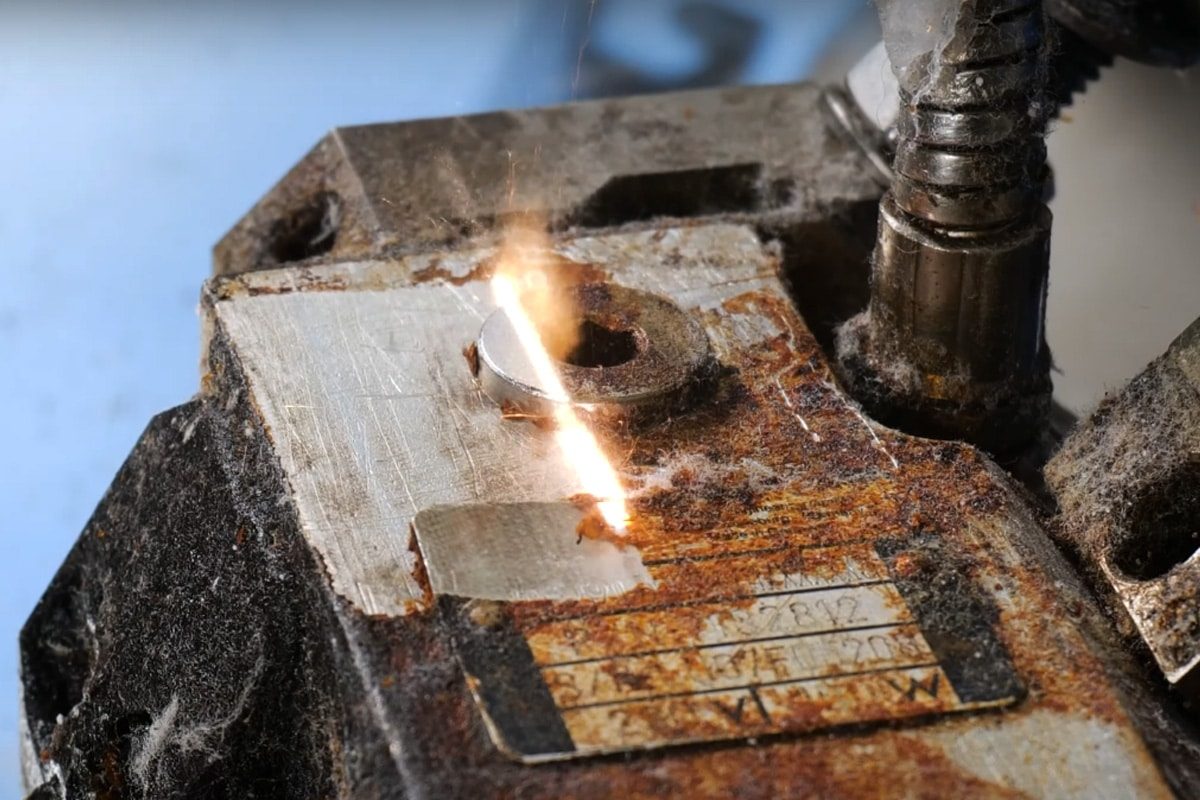
How fast is laser cleaning?
Laser cleaning is an efficient and environmentally friendly surface treatment technology that uses high-energy laser beams to interact with the surface of pollutants to remove them from the surface of the substrate. The advantages of laser cleaning are not only reflected in its excellent cleaning effect but also because it does not use chemicals or water, avoiding the environmental pollution problems in traditional cleaning methods. Therefore, it is widely used in many industries, such as metal rust removal, coating removal, oil cleaning, welding pretreatment, etc. Laser cleaning technology not only improves product quality but also reduces the environmental burden in the production process. Therefore, it is favored by more and more companies.
However, the cleaning speed of laser cleaning is one of the key factors affecting its widespread application. The cleaning speed is affected by many factors, including laser power, beam quality, laser wavelength, pulse duration, type of material, nature of contaminants, etc. Different materials and contaminants may require different laser parameters and treatment methods to ensure the best cleaning effect and the fastest processing speed.
This article will explore the factors that affect laser cleaning speed from multiple perspectives, introduce typical cleaning speeds, and provide some effective methods to help companies optimize the laser cleaning process and improve overall production efficiency. By analyzing these key factors, companies can better understand the application potential of laser cleaning and achieve efficient and precise surface cleaning.
