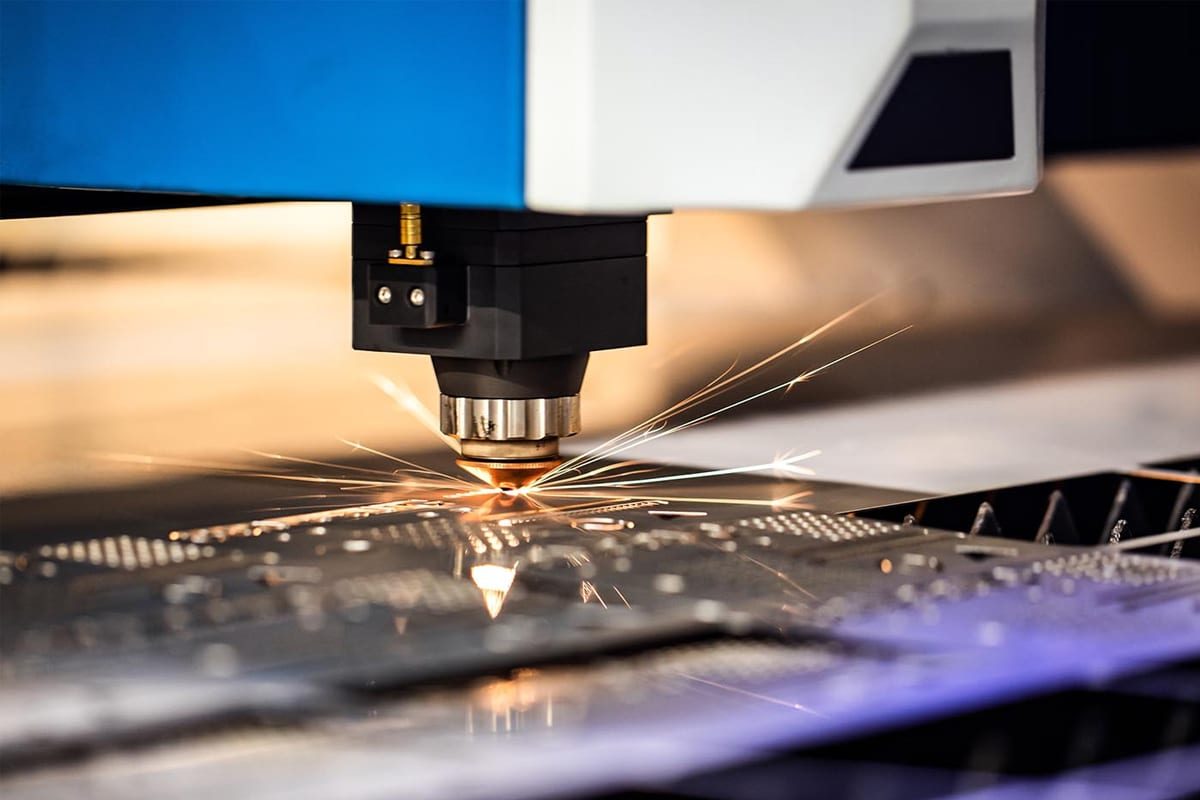
Волоконная лазерная резка VS плазменная резка
В динамичном мире металлообработки выбор правильной технологии резки помогает достичь точности, эффективности и экономичности. Резка волоконным лазером и плазменная резка — два выдающихся метода, которые произвели революцию в отрасли. В этой статье представлено всестороннее сравнение резки волоконным лазером и плазменной резки, рассматриваются их принципы, преимущества, ограничения и идеальные области применения. Углубляясь в особенности каждого метода, мы стремимся снабдить вас знаниями для принятия обоснованных решений, которые соответствуют вашим производственным потребностям и расширяют ваши эксплуатационные возможности.
Оглавление
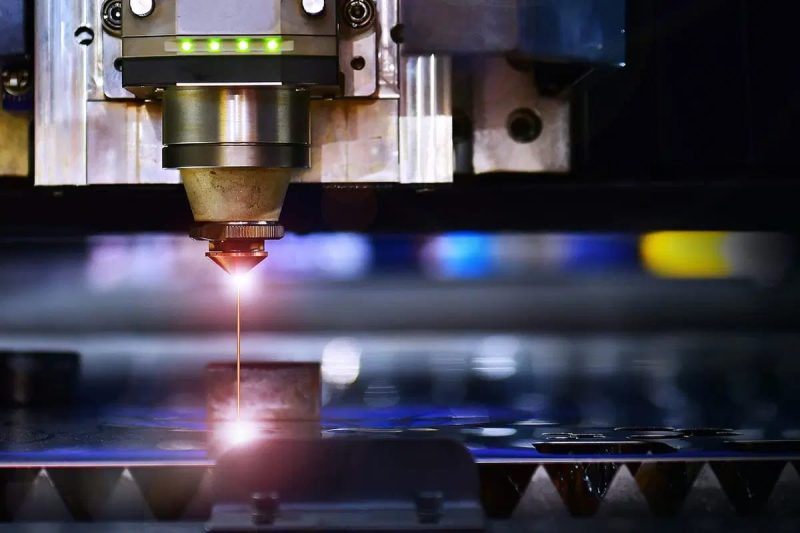
Что такое волоконная лазерная резка?
