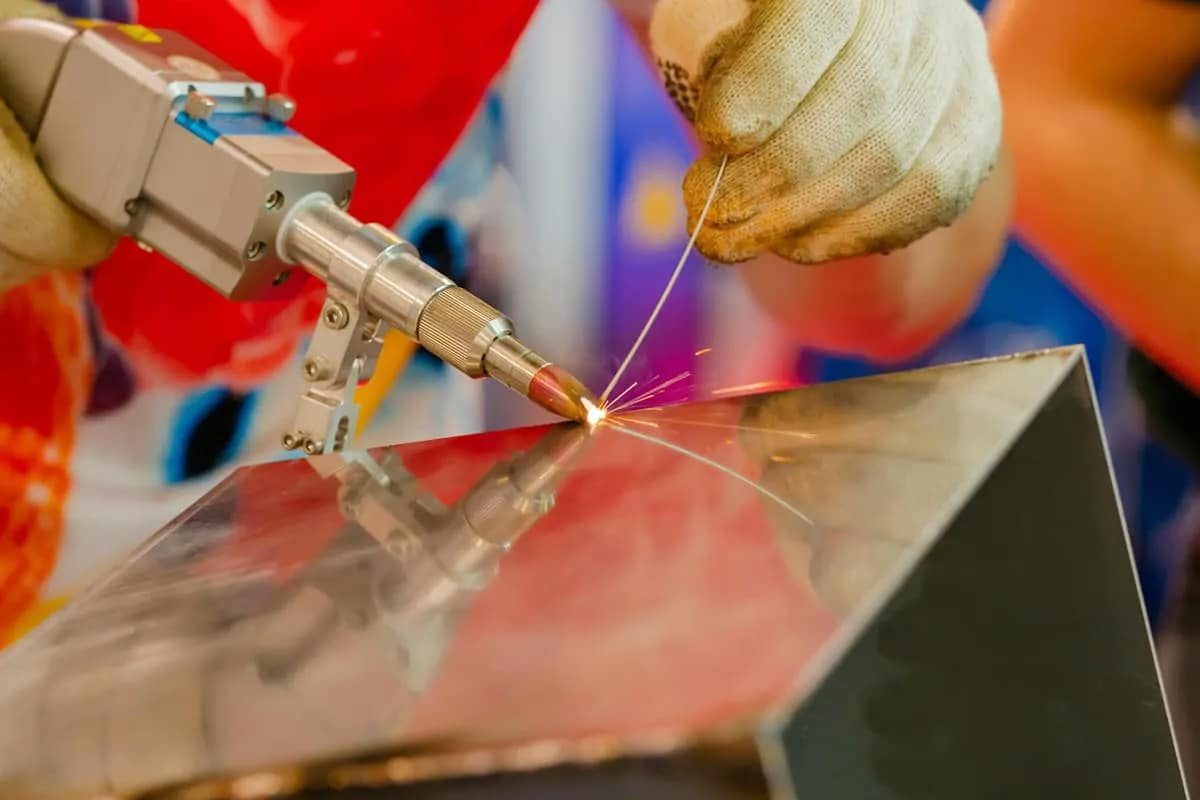
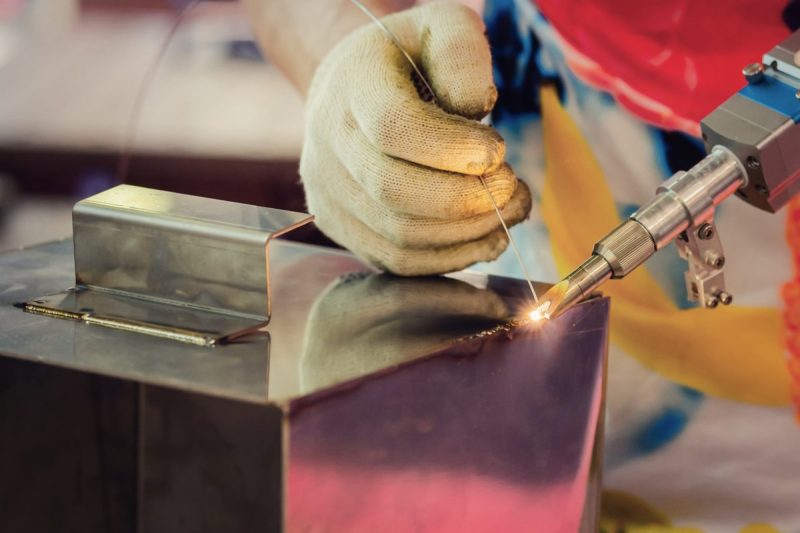
Parâmetros de laser
Potência do Laser
A potência do laser é um parâmetro fundamental na soldagem a laser e determina a quantidade de energia entregue à área de solda. A configuração de potência afeta a velocidade de soldagem e a profundidade de penetração.
- Alta Potência: O uso de alta potência do laser aumenta a velocidade de soldagem e a profundidade de penetração, permitindo a soldagem de materiais mais espessos. É particularmente útil para aplicações que requerem soldas profundas ou alta produtividade. No entanto, uma potência muito alta pode causar superaquecimento, derretimento excessivo e defeitos como respingos e porosidade.
- Baixa potência: Potências de laser mais baixas são adequadas para materiais mais finos e aplicações que exigem alta precisão, como microssoldagem. No entanto, a potência insuficiente pode resultar em soldas fracas devido à fusão incompleta ou à penetração insuficiente.
- Otimização: Alcançar a potência ideal do laser requer equilibrar as necessidades de penetração e velocidade com riscos de defeitos. Isso requer calibração cuidadosa com base no tipo de material, espessura e requisitos específicos de soldagem.
Comprimento de onda
O comprimento de onda de um laser afeta a forma como o material a ser soldado absorve a energia do laser. Diferentes materiais têm diferentes características de absorção em diferentes comprimentos de onda.
- Comprimentos de onda comuns: Os comprimentos de onda típicos usados na soldagem a laser incluem infravermelho (IR), luz visível e ultravioleta (UV). Cada comprimento de onda tem suas vantagens, dependendo do material e da aplicação.
- Lasers infravermelhos (IR): Lasers IR, como lasers de CO2 e de fibra, são comumente usados para soldar metais e são eficazes em materiais com alta absorção no espectro infravermelho.
- Lasers visíveis e UV: Esses comprimentos de onda são mais facilmente absorvidos por não-metais e alguns metais refletivos, tornando-os úteis para aplicações que envolvem plásticos e cerâmicas.
- Considerações específicas do material: Materiais como alumínio e cobre, que são altamente refletivos na faixa infravermelha, podem exigir lasers com comprimentos de onda que são mais facilmente absorvidos por esses metais. Revestimentos especiais ou fontes de laser com comprimentos de onda específicos podem aumentar a absorção e a eficiência da soldagem.
