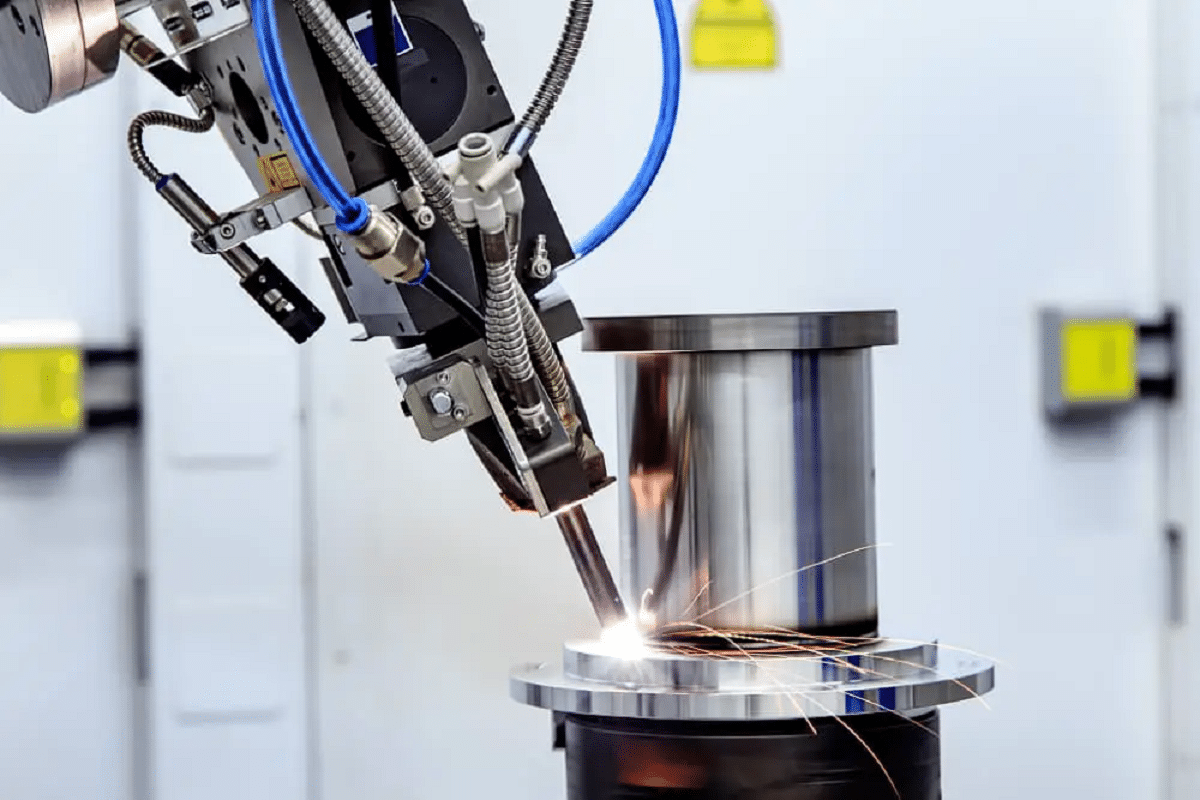
การเชื่อมด้วยเลเซอร์มีข้อบกพร่องอะไรบ้าง? วิธีแก้ปัญหา?
