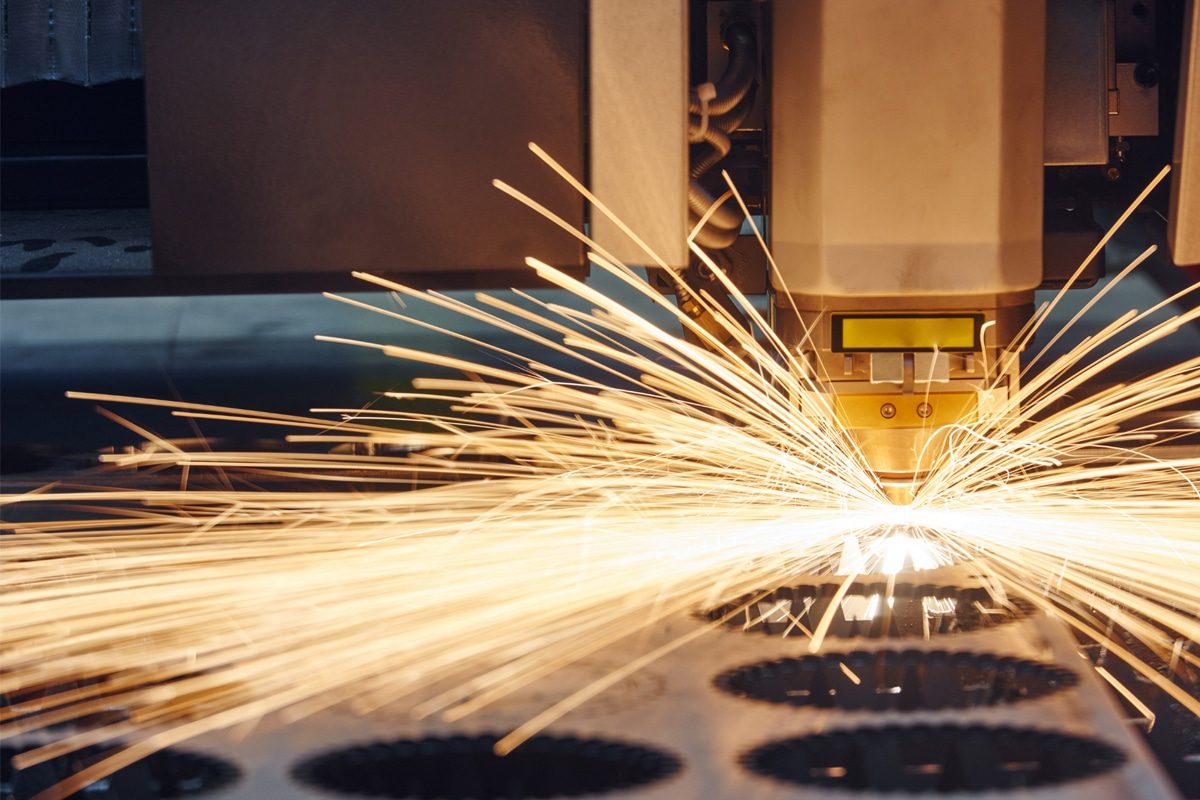
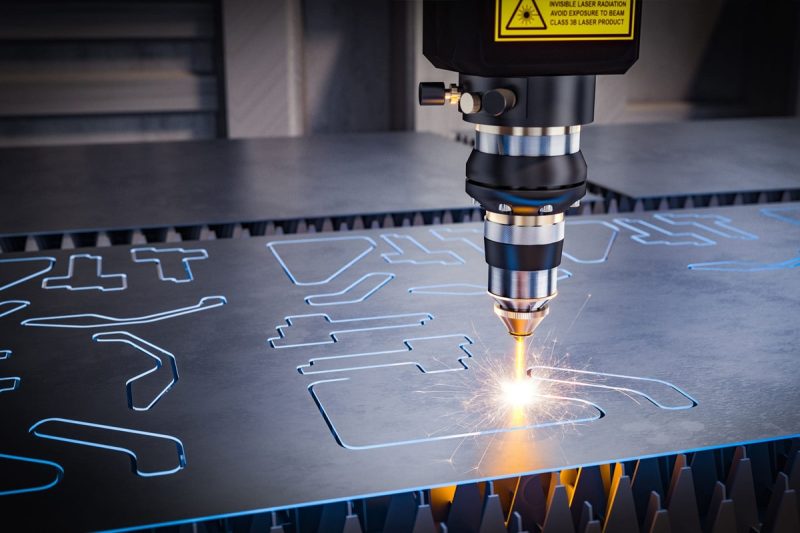
Введение в лазерную и плазменную резку
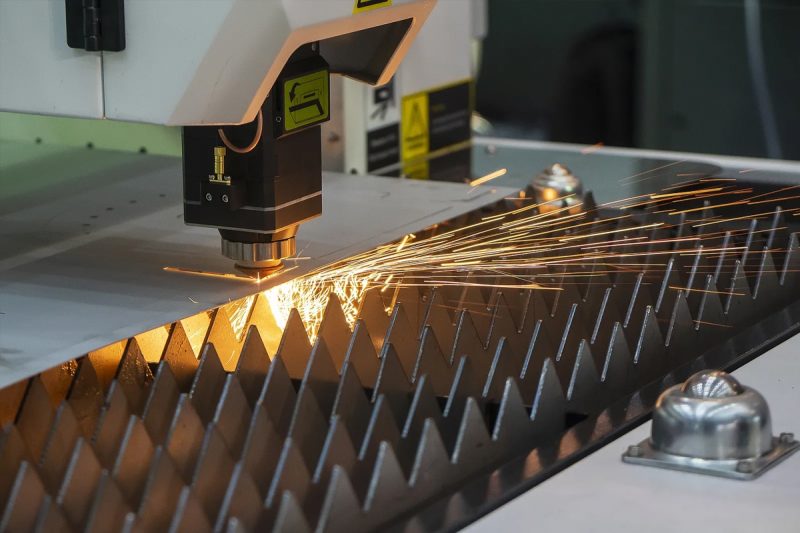
Принцип работы: лазерная резка против плазменной резки
Принцип работы лазерной резки
Лазерная резка использует мощный, сфокусированный луч света для резки или гравировки материалов с исключительной точностью. Термин «LASER» означает Light Amplification by Stimulated Emission of Radiation (Усиление света путем вынужденного излучения). Вот как работает этот процесс:
- Генерация лазера: лазерный источник, такой как волоконный лазер или CO2-лазер, генерирует когерентный луч монохроматического света. Этот свет создается путем возбуждения атомов в лазерной среде, заставляя их испускать фотоны в унисон.
