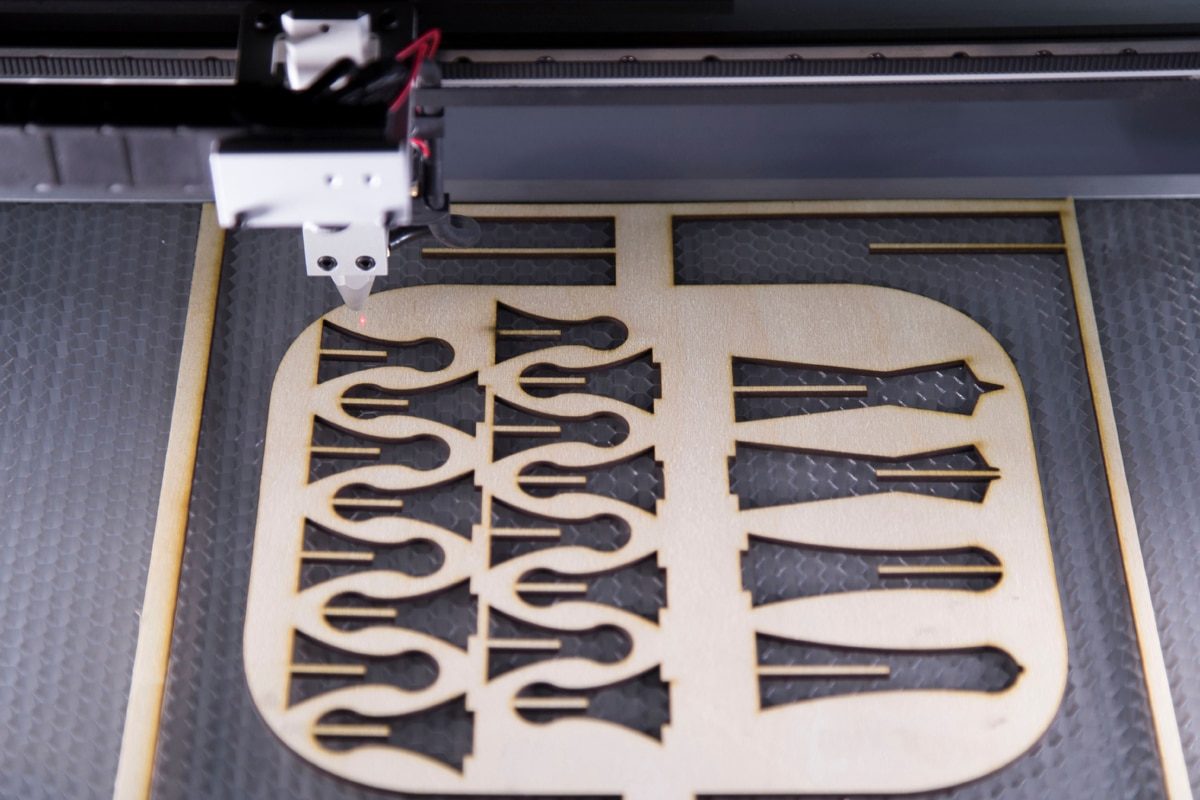
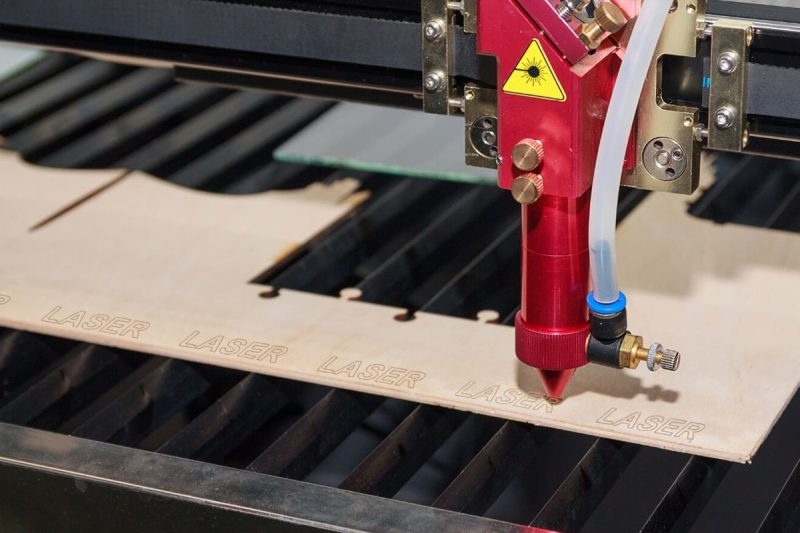
Основы резки лазером CO2
Принципы работы
Распространенные приложения
Резка лазером CO2 известна своей универсальностью и адаптивностью, что делает ее ценным инструментом в различных отраслях. Некоторые из ее основных применений включают:
- Автомобильная промышленность: CO2-лазеры используются для резки внутренних и внешних неметаллических компонентов, включая приборные панели, обивку и уплотнители. Точность и скорость CO2-лазеров также делают их идеальными для резки сложных форм в автомобильных пластиках и композитах.
