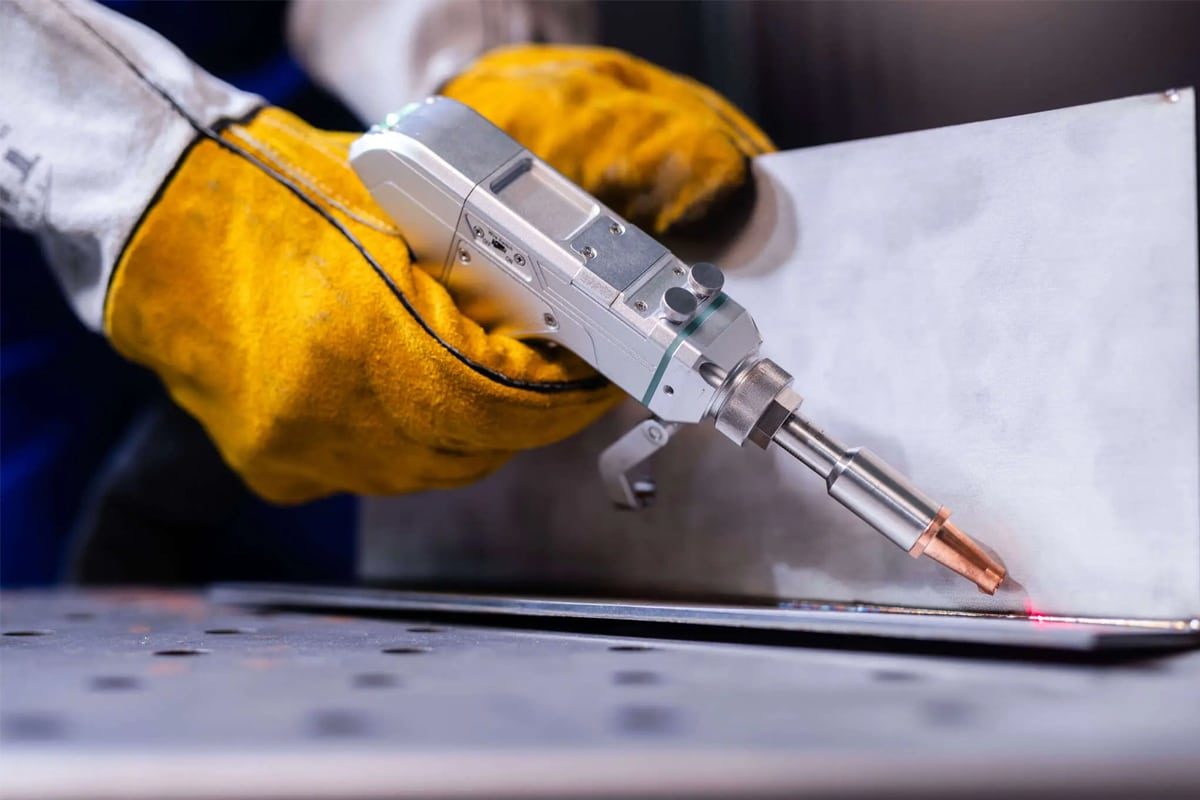
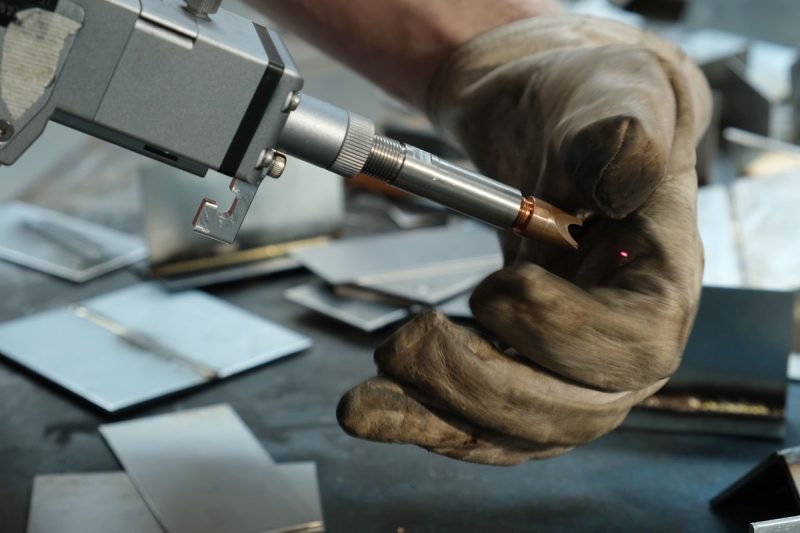
การเชื่อมด้วยเลเซอร์ทำงานอย่างไร
หลักการเชื่อมด้วยเลเซอร์
การเชื่อมด้วยเลเซอร์ทำงานโดยการโฟกัสแสงเลเซอร์พลังงานสูงไปที่บริเวณเล็กๆ ของวัสดุ พลังงานที่เข้มข้นนี้จะทำให้วัสดุร้อนขึ้นอย่างรวดเร็ว ส่งผลให้วัสดุหลอมละลายและหลอมรวมเข้าด้วยกัน ซึ่งแตกต่างจากการเชื่อมแบบเดิมที่มักอาศัยโซนความร้อนที่กว้างกว่า การเชื่อมด้วยเลเซอร์จะเน้นที่การสร้างโซนที่ได้รับผลกระทบจากความร้อนน้อยที่สุด ลดการบิดเบือน และให้รอยต่อที่สะอาดและมีคุณภาพสูง การหลอมรวมเกิดขึ้นในโหมดหลัก 1 ใน 2 โหมด ได้แก่ โหมดการนำไฟฟ้าหรือโหมดคีย์โฮล
- กำลังและโฟกัสของเลเซอร์: ความหนาแน่นของกำลังเลเซอร์และขนาดจุดจะกำหนดความลึกและความกว้างของรอยเชื่อม ความหนาแน่นของกำลังที่สูงกว่าจะสร้างรอยเชื่อมที่ลึกกว่า ในขณะที่การตั้งค่ากำลังที่ต่ำลงจะใช้สำหรับรอยเชื่อมที่ละเอียดและตื้นกว่า
- การควบคุมความร้อน: การเชื่อมด้วยเลเซอร์ช่วยให้ควบคุมปริมาณความร้อนได้อย่างแม่นยำ ซึ่งถือเป็นสิ่งสำคัญสำหรับการเชื่อมวัสดุที่ไวต่อความร้อนหรือชิ้นส่วนที่ซับซ้อน
ประเภทของโหมดการเชื่อมเลเซอร์
การเชื่อมแบบการนำไฟฟ้า
คุณสมบัติ:
- การเจาะเชื่อมตื้น โดยทั่วไปน้อยกว่า 2 มม.
