produto ou serviço pós-venda, Laser AccTek se esforça para fornecer aos clientes as melhores soluções para ajudá-los a obter uma vantagem na acirrada competição do mercado e aumentar ainda mais a competitividade geral da empresa.
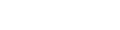
Informações de contato
- [email protected]
- [email protected]
- +86-19963414011
- No. 3 Zona A, Zona Industrial de Lunzhen, Cidade de Yucheng, Província de Shandong.
Obtenha soluções a laser