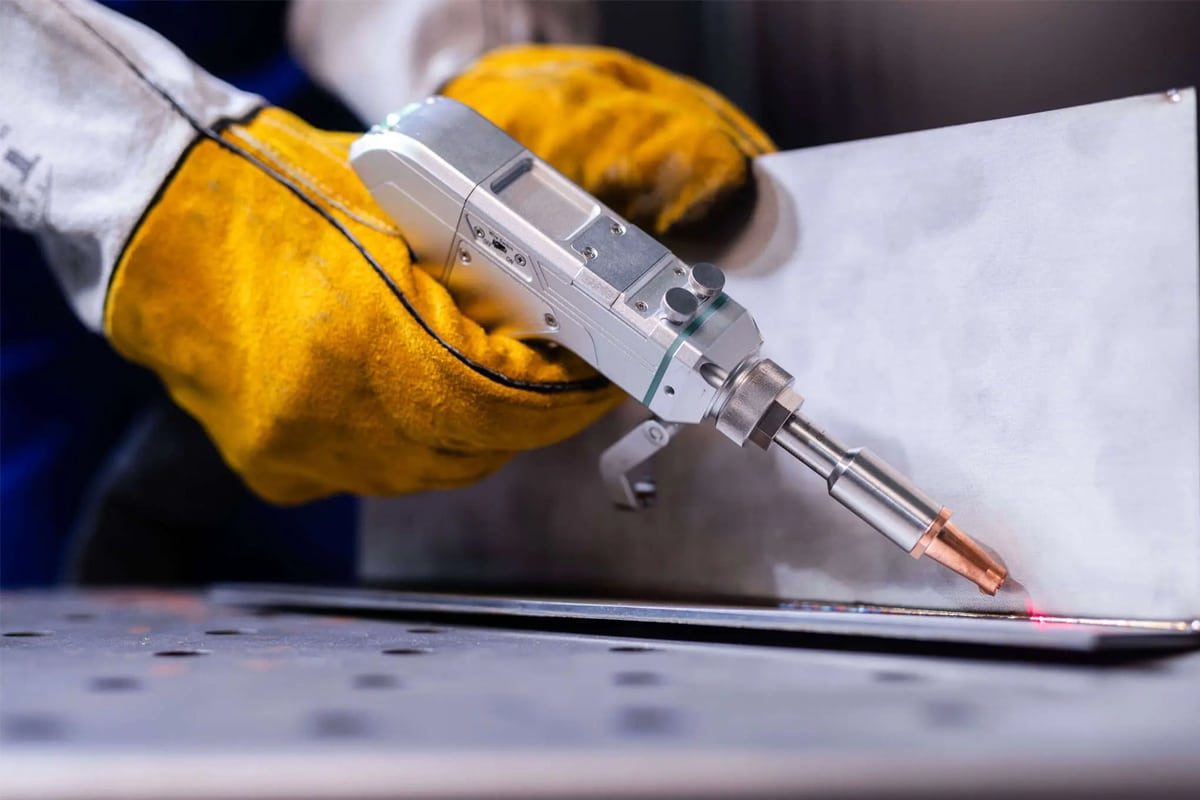
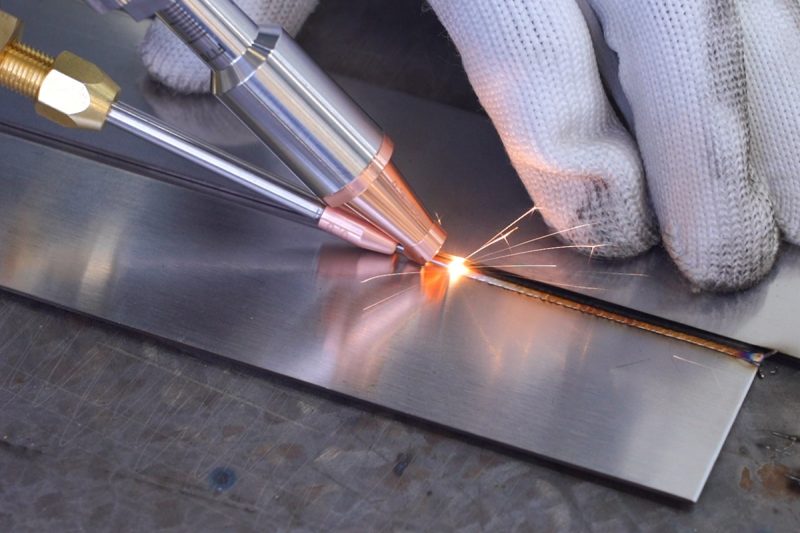
ภาพรวมของการเชื่อมด้วยเลเซอร์
การเชื่อมเลเซอร์คืออะไร?
การเชื่อมด้วยเลเซอร์เป็นกระบวนการเชื่อมที่แม่นยำและมีประสิทธิภาพซึ่งใช้ลำแสงเลเซอร์ที่มีความเข้มข้นสูงในการให้ความร้อนและหลอมรวมวัสดุ ลำแสงเลเซอร์จะสร้างแหล่งความร้อนที่เข้มข้น ทำให้สามารถเชื่อมได้แคบและลึกโดยมีโซนที่ได้รับผลกระทบจากความร้อน (HAZ) น้อยที่สุด การเชื่อมด้วยเลเซอร์ทำงานในสองโหมดหลัก ขึ้นอยู่กับความหนาแน่นของพลังงานและคุณสมบัติของวัสดุ:
- การเชื่อมแบบรูกุญแจ: ในโหมดนี้ ลำแสงเลเซอร์ที่มีความหนาแน่นกำลังสูงจะทำให้วัสดุระเหย ทำให้เกิดรูกุญแจที่แคบและลึกซึ่งเต็มไปด้วยโลหะหลอมเหลวและไอระเหย รูกุญแจทำหน้าที่เป็นตัวกลางสำหรับพลังงานเลเซอร์ ทำให้สามารถเจาะลึกและเชื่อมด้วยอัตราส่วนภาพสูงได้ โหมดนี้เหมาะอย่างยิ่งสำหรับการใช้งานที่ต้องการการเชื่อมแบบลึกและแคบ เช่น ในอุตสาหกรรมยานยนต์และอวกาศ
- การเชื่อมด้วยโหมดการนำไฟฟ้า: โหมดนี้ใช้ความหนาแน่นพลังงานต่ำกว่าเมื่อเปรียบเทียบกับการเชื่อมแบบรูกุญแจ ซึ่งเลเซอร์จะให้ความร้อนกับวัสดุโดยไม่ทำให้ระเหย การนำความร้อนจากพื้นผิวจะสร้างแอ่งเชื่อมที่ตื้นและกว้างขึ้น การเชื่อมด้วยโหมดการนำไฟฟ้าเหมาะสำหรับวัสดุที่มีความบางหรือเมื่อต้องการการเจาะทะลุและการป้อนความร้อนขั้นต่ำ
ข้อดีของการเชื่อมด้วยเลเซอร์
การเชื่อมด้วยเลเซอร์มีข้อดีหลายประการที่ทำให้มีข้อได้เปรียบเหนือวิธีการเชื่อมแบบดั้งเดิม:
- ความแม่นยำและความถูกต้อง: ลำแสงเลเซอร์ที่มีความเข้มข้นช่วยให้ควบคุมได้อย่างแม่นยำ ทำให้เกิดการเชื่อมที่แม่นยำพร้อมการบิดเบือนที่น้อยที่สุด
- การประมวลผลความเร็วสูง: ความหนาแน่นพลังงานสูงของเลเซอร์ช่วยให้เชื่อมได้รวดเร็วขึ้น เพิ่มผลผลิต และลดเวลาในรอบการทำงาน
- โซนที่ได้รับผลกระทบจากความร้อนน้อยที่สุด: การแพร่กระจายความร้อนที่ลดลงช่วยลดการบิดเบือน ทำให้การเชื่อมเลเซอร์เหมาะสำหรับส่วนประกอบที่บอบบางหรือบาง
- ความสามารถด้านระบบอัตโนมัติ: การเชื่อมด้วยเลเซอร์สามารถรวมเข้ากับระบบอัตโนมัติและแขนหุ่นยนต์ได้อย่างง่ายดาย ช่วยเพิ่มประสิทธิภาพสำหรับการผลิตปริมาณมาก
- ความเก่งกาจของวัสดุ: สามารถเชื่อมโลหะและโลหะผสมได้หลากหลายชนิด รวมถึงวัสดุที่เชื่อมยาก เช่น ไททาเนียมและสเตนเลส
- กระบวนการที่ไม่ต้องสัมผัส: ไม่จำเป็นต้องสัมผัสทางกายภาพ ลดการสึกหรอของเครื่องมือและขจัดความเสี่ยงของการปนเปื้อนของอิเล็กโทรด
การประยุกต์ใช้งานการเชื่อมด้วยเลเซอร์
การเชื่อมด้วยเลเซอร์ใช้ในอุตสาหกรรมต่างๆ มากมายเนื่องจากความสามารถเฉพาะตัวและความแม่นยำ:
- อุตสาหกรรมยานยนต์: ใช้สำหรับเชื่อมแผงตัวถังรถ เฟือง ชิ้นส่วนส่งกำลัง และระบบไอเสีย ซึ่งความแม่นยำและความเร็วสูงเป็นสิ่งสำคัญ
- อุตสาหกรรมการบินและอวกาศ: เหมาะสำหรับการเชื่อมชิ้นส่วนน้ำหนักเบาและมีความแข็งแรงสูง เช่น ใบพัดกังหัน ชิ้นส่วนโครงสร้าง และส่วนประกอบเครื่องยนต์
- อุตสาหกรรมอิเล็กทรอนิกส์: เหมาะสำหรับการเชื่อมไมโครวงจรอันละเอียดอ่อน ขั้วต่อ และกล่องหุ้มในอุปกรณ์อิเล็กทรอนิกส์
