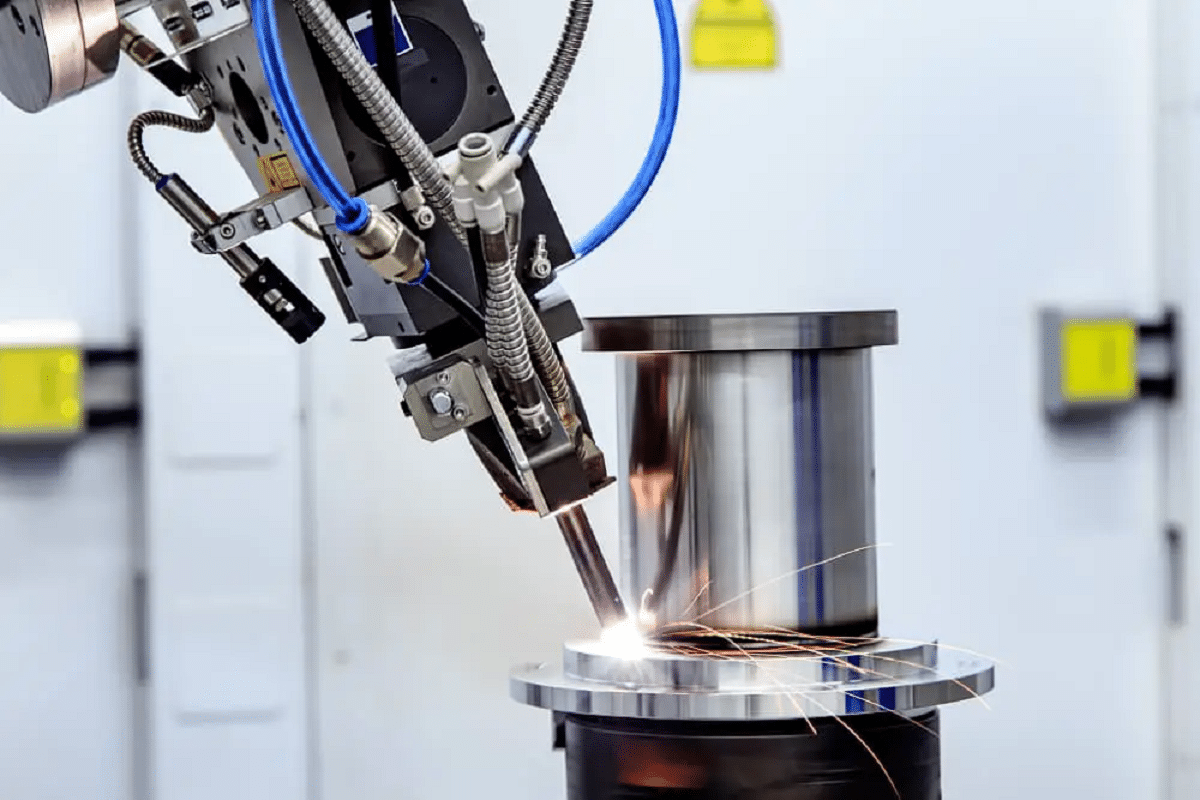
Quais defeitos de soldagem podem ocorrer na soldagem a laser? Como resolver isso?
A soldagem a laser é amplamente utilizada em vários setores devido às suas vantagens de alta eficiência, alta precisão, bom efeito e fácil integração de automação. Desempenha um papel importante na produção e fabricação industrial, incluindo indústrias militares, médicas, aeroespaciais, de novas energias e outras. No entanto, qualquer método de processamento, se os seus princípios e processos não forem devidamente compreendidos, pode produzir defeitos ou produtos defeituosos, e a soldadura a laser não é exceção. Para maximizar o valor da soldagem a laser e produzir um produto de qualidade com aparência impecável, é importante compreender essas armadilhas e aprender como evitá-las.
