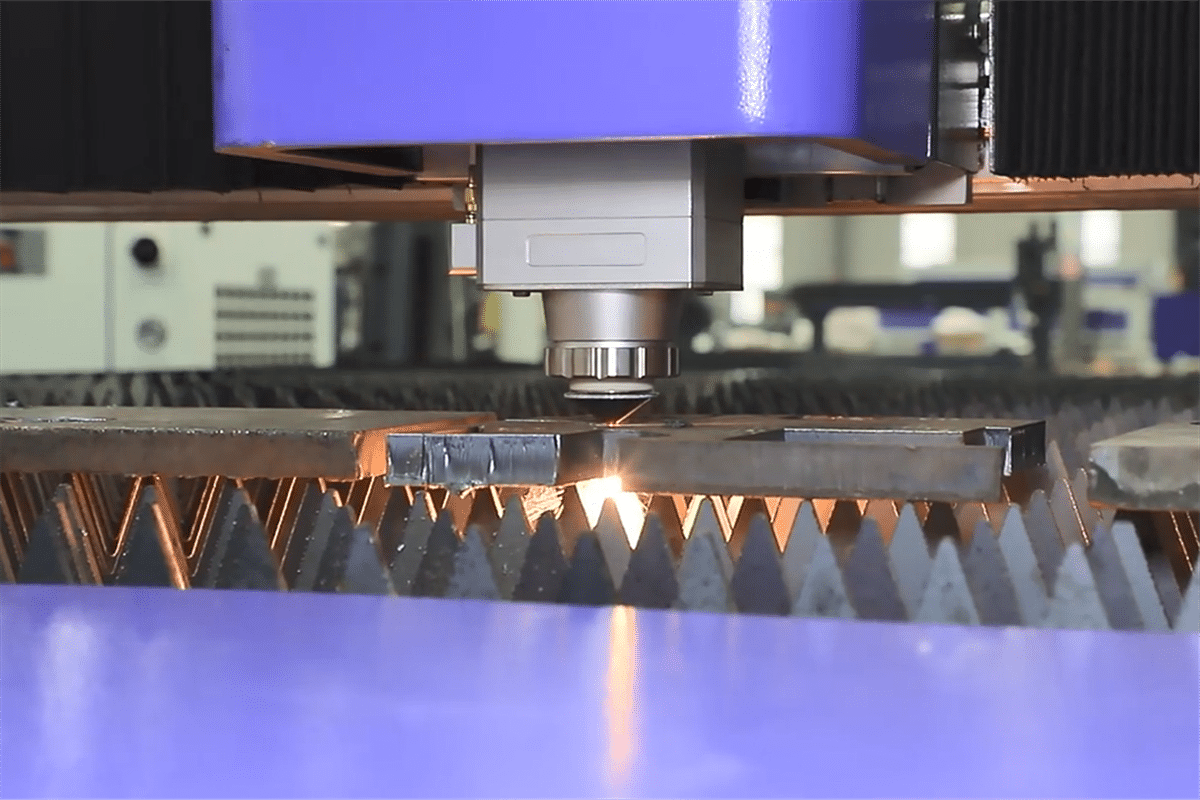
Как правильно выбрать вспомогательный газ для лазерной резки
Волоконно-лазерная резка это продвинутый ЧПУ металлорежущее оборудование, который может справиться с требованиями резки различных материалов и сложных форм и широко используется в металлообрабатывающей промышленности. В процессе лазерной резки для получения высококачественных заготовок, помимо лазерного генератора, способного обеспечить высокую энергию, важной частью настройки процесса резки является выбор подходящего вспомогательного газа.
В зависимости от материала и толщины режущей заготовки требования к использованию вспомогательного газа также различны. В этой статье подробно описана роль вспомогательного газа и четырех общих вспомогательных газов для резки. Продолжайте читать, чтобы узнать, как выбрать правильный вспомогательный газ для ваших нужд обработки, чтобы помочь вам завершить ваши проекты по металлу.
