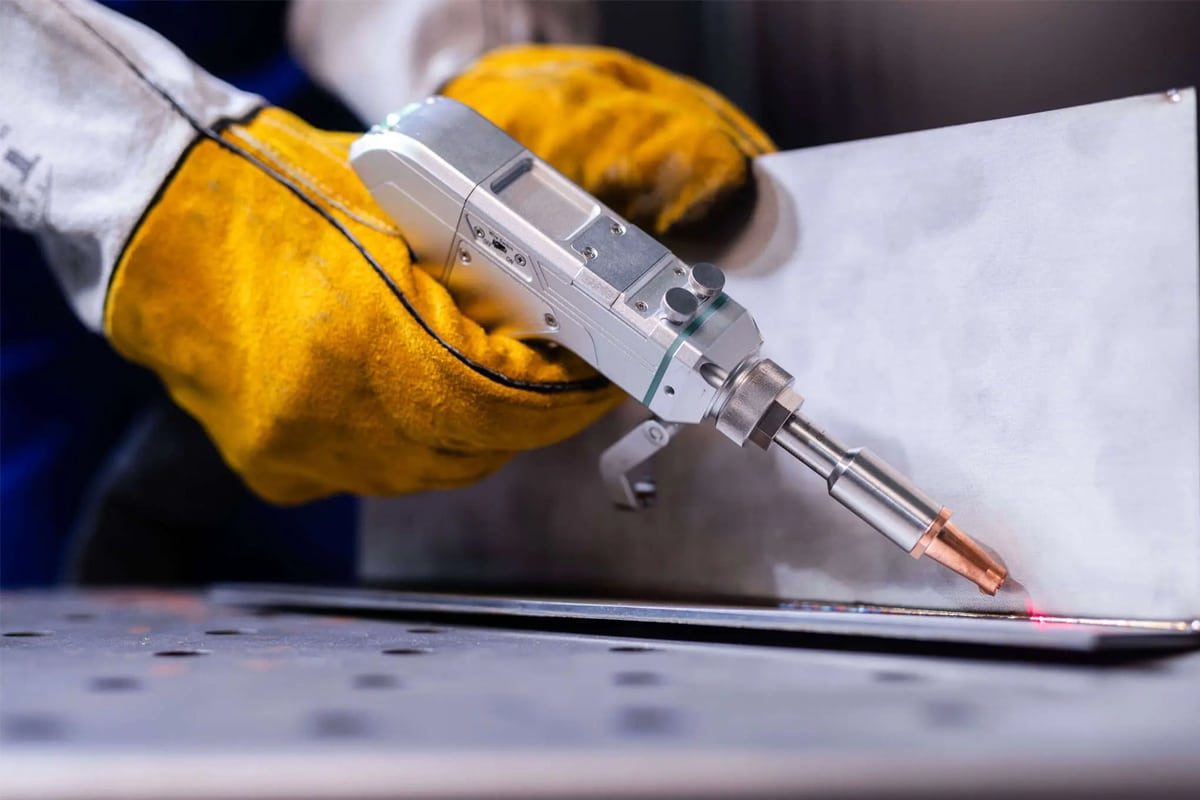
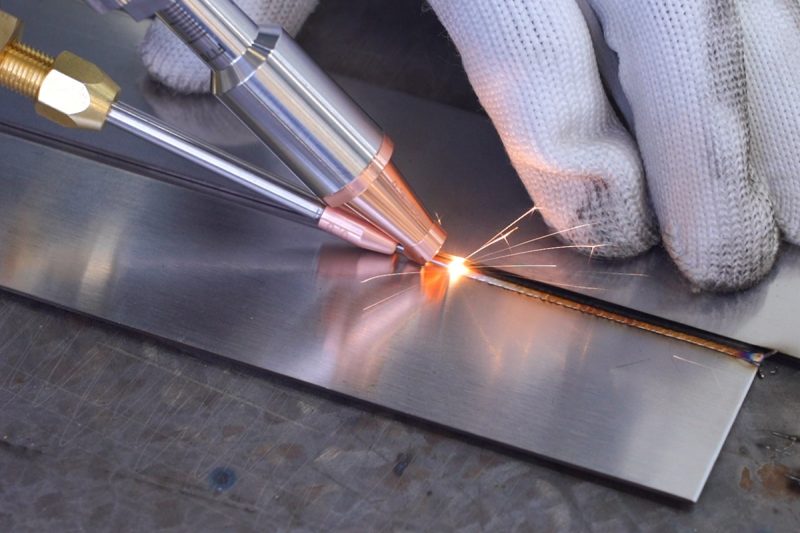
Visão geral da soldagem a laser
O que é soldagem a laser?