Índice
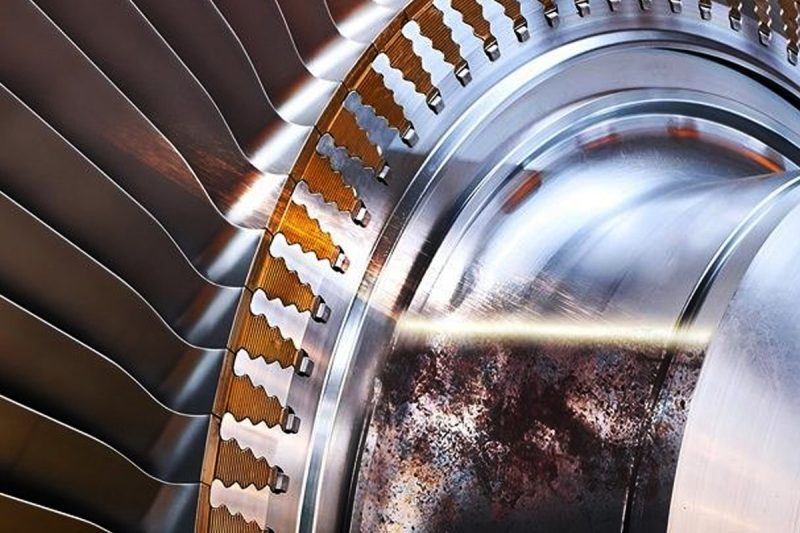
Laser Cleaning Introduction
Laser cleaning is a non-contact cleaning technology that uses a high-energy laser beam to irradiate the surface of a material to rapidly evaporate, vaporize, or peel off pollutants, oxide layers, or coatings. Laser cleaning is more precise, environmentally friendly, and efficient than traditional chemical or mechanical cleaning methods, so it has been widely used in many industries, especially in metal surface treatment, coating removal, rust removal, degreasing, welding pre- and post-treatment, and other fields.
Laser cleaning can be divided into two main types, depending on the mechanism of interaction between the laser and the contaminant:
- Thermal laser cleaning: Thermal laser cleaning uses a high-power laser beam to irradiate the surface of the material, causing the contamination layer, oxide layer, or coating to heat up rapidly and reach a temperature at which it vaporizes or peels off. The rapid release of laser energy causes the surface of the contaminant to expand rapidly and detach from the substrate, resulting in a significant cleaning effect. Thermal laser cleaning is widely used to clean harder contaminants, such as metal rust, pain, or coating removal.
- Non-thermal laser cleaning: Non-thermal laser cleaning mainly relies on short-pulse lasers to react physically and chemically with the surface of the material to remove contaminants. Unlike thermal laser cleaning, non-thermal laser cleaning does not significantly heat the surface of the substrate, avoiding deformation or damage to the substrate, so it is suitable for some heat-sensitive materials, such as plastics, glass, or some delicate coating removal. This cleaning method uses the high energy density of the laser to quickly evaporate the contaminants without causing thermal effects on the substrate.
Compared with traditional chemical cleaning (usually using acidic or alkaline solvents) or sandblasting cleaning (removing contaminants mechanically), laser cleaning is not only precise and efficient but also more environmentally friendly. Its non-contact working method avoids any physical damage to the surface while reducing the use of chemicals, which meets modern environmental protection requirements. Therefore, laser cleaning technology has been widely used in aerospace, automobile manufacturing, cultural relics restoration, the electronics industry, and other fields, becoming an important solution for cleaning and surface treatment in these industries.
