
Как резка лазером CO2 минимизирует отходы материала?
Технология резки лазером CO2 широко используется в производстве, особенно в обработке металла, резке пластика, гравировке дерева и других областях. Лазерная резка ценится за точность, скорость и гибкость. Однако отходы материала — это проблема, которую нельзя игнорировать в процессе резки. Как минимизировать отходы материала с помощью резки лазером CO2, это не только связано с контролем затрат, но и напрямую влияет на эффективность производства и экологическую устойчивость. В этой статье будет рассмотрено, как сократить отходы материала путем оптимизации процессов и технологий лазерной резки.
Оглавление
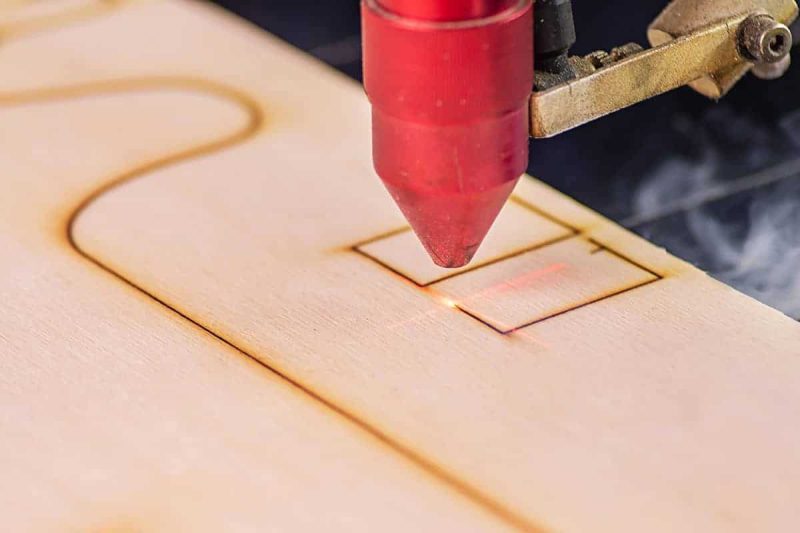
Точный контроль параметров резки
Преимуществом лазерной резки CO2 является ее превосходная точность, которая позволяет минимизировать отходы материала за счет точного управления несколькими параметрами резки. К основным параметрам относятся мощность лазера, скорость резки и расход газа. Оптимизация этих параметров может улучшить результаты резки и повысить эффективность производства, одновременно сокращая отходы.
Регулировка мощности лазера
Мощность лазера напрямую определяет подвод тепла в процессе резки. Избыточная мощность приведет к чрезмерной абляции материала и неровным краям, что приведет к ненужным отходам. Разумная регулировка мощности лазера в соответствии с типом и толщиной различных материалов может гарантировать, что лазерный луч точно концентрирует энергию на зоне резки, снижает тепловое воздействие на окружающую область и позволяет избежать чрезмерных потерь материала. Соответствующие настройки мощности также могут уменьшить плавление и подгорание в процессе резки и улучшить качество поверхности реза.
Оптимизация скорости резки
Регулировка скорости резки имеет решающее значение для сокращения отходов материала. Слишком низкая скорость увеличит поступление тепла, что приведет к перегреву поверхности реза, что может привести к ожогам кромок или чрезмерному плавлению, потере материала и снижению качества резки. Слишком высокая скорость резки может привести к неполным или неровным разрезам, что приведет к неразрезанным остаткам материала. Поэтому оптимизация скорости резки для обеспечения ее адаптации к характеристикам и толщине различных материалов может эффективно сократить ненужные отходы и улучшить качество резки.
Регулирование расхода газа
Поток газа играет важную роль в процессе резки лазером CO2, поскольку он помогает охлаждать зону резки и удалять расплавленный металл. Слишком большой поток газа может привести к неровной поверхности резки или разбрызгиванию шлака, нестабильному потоку воздуха и увеличению отходов; в то время как слишком малый поток газа может привести к неудовлетворительному эффекту резки, неспособному эффективно выдувать расплавленный металл или избегать окисления. Таким образом, путем точной регулировки потока газа можно гарантировать стабильность резки и высококачественный эффект резки, сокращая ненужные отходы материала.
Благодаря точному контролю этих параметров резки можно не только улучшить качество резки, но и эффективно оптимизировать эффективность использования материала, сократить отходы и повысить эффективность производства.
