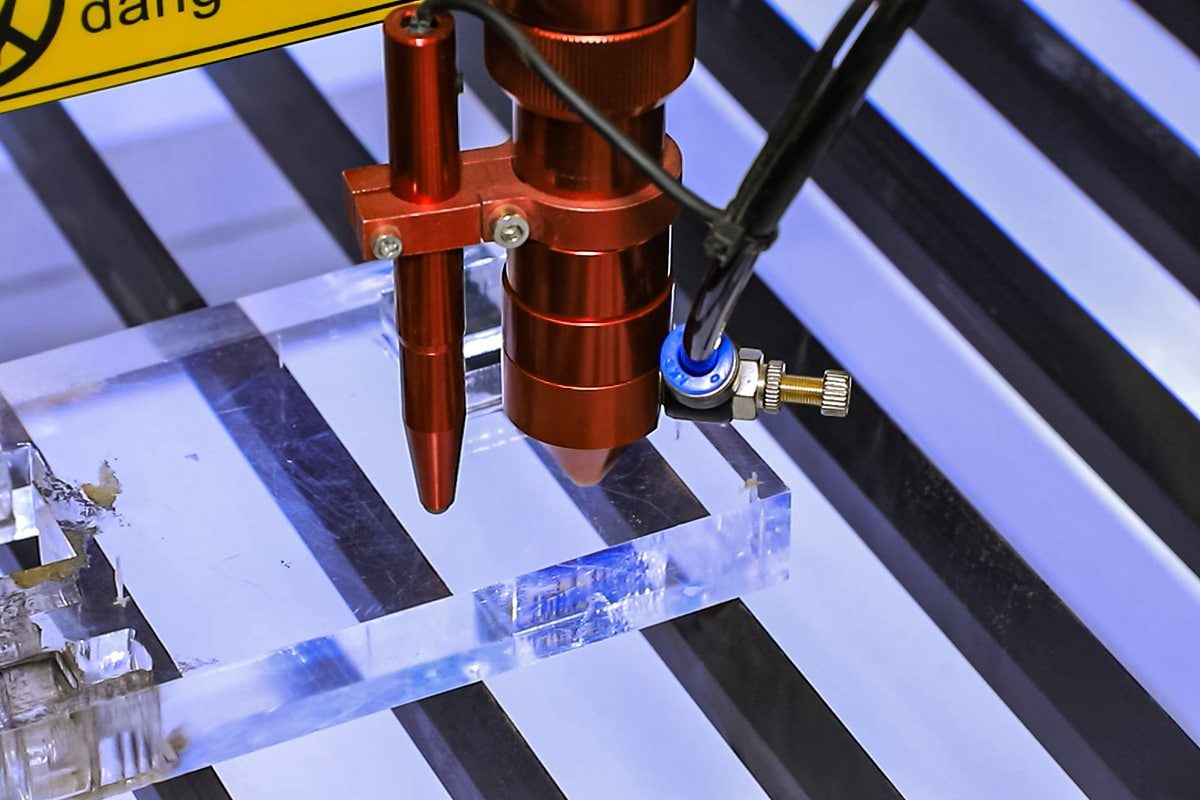
Можно ли с помощью лазерной резки CO2 добиться высокой точности сложных конструкций?
Резка лазером CO2 стала краеугольным камнем в современном производстве, революционизировав подход отраслей к обработке материалов. Используя силу концентрированного лазерного луча, эта технология способна точно резать широкий спектр материалов, включая металлы, пластики и композиты. Ее бесконтактная природа минимизирует деформацию материала, что делает ее идеальной для применений, требующих высокой точности и сложных деталей. Универсальность Станки для лазерной резки CO2 позволило использовать их в различных областях: от промышленного производства до креативного дизайна, продемонстрировав их адаптивность и эффективность.
Резка лазером CO2 демонстрирует непревзойденную точность в сложных конструкциях и может легко обрабатывать сложные узоры и детали, обеспечивая строгие допуски. Это не только улучшает качество готовой продукции и снижает потребность во вторичной обработке, но и значительно снижает затраты и повышает эффективность производства. Благодаря постоянным инновациям в отрасли резка лазером CO2 стала ключевой движущей силой точного машиностроения и передового производства.