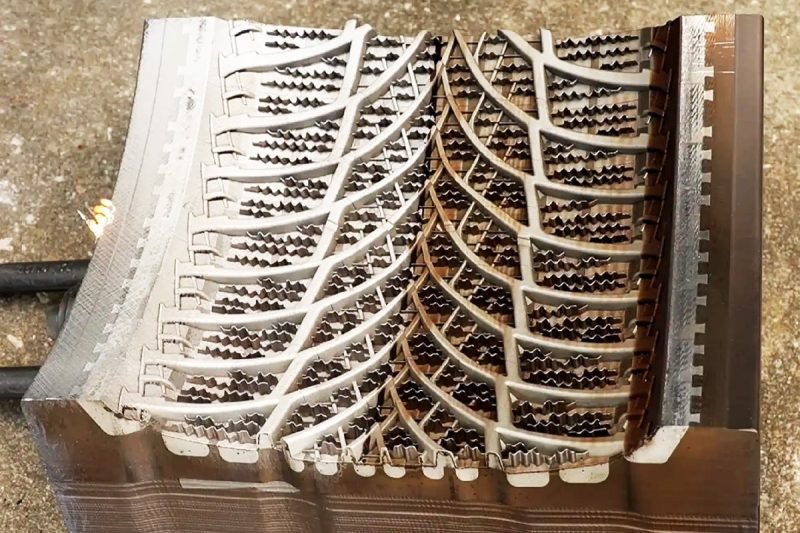
Factors affecting laser cleaning speed
The speed of laser cleaning is affected by many factors, including the parameters of the laser equipment, the characteristics of the material to be cleaned, and external environmental conditions. Different application scenarios have different requirements for cleaning efficiency, so multiple variables need to be considered comprehensively to optimize the cleaning effect and work efficiency. The following are the key factors that affect the speed of laser cleaning:
- Laser power: Laser power is one of the most direct factors affecting cleaning speed. The higher the power, the more energy is provided per unit of time, which speeds up the removal of pollutants. For example, a 100W laser cleaning machineis suitable for small precision cleaning, while a 1000W laser cleaning machine or even higher power laser generator is more suitable for large-area rapid cleaning, such as rust removal of ship hulls or cleaning of steel structures. However, too high power may cause thermal damage to the substrate, so it is necessary to weigh the cleaning speed and material safety when selecting the power.
- Beam quality: The beam quality determines the energy distribution and focusing ability of the laser. Good beam quality (such as a fiber laser generator with a high M2 factor) can provide more precise and uniform energy distribution, improve cleaning efficiency, and reduce thermal effects on the substrate. For example, a nanosecond pulse laser with high beam quality can reduce material damage while ensuring cleaning speed, while a low-quality beam may cause uneven cleaning or excessive heating.
- Laser wavelength: The wavelength of the laser determines the material’s absorption efficiency of the laser. Different materials have different absorption rates for lasers of specific wavelengths, so choosing the right wavelength is crucial. For example, 1064nm fiber lasers are particularly suitable for cleaning metal surfaces, while other wavelengths may be more suitable for removing organic matter or non-metallic materials.
- Pulse duration and frequency: The duration (nanosecond, picosecond, or femtosecond) and frequency (Hz/kHz/MHz) of the pulsed laser directly affect the cleaning effect and speed. Short-pulse lasers have higher energy density and can remove contaminants in a very short time without causing thermal effects on the substrate. High-frequency lasers can increase the number of laser actions per unit of time and improve cleaning efficiency. For example, a laser generator with a pulse frequency adjustment range of 20-200kHz can flexibly adjust the cleaning speed and effect according to different cleaning needs.
- Material type: Different materials absorb and react to lasers differently, which directly affects the cleaning speed. For example, metal materials (such as aluminum, copper, and steel) have a higher absorption rate for 1064nm fiber lasers, so the cleaning efficiency is faster; while plastics or ceramics may require special wavelengths or lower energy lasers for cleaning to avoid deformation or damage to the material.
- Contaminant type: The objects of laser cleaning may include rust, paint, coating, oil, oxide layer, etc. These contaminants have different absorption characteristics and adhesion strength, which affects the cleaning speed. For example, a thick corrosion layer or oxide layer may require multiple scans or a higher power laser to completely remove, while an oil or light oxide layer may only need one scan to remove.
- Surface area: The size of the cleaning area determines the required cleaning time. Larger surfaces usually require higher power, higher scanning efficiency, or larger spot diameter to cover a larger area and speed up the cleaning speed. In addition, multi-axis robots or automated cleaning systems can improve the cleaning efficiency of large-area workpieces.
- Scanning speed and coverage: The scanning method and speed of the laser beam determine the uniform distribution of energy. High-speed scanning can reduce heat accumulation and improve cleaning uniformity, while optimized scanning paths can ensure that cleaning coverage is not missed. For example, using a high-precision galvanometer scanning system can greatly improve work efficiency while ensuring fine cleaning.