การเชื่อมด้วยเลเซอร์ถูกนำมาใช้กันอย่างแพร่หลายในอุตสาหกรรมต่างๆ เนื่องจากมีข้อดีคือมีประสิทธิภาพสูง ความแม่นยำสูง ให้ผลลัพธ์ที่ดี และบูรณาการระบบอัตโนมัติได้ง่าย มีบทบาทสำคัญในการผลิตทางอุตสาหกรรมและการผลิต รวมถึงการทหาร การแพทย์ การบินและอวกาศ พลังงานใหม่ และอุตสาหกรรมอื่นๆ อย่างไรก็ตาม วิธีการประมวลผลใดๆ หากไม่เข้าใจหลักการและกระบวนการอย่างถูกต้อง อาจก่อให้เกิดข้อบกพร่องหรือผลิตภัณฑ์ที่มีข้อบกพร่อง และการเชื่อมด้วยเลเซอร์ก็ไม่มีข้อยกเว้น เพื่อเพิ่มมูลค่าของการเชื่อมด้วยเลเซอร์ให้สูงสุดและผลิตผลิตภัณฑ์ที่มีคุณภาพพร้อมรูปลักษณ์ที่ไร้ที่ติ สิ่งสำคัญคือต้องเข้าใจข้อผิดพลาดเหล่านี้และเรียนรู้วิธีหลีกเลี่ยง
สารบัญ
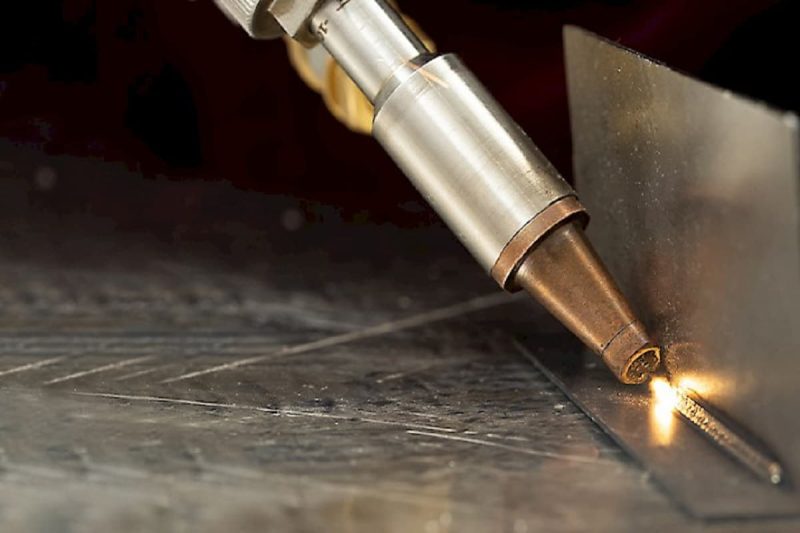
หลักการเชื่อมด้วยเลเซอร์
การเชื่อมด้วยเลเซอร์เป็นหนึ่งในการใช้งานที่สำคัญของเทคโนโลยีการประมวลผลวัสดุด้วยเลเซอร์ การเชื่อมด้วยเลเซอร์ทำงานในสองโหมดที่แตกต่างกันโดยพื้นฐาน: การเชื่อมแบบจำกัดการนำไฟฟ้าและการเชื่อมแบบรูลึก การนำความร้อนเกิดขึ้นระหว่างกระบวนการเชื่อม กล่าวคือ รังสีเลเซอร์จะทำให้พื้นผิวร้อนขึ้น และความร้อนที่พื้นผิวจะกระจายไปยังภายในผ่านการนำความร้อน โดยการควบคุมความกว้างของพัลส์เลเซอร์ พลังงาน กำลังสูงสุดและความถี่การเกิดซ้ำ การหลอมละลายขององค์ประกอบ และพารามิเตอร์อื่นๆ จะทำให้เกิดแอ่งน้ำที่หลอมละลายขึ้นบนพื้นผิวโลหะ ความร้อนจะละลายวัสดุเพื่อสร้างรอยเชื่อมระหว่างพื้นผิวทั้งสอง ทำให้การเชื่อมเสร็จสมบูรณ์
การเชื่อมด้วยเลเซอร์มีความแม่นยำในการเชื่อมและคุณภาพการเชื่อมสูง เนื่องจากตัวเลเซอร์สร้างความร้อนน้อยมาก รอยเชื่อมที่เกิดขึ้นหลังจากการเชื่อมด้วยเลเซอร์จึงมีขนาดค่อนข้างเล็กเช่นกัน ซึ่งทำให้การเชื่อมด้วยเลเซอร์เหมาะอย่างยิ่งสำหรับวัสดุที่บางกว่า เช่น อุปกรณ์อิเล็กทรอนิกส์หรือซีลแก้ว/โลหะ ในขณะที่เชื่อมวัสดุที่หนาขึ้น จะเกิดรอยเชื่อมที่แคบและลึกขึ้นระหว่างชิ้นส่วนที่มีขอบสี่เหลี่ยม นอกจากนี้ เลเซอร์ยังสามารถเข้าถึงอุณหภูมิสูงอย่างเหลือเชื่อ (หลายพันองศาเซลเซียส) ดังนั้นจึงสามารถสร้างรอยเชื่อมที่แข็งแรงและทนทานซึ่งสามารถทนต่ออุณหภูมิที่รุนแรงและสภาพแวดล้อมที่เลวร้ายได้
