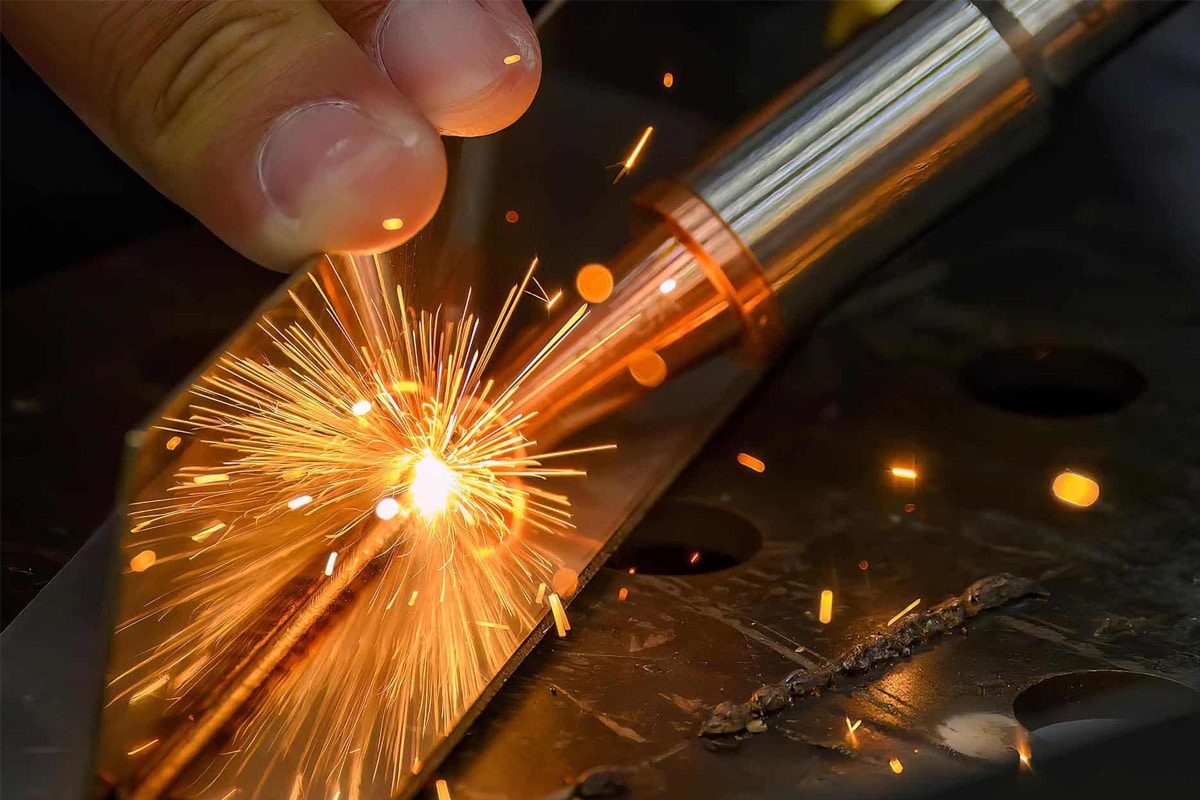
How Does Laser Welding Produce High-Quality Weld Seams?
Laser welding is an efficient and precise welding technology that uses the powerful energy of a laser beam to create high-strength weld joints between materials. This technology is widely used in aerospace, automotive manufacturing, electronics, and other industries, particularly for production tasks that require strict welding precision and quality. Compared to traditional welding methods, laser welding offers finer heat control, a smaller heat-affected zone (HAZ), and faster welding speeds, resulting in highly efficient and accurate welds.
To achieve high-quality weld seams, laser welding relies not only on the characteristics of the laser but also on the precise adjustment of process parameters such as laser power, beam diameter, and welding speed. Additionally, the selection of welding materials and the performance of the laser equipment play a decisive role. By considering all these factors, it is possible to ensure that the weld joints have excellent mechanical properties, good surface quality, and long-term stability. This article will delve into how precise control of welding parameters and material properties can achieve the ideal laser welding results.