- Cooling and debris removal: During the cleaning process, evaporated or peeled contaminants may be redeposited on the material surface, affecting cleaning efficiency. Therefore, an effective cooling system (such as an air cooling or water cooling system) and an efficient debris removal device (such as a vacuum suction or purge system) can greatly improve the cleaning speed and effect.
- Environmental conditions: External environmental factors (such as temperature, humidity, air quality, etc.) can also affect the stability and efficiency of laser cleaning. For example, in a high-humidity environment, water vapor in the air may affect the transmission of laser energy, thereby reducing the cleaning efficiency. In addition, a dusty environment may affect the performance of optical components, so regular maintenance and cleaning of the optical system is required.
Laser cleaning speed is not determined by a single factor but by multiple factors such as laser parameters, material properties, contaminant type, scanning system, etc. In practical applications, different working conditions require targeted adjustments to laser power, pulse parameters, scanning speed, etc. to achieve the best cleaning effect. By optimizing these parameters, companies can improve cleaning efficiency, reduce energy consumption, and ensure more stable and high-quality cleaning results.
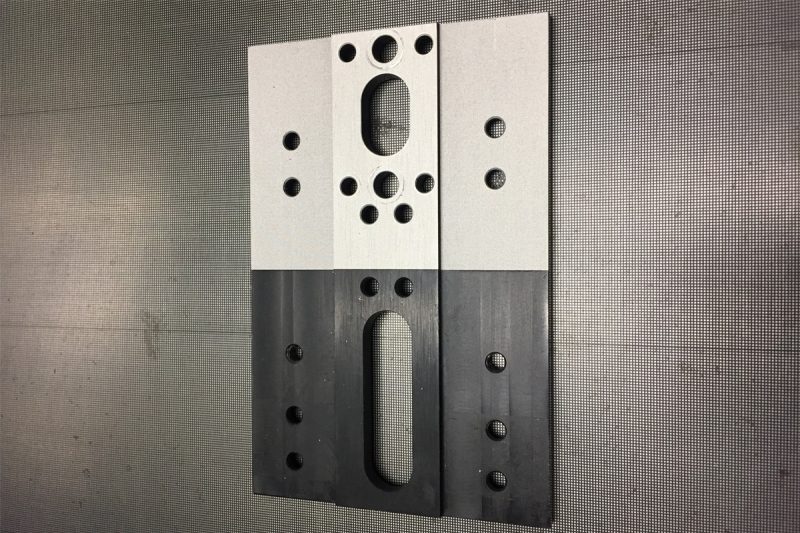
Typical cleaning speed
The speed of laser cleaning is affected by many factors, and the parameter settings in different application scenarios may vary significantly. Generally speaking, the working efficiency of máquina de limpeza a laser is closely related to laser power, as well as factors such as contaminant type, surface condition, and scanning system. For example:
Rust removal application: In the process of metal rust removal, a 1000W fiber laser cleaning machine can clean about 8-12㎡ metal surfaces in one hour. This speed is suitable for medium-thick rust or oxide layers. In practical applications, if the contamination layer is thicker or has strong adhesion, it may be necessary to increase the laser power or perform multiple scans to ensure complete removal. At the same time, pay attention to adjusting the laser focus and scanning speed during cleaning to avoid overheating of the metal substrate.
Paint removal applications: For the removal of thin layers of paint, a 1000W laser can achieve a cleaning efficiency of 6-10㎡ per hour. This application usually requires a higher energy density to quickly vaporize or peel off the paint layer, but at the same time requires fine control to avoid damage to the underlying material. If the paint layer is thicker, a higher-power laser or an increased number of scans is usually required to achieve complete paint removal.
Oil and grease removal applications: Oil and grease are loosely attached and absorb laser energy well, so when using a 500W laser cleaning machine, the cleaning speed can reach 10-15㎡/hour. This faster cleaning speed can meet the needs of many production sites for high-efficiency cleaning, but the specific effect will still be affected by the thickness of the contaminant and the absorption characteristics of the material.
In general, different equipment, process parameters and surface conditions will affect the actual speed of laser cleaning. Therefore, it is recommended that companies adjust the laser power, scanning speed and pulse parameters according to the specific working conditions, target materials and pollutant types when selecting laser cleaning equipment, so as to achieve the best working efficiency while ensuring the cleaning quality. Through reasonable parameter optimization, the cleaning speed can be improved and unnecessary damage to the substrate can be avoided, thus achieving efficient and environmentally friendly surface treatment effects.