Índice
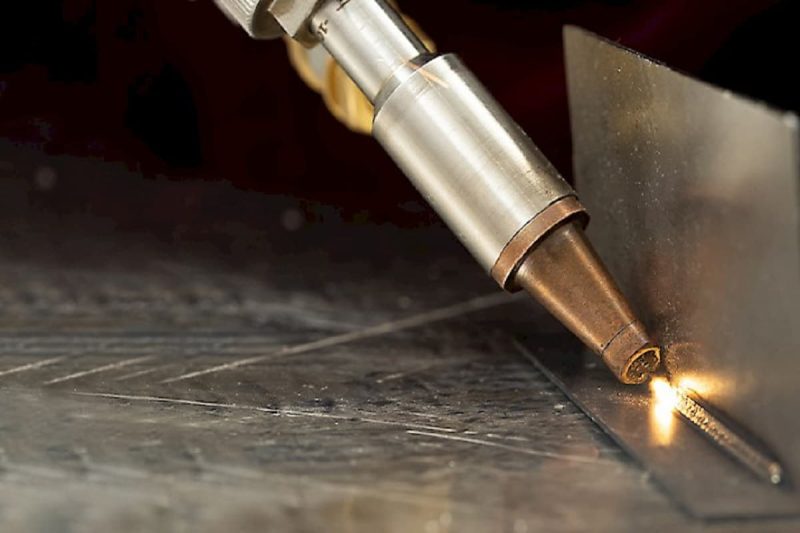
Princípios da soldagem a laser
A soldagem a laser é uma das aplicações importantes da tecnologia de processamento de materiais a laser. A soldagem a laser opera em dois modos fundamentalmente diferentes: soldagem limitada por condução e soldagem de furo profundo. A condução de calor é realizada durante o processo de soldagem, ou seja, a radiação do laser aquece a superfície, e o calor da superfície se difunde para o interior por condução de calor. Ao controlar a largura do pulso do laser, energia, potência de pico e frequência de repetição, fusão do elemento e outros parâmetros, uma poça de fusão específica é formada na superfície do metal. O calor derrete o material para criar um cordão de solda entre as duas superfícies, completando a solda.
A soldagem a laser possui alta precisão e qualidade de soldagem. Como o próprio laser gera muito pouco calor, a costura de solda produzida após a soldagem a laser também é relativamente pequena, o que torna a soldagem a laser especialmente adequada para materiais mais finos, como eletrônicos ou vedações de vidro/metal. Considerando que, ao soldar materiais mais espessos, soldas estreitas e profundas são produzidas entre peças com arestas quadradas. Além disso, o laser pode atingir temperaturas incrivelmente altas (milhares de graus Celsius), portanto, pode produzir soldas muito fortes e duráveis que podem suportar temperaturas extremas e ambientes hostis.
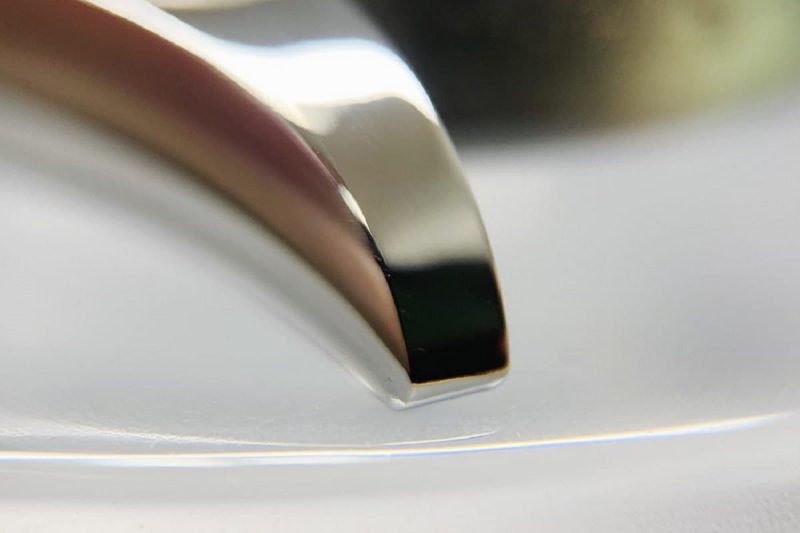
Defeitos de soldagem comuns na soldagem a laser e como resolvê-los
A soldagem a laser tem as vantagens de alta eficiência, alta precisão, bom efeito, fácil automação, integração, etc., mas a operação inadequada também pode levar a sérios defeitos de qualidade nos produtos. Somente compreendendo bem esses defeitos é que o valor da soldagem a laser pode ser aproveitado ao máximo, e produtos com aparência bonita e alta qualidade podem ser processados. A seguir estão 8 defeitos de soldagem que ocorrem frequentemente na soldagem a laser.
