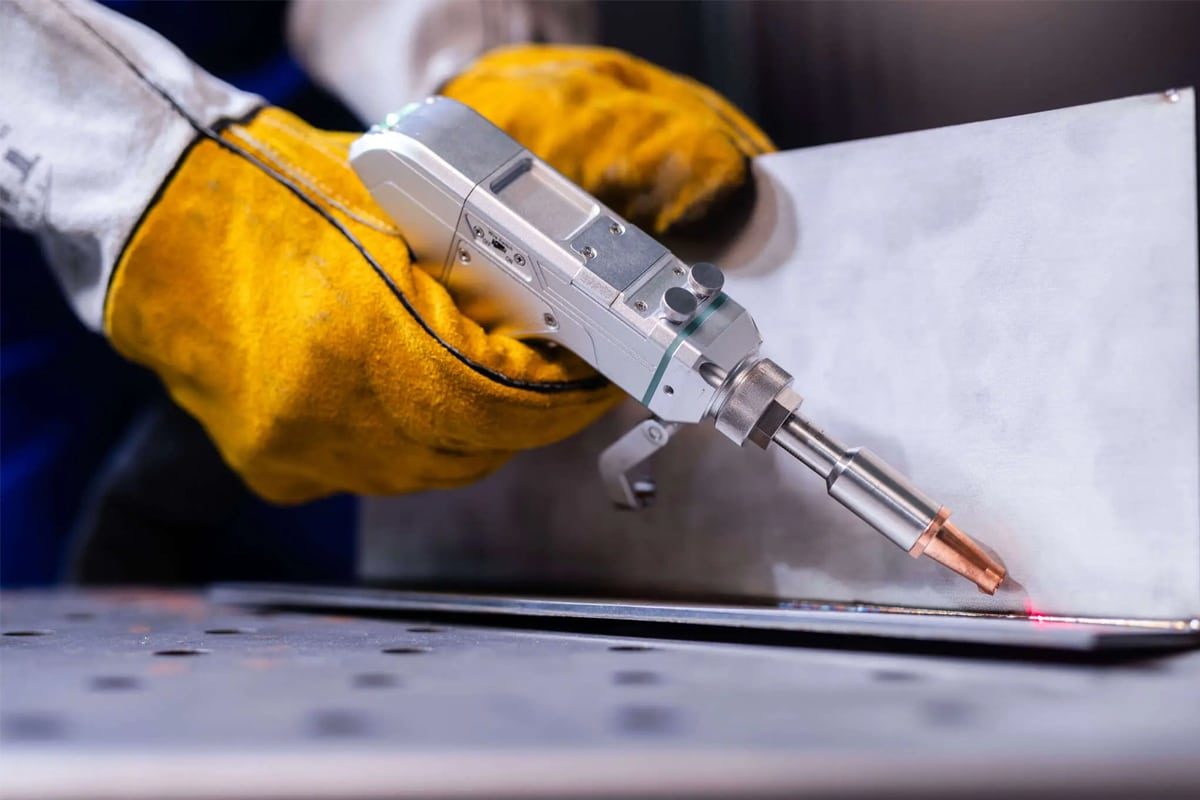
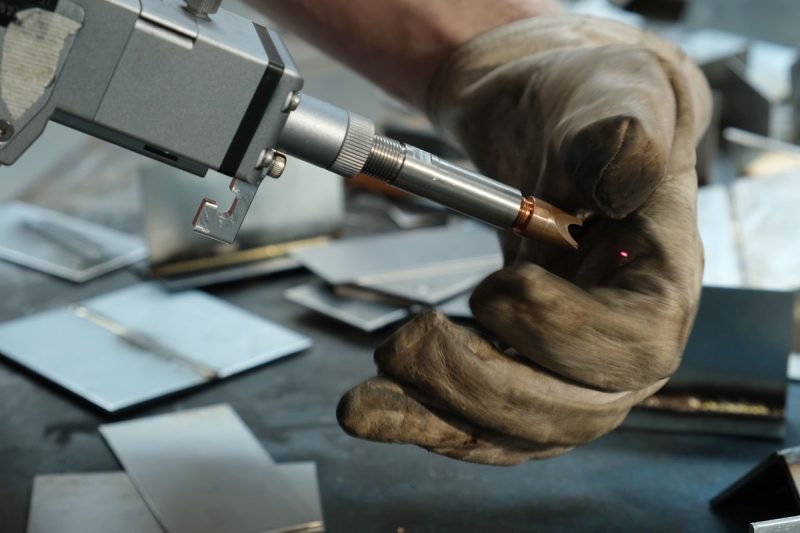
Como funciona a soldagem a laser
Princípios da soldagem a laser
A soldagem a laser funciona concentrando luz laser de alta energia em uma pequena área do material. Essa energia concentrada aquece o material rapidamente, fazendo com que ele derreta e se funda. Ao contrário da soldagem tradicional, que geralmente depende de zonas de calor mais amplas, a soldagem a laser se concentra em criar zonas mínimas afetadas pelo calor, reduzindo a distorção e fornecendo juntas mais limpas e de alta qualidade. A fusão ocorre em um dos dois modos principais: Modo de Condução ou Modo Keyhole.