- Фокусировка луча: лазерный луч направляется через ряд зеркал и линз, которые фокусируют его на очень маленькую, точную точку на поверхности материала. Фокусирующий механизм концентрирует луч до диаметра всего 0,1 мм, увеличивая его интенсивность.
- Взаимодействие с материалами: Когда сфокусированный лазерный луч попадает на материал, его энергия поглощается, что приводит к быстрому нагреванию материала. В зависимости от мощности лазера и свойств материала это может привести к:
- Плавление: Материал плавится из-за высокой температуры.
- Испарение: Материал испаряется, если температура превышает точку кипения.
- Горение: В некоторых случаях, особенно в случае с неметаллами, материал может воспламениться.
- Вспомогательный газ: Вспомогательный газ, такой как кислород, азот или сжатый воздух, продувается коаксиально с лазерным лучом через сопло. Газ служит нескольким целям:
- Выброс расплавленного материала: выдувает расплавленный или испарившийся материал из пропила (зазора между резанием и резанием).
- Повышение скорости резки: кислород может вступать в экзотермическую реакцию с материалом, увеличивая скорость резки.
- Защита линзы: предотвращает загрязнение фокусирующей линзы парами и частицами.
- Управляемое движение: системы ЧПУ (числовое программное управление) направляют лазерную режущую головку по материалу в соответствии с запрограммированным рисунком, обеспечивая точные разрезы и сложные формы.
Основные характеристики лазерной резки:
- Точность: Возможность резки с допусками до ±0,1 мм.
- Качество кромок: обеспечивает гладкие, чистые кромки, которые часто не требуют дальнейшей отделки.
- Универсальность: подходит для резки широкого спектра материалов, включая металлы, пластик, дерево и стекло (в зависимости от типа лазера).
- Минимальная зона теплового воздействия: сфокусированный луч сводит к минимуму термическую деформацию окружающего материала.
Принцип работы плазменной резки
Плазменная резка — это процесс, который разрезает электропроводящие материалы с помощью струи горячей плазмы. Вот пошаговое объяснение того, как работает плазменная резка:
- Электропитание и газ: плазменный резак использует источник питания для создания дуги постоянного тока (DC) и подачу газа (обычно сжатого воздуха, азота или кислорода), который образует плазму.
- Инициирование дуги: плазменный резак инициирует дугу между электродом (расположенным в горелке) и заготовкой. Это может быть инициировано:
- Контактное начало: прикосновение наконечника горелки к заготовке для замыкания цепи.
- Высокочастотный запуск: использование высоковольтной высокочастотной цепи для бесконтактной ионизации газа.
- Формирование плазмы: Газ на большой скорости продавливается через узкое сопло внутри горелки. Когда газ проходит через электрическую дугу, он ионизируется, превращаясь в плазму — горячий, электропроводящий газ.
- Плавление и удаление материала:
- Плавление: плазма достигает температуры до 30 000 ℃ (54 000 ℉), мгновенно расплавляя металл в точке контакта.
- Сдув расплавленного металла: высокоскоростной поток плазмы сдувает расплавленный металл с места реза, создавая пропил.
- Движение резака: подобно лазерной резке, системы ЧПУ управляют движением плазменного резака, чтобы точно следовать желаемой траектории резки.
Основные характеристики плазменной резки:
- Скорость резки: Более высокая скорость резки толстых материалов по сравнению с лазерной резкой.
- Толщина материала: Эффективен для резки металлических пластин толщиной до нескольких дюймов.
- Только токопроводящие материалы: можно резать только материалы, проводящие электричество, такие как сталь, нержавеющая сталь, алюминий, латунь и медь.
- Более широкий пропил и зона термического воздействия: приводит к большей ширине реза и большей площади, подверженной термическому воздействию, что может привести к большему количеству отходов материала и потенциальной деформации.
