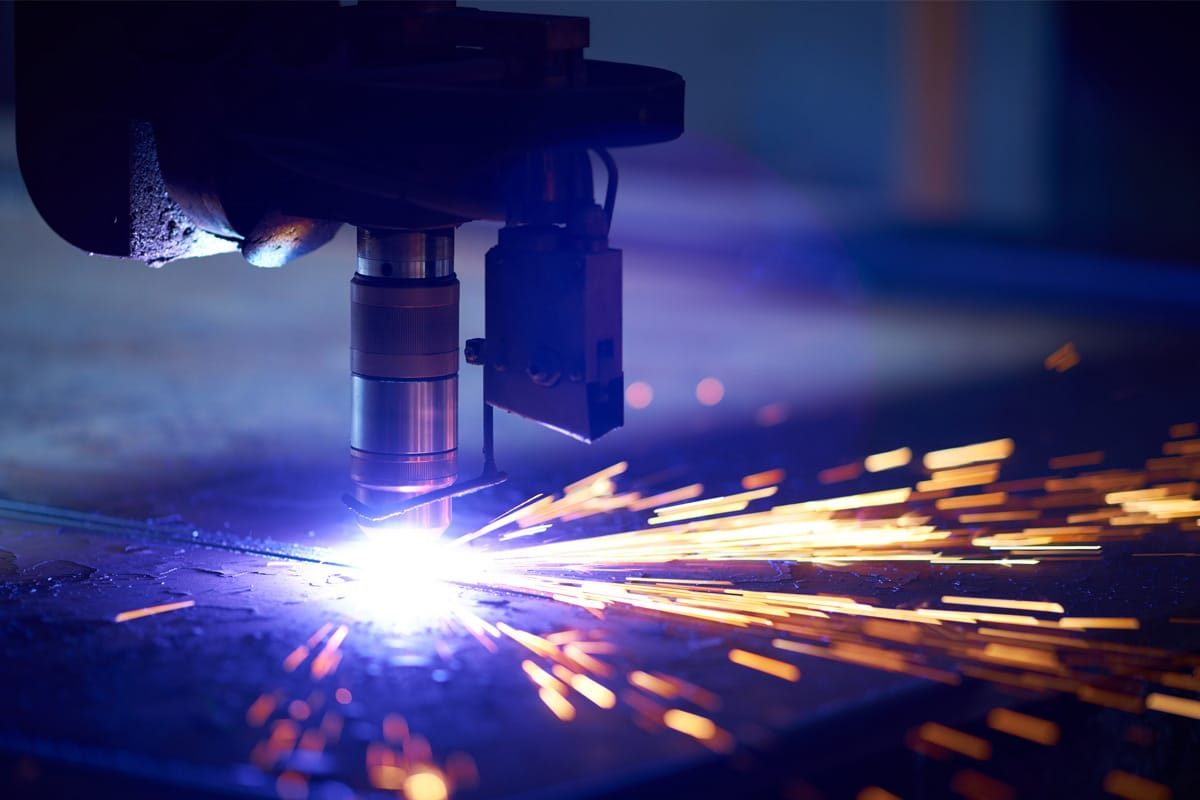
Problemas comuns e soluções para corte a laser de fibra
A tecnologia de corte a laser de fibra é amplamente usada no corte e processamento de vários materiais metálicos e não metálicos devido à sua alta eficiência, alta precisão e operação flexível. Ela usa um feixe de laser de alta potência para irradiar a superfície da peça de trabalho para derretê-la ou vaporizá-la, obtendo assim um corte preciso da peça de trabalho. No entanto, em aplicações práticas, o corte a laser de fibra também enfrenta alguns problemas e desafios comuns, como qualidade de corte reduzida, baixa eficiência de corte e perda rápida de equipamento. Entender e lidar com esses problemas pode não apenas estender a vida útil do equipamento, mas também melhorar a eficiência da produção e a qualidade do processamento.
Índice
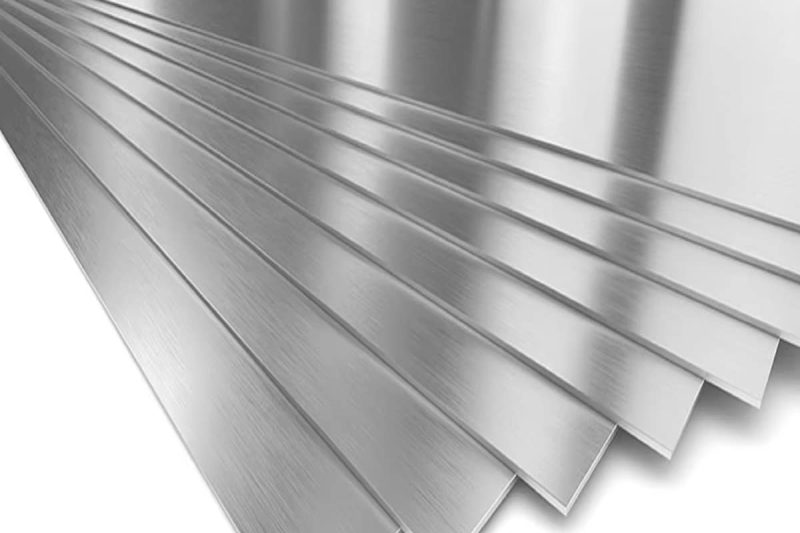
Desafios relacionados a materiais
Refletividade e Condutividade
Quanto melhor a condutividade do material, menor a taxa de absorção da energia do laser. Por exemplo, ouro, prata, cobre, alumínio e outros materiais têm boa condutividade e baixa absorção de energia, o que também pode ser dito para refletir o comprimento de onda do laser. Portanto, quanto maior a condutividade do metal, maior sua refletividade.
Desafio
- Alta refletividade: Metais como alumínio e cobre têm alta refletividade. Especialmente quando o feixe de laser incide em um ângulo próximo ao normal da superfície do material, a maior parte da energia do laser será refletida para o gerador de laser ou sistema de transmissão de laser, o que não apenas reduz a eficiência do processamento, mas também pode causar danos ao equipamento de laser, como queimar a lente ou a fibra óptica.
- Absorção de energia insuficiente: Devido à alta refletividade, a energia efetiva do laser absorvida pela superfície do material é reduzida, resultando em profundidade de processamento insuficiente, velocidade de corte lenta ou qualidade de processamento abaixo do padrão.
Solução
- Use lasers de alta potência: Aumentar a potência do gerador de laser pode aumentar diretamente a energia do laser irradiada para a superfície do material. Mesmo que parte da energia seja refletida, a energia restante é suficiente para um processamento eficiente. Selecione um gerador de laser com uma largura de pulso e frequência adequadas para materiais específicos para otimizar a transferência de energia e os efeitos do processamento.