- การผลิตอุปกรณ์ทางการแพทย์: ใช้สำหรับการเชื่อมอุปกรณ์ทางการแพทย์ที่ซับซ้อน เครื่องมือผ่าตัด และส่วนประกอบที่ปลูกถ่ายได้ซึ่งความแม่นยำและความสะอาดเป็นสิ่งสำคัญที่สุด
- เครื่องประดับและศิลปะ: ช่วยให้สามารถซ่อมแซมและประดิษฐ์เครื่องประดับที่มีดีไซน์ซับซ้อนและงานโลหะที่เป็นศิลปะได้
- การผลิตทางอุตสาหกรรม: นำมาประยุกต์ใช้ในการเชื่อมต่อแผ่นโลหะ ท่อ และส่วนประกอบโครงสร้างงานหนักในภาคอุตสาหกรรมต่างๆ
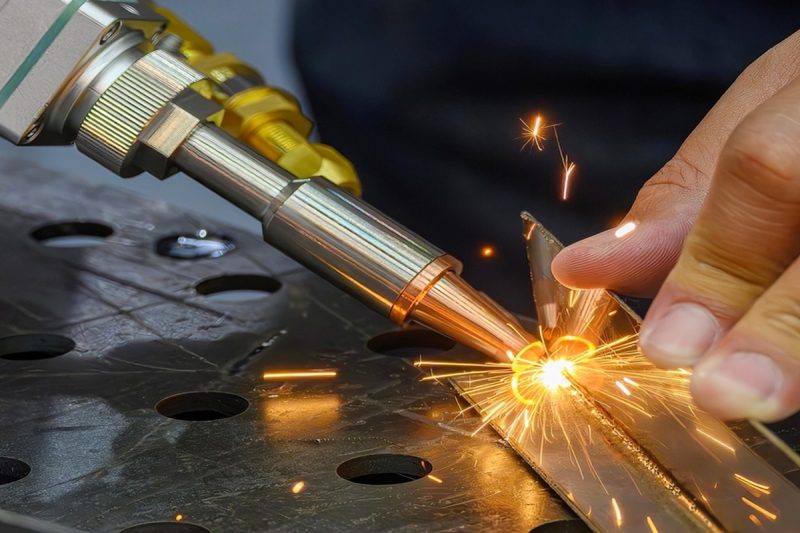
ข้อบกพร่องทั่วไปในการเชื่อมด้วยเลเซอร์
ความพรุน
สาเหตุ
- การปนเปื้อนบนพื้นผิว: น้ำมัน จารบี ความชื้น และสนิมบนพื้นผิวชิ้นงานสามารถสร้างก๊าซเมื่อได้รับความร้อน ทำให้เกิดฟองอากาศที่ติดอยู่ภายในรอยเชื่อม
- ปัญหาแก๊สป้องกัน: การครอบคลุมแก๊สป้องกันที่ไม่เพียงพอ อัตราการไหลที่ต่ำ หรือประเภทแก๊สที่ไม่เหมาะสม อาจส่งผลให้เกิดการปนเปื้อนในบรรยากาศ เช่น ออกซิเจนและไนโตรเจนที่แทรกซึมเข้ามา ซึ่งทำให้เกิดโพรงแก๊ส
- องค์ประกอบของวัสดุ: ความเข้มข้นสูงของไฮโดรเจน กำมะถัน คาร์บอน หรือสิ่งเจือปนอื่นๆ ในโลหะพื้นฐานอาจทำให้เกิดก๊าซเกิดขึ้นในระหว่างการเชื่อม
- การระบายความร้อนอย่างรวดเร็ว: การแข็งตัวอย่างรวดเร็วของสระที่หลอมละลายสามารถกักเก็บก๊าซไว้ก่อนที่จะหลบหนี
โซลูชั่น
- การทำความสะอาดพื้นผิว: ทำความสะอาดชิ้นงานให้ทั่วถึงก่อนการเชื่อม โดยกำจัดสิ่งปนเปื้อน เช่น จารบี น้ำมัน และสนิม
- การไหลของก๊าซป้องกันที่เหมาะสม: ใช้ก๊าซป้องกันที่เหมาะสม เช่น อาร์กอนหรือฮีเลียม โดยรับรองอัตราการไหลและการครอบคลุมที่ถูกต้องเพื่อปกป้องแอ่งเชื่อม
- การเลือกและการเตรียมวัสดุ: เลือกวัสดุที่มีปริมาณสิ่งเจือปนต่ำ และดำเนินการบำบัดก่อนเชื่อม เช่น การไล่ก๊าซออก
- การปรับพารามิเตอร์: ปรับพารามิเตอร์เลเซอร์เพื่อให้การระบายความร้อนได้รับการควบคุม โดยให้ก๊าซมีเวลาในการหลบหนี
การแตกร้าว
ประเภทของการแตกร้าว
- การแตกร้าวจากความร้อน: เกิดขึ้นที่อุณหภูมิสูงในระหว่างการแข็งตัวอันเนื่องมาจากความเค้นดึงหรือการแยกตัวของสิ่งเจือปน (เช่น กำมะถัน)
- การแตกร้าวจากความเย็น: เกิดขึ้นหลังจากการเย็นตัว โดยมักสัมพันธ์กับความเปราะเนื่องจากไฮโดรเจน ความเครียดตกค้าง หรือองค์ประกอบของวัสดุที่ไม่เหมาะสม
สาเหตุ
- การไล่ระดับความร้อนสูง: รอบการทำความร้อนและทำความเย็นที่รวดเร็วอาจทำให้เกิดความเค้นตกค้างที่กระตุ้นให้เกิดการแตกร้าว
- องค์ประกอบของวัสดุ: โลหะผสมบางชนิด โดยเฉพาะโลหะผสมที่มีกำมะถันหรือคาร์บอนสูง จะเสี่ยงต่อการแตกร้าวได้ง่ายขึ้น
- สิ่งเจือปน: ธาตุต่างๆ เช่น กำมะถันและฟอสฟอรัสสามารถแยกตัวที่ขอบเกรน ทำให้โครงสร้างอ่อนแอลง
- การดูดซับไฮโดรเจน: ไฮโดรเจนที่เข้ามาผ่านความชื้น ก๊าซป้องกันที่ปนเปื้อน หรือโลหะฐานสามารถทำให้เกิดการแตกร้าวได้ล่าช้า
โซลูชั่น
- การอุ่นล่วงหน้าและการอบชุบด้วยความร้อนหลังการเชื่อม: อุ่นชิ้นงานล่วงหน้าเพื่อลดการไล่ระดับความร้อนและทำการอบชุบด้วยความร้อนหลังการเชื่อมเพื่อบรรเทาความเค้นที่เหลืออยู่
