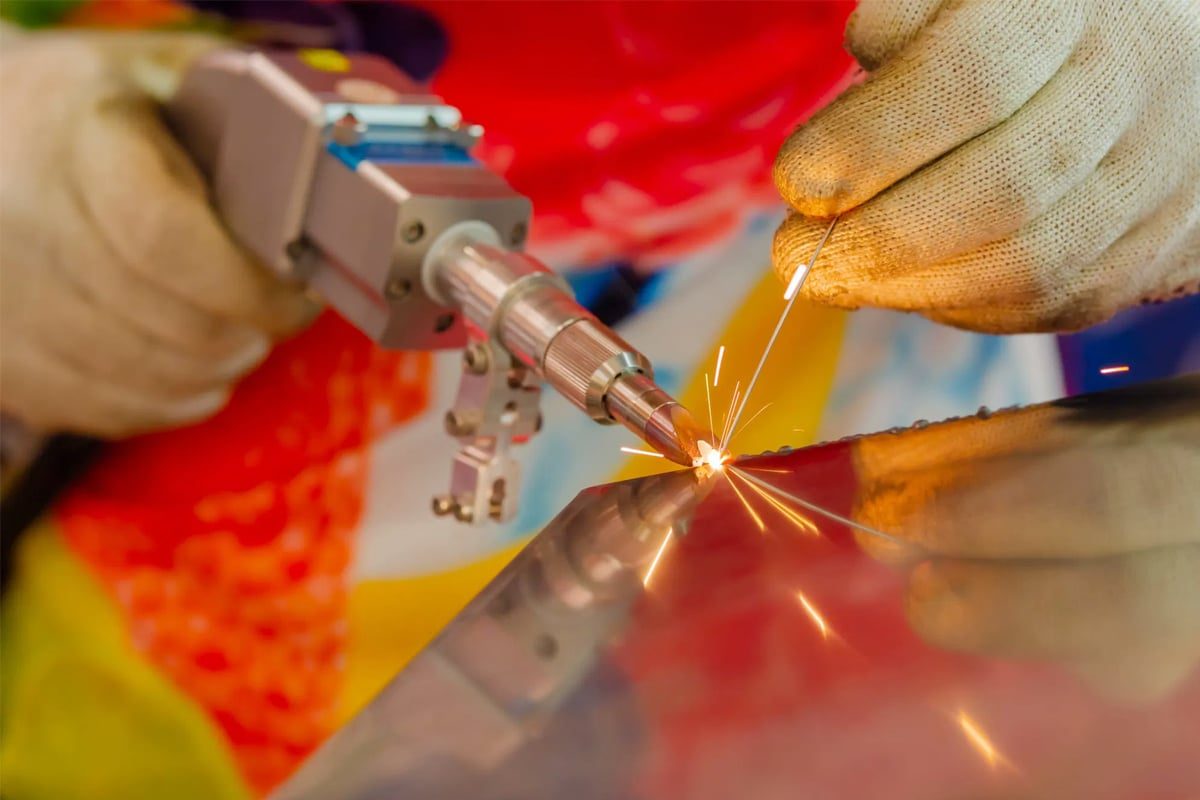
Quais são os fatores que afetam a espessura da soldagem a laser
Na soldagem a laser, controlar a espessura da solda é essencial para garantir a resistência, durabilidade e qualidade estética da junta. A espessura de uma solda a laser é influenciada por uma variedade de fatores, desde configurações do laser como potência, foco do feixe e velocidade até as propriedades físicas e químicas do material que está sendo soldado. Além disso, o design da junta, a escolha do gás de proteção e as condições ambientais no espaço de trabalho desempenham papéis críticos na determinação da profundidade de penetração do laser no material e no perfil geral da solda. Ao otimizar esses fatores, os fabricantes podem obter espessura de solda precisa, o que é especialmente importante em indústrias onde precisão e consistência são cruciais, como automotiva, aeroespacial e eletrônica. Este artigo explora as muitas variáveis que afetam a espessura da solda na soldagem a laser, oferecendo insights sobre como os ajustes nos parâmetros do processo e materiais podem impactar a profundidade e a qualidade da solda.
Índice
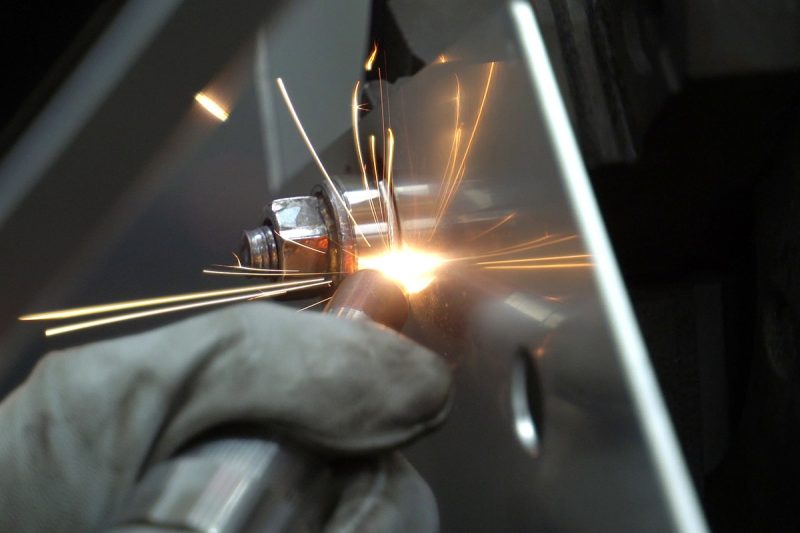
Compreendendo a soldagem a laser
A soldagem a laser depende de um feixe de laser focado como uma fonte de calor intensa para unir materiais, principalmente metais. O feixe de laser, normalmente produzido por uma fonte de laser como uma fibra, CO2 ou laser de estado sólido, é focado na superfície do material. A energia intensa do laser aquece e derrete rapidamente a área alvo, criando uma poça derretida que funde as peças. Conforme o laser se move ao longo da junta, a poça derretida se solidifica, resultando em uma solda contínua.