Duração e frequência do pulso
A duração e a frequência do pulso são parâmetros críticos na soldagem a laser pulsado, onde o laser opera em pulsos curtos em vez de uma onda contínua.
- Duração do pulso: A duração de cada pulso de laser pode afetar significativamente as características térmicas da solda. Pulsos mais curtos fornecem energia em rajadas breves e intensas, minimizando a zona afetada pelo calor (HAZ) e reduzindo a deformação térmica. Durações de pulso mais longas fornecem mais energia, mas podem aumentar a ZTA e o risco de danos térmicos.
- Frequência de pulso: A frequência dos pulsos, ou o número de pulsos por segundo, afeta o fornecimento geral de energia e a velocidade de soldagem. Frequências mais altas podem aumentar as velocidades de soldagem, mas também podem aumentar o risco de acúmulo de calor cumulativo, o que pode causar defeitos.
- Otimização: A combinação de duração e frequência do pulso deve ser otimizada com base nas propriedades do material e nas características desejadas da solda. O ajuste fino desses parâmetros ajuda a alcançar um equilíbrio entre velocidade de soldagem, penetração e efeito térmico.
Qualidade do feixe
A qualidade de um feixe de laser é definida por parâmetros como estrutura de modo e perfil do feixe, que impactam diretamente na eficiência da soldagem.
- Modo de feixe: O modo de um feixe de laser (por exemplo, TEM00) determina sua distribuição de intensidade. Uma estrutura modal de alta qualidade garante fornecimento de energia concentrado e uniforme, resultando em soldagem consistente e precisa.
- Perfil do feixe: Um perfil de feixe uniforme e bem definido minimiza as perdas de energia e garante o máximo fornecimento de energia para a área de solda. A má qualidade do feixe (caracterizada por um perfil distorcido ou irregular) resulta em aquecimento desigual e defeitos de solda.
- Viabilidade: A alta qualidade do feixe permite melhor foco, permitindo que o laser atinja tamanhos de pontos menores para aplicações que exigem alta precisão e detalhes finos.
Posição Focal
A posição do ponto focal do laser em relação à superfície do material é um parâmetro crítico que afeta a eficiência e a qualidade da soldagem.
- Foco correto: O foco correto do feixe de laser na área de solda garante máxima densidade de energia e fusão eficiente do material. A posição focal ideal depende da espessura do material e das características desejadas da solda. Para soldagem de penetração profunda, o ponto focal geralmente é colocado ligeiramente abaixo da superfície do material.
- Distância focal: A distância focal da óptica do laser determina a profundidade focal e o tamanho focal. Distâncias focais curtas produzem tamanhos de pontos menores e densidades de energia mais altas para tarefas de soldagem fina. Distâncias focais maiores proporcionam maiores profundidades focais, o que é benéfico para soldagem de materiais mais espessos.
- Tolerância de foco: Manter uma posição focal consistente pode ajudar a obter uma qualidade de solda uniforme. Variações na posição focal podem resultar em penetração inconsistente, fusão incompleta e defeitos. Sistemas automatizados com ajuste de foco em tempo real podem ajudar a manter o foco ideal durante o processo de soldagem.
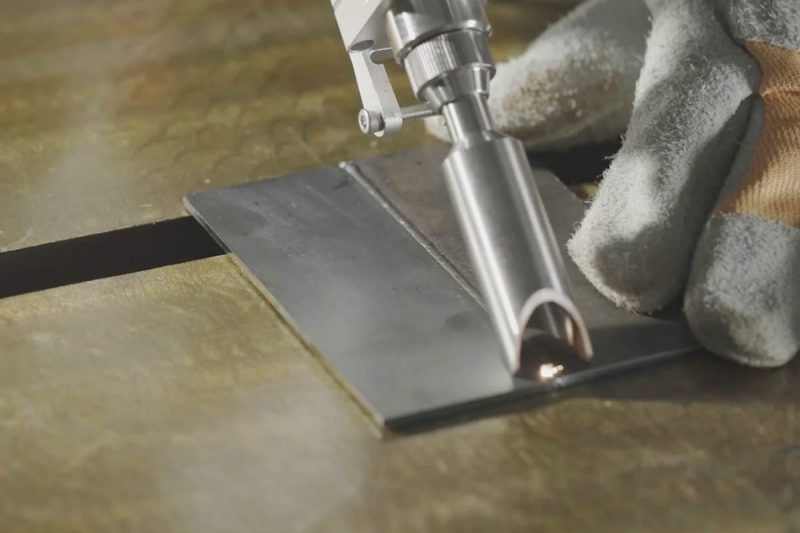
Propriedades do Material
tipo de material
O tipo de material a ser soldado é o principal fator na determinação da eficiência da soldagem a laser. Diferentes materiais absorvem e conduzem a energia do laser de diferentes maneiras, afetando a qualidade da solda e os parâmetros do processo.
- Metais: Os metais comumente soldados incluem aço, alumínio, titânio e cobre. Cada metal tem propriedades diferentes:
- Aço: Geralmente pode ser bem soldado com laser devido à sua boa absorção da energia do laser. Vários tipos de aço, incluindo aço carbono, aço inoxidável e aço-liga, podem exigir diferentes configurações de laser.
- Alumínio: O alumínio é conhecido por sua alta refletividade e condutividade térmica, e soldar alumínio com laser pode ser um desafio. Comprimentos de onda ou revestimentos especiais podem melhorar a absorção.
- Titânio: O titânio pode ser soldado de forma eficaz com um laser devido à sua refletividade moderada e propriedades térmicas. É amplamente utilizado em aplicações aeroespaciais e médicas.
- Cobre: A alta refletividade e condutividade térmica do cobre dificultam a soldagem com uma configuração de laser tradicional. Lasers de fibra com comprimentos de onda específicos são frequentemente usados para melhorar a eficiência.
- Não metais: Materiais como plásticos, cerâmicas e compósitos também podem ser soldados a laser. Cada não-metal requer parâmetros de laser específicos para uma soldagem eficiente:
- Plásticos: Os plásticos geralmente absorvem bem a energia do laser, mas suas propriedades térmicas requerem um controle cuidadoso dos parâmetros de soldagem para evitar queimaduras ou derretimento.
- Cerâmica: A cerâmica é frágil e pode rachar sob estresse térmico. A cerâmica para soldagem a laser geralmente requer pré-aquecimento e uso de lasers com comprimentos de onda específicos para reduzir o estresse.
- Compósitos: Os compósitos combinam diferentes materiais e requerem ajuste cuidadoso de parâmetros para garantir qualidade de solda uniforme em diferentes componentes.
Grossura
A espessura do material é um fator chave que afeta a eficiência da soldagem a laser. Afeta a potência necessária do laser, a velocidade de soldagem e a estabilidade geral do processo.
