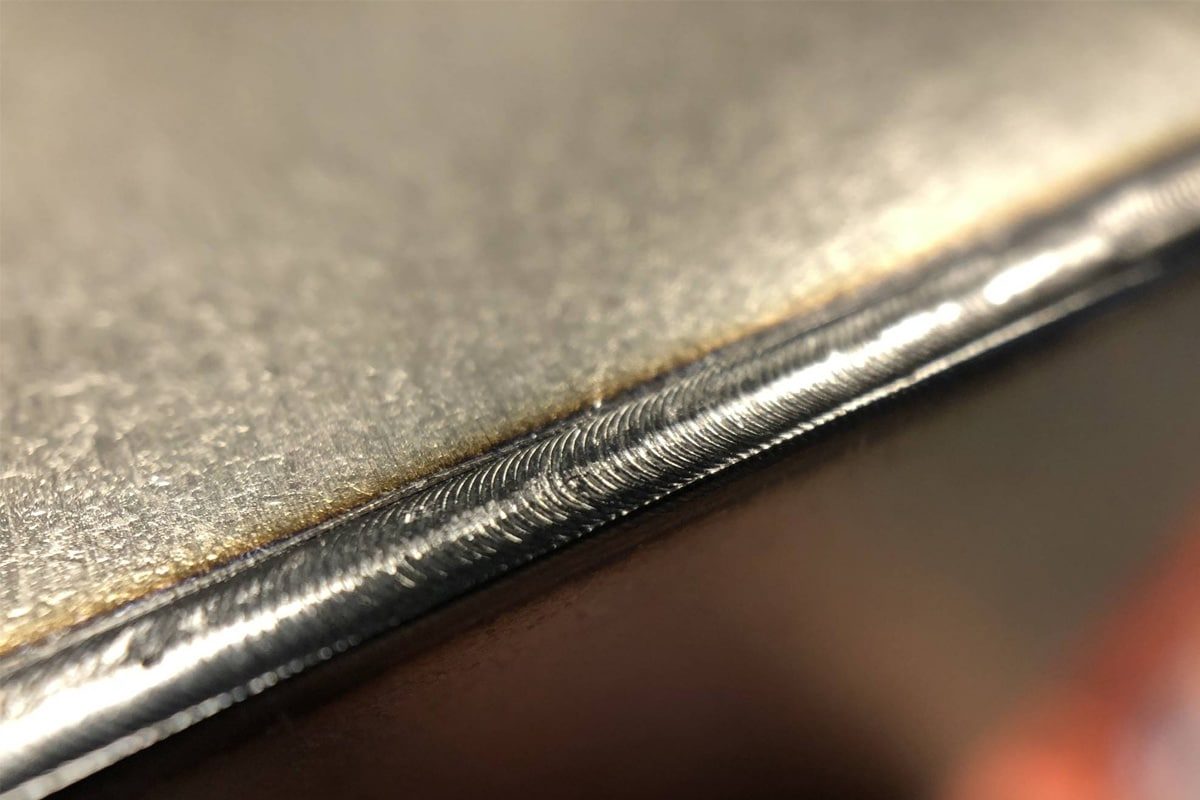
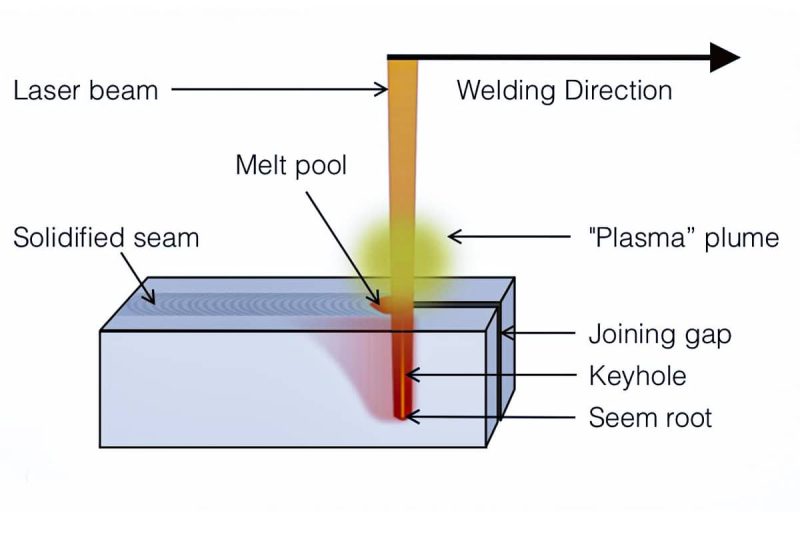
Compreendendo a soldagem a laser
Noções básicas de soldagem a laser
Tipo de soldagem a laser
- Soldagem a laser de onda contínua: adequada para necessidades de soldagem de alta intensidade e longo prazo, amplamente utilizada para conexão e vedação de chapas metálicas espessas.