A alta densidade de energia do laser permite penetração precisa e profunda com zonas afetadas pelo calor (HAZ) mínimas, reduzindo a distorção térmica em comparação aos métodos de soldagem convencionais. A soldagem a laser pode ser realizada em diferentes ambientes, incluindo câmaras de vácuo, atmosferas de gás inerte ou ao ar livre, dependendo da aplicação específica e dos requisitos do material. Essa versatilidade e precisão tornam a soldagem a laser altamente eficaz para geometrias e materiais complexos com propriedades térmicas variadas.
Noções básicas do processo de soldagem a laser
O processo de soldagem a laser normalmente envolve três etapas principais: preparação pré-soldagem, interação laser-material e resfriamento e solidificação pós-soldagem.
- Preparação pré-soldagem: Antes da soldagem, as superfícies dos materiais devem estar limpas, livres de contaminantes e alinhadas adequadamente. Contaminantes como óleos, óxidos ou detritos podem interferir na absorção de energia e reduzir a qualidade da solda.
- Interação Laser-Material: Durante a soldagem, o feixe de laser é focado na peça de trabalho, onde sua energia é absorvida pela superfície, levando à fusão localizada. Existem dois modos primários de interação laser-material:
- Soldagem por Condução: Isso ocorre quando a densidade de potência do laser é relativamente baixa, causando derretimento da superfície sem vaporização. O calor é conduzido para dentro do material, resultando em soldas rasas e largas. Este modo é frequentemente usado para aplicações que priorizam estética e baixa entrada de calor.
- Soldagem Keyhole: Quando a densidade de potência do laser é alta o suficiente para vaporizar o material, ela forma um keyhole ou cavidade de vapor dentro da poça derretida. O keyhole permite que a energia do laser penetre profundamente, criando soldas estreitas e profundas com uma alta relação de aspecto. A soldagem Keyhole é bem adequada para materiais espessos e aplicações que exigem juntas fortes.
- Resfriamento e solidificação pós-soldagem: Conforme o laser se move ao longo da junta de solda, a poça derretida se solidifica, formando uma ligação contínua entre os materiais. A taxa de resfriamento adequada pode evitar defeitos como rachaduras ou tensões residuais e atingir as propriedades mecânicas desejadas da solda.
A soldagem a laser oferece alta precisão, distorção mínima e a capacidade de produzir juntas limpas e robustas. No entanto, fatores como potência do laser, foco do feixe, velocidade de soldagem e características do material devem ser cuidadosamente controlados para atingir a espessura e a qualidade de solda desejadas, tornando a soldagem a laser um processo complexo e altamente adaptável para a fabricação moderna.
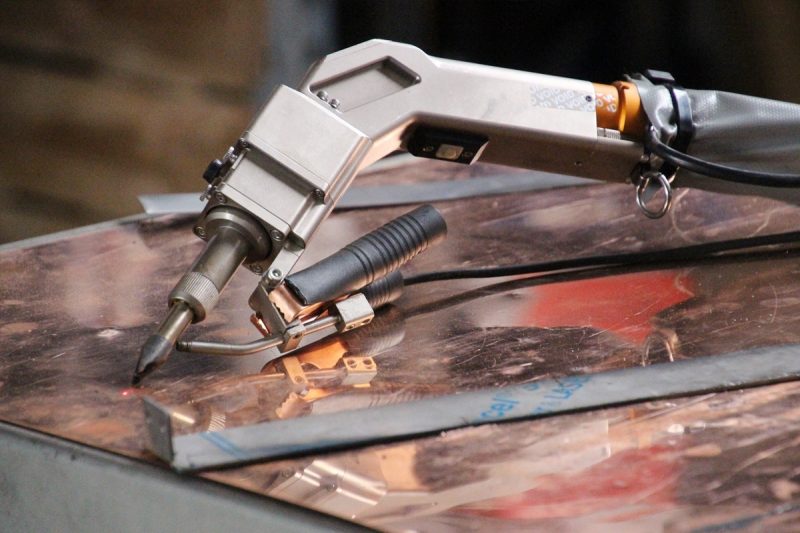
Aplicações da soldagem a laser
A soldagem a laser se tornou uma tecnologia fundamental em várias indústrias, devido à sua precisão, velocidade e capacidade de produzir soldas consistentes e de alta qualidade com distorção térmica mínima. À medida que as demandas de fabricação evoluem, a versatilidade e a adaptabilidade da soldagem a laser continuam a torná-la uma ferramenta inestimável.
- Indústria automotiva: No setor automotivo, a soldagem a laser é amplamente usada para montar carrocerias de automóveis, componentes de motor, engrenagens de transmissão, sistemas de escapamento e módulos de bateria para veículos elétricos. O processo permite juntas fortes e de alta precisão, ao mesmo tempo em que minimiza o peso dos componentes. A capacidade da soldagem a laser de unir materiais diferentes, como alumínio e aço, a torna especialmente útil para projetos de veículos leves e com eficiência energética.