- Materiais finos: Materiais finos requerem menor potência do laser e velocidades de soldagem mais altas para evitar queimaduras e entrada excessiva de calor. O controle preciso dos parâmetros do laser permite soldas limpas e sem defeitos.
- Materiais Grossos: A soldagem de materiais espessos requer maior potência do laser e velocidades de soldagem mais lentas para garantir penetração e fusão adequadas. Técnicas avançadas, como soldagem multipasse ou soldagem híbrida (combinando soldagem a laser e a arco), podem ser usadas para obter penetração total.
- Zona de Transição: Ao soldar materiais de diferentes espessuras, os parâmetros do laser precisam ser ajustados dinamicamente para acomodar diferenças na absorção e condução de calor.
Condição da superfície
A condição da superfície de um material pode afetar a absorção do laser, a transferência de calor e a qualidade geral da solda. A preparação adequada da superfície ajuda a obter uma soldagem a laser eficiente.
- Limpeza: Contaminantes como óleo, graxa, sujeira e camadas de óxido podem interferir na absorção do laser e causar defeitos na solda. É necessária uma limpeza completa da superfície antes da soldagem para garantir resultados ideais.
- Rugosidade da superfície: A rugosidade da superfície de um material pode afetar a interação do feixe de laser. Superfícies mais lisas geralmente resultam em melhor absorção do laser e soldas mais consistentes. Tratamentos de superfície, como polimento ou jateamento, podem ser usados para melhorar as condições da superfície.
- Revestimentos e Tratamentos: Alguns materiais podem ter revestimentos ou tratamentos que afetam a soldagem a laser. Por exemplo, o aço galvanizado possui um revestimento de zinco que requer configurações específicas do laser para evitar evaporação e porosidade. Compreender os efeitos desses revestimentos pode ajudar a ajustar os parâmetros de soldagem de acordo.
Propriedades térmicas
As propriedades térmicas de um material, incluindo condutividade térmica, capacidade térmica específica e ponto de fusão, afetam a forma como o material interage com a energia do laser.
- Condutividade Térmica: Materiais com alta condutividade térmica, como cobre e alumínio, dissipam o calor rapidamente e requerem potências de laser mais altas para alcançar a fusão adequada. Materiais com baixa condutividade térmica, como o aço inoxidável, retêm o calor por mais tempo, portanto a entrada de calor precisa ser cuidadosamente controlada para evitar derretimento excessivo.
- Capacidade térmica específica: A capacidade térmica específica de um material determina a quantidade de energia necessária para aumentar sua temperatura. Materiais com altas capacidades de calor específico requerem mais energia para soldar, o que afeta a escolha da potência do laser e da velocidade de soldagem.
- Ponto de fusão: O ponto de fusão de um material determina a quantidade de energia necessária para iniciar a fusão e a fusão. Materiais de alto ponto de fusão, como titânio e certas ligas, exigem potências de laser mais altas e controle preciso dos parâmetros de soldagem para obter uma soldagem eficiente.
Propriedades Metalúrgicas
As propriedades metalúrgicas de um material, incluindo sua composição, microestrutura e transformações de fase, desempenham um papel crítico no processo de soldagem a laser.
- Composição: A composição química de um material afeta sua soldabilidade. Os elementos de liga afetam a absorção da energia do laser pelo material, o comportamento de fusão e a suscetibilidade a defeitos como rachaduras e porosidade. Compreender a composição ajuda a selecionar os parâmetros de laser e o gás de proteção apropriados.
- Microestrutura: A microestrutura de um material, incluindo tamanho de grão e distribuição de fases, afeta suas propriedades mecânicas e resposta à soldagem. Materiais de granulação fina geralmente soldam melhor do que materiais de granulação grossa, o que pode exigir atenção especial para evitar rachaduras e deformações.
- Transformações de Fase: Alguns materiais passam por transformações de fase durante a soldagem, o que pode afetar as propriedades finais da solda. Por exemplo, alguns aços transformam-se de austenita em martensita à medida que esfriam, resultando em uma solda dura e quebradiça. O controle das taxas de resfriamento e do tratamento térmico pós-soldagem pode ajudar a controlar essas transformações e melhorar a qualidade da solda.
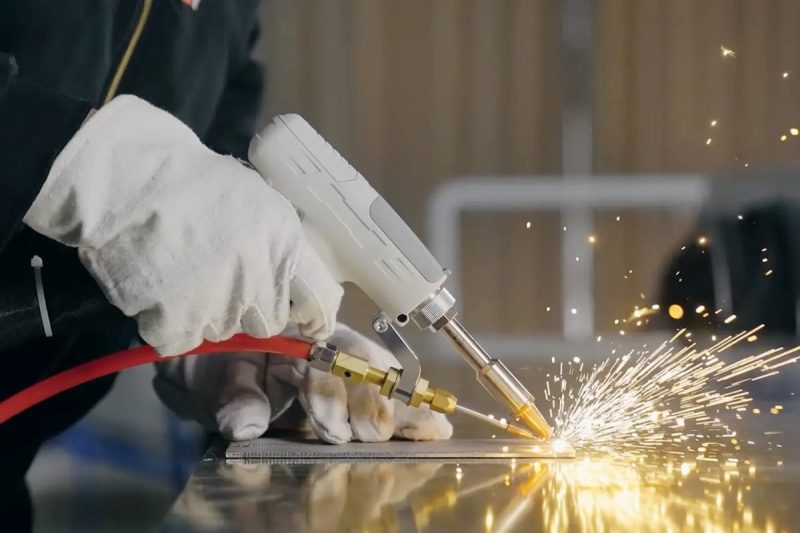
Projeto Conjunto
Configuração Conjunta
A configuração da junta tem um impacto significativo no processo de soldagem a laser. Diferentes tipos de juntas oferecem vários graus de acessibilidade, facilidade de soldagem e resistência mecânica.
- Junta de topo: Em uma junta de topo, dois pedaços de material são colocados de ponta a ponta. Esta configuração é comum na soldagem a laser porque é simples e permite penetração profunda. No entanto, apenas o alinhamento preciso e as lacunas mínimas podem garantir uma solda de alta qualidade.
- Junta sobreposta: Em uma junta sobreposta, um pedaço de material se sobrepõe a outro. Esta configuração é frequentemente usada para soldar materiais finos e é fácil de montar. No entanto, requer um controle cuidadoso dos parâmetros do laser para evitar derretimento excessivo e garantir que as duas camadas estejam devidamente fundidas.
- Junta em T: As juntas em T são formadas pela soldagem de uma peça de material perpendicular a outra. Esta configuração é frequentemente usada em aplicações estruturais. O desafio das juntas em T é conseguir uma penetração uniforme e evitar defeitos na intersecção.
- Junta de canto: As juntas de canto são usadas para unir duas peças de material em ângulos retos. Eles são freqüentemente usados em estruturas e molduras tipo caixa. Garantir a fusão adequada nos cantos requer controle preciso dos parâmetros do laser e preparação da junta.