Определение и основные принципы
Резка волоконным лазером — это современный производственный процесс, который использует мощный волоконный лазерный луч для резки и гравировки материалов с исключительной точностью и скоростью. Технология основана на усилении света в оптических волокнах, легированных редкоземельными элементами, что приводит к образованию сфокусированного лазерного луча, способного плавить, сжигать или испарять материал контролируемым образом. Этот метод широко известен своей эффективностью при резке металлов и обеспечивает превосходное качество кромки по сравнению с традиционными методами резки.
Как работают волоконные лазеры
В основе волоконно-лазерной резки лежит сам волоконно-лазерный генератор, работающий по следующим принципам:
- Генерация лазера: затравочный лазер излучает маломощный луч света, который затем вводится в оптоволоконный кабель, легированный редкоземельными элементами, такими как иттербий.
- Усиление: Когда свет проходит через легированное волокно, он взаимодействует с ионами редкоземельных металлов, заставляя их испускать дополнительные фотоны той же длины волны и фазы — процесс, известный как стимулированное излучение. Это усиливает свет в мощный лазерный луч.
- Доставка луча: усиленный лазерный свет передается по гибким оптоволоконным кабелям к режущей головке без необходимости использования сложных зеркал или линз.
- Фокусировка луча: режущая головка содержит линзу, которая фокусирует лазерный луч на очень маленькую точку на поверхности материала, достигая чрезвычайно высокой плотности мощности.
- Взаимодействие с материалом: Концентрированная энергия расплавляет или испаряет материал в фокусе. Вспомогательные газы, такие как азот или кислород, часто используются для выдувания расплавленного материала, улучшая процесс резки и предотвращая окисление.
- Управляемое движение: система числового программного управления (ЧПУ) управляет движением режущей головки или заготовки, следуя точным шаблонам для достижения желаемых форм реза.
Преимущества
- Высокая точность и качество: волоконные лазеры обеспечивают малый диаметр фокуса и высокую плотность энергии, что обеспечивает точные, чистые разрезы с минимальной тепловой деформацией.
- Эффективность: они обеспечивают более высокую скорость резки, особенно при работе с тонкими и средними по толщине материалами, что повышает производительность.
- Универсальность: Возможность резки широкого спектра металлов, включая сталь, нержавеющую сталь, алюминий, латунь и медь.
- Низкие эксплуатационные расходы: волоконные лазерные генераторы имеют твердотельную конструкцию без подвижных частей или зеркал в источнике генерации света, что снижает требования к техническому обслуживанию и время простоя.
- Энергоэффективность: они потребляют меньше энергии по сравнению с традиционными Станки для лазерной резки CO2 и системы плазменной резки, что приводит к снижению эксплуатационных расходов.
- Длительный срок службы: Диоды в волоконных лазерах имеют длительный срок службы, часто превышающий 100 000 часов работы.
- Компактная конструкция: волоконно-оптическая система доставки позволяет уменьшить площадь установки машины, экономя ценное пространство на полу.
Недостатки
- Высокие первоначальные инвестиции: передовые технологии и компоненты приводят к более высоким первоначальным затратам по сравнению с другими методами резки, такими как плазменная резка.
- Ограничения по материалам: Волоконные лазеры менее эффективны на более толстых материалах (обычно более 25 мм для стали) и не подходят для неметаллических материалов, таких как дерево или пластик.
- Проблемы с отражающими материалами: резка металлов с высокой отражающей способностью, таких как медь и латунь, может представлять сложность из-за потенциального повреждения источника лазерного излучения обратным отражением, хотя современные станки оснащены функциями, позволяющими снизить этот риск.
- Требуются технические знания: операторам необходимо пройти специальную подготовку для работы с оборудованием и оптимизации параметров резки для различных материалов.
Приложения
Резка волоконным лазером применяется в различных отраслях промышленности благодаря своей точности и эффективности:
- Аэрокосмическая промышленность: для резки сложных деталей, требующих высокой точности и минимального термического воздействия.
- Автомобилестроение: производство таких деталей, как кузовные панели, компоненты двигателя и сложные конструкции.
- Электроника: резка небольших, точных деталей, используемых в электронных устройствах и схемах.
- Медицинские приборы: производство хирургических инструментов и медицинского оборудования, требующих высокой точности.
- Изготовление металлоконструкций: общие производственные работы, включающие изготовление нестандартных металлических деталей, корпусов и конструктивных элементов.
- Изготовление ювелирных изделий: создание сложных конструкций из драгоценных металлов с высокой точностью.
- Вывески и декоративно-прикладное искусство: создание детализированных металлических вывесок, произведений искусства и декоративных элементов.
Используя преимущества волоконно-лазерной резки, производители могут добиться превосходного качества, сократить сроки производства и расширить свои возможности для удовлетворения растущих потребностей современных отраслей промышленности.