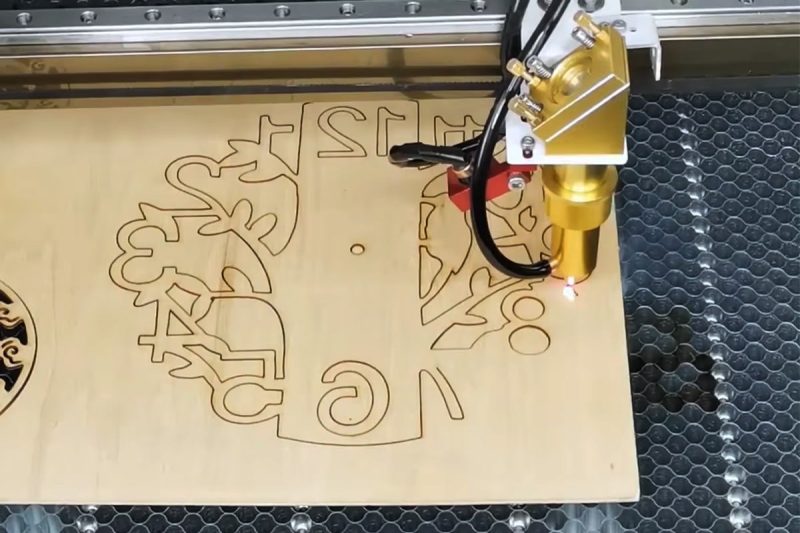
Оптимизация макета материала
Важность размещения материалов при лазерной резке CO2 очевидна. Разумное размещение может не только повысить эффективность использования материалов, но и сократить отходы, а также повысить точность резки и эффективность производства. Оптимизируя проектирование компоновки, можно минимизировать неиспользуемые зазоры, сэкономить материалы и сократить расходы. В практических приложениях оптимизация размещения материалов включает в себя множество аспектов, включая компоновку деталей, проектирование траектории резки и последовательность резки.
Эффективный дизайн типографики
Эффективный дизайн макета является ключом к максимальному использованию материала. Использование профессионального программного обеспечения для макетирования может помочь дизайнерам точно организовать макет деталей. С помощью функции автоматического макетирования дизайнеры могут рассчитать наилучшее расположение деталей за короткое время, чтобы гарантировать, что отходы будут максимально сведены к минимуму. При макетировании очень важно спланировать траекторию резки и минимизировать зазор между деталями (т. е. отходы). Разумная настройка зазора может не только сократить отходы материала, но и сократить последующее время и стоимость постобработки.
При проектировании макета необходимо также учитывать технические характеристики и толщину материалов. Для материалов разных размеров требуются разные стратегии макета. Например, для крупногабаритных материалов разумное расположение траектории и направления резки может не только сократить отходы, но и избежать деформации материала или некачественной резки; в то время как для мелкогабаритных материалов макет должен максимально использовать площадь резки каждого куска материала, чтобы избежать отходов.
В то же время программное обеспечение может также моделировать процесс резки и рассчитывать наилучшую последовательность резки, чтобы гарантировать, что каждая часть будет вырезана в правильном месте, сокращая ненужные зазоры и отходы и повышая эффективность производства. Например, во время процесса резки, избегая слишком большого количества пустых областей, можно гарантировать, что каждый кусок материала будет полностью использован.
Избегайте лишней резки
Избыточная резка относится к многократной резке или ненужной повторной резке из-за необоснованного дизайна или неправильного планирования траектории резки. Избыточная резка не только приводит к потере материалов, но и увеличивает время производства и снижает эффективность работы. В процессе лазерной резки крайне важно избегать повторной резки или бессмысленных траекторий, насколько это возможно, чтобы улучшить использование материала.
Разумное планирование траекторий резки может гарантировать, что каждая деталь может достичь ожидаемого эффекта при первой резке, не создавая дополнительных отходов из-за последующей корректировки траектории или дополнительной резки. Особенно в массовом производстве, предотвращение избыточной резки особенно важно для повышения эффективности производства и экономии материалов. Например, использование программного обеспечения для оптимизации для определения последовательности резки и обеспечения того, чтобы траектория резки каждой детали была как можно короче и не пересекалась, может значительно снизить возникновение избыточной резки.