- Indústria aeroespacial: A soldagem a laser é vital na indústria aeroespacial devido à sua capacidade de criar juntas precisas e de alta resistência para componentes críticos como lâminas de turbina, armações estruturais e tanques de combustível. Sua zona mínima afetada pelo calor ajuda a manter a integridade estrutural de materiais aeroespaciais leves e sensíveis ao calor, como ligas de titânio e compostos. A precisão da soldagem a laser garante a conformidade com padrões rigorosos de segurança e desempenho.
- Energia e geração de energia: No setor de energia, a soldagem a laser é usada para fabricar componentes para turbinas eólicas, painéis solares, equipamentos de petróleo e gás e usinas nucleares. A capacidade de produzir soldas fortes e sem defeitos garante confiabilidade e segurança em ambientes de alta pressão e alta temperatura. A soldagem a laser também dá suporte à fabricação de trocadores de calor, tubos e vasos de alta pressão.
- Indústria Naval e Marinha: A indústria naval se beneficia da capacidade da soldagem a laser de produzir soldas fortes e resistentes à corrosão. Ela é usada para unir chapas de aço estruturais, componentes de casco e acessórios internos. O processo reduz o peso geral das embarcações marítimas, aumenta a eficiência de combustível e suporta projetos complexos com alta precisão.
- Eletrônicos de consumo e eletrodomésticos: A soldagem a laser é empregada na montagem de eletrônicos de consumo, como smartphones, tablets e eletrodomésticos. Ela garante juntas confiáveis e esteticamente atraentes em invólucros de metal, conectores e baterias. O processo suporta linhas de produção automatizadas de alta velocidade, aumentando a produtividade e a consistência.
- Indústria de Alimentos e Bebidas: A soldagem a laser é usada na indústria de alimentos e bebidas para produzir equipamentos de aço inoxidável, como tubos, equipamentos de cervejaria e máquinas de envase. As soldas higiênicas e sem emendas produzidas pela soldagem a laser previnem o crescimento bacteriano e simplificam os processos de limpeza, tornando-a ideal para aplicações de grau alimentício.
- Construção e Arquitetura: A soldagem a laser encontra aplicações nos setores de construção e arquitetura para criar estruturas metálicas fortes e esteticamente agradáveis. É usada para fabricar vigas estruturais, elementos decorativos, fachadas e muito mais. A precisão e a velocidade do processo permitem a criação de designs personalizados e geometrias complexas.
- Agricultura e Maquinário Pesado: A indústria agrícola depende da soldagem a laser para fabricar componentes robustos para máquinas e equipamentos, como arados, tratores e carregadeiras. As juntas soldadas a laser fornecem alta resistência e durabilidade para suportar condições operacionais severas.
As diversas aplicações da soldagem a laser em todas as indústrias destacam seu papel como uma ferramenta crítica para a fabricação e engenharia modernas. A capacidade de controlar a espessura e a qualidade das soldas com precisão garante que a soldagem a laser atenda às demandas exigentes de produtos de alto desempenho, montagens complexas e padrões regulatórios rigorosos.
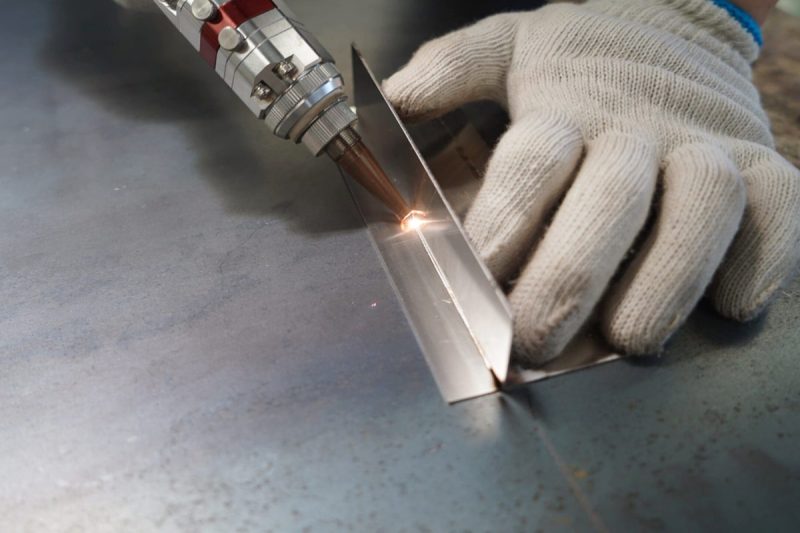
Fatores que afetam a espessura da soldagem a laser
Atingir a espessura desejada na soldagem a laser é um processo complexo influenciado por vários fatores. Cada um desses fatores impacta diretamente a profundidade de penetração, qualidade e integridade da solda. Entender essas variáveis permite que os fabricantes adaptem o processo de soldagem a laser para espessura, resistência e precisão ideais.
Potência do Laser
- Impacto na Espessura da Solda: A potência do laser é um dos fatores mais críticos na determinação da espessura da solda. Maior potência do laser aumenta a entrada de energia, permitindo penetração mais profunda e soldas mais espessas. Por outro lado, níveis de potência mais baixos produzem soldas mais rasas, que podem ser mais adequadas para materiais finos ou aplicações onde a entrada mínima de calor é necessária.
