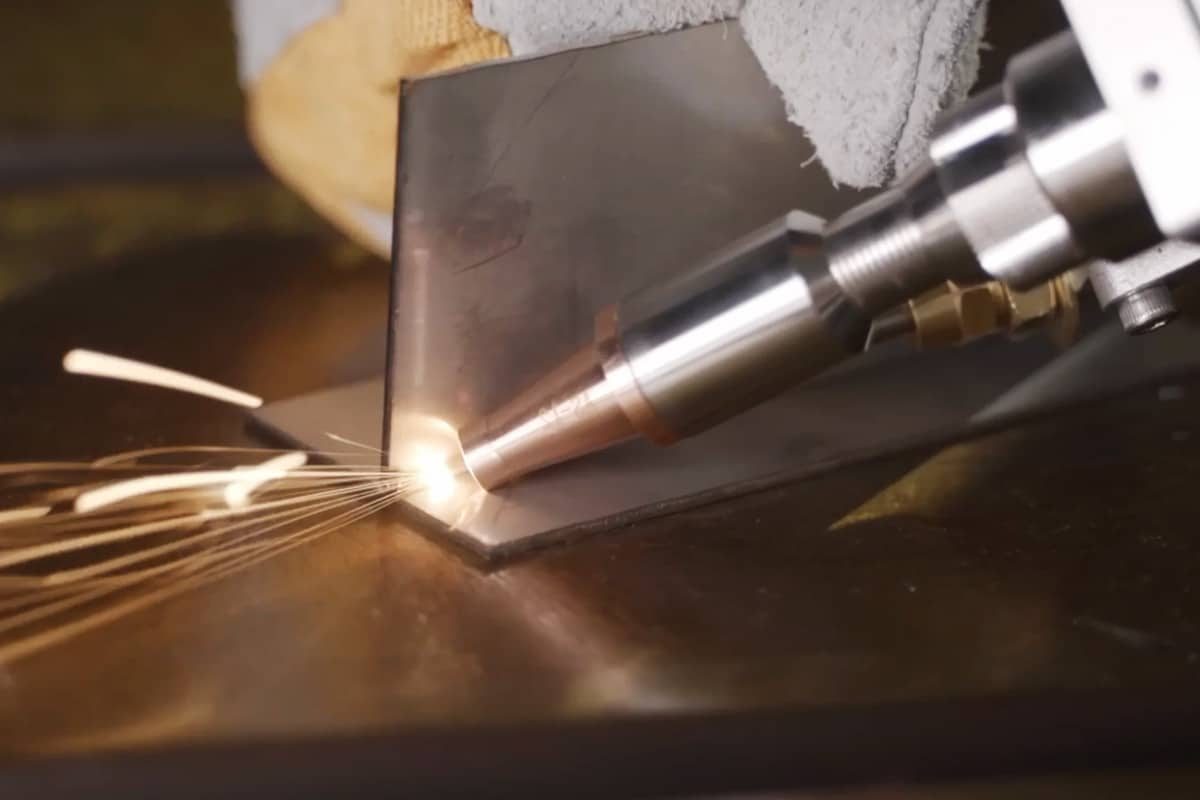
การออกแบบข้อต่อเชื่อมด้วยเลเซอร์
การเชื่อมด้วยเลเซอร์ได้รับการใช้กันอย่างแพร่หลายในอุตสาหกรรมการบินและอวกาศ การผลิตยานยนต์ อุปกรณ์อิเล็กทรอนิกส์ อุปกรณ์ทางการแพทย์ และอุตสาหกรรมอื่นๆ เนื่องจากมีความแม่นยำสูง ปริมาณความร้อนต่ำ และประสิทธิภาพสูง เมื่อเปรียบเทียบกับวิธีการเชื่อมแบบดั้งเดิม การเชื่อมด้วยเลเซอร์มีข้อได้เปรียบคือมีรอยเชื่อมแคบ ความเร็วในการเชื่อมเร็ว พื้นที่ที่ได้รับผลกระทบจากความร้อนน้อย และการเสียรูปต่ำ ทำให้เป็นตัวเลือกที่เหมาะสำหรับสาขาการผลิตที่มีความต้องการสูง อย่างไรก็ตาม แม้ว่าการเชื่อมด้วยเลเซอร์จะมีข้อดีหลายประการ แต่ความเสถียรของคุณภาพการเชื่อมและความน่าเชื่อถือของผลิตภัณฑ์ขั้นสุดท้ายยังคงขึ้นอยู่กับการออกแบบรอยเชื่อมเป็นอย่างมาก การออกแบบรอยเชื่อมที่เหมาะสมสามารถรับประกันความสมบูรณ์และความแข็งแรงเชิงกลของรอยเชื่อม และลดข้อบกพร่อง เช่น รอยแตก รูพรุน และรอยเชื่อมทะลุที่อาจเกิดขึ้นระหว่างกระบวนการเชื่อม ขณะเดียวกันก็เพิ่มประสิทธิภาพในการป้อนพลังงาน ปรับปรุงประสิทธิภาพการผลิต และลดอัตราการทำซ้ำและต้นทุนการผลิต
ในงานเชื่อมเลเซอร์ การออกแบบข้อต่อต้องพิจารณาปัจจัยหลายประการ รวมถึงคุณสมบัติทางโลหะวิทยาของพื้นผิว วิธีการเชื่อม กำลังของเลเซอร์ รูปร่างของรอยเชื่อม ความแม่นยำในการประกอบ และข้อกำหนดในการประมวลผลที่ตามมา การออกแบบข้อต่อที่ดีเยี่ยมสามารถใช้ประโยชน์จากการเชื่อมเลเซอร์ได้อย่างเต็มที่เพื่อให้ได้ผลลัพธ์การเชื่อมที่มีคุณภาพสูงและต้นทุนต่ำ บทความนี้จะสำรวจหลักการพื้นฐาน ปัจจัยที่มีอิทธิพล และกลยุทธ์การปรับให้เหมาะสมของการออกแบบข้อต่อการเชื่อมเลเซอร์อย่างละเอียด เพื่อช่วยให้บริษัทและวิศวกรปรับปรุงคุณภาพการเชื่อม เพิ่มประสิทธิภาพกระบวนการผลิต และยืดอายุการใช้งานของโครงสร้างที่เชื่อมในการใช้งานจริง
สารบัญ
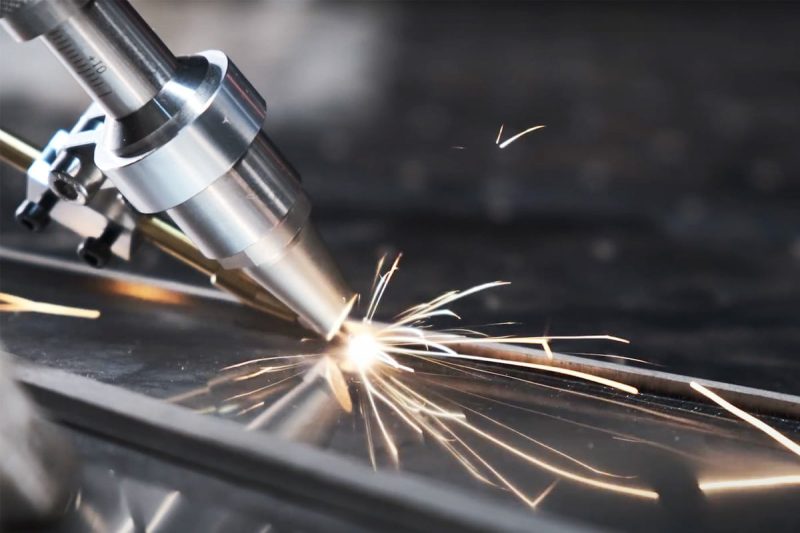
หลักการพื้นฐานในการออกแบบข้อต่อเชื่อมเลเซอร์