В то же время, избегая слишком большого количества пауз в резке, перемещений или повторной работы в процессе резки, можно сократить ненужное потребление энергии и потери времени, а также повысить общую эффективность производства. Рациональное планирование последовательности и пути резки может гарантировать, что каждое действие резки необходимо, тем самым эффективно избегая избыточной резки и отходов материала.
Интеллектуальный набор текста и совместная работа над процессами
С непрерывным развитием технологий лазерной резки все больше и больше интеллектуального программного обеспечения для компоновки может работать с производственной линией, чтобы корректировать дизайн компоновки в реальном времени для удовлетворения различных требований к материалам. Благодаря анализу данных и машинному обучению интеллектуальная компоновка может оптимизировать траекторию резки и компоновку на основе исторических данных и обратной связи в реальном времени, не только учитывая размер и форму материала, но и внося оптимальные корректировки на основе требований процесса. Этот интеллектуальный метод компоновки значительно улучшает использование материалов и снижает необходимость ручного вмешательства.
Например, интеллектуальная система может автоматически регулировать траекторию и последовательность резки во время производственного процесса, динамически регулировать в соответствии с характеристиками различных материалов и ритмом производства, а также оптимизировать макет и траекторию резки в реальном времени для минимизации отходов. Эта технология может сделать производственный процесс более эффективным и интеллектуальным, значительно сократить отходы материала и повысить точность резки.
Оптимизация размещения материалов является ключевым фактором в улучшении использования материалов и сокращении отходов при резке лазером CO2. Благодаря эффективному проектированию размещения, избеганию избыточной резки и интеллектуальной технологии размещения ненужные отходы могут быть эффективно сокращены, эффективность производства может быть повышена, а затраты могут быть снижены. Разумное размещение может не только оптимизировать использование материалов, но и улучшить качество резки, гарантируя, что каждый процесс резки будет эффективным и точным. В современном производстве оптимизация размещения материалов стала важной стратегией для повышения эффективности производства и сокращения отходов.
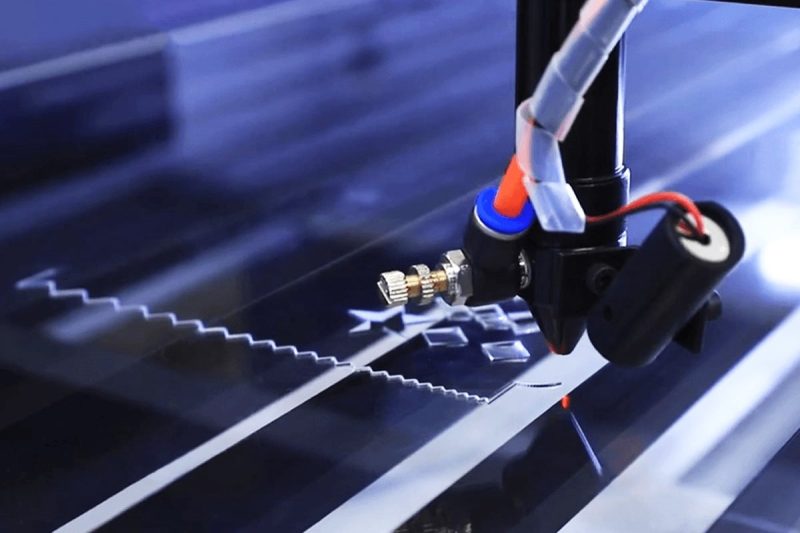
Используйте высококачественный станок лазерной резки
Производительность и технология оборудования напрямую влияют на точность резки и отходы материала. Для достижения цели высокой эффективности и низкого уровня отходов в процессе резки лазером CO2 очень важно выбрать высококачественный станок для лазерной резки. Высококачественные станки для лазерной резки не только оснащены передовой технологией управления лучом и точными системами регулировки фокуса, но также имеют стабильную производительность и эффективные возможности резки, которые могут обеспечить точность резки при минимизации отходов материала.
Точное управление лучом
Современные высококлассные станки для лазерной резки CO2 оснащены сложной технологией управления лучом, которая гарантирует, что лазерный луч всегда сфокусирован на области резки материала. Эта технология включает в себя высокоточную регулировку лазерного луча и систему управления фокусом, которая может точно фокусировать энергию лазера на поверхности материала, что приводит к уменьшению зоны термического воздействия и более чистым краям реза. Уменьшение зоны термического воздействия и обжига не только помогает улучшить качество резки, но и снижает ненужные отходы материала.
