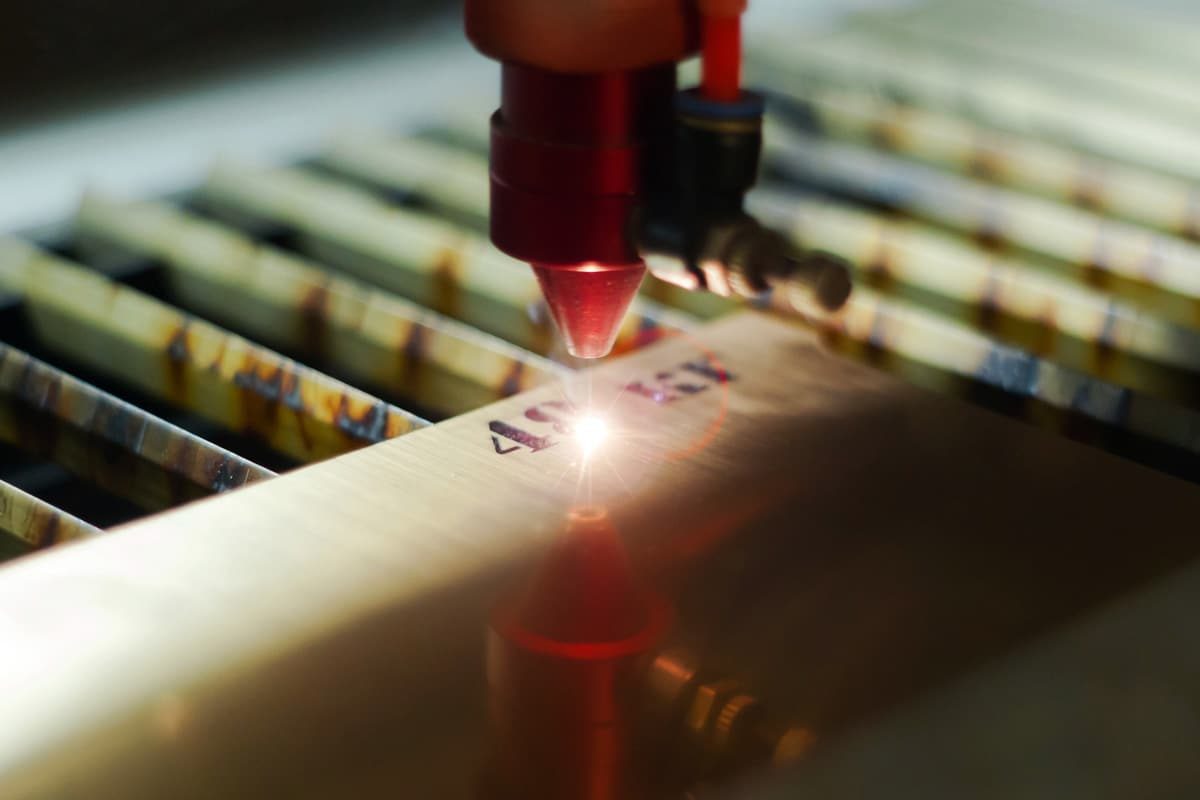
Como obter alto contraste na marcação a laser
Como um método de marcação eficiente e preciso, a marcação a laser é amplamente usada em muitas indústrias, especialmente na fabricação de eletrônicos, dispositivos médicos, peças automotivas, aeroespacial, joias, embalagens e outros campos. De números de série de produtos, códigos QR, logotipos de marcas a gráficos complexos, a tecnologia de marcação a laser pode obter marcação permanente em uma variedade de materiais. Essa tecnologia se tornou uma parte indispensável da indústria de fabricação moderna com sua alta velocidade, baixo custo e alta precisão sem contato. O contraste é um fator-chave que afeta a qualidade da marcação a laser. O alto contraste não apenas melhora a legibilidade da marca, mas também afeta diretamente o efeito visual do produto e da marca. Seja leitura automática de código de barras, clareza de logotipos de marcas ou marcações industriais complexas, um bom contraste é essencial para garantir a qualidade da marca. Então, como obter alto contraste na marcação a laser? Este artigo explorará as tecnologias relevantes e as melhores práticas em detalhes para ajudá-lo a obter excelentes efeitos de marcação a laser em vários cenários de aplicação.