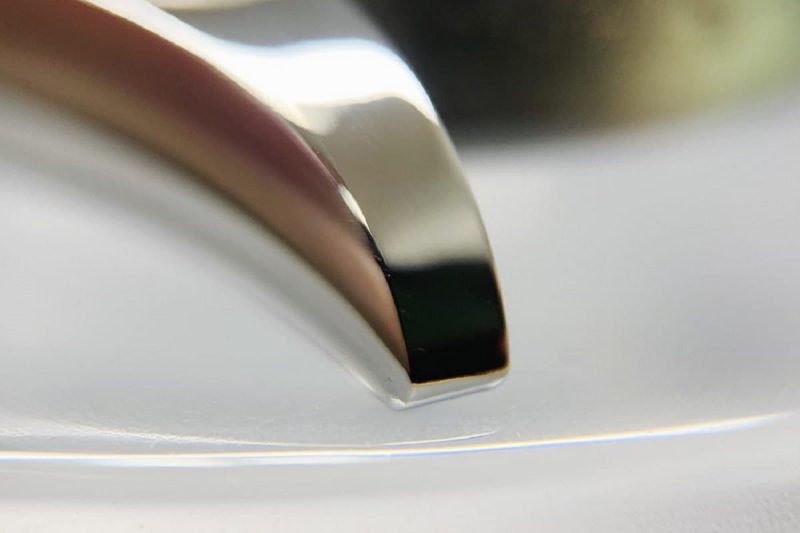
ข้อบกพร่องในการเชื่อมทั่วไปในการเชื่อมด้วยเลเซอร์และวิธีแก้ไข
การเชื่อมด้วยเลเซอร์มีข้อได้เปรียบในด้านประสิทธิภาพสูง ความแม่นยำสูง ผลดี ระบบอัตโนมัติที่ง่าย การผสานรวม ฯลฯ แต่การทำงานที่ไม่เหมาะสมอาจนำไปสู่ข้อบกพร่องด้านคุณภาพอย่างร้ายแรงในผลิตภัณฑ์ การทำความเข้าใจข้อบกพร่องเหล่านี้อย่างดีเท่านั้นจึงจะสามารถนำคุณค่าของการเชื่อมด้วยเลเซอร์มาใช้ได้อย่างเต็มที่ และผลิตภัณฑ์ที่มีรูปลักษณ์สวยงามและคุณภาพสูงสามารถแปรรูปได้ ต่อไปนี้คือข้อบกพร่องในการเชื่อม 8 ประการที่มักเกิดขึ้นในการเชื่อมด้วยเลเซอร์
ความพรุน
รูพรุนเป็นหนึ่งในข้อบกพร่องที่มักเกิดขึ้นในการเชื่อมด้วยเลเซอร์ รูพรุนในการเชื่อมด้วยเลเซอร์อาจเกิดจากการปนเปื้อนของบอร์ดหรือพื้นผิว หรือการทำความสะอาดล่วงหน้าไม่เพียงพอ เช่น จาระบี น้ำมัน ออกไซด์ ไอน้ำที่ดูดซับ ของเหลวในการตัดที่ตกค้าง ฯลฯ สระเชื่อมเลเซอร์ลึกและแคบ และความเร็วในการระบายความร้อน รวดเร็ว ก๊าซที่สร้างขึ้นในสระหลอมเหลวไม่มีเวลาที่จะหลบหนีเนื่องจากมลภาวะที่พื้นผิว และง่ายต่อการสร้างรูพรุน อย่างไรก็ตาม การเชื่อมด้วยเลเซอร์จะเย็นลงอย่างรวดเร็ว และรูพรุนที่เกิดขึ้นโดยทั่วไปจะมีขนาดเล็กกว่าการเชื่อมแบบฟิวชันแบบดั้งเดิม
เพื่อหลีกเลี่ยงการเกิดรูพรุนในการเชื่อมด้วยเลเซอร์:
- ตรวจสอบให้แน่ใจว่ามีก๊าซป้องกันที่เหมาะสม: ใช้ก๊าซป้องกันคุณภาพสูง (โดยปกติจะเป็นส่วนผสมของอาร์กอนหรือฮีเลียม) เพื่อให้มีการป้องกันที่เพียงพอจากก๊าซในชั้นบรรยากาศ
- เพิ่มประสิทธิภาพการไหลของก๊าซ: ตั้งค่าการไหลของก๊าซป้องกันที่เหมาะสมและทิศทาง เพื่อป้องกันพื้นที่เชื่อมในระดับสูงสุดอย่างมีประสิทธิภาพ
- ทำความสะอาดพื้นผิวของชิ้นงาน: ทำความสะอาดพื้นผิวที่จะเชื่อมให้ทั่วถึงเพื่อขจัดสิ่งปนเปื้อนใดๆ เช่น น้ำมัน จาระบี สนิม หรือสิ่งสกปรก เพื่อป้องกันการกักเก็บก๊าซ ใช้วิธีการทำความสะอาดที่เหมาะสม เช่น การทำความสะอาดด้วยตัวทำละลาย การทำความสะอาดเชิงกล หรือการทำความสะอาดด้วยสารเคมีตามต้องการ