- Tecnologia antirreflexo: Ao ajustar a forma e o ângulo de divergência do feixe de laser, a energia do laser é distribuída de forma mais uniforme na superfície do material, reduzindo o problema de reflexão local excessiva. Use elementos ópticos ajustáveis dinamicamente (como espelhos deformáveis ou moduladores de luz espacial de cristal líquido) para corrigir a distorção da frente de onda do feixe de laser em tempo real, melhorar a qualidade de foco do feixe de laser e reduzir a reflexão e a dispersão. Alguns metais têm características de reflexão diferentes para lasers em diferentes estados de polarização. Ao ajustar a direção de polarização do laser, a perda de reflexão pode ser reduzida.
- Otimizar o tratamento da superfície do material: aplicar um revestimento ou filme que absorva energia do laser na superfície do material para aumentar a taxa de absorção da energia do laser e reduzir a refletividade. Aumentar a rugosidade da superfície do material por meio de pré-tratamento mecânico, químico ou a laser, melhorar a dispersão e absorção da energia do laser e reduzir a reflexão direta. Formar uma camada de absorção na superfície do material ou alterar suas propriedades químicas da superfície para aumentar a taxa de absorção do laser.
- Ajuste os parâmetros de processamento: Otimize o ângulo de incidência do feixe de laser para evitar que o feixe de laser seja incidente diretamente perpendicular à superfície do material para reduzir a reflexão especular. Ajuste a velocidade, potência, distância focal e outros parâmetros do processamento do laser para encontrar as melhores condições de processamento para garantir a qualidade e eficiência do processamento.
Deformação e empenamento de materiais
A deformação do material é causada pela deformação, que é causada pelo estresse residual dentro do material e é distribuída de forma desigual ao longo da largura e do comprimento do material.
Desafio
Durante o processo de corte a laser, o aquecimento local pode causar deformação do material, especialmente em materiais de chapa fina. Isso ocorre porque o laser concentrará uma grande quantidade de energia térmica em uma pequena área durante o corte, fazendo com que a temperatura da área aumente rapidamente, causando assim expansão e contração térmica do material e, finalmente, fazendo com que o material se deforme e entorte.
Solução
- Ajuste a potência do laser: Reduzir a potência do laser pode reduzir a concentração de calor, reduzindo assim a deformação térmica do material.
- Otimize a velocidade de corte: aumentar adequadamente a velocidade de corte pode reduzir o tempo de residência do laser no material e reduzir o acúmulo de calor.
- Use gás auxiliar: Selecionar um gás auxiliar adequado (como nitrogênio ou oxigênio) e ajustar sua vazão pode remover efetivamente o calor gerado durante o processo de corte e reduzir a deformação do material.
Espessura do material
No processo de corte a laser de fibra, a espessura do material afetará diretamente a qualidade do corte, a eficiência e o desempenho da máquina. Materiais mais finos são mais fáceis de cortar, com maior velocidade e maior precisão, mas materiais mais grossos podem resultar em bordas de corte ásperas ou exigir maior potência e gás auxiliar.
Desafio
Ao cortar materiais mais grossos, o laser demora mais para penetrar no material, o que pode facilmente levar a um corte irregular. Materiais grossos têm baixa condutividade térmica e o calor não é facilmente dissipado, resultando em escória e superfícies de corte irregulares na aresta de corte.
Solução
- Escolha a potência do laser apropriada: Escolha a potência do laser apropriada de acordo com a espessura do material para garantir que a energia do feixe seja concentrada na área de corte para obter o melhor efeito de corte.
- Ajuste os parâmetros de corte: incluindo parâmetros como velocidade de corte, posição focal e pressão do gás auxiliar para garantir a estabilidade e uniformidade do processo de corte.
- Corte múltiplo: para materiais particularmente espessos, vários métodos de corte podem ser usados, cortando uma parte da espessura de cada vez, cortando camada por camada, para reduzir o acúmulo de calor e problemas de corte irregular.
Por meio dos métodos acima, os problemas de alta reflexão de material, empenamento, deformação e corte irregular de materiais espessos durante o corte a laser podem ser resolvidos de forma eficaz, e a qualidade e a eficiência do corte podem ser melhoradas.
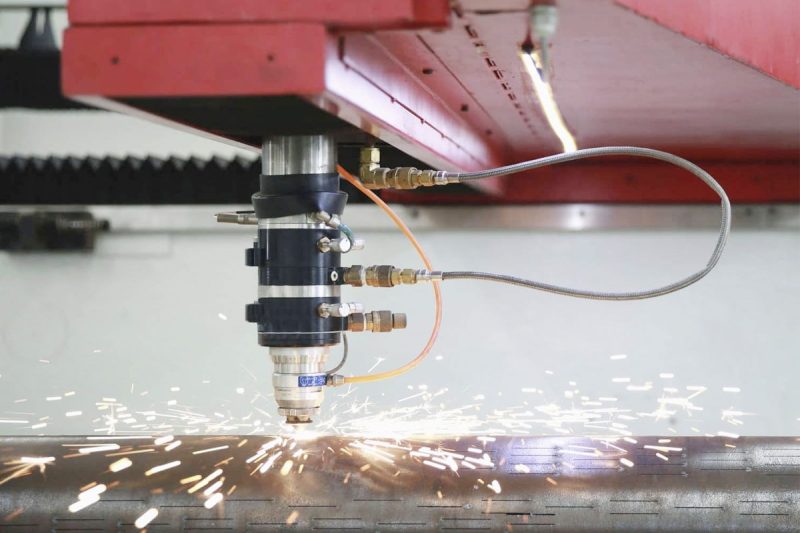
Qualidade da aresta e largura do corte
A suavidade da borda cortada e a quantidade de rebarbas são essenciais para avaliar a precisão do corte. Se a energia do laser for distribuída de forma desigual ou a velocidade de corte não for apropriada, a borda pode parecer áspera ou com rebarbas. A largura da fenda depende da estabilidade do foco do laser. Se o foco for instável ou a potência do laser flutuar, a largura da fenda pode variar de forma inconsistente, afetando a precisão do corte.
Bordas ásperas e rebarbas
Desafio
- Durante o corte a laser, se a energia for irregular ou a velocidade de corte for muito rápida ou muito lenta, a aresta de corte frequentemente terá rebarbas e irregularidades. Especialmente quando a saída de potência do feixe de laser é instável, a superfície do material cortado pode ser superaquecida localmente ou derretida de forma irregular, resultando em bordas ásperas.
- Para alguns materiais metálicos (como alumínio, aço inoxidável, etc.), a distribuição irregular de calor induzirá estresse térmico, o que leva à formação de rebarbas.
- Além disso, o uso inadequado de gás auxiliar (fluxo de ar insuficiente ou pressão inadequada) também afetará a eficiência de descarga do material fundido e aumentará o número de rebarbas.
Solução
- É essencial otimizar as configurações de potência do laser e a velocidade de corte. Certifique-se de que a potência do laser seja alta o suficiente e a saída seja estável para manter uma distribuição uniforme do calor na superfície do material. Ao mesmo tempo, a velocidade de corte precisa ser ajustada de acordo com a espessura e as características do material, nem muito rápida (para evitar corte insuficiente do material) nem muito lenta (para evitar derretimento excessivo).