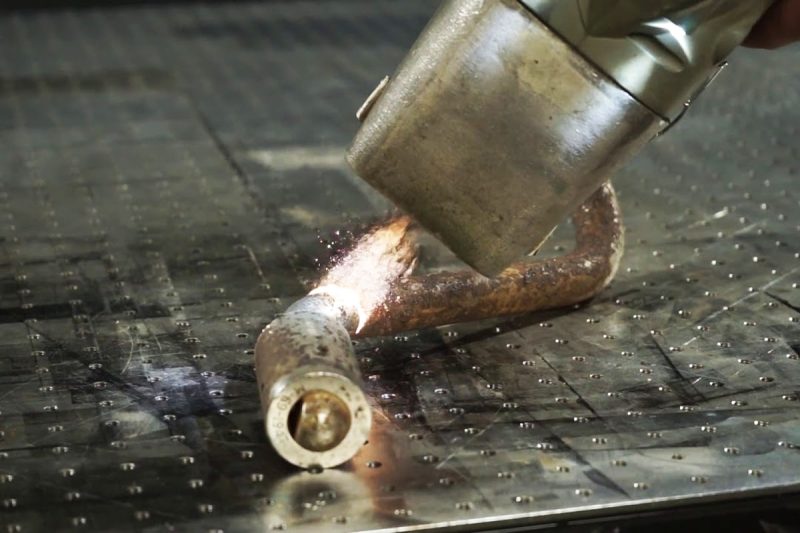
Methods to improve laser cleaning speed
To improve cleaning efficiency, companies can optimize the laser cleaning process from multiple angles. Here are some effective speed-up measures:
- Optimize laser power: It is crucial to choose laser equipment with appropriate power. Appropriate laser power can not only ensure sufficient energy output and quickly remove contaminants, but also ensure that energy consumption and cleaning efficiency are balanced. Excessive power may cause overheating or damage to the substrate, while insufficient power will prolong the cleaning time. Therefore, according to the specific cleaning object and the degree of contamination, adjusting the laser power can protect the workpiece while increasing the cleaning speed.
- Adjust pulse duration and frequency: Laser pulse parameters have a direct impact on the cleaning effect. By shortening the pulse duration and increasing the pulse frequency, the energy of each laser acting on the surface of the workpiece can be concentrated and transmitted instantly, thereby stripping the contamination layer more efficiently. At the same time, adjusting these two parameters according to the absorption characteristics of the material can help to further increase the cleaning speed and reduce the thermal impact on the substrate while ensuring the cleaning quality.
- Improve beam transmission and spot size: Optimizing the optical system, improving the beam transmission path, and focusing methods can effectively improve the utilization rate of laser energy. A reasonably designed optical system can focus the laser into a spot of appropriate size, so that the laser has higher energy density and uniformity during the cleaning process, thereby speeding up the cleaning process and ensuring the consistency of the cleaning effect.
- Enhanced scanning system: The use of high-speed scanning galvanometers or other high-precision scanning equipment can make the laser beam move quickly on the surface of the workpiece and cover a larger area. The enhanced scanning system not only increases the cleaning speed but also ensures that each area is evenly irradiated by the laser, avoiding missed scans or repeated cleaning, thereby achieving efficient and uniform cleaning effects.
- Optimized motion system: In large-area cleaning applications, equipped with precise and stable motion control systems (such as CNC platforms or automated robots) can ensure that the laser head runs smoothly along the preset trajectory. Precise motion control not only ensures stable coverage of the laser beam but also maintains a constant speed when working on a large area, thereby effectively shortening the overall cleaning time.
- Improved cooling system: During laser cleaning, high-energy laser output generates a lot of heat, which can easily cause the equipment to overheat and affect working stability. By optimizing the cooling system (such as using efficient water cooling or air cooling solutions), the stable operation of the laser equipment can be maintained, and the laser output parameters can be ensured to be continuously stable, thereby improving cleaning efficiency and extending the service life of the equipment.
- Use advanced control software: Using intelligent control software, the cleaning path and working mode can be automatically optimized by adjusting the laser parameters through real-time monitoring and feedback. Advanced software algorithms can not only dynamically adjust laser power, pulse frequency, and scanning speed according to different working conditions, but also reduce human operation errors, improve overall process efficiency, and achieve automation and refined management.