- การเตรียมข้อต่อที่เหมาะสม: ตรวจสอบให้แน่ใจว่าข้อต่อเหมาะสมและจัดตำแหน่งเพื่อหลีกเลี่ยงการสร้างช่องว่างที่ก๊าซอาจติดอยู่ หากทำได้ ให้ใช้เทคนิคการไล่กลับเพื่อป้องกันการกักเก็บก๊าซ
ตัดราคา
อันเดอร์คัตคือร่องหรือร่องที่เกิดขึ้นที่ขอบของรอยเชื่อม มักเกิดจากความร้อนหรือความเร็วในการเชื่อมมากเกินไป เมื่อความเร็วในการเชื่อมเร็วเกินไป โลหะเหลวที่อยู่ด้านหลังรูเล็กๆ ตรงกลางรอยเชื่อมจะไม่มีเวลากระจายตัว และมันจะแข็งตัวบนรอยเชื่อมทั้งสองด้านเพื่อสร้างรอยตัดด้านล่าง
เพื่อหลีกเลี่ยงรอยตัดด้านล่างในการเชื่อมด้วยเลเซอร์:
- การปรับพารามิเตอร์เลเซอร์ให้เหมาะสม: ปรับพลังงานเลเซอร์ ระยะเวลาของพัลส์ และตำแหน่งโฟกัสเพื่อให้ได้ความร้อนที่เหมาะสม หลีกเลี่ยงการใช้กำลังไฟสูงเกินไปหรือการเชื่อมเร็วเกินไป เนื่องจากอาจทำให้เกิดความร้อนสูงเกินและการตัดต่ำเกินไป
- รักษาความเร็วในการเชื่อมให้สม่ำเสมอ: ควบคุมการเคลื่อนที่ของลำแสงเลเซอร์หรือชิ้นงานเพื่อรักษาความเร็วในการเคลื่อนที่ให้คงที่ การเปลี่ยนแปลงความเร็วอย่างรวดเร็วอาจทำให้การกระจายความร้อนไม่สม่ำเสมอและเกิดรอยตัดด้านล่าง
- การออกแบบข้อต่อที่เหมาะสมและความพอดี: ตรวจสอบให้แน่ใจว่ามีการเตรียมข้อต่อที่เหมาะสม รวมถึงความพอดีที่ถูกต้อง มุมเอียงที่เหมาะสม และความทนทานต่อช่องว่างที่เหมาะสม การรักษาความพอดีช่วยป้องกันไม่ให้ขอบละลายมากเกินไปและลดการตัดราคา
รอยร้าวจากการเชื่อม
รอยร้าวร้อนจากการเชื่อมหมายถึงรอยร้าวที่เกิดขึ้นในบริเวณที่มีอุณหภูมิสูงเมื่อโลหะในบริเวณรอยเชื่อมและบริเวณที่ได้รับผลกระทบจากความร้อนเย็นลงจนใกล้กับเส้นโซลิดัสในระหว่างกระบวนการเชื่อม โดยทั่วไปสามารถแบ่งออกเป็นรอยแตกที่อุณหภูมิสูงและรอยแตกที่อุณหภูมิต่ำ ในระหว่างกระบวนการเชื่อมด้วยเลเซอร์ เนื่องจากการป้อนความร้อนเพียงเล็กน้อยของเลเซอร์ การเสียรูปหลังการเชื่อมจึงมีขนาดเล็ก และความเค้นที่เกิดจากการเชื่อมก็น้อยเช่นกัน ดังนั้นโดยทั่วไปแล้วรอยร้าวที่อุณหภูมิสูงจะไม่เกิดขึ้น อย่างไรก็ตาม เนื่องจากวัสดุที่แตกต่างกันและการเลือกพารามิเตอร์กระบวนการที่ไม่เหมาะสม รอยแตกที่อุณหภูมิสูงจะปรากฏในรูปแบบของข้อบกพร่อง