A soldagem a laser é um processo de junção preciso e eficiente que usa um feixe de laser altamente focado para aquecer e fundir materiais. O feixe de laser gera uma fonte de calor concentrada, permitindo soldas estreitas e profundas com zonas afetadas pelo calor (HAZ) mínimas. A soldagem a laser opera em dois modos principais, dependendo da densidade de potência e das propriedades do material:
- Soldagem no Modo Keyhole: Neste modo, um feixe de laser de alta densidade de potência vaporiza o material, criando um keyhole estreito e profundo cheio de metal fundido e vapor. O keyhole atua como um conduíte para a energia do laser, permitindo soldas de penetração profunda e alta relação de aspecto. Este modo é ideal para aplicações que exigem soldas profundas e estreitas, como nas indústrias automotiva e aeroespacial.
- Soldagem no Modo de Condução: Este modo ocorre em densidades de potência mais baixas em comparação à soldagem keyhole, onde o laser aquece o material sem vaporizá-lo. A condução de calor da superfície cria uma poça de solda rasa e mais larga. A soldagem no modo de condução é adequada para materiais finos ou quando penetração e entrada de calor mínimas são desejadas.
Vantagens da soldagem a laser
A soldagem a laser oferece vários benefícios que a tornam vantajosa em relação aos métodos de soldagem tradicionais:
- Precisão e exatidão: O feixe de laser concentrado permite um controle preciso, produzindo soldas precisas com distorção mínima.
- Processamento de alta velocidade: a alta densidade de energia do laser permite altas velocidades de soldagem, aumentando a produtividade e reduzindo os tempos de ciclo.
- Zona mínima afetada pelo calor: a redução da propagação térmica minimiza a distorção, tornando a soldagem a laser adequada para componentes delicados ou finos.
- Capacidade de automação: a soldagem a laser é facilmente integrada a sistemas automatizados e braços robóticos, aumentando a eficiência da produção em alto volume.
- Versatilidade do material: Capaz de soldar uma ampla gama de metais e ligas, incluindo materiais difíceis de soldar, como titânio e aço inoxidável.
- Processo sem contato: não é necessário contato físico, o que reduz o desgaste das ferramentas e elimina o risco de contaminação do eletrodo.
Aplicações da soldagem a laser
A soldagem a laser é usada em vários setores devido às suas capacidades e precisão únicas:
- Indústria automotiva: usada para soldar painéis de carroceria, engrenagens, componentes de transmissão e sistemas de escapamento, onde alta precisão e velocidade são essenciais.
- Indústria aeroespacial: adequada para soldagem de componentes leves e de alta resistência, como lâminas de turbina, peças estruturais e componentes de motor.
- Indústria eletrônica: Ideal para microssoldagem de circuitos delicados, conectores e invólucros em dispositivos eletrônicos.
- Fabricação de dispositivos médicos: usada para soldar dispositivos médicos complexos, instrumentos cirúrgicos e componentes implantáveis onde precisão e limpeza são primordiais.
- Joias e arte: permite reparos complexos e fabricação de designs complexos de joias e trabalhos artísticos em metal.
- Fabricação industrial: Aplicada na união de chapas metálicas, tubulações e componentes estruturais de alta resistência em vários setores industriais.
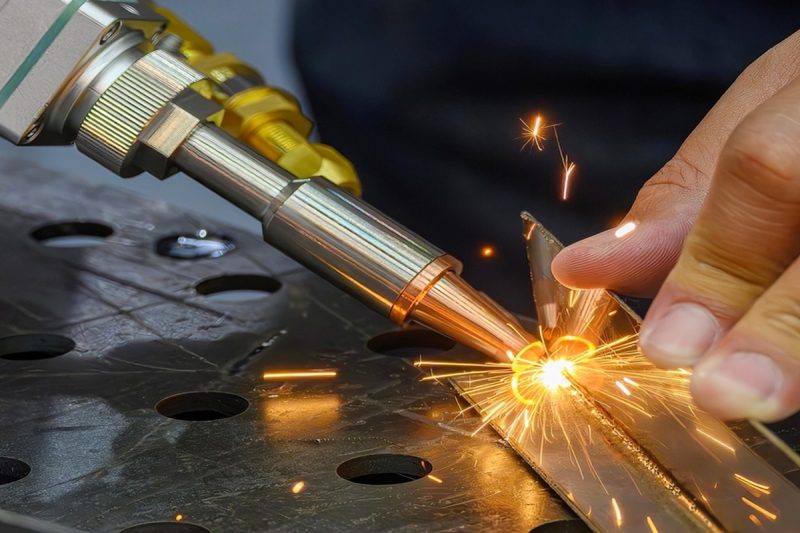
Defeitos comuns de soldagem em soldagem a laser
Porosidade
Causas
- Contaminação da superfície: óleo, graxa, umidade e ferrugem na superfície da peça de trabalho podem gerar gás quando aquecidos, causando bolhas presas na solda.