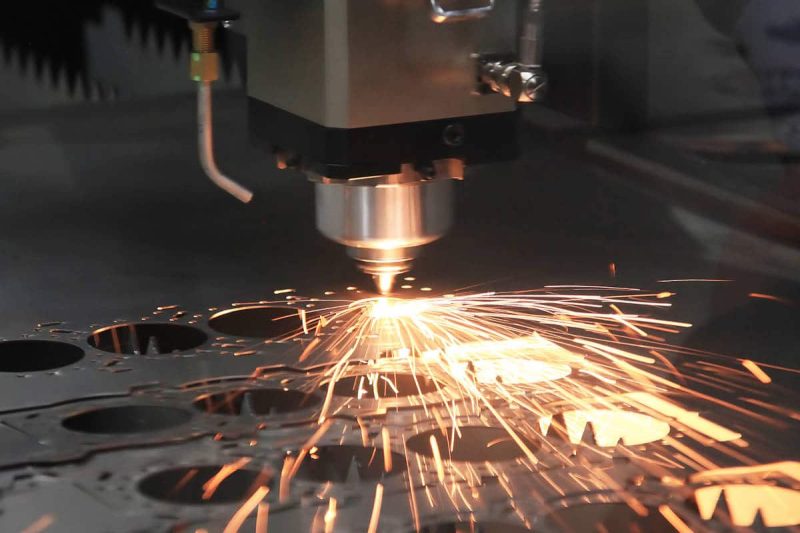
Основные различия между лазерной и плазменной резкой
Режущий механизм
- Лазерная резка: Лазерная резка работает путем фокусировки мощного лазерного луча на поверхности материала, расплавляя, сжигая или испаряя материал. Поток вспомогательного газа (например, азота, кислорода или сжатого воздуха) помогает вытеснить расплавленный материал и создать чистый срез. Лазерный луч генерируется из волоконного или CO2-лазера, в зависимости от разрезаемого материала. Лазерная резка обеспечивает непревзойденную точность и управляется системой ЧПУ (числовое программное управление), что позволяет создавать замысловатые и сложные конструкции.
- Плазменная резка: плазменная резка, напротив, основана на струе горячей плазмы, создаваемой путем электрической ионизации газа, например кислорода или азота, для плавления электропроводящих материалов, таких как сталь или алюминий. Плазменная дуга образуется путем пропускания газа через сопло при применении электрической дуги, создавая поток, достаточно горячий для плавления материала. Плазменная резка эффективна для более толстых металлов, но не обеспечивает такого же уровня точности, как лазерная резка.
Совместимость материалов
- Лазерная резка: Лазерная резка очень универсальна, когда дело касается совместимости материалов. Она может резать как металлические, так и неметаллические материалы. Волоконные лазеры в основном используются для резки металлов, таких как сталь, нержавеющая сталь, алюминий, латунь и медь. Станки для лазерной резки CO2, с другой стороны, больше подходят для резки неметаллов, таких как дерево, пластик, ткань и стекло. Однако волоконные лазеры наиболее эффективны для резки металлов, и они не могут резать материалы с высокой отражающей способностью, такие как алюминий, без регулировки мощности лазера и настроек.
- Плазменная резка: плазменная резка ограничена электропроводящими материалами. Сюда входят такие металлы, как углеродистая сталь, нержавеющая сталь, алюминий, латунь, медь и другие сплавы. Она не может резать непроводящие материалы, такие как пластик, дерево или стекло, что ограничивает ее применение металлообрабатывающей промышленностью. Для резки более толстых металлов плазменная резка предлагает более быстрый и эффективный вариант.
Скорость резки
- Лазерная резка: Лазерная резка обычно отлично подходит для резки тонких материалов с высокой скоростью и точностью. Для металлов толщиной менее 6 мм лазерная резка значительно быстрее плазменной, особенно когда требуются высокоточные разрезы. Однако по мере увеличения толщины материала скорость резки лазером снижается. Лазерная резка лучше всего подходит для детальной работы, где точность важнее чистой скорости.
- Плазменная резка: плазменная резка, напротив, быстрее лазерной, когда дело касается более толстых материалов, особенно металлов толщиной более 10 мм. Плазменные резаки могут резать эти толстые материалы на высокой скорости, что делает их идеальными для тяжелых промышленных применений, таких как судостроение или строительство. Для более толстых металлов плазменная резка может быть более эффективной по времени, чем лазерная резка.
Толщина резки
- Лазерная резка: Лазерная резка очень эффективна для тонких материалов, обычно до 30 мм в толщину для металлов при использовании высокомощных волоконных лазеров. За пределами этой толщины эффективность и скорость лазерной резки снижаются, и резка может стать менее практичной из-за ограничений мощности и потенциальной деформации материала от тепла.
- Плазменная резка: плазменная резка отлично подходит для резки более толстых материалов, часто до 50 мм и более в зависимости от мощности плазменного резака. Это делает плазменную резку лучшим выбором для применений, где требуется резка толстых металлов, например, в тяжелой промышленности. Для материалов толщиной более 30 мм плазменная резка, как правило, быстрее и экономичнее лазерной.
Точность и аккуратность
- Лазерная резка: одним из главных преимуществ лазерной резки является ее точность. Узкий лазерный луч в сочетании с ЧПУ-управлением позволяет выполнять высокоточную резку с жесткими допусками, часто в пределах ±0,1 мм. Это делает лазерную резку идеальной для сложных конструкций, подробных компонентов и приложений, где высокая точность имеет решающее значение, например, в аэрокосмической, электронной и автомобильной промышленности. Узкий пропил (ширина реза) дополнительно снижает отходы материала.