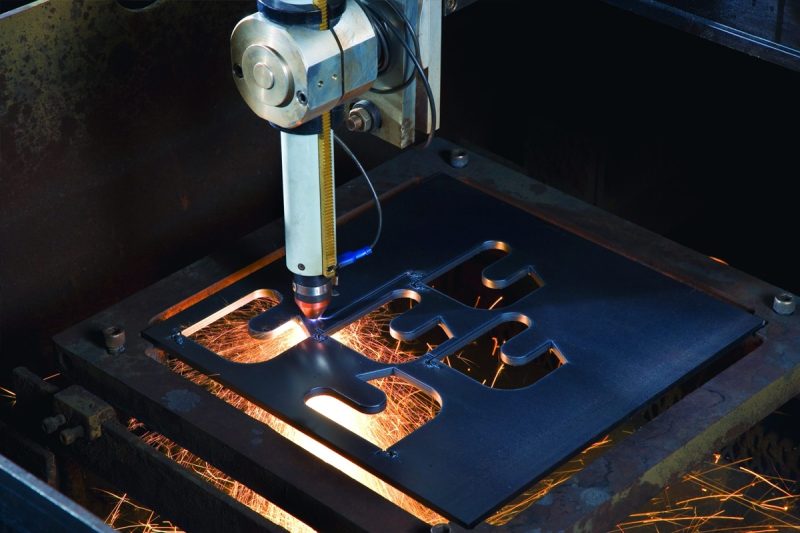
Что такое плазменная резка?
Определение и основные принципы
Плазменная резка — это процесс термической резки, который использует высокоскоростную струю ионизированного газа, известного как плазма, для расплавления и разделения электропроводящих материалов. Процесс включает в себя создание электрической дуги, которая проходит через газ, преобразуя его в плазму, способную достигать температуры до 30 000 ℃ (54 000 ℉). Это интенсивное тепло плавит металл, в то время как кинетическая энергия высокоскоростного газа удаляет расплавленный материал, создавая чистый срез. Плазменная резка широко используется из-за ее эффективности при резке толстых металлов и ее способности работать с различными проводящими материалами.
Как работает плазменная резка
Процесс плазменной резки работает по следующим принципам:
- Инициирование дуги: Источник электроэнергии создает дугу постоянного тока (DC) между электродом (отрицательный заряд) внутри плазменной горелки и заготовкой (положительный заряд).
- Ионизация газа: сжатый газ (например, воздух, азот, аргон или кислород) на большой скорости подается через узкое сопло в дугу. Интенсивная энергия дуги ионизирует газ, превращая его в плазму.
- Формирование плазменной струи: Плазма выходит из сопла в виде сфокусированной, высокоскоростной струи ионизированного газа. Узкое сопло сужает дугу, увеличивая ее температуру и скорость.
- Плавление материала: плазменная струя достигает чрезвычайно высоких температур, плавя материал в точке контакта.
- Удаление материала: высокоскоростная плазма и вторичные газы выдувают расплавленный металл из реза, оставляя узкий пропил.
- Управляемое движение: плазменная горелка направляется по желаемой траектории резки вручную или с помощью системы числового программного управления (ЧПУ) для достижения точных резов.
Преимущества
- Возможность резки толстых материалов: плазменная резка отлично подходит для резки толстых металлических пластин, часто до 80 мм (3 дюймов) и более, в зависимости от мощности плазменной системы.
- Универсальность: Эффективен для всех электропроводящих металлов, включая углеродистую сталь, нержавеющую сталь, алюминий, медь, латунь и чугун.
- Высокие скорости резки: быстрее, чем при кислородной резке материалов толщиной менее 50 мм, что повышает производительность при обработке металла.
- Меньшие первоначальные инвестиции: как правило, первоначальные затраты ниже по сравнению с системами резки волоконным лазером, что делает их доступными для малого и среднего бизнеса.
- Простота использования: более простая настройка и эксплуатация, требующая меньших технических знаний по сравнению с системами лазерной резки.
- Портативность: Оборудование для плазменной резки может быть относительно компактным и портативным, подходящим для проведения ремонтных и строительных работ на месте.
Недостатки
- Более низкая точность: плазменная резка обеспечивает более широкий пропил (ширину реза) и менее точные разрезы по сравнению с резкой волоконным лазером, что может потребовать дополнительной отделки.
- Зона термического влияния (ЗТВ): Образует большую ЗТВ, что может изменить свойства металла вблизи кромки реза и привести к короблению или искажению.
- Более грубое качество кромок: кромки могут иметь больше окалины (остаточного шлака) и быть шероховатыми, что требует вторичной обработки для применений, требующих высококачественной отделки.
- Ограниченная возможность мелкой детализации: не подходит для резки сложных узоров или небольших отверстий из-за размера плазменной дуги и ширины реза.
- Более высокое энергопотребление: как правило, потребляет больше электроэнергии, чем волоконные лазерные системы, что со временем приводит к увеличению эксплуатационных расходов.