- Problemas com gás de proteção: cobertura inadequada de gás de proteção, baixas taxas de fluxo ou tipo de gás inadequado podem resultar em contaminação atmosférica, como intrusão de oxigênio e nitrogênio, que forma bolsas de gás.
- Composição do material: Altas concentrações de hidrogênio, enxofre, carbono ou outras impurezas no metal base podem levar à evolução de gás durante a soldagem.
- Resfriamento rápido: a solidificação rápida da poça de fusão pode reter o gás antes que ele escape.
Soluções
- Limpeza de superfície: limpe completamente as peças de trabalho antes de soldar, removendo contaminantes como graxa, óleo e ferrugem.
- Fluxo de gás de proteção otimizado: use gases de proteção apropriados, como argônio ou hélio, garantindo a vazão e a cobertura corretas para proteger a poça de solda.
- Seleção e preparação de materiais: escolha materiais com baixo teor de impurezas e realize tratamentos de pré-soldagem, como desgaseificação.
- Ajuste de parâmetros: ajuste os parâmetros do laser para permitir o resfriamento controlado, dando tempo para os gases escaparem.
Rachaduras
Tipos de rachaduras
- Trincamento a quente: ocorre em altas temperaturas durante a solidificação devido a tensões de tração ou segregação de impurezas (por exemplo, enxofre).
- Trincas a frio: ocorrem após o resfriamento, geralmente associadas à fragilização por hidrogênio, tensões residuais ou composição inadequada do material.
Causas
- Altos gradientes térmicos: ciclos rápidos de aquecimento e resfriamento podem introduzir tensões residuais que promovem rachaduras.
- Composição do material: Certas ligas, particularmente aquelas com alto teor de enxofre ou carbono, são mais suscetíveis a rachaduras.
- Impurezas: Elementos como enxofre e fósforo podem se segregar nos limites dos grãos, enfraquecendo a estrutura.
- Absorção de hidrogênio: o hidrogênio introduzido através de umidade, gás de proteção contaminado ou metal base pode levar ao craqueamento tardio.
Soluções
- Pré-aquecimento e tratamento térmico pós-soldagem: pré-aqueça a peça de trabalho para reduzir gradientes térmicos e execute tratamentos térmicos pós-soldagem para aliviar tensões residuais.
- Controle de materiais: selecione materiais com baixos níveis de impurezas e otimize sua composição química para reduzir a suscetibilidade a rachaduras.
- Controle de hidrogênio: materiais secos e uso de processos com baixo teor de hidrogênio, como uso de gases de proteção secos e evitando umidade.
- Técnicas de alívio de tensões: use dispositivos de fixação e projetos de juntas adequados para minimizar a concentração de tensões.
Corte inferior
Causas
- Entrada excessiva de calor: alta potência do laser ou velocidades lentas de deslocamento podem causar fusão localizada e perda de material sem metal de adição suficiente.
- Ângulo de feixe incorreto: o desalinhamento do feixe de laser em relação à junta pode levar à remoção do material em vez da fusão.
- Foco incorreto: o foco impreciso do laser pode concentrar a energia de forma desigual.
Soluções
- Otimize a entrada de calor: ajuste a potência do laser, a velocidade de deslocamento e o diâmetro do feixe para controlar a distribuição de calor.
- Alinhamento do feixe: alinhe corretamente o feixe de laser com a junta para garantir fusão e preenchimento uniformes.
- Técnica de soldagem: Ajuste o ângulo e o posicionamento do laser para reduzir a perda de material.
Falta de Fusão
Causas
- Entrada de calor insuficiente: baixa potência do laser ou velocidade de deslocamento excessiva podem impedir a fusão completa dos materiais de base.