- Плазменная резка: Хотя плазменная резка эффективна для более толстых материалов, она менее точна, чем лазерная резка. Плазменные резаки создают более широкий пропил, что ограничивает возможность получения тонких, сложных разрезов. Хотя плазменная резка подходит для многих промышленных применений, для улучшения качества реза и удаления заусенцев может потребоваться постобработка, такая как шлифование или полировка, особенно для детальной работы или тонких материалов.
Зона термического влияния (ЗТВ)
- Лазерная резка: Лазерная резка создает меньшую зону термического влияния (ЗТВ) по сравнению с плазменной резкой. Высококонцентрированный лазерный луч расплавляет небольшую часть материала, не оказывая существенного влияния на окружающую область. Эта минимизированная ЗТВ приводит к меньшей тепловой деформации, снижая риск коробления или деформации материала, что особенно важно для тонких или деликатных заготовок.
- Плазменная резка: плазменная резка создает гораздо большую зону термического воздействия из-за высоких температур плазменной дуги. Эта большая зона термического влияния увеличивает вероятность деформации или искажения материала, особенно при резке более тонких материалов. Для более толстых металлов зона термического влияния может быть менее серьезной проблемой, но для точных применений или материалов, склонных к тепловому повреждению, лазерная резка является лучшим вариантом.
Качество края
- Лазерная резка: Лазерная резка обеспечивает превосходное качество кромок с гладкими, чистыми разрезами, которые часто не требуют дальнейшей отделки. Узкий пропил и минимальное воздействие тепла приводят к кромкам без заусенцев и точным. Это особенно выгодно для применений, где требуется эстетика или высококачественная отделка.
- Плазменная резка: плазменная резка, хотя и быстрая, часто дает более грубые края по сравнению с лазерной резкой. Более широкий пропил и большая зона термического влияния могут привести к образованию окалины или шлака (остаточного материала) на краях, что требует дополнительной постобработки для достижения гладкой поверхности. Для применений, где качество кромок не имеет решающего значения, плазменная резка остается подходящим вариантом.
Заключение: основные различия
- Механизм резки: лазерная резка использует сфокусированный луч света, в то время как плазменная резка основана на потоке ионизированного газа (плазмы).
- Совместимость материалов: лазерная резка может обрабатывать как металлы, так и неметаллы, в то время как плазменная резка ограничивается электропроводящими металлами.
- Скорость резки: лазерная резка быстрее подходит для тонких материалов, тогда как плазменная резка отлично подходит для быстрой резки более толстых металлов.
- Толщина резки: лазерная резка более эффективна для более тонких материалов, в то время как плазменная резка эффективнее обрабатывает толстые металлы.
- Точность и аккуратность: лазерная резка обеспечивает более высокую точность и чистоту срезов, в то время как плазменная резка менее точна и может потребовать последующей обработки.
- Зона термического влияния (ЗТВ): лазерная резка имеет меньшую ЗТВ, что снижает термическую деформацию, тогда как плазменная резка создает большую ЗТВ, что увеличивает риск коробления.
- Качество кромок: лазерная резка обеспечивает гладкие, высококачественные кромки, в то время как плазменная резка может создавать более грубые кромки, требующие дополнительной отделки.
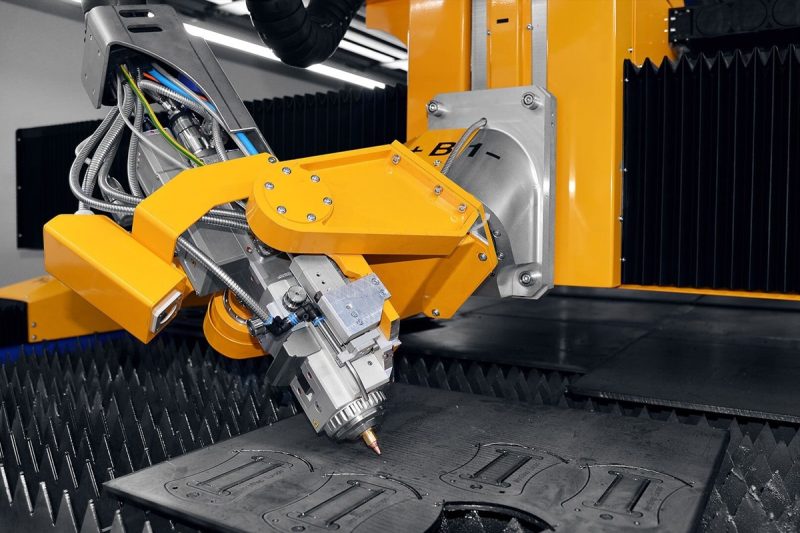
Применение: лазерная резка против плазменной резки
Применение лазерной резки
Лазерная резка известна своей высокой точностью, мелкой детализацией и чистыми срезами, что делает ее идеальной для отраслей и приложений, где точность и качество имеют первостепенное значение. Лазерная резка широко используется в следующих отраслях:
- Авиакосмическая промышленность: В аэрокосмическом производстве компоненты должны соответствовать чрезвычайно высоким стандартам точности. Лазерная резка является предпочтительным методом для резки сложных деталей из легких металлов, таких как титан и алюминий, а также для создания небольших, детализированных деталей с минимальными допусками.
- Автомобилестроение: Лазерная резка широко применяется в автомобильной промышленности для резки сложных деталей, включая компоненты из листового металла, панели приборов и детали двигателя. Ее точность позволяет создавать индивидуальные и подробные детали, которые отвечают высоким требованиям современных транспортных средств.