Точное управление лучом является основой для обеспечения высококачественной резки. Когда положение фокуса лазера точное, энергия лазерного луча может быть сконцентрирована и передана материалу, избегая чрезмерного рассеивания энергии в окружающую область, тем самым уменьшая потери тепла и ненужные потери материала. Кроме того, точное управление лучом также может сохранять поверхность реза плоской и бездефектной при резке сложных форм и мелких деталей, тем самым избегая отходов материала.
Автоматическая система регулировки
Современные станки для лазерной резки CO2 оснащены автоматической системой регулировки, которая может автоматически регулировать мощность лазера, расход газа, скорость резки и другие параметры на основе данных обратной связи в реальном времени, чтобы гарантировать, что каждый путь резки находится в наилучшем состоянии. Эта функция автоматической регулировки играет важную роль в процессе резки и может оптимизировать параметры резки в реальном времени для различных материалов и условий резки, чтобы избежать нестабильности, вызванной неправильным управлением человека или изменениями окружающей среды.
Например, автоматическая регулировка мощности лазера и расхода газа может динамически оптимизироваться в зависимости от толщины и типа материала, обеспечивая умеренный подвод тепла в процессе резки и уменьшая абляцию и деформацию материала, вызванные чрезмерным подводом тепла. В то же время автоматическая регулировка скорости резки может регулироваться в зависимости от характеристик материала и сложности резки, тем самым обеспечивая непрерывность и качество траектории резки. Благодаря этому эффективному мониторингу и регулировке в реальном времени, станок для лазерной резки позволяет не только повысить эффективность производства, но и значительно сократить ненужные отходы.
Кроме того, система автоматической регулировки может также вносить исправления на основе данных обратной связи в реальном времени во время процесса резки, исправляя любые ошибки, вызванные изменениями положения заготовки, свойств материала или точности оборудования, тем самым поддерживая стабильное качество резки и минимальные отходы материала. Эта функция регулировки в реальном времени значительно сокращает отходы, вызванные человеческими ошибками или технологическими задержками, гарантируя, что каждый разрез будет выполнен в наилучшем состоянии.
Технология многоосевой резки
Многие высококлассные станки для лазерной резки CO2 также оснащены технологией многоосевой резки, которая позволяет достигать более сложных и точных траекторий резки. Многоосевая технология позволяет резать в нескольких направлениях одновременно, что не только повышает эффективность резки, но и сокращает отходы материала. Например, некоторые станки для резки могут регулировать положение лазерной головки для более точной настройки угла и траектории резки, так что каждая траектория резки минимизирует зазоры и сокращает образование бесполезных отходов.
Многоосевая технология позволяет лазерным режущим машинам выполнять более гибкое планирование траектории во время процесса резки, особенно при резке сложных деталей, что может эффективно избегать чрезмерных отходов из-за неправильного планирования траектории. Кроме того, многоосевая технология резки может также сократить возникновение повторной резки и избыточных траекторий, тем самым дополнительно сокращая отходы материала и производственные затраты.
Длина волны лазера и технология фокусировки
Различные станки для лазерной резки CO2 могут использовать лазерные лучи с разной длиной волны, и выбор длины волны лазера оказывает важное влияние на точность и эффективность резки. Генераторы лазеров CO2 обычно используют лазеры с длиной волны 10,6 мкм, которые имеют очень высокую скорость поглощения при резке металлов и некоторых неметаллических материалов, поэтому они могут эффективно улучшить эффект резки. Высококачественные станки для лазерной резки CO2 оснащены передовыми оптическими системами, которые гарантируют, что лазерный луч может быть сфокусирован на поверхности материала и достигать высокоточной резки.
Благодаря точному управлению длиной волны лазера и фокусировкой луча, станки для лазерной резки CO2 могут достигать эффективных и высококачественных результатов резки при резке различных материалов. Более высокое качество луча означает лучшую концентрацию лазерной энергии, тем самым уменьшая рассеивание энергии и отходы, гарантируя более эффективное использование материалов.