- การควบคุมวัสดุ: เลือกวัสดุที่มีระดับสิ่งเจือปนต่ำและปรับองค์ประกอบทางเคมีให้เหมาะสมเพื่อลดโอกาสเกิดรอยแตกร้าว
- การควบคุมไฮโดรเจน: วัสดุแห้งและใช้กระบวนการที่มีไฮโดรเจนต่ำ เช่น การใช้ก๊าซป้องกันแห้งและหลีกเลี่ยงความชื้น
- เทคนิคการบรรเทาความเครียด: ใช้อุปกรณ์ยึดและการออกแบบข้อต่อที่เหมาะสมเพื่อลดความเครียดที่สะสม
ตัดราคา
สาเหตุ
- ความร้อนที่มากเกินไป: กำลังเลเซอร์ที่สูงหรือความเร็วในการเดินทางที่ช้าอาจทำให้เกิดการหลอมละลายในบริเวณนั้นและสูญเสียวัสดุได้หากไม่มีโลหะเติมเพียงพอ
- มุมลำแสงไม่ถูกต้อง: การจัดตำแหน่งที่ไม่ถูกต้องของลำแสงเลเซอร์เมื่อเทียบกับข้อต่ออาจทำให้มีการกำจัดวัสดุมากกว่าการหลอมรวม
- โฟกัสไม่ถูกต้อง: การโฟกัสเลเซอร์ที่ไม่แม่นยำสามารถรวมพลังงานได้ไม่สม่ำเสมอ
โซลูชั่น
- เพิ่มประสิทธิภาพการป้อนความร้อน: ปรับกำลังเลเซอร์ ความเร็วการเดินทาง และเส้นผ่านศูนย์กลางลำแสงเพื่อควบคุมการกระจายความร้อน
- การจัดตำแหน่งลำแสง: จัดตำแหน่งลำแสงเลเซอร์ให้ตรงกับข้อต่ออย่างถูกต้องเพื่อให้แน่ใจว่าละลายและอุดอย่างสม่ำเสมอ
- เทคนิคการเชื่อม: ปรับมุมและตำแหน่งของเลเซอร์เพื่อลดการสูญเสียวัสดุ
การขาดการหลอมรวม
สาเหตุ
- ความร้อนที่ไม่เพียงพอ: พลังงานเลเซอร์ต่ำหรือความเร็วการเดินทางที่มากเกินไปอาจป้องกันไม่ให้วัสดุฐานหลอมรวมกันอย่างสมบูรณ์
- การเตรียมข้อต่อที่ไม่เหมาะสม: การประกอบที่ไม่ดี ช่องว่าง หรือการจัดตำแหน่งที่ไม่ถูกต้องระหว่างชิ้นงานอาจขัดขวางการหลอมรวมอย่างสมบูรณ์
- การปนเปื้อน: ออกไซด์บนพื้นผิว สิ่งสกปรก หรือสิ่งปนเปื้อนอื่นๆ อาจทำหน้าที่เป็นสิ่งกีดขวางการหลอมรวม
โซลูชั่น
- เพิ่มอินพุตความร้อน: ใช้พลังงานเลเซอร์ที่เพียงพอหรือลดความเร็วในการเดินทางเพื่อให้เกิดการหลอมรวมที่เหมาะสม
- ปรับปรุงการประกอบข้อต่อ: รับรองการจัดตำแหน่งและความพอดีที่เหมาะสมระหว่างชิ้นงานเพื่อให้การเชื่อมทะลุได้สม่ำเสมอ
- การทำความสะอาดพื้นผิว: กำจัดออกไซด์ น้ำมัน และสิ่งปนเปื้อนอื่นๆ ออกจากพื้นผิวการเชื่อม
การเจาะทะลุที่ไม่สมบูรณ์
สาเหตุ
- กำลังเลเซอร์ต่ำ: ปริมาณพลังงานที่ป้อนเข้าไม่เพียงพอที่จะหลอมผ่านความหนาของวัสดุได้อย่างสมบูรณ์
- ความเร็วในการเดินทางสูง: เลเซอร์เคลื่อนที่เร็วเกินกว่าที่จะให้ความร้อนและละลายข้อต่อได้เต็มที่
- การโฟกัสลำแสงที่ไม่เหมาะสม: การโฟกัสเลเซอร์ที่ไม่ถูกต้องอาจทำให้เกิดการเจาะทะลุได้ตื้น
โซลูชั่น
- เพิ่มพลังเลเซอร์: ปรับการตั้งค่าพลังเพื่อให้แน่ใจว่าสามารถทะลุผ่านข้อต่อได้เต็มที่
- ลดความเร็วในการเดินทาง: ให้เวลาเลเซอร์ในการให้ความร้อนและละลายวัสดุมากขึ้น
- โฟกัสลำแสงที่ถูกต้อง: โฟกัสเลเซอร์อย่างเหมาะสมเพื่อให้ได้ความลึกการเจาะที่สม่ำเสมอ
โปรยลงมา
สาเหตุ
- กำลังเลเซอร์ที่มากเกินไป: การตั้งค่ากำลังสูงอาจทำให้สระที่หลอมละลายเดือดอย่างรุนแรง
- สารปนเปื้อน: สิ่งสกปรกบนพื้นผิวอาจทำปฏิกิริยากับความร้อน ทำให้เกิดการระเหยอย่างรวดเร็ว
- ก๊าซป้องกันที่ไม่เหมาะสม: การป้องกันที่ไม่เพียงพออาจทำให้เกิดการออกซิเดชัน ส่งผลให้เกิดการกระเซ็น
โซลูชั่น
- ปรับพารามิเตอร์เลเซอร์: ลดพลังงานเลเซอร์และเพิ่มประสิทธิภาพการตั้งค่าพัลส์เพื่อป้องกันการป้อนพลังงานมากเกินไป