- Potência e Foco do Laser: A densidade de potência do laser e o tamanho do ponto determinam a profundidade e a largura da solda. Densidades de potência mais altas produzem soldas mais profundas, enquanto configurações de potência mais baixas são usadas para soldas mais finas e rasas.
- Controle de calor: a soldagem a laser permite um controle preciso sobre a entrada de calor, essencial para unir materiais sensíveis ao calor ou peças complexas.
Tipos de modos de soldagem a laser
Soldagem em Modo de Condução
Características:
- Penetração de solda rasa, normalmente menor que 2 mm.
- Soldas suaves e largas com deformação superficial mínima.
- Risco mínimo de formação de buracos de fechadura, reduzindo a probabilidade de porosidade ou vazios.
Aplicações:
- Comumente usado para materiais finos e aplicações onde a qualidade visual é crucial.
- Ideal para aplicações em joias, dispositivos médicos e eletrônicos, onde é necessário um acabamento de superfície limpo.
Soldagem em modo buraco de fechadura
Características:
- Penetração profunda da solda (até vários centímetros) com largura estreita.
- Alta relação de aspecto, resultando em soldas fortes e focadas.
- A absorção eficiente de energia devido a múltiplas reflexões dentro do furo da fechadura promove uma penetração mais profunda da solda.