- Soldagem a laser pulsado: aquece o material por meio de pulsos de alta energia de curta duração, mais adequado para soldagem de chapas finas ou microcomponentes, com maior precisão de controle.
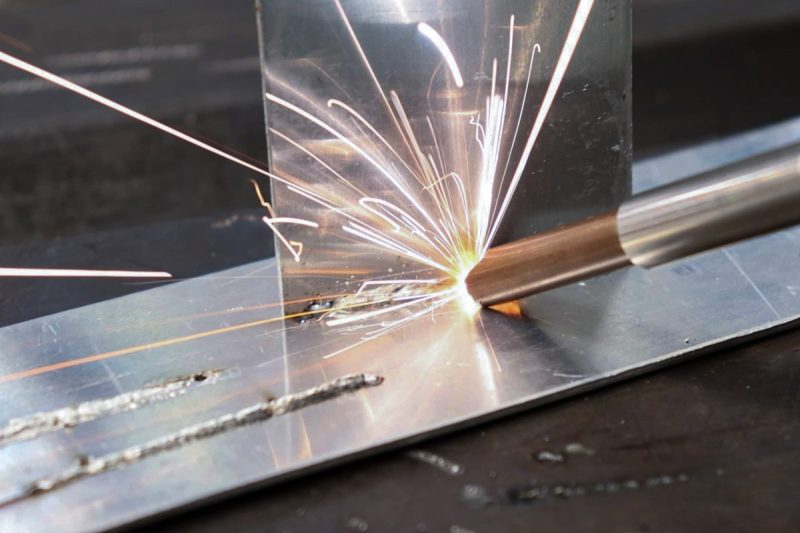
Fatores que afetam a largura da solda
Parâmetros de laser
- Potência do laser: A potência do laser é um dos parâmetros mais críticos que afetam os resultados da soldagem. Quanto maior a potência do laser, mais calor é gerado, e o volume da zona afetada pelo calor e da poça de fusão também aumenta, o que aumenta a largura da solda. Por outro lado, se a potência for muito baixa, ela não pode fornecer energia suficiente para derreter o material, e a junta de solda pode ser insuficiente, resultando em uma solda estreita ou incompleta. Portanto, a potência do laser precisa ser razoavelmente selecionada de acordo com a espessura, tipo e velocidade de soldagem do material para atingir a largura ideal da solda.
- Velocidade de soldagem: A velocidade de soldagem tem uma influência importante na entrada de calor. Quando a velocidade de soldagem é lenta, o laser permanece na área de soldagem por mais tempo, resultando em mais transferência de calor para o material base, formando uma poça de fusão maior e zona afetada pelo calor, aumentando assim a largura da solda. Por outro lado, uma velocidade de soldagem muito rápida reduzirá a entrada de calor, resultando em soldagem incompleta, soldas muito estreitas e possivelmente soldas fracas. Portanto, o controle razoável da velocidade de soldagem é a chave para garantir a largura de solda apropriada.