- Угрозы безопасности: создает интенсивный свет, шум и пары, требуя соответствующих мер безопасности, таких как защита глаз, защита органов слуха и надлежащая вентиляция.
Приложения
Плазменная резка широко применяется в отраслях промышленности и там, где требуется резка толстых токопроводящих металлов:
- Строительство и инфраструктура: резка элементов конструкционной стали для зданий, мостов и инфраструктурных проектов.
- Судостроение: изготовление крупных стальных секций для судов и морских платформ.
- Ремонт и производство автомобилей: резка и ремонт компонентов шасси, рам и деталей кузова.
- Цеха по изготовлению металлоконструкций: общее изготовление тяжелых металлических деталей, сборка по индивидуальному заказу и ремонтные работы.
- Производство сельскохозяйственной и тяжелой техники: производство комплектующих для тракторов, экскаваторов и промышленного оборудования.
- Переработка металлолома: резка крупных металлических изделий на более мелкие части для переработки.
- Техническое обслуживание и ремонт: Резка и модификация металлоконструкций и оборудования на месте в различных отраслях промышленности.
Понимание основ плазменной резки позволяет производителям оценить ее пригодность для своих конкретных нужд. Хотя плазменная резка дает преимущества при резке толстых материалов и более низкие первоначальные затраты, она может не соответствовать точности и качеству кромок, которые обеспечивают системы резки волоконным лазером.
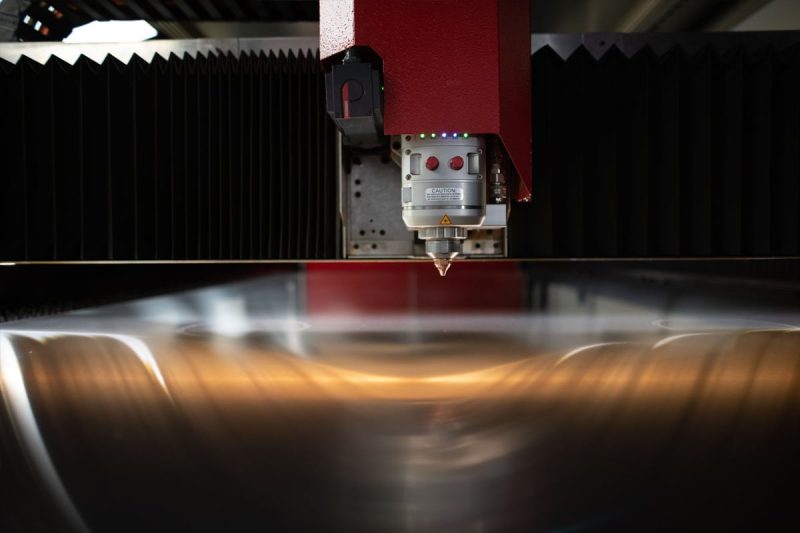
Сравнение резки волоконным лазером и плазменной резки
При выборе между волоконной лазерной резкой и плазменной резкой важно понимать, как каждый метод работает по различным критериям. Ниже приведено подробное сравнение, которое подчеркивает сильные и слабые стороны обеих технологий.
Качество резки
Волоконный лазер для резки
- Качество кромок: обеспечивает превосходное качество кромок с гладкими, чистыми срезами и минимальным количеством окалины (остаточного шлака).
- Зона термического влияния (ЗТВ): Меньшая ЗТВ из-за концентрированного лазерного луча, что снижает риск тепловой деформации.
- Точная резка: идеально подходит для сложных конструкций и жестких допусков, что делает его пригодным для применений, требующих высокой точности.
Плазменная резка
- Качество кромок: обычно дает более грубые кромки с большим количеством окалины, что может потребовать вторичной отделки.
- Зона термического влияния (ЗТВ): большая зона термического влияния из-за более широкой плазменной дуги, что увеличивает вероятность коробления и искажения.
- Грубая резка: лучше подходит для менее детальной работы, где сверхтонкая точность не имеет решающего значения.
Скорость резки
Волоконный лазер для резки
- Тонкие и средние материалы: обеспечивает более высокую скорость резки тонких и средних металлов (обычно до 25 мм для стали).
- Эффективность: Высокоскоростная обработка повышает производительность и сокращает сроки выполнения заказов.
Плазменная резка
- Толстые материалы: Обычно быстрее при резке толстых материалов (более 25 мм), где эффективность лазера снижается.
- Компромисс между скоростью и качеством: несмотря на возможность работы на высоких скоростях, увеличение скорости может еще больше ухудшить качество реза.
Совместимость материалов
Волоконный лазер для резки
- Металлические материалы: отлично подходит для резки различных металлов, включая углеродистую сталь, нержавеющую сталь, алюминий, латунь и медь.
- Неметаллы: Не подходит для резки неметаллических материалов из-за особенностей поглощения длины волны лазера.
- Отражающие металлы: Современные волоконные лазеры могут обрабатывать отражающие металлы, такие как медь и латунь, при использовании соответствующей технологии для предотвращения повреждений, вызванных обратным отражением.