Выбираем высококачественный Станок для лазерной резки CO2 является ключом к достижению эффективной резки и сокращению отходов материала. Комплексное применение прецизионного управления лучом, автоматической системы регулировки, технологии многоосевой резки, длины волны лазера и технологии фокусировки может не только повысить точность резки, но и значительно уменьшить зону термического воздействия, а также уменьшить абляцию и отходы материала. Благодаря постоянному развитию технологии лазерной резки современные лазерные режущие станки смогли достичь эффективной и точной резки, тем самым значительно улучшив использование материала и снизив производственные затраты, при этом гарантируя качество резки.
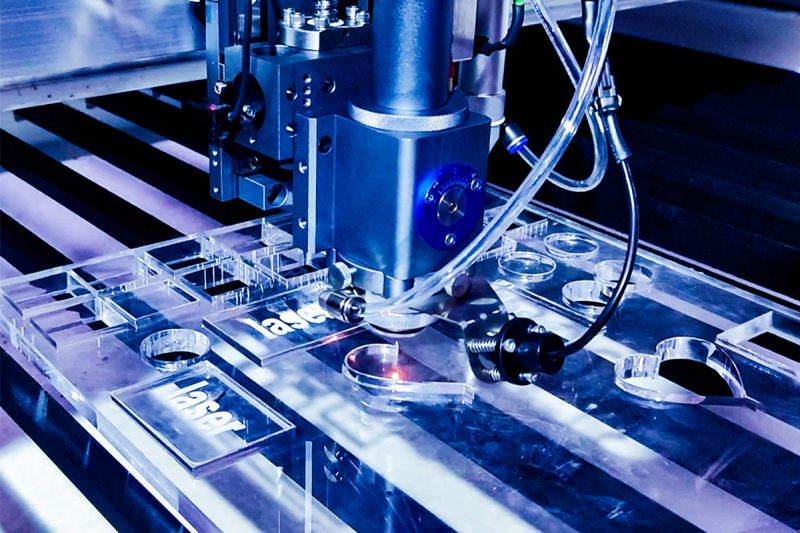
Разумный выбор режущих материалов
Выбор правильного режущего материала имеет решающее значение для сокращения отходов материала при лазерной резке CO2. Станки для лазерной резки CO2 в основном используются для резки неметаллических материалов, особенно некоторых термопластиков, дерева, бумаги и тканей. Поглощающая способность, теплопроводность, отражательная способность и другие характеристики различных материалов при лазерной резке оказывают непосредственное влияние на эффект резки и отходы материала. Поэтому выбор правильного режущего материала является важным шагом для повышения эффективности и сокращения отходов.
Выбор применимого материала
Преимущество станка для лазерной резки CO2 заключается в его высокой эффективности при резке неметаллических материалов. При выборе материалов для резки решающее значение имеют поглощающая и отражающая способность материала. Для станков для лазерной резки CO2 выбор материалов с высоким поглощением длины волны лазера CO2 может помочь повысить эффективность резки и сократить отходы.
- Бумага и картон: Бумага и картон имеют высокую скорость поглощения CO2-лазеров, что позволяет поддерживать высокую эффективность и сокращать отходы при резке. Эти материалы часто используются в упаковочной, рекламной и дизайнерской областях.
- Пластики (такие как акрил, ПВХ): CO2-лазеры хорошо режущие термопластики (такие как акрил, ПВХ и т. д.) и позволяют точно контролировать кромку реза, избегая ненужных зон термического воздействия и отходов материала.
- Древесина и композитные материалы: станки для лазерной резки CO2 также широко используются для резки древесины и композитных материалов. Эти материалы хорошо поглощают лазеры CO2, что позволяет добиться чистой резки, уменьшить подгорание и тепловые повреждения, а также обеспечить максимальное использование материала.
Выберите правильную толщину материала
Помимо типа материала, на эффект резки CO2-лазером влияет и толщина материала. Для более тонких материалов слишком высокая мощность лазера может привести к чрезмерному подводу тепла, что приведет к образованию избыточных зон термического воздействия, что приведет к чрезмерной абляции и отходам материала. И наоборот, для более толстых материалов слишком низкая мощность лазера может привести к неполной резке.
- Тонкие материалы: При резке тонких материалов избегайте чрезмерной мощности лазера или низкой скорости резки. Установите мощность и скорость соответствующим образом, чтобы избежать чрезмерного сжигания и отходов.