เพื่อหลีกเลี่ยงรอยเชื่อม:
- ควบคุมความร้อนเข้า: ปรับพารามิเตอร์เลเซอร์ให้เหมาะสมเพื่อควบคุมความร้อนเข้าและลดความเครียดจากความร้อน หลีกเลี่ยงการสะสมความร้อนมากเกินไปและอัตราการเย็นตัวอย่างรวดเร็ว ซึ่งอาจส่งผลให้เกิดการแตกร้าว สามารถทำได้โดยการปรับกำลังเลเซอร์และระยะเวลาของพัลส์หรือใช้เทคนิคการสร้างพัลส์
- การให้ความร้อนก่อนการเชื่อมและหลังการเชื่อม: การอุ่นชิ้นงานก่อนการเชื่อมช่วยลดการไล่ระดับความร้อนและความเค้นและปรับปรุงความสามารถในการเชื่อม เทคนิคการอบชุบด้วยความร้อนหลังการเชื่อม เช่น การหลอมหรือการคลายความเค้นสามารถใช้เพื่อลดความเค้นตกค้าง เพิ่มคุณสมบัติเชิงกล และลดความเสี่ยงของการแตกร้าว
- การเลือกวัสดุอุด: ใช้วัสดุอุดที่มีองค์ประกอบและความเหนียวที่เหมาะสมเพื่อให้ตรงกับวัสดุฐานเพื่อลดความเสี่ยงของการแตกร้าว
ฟิวชั่นไม่สมบูรณ์หรือขาดการเจาะ
ฟิวชั่นที่ไม่สมบูรณ์หรือการแทรกซึมที่ไม่สมบูรณ์เกิดขึ้นเมื่อโลหะเชื่อมไม่หลอมรวมกับไม้หรือทะลุความหนาเต็มของรอยต่อ
เพื่อหลีกเลี่ยงการหลอมรวมที่ไม่สมบูรณ์หรือไม่ทะลุทะลวง:
- ปรับพารามิเตอร์เลเซอร์ให้เหมาะสม: ปรับกำลังเลเซอร์ ระยะเวลาของพัลส์ และตำแหน่งโฟกัสเพื่อให้ได้การหลอมรวมวัสดุและการแทรกซึมที่เหมาะสม การตั้งค่าพลังงานที่สูงขึ้นหรือการปรับตำแหน่งโฟกัสสามารถช่วยให้เจาะลึกได้มากขึ้น
- การเตรียมข้อต่อและการประกอบ: ตรวจสอบให้แน่ใจว่าการออกแบบและการประกอบข้อต่อถูกต้อง ควรเลือกมุมร่อง ความคลาดเคลื่อนของช่องว่าง และเทคนิคการเตรียมข้อต่อเพื่อส่งเสริมการหลอมรวมและการเจาะที่เหมาะสม
- ปรับความเร็วการเชื่อม: ปรับความเร็วการเชื่อมเพื่อให้ความร้อนเข้าเพียงพอและการแทรกซึมเข้าไปในรอยต่อ การปรับความเร็วในการเชื่อมให้เหมาะสมทำให้มั่นใจได้ว่าพลังงานเลเซอร์จะทำปฏิกิริยากับวัสดุอย่างเต็มที่
สาด
สะเก็ดที่เกิดจากการเชื่อมด้วยเลเซอร์อาจส่งผลกระทบร้ายแรงต่อคุณภาพพื้นผิวของรอยเชื่อม หลังจากการเชื่อม อนุภาคโลหะจำนวนมากอาจปรากฏขึ้นบนพื้นผิวของชิ้นงานหรือวัสดุ ซึ่งไม่เพียงส่งผลต่อรูปลักษณ์เท่านั้น แต่ยังส่งผลต่อการใช้งานด้วย เมื่อละอองน้ำกระเด็นรุนแรง ก็จะก่อให้เกิดมลพิษและทำให้เลนส์เสียหายด้วย