การเชื่อมด้วยเลเซอร์เป็นกระบวนการเชื่อมที่มีความแม่นยำสูงและมีประสิทธิภาพสูง ซึ่งใช้กันอย่างแพร่หลายในอุตสาหกรรมต่างๆ เช่น การผลิตยานยนต์ อวกาศ อุปกรณ์อิเล็กทรอนิกส์ และอุปกรณ์ทางการแพทย์ การออกแบบรอยเชื่อมที่เหมาะสมมีความสำคัญต่อความสมบูรณ์ ความแข็งแรง และประสิทธิภาพการผลิตของรอยเชื่อม การออกแบบรอยเชื่อมที่เหมาะสมไม่เพียงแต่จะช่วยลดข้อบกพร่องในการเชื่อมและปรับปรุงคุณภาพการเชื่อมเท่านั้น แต่ยังช่วยลดต้นทุนการผลิตและปรับปรุงประสิทธิภาพการผลิตโดยรวมอีกด้วย บทความนี้จะกล่าวถึงส่วนประกอบสำคัญของรอยเชื่อมด้วยเลเซอร์และบทบาทของส่วนประกอบเหล่านี้ในการปรับปรุงคุณภาพการเชื่อม และวิเคราะห์วิธีการบรรลุผลการเชื่อมที่มีประสิทธิภาพและเสถียรผ่านการออกแบบทางวิทยาศาสตร์
ส่วนประกอบสำคัญของข้อต่อเชื่อมด้วยเลเซอร์
พื้นผิว
การเลือกวัสดุฐานส่งผลโดยตรงต่อคุณภาพของการเชื่อมและประสิทธิภาพของผลิตภัณฑ์ขั้นสุดท้าย เมื่อเลือกวัสดุเชื่อม มีปัจจัยสำคัญหลายประการที่ต้องพิจารณา:
- คุณสมบัติทางกล: ความแข็งแกร่ง ความแข็ง ความเหนียว และคุณสมบัติอื่น ๆ ของวัสดุจะส่งผลกระทบต่อเสถียรภาพของข้อต่อที่เชื่อม
- คุณสมบัติทางโลหะวิทยา: รวมถึงองค์ประกอบของโลหะผสม ความเข้ากันได้ และการเปลี่ยนแปลงโครงสร้างจุลภาคหลังการเชื่อมของวัสดุเพื่อให้แน่ใจถึงความน่าเชื่อถือของรอยเชื่อม
- การนำความร้อนและอุณหภูมิการหลอมเหลว: ส่งผลต่อการดูดซับและการถ่ายโอนพลังงานเลเซอร์ วัสดุที่มีการนำความร้อนสูง (เช่น ทองแดง) อาจต้องใช้เครื่องกำเนิดเลเซอร์ที่มีกำลังสูงกว่า ในขณะที่วัสดุที่มีการนำความร้อนต่ำ (เช่น ไททาเนียม) ควรหลีกเลี่ยงความเสียหายของโครงสร้างที่เกิดจากความร้อนสูงเกินไป
การกำหนดค่าตัวเชื่อมต่อ
ข้อต่อประเภทต่างๆ เหมาะกับความต้องการในการเชื่อมที่แตกต่างกัน ข้อต่อประเภททั่วไป ได้แก่:
- ข้อต่อแบบชน: เหมาะสำหรับการเชื่อมที่มีความแข็งแรงสูง โดยมีประสิทธิภาพการเชื่อมที่ยอดเยี่ยม แต่ต้องการความแม่นยำในการประมวลผลสูง
- การเชื่อมแบบซ้อน: เหมาะสำหรับการเชื่อมแผ่นบาง กระบวนการเรียบง่าย และความเร็วในการเชื่อมที่รวดเร็ว แต่ควรใส่ใจกับการลดความเข้มข้นของความเค้น
- ข้อต่อแบบ T: นิยมใช้ในการเชื่อมโครงสร้าง โดยมีความสามารถในการรับน้ำหนักรอยเชื่อมได้ดี แต่จำเป็นต้องแน่ใจว่ามีการเจาะทะลุที่เพียงพอเพื่อหลีกเลี่ยงข้อบกพร่องในการเชื่อม