- รอยเชื่อมเรียบและกว้างโดยมีการเสียรูปของพื้นผิวน้อยที่สุด
- ความเสี่ยงในการเกิดรูกุญแจน้อยที่สุด ทำให้โอกาสที่จะเกิดรูพรุนหรือช่องว่างลดลง
การใช้งาน:
- มักใช้กับวัสดุบางและการใช้งานที่คุณภาพของภาพเป็นสิ่งสำคัญ
- เหมาะสำหรับการใช้งานในเครื่องประดับ อุปกรณ์การแพทย์ และอุปกรณ์อิเล็กทรอนิกส์ที่จำเป็นต้องมีพื้นผิวที่เรียบเนียน
การเชื่อมแบบคีย์โฮล
คุณสมบัติ:
- การเจาะเชื่อมลึก (สูงสุดหลายเซนติเมตร) ด้วยความกว้างที่แคบ
- อัตราส่วนภาพสูง ส่งผลให้เชื่อมได้แข็งแรงและตรงจุด
- การดูดซับพลังงานอย่างมีประสิทธิภาพเนื่องจากการสะท้อนหลายครั้งภายในรูกุญแจช่วยให้เชื่อมได้ลึกขึ้น
การใช้งาน:
- เหมาะสำหรับการใช้งานหนักที่ต้องการข้อต่อที่แข็งแรงทนทาน เช่น ในส่วนประกอบยานยนต์และอวกาศ
- มีประสิทธิภาพสำหรับวัสดุหนาและโลหะที่มีความแข็งแรงสูงซึ่งจำเป็นต้องมีการหลอมรวมอย่างล้ำลึก
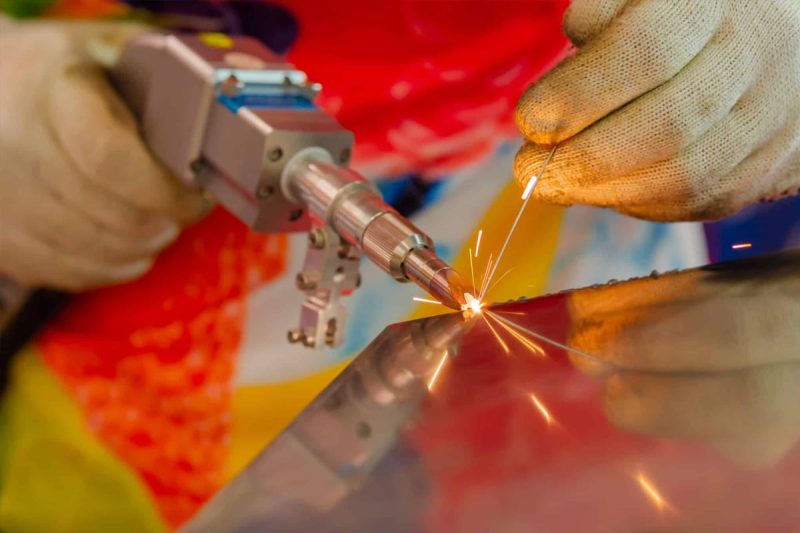
ข้อดีของการเชื่อมด้วยเลเซอร์
ความแม่นยำและความแม่นยำ
ความเร็วในการเชื่อมสูง
กระบวนการแบบไม่สัมผัส
การเจาะลึกและการเชื่อมแบบแคบ
ความสามารถในการเชื่อมวัสดุที่เชื่อมยาก
ความบิดเบือนขั้นต่ำและโซนที่ได้รับผลกระทบจากความร้อน
รอยเชื่อมที่สะอาดและสวยงาม
ต้นทุนการบำรุงรักษาและการดำเนินงานต่ำ
ประสิทธิภาพการใช้พลังงาน
ระบบอัตโนมัติและความยืดหยุ่น
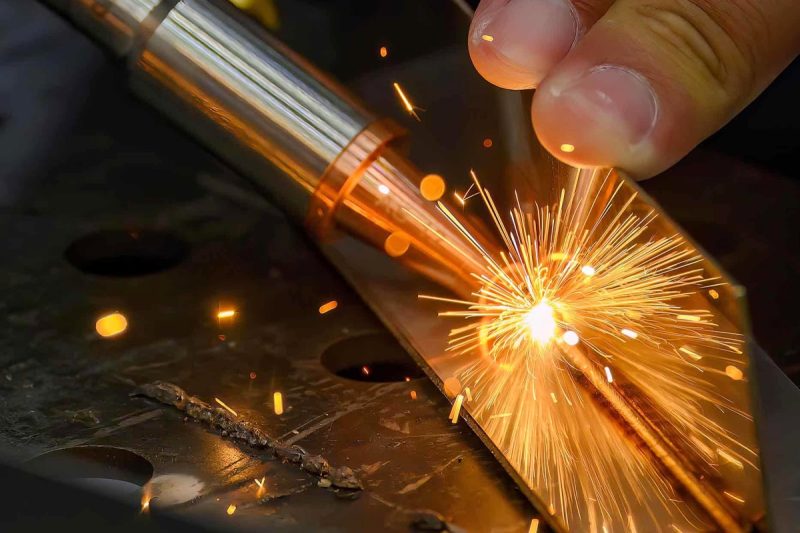
ข้อเสียของการเชื่อมด้วยเลเซอร์
การลงทุนเริ่มต้นสูง
การเชื่อมแบบความหนาจำกัด
ความไวต่อการปรับข้อต่อ
ข้อกังวลด้านความปลอดภัย
ปัญหาเรื่องการสะท้อนแสง
ความซับซ้อนทางเทคนิค
ความไวของอุปกรณ์
การใช้สนามจำกัด
ต้องใช้ผู้ปฏิบัติงานที่มีทักษะ
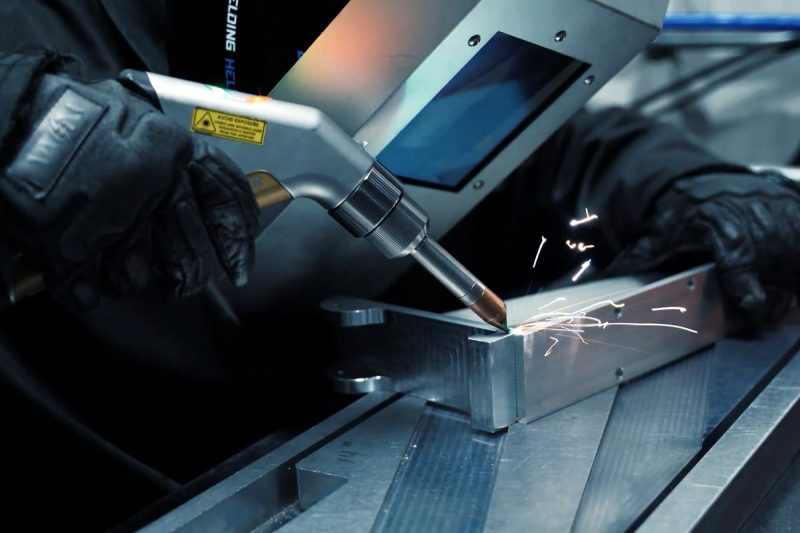
การประยุกต์ใช้งานการเชื่อมด้วยเลเซอร์
อุตสาหกรรมยานยนต์
การประยุกต์ใช้ในยานยนต์:
- แผงตัวถังและช่องว่างที่ออกแบบมาโดยเฉพาะ
- ส่วนประกอบเครื่องยนต์ รวมถึงชิ้นส่วนระบบส่งกำลัง
- ปลอกหุ้มถุงลมนิรภัยต้องอาศัยความแม่นยำและความน่าเชื่อถือ
- ระบบไอเสีย จำเป็นต้องมีการเชื่อมที่สามารถทนต่ออุณหภูมิและแรงดันสูงได้
อุตสาหกรรมการบินและอวกาศ
การประยุกต์ใช้ในอวกาศ:
- ระบบเชื้อเพลิงและท่อไฮดรอลิกต้องมีการเชื่อมป้องกันการรั่วไหล
- ส่วนประกอบโครงสร้าง ได้แก่ ชิ้นส่วนลำตัวเครื่องบินและขาลงจอด
- ใบพัดและชิ้นส่วนเครื่องยนต์อื่นๆ ซึ่งความแข็งแกร่งและการทนทานต่ออุณหภูมิถือเป็นสิ่งสำคัญ
- อุปกรณ์อิเล็กทรอนิกส์ในอุตสาหกรรมการบินและอวกาศ จำเป็นต้องมีการเชื่อมที่แม่นยำและสะอาดเพื่อให้มั่นใจถึงความน่าเชื่อถือในระยะยาว
การผลิตอุปกรณ์การแพทย์