- การทำความสะอาดพื้นผิว: ตรวจสอบให้แน่ใจว่าพื้นผิวปราศจากสิ่งปนเปื้อนก่อนการเชื่อม
- การเพิ่มประสิทธิภาพก๊าซป้องกัน: ใช้ก๊าซป้องกันที่เหมาะสมและรักษาอัตราการไหลให้เหมาะสม
ความผิดปกติของรอยเชื่อม
สาเหตุ
- ความเร็วการเดินทางที่ไม่สม่ำเสมอ: ความผันผวนของความเร็วทำให้การทำความร้อนเข้าไม่สม่ำเสมอ
- ความแปรผันของกำลังเลเซอร์: การเปลี่ยนแปลงกำลังเลเซอร์ที่ส่งออกอาจส่งผลให้การหลอมเหลวไม่สม่ำเสมอ
- โฟกัสลำแสงไม่ถูกต้อง: โฟกัสที่ไม่ถูกต้องทำให้การกระจายพลังงานไม่สม่ำเสมอ
โซลูชั่น
- รักษาความเร็วการเดินทางที่สม่ำเสมอ: ให้แน่ใจว่าความเร็วสม่ำเสมอตลอดกระบวนการเชื่อม
- รักษาเสถียรภาพเอาต์พุตพลังงาน: ใช้แหล่งพลังงานที่เสถียรเพื่อรักษาเอาต์พุตเลเซอร์ที่สม่ำเสมอ
- ปรับโฟกัสลำแสง: ตรวจสอบให้แน่ใจว่าลำแสงเรียงตำแหน่งและโฟกัสอย่างถูกต้องเพื่อการส่งพลังงานที่สม่ำเสมอ
การเผาไหม้ผ่าน
สาเหตุ
- ความร้อนที่มากเกินไป: กำลังเลเซอร์ที่สูงหรือความเร็วในการเดินทางที่ช้าอาจทำให้เกิดการหลอมละลายที่มากเกินไป
- วัสดุบาง: แผ่นที่บางมีแนวโน้มที่จะไหม้ได้มากกว่า
- โฟกัสลำแสงไม่ถูกต้อง: การรวมพลังงานไว้ในพื้นที่เล็กๆ อาจทำให้การหลอมละลายรุนแรงขึ้น
โซลูชั่น
- ลดการป้อนความร้อน: ลดกำลังเลเซอร์หรือเพิ่มความเร็วในการเดินทาง
- ขยายโฟกัสลำแสง: กระจายพลังงานเลเซอร์ให้สม่ำเสมอมากขึ้น
- ใช้ความหนาของวัสดุที่เหมาะสม: เลือกความหนาของวัสดุให้ตรงกับข้อกำหนดในการเชื่อม
การเสียรูปและการบิดเบือน
สาเหตุ
- ความเครียดจากความร้อน: วงจรความร้อนและการทำความเย็นที่รวดเร็วทำให้เกิดการขยายตัวและหดตัว
- วัสดุบาง: มีแนวโน้มที่จะบิดงอได้ง่าย
- ความร้อนที่มากเกินไป: ปริมาณพลังงานที่มากเกินไปอาจทำให้เกิดการบิดเบือนอย่างรุนแรง
โซลูชั่น
- เพิ่มประสิทธิภาพการป้อนความร้อน: ใช้พารามิเตอร์เลเซอร์ควบคุมเพื่อลดความร้อนที่มากเกินไป
- อุปกรณ์จับยึดและการยึด: ยึดชิ้นงานเข้าที่ด้วยอุปกรณ์จับยึดเพื่อลดการเคลื่อนไหว
- การเชื่อมแบบสมดุล: ใช้เทคนิคที่สมดุลความร้อนและลดความเครียดให้เหลือน้อยที่สุด
ออกซิเดชันและการเปลี่ยนสี
สาเหตุ
- ก๊าซป้องกันไม่เพียงพอ: การไหลของก๊าซที่ต่ำหรือการครอบคลุมที่ไม่ดีอาจทำให้แอ่งเชื่อมสัมผัสกับอากาศ
- องค์ประกอบของก๊าซไม่เหมาะสม: การเลือกก๊าซป้องกันที่ไม่ถูกต้องอาจไม่สามารถป้องกันการออกซิเดชันได้
- สารปนเปื้อน: สิ่งสกปรกบนพื้นผิวอาจทำปฏิกิริยาและทำให้เกิดออกซิเดชันได้
โซลูชั่น
- ต้องแน่ใจว่ามีการป้องกันที่เหมาะสม: ใช้ก๊าซป้องกันในปริมาณที่เพียงพอเพื่อป้องกันแอ่งเชื่อม
- เลือกองค์ประกอบก๊าซที่เหมาะสม: เลือกก๊าซป้องกันที่ป้องกันการเกิดออกซิเดชันได้อย่างมีประสิทธิภาพ (เช่น อาร์กอน)
- การทำความสะอาดพื้นผิว: ทำความสะอาดพื้นผิวชิ้นงานอย่างทั่วถึงเพื่อลดปฏิกิริยาที่เกิดขึ้นระหว่างการเชื่อม
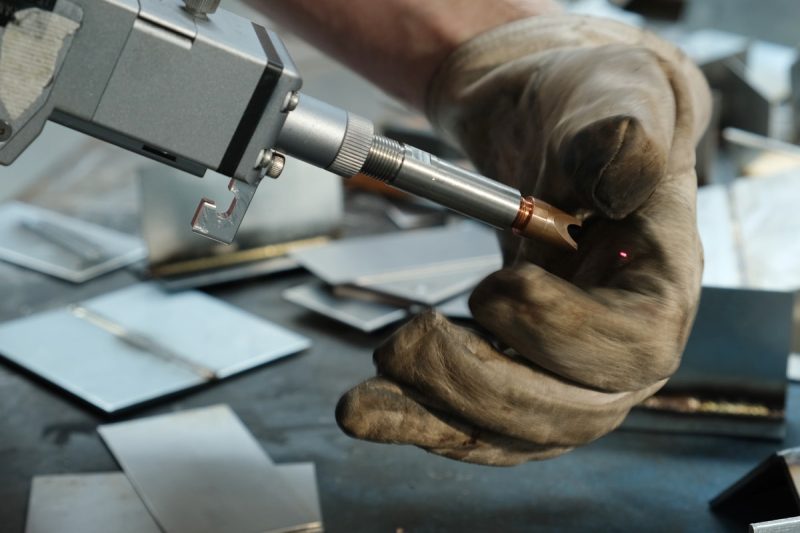
ปัจจัยที่มีอิทธิพลต่อข้อบกพร่องในการเชื่อม
คุณสมบัติของวัสดุ
คุณสมบัติของวัสดุที่จะเชื่อมมีบทบาทสำคัญในการกำหนดคุณภาพของการเชื่อมและความเป็นไปได้ที่จะเกิดข้อบกพร่อง