- Comprimento de onda: O comprimento de onda do laser determina como o laser interage com o material. Lasers de comprimento de onda curto (como aqueles emitidos por geradores de laser de fibra) podem ser melhor absorvidos por materiais metálicos porque têm uma concentração de energia mais alta e podem fornecer mais energia em uma área menor, melhorando assim a eficiência da soldagem e tornando a solda mais estreita. Relativamente falando, lasers de comprimento de onda longo (como aqueles emitidos por tubos de laser de CO2) têm baixa absorção de materiais metálicos, e a distribuição de energia durante a soldagem é relativamente ampla, o que facilmente leva a uma largura de solda maior. Portanto, lasers de comprimento de onda curto são mais adequados para soldagem de alta precisão.
- Duração do pulso: A soldagem a laser pulsado tem a vantagem única de otimizar a soldagem ajustando a duração do pulso. Quanto menor a duração do pulso, menor o tempo de entrada de calor do laser, o que ajuda a reduzir a expansão da zona afetada pelo calor e a formar uma solda menor. Durações de pulso mais longas resultam em mais entrada de calor e uma solda mais larga. Por meio da tecnologia de modelagem de pulso, a largura e o intervalo do pulso do laser podem ser controlados com precisão para otimizar a distribuição de calor e a morfologia da solda durante a soldagem.
- Qualidade do feixe: A qualidade e o controle do foco do feixe de laser são essenciais para a precisão da soldagem. Lasers com melhor qualidade de feixe têm tamanhos de foco menores e energia mais concentrada, o que pode atingir uma soldagem de maior precisão. Uma qualidade de feixe mais alta ajuda a reduzir a difusão de calor para que o calor fique mais concentrado na área de soldagem e a largura da solda se torne menor. Se a qualidade do feixe for ruim, isso causará uma distribuição desigual da energia do laser, aumentando assim a largura da solda.
Propriedades do Material
- Taxa de absorção: A taxa de absorção do material para o laser afeta diretamente o efeito da soldagem. A taxa de absorção de materiais metálicos é geralmente alta, especialmente quando o laser de comprimento de onda curto é combinado com o metal, a taxa de absorção é ainda melhorada. No processo de soldagem a laser, uma taxa de absorção mais alta significa que a energia do laser pode ser efetivamente convertida em energia térmica, resultando em uma solda menor. Por outro lado, se a taxa de absorção do material for baixa, a taxa de utilização efetiva da energia do laser é baixa, o que pode fazer com que a solda fique muito larga ou incompleta.
- Condutividade térmica: A condutividade térmica do material afeta a taxa de difusão de calor no substrato. Materiais com maior condutividade térmica (como cobre e alumínio) dispersará o calor rapidamente, resultando em dispersão excessiva de calor na área de soldagem e soldas mais largas. Em contraste, materiais com menor condutividade térmica (como aço inoxidável) pode manter mais calor concentrado na área de soldagem, formando uma solda mais estreita. Portanto, ao soldar materiais com diferentes condutividades térmicas, é necessário ajustar os parâmetros de soldagem de acordo com suas propriedades térmicas para garantir que a largura da solda seja apropriada.
- Refletividade: Materiais com alta refletividade (como alumínio e cobre) produzirão maior reflexão do laser e reduzirão a eficiência de absorção da energia do laser, afetando assim a qualidade da soldagem e podem causar o aumento da largura da solda. Para superar esse problema, você pode escolher um tipo de laser adequado para materiais altamente refletivos (como usar um laser de comprimento de onda curto) ou aumentar a potência do laser para compensar a perda de reflexão. Além disso, usar um feixe focado e um comprimento de onda de laser apropriado também pode ajudar a aumentar a taxa de absorção do laser de materiais refletivos.
Ambiente de soldagem
- Gás de proteção: O gás de proteção desempenha um papel importante na soldagem a laser. Ele não apenas previne a oxidação e a contaminação durante a soldagem, mas também afeta a condução de calor e a largura da solda controlando o fluxo de gás. Por exemplo, argônio e nitrogênio são frequentemente usados como gases de proteção na soldagem a laser. Eles podem efetivamente reduzir o alcance da zona afetada pelo calor e evitar a geração de soldas excessivas. A seleção e o controle do gás de proteção precisam ser ajustados de acordo com os materiais específicos e os requisitos de soldagem.