Índice
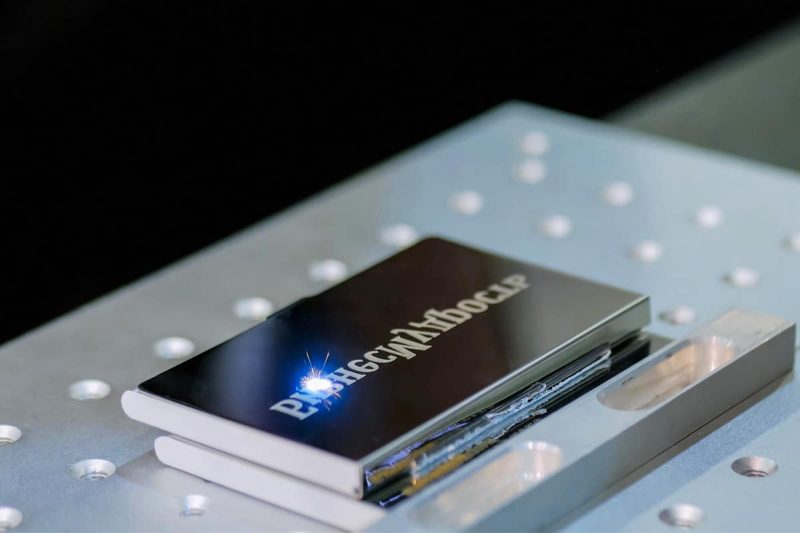
Aprenda sobre a tecnologia de marcação a laser
A tecnologia de marcação a laser tem sido amplamente usada na indústria por seus métodos de marcação sem contato, de alta precisão e diversos. Dependendo do material de marcação e dos requisitos de marcação, a marcação a laser pode ser obtida de várias maneiras, incluindo gravação, recozimento, formação de espuma, ablação e migração de carbono. Cada tecnologia tem diferentes princípios de trabalho e efeitos de marcação, adequados para diferentes cenários de aplicação. Abaixo, exploraremos cada tecnologia de marcação em profundidade para ajudar você a entender suas vantagens e áreas de aplicação.
Gravação
A gravação é uma técnica que usa lasers de alta energia para remover a camada superficial de um material para criar uma marca. A alta temperatura do laser faz com que o material evapore ou derreta, deixando uma marca permanente rebaixada. Essa técnica é frequentemente usada para marcar materiais profundamente ou permanentemente e é adequada para aplicações que exigem durabilidade de longo prazo e resistência ao desgaste.
- Materiais aplicáveis: metal, plástico, cerâmica, madeira, etc.
- Vantagens: A profundidade da gravação é controlável, a marcação é muito resistente ao desgaste e é adequada para peças que trabalham em ambientes agressivos, como peças automotivas e ferramentas.
- Indústrias de aplicação: fabricação automotiva, equipamentos eletrônicos, processamento de metais, joias, identificação de ferramentas, etc.
A tecnologia de gravação é particularmente adequada para marcar materiais duros, como aço inoxidável e ligas de alumínio. Ela pode criar marcas duráveis e claras, garantindo que as marcas ainda sejam legíveis mesmo em condições adversas.
anelamento
A tecnologia de recozimento é usada principalmente para materiais metálicos. O laser aquece a superfície do material, causando uma reação de oxidação na superfície para formar marcas de cores diferentes. Como a camada superficial do material apenas muda de cor sem remover nenhum material, a superfície lisa da marca de recozimento é adequada para aplicações que têm altos requisitos na superfície do material.
- Materiais aplicáveis: aço inoxidável, liga de titânio, cromo e outros materiais metálicos.
- Vantagens: sem danos mecânicos à superfície do material, superfície lisa, adequado para equipamentos médicos e peças de alta demanda.
- Indústrias de aplicação: equipamentos médicos, instrumentos cirúrgicos, peças aeroespaciais, etc.
A vantagem significativa da tecnologia de marcação por recozimento é sua capacidade de fornecer marcas de alto contraste, mantendo a integridade da superfície do material, tornando-a a primeira escolha para indústrias com altos requisitos de desempenho do material.
espumante
A tecnologia de espuma é frequentemente usada para marcação de plástico. O laser aquece a superfície do material, fazendo com que ele vaporize localmente e forme pequenas bolhas. Essas bolhas alteram as propriedades reflexivas do material, criando uma diferença de cor perceptível. A espuma geralmente faz com que a superfície do material fique levemente elevada, adicionando um efeito tridimensional à marca.
- Materiais aplicáveis: materiais não metálicos, como plásticos e borracha.
- Vantagens: A marca de espuma é clara e tem alto contraste, especialmente adequada para materiais plásticos escuros.
- Indústrias de aplicação: componentes eletrônicos, produtos plásticos, embalagens de produtos de consumo, etc.
A marcação de espuma pode atingir marcação óbvia sem alterar a estrutura geral do plástico. É frequentemente usada nos campos de produtos eletrônicos, materiais de embalagem e bens de consumo.