Índice
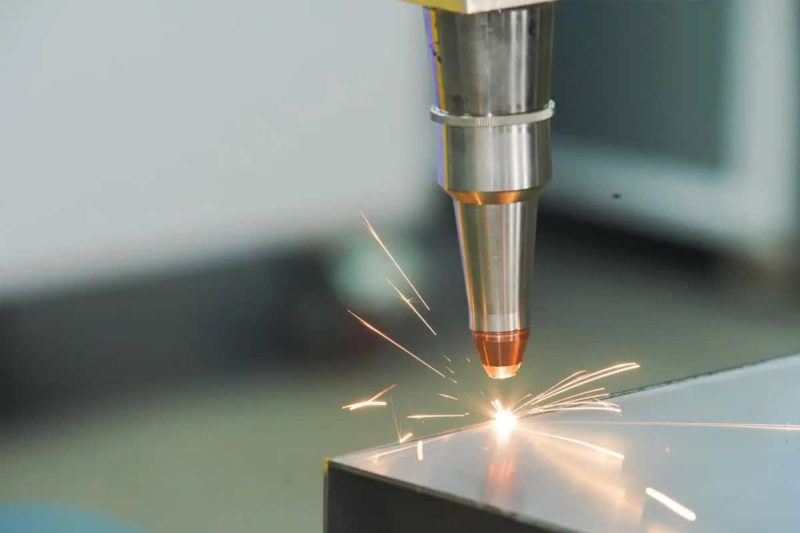
Introdução à soldagem a laser
Definition:Laser welding is a technique that uses the high energy density of a laser beam to heat metal or other materials to their melting point, forming a weld joint.
Working Principle:The working principle of laser welding involves focusing a high-intensity laser beam on the surface of the material, locally heating it to rapidly reach the melting point. As the laser energy is transferred to the material’s surface, it melts locally, forming a weld pool. Under the influence of the laser energy, the weld pool gradually expands, and eventually cools and solidifies, forming a strong weld joint.
Tipos de geradores de laser
There are two main types of laser generators commonly used in laser welding: fiber laser generators and CO2 laser generators.
- Fiber laser generator: Fiber laser generator is widely used in the welding industry for its high efficiency, stability, and low operating cost. The fiber laser generator has superior beam quality, which can achieve high-precision and high-speed welding. It is suitable for welding various metal materials, especially for occasions requiring high-strength welded joints, such as automobile, aviation, and precision instrument manufacturing.
- CO2 laser generator: CO2 laser generator is also used in industrial welding. Its laser wavelength is longer, which is suitable for welding thick materials and large areas.
Depending on specific welding needs and material properties, selecting the appropriate laser generator can significantly improve welding efficiency and quality. By precisely controlling the output power and beam characteristics of the laser generator, more precise and higher-quality welding results can be achieved.
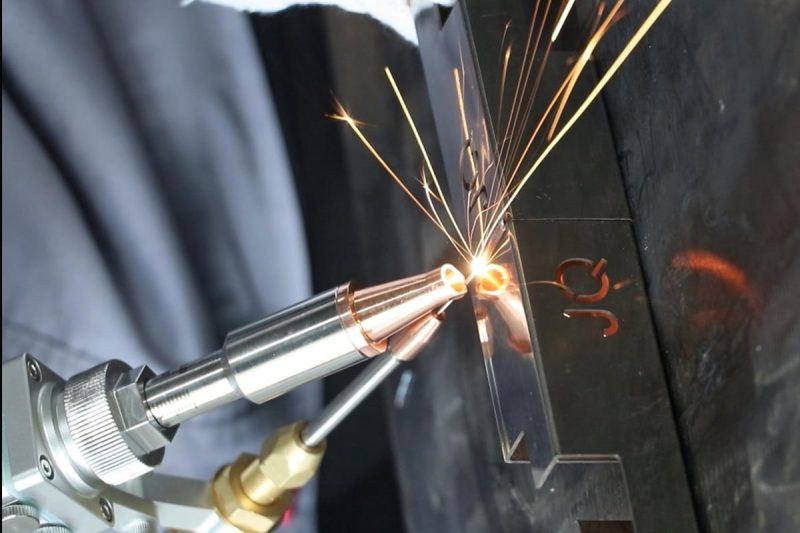
Laser Welding Process Parameters
The quality and effect of laser welding are affected by multiple process parameters, among which laser power, beam diameter, focus position, welding speed, and beam quality are key factors. Reasonable adjustment of these parameters can not only control the heat input during welding, but also ensure the accuracy, strength, and stability of the welded joint. Different materials and welding needs have different requirements for these parameters, and optimizing the selection of process parameters is crucial to achieving high-quality welding. In this section, we will take a deep look at these key parameters and their impact on welding quality.