- Condições ambientais: Fatores ambientais como temperatura e umidade também têm um certo impacto no efeito da soldagem a laser. Em ambientes de baixa temperatura, a condutividade térmica dos materiais metálicos pode mudar, o que afeta o gerenciamento térmico durante a soldagem. Além disso, ambientes de alta umidade podem causar dispersão de energia do laser e afetar a qualidade da soldagem. Condições ambientais estáveis ajudam a manter a estabilidade do feixe de laser e garantem a consistência da largura da solda durante a soldagem.
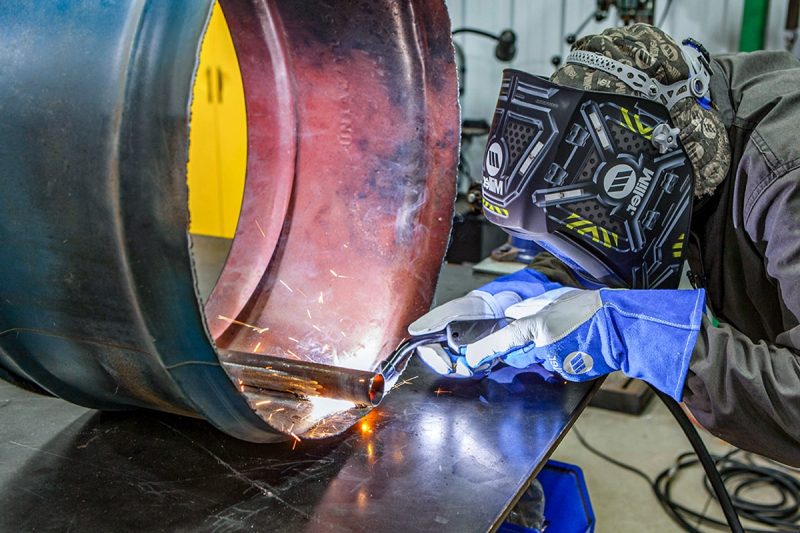
Tecnologia para atingir a largura mínima de solda
Seleção do tipo de laser
- Gerador de laser de fibra: O gerador de laser de fibra é uma das fontes de laser mais amplamente utilizadas em soldagem a laser. Ele tem alta potência, alta qualidade de feixe e excelente capacidade de foco. O feixe do gerador de laser de fibra pode ser focado precisamente em uma área muito pequena, tornando a largura da solda menor e capaz de processar materiais de chapa fina de forma eficiente. Os geradores de laser de fibra são muito adequados para tarefas de soldagem rápidas e de alta precisão e podem atingir pequenas soldas de alta qualidade e reduzir a expansão da zona afetada pelo calor (HAZ) do material.
- Tubo laser de CO2: O tubo laser de CO2 é outra fonte de laser comumente usada para soldagem de metais. Embora a qualidade do feixe dos tubos laser de CO2 geralmente não seja tão boa quanto a dos geradores de laser de fibra, ele pode fornecer maior potência e profundidade de penetração mais profunda, o que é adequado para soldar materiais mais espessos. Embora não seja tão preciso quanto o laser de fibra, larguras de solda relativamente pequenas podem ser obtidas por meio de regulação de potência razoável e velocidade de soldagem otimizada.
Seleção de comprimento de onda do laser
Otimização de parâmetros do laser
- Ajuste de potência do laser: A potência do laser é o principal fator que afeta a entrada de calor da soldagem. A potência excessiva fará com que o calor excessivo se espalhe para a área ao redor, alargando assim a solda e até mesmo causando defeitos de soldagem. Reduzir a potência adequadamente pode ajudar a reduzir a entrada de calor e estreitar a largura da solda, especialmente ao soldar materiais de chapa fina. No entanto, potência muito baixa pode resultar em soldagem inadequada. Portanto, o ajuste razoável da potência do laser para combiná-la com as propriedades do material, velocidade de soldagem e requisitos de soldagem pode obter uma soldagem precisa e controlar efetivamente a largura da solda.