นอกจากนี้ ในระหว่างกระบวนการเชื่อม ขนาดช่องว่าง ความแม่นยำในการประกอบ และการจัดตำแหน่งของรอยเชื่อมจะส่งผลโดยตรงต่อคุณภาพของรอยเชื่อม การปรับพารามิเตอร์เหล่านี้ให้เหมาะสมสามารถลดการเสียรูปจากการเชื่อมและปรับปรุงความแข็งแรงของรอยเชื่อมได้
วัสดุอุด
ในงานเชื่อมเลเซอร์บางประเภท สามารถใช้สารตัวเติมเพื่อเพิ่มประสิทธิภาพคุณภาพการเชื่อมได้ ผลลัพธ์หลักๆ ได้แก่:
- เพิ่มความแข็งแรงในการเชื่อม ป้องกันรอยแตกร้าวจากการเชื่อม และปรับปรุงคุณสมบัติเชิงกลของรอยเชื่อม
- ปรับคุณสมบัติทางโลหะวิทยาและปรับปรุงโครงสร้างการเชื่อมโดยการเพิ่มองค์ประกอบของโลหะผสมให้เหมาะสม
- ลดข้อบกพร่องในการเชื่อม เช่น รูพรุนและการขาดการหลอมรวม และปรับปรุงเสถียรภาพในการเชื่อม
การเลือกใช้วัสดุเติมควรตรงกับคุณลักษณะของวัสดุฐาน และควรมีการดัดแปลงอย่างเหมาะสมร่วมกับกระบวนการเชื่อม
ส่วนประกอบสำคัญของข้อต่อเชื่อมด้วยเลเซอร์
การออกแบบรอยเชื่อมที่เหมาะสมที่สุดจะต้องบรรลุวัตถุประสงค์ต่อไปนี้พร้อมๆ กัน:
- รับประกันความสมบูรณ์และความแข็งแรงของรอยเชื่อม: ออกแบบโครงสร้างรอยเชื่อมอย่างมีเหตุผลเพื่อให้แน่ใจว่ามีการหลอมรวมที่ดีและมีความแข็งแรงเชิงกลเพียงพอในพื้นที่เชื่อม
- ลดข้อบกพร่องในการเชื่อม: ลดปัญหาทั่วไป เช่น รูพรุน รอยแตกร้าว และการขาดการหลอมรวม โดยการปรับปรุงการเลือกใช้วัสดุ โครงสร้างข้อต่อ และกระบวนการเชื่อมให้เหมาะสม
- เพิ่มประสิทธิภาพและผลผลิตของกระบวนการ: ออกแบบการกำหนดค่าข้อต่อที่เหมาะสมเพื่อเพิ่มความเร็วในการเชื่อม ลดของเสียจากวัสดุ และลดต้นทุนการประมวลผล จึงปรับปรุงประสิทธิภาพการผลิตโดยรวมให้ดีขึ้น
การออกแบบรอยเชื่อมเลเซอร์มีความสำคัญต่อคุณภาพการเชื่อมและประสิทธิภาพการผลิต โดยการเลือกวัสดุฐานอย่างมีเหตุผล การปรับโครงสร้างรอยเชื่อมและวัสดุอุดให้เหมาะสม และการปรับแต่งกระบวนการเชื่อมอย่างละเอียด จะทำให้คุณภาพการเชื่อมดีขึ้นอย่างมีประสิทธิภาพ ลดข้อบกพร่อง และเพิ่มประสิทธิภาพการผลิตได้ การออกแบบรอยเชื่อมอย่างเป็นวิทยาศาสตร์ไม่เพียงแต่รับประกันความแข็งแรงและความเสถียรของรอยเชื่อมเท่านั้น แต่ยังเพิ่มประสิทธิภาพกระบวนการผลิตอีกด้วย ช่วยให้บริษัทต่างๆ สามารถรักษาความสามารถในการแข่งขันในด้านการผลิตที่มีความแม่นยำสูงได้