Ablação
A tecnologia de ablação usa lasers de alta energia para remover precisamente revestimentos ou filmes da superfície dos materiais. Ao contrário da gravação, a ablação remove apenas a camada da superfície sem afetar o material subjacente. Essa tecnologia é frequentemente usada para marcação de alta precisão de materiais revestidos, removendo o revestimento da superfície para expor o material subjacente, criando assim um contraste.
- Materiais aplicáveis: metais revestidos, plásticos, vidro, etc.
- Vantagens: Marcação de alta precisão, adequada para aplicações com altos requisitos de aparência e marcação fina.
- Indústrias de aplicação: componentes eletrônicos, invólucros de eletrodomésticos, instrumentos, etc.
A marcação por ablação é adequada para materiais multicamadas, especialmente em aplicações onde o material subjacente precisa ser revelado, como invólucros de produtos eletrônicos, componentes automotivos e marcação de instrumentos de precisão.
migração de carbono
A migração de carbono altera o conteúdo de carbono de um material por meio de lasers, fazendo com que a superfície do material mude de cor e forme uma marca permanente. A migração de carbono é usada principalmente em materiais metálicos, especialmente aqueles que contêm carbono. Ela controla precisamente a energia do laser para redistribuir ou sublimar o elemento de carbono no material, formando uma mudança de cor.
- Materiais aplicáveis: aço carbono, aço inoxidável, titânio e outros materiais metálicos que contenham carbono.
- Vantagens: Pode atingir contraste extremamente alto sem danificar o acabamento da superfície e é particularmente adequado para produtos com altos requisitos de aparência.
- Indústrias de aplicação: dispositivos médicos, joias, produtos de consumo, etc.
A tecnologia de marcação por migração de carbono é amplamente utilizada para marcar ligas de aço inoxidável e titânio, como instrumentos cirúrgicos e artigos de luxo, porque não danifica a superfície do material.
Diferentes tecnologias de marcação a laser oferecem uma ampla gama de opções para diversas aplicações. A tecnologia de gravação fornece marcas profundas e duráveis, a tecnologia de recozimento garante uma superfície de metal lisa enquanto obtém mudanças de cor; a formação de espuma é adequada para materiais plásticos, a ablação é boa no processamento de materiais revestidos e a migração de carbono pode fornecer resultados inigualáveis para marcação de metal de alto contraste. Dependendo do tipo de material e dos requisitos de marcação, escolher o método de marcação apropriado pode melhorar muito a qualidade e a legibilidade das marcações do produto. Na produção industrial, é crucial entender essas tecnologias e fazer escolhas com base em cenários de aplicação específicos.

Compreendendo o contraste na marcação a laser
No processo de marcação a laser, o contraste é um dos fatores importantes que determinam a qualidade da marca. Marcas de alto contraste tornam as informações mais fáceis de identificar e ler, especialmente em aplicações industriais, onde a qualidade do contraste afeta diretamente a eficiência da produção e o desempenho do produto. A seguir detalharemos a definição de contraste na marcação a laser e sua importância em vários setores.
Definição de Contraste
Na marcação a laser, contraste se refere à diferença de claro e escuro entre a parte marcada e a área não marcada ao redor. Especificamente, a cor, brilho ou refletividade da área marcada forma um contraste nítido com a área não marcada, produzindo um efeito visual claro. Quanto maior o contraste, mais clara a marca, o que é crucial para ler ou escanear as informações marcadas.
A geração de contraste depende principalmente dos seguintes aspectos:
- Propriedades da superfície do material: A absortividade e a refletividade de diferentes materiais afetam a interação do laser com o material, afetando assim a cor e a clareza da marca. Por exemplo, a marcação a laser em plástico preto será significativamente diferente do que em plástico branco.
- Parâmetros do laser: potência, frequência de pulso, velocidade de varredura e outros parâmetros afetarão a profundidade da marcação a laser, a mudança de cor e o brilho no material, afetando diretamente o contraste da marca.
- Condições ambientais: temperatura, umidade e outros fatores também podem afetar as propriedades físicas do material e o efeito da marcação a laser.
Seja um código de barras, código QR, texto ou padrão, a marcação clara depende de contraste suficiente. Especialmente na produção industrial, se a marcação é clara está diretamente relacionada à rastreabilidade e legibilidade do produto.
A importância do alto contraste
A marcação a laser de alto contraste não é apenas mais proeminente visualmente, mas também melhora significativamente a eficiência da automação industrial e da identificação manual. Isso é particularmente crítico nos seguintes aspectos:
- Melhor legibilidade e reconhecimento: Marcações de alto contraste tornam as informações visíveis em diferentes luzes, ângulos e distâncias. Especialmente em ambientes industriais complexos, fatores como luz forte, reflexos ou poeira podem afetar a visibilidade de marcações de baixo contraste, enquanto o alto contraste garante fácil reconhecimento mesmo em condições adversas.