เพื่อหลีกเลี่ยงการกระเด็นในการเชื่อมด้วยเลเซอร์:
- ปรับโฟกัสและตำแหน่งของลำแสงเลเซอร์ให้เหมาะสม: ปรับตำแหน่งและรูปร่างของลำแสงเลเซอร์ให้เหมาะสมเพื่อให้ได้การเชื่อมที่มั่นคงและแม่นยำ หลีกเลี่ยงการวางแนวหรือโฟกัสที่ไม่แน่นอนของลำแสงเลเซอร์ ซึ่งอาจทำให้เกิดการกระเด็น
- ใช้ก๊าซป้องกันและอัตราการไหลที่เหมาะสม: เลือกองค์ประกอบของก๊าซป้องกันและอัตราการไหลที่เหมาะสมเพื่อให้การป้องกันเพียงพอ ก๊าซป้องกันช่วยป้องกันการเกิดออกซิเดชันและการปนเปื้อนของบ่อเชื่อมและลดการกระเด็น จำเป็นต้องปรับการไหลของแก๊สตามความต้องการในการเชื่อม
- ทำความสะอาดพื้นผิวของชิ้นงาน: ทำความสะอาดพื้นผิวของชิ้นงานอย่างทั่วถึงและขจัดสิ่งปนเปื้อนที่อาจก่อให้เกิดการกระเด็น
การเสียรูป
การเสียรูปหมายถึงการเสียรูปหรือการบิดงอของโครงสร้างหรือชิ้นงานที่เชื่อมเนื่องจากกระบวนการเชื่อม
เพื่อหลีกเลี่ยงการเสียรูปในการเชื่อมด้วยเลเซอร์:
- ใช้เทคนิคการตรึงและการหนีบที่ถูกต้อง: ยึดชิ้นงานหรือโครงสร้างเพื่อลดการเคลื่อนไหวหรือการเสียรูประหว่างการเชื่อม การสนับสนุนและการจัดตำแหน่งชิ้นงานที่เพียงพอช่วยรักษาเสถียรภาพของมิติ
- การอุ่นชิ้นงาน: พิจารณาการอุ่นชิ้นงานเพื่อลดการไล่ระดับความร้อนและลดการบิดเบือน
- การทำความเย็นแบบควบคุม: ใช้เทคนิคการระบายความร้อนแบบควบคุม เช่น การใช้ฮีตซิงก์หรือฟิกซ์เจอร์ เพื่อควบคุมอัตราการทำความเย็นและลดการไล่ระดับความร้อนให้เหลือน้อยที่สุด
ปัญหาโซนได้รับผลกระทบจากความร้อน (HAZ)
การเชื่อมด้วยเลเซอร์จะสร้างโซนที่ได้รับความร้อนที่มีความเข้มข้นสูงรอบๆ แนวเชื่อม โซนที่ได้รับผลกระทบจากความร้อนจะมีการหมุนเวียนความร้อนและการเปลี่ยนแปลงโครงสร้างจุลภาค ซึ่งอาจส่งผลให้ความแข็งแรงลดลงและความแข็งของวัสดุเปลี่ยนไป
เพื่อหลีกเลี่ยงปัญหา HAZ:
- การปรับพารามิเตอร์เลเซอร์ให้เหมาะสม: ปรับพารามิเตอร์เลเซอร์เพื่อลดขนาดและความลึกของโซนที่ได้รับผลกระทบจากความร้อน ซึ่งรวมถึงการควบคุมพลังงานเลเซอร์ ระยะเวลาของพัลส์ และการโฟกัสของลำแสง