- Аэрокосмическая промышленность и электроника: Высокая точность лазеров CO2 позволяет производителям создавать сложные компоненты для аэрокосмической и электронной продукции. Тонкие материалы, такие как полиимидные пленки, используемые в гибкой электронике, и композиты для аэрокосмической промышленности часто обрабатываются с помощью резки лазером CO2.
- Текстиль и одежда: Резка лазером CO2 приобрела популярность для резки тканей, кожи и других текстильных материалов. Бесконтактный характер лазерного луча позволяет создавать сложные узоры без осыпания или искажения, что является важным требованием в индустрии моды и одежды.
- Вывески и реклама: CO2-лазеры отлично подходят для резки таких материалов, как акрил, дерево и некоторые виды пластика, которые обычно используются в производстве вывесок. Они позволяют создавать детальные проекты, сложные формы и чистые края, создавая высококачественные и визуально привлекательные вывески.
- Упаковка: В сфере упаковки CO2-лазеры с высокой точностью режут картон, бумагу и тонкие пластиковые пленки, предлагая универсальное решение для дизайна упаковки, высечки и создания сложных форм.
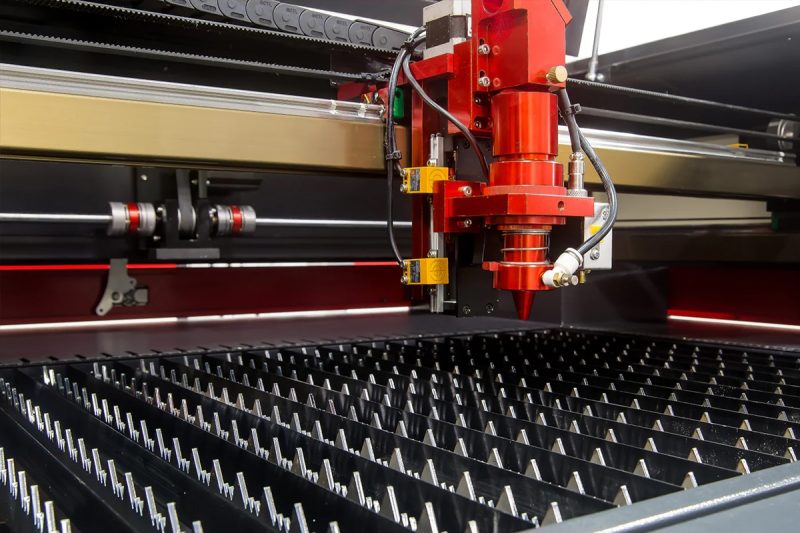
Ключевые факторы, влияющие на скорость резки
Скорость резки станков лазерной резки CO2 зависит от различных взаимосвязанных факторов. Оптимизация этих факторов имеет важное значение для достижения эффективной, точной и высококачественной резки.