- Eficiência de leitura de equipamentos automatizados: Em muitas indústrias, como fabricação de automóveis, produtos eletrônicos, logística e equipamentos médicos, marcas de informação como códigos de barras e códigos QR são geralmente reconhecidas por equipamentos de leitura de código automatizados. Se o contraste da marca for insuficiente, o dispositivo de leitura de código terá mais probabilidade de cometer erros de reconhecimento ou exigir várias varreduras, o que reduzirá a eficiência da produção. Marcações de alto contraste podem reduzir erros de reconhecimento e falhas de leitura, melhorando significativamente a eficiência do equipamento automatizado.
- Garanta a rastreabilidade e a conformidade do produto: Em indústrias de alto padrão, como eletrônicos, automóveis e equipamentos médicos, a rastreabilidade do produto é uma parte importante para garantir a segurança e a qualidade. A marcação a laser é amplamente usada para marcar peças nessas indústrias. As marcações de alto contraste não apenas ajudam a rastrear produtos durante a produção, transporte e uso, mas também garantem que os requisitos das regulamentações da indústria sejam atendidos.
- Melhore a marca e os efeitos visuais: Em alguns campos de bens de consumo, como joias, bens de luxo, capas de celular, etc., a marcação a laser é frequentemente usada para identificação de marca. Marcações de alto contraste não apenas aumentam a estética do produto, mas também melhoram o reconhecimento da marca. Marcações claras e duráveis não apenas destacam a imagem da marca, mas também fornecem aos consumidores uma boa experiência visual.
Exemplos de aplicação na indústria
- Indústria automotiva: A marcação de alto contraste é usada para números de série, datas de produção e números de lote de peças para garantir a rastreabilidade na linha de produção e a precisão da leitura automatizada do código.
- Indústria eletrônica: A marcação a laser de componentes como chips e placas de circuito impresso geralmente requer finura e alto contraste para garantir uma leitura precisa do equipamento em linhas de produção de alta velocidade.
- Indústria de dispositivos médicos: Para instrumentos cirúrgicos e dispositivos médicos, a marcação a laser de alto contraste garante a exclusividade e a rastreabilidade dos produtos, assegurando que eles atendam aos rigorosos requisitos de higiene e qualidade.
- Aeroespacial: Devido a materiais especiais e ambientes adversos, a marcação de alto contraste pode garantir a legibilidade clara das peças durante a produção, instalação e manutenção.
Alto contraste não é apenas um símbolo de qualidade de marcação a laser, mas também um fator importante para garantir a eficiência da produção industrial e a rastreabilidade do produto. Em indústrias com requisitos rigorosos sobre clareza de marcação, obter marcação de alto contraste desempenha um papel insubstituível na melhoria do desempenho do equipamento de leitura de código automatizado, reduzindo erros e garantindo a conformidade do produto. Portanto, selecionar parâmetros e materiais de laser apropriados e otimizar o processo de marcação são etapas importantes para obter alto contraste.
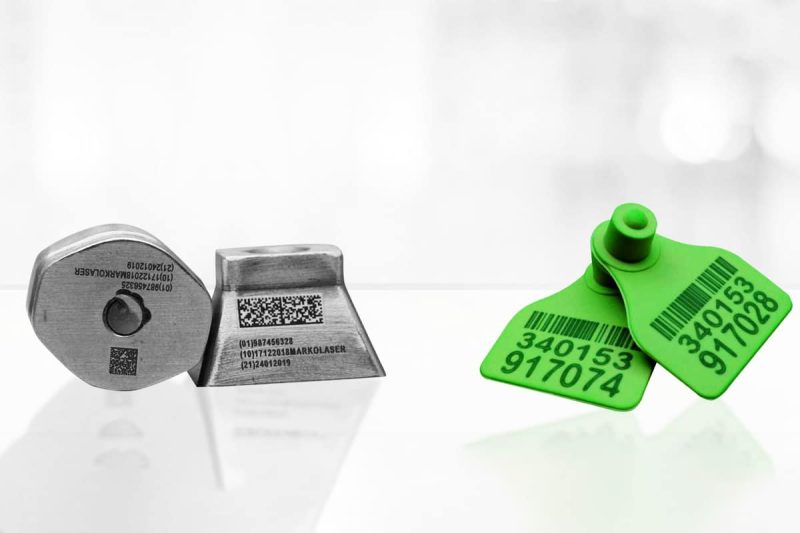
Fatores que afetam o contraste da marcação a laser
O contraste da marcação a laser é afetado por múltiplos fatores, entre os quais as características do material, parâmetros do laser, condições ambientais e preparação da superfície desempenham um papel fundamental. Entender esses fatores e fazer ajustes de otimização de acordo pode melhorar significativamente a clareza e a qualidade de suas marcas. Abaixo, discutiremos em detalhes como obter marcação a laser de alto contraste controlando esses fatores de vários aspectos.
