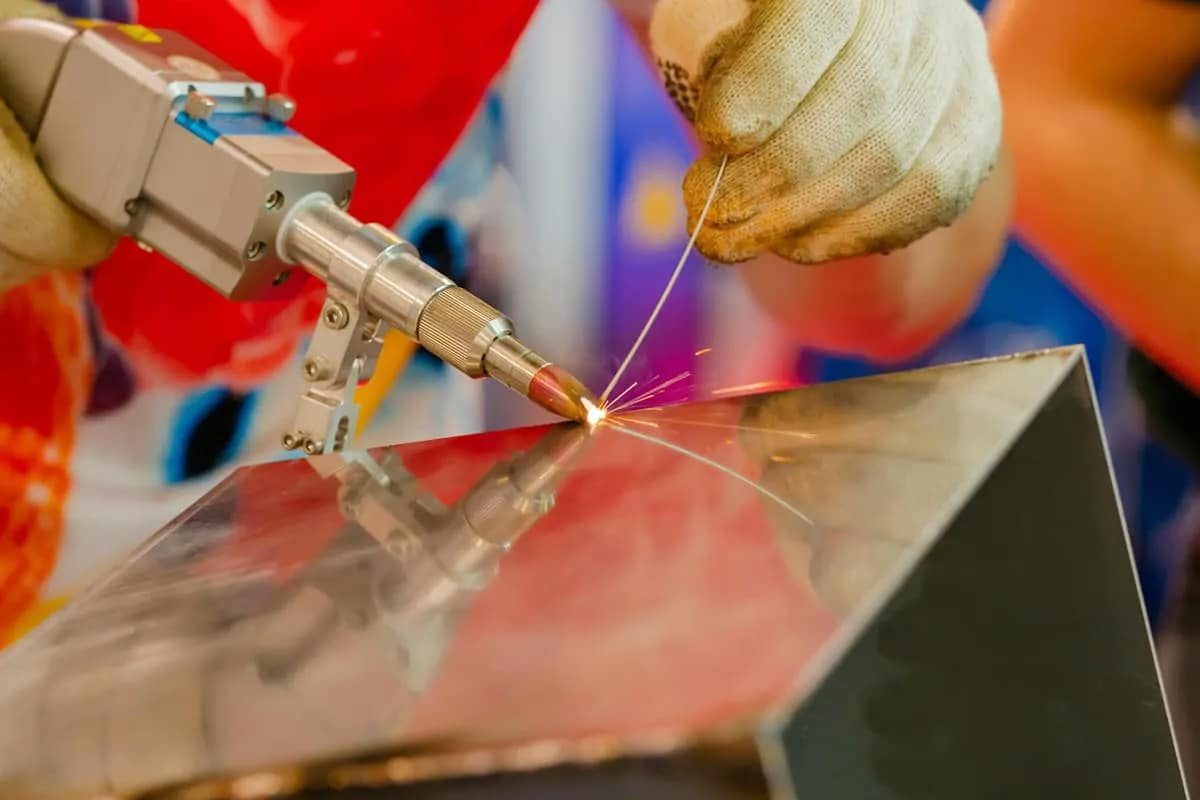
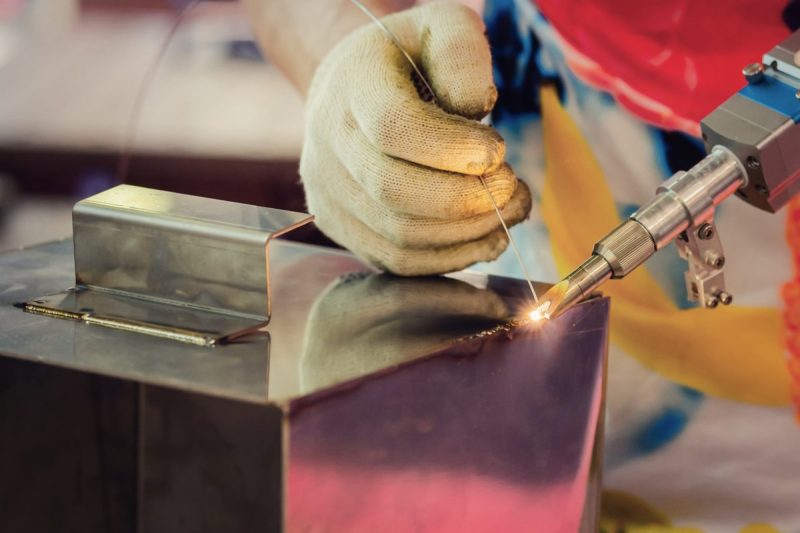
พารามิเตอร์เลเซอร์
พลังเลเซอร์
กำลังเลเซอร์เป็นตัวแปรพื้นฐานในการเชื่อมด้วยเลเซอร์และกำหนดปริมาณพลังงานที่ส่งไปยังพื้นที่เชื่อม การตั้งค่ากำลังส่งผลต่อความเร็วในการเชื่อมและความลึกของการเจาะ
- กำลังสูง: การใช้กำลังเลเซอร์สูงจะเพิ่มความเร็วในการเชื่อมและความลึกในการเจาะ ทำให้สามารถเชื่อมวัสดุที่มีความหนามากขึ้นได้ มีประโยชน์อย่างยิ่งสำหรับการใช้งานที่ต้องการการเชื่อมลึกหรือประสิทธิภาพการผลิตสูง อย่างไรก็ตาม พลังงานที่สูงเกินไปอาจทำให้เกิดความร้อนสูงเกินไป การหลอมเหลวมากเกินไป และข้อบกพร่อง เช่น การกระเด็นและความพรุน
- พลังงานต่ำ: กำลังเลเซอร์ที่ต่ำกว่าเหมาะสำหรับวัสดุที่บางกว่าและการใช้งานที่ต้องการความแม่นยำสูง เช่น การเชื่อมแบบไมโคร อย่างไรก็ตาม กำลังที่ไม่เพียงพออาจส่งผลให้เกิดการเชื่อมที่อ่อนแอเนื่องจากการหลอมเหลวที่ไม่สมบูรณ์หรือการเจาะที่ไม่เพียงพอ
- การเพิ่มประสิทธิภาพ: การได้รับพลังงานเลเซอร์ที่เหมาะสมที่สุดนั้นจำเป็นต้องมีความสมดุลในการเจาะและความเร็ว พร้อมความเสี่ยงต่อข้อบกพร่อง ซึ่งต้องมีการสอบเทียบอย่างระมัดระวังโดยพิจารณาจากประเภทวัสดุ ความหนา และข้อกำหนดในการเชื่อมเฉพาะ
ความยาวคลื่น
ความยาวคลื่นของเลเซอร์ส่งผลต่อการที่วัสดุที่กำลังเชื่อมดูดซับพลังงานเลเซอร์ได้ดีเพียงใด วัสดุที่แตกต่างกันมีลักษณะการดูดกลืนแสงที่แตกต่างกันที่ความยาวคลื่นต่างกัน
- ความยาวคลื่นทั่วไป: ความยาวคลื่นทั่วไปที่ใช้ในการเชื่อมด้วยเลเซอร์ ได้แก่ อินฟราเรด (IR) แสงที่มองเห็นได้ และอัลตราไวโอเลต (UV) แต่ละความยาวคลื่นมีข้อดีของมัน ขึ้นอยู่กับวัสดุและการใช้งาน
- เลเซอร์อินฟราเรด (IR): เลเซอร์ IR เช่น CO2 และเลเซอร์ไฟเบอร์ มักใช้ในการเชื่อมโลหะและมีประสิทธิภาพกับวัสดุที่มีการดูดกลืนแสงสูงในสเปกตรัมอินฟราเรด
- เลเซอร์ที่มองเห็นได้และเลเซอร์ยูวี: ความยาวคลื่นเหล่านี้ถูกดูดซับได้ง่ายขึ้นโดยอโลหะและโลหะสะท้อนแสงบางชนิด ทำให้มีประโยชน์สำหรับการใช้งานที่เกี่ยวข้องกับพลาสติกและเซรามิก
- ข้อควรพิจารณาเฉพาะวัสดุ: วัสดุ เช่น อลูมิเนียมและทองแดงที่มีการสะท้อนแสงสูงในช่วงอินฟราเรดอาจต้องใช้เลเซอร์ที่มีความยาวคลื่นซึ่งโลหะเหล่านี้ดูดซับได้ง่ายกว่า การเคลือบพิเศษหรือแหล่งกำเนิดเลเซอร์ที่มีความยาวคลื่นเฉพาะสามารถเพิ่มประสิทธิภาพการดูดซับและการเชื่อมได้
ระยะเวลาและความถี่ของพัลส์
ระยะเวลาและความถี่ของพัลส์เป็นตัวแปรสำคัญในการเชื่อมด้วยพัลส์เลเซอร์ โดยที่เลเซอร์ทำงานในพัลส์สั้นแทนที่จะเป็นคลื่นต่อเนื่อง
- ระยะเวลาพัลส์: ความยาวของพัลส์เลเซอร์แต่ละตัวสามารถส่งผลกระทบอย่างมากต่อคุณลักษณะทางความร้อนของการเชื่อม พัลส์ที่สั้นกว่าจะส่งพลังงานในช่วงสั้นๆ และระเบิดที่รุนแรง ช่วยลดโซนที่ได้รับผลกระทบจากความร้อน (HAZ) และลดการเสียรูปเนื่องจากความร้อน ระยะเวลาการเต้นของชีพจรที่นานขึ้นจะให้พลังงานมากขึ้น แต่สามารถเพิ่ม HAZ และความเสี่ยงต่อความเสียหายจากความร้อนได้
- ความถี่พัลส์: ความถี่ของพัลส์หรือจำนวนพัลส์ต่อวินาที ส่งผลต่อการส่งพลังงานโดยรวมและความเร็วการเชื่อม ความถี่ที่สูงขึ้นสามารถเพิ่มความเร็วในการเชื่อม แต่ยังเพิ่มความเสี่ยงของการสะสมความร้อนสะสม ซึ่งอาจทำให้เกิดข้อบกพร่องได้
- การเพิ่มประสิทธิภาพ: การผสมผสานระหว่างระยะเวลาและความถี่ของพัลส์ต้องได้รับการปรับให้เหมาะสมโดยพิจารณาจากคุณสมบัติของวัสดุและลักษณะการเชื่อมที่ต้องการ การปรับพารามิเตอร์เหล่านี้อย่างละเอียดจะช่วยให้เกิดความสมดุลระหว่างความเร็วการเชื่อม การเจาะทะลุ และผลกระทบจากความร้อน