Плазменная резка
- Проводящие металлы: может резать все электропроводящие металлы, включая сталь, нержавеющую сталь, алюминий, медь, латунь и чугун.
- Неметаллы: неэффективен для непроводящих материалов, таких как пластик, стекло или дерево.
Возможности толщины
Волоконный лазер для резки
- Оптимальный диапазон толщины: высокоэффективен для материалов тонкой и средней толщины, обычно до 25 мм для стали.
- Ограничения для толстых материалов: резка более толстых материалов может потребовать значительно больше мощности и привести к снижению качества и скорости резки.
Плазменная резка
- Резка толстых материалов: позволяет эффективно резать более толстые материалы, часто до 80 мм и более в зависимости от мощности плазменной системы.
- Тонкие материалы: может резать тонкие материалы, но может вызвать чрезмерное нагревание, что приведет к короблению или снижению качества резки.
Точность и аккуратность
Волоконный лазер для резки
- Высокая точность: обеспечивает чрезвычайно жесткие допуски и сложную резку с точностью, часто составляющей ±0,1 мм.
- Малая ширина реза: узкая фокусировка лазерного луча обеспечивает минимальный пропил, что позволяет экономить материал и создавать детальные конструкции.
Плазменная резка
- Средняя точность: подходит для применений, где точность не столь важна, с допусками обычно в пределах от ±0,5 мм до ±1 мм.
- Большая ширина реза: плазменная дуга создает более широкий разрез, что может ограничить возможность резки мелких деталей или близко расположенных компонентов.
Эксплуатационные расходы
Волоконный лазер для резки
- Первоначальные инвестиции: более высокие первоначальные затраты из-за передовых технологий и оборудования.
- Эксплуатационные расходы: более низкие текущие расходы обусловлены более высокой энергоэффективностью и сокращением использования расходных материалов.
- Потребление энергии: более энергоэффективно, что со временем приводит к снижению затрат на электроэнергию.
Плазменная резка
- Первоначальные инвестиции: более низкая цена покупки делает ее доступной для предприятий с ограниченным бюджетом.
- Эксплуатационные расходы: более высокие эксплуатационные расходы из-за большего потребления энергии и частой замены расходных материалов, таких как электроды и сопла.
- Расходные материалы: Постоянные расходы на расходные материалы могут накапливаться, увеличивая общую стоимость владения.
Обслуживание
Волоконный лазер для резки
- Низкие требования к техническому обслуживанию: Твердотельная конструкция с меньшим количеством движущихся частей снижает потребность в техническом обслуживании.
- Долговечность компонентов: ключевые компоненты, такие как диоды, имеют длительный срок службы, часто превышающий 100 000 часов.
- Простои: менее частое техническое обслуживание приводит к повышению доступности и производительности оборудования.
Плазменная резка
- Более высокие требования к техническому обслуживанию: расходные детали, такие как электроды и сопла, требуют регулярной замены из-за износа.
- Износ оборудования: Интенсивное тепло и электрические дуги могут привести к более частому обслуживанию и замене деталей.
- Простои: Увеличение объема технического обслуживания может привести к увеличению простоев оборудования, что скажется на производительности.
Соображения безопасности
Волоконный лазер для резки
- Лазерное излучение: требуются строгие меры безопасности для защиты операторов от воздействия лазера, включая защитные очки и кожухи.
- Вытяжка дыма: При резке металлов могут образовываться дымы, поэтому требуются надлежащие системы вентиляции или вытяжки.
- Уровень шума: в целом более тихая работа по сравнению с плазменной резкой.
Плазменная резка
- Риск поражения электрическим током: Высокое напряжение и ток представляют опасность поражения электрическим током, если не соблюдать правила безопасности.
- УФ- и инфракрасное излучение: создает интенсивное УФ- и ИК-излучение, требующее защитной одежды и защиты глаз.
- Выделение дыма и шума: производит значительное количество дыма и высокий уровень шума, требующий защиты органов слуха и эффективной системы вентиляции.
Воздействие на окружающую среду
Волоконный лазер для резки
- Энергоэффективность: более высокая энергоэффективность, снижение общего углеродного следа операций.
- Сокращение выбросов: выделяет меньше дыма и выбросов по сравнению с плазменной резкой.
- Вспомогательные газы: Используются инертные газы, такие как азот, которые оказывают минимальное воздействие на окружающую среду.
Плазменная резка
- Более высокое потребление энергии: Менее эффективное использование энергии приводит к большему воздействию на окружающую среду.
- Образование дыма: производит больше дыма и твердых частиц, которые могут повлиять на качество воздуха, если не контролировать их должным образом.
- Расходные материалы: Частая замена расходных материалов увеличивает образование отходов.
При рассмотрении этих критических факторов становится очевидным, что как волоконная лазерная резка, так и плазменная резка имеют определенные преимущества и ограничения. Волоконная лазерная резка является предпочтительным выбором для приложений, требующих высокой точности, превосходного качества резки и эффективности на тонких и средних материалах. Напротив, плазменная резка выгодна для резки более толстых материалов, где сверхвысокая точность менее критична, а первоначальные инвестиционные затраты являются важным фактором.