- Usar o gás de assistência correto, como nitrogênio ou oxigênio, pode melhorar os resultados de corte e garantir uma superfície de corte limpa e suave. O nitrogênio é frequentemente usado para evitar oxidação e reduzir rebarbas nas bordas, enquanto o oxigênio ajuda a aumentar a eficiência de corte e a velocidade de derretimento.
Variação da largura da fenda
Desafio
- O principal motivo para largura de fenda inconsistente geralmente está relacionado à instabilidade do foco do laser ou à flutuação da potência do laser. Quando o foco do laser é deslocado, a concentração de energia mudará de acordo, resultando em flutuações na largura da fenda. Se a potência do laser for instável, a flutuação de saída de energia afetará diretamente a precisão do corte e causará mudanças na largura da fenda.
- Além disso, contaminação ou danos aos componentes ópticos também podem causar alterações na qualidade do feixe, afetando assim a uniformidade da linha de corte. O desgaste das partes mecânicas do equipamento, como trilhos-guia e rolamentos, também afetará a precisão do movimento do cabeçote do laser, resultando em fendas inconsistentes.
Solução
- Verifique e faça a manutenção regular do sistema óptico para garantir foco e energia do laser estáveis.
- Limpe ou substitua lentes ópticas contaminadas para evitar refração ou dispersão desnecessárias durante a transmissão do feixe.
- Calibre regularmente o foco e a potência de saída do equipamento laser para garantir sua precisão durante a operação.
- Faça a manutenção das peças mecânicas do equipamento para garantir o movimento suave e desobstruído do cabeçote do laser para reduzir erros de corte causados pelo desgaste mecânico.
Em resumo, ao definir corretamente os parâmetros e fazer a manutenção regular do sistema óptico, a qualidade da borda pode ser efetivamente melhorada e a largura do corte pode ser controlada.
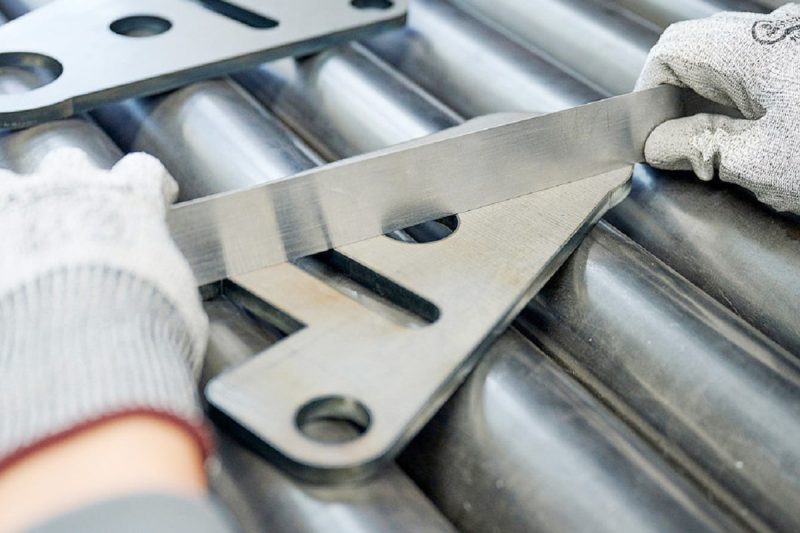
Desafios relacionados ao processo
Os desafios relacionados ao processo envolvem principalmente problemas técnicos que podem ser encontrados durante o processo de corte a laser de fibra. Os desafios comuns relacionados ao processo incluem acúmulo de escória, que é um desafio comum no processo de corte a laser de fibra, especialmente ao cortar materiais mais espessos ou difíceis de cortar. Normalmente, o acúmulo de escória é causado pela falha do material em derreter ou evaporar completamente, ou um suprimento insuficiente de gás auxiliar para soprar o material fundido para longe da área de corte a tempo.
Acumulação de escória
Desafio
- Quando a energia do laser é insuficiente ou o foco do feixe de laser é deslocado, a superfície do material não consegue atingir a temperatura para derreter ou evaporar, resultando em algum material permanecendo na aresta de corte. Especialmente no processamento de chapas grossas, a energia do laser precisa ser forte o suficiente para penetrar toda a espessura do material.
- Gases auxiliares como oxigênio ou nitrogênio são frequentemente usados para ajudar a soprar o material fundido para longe da área de corte. Se a pressão do gás for muito baixa e o material fundido não puder ser removido efetivamente, a escória se acumulará na aresta de corte.
- Uma velocidade de corte muito rápida fará com que o laser não continue a atuar na mesma área, o material não derreta completamente ou o gás não consiga expelir o resíduo a tempo, resultando em acúmulo de escória.
Solução
- Certifique-se de que pressão de gás suficiente seja fornecida para ajudar a remover efetivamente o material fundido e evitar o acúmulo de escória. O nitrogênio é adequado para materiais não oxidantes, enquanto o oxigênio pode acelerar a velocidade de corte, mas requer maior pressão de gás.
- Otimize a velocidade de corte de acordo com a espessura e as características do material para garantir que a energia do laser possa atuar totalmente na área de corte. A combinação apropriada de potência do laser e velocidade de corte pode reduzir zonas afetadas pelo calor desnecessárias, evitando assim o problema de derretimento incompleto de materiais.
- Certifique-se de que os componentes ópticos do gerador de laser estejam nas melhores condições e possam produzir de forma estável a potência do laser necessária para garantir a consistência do processo de corte.
Ao ajustar esses parâmetros de forma abrangente, os problemas de acúmulo de escória podem ser reduzidos significativamente, a qualidade do corte pode ser melhorada e o trabalho subsequente de retificação e limpeza pode ser reduzido.