Potência do Laser
Laser power is a key parameter that determines welding depth and speed. Appropriate laser power can ensure that the material is fully melted and a stable weld joint is quickly formed. If the power is too low, the weld joint may not be strong or even fail to melt the material; while too high power may cause excessive melting, excessive heat affected zone (HAZ), or excessive spatter, thus affecting the welding quality. The correct power selection needs to be adjusted according to the material thickness, type, and welding requirements.
Beam Diameter and Focus
The beam diameter and focal position directly affect the heat input and welding accuracy during welding. A smaller beam diameter can concentrate more energy in the welding area, increase the temperature of the molten pool, and thus achieve higher welding accuracy. In addition, the focal position of the laser beam determines the concentration of the laser energy. The correct focal position can ensure uniform distribution of heat in the welding area and improve the quality of the welded joint.
Velocidade de soldagem
Welding speed is another important process parameter that directly affects the quality and appearance of the weld. Too fast a speed may result in incomplete welding and insufficient weld joint strength, while too slow a speed may result in excessive heat input, causing excessive melting of the material and producing an irregular weld. The welding speed needs to be optimized based on the thermal conductivity, thickness and required welding depth of the material.
Qualidade do feixe
Beam quality is one of the core parameters of laser welding, which directly affects the accuracy and stability of welding. High-quality beams have better-focusing ability and can deliver higher energy in a smaller area, thus ensuring the uniformity and stability of the welding process. High-quality beams can reduce thermal damage, ensure uniform microstructure of the welded joint, and improve welding quality.
Laser welding process parameters play a vital role in achieving high-quality welded joints. Reasonable selection and precise control of laser power, beam diameter and focus, welding speed, and beam quality can ensure the strength, stability, and aesthetics of the welded joint. Changes in each parameter will have different effects on the welding effect. Therefore, adjusting these process parameters for different materials and welding requirements is the key to improving welding quality. By optimizing these parameters, the efficiency and consistency of the welding process can be ensured to meet various high-precision manufacturing needs.
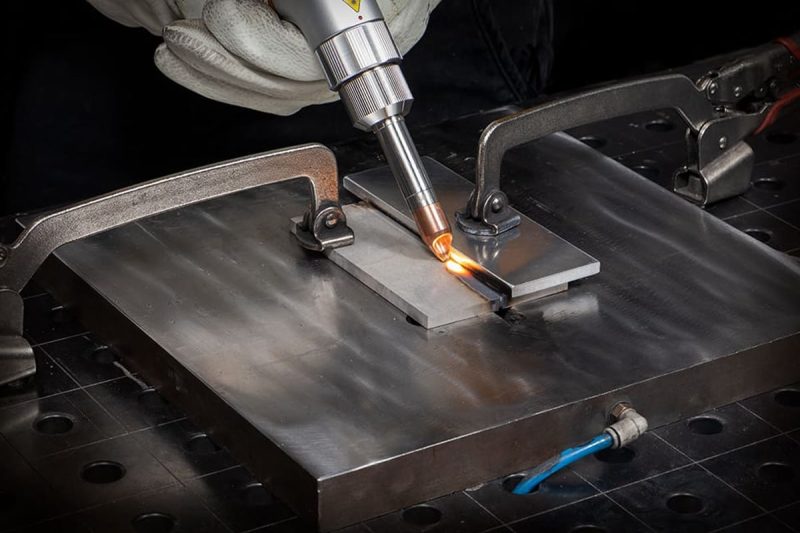
Factors Affecting High Quality Laser Welding
High-quality laser welding depends on several key factors, including precision control, deep penetration, cleanliness and purity, and metallurgical properties. Each factor directly affects the quality, strength, and stability of the welded joint. Precise control of the heat-affected zone and welding speed to ensure minimal deformation and damage of the material during welding is the basis for obtaining an ideal welded joint. At the same time, uniform penetration and a clean welding environment are essential to improving welding quality. To meet the needs of different applications, the welding process must be optimized and adjusted in many aspects.
Precisão e Controle
- Maintain a narrow heat-affected zone (HAZ): The width of the heat-affected zone directly affects the quality of the weld joint. Laser welding can precisely control the heat input and keep the heat-affected zone narrow, thereby reducing thermal damage to the material. A narrower HAZ can effectively avoid deformation and discoloration of the material, which is especially important in high-precision welding applications.