- Более толстые материалы: для толстых материалов требуется более высокая мощность лазера, чтобы обеспечить полную резку, но при этом следует избегать чрезмерной мощности, которая приводит к потере тепла или неровным краям.
Связь между теплопроводностью и лазерной резкой
Теплопроводность различных материалов также оказывает существенное влияние на эффективность лазерной резки. Материалы с высокой теплопроводностью (например, металлы) быстро отводят тепло от зоны резки, что может привести к неполной резке или избыточным зонам термического воздействия, увеличивая отходы материала. Напротив, материалы с низкой теплопроводностью (например, дерево и пластик) помогают концентрировать тепло, тем самым улучшая результаты резки и сокращая отходы.
При резке CO2-лазером обычные неметаллические материалы, такие как пластик и дерево, обладают низкой теплопроводностью, что позволяет эффективно использовать энергию лазера и уменьшить зону термического воздействия в процессе резки.
Влияние обработки поверхности материала на эффективность резания
Обработка поверхности материалов также имеет решающее значение при резке лазером CO2. Для неметаллических материалов поверхностная грязь, жир, оксидный слой и т. д. снижают эффективность поглощения лазера, что приводит к потере энергии. Поэтому перед лазерной резкой необходимо убедиться, что поверхность материала чистая и не загрязнена, что может эффективно повысить эффективность резки и сократить отходы.
Например, чистые пластиковые или деревянные поверхности поглощают лазерную энергию более эффективно, что приводит к более эффективной резке и меньшему количеству отходов. Если поверхность материала содержит масло или примеси, скорость поглощения лазерной энергии будет снижена, эффект резки будет плохим, и будут образовываться отходы.
Для станков для лазерной резки CO2 очень важно выбрать правильный неметаллический материал и толщину материала. В процессе резки скорость поглощения материала, теплопроводность и состояние обработки поверхности будут напрямую влиять на эффективность использования лазерной энергии, тем самым влияя на отходы материала. Разумный выбор подходящих материалов и настройка параметров резки могут не только повысить эффективность резки, но и минимизировать отходы материала и снизить производственные затраты. Оптимизируя выбор материала и настройки резки, компании могут добиться более высокого использования материала, обеспечивая при этом качество резки.
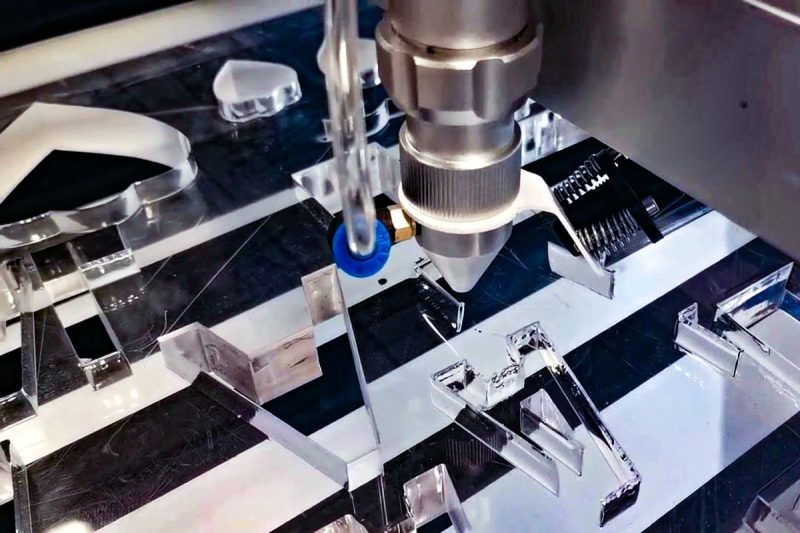
Поддержание и оптимизация производительности оборудования
Поддержание хорошей производительности лазерной режущей машины является ключевым фактором в обеспечении точности резки, повышении эффективности производства и сокращении отходов материала. Регулярное техническое обслуживание оборудования может не только продлить срок службы лазерной режущей машины, но и обеспечить стабильность оборудования в процессе резки, тем самым эффективно сокращая отходы, вызванные отказом оборудования или ухудшением производительности. Для того чтобы максимизировать производительность оборудования, лазерная режущая машина требует ряда регулярных проверок, обслуживания и оптимизации. Вот некоторые основные этапы и предложения по обслуживанию:
Регулярно проверяйте оптику
Оптические компоненты, такие как лазерные головки, отражатели и линзы, напрямую влияют на качество фокусировки лазерного луча и точность резки. Со временем эти оптические компоненты могут быть повреждены или деградированы из-за пыли, загрязнений или высоких температур, что повлияет на качество лазерной резки. Для обеспечения наилучшей производительности лазерного режущего станка необходимо регулярно проверять и чистить оптические компоненты. Конкретные операции следующие:
- Чистка оптических компонентов: Используйте чистую ткань и профессиональную чистящую жидкость для регулярной очистки линз и объектива. Избегайте использования грубых материалов, чтобы не поцарапать поверхность оптических компонентов. Поддержание чистоты линз и объектива может обеспечить качество фокусировки лазерного луча и снизить потери энергии.