- Coordination of pre-treatment and post-treatment technologies: In some cases, pre-treatment processes (such as ultrasonic cleaning and chemical-assisted cleaning) can soften or partially remove stubborn contaminants first, making laser cleaning more efficient. Similarly, post-treatment processes can further refine the cleaned surface to improve cleanliness, thereby shortening the cleaning time overall.
- Consider material and contaminant properties: Different substrates have different absorption and thermal conductivity properties for laser energy, and various contaminants (such as rust, paint, and grease) have different physical and chemical properties. By deeply analyzing the material and contaminant characteristics of the workpiece, and selecting and adjusting the most suitable laser parameters, it is possible to speed up the cleaning speed and minimize damage to the workpiece while ensuring thorough cleaning.
By combining the above measures, from laser equipment selection to parameter control, and then to the coordination of automation systems and auxiliary processes, companies can significantly improve cleaning efficiency and achieve a faster, more precise, environmentally friendly, and efficient laser cleaning process.
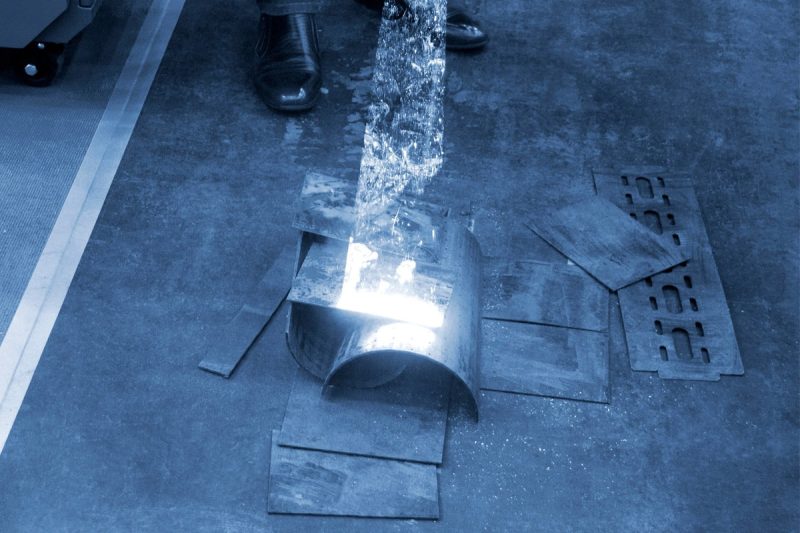
Vantagens da limpeza a laser
Compared with traditional chemical cleaning and mechanical cleaning methods, laser cleaning technology has many advantages:
- Precision cleaning: Laser cleaning can accurately remove specific contamination layers, such as rust, paint, or coating, without damaging the surface of the substrate. This high-precision cleaning method is particularly suitable for industries with strict surface quality requirements, such as aerospace, electronic manufacturing, and precision machining.
- Non-contact process: Unlike traditional mechanical cleaning methods, laser cleaning is a non-contact process. The laser beam does not physically contact the surface being cleaned, reducing the risk of mechanical damage, and is particularly suitable for complex structures or vulnerable parts.
- Environmental protection: No chemical agents are required during laser cleaning, and no hazardous waste is generated. The cleaned waste is usually solid powder, which is small in size and easy to store and recycle, meeting the high environmental protection requirements of modern industry.
- Versatility: Laser cleaning is suitable for a variety of materials, including metals, plastics, ceramics, etc. This versatility makes it widely used in many fields such as automobile manufacturing, mold cleaning, and cultural relics protection.
- Automation and integration: The laser cleaning system can be integrated with industrial robots and production lines to achieve automated cleaning. Through intelligent control, laser cleaning can complete cleaning tasks under high speed and high precision conditions, improve production efficiency, and reduce labor costs.
- Cost-effectiveness: Although the initial investment in laser cleaning equipment may be high, it has significant cost advantages in the long run due to its high efficiency and low maintenance costs. It reduces the use of chemicals and waste disposal costs, while improving production efficiency, bringing considerable economic benefits.
In summary, laser cleaning technology is gradually replacing traditional cleaning methods and becoming an important technology in the field of modern industrial cleaning due to its precision, environmental friendliness, versatility, automation, and cost-effectiveness. With the continuous advancement of technology, the application scope and effect of laser cleaning will be further improved, driving various industries to develop in a more efficient and environmentally friendly direction.