- Preparação inadequada da junta: encaixe inadequado, folgas ou desalinhamento entre as peças de trabalho podem inibir a fusão completa.
- Contaminação: Óxidos de superfície, sujeira ou outros contaminantes podem atuar como barreiras à fusão.
Soluções
- Aumente a entrada de calor: use potência de laser suficiente ou reduza a velocidade de deslocamento para obter a fusão adequada.
- Melhore o encaixe das juntas: garanta o alinhamento e o encaixe adequados entre as peças de trabalho para uma penetração de solda consistente.
- Limpeza de superfícies: Remova óxidos, óleos e outros contaminantes das superfícies de soldagem.
Penetração incompleta
Causas
- Baixa potência do laser: entrada de energia insuficiente para derreter completamente a espessura do material.
- Alta velocidade de deslocamento: o laser se move muito rápido para aquecer e derreter completamente a junta.
- Foco incorreto do feixe: Focar o laser incorretamente pode levar a uma penetração superficial.
Soluções
- Aumente a potência do laser: ajuste as configurações de potência para garantir a penetração total na articulação.
- Reduza a velocidade de deslocamento: dê mais tempo para o laser aquecer e derreter o material.
- Foco correto do feixe: foque corretamente o laser para obter uma profundidade de penetração consistente.
respingos
Causas
- Potência excessiva do laser: configurações de alta potência podem causar ebulição violenta da poça de fusão.
- Contaminantes: impurezas da superfície podem reagir com o calor, criando vaporização rápida.
- Gás de proteção inadequado: a proteção inadequada pode permitir oxidação, causando respingos.
Soluções
- Ajuste os parâmetros do laser: reduza a potência do laser e otimize as configurações de pulso para evitar entrada excessiva de energia.
- Limpeza de superfícies: certifique-se de que as superfícies estejam livres de contaminantes antes de soldar.
- Otimização do gás de proteção: use gás de proteção apropriado e mantenha vazões adequadas.
Irregularidades no cordão de solda
Causas
- Velocidade de deslocamento inconsistente: flutuações na velocidade levam a uma entrada de calor irregular.
- Variabilidade da potência do laser: alterações na potência de saída podem resultar em fusão inconsistente.
- Foco incorreto do feixe: foco desalinhado leva à distribuição desigual de energia.
Soluções
- Mantenha uma velocidade de deslocamento consistente: garanta uma velocidade uniforme durante todo o processo de soldagem.
- Estabilizar a saída de energia: use uma fonte de energia estável para manter a saída do laser consistente.
- Ajuste o foco do feixe: garanta o alinhamento e o foco corretos do feixe para uma distribuição uniforme de energia.
Queimadura
Causas
- Entrada excessiva de calor: alta potência do laser ou velocidades lentas de deslocamento podem levar ao derretimento excessivo.
- Material fino: folhas finas são mais propensas a queimar.
- Foco incorreto do feixe: concentrar energia em uma área pequena pode agravar o derretimento.
Soluções
- Reduza a entrada de calor: diminua a potência do laser ou aumente a velocidade de deslocamento.
- Amplie o foco do feixe: distribua a energia do laser de maneira mais uniforme.
- Use espessura de material apropriada: combine a espessura do material com os requisitos de soldagem.
Deformação e Distorção
Causas
- Estresses térmicos: ciclos rápidos de aquecimento e resfriamento causam expansão e contração.
- Materiais finos: Mais suscetíveis a empenamentos e dobras.
- Entrada excessiva de calor: alta entrada de energia pode levar a distorções severas.
Soluções
- Otimize a entrada de calor: use parâmetros de laser controlados para minimizar o calor excessivo.
- Fixação e fixação: mantenha as peças de trabalho no lugar com fixações para reduzir o movimento.
- Soldagem balanceada: use técnicas que equilibram o aquecimento e minimizam o estresse.
Oxidação e descoloração
Causas
- Gás de proteção inadequado: baixo fluxo de gás ou cobertura insuficiente podem expor a poça de solda ao ar.
- Composição inadequada do gás: a escolha incorreta do gás de proteção pode não impedir a oxidação.
- Contaminantes: impurezas da superfície podem reagir e causar oxidação.
Soluções
- Garanta a blindagem adequada: use um fluxo adequado de gás de proteção para proteger a poça de solda.
- Selecione a composição de gás apropriada: escolha um gás de proteção que previna efetivamente a oxidação (por exemplo, argônio).