Оглавление
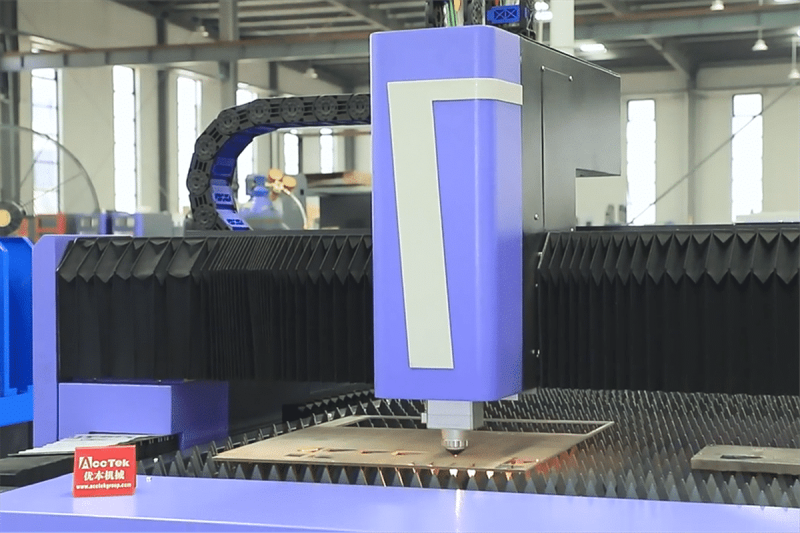
Какова роль вспомогательного газа в процессе лазерной резки?
Пользователи, использующие станок для лазерной резки впервые у них может возникнуть вопрос: почему станок для лазерной резки должен полагаться на вспомогательный газ для резки? Здесь представлено введение в роль вспомогательного газа при лазерной резке металлов. Прочитав это, вы поймете, что при резке очень необходимо использовать вспомогательный газ.
- Удаление материала и очистка зоны резки. Одна из основных функций вспомогательного газа — выдувать расплавленный или испаренный материал из зоны резки. Когда лазерный луч нагревает материал, он плавится или испаряется, образуя лужу расплавленного материала. Вспомогательный газ (обычно сжатый воздух, азот, кислород или газовая смесь) сдувает этот материал, не позволяя ему мешать процессу резки и гарантируя, что лазер может продолжать беспрепятственно прорезать материал.
- Охлаждение материала. Одной из основных функций вспомогательного газа (обычно азота или сжатого воздуха) является охлаждение разрезаемого материала. Лазерная резка генерирует сильный нагрев в точке резки, в результате чего материал плавится или испаряется. Вспомогательный газ быстро охлаждает окружающую среду, сдувая расплавленный или испаренный материал. Такое охлаждение предотвращает перегрев, деформацию или повреждение материала в процессе резки.
- Азотная защита. Азот часто используется в качестве вспомогательного газа при резке таких материалов, как нержавеющая сталь или алюминий. Он действует как защитный газ, предотвращая реакцию материала с кислородом, которая в противном случае могла бы привести к окислению и шероховатостям режущих кромок. Азот создает чистую кромку реза без оксидов.
- Способствует горению: в некоторых случаях лазерной резки кислород используется в качестве вспомогательного газа. Когда лазерный луч взаимодействует с кислородом, он воспламеняется и вступает в химическую реакцию с разрезаемым материалом. Этот процесс называется кислородной резкой горением. Однако поток кислорода необходимо контролировать, чтобы предотвратить чрезмерное окисление. Чрезмерное окисление может привести к неровным краям или нежелательным изменениям свойств материала.
- Улучшите качество резки. Выбор вспомогательного газа и его расхода повлияют на качество кромки реза. Выбирая правильный газ для материала и оптимизируя его скорость потока, операторы могут добиться более гладких кромок, минимальных заусенцев и точных разрезов.
- Защита оптических компонентов. Вспомогательный газ помогает защитить оптические компоненты, создавая барьер между ними и мусором, образующимся в процессе резки, помогая уменьшить накопление остатков и загрязнений на оптике лазерной режущей головки. Это защищает оптику от загрязнения или повреждения, обеспечивая фокусировку и точность лазерного луча.