Propriedades do Material
As propriedades físicas e químicas do material têm um impacto direto no efeito da marcação a laser, especialmente ao obter uma marcação de alto contraste. A taxa de absorção do material, a refletividade, a cor da superfície e a condição da superfície são todos fatores-chave.
- Taxa de absorção: A taxa de absorção da energia do laser por um material é um dos principais fatores que determinam o efeito da marcação. Materiais com alta absortividade podem converter energia do laser em energia térmica de forma mais eficiente, resultando em mudanças mais óbvias na superfície do material. Por exemplo, materiais como plásticos, madeira e metais revestidos normalmente têm altas taxas de absorção do laser e, portanto, produzem marcas mais nítidas. Vidro e alguns metais têm taxas de absorção mais baixas e podem exigir maior potência ou comprimentos de onda especiais do laser para atingir o efeito desejado.
- Refletividade: Materiais com alta refletividade, como alumínio, prata e cobre, tendem a refletir a maior parte da energia do laser, fazendo com que o efeito de marcação seja insignificante. Ao marcar esse tipo de material, geralmente é necessário usar um laser de um comprimento de onda específico (como laser de fibra ou laser verde) para garantir absorção de energia suficiente e melhorar o contraste da marcação. O tratamento de superfície adequado ou pré-revestimento também pode ajudar a reduzir a refletividade e melhorar a marcação.
- Cor e composição da superfície: A cor do material também tem um impacto significativo no contraste da marcação a laser. Materiais de cor escura (como plásticos pretos e revestimentos de metal preto) têm mais probabilidade de produzir contraste significativo porque materiais de cor escura geralmente absorvem a energia do laser de forma mais eficiente. Por outro lado, materiais de cor clara, como plástico branco ou metal prateado, podem exigir maior potência do laser ou ajustes de parâmetros mais finos para atingir o contraste ideal.
- Condição da superfície: A suavidade ou aspereza da superfície do material afeta diretamente a interação entre o laser e o material. Superfícies lisas geralmente refletem a luz do laser de forma mais uniforme, resultando em maior contraste, enquanto superfícies muito ásperas podem fazer com que a energia do laser se disperse, reduzindo o efeito da marcação. No entanto, uma superfície moderadamente áspera pode facilitar a absorção da energia do laser, melhorando assim a eficácia da marcação. Isso significa que, dependendo do material e dos requisitos da aplicação, escolher a aspereza correta da superfície também pode ter um impacto positivo na melhoria do contraste.
Parâmetros de laser
Durante a marcação a laser, as configurações de parâmetros do equipamento a laser desempenham um papel importante na qualidade, precisão e contraste da marca. Ao otimizar a potência do laser, velocidade, frequência de pulso e foco, o efeito da marcação pode ser melhorado e o contraste marcado pode ser aumentado.
- Potência: A potência do laser determina a quantidade de energia que ele fornece à superfície do material. Uma potência muito baixa pode resultar em marcação pouco nítida e contraste insuficiente, enquanto uma potência muito alta pode causar queima ou derretimento excessivo do material, ou até mesmo danificar a superfície do material. Para obter uma marcação de alto contraste, a seleção de potência precisa ser ajustada com precisão para garantir que a energia do laser corresponda às características do material, obtendo uma marcação clara sem danificar o material.
- Velocidade: A velocidade na qual a cabeça do laser se move afeta o tempo que o laser atua na superfície do material. Velocidades mais lentas permitem que o laser permaneça na superfície do material por mais tempo, aumentando o acúmulo de energia térmica e, assim, melhorando a profundidade e o contraste da marcação. No entanto, uma velocidade muito lenta também pode fazer com que o material superaqueça e afete a clareza da marca. Portanto, o ajuste de velocidade deve ser considerado em conjunto com a potência para atingir o melhor efeito de marcação.
- Frequência de pulso: A frequência de pulso do laser determina a taxa de repetição do laser, ou seja, o número de pulsos de laser por unidade de tempo. Os pulsos de laser de alta frequência são mais adequados para marcações de padrões delicados e complexos porque podem cobrir mais área em um curto espaço de tempo; enquanto os pulsos de laser de baixa frequência são adequados para marcação profunda. Para obter marcação de alto contraste, escolher a frequência de pulso apropriada pode ajudar a produzir marcas mais uniformes e claras na superfície do material.