Оглавление
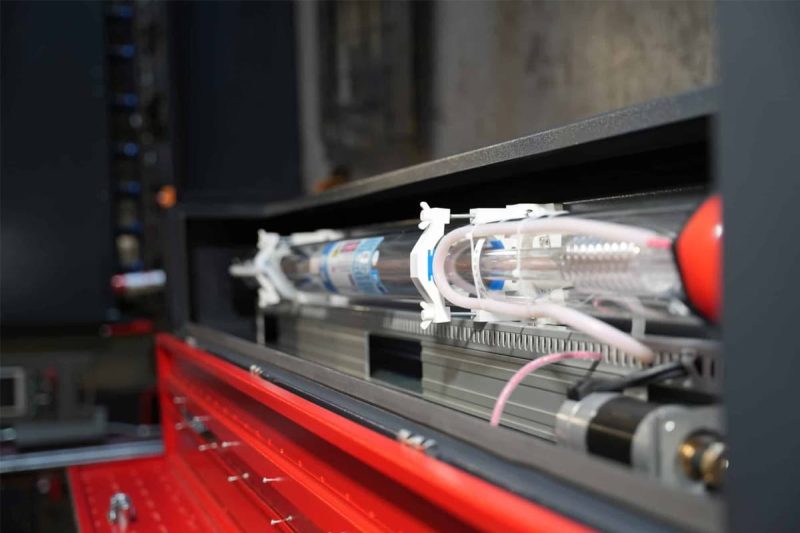
Понимание резки лазером CO2
Резка лазером CO2 стала ключевой технологией в современном производстве и проектировании благодаря своей высокой точности и сложным возможностям проектирования. Глубокое понимание ее принципов и функций может помочь компаниям максимально использовать ее потенциал и удовлетворять разнообразные потребности в применении.
Принципы резки лазером CO2
Резка лазером CO2 использует генератор лазера на углекислом газе для излучения высокоэнергетического инфракрасного луча для резки, гравировки или травления материалов с чрезвычайно высокой точностью. Его основные принципы включают: использование лазерной среды, смешанной с углекислым газом, азотом и гелием, для генерации лазерного луча; фокусировка луча на поверхности материала через линзы и линзы; использование автоматизированных систем, таких как ЧПУ, для точного направления лазерной головки для завершения сложных узоров; и использование вспомогательных газов, таких как кислород, азот или воздух, для повышения эффективности резки, предотвращения окисления и удаления шлака.
Обзор технологии резки и возможностей точности
Процесс резки лазерной системой CO2 обеспечивает точность и качество благодаря тщательно контролируемым этапам, включая генерацию лазерного луча, поглощение энергии материалом, вызывающее плавление или испарение, и вспомогательный газ для удаления расплавленного материала, оставляя чистый край. Его прецизионные возможности отражаются в высокой точности (допуск резки до ±0,1 мм), узком пропиле для сокращения отходов материала, автоматизированной системе для обеспечения повторяемости и широкой совместимости с различными материалами, такими как металл, акрил, дерево и т. д.
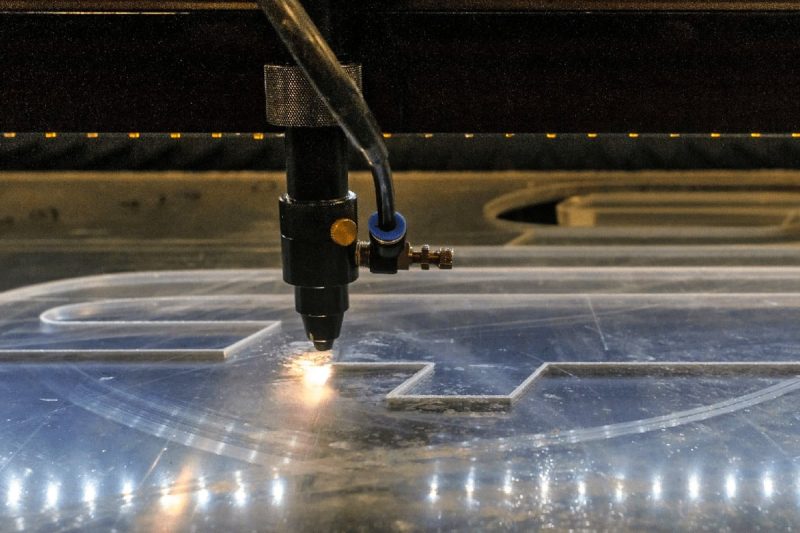
Ключевые факторы, влияющие на точность резки CO2-лазером
Достижение высокой точности при резке лазером CO2 зависит от нескольких критических факторов. Понимание и оптимизация этих элементов может повысить точность и эффективность резки.