Мощность лазера
Тип и толщина материала
Тип и давление вспомогательного газа
Вспомогательные газы играют важную роль в процессе резки, выталкивая расплавленный материал, охлаждая зону резки и иногда способствуя реакциям окисления, которые повышают скорость резки. Тип и давление вспомогательного газа влияют на то, насколько эффективно происходит процесс резки:
- Кислород (O2): Кислород обычно используется для резки материалов на основе углерода, поскольку он реагирует с материалом, выделяя дополнительное тепло (окисление), ускоряя процесс резки. Он особенно эффективен для толстых материалов, но может привести к окислению на кромках реза.
- Азот (N2): Азот часто используется для резки нержавеющей стали и алюминия, поскольку он предотвращает окисление и обеспечивает более чистые разрезы. Он не способствует нагреванию при резке, поэтому обычно приводит к более низкой скорости резки по сравнению с кислородом.
- Воздух: В некоторых приложениях сжатый воздух используется как экономичный вспомогательный газ. Хотя он может быть эффективен для тонких материалов и неметаллических материалов, он, как правило, не обеспечивает того же качества резки, что кислород или азот для металлов.
Качество луча
Положение фокуса
Настройки скорости резки
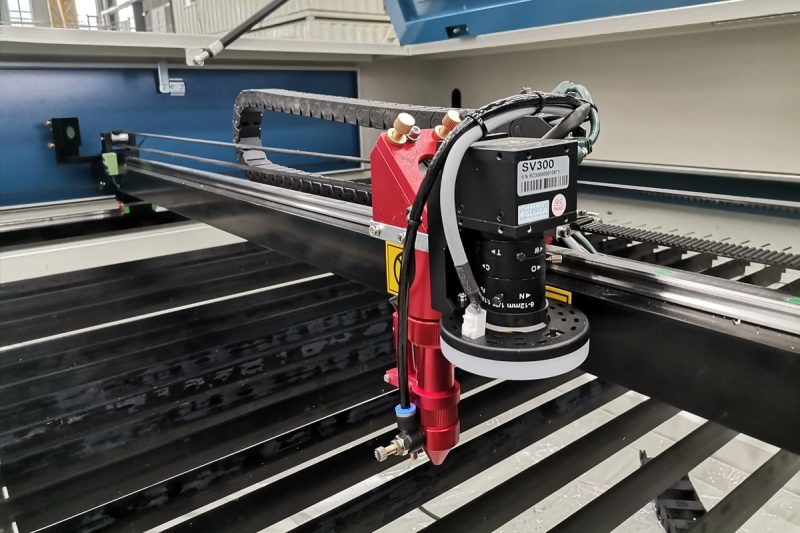
Ключевые факторы, влияющие на точность резки
Точность и стабильность машины
Фокусировка луча и размер пятна
Конструкция и состояние форсунки
Свойства материала
Условия окружающей среды
Навыки и опыт оператора
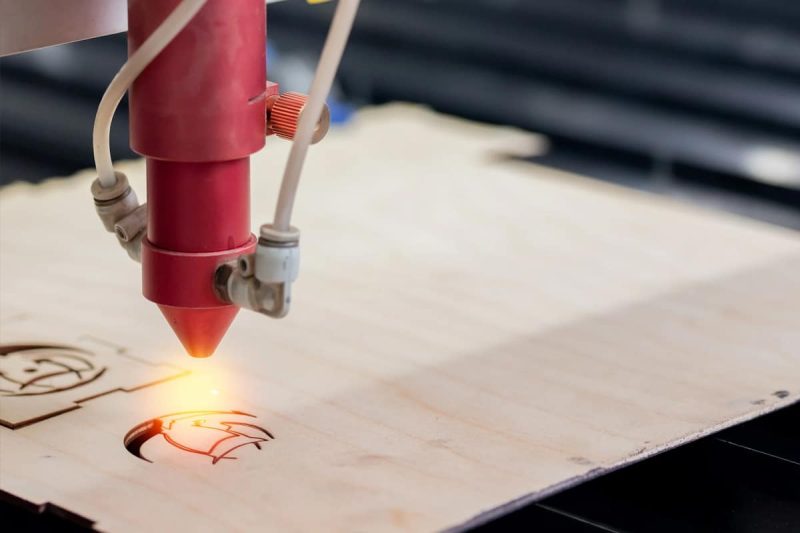
Стратегии оптимизации
Выбор параметров
Выбор правильных параметров — один из самых эффективных способов оптимизации скорости и точности резки CO2-лазером. Ключевые параметры включают мощность лазера, скорость резки, тип и давление вспомогательного газа, а также положение фокуса. Тонкая настройка этих параметров для каждого материала и толщины обеспечивает оптимальную производительность резки.