Aplicações:
- Adequado para aplicações pesadas que exigem juntas fortes e duráveis, como em componentes automotivos e aeroespaciais.
- Eficaz para materiais espessos e metais de alta resistência onde é necessária fusão profunda.
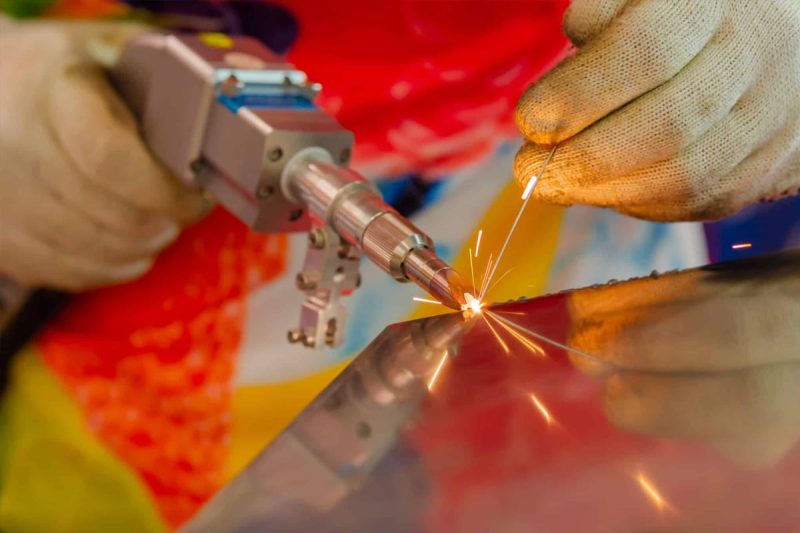
Vantagens da soldagem a laser
Precisão e exatidão
Alta velocidade de soldagem
Processo sem contato
Penetração profunda e soldas estreitas
Capacidade de soldar materiais difíceis
Distorção mínima e zonas afetadas pelo calor
Soldas limpas e estéticas
Baixos custos de manutenção e operação
Eficiência energética
Automação e Flexibilidade
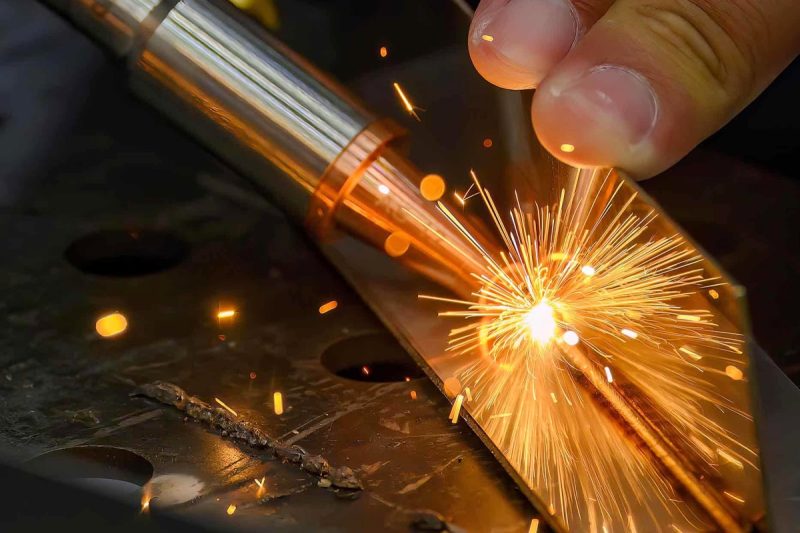
Desvantagens da soldagem a laser
Alto Investimento Inicial
Soldagem de Espessura Limitada
Sensibilidade ao ajuste das articulações
Preocupações de segurança
Problemas de refletividade
Complexidade Técnica
Sensibilidade do equipamento
Uso limitado em campo
Requer operadores qualificados
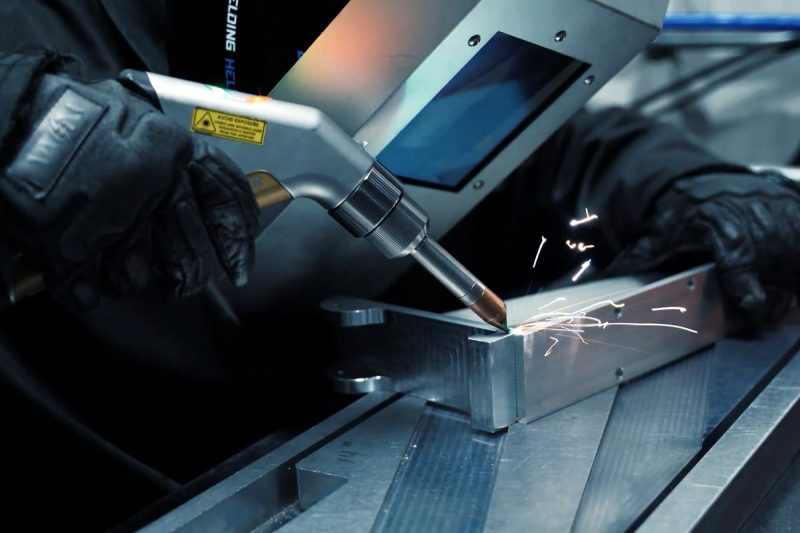
Aplicações da soldagem a laser
Indústria automobilística
Aplicações na indústria automotiva:
- Painéis de carroceria e blanks personalizados.
- Componentes do motor, incluindo peças de transmissão.
- As carcaças dos airbags exigem precisão e confiabilidade.