- Limpeza de superfícies: limpe cuidadosamente as superfícies das peças de trabalho para minimizar reações durante a soldagem.
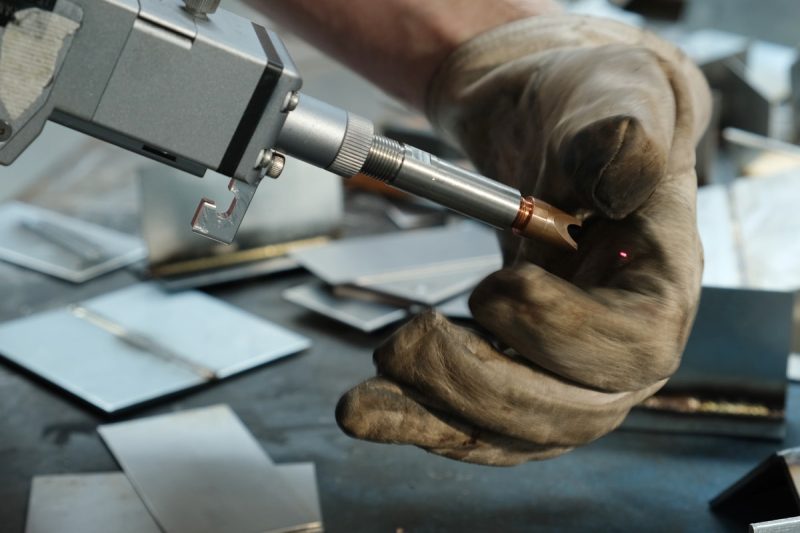
Fatores que influenciam defeitos de soldagem
Propriedades do Material
As propriedades dos materiais soldados desempenham um papel significativo na determinação da qualidade da solda e da probabilidade de defeitos.
- Condutividade térmica: Materiais com alta condutividade térmica, como alumínio, tendem a dissipar calor rapidamente, exigindo maior potência do laser ou velocidades de deslocamento mais lentas para atingir penetração e fusão suficientes. Controle insuficiente pode levar a defeitos como falta de fusão ou penetração incompleta.
- Ponto de fusão: Materiais com pontos de fusão variados exigem parâmetros de laser diferentes. Por exemplo, o titânio tem um ponto de fusão alto e requer maior entrada de energia, enquanto materiais de baixo ponto de fusão, como o zinco, podem sofrer de burn-through se não forem cuidadosamente gerenciados.
- Refletividade: Materiais altamente refletivos, como cobre e certas ligas de alumínio, podem refletir uma parte da energia do laser, reduzindo a entrada efetiva de calor. Isso pode resultar em fusão incompleta, penetração inconsistente ou respingos, pois a energia refletida pode afetar as áreas ao redor.
- Composição do material e impurezas: Elementos como enxofre, fósforo e hidrogênio no material podem aumentar a probabilidade de defeitos como porosidade e rachaduras. Por exemplo, alto teor de hidrogênio pode causar porosidade, enquanto enxofre e fósforo aumentam o risco de rachaduras a quente. Selecionar materiais com baixos níveis de impurezas ou conduzir tratamentos de pré-soldagem pode ajudar a mitigar esses problemas.
Parâmetros de soldagem
A seleção e o controle adequados dos parâmetros de soldagem a laser são cruciais para evitar defeitos. Os parâmetros-chave incluem:
- Potência do laser: potência adequada do laser é essencial para atingir penetração e fusão completas. Potência insuficiente pode levar à falta de fusão ou penetração incompleta, enquanto potência excessiva pode causar queimadura, respingos e deformação.
- Velocidade de deslocamento: A velocidade de deslocamento afeta a entrada de calor por unidade de comprimento da solda. Uma velocidade muito alta pode impedir que o material aqueça adequadamente, resultando em defeitos como falta de fusão e penetração incompleta. Por outro lado, uma velocidade muito lenta pode causar entrada excessiva de calor, levando à queima e distorção.
- Foco do feixe: O foco correto do feixe é essencial para a concentração de energia. Desalinhamento ou posição focal incorreta pode levar à penetração insuficiente, perfis de cordão irregulares e porosidade da solda. Para penetração profunda, um feixe focado com um tamanho de ponto pequeno é necessário, enquanto um feixe desfocado pode ser adequado para soldas mais largas e rasas.