- การนำความร้อน: วัสดุที่มีการนำความร้อนสูง เช่น อลูมิเนียม มีแนวโน้มที่จะระบายความร้อนได้อย่างรวดเร็ว ต้องใช้กำลังเลเซอร์ที่สูงกว่าหรือความเร็วในการเคลื่อนที่ที่ช้ากว่าเพื่อให้เกิดการทะลุทะลวงและการหลอมรวมที่เพียงพอ การควบคุมที่ไม่เพียงพออาจนำไปสู่ข้อบกพร่อง เช่น การหลอมรวมที่ไม่เพียงพอหรือการทะลุทะลวงที่ไม่สมบูรณ์
- จุดหลอมเหลว: วัสดุที่มีจุดหลอมเหลวต่างกันต้องใช้พารามิเตอร์เลเซอร์ที่แตกต่างกัน ตัวอย่างเช่น ไททาเนียมมีจุดหลอมเหลวสูงและต้องใช้พลังงานมากกว่า ในขณะที่วัสดุที่มีจุดหลอมเหลวต่ำ เช่น สังกะสี อาจเกิดการเผาไหม้ได้หากไม่ได้รับการจัดการอย่างระมัดระวัง
- การสะท้อนแสง: วัสดุที่สะท้อนแสงสูง เช่น ทองแดงและโลหะผสมอลูมิเนียมบางชนิด อาจสะท้อนพลังงานเลเซอร์บางส่วน ทำให้ความร้อนที่ป้อนเข้ามาลดลง ซึ่งอาจส่งผลให้เกิดการหลอมรวมที่ไม่สมบูรณ์ การแทรกซึมที่ไม่สม่ำเสมอ หรือการกระเซ็นของแสง เนื่องจากพลังงานที่สะท้อนออกมาอาจส่งผลกระทบต่อพื้นที่โดยรอบ
- องค์ประกอบของวัสดุและสิ่งเจือปน: ธาตุต่างๆ เช่น กำมะถัน ฟอสฟอรัส และไฮโดรเจนในวัสดุสามารถเพิ่มโอกาสที่วัสดุจะเกิดข้อบกพร่อง เช่น รูพรุนและรอยแตกร้าวได้ ตัวอย่างเช่น ปริมาณไฮโดรเจนที่สูงอาจทำให้เกิดรูพรุน ในขณะที่กำมะถันและฟอสฟอรัสจะเพิ่มความเสี่ยงของรอยแตกร้าวจากความร้อน การเลือกวัสดุที่มีระดับสิ่งเจือปนต่ำหรือการบำบัดก่อนการเชื่อมสามารถช่วยลดปัญหาเหล่านี้ได้
พารามิเตอร์การเชื่อม
การเลือกและควบคุมพารามิเตอร์การเชื่อมเลเซอร์อย่างเหมาะสมถือเป็นสิ่งสำคัญในการป้องกันข้อบกพร่อง พารามิเตอร์หลัก ได้แก่:
- กำลังเลเซอร์: กำลังเลเซอร์ที่เพียงพอถือเป็นสิ่งสำคัญสำหรับการทะลุทะลวงและการหลอมรวมอย่างสมบูรณ์ กำลังที่ไม่เพียงพออาจนำไปสู่การหลอมรวมที่ไม่เพียงพอหรือทะลุทะลวงได้ไม่สมบูรณ์ ในขณะที่กำลังที่มากเกินไปอาจทำให้เกิดการไหม้ การกระเด็น และการเสียรูป
- ความเร็วในการเดินทาง: ความเร็วในการเดินทางส่งผลต่อปริมาณความร้อนที่ป้อนต่อหน่วยความยาวของรอยเชื่อม ความเร็วที่สูงเกินไปอาจทำให้วัสดุไม่ได้รับความร้อนอย่างเพียงพอ ส่งผลให้เกิดข้อบกพร่อง เช่น การหลอมเหลวไม่เพียงพอและการเจาะทะลุไม่สมบูรณ์ ในทางกลับกัน ความเร็วที่ช้าเกินไปอาจทำให้เกิดความร้อนมากเกินไป ทำให้เกิดการไหม้และการบิดเบือน
- โฟกัสลำแสง: โฟกัสลำแสงที่ถูกต้องมีความสำคัญต่อความเข้มข้นของพลังงาน การจัดตำแหน่งที่ไม่ถูกต้องหรือตำแหน่งโฟกัสที่ไม่ถูกต้องอาจส่งผลให้การเจาะทะลุไม่เพียงพอ โปรไฟล์ลูกปัดไม่สม่ำเสมอ และรอยเชื่อมมีรูพรุน สำหรับการเจาะทะลุลึก จำเป็นต้องใช้ลำแสงที่โฟกัสที่มีขนาดจุดเล็ก ในขณะที่ลำแสงที่โฟกัสไม่โฟกัสอาจเหมาะสำหรับรอยเชื่อมที่กว้างและตื้น
- ระยะเวลาของพัลส์ (ในการเชื่อมด้วยเลเซอร์แบบพัลส์): ระยะเวลาของพัลส์ส่งผลต่อปริมาณพลังงานที่ส่งในแต่ละพัลส์ พัลส์ที่สั้นจะช่วยลดปริมาณความร้อนที่ป้อนเข้ามาและลดความเสี่ยงของการเสียรูป ทำให้เหมาะอย่างยิ่งสำหรับวัสดุที่บอบบางหรือไวต่อความร้อน พัลส์ที่ยาวขึ้นจะทำให้เจาะทะลุได้มากขึ้นแต่ก็อาจเพิ่มความเสี่ยงของข้อบกพร่อง เช่น การกระเด็นและรูพรุน