- Sistemas de exaustão precisam de soldas que suportem altas temperaturas e pressões.
Indústria aeroespacial
Aplicações na indústria aeroespacial:
- Sistemas de combustível e linhas hidráulicas exigem soldas à prova de vazamentos.
- Componentes estruturais, incluindo peças da fuselagem e trem de pouso.
- Lâminas de turbina e outras peças de motor, onde resistência e temperatura são críticas.
- A eletrônica aeroespacial precisa de soldas precisas e limpas para garantir confiabilidade a longo prazo.
Fabricação de dispositivos médicos
Aplicações na fabricação de dispositivos médicos:
- Instrumentos cirúrgicos, onde a resistência à corrosão e a limpeza são essenciais.
- Implantes médicos, como invólucros de marcapassos e dispositivos ortopédicos, exigem soldas biocompatíveis e herméticas.
- Cateteres e endoscópios precisam de soldas finas e precisas em componentes pequenos.
- Gabinetes de bateria para dispositivos médicos, onde a integridade da solda é essencial para uso a longo prazo.
Indústria Eletrônica
Aplicações em Eletrônica:
- Conexões de placas de circuito proporcionam soldas finas e precisas sem danificar componentes próximos.
- Os invólucros dos sensores e as conexões da bateria exigem juntas fortes e duráveis.
- Gabinetes para componentes eletrônicos sensíveis, garantindo proteção contra fatores ambientais.
- Microssoldagem na fabricação de semicondutores, onde precisão e limpeza são cruciais.
Indústria de Joias
Aplicações em Joias:
- Reparos em joias existentes, como redimensionamento de anéis ou conserto de correntes quebradas.
- Engaxetamento de pedras, permitindo soldas seguras perto de pedras preciosas sem danos causados pelo calor.
- Trabalhos em metal complexos em designs de joias personalizadas, onde soldas detalhadas e delicadas são necessárias.
- Criação de designs com metais mistos, como a união de ouro e platina, com costuras de solda limpas e invisíveis.
Setor de Energia
Aplicações em Energia:
- Fabricação de baterias, onde a soldagem a laser cria conexões duráveis entre células e terminais.
- Células de combustível e componentes de painéis solares se beneficiam de soldas limpas e precisas.
- Tubulações de petróleo e gás, onde soldas de alta resistência são essenciais para a segurança sob alta pressão.
- Os componentes da turbina eólica, incluindo peças estruturais, precisam suportar exposição climática e tensões mecânicas.
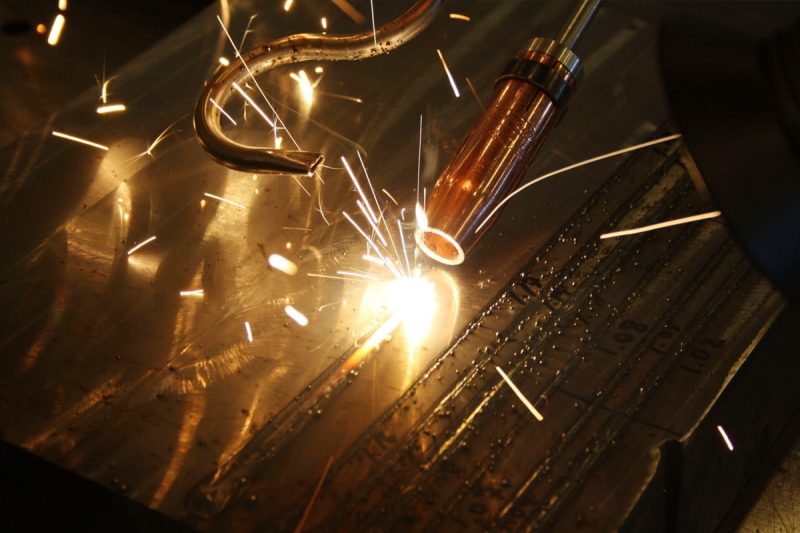
Comparação com métodos tradicionais de soldagem
Soldagem a laser vs. Soldagem TIG
- A soldagem TIG (Tungsten Inert Gas) é conhecida por produzir soldas limpas e de alta qualidade em uma ampla gama de metais, incluindo alumínio, aço inoxidável e cobre. A soldagem TIG usa um eletrodo de tungstênio para criar um arco entre o eletrodo e a peça de trabalho, derretendo o metal e frequentemente exigindo um material de enchimento.