- Tecnologia de modelagem de pulso: A tecnologia de soldagem a laser de pulso pode controlar com precisão a entrada de calor durante a soldagem ajustando a frequência, duração e energia do pulso do laser. Quanto menor a largura do pulso, menor o tempo de entrada de calor e menor o acúmulo de calor na área de soldagem, tornando a solda mais estreita. Além disso, ajustando a frequência e a energia do pulso, a velocidade de soldagem e a morfologia da poça de fusão podem ser controladas, o que por sua vez afeta a largura da solda. Usando a tecnologia de modelagem de pulso, especialmente na micro soldagem, a distribuição de calor de cada pulso pode ser controlada com precisão para atingir efetivamente a largura mínima da solda.
- Controle do foco do feixe: A precisão e a largura da solda da soldagem a laser estão intimamente relacionadas à posição focal do feixe. Quanto menor o foco do feixe de laser, maior a densidade de energia, que pode ser concentrada na área de soldagem, produzindo assim uma solda estreita e fina. Portanto, o controle do foco do laser é muito importante. Ao ajustar a posição do foco, a energia do feixe de laser pode ser mais concentrada na área de soldagem, evitando a difusão de calor para a área circundante e, assim, reduzindo a largura da solda.
Preparação de Materiais
- Limpeza da superfície: A limpeza da superfície do material de soldagem afeta diretamente o efeito da soldagem a laser. Óxidos, óleo, ferrugem e outros contaminantes na superfície afetarão a taxa de absorção do laser, resultando na incapacidade de concentrar efetivamente o calor na área de soldagem, afetando assim a qualidade da soldagem e aumentando a largura da solda. Garantir que a superfície de soldagem esteja limpa e livre de contaminação é um pré-requisito para otimizar a qualidade da soldagem. Os contaminantes da superfície geralmente podem ser removidos por limpeza química, limpeza mecânica ou limpeza a laser.
- Revestimento de superfície: Em alguns casos, especialmente para materiais difíceis de soldar, o revestimento de superfície pode melhorar significativamente a eficiência de absorção do laser. Materiais de revestimento (como revestimento de cobre, revestimento de zinco, etc.) podem melhorar a interação entre o laser e o material e aumentar o acúmulo de calor na área de soldagem, ajudando assim a controlar com precisão a largura da solda durante o processo de soldagem. Além disso, revestimentos especiais também podem melhorar a estabilidade da poça de fusão durante a soldagem e reduzir defeitos durante a soldagem.
Tecnologia de soldagem avançada
- Soldagem a laser híbrida: A tecnologia de soldagem a laser híbrida combina as vantagens dos métodos de soldagem a laser e tradicionais (como soldagem TIG ou soldagem MIG) e melhora a entrada de calor e a precisão da soldagem ao combinar as vantagens de diferentes fontes de calor. A combinação de métodos de soldagem a laser e tradicionais pode efetivamente reduzir a largura da solda, especialmente ao soldar materiais mais espessos. A tecnologia de soldagem a laser híbrida pode fornecer maior estabilidade de poça de fusão e menores zonas afetadas pelo calor, alcançando assim efeitos de soldagem mais refinados.
- Tecnologia de microssoldagem: A microssoldagem a laser é uma tecnologia de soldagem de alta precisão para processamento de soldas ultrapequenas, especialmente adequada para conectar peças pequenas. A tecnologia de microssoldagem usa pulsos de laser finamente controlados para obter transferência de energia eficiente em uma área de soldagem muito pequena, garantindo a formação de soldas muito estreitas. A microssoldagem é comumente usada em indústrias como eletrônica, instrumentos de precisão e dispositivos médicos, e pode obter alta precisão de soldagem e minimizar o impacto térmico da área de soldagem.