- Duração do pulso (em soldagem a laser pulsado): A duração do pulso afeta a quantidade de energia fornecida em cada pulso. Pulsos curtos reduzem a entrada de calor e minimizam o risco de deformação, tornando-os ideais para materiais delicados ou sensíveis ao calor. Pulsos mais longos permitem maior penetração, mas podem aumentar o risco de defeitos como respingos e porosidade.
Projeto Conjunto
O projeto e a preparação da junta podem influenciar significativamente a qualidade da solda e a probabilidade de defeitos.
- Tolerância de ajuste: O ajuste adequado da junta é essencial para atingir qualidade de solda consistente. Lacunas ou desalinhamento entre peças de trabalho podem resultar em falta de fusão, porosidade ou penetração inconsistente. Ajustes apertados permitem melhor controle da poça de fusão e minimizam o risco de defeitos.
- Tipo de junta: Diferentes tipos de junta (por exemplo, topo, sobreposição, filete) exigem diferentes técnicas e parâmetros de soldagem a laser. Por exemplo, juntas de topo com alinhamento ruim podem levar a rebaixos ou falta de fusão, enquanto juntas de sobreposição com sobreposição excessiva podem causar respingos e fusão insuficiente.
- Acessibilidade: Em estruturas complexas, o acesso limitado à junta pode restringir o alcance do feixe de laser, levando à fusão incompleta ou à formação irregular de esferas. Fixação adequada e alinhamento a laser são necessários para juntas com acessibilidade limitada.
- Preparação e limpeza: A preparação e limpeza adequadas da área da junta são críticas, pois contaminantes da superfície podem levar à porosidade, rachaduras e respingos. A limpeza remove óxidos, óleos e outras impurezas que podem interferir na fusão e introduzir defeitos.
Fatores Ambientais
As condições ambientais na área de soldagem podem afetar diretamente a qualidade da solda e a ocorrência de defeitos.
- Temperatura ambiente: Soldar em temperaturas extremas, muito frias ou muito quentes, pode afetar a taxa de resfriamento da solda e levar a estresse térmico e rachaduras. Ambientes frios, por exemplo, podem causar resfriamento rápido, levando a soldas quebradiças e rachaduras.
- Umidade e Umidade: A umidade no ambiente pode introduzir hidrogênio na poça de solda, aumentando o risco de porosidade e rachaduras induzidas por hidrogênio. Soldar em um ambiente seco e controlado ou tomar precauções para evitar a exposição à umidade é essencial para soldas de alta qualidade.
- Qualidade e fluxo do gás de proteção: O gás de proteção protege a poça de solda fundida da contaminação atmosférica. O fluxo inadequado de gás de proteção ou o uso de gás de baixa pureza pode levar à oxidação, porosidade e descoloração. Além disso, gases de proteção como argônio e hélio devem ser usados com base nos requisitos do material para evitar contaminação.
- Vibração e movimento: vibrações ambientais ou movimento na configuração de soldagem podem levar a cordões de solda inconsistentes e outros defeitos. Fixação estável e minimização de movimento externo são essenciais para garantir resultados consistentes.
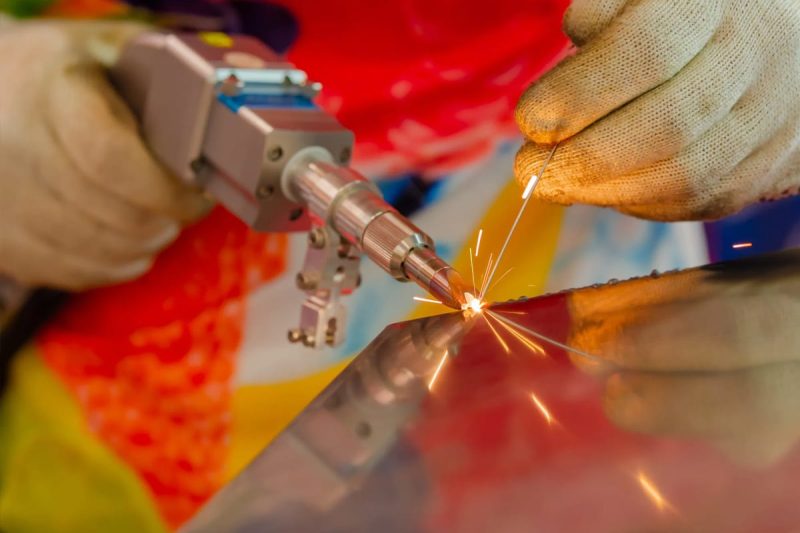
Considerações adicionais e melhores práticas
Seleção adequada de materiais
Escolher os materiais certos para soldagem a laser é essencial para obter soldas de alta qualidade e minimizar defeitos.