- Стабилизирует процесс резки. Поток вспомогательного газа стабилизирует процесс резки, создавая контролируемую среду вокруг зоны резки. Это помогает поддерживать постоянные условия взаимодействия лазерного луча с материалом, обеспечивая равномерный и предсказуемый рез.
- Удаление дыма: лазерная резка производит дым, особенно при резке органических материалов. Вспомогательный газ помогает удалить эти выбросы из зоны резки, поддерживая чистую и безопасную рабочую среду.
Вспомогательный газ играет жизненно важную роль в процессе лазерной резки. Он имеет несколько важных функций, которые помогают повысить эффективность и качество лазерной резки. Выбор вспомогательного газа зависит от типа разрезаемого материала и конкретных требований операции резки и является важным параметром для оптимизации процесса лазерной резки для различных применений.
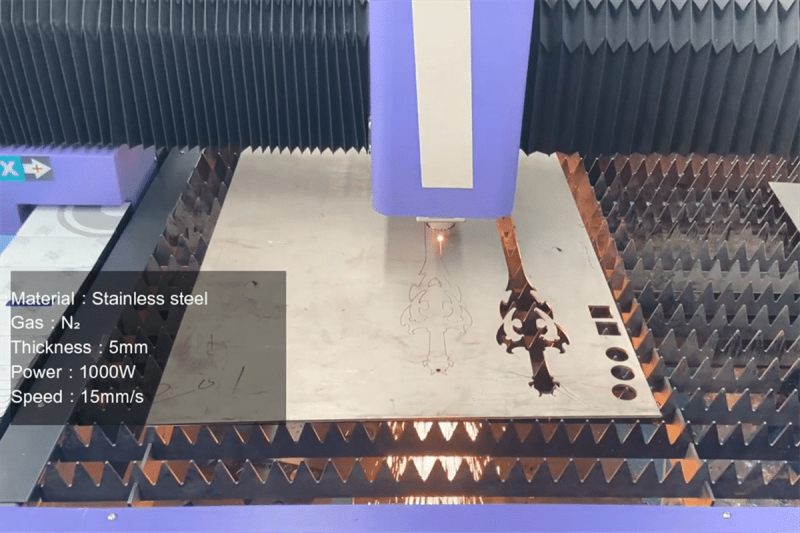
Какие вспомогательные газы являются наиболее распространенными?
Использование вспомогательного газа играет важную роль в работе станков лазерной резки. В настоящее время в процессах лазерной резки металлов обычно используются четыре вспомогательных газа. Их специфические характеристики заключаются в следующем:
Сжатый воздух
Воздух представляет собой смесь азота, кислорода и других газов. Сжатый воздух сжимается в резервуар для хранения воздуха с помощью воздушного компрессора, а затем извлекается после фильтрации, охлаждения и сушки. Метод его сбора относительно прост, и это самый дешевый вспомогательный газ. Следует отметить, что сжатый воздух не должен содержать воды, масла и пыли, чтобы избежать загрязнения оптических компонентов станка для лазерной резки и повреждения. Поэтому для обеспечения чистоты воздуха необходимы фильтры.
Кислород
Кислород был одним из первых вспомогательных газов, используемых при лазерной резке, из-за его реакционной способности при резке. Реакция между кислородом и металлом фактически производит дополнительную энергию в виде тепла, которая поддерживает процесс резки и способствует горению. В процессе резки кислород вступает в реакцию с теплом, что может значительно повысить эффективность резки. Образующаяся оксидная пленка увеличивает спектральный показатель поглощения луча отражающим материалом, что позволяет более эффективно использовать энергию лазера и ускоряет работу станка для лазерной резки.
Азот
Азот химически неактивен и с трудом окисляется вместе с обрабатываемой заготовкой. В большинстве случаев, за исключением некоторых специальных материалов, таких как титан, азот считается нереакционноспособным или инертным вспомогательным газом. Это означает, что азот не вступает в реакцию ни с какими компонентами металла в процессе резки. В большинстве случаев азот считается вспомогательным газом, который помогает добиться наилучшего качества кромки заготовки. При резке азотом требуется более высокая чистота.