- Junta de Borda: As juntas de borda envolvem soldagem ao longo da borda de uma ou ambas as peças de material. Esta configuração é adequada para materiais finos e aplicações onde é necessária uma sobreposição mínima. Conseguir soldas consistentes em juntas de borda requer alinhamento preciso e controle de folga.
Preparação conjunta
A preparação adequada das juntas ajuda a obter soldas de alta qualidade. A condição da superfície da junta afeta diretamente a absorção do laser, a transferência de calor e a integridade geral da solda.
- Limpeza: A superfície da junta deve estar livre de contaminantes como óleo, graxa, sujeira e óxidos. Os contaminantes podem interferir na absorção do laser e causar defeitos como porosidade e fusão incompleta. Métodos de limpeza como desengorduramento, escovação de aço e limpeza química podem ser utilizados, dependendo do material e dos contaminantes presentes.
- Tratamento de superfície: Tratamentos de superfície como jato de areia, retificação ou usinagem podem melhorar a condição da superfície e aumentar a absorção do laser. Esses tratamentos ajudam a criar uma superfície lisa e uniforme com risco reduzido de defeitos.
- Preparação das bordas: A preparação adequada das bordas garante um bom ajuste e minimiza lacunas. Técnicas como chanfro, chanfro e arredondamento de arestas podem melhorar o ajuste da junta e promover uma melhor fusão.
Tolerância de lacuna
Manter tolerâncias de folga restritas pode ajudar a obter soldas a laser consistentes e de alta qualidade. As lacunas entre as superfícies das juntas podem resultar em fusão incompleta, soldas fracas e defeitos.
- Folga Mínima: Idealmente, as superfícies das juntas devem ter uma folga mínima para garantir a fusão completa e uma solda forte. Pequenas lacunas podem ser preenchidas com material fundido, mas lacunas excessivas podem resultar em fusão incompleta e em uma junta fraca.
- Tolerância permitida: A tolerância de folga permitida depende do material, da configuração da junta e dos parâmetros de soldagem. Em geral, aplicações de alta precisão e materiais finos exigem tolerâncias mais restritas, enquanto materiais mais espessos podem tolerar folgas ligeiramente maiores.
- Ajustes: Se existirem lacunas, o ajuste da potência do laser, da velocidade de soldagem e da posição do foco pode ajudar a compensar e garantir a fusão adequada. Entretanto, folgas excessivas devem ser evitadas, pois podem afetar a qualidade e a resistência da solda.
Dispositivos elétricos e fixação
Acessórios e dispositivos de fixação eficazes podem garantir a estabilidade e o alinhamento da junta durante o processo de soldagem a laser. Fixações e dispositivos de fixação adequados evitam movimentos, deformações e desalinhamentos, melhorando assim a eficiência e a qualidade da soldagem.
- Estabilidade: O acessório deve segurar firmemente o material no lugar para evitar qualquer movimento durante o processo de soldagem. Mesmo um leve movimento pode causar desalinhamento, defeitos e alterações na qualidade da solda.
- Alinhamento: O sistema de fixação deve garantir que as superfícies da junta estejam alinhadas com precisão. O desalinhamento pode causar fusão deficiente e soldas fracas. Acessórios ajustáveis e ferramentas de fixação de precisão podem ajudar a obter um alinhamento preciso.
- Gerenciamento de Calor: Os acessórios e braçadeiras também devem gerenciar o calor gerado durante o processo de soldagem. O calor excessivo pode fazer com que a junta se deforme e se mova. O uso de materiais com boa condutividade térmica para o equipamento ou sistemas de resfriamento integrados pode ajudar a gerenciar o calor e manter a estabilidade.
- Acessibilidade: O projeto do sistema de fixação e fixação deve permitir que o feixe de laser alcance facilmente a área de soldagem. Geometrias complexas e espaços apertados exigem acessórios personalizados para garantir acesso adequado ao laser e condições ideais de soldagem.
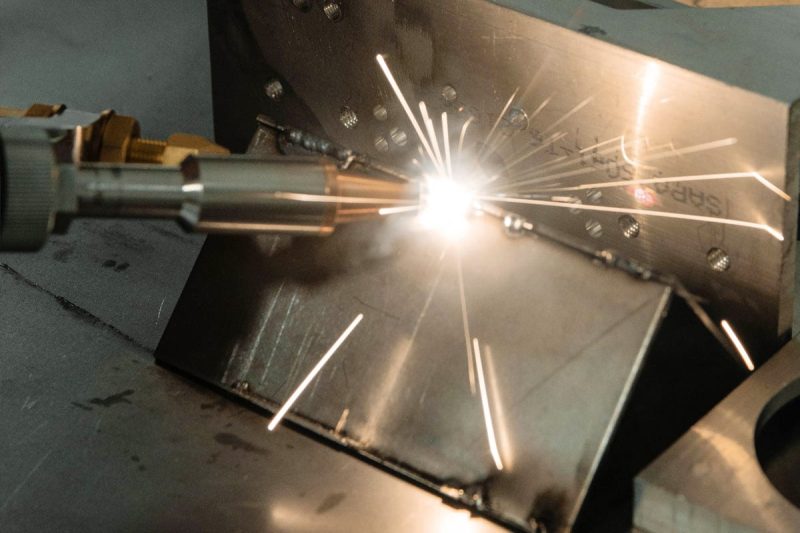
Condições ambientais
Temperatura ambiente
A temperatura ambiente pode afetar o processo de soldagem a laser de diversas maneiras. Manter um ambiente de temperatura controlada garante uma qualidade de solda consistente e evita problemas no equipamento.
- Desempenho consistente de soldagem: Temperaturas extremas, sejam muito altas ou muito baixas, podem afetar as características térmicas dos materiais que estão sendo soldados. Altas temperaturas ambientes podem resultar em entrada excessiva de calor e aumento de deformação térmica, enquanto baixas temperaturas podem causar resfriamento rápido e possíveis rachaduras.
- Estabilidade do equipamento: O equipamento de soldagem a laser, incluindo a fonte do laser e o sistema de resfriamento, funciona melhor dentro de uma faixa de temperatura específica:
- Alta Temperatura: O calor excessivo pode causar expansão térmica do material de solda, levando ao desalinhamento e deformação. Também pode afetar a taxa de resfriamento da solda, afetando a microestrutura e as propriedades mecânicas da junta.
- Baixa temperatura: Ambientes extremamente frios podem causar condensação na óptica do laser e nas superfícies dos materiais, interferindo na absorção do laser e podendo causar defeitos. Baixas temperaturas também podem afetar a condutividade térmica e o comportamento de fusão do material.