- Otimização: Ajustar a potência do laser de acordo com a espessura do material e a profundidade de penetração desejada garante a utilização efetiva da energia. Para materiais mais espessos ou soldas profundas, deve-se aplicar potência suficiente para atingir a penetração necessária sem causar zonas afetadas pelo calor (HAZ) excessivas.
Velocidade de soldagem
- Impacto na Espessura da Solda: A velocidade de soldagem, ou a taxa na qual o laser se move ao longo da junta, influencia significativamente a espessura da solda. Uma velocidade de soldagem mais lenta permite que mais energia do laser seja absorvida pelo material, resultando em soldas mais espessas e profundas. Por outro lado, velocidades mais rápidas reduzem a entrada de calor, levando a soldas mais rasas.
- Otimização: Equilibrar a velocidade de soldagem com a potência do laser é essencial para atingir a espessura desejada. Velocidades excessivamente lentas podem levar a superaquecimento e defeitos, enquanto altas velocidades podem resultar em fusão incompleta ou falta de penetração.
Posição Focal
- Impacto na Espessura da Solda: A posição focal do feixe de laser afeta onde a energia é concentrada na peça de trabalho. Focar o feixe precisamente na superfície do material ou ligeiramente abaixo dela pode aumentar a profundidade de penetração, resultando em soldas mais espessas. O desalinhamento do ponto focal pode levar à penetração inconsistente ou insuficiente.
- Otimização: Ao ajustar o ponto focal de acordo com a espessura do material e o modo de soldagem (condução ou keyhole), os fabricantes podem obter uma espessura de solda mais controlada. O foco preciso melhora a concentração de energia e garante profundidade consistente.
Qualidade e modo do feixe
- Impacto na espessura da solda: A qualidade e o modo do feixe (TEM00, TEM01, etc.) afetam como a energia do laser é distribuída pela área de trabalho. Um feixe monomodo de alta qualidade (TEM00) fornece um ponto mais focado e intenso, permitindo penetração mais profunda e soldas mais espessas. Feixes multimodo, por outro lado, podem levar a soldas mais amplas, mas mais rasas, devido à propagação de energia.
- Otimização: Selecionar um laser com a qualidade de feixe e modo apropriados melhora o controle sobre a espessura da solda. Para aplicações que exigem soldas profundas e estreitas, um laser monomodo de alta qualidade é ideal.
Propriedades do Material
- Impacto na Espessura da Solda: Diferentes materiais respondem à energia do laser de forma diferente com base em propriedades como condutividade térmica, ponto de fusão e refletividade. Por exemplo, metais com alta condutividade térmica, como alumínio e cobre, dissipam calor rapidamente, exigindo maior potência do laser para atingir a penetração desejada. Materiais com alta refletividade também podem reduzir a absorção de energia, afetando a espessura.
- Otimização: Entender as propriedades específicas do material ajuda a ajustar os parâmetros do laser para atingir a espessura do alvo. Por exemplo, materiais refletivos podem se beneficiar de tratamentos de superfície para melhorar a absorção ou exigir maior potência para penetração efetiva.
Pré-aquecimento
- Impacto na Espessura da Solda: Pré-aquecer o material antes da soldagem pode reduzir gradientes térmicos, permitindo penetração mais suave e soldas mais espessas. Também minimiza o risco de rachaduras em materiais propensos a estresse térmico, como aços de alto carbono.
- Otimização: O pré-aquecimento ajuda a atingir espessura consistente, especialmente em seções mais espessas, onde o resfriamento rápido poderia levar a defeitos. O grau de pré-aquecimento deve ser controlado para evitar entrada térmica excessiva.
Condição da superfície
- Impacto na Espessura da Solda: A condição da superfície do material, incluindo limpeza e oxidação, impacta a absorção e penetração de energia. Contaminantes como óleos, óxidos e sujeira podem reduzir a absorção de energia do laser, levando a espessura inconsistente e soldas mais fracas.
- Otimização: A limpeza e preparação da superfície antes da soldagem garantem que a energia do laser seja efetivamente absorvida, levando a uma espessura controlada. Tratamentos de superfície, como esmerilhamento ou jateamento de areia, também podem melhorar a qualidade da solda.
Gás de proteção e gás auxiliar
- Impacto na Espessura da Solda: Gás de proteção (como argônio, hélio ou nitrogênio) protege a poça de solda da contaminação atmosférica e pode influenciar a penetração e a espessura da solda. Gases diferentes têm propriedades térmicas variadas, que afetam a entrada de calor e as características da solda. Gases auxiliares, frequentemente usados no corte, também podem desempenhar um papel na manutenção de uma poça de solda estável.
- Otimização: Escolher o gás de proteção apropriado melhora a penetração da solda. Por exemplo, o hélio, com alta condutividade térmica, pode aumentar a penetração, afetando a espessura da solda. Ajustar as taxas de fluxo de gás garante proteção suficiente sem introduzir turbulência ou defeitos.
Modo de soldagem (condução x buraco de fechadura)
- Impacto na Espessura da Solda: A soldagem a laser pode ocorrer em modo de condução ou buraco de fechadura, cada um dos quais afeta a espessura de solda atingível. A soldagem por condução produz soldas largas e rasas, adequadas para aplicações de nível de superfície, enquanto a soldagem por buraco de fechadura cria soldas profundas e estreitas, ideais para materiais mais espessos.