การประยุกต์ใช้ในการผลิตอุปกรณ์ทางการแพทย์:
- เครื่องมือผ่าตัดที่ต้องทนทานต่อการกัดกร่อนและความสะอาดเป็นสิ่งสำคัญ
- อุปกรณ์ปลูกถ่ายทางการแพทย์ เช่น ปลอกเครื่องกระตุ้นหัวใจ และอุปกรณ์กระดูกและข้อ ต้องใช้การเชื่อมแบบกันอากาศเข้าได้กับร่างกาย
- สายสวนและกล้องส่องตรวจต้องมีการเชื่อมชิ้นส่วนขนาดเล็กให้ละเอียดและแม่นยำ
- กล่องใส่แบตเตอรี่สำหรับอุปกรณ์ทางการแพทย์ซึ่งความสมบูรณ์ของรอยเชื่อมเป็นสิ่งสำคัญสำหรับการใช้งานในระยะยาว
อุตสาหกรรมอิเล็กทรอนิกส์
การประยุกต์ใช้ในอิเล็กทรอนิกส์:
- การเชื่อมต่อแผงวงจรให้การเชื่อมที่ละเอียดและแม่นยำโดยไม่ทำให้ส่วนประกอบบริเวณใกล้เคียงเสียหาย
- ตัวเรือนเซ็นเซอร์และการเชื่อมต่อแบตเตอรี่ต้องมีข้อต่อที่แข็งแรงและทนทาน
- กล่องสำหรับส่วนประกอบอิเล็กทรอนิกส์ที่ละเอียดอ่อน ช่วยปกป้องจากปัจจัยด้านสิ่งแวดล้อม
- การเชื่อมด้วยไมโครในกระบวนการผลิตเซมิคอนดักเตอร์ ซึ่งความแม่นยำและความสะอาดเป็นสิ่งสำคัญ
อุตสาหกรรมเครื่องประดับ
การประยุกต์ใช้ในเครื่องประดับ:
- การซ่อมแซมเครื่องประดับที่มีอยู่ เช่น การเปลี่ยนขนาดแหวน หรือการซ่อมแซมโซ่ที่ขาด
- การฝังหินช่วยให้เชื่อมติดกับอัญมณีได้อย่างแน่นหนาโดยไม่เกิดความเสียหายจากความร้อน
- งานโลหะที่ซับซ้อนในการออกแบบเครื่องประดับที่กำหนดเอง ซึ่งต้องมีการเชื่อมที่มีรายละเอียดและละเอียดอ่อน
- การสร้างสรรค์งานออกแบบโลหะผสม เช่น การเชื่อมทองและแพลตตินัม โดยมีรอยเชื่อมที่สะอาดและมองไม่เห็น
ภาคพลังงาน
การประยุกต์ใช้ในด้านพลังงาน:
- การผลิตแบตเตอรี่ซึ่งการเชื่อมด้วยเลเซอร์จะสร้างการเชื่อมต่อที่ทนทานระหว่างเซลล์และขั้วต่างๆ
- เซลล์เชื้อเพลิงและส่วนประกอบแผงโซลาร์เซลล์ได้รับประโยชน์จากการเชื่อมที่สะอาดและแม่นยำ
- ท่อน้ำมันและก๊าซซึ่งต้องมีการเชื่อมด้วยความแข็งแรงสูงเพื่อความปลอดภัยภายใต้แรงดันสูง
- ส่วนประกอบของกังหันลม รวมถึงชิ้นส่วนโครงสร้างต้องทนต่อสภาพอากาศและความเค้นทางกล
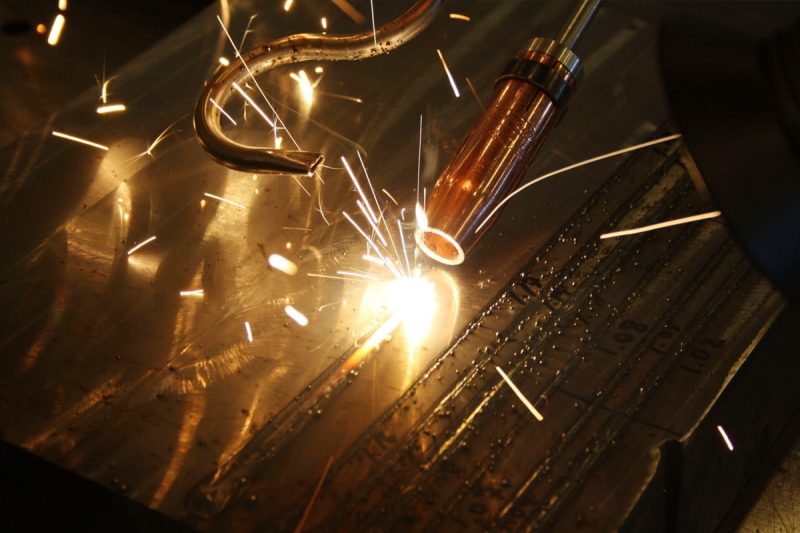
การเปรียบเทียบกับวิธีการเชื่อมแบบดั้งเดิม
การเชื่อมด้วยเลเซอร์เทียบกับการเชื่อม TIG
- การเชื่อมด้วยก๊าซเฉื่อยทังสเตน (TIG) เป็นที่รู้จักกันว่าสามารถให้รอยเชื่อมที่มีคุณภาพสูงและสะอาดบนโลหะได้หลากหลายประเภท รวมถึงอลูมิเนียม สแตนเลส และทองแดง การเชื่อม TIG ใช้ขั้วไฟฟ้าทังสเตนเพื่อสร้างส่วนโค้งระหว่างขั้วไฟฟ้าและชิ้นงาน ทำให้โลหะหลอมละลายและมักต้องใช้สารอุด