- Foco: O foco preciso do laser garante que a energia do laser seja concentrada em uma área específica na superfície do material, alcançando assim a transferência de energia mais eficiente. O foco impreciso pode fazer com que a energia do laser se disperse, afetando a clareza e o contraste da marca. Ao ajustar o foco do laser, você pode garantir que a área marcada obtenha o máximo de energia do laser e melhore o contraste.
Condições ambientais
As condições ambientais também afetam o efeito da marcação durante a marcação a laser. Temperatura, umidade e a limpeza do ambiente de trabalho mudarão as propriedades físicas do material e a eficiência da transmissão de energia do laser, afetando assim o contraste.
- Temperatura: A temperatura ambiente tem um certo impacto nas propriedades físicas dos materiais e na transmissão de energia do laser. Ambientes de alta temperatura podem reduzir a taxa de absorção dos materiais, especialmente em materiais sensíveis ao calor, como plásticos. Altas temperaturas podem fazer com que os materiais amoleçam ou deformem antecipadamente, afetando o efeito da marcação. Portanto, quando a marcação a laser é realizada em um ambiente de alta temperatura, pode ser necessário reduzir a potência do laser ou otimizar outros parâmetros.
- Umidade: A umidade tem um impacto significativo no efeito de marcação a laser de certos materiais, especialmente plásticos e madeira. Um ambiente de alta umidade pode fazer com que o vapor de água se condense na superfície do material, afetando a transmissão de energia do laser e reduzindo a clareza da marca. Para garantir o contraste da marca, em ambientes com alta umidade, é melhor garantir que a superfície do material esteja seca.
- Limpeza: Poeira, graxa, óxidos e outros poluentes na superfície do material interferirão na transmissão de energia do laser, causando dispersão de energia e, portanto, afetando o efeito da marcação. Especialmente para marcação a laser com requisitos de alta precisão, é crucial garantir que a superfície do material esteja limpa. Limpar a superfície do material antes da marcação a laser pode melhorar significativamente o contraste da marca.
Preparação da superfície
Antes da marcação a laser, a preparação da superfície do material afetará diretamente a qualidade e o contraste da marca final. Limpeza razoável da superfície, ajuste de rugosidade e pré-tratamento necessário ajudam a garantir que a energia do laser seja transferida eficientemente para a superfície do material e produza marcas claras.
- Limpeza: A superfície do material deve ser completamente limpa antes da marcação para remover poeira, graxa, camadas de óxido ou outros contaminantes que podem afetar o efeito da marcação a laser. Usar solventes, escovas ou equipamentos de limpeza ultrassônica pode ajudar a garantir que a superfície esteja livre de qualquer resíduo, melhorando assim o contraste da marcação a laser.
- Rugosidade da superfície: A rugosidade adequada da superfície pode ajudar o material a absorver melhor a energia do laser, especialmente em materiais altamente refletivos. Aumentar a rugosidade da superfície pode reduzir a refletividade e, assim, melhorar o efeito de marcação. No entanto, para aplicações que exigem superfícies lisas, como dispositivos médicos de alta precisão ou componentes eletrônicos, é necessário garantir a suavidade da superfície para melhores resultados de marcação.
- Pré-tratamento: Alguns materiais podem exigir pré-tratamento para garantir o melhor desempenho do efeito de marcação a laser. Por exemplo, materiais metálicos podem ser polidos ou revestidos, e materiais plásticos podem ser tratados com tratamento químico de superfície. Essas etapas ajudam a melhorar a absorção de energia do laser pela superfície do material, obtendo assim maior contraste.
Os fatores que afetam o contraste da marcação a laser são complexos e variados, incluindo as características do material, os parâmetros do equipamento a laser, as condições ambientais e a preparação da superfície. Ao ajustar esses fatores de forma direcionada, o contraste da marcação a laser pode ser efetivamente melhorado para garantir que o efeito da marcação seja claro e durável. Isso pode não apenas atender aos requisitos de rastreabilidade e identificação na produção industrial, mas também obter melhores efeitos visuais em aplicações como identificação de marca.