- Электроника: Электронная промышленность часто требует деликатной и сложной резки для небольших компонентов, таких как печатные платы (ПП). Способность лазерной резки обрабатывать тонкие материалы и обеспечивать высокоточные разрезы с минимальным тепловым повреждением делает ее идеальной для этих применений.
- Медицинские приборы: лазерная резка используется для производства медицинских приборов, таких как хирургические инструменты, имплантаты и другие прецизионные компоненты, требующие сложной детализации. Высокая точность гарантирует, что медицинские приборы соответствуют строгим нормативным стандартам.
- Ювелирные изделия и мода: лазерная резка часто используется для резки и гравировки в ювелирной и модной промышленности. Будь то резка драгоценных металлов для ювелирных изделий или сложных узоров на тканях и коже, лазерная технология обеспечивает чистые и точные разрезы, которые повышают эстетическую привлекательность продукции.
- Резка текстиля и тканей: CO2-лазеры обычно используются в текстильной промышленности для резки тканей, кожи и синтетических материалов. Лазерная резка обеспечивает быструю, точную и бесконтактную резку, что имеет решающее значение для деликатных материалов, которые можно легко повредить.
- Производство вывесок и дисплеев: лазерная резка также популярна в индустрии вывесок для создания подробных логотипов, сложных дизайнов и надписей на таких материалах, как акрил, пластик и дерево. Чистые края и точные разрезы идеально подходят для визуально привлекательных дисплеев.
Применение плазменной резки
Плазменная резка известна своей скоростью и способностью эффективно резать толстые, проводящие материалы. Обычно она используется в тяжелых отраслях промышленности, где точность не так важна, но требуется высокоскоростная резка большого масштаба. Плазменная резка обычно используется в следующих областях:
- Строительство: плазменная резка широко используется в строительной отрасли для резки толстых стальных пластин, структурных балок и металлической арматуры. Ее способность быстро резать толстые материалы делает ее идеальной для крупномасштабных проектов, таких как мосты, здания и другая инфраструктура.
- Судостроение: В судостроительной отрасли плазменная резка необходима для резки толстых стальных листов, используемых при строительстве судов. Скорость и экономичность плазменной резки делают ее популярным методом изготовления крупных металлических компонентов, включая корпуса и рамы.
- Изготовление металла: плазменная резка популярна в цехах по изготовлению металла для резки толстых металлических листов, труб и рам. Производители ценят скорость и мощность плазменной резки, особенно для работ, связанных с высокопрочными материалами, такими как нержавеющая сталь или алюминий.
- Ремонт и кастомизация автомобилей: лазерная резка часто используется в производстве автомобильных деталей, а плазменная резка идеально подходит для авторемонтных мастерских, которым нужно быстро резать толстый металл. Плазменные резаки часто используются для ремонта рам автомобилей, выхлопных систем и нестандартных металлических конструкций.
- Производство тяжелого оборудования: Отрасли, производящие тяжелое оборудование, например, горнодобывающее, сельскохозяйственное и промышленное, часто используют плазменную резку для обработки толстых стальных и металлических компонентов, из которых состоят эти машины. Способность плазменной резки работать через толстые материалы делает ее очень эффективной для производства деталей большой грузоподъемности.
- Строительство трубопроводов: В нефтегазовой промышленности плазменная резка используется для резки и формовки толстых металлических труб. Возможность резки толстых материалов на высоких скоростях имеет важное значение для отраслей, где требуется точность при работе с большими трубами и металлическими компонентами для транспортных систем.
Заключение: Приложения
- Лазерная резка лучше всего подходит для приложений, требующих точности, мелкой детализации и высококачественной отделки. Она отлично подходит для таких отраслей, как аэрокосмическая промышленность, автомобилестроение, электроника и производство медицинских приборов, где точность и чистота краев имеют решающее значение.
- Плазменная резка идеально подходит для тяжелых условий эксплуатации, когда требуется быстрая и эффективная резка толстых материалов. Такие отрасли, как строительство, судостроение и металлообработка, выигрывают от скорости и экономической эффективности плазменной резки, особенно когда точность не так важна.
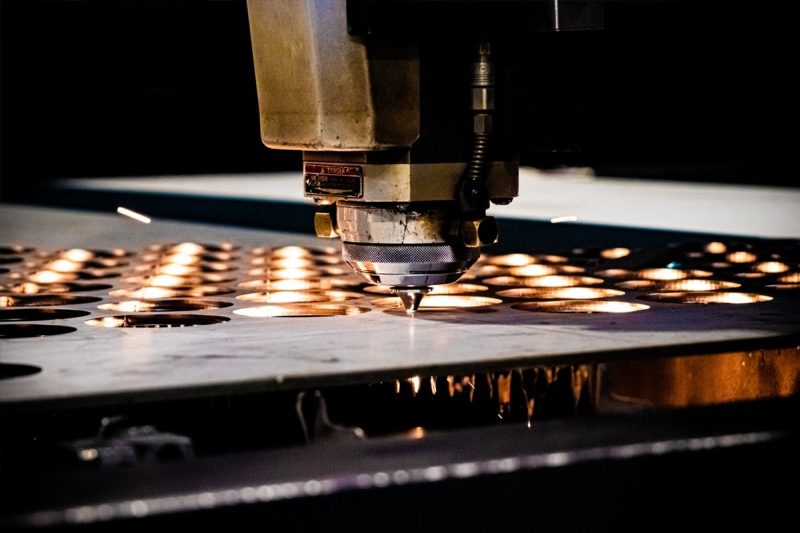
Сравнение стоимости: лазерная резка против плазменной резки
Первоначальные инвестиции
- Лазерная резка: Начальные инвестиции в лазерную резку обычно выше, чем в плазменную резку. Лазерные режущие машины, особенно волоконные лазеры, известны своей точностью и передовыми технологиями, которые имеют более высокую цену. Стоимость волоконно-лазерная резка может варьироваться от $15,000 до более $500,000 в зависимости от мощности, характеристик и индивидуальных конфигураций. Например, мощная промышленная система лазерной резки, используемая при изготовлении металла, может стоить значительно дороже, чем базовая машина, предназначенная для более тонких материалов или мелкосерийного производства.