Выбор правильной технологии зависит от таких факторов, как типы обрабатываемых материалов, требуемый диапазон толщины, желаемое качество резки, соображения эксплуатационных расходов, а также приоритеты в области охраны окружающей среды и безопасности. Используя сильные стороны каждого метода, производители могут оптимизировать свои производственные процессы, снизить затраты и улучшить общее качество продукции.
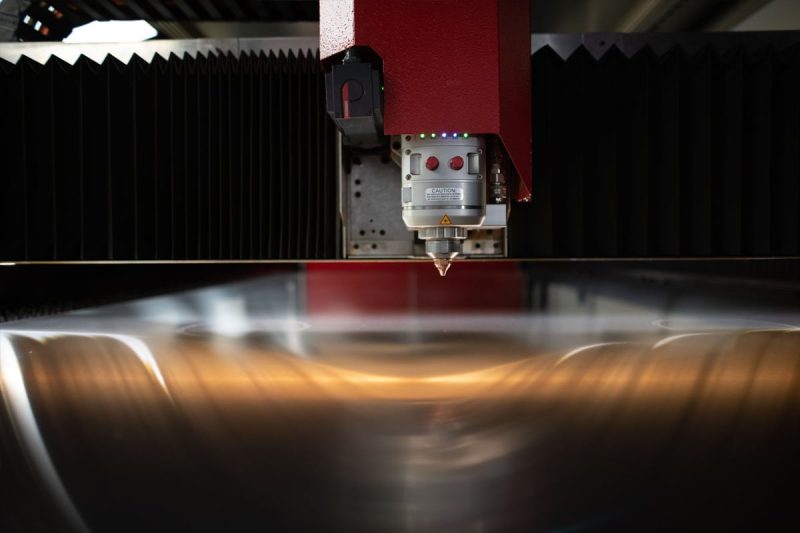
Выбор между волоконным лазером и плазменной резкой
Выбор подходящей технологии резки для ваших производственных нужд является критически важным решением, которое может существенно повлиять на эффективность вашего производства, качество продукции и общие эксплуатационные расходы. Как резка волоконным лазером, так и плазменная резка предлагают уникальные преимущества и подходят для различных применений.
Факторы, которые следует учитывать
Тип и толщина материала
- Совместимость материалов: Резка волоконным лазером идеально подходит для таких металлов, как углеродистая сталь, нержавеющая сталь, алюминий, латунь и медь. Плазменная резка эффективна для всех электропроводящих металлов, но может иметь проблемы с качеством резки цветных металлов.
- Возможности толщины: Волоконные лазеры отлично подходят для резки тонких и средних материалов (до 25 мм), обеспечивая высокую точность и скорость. Плазменные резаки эффективно обрабатывают более толстые материалы (до 80 мм и более), но с меньшей точностью.
Точность и качество резки
- Требования к точности: если ваши проекты требуют высокой точности с минимальной шероховатостью кромок, волоконная лазерная резка станет лучшим выбором.
- Качество кромок: Волоконные лазеры создают более гладкие кромки с меньшей зоной термического воздействия (ЗТВ), что снижает необходимость во вторичной отделке. Плазменная резка может привести к более грубым кромкам и большей ЗТВ.
Объем и скорость производства
- Скорость резки: Для тонких материалов волоконные лазеры обеспечивают более высокую скорость резки, повышая производительность для крупносерийного производства. Плазменные резаки могут быть быстрее на более толстых материалах, но, как правило, медленнее на более тонких.
- Повторяемость: волоконные лазеры обеспечивают стабильные результаты, что имеет решающее значение для массового производства, где единообразие имеет решающее значение.
Эксплуатационные расходы
- Первоначальные инвестиции: Станки для резки волоконным лазером имеют более высокую первоначальную стоимость из-за передовых технологий. Машины плазменной резки изначально менее дороги.
- Эксплуатационные расходы: учитывайте потребление энергии, обслуживание и расходные материалы. Волоконные лазеры более энергоэффективны и требуют меньших затрат на долгосрочное обслуживание.
Сложность конструкции
- Сложные разрезы: Волоконные лазеры могут обрабатывать сложные и детальные конструкции с высокой точностью. Плазменные резаки менее подходят для сложных работ из-за более широкого реза.
Техническое обслуживание и время простоя
- Надежность машины: волоконные лазеры имеют меньше движущихся частей и требуют менее частого обслуживания, что приводит к сокращению времени простоя.
- Расходные материалы: машины плазменной резки требуют регулярной замены электродов и сопел, что увеличивает потребность в техническом обслуживании.
Безопасность и воздействие на окружающую среду
- Меры безопасности: волоконные лазеры требуют мер предосторожности против лазерного излучения, в то время как плазменная резка сопряжена с рисками, связанными с высокими температурами, УФ-излучением и парами.
- Экологические аспекты: волоконные лазеры более энергоэффективны и производят меньше выбросов, что соответствует принципам устойчивого развития.