- Precisão e exatidão: tanto a soldagem a laser quanto a TIG oferecem alta precisão, mas a soldagem a laser tem uma vantagem devido ao seu feixe focado, que pode criar soldas extremamente estreitas com zonas afetadas pelo calor (HAZ) mínimas. A soldagem TIG requer mais controle manual e é mais lenta, tornando-a menos adequada para soldas pequenas e complexas em componentes sensíveis.
- Entrada de Calor e Distorção: A entrada de energia concentrada da soldagem a laser cria uma HAZ muito menor em comparação à soldagem TIG. Isso reduz o risco de distorção térmica, o que é particularmente importante para materiais finos e aplicações sensíveis ao calor. A soldagem TIG, embora controlada, gera mais calor espalhado por uma área maior, o que pode causar empenamento em materiais mais finos.
- Velocidade: A soldagem a laser é significativamente mais rápida do que a soldagem TIG, tornando-a mais adequada para produção de alto volume. A soldagem TIG, embora capaz de produzir resultados de alta qualidade, é mais lenta devido à operação manual e à precisão necessária, tornando-a mais apropriada para projetos ou reparos menores.
- Aplicações: A soldagem TIG é frequentemente usada em projetos de pequena escala e precisão, como peças aeroespaciais e automotivas, mas geralmente é limitada em velocidade e compatibilidade de automação. A soldagem a laser é ideal para aplicações que precisam de velocidade e precisão, como eletrônicos, dispositivos médicos e componentes automotivos de alto volume.
Soldagem a laser vs. Soldagem MIG
- A soldagem por gás inerte metálico (MIG) é um método de soldagem comum usado para unir materiais mais espessos, especialmente em aplicações onde velocidade e volume de produção são prioridades. A soldagem MIG usa um eletrodo de arame alimentado continuamente que derrete para formar uma solda, frequentemente produzindo uma área de solda mais ampla e exigindo pós-processamento para remover respingos.
- Penetração e Largura da Solda: A soldagem a laser pode atingir penetração profunda com um cordão de solda estreito, mesmo em materiais espessos, sem a necessidade de material de enchimento. A soldagem MIG produz uma solda mais larga e menos precisa que frequentemente requer limpeza e acabamento adicionais. Para aplicações que exigem soldas fortes e estreitas, a soldagem a laser é mais adequada.
- Zona Afetada pelo Calor: A soldagem MIG gera mais calor do que a soldagem a laser, criando uma HAZ maior e aumentando o risco de distorção térmica. O calor concentrado da soldagem a laser reduz a HAZ, preservando as propriedades mecânicas do material ao redor e minimizando a distorção pós-soldagem, especialmente em materiais finos ou sensíveis ao calor.
- Automação e Velocidade de Produção: A soldagem a laser é altamente compatível com automação e pode operar em velocidades muito mais altas, tornando-a ideal para ambientes de produção de alto volume. A soldagem MIG, embora mais rápida que a TIG, é geralmente mais adequada para processos manuais ou semiautomatizados devido à necessidade de alimentação de arame e gás de proteção.
- Materiais: A soldagem MIG é eficaz para materiais mais espessos e metais comumente usados, como aço e alumínio, mas tem dificuldades com materiais diferentes e materiais muito finos, onde precisão e baixa entrada de calor são necessárias. A soldagem a laser se destaca na união de metais finos e diferentes, como cobre e aço inoxidável, devido ao seu controle preciso de energia.