- ความแม่นยำและความถูกต้อง: การเชื่อมด้วยเลเซอร์และ TIG ให้ความแม่นยำสูง แต่การเชื่อมด้วยเลเซอร์มีข้อได้เปรียบกว่าเนื่องจากลำแสงที่โฟกัส ซึ่งสามารถสร้างรอยเชื่อมที่แคบมากโดยมีโซนที่ได้รับผลกระทบจากความร้อน (HAZ) น้อยที่สุด การเชื่อม TIG ต้องใช้การควบคุมด้วยมือมากกว่าและช้ากว่า ทำให้ไม่เหมาะกับการเชื่อมชิ้นส่วนที่ละเอียดอ่อนที่มีขนาดเล็กและซับซ้อน
- ความร้อนที่เข้ามาและการบิดเบือน: ความร้อนที่เข้ามาจากการเชื่อมด้วยเลเซอร์จะสร้าง HAZ ที่น้อยกว่ามากเมื่อเทียบกับการเชื่อม TIG ซึ่งจะช่วยลดความเสี่ยงของการบิดเบือนจากความร้อน ซึ่งมีความสำคัญอย่างยิ่งสำหรับวัสดุที่บางและการใช้งานที่ไวต่อความร้อน การเชื่อม TIG แม้จะควบคุมได้ แต่จะสร้างความร้อนที่กระจายไปทั่วพื้นที่ที่กว้างขึ้น ซึ่งอาจทำให้วัสดุที่บางกว่าบิดเบี้ยวได้
- ความเร็ว: การเชื่อมด้วยเลเซอร์นั้นเร็วกว่าการเชื่อมแบบ TIG อย่างเห็นได้ชัด ทำให้เหมาะสำหรับการผลิตปริมาณมาก การเชื่อมแบบ TIG นั้นสามารถให้ผลลัพธ์ที่มีคุณภาพสูงได้ แต่ช้ากว่าเนื่องจากต้องดำเนินการด้วยมือและต้องมีความแม่นยำ จึงเหมาะสำหรับโครงการหรือการซ่อมแซมขนาดเล็กมากกว่า
- การใช้งาน: การเชื่อม TIG มักใช้ในโครงการขนาดเล็กและงานที่ต้องการความแม่นยำ เช่น การบินและอวกาศและชิ้นส่วนยานยนต์ แต่โดยทั่วไปแล้วจะมีข้อจำกัดในด้านความเร็วและความเข้ากันได้กับระบบอัตโนมัติ การเชื่อมด้วยเลเซอร์เหมาะอย่างยิ่งสำหรับการใช้งานที่ต้องการทั้งความเร็วและความแม่นยำ เช่น อิเล็กทรอนิกส์ อุปกรณ์ทางการแพทย์ และชิ้นส่วนยานยนต์ที่มีปริมาณมาก
การเชื่อมด้วยเลเซอร์เทียบกับการเชื่อมด้วย MIG
- การเชื่อมด้วยก๊าซเฉื่อย (MIG) เป็นวิธีการเชื่อมที่นิยมใช้ในการเชื่อมวัสดุที่มีความหนา โดยเฉพาะอย่างยิ่งในการใช้งานที่ความเร็วและปริมาณการผลิตเป็นสิ่งสำคัญ การเชื่อมด้วย MIG จะใช้ลวดอิเล็กโทรดที่ป้อนอย่างต่อเนื่องซึ่งจะหลอมละลายเพื่อสร้างรอยเชื่อม ซึ่งมักจะทำให้ได้พื้นที่เชื่อมที่กว้างขึ้นและต้องมีการประมวลผลภายหลังเพื่อขจัดสะเก็ดไฟ
- การเจาะทะลุและความกว้างของรอยเชื่อม: การเชื่อมด้วยเลเซอร์สามารถเจาะทะลุได้ลึกด้วยรอยเชื่อมที่แคบ แม้กระทั่งกับวัสดุหนา โดยไม่จำเป็นต้องใช้สารตัวเติม การเชื่อม MIG ทำให้ได้รอยเชื่อมที่กว้างขึ้นและแม่นยำน้อยลง ซึ่งมักต้องทำความสะอาดและตกแต่งเพิ่มเติม สำหรับการใช้งานที่ต้องใช้รอยเชื่อมที่แคบและแข็งแรง การเชื่อมด้วยเลเซอร์จะเหมาะสมกว่า
- โซนที่ได้รับผลกระทบจากความร้อน: การเชื่อม MIG ก่อให้เกิดความร้อนมากกว่าการเชื่อมด้วยเลเซอร์ ทำให้เกิด HAZ ที่มากขึ้นและเพิ่มความเสี่ยงของการบิดเบือนเนื่องจากความร้อน ความร้อนที่เข้มข้นของการเชื่อมด้วยเลเซอร์จะลด HAZ โดยรักษาคุณสมบัติเชิงกลของวัสดุโดยรอบและลดการบิดเบือนหลังการเชื่อมให้น้อยที่สุด โดยเฉพาะในวัสดุที่บางหรือไวต่อความร้อน