- Otimização: Selecionar o modo de soldagem apropriado permite controle preciso sobre a espessura. O modo de condução é usado quando soldas de superfície estéticas são necessárias, enquanto o modo keyhole é ideal para aplicações que exigem maior profundidade de penetração.
Configuração Conjunta
- Impacto na Espessura da Solda: A configuração da junta, como junta de topo, sobreposta ou T, afeta como a energia do laser interage com os materiais e determina a espessura atingível. Por exemplo, juntas de topo permitem soldagem de penetração total, enquanto juntas de sobreposta podem exigir mais potência do laser para profundidade equivalente.
- Otimização: A escolha da configuração correta da junta com base na espessura do material e nos requisitos da aplicação garante uma distribuição eficaz de energia e espessura da solda.
Comprimento de onda do laser
- Impacto na Espessura da Solda: O comprimento de onda do laser impacta a eficiência com que o material absorve energia. Por exemplo, comprimentos de onda mais curtos, como os de lasers de fibra, são absorvidos melhor por metais do que comprimentos de onda mais longos de lasers de CO2, afetando a profundidade de penetração e a espessura da solda.
- Otimização: Selecionar um laser com comprimento de onda que corresponda às características de absorção do material garante o uso eficiente de energia, permitindo uma espessura de solda ideal.
Processamento pré e pós-soldagem
- Processamento Pré-Soldagem: Preparação de superfície, limpeza e alinhamento antes da soldagem melhoram a absorção de energia do laser, resultando em espessura consistente. Quaisquer contaminantes ou desalinhamentos podem causar defeitos ou penetração inconsistente.
- Processamento Pós-Soldagem: Tratamentos pós-soldagem, como tratamento térmico ou resfriamento controlado, influenciam a estrutura e a estabilidade da solda. Taxas de resfriamento controladas ajudam a manter a espessura uniforme, prevenindo tensão residual ou empenamento.
- Otimização: O processamento adequado pré e pós-soldagem melhora a qualidade da solda, permitindo espessura de solda e propriedades mecânicas consistentes.
Cada um desses fatores desempenha um papel crucial na determinação da espessura e qualidade das soldas a laser. Ao ajustar e otimizar cuidadosamente cada variável, os fabricantes podem atingir as espessuras de solda desejadas, garantindo que a soldagem a laser atenda aos requisitos rigorosos de várias aplicações industriais.
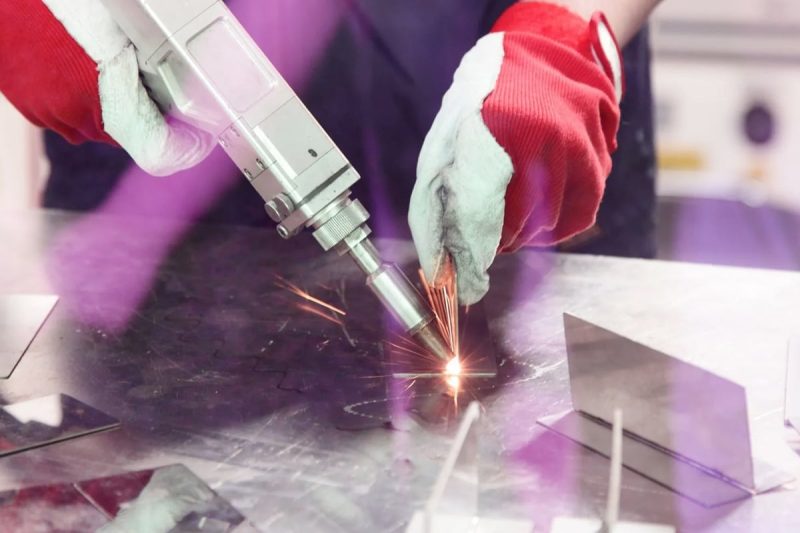
Otimizando a espessura da solda
Otimizar a espessura da soldagem a laser envolve equilibrar cuidadosamente múltiplos parâmetros de processo e empregar estratégias para controle preciso. Alcançar a espessura de solda desejada é essencial para garantir a resistência da solda, minimizar defeitos e atender às especificações do projeto.
Ajuste de Parâmetros de Processo
Ajuste de potência do laser
- Impacto: A potência do laser afeta diretamente a profundidade de penetração e a espessura da solda. Aumentar a potência fornece mais energia ao banho de solda, permitindo soldas mais profundas e espessas, enquanto reduzir a potência resulta em penetração mais rasa.
- Estratégia de Otimização: Para atingir a espessura de solda ideal, a potência do laser deve ser cuidadosamente ajustada com base nas propriedades do material, configuração da junta e requisitos de espessura. Potência excessiva pode levar a defeitos como porosidade ou derretimento excessivo, então é crucial encontrar um equilíbrio que maximize a penetração enquanto minimiza os efeitos indesejados.
Controle de velocidade de soldagem
- Impacto: A velocidade de soldagem determina a quantidade de tempo que o laser interage com o material. Velocidades mais lentas aumentam a absorção de energia, resultando em soldas mais profundas e espessas, enquanto velocidades mais rápidas reduzem a entrada de calor e produzem soldas mais finas.
- Estratégia de Otimização: Ajustar a velocidade de soldagem em conjunto com a potência do laser garante espessura consistente. Velocidades mais lentas podem ser usadas para materiais mais espessos ou penetração mais profunda, mas devem ser controladas para evitar superaquecimento ou zonas excessivamente afetadas pelo calor.