- การใช้เทคนิคการกวาดหรือสั่น: การใช้เทคนิคการกวาดหรือการสั่นช่วยให้กระจายความร้อนได้ทั่วถึงยิ่งขึ้น และลดความเข้มข้นของความร้อนในพื้นที่เฉพาะ จึงช่วยลดปัญหาที่เกี่ยวข้องกับโซนที่ได้รับผลกระทบจากความร้อน
- ดำเนินการบำบัดความร้อนหลังการเชื่อม: ใช้กระบวนการบำบัดความร้อนหลังการเชื่อมที่เหมาะสม เช่น การหลอมหรือการคลายความเครียด เพื่อปรับแต่งโครงสร้างจุลภาคและลดปัญหาที่เกี่ยวข้องกับโซนที่ได้รับผลกระทบจากความร้อน การรักษาความร้อนช่วยฟื้นฟูคุณสมบัติของวัสดุในบริเวณที่ได้รับผลกระทบจากความร้อน
รอยเชื่อมยุบ
การพังทลายของแนวเชื่อมด้วยเลเซอร์หมายถึงการเสียรูปด้านในหรือการยุบตัวของรอยเชื่อมในระหว่างกระบวนการเชื่อม สิ่งนี้สามารถเกิดขึ้นได้จากหลายสาเหตุ เช่น กำลังเลเซอร์สูงเกินไป การควบคุมบ่อหลอมเหลวไม่เพียงพอ การรองรับวัสดุไม่เพียงพอ การประกอบข้อต่อที่ไม่เหมาะสม การจัดการความร้อนที่ไม่ดี ปัญหาการเลือกวัสดุ และการขาดการตรวจสอบและควบคุมกระบวนการ
เพื่อหลีกเลี่ยงการพังทลายของรอยเชื่อม:
- ปรับพารามิเตอร์เลเซอร์ให้เหมาะสม: ลดพลังงานเลเซอร์หรือความหนาแน่นของพลังงานเพื่อป้องกันการหลอมเหลวมากเกินไปของวัสดุโดยรอบ ปรับกำลังเลเซอร์ ระยะเวลาของพัลส์ และรูปร่างของลำแสงเพื่อให้เกิดความสมดุลระหว่างการเจาะทะลุและหลีกเลี่ยงการหลอมละลายมากเกินไปที่อาจนำไปสู่การยุบตัว
- การสนับสนุนวัสดุที่เหมาะสม: ให้การสนับสนุนวัสดุที่เหมาะสมระหว่างการเชื่อมโดยใช้ฟิกซ์เจอร์ จิ๊ก หรือแคลมป์เพื่อยึดชิ้นงานให้อยู่กับที่และให้ความมั่นคง พิจารณาใช้แท่งรองรับหรือแผ่นระบายความร้อนเพื่อกระจายความร้อนและให้การสนับสนุนเพิ่มเติมสำหรับข้อต่อ
- ตรวจสอบการประกอบข้อต่อที่เหมาะสม: การประกอบข้อต่อที่เหมาะสมช่วยป้องกันการยุบตัว ตรวจสอบให้แน่ใจว่าได้เตรียมพื้นผิวการผสมพันธุ์และจัดตำแหน่งอย่างถูกต้องก่อนทำการเชื่อม เพิ่มความแข็งแรงและความมั่นคงของข้อต่อโดยใช้การออกแบบข้อต่อที่เหมาะสมและเทคนิคการเตรียมขอบ
- จัดการอินพุตความร้อน: ควบคุมอินพุตความร้อนและจัดการรอบความร้อนอย่างเหมาะสม ปรับกลยุทธ์การสแกนหรือการเคลื่อนไหวให้เหมาะสมเพื่อกระจายความร้อนอย่างสม่ำเสมอและหลีกเลี่ยงความร้อนสูงเกินไปเฉพาะที่ ใช้เทคนิคการอุ่นหรือควบคุมความเย็นเพื่อลดการไล่ระดับความร้อนและลดความเสี่ยงของการพังทลาย