- ระบบอัตโนมัติและความเร็วในการผลิต: การเชื่อมด้วยเลเซอร์เข้ากันได้ดีกับระบบอัตโนมัติและสามารถทำงานด้วยความเร็วที่สูงกว่ามาก ทำให้เหมาะอย่างยิ่งสำหรับสภาพแวดล้อมการผลิตปริมาณมาก การเชื่อม MIG เร็วกว่า TIG แต่โดยทั่วไปแล้วเหมาะสำหรับกระบวนการแบบแมนนวลหรือกึ่งอัตโนมัติมากกว่า เนื่องจากต้องใช้ลวดป้อนและก๊าซป้องกัน
- วัสดุ: การเชื่อม MIG มีประสิทธิภาพสำหรับวัสดุที่มีความหนากว่าและโลหะที่ใช้กันทั่วไป เช่น เหล็กและอลูมิเนียม แต่มีปัญหาในการเชื่อมกับวัสดุต่างชนิดและวัสดุที่บางมาก ซึ่งต้องใช้ความแม่นยำและความร้อนต่ำ การเชื่อมด้วยเลเซอร์เหมาะสำหรับการเชื่อมโลหะที่มีความบางและไม่เหมือนกัน เช่น ทองแดง กับสแตนเลส เนื่องจากสามารถควบคุมพลังงานได้อย่างแม่นยำ
การเชื่อมด้วยเลเซอร์เทียบกับการเชื่อมด้วยลำแสงอิเล็กตรอน
- การเชื่อมด้วยลำแสงอิเล็กตรอน (EB) เป็นกระบวนการเชื่อมพลังงานสูงที่คล้ายกับการเชื่อมด้วยเลเซอร์ โดยสามารถเชื่อมวัสดุได้ลึกและแม่นยำ การเชื่อมด้วยลำแสงอิเล็กตรอนแบบ EB ใช้ลำแสงอิเล็กตรอนที่รวมศูนย์ในสุญญากาศเพื่อเชื่อมวัสดุเข้าด้วยกัน จึงเหมาะสำหรับการใช้งานหนักที่ต้องเจาะลึกมากและมีสภาพแวดล้อมที่ควบคุมได้
- สภาพแวดล้อมและการตั้งค่า: การเชื่อมด้วยเลเซอร์นั้นแตกต่างจากการเชื่อมแบบเปิดโล่ง การเชื่อมแบบ EB ต้องใช้ห้องสูญญากาศเพื่อรักษาลำแสงอิเล็กตรอน การตั้งค่าสูญญากาศนี้ทำให้การเชื่อมแบบ EB ซับซ้อน มีค่าใช้จ่ายสูง และมีความยืดหยุ่นน้อยกว่าการเชื่อมด้วยเลเซอร์ ซึ่งสามารถใช้ได้ในสภาพแวดล้อมที่หลากหลายกว่า รวมถึงห้องปลอดเชื้อหรือสายการผลิตแบบกึ่งอัตโนมัติ
- ความลึกและความแข็งแรงของการเจาะทะลุ: การเชื่อม EB สามารถเจาะทะลุได้ลึกกว่าการเชื่อมด้วยเลเซอร์ ทำให้เหมาะอย่างยิ่งสำหรับวัสดุที่มีความหนาหรือการใช้งานโครงสร้างที่ต้องใช้การเชื่อมที่แข็งแรงมาก อย่างไรก็ตาม สำหรับวัสดุที่มีความหนาปานกลางถึงบาง การเชื่อมด้วยเลเซอร์มักจะมีประสิทธิภาพมากกว่าและใช้งานง่ายกว่า
- ความเร็วและระบบอัตโนมัติ: การเชื่อมด้วยเลเซอร์สามารถให้ความเร็วสูงขึ้นและผสานเข้ากับสายการผลิตอัตโนมัติได้ง่ายกว่า ทำให้เหมาะสำหรับการผลิตปริมาณมาก การเชื่อมด้วยเลเซอร์แบบ EB แม้จะมีประสิทธิภาพ แต่โดยทั่วไปจะช้ากว่าและปรับให้เข้ากับสภาพแวดล้อมการผลิตอัตโนมัติที่รวดเร็วได้น้อยกว่า เนื่องจากต้องใช้ห้องสุญญากาศ