- Medidas de controle: A implementação de um sistema de controle climático no ambiente de soldagem pode ajudar a manter uma temperatura ambiente estável. Isto garante consistência no comportamento do material e no desempenho do equipamento, resultando em um processo de soldagem mais eficiente e confiável.
Umidade
Os níveis de umidade no ambiente de soldagem podem afetar tanto o equipamento laser quanto os materiais que estão sendo soldados.
- Condensação: A alta umidade pode causar a formação de condensação na óptica do laser e nas superfícies dos materiais. Isto pode dispersar o feixe de laser, reduzindo sua intensidade e precisão, e também pode introduzir contaminantes na solda.
- Oxidação e Corrosão: Materiais suscetíveis à oxidação e corrosão são afetados pela alta umidade. A presença de umidade pode acelerar esses processos, levando à contaminação da superfície e defeitos de solda.
- Comportamento do Material: Alguns materiais, especialmente aqueles que são sensíveis à umidade, podem apresentar alterações nas propriedades devido à umidade. Isto pode afetar a sua soldabilidade e a qualidade da solda final.
- Medidas de controle: Usar um desumidificador e garantir ventilação adequada pode ajudar a controlar os níveis de umidade. Manter a área de soldagem seca e livre de umidade pode manter condições ideais de soldagem.
Gás de proteção
O uso de gás de proteção pode ajudar a obter uma soldagem a laser bem-sucedida, protegendo a área de solda de contaminantes atmosféricos e melhorando a qualidade da solda.
- Tipos de gases de proteção: Os gases de proteção comuns usados na soldagem a laser incluem argônio, hélio, nitrogênio e misturas desses gases. A escolha do gás de proteção depende do material de solda e das características de solda exigidas.
- Argônio: O argônio é amplamente utilizado devido à sua inércia e oferece excelente proteção contra oxidação e contaminação. É adequado para soldar uma variedade de metais, incluindo aço, alumínio e titânio.
- Hélio: O hélio pode aumentar a penetração da solda e reduzir a porosidade, tornando-o ideal para soldas profundas e materiais de alta condutividade térmica, como cobre e alumínio.
- Nitrogênio: O nitrogênio é frequentemente usado em combinação com outros gases para melhorar a qualidade da solda em alguns materiais, mas deve ser usado com cautela devido à sua potencial reatividade com alguns metais.
- Fluxo e Cobertura: O fluxo e a cobertura do gás de proteção devem ser cuidadosamente controlados para garantir proteção adequada da área de solda. O fluxo de gás insuficiente pode causar contaminação e defeitos, enquanto o fluxo excessivo pode causar turbulência e problemas de resfriamento.
- Projeto do bocal: O projeto e o posicionamento do bocal de gás de proteção podem ajudar a obter uma cobertura de gás eficaz. O design adequado do bico garante um fluxo contínuo e uniforme de gás sobre a área de solda, melhorando a qualidade e a eficiência da solda.
Ventilação
A ventilação adequada da área de soldagem ajuda a manter um ambiente de soldagem seguro e eficiente.
- Extração de Fumos: A soldagem a laser produz fumos e gases prejudiciais ao operador e podem afetar o processo de soldagem. Um sistema eficaz de extração de fumos remove esses contaminantes da área de trabalho, garantindo um ambiente limpo e seguro.
- Controle do fluxo de ar: O fluxo de ar controlado ajuda a manter um ambiente de soldagem estável, evitando o acúmulo de fumos e mantendo uma cobertura consistente de gás na área de soldagem. Fluxo de ar descontrolado ou turbulência podem interromper o gás de proteção e afetar a qualidade da solda.
- Gerenciamento de calor: A ventilação ajuda a gerenciar o calor gerado durante o processo de soldagem. O fluxo de ar adequado evita o superaquecimento de materiais e equipamentos, reduzindo o risco de distorção térmica e falha do equipamento.
- Qualidade do Ar: Manter uma boa qualidade do ar no ambiente de soldagem evita o acúmulo de poeira e outras partículas que podem interferir no feixe de laser e no processo de soldagem. O ar limpo garante uma qualidade de feixe consistente e reduz o risco de defeitos.
- Medidas de segurança: Garantir uma ventilação adequada reduz o risco de exposição a vapores perigosos e melhora a segurança geral no local de trabalho. Também ajuda a manter a integridade da óptica do laser e de outros componentes sensíveis, evitando a contaminação e o acúmulo de partículas.
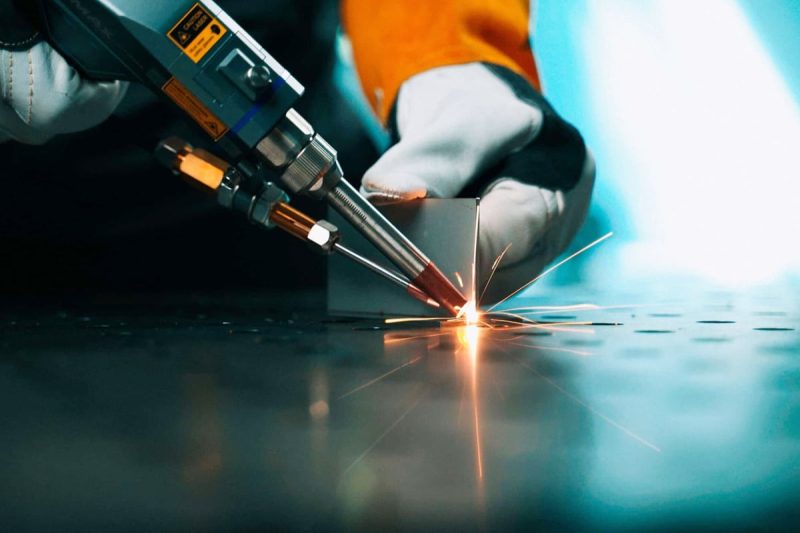
Velocidade de soldagem
Velocidade ideal de soldagem
Alcançar a velocidade de soldagem ideal é um equilíbrio delicado entre qualidade de solda e produtividade. A velocidade certa garante que os materiais sejam totalmente fundidos sem causar defeitos.
- Fusão Completa: Na velocidade ideal de soldagem, o laser fornece energia suficiente para derreter e fundir completamente os materiais. Isto produz uma solda forte, sem defeitos e com boas propriedades mecânicas.
- Qualidade Consistente: Velocidades de soldagem consistentes garantem entrada de calor uniforme ao longo da solda, resultando em qualidade de solda consistente. Variações de velocidade podem causar irregularidades que afetam a resistência e a aparência da solda.
Efeitos de altas velocidades de soldagem
Altas velocidades de soldagem podem melhorar a produtividade, mas apresentam desafios específicos e possíveis desvantagens.
- Maior produtividade: Velocidades de soldagem mais altas reduzem o tempo do ciclo, permitindo que mais soldas sejam concluídas em um determinado tempo. Isto é particularmente benéfico em ambientes de produção de alto volume.