Ajuste da posição focal
- Impacto: A posição do foco do laser em relação à superfície do material afeta a concentração de energia. Um feixe focado na superfície ou ligeiramente abaixo dela maximiza a penetração e aumenta a espessura da solda, enquanto uma posição focal alinhada incorretamente pode levar a resultados inconsistentes.
- Estratégia de Otimização: O ajuste preciso do ponto focal garante entrega de energia consistente à peça de trabalho, aumentando a espessura da solda. Ajustes de posição focal podem ser necessários para diferentes materiais ou configurações de junta para atingir os resultados desejados.
Otimização da qualidade e do modo do feixe
- Impacto: Feixes de laser de alta qualidade com uma estrutura de modo estável oferecem melhor concentração de energia, resultando em soldas mais profundas e controladas.
- Estratégia de Otimização: Garantir o uso de feixes de alta qualidade e selecionar o modo de feixe apropriado ajuda a atingir espessura de solda precisa e consistente. Manter a saída de laser estável e a qualidade do feixe por meio de manutenção regular do equipamento é essencial.
Blindagem e fluxo de gás auxiliar
- Impacto: O tipo e a vazão do gás de proteção influenciam a estabilidade e a penetração da poça de solda. A proteção adequada protege contra contaminação e pode aumentar a absorção de energia, enquanto os gases auxiliares ajudam a manter um ambiente de solda estável.
- Estratégia de Otimização: Selecionar o gás de proteção apropriado (por exemplo, argônio, hélio ou nitrogênio) e ajustar as taxas de fluxo para garantir penetração e espessura de solda ideais. O gás de proteção deve ser adaptado ao material e às condições de soldagem para maximizar sua eficácia.
Taxas de pré-aquecimento e resfriamento
- Impacto: Materiais de pré-aquecimento reduzem gradientes térmicos, melhorando a absorção de energia e penetração. Taxas de resfriamento afetam o processo de solidificação e a estrutura da solda.
- Estratégia de otimização: a implementação de pré-aquecimento controlado e resfriamento pós-soldagem garante espessura uniforme e minimiza o risco de defeitos como rachaduras ou empenamentos.
Estratégias de Controle
Mapeamento e Simulação de Processos
Desenvolver um mapa de processo que correlaciona parâmetros do laser (por exemplo, potência, velocidade, posição focal) com a espessura da solda ajuda a identificar configurações ótimas para diferentes materiais e configurações de junta. O software de simulação de soldagem pode auxiliar ainda mais na previsão dos efeitos de mudanças de parâmetros na espessura da solda, reduzindo a necessidade de tentativa e erro dispendiosos.
Sistemas de monitoramento e feedback em tempo real
Implementar sensores e sistemas de monitoramento durante a soldagem a laser fornece dados em tempo real sobre penetração, espessura e qualidade da solda. Sistemas de feedback automatizados podem ajustar parâmetros em resposta a mudanças no ambiente de soldagem, garantindo espessura de solda consistente.
Sistemas de Controle Adaptativo
Sistemas avançados de soldagem a laser podem ajustar automaticamente a potência do laser, a velocidade e outros parâmetros com base em feedback em tempo real. Essa capacidade minimiza a variabilidade e garante espessura de solda uniforme em geometrias complexas ou condições de material variáveis.
Preparação de Superfície e Condicionamento de Material
A preparação adequada da superfície, incluindo limpeza e condicionamento, melhora a absorção de energia e a consistência da solda. Estratégias como esmerilhamento, jateamento de areia ou aplicação de revestimentos de superfície melhoram a interação da energia do laser, resultando em espessura mais consistente.
Otimização do projeto e montagem das juntas
Minimizar lacunas e garantir o alinhamento preciso dos componentes melhora a transferência de energia e a consistência na espessura da solda. Usar técnicas de fixação e fixação apropriadas ajuda a manter condições ideais de junta durante a soldagem.
Validação e Teste de Processos
A realização de testes e validações regulares de processos de soldagem a laser ajuda a identificar configurações de parâmetros ideais para aplicações específicas. A melhoria contínua do processo garante que a espessura da solda permaneça dentro das tolerâncias desejadas.
Ao ajustar os principais parâmetros do processo e implementar estratégias de controle eficazes, os fabricantes podem atingir a espessura de solda ideal, melhorar a qualidade da junta e aumentar a eficiência geral de suas operações de soldagem a laser. Essas práticas garantem que a soldagem a laser continue sendo uma solução confiável e versátil para diversas aplicações industriais.