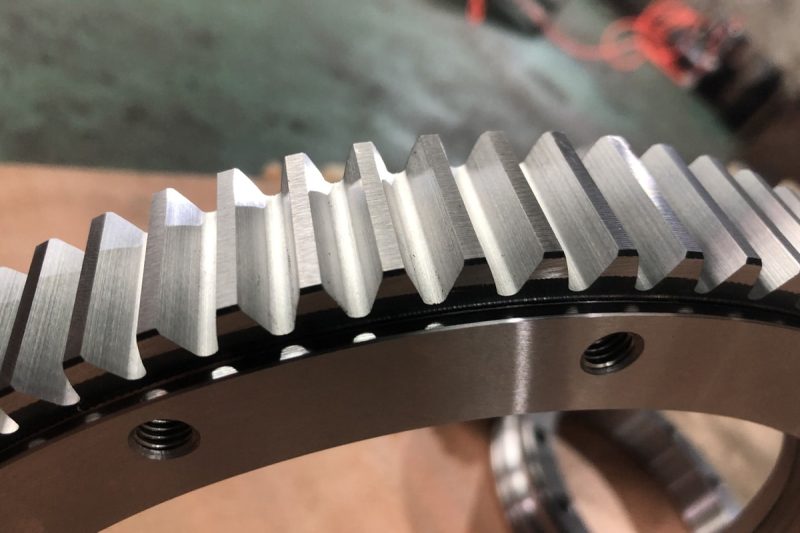
Problemas de perfuração e inicialização
Durante o processo de corte a laser de fibra, problemas de perfuração e inicialização são desafios comuns, especialmente ao lidar com materiais mais espessos ou altamente refletivos. O processo de perfuração é o ponto de partida do corte a laser, e sua estabilidade e eficiência afetam diretamente o efeito de todo o processo de corte. Se o tempo de perfuração for muito longo ou falhar, pode levar ao desperdício de material e desgaste do equipamento, e até mesmo afetar a qualidade do corte. A instabilidade do processo de inicialização levará a fendas irregulares e baixa qualidade da aresta de corte, afetando a precisão e a aparência do produto acabado.
Atrasos e falhas de perfuração
Desafio
Atrasos de perfuração são geralmente causados pelo feixe de laser falhando em focar rapidamente energia suficiente para penetrar o material, resultando em um longo tempo de perfuração. Atrasos de perfuração são especialmente perceptíveis em materiais mais espessos ou materiais refletivos (como alumínio e cobre), e podem até causar falhas de perfuração. Os motivos para falhas de perfuração podem incluir potência de laser insuficiente, foco de laser impreciso, gás auxiliar insuficiente ou seleção de gás inadequada. Isso pode causar inícios de corte irregulares ou com falha, desperdício de material e potencialmente danificar o equipamento de laser.
Solução
- Certifique-se de que a potência do laser possa ser concentrada rapidamente, especialmente em materiais de chapa espessa, onde é necessária mais energia para perfuração. Ajuste o foco do laser para garantir que ele esteja concentrado na superfície do material, reduzindo a dispersão de energia e encurtando o tempo de perfuração.
- Ao perfurar no modo de pulso curto, o superaquecimento e a deformação do material podem ser reduzidos, enquanto a chance de falha de perfuração é reduzida. Esta técnica é particularmente adequada para materiais mais espessos e materiais altamente refletivos.
- O uso de nitrogênio e oxigênio tem um impacto significativo no processo de perfuração. O oxigênio pode acelerar o processo de perfuração, mas pode causar oxidação do material, então o gás e a pressão apropriados precisam ser selecionados com base nas características do material.
- Para materiais muito espessos, técnicas de perfuração multiestágio podem ser usadas, que penetram o material camada por camada em vez de todas de uma vez. Este método pode efetivamente evitar falhas de perfuração e efeitos térmicos excessivos.
Inicialização instável
Desafio
A inicialização instável se manifesta principalmente como largura de corte irregular e baixa qualidade da borda no início do corte a laser, e pode até levar à falha do processo de corte. Isso geralmente é causado por energia laser instável, mudanças na taxa de fluxo de gás, características inconsistentes da superfície do material (como oxidação ou revestimento), etc. Uma inicialização instável pode levar à baixa qualidade de corte na parte inicial, especialmente em aplicações de corte de precisão, essa instabilidade afetará a precisão e a consistência do produto acabado.
Solução
- Antes de começar, a superfície do material pode ser pré-aquecida, especialmente em materiais altamente refletivos. Isso ajuda a reduzir os reflexos do laser e torna o processo de corte mais suave.
- Garanta que o gerador de laser atinja rapidamente um estado estável na inicialização ajustando a taxa de aumento da potência do laser e a taxa de fluxo do gás auxiliar. Isso pode efetivamente evitar flutuações de energia na inicialização.
- Para materiais com camadas de óxido ou outras impurezas na superfície, uma limpeza simples da superfície ou remoção do revestimento pode ser realizada antes da inicialização para reduzir os reflexos do laser e a instabilidade durante o processo de inicialização.
- Use um sistema de monitoramento em tempo real para monitorar o processo de corte, especialmente durante a fase de inicialização, e garanta a estabilidade e a consistência do processo de corte ajustando os parâmetros.
Em geral, ao otimizar os parâmetros do laser, selecionar o gás auxiliar apropriado, usar a tecnologia de perfuração de pulso e pré-processar antes de começar, os problemas de atraso de perfuração, falha e partida instável podem ser significativamente reduzidos, e a eficiência e a qualidade do corte podem ser melhoradas. Essas soluções não apenas melhoram a eficiência operacional, mas também garantem a operação estável de longo prazo do equipamento.
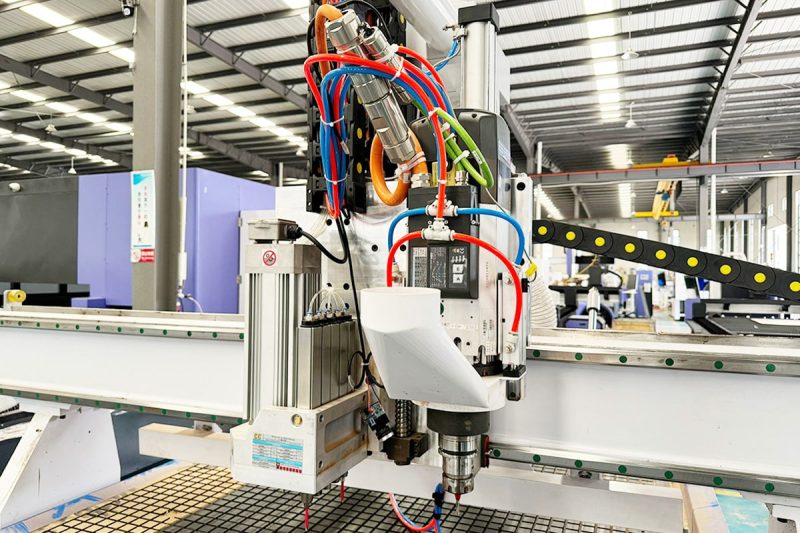
Desafios relacionados a máquinas
No corte a laser de fibra, o desempenho da máquina afeta diretamente a qualidade e a eficiência do corte. O sistema de transmissão do feixe e os componentes mecânicos da própria máquina podem ter vários problemas após o uso a longo prazo, o que afetará a precisão e a estabilidade do corte a laser.
Problemas no sistema de entrega de feixes
Desafio
O sistema de transmissão do feixe é o sistema central que transmite a energia da fonte de laser para a cabeça de corte. Seu desempenho determina diretamente a estabilidade de energia do feixe de laser e a qualidade do corte. Se o sistema de transmissão do feixe não for inspecionado e mantido regularmente, poeira, impurezas ou desgaste mecânico também podem danificar os componentes ópticos, reduzindo ainda mais a eficiência do sistema.