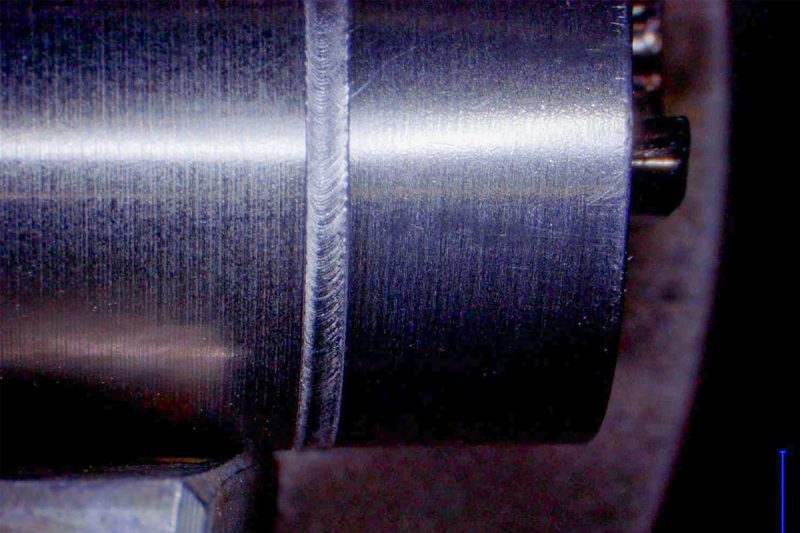
Desafios e Soluções
Gestão Térmica
Desafio
Solução
- Use resfriamento de gás auxiliar: Usar gás de proteção apropriado ou gás auxiliar (como argônio, nitrogênio ou oxigênio) pode não apenas evitar a oxidação da área de soldagem, mas também remover efetivamente o excesso de calor gerado durante a soldagem, reduzindo assim a expansão da zona afetada pelo calor. A vazão e a pressão do gás auxiliar precisam ser otimizadas de acordo com o material de soldagem, velocidade de soldagem e potência do laser para garantir o melhor efeito de resfriamento.
- Otimização da velocidade de soldagem: Aumentar adequadamente a velocidade de soldagem pode reduzir a entrada de calor por unidade de tempo e reduzir o tempo de aquecimento do material, evitando assim efetivamente o superaquecimento da área de soldagem. Velocidades de soldagem mais altas podem fazer com que o calor se espalhe rapidamente para uma área maior, reduzir o aumento da temperatura local e, assim, controlar a largura da solda e a zona afetada pelo calor.
- Regulação da fonte de calor: Ao ajustar a potência do laser ou usar um laser pulsado, a entrada de calor pode ser controlada com precisão durante o processo de soldagem. Especialmente na soldagem por pulso, pulsos curtos e frequências de pulso mais altas podem garantir que o calor seja rapidamente focado e distribuído na área de soldagem para evitar a difusão de calor.
Refletividade do material
Desafio
Solução
- Use lasers de comprimento de onda curto: Lasers de comprimento de onda curto (como aqueles produzidos por geradores de laser de fibra) têm uma taxa de absorção mais alta para materiais altamente refletivos. Lasers de comprimento de onda curto podem ser melhor absorvidos por materiais, reduzir reflexões e garantir que mais energia laser seja efetivamente usada no processo de soldagem, melhorando assim a eficiência da soldagem e reduzindo a largura da solda. Comparados com lasers de CO2 de comprimento de onda longo, geradores de laser de fibra são mais adequados para processar materiais com maior refletividade.
- Ajuste de potência do laser: Para materiais com alta refletividade, reduzir adequadamente a potência do laser pode evitar reflexão excessiva de energia. Configurações de potência mais baixas ajudam a reduzir reflexões e evitar desperdício de energia, controlando assim efetivamente a largura da solda e otimizando a qualidade da soldagem.
- Use materiais revestidos: Alguns materiais metálicos altamente refletivos, como alumínio e cobre, podem usar tecnologia de revestimento, como revestimento de alumínio, revestimento de cobre e outros métodos de tratamento de superfície. Esses revestimentos têm menor refletividade, o que pode melhorar a eficiência de absorção do laser e reduzir a interferência da reflexão no processo de soldagem, controlando melhor a largura da solda.