Soldagem a laser vs. Soldagem por feixe de elétrons
- A soldagem por feixe de elétrons (EB) é um processo de soldagem de alta energia semelhante à soldagem a laser em sua capacidade de produzir soldas profundas e precisas. A soldagem EB usa um feixe focado de elétrons em um vácuo para unir materiais, tornando-a adequada para aplicações exigentes que exigem penetração muito profunda e um ambiente controlado.
- Ambiente e configuração: Diferentemente da soldagem a laser, que pode operar ao ar livre, a soldagem EB requer uma câmara de vácuo para manter o feixe de elétrons. Essa configuração de vácuo torna a soldagem EB mais complexa, custosa e menos flexível do que a soldagem a laser, que pode ser usada em uma gama mais ampla de ambientes, incluindo salas limpas ou linhas de produção semiautomatizadas.
- Profundidade e Força de Penetração: A soldagem EB pode atingir uma penetração mais profunda do que a soldagem a laser, tornando-a ideal para materiais espessos ou aplicações estruturais que exigem soldas muito fortes. No entanto, para materiais moderadamente espessos a finos, a soldagem a laser é frequentemente mais eficiente e fácil de implementar.
- Velocidade e automação: a soldagem a laser pode atingir velocidades mais altas e é mais fácil de integrar em linhas de produção automatizadas, tornando-a adequada para produção de alto volume. A soldagem EB, embora eficaz, é geralmente mais lenta e menos adaptável a ambientes de produção automatizados e de ritmo acelerado devido aos requisitos da câmara de vácuo.
- Custo e manutenção: Os sistemas de soldagem EB são caros e exigem manutenção especializada, particularmente para o sistema de vácuo. A soldagem a laser tem requisitos de manutenção mais baixos, tornando-a mais acessível e econômica para a fabricação regular. Além disso, o tempo de configuração e manutenção para soldagem EB pode levar a tempos de inatividade mais longos em comparação com a soldagem a laser.
Comparação
- Soldas precisas e limpas: a soldagem a laser supera a soldagem MIG e TIG em precisão, ao mesmo tempo em que compete com a soldagem EB por resultados limpos e precisos.
- Velocidade: A soldagem a laser é mais rápida que a soldagem TIG e MIG e geralmente mais adequada para produção automatizada de alta velocidade, especialmente onde precisão é necessária.
- Ambiente: A flexibilidade da soldagem a laser em ambientes com ar a torna mais versátil do que a soldagem EB, que requer vácuo.
- Zona afetada pelo calor: a ZTA mínima da soldagem a laser a torna ideal para materiais finos e sensíveis ao calor, superando a soldagem TIG e MIG nesse aspecto.
- Custo e complexidade: a soldagem a laser tem um alto custo inicial, mas oferece menores custos de manutenção e operação em comparação à soldagem EB, que envolve equipamentos e necessidades de manutenção mais complexos.
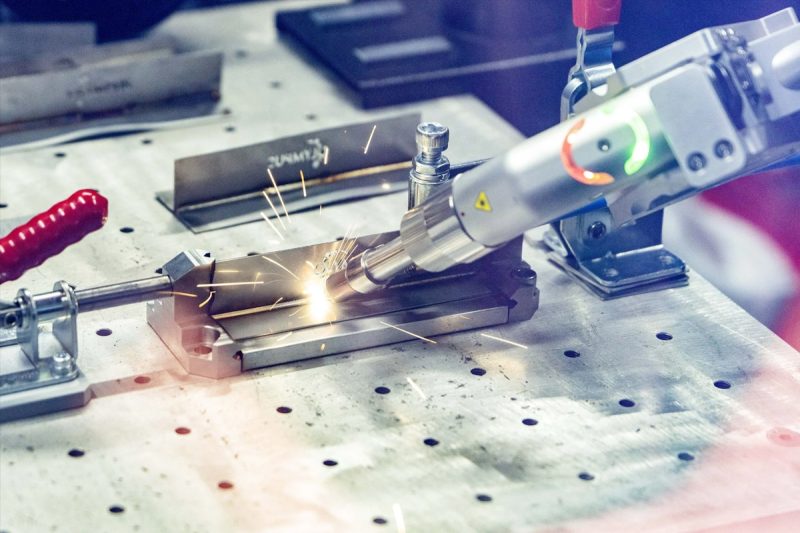
Fatores que afetam a qualidade da soldagem a laser
Parâmetros de laser
As configurações e características do próprio laser desempenham um papel crucial na determinação da qualidade da solda. Os principais parâmetros do laser incluem potência, tamanho do ponto de foco, velocidade de soldagem e frequência de pulso (para lasers pulsados).