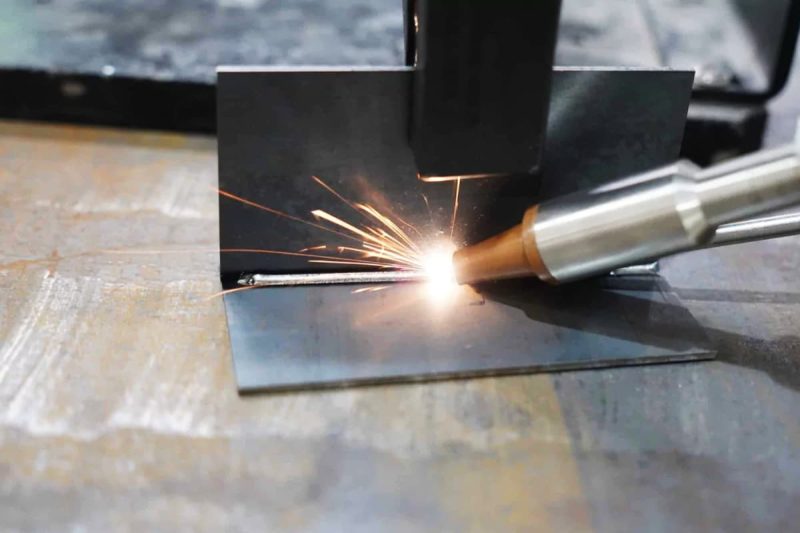
ปัจจัยที่มีผลต่อการออกแบบข้อต่อเชื่อมเลเซอร์
การออกแบบรอยเชื่อมด้วยเลเซอร์ไม่เพียงแต่เกี่ยวข้องกับการเลือกโครงสร้างพื้นฐานเท่านั้น แต่ยังได้รับผลกระทบจากปัจจัยหลายประการ เช่น คุณสมบัติของวัสดุ การกำหนดค่ารอยเชื่อม พารามิเตอร์การเชื่อม และข้อกำหนดการใช้งาน การพิจารณาปัจจัยเหล่านี้อย่างเหมาะสมสามารถช่วยปรับคุณภาพการเชื่อมให้เหมาะสม ปรับปรุงความแข็งแรงของรอยเชื่อม ลดข้อบกพร่อง และปรับปรุงประสิทธิภาพการผลิต
คุณสมบัติของวัสดุ
คุณสมบัติทางกายภาพและเคมีของสารตั้งต้นมีบทบาทสำคัญต่อประสิทธิภาพของรอยเชื่อมด้วยเลเซอร์ เมื่อออกแบบรอยเชื่อม สิ่งสำคัญคือต้องเน้นที่ประเด็นสำคัญต่อไปนี้:
- ความเข้ากันได้ของวัสดุพื้นฐาน: ความเข้ากันได้ของวัสดุโลหะต่างชนิดในการเชื่อมจะกำหนดคุณภาพของการเชื่อม ตัวอย่างเช่น โลหะผสมที่มีองค์ประกอบคล้ายคลึงกันมักมีคุณสมบัติการหลอมรวมที่ดี ในขณะที่การเชื่อมโลหะต่างชนิดอาจทำให้เกิดรอยแตกร้าวหรือข้อบกพร่องในการเชื่อมเนื่องจากค่าสัมประสิทธิ์การขยายตัวเนื่องจากความร้อนที่แตกต่างกันหรือการเกิดสารประกอบอินเตอร์เมทัลลิกที่เปราะบาง
- คุณสมบัติทางกลและทางโลหะวิทยา: คุณสมบัติทางกลศาสตร์ (เช่น ความแข็ง ความเหนียว และความแข็งแรงในการดึง) ส่งผลต่อความน่าเชื่อถือของการเชื่อม คุณสมบัติทางโลหะวิทยาจะกำหนดการเปลี่ยนแปลงขององค์ประกอบโลหะผสมระหว่างการเชื่อม ตัวอย่างเช่น เหล็กกล้าคาร์บอนสูงบางชนิดอาจทำให้โครงสร้างแข็งตัวระหว่างการเชื่อม ทำให้มีความเสี่ยงต่อการเกิดรอยแตกร้าวมากขึ้น ดังนั้น จำเป็นต้องปรับพารามิเตอร์ของกระบวนการเชื่อมให้เหมาะกับคุณสมบัติของวัสดุที่แตกต่างกันเพื่อให้แน่ใจถึงคุณภาพของการเชื่อม
- การนำความร้อนและอุณหภูมิการหลอมเหลว: การนำความร้อนและจุดหลอมเหลวของวัสดุส่งผลต่อการส่งผ่านและการดูดซับพลังงานเลเซอร์ ตัวอย่างเช่น โลหะที่มีการนำความร้อนสูง (เช่น ทองแดง และ อลูมิเนียม) ระบายความร้อนได้อย่างรวดเร็วและต้องใช้พลังงานเลเซอร์ที่สูงกว่าหรือพลังงานที่เข้มข้นกว่า วัสดุที่มีจุดหลอมเหลวสูงอาจต้องใช้พลังงานเชื่อมที่มากขึ้นเพื่อให้มั่นใจว่าจุดหลอมเหลวและจุดเชื่อมมีความแข็งแรงเพียงพอ