- Minimize distortion and warping during welding: Laser welding reduces heat diffusion and excessive heat input through precise energy control, which can greatly reduce the risk of material deformation during welding and ensure the stability and high precision of the weld joint. This is especially important for industries that require perfect weld joints, such as precision machinery manufacturing and aerospace.
Deep Penetration Capability
- Efficient welding of thick materials: Laser welding is capable of welding thicker metal materials due to its high power density. This gives it a clear advantage in applications that require deep penetration and can efficiently weld thick materials without losing weld quality.
- Uniform penetration: By precisely adjusting the laser power and welding speed, laser welding can ensure uniformity of weld depth, and the consistency of weld penetration helps improve the overall strength of the weld joint. Weld joints with uniform depth can effectively avoid performance problems caused by uneven joints and ensure the stability and durability of weld joints.
Cleanliness and Purity
- Minimum spatter and oxide formation: Laser welding, due to its concentrated heating and efficient energy transfer characteristics, can complete the welding process in a shorter time, greatly reducing the spatter. Low spatter and oxide generation rates during welding help to improve the cleanliness of the welded joint and reduce the adhesion of contaminants.
- Reduced risk of contamination and defects: Reducing spatter and oxide formation not only helps to maintain the purity of the welded joint but also effectively reduces the risk of welding defects such as holes, pores, and cracks, which is especially important for high-strength welded joints. High cleanliness during welding ensures the strength and durability of the welded joint.
Propriedades Metalúrgicas
- Uniform microstructure: Laser welding can form a uniform microstructure in the molten pool area, ensuring that the weld joint has a uniform grain structure. The uniform microstructure enhances the mechanical properties of the weld joint and avoids the influence of grain coarsening or uneven distribution on the strength and toughness of the weld joint.
- Improve the strength and toughness of the joint: Through precise laser welding control, the weld joint can obtain higher strength and toughness, especially in applications that need to withstand high loads or harsh working environments. The metallurgical properties of the weld joint play an important role in the service life and reliability of the overall product. Good metallurgical properties not only ensure the performance of the weld joint but also improve the overall quality and durability of the product.
The factors that affect high-quality laser welding are interrelated and together determine the performance and reliability of the welded joint. By optimizing heat-affected zone control, deep penetration capability, cleanliness, and metallurgical properties, the welding quality can be effectively improved to ensure the strength and durability of the joint. Precise process control can not only reduce welding defects and material damage but also improve the overall mechanical properties of the product and extend its service life. Mastering these key factors, laser welding can provide efficient and stable welding solutions in complex applications.
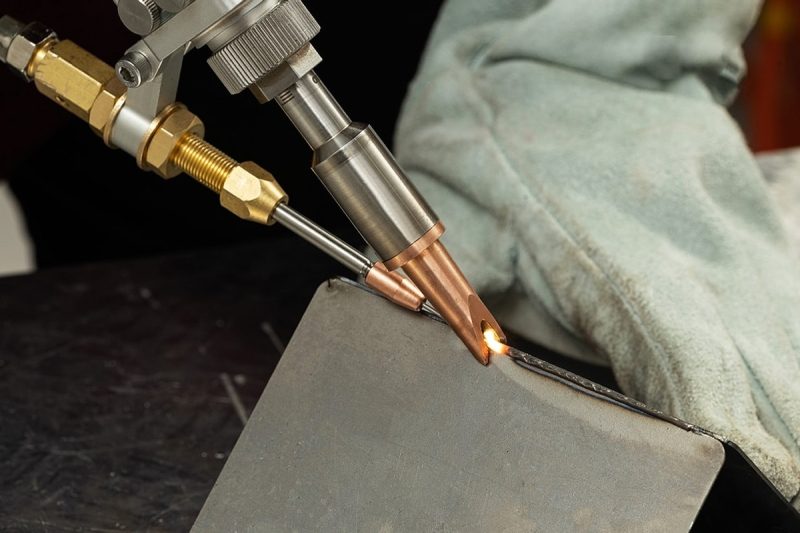
Benefits of High-Quality Laser Welding
High-quality laser welding can bring several significant advantages. First, the strength and toughness of the welded joint can be improved, thereby enhancing the overall mechanical properties of the product. Second, laser welding can reduce material waste and production time through efficient processes, thereby effectively reducing production costs. Finally, laser welding provides a fine welding effect, which can improve the appearance and surface finish of the product.