คุณภาพของลำแสง
คุณภาพของลำแสงเลเซอร์ถูกกำหนดโดยพารามิเตอร์ต่างๆ เช่น โครงสร้างโหมดและโปรไฟล์ลำแสง ซึ่งส่งผลโดยตรงต่อประสิทธิภาพการเชื่อม
- โหมดลำแสง: โหมดของลำแสงเลเซอร์ (เช่น TEM00) จะกำหนดการกระจายความเข้มของแสง โครงสร้างโหมดคุณภาพสูงช่วยให้มั่นใจได้ถึงการส่งพลังงานที่เข้มข้นและสม่ำเสมอ ส่งผลให้การเชื่อมสม่ำเสมอและแม่นยำ
- โปรไฟล์ลำแสง: โปรไฟล์ลำแสงที่สม่ำเสมอและมีการกำหนดไว้อย่างดีจะช่วยลดการสูญเสียพลังงานและรับประกันการส่งพลังงานสูงสุดไปยังบริเวณรอยเชื่อม คุณภาพของลำแสงต่ำ (มีลักษณะพิเศษคือโปรไฟล์ที่บิดเบี้ยวหรือไม่สม่ำเสมอ) ส่งผลให้เกิดความร้อนที่ไม่สม่ำเสมอและข้อบกพร่องในการเชื่อม
- ความเป็นไปได้: คุณภาพลำแสงสูงช่วยให้สามารถโฟกัสได้ดีขึ้น ช่วยให้เลเซอร์ได้ขนาดลำแสงที่เล็กลงสำหรับการใช้งานที่ต้องการความแม่นยำสูงและรายละเอียดที่ละเอียด
ตำแหน่งโฟกัส
ตำแหน่งของจุดโฟกัสเลเซอร์ที่สัมพันธ์กับพื้นผิวของวัสดุเป็นตัวแปรสำคัญที่ส่งผลต่อประสิทธิภาพและคุณภาพของการเชื่อม
- โฟกัสที่ถูกต้อง: การโฟกัสลำแสงเลเซอร์อย่างถูกต้องบนพื้นที่เชื่อมทำให้มั่นใจได้ถึงความหนาแน่นของพลังงานสูงสุดและการหลอมเหลวของวัสดุอย่างมีประสิทธิภาพ ตำแหน่งโฟกัสที่เหมาะสมที่สุดขึ้นอยู่กับความหนาของวัสดุและลักษณะการเชื่อมที่ต้องการ สำหรับการเชื่อมแบบเจาะลึก จุดโฟกัสมักจะอยู่ใต้พื้นผิววัสดุเล็กน้อย
- ความยาวโฟกัส: ความยาวโฟกัสของเลนส์เลเซอร์จะกำหนดความลึกโฟกัสและขนาดโฟกัส ทางยาวโฟกัสสั้นทำให้ขนาดจุดเล็กลงและมีความหนาแน่นของพลังงานสูงขึ้นสำหรับงานเชื่อมละเอียด ทางยาวโฟกัสที่ยาวขึ้นจะให้ความลึกโฟกัสที่มากขึ้น ซึ่งเป็นประโยชน์สำหรับการเชื่อมวัสดุที่มีความหนามากขึ้น
- ความทนทานต่อการโฟกัส: การรักษาตำแหน่งโฟกัสที่สม่ำเสมอสามารถช่วยให้ได้คุณภาพการเชื่อมที่สม่ำเสมอ ความแปรผันของตำแหน่งโฟกัสอาจส่งผลให้เกิดการเจาะที่ไม่สอดคล้องกัน การหลอมรวมที่ไม่สมบูรณ์ และข้อบกพร่อง ระบบอัตโนมัติที่มีการปรับโฟกัสแบบเรียลไทม์สามารถช่วยรักษาโฟกัสที่เหมาะสมที่สุดในระหว่างกระบวนการเชื่อมได้
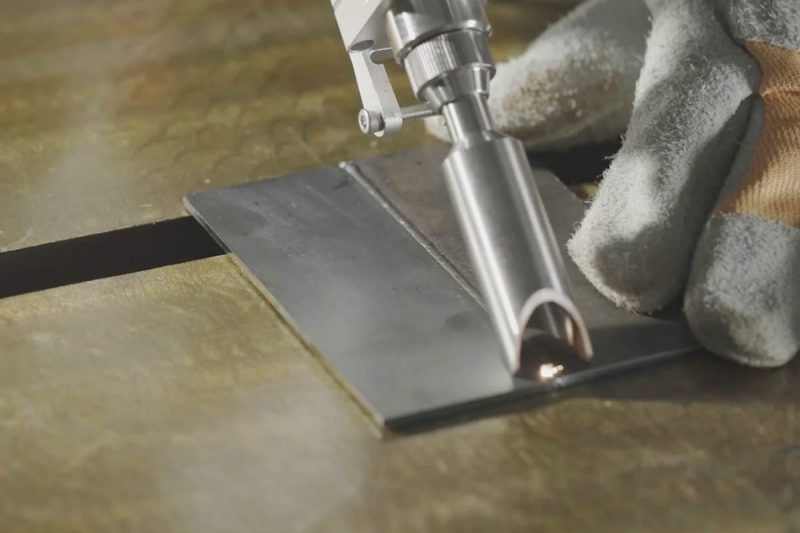
คุณสมบัติของวัสดุ
ประเภทวัสดุ
ประเภทของวัสดุที่ทำการเชื่อมเป็นปัจจัยหลักในการพิจารณาประสิทธิภาพการเชื่อมด้วยเลเซอร์ วัสดุที่แตกต่างกันดูดซับและนำพลังงานเลเซอร์ในรูปแบบที่แตกต่างกัน ซึ่งส่งผลต่อคุณภาพการเชื่อมและพารามิเตอร์กระบวนการ
- โลหะ: โลหะเชื่อมทั่วไป ได้แก่ เหล็ก อลูมิเนียม ไทเทเนียม และทองแดง โลหะแต่ละชนิดมีคุณสมบัติที่แตกต่างกัน:
- เหล็ก: โดยทั่วไปสามารถเชื่อมด้วยเลเซอร์ได้ดีเนื่องจากการดูดซับพลังงานเลเซอร์ได้ดี เหล็กหลายเกรด รวมถึงเหล็กกล้าคาร์บอน สแตนเลส และโลหะผสม อาจต้องใช้การตั้งค่าเลเซอร์ที่แตกต่างกัน
- อลูมิเนียม: อลูมิเนียมมีชื่อเสียงในด้านความสามารถในการสะท้อนแสงและการนำความร้อนสูง และการเชื่อมอลูมิเนียมด้วยเลเซอร์อาจเป็นเรื่องท้าทาย ความยาวคลื่นหรือสารเคลือบพิเศษสามารถปรับปรุงการดูดกลืนแสงได้
- ไทเทเนียม: ไทเทเนียมสามารถเชื่อมได้อย่างมีประสิทธิภาพด้วยเลเซอร์เนื่องจากมีการสะท้อนแสงและคุณสมบัติทางความร้อนปานกลาง มีการใช้กันอย่างแพร่หลายในด้านการบินและอวกาศและการแพทย์
- ทองแดง: การสะท้อนแสงและการนำความร้อนสูงของทองแดงทำให้ยากต่อการเชื่อมด้วยการตั้งค่าเลเซอร์แบบดั้งเดิม ไฟเบอร์เลเซอร์ที่มีความยาวคลื่นเฉพาะมักใช้เพื่อปรับปรุงประสิทธิภาพ
- อโลหะ: วัสดุ เช่น พลาสติก เซรามิก และวัสดุคอมโพสิตสามารถเชื่อมด้วยเลเซอร์ได้ อโลหะแต่ละตัวต้องใช้พารามิเตอร์เลเซอร์เฉพาะเพื่อการเชื่อมที่มีประสิทธิภาพ:
- พลาสติก: พลาสติกโดยทั่วไปดูดซับพลังงานเลเซอร์ได้ดี แต่คุณสมบัติทางความร้อนจำเป็นต้องมีการควบคุมพารามิเตอร์การเชื่อมอย่างระมัดระวังเพื่อหลีกเลี่ยงการไหม้หรือการหลอมละลาย
- เซรามิกส์: เซรามิกส์เปราะและอาจแตกร้าวได้ภายใต้ความเครียดจากความร้อน โดยทั่วไปแล้ว เซรามิกการเชื่อมด้วยเลเซอร์จะต้องมีการอุ่นก่อนและใช้เลเซอร์ที่มีความยาวคลื่นเฉพาะเพื่อลดความเครียด
- คอมโพสิต: คอมโพสิตผสมผสานวัสดุที่แตกต่างกันและต้องมีการปรับพารามิเตอร์อย่างระมัดระวังเพื่อให้แน่ใจว่าคุณภาพการเชื่อมที่สม่ำเสมอบนส่วนประกอบต่างๆ
ความหนา
ความหนาของวัสดุเป็นปัจจัยสำคัญที่ส่งผลต่อประสิทธิภาพของการเชื่อมด้วยเลเซอร์ ซึ่งจะส่งผลต่อกำลังเลเซอร์ที่ต้องการ ความเร็วในการเชื่อม และความเสถียรของกระบวนการโดยรวม
- วัสดุบาง: วัสดุบางต้องใช้พลังงานเลเซอร์ต่ำกว่าและความเร็วในการเชื่อมที่สูงขึ้น เพื่อป้องกันการเผาไหม้และความร้อนที่มากเกินไป การควบคุมพารามิเตอร์เลเซอร์ที่แม่นยำช่วยให้รอยเชื่อมสะอาดปราศจากข้อบกพร่อง
- วัสดุหนา: การเชื่อมวัสดุหนาต้องใช้พลังงานเลเซอร์ที่สูงขึ้นและความเร็วในการเชื่อมที่ช้าลงเพื่อให้แน่ใจว่ามีการเจาะและการหลอมละลายที่เพียงพอ สามารถใช้เทคนิคขั้นสูง เช่น การเชื่อมหลายรอบหรือการเชื่อมแบบไฮบริด (การเชื่อมด้วยเลเซอร์และการเชื่อมอาร์ก) เพื่อให้สามารถเจาะทะลุได้เต็มรูปแบบ
- โซนการเปลี่ยนผ่าน: เมื่อเชื่อมวัสดุที่มีความหนาต่างกัน พารามิเตอร์เลเซอร์จำเป็นต้องได้รับการปรับแบบไดนามิกเพื่อรองรับความแตกต่างในการดูดซับความร้อนและการนำไฟฟ้า
สภาพพื้นผิว
สภาพพื้นผิวของวัสดุอาจส่งผลต่อการดูดกลืนแสงเลเซอร์ การถ่ายเทความร้อน และคุณภาพการเชื่อมโดยรวม การเตรียมพื้นผิวที่เหมาะสมช่วยให้การเชื่อมด้วยเลเซอร์มีประสิทธิภาพ
- ความสะอาด: สารปนเปื้อน เช่น น้ำมัน จาระบี สิ่งสกปรก และชั้นออกไซด์อาจรบกวนการดูดซับของเลเซอร์และทำให้เกิดข้อบกพร่องในการเชื่อม จำเป็นต้องทำความสะอาดพื้นผิวอย่างละเอียดก่อนการเชื่อมเพื่อให้ได้ผลลัพธ์ที่ดีที่สุด
- ความหยาบของพื้นผิว: ความหยาบของพื้นผิวของวัสดุอาจส่งผลต่อปฏิกิริยาของลำแสงเลเซอร์ โดยทั่วไปพื้นผิวที่เรียบกว่าจะส่งผลให้มีการดูดซับเลเซอร์ได้ดีขึ้นและรอยเชื่อมที่สม่ำเสมอยิ่งขึ้น การรักษาพื้นผิว เช่น การขัดเงาหรือการขัดด้วยกรวดสามารถใช้เพื่อปรับปรุงสภาพพื้นผิวได้
- การเคลือบและการบำบัด: วัสดุบางชนิดอาจมีการเคลือบหรือการบำบัดที่ส่งผลต่อการเชื่อมด้วยเลเซอร์ ตัวอย่างเช่น เหล็กชุบสังกะสีมีการเคลือบสังกะสีที่ต้องมีการตั้งค่าเลเซอร์เฉพาะเพื่อป้องกันการระเหยและความพรุน การทำความเข้าใจผลกระทบของการเคลือบเหล่านี้สามารถช่วยปรับพารามิเตอร์การเชื่อมให้เหมาะสมได้
คุณสมบัติทางความร้อน
คุณสมบัติทางความร้อนของวัสดุ รวมถึงการนำความร้อน ความจุความร้อนจำเพาะ และจุดหลอมเหลว ส่งผลต่อวิธีที่วัสดุมีปฏิกิริยากับพลังงานเลเซอร์
- การนำความร้อน: วัสดุที่มีค่าการนำความร้อนสูง เช่น ทองแดงและอะลูมิเนียม จะกระจายความร้อนได้อย่างรวดเร็วและต้องใช้กำลังเลเซอร์ที่สูงขึ้นเพื่อให้ได้ฟิวชั่นที่เหมาะสม วัสดุที่มีค่าการนำความร้อนต่ำ เช่น สแตนเลส จะกักเก็บความร้อนได้นานกว่า ดังนั้นจึงต้องควบคุมความร้อนที่ได้รับอย่างระมัดระวังเพื่อหลีกเลี่ยงการหลอมละลายมากเกินไป
- ความจุความร้อนจำเพาะ: ความจุความร้อนจำเพาะของวัสดุกำหนดปริมาณพลังงานที่ต้องใช้ในการเพิ่มอุณหภูมิ วัสดุที่มีความจุความร้อนจำเพาะสูงต้องใช้พลังงานในการเชื่อมมากกว่า ซึ่งส่งผลต่อการเลือกกำลังเลเซอร์และความเร็วในการเชื่อม