การกำหนดค่าตัวเชื่อมต่อ
ประเภท ความแม่นยำในการประกอบ และการจัดตำแหน่งของข้อต่อส่งผลโดยตรงต่อเสถียรภาพของกระบวนการเชื่อมและคุณภาพของรอยเชื่อม ประเภทข้อต่อทั่วไป ได้แก่:
- ข้อต่อแบบชน: เหมาะสำหรับงานเชื่อมที่ต้องการความแข็งแรงสูงและการเสียรูปต่ำ ช่องว่างของข้อต่อแบบชนต้องได้รับการควบคุมอย่างเข้มงวดเพื่อให้แน่ใจว่าหลอมรวมได้สมบูรณ์และหลีกเลี่ยงข้อบกพร่อง เช่น การหลอมรวมไม่สมบูรณ์หรือการรวมตัวของตะกรัน
- รอยเชื่อมแบบซ้อนทับ: เหมาะสำหรับการเชื่อมแผ่นบาง ส่วนที่ซ้อนทับของรอยเชื่อมสามารถเพิ่มความแข็งแรงได้ อย่างไรก็ตาม เนื่องมาจากเอฟเฟกต์การซ้อนกัน ก๊าซอาจยังคงอยู่ในช่องว่าง และจำเป็นต้องปรับพารามิเตอร์การเชื่อมให้เหมาะสมเพื่อลดรูพรุน
- ข้อต่อแบบ T: มักใช้กับชิ้นส่วนโครงสร้างที่ต้องรับแรงกดมาก การเชื่อมข้อต่อแบบ T ต้องมีการเจาะทะลุที่เพียงพอเพื่อหลีกเลี่ยงการแตกร้าวที่เกิดจากการรวมตัวของแรงกด
นอกจากนี้ในการออกแบบรอยเชื่อมยังจำเป็นต้องพิจารณาสิ่งต่อไปนี้ด้วย
- การประกอบและขนาดช่องว่าง: ช่องว่างที่มากเกินไปอาจทำให้การเชื่อมเติมได้ไม่เพียงพอ ในขณะที่ช่องว่างที่เล็กเกินไปอาจทำให้การเชื่อมหลอมเหลวไม่สมบูรณ์หรือเกิดการเสียรูป ดังนั้น การประกอบและการควบคุมช่องว่างที่แม่นยำจึงมีความสำคัญต่อคุณภาพการเชื่อม
- การส่งลำแสงเลเซอร์และช่องทางการประมวลผลชิ้นส่วน: ให้แน่ใจว่าลำแสงเลเซอร์สามารถเข้าถึงพื้นที่เชื่อมได้อย่างราบรื่นเพื่อหลีกเลี่ยงผลกระทบต่อเอฟเฟกต์การเชื่อมอันเนื่องมาจากการอุดตันหรือการสะท้อนของลำแสง ในเวลาเดียวกัน ในสายการผลิตอัตโนมัติ วิธีการยึดชิ้นส่วนและการออกแบบช่องทางเชื่อมยังต้องได้รับการปรับให้เหมาะสมเพื่อให้มั่นใจถึงความเสถียรและความสม่ำเสมอในการเชื่อม
พารามิเตอร์การเชื่อม
การปรับพารามิเตอร์การเชื่อมอย่างเหมาะสมสามารถเพิ่มประสิทธิภาพคุณภาพการเชื่อมและลดข้อบกพร่องในการเชื่อมได้ พารามิเตอร์หลักทั่วไป ได้แก่:
- กำลังเลเซอร์: มีผลต่อความลึกในการเชื่อมและการก่อตัวของแอ่งหลอมเหลว กำลังสูงเหมาะสำหรับการเชื่อมแบบเจาะลึก ในขณะที่กำลังต่ำเหมาะสำหรับการเชื่อมแบบแม่นยำ