- Мощность лазера: Регулировка мощности лазера в зависимости от типа и толщины материала обеспечивает точную резку без чрезмерного нагрева или тепловой деформации. Более высокая мощность подходит для толстых материалов, но может потребовать более низкой скорости для поддержания точности.
- Скорость резки: Баланс скорости резки с мощностью лазера имеет решающее значение. Слишком высокие скорости могут ухудшить качество кромки, тогда как более низкие скорости могут повысить точность, но снизить производительность. Идеальная скорость зависит от свойств материала и желаемого качества резки.
- Вспомогательный газ: выбор подходящего вспомогательного газа (кислорода, азота или воздуха) и регулировка его давления оптимизируют съем материала, улучшают качество кромок и могут ускорить процесс резки.
- Положение фокуса: Правильное расположение фокуса гарантирует, что лазерный луч будет сконцентрирован в правильной точке на материале, максимизируя передачу энергии и точность. Регулировка фокуса в зависимости от толщины и типа материала имеет важное значение для достижения стабильных результатов.
Практика технического обслуживания
Регулярное техническое обслуживание имеет решающее значение для поддержания максимальной производительности станка для лазерной резки CO2. Хорошо обслуживаемый станок обеспечивает более точную резку, работает более эффективно и реже выходит из строя. Основные методы технического обслуживания включают:
- Чистка оптических компонентов: зеркала, линзы и другие оптические компоненты следует регулярно чистить, чтобы грязь и мусор не снижали качество и точность луча.
- Техническое обслуживание сопла: проверка и очистка сопла обеспечивают постоянный поток вспомогательного газа, что имеет решающее значение для точной и эффективной резки.
- Проверки выравнивания: периодические проверки и выравнивание оптических компонентов помогают поддерживать постоянную фокусировку луча и распределение энергии.
- Смазка: Регулярная смазка движущихся частей снижает износ и обеспечивает плавность движения, повышая скорость и точность.
- Калибровка: Регулярная калибровка системы движения лазерного резака и других компонентов помогает поддерживать точность и предотвращать механический дрейф.
Программное обеспечение и системы управления
Передовое программное обеспечение и системы управления играют решающую роль в оптимизации производительности резки лазером CO2. Правильное программное обеспечение может повысить скорость резки, улучшить точность и обеспечить сложную геометрию. Основные характеристики, на которые следует обратить внимание, включают:
- Оптимизация траектории: программное обеспечение, оптимизирующее траекторию резки, сводит к минимуму ненужные движения и сокращает время цикла, повышая производительность без ущерба для точности.
- Мониторинг в реальном времени: системы обратной связи и мониторинга в реальном времени позволяют операторам вносить коррективы на лету, обеспечивая стабильную производительность резки.
- Автоматизация: Интеграция функций автоматизации, таких как автоматическая загрузка/выгрузка или корректировка параметров процесса, снижает количество человеческих ошибок и повышает эффективность работы.
- Удобные интерфейсы: интуитивно понятные программные интерфейсы позволяют операторам легко устанавливать и регулировать параметры, контролировать производительность и устранять неполадки, повышая общую производительность и точность резки.