Качество лазерного луча:Качество лазерного луча измеряется коэффициентом M2. Чем ближе значение M2 к 1, тем более концентрированным является лазерный луч и тем тоньше эффект резки. Высококачественный лазерный луч может обеспечить меньшее пятно, повысить точность резки и уменьшить зону термического воздействия, тем самым обеспечивая точность траектории резки.
Настройки фокуса: положение фокуса влияет на тонкость режущей кромки. Правильная настройка фокуса гарантирует, что лазерный луч образует подходящую точку на поверхности материала, обеспечивая точную глубину реза и высококачественные кромки.
Стабильность системы: Стабильность лазерной режущей машины определяет точность резки. Нестабильная мощность лазера или механическая вибрация вызовут колебания точности. Стабильный лазерный генератор и точная система движения могут обеспечить непрерывную высокоточную резку.
Достижимые допуски: резка лазером CO2 может достигать точности ±0,1 мм, что делает ее пригодной для областей, требующих высокой точности, таких как обработка прецизионных деталей и электронных изделий.
Качество кромок: Резка лазером CO2 обеспечивает гладкие кромки реза. Высококачественный лазерный луч и управление фокусировкой уменьшают заусенцы и зоны термического воздействия, улучшая качество резки и снижая необходимость во вторичных операциях.
Системы управления движением: Точность позиционирования и динамическая реакция режущего станка напрямую влияют на точность траектории резки, особенно при работе со сложными конструкциями.
Свойства и толщина материала: Плотность, теплопроводность и толщина материала влияют на эффективность поглощения энергии лазера, тем самым влияя на эффект и точность резки.
Скорость и мощность резки: Слишком высокая скорость резки или недостаточная мощность могут привести к неполной резке, в то время как чрезмерная мощность может привести к истиранию материала или повлиять на качество кромок.
Короче говоря, резка лазером CO2 обеспечивает высокоточную резку и высококачественные кромочные эффекты за счет точного управления лазерным лучом и стабильности системы и широко применяется в областях высокоточной обработки.
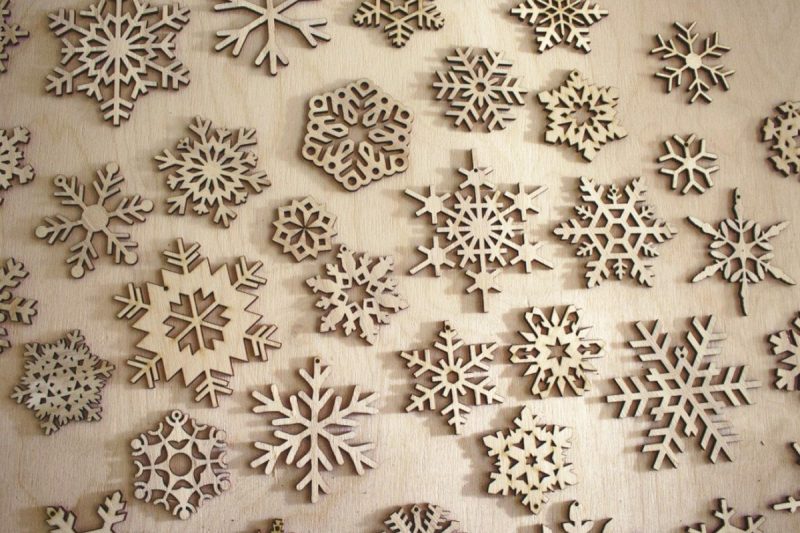
Сложность конструкции
В области лазерной резки сложные конструкции относятся к проектам, которые содержат мелкие детали и сложные узоры и требуют строгих допусков. Реализация этих конструкций предъявляет чрезвычайно высокие требования к точности, стабильности и возможностям обработки оборудования, а также ставит новые задачи перед технологией обработки.