การออกแบบร่วมกัน
การออกแบบและการเตรียมข้อต่อสามารถส่งผลอย่างมากต่อคุณภาพของการเชื่อมและความเป็นไปได้ของข้อบกพร่อง
- ความคลาดเคลื่อนในการติดตั้ง: การติดตั้งรอยต่ออย่างถูกต้องถือเป็นสิ่งสำคัญในการทำให้รอยเชื่อมมีคุณภาพสม่ำเสมอ ช่องว่างหรือการจัดตำแหน่งที่ไม่ถูกต้องระหว่างชิ้นงานอาจส่งผลให้การหลอมเหลวขาดความพรุนหรือการเจาะทะลุไม่สม่ำเสมอ การติดตั้งให้แน่นหนาจะช่วยให้ควบคุมแอ่งหลอมเหลวได้ดีขึ้นและลดความเสี่ยงของข้อบกพร่อง
- ประเภทของข้อต่อ: ประเภทของข้อต่อที่แตกต่างกัน (เช่น รอยต่อแบบชน รอยต่อแบบทับ รอยต่อแบบร่อง) ต้องใช้เทคนิคและพารามิเตอร์การเชื่อมด้วยเลเซอร์ที่แตกต่างกัน ตัวอย่างเช่น รอยต่อแบบชนที่มีการจัดตำแหน่งที่ไม่ดีอาจทำให้เกิดรอยตัดด้านล่างหรือการเชื่อมขาด ในขณะที่รอยต่อแบบทับที่มีการทับซ้อนกันมากเกินไปอาจทำให้เกิดการกระเด็นและการหลอมรวมที่ไม่เพียงพอ
- การเข้าถึง: ในโครงสร้างที่ซับซ้อน การเข้าถึงข้อต่อที่จำกัดอาจทำให้ระยะของลำแสงเลเซอร์ถูกจำกัด ส่งผลให้การหลอมรวมไม่สมบูรณ์หรือเกิดการสร้างลูกปัดที่ไม่สม่ำเสมอ จำเป็นต้องมีอุปกรณ์จับยึดและการจัดตำแหน่งเลเซอร์ที่เหมาะสมกับข้อต่อที่เข้าถึงได้จำกัด
- การเตรียมและทำความสะอาด: การเตรียมและทำความสะอาดบริเวณข้อต่ออย่างถูกต้องถือเป็นสิ่งสำคัญ เนื่องจากสิ่งปนเปื้อนบนพื้นผิวอาจทำให้เกิดรูพรุน รอยแตกร้าว และการกระเด็น การทำความสะอาดจะช่วยขจัดออกไซด์ น้ำมัน และสิ่งสกปรกอื่นๆ ที่อาจขัดขวางการหลอมรวมและทำให้เกิดข้อบกพร่อง
ปัจจัยด้านสิ่งแวดล้อม
สภาพแวดล้อมในพื้นที่เชื่อมสามารถส่งผลโดยตรงต่อคุณภาพของการเชื่อมและการเกิดข้อบกพร่องได้
- อุณหภูมิแวดล้อม: การเชื่อมในอุณหภูมิที่รุนแรง ไม่ว่าจะเย็นหรือร้อนเกินไป อาจส่งผลต่ออัตราการเย็นตัวของรอยเชื่อม และนำไปสู่ความเครียดจากความร้อนและการแตกร้าว ตัวอย่างเช่น สภาพแวดล้อมที่เย็นจัดอาจทำให้เย็นตัวลงอย่างรวดเร็ว ส่งผลให้รอยเชื่อมเปราะและแตกร้าว
- ความชื้นและความชื้น: ความชื้นในสิ่งแวดล้อมสามารถปล่อยไฮโดรเจนเข้าไปในแอ่งเชื่อม ทำให้มีความเสี่ยงต่อการเกิดรูพรุนและการแตกร้าวที่เกิดจากไฮโดรเจนมากขึ้น การเชื่อมในสภาพแวดล้อมที่แห้งและควบคุมได้ หรือการป้องกันการสัมผัสความชื้นถือเป็นสิ่งสำคัญสำหรับการเชื่อมที่มีคุณภาพสูง
- คุณภาพและการไหลของก๊าซป้องกัน: ก๊าซป้องกันจะปกป้องแอ่งเชื่อมที่หลอมละลายจากการปนเปื้อนในชั้นบรรยากาศ การไหลของก๊าซป้องกันที่ไม่เพียงพอหรือการใช้ก๊าซที่มีความบริสุทธิ์ต่ำอาจทำให้เกิดการออกซิเดชัน ความพรุน และการเปลี่ยนสี นอกจากนี้ ควรใช้ก๊าซป้องกัน เช่น อาร์กอนและฮีเลียม ตามความต้องการของวัสดุเพื่อป้องกันการปนเปื้อน
- การสั่นสะเทือนและการเคลื่อนไหว: การสั่นสะเทือนจากสิ่งแวดล้อมหรือการเคลื่อนไหวในการติดตั้งเครื่องเชื่อมอาจส่งผลให้รอยเชื่อมไม่สม่ำเสมอและเกิดข้อบกพร่องอื่นๆ การติดตั้งอุปกรณ์ให้มั่นคงและลดการเคลื่อนไหวภายนอกให้เหลือน้อยที่สุดถือเป็นสิ่งสำคัญเพื่อให้มั่นใจว่าจะได้ผลลัพธ์ที่สม่ำเสมอ