- ต้นทุนและการบำรุงรักษา: ระบบเชื่อม EB มีราคาแพงและต้องมีการบำรุงรักษาเฉพาะทาง โดยเฉพาะระบบสูญญากาศ การเชื่อมด้วยเลเซอร์มีข้อกำหนดในการบำรุงรักษาน้อยกว่า ทำให้เข้าถึงได้ง่ายกว่าและคุ้มต้นทุนสำหรับการผลิตทั่วไป นอกจากนี้ เวลาในการเตรียมและการบำรุงรักษาสำหรับการเชื่อม EB อาจทำให้มีเวลาหยุดทำงานนานกว่าเมื่อเทียบกับการเชื่อมด้วยเลเซอร์
การเปรียบเทียบ
- การเชื่อมที่แม่นยำและสะอาด: การเชื่อมด้วยเลเซอร์เหนือกว่าการเชื่อม MIG และ TIG ในด้านความแม่นยำ ในขณะที่แข่งขันกับการเชื่อม EB เพื่อให้ได้ผลลัพธ์ที่สะอาดและแม่นยำ
- ความเร็ว: การเชื่อมเลเซอร์นั้นเร็วกว่าการเชื่อม TIG และ MIG และโดยทั่วไปแล้วจะเหมาะสำหรับการผลิตอัตโนมัติความเร็วสูง โดยเฉพาะอย่างยิ่งเมื่อต้องมีความแม่นยำ
- สภาพแวดล้อม: ความยืดหยุ่นของการเชื่อมเลเซอร์ในสภาพแวดล้อมที่มีอากาศทำให้มีความอเนกประสงค์มากกว่าการเชื่อมแบบ EB ซึ่งต้องใช้สุญญากาศ
- โซนที่ได้รับผลกระทบจากความร้อน: HAZ ที่น้อยที่สุดของการเชื่อมเลเซอร์ทำให้เหมาะอย่างยิ่งสำหรับวัสดุบางและไวต่อความร้อน ให้ประสิทธิภาพเหนือกว่าการเชื่อม TIG และ MIG ในแง่นี้
- ต้นทุนและความซับซ้อน: การเชื่อมด้วยเลเซอร์มีต้นทุนเริ่มต้นสูง แต่มีต้นทุนการบำรุงรักษาและการดำเนินการต่ำกว่าเมื่อเทียบกับการเชื่อมแบบ EB ซึ่งต้องใช้เครื่องมือและการบำรุงรักษาที่ซับซ้อนกว่า
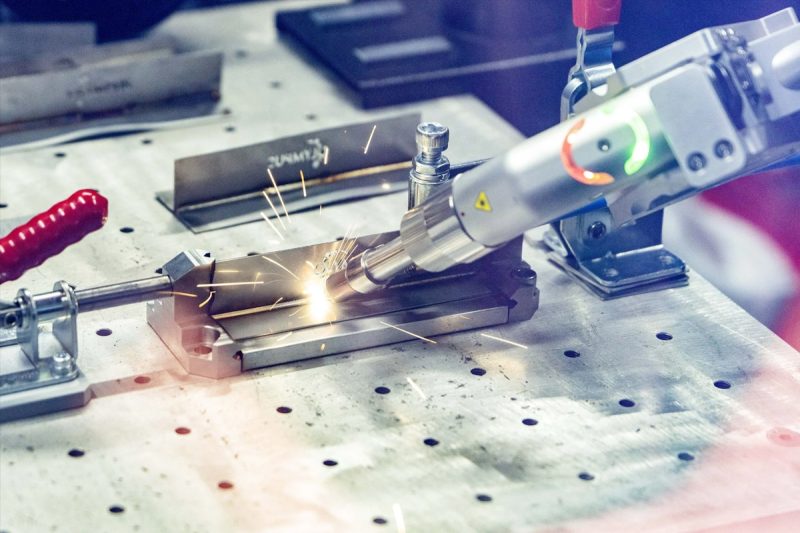
ปัจจัยที่มีผลต่อคุณภาพการเชื่อมด้วยเลเซอร์
พารามิเตอร์เลเซอร์
การตั้งค่าและคุณลักษณะของเลเซอร์เองมีบทบาทสำคัญในการกำหนดคุณภาพของการเชื่อม พารามิเตอร์หลักของเลเซอร์ ได้แก่ พลังงาน ขนาดจุดโฟกัส ความเร็วในการเชื่อม และความถี่ของพัลส์ (สำหรับเลเซอร์แบบพัลส์)
- กำลังเลเซอร์: กำลังเลเซอร์ที่สูงขึ้นจะช่วยเพิ่มความลึกในการเจาะและทำให้เชื่อมได้เร็วขึ้น แต่ก็อาจทำให้เกิดความร้อนมากเกินไปได้หากไม่ได้รับการควบคุมอย่างเหมาะสม กำลังที่มากเกินไปอาจทำให้เกิดการกระเด็นหรือไหม้ ในขณะที่กำลังที่น้อยเกินไปอาจทำให้เชื่อมได้ไม่แน่นหรือไม่สมบูรณ์
- ความเร็วในการเชื่อม: ความเร็วที่เลเซอร์เคลื่อนที่ผ่านชิ้นงานส่งผลต่อคุณภาพของการเชื่อม ความเร็วในการเชื่อมที่สูงสามารถลดปริมาณความร้อนที่เข้ามา ลดพื้นที่ที่ได้รับผลกระทบจากความร้อน (HAZ) และลดการบิดเบือน อย่างไรก็ตาม ความเร็วที่สูงเกินไปอาจทำให้วัสดุไม่สามารถหลอมรวมเข้าด้วยกันได้อย่างสมบูรณ์ ส่งผลให้ข้อต่อไม่แข็งแรง ความเร็วที่ต่ำลงทำให้สามารถเจาะลึกลงไปได้ แต่สามารถเพิ่มการสะสมความร้อนได้ ซึ่งอาจทำให้เกิดการบิดเบือนจากความร้อนได้