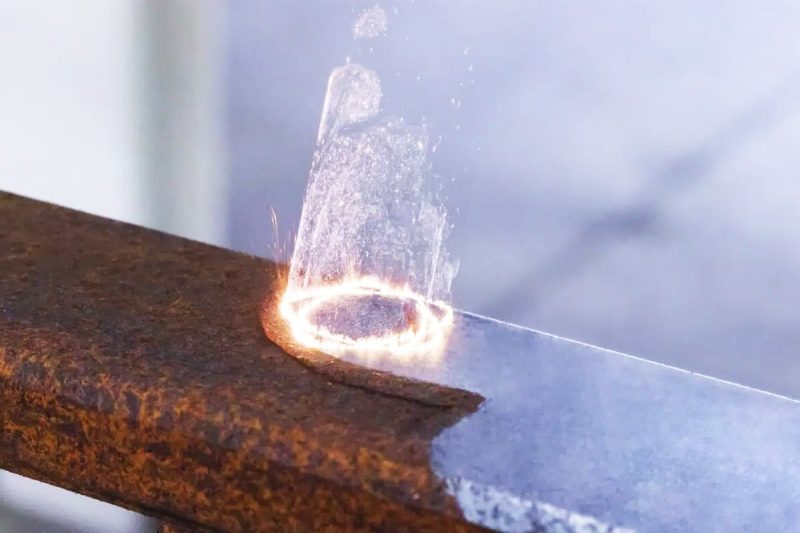
Laser Cleaning Applications
Laser cleaning technology has been widely used in many fields due to its high efficiency, environmental protection, and precision, demonstrating its great potential in industrial upgrading and technological innovation. The following is an extended description of the application in major industries:
- Aerospace industry: In the aerospace field, laser cleaning technology is mainly used for cleaning engine parts and aircraft components. The precise removal of oxide layers and dust on the surface of parts by high-energy lasers can not only restore the original physical properties of the metal but also improve the working efficiency and safety of the engine. At the same time, this technology also performs well in the coating removal and maintenance of aircraft shells, effectively reducing the damage that may be caused to the substrate during traditional cleaning.
- Automobile industry: In automobile manufacturing and maintenance, laser cleaning is widely used in pretreatment before welding and cleaning after welding. Laser can quickly remove oil, rust, and old coatings on the surface of body parts, and ensure the reliability of welding and bonding processes, thereby improving the structural strength and assembly quality of the whole vehicle. In addition, laser cleaning is also often used for regular cleaning of molds to maintain mold precision and extend the service life of equipment.
- Cultural heritage protection: Laser cleaning has irreplaceable advantages in the protection of cultural relics and artworks. Due to its non-contact cleaning method, the laser can finely remove stains and oxides from the surface of sculptures, murals, and historical relics without causing any physical or chemical damage to the precious substrate, thereby effectively protecting the historical and artistic value of cultural heritage.
- Electronics industry: In the electronics industry, laser cleaning technology is mainly used to remove tiny oxides and contaminants on the surface of electronic components before and after welding. Through high-precision cleaning, excellent electrical contact between circuit boards and components can be ensured, and welding quality and overall product performance can be improved. At the same time, this process is also suitable for the maintenance of precision instruments, helping to improve the stability and service life of electronic products.
- Nuclear industry: The nuclear industry has extremely high requirements for equipment cleaning, and laser cleaning technology plays an important role in nuclear facility decommissioning and equipment maintenance. It can efficiently remove radioactive pollutants and other harmful deposits on the surface of nuclear facilities while ensuring safety, avoiding secondary pollution caused by the use of chemical cleaning agents, and providing reliable guarantees for the safe dismantling and environmental governance of nuclear facilities.
- Manufacturing and processing: In traditional manufacturing and modern processing industries, laser cleaning technology is mainly used for metal surface treatment, mold cleaning, and maintenance of precision instruments. Removing rust, paint, and other contaminants on the metal surface, can not only improve the accuracy of subsequent processing but also extend the service life of equipment and molds, significantly improving production efficiency and product quality.
In summary, laser cleaning technology is gradually replacing traditional cleaning methods with its significant advantages such as precision, non-contact, environmental protection, versatility, and easy automation integration, helping various industries to achieve more efficient, safer, and more sustainable production and maintenance processes.