- ตำแหน่งโฟกัสและเส้นผ่านศูนย์กลางลำแสง: การควบคุมโฟกัสที่แม่นยำส่งผลต่อความหนาแน่นของพลังงานและความลึกในการเชื่อม เส้นผ่านศูนย์กลางลำแสงที่เล็กกว่าเหมาะสำหรับการเชื่อมที่มีความแม่นยำสูง ในขณะที่ลำแสงขนาดใหญ่สามารถใช้สำหรับความต้องการการเชื่อมที่กว้าง
- ความเร็วการเชื่อมและทิศทางการเคลื่อนที่: ความเร็วในการเชื่อมที่เร็วเกินไปอาจทำให้การเจาะทะลุไม่เพียงพอและส่งผลต่อความแข็งแรงของรอยเชื่อม ในขณะที่ความเร็วที่ช้าเกินไปอาจทำให้การเชื่อมผิดรูปหรือบริเวณที่ได้รับผลกระทบจากความร้อน (HAZ) ขยายตัว ดังนั้น จำเป็นต้องปรับความเร็วในการเชื่อมร่วมกับวัสดุและโครงสร้างรอยเชื่อม
- การควบคุมก๊าซป้องกันและบรรยากาศ: การใช้ก๊าซป้องกันที่เหมาะสม (เช่น อาร์กอน ไนโตรเจน หรือก๊าซผสม) สามารถลดการเกิดออกซิเดชันระหว่างการเชื่อมและปรับคุณภาพการเชื่อมให้เหมาะสมที่สุด วัสดุแต่ละชนิดมีข้อกำหนดสำหรับก๊าซที่แตกต่างกัน ตัวอย่างเช่น โลหะผสมไททาเนียมต้องแยกออกจากออกซิเจนอย่างสมบูรณ์ ในขณะที่ สแตนเลส สามารถได้รับการปกป้องด้วยอาร์กอนเพื่อลดการเปลี่ยนสีและการเกิดออกซิเดชันจากการเชื่อม
ข้อกำหนดการสมัคร
นอกเหนือจากปัจจัยด้านวัสดุและกระบวนการแล้ว การออกแบบรอยเชื่อมยังต้องตอบสนองความต้องการของสถานการณ์การใช้งานเฉพาะด้วย ได้แก่:
- ข้อกำหนดด้านการทำงานและโครงสร้าง: เลือกประเภทข้อต่อและโครงสร้างการเชื่อมที่เหมาะสมตามการใช้งานผลิตภัณฑ์ขั้นสุดท้าย ตัวอย่างเช่น การเชื่อมด้วยเลเซอร์ในอุตสาหกรรมยานยนต์มักต้องการความแข็งแรงสูงและน้ำหนักเบา ในขณะที่การเชื่อมอุปกรณ์อิเล็กทรอนิกส์เน้นที่การปรับปรุงและการควบคุมโซนที่ได้รับผลกระทบจากความร้อน
- การตกแต่งพื้นผิวและรูปลักษณ์: ในบางการใช้งาน เช่น อุปกรณ์อิเล็กทรอนิกส์สำหรับผู้บริโภคหรืออุปกรณ์ทางการแพทย์ ความสวยงามของรอยเชื่อมถือเป็นสิ่งสำคัญ ซึ่งต้องปรับพารามิเตอร์การเชื่อมให้เหมาะสม ลดการกระเด็นของรอยเชื่อมและตะกรัน และปรับปรุงการตกแต่งพื้นผิว
- กระบวนการหลังการเชื่อมและกระบวนการรอง: กระบวนการเชื่อมบางประเภทอาจต้องมีกระบวนการหลังการเชื่อมเพิ่มเติม เช่น การเจียร การอบชุบด้วยความร้อน หรือการเคลือบ เพื่อให้เป็นไปตามมาตรฐานคุณภาพของผลิตภัณฑ์ขั้นสุดท้าย ดังนั้น เมื่อออกแบบรอยเชื่อม จะต้องพิจารณาถึงความเป็นไปได้และต้นทุนของกระบวนการขั้นต่อไปด้วย