- ขนาดจุดโฟกัส: ขนาดจุดโฟกัสที่เล็กกว่าจะรวมพลังงานไว้ในพื้นที่เล็กๆ ทำให้สามารถเชื่อมได้ละเอียดและแคบ ขนาดจุดโฟกัสควรตรงกับความกว้างของรอยเชื่อม หากมีขนาดใหญ่เกินไป อาจทำให้เกิดความร้อนและการบิดเบือนมากเกินไป หากมีขนาดเล็กเกินไป อาจไม่สามารถเจาะลึกได้เพียงพอสำหรับวัสดุที่หนากว่า
- ความถี่พัลส์ (เลเซอร์พัลส์): สำหรับการใช้งานที่ต้องใช้เลเซอร์พัลส์ การปรับความถี่พัลส์จะช่วยควบคุมปริมาณพลังงานที่ส่งไปยังรอยเชื่อม ความถี่พัลส์ที่สูงขึ้นจะช่วยให้รอยเชื่อมมีความราบรื่นและต่อเนื่องมากขึ้น ในขณะที่ความถี่ที่ต่ำกว่าจะส่งพลังงานเป็นช่วงๆ ซึ่งมีประโยชน์สำหรับการใช้งานที่ต้องการความร้อนน้อยที่สุด
คุณสมบัติของวัสดุ
วัสดุที่ถูกเชื่อมส่งผลต่อการที่เลเซอร์ทำปฏิกิริยากับพื้นผิวและทะลุผ่านโลหะ ปัจจัยต่างๆ เช่น การสะท้อนแสง การนำความร้อน และองค์ประกอบของโลหะผสม ล้วนส่งผลต่อคุณภาพของการเชื่อม
- การสะท้อนแสง: วัสดุที่มีค่าการสะท้อนแสงสูง เช่น อะลูมิเนียมและทองแดง สามารถสะท้อนพลังงานเลเซอร์ได้ในปริมาณมาก ทำให้การดูดซับลดลง ความยาวคลื่นเลเซอร์ที่ต่ำลงหรือวัสดุสะท้อนแสงที่ผ่านการบำบัดเบื้องต้นสามารถช่วยเพิ่มการดูดซับและปรับปรุงคุณภาพของการเชื่อมได้
- การนำความร้อน: วัสดุที่มีการนำความร้อนสูง เช่น ทองแดง ระบายความร้อนได้อย่างรวดเร็ว ต้องใช้กำลังเลเซอร์ที่สูงขึ้นหรือปรับพารามิเตอร์เพื่อให้ได้การเจาะทะลุที่เหมาะสม วัสดุที่มีการนำความร้อนต่ำ เช่น ไททาเนียม จะกักเก็บความร้อนไว้ ทำให้เชื่อมได้ลึกขึ้นโดยใช้กำลังน้อยกว่า
- องค์ประกอบของโลหะผสม: โลหะผสมมักจะมีจุดหลอมเหลวที่แตกต่างกันและอาจต้องใช้การตั้งค่าเลเซอร์ที่แตกต่างกันเพื่อให้ได้การเชื่อมที่สม่ำเสมอ โลหะผสมบางชนิดยังทำให้เกิดการกระเซ็นมากขึ้นหรือต้องการความถี่พัลส์ที่แตกต่างกันเพื่อหลีกเลี่ยงการแตกร้าว โดยเฉพาะโลหะผสมที่มีองค์ประกอบที่สามารถระเหยได้ที่อุณหภูมิในการเชื่อม
- สภาพพื้นผิว: ความสะอาดและการตกแต่งพื้นผิวของวัสดุมีผลต่อการดูดซับลำแสงเลเซอร์ ออกไซด์ น้ำมัน หรือสิ่งปนเปื้อนบนพื้นผิวอาจขัดขวางกระบวนการเชื่อมและทำให้รอยเชื่อมอ่อนแอลง การทำความสะอาดหรือเตรียมพื้นผิวก่อนเชื่อมอาจช่วยปรับปรุงความสม่ำเสมอและความแข็งแรงของรอยเชื่อมได้
การออกแบบและประกอบข้อต่อ
การออกแบบข้อต่อและคุณภาพการประกอบมีผลอย่างมากต่อคุณภาพการเชื่อมขั้นสุดท้าย การออกแบบข้อต่อที่เหมาะสมและการประกอบที่แน่นหนาทำให้มั่นใจได้ว่าเลเซอร์สามารถหลอมรวมวัสดุได้อย่างแม่นยำโดยไม่มีช่องว่างหรือการจัดตำแหน่งที่ไม่ถูกต้อง
- การออกแบบข้อต่อ: ข้อต่อประเภทต่างๆ (เช่น ข้อต่อแบบชน ข้อต่อแบบทับ และข้อต่อแบบร่อง) ต้องใช้การตั้งค่าเลเซอร์และการโฟกัสเฉพาะเพื่อให้ได้ผลลัพธ์ที่ดีที่สุด ตัวอย่างเช่น ข้อต่อแบบชนอาจต้องเจาะลึกกว่า ในขณะที่ข้อต่อแบบทับอาจตื้นกว่าแต่ต้องควบคุมเพื่อหลีกเลี่ยงการกระจายความร้อนที่มากเกินไป