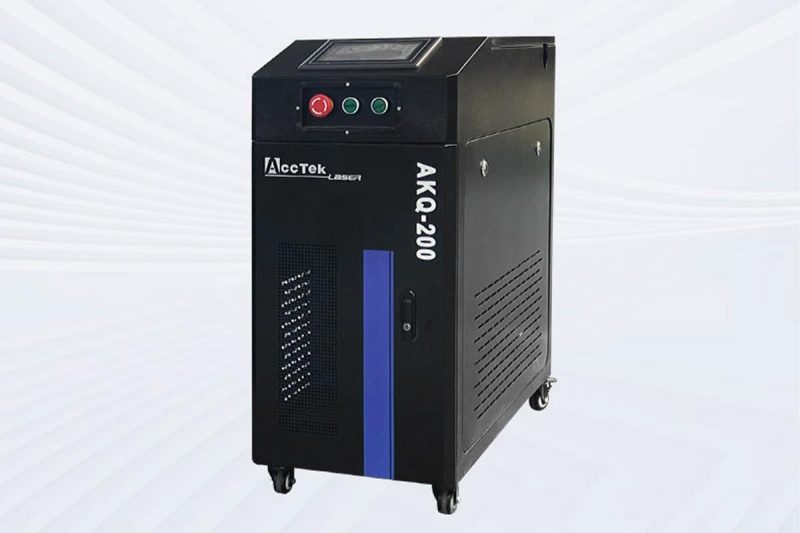
Resumir
As an efficient and environmentally friendly industrial cleaning method, laser cleaning technology has been widely used in many industries. Its cleaning speed is affected by many factors, including laser power, beam quality, material type, etc. Depending on the application, the cleaning speed can reach 6-15m2 per hour, and the efficiency can be further improved by optimizing parameters and systems. With its advantages of high precision, non-contact, automation, and environmental protection, laser cleaning is becoming an indispensable surface treatment solution for modern manufacturing.
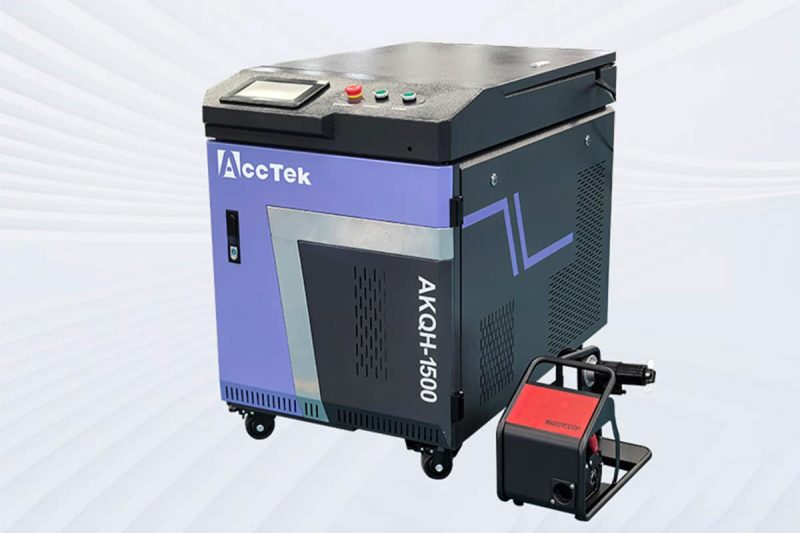
Obtenha soluções de limpeza a laser
If you are looking for an efficient laser cleaning machine, AccTek Laser offers a variety of fiber laser cleaning equipment that is suitable for various industrial cleaning needs and helps companies improve production efficiency. Our product lines include:
- Portable laser cleaning machine: suitable for on-site cleaning, easy to operate, and convenient to move.
- High-power laser cleaning machine: used for large-area cleaning, high processing efficiency, suitable for large-scale production lines.
- Laser cleaning and welding all-in-one machine: integrates cleaning and welding functions, saves space, and improves work efficiency.
For more product information or professional solutions, please visit AccTek Laser’s official website or contact us directly. Our team will provide customized laser cleaning solutions based on your specific needs to help your business development.
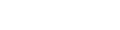
Informações de contato
- [email protected]
- [email protected]
- +86-19963414011
- No. 3 Zona A, Zona Industrial de Lunzhen, Cidade de Yucheng, Província de Shandong.
Obtenha soluções a laser