- Potência do Laser: Maior potência aumenta a profundidade de penetração e permite soldagem mais rápida, mas pode levar a calor excessivo se não for controlado adequadamente. Muita potência pode causar respingos ou queimaduras, enquanto pouca potência pode resultar em soldas fracas ou incompletas.
- Velocidade de soldagem: A velocidade na qual o laser se move sobre a peça de trabalho afeta a qualidade da solda. Altas velocidades de soldagem podem reduzir a entrada de calor, minimizando a zona afetada pelo calor (HAZ) e reduzindo a distorção. No entanto, velocidades muito altas podem impedir a fusão completa dos materiais, resultando em juntas fracas. Velocidades mais lentas permitem uma penetração mais profunda, mas podem aumentar o acúmulo de calor, causando potencialmente distorção térmica.
- Tamanho do ponto de foco: Um tamanho menor de ponto de foco concentra energia em uma área minúscula, permitindo soldas finas e estreitas. O tamanho do ponto de foco deve corresponder à largura da junta; se for muito grande, pode causar calor excessivo e distorção. Se for muito pequeno, pode não penetrar profundamente o suficiente para materiais mais espessos.
- Frequência de pulso (lasers pulsados): Para aplicações que exigem lasers pulsados, ajustar a frequência de pulso ajuda a controlar a quantidade de energia fornecida à solda. Frequências de pulso mais altas podem fornecer soldas mais suaves e contínuas, enquanto frequências mais baixas fornecem rajadas de energia intermitentes, úteis para aplicações que precisam de entrada mínima de calor.
Propriedades do Material
O material que está sendo soldado influencia como o laser interage com a superfície e penetra no metal. Fatores como refletividade, condutividade térmica e composição da liga afetam a qualidade da solda.
- Refletividade: Materiais com alta refletividade, como alumínio e cobre, podem refletir uma porção significativa da energia do laser, reduzindo a absorção. Comprimentos de onda de laser mais baixos ou pré-tratamento de materiais refletivos podem ajudar a aumentar a absorção e melhorar a qualidade da solda.
- Condutividade Térmica: Materiais com alta condutividade térmica, como cobre, dissipam calor rapidamente, exigindo maior potência do laser ou parâmetros ajustados para atingir a penetração adequada. Materiais com baixa condutividade, como titânio, retêm calor, permitindo soldas mais profundas com menos potência.
- Composição da liga: As ligas geralmente têm pontos de fusão variados e podem exigir diferentes configurações de laser para obter soldas consistentes. Algumas ligas também produzem mais respingos ou exigem diferentes frequências de pulso para evitar rachaduras, particularmente aquelas com elementos que podem evaporar em temperaturas de soldagem.
- Condição da superfície: A limpeza e o acabamento da superfície do material impactam o quão bem o feixe de laser é absorvido. Óxidos, óleos ou contaminantes de superfície podem interromper o processo de soldagem e levar a juntas mais fracas. A limpeza ou preparação da superfície antes da soldagem pode ajudar a melhorar a consistência e a resistência da solda.
Projeto e montagem de juntas
O design da junta e a qualidade do encaixe afetam significativamente a qualidade final da solda. O design adequado da junta e o encaixe firme garantem que o laser possa fundir precisamente os materiais sem lacunas ou desalinhamento.
- Projeto de junta: Diferentes tipos de junta (como juntas de topo, juntas de sobreposição e juntas de filete) exigem configurações de laser específicas e foco para garantir resultados ideais. Por exemplo, juntas de topo podem precisar de penetração mais profunda, enquanto juntas de sobreposição podem ser mais rasas, mas exigem controle para evitar propagação excessiva de calor.