- Defeitos potenciais: Soldar em uma velocidade muito rápida pode resultar em entrada de calor insuficiente, o que pode levar a fusão incompleta, soldas fracas e possíveis rachaduras. O movimento rápido pode não permitir tempo suficiente para que os materiais derretam e se unam adequadamente.
- Irregularidades de superfície: Em velocidades muito altas, a poça de fusão pode não ter tempo suficiente para assentar, resultando em irregularidades de superfície, como ondulações e respingos.
Efeitos de baixas velocidades de soldagem
Embora velocidades de soldagem mais lentas possam melhorar a qualidade da solda, existem certas limitações e considerações.
- Penetração melhorada: Velocidades de soldagem mais lentas aumentam a entrada de calor por unidade de comprimento de solda, o que melhora a penetração e garante a fusão completa de materiais mais espessos.
- Aumento da Zona Afetada pelo Calor (HAZ): Velocidades mais lentas resultam em entrada excessiva de calor, o que resulta em uma HAZ maior. Isto pode causar distorção térmica, propriedades mecânicas reduzidas e possível empenamento do componente soldado.
- Produtividade reduzida: Velocidades de soldagem mais lentas reduzem a produtividade e aumentam o tempo total necessário para concluir uma tarefa de soldagem. Em um ambiente de produção de alto volume, isso pode ser uma desvantagem significativa.
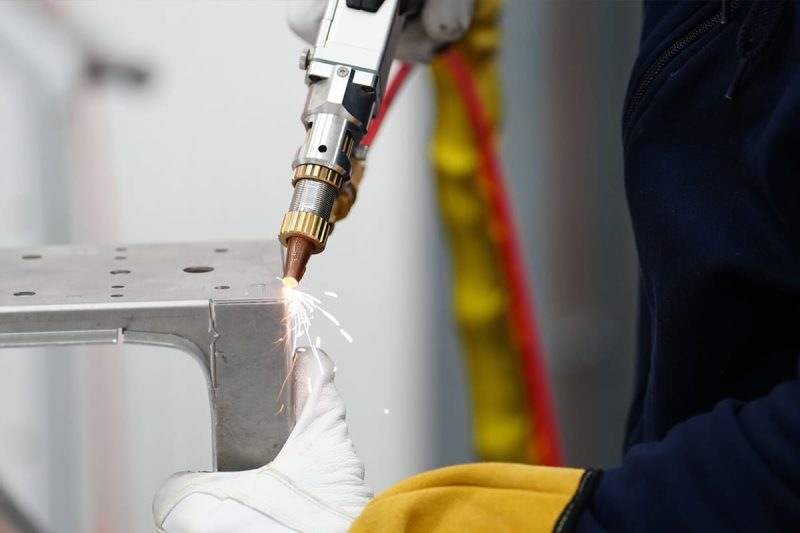
Habilidades e experiência do operador
Importância das habilidades e experiência do operador
A proficiência do operador é crítica por vários motivos, incluindo a configuração adequada do equipamento de soldagem, ajustes precisos de parâmetros e a capacidade de identificar e resolver rapidamente problemas que possam surgir durante o processo de soldagem.
- Configuração e calibração: Operadores qualificados são adeptos da configuração e calibração de equipamentos de soldagem a laser. Isso inclui alinhar o laser, ajustar o foco, definir a potência do laser apropriada e configurar o fluxo do gás de proteção. A configuração adequada garante que o processo de soldagem comece com a base correta, minimizando o risco de defeitos e ineficiências.
- Ajuste de parâmetros: Operadores experientes possuem um profundo conhecimento da relação entre os parâmetros de soldagem e a qualidade da solda. Eles podem fazer ajustes precisos em parâmetros como velocidade de soldagem, potência do laser e frequência de pulso para otimizar o processo de soldagem para diferentes materiais e configurações de juntas.
- Solução de problemas e solução de problemas: Durante o processo de soldagem, diversos problemas podem ocorrer, como desalinhamento, má penetração ou formação de defeitos como porosidade e rachaduras. Operadores qualificados podem diagnosticar rapidamente esses problemas e implementar ações corretivas, garantindo tempo de inatividade mínimo e qualidade de solda consistente.
- Adaptabilidade ao processo: Diferentes materiais, configurações de juntas e tarefas de soldagem requerem ajustes específicos. Operadores experientes podem ajustar os parâmetros do processo para atender diferentes condições, garantindo uma qualidade de solda consistente em todas as aplicações.
Treinamento e Certificação
O treinamento e a certificação adequados ajudam a desenvolver e manter um alto nível de habilidades do operador. O programa de treinamento abrangente deve abranger:
- Conhecimento Teórico: É fundamental compreender os princípios da soldagem a laser, incluindo a interação entre a energia do laser e os materiais. Os operadores devem estar bem familiarizados com a ciência por trás do processo para tomar decisões informadas.
- Experiência prática: O treinamento prático com equipamentos de soldagem a laser permite que os operadores ganhem experiência na configuração, calibração e operação da máquina. A experiência prática ajuda a construir confiança e competência no mundo real.
- Protocolos de segurança: A soldagem a laser envolve riscos potenciais, incluindo luz intensa, fumaça e calor. A formação deve enfatizar os protocolos de segurança para proteger os operadores e garantir um ambiente de trabalho seguro.
- Programas de Certificação: Os programas de certificação validam as habilidades e conhecimentos dos operadores, reconhecendo formalmente sua experiência. Operadores certificados geralmente são mais capazes de lidar com tarefas complexas de soldagem e solucionar problemas de maneira eficaz.
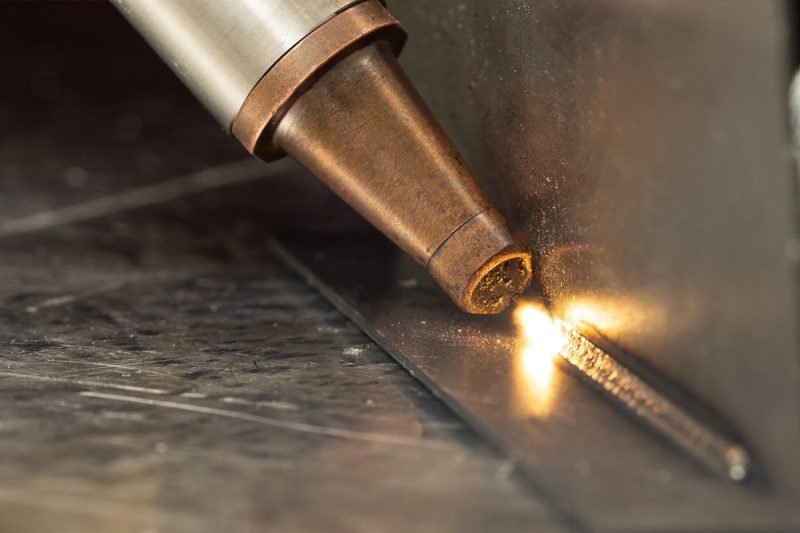
Equipamentos e Manutenção
Fonte Laser
A fonte do laser é o coração de um sistema de soldagem a laser de fibra, produzindo o feixe de alta intensidade necessário para soldagem.