- Плазменная резка: плазменные режущие машины, напротив, имеют более низкую начальную стоимость. Стандартный плазменный резак обычно стоит от $15,000 до $100,000, в зависимости от мощности машины и размера материалов, которые она может обрабатывать. Даже плазменные резаки высокого класса, как правило, более доступны, чем лазерные резаки. Эта более низкая цена делает плазменную резку более доступной для малых и средних предприятий, которым необходимо резать толстые металлы, но не требуется высокая точность лазерной резки.
Эксплуатационные расходы
- Лазерная резка: Хотя первоначальная стоимость станки для лазерной резки чем выше, тем ниже эксплуатационные расходы с течением времени. Лазерная резка потребляет меньше энергии во время работы, особенно при использовании эффективных волоконных лазеров. Расходные материалы, такие как вспомогательные газы (например, азот, кислород или сжатый воздух), относительно недороги и способствуют общей эффективности машины. Кроме того, поскольку лазерная резка обеспечивает точные, чистые разрезы, часто нет необходимости в последующей обработке, что снижает затраты на рабочую силу, связанные с отделочными работами.
- Плазменная резка: Установки плазменной резки имеют более высокие эксплуатационные расходы по сравнению с установками лазерной резки. Это в первую очередь связано с большим потреблением энергии, необходимым для создания и поддержания плазменной дуги. Расходные материалы, такие как электроды и сопла, изнашиваются быстрее при плазменной резке и требуют более частой замены. Использование газов (таких как кислород, азот или аргон) для резки также увеличивает текущие эксплуатационные расходы. Кроме того, материалы, разрезанные плазмой, часто требуют вторичной отделки, такой как шлифовка или зачистка, для сглаживания грубых краев, что увеличивает затраты на рабочую силу.
Расходы на техническое обслуживание
- Лазерная резка: Лазерные режущие станки требуют регулярного обслуживания для обеспечения долговечности лазерного источника и других компонентов. Однако волоконные лазеры известны своим долгим сроком службы и низкими требованиями к обслуживанию по сравнению со старыми CO2-лазерами. Наиболее распространенные задачи по обслуживанию включают очистку оптики и замену изношенных линз или зеркал, но эти задачи, как правило, недороги и выполняются нечасто. При правильном обслуживании волоконные лазеры могут иметь минимальное время простоя и относительно низкие расходы на обслуживание в течение всего срока службы.
- Плазменная резка: плазменные резаки, хотя и более просты по конструкции, как правило, требуют более высоких затрат на техническое обслуживание с течением времени. Расходные детали, такие как электроды, сопла и щитки, требуют регулярной замены из-за износа, вызванного плазменной дугой. Кроме того, эти детали могут изнашиваться быстрее при резке более толстых материалов на более высоких уровнях мощности. Частота замены увеличивает долгосрочные расходы на техническое обслуживание. Хотя стоимость одной детали может быть низкой, необходимость частой замены может со временем привести к увеличению расходов.
Потребление энергии
- Лазерная резка: Одно из самых больших преимуществ лазерной резки — ее энергоэффективность. В частности, машины для резки волоконным лазером потребляют значительно меньше электроэнергии, чем плазменные резаки, особенно при резке тонких материалов. Высокосфокусированный лазерный луч обеспечивает эффективную резку без необходимости использования чрезмерной мощности. Для компаний, стремящихся сократить свои энергетические затраты и эксплуатационные расходы, лазерная резка часто является лучшим выбором, особенно для долгосрочного использования.
- Плазменная резка: машины для плазменной резки, хотя и эффективны для резки толстых материалов, как правило, потребляют больше энергии. Процесс ионизации газа для создания плазменной дуги требует значительной электрической мощности, особенно при работе с высокой силой тока для более толстых материалов. Потребление энергии машиной для плазменной резки может быть в 2–3 раза выше, чем у резака с волоконным лазером, что делает его эксплуатацию более дорогой в долгосрочной перспективе.
Заключение: Сравнение стоимости
- Начальные инвестиции: Станки для лазерной резки имеют более высокую первоначальную стоимость, но предлагают превосходную точность и возможности. Станки для плазменной резки изначально более доступны, что делает их идеальными для предприятий, которые фокусируются на толстых материалах без необходимости в чрезвычайной точности.
- Эксплуатационные расходы: Лазерная резка имеет более низкие эксплуатационные расходы из-за меньшего количества расходных материалов, эффективного использования энергии и минимальных требований к постобработке. Плазменная резка, хотя и менее затратна для приобретения, влечет более высокие эксплуатационные расходы из-за частой замены расходных материалов и более высокого потребления энергии.