Примеры применения
Производство автомобилей
- Резка волоконным лазером: используется для точной резки панелей кузова, сложных компонентов и нестандартных деталей, где точность имеет решающее значение.
- Плазменная резка: подходит для резки более толстых конструктивных компонентов, таких как рамы и детали шасси.
Изготовление Металлоконструкций
- Резка волоконным лазером: идеально подходит для создания детализированных металлических произведений искусства, вывесок и компонентов, требующих высокой точности.
- Плазменная резка: эффективна для общего изготовления деталей и оборудования большой грузоподъемности, где мелкие детали не столь важны.
Строительная промышленность
- Резка волоконным лазером: используется для резки металлических шпилек, кронштейнов и фитингов, требующих точности.
- Плазменная резка: подходит для резки больших стальных листов и балок, используемых в строительных конструкциях.
Судостроение и тяжелое машиностроение
- Резка волоконным лазером: применяется для резки тонких материалов, используемых в некоторых судовых компонентах и деталях машин.
- Плазменная резка: предпочтительна для резки толстых стальных листов и тяжелых компонентов на судах и в промышленном оборудовании.
Аэрокосмическая промышленность
- Резка волоконным лазером: применяется для прецизионной резки легких металлов и сплавов, используемых в компонентах самолетов.
- Плазменная резка: ограниченное применение из-за низкой точности, но может использоваться для резки более толстых опорных конструкций.
Анализ затрат и выгод
Первоначальные инвестиции
Резка волоконным лазером:
- Затраты: более высокая первоначальная цена покупки из-за сложных технологий и компонентов.
- Преимущества: Инвестиции приводят к повышению точности, улучшению качества резки и долгосрочной экономии эксплуатационных расходов.
Плазменная резка:
- Расходы: более низкие первоначальные затраты, что делает решение более доступным для предприятий с ограниченным бюджетом.
- Преимущества: Возможность мгновенной резки толстых материалов без значительных капитальных затрат.
Операционные затраты
Резка волоконным лазером:
- Потребление энергии: более энергоэффективно, что приводит к меньшим счетам за электроэнергию.
- Техническое обслуживание: более низкие затраты на техническое обслуживание за счет меньшего количества расходных материалов и менее частой замены деталей.
- Расходные материалы: Минимальные затраты на расходные материалы, в основном ограничиваются вспомогательными газами.
Плазменная резка:
- Потребление энергии: более высокое потребление энергии увеличивает эксплуатационные расходы.
- Техническое обслуживание: Более высокие затраты на техническое обслуживание из-за частой замены расходных материалов, таких как электроды и сопла.
- Расходные материалы: Текущие расходы на расходные материалы со временем могут увеличиться.
Производительность и качество
Резка волоконным лазером:
- Производительность: более высокие скорости резки тонких и средних материалов повышают производительность.
- Качество: Превосходное качество кромок снижает или исключает необходимость вторичной отделки, экономя время и трудозатраты.
Плазменная резка:
- Производительность: Эффективно для более толстых материалов, но может потребоваться дополнительное время на последующую обработку из-за более низкого качества резки.
- Качество: для достижения желаемой гладкости кромок может потребоваться шлифовка или полировка, что увеличивает затраты на рабочую силу.
Возврат инвестиций (ROI)
Резка волоконным лазером:
- Долгосрочная экономия: энергоэффективность и низкие эксплуатационные расходы со временем способствуют экономии средств.
- Рыночное преимущество: Высокая точность и качество могут открыть новые возможности для бизнеса и повысить удовлетворенность клиентов.
Плазменная резка:
- Доступность в краткосрочной перспективе: более низкие первоначальные затраты обеспечивают более быстрое развертывание.
- Ограничения: потенциально более высокие долгосрочные затраты из-за обслуживания и более низкой эффективности.
Выбор между волоконно-лазерной и плазменной резкой зависит от ваших конкретных эксплуатационных требований, бюджета и долгосрочных бизнес-целей. Если ваша работа в основном заключается в резке тонких и средних металлов с необходимостью высокой точности и превосходного качества кромок, то выгодно инвестировать в станок для волоконно-лазерной резки. Более высокая начальная стоимость компенсируется более низкими эксплуатационными расходами и возможностью производить высококачественную продукцию, соответствующую строгим отраслевым стандартам.
И наоборот, если ваши операции сосредоточены на резке более толстых материалов, где точность не так важна, и вам нужно экономически эффективное решение с меньшими начальными инвестициями, плазменная резка может быть подходящим выбором. Она обеспечивает возможность эффективного выполнения тяжелых задач по резке.