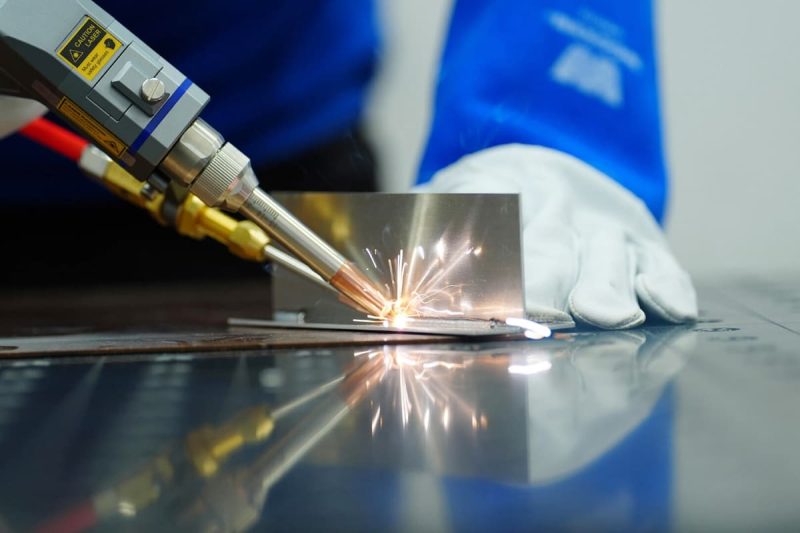
Desafios e Considerações
Otimizar a espessura da soldagem a laser não é isento de desafios. Vários fatores podem impactar a consistência, qualidade e desempenho da solda. Ao entender problemas comuns e implementar medidas robustas de controle de qualidade, os fabricantes podem melhorar seus processos e garantir soldas confiáveis.
Problemas comuns
Profundidade de penetração inconsistente
- Desafio: Variações na potência do laser, foco do feixe, espessura do material ou alinhamento da junta podem levar a profundidades de penetração inconsistentes, afetando a espessura da solda. Essa inconsistência pode resultar em juntas fracas, falta de fusão ou defeitos estruturais, comprometendo a integridade da solda.
- Consideração: A calibração regular da fonte do laser, o monitoramento do foco do feixe e o controle preciso dos parâmetros de soldagem são essenciais para uma penetração e espessura de solda consistentes.
Zonas Afetadas pelo Calor (ZTA)
- Desafio: A entrada excessiva de calor pode criar uma grande zona afetada pelo calor, alterando a microestrutura do material e reduzindo as propriedades mecânicas perto da solda. Isso pode levar a empenamento, estresse residual ou rachaduras, especialmente em materiais sensíveis ao estresse térmico.
- Consideração: Otimizar a potência do laser e a velocidade de soldagem, bem como usar gases de proteção apropriados, pode minimizar as zonas afetadas pelo calor e manter uma espessura de solda consistente.
Porosidade e aprisionamento de gás
- Desafio: Gases presos na poça de solda podem causar porosidade, reduzindo a resistência mecânica da solda e levando a inconsistências na espessura da solda. A porosidade pode surgir de contaminantes, gás de proteção insuficiente ou configurações de processo impróprias.
- Consideração: Limpar a superfície antes da soldagem, otimizar o fluxo de gás de proteção e reduzir contaminantes pode minimizar a porosidade. O monitoramento em tempo real ajuda a detectar e resolver problemas de porosidade no início do processo.
Refletividade dos materiais
- Desafio: Materiais altamente refletivos, como alumínio e cobre, refletem uma porção significativa da energia do laser, levando a dificuldades em atingir penetração adequada e espessura consistente. Esses materiais podem exigir considerações especiais para aumentar a absorção de energia.
- Consideração: Tratamentos de superfície, como revestimentos ou texturização, e o uso de lasers com comprimentos de onda mais curtos podem melhorar a absorção de energia e a consistência de materiais refletivos.
Desalinhamento e lacunas nas juntas
- Desafio: Juntas desalinhadas ou lacunas entre componentes reduzem a capacidade do laser de atingir penetração consistente. Isso pode levar a cortes inferiores, fusão incompleta e espessura de solda variável.
- Consideração: Fixação, alinhamento e controle de montagem adequados garantem condições consistentes da junta, reduzindo a probabilidade de defeitos.
Distorção térmica e estresse
- Desafio: A distribuição irregular de calor e o resfriamento rápido podem causar distorção térmica, estresse residual e empenamento, o que pode afetar a espessura da solda e a integridade da junta.
- Consideração: Pré-aquecimento, resfriamento controlado e velocidades de soldagem otimizadas ajudam a reduzir tensões térmicas e manter dimensões de solda consistentes.
Medidas de controle de qualidade
Monitoramento de Processos em Tempo Real
- Medida: Implementar sistemas de monitoramento em tempo real fornece feedback sobre parâmetros-chave, como potência do laser, velocidade de soldagem e profundidade de penetração. Isso permite ajustes imediatos, reduzindo variações na espessura da solda e melhorando a consistência geral.
- Consideração: Sensores ópticos, monitores de temperatura e sistemas de feedback a laser são exemplos de ferramentas que podem ser usadas para manter a estabilidade do processo.
Preparação da superfície pré-soldada
- Medida: Garantir que a superfície da peça de trabalho esteja limpa, livre de contaminantes e devidamente preparada é fundamental para obter absorção de energia e qualidade de solda consistentes.
- Consideração: Tratamentos de superfície como retificação, desengorduramento ou aplicação de revestimentos ajudam a minimizar contaminantes que podem interferir na transferência de energia.
Calibração e Manutenção de Equipamentos
- Medida: A calibração e manutenção regulares de fontes de laser, óptica e outros componentes do sistema garantem qualidade de feixe estável, potência de saída e precisão.
- Consideração: Verificações periódicas evitam a degradação do desempenho, o que pode afetar a espessura da solda e a qualidade geral.
Ensaios Não Destrutivos (END)
- Medição: Técnicas como testes ultrassônicos, radiografia e inspeções visuais ajudam a avaliar a qualidade da solda sem danificar a peça. Os métodos NDT detectam porosidade, rachaduras, fusão incompleta e outros problemas.