Porosidade
Os poros são um dos defeitos mais propensos a ocorrer na soldagem a laser. A porosidade na soldagem a laser pode ser causada pela contaminação da placa ou da superfície ou pré-limpeza insuficiente, como graxa, óleo, óxidos, vapor de água absorvido, resíduos de fluido de corte, etc. é rápido. O gás gerado na poça de fusão líquida não tem tempo de escapar devido à poluição da superfície e é fácil formar poros. No entanto, a soldagem a laser esfria rapidamente e os poros produzidos são geralmente menores do que na soldagem por fusão tradicional.
Para evitar a porosidade na soldagem a laser:
- garantir um gás de proteção adequado: Use um gás de proteção de alta qualidade (geralmente uma mistura de argônio ou hélio) para fornecer proteção adequada contra gases atmosféricos.
- otimize o fluxo de gás: defina o fluxo e a direção do gás de proteção apropriados, para proteger efetivamente a área de soldagem ao máximo.
- Limpe a superfície da peça de trabalho: Limpe completamente a superfície a ser soldada para remover quaisquer contaminantes, como óleo, graxa, ferrugem ou sujeira, para evitar o acúmulo de gás. Use métodos de limpeza apropriados, como limpeza com solvente, limpeza mecânica ou limpeza química, conforme necessário.
- Preparação adequada da junta: Certifique-se de que o encaixe e o alinhamento da junta são adequados para evitar a criação de lacunas onde o gás possa ficar preso. Se aplicável, use técnicas de purga inversa para evitar o aprisionamento de gás.
Corte inferior
Um rebaixo é uma ranhura ou depressão formada na borda de uma solda. Geralmente causado por entrada excessiva de calor ou velocidade de soldagem. Quando a velocidade de soldagem é muito rápida, o metal líquido atrás do pequeno orifício no centro da solda não tem tempo para se redistribuir e solidifica em ambos os lados da solda para formar um rebaixo.
Para evitar rebaixos na soldagem a laser:
- Otimizando os parâmetros do laser: ajuste a potência do laser, a duração do pulso e a posição do foco para obter uma entrada de calor adequada. Evite usar uma potência muito alta ou soldar muito rápido, pois isso pode causar superaquecimento e rebaixamento.
- Mantenha uma velocidade de soldagem consistente: controle o movimento do feixe de laser ou da peça de trabalho para manter uma velocidade de deslocamento constante. Mudanças rápidas de velocidade podem causar distribuição desigual de calor e formação de corte inferior.
- Projeto e encaixe adequados da junta: Assegure a preparação adequada da junta, incluindo encaixe preciso, ângulo de chanfro adequado e tolerância de folga adequada. Manter um ajuste firme ajuda a evitar o derretimento excessivo das bordas e reduz o rebaixo.
Rachaduras de solda
As trincas a quente de soldagem referem-se às trincas geradas na área de alta temperatura quando o metal na solda e na zona afetada pelo calor esfria para perto da linha solidus durante o processo de soldagem. Geralmente pode ser dividido em rachaduras de alta temperatura e rachaduras de baixa temperatura. Durante o processo de soldagem a laser, devido à pequena entrada de calor do laser, a deformação após a soldagem é pequena e a tensão gerada pela soldagem também é pequena, portanto, geralmente não ocorrem rachaduras em alta temperatura. No entanto, devido a diferentes materiais e seleção inadequada de parâmetros de processo, rachaduras de alta temperatura aparecerão na forma de defeitos.
Para evitar rachaduras na solda:
- entrada de calor de controle: otimize os parâmetros do laser para controlar a entrada de calor e reduzir o estresse térmico. Evite o acúmulo excessivo de calor e taxas de resfriamento rápidas, que podem resultar em rachaduras. Isso pode ser alcançado ajustando a potência do laser e a duração do pulso ou usando técnicas de modelagem de pulso.