Аргон
Аргон также является инертным газом с неактивными химическими свойствами и не легко окисляется обрабатываемой заготовкой. Его использование дороже, чем другие вспомогательные газы, и это самый редкий и дорогой газ, используемый большинством производителей металлов. Материалы, которые хорошо режутся азотом, также можно резать аргоном, что позволяет получить кромки такого же высокого качества. Основная причина использования более дорогого аргона заключается в том, что при резке чистым азотом часть металла все еще остается химически активной.
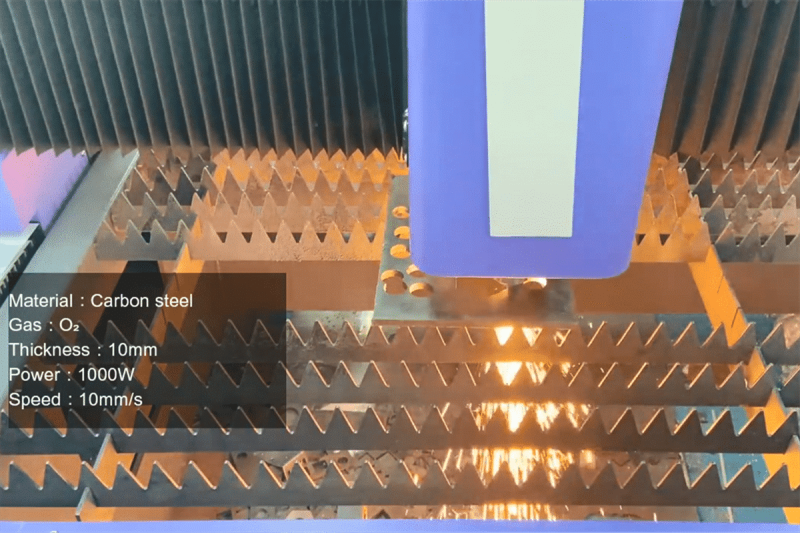
Какой вспомогательный газ необходим для лазерной резки металла?
Приступая к проекту лазерной резки, вам необходимо выбрать правильный вспомогательный газ для материала и толщины листового металла. Различные вспомогательные газы имеют свои функции и преимущества. Только правильно используя преимущества различных газов, мы можем добиться более высокого качества резки и более высокой скорости резки.
Применение сжатого воздуха при лазерной резке
Сжатый воздух в основном используется в тех случаях, когда металлические листы не требуют особого подхода к резке торцов. Он использует энергию лазера для плавления металлических заготовок и использует высокое давление воздуха для выдувания расплавленного материала. Когда для резки заготовки используется сжатый воздух, обрезанная торцевая поверхность заготовки становится желтой. Сжатый воздух в основном подходит для резки углеродистой стали, алюминия, алюминиевых сплавов, латуни, стальных пластин с гальваническим покрытием и других металлических материалов. Он широко используется в некоторых отраслях промышленности, таких как шасси из листового металла, шкафы и шкафы. При использовании сжатого воздуха для резки необходимо уделять внимание обслуживанию воздушного компрессора. Если воздух загрязнен, это приведет к повреждению лазерной режущей головки, линзы и генератора волоконного лазера, а также окажет большое влияние на качество резки заготовки.
Преимущество сжатого воздуха заключается в том, что его стоимость очень низкая и его можно подавать непосредственно с помощью воздушного компрессора, поэтому его очень удобно использовать по сравнению с другими газами. Однако сжатый воздух также имеет очевидные недостатки при резке металла. На режущей поверхности образуются заусенцы, и может потребоваться вторичная обработка. Кроме того, поскольку сжатый воздух содержит около 20% кислорода, разрезанная заготовка станет черной, что повлияет на качество продукции, а эффективность резки будет намного ниже, чем при кислородной резке.
Применение кислорода при лазерной резке
При резке кислородом материал нагревается лазерным лучом до определенной температуры, а затем горит и испаряется. Кислород является стандартным химически активным вспомогательным газом, используемым при лазерной резке углеродистой стали, и он может резать более толстую сталь, поскольку его реактивная природа увеличивает теплоту резки. При резке углеродистой стали кислород сжигает углерод в пропиле углеродистой стали, создавая дополнительное тепло, что позволяет менее мощным лазерным генераторам резать более толстые материалы.