- Improve mechanical properties: High-quality laser welding can significantly enhance the strength and toughness of welded joints, ensuring that the product can withstand greater pressure and load during use. This high-quality welded joint not only improves the overall mechanical properties but also enhances the durability of the welded parts and extends the service life of the product.
- Cost savings: Laser welding is known for its high efficiency and low material waste. Through precise energy control, less material is lost during the welding process. In addition, laser welding is faster, reducing production time, thereby reducing overall manufacturing costs and improving production efficiency.
- Enhanced aesthetics and surface finish: The laser welding process can achieve fine welding effects, ensuring that the surface of the welded joint is smooth and free of obvious flaws. Due to the smaller heat input, there is less deformation and oxidation in the welding area, the appearance of the welded joint is cleaner and more beautiful, and the overall appearance and texture of the product are improved.
High-quality laser welding can not only improve the mechanical properties of the welded joint but also save production costs and improve the appearance of the product. High-quality laser welding technology brings higher production efficiency and product value to the modern manufacturing industry.
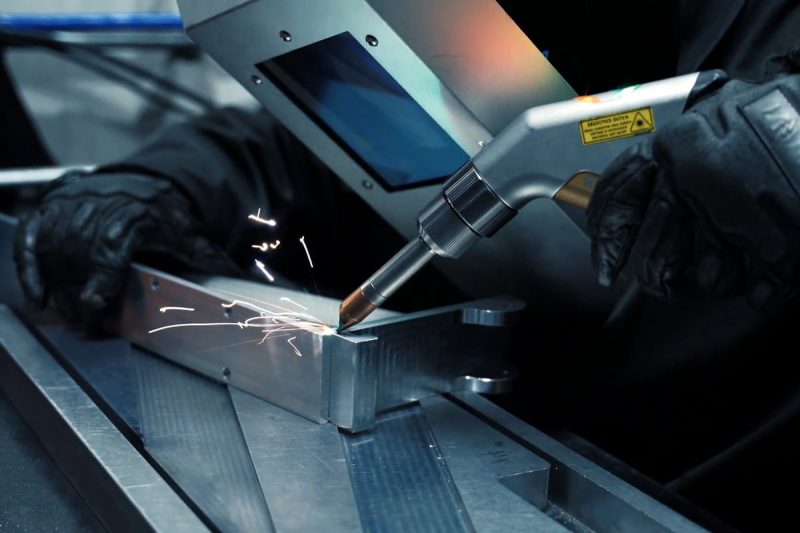
Challenges and Considerations for Achieving High Quality Welds
Although laser welding has significant advantages in improving welding quality and efficiency, it still faces some challenges in practical applications. First of all, precise control of welding parameters is a key factor in ensuring welding quality. Small changes in parameters such as laser power, welding speed, focus position, etc. can cause significant changes in the strength, appearance, and durability of the welded joint. Precise adjustment and control of these parameters requires advanced equipment and extensive experience of operators.
In addition, laser welding also has high requirements for the characteristics of materials. Different materials have different characteristics such as thermal conductivity, reflectivity, and melting point, and welding parameters need to be adjusted according to the specific materials. If the material is not selected properly or the welding process cannot be correctly matched, the welding quality may not meet the standards, such as loose welding, too large heat-affected zone, and other problems.
Equipment commissioning and maintenance is also an important consideration for achieving high-quality welding. Laser welding equipment requires regular precision adjustment to ensure the accuracy and stability of the laser beam focus. Any equipment failure or improper setting will directly affect the welding effect.
Finally, the production environment also has a certain impact on the welding quality. For example, the welding process may be affected by temperature, humidity, and air quality, all of which may affect the melting and cooling process of the welding material, thereby affecting the welding quality. Therefore, maintaining a suitable production environment and ensuring that the equipment and operators are in the best working condition is the basis for achieving high-quality laser welding.