- Проверьте оптическое выравнивание: выравнивание лазерной головки, отражателя и линзы напрямую влияет на траекторию и фокусное положение лазерного луча. Регулярная проверка выравнивания оптических компонентов для обеспечения точной фокусировки лазерного луча на зоне резки поможет улучшить качество резки и сократить отходы.
Техническое обслуживание и очистка лазерной головки
Лазерная головка является одним из основных компонентов лазерной режущей машины, отвечающим за фокусировку лазерного луча на материале. Со временем лазерная головка может загрязняться или изнашиваться, что приводит к неточной фокусировке лазера и влияет на эффект резки. Поэтому регулярная очистка и техническое обслуживание лазерной головки имеют важное значение. При очистке избегайте царапин или повреждений поверхности лазерной головки, чтобы избежать вторичного повреждения. При очистке обращайте особое внимание на следующие моменты:
- Проверьте оптические компоненты лазерной головки: Линзы и зеркала внутри лазерной головки необходимо регулярно проверять, чтобы убедиться в отсутствии пятен, царапин или других дефектов. Если они повреждены или загрязнены, их следует немедленно заменить.
- Проверьте систему охлаждения: Лазерная головка обычно оснащена системой охлаждения, чтобы гарантировать стабильную работу лазерной головки при высоких температурах. Регулярно проверяйте систему охлаждения и отвода тепла, чтобы убедиться, что они работают правильно, чтобы избежать ухудшения производительности лазерной головки из-за перегрева.
Калибровка и оптимизация параметров лазерной резки
Производительность лазерного режущего станка зависит не только от качества оборудования, но и от его параметров резки. Со временем рабочее состояние и производительность резки оборудования могут меняться, поэтому лазерный режущий станок необходимо регулярно калибровать и оптимизировать. В зависимости от материала может потребоваться настройка таких параметров, как мощность лазера, скорость резки, расход газа и положение фокуса. Обеспечение того, чтобы настройки параметров лазерного режущего станка всегда были в наилучшем состоянии, может значительно сократить отходы материала в процессе резки.
- Регулярно калибруйте мощность лазера и скорость резки: В процессе лазерной резки мощность и скорость резки являются ключевыми факторами, влияющими на результаты резки и отходы материала. Регулярно калибруйте оборудование, чтобы гарантировать, что мощность лазера и скорость резки всегда находятся в оптимальном рабочем диапазоне, чтобы избежать чрезмерного подвода тепла или неполной резки.
- Оптимизируйте положение фокуса и качество луча: Положение фокуса лазера и качество луча напрямую определяют точность и эффективность резки. Калибруя положение фокуса, гарантируйте, что энергия лазерного луча будет сконцентрирована в зоне резки, эффективно повышайте точность резки и сокращайте отходы, вызванные неточной резкой.
Регулярно проверяйте поток газа и систему охлаждения
Расход вспомогательного газа имеет решающее значение для стабильности процесса лазерной резки. Слишком высокий или слишком низкий расход газа может повлиять на качество резки и увеличить отходы материала. Поэтому регулярный осмотр и оптимизация расхода газа являются необходимой мерой для поддержания эффективной работы лазерного режущего станка. Стабильность расхода газа напрямую влияет на эффект резки, качество режущей кромки и степень отходов материала.
Кроме того, нельзя игнорировать обслуживание системы охлаждения. Источник лазера и оптические компоненты лазерной режущей машины должны работать в соответствующем температурном диапазоне, чтобы избежать перегрева или недостаточного охлаждения, которые могут привести к повреждению оборудования. Обеспечение нормальной работы системы охлаждения может не только продлить срок службы оборудования, но и повысить точность резки и сократить отходы, вызванные отказом оборудования.