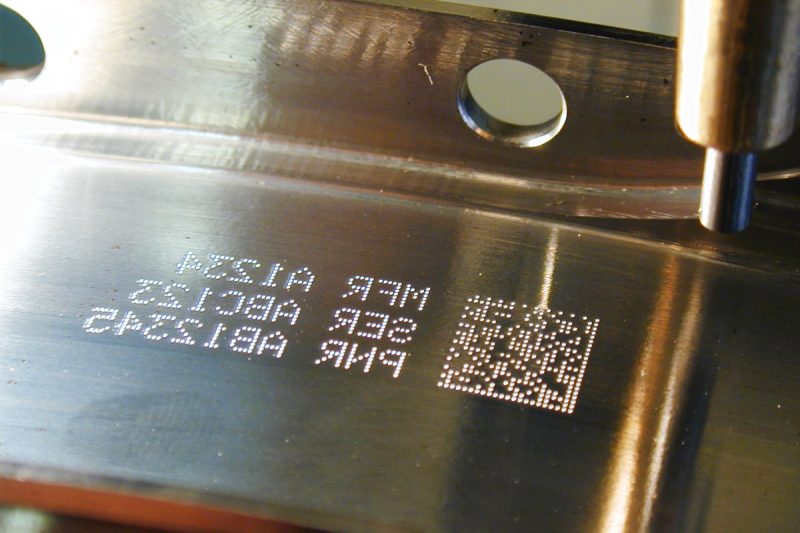
Sete práticas essenciais para obter alto contraste
Para atingir alto contraste na marcação a laser, uma série de melhores práticas precisa ser adotada, desde a seleção do tipo de laser até o controle ambiental e a aplicação da tecnologia de pós-processamento. Por meio de operação e ajuste razoáveis, efeitos de marcação claros e duráveis podem ser obtidos em diferentes materiais.
Escolha o tipo de laser certo
O comprimento de onda do laser tem diferentes taxas de absorção para diferentes materiais, então escolher o tipo certo de laser é crucial. Os geradores de laser de fibra são adequados para materiais metálicos como aço inoxidável, alumínio e cobre, e podem produzir marcas claras. Os lasers de CO2 são mais adequados para plásticos, materiais orgânicos e alguns materiais não metálicos como madeira, couro, etc. Escolher um gerador de laser que corresponda às propriedades do material pode garantir maior absorção de energia, melhorando assim o contraste da marcação.
Preparação de Materiais
A preparação da superfície do material tem um impacto direto nos resultados da marcação. A superfície deve estar limpa e plana para que a energia do laser seja distribuída e absorvida uniformemente. Dependendo do material, pode ser necessário um pré-tratamento como polimento, jateamento de areia, limpeza química, etc. para remover quaisquer impurezas que possam interferir na marcação. Este tipo de preparação ajuda a otimizar o efeito de transmissão do laser e a melhorar o contraste e a clareza da marca.
Otimização de parâmetros do laser
A configuração dos parâmetros do laser é crucial para atingir alto contraste. Parâmetros como potência, velocidade, frequência de pulso, etc. precisam ser ajustados de acordo com as características do material. Geralmente, uma potência maior aumenta a profundidade da marca, mas uma potência muito alta pode causar queimaduras ou processamento excessivo do material. Uma velocidade de marcação mais lenta ajuda a aumentar a interação entre o laser e o material, melhorando assim o contraste. Por meio de uma série de testes experimentais, as configurações do laser mais adequadas para diferentes materiais podem ser encontradas para garantir o melhor efeito de marcação.
Condições ambientais controladas
A temperatura, umidade e limpeza do ambiente afetarão a estabilidade da marcação a laser. Temperatura ou umidade excessivas podem alterar as propriedades físicas do material, o que por sua vez afeta a eficiência de absorção e condução do laser. Manter condições ambientais constantes, especialmente ao marcar a laser em materiais sensíveis à umidade, pode garantir resultados de marcação consistentes. Limpe a área de trabalho regularmente para evitar poeira ou impurezas que interfiram no processo de marcação para garantir qualidade de marcação de alto contraste.
Instalações e movimentação de materiais
Durante o processo de marcação, o material deve permanecer estável e imóvel. Qualquer movimento leve resultará em marcações pouco claras ou erros. Usar fixações de alta precisão e fixações de material pode garantir a estabilidade e consistência da posição de marcação, evitando processamento repetido ou marcações borradas. Especialmente ao marcar grandes áreas ou padrões complexos, uma fixação estável pode melhorar a qualidade geral da marcação.
Software e Sistemas de Controle
Os sistemas modernos de marcação a laser são equipados com software de controle altamente inteligente que pode ajudar a gerenciar com precisão a potência de saída do laser, o caminho e a velocidade de marcação. O uso adequado dessas funções pode atingir o ajuste automático de parâmetros e melhorar a eficiência operacional. Além disso, o software também pode registrar as melhores configurações de parâmetros para diferentes materiais para facilitar as operações subsequentes e garantir que cada marcação possa atingir o contraste ideal.
Tecnologia de Pós-Processamento
Em alguns casos, o pós-processamento após a marcação a laser pode melhorar ainda mais o contraste. Por exemplo, superfícies de metal podem ser oxidadas ou pulverizadas com uma camada protetora para melhorar o efeito da marcação. Às vezes, uma etapa de limpeza pós-marcação também pode ajudar a remover resíduos do processo de marcação, tornando a marca mais clara e durável. Essas técnicas de pós-processamento podem ser usadas de forma flexível de acordo com diferentes materiais e cenários de aplicação para melhorar a qualidade geral da marcação a laser.