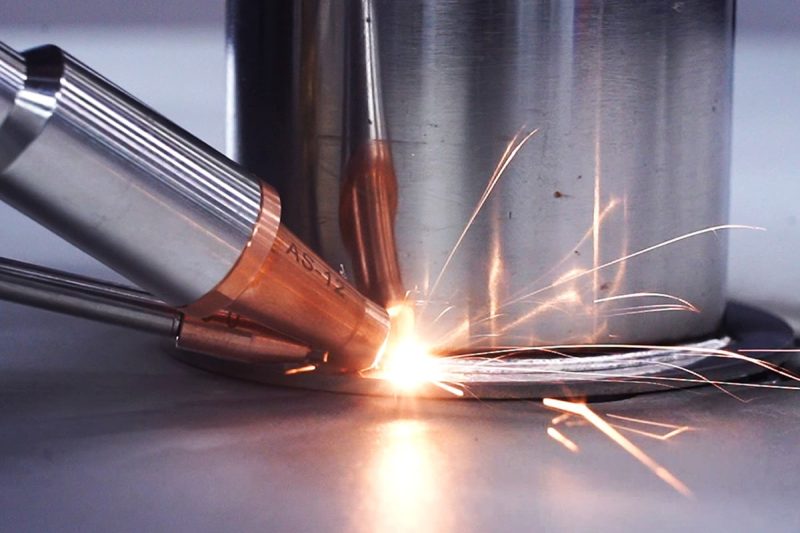
Resumir
High-quality laser welding not only depends on precise process parameters and advanced laser equipment, but also requires comprehensive consideration of multiple factors such as material properties, precise control of operators, and production environment. By rationally adjusting key parameters such as laser power, welding speed, and beam quality, the welding process can be precisely controlled to ensure that the welded joint has excellent strength, toughness, and aesthetics.
In addition, the characteristics of the material also have an important influence on the effect of laser welding. The thermal conductivity, reflectivity, and melting point of different materials need to be adjusted according to the actual situation to achieve the ideal welding quality. Based on ensuring the matching of process parameters and materials, good operating experience and a stable production environment are also crucial. By optimizing these factors, the welding quality can be greatly improved, which not only improves production efficiency but also ensures that the product has higher mechanical properties and long-term stability during use.
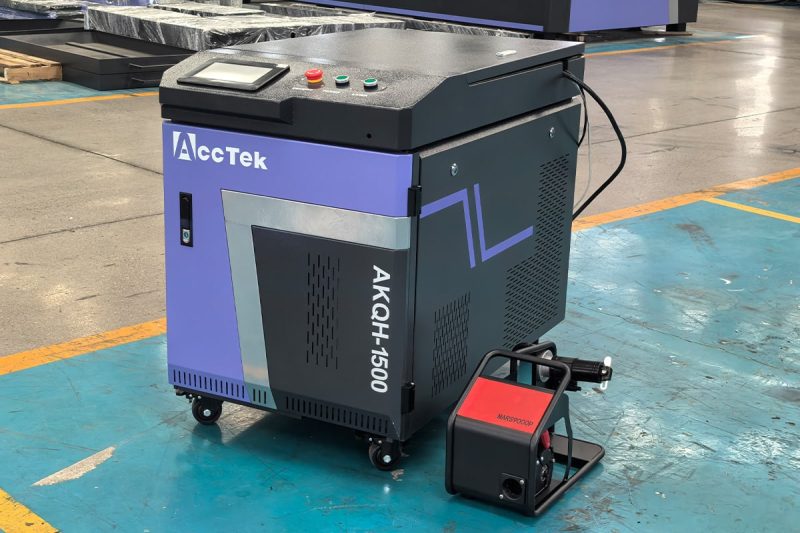
Obtenha soluções a laser
When choosing laser welding technology, Laser AccTek provides you with first-class solutions to help you achieve high-quality and efficient welding. We provide a variety of power máquinas de solda a laser, handheld welding machines, and automatic welding machines, covering a variety of materials and application requirements. Whether you need high-precision welding, welding heavy materials, or pursuing surface finish and aesthetics, we can recommend the most suitable equipment for you.
Cooperating with us, you can not only enjoy high-performance laser welding equipment but also get professional technical support. We provide customers with comprehensive after-sales services, including equipment warranty, installation guidance, and operation training, to ensure that your production line is put into use quickly and smoothly. With our rich experience and technical advantages, AccTek Laser will be your ideal choice for high-quality welding, helping you improve production efficiency, reduce cost, and ensure the long-term stability of products.
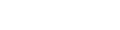
Informações de contato
- [email protected]
- [email protected]
- +86-19963414011
- No. 3 Zona A, Zona Industrial de Lunzhen, Cidade de Yucheng, Província de Shandong.
Obtenha soluções a laser