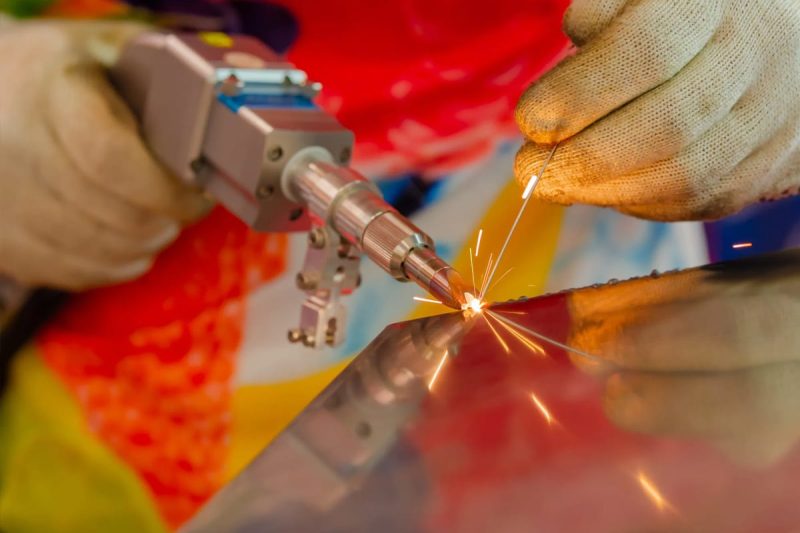
ข้อควรพิจารณาเพิ่มเติมและแนวทางปฏิบัติที่ดีที่สุด
การเลือกใช้วัสดุอย่างเหมาะสม
การเลือกวัสดุที่เหมาะสมสำหรับการเชื่อมเลเซอร์ถือเป็นสิ่งสำคัญเพื่อให้ได้การเชื่อมที่มีคุณภาพสูงและลดข้อบกพร่องให้น้อยที่สุด
- ความเข้ากันได้ของวัสดุ: ตรวจสอบให้แน่ใจว่าวัสดุฐานเข้ากันได้กับการเชื่อมด้วยเลเซอร์ วัสดุต่างๆ ตอบสนองต่อพลังงานเลเซอร์แตกต่างกันเนื่องจากจุดหลอมเหลว การนำความร้อน และการสะท้อนแสงที่แตกต่างกัน ตัวอย่างเช่น วัสดุสะท้อนแสง เช่น อะลูมิเนียม อาจต้องใช้มาตรการพิเศษเพื่อลดการสะท้อนแสงและเพิ่มประสิทธิภาพการดูดซับความร้อน
- ความบริสุทธิ์ของวัสดุ: ใช้วัสดุที่มีสิ่งเจือปนในระดับต่ำ เช่น กำมะถันและฟอสฟอรัส ซึ่งอาจทำให้เกิดรูพรุน แตกร้าว และข้อบกพร่องอื่นๆ ได้
- ความหนาของวัสดุ: พิจารณาความหนาของวัสดุที่จะเชื่อม เนื่องจากมีผลต่อกำลังเลเซอร์และความร้อนที่ต้องใช้
ประเภทและการตั้งค่าเลเซอร์
การเลือกประเภทเลเซอร์ที่เหมาะสมและปรับแต่งการตั้งค่าให้เหมาะสมถือเป็นปัจจัยสำคัญสำหรับการเชื่อมด้วยเลเซอร์ที่ประสบความสำเร็จ
- ประเภทเลเซอร์: เลือกได้ระหว่างเลเซอร์แบบคลื่นต่อเนื่อง (CW) และเลเซอร์แบบพัลส์ตามการใช้งาน เลเซอร์แบบ CW เหมาะอย่างยิ่งสำหรับการเชื่อมความเร็วสูง ในขณะที่เลเซอร์แบบพัลส์เหมาะสำหรับชิ้นส่วนที่บอบบางหรือไวต่อความร้อน
- การตั้งค่ากำลังและความเร็ว: ปรับกำลังเลเซอร์ ความเร็วในการเดินทาง และระยะเวลาของพัลส์ให้เหมาะสม เพื่อให้ได้การเจาะทะลุตามต้องการ ลดข้อบกพร่อง เช่น การกระเซ็นหรือรูพรุน และควบคุมปริมาณความร้อนที่เข้ามา
- โฟกัสและตำแหน่งของลำแสง: การจัดตำแหน่งและโฟกัสของลำแสงที่เหมาะสมมีความจำเป็นสำหรับการกระจายพลังงานที่สม่ำเสมอและการเชื่อมที่สม่ำเสมอ
การออกแบบและประกอบข้อต่อ
การออกแบบข้อต่อและการประกอบที่ถูกต้องจะช่วยให้ได้คุณภาพการเชื่อมที่สม่ำเสมอและลดโอกาสที่เกิดข้อบกพร่อง เช่น การขาดการหลอมรวม ความพรุน และการจัดตำแหน่งที่ไม่ถูกต้อง
- ความคลาดเคลื่อนในการติดตั้ง: ตรวจสอบให้แน่ใจว่าข้อต่อมีการติดตั้งที่แน่นหนาและสม่ำเสมอ ลดช่องว่างที่อาจทำให้การหลอมรวมที่ไม่สม่ำเสมอหรือรูพรุน
- การเข้าถึงข้อต่อ: ออกแบบข้อต่อเพื่อให้ลำแสงเลเซอร์เข้าถึงได้ง่าย ลดความเสี่ยงของการหลอมรวมที่ไม่สมบูรณ์หรือลูกปัดที่ไม่สม่ำเสมอ
- การเตรียมข้อต่อ: ทำความสะอาดและเตรียมพื้นผิวข้อต่ออย่างถูกต้องเพื่อขจัดสิ่งปนเปื้อน เช่น น้ำมัน ออกไซด์ และสิ่งเจือปนอื่นๆ
การเลือกใช้ก๊าซป้องกัน
ก๊าซป้องกันช่วยปกป้องแอ่งเชื่อมที่หลอมละลายจากการปนเปื้อนในบรรยากาศ ป้องกันการเกิดออกซิเดชัน ความพรุน และข้อบกพร่องอื่นๆ
- ประเภทก๊าซ: เลือกก๊าซป้องกันที่เหมาะสม เช่น อาร์กอน ฮีเลียม หรือส่วนผสม โดยพิจารณาจากวัสดุพื้นฐานและลักษณะการเชื่อมที่ต้องการ ตัวอย่างเช่น อาร์กอนมักใช้กับสแตนเลส ในขณะที่ฮีเลียมสามารถปรับปรุงการแทรกซึมสำหรับวัสดุที่หนากว่าได้
- อัตราการไหล: ตรวจสอบให้แน่ใจว่าอัตราการไหลของก๊าซป้องกันเพียงพอที่จะครอบคลุมแอ่งเชื่อมโดยไม่เกิดการปั่นป่วนหรือการครอบคลุมที่ไม่เพียงพอ