- Precisão de encaixe: O alinhamento preciso entre as peças é essencial para uma qualidade de solda consistente. Quaisquer lacunas ou desalinhamentos podem levar à fusão incompleta, criando pontos fracos na solda. Encaixes apertados garantem que a energia do laser seja efetivamente absorvida pela junta, minimizando a chance de defeitos. Para aplicações que exigem tolerâncias extremamente estreitas, sistemas de fixação e fixação podem ser usados para segurar as peças com segurança durante a soldagem.
- Compatibilidade de espessura: A espessura da junta também afeta a resistência da solda. Ao soldar materiais espessos, os parâmetros do laser devem ser ajustados para penetrar completamente sem superaquecer o material ao redor. Materiais finos, por outro lado, exigem configurações de potência mais baixas para evitar empenamento ou queima.
Gás de proteção
Usar gás de proteção ajuda a proteger a área de solda contra contaminação e oxidação, o que pode impactar a qualidade e a aparência da solda. A escolha e o fluxo do gás de proteção desempenham um papel significativo na obtenção de soldas de alta qualidade.
- Tipo de gás: Os gases de proteção comuns incluem argônio, hélio e nitrogênio. O argônio fornece uma atmosfera estável e é amplamente usado para uma variedade de metais. O hélio é frequentemente usado para penetração profunda devido à sua alta condutividade térmica, mas é mais caro. O nitrogênio às vezes é usado para materiais específicos, como aço inoxidável, mas pode causar nitretos em alguns metais, afetando potencialmente a resistência.
- Taxa de fluxo de gás: A taxa de fluxo do gás de proteção deve ser ajustada de acordo com o material e os parâmetros de soldagem. Uma taxa de fluxo muito alta pode romper a poça de solda e levar à turbulência, enquanto uma taxa de fluxo muito baixa pode não proteger totalmente a solda, permitindo oxidação e levando à descoloração ou porosidade.
- Método de Entrega: O gás de proteção pode ser entregue diretamente por um bico próximo ao cabeçote do laser ou, em alguns casos, por uma linha de gás secundária para maior cobertura. A entrega adequada de gás garante uma distribuição uniforme, protegendo a solda da exposição ao ar e promovendo um acabamento de solda limpo e estético.

Resumo
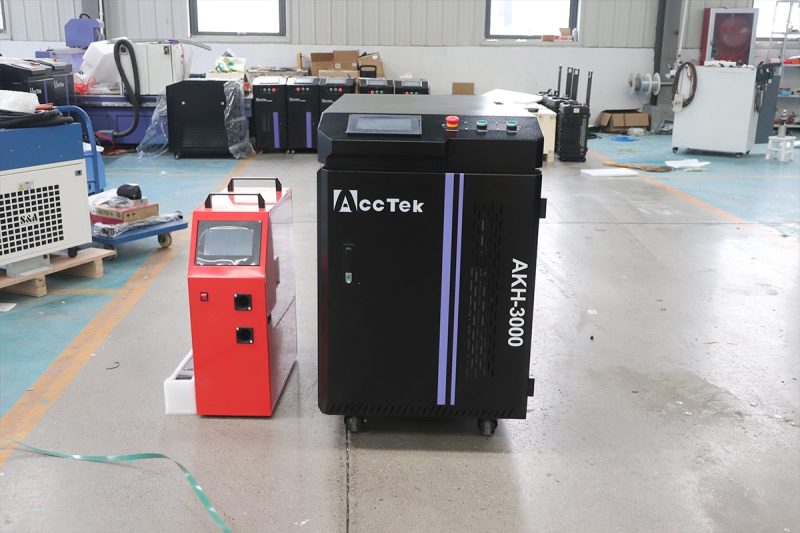
Obtenha soluções de soldagem a laser
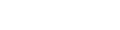
- [email protected]
- [email protected]
- +86-19963414011
- No. 3 Zona A, Zona Industrial de Lunzhen, Cidade de Yucheng, Província de Shandong.