Solução
- Lentes ópticas e lentes em sistemas de corte a laser de fibra são propensas a acúmulo de poeira e óleo. A limpeza regular pode evitar o declínio da eficiência de transmissão do feixe de laser e garantir a estabilidade do feixe.
- Garantir a estabilidade dos conectores de fibra e o alinhamento preciso dos feixes de laser pode reduzir a perda de energia. Verifique as conexões de fibra regularmente para garantir que não haja folga ou desgaste.
- Se ocorrerem problemas frequentes de instabilidade do feixe, considere usar a tecnologia de óptica adaptativa para ajustar o sistema de transmissão do feixe em tempo real e garantir a melhor qualidade do feixe.
- O acúmulo de calor durante a transmissão do feixe afeta a qualidade do feixe, por isso é crucial manter o sistema de resfriamento funcionando efetivamente. Verifique o sistema de resfriamento regularmente para garantir que ele possa dissipar o calor normalmente e reduzir o impacto térmico durante a transmissão do feixe.
Desgaste mecânico
Desafio
Os componentes mecânicos em máquinas de corte a laser de fibra, incluindo trilhos-guia, servomotores e sistemas de acionamento, irão se desgastar gradualmente ao longo do tempo sob uso intensivo. O desgaste mecânico não só causará movimento instável da cabeça de corte, mas também pode afetar a precisão do caminho de corte e, finalmente, a qualidade do produto acabado. Especialmente sob requisitos de corte de alta velocidade e alta precisão, o desgaste mecânico acelerará o envelhecimento do equipamento e aumentará os custos de manutenção e o tempo de inatividade. Além disso, o aumento da vibração e do ruído também são sintomas comuns de desgaste mecânico.
Solução
- Os trilhos-guia e os sistemas de transmissão precisam ser lubrificados regularmente para reduzir o atrito e estender a vida útil das peças mecânicas. Ao mesmo tempo, o sistema de lubrificação deve ser verificado para garantir sua operação normal e evitar desgaste excessivo das peças devido à lubrificação insuficiente.
- Se os trilhos-guia, engrenagens ou outras peças estiverem desgastadas ou deslocadas, as peças danificadas devem ser substituídas a tempo para garantir a precisão e a estabilidade da máquina.
- Em operações de alta precisão, a vibração pode prejudicar a precisão do corte. Ao instalar dispositivos antivibração ou otimizar a posição de instalação da máquina, o impacto da vibração em peças mecânicas pode ser reduzido, retardando assim o desgaste.
- Moderno máquinas de corte a laser de fibra pode ser equipado com um sistema de monitoramento para monitorar o status das peças mecânicas em tempo real, prever possíveis falhas com antecedência por meio da análise de dados e evitar paradas repentinas causadas por desgaste mecânico.
Por meio da manutenção regular e otimização do sistema de transmissão do feixe e dos componentes mecânicos, o desempenho e a estabilidade da máquina de corte a laser de fibra podem ser significativamente melhorados, garantindo a continuidade e a alta qualidade do efeito de corte.
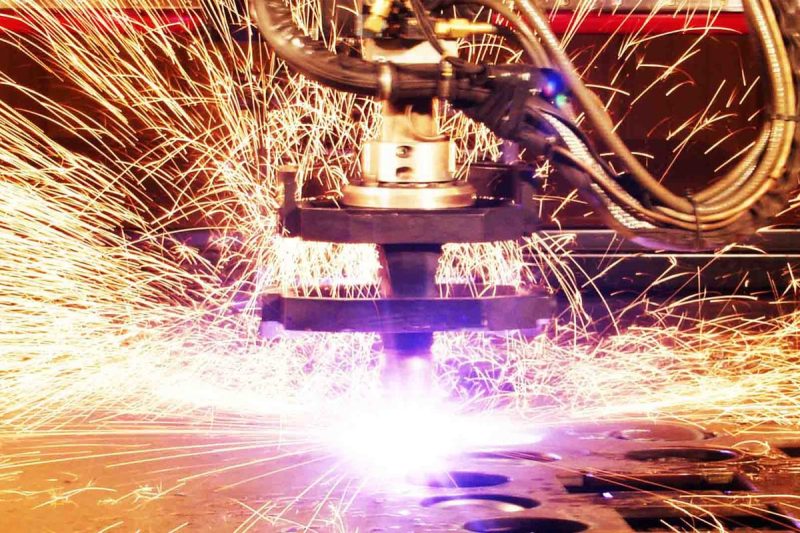
Desvio cônico e angular
Desvio de ângulo e conicidade são dois desafios comuns de precisão no processo de corte a laser de fibra. Problemas de conicidade geralmente se manifestam como larguras superiores e inferiores inconsistentes da borda de corte, enquanto desvio de ângulo se refere à falta de perpendicularidade entre o feixe de laser e o material, resultando em uma superfície de corte inclinada. Esses problemas afetam a qualidade e a aparência da peça de trabalho final, especialmente em tarefas de corte de alta precisão.
Cone
Desafio
O fenômeno de afunilamento geralmente ocorre ao cortar materiais grossos e se manifesta como a aresta de corte estreita na parte superior e larga na parte inferior, ou larga na parte superior e estreita na parte inferior. Isso ocorre porque a distribuição de energia do feixe de laser é irregular ao passar pelo material. Quanto maior a profundidade de corte, mais óbvia é a atenuação da energia do laser, resultando em uma diferença nas larguras superior e inferior da aresta de corte. O afunilamento afetará a precisão da peça de trabalho, especialmente no caso de montagem de alta precisão. O afunilamento causará dificuldades de montagem e até mesmo descartará a peça de trabalho. Além disso, a pressão de gás auxiliar inadequada e a potência instável do laser também agravarão o fenômeno de afunilamento.
Solução
- Problemas de conicidade podem ser efetivamente reduzidos otimizando a profundidade e a posição do foco do laser. Posicionar o foco no meio do material em vez de na superfície ajuda a manter uma distribuição uniforme da energia do laser por toda a espessura do corte.
- Para materiais mais espessos, usar um gerador de laser de maior potência pode manter uma saída de energia mais estável durante o processo de corte e reduzir problemas de conicidade causados pela atenuação do laser.
- A conicidade pode ser reduzida ajustando adequadamente a pressão do gás auxiliar, mantendo a área de corte limpa e resfriando efetivamente a aresta de corte. Especialmente no corte de material espesso, o papel do gás auxiliar é crucial.
- Qualquer pequeno problema com o sistema óptico causará distribuição desigual de energia do feixe de laser. Portanto, a manutenção e limpeza regulares dos componentes ópticos para garantir a qualidade do feixe de laser podem reduzir efetivamente a conicidade.
Desvio angular
Desafio
Desvio angular refere-se à falta de verticalidade do feixe de laser em relação ao material, resultando em uma aresta de corte inclinada. Isso pode ser causado por instalação instável do cabeçote do laser, alinhamento incorreto do feixe ou precisão insuficiente do sistema mecânico. O desvio angular fará com que a superfície de corte da peça de trabalho fique irregular, afetando a precisão e a aparência, especialmente quando a peça de trabalho precisa ser cortada em ângulos retos.