Estabilidade do Processo
Desafio
Solução
- Sistema avançado de controle de laser: Ao usar sistemas avançados de controle de laser, parâmetros-chave como potência do laser, velocidade de soldagem, foco do feixe, etc. podem ser monitorados e ajustados em tempo real para garantir a consistência dos parâmetros do laser durante cada processo de soldagem. Os sistemas modernos de soldagem a laser geralmente são equipados com sensores de alta precisão e funções de ajuste automático, que podem detectar a temperatura da área de soldagem, a morfologia da poça de fusão e a posição do feixe em tempo real, e ajustar automaticamente a saída do laser para manter a estabilidade do processo de soldagem.
- Feedback em tempo real e controle de malha fechada: O uso da tecnologia de feedback em tempo real e controle de malha fechada pode ajustar parâmetros em tempo real durante o processo de soldagem para lidar com mudanças nas propriedades do material e no ambiente de soldagem. Por exemplo, sensores podem monitorar o tamanho, a forma e a temperatura da poça de fusão, e o sistema pode ajustar automaticamente a potência do laser e a velocidade de soldagem para manter a consistência da qualidade da soldagem. Esta tecnologia pode melhorar significativamente a confiabilidade do processo de soldagem e evitar problemas de soldagem causados por flutuações do processo.
- Otimização do caminho de soldagem: Durante o processo de soldagem, otimizar o planejamento do caminho do laser é outra maneira importante de melhorar a estabilidade do processo. Ao controlar com precisão o caminho de soldagem e a sequência de soldagem, a deformação do material e as mudanças na zona afetada pelo calor podem ser reduzidas, garantindo uma distribuição consistente da temperatura durante cada processo de soldagem e, assim, alcançando resultados de soldagem estáveis.
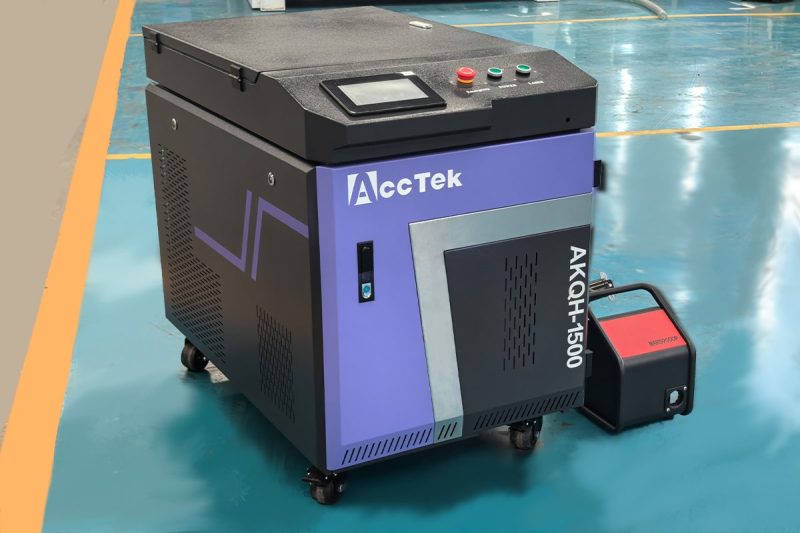
Resumir
Neste processo, a nossa máquinas de solda a laser tornaram-se líderes na indústria com sua tecnologia superior e design inovador. As máquinas de solda a laser da nossa empresa usam a mais recente tecnologia de laser de fibra, que pode atingir uma soldagem eficiente, garantindo controle preciso da temperatura durante o processo de soldagem, controlando assim efetivamente a largura da solda e reduzindo a zona afetada pelo calor. Nosso equipamento de soldagem não só tem capacidades de ajuste de feixe de laser de alta precisão, mas também é equipado com um sistema avançado de controle de temperatura que pode ajustar automaticamente os parâmetros durante o processo de soldagem, otimizando assim o efeito da soldagem e garantindo qualidade estável e consistente em cada ponto de soldagem.
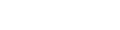
- [email protected]
- [email protected]
- +86-19963414011
- No. 3 Zona A, Zona Industrial de Lunzhen, Cidade de Yucheng, Província de Shandong.