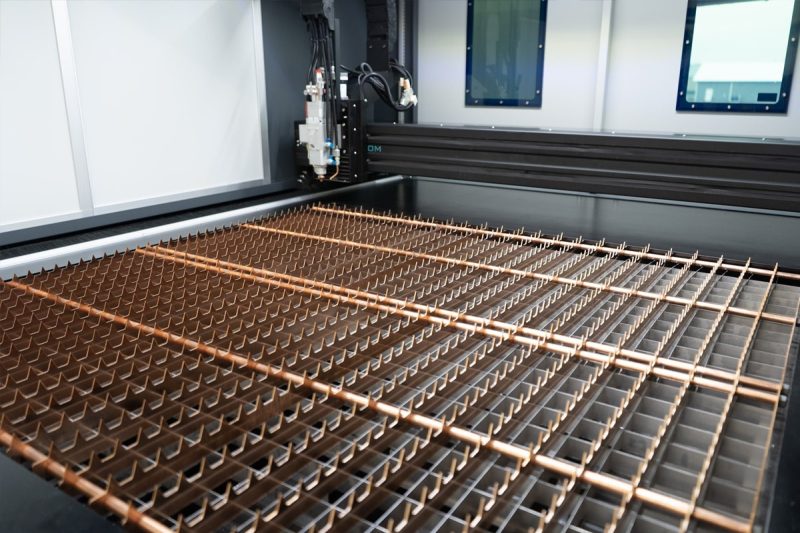
Краткое содержание
Выбор правильной техники резки может помочь достичь наилучших результатов при изготовлении металла. Резка волоконным лазером отличается высокой точностью, превосходным качеством кромок и эффективностью резки тонких и средних металлов. Она идеально подходит для отраслей, где требуются сложные конструкции и жесткие допуски. С другой стороны, плазменная резка отлично подходит для резки более толстых материалов и предлагает меньшие первоначальные инвестиции, хотя она может давать более грубые кромки, требующие дополнительной отделки. Такие факторы, как тип и толщина материала, требуемая точность, эксплуатационные расходы и особые требования к применению, играют важную роль в определении наиболее подходящего метода. Тщательно оценив эти факторы, производители могут выбрать технологию резки, которая наилучшим образом соответствует их производственным целям и бюджетным ограничениям.
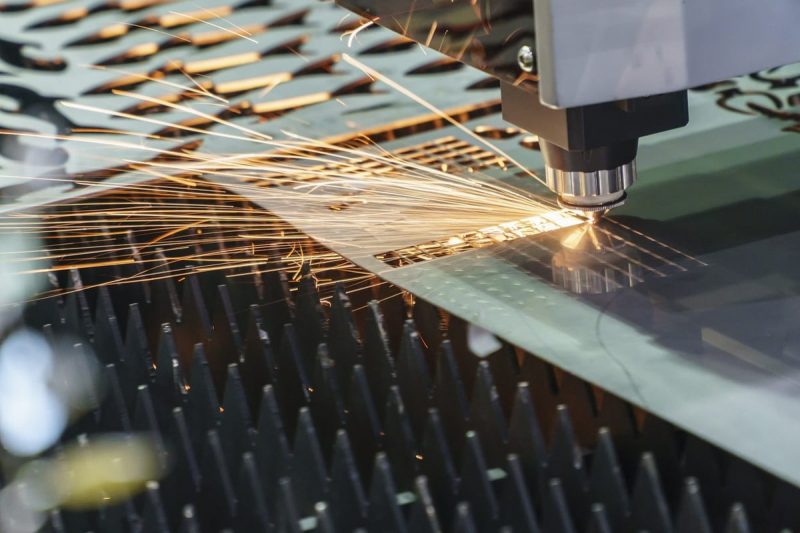
Получите решения для лазерной резки
Если вы определили, что волоконно-лазерная резка является оптимальным выбором для ваших производственных нужд, AccTek Laser готова предоставить вам передовые решения. Как профессиональный производитель лазерных режущих станков, мы специализируемся на поставке высококачественных волоконно-лазерных режущих систем, которые сочетают в себе точность, эффективность и надежность. Наши станки предназначены для обработки широкого спектра материалов и толщин, что делает их подходящими для различных отраслей промышленности, таких как аэрокосмическая, автомобильная, электронная и металлообработка.
В Актек Лазер, мы предлагаем персонализированные решения, адаптированные к вашим конкретным приложениям. Наша команда экспертов будет тесно сотрудничать с вами, чтобы понять ваши требования и порекомендовать наиболее подходящее оборудование из нашей обширной линейки продукции. Мы стремимся помочь вам улучшить ваши производственные возможности, сократить эксплуатационные расходы и достичь превосходного качества резки.
В дополнение к станки для лазерной резки, мы также предоставляем лазерные сварочные аппараты, машины для лазерной очистки, и машины для лазерной маркировки, предлагая комплексный набор лазерных технологий для решения всех ваших производственных задач. Выбирая AccTek Laser, вы инвестируете в передовые технологии, которые дадут вам конкурентное преимущество на сегодняшнем быстро меняющемся рынке.
Свяжитесь с нами сегодня, чтобы узнать, как наши решения для резки волоконным лазером могут преобразовать ваши операции и продвинуть ваш бизнес вперед. Позвольте нам стать вашим партнером в достижении совершенства в точном изготовлении металла.
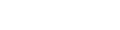
Контактная информация
- [email protected]
- [email protected]
- +86-19963414011
- Зона № 3 А, промышленная зона Лунчжэнь, город Юйчэн, провинция Шаньдун.
Получить лазерные решения