Solução
- Garantir que o cabeçote do laser esteja firmemente montado e perpendicular ao material é o primeiro passo para resolver o problema de desvio de ângulo. A calibração regular do cabeçote do laser e do sistema mecânico garante que o feixe de laser sempre mantenha o ângulo correto durante o corte.
- Velocidade de corte, potência de saída e configurações de gás auxiliar afetam o desvio do ângulo. Ao otimizar esses parâmetros, o feixe de laser pode ser mantido estável durante o corte, reduzindo assim o desvio do ângulo.
- A óptica adaptativa pode ajustar o caminho de propagação e o foco do feixe de laser em tempo real para garantir que o ângulo correto com o material seja sempre mantido durante o corte, reduzindo assim o desvio do ângulo.
- Fatores externos, como mudanças de temperatura e umidade e vibrações, podem afetar a precisão do ângulo do corte a laser. O desvio do ângulo pode ser reduzido ainda mais mantendo a estabilidade do ambiente de corte, como redução de vibração, controle de temperatura e umidade, etc.
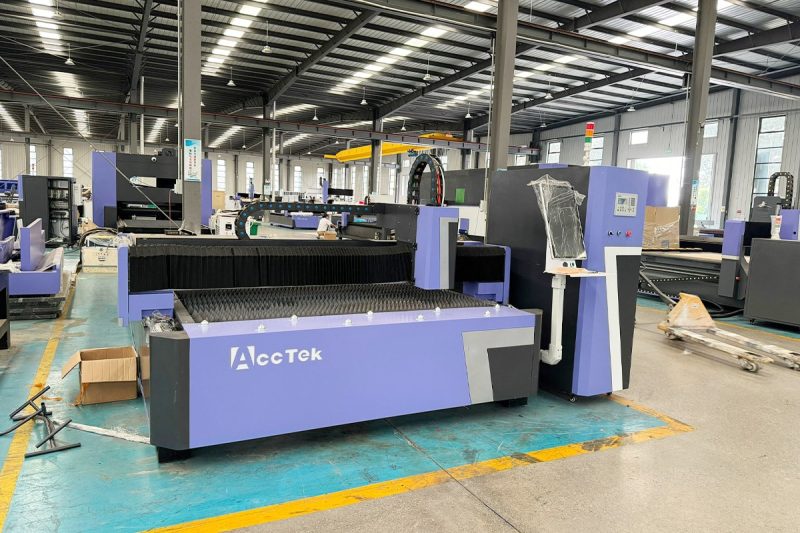
Fatores Ambientais
Fatores ambientais têm impacto direto na estabilidade e qualidade do processo de corte a laser de fibra. Flutuações na temperatura e umidade, bem como mudanças na qualidade do ar, podem impactar negativamente o desempenho do sistema a laser, a qualidade do corte e a vida útil da máquina. Entender e controlar esses fatores ambientais pode garantir que o equipamento opere da melhor forma possível, reduzindo falhas desnecessárias e requisitos de manutenção.
Flutuações de temperatura e umidade
Desafio
Flutuações de temperatura e umidade são um grande desafio no processo de corte a laser. O gerador de laser e o sistema óptico são muito sensíveis a mudanças de temperatura e umidade. Por exemplo, uma temperatura muito alta pode fazer com que o gerador de laser superaqueça, afetando a qualidade e a estabilidade do feixe de laser; enquanto uma temperatura muito baixa pode fazer com que o gerador de laser não atinja a temperatura operacional necessária, afetando assim a saída de energia. Uma umidade muito alta pode causar condensação nos componentes ópticos, afetando a eficiência de transmissão do feixe de laser e até mesmo danificando os dispositivos ópticos. Uma umidade muito baixa pode aumentar o risco de eletricidade estática, o que pode interferir na operação normal dos componentes eletrônicos.
Solução
- Para lidar com flutuações de temperatura e umidade, é recomendado instalar sistemas de controle ambiental especializados, como ar condicionado e equipamento de desumidificação na oficina de corte. Esses sistemas podem manter temperatura e umidade constantes na oficina para garantir que o equipamento a laser funcione em condições ideais.
- Instale sensores de temperatura e umidade ao redor do equipamento de corte para monitorar as condições ambientais em tempo real. Uma vez que uma anormalidade é detectada, o sistema de controle ambiental pode ser ajustado automaticamente, ou o processo de corte pode ser suspenso se necessário para evitar danos ao equipamento.
- Em um ambiente seco, aumente a umidade do ar para reduzir o risco de eletricidade estática e use pisos antiestáticos e medidas de aterramento do equipamento para garantir uma operação segura.
Qualidade do ar
Desafio
O impacto da qualidade do ar no processo de corte a laser não pode ser ignorado. Poeira, névoa de óleo e outros poluentes suspensos no ar podem entrar no sistema óptico ou na área de corte do gerador de laser, afetando a transmissão e o foco do feixe de laser. Poluentes no ar também podem reagir com o feixe de laser durante o processo de corte, resultando em resultados de corte ruins ou até mesmo danos à superfície da peça de trabalho. Além disso, a exposição prolongada ao ar de baixa qualidade aumentará a frequência de manutenção da máquina e encurtará a vida útil do equipamento.
Solução
- Instale um sistema de purificação de ar na oficina de corte a laser para filtrar partículas e poluentes no ar para garantir ar limpo. Especialmente ao cortar certos materiais (como plásticos e madeira), esses materiais podem liberar gases nocivos durante o processo de corte a laser, então um sistema de purificação de ar eficaz é particularmente importante.
- Mesmo com um sistema de purificação de ar, ainda é necessário limpar o sistema óptico do gerador de laser regularmente. Remova a poeira e os poluentes que podem se acumular para garantir a qualidade do feixe de laser e o efeito de corte.
- Em alguns equipamentos ou áreas importantes, medidas de proteção de pressão positiva podem ser adotadas, ou seja, ao introduzir ar filtrado, a pressão do ar na área é mantida mais alta que a externa para evitar a entrada de poluentes.