Определение сложного дизайна в контексте лазерной резки
Сложные конструкции обычно относятся к конструкциям, требующим высокой точности и аккуратности в эксплуатации, в том числе:
- Мелкие детали, такие как микрогравюры или декоративные узоры, требуют от лазерного режущего станка стабильного и высокоточного позиционирования.
- Сложные узоры: траектория резки, включающая нестандартные формы или иерархические геометрические конструкции, требует многочисленных корректировок и эффективного планирования.
- Жесткие допуски: в производстве, требующем чрезвычайно высокой точности, отклонения резки должны контролироваться в диапазоне микрометров или 0,1 мм.
Эти конструкции предъявляют высокие требования к основным характеристикам оборудования для лазерной резки, таким как качество луча, управление движением и стабильность питания.
Проблемы сложных моделей
Обработка сложных узоров является серьезной проблемой в технологии лазерной резки, особенно при точном воспроизведении многослойных или асимметричных дизайнов. Следующие проблемы особенно заметны:
- Планирование сложной траектории: при резке сложных узоров система ЧПУ должна оптимизировать переменную траекторию резки, чтобы сократить потери времени и количество ошибок.
- Накопление термических эффектов: Длительная непрерывная резка сложных узоров может привести к локальному накоплению тепла, что может привести к короблению или деформации материала.
- Контроль согласованности: при выполнении повторяющихся задач по обработке необходимо гарантировать, что каждый готовый продукт остается согласованным в сложных конструкциях без каких-либо отклонений или дефектов.
Проблема мелких деталей
Обеспечение резки мелких деталей предъявляет повышенные требования к производительности лазерного режущего станка:
- Ограничение диаметра луча: для получения тонких линий реза диаметр пятна лазерного луча должен быть очень малым, обычно в микрометровом диапазоне.
- Стабильность мощности: Колебания мощности лазерного излучения напрямую влияют на четкость деталей и качество кромок, что может привести к неровной резке или появлению заусенцев.
- Высокие требования к динамическому отклику: управление движением лазерной головки должно быстро реагировать, чтобы гарантировать отсутствие смещения или перекрытия траектории при выполнении сложной резки в тонких областях.
Эти технические требования делают обработку мелких деталей при лазерной резке весьма сложной задачей.
Проблемы жестких допусков
Жесткие допуски являются обязательным требованием в высокотехнологичном производстве, особенно в таких отраслях, как медицина и аэрокосмическая промышленность. Чтобы соответствовать этим требованиям, лазерная резка сталкивается со следующими трудностями:
- Высокоточное позиционирование: станок для лазерной резки должен быть оснащен системой обратной связи по положению с высоким разрешением, чтобы обеспечить точность позиционирования режущей головки на микронном уровне.
- Компенсация тепловой деформации: Материал может расширяться или деформироваться из-за тепла в процессе резки. Лазерный режущий станок должен контролироваться в режиме реального времени и автоматически настраиваться для обеспечения размера резки.
- Качество луча: использование высококачественных оптических компонентов позволяет уменьшить рассеивание и отклонение луча, обеспечивая четкость и точность режущей кромки.
Необходимость поддержания высокой эффективности обработки при соблюдении строгих допусков еще больше усложняет процесс резки.
Решая эти проблемы, технология лазерной резки стала важнейшим инструментом для реализации сложных конструкций, открывая новые возможности в мире точного производства.
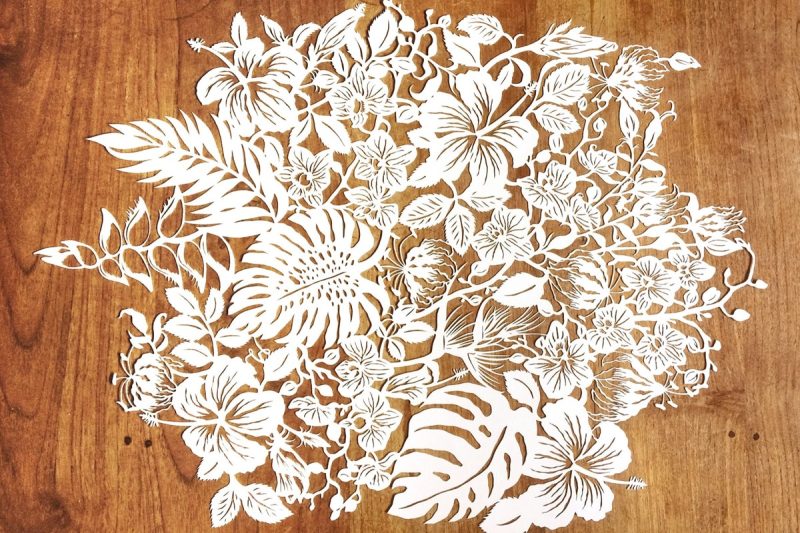
Технология повышения точности лазерной резки
В постоянно развивающейся области лазерной резки технологические достижения значительно повысили точность, эффективность и универсальность. Эти инновации решают проблемы, связанные с точностью и постоянством, особенно при работе со сложными конструкциями и различными типами материалов. Ниже мы рассмотрим три ключевых прорыва в лазерной резке CO2: автоматическая регулировка фокуса, системы мониторинга в реальном времени и интеграция CAD/CAM.
Регулировка автофокуса: повышение точности при работе с различными материалами
Автоматическая регулировка фокуса — это преобразующая функция в системах лазерной резки CO2. Она позволяет лазеру динамически подстраиваться под различную толщину материала и контуры поверхности, гарантируя, что лазерный луч остается в оптимальной фокусной точке, что имеет решающее значение для точной резки.
- Точность для разных типов материалов: различные материалы (например, металлы, пластик, стекло) требуют определенных настроек фокусировки для чистых разрезов. Автоматическая фокусировка устраняет необходимость ручной настройки, сокращая как время простоя, так и человеческие ошибки.
- Улучшенное качество кромок: сохраняя правильное фокусное расстояние, автофокусировка сводит к минимуму такие проблемы, как неровные кромки, неполные разрезы или прожоги материала, особенно в сложных узорах.
- Повышение эффективности: автоматизированные настройки оптимизируют процесс резки, делая его более быстрым и надежным, особенно при переключении между материалами или работе с многослойными конструкциями.
Системы мониторинга в реальном времени: обеспечение согласованности посредством корректировки в реальном времени
Системы мониторинга в реальном времени позволяют машинам для лазерной резки CO2 поддерживать точность и последовательность на протяжении всего процесса резки. Эти системы используют датчики и контуры обратной связи для мониторинга таких параметров, как выходная мощность, выравнивание луча и взаимодействие материалов.
- Динамическая регулировка: системы мониторинга могут автоматически регулировать такие параметры, как мощность лазера и скорость резки, чтобы учитывать изменения плотности материала или непредвиденные неровности.
- Минимизация дефектов: обнаружение в реальном времени таких проблем, как тепловая деформация или несоосность луча, предотвращает возникновение дефектов до их возникновения, гарантируя более высокое качество результатов.
- Повышение производительности: постоянная обратная связь снижает необходимость в проверках после резки и доработке, увеличивая производительность и экономическую эффективность.
Интеграция CAD/CAM: точное проектирование и исполнение
Интеграция программного обеспечения для автоматизированного проектирования (САПР) и автоматизированного производства (CAM) с системами резки CO2-лазером произвела революцию в том, как проекты преобразуются в физические компоненты. Эта синергия обеспечивает бесшовное выполнение и оптимизацию проектирования.
- Точное планирование пути: программное обеспечение CAD/CAM генерирует точные пути резки, гарантируя, что даже самые сложные конструкции будут выполнены безупречно. Это имеет решающее значение для отраслей, требующих жестких допусков, таких как аэрокосмическая промышленность и производство медицинских приборов.
- Оптимизация материалов: современное программное обеспечение моделирует траектории резки и использование материалов, сокращая отходы и повышая экономическую эффективность.
- Настраиваемые параметры: операторы могут заранее задать настройки лазерного генератора (например, мощность и скорость резки) в программном обеспечении, обеспечивая единообразие при различных производственных циклах и материалах.
- Автоматизация и масштабируемость: интеграция CAD/CAM поддерживает автоматизированные рабочие процессы, облегчая масштабируемое производство без ущерба для точности или качества.
Сочетание автоматической регулировки фокуса, мониторинга в реальном времени и интеграции CAD/CAM устанавливает новый стандарт точности резки CO2-лазером. Эти технологические достижения не только повышают точность резки, но и повышают эффективность, сокращают отходы материала и снижают эксплуатационные расходы. Вместе они позволяют производителям браться за сложные конструкции и достигать превосходной согласованности в широком спектре применений.
Используя эти передовые технологии, компании могут максимально использовать потенциал генераторов лазеров CO2 и обеспечивать высококачественные результаты, которые отвечают потребностям современной промышленности. Будь то сложные ювелирные изделия, прецизионные медицинские компоненты или автомобильные детали, эти технологические достижения прокладывают путь для будущего решений лазерной резки.
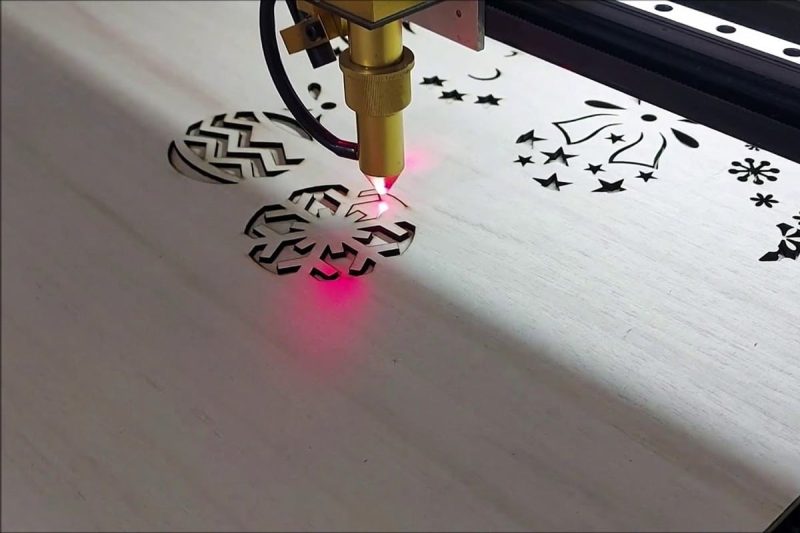
Преимущества высокоточной резки CO2-лазером
Улучшенное качество и единообразие деталей
Высокоточная резка лазером CO2 обеспечивает превосходное качество поверхности и однородность. Эта технология гарантирует, что каждое изделие сохраняет высокую однородность размера и формы, будь то массовое производство или изготовление деталей на заказ. По сравнению с традиционными методами резки, резка лазером CO2 значительно снижает отклонения, вызванные человеческим фактором или проблемами механической точности, тем самым значительно повышая однородность и качество продукции. Особенно в отраслях со строгими требованиями к качеству поверхности, таких как автомобилестроение, аэрокосмическая промышленность и производство медицинских приборов, лазерная резка обеспечивает более гладкие края с меньшим количеством заусенцев и неровных форм.
Сокращение потребности во вторичной переработке
Возможности точной резки лазерных генераторов CO2 значительно снижают необходимость в корректировках после резки. Традиционные методы резки часто требуют нескольких вторичных операций для улучшения кромок реза или корректировки размеров. Напротив, высокоточная лазерная резка может достигать желаемых результатов резки за один проход, экономя время и затраты на последующие корректировки. Это преимущество особенно ценно для производства сложных или прецизионных деталей, таких как прецизионные инструменты, аэрокосмические компоненты и электронные корпуса, сокращая трудозатраты и время производства.
Экономия средств и повышение производительности
Минимизируя вторичную обработку и оптимизируя процесс резки, высокоточная резка CO2-лазером значительно повышает эффективность производства. Лазерные генераторы могут выполнять эффективную резку с минимальным вмешательством человека, сокращая производственные циклы и гарантируя постоянное качество деталей, что снижает доработку и отходы материала. Этот автоматизированный и точный метод производства не только снижает эксплуатационные расходы, но и увеличивает пропускную способность, тем самым повышая общую производительность предприятий. Для крупных производителей высокоточная резка CO2-лазером является ключевым инструментом для оптимизации производственных процессов и повышения конкурентоспособности.
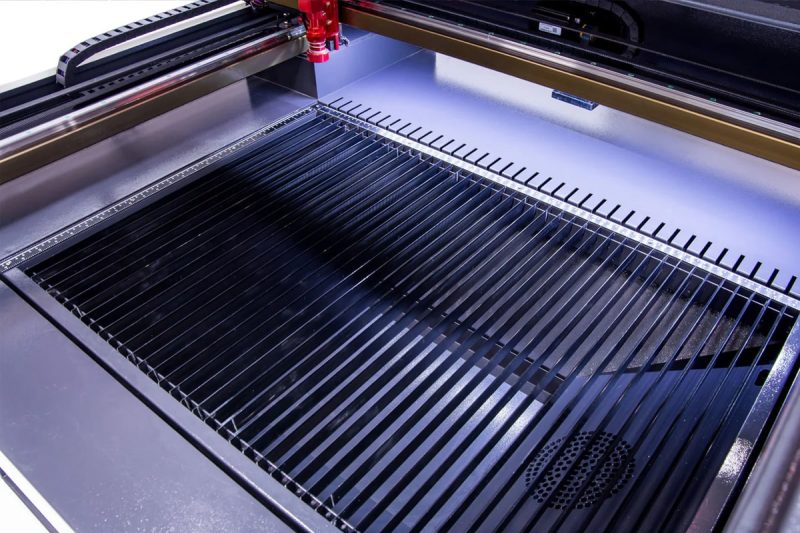
Приложения, требующие высокоточной резки
Высокоточная резка используется в самых разных областях, некоторые из основных применений включают в себя:
Аэрокосмические компоненты: Аэрокосмическая промышленность требует чрезвычайно высокой точности резки для обеспечения производительности и безопасности компонентов. Например, производство компонентов двигателя, структурных рам и прецизионных деталей требует технологии лазерной резки, чтобы гарантировать, что каждый компонент соответствует строгим требованиям по размеру, форме и прочности. Любое небольшое отклонение может повлиять на общую производительность или безопасность, поэтому высокоточная технология резки имеет важное значение.
Электроника и микроэлектроника: Поскольку электронные устройства становятся все более миниатюрными, к микроэлектронным компонентам предъявляются все более строгие требования к точности. В таких приложениях, как упаковка чипов, резка печатных плат и производство датчиков, лазерная резка может достигать чрезвычайно высокой точности, гарантируя, что каждая схема и компонент подключены правильно, тем самым обеспечивая надежность и производительность электронных устройств.
Медицинские приборы: Медицинские приборы и оборудование, особенно минимально инвазивные хирургические инструменты и имплантаты, требуют очень высокой точности резки. Эти приборы часто имеют сложную геометрию и чрезвычайно малые размеры, а лазерная резка может резать металлы, пластик и другие биосовместимые материалы с чрезвычайно высокой точностью, чтобы гарантировать, что прибор соответствует строгим медицинским стандартам с точки зрения функциональности и безопасности.
Архитектурные модели и прототипы: В архитектурном проектировании и прототипировании технология лазерной резки используется для создания сложных архитектурных моделей и деликатных компонентов. Она может точно резать различные материалы, такие как дерево, пластик и металл, для проверки дизайна и производства образцов. Это очень важно для демонстрации концепций дизайна, тестирования инженерных решений и общения с клиентами.
Эти приложения демонстрируют незаменимую роль высокоточной технологии резки в различных областях, которая позволяет соблюдать строгие допуски и сложные требования к конструкции, обеспечивая производительность и качество продукции.
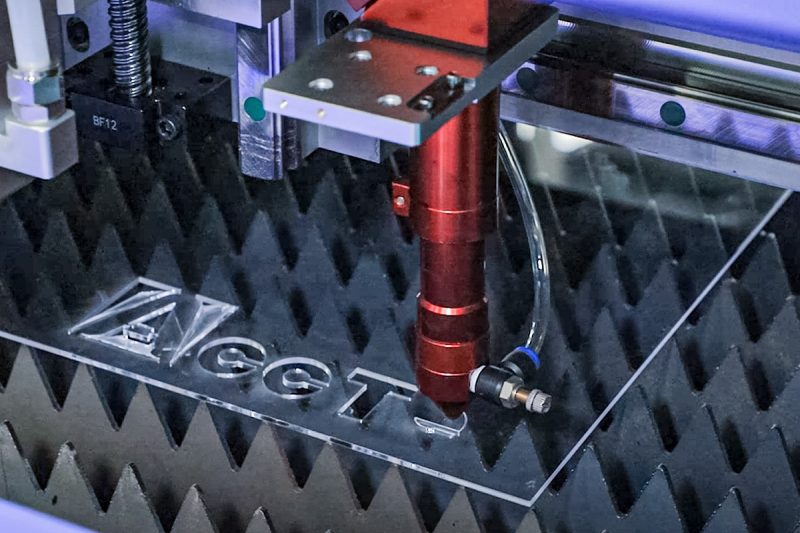
Подведем итог
Технология резки лазером CO2 с ее высокой точностью и превосходной адаптивностью доказала свои непревзойденные преимущества в области сложных конструкций и строгих допусков. От качества лазерного луча до функций автоматизации, каждый аспект поддерживает реализацию высокоточной резки. Будь то ключевые детали для аэрокосмической отрасли или точные потребности микроэлектроники и медицинского оборудования, резка лазером CO2 не только улучшает однородность и качество деталей, но и значительно снижает затраты на вторичную обработку и повышает общую эффективность производства.
Заглядывая в будущее, с постоянными инновациями технологий, лазерная резка CO2 покажет свой потенциал в большем количестве областей, предоставляя более эффективные и экономичные решения для точной обработки и сложного проектирования в обрабатывающей промышленности. Эта технология является не только основным инструментом для высокопроизводительного производства, но и продолжит продвигать отрасли к более точному и эффективному будущему.
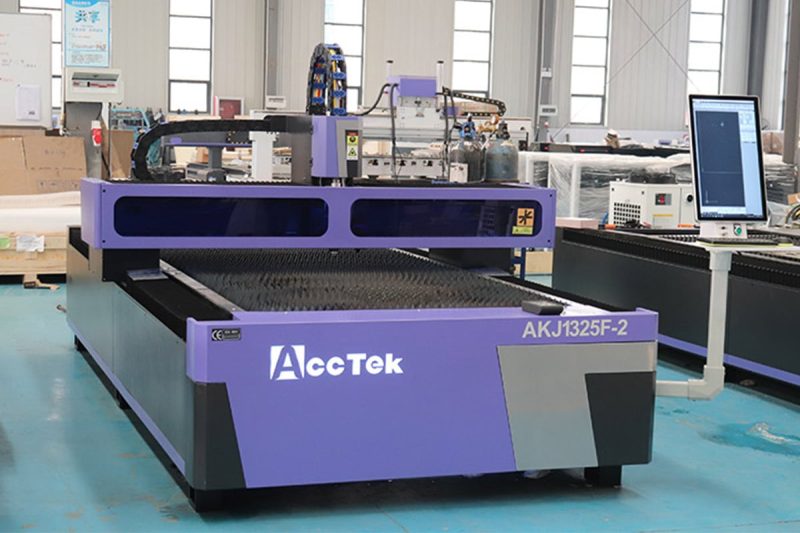
Получить лазерные решения
Хотите добиться высокоточной резки сложных конструкций? Актек Лазер предоставляет вам идеальное решение! Как эксперты в области лазерных технологий, мы сосредоточены на предоставлении клиентам высокопроизводительных и высоконадежных станков для лазерной резки CO2, чтобы удовлетворить ваши различные потребности в точном производстве. От деталей аэрокосмической отрасли до микрообработки электронных устройств, наше режущее оборудование поможет вам легко решать сложные задачи проектирования с превосходной точностью и стабильностью. Свяжитесь с нами сейчас, чтобы получить индивидуальное решение для лазерной резки, которое сделает ваш производственный процесс более эффективным и лучшим!
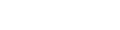
Контактная информация
- [email protected]
- [email protected]
- +86-19963414011
- Зона № 3 А, промышленная зона Лунчжэнь, город Юйчэн, провинция Шаньдун.
Получить лазерные решения