- ความแม่นยำในการติดตั้ง: การจัดตำแหน่งที่แม่นยำระหว่างชิ้นส่วนมีความสำคัญต่อคุณภาพการเชื่อมที่สม่ำเสมอ ช่องว่างหรือการจัดตำแหน่งที่ไม่ถูกต้องใดๆ อาจทำให้การเชื่อมหลอมรวมไม่สมบูรณ์ ทำให้เกิดจุดอ่อนในการเชื่อม การติดตั้งให้แน่นหนาจะช่วยให้พลังงานเลเซอร์ถูกดูดซับอย่างมีประสิทธิภาพทั่วรอยต่อ ช่วยลดโอกาสเกิดข้อบกพร่อง สำหรับการใช้งานที่ต้องการความคลาดเคลื่อนต่ำมาก อาจใช้ระบบการยึดและการติดตั้งเพื่อยึดชิ้นส่วนให้แน่นหนาในระหว่างการเชื่อม
- ความเข้ากันได้ของความหนา: ความหนาของรอยเชื่อมยังส่งผลต่อความแข็งแรงของรอยเชื่อมอีกด้วย เมื่อเชื่อมวัสดุที่มีความหนา จะต้องปรับพารามิเตอร์ของเลเซอร์ให้สามารถเจาะทะลุได้เต็มที่โดยไม่ทำให้วัสดุโดยรอบร้อนเกินไป ในทางตรงกันข้าม วัสดุที่บางจะต้องใช้การตั้งค่าพลังงานที่ต่ำกว่าเพื่อหลีกเลี่ยงการบิดงอหรือไหม้
ก๊าซป้องกัน
การใช้ก๊าซป้องกันจะช่วยปกป้องบริเวณเชื่อมจากการปนเปื้อนและการเกิดออกซิเดชัน ซึ่งอาจส่งผลกระทบต่อคุณภาพและรูปลักษณ์ของรอยเชื่อม การเลือกและการไหลของก๊าซป้องกันมีบทบาทสำคัญในการทำให้รอยเชื่อมมีคุณภาพสูง
- ประเภทของก๊าซ: ก๊าซป้องกันทั่วไป ได้แก่ อาร์กอน ฮีเลียม และไนโตรเจน อาร์กอนให้บรรยากาศที่เสถียรและใช้กันอย่างแพร่หลายกับโลหะหลายชนิด ฮีเลียมมักใช้ในการทะลุทะลวงลึกเนื่องจากมีความสามารถในการนำความร้อนสูง แต่มีราคาแพงกว่า ไนโตรเจนบางครั้งใช้ทำวัสดุเฉพาะ เช่น สเตนเลส แต่สามารถทำให้โลหะบางชนิดมีไนไตรด์ ซึ่งอาจส่งผลต่อความแข็งแรงได้
- อัตราการไหลของก๊าซ: อัตราการไหลของก๊าซป้องกันจะต้องปรับตามวัสดุและพารามิเตอร์การเชื่อม อัตราการไหลที่สูงเกินไปอาจรบกวนแอ่งเชื่อมและทำให้เกิดการปั่นป่วน ในขณะที่อัตราการไหลที่ต่ำเกินไปอาจไม่สามารถป้องกันรอยเชื่อมได้อย่างเต็มที่ ทำให้เกิดการออกซิเดชันและนำไปสู่การเปลี่ยนสีหรือรูพรุน
- วิธีการส่ง: สามารถส่งก๊าซป้องกันโดยตรงผ่านหัวฉีดใกล้หัวเลเซอร์หรือในบางกรณี สามารถส่งผ่านท่อก๊าซรองเพื่อให้ครอบคลุมมากขึ้น การส่งก๊าซที่เหมาะสมจะช่วยให้กระจายได้สม่ำเสมอ ช่วยปกป้องรอยเชื่อมจากการสัมผัสอากาศ และส่งเสริมให้รอยเชื่อมมีความสะอาดและสวยงาม

สรุป
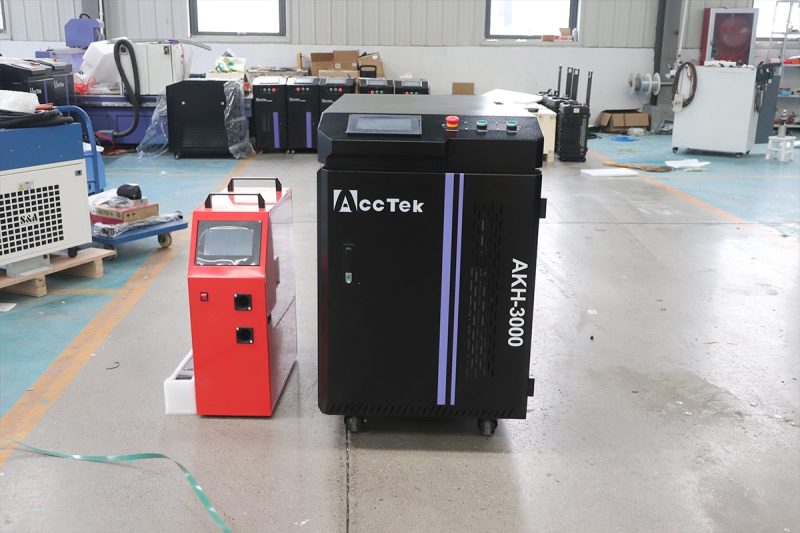
รับโซลูชั่นการเชื่อมด้วยเลเซอร์
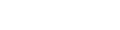
- [email protected]
- [email protected]
- +86-19963414011
- หมายเลข 3 โซน A เขตอุตสาหกรรม Luzhen เมือง Yucheng มณฑลซานตง