- ความบริสุทธิ์: ใช้ก๊าซป้องกันที่มีความบริสุทธิ์สูงเพื่อหลีกเลี่ยงการปนเปื้อน
การบำบัดก่อนและหลังการเชื่อม
การบำบัดก่อนและหลังการเชื่อมสามารถลดโอกาสเกิดข้อบกพร่องและปรับปรุงคุณภาพการเชื่อมโดยรวมได้อย่างมาก
- การทำความสะอาดก่อนเชื่อม: ทำความสะอาดชิ้นงานอย่างทั่วถึงเพื่อขจัดสิ่งปนเปื้อน เช่น น้ำมัน สนิม และความชื้น ซึ่งอาจทำให้เกิดรูพรุน รอยแตกร้าว และข้อบกพร่องอื่นๆ
- การอุ่นล่วงหน้า: การอุ่นล่วงหน้าวัสดุ โดยเฉพาะอย่างยิ่งวัสดุที่มีแนวโน้มจะแตกร้าว สามารถลดการกระจายความร้อนและลดความเค้นตกค้างให้เหลือน้อยที่สุด
- การอบชุบด้วยความร้อนหลังการเชื่อม: ทำการอบชุบด้วยความร้อนหลังการเชื่อม เช่น การอบอ่อนหรือการบรรเทาความเค้น เพื่อลดความเค้นที่เหลืออยู่และปรับปรุงคุณสมบัติเชิงกลของรอยเชื่อม
การฝึกอบรมผู้ปฏิบัติงาน
ผู้ปฏิบัติงานที่มีทักษะมีบทบาทสำคัญในการรับประกันการเชื่อมเลเซอร์ให้มีคุณภาพสูงและสม่ำเสมอ
- การฝึกอบรมด้านเทคนิค: ฝึกอบรมผู้ปฏิบัติงานเกี่ยวกับการจัดการอุปกรณ์เชื่อมเลเซอร์อย่างถูกต้อง รวมถึงการวางตำแหน่ง การควบคุมความเร็ว และการปรับพารามิเตอร์
- การระบุข้อบกพร่อง: ให้ความรู้แก่ผู้ปฏิบัติงานในการจดจำข้อบกพร่องทั่วไป สาเหตุ และวิธีการปรับปรุงที่จำเป็นเพื่อป้องกันไม่ให้เกิดขึ้นซ้ำ
- โปรโตคอลความปลอดภัย: ให้แน่ใจว่าผู้ปฏิบัติงานได้รับการฝึกอบรมเกี่ยวกับขั้นตอนความปลอดภัยของเลเซอร์เพื่อปกป้องตนเองและสภาพแวดล้อมการทำงาน
การบำรุงรักษาอุปกรณ์
การบำรุงรักษาอุปกรณ์เชื่อมเลเซอร์อย่างสม่ำเสมอเป็นสิ่งสำคัญเพื่อให้มั่นใจถึงประสิทธิภาพที่สม่ำเสมอและป้องกันข้อบกพร่อง
- การทำความสะอาดเลนส์: ทำความสะอาดเลนส์ กระจก และส่วนประกอบออปติกอื่นๆ เป็นประจำเพื่อรักษาคุณภาพและความแม่นยำของลำแสง
- การสอบเทียบ: สอบเทียบระบบเลเซอร์เป็นระยะเพื่อให้แน่ใจว่ากำลังส่งออก การจัดตำแหน่งลำแสง และการโฟกัสมีความแม่นยำ
- การตรวจสอบส่วนประกอบ: ตรวจสอบและเปลี่ยนส่วนประกอบที่สึกหรอหรือเสียหาย เช่น หัวฉีดและเลนส์ เพื่อรักษาความสม่ำเสมอของการเชื่อม
การติดตามกระบวนการ
การตรวจสอบและควบคุมกระบวนการมีความสำคัญต่อการบรรลุการเชื่อมที่สม่ำเสมอและปราศจากข้อบกพร่อง
- การตรวจสอบแบบเรียลไทม์: ใช้เซ็นเซอร์และระบบตรวจสอบเพื่อตรวจจับและแก้ไขความเบี่ยงเบนในพารามิเตอร์การเชื่อม เช่น ความผันผวนของพลังงาน ความเร็วในการเดินทาง และโฟกัสของลำแสง แบบเรียลไทม์
- การบันทึกข้อมูล: บันทึกพารามิเตอร์และผลลัพธ์การเชื่อมเพื่อวิเคราะห์แนวโน้ม ระบุสาเหตุหลักของข้อบกพร่อง และนำมาตรการปรับปรุงอย่างต่อเนื่องมาใช้
- การตรวจสอบคุณภาพ: ดำเนินการตรวจสอบเป็นประจำ รวมถึงวิธีการทดสอบแบบไม่ทำลาย (NDT) เพื่อตรวจสอบคุณภาพของการเชื่อม
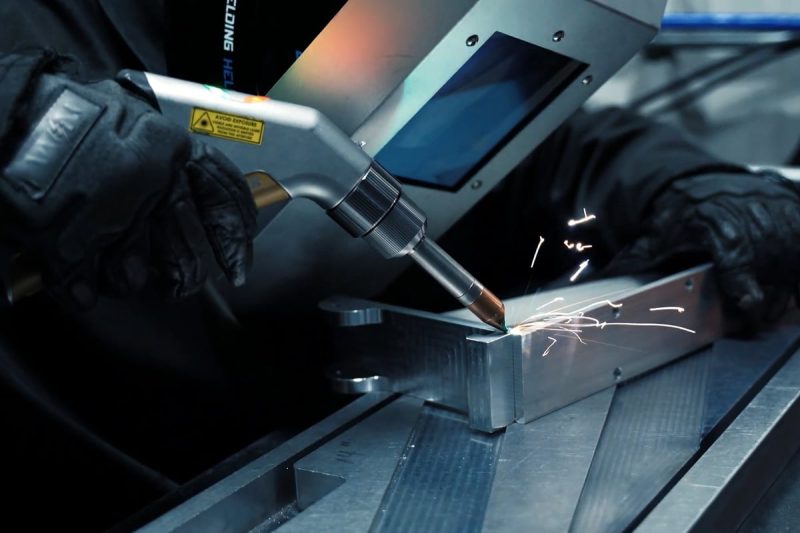
สรุป
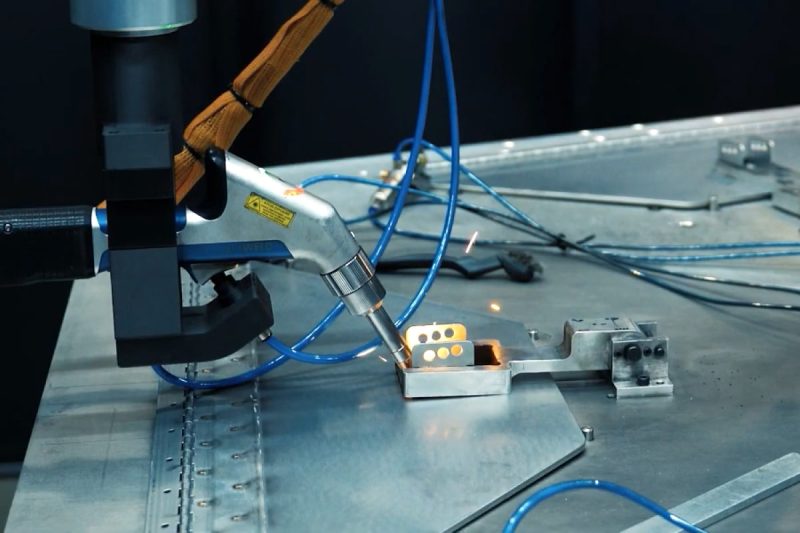
รับโซลูชั่นการเชื่อมด้วยเลเซอร์
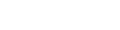
- [email protected]
- [email protected]
- +86-19963414011
- หมายเลข 3 โซน A เขตอุตสาหกรรม Luzhen เมือง Yucheng มณฑลซานตง