- Pré-aquecimento e tratamento térmico pós-soldagem: pré-aquecer a peça de trabalho antes da soldagem ajuda a reduzir gradientes térmicos e tensões e melhorar a soldabilidade. Técnicas de tratamento térmico pós-soldagem, como recozimento ou alívio de tensões, também podem ser usadas para aliviar tensões residuais, melhorar as propriedades mecânicas e reduzir o risco de rachaduras.
- Seleção do material de preenchimento: Use um material de preenchimento com composição e ductilidade adequadas para combinar com o material de base para minimizar o risco de rachaduras.
Fusão incompleta ou falta de penetração
A fusão incompleta, ou penetração incompleta, ocorre quando o metal de solda não se funde totalmente com a madeira ou penetra em toda a espessura da junta.
Para evitar fusão incompleta ou não penetrada:
- otimizar os parâmetros do laser: ajuste a potência do laser, a duração do pulso e a posição do foco para obter a fusão e penetração adequadas do material. Uma configuração de potência mais alta ou o ajuste da posição do foco podem ajudar a alcançar uma penetração mais profunda.
- Preparação e montagem da junta: Certifique-se de que o projeto e a montagem da junta são adequados. Ângulos de ranhura, tolerâncias de folga e técnicas de preparação de juntas devem ser selecionados para promover a fusão e penetração adequadas.
- Ajuste a velocidade de soldagem: Ajuste a velocidade de soldagem para permitir entrada de calor suficiente e penetração na junta. A otimização da velocidade de soldagem garante que a energia do laser interaja totalmente com o material.
Respingo
Os respingos produzidos pela soldagem a laser podem afetar seriamente a qualidade da superfície da costura de solda. Após a soldagem, muitas partículas metálicas podem aparecer na superfície da peça ou material, o que não só afeta a aparência, mas também o uso. Quando o respingo é sério, também polui e danifica a lente.
Para evitar respingos na soldagem a laser:
- otimizar o foco e a posição do feixe de laser: ajuste adequadamente a posição e a forma do foco do feixe de laser para obter uma soldagem estável e precisa. Evite desalinhamento ou foco instável do feixe de laser, o que pode causar respingos.
- Use gás de proteção e taxa de fluxo adequados: Escolha a composição do gás de proteção e a taxa de fluxo adequadas para fornecer proteção adequada. O gás de proteção ajuda a prevenir a oxidação e a contaminação da poça de fusão e reduz os respingos. O fluxo de gás precisa ser ajustado de acordo com os requisitos de soldagem.
- Limpe a superfície da peça de trabalho: Limpe completamente a superfície da peça de trabalho e remova qualquer contaminação que possa causar a formação de respingos.
Deformação
Deformação refere-se à deformação ou flexão de uma estrutura ou peça soldada devido ao processo de soldagem.
Para evitar a deformação da soldagem a laser:
- Use a técnica correta de fixação e fixação: Fixe a peça de trabalho ou estrutura para minimizar o movimento ou deformação durante a soldagem. O suporte adequado e o alinhamento da peça de trabalho ajudam a manter a estabilidade dimensional.
- pré-aquecer a peça de trabalho: Considere pré-aquecer a peça de trabalho para reduzir os gradientes térmicos e minimizar a distorção.
- Resfriamento controlado: implemente técnicas de resfriamento controlado, como o uso de dissipadores de calor ou acessórios, para regular as taxas de resfriamento e minimizar os gradientes térmicos.
Problemas de Zona Afetada pelo Calor (HAZ)
A soldagem a laser cria uma zona afetada pelo calor altamente concentrada ao redor da solda. A zona afetada pelo calor sofre ciclos térmicos e mudanças microestruturais que podem resultar em resistência reduzida e mudanças na dureza do material.
Para evitar problemas de HAZ:
- Otimizando os parâmetros do laser: Ajuste os parâmetros do laser para minimizar o tamanho e a profundidade da zona afetada pelo calor. Isso inclui controlar a potência do laser, a duração do pulso e o foco do feixe.
- Usando técnicas de varredura ou oscilação: O uso de técnicas de varredura ou oscilação permite uma distribuição mais uniforme do calor e reduz a concentração de calor em áreas específicas, minimizando assim os problemas associados às zonas afetadas pelo calor.