- จุดหลอมเหลว: จุดหลอมเหลวของวัสดุกำหนดปริมาณพลังงานที่ต้องใช้ในการเริ่มต้นการหลอมเหลวและฟิวชัน วัสดุที่มีจุดหลอมเหลวสูง เช่น ไทเทเนียมและโลหะผสมบางชนิด ต้องใช้กำลังเลเซอร์ที่สูงกว่าและการควบคุมพารามิเตอร์การเชื่อมที่แม่นยำเพื่อให้การเชื่อมมีประสิทธิภาพ
สมบัติทางโลหะวิทยา
คุณสมบัติทางโลหะวิทยาของวัสดุ รวมถึงองค์ประกอบ โครงสร้างจุลภาค และการเปลี่ยนเฟส มีบทบาทสำคัญในกระบวนการเชื่อมด้วยเลเซอร์
- ส่วนประกอบ: องค์ประกอบทางเคมีของวัสดุส่งผลต่อความสามารถในการเชื่อม องค์ประกอบโลหะผสมส่งผลต่อการดูดซับพลังงานเลเซอร์ของวัสดุ พฤติกรรมการหลอมเหลว และความไวต่อข้อบกพร่อง เช่น การแตกร้าวและความพรุน การทำความเข้าใจองค์ประกอบจะช่วยเลือกพารามิเตอร์เลเซอร์และก๊าซป้องกันที่เหมาะสม
- โครงสร้างจุลภาค: โครงสร้างจุลภาคของวัสดุ รวมถึงขนาดเกรนและการกระจายเฟส ส่งผลต่อคุณสมบัติทางกลและการตอบสนองต่อการเชื่อม โดยทั่วไปวัสดุเนื้อละเอียดจะเชื่อมได้ดีกว่าวัสดุเนื้อหยาบ ซึ่งอาจต้องได้รับการดูแลเป็นพิเศษเพื่อหลีกเลี่ยงการแตกร้าวและการเสียรูป
- การแปลงเฟส: วัสดุบางชนิดผ่านการเปลี่ยนเฟสระหว่างการเชื่อม ซึ่งอาจส่งผลต่อคุณสมบัติการเชื่อมขั้นสุดท้าย ตัวอย่างเช่น เหล็กบางชนิดเปลี่ยนจากออสเทนไนต์เป็นมาร์เทนไซต์เมื่อเย็นตัวลง ส่งผลให้เกิดการเชื่อมที่แข็งและเปราะ การควบคุมอัตราการทำความเย็นและการบำบัดความร้อนหลังการเชื่อมสามารถช่วยควบคุมการเปลี่ยนแปลงเหล่านี้และปรับปรุงคุณภาพการเชื่อมได้
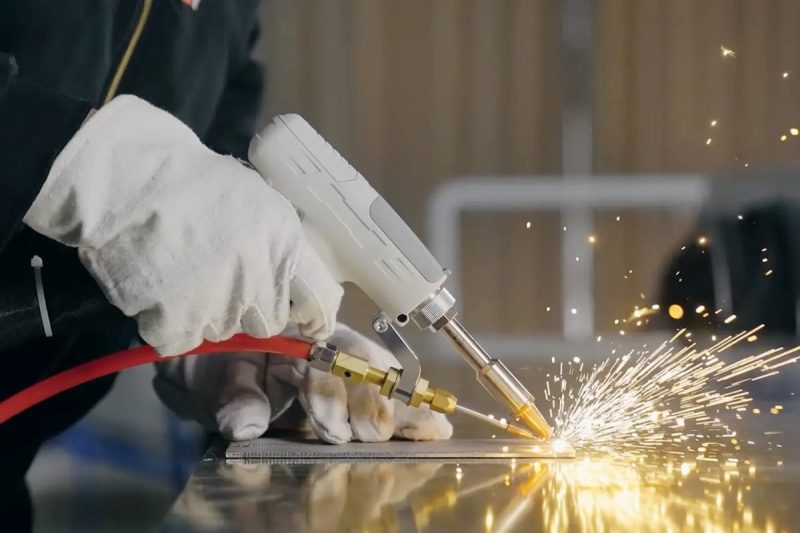
การออกแบบร่วมกัน
การกำหนดค่าร่วม
โครงสร้างข้อต่อมีผลกระทบอย่างมากต่อกระบวนการเชื่อมด้วยเลเซอร์ ข้อต่อประเภทต่างๆ มีระดับการเข้าถึงที่แตกต่างกัน ความง่ายในการเชื่อม และความแข็งแรงทางกล
- ข้อต่อชน: ในข้อต่อชน จะมีการวางวัสดุสองชิ้นแบบจรดขอบ การกำหนดค่านี้เป็นเรื่องปกติในการเชื่อมด้วยเลเซอร์เนื่องจากง่ายและช่วยให้สามารถเจาะลึกได้ อย่างไรก็ตาม การจัดตำแหน่งที่แม่นยำและช่องว่างน้อยที่สุดเท่านั้นที่จะรับประกันการเชื่อมคุณภาพสูงได้
- ข้อต่อตัก: ในข้อต่อตัก วัสดุชิ้นหนึ่งทับซ้อนกัน การกำหนดค่านี้มักใช้ในการเชื่อมวัสดุบางและประกอบได้ง่าย อย่างไรก็ตาม จำเป็นต้องมีการควบคุมพารามิเตอร์เลเซอร์อย่างระมัดระวังเพื่อหลีกเลี่ยงการหลอมเหลวมากเกินไป และให้แน่ใจว่าสองชั้นหลอมรวมเข้าด้วยกันอย่างเหมาะสม
- T-Joint: ข้อต่อ T เกิดขึ้นจากการเชื่อมวัสดุชิ้นหนึ่งตั้งฉากกับอีกชิ้นหนึ่ง การกำหนดค่านี้มักใช้ในการใช้งานเชิงโครงสร้าง ความท้าทายของข้อต่อตัว T คือการเจาะทะลุที่สม่ำเสมอและหลีกเลี่ยงข้อบกพร่องที่ทางแยก
- ข้อต่อมุม: ข้อต่อมุมใช้สำหรับเชื่อมต่อวัสดุสองชิ้นที่มุมฉาก มักใช้ในโครงสร้างและกรอบคล้ายกล่อง การตรวจสอบให้แน่ใจว่าฟิวชั่นที่เหมาะสมที่มุมจำเป็นต้องมีการควบคุมพารามิเตอร์เลเซอร์และการเตรียมข้อต่ออย่างแม่นยำ
- ข้อต่อขอบ: ข้อต่อขอบเกี่ยวข้องกับการเชื่อมตามขอบของวัสดุชิ้นเดียวหรือทั้งสองชิ้น การกำหนดค่านี้เหมาะสำหรับวัสดุบางและการใช้งานที่ต้องการการทับซ้อนกันน้อยที่สุด การบรรลุรอยเชื่อมที่สม่ำเสมอในข้อต่อขอบจำเป็นต้องมีการจัดตำแหน่งที่แม่นยำและการควบคุมช่องว่าง
การเตรียมการร่วมกัน
การเตรียมข้อต่ออย่างเหมาะสมช่วยให้ได้งานเชื่อมคุณภาพสูง สภาพของพื้นผิวรอยต่อส่งผลโดยตรงต่อการดูดซับเลเซอร์ การถ่ายเทความร้อน และความสมบูรณ์ของการเชื่อมโดยรวม
- ความสะอาด: พื้นผิวข้อต่อต้องปราศจากสิ่งปนเปื้อน เช่น น้ำมัน จาระบี สิ่งสกปรก และออกไซด์ สารปนเปื้อนอาจรบกวนการดูดซับของเลเซอร์และทำให้เกิดข้อบกพร่อง เช่น ความพรุนและการหลอมรวมที่ไม่สมบูรณ์ สามารถใช้วิธีการทำความสะอาด เช่น การล้างไขมัน การแปรงลวด และการทำความสะอาดด้วยสารเคมี ทั้งนี้ขึ้นอยู่กับวัสดุและสิ่งปนเปื้อนที่มีอยู่
- การรักษาพื้นผิว: การรักษาพื้นผิว เช่น การพ่นทราย การเจียร หรือการตัดเฉือน สามารถปรับปรุงสภาพพื้นผิวและเพิ่มการดูดซับเลเซอร์ได้ การรักษาเหล่านี้ช่วยสร้างพื้นผิวที่เรียบสม่ำเสมอและลดความเสี่ยงต่อการเกิดข้อบกพร่อง
- การเตรียมขอบ: การเตรียมขอบที่เหมาะสมช่วยให้มั่นใจว่ามีขนาดพอดีและลดช่องว่างให้เหลือน้อยที่สุด เทคนิคต่างๆ เช่น การเอียง การลบมุม และการปัดเศษของขอบสามารถปรับปรุงความพอดีของข้อต่อและส่งเสริมการหลอมรวมที่ดีขึ้น
ความอดทนช่องว่าง
การรักษาความคลาดเคลื่อนของช่องว่างที่แคบสามารถช่วยให้ได้การเชื่อมเลเซอร์ที่สม่ำเสมอและมีคุณภาพสูง ช่องว่างระหว่างพื้นผิวข้อต่ออาจส่งผลให้เกิดการหลอมรวมที่ไม่สมบูรณ์ รอยเชื่อมที่อ่อนแอ และข้อบกพร่อง
- ช่องว่างขั้นต่ำ: ตามหลักการแล้ว พื้นผิวข้อต่อควรมีช่องว่างขั้นต่ำเพื่อให้แน่ใจว่ามีการหลอมรวมอย่างสมบูรณ์และรอยเชื่อมแข็งแรง ช่องว่างเล็กๆ สามารถเชื่อมเข้าด้วยกันได้ด้วยวัสดุที่หลอมละลาย แต่ช่องว่างที่มากเกินไปอาจส่งผลให้เกิดการหลอมรวมที่ไม่สมบูรณ์และข้อต่อที่อ่อนแอ
- ความคลาดเคลื่อนที่อนุญาต: ความคลาดเคลื่อนของช่องว่างที่อนุญาตนั้นขึ้นอยู่กับวัสดุ โครงร่างข้อต่อ และพารามิเตอร์การเชื่อม โดยทั่วไป การใช้งานที่มีความแม่นยำสูงและวัสดุบางจำเป็นต้องมีพิกัดความเผื่อที่เข้มงวดมากขึ้น ในขณะที่วัสดุที่หนากว่าสามารถทนต่อช่องว่างที่ใหญ่กว่าเล็กน้อยได้
- การปรับเปลี่ยน: หากมีช่องว่าง การปรับกำลังเลเซอร์ ความเร็วในการเชื่อม และตำแหน่งโฟกัสสามารถช่วยชดเชยและรับประกันฟิวชั่นที่เพียงพอ อย่างไรก็ตาม ควรหลีกเลี่ยงช่องว่างที่มากเกินไป เนื่องจากอาจส่งผลต่อคุณภาพและความแข็งแรงของการเชื่อม
อุปกรณ์จับยึดและการหนีบ
อุปกรณ์จับยึดและอุปกรณ์จับยึดที่มีประสิทธิภาพสามารถรับประกันความเสถียรและการจัดตำแหน่งของข้อต่อในระหว่างกระบวนการเชื่อมด้วยเลเซอร์ อุปกรณ์จับยึดและอุปกรณ์จับยึดที่เหมาะสมจะป้องกันการเคลื่อนตัว การเสียรูป และการวางแนวที่ไม่ตรง ซึ่งจะช่วยปรับปรุงประสิทธิภาพและคุณภาพของการเชื่อม
- ความเสถียร: ฟิกซ์เจอร์จะต้องยึดวัสดุให้อยู่กับที่อย่างแน่นหนา เพื่อป้องกันการเคลื่อนไหวใด ๆ ในระหว่างกระบวนการเชื่อม การเคลื่อนไหวแม้เพียงเล็กน้อยอาจทำให้เกิดการเยื้องศูนย์ ข้อบกพร่อง และการเปลี่ยนแปลงคุณภาพการเชื่อมได้
- การจัดตำแหน่ง: ระบบจับยึดควรตรวจสอบให้แน่ใจว่าพื้นผิวข้อต่ออยู่ในแนวที่ถูกต้อง การวางแนวที่ไม่ถูกต้องอาจทำให้เกิดการหลอมรวมที่ไม่ดีและรอยเชื่อมที่อ่อนแอ ฟิกซ์เจอร์ที่ปรับได้และเครื่องมือจับยึดที่แม่นยำสามารถช่วยให้จัดตำแหน่งได้อย่างแม่นยำ
- การจัดการความร้อน: อุปกรณ์จับยึดและแคลมป์ควรจัดการความร้อนที่เกิดขึ้นในระหว่างกระบวนการเชื่อมด้วย ความร้อนที่มากเกินไปอาจทำให้ข้อต่อเสียรูปและเคลื่อนที่ได้ การใช้วัสดุที่มีค่าการนำความร้อนที่ดีสำหรับฟิกซ์เจอร์หรือระบบทำความเย็นแบบรวมสามารถช่วยจัดการความร้อนและรักษาเสถียรภาพได้
- การเข้าถึง: การออกแบบฟิกซ์เจอร์และระบบจับยึดควรช่วยให้ลำแสงเลเซอร์เข้าถึงบริเวณการเชื่อมได้ง่าย รูปทรงที่ซับซ้อนและพื้นที่แคบจำเป็นต้องมีอุปกรณ์จับยึดแบบกำหนดเองเพื่อให้แน่ใจว่าสามารถเข้าถึงเลเซอร์ได้อย่างเหมาะสมและสภาวะการเชื่อมที่เหมาะสมที่สุด
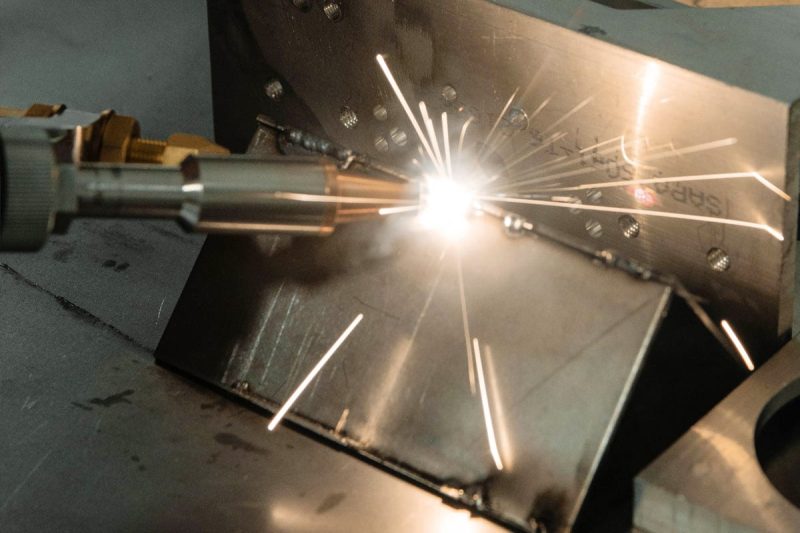
สภาพแวดล้อม
อุณหภูมิโดยรอบ
อุณหภูมิแวดล้อมอาจส่งผลต่อกระบวนการเชื่อมด้วยเลเซอร์ได้หลายวิธี การรักษาสภาพแวดล้อมที่มีอุณหภูมิควบคุมทำให้มั่นใจในคุณภาพการเชื่อมที่สม่ำเสมอและป้องกันปัญหาเกี่ยวกับอุปกรณ์
- ประสิทธิภาพการเชื่อมที่สม่ำเสมอ: อุณหภูมิที่สูงเกินไปหรือต่ำเกินไป อาจส่งผลต่อคุณลักษณะทางความร้อนของวัสดุที่กำลังเชื่อมได้ อุณหภูมิโดยรอบที่สูงอาจส่งผลให้มีความร้อนเข้ามามากเกินไปและการเปลี่ยนรูปเนื่องจากความร้อนเพิ่มขึ้น ในขณะที่อุณหภูมิต่ำอาจทำให้เย็นลงอย่างรวดเร็วและอาจเกิดการแตกร้าวได้
- ความเสถียรของอุปกรณ์: อุปกรณ์การเชื่อมด้วยเลเซอร์ รวมถึงแหล่งกำเนิดเลเซอร์และระบบทำความเย็น ทำงานได้ดีที่สุดภายในช่วงอุณหภูมิที่กำหนด:
- อุณหภูมิสูง: ความร้อนที่มากเกินไปอาจทำให้เกิดการขยายตัวทางความร้อนของวัสดุเชื่อม ส่งผลให้เกิดการวางแนวที่ไม่ตรงและการเสียรูป นอกจากนี้ยังอาจส่งผลต่ออัตราการเย็นตัวของรอยเชื่อม ส่งผลต่อโครงสร้างจุลภาคและคุณสมบัติทางกลของรอยต่อ
- อุณหภูมิต่ำ: สภาพแวดล้อมที่เย็นจัดอาจทำให้เกิดการควบแน่นบนเลนส์เลเซอร์และพื้นผิววัสดุ ซึ่งรบกวนการดูดซับของเลเซอร์และอาจทำให้เกิดข้อบกพร่องได้ อุณหภูมิต่ำยังส่งผลต่อการนำความร้อนและพฤติกรรมการหลอมละลายของวัสดุอีกด้วย
- มาตรการควบคุม: การใช้ระบบควบคุมสภาพอากาศในสภาพแวดล้อมการเชื่อมสามารถช่วยรักษาอุณหภูมิโดยรอบให้คงที่ได้ สิ่งนี้ทำให้มั่นใจได้ถึงความสม่ำเสมอของพฤติกรรมของวัสดุและประสิทธิภาพของอุปกรณ์ ส่งผลให้กระบวนการเชื่อมมีประสิทธิภาพและเชื่อถือได้มากขึ้น
ความชื้น
ระดับความชื้นในสภาพแวดล้อมการเชื่อมอาจส่งผลต่อทั้งอุปกรณ์เลเซอร์และวัสดุที่กำลังเชื่อม
- การควบแน่น: ความชื้นสูงอาจทำให้เกิดการควบแน่นบนเลนส์เลเซอร์และพื้นผิววัสดุ สิ่งนี้สามารถกระจายลำแสงเลเซอร์ ส่งผลให้ความเข้มและความแม่นยำลดลง และยังสามารถนำสิ่งปนเปื้อนเข้าสู่การเชื่อมอีกด้วย
- ออกซิเดชันและการกัดกร่อน: วัสดุที่ไวต่อการเกิดออกซิเดชันและการกัดกร่อนจะได้รับผลกระทบจากความชื้นสูง การมีความชื้นสามารถเร่งกระบวนการเหล่านี้ได้ ซึ่งนำไปสู่การปนเปื้อนที่พื้นผิวและข้อบกพร่องในการเชื่อม
- พฤติกรรมของวัสดุ: วัสดุบางชนิด โดยเฉพาะวัสดุที่ไวต่อความชื้น อาจแสดงการเปลี่ยนแปลงคุณสมบัติเนื่องจากความชื้นได้ ซึ่งอาจส่งผลต่อความสามารถในการเชื่อมและคุณภาพของการเชื่อมขั้นสุดท้าย
- มาตรการควบคุม: การใช้เครื่องลดความชื้นและการระบายอากาศที่เหมาะสมสามารถช่วยควบคุมระดับความชื้นได้ การรักษาพื้นที่การเชื่อมให้แห้งและปราศจากความชื้นสามารถรักษาสภาพการเชื่อมที่เหมาะสมได้
ก๊าซป้องกัน
การใช้แก๊สป้องกันสามารถช่วยให้การเชื่อมด้วยเลเซอร์ประสบความสำเร็จโดยการปกป้องพื้นที่เชื่อมจากการปนเปื้อนในชั้นบรรยากาศและปรับปรุงคุณภาพการเชื่อม
- ประเภทของก๊าซป้องกัน: ก๊าซป้องกันทั่วไปที่ใช้ในการเชื่อมด้วยเลเซอร์ ได้แก่ อาร์กอน ฮีเลียม ไนโตรเจน และส่วนผสมของก๊าซเหล่านี้ การเลือกใช้แก๊สป้องกันขึ้นอยู่กับวัสดุในการเชื่อมและลักษณะการเชื่อมที่ต้องการ
- อาร์กอน: อาร์กอนมีการใช้กันอย่างแพร่หลายเนื่องจากมีความเฉื่อยและให้การป้องกันการเกิดออกซิเดชันและการปนเปื้อนที่ดีเยี่ยม เหมาะสำหรับการเชื่อมโลหะหลายชนิด เช่น เหล็ก อลูมิเนียม และไทเทเนียม
- ฮีเลียม: ฮีเลียมสามารถเพิ่มการเจาะทะลุของรอยเชื่อมและลดความพรุน ทำให้เหมาะสำหรับการเชื่อมลึกและวัสดุที่มีค่าการนำความร้อนสูง เช่น ทองแดงและอลูมิเนียม
- ไนโตรเจน: ไนโตรเจนมักใช้ร่วมกับก๊าซอื่นๆ เพื่อปรับปรุงคุณภาพการเชื่อมบนวัสดุบางชนิด แต่ต้องใช้ด้วยความระมัดระวังเนื่องจากอาจเกิดปฏิกิริยากับโลหะบางชนิดได้
- การไหลและความครอบคลุม: การไหลและความครอบคลุมของก๊าซป้องกันจะต้องได้รับการควบคุมอย่างระมัดระวังเพื่อให้แน่ใจว่ามีการป้องกันบริเวณรอยเชื่อมอย่างเพียงพอ การไหลของก๊าซไม่เพียงพออาจทำให้เกิดการปนเปื้อนและข้อบกพร่องได้ ในขณะที่การไหลมากเกินไปอาจทำให้เกิดปัญหาความวุ่นวายและการระบายความร้อนได้
- การออกแบบหัวฉีด: การออกแบบและการวางตำแหน่งของหัวฉีดแก๊สป้องกันสามารถช่วยให้ครอบคลุมก๊าซได้อย่างมีประสิทธิภาพ การออกแบบหัวฉีดที่เหมาะสมช่วยให้มั่นใจได้ถึงการไหลของก๊าซอย่างต่อเนื่องและสม่ำเสมอเหนือพื้นที่เชื่อม ปรับปรุงคุณภาพและประสิทธิภาพของการเชื่อม
การระบายอากาศ
การระบายอากาศที่เหมาะสมของพื้นที่เชื่อมช่วยรักษาสภาพแวดล้อมการเชื่อมที่ปลอดภัยและมีประสิทธิภาพ
- การดูดควัน: การเชื่อมด้วยเลเซอร์ทำให้เกิดควันและก๊าซที่เป็นอันตรายต่อผู้ปฏิบัติงานและอาจส่งผลต่อกระบวนการเชื่อม ระบบสกัดควันที่มีประสิทธิภาพจะขจัดสิ่งปนเปื้อนเหล่านี้ออกจากพื้นที่ทำงาน เพื่อให้มั่นใจว่าสภาพแวดล้อมจะสะอาดและปลอดภัย
- การควบคุมการไหลของอากาศ: การไหลของอากาศที่มีการควบคุมช่วยรักษาสภาพแวดล้อมการเชื่อมที่มั่นคงโดยป้องกันการสะสมควันและรักษาความครอบคลุมของก๊าซที่สม่ำเสมอในพื้นที่การเชื่อม การไหลของอากาศหรือความปั่นป่วนที่ไม่สามารถควบคุมได้อาจรบกวนก๊าซป้องกันและส่งผลต่อคุณภาพการเชื่อม
- การจัดการความร้อน: การระบายอากาศช่วยจัดการความร้อนที่เกิดขึ้นในระหว่างกระบวนการเชื่อม การไหลเวียนของอากาศที่เหมาะสมจะช่วยป้องกันความร้อนสูงเกินไปของวัสดุและอุปกรณ์ ลดความเสี่ยงของการบิดเบือนความร้อนและความล้มเหลวของอุปกรณ์
- คุณภาพอากาศ: การรักษาคุณภาพอากาศที่ดีในสภาพแวดล้อมการเชื่อมจะป้องกันการสะสมของฝุ่นและอนุภาคอื่น ๆ ที่อาจรบกวนลำแสงเลเซอร์และกระบวนการเชื่อม อากาศที่สะอาดช่วยให้มั่นใจได้ถึงคุณภาพของลำแสงที่สม่ำเสมอและลดความเสี่ยงของข้อบกพร่อง
- มาตรการความปลอดภัย: การระบายอากาศที่เหมาะสมช่วยลดความเสี่ยงในการสัมผัสกับควันอันตราย และปรับปรุงความปลอดภัยโดยรวมในที่ทำงาน นอกจากนี้ยังช่วยรักษาความสมบูรณ์ของเลนส์เลเซอร์และส่วนประกอบที่ละเอียดอ่อนอื่นๆ โดยป้องกันการปนเปื้อนและการสะสมของอนุภาค
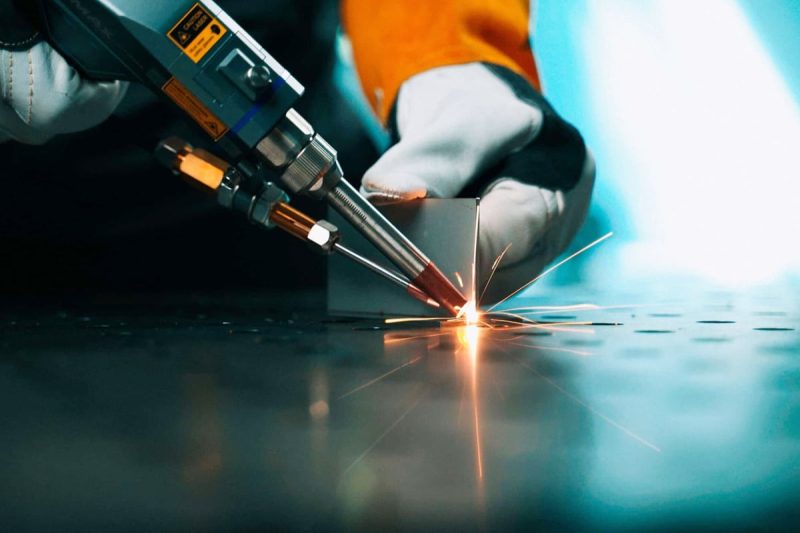
ความเร็วในการเชื่อม
ความเร็วการเชื่อมที่เหมาะสมที่สุด
การบรรลุความเร็วการเชื่อมที่เหมาะสมที่สุดคือความสมดุลที่ละเอียดอ่อนระหว่างคุณภาพการเชื่อมและประสิทธิภาพการผลิต ความเร็วที่เหมาะสมช่วยให้มั่นใจได้ว่าวัสดุจะถูกหลอมรวมอย่างสมบูรณ์โดยไม่ทำให้เกิดข้อบกพร่อง
- การเชื่อมแบบสมบูรณ์: ด้วยความเร็วการเชื่อมที่เหมาะสมที่สุด เลเซอร์จะให้พลังงานเพียงพอในการหลอมและหลอมวัสดุโดยสมบูรณ์ ทำให้เกิดการเชื่อมที่แข็งแรง ปราศจากข้อบกพร่อง พร้อมคุณสมบัติทางกลที่ดี
- คุณภาพที่สม่ำเสมอ: ความเร็วในการเชื่อมที่สม่ำเสมอช่วยให้มั่นใจได้ถึงความร้อนที่สม่ำเสมอตลอดแนวเชื่อม ส่งผลให้คุณภาพการเชื่อมสม่ำเสมอ การเปลี่ยนแปลงความเร็วอาจทำให้เกิดความผิดปกติที่ส่งผลต่อความแข็งแรงและรูปลักษณ์ของรอยเชื่อม
ผลกระทบของความเร็วในการเชื่อมสูง
ความเร็วในการเชื่อมที่สูงสามารถปรับปรุงประสิทธิภาพการผลิตได้ แต่สิ่งเหล่านี้มาพร้อมกับความท้าทายและข้อเสียที่อาจเกิดขึ้นโดยเฉพาะ
- ผลผลิตที่เพิ่มขึ้น: ความเร็วในการเชื่อมที่สูงขึ้นจะช่วยลดรอบเวลา ทำให้สามารถเชื่อมให้แล้วเสร็จได้มากขึ้นในเวลาที่กำหนด ซึ่งเป็นประโยชน์อย่างยิ่งในสภาพแวดล้อมการผลิตที่มีปริมาณมาก
- ข้อบกพร่องที่อาจเกิดขึ้น: การเชื่อมด้วยความเร็วเกินไปอาจส่งผลให้ได้รับความร้อนไม่เพียงพอ ซึ่งอาจนำไปสู่การหลอมเหลวที่ไม่สมบูรณ์ รอยเชื่อมอ่อน และรอยแตกร้าวที่อาจเกิดขึ้นได้ การเคลื่อนไหวอย่างรวดเร็วอาจทำให้มีเวลาไม่เพียงพอสำหรับวัสดุที่จะละลายและยึดเกาะอย่างเหมาะสม
- ความผิดปกติของพื้นผิว: ที่ความเร็วสูงมาก สระที่หลอมละลายอาจมีเวลาไม่เพียงพอที่จะเกาะตัว ส่งผลให้เกิดความผิดปกติของพื้นผิว เช่น ระลอกคลื่นและการกระเด็น
ผลกระทบของความเร็วการเชื่อมต่ำ
แม้ว่าความเร็วในการเชื่อมที่ช้าลงสามารถปรับปรุงคุณภาพการเชื่อมได้ แต่ก็มีข้อจำกัดและข้อควรพิจารณาบางประการ
- การเจาะทะลุที่ได้รับการปรับปรุง: ความเร็วในการเชื่อมที่ช้าลงจะเพิ่มการป้อนความร้อนต่อความยาวหน่วยของการเชื่อม ซึ่งช่วยเพิ่มการเจาะทะลุและรับประกันการหลอมรวมของวัสดุที่หนาขึ้นอย่างสมบูรณ์
- โซนได้รับผลกระทบจากความร้อน (HAZ) ที่เพิ่มขึ้น: ความเร็วที่ช้าลงส่งผลให้มีความร้อนเข้ามากเกินไป ซึ่งส่งผลให้ HAZ มีขนาดใหญ่ขึ้น สิ่งนี้สามารถทำให้เกิดการบิดเบือนจากความร้อน ลดคุณสมบัติทางกล และอาจเกิดการบิดงอของส่วนประกอบที่เชื่อมได้
- ผลผลิตลดลง: ความเร็วในการเชื่อมที่ช้าลงจะลดประสิทธิภาพการผลิตและเพิ่มเวลาทั้งหมดที่จำเป็นในการเชื่อมให้เสร็จสิ้น ในสภาพแวดล้อมการผลิตที่มีปริมาณมาก นี่อาจเป็นข้อเสียเปรียบที่สำคัญ
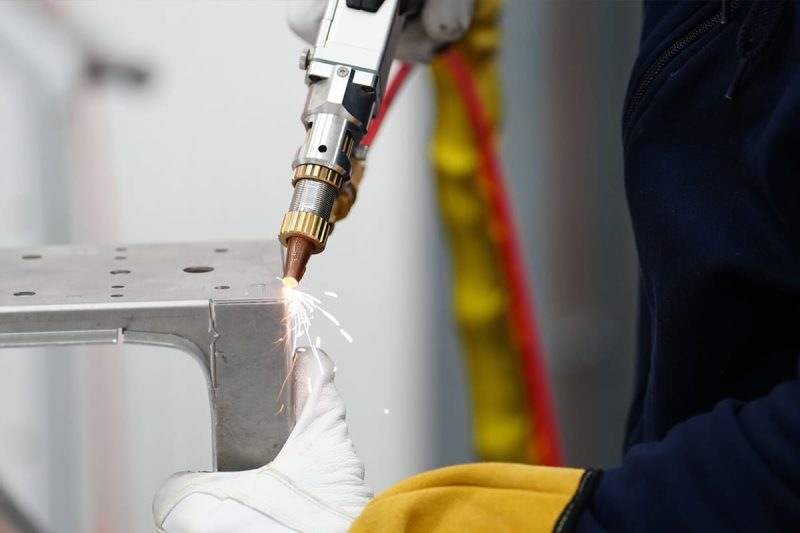
ทักษะและประสบการณ์ของผู้ปฏิบัติงาน
ความสำคัญของทักษะและประสบการณ์ของผู้ปฏิบัติงาน
ความเชี่ยวชาญของผู้ปฏิบัติงานเป็นสิ่งสำคัญด้วยเหตุผลหลายประการ รวมถึงการตั้งค่าอุปกรณ์การเชื่อมที่เหมาะสม การปรับพารามิเตอร์ที่แม่นยำ และความสามารถในการระบุและแก้ไขปัญหาที่อาจเกิดขึ้นระหว่างกระบวนการเชื่อมได้อย่างรวดเร็ว
- การตั้งค่าและการสอบเทียบ: ผู้ปฏิบัติงานที่มีทักษะมีความเชี่ยวชาญในการตั้งค่าและสอบเทียบอุปกรณ์การเชื่อมด้วยเลเซอร์ ซึ่งรวมถึงการจัดแนวเลเซอร์ การปรับโฟกัส การตั้งค่ากำลังเลเซอร์ที่เหมาะสม และการกำหนดค่าการไหลของก๊าซป้องกัน การตั้งค่าที่เหมาะสมช่วยให้แน่ใจว่ากระบวนการเชื่อมเริ่มต้นด้วยฐานที่ถูกต้อง ซึ่งช่วยลดความเสี่ยงของข้อบกพร่องและความไร้ประสิทธิภาพ
- การปรับพารามิเตอร์: ผู้ปฏิบัติงานที่มีประสบการณ์มีความเข้าใจอย่างลึกซึ้งเกี่ยวกับความสัมพันธ์ระหว่างพารามิเตอร์การเชื่อมและคุณภาพการเชื่อม พวกเขาสามารถปรับพารามิเตอร์ได้อย่างแม่นยำ เช่น ความเร็วในการเชื่อม กำลังเลเซอร์ และความถี่พัลส์ เพื่อเพิ่มประสิทธิภาพกระบวนการเชื่อมสำหรับวัสดุที่แตกต่างกันและการกำหนดค่าข้อต่อ
- การแก้ไขปัญหาและการแก้ปัญหา: ในระหว่างกระบวนการเชื่อม อาจเกิดปัญหาต่างๆ มากมาย เช่น การวางแนวไม่ตรง การเจาะไม่ดี หรือการก่อตัวของข้อบกพร่อง เช่น ความพรุนและรอยแตก ผู้ปฏิบัติงานที่มีทักษะสามารถวินิจฉัยปัญหาเหล่านี้ได้อย่างรวดเร็วและดำเนินการแก้ไข เพื่อให้มั่นใจว่ามีเวลาหยุดทำงานน้อยที่สุดและมีคุณภาพการเชื่อมที่สม่ำเสมอ
- ความสามารถในการปรับตัวตามกระบวนการ: วัสดุที่แตกต่างกัน การกำหนดค่าข้อต่อ และงานเชื่อมจำเป็นต้องมีการปรับเปลี่ยนเฉพาะ ผู้ปฏิบัติงานที่มีประสบการณ์สามารถปรับพารามิเตอร์กระบวนการให้เหมาะสมกับสภาวะที่แตกต่างกัน ทำให้มั่นใจได้ถึงคุณภาพการเชื่อมที่สม่ำเสมอในทุกการใช้งาน
การฝึกอบรมและการรับรอง
การฝึกอบรมและการรับรองที่เหมาะสมช่วยพัฒนาและรักษาทักษะการปฏิบัติงานในระดับสูง โปรแกรมการฝึกอบรมที่ครอบคลุมควรครอบคลุมถึง:
- ความรู้ทางทฤษฎี: จำเป็นอย่างยิ่งที่จะต้องเข้าใจหลักการเชื่อมด้วยเลเซอร์ รวมถึงปฏิสัมพันธ์ระหว่างพลังงานเลเซอร์และวัสดุ ผู้ปฏิบัติงานควรรอบรู้ในด้านวิทยาศาสตร์ที่อยู่เบื้องหลังกระบวนการเพื่อทำการตัดสินใจโดยมีข้อมูลครบถ้วน
- ประสบการณ์จริง: การฝึกอบรมภาคปฏิบัติด้วยอุปกรณ์การเชื่อมด้วยเลเซอร์