- Consideração: A implementação de procedimentos de END ajuda a verificar a consistência da solda e a adesão às especificações, reduzindo a probabilidade de falhas no produto.
Uso de gás de proteção e gás auxiliar
- Medida: A seleção adequada e o controle do fluxo de gases de proteção protegem a poça de solda da contaminação atmosférica e influenciam a penetração da solda.
- Consideração: Ajustar o tipo e a vazão dos gases de proteção pode minimizar a oxidação, a porosidade e as inconsistências na espessura da solda.
Otimização do Processo de Soldagem
- Medição: Desenvolver um mapa de processo que correlacione os parâmetros do laser (por exemplo, potência, velocidade, posição focal) com a espessura da solda garante configurações ideais para diferentes materiais e configurações de juntas.
- Consideração: A melhoria contínua do processo, apoiada por testes e simulação, melhora o controle sobre a espessura da solda e reduz a variabilidade.
Treinamento e operadores qualificados
- Medida: Operadores qualificados com profundo conhecimento dos parâmetros, materiais e técnicas de soldagem a laser contribuem significativamente para manter a consistência e a qualidade da soldagem.
- Consideração: O treinamento contínuo e o desenvolvimento de habilidades permitem que os operadores identifiquem e resolvam problemas rapidamente, melhorando o controle do processo.
Ao abordar desafios comuns e implementar medidas robustas de controle de qualidade, os fabricantes podem otimizar os processos de soldagem a laser para obter espessura de solda consistente, alta integridade estrutural e qualidade superior.

Resumo
A espessura da soldagem a laser é um fator crítico que influencia a resistência, a precisão e o desempenho geral das juntas de solda. Alcançar a espessura ideal requer um profundo entendimento de vários fatores, incluindo potência do laser, velocidade de soldagem, qualidade do feixe, posição focal, propriedades do material e gases de proteção. Ajustar esses parâmetros garante entrada de energia precisa e penetração consistente, resultando em soldas de alta qualidade e sem defeitos. Tratamentos pré e pós-soldagem, bem como configuração da junta e condições de superfície, impactam ainda mais o resultado da soldagem. Ao abordar desafios comuns, como penetração inconsistente, porosidade e distorção térmica, os fabricantes podem otimizar a espessura da solda e aumentar a confiabilidade geral do processo. Implementar medidas robustas de controle de qualidade, incluindo monitoramento em tempo real, calibração adequada do equipamento e treinamento do operador, garante resultados consistentes e confiáveis. Com esses insights, a soldagem a laser continua sendo uma solução indispensável para indústrias que exigem precisão, resistência e alta produtividade.
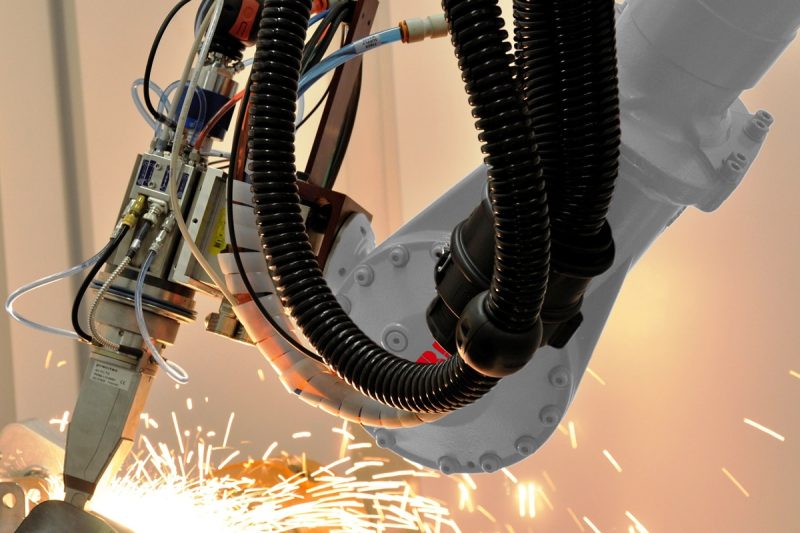
Obtenha soluções de soldagem a laser
Otimizar a espessura da soldagem a laser é essencial para obter soldas precisas, fortes e confiáveis em várias aplicações. Na AccTek Laser, fornecemos soluções avançadas de soldagem a laser adaptadas para atender às demandas exclusivas do seu setor. Nossos sistemas de soldagem a laser de última geração oferecem controle excepcional sobre parâmetros-chave, como potência do laser, foco do feixe e velocidade de soldagem, garantindo penetração consistente e resultados de alta qualidade. Nossa equipe de especialistas se dedica a ajudar você a selecionar o máquina de solda a laser com base no tipo de material, configuração da junta e necessidades específicas da aplicação.
Quer você precise soldar componentes finos e delicados ou peças estruturais espessas, as soluções da AccTek Laser oferecem precisão superior, zonas mínimas afetadas pelo calor e eficiência inigualável. Com nosso suporte abrangente, incluindo consultoria de pré-vendas, integração de sistemas, treinamento e manutenção, você pode otimizar seu processo de soldagem e atingir desempenho inigualável. Contate-nos hoje para descobrir a solução de soldagem a laser perfeita para suas necessidades de produção.
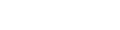
Informações de contato
- [email protected]
- [email protected]
- +86-19963414011
- No. 3 Zona A, Zona Industrial de Lunzhen, Cidade de Yucheng, Província de Shandong.
Obtenha soluções a laser