- realizar tratamento térmico pós-soldagem: Aplique processos de tratamento térmico pós-soldagem adequados, como recozimento ou alívio de tensões, para refinar a microestrutura e reduzir problemas associados à zona afetada pelo calor. O tratamento térmico ajuda a restaurar as propriedades do material na zona afetada pelo calor.
Colapso de solda
O colapso da soldagem a laser refere-se à deformação interna ou afundamento da costura de solda durante o processo de soldagem. Isso pode acontecer por vários motivos, como potência do laser muito alta, controle insuficiente da poça de fusão, suporte de material insuficiente, montagem de junta inadequada, gerenciamento térmico inadequado, problemas de seleção de material e falta de monitoramento e controle do processo.
Para evitar o colapso da solda:
- otimizar os parâmetros do laser: reduza a potência do laser ou a densidade de energia para evitar o derretimento excessivo dos materiais circundantes. Ajuste a potência do laser, a duração do pulso e a forma do feixe para obter um equilíbrio entre a penetração e evitar o derretimento excessivo que pode levar ao colapso.
- Suporte de material adequado: Forneça suporte de material adequado durante a soldagem usando acessórios, gabaritos ou grampos para manter a peça de trabalho no lugar e fornecer estabilidade. Considere o uso de hastes de suporte ou dissipadores de calor para dissipar o calor e fornecer suporte adicional para as juntas.
- garantir a montagem adequada da junta: A montagem adequada da junta ajuda a evitar o colapso. Certifique-se de que as superfícies de contato estejam devidamente preparadas e alinhadas antes de soldar. Aumente a força e a estabilidade das juntas implementando técnicas adequadas de design de juntas e preparação de arestas.
- Gerencie a entrada de calor: controle a entrada de calor e gerencie adequadamente os ciclos térmicos. Otimize as estratégias de varredura ou movimento para distribuir uniformemente o calor e evitar o superaquecimento localizado. Implemente técnicas de pré-aquecimento ou resfriamento controlado para minimizar os gradientes térmicos e reduzir o risco de colapso.
- Seleção e compatibilidade de materiais: Selecione materiais apropriados e parâmetros de soldagem mutuamente compatíveis. Considere as propriedades do material, como condutividade térmica e ponto de fusão, para garantir a transferência de calor adequada e evitar o derretimento localizado excessivo.
- Monitoramento e controle do processo: Implemente um sistema de monitoramento e controle do processo em tempo real para detectar sinais de colapso ou desvios dos parâmetros de soldagem desejados. Use mecanismos de feedback durante a soldagem para ajustar os parâmetros do laser, a velocidade de varredura ou o suporte do material. Adote tecnologias avançadas, como sistemas de controle adaptativo ou controle de feedback de circuito fechado para obter condições de soldagem consistentes e estáveis.
- Garanta o controle adequado da poça de fusão: controle o tamanho e a forma da poça de fusão ajustando os parâmetros do laser e a velocidade de escaneamento. Use técnicas de soldagem adequadas, como soldagem de buraco de fechadura ou soldagem de modo de condução, para garantir uma formação de poça de fusão estável e controlada.
Resumir
Obviamente, outras falhas podem ser associadas à soldagem a laser. Além dos problemas técnicos operacionais, alguns defeitos podem levar a alterações nas propriedades do material. Somente entendendo corretamente os defeitos que podem ocorrer no processo de soldagem a laser e as causas de diferentes defeitos, podemos resolver o problema de soldagem anormal de maneira mais direcionada.
AccTek Laser tem uma ampla gama de máquinas de solda a laser, incluindo portátil, limpeza e soldagem Máquinas de solda a laser 3 em 1, adequado para soldar chapas e tubos de metal. Se você procura uma máquina para uma aplicação especial, Laser AccTek também pode ser equipado com componentes adequados para realizar uma solução personalizada de acordo com os requisitos do cliente.
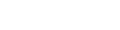
Informações de contato
- [email protected]
- [email protected]
- +86-19963414011
- No. 3 Zona A, Zona Industrial de Lunzhen, Cidade de Yucheng, Província de Shandong.
Obtenha soluções a laser