- Расходы на обслуживание: Лазерная резка обычно требует меньшего обслуживания, особенно с более прочными волоконными лазерами. Плазменная резка, хотя и проста, требует частой замены деталей, что приводит к более высоким долгосрочным расходам на обслуживание.
- Потребление энергии: Лазерная резка, особенно с использованием волоконных лазеров, намного более энергоэффективна, чем плазменная резка, для работы которой требуется больше энергии.
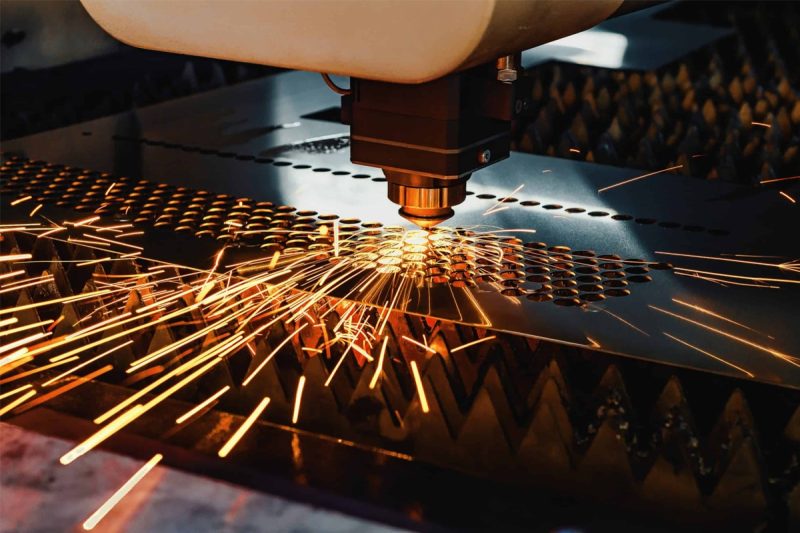
Воздействие на окружающую среду: лазерная резка против плазменной резки
Энергоэффективность
- Лазерная резка: Лазерная резка, особенно волоконные лазеры, известна своей высокой энергоэффективностью. Волоконные лазеры могут преобразовывать электрическую энергию в свет с минимальными отходами, используя меньше энергии для создания необходимой силы резки. Это сниженное потребление энергии делает лазерную резку более экологически чистой, особенно при резке тонких и средних по толщине материалов. Кроме того, точный и контролируемый характер лазерной резки снижает отходы материала, способствуя более устойчивому производственному процессу.
- Плазменная резка: плазменная резка, хотя и эффективна для резки более толстых материалов, в целом менее энергоэффективна по сравнению с лазерной резкой. Процесс генерации и поддержания плазменной дуги потребляет значительное количество электроэнергии, особенно при резке толстых металлических пластин. Эта более высокая потребность в энергии приводит к большему углеродному следу, что делает плазменную резку менее экологичным вариантом с точки зрения потребления энергии.
Выбросы и качество воздуха
- Лазерная резка: Лазерная резка обычно производит меньше вредных выбросов во время работы. Хотя в процессе резки используются такие газы, как азот или кислород, они не выделяют значительных загрязняющих веществ. Волоконные лазеры, в частности, оказывают минимальное воздействие на окружающую среду с точки зрения качества воздуха. Однако при резке определенных материалов, таких как пластик или композиты, лазерная резка может выделять пары, которые требуют надлежащей вентиляции или систем фильтрации для защиты работников и снижения загрязнения воздуха.
- Плазменная резка: плазменная резка выделяет больше загрязняющих веществ из-за ионизации газов, включая кислород, азот или аргон, во время процесса резки. Тепло, выделяемое плазменной резкой, может привести к выделению опасных паров, особенно при резке покрытых или обработанных металлов. Эти пары могут содержать вредные частицы и газы, такие как оксиды азота (NOx), которые могут способствовать загрязнению воздуха и представлять опасность для здоровья операторов. Поэтому плазменная резка обычно требует более надежных систем вентиляции и фильтрации для смягчения ее воздействия на качество воздуха.
Материальные отходы
- Лазерная резка: Одним из ключевых экологических преимуществ лазерной резки является ее способность производить минимальные отходы материала. Точность лазерной резки позволяет использовать более жесткие допуски и меньшие пропилы (ширину реза), что означает меньшие потери материала в процессе резки. Это не только снижает количество производимых отходов, но и повышает эффективность использования материала, делая лазерную резку более экологичным выбором, особенно для дорогих материалов.
- Плазменная резка: плазменная резка имеет тенденцию производить больше отходов материала из-за более широкого реза и более грубых кромок, которые она оставляет на разрезаемых материалах. Большая зона термического влияния (HAZ) также может привести к деформации или короблению, что приводит к дополнительным отходам материала. Более того, детали, вырезанные плазмой, часто требуют последующей обработки для удаления заусенцев и грубых кромок, что приводит к дальнейшим потерям материала. Это делает плазменную резку менее эффективной и потенциально более расточительной с точки зрения использования сырья.
Расходные материалы и использование ресурсов
- Лазерная резка: Лазерная резка, особенно с использованием волоконных лазеров, имеет относительно низкие требования к расходным материалам. Волоконные лазеры не требуют частой замены компонентов, таких как электроды или сопла, что делает их более экологически устойчивыми с течением времени. Вспомогательные газы, используемые при лазерной резке (азот или кислород), также широко доступны и оказывают меньшее воздействие на окружающую среду по сравнению с газами, используемыми при плазменной резке.