การออกแบบรอยเชื่อมเลเซอร์ได้รับผลกระทบจากหลายปัจจัย รวมถึงลักษณะของพื้นผิว การกำหนดค่ารอยเชื่อม พารามิเตอร์การเชื่อม และข้อกำหนดการใช้งานขั้นสุดท้าย ด้วยการเลือกวัสดุอย่างมีเหตุผล ปรับโครงสร้างรอยเชื่อมให้เหมาะสม ควบคุมพารามิเตอร์กระบวนการเชื่อมอย่างแม่นยำ และปรับตามข้อกำหนดการใช้งานเฉพาะ คุณภาพการเชื่อมสามารถปรับปรุงได้อย่างมีประสิทธิภาพ ลดข้อบกพร่อง และเพิ่มประสิทธิภาพการผลิตได้ การออกแบบรอยเชื่อมที่เป็นวิทยาศาสตร์และสมเหตุสมผลไม่เพียงแต่รับประกันความแข็งแรงและความเสถียรของรอยเชื่อมเท่านั้น แต่ยังเพิ่มประสิทธิภาพกระบวนการผลิต ปรับปรุงความสามารถในการแข่งขันของการผลิตในขณะที่รับประกันคุณภาพของผลิตภัณฑ์
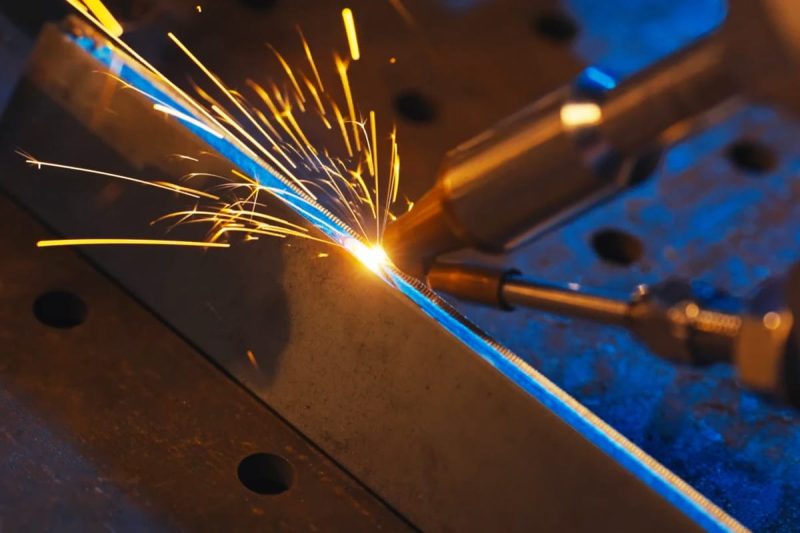
กลยุทธ์การเพิ่มประสิทธิภาพสำหรับการออกแบบข้อต่อเชื่อมเลเซอร์
เป้าหมายของการปรับปรุงการออกแบบรอยเชื่อมด้วยเลเซอร์คือการปรับปรุงคุณภาพการเชื่อม รับรองความสมบูรณ์และความแข็งแรงของรอยเชื่อม ลดข้อบกพร่อง และปรับปรุงประสิทธิภาพการผลิต กลยุทธ์การเพิ่มประสิทธิภาพหลักประกอบด้วยประเด็นต่อไปนี้:
ลดพื้นที่ได้รับผลกระทบจากความร้อน (HAZ)
โซนที่ได้รับผลกระทบจากความร้อนขนาดใหญ่ (HAZ) อาจส่งผลต่อคุณสมบัติของวัสดุและอาจทำให้รอยเชื่อมเปราะได้ การปรับกำลังของเลเซอร์ ความเร็วในการเชื่อม และโฟกัสของลำแสงให้เหมาะสมจะช่วยให้ควบคุมปริมาณความร้อนได้อย่างมีประสิทธิภาพเพื่อลดโซนที่ได้รับผลกระทบจากความร้อน นอกจากนี้ การเลือกประเภทของรอยเชื่อมที่เหมาะสม เช่น รอยต่อแบบชนกันหรือรอยต่อแบบทับซ้อน ยังช่วยลดการสะสมความร้อนและปรับปรุงเสถียรภาพในการเชื่อมได้อีกด้วย
เพิ่มความแข็งแรงในการเชื่อม
กุญแจสำคัญในการรับรองความแข็งแรงของรอยเชื่อมอยู่ที่การกระจายความร้อนอย่างเหมาะสม การควบคุมขนาดช่องว่าง และการจัดตำแหน่งชิ้นงานให้ถูกต้อง กระบวนการเชื่อมที่เหมาะสมสามารถลดความเข้มข้นของความเค้นและหลีกเลี่ยงปัญหาต่างๆ เช่น การขาดการหลอมรวม ในการใช้งานบางกรณี การใช้สารตัวเติมที่เข้าคู่กันสามารถเพิ่มการยึดติดของรอยเชื่อมและปรับปรุงความแข็งแรงและความทนทานโดยรวมของรอยเชื่อม