A marcação a laser de alto contraste pode ser obtida selecionando o tipo certo de laser, ajustando parâmetros, controlando condições ambientais e usando técnicas de pós-processamento. Essas melhores práticas ajudarão a melhorar a clareza e a durabilidade da marca e garantirão que a marca tenha um bom desempenho em uma variedade de materiais.
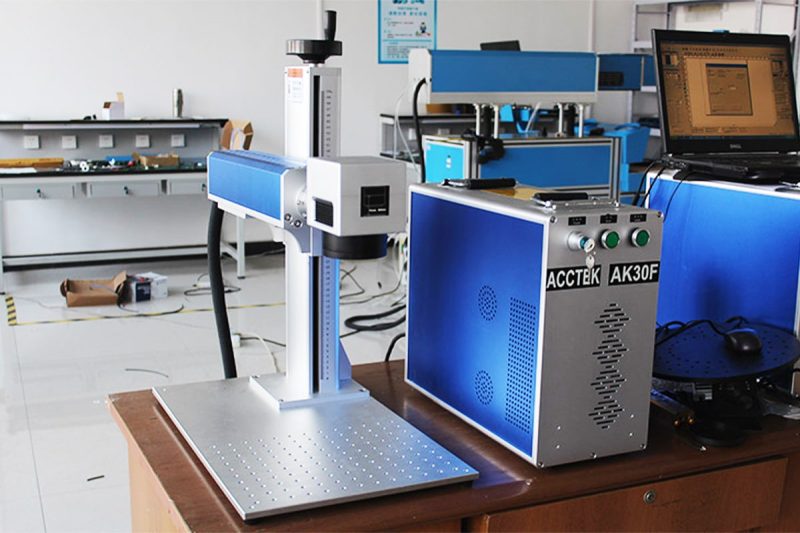
Resumir
Para obter marcação a laser de alto contraste, é necessário considerar uma variedade de fatores, como materiais, parâmetros do laser e ambiente. Ao selecionar adequadamente o tipo de laser, otimizar as configurações de marcação e manter a limpeza do material, as empresas podem melhorar muito a qualidade da marcação e trazer efeitos de marcação mais bonitos e práticos.
Em termos de preparação de material, diferentes materiais têm diferentes absorções e refletividades, portanto, escolher o gerador de laser certo é essencial. máquina de marcação a laser de fibra fornecido pela AccTek é particularmente adequado para materiais metálicos, como aço inoxidável e alumínio, enquanto a máquina de marcação a laser de CO2 é mais adequada para plásticos e materiais orgânicos. O pré-tratamento adequado de acordo com as características do material, como polimento e limpeza, pode garantir que a energia do laser seja absorvida uniformemente e o contraste da marcação seja mais claro.
Ajustar os parâmetros do laser é igualmente importante. Ao marcar, nosso equipamento a laser suporta ajuste de parâmetros flexível e pode encontrar as configurações mais adequadas com base em potência, velocidade e frequência. Seja uma marca profunda em metal ou uma marca superficial em plástico, efeitos de alto contraste podem ser garantidos. Mesmo para materiais altamente refletivos, a máquina de marcação a laser de fibra da AccTek pode lidar facilmente com isso.
Controlar as condições ambientais também é uma etapa que não pode ser ignorada. Manter o ambiente de marcação seco e limpo pode efetivamente evitar que poeira ou umidade afetem o efeito da marcação. Nosso equipamento tem bom desempenho em vários ambientes industriais e tem forte estabilidade, ajudando as empresas a obter resultados de marcação consistentes sob diferentes condições. Nas operações diárias, nossas máquinas de marcação a laser são simples em design e fáceis de manter. Ao usar nossas máquinas de marcação a laser de forma razoável, os clientes podem obter uma marcação rápida e precisa e melhorar a qualidade geral e a imagem da marca do produto. Por meio desses esforços, não apenas o produto pode ficar mais bonito, mas também os clientes podem se interessar por nossas soluções de marcação a laser, promovendo assim o crescimento dos pedidos.
Se você estiver interessado em nossas máquinas de marcação a laser, sinta-se à vontade para entrar em contato conosco para saber mais sobre soluções personalizadas adequadas ao seu negócio.
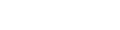
Informações de contato
- [email protected]
- [email protected]
- +86-19963414011
- No. 3 Zona A, Zona Industrial de Lunzhen, Cidade de Yucheng, Província de Shandong.
Obtenha soluções a laser