Обучение и развитие навыков
Навыки и опыт оператора машины могут существенно влиять на производительность станка для лазерной резки CO2. Инвестиции в обучение и развитие навыков оператора имеют важное значение для оптимизации скорости и точности. Эффективные стратегии включают:
- Программы обучения: комплексные программы обучения, охватывающие эксплуатацию машины, оптимизацию параметров и методы технического обслуживания, гарантируют операторам возможность принимать обоснованные решения для максимального повышения производительности резки.
- Практический опыт: поощрение операторов к получению практического опыта работы с различными материалами и сценариями резки позволяет им развивать практические навыки и быстро выявлять потенциальные проблемы.
- Непрерывное обучение: предоставление возможностей для постоянного обучения новейшим технологиям, функциям программного обеспечения и методам резки позволяет операторам быть в курсе последних событий и оптимизировать производительность машины.
- Навыки устранения неполадок: предоставление операторам навыков диагностики и устранения неполадок обеспечивает минимальное время простоя и стабильную производительность, повышая как скорость, так и точность.
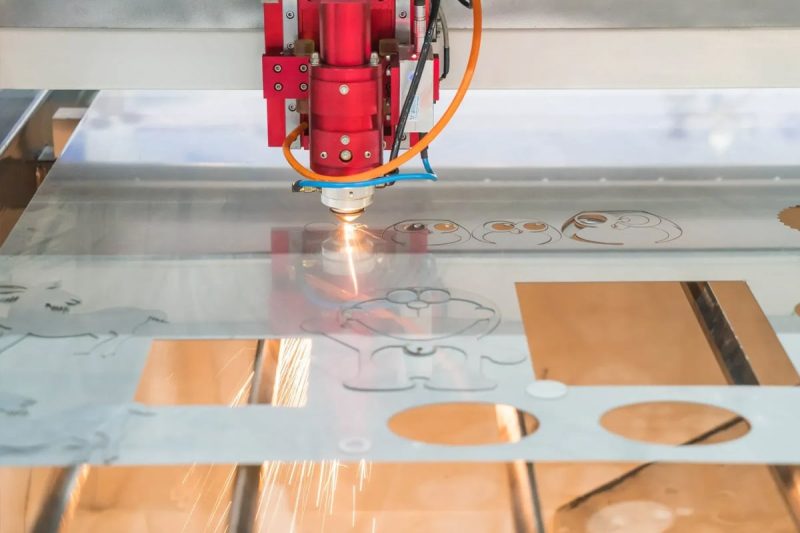
Краткое содержание
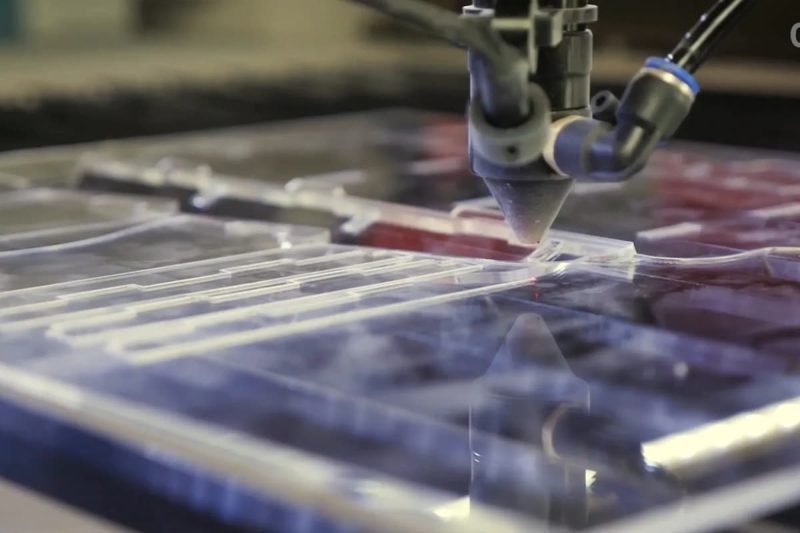
Получите решения для лазерной резки
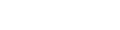
- [email protected]
- [email protected]
- +86-19963414011
- Зона № 3 А, промышленная зона Лунчжэнь, город Юйчэн, провинция Шаньдун.