Тем не менее, эта реактивность кислородной резки может также иметь некоторые негативные последствия. Если требуется хорошее качество кромки, обычно скорость резки материала и давление воздуха ограничиваются. Во время кислородной резки химическая реакция усиливается по мере увеличения давления газа и скорости потока. Это приводит к повышенному нагреву заготовки и, как следствие, к увеличению плавления кромок. Это не идеально подходит для применений, требующих высокого качества режущих кромок. Кроме того, кислородная резка металла часто также образует на кромках реза оксиды, из-за чего поверхность заготовки чернеет и может потребоваться очистка заготовки.
Применение азота при лазерной резке
Лазерная резка с использованием азота позволяет получить очень качественные кромки различных материалов с очень тонкими зонами термического воздействия. Азот обеспечивает наилучшее качество кромок по экономичной цене и высокую скорость резки большинства видов алюминия, мягкой стали, оцинкованной стали и автомобильной стали UHSS. При использовании азота в качестве вспомогательного газа для резки азот образует защитную атмосферу вокруг расплавленного металла, предотвращая окисление материала, предотвращая образование оксидных пленок и обеспечивая резку без окисления. Благодаря этой особенности азот обычно используется для деталей, которые необходимо хранить в течение определенного периода времени перед использованием, поскольку резка кислородом и воздухом может вызвать ржавчину на кромках разреза при длительном хранении. Кроме того, режущие детали без окисления имеют характеристики прямой сварки, высокую коррозионную стойкость и т. д., а торцевая поверхность разреза белая. Во время резки азотом изменения в потоке газа оказывают большое влияние на резку. При обеспечении давления режущего газа необходимо обеспечить достаточный поток газа.
Азот также имеет недостатки при использовании в качестве вспомогательного газа при резке металла. Поскольку азот не вступает в химическую реакцию с металлом, теплота реакции отсутствует, и режущая способность не так хороша, как при резке кислородом. Расход азота при азотной резке в несколько раз превышает расход кислорода, а стоимость резки выше, чем при кислородной резке. С точки зрения потребления, кислородная резка требует давления 2 бар и расхода примерно 10 м³/ч. Для резки азотом требуется давление 22/30 бар и расход примерно от 40 до 60/120 м³/ч. Кроме того, скорость резки азотным лазером примерно на 30% медленнее, чем скорость кислородной лазерной резки.
Применение аргона при лазерной резке
Аргон — это инертный газ, используемый для металлов, вступающих в химические реакции при резке азотом. Он может предотвратить окисление и азотирование во время лазерной резки. Газ аргон часто используется для обработки титана и титановых сплавов. При температурах, до которых нагревают металл лазерные резаки, титан вступает в химическую реакцию даже в атмосфере чистого азота, что является основной причиной выбора аргона вместо азота. Однако аргон очень дорог и не пригоден для длительного использования.
Подведем итог
Благодаря приведенному выше введению мы можем понять функции и преимущества каждого вспомогательного газа, а также их ограничения. Сжатый воздух можно использовать в тех случаях, когда нет жестких требований к цвету поверхности разреза. Его легко получить и он дешевле. Кислород можно использовать для толстых металлов, не требующих большого сечения резки, тем самым увеличивая скорость резки. Азот можно использовать в тех случаях, когда требуется высокое качество режущей поверхности. Заготовка имеет высокую точность и может быть непосредственно обработана на следующем этапе. Газ аргон в основном используется для титана и титановых сплавов.
Выбор подходящего вспомогательного газа в соответствии с характеристиками обрабатываемого металла может помочь пользователям сэкономить дополнительные эксплуатационные расходы, обеспечивая при этом качество резки. Если вы хотите узнать больше о лазерной резке, обратите внимание на Актек Лазер.
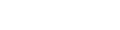
Контактная информация
- [email protected]
- [email protected]
- +86-19963414011
- Зона № 3 А, промышленная зона Лунчжэнь, город Юйчэн, провинция Шаньдун.
Получить лазерные решения