Предотвращение отказов оборудования и своевременный ремонт
Отказ оборудования является одной из основных причин проблем в процессе лазерной резки. Чтобы избежать перерывов в производстве и отходов материала, вызванных отказом оборудования, необходимы регулярный осмотр оборудования и профилактика неисправностей. Регулярные проверки механических частей, электрических систем, лазерных источников и т. д. для обеспечения их хорошего рабочего состояния могут эффективно предотвратить отказ оборудования. Кроме того, при обнаружении проблем следует незамедлительно выполнять ремонт и замену поврежденных частей, чтобы избежать низкой эффективности производства или отходов материала из-за отказа оборудования.
Регулярное техническое обслуживание и оптимизация оборудования не только помогают продлить срок службы лазерной режущей машины, но и гарантируют, что оборудование всегда находится в наилучшем рабочем состоянии, тем самым повышая точность резки, стабильность и использование материала. Проверяя и очищая оптические компоненты, калибруя параметры резки, оптимизируя поток газа и системы охлаждения и т. д., можно значительно сократить отходы, вызванные снижением производительности оборудования. Кроме того, своевременное техническое обслуживание и профилактика неисправностей также являются важными средствами обеспечения непрерывной и эффективной работы оборудования. Благодаря комплексному управлению и оптимизации производительности оборудования лазерная режущая машина может поддерживать эффективную работу в течение длительного времени, минимизировать отходы материала и повысить эффективность производства.
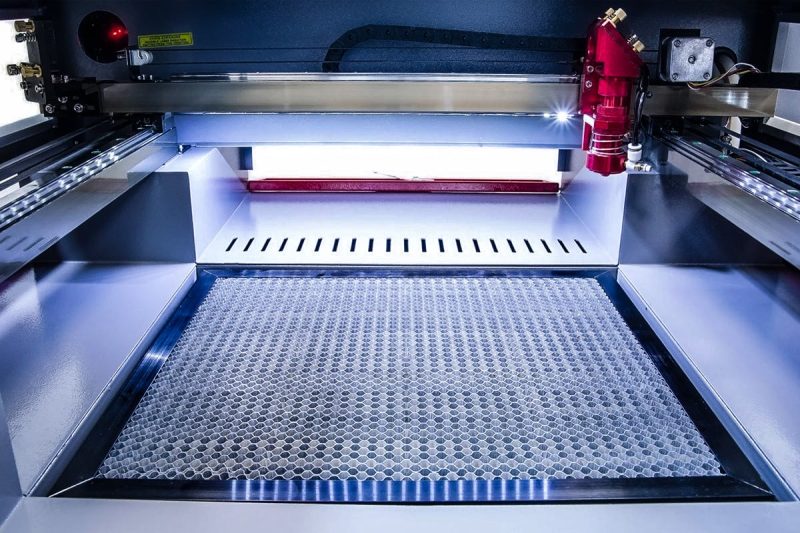
Подведем итог
Резка лазером CO2 является эффективной и точной технологией резки, но в практическом применении отходы материала по-прежнему являются важной проблемой. Точно контролируя параметры резки, оптимизируя размещение материалов и выбирая соответствующее оборудование и материалы, отходы материала могут быть минимизированы, эффективность производства может быть повышена, а затраты могут быть снижены. Благодаря постоянному развитию лазерных технологий и улучшению производительности оборудования, резка лазером CO2 в будущем станет более экологически чистой и экономичной и принесет больше возможностей для устойчивого развития в обрабатывающую промышленность.
В этом отношении, Актек Лазер Станок для лазерной резки CO2 с его превосходной технологией, точной системой управления и эффективными возможностями резки может предоставить клиентам более эффективные и экологически чистые решения для резки, помогая компаниям минимизировать отходы материалов и повысить эффективность производства и рентабельность. Если вам нужен станок для лазерной резки CO2, свяжитесь с нами немедленно для получения сметы.
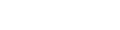
Контактная информация
- [email protected]
- [email protected]
- +86-19963414011
- Зона № 3 А, промышленная зона Лунчжэнь, город Юйчэн, провинция Шаньдун.
Получить лазерные решения