- Compatibilidade de materiais: Certifique-se de que os materiais de base sejam compatíveis com soldagem a laser. Diferentes materiais respondem de forma diferente à energia do laser devido a variações nos pontos de fusão, condutividade térmica e refletividade. Por exemplo, materiais refletivos como alumínio podem exigir medidas especiais para reduzir a reflexão e otimizar a absorção de calor.
- Pureza do material: use materiais com baixos níveis de impurezas, como enxofre e fósforo, que podem contribuir para porosidade, rachaduras e outros defeitos.
- Espessura do material: considere a espessura dos materiais a serem soldados, pois ela influencia a potência do laser necessária e a entrada de calor.
Tipo e configurações do laser
Selecionar o tipo de laser apropriado e ajustar suas configurações são fatores essenciais para o sucesso da soldagem a laser.
- Tipo de laser: Escolha entre lasers de onda contínua (CW) e pulsados com base na aplicação. Os lasers CW são ideais para soldagem de alta velocidade, enquanto os lasers pulsados são adequados para componentes delicados ou sensíveis ao calor.
- Configurações de potência e velocidade: otimize a potência do laser, a velocidade de deslocamento e a duração do pulso para atingir a penetração desejada, minimizar defeitos como respingos ou porosidade e controlar a entrada de calor.
- Foco e posicionamento do feixe: o alinhamento e o foco adequados do feixe são essenciais para uma distribuição uniforme de energia e soldas consistentes.
Projeto e montagem de juntas
O projeto e o encaixe adequados das juntas garantem uma qualidade de solda consistente e reduzem a probabilidade de defeitos como falta de fusão, porosidade e desalinhamento.
- Tolerâncias de encaixe: garanta que as juntas tenham encaixes firmes e consistentes, minimizando lacunas que podem levar à fusão irregular ou porosidade.
- Acessibilidade das articulações: projete as articulações para permitir fácil acesso ao feixe de laser, minimizando o risco de fusão incompleta ou de cordões irregulares.
- Preparação das juntas: limpe e prepare adequadamente as superfícies das juntas para remover contaminantes, como óleos, óxidos e outras impurezas.
Seleção de gás de proteção
O gás de proteção protege a poça de solda fundida da contaminação atmosférica, prevenindo oxidação, porosidade e outros defeitos.
- Tipo de gás: Selecione gases de proteção apropriados, como argônio, hélio ou misturas, com base no material base e nas características de solda desejadas. Por exemplo, o argônio é frequentemente usado para aço inoxidável, enquanto o hélio pode melhorar a penetração para materiais mais espessos.
- Taxa de fluxo: certifique-se de que a taxa de fluxo do gás de proteção seja suficiente para cobrir a poça de solda sem turbulência ou cobertura inadequada.
- Pureza: Use gás de proteção de alta pureza para evitar contaminação.
Tratamentos pré e pós-soldagem
Os tratamentos pré e pós-soldagem podem reduzir significativamente a probabilidade de defeitos e melhorar a qualidade geral da solda.
- Limpeza pré-soldagem: limpe completamente as peças de trabalho para remover contaminantes, como óleos, ferrugem e umidade, que podem causar porosidade, rachaduras e outros defeitos.
- Pré-aquecimento: O pré-aquecimento de materiais, especialmente aqueles propensos a rachaduras, pode reduzir gradientes térmicos e minimizar tensões residuais.
- Tratamento térmico pós-soldagem: realize tratamentos térmicos pós-soldagem, como recozimento ou alívio de tensões, para reduzir tensões residuais e melhorar as propriedades mecânicas da solda.
Treinamento do Operador
Operadores qualificados desempenham um papel fundamental para garantir soldas a laser consistentes e de alta qualidade.
- Treinamento técnico: treine os operadores sobre o manuseio adequado de equipamentos de soldagem a laser, incluindo posicionamento, controle de velocidade e ajustes de parâmetros.
- Identificação de defeitos: eduque os operadores para reconhecer defeitos comuns, suas causas e como fazer os ajustes necessários para evitar recorrências.
- Protocolos de segurança: garanta que os operadores sejam treinados em procedimentos de segurança a laser para proteger a si mesmos e ao ambiente de trabalho.