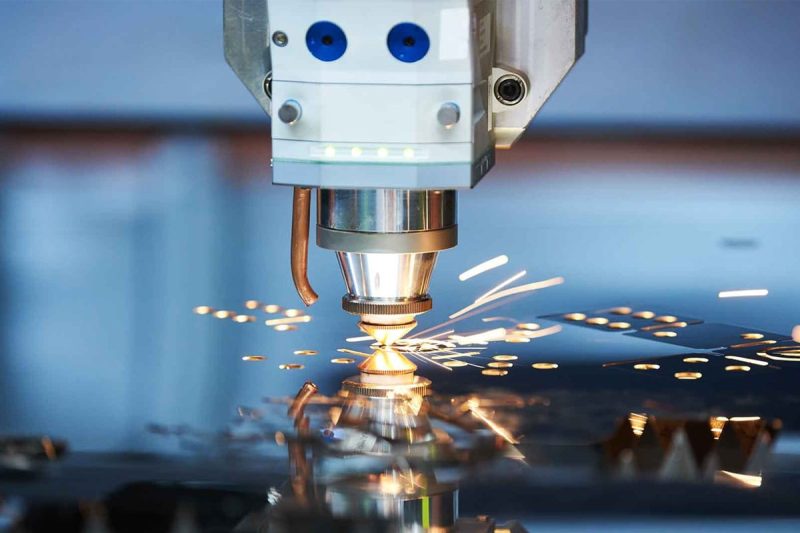
Desafios relacionados ao operador
Além dos fatores ambientais, o nível de habilidade e a eficiência do trabalho do operador também afetam diretamente a qualidade e a eficiência do corte a laser de fibra. A falta de treinamento e experiência, ou fluxo de trabalho ineficiente, pode levar à operação inadequada, aumento das taxas de erro e até mesmo danos ao equipamento ou acidentes de segurança. Portanto, melhorar o profissionalismo do operador e otimizar o fluxo de trabalho são elos importantes para garantir a qualidade do corte e a eficiência da produção.
Falta de treinamento e experiência
Desafio
O corte a laser de fibra é uma tecnologia de alta precisão que exige que os operadores tenham alto conhecimento e habilidades profissionais. No entanto, em algumas empresas, os operadores podem não ter treinamento suficiente e não conseguem entender e dominar completamente a complexidade do corte a laser. Essa situação pode fazer com que os operadores não consigam responder efetivamente quando confrontados com problemas técnicos ou peças de trabalho complexas, o que pode afetar a qualidade do corte, aumentar o desgaste do equipamento e até mesmo causar riscos à segurança. Além disso, a manutenção e o cuidado do equipamento exigem habilidades e conhecimentos específicos. A falta de conhecimento do operador pode fazer com que o equipamento não seja mantido e cuidado prontamente, encurtando a vida útil do equipamento.
Solução
- As empresas devem fornecer treinamento sistemático para os operadores, incluindo os princípios básicos do corte a laser, guia de operação do equipamento, solução de problemas e soluções para problemas comuns, etc. Por meio de treinamento regular, garanta que os operadores sempre dominem as tecnologias e especificações operacionais mais recentes.
- Estabeleça um sistema de certificação de operação para operadores, e somente pessoal certificado pode operar equipamentos de corte a laser. Isso não apenas melhora o senso de responsabilidade do operador, mas também garante a qualidade e a segurança da operação.
- Forneça forte suporte técnico aos operadores, como a criação de um departamento especial de consultoria técnica ou a contratação de especialistas técnicos para orientação regular e ajuda aos operadores a resolver problemas nas operações diárias.
Fluxo de trabalho ineficiente
Desafio
A eficiência do fluxo de trabalho afeta diretamente a eficiência geral da produção e a qualidade do corte a laser. Em algumas empresas, devido ao design de fluxo de trabalho irracional ou coordenação insuficiente, os operadores podem gastar muito tempo alternando tarefas, depurando equipamentos ou manuseando materiais. Esse fluxo de trabalho ineficiente não apenas desperdiça tempo e recursos, mas também pode causar fadiga do operador e aumentar a possibilidade de erros. Além disso, se a empresa não otimizar o fluxo de trabalho prontamente, à medida que o volume de pedidos aumenta, o processo ineficiente se tornará mais proeminente, afetando seriamente a capacidade de produção e a competitividade corporativa.
Solução
- Ao analisar e avaliar o fluxo de trabalho atual, podemos identificar gargalos e links ineficientes e fazer otimizações direcionadas. Por exemplo, podemos organizar a ordem das tarefas de forma razoável, reduzir o tempo para comissionamento de equipamentos e manuseio de materiais e melhorar a eficiência do trabalho.
- A introdução de tecnologias de automação, como sistemas automáticos de carga e descarga e software de composição inteligente, pode reduzir significativamente o tempo e os erros de precisão das operações manuais e melhorar a eficiência do fluxo de trabalho geral.
- Aplique princípios de produção enxuta para reduzir desperdícios e otimizar a alocação de recursos. Por meio de melhoria contínua e participação dos funcionários, podemos estabelecer um fluxo de trabalho eficiente e flexível para garantir a eficiência e a alta qualidade do processo de corte a laser.
Ao abordar esses desafios ambientais e relacionados ao operador, as empresas podem melhorar muito a eficiência e a qualidade do corte a laser de fibra, ganhando assim uma vantagem na competição de mercado.
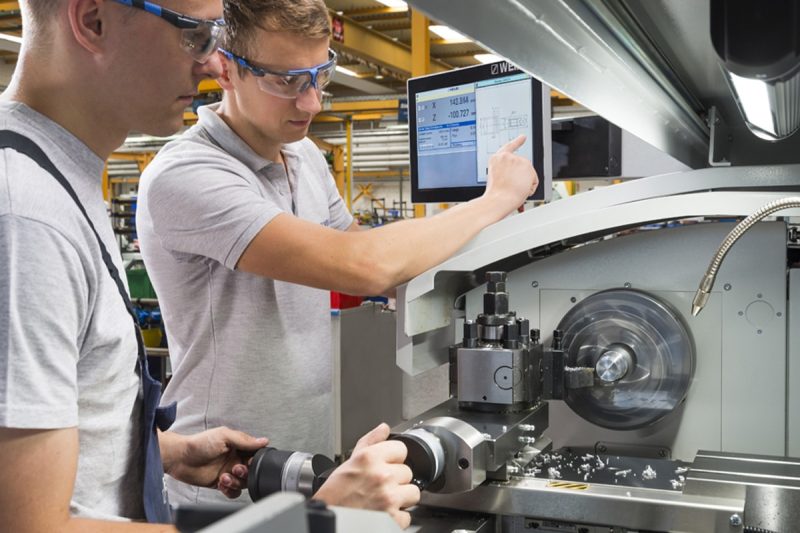
Precauções e Melhores Práticas
Para garantir a operação eficiente contínua do corte a laser de fibra, é essencial tomar medidas preventivas e melhores práticas. Por meio de manutenção regular da máquina, otimização de parâmetros, treinamento do operador e melhoria contínua, as empresas podem reduzir efetivamente as taxas de falha, melhorar a qualidade do corte e estender a vida útil do equipamento.
Manutenção regular da máquina
Desafio
A operação de longo prazo do equipamento de corte a laser pode levar à contaminação de componentes ópticos, desgaste do cabeçote do laser e falha do sistema de resfriamento. Se houver falta de manutenção regular, esses problemas podem afetar o desempenho do gerador de laser, aumentar o tempo de inatividade da produção e até mesmo causar falha do equipamento.
Solução
- Limpe o sistema óptico regularmente para garantir a eficiência da transmissão do feixe de laser.