- Lasers de fibra: Conhecidos por sua alta eficiência, excelente qualidade de feixe e robustez, os lasers de fibra são ideais para soldar uma ampla variedade de materiais, incluindo metais refletivos, como alumínio e cobre.
- Manutenção: Monitore regularmente a saída de energia para garantir um desempenho consistente, limpe a óptica para evitar contaminação e verifique o alinhamento para manter a precisão do feixe.
Óptica
A óptica direciona e foca o feixe de laser para a área de solda, garantindo um fornecimento preciso de energia.
- Sistema de entrega de feixe: Inclui fibra óptica e colimador para entregar o feixe de laser com perdas mínimas.
- Óptica de Focagem: Lentes ou cabeças de focagem que concentram o feixe de laser em um tamanho de ponto pequeno, aumentando assim a densidade de energia.
- Manutenção: A limpeza regular de lentes, espelhos e janelas de proteção, a inspeção de danos e as verificações de alinhamento podem ajudar a manter a qualidade ideal do feixe.
Sistema de movimento
O sistema de movimento controla o movimento do feixe de laser e da peça de trabalho, garantindo posicionamento preciso e operação suave.
- Tipos: Sistemas cartesianos para movimento linear de três eixos, braços robóticos para movimento multieixos e sistemas de pórtico para aplicações em larga escala.
- Manutenção: A lubrificação regular das peças móveis, a calibração regular para movimentos precisos e a verificação de desgaste ou desalinhamento ajudam a garantir uma operação confiável.
Sistema de refrigeração
O sistema de resfriamento evita o superaquecimento da fonte do laser e de outros componentes importantes e mantém uma operação estável.
- Resfriamento a água: É frequentemente usado em geradores de laser de fibra de alta potência devido ao seu bom efeito de dissipação de calor.
- Componentes: Bombas, trocadores de calor e reservatórios de refrigerante são elementos-chave do sistema de refrigeração.
- Manutenção: Verifique regularmente se há vazamentos e bloqueios, monitore a qualidade do líquido refrigerante e substitua os filtros conforme necessário para garantir um resfriamento eficiente.
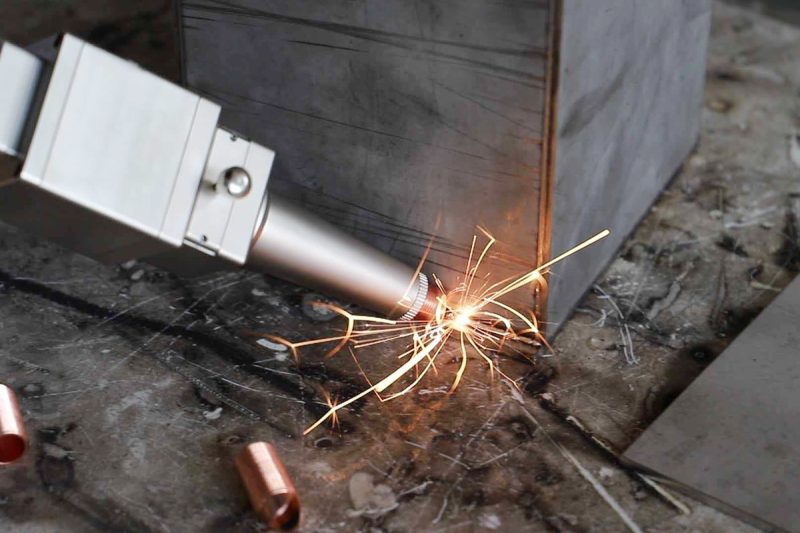
Sistemas de Automação e Controle
Monitoramento em tempo real
Os sistemas de monitoramento em tempo real fornecem feedback contínuo sobre o processo de soldagem, permitindo que ajustes sejam feitos imediatamente para garantir um desempenho ideal.
- Monitoramento da qualidade da solda: Sensores e câmeras monitoram a poça de fusão, detectando defeitos como porosidade, trincas e desalinhamentos em tempo real. Isso permite que o operador ajuste a potência, a velocidade e o foco do laser em tempo real.
- Monitoramento de potência do laser: O sistema rastreia continuamente a saída de potência do laser para garantir que ela permaneça dentro da faixa desejada. Isso ajuda a manter o fornecimento consistente de energia e a penetração da solda.
Controle Adaptativo
Os sistemas de controle adaptativos ajustam dinamicamente os parâmetros de soldagem com base em dados em tempo real para otimizar o processo para condições variadas.
- Ajuste de parâmetros: Esses sistemas ajustam automaticamente a potência do laser, a velocidade de soldagem e a posição do foco com base nas alterações nas propriedades do material, espessura e configuração da junta. Isso garante qualidade de soldagem uniforme e consistente em diferentes partes da peça.
- Loops de feedback: A incorporação de loops de feedback permite que o sistema aprenda com soldas anteriores, melhorando a precisão e a eficiência ao longo do tempo.
Integração com Sistemas Robóticos
A integração da soldagem a laser de fibra com sistemas robóticos aumenta a automação, flexibilidade e repetibilidade.
- Movimento multieixo: O braço robótico fornece movimento multieixo para soldagem precisa de geometrias complexas e áreas de difícil acesso.
- Qualidade Constante: O robô garante uma qualidade de solda consistente controlando com precisão o caminho, a velocidade e o ângulo da solda, reduzindo as variações associadas à soldagem manual.
- Aumente o rendimento: a automação robótica aumenta o rendimento, permitindo a operação contínua e reduzindo os tempos de ciclo, resultando em ganhos significativos de produtividade.
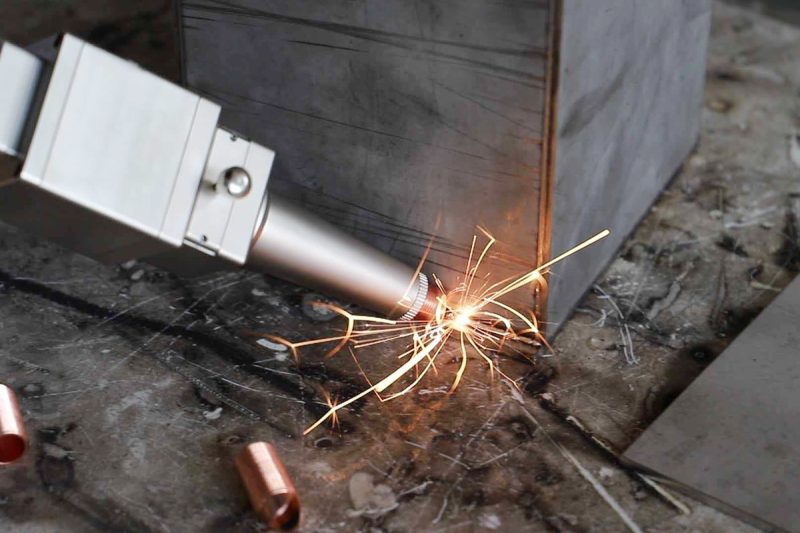
Considerações Específicas da Aplicação
Combinações de materiais
Diferentes materiais reagem de forma única à soldagem a laser e suas combinações podem apresentar desafios específicos.