- การเลือกวัสดุและความเข้ากันได้: เลือกวัสดุที่เหมาะสมและพารามิเตอร์การเชื่อมที่เข้ากันได้ พิจารณาคุณสมบัติของวัสดุ เช่น การนำความร้อนและจุดหลอมเหลวเพื่อให้แน่ใจว่ามีการถ่ายเทความร้อนที่เหมาะสมและป้องกันการหลอมเหลวที่มากเกินไป
- การตรวจสอบและควบคุมกระบวนการ: ใช้ระบบตรวจสอบและควบคุมกระบวนการตามเวลาจริงเพื่อตรวจจับสัญญาณของการพังทลายหรือการเบี่ยงเบนจากพารามิเตอร์การเชื่อมที่ต้องการ ใช้กลไกป้อนกลับระหว่างการเชื่อมเพื่อปรับพารามิเตอร์เลเซอร์ ความเร็วในการสแกน หรือการรองรับวัสดุ นำเทคโนโลยีขั้นสูงมาใช้ เช่น ระบบควบคุมแบบปรับได้หรือการควบคุมป้อนกลับแบบวงปิดเพื่อให้ได้สภาวะการเชื่อมที่สม่ำเสมอและเสถียร
- ตรวจสอบการควบคุมบ่อหลอมละลายที่เหมาะสม: ควบคุมขนาดและรูปร่างของบ่อหลอมโดยการปรับพารามิเตอร์เลเซอร์และความเร็วในการสแกน ใช้เทคนิคการเชื่อมที่เหมาะสม เช่น การเชื่อมแบบรูกุญแจหรือการเชื่อมแบบโหมดการนำไฟฟ้า เพื่อให้แน่ใจว่าการก่อตัวของบ่อเชื่อมที่มั่นคงและควบคุมได้
สรุป
แน่นอน ข้อบกพร่องอื่น ๆ อาจเกี่ยวข้องกับการเชื่อมด้วยเลเซอร์ นอกจากปัญหาทางเทคนิคในการปฏิบัติงานแล้ว ข้อบกพร่องบางอย่างอาจนำไปสู่การเปลี่ยนแปลงคุณสมบัติของวัสดุได้ การทำความเข้าใจข้อบกพร่องที่อาจเกิดขึ้นในกระบวนการเชื่อมด้วยเลเซอร์และสาเหตุของข้อบกพร่องต่างๆ ให้ถูกต้องเท่านั้น เราจึงจะสามารถแก้ปัญหาการเชื่อมที่ผิดปกติในลักษณะที่ตรงเป้าหมายมากขึ้นได้
AccTek Laser มีหลากหลายประเภท เครื่องเชื่อมเลเซอร์รวมถึงการพกพา การทำความสะอาด และการเชื่อม เครื่องเชื่อมเลเซอร์ 3-in-1เหมาะสำหรับการเชื่อมแผ่นโลหะและท่อของคุณ หากคุณกำลังมองหาเครื่องจักรสำหรับงานพิเศษ แอคเทค เลเซอร์ นอกจากนี้ยังสามารถติดตั้งส่วนประกอบที่เหมาะสมเพื่อให้ได้โซลูชันที่ปรับแต่งตามความต้องการของลูกค้า
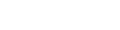
ข้อมูลติดต่อ
- [email protected]
- [email protected]
- +86-19963414011
- หมายเลข 3 โซน A เขตอุตสาหกรรม Luzhen เมือง Yucheng มณฑลซานตง
รับโซลูชันเลเซอร์