มั่นใจคุณภาพการเชื่อม
คุณภาพการเชื่อมได้รับผลกระทบจากหลายปัจจัย เช่น กำลังของเลเซอร์ ตำแหน่งโฟกัส ความเร็วในการเชื่อม และการใช้ก๊าซป้องกัน การปรับพารามิเตอร์เหล่านี้อย่างเหมาะสมสามารถลดข้อบกพร่อง เช่น รูพรุนและรอยแตก นอกจากนี้ การใช้เทคโนโลยีตรวจสอบออนไลน์เพื่อตรวจสอบคุณภาพสามารถรับประกันความสม่ำเสมอของการเชื่อมและปรับปรุงอัตราคุณสมบัติของผลิตภัณฑ์ได้
การปรับปรุงการออกแบบรอยเชื่อมเลเซอร์เป็นวิธีการสำคัญในการปรับปรุงคุณภาพการเชื่อมและประสิทธิภาพการผลิต โดยการลดบริเวณที่ได้รับผลกระทบจากความร้อน เพิ่มความแข็งแรงของรอยเชื่อม และควบคุมคุณภาพการเชื่อมอย่างเคร่งครัด จะสามารถปรับปรุงประสิทธิภาพการเชื่อมได้อย่างมีประสิทธิภาพเพื่อให้ตรงตามมาตรฐานการผลิตในอุตสาหกรรมระดับสูง
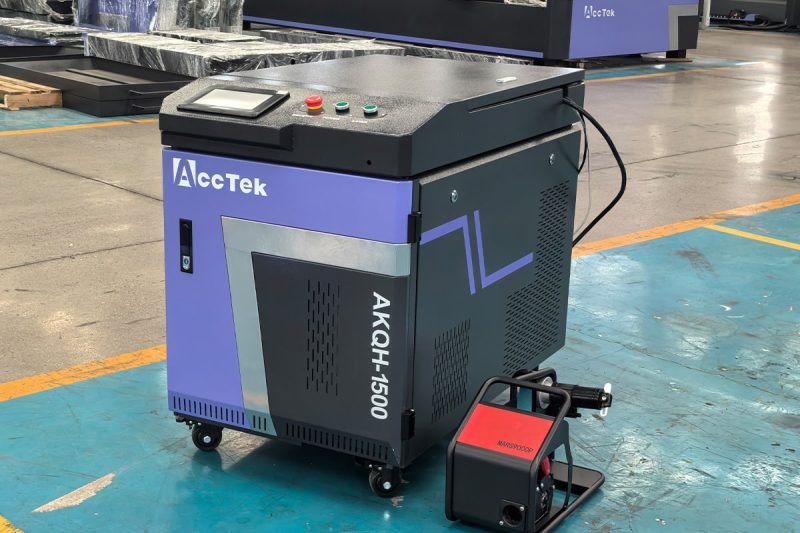
สรุป
การออกแบบรอยเชื่อมด้วยเลเซอร์เป็นปัจจัยสำคัญในการกำหนดคุณภาพการเชื่อมและประสิทธิภาพการผลิต โดยการทำความเข้าใจหลักการพื้นฐาน ปัจจัยที่มีอิทธิพล และกลยุทธ์การปรับให้เหมาะสมของการออกแบบรอยเชื่อมอย่างลึกซึ้ง ผู้ผลิตสามารถรับประกันความสมบูรณ์ของรอยเชื่อม ลดข้อบกพร่อง และปรับปรุงคุณภาพการเชื่อมโดยรวมได้ การออกแบบรอยเชื่อมที่เหมาะสมไม่เพียงแต่จะปรับปรุงความแข็งแรงในการเชื่อมเท่านั้น แต่ยังปรับให้กระบวนการผลิตเหมาะสมเพื่อตอบสนองความต้องการของสถานการณ์การใช้งานที่แตกต่างกันอีกด้วย
หากคุณกำลังมองหาโซลูชันการเชื่อมเลเซอร์ที่มีประสิทธิภาพและแม่นยำ แอคเทค เลเซอร์ เสนอบริการขั้นสูง เครื่องเชื่อมเลเซอร์ที่ตรงตามมาตรฐานคุณภาพและประสิทธิภาพสูงสุด อุปกรณ์ของเราใช้เทคโนโลยีเลเซอร์ขั้นสูงเพื่อให้แน่ใจว่าการเชื่อมมีความเสถียรและสม่ำเสมอ เพื่อช่วยให้คุณบรรลุเป้าหมายการผลิตของคุณ ติดต่อเรา เพื่อเรียนรู้เพิ่มเติมเกี่ยวกับวิธีที่ผลิตภัณฑ์ของเราสามารถช่วยคุณเพิ่มประสิทธิภาพกระบวนการเชื่อมของคุณได้อย่างไร!
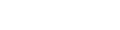
ข้อมูลติดต่อ
- [email protected]
- [email protected]
- +86-19963414011
- หมายเลข 3 โซน A เขตอุตสาหกรรม Luzhen เมือง Yucheng มณฑลซานตง
รับโซลูชันเลเซอร์