- Verifique e substitua peças vulneráveis, como bicos de corte, lentes de laser e sistemas de filtro.
- Verifique o sistema de resfriamento regularmente para garantir que ele funcione corretamente e evitar o superaquecimento do gerador de laser.
Otimização de Parâmetros
Desafio
Diferentes materiais e espessuras exigem diferentes potências de laser, velocidades de corte e pressões de gás. Configurações de parâmetros inadequadas podem resultar em redução da qualidade de corte, como aumento de rebarbas ou cortes muito largos ou muito estreitos.
Solução
- Desenvolva tabelas detalhadas de parâmetros de corte para diferentes materiais para garantir a correspondência precisa de potência e velocidade.
- Teste regularmente a saída do laser do equipamento para garantir potência e foco estáveis.
- Use software auxiliar para otimização automatizada de parâmetros para melhorar a eficiência e a qualidade do corte.
Treinamento do Operador
Desafio
A falta de experiência ou habilidade do operador pode levar a erros operacionais, aumentar a taxa de falhas e afetar o efeito de corte.
Solução
- Forneça treinamento técnico aos operadores regularmente para garantir que eles dominem as especificações operacionais do equipamento a laser.
- Forneça manuais detalhados de operação do equipamento e crie uma equipe de suporte técnico para resolver problemas diários.
- Implemente um sistema de certificação de operadores para garantir que somente pessoas qualificadas possam operar o equipamento.
Melhoria Contínua
Desafio
Mudanças rápidas na tecnologia e nos mercados exigem que as empresas otimizem continuamente os processos de produção e as tecnologias para permanecerem competitivas.
Solução
- Introduzir conceitos de produção enxuta, analisar e otimizar continuamente os processos de produção, reduzir o desperdício e melhorar a eficiência.
- Acompanhe a tendência de desenvolvimento da tecnologia de corte a laser e atualize equipamentos e softwares prontamente.
- Colete dados de produção, analise indicadores de desempenho e melhore continuamente os parâmetros de corte e os procedimentos operacionais.
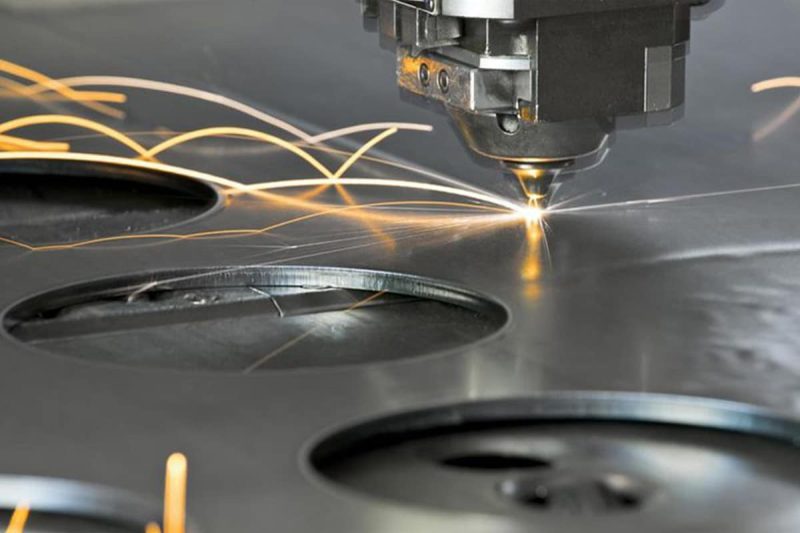
Resumir
Os desafios do corte a laser de fibra envolvem muitos aspectos, incluindo propriedades do material, desempenho do equipamento, condições ambientais, etc. Por meio de manutenção regular, parâmetros otimizados, treinamento aprimorado e uso de tecnologia avançada, a qualidade e a eficiência do corte podem ser significativamente melhoradas. As soluções devem ser implementadas caso a caso para melhorar a estabilidade do processo de corte e reduzir o tempo de inatividade da máquina e os custos de manutenção.
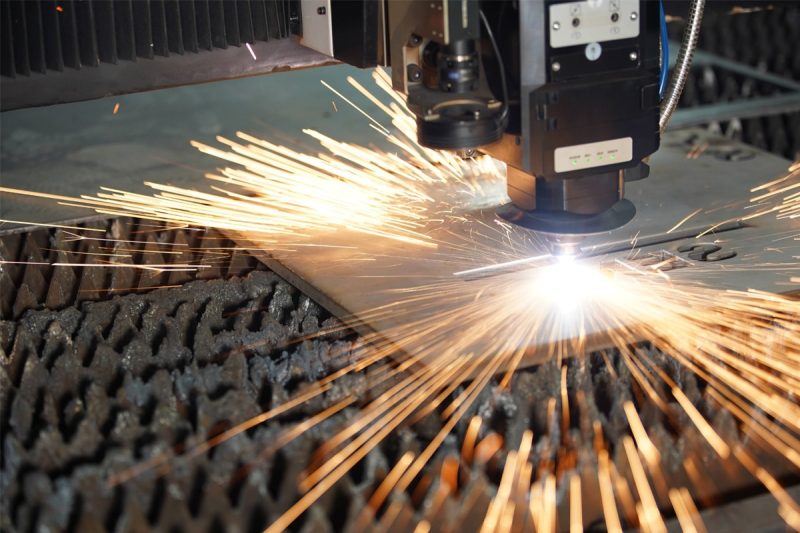
Obtenha soluções a laser
Escolher a máquina de corte a laser de fibra certa pode ajudar a otimizar o consumo de energia e atingir alta eficiência operacional. Trabalhar com um fornecedor confiável garante acesso a tecnologia avançada, consultoria personalizada e suporte contínuo. Na AccTek Laser, oferecemos uma gama abrangente de equipamentos de máquina de corte a laser de fibra projetados para atender a uma variedade de necessidades industriais. Nossos especialistas podem ajudá-lo a escolher o modelo e a configuração mais eficientes em termos de energia, levando em consideração fatores como tipo de material, espessura e volume de produção. Também oferecemos recursos de ponta, como geradores a laser de alta eficiência, sistemas de resfriamento inteligentes e software de gerenciamento de energia para maximizar o desempenho e minimizar o uso de energia. Além disso, nossa equipe fornece serviços de manutenção regular e suporte técnico para manter seu equipamento com eficiência máxima. Ao trabalhar conosco, você pode obter economias significativas de energia, reduzir custos operacionais e aprimorar seus esforços de sustentabilidade. Se você tiver alguma dúvida, entre em contato conosco a tempo, a AccTek Laser está comprometida em fornecer soluções de laser perfeitas para cada cliente!
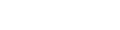
Informações de contato
- [email protected]
- [email protected]
- +86-19963414011
- No. 3 Zona A, Zona Industrial de Lunzhen, Cidade de Yucheng, Província de Shandong.
Obtenha soluções a laser