- Плазменная резка: плазменная резка в большей степени зависит от расходных материалов, включая электроды, сопла и щитки, которые требуют регулярной замены из-за износа. Эта частая потребность в расходных деталях не только увеличивает эксплуатационные расходы, но и увеличивает потребление ресурсов и образование отходов. Утилизация изношенных компонентов, особенно если они не перерабатываются должным образом, вносит свой вклад в экологический след плазменной резки.
Шумовое загрязнение
- Лазерная резка: Лазерная резка работает относительно тихо по сравнению с другими промышленными методами резки. Процесс резки производит минимальный шум, что способствует более безопасной и приятной рабочей среде. Снижение шумового загрязнения также является экологическим преимуществом, особенно в городских или жилых районах, где нормы по шуму могут быть строгими.
- Плазменная резка: плазменная резка создает больше шума, особенно при резке толстых материалов на высокой мощности. Шум, производимый плазменной дугой и выбросом расплавленного металла, может способствовать шумовому загрязнению на рабочем месте, что требует защиты органов слуха для операторов. Чрезмерный уровень шума также может нарушать окружающую среду, делая плазменную резку менее желательной в зонах, чувствительных к шуму.
Заключение: Воздействие на окружающую среду
- Энергоэффективность: Лазерная резка, особенно с использованием волоконных лазеров, более энергоэффективна, чем плазменная резка, что делает ее более экологичным вариантом.
- Выбросы: плазменная резка выделяет больше вредных паров и частиц, особенно при резке покрытых или обработанных металлов. Лазерная резка производит меньше выбросов, но все равно может потребовать надлежащей вентиляции для определенных материалов.
- Отходы материала: лазерная резка производит меньше отходов благодаря своей точности, в то время как плазменная резка производит больше отходов и может потребовать дополнительной постобработки.
- Расходные материалы: плазменная резка требует больше расходных материалов, что приводит к более высокому использованию ресурсов и образованию отходов, в то время как лазерная резка требует меньше расходных материалов.
- Шумовое загрязнение: Лазерная резка тише и производит меньше шумового загрязнения по сравнению с более громким процессом плазменной резки.
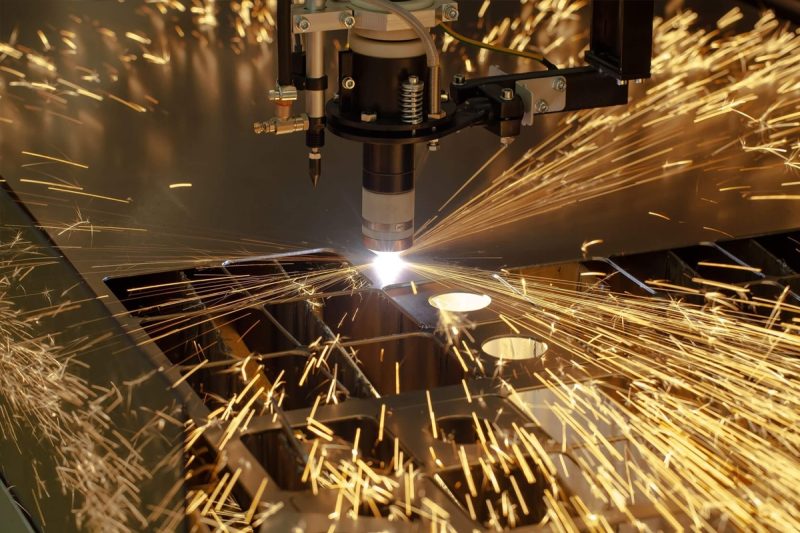
Краткое содержание
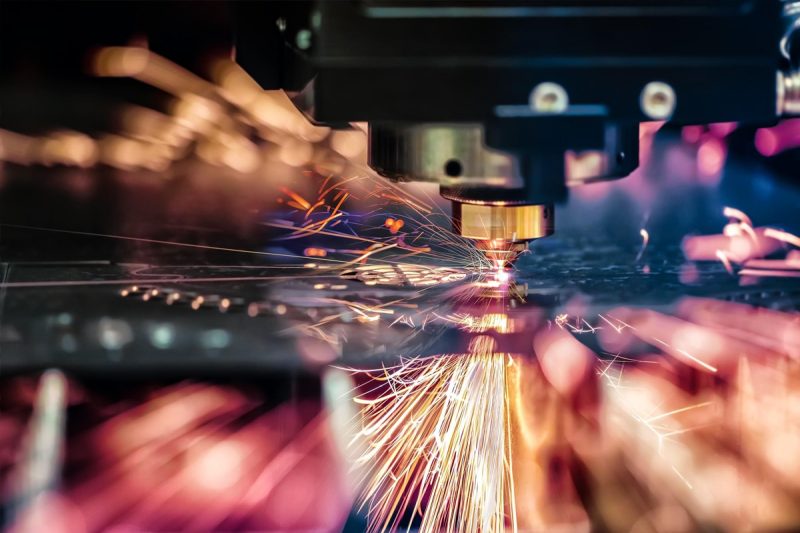
Получите лазерные решения с AccTek Laser
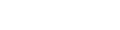
- [email protected]
- [email protected]
- +86-19963414011
- Зона № 3 А, промышленная зона Лунчжэнь, город Юйчэн, провинция Шаньдун.