Manutenção de Equipamento
A manutenção regular do equipamento de soldagem a laser é essencial para garantir um desempenho consistente e evitar defeitos.
- Limpeza óptica: limpe lentes, espelhos e outros componentes ópticos regularmente para manter a qualidade e a precisão do feixe.
- Calibração: Calibre os sistemas de laser periodicamente para garantir saída de potência precisa, alinhamento do feixe e foco.
- Inspeção de componentes: inspecione e substitua componentes desgastados ou danificados, como bicos e lentes, para manter a consistência da solda.
Monitoramento de Processos
O monitoramento e o controle do processo são essenciais para obter soldas consistentes e sem defeitos.
- Monitoramento em tempo real: use sensores e sistemas de monitoramento para detectar e corrigir desvios nos parâmetros de soldagem, como flutuações de potência, velocidade de deslocamento e foco do feixe, em tempo real.
- Registro de dados: registre parâmetros e resultados de soldagem para analisar tendências, identificar causas raiz de defeitos e implementar medidas de melhoria contínua.
- Inspeções de qualidade: realize inspeções regulares, incluindo métodos de testes não destrutivos (END), para verificar a qualidade da solda.
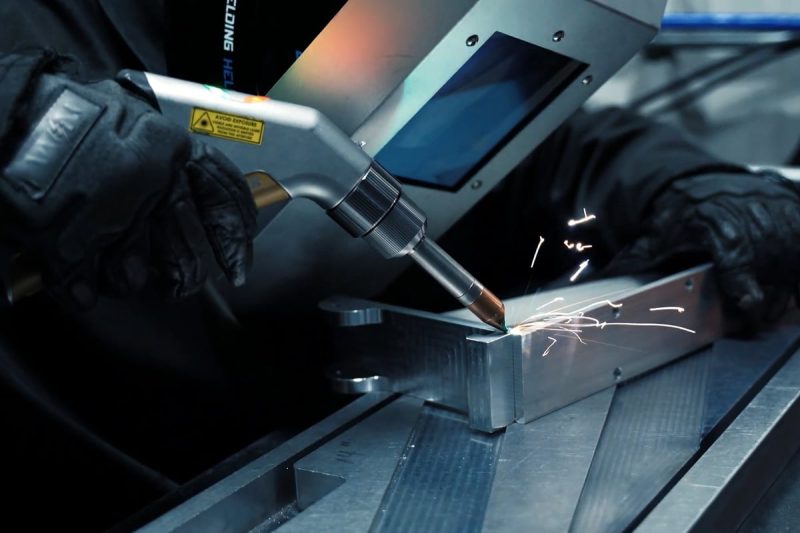
Resumo
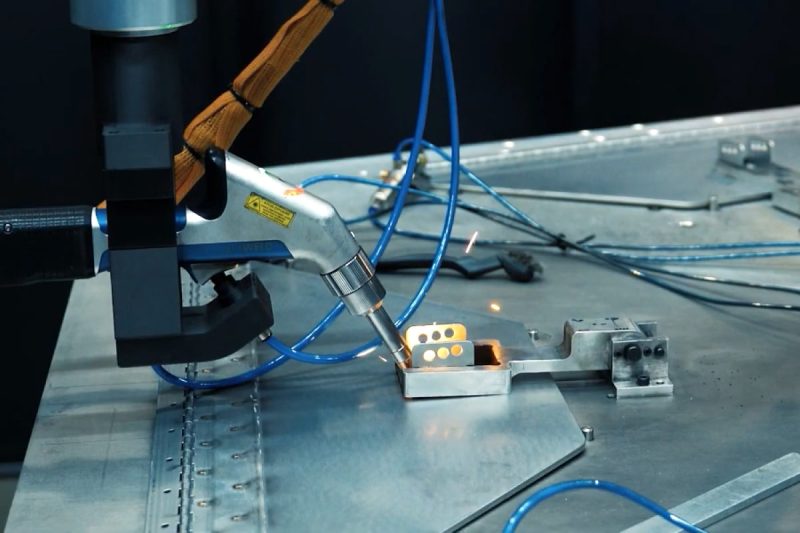
Obtenha soluções de soldagem a laser
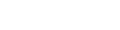
- [email protected]
- [email protected]
- +86-19963414011
- No. 3 Zona A, Zona Industrial de Lunzhen, Cidade de Yucheng, Província de Shandong.