- Materiais diferentes: Soldar materiais diferentes, como alumínio e aço, pode ser um desafio devido às diferenças nos pontos de fusão, condutividades térmicas e taxas de absorção do laser. Os lasers de fibra são eficazes na soldagem dessas combinações, mas exigem controle preciso sobre os parâmetros para gerenciar a entrada de calor e evitar defeitos.
- Materiais reflexivos: Materiais como cobre e alumínio refletem uma porção significativa da energia do laser, o que pode reduzir a eficiência da soldagem. Os lasers de fibra, particularmente com comprimentos de onda mais curtos, são mais adequados para estes materiais, mas a otimização dos parâmetros do laser é essencial para garantir uma absorção eficaz de energia.
- Ligas e Compósitos: Cada liga ou material compósito pode exigir configurações específicas para uma soldagem ideal. Compreender as propriedades do material e ajustar a potência, a velocidade e o foco do laser de acordo é fundamental para obter soldas de alta qualidade.
Geometria de soldagem
A geometria da junta soldada afeta o processo de soldagem e deve ser cuidadosamente considerada para garantir a eficiência.
- Geometrias Complexas: A soldagem de geometrias complexas, como formas curvas ou complexas, requer controle preciso do feixe de laser e do sistema de movimento. Os lasers de fibra podem lidar com essas geometrias com eficácia quando integrados a sistemas de movimento avançados e braços robóticos.
- Seções Finas VS Grossas: A soldagem de seções finas requer menor potência e maior precisão para evitar queimaduras, enquanto seções grossas requerem maior potência e velocidades mais baixas para penetrar totalmente. Ajustar os parâmetros do laser para geometrias específicas pode alcançar uma soldagem eficiente.
- Preparação das bordas: A preparação adequada das bordas, como chanfro ou limpeza, garante melhor ajuste e fusão. Manter a qualidade consistente das arestas pode ajudar a obter soldas uniformes.
Volume de produção
O volume de produção afeta a escolha do equipamento de soldagem a laser e os parâmetros do processo.
- Produção de pequenos lotes ou personalizada: Para produção de pequenos lotes ou personalizada, flexibilidade e adaptabilidade são fundamentais. A versatilidade dos lasers de fibra permite o ajuste rápido dos parâmetros e configurações de soldagem, tornando-os adequados para uma variedade de tarefas especializadas de soldagem.
- Produção de alto volume: A produção de alto volume requer consistência, velocidade e automação. Os sistemas de laser de fibra integrados com sistemas de controle automatizados e braços robóticos fornecem a precisão e a repetibilidade necessárias, aumentando significativamente a produção e a eficiência.
- Otimização do tempo de ciclo: Em um ambiente de produção, minimizar o tempo de ciclo pode melhorar a eficiência. Os sistemas de laser de fibra equipados com monitoramento em tempo real e controle adaptativo podem reduzir o tempo de configuração e garantir velocidades de soldagem ideais, aumentando assim a produtividade geral.
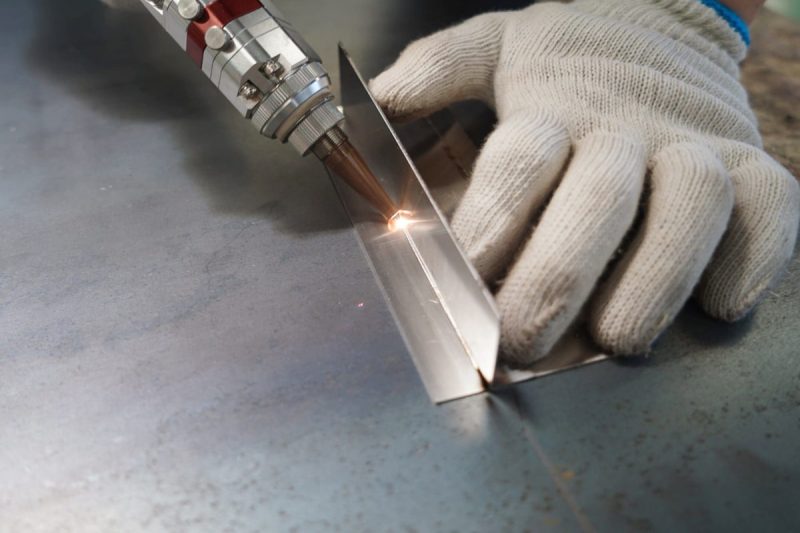
Resumo
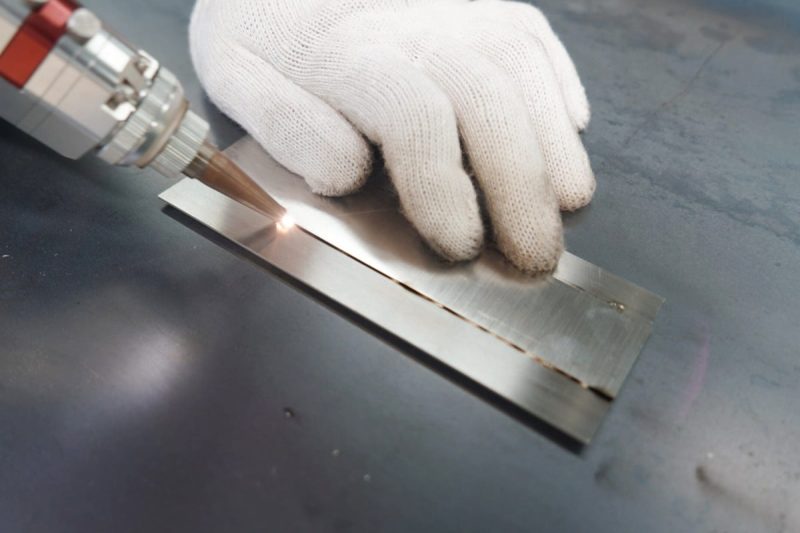
Obtenha soluções de soldagem a laser
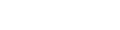
- [email protected]
- [email protected]
- +86-19963414011
- No. 3 Zona A, Zona Industrial de Lunzhen, Cidade de Yucheng, Província de Shandong.