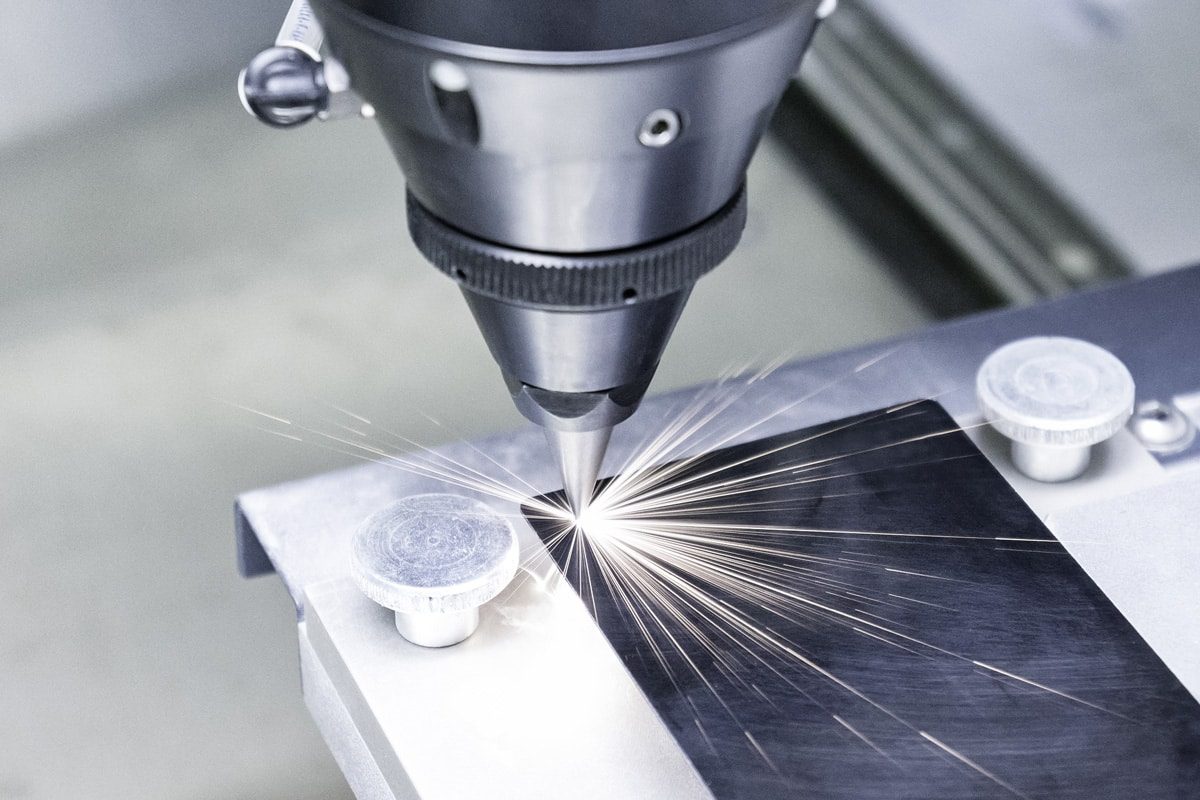
Sustainability of Laser Cutting Technology
In today’s rapidly developing global economy, companies not only face pressure to improve production efficiency but also shoulder a more important social responsibility – promoting environmental protection and sustainable development. In this context, laser cutting technology, as a highly precise and efficient processing method, is playing an increasingly important role in the manufacturing industry. This technology can not only significantly improve production efficiency, but also has many environmental advantages, helping companies reduce resource waste, reduce energy consumption, and reduce harmful emissions. With the increasing emphasis on environmental protection standards, laser cutting technology is becoming one of the key tools to promote green manufacturing due to its innovative and energy-saving characteristics.
Laser cutting technology has obvious advantages in the application of sustainable development. It can not only optimize the production process but also have a positive impact on the environment in many ways. This article will explore the sustainability of laser cutting technology in depth, analyze its positive impact on the environment, the difference from traditional cutting methods, how companies can implement environmental practices when using laser cutting technology, and explore the challenges encountered in the process of promoting sustainable development and the corresponding solutions. Through this series of discussions, we hope to fully demonstrate the potential of laser cutting technology in green manufacturing and help more companies move towards an environmentally friendly and sustainable future while pursuing efficient production.
Table of Contents
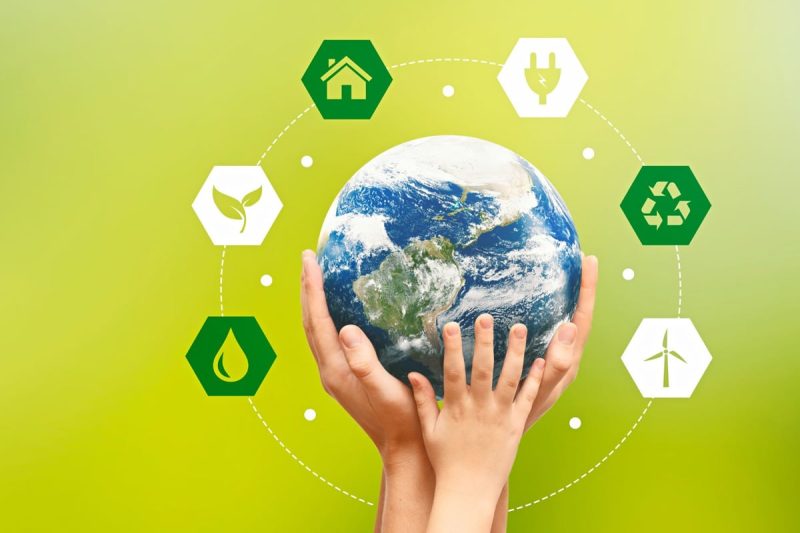
Environmental Impact of Laser Cutting
In the contemporary manufacturing industry, laser cutting technology stands out for its high precision and flexibility, becoming a green technology that not only improves production efficiency but also effectively reduces negative impacts on the environment. By optimizing energy utilization, reducing material waste, and controlling emissions, laser cutting technology shows great potential in environmental protection and sustainable development, which is specifically reflected in the following aspects:
Energy Efficiency
- Efficient power conversion: Laser cutting machines are known for their excellent energy efficiency and can convert electrical energy into cutting power more efficiently. Under the same power consumption, laser cutting can complete more work.
- Reduce energy waste: Compared with traditional mechanical cutting or combustion cutting technology, laser cutting does not require a lot of energy to drive mechanical parts or maintain combustion temperatures. This reduces a large amount of energy being wasted due to inefficient energy transfer in traditional methods.
- Optimized parameters and automatic control: Laser cutting equipment can further reduce power consumption through precise parameter optimization and automatic control to ensure maximum energy usage efficiency. This not only helps companies reduce energy costs but also reduces reliance on fossil fuels, thereby reducing carbon emissions.
Save Materials
- High precision reduces scraps: Laser cutting technology has extremely high precision and can reduce material waste. Traditional cutting methods often produce a lot of scraps due to insufficient precision, especially when multiple processing and adjustments are required. The error of laser cutting is usually only at the micron level, which greatly reduces waste.
- Improve material utilization: Laser cutting can optimize the cutting method of materials and maximize material utilization. For example, in high-precision industries such as electronic components, aviation parts, and automotive parts, laser cutting reduces material waste while improving product accuracy.
- Save natural resources: Through more efficient material utilization, companies not only reduce the procurement cost of raw materials, but also reduce the consumption of natural resources, promote the sustainable use of resources, and meet the requirements of green production.
Reducing Greenhouse Gas Emissions
- No combustion process reduces emissions: Traditional cutting methods, especially oxygen cutting or plasma cutting that rely on combustion or chemical reactions, usually produce a lot of greenhouse gases. Laser cutting uses light energy cutting, there is no combustion process, so almost no direct harmful gases are produced.
- Reduce indirect carbon emissions: Due to its high energy utilization efficiency, laser cutting equipment can reduce the power consumption required to complete the same amount of work, thereby indirectly reducing greenhouse gas emissions generated in the energy production process and helping companies reduce carbon emissions.
- Reduce waste gas emissions in the production process: Laser cutting equipment is often equipped with exhaust systems and air filtration technology, which can effectively control waste gas emissions and further reduce pollution to the atmosphere.
Waste Minimization
- Reduce waste in the heat-affected zone: Laser cutting technology can avoid waste caused by thermal deformation of materials due to its high-precision cutting and small heat-affected zone. This is in sharp contrast to the large amount of tool wear and heat damage waste generated by traditional cutting methods.
- Recycling and reuse of scraps: Laser cutting technology produces relatively little waste, and these wastes can usually be recycled and reused, reducing the burden on the environment and conforming to the concept of circular economy.
- Reduce waste disposal costs: Due to the high material utilization rate of laser cutting and the recyclability of waste, enterprises have greatly reduced the cost of waste disposal, while reducing the impact of waste on the environment, further enhancing the environmental image of the enterprise.
Overall, laser cutting technology has demonstrated significant advantages in energy efficiency, material saving, greenhouse gas emission reduction, and waste minimization, becoming a powerful tool for the manufacturing industry to promote green manufacturing and sustainable development. By using laser cutting, companies can not only improve production efficiency but also contribute to environmental protection and energy conservation, complying with the global trend of sustainable development.
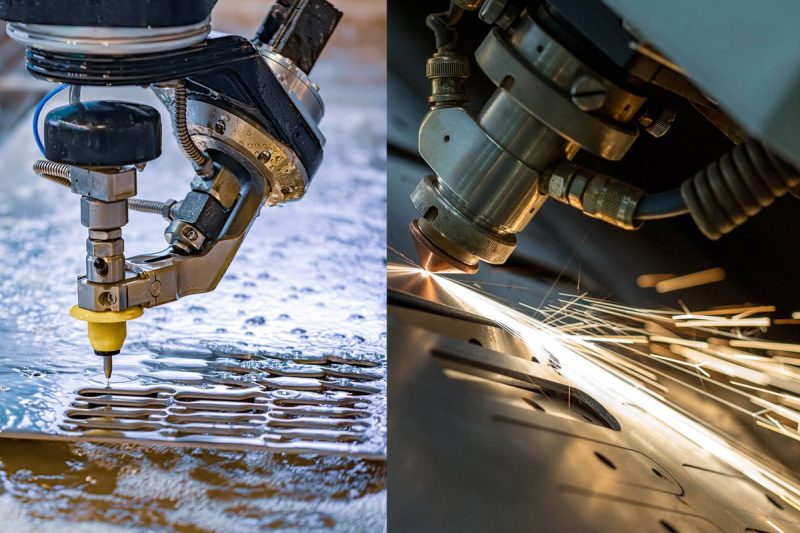
Comparison with Traditional Cutting Methods
Compared with traditional cutting methods, laser cutting technology has significant advantages in material saving, energy consumption, and reduction of harmful emissions, reflecting its superiority in sustainability. The specific performance is as follows:
Reduce Material Waste
- High precision reduces waste: Traditional cutting methods usually produce a lot of waste due to their low precision, especially when cutting complex shapes or fine parts, the material waste is even more serious. Laser cutting, with its extremely high precision, can greatly reduce the waste of scraps. By precisely controlling the cutting path and cutting thickness, the laser cutting machine can maximize material utilization and reduce losses.
- Flexible processing of different materials: The laser cutting machine can handle a variety of materials, whether it is metal, plastic, or other composite materials, it can ensure efficient and accurate cutting. This diverse material adaptability further reduces the waste problem caused by different material properties.
- Precise processing of complex shapes: Laser cutting can process very complex and fine shapes without changing tools or re-adjusting equipment. This flexibility ensures higher material utilization and less waste when processing complex shapes.
Reduce Energy Consumption
- Optimize energy use: Traditional mechanical or thermal cutting methods often consume large amounts of energy, especially when processing thicker or harder materials. Laser cutting significantly reduces energy consumption by using an efficient laser generator to more effectively convert electrical energy into the light energy required for cutting.
- Adjustable cutting parameters: The laser cutting machine can flexibly adjust the cutting power and speed according to the thickness, density, and other characteristics of the material to further optimize energy efficiency. Compared with traditional methods, laser cutting reduces excess energy waste and ensures that the cutting task is completed with minimal energy consumption.
- Efficient power management: Modern laser cutting machines are equipped with intelligent power management systems that can automatically adjust power output according to the workload to avoid unnecessary waste of energy. This intelligent regulation function helps further reduce overall energy consumption, especially in large-scale industrial production.
Minimize Harmful Emissions
- Reduce harmful gas and particle emissions: Traditional cutting methods, especially combustion cutting methods (such as flame cutting), will produce a large amount of harmful gases and fine particles during operation. These pollutants will have adverse effects on the environment and workers’ health. In contrast, laser cutting reduces pollutants produced by high-temperature combustion through non-contact cutting, which helps to improve the working environment.
- Exhaust system and filter device: Laser cutting equipment is usually equipped with efficient exhaust system and air filtration technology, which can effectively filter the small amount of exhaust gas and particles generated during the cutting process, further reducing the emission of harmful substances. This not only helps to protect the environment but also meets strict environmental regulations.
- Reduce the heat-affected zone during processing: Laser cutting can confine heating to a smaller area due to its efficient and concentrated beam, reducing the heat-affected zone (HAZ) of the material during processing, thereby reducing harmful gases produced by high-temperature combustion.
Water Resources and Resource Protection
- No water support required: Traditional cutting methods such as waterjet cutting require a large amount of water as a medium, which not only increases water consumption but also creates wastewater treatment problems. Laser cutting does not rely on water resources at all for processing, eliminating dependence on water and greatly reducing the waste of water resources.
- Reduce the need for wastewater treatment: Since laser cutting does not produce wastewater, companies do not need to invest additional costs and resources for wastewater treatment, which reduces the impact of wastewater discharge on the environment and reduces the pressure on companies in terms of environmental compliance.
- High resource utilization: In addition to reducing the use of water resources, laser cutting is also more efficient in the entire resource utilization process. Whether it is reducing material waste or energy consumption, laser cutting is known for its high resource utilization, helping companies better achieve green production and sustainable development goals.
In summary, laser cutting technology has shown significant advantages over traditional cutting methods in terms of material saving, energy consumption, harmful emissions, and resource protection. By making rational use of these advantages, companies can not only improve production efficiency but also better fulfill their environmental responsibilities and promote the sustainable development of the industry.
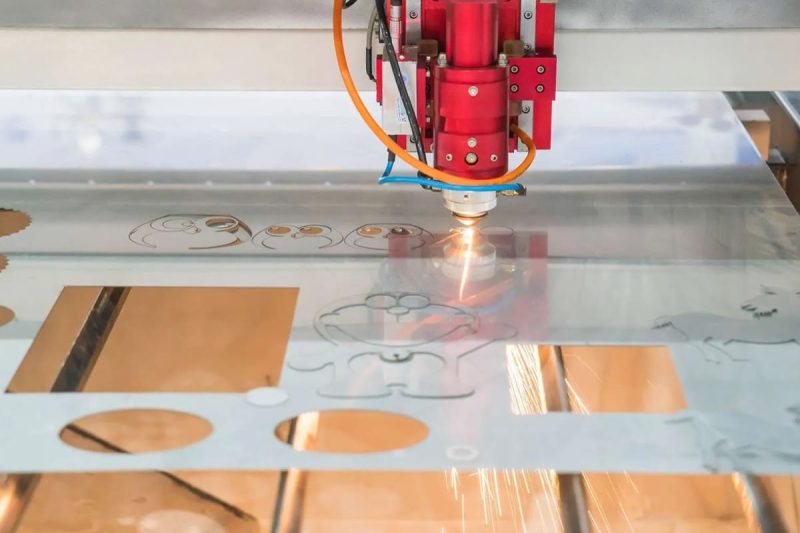
Environmentally Friendly Practices of Laser Cutting
To further tap the environmental protection potential of laser cutting technology, laser cutting manufacturers and users can take the following practical measures:
Energy Efficiency Measures
- Optimize cutting parameters: By accurately adjusting the power and cutting speed of laser cutting, the best cutting effect can be achieved under different materials and thicknesses, thereby reducing unnecessary energy consumption. Optimizing cutting parameters not only improves production efficiency but also ensures maximum energy utilization.
- Use an efficient laser generator: Choosing a high-efficiency laser generator can significantly improve the overall energy conversion efficiency of the laser cutting machine. These laser generators are more advanced in design and can complete the same cutting task with less energy consumption, thereby reducing the overall energy consumption in the production process.
- Intelligent power management systems: Modern laser cutting equipment is equipped with intelligent power management systems that automatically adjust power output based on cutting load. By reducing unnecessary power consumption, intelligent power management systems further improve energy efficiency and reduce energy costs.
Reduce Emissions
- Use clean energy: Providing clean energy, such as solar or wind power, to laser cutting equipment can effectively reduce carbon emissions generated during the production process. This not only helps reduce the company’s carbon emissions but also meets increasingly stringent environmental regulations and standards around the world.
- Install an exhaust system: A certain amount of exhaust gas may be generated during the laser cutting process. By installing an efficient exhaust system, these exhaust gases can be effectively discharged into the environment. The exhaust system can remove exhaust gas in a timely manner to prevent it from having a negative impact on worker health and the environment.
- Use air filtration devices: Equipping air filtration devices can further reduce the fine particles and harmful gases generated during the laser cutting process. These filters can capture and remove pollutants in the air, ensuring that emissions meet environmental standards and protect workers’ respiratory health.
Waste Reduction and Recycling
- Material utilization technology: Using computer-aided design (CAD) and computer numerical control (CNC) technology to precisely control the cutting path of the material can maximize the utilization rate of the material. By reducing the scraps generated during the cutting process, companies can effectively save raw materials and reduce production costs.
- Waste recycling: Recycling and reusing waste generated during laser cutting is an important measure to achieve a circular economy. Waste can be collected and sent to specialized recycling facilities for treatment and then processed into raw materials or other products, thereby reducing the impact of waste on the environment.
- Promoting a circular economy: By implementing waste recycling and reuse measures, companies can not only reduce waste disposal costs but also contribute to a circular economy. This practice supports the sustainable use of resources and is in line with the trend of global environmental protection.
In general, by implementing the above environmental practices, laser cutting technology can further improve its environmental performance and achieve a more efficient and sustainable production method. These measures not only help companies reduce the environmental burden during the production process but also promote the development of green manufacturing, which meets the requirements of global environmental protection and sustainable development.
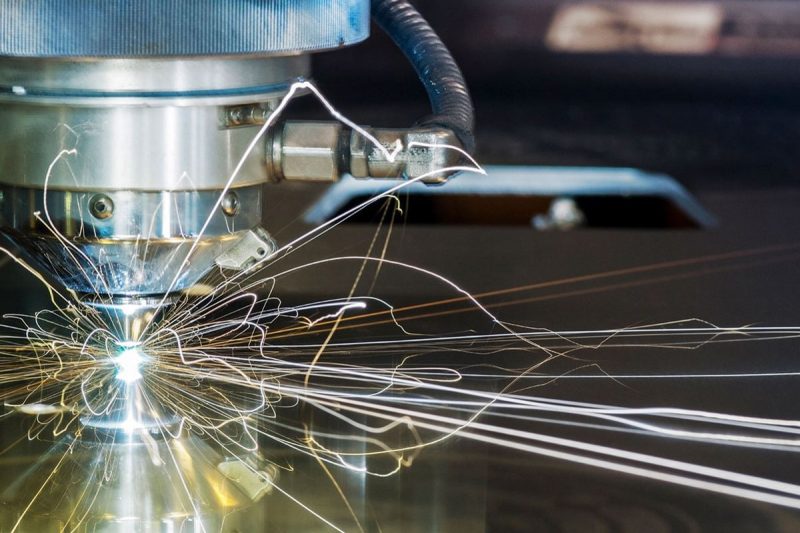
Challenges and Solutions
Despite the many sustainability advantages of laser cutting technology, there are still some challenges in its promotion and application. The following is a detailed discussion of these challenges and their potential solutions:
Cost Considerations
- High initial investment: The initial investment for high-efficiency laser generators and energy-saving equipment is high, especially for small businesses, which can be a major factor preventing them from introducing new technologies. These devices not only require large capital investment but also involve high installation and maintenance costs.
- Technological progress reduces costs: With the continuous advancement of laser cutting technology and large-scale production, the production cost of equipment has gradually declined. Technological innovation has brought higher cost performance, allowing more companies to afford high-efficiency laser cutting equipment.
- Long-term energy saving benefits: Although the initial investment is high, laser cutting equipment can significantly reduce energy costs during long-term use. Efficient energy utilization and reduced material waste can effectively balance the initial investment in equipment and bring long-term economic benefits to the enterprise.
Technical Limitations
- Material and thickness limitations: Although laser cutting technology is widely used in a variety of materials, there are still certain technical limitations for certain specific materials or very thick materials. For example, some highly reflective materials may cause inefficient laser cutting, while very thick materials may require multiple cuts to complete.
- Technological innovation breakthroughs: To overcome these technical limitations, the industry needs to continuously promote technological innovation. Research and development of new laser sources, improved cutting processes, and development of cutting technologies suitable for special materials can effectively break through existing technical bottlenecks.
- Material research and development: Enterprises and research institutions can cooperate in material research to develop new materials and new processing methods suitable for laser cutting, thereby expanding the application scope of laser cutting technology.
Regulatory Compliance
- Environmental regulations: As environmental regulations become increasingly stringent, companies need to ensure that their laser cutting equipment meets local environmental standards and regulatory requirements. This involves not only emission control of the equipment but also waste management and energy use during operation.
- Continuous optimization of equipment: Companies need to continue to invest resources to optimize laser cutting equipment and production processes to ensure compliance with ever-changing environmental regulations. Regular equipment upgrades and maintenance can help companies maintain compliance and reduce environmental risks.
- Certification of compliance with standards: Obtaining relevant environmental certifications can help companies prove that their equipment and production processes meet the prescribed standards, which not only enhances the company’s market competitiveness but also avoids penalties or legal risks due to non-compliance.
Collaboration and Industry Partnerships
- Inter-industry collaboration: Promoting the sustainable development of laser cutting technology is inseparable from inter-industry collaboration. Enterprises can establish cooperative relationships with scientific research institutions, equipment manufacturers, and environmental protection organizations to jointly research and develop more environmentally friendly and efficient laser cutting solutions.
- Technology sharing and cooperation: Through technology sharing and cooperation, all parties in the industry can jointly overcome technical bottlenecks, promote technological innovation, and improve the environmental performance of laser cutting technology. For example, jointly develop new laser generators or improve exhaust systems.
- Green standard formulation: Cooperating with industry partners and participating in the formulation and promotion of green standards can promote the sustainable development of the entire industry. By jointly formulating and complying with green standards, the industry can improve the overall environmental protection level and promote the popularization of green manufacturing.
Overall, although laser cutting technology has demonstrated significant advantages in terms of sustainability, the above challenges still need to be addressed during its promotion and application. By reducing costs, promoting technological innovation, ensuring compliance, and strengthening industry collaboration, companies can better address these challenges, fully leverage the environmental potential of laser cutting technology, and achieve sustainable development goals.
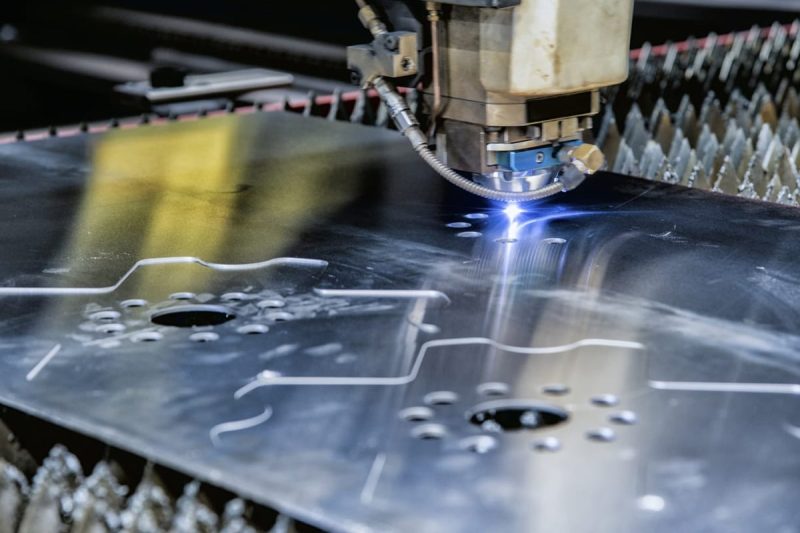
Summarize
Laser cutting technology has performed well in promoting the sustainable development of manufacturing industry with its excellent advantages of high precision, low energy consumption, and material saving. Laser cutting can not only complete complex cutting tasks accurately, but also performs well in material utilization, greatly reducing the waste of leftover materials. In terms of energy use, laser-cutting technology significantly reduces energy consumption in the production process through efficient energy conversion and intelligent power management. In addition, the laser cutting process produces very little waste material, and these waste materials can be recycled and reused, further reducing the burden on the environment. To further reduce the impact on the environment, laser cutting manufacturers and users actively adopt a series of environmental protection practices, including improving energy efficiency, reducing harmful emissions, and promoting material recycling. These measures make laser-cutting technology play an active role in environmental protection.
Although laser cutting technology has demonstrated significant advantages in terms of sustainability, it still faces some challenges in its promotion and application. These challenges include high initial investment costs, technology limitations, and increasingly stringent environmental regulations. However, through continued industry collaboration and technological innovation, these issues can be effectively addressed. Enterprises can overcome these challenges by reducing equipment costs, breaking through technical bottlenecks, ensuring compliance, and strengthening cooperation with scientific research institutions and environmental organizations. Looking to the future, laser cutting technology is expected to play a more sustainable role in manufacturing and become an important tool to achieve green manufacturing and environmental protection goals.
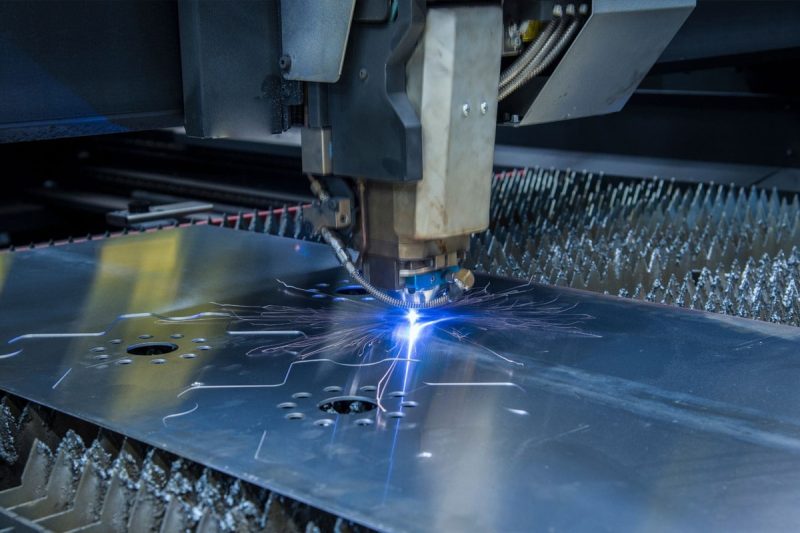
Get Laser Solutions
Choosing the right fiber laser cutting machine can help optimize power consumption and achieve high operational efficiency. Working with a trusted supplier ensures access to advanced technology, tailored advice, and ongoing support. At AccTek Laser, we offer a comprehensive range of laser cutting equipment designed to meet a variety of industrial needs. Our experts can help you choose the most energy-efficient model and configuration, taking into account factors such as material type, thickness, and production volume. We also offer cutting-edge features such as smart cooling systems and energy management software to maximize performance and minimize energy use. In addition, our team provides regular maintenance services and technical support to keep your equipment at peak efficiency. By partnering with AccTek Laser, you can achieve significant energy savings, reduce operating costs, and enhance your sustainability efforts. Contact us today to learn more about our innovative laser solutions and how they can benefit your business.
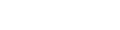
Contact information
- [email protected]
- [email protected]
- +86-19963414011
- No. 3 Zone A, Lunzhen Industrial Zone,Yucheng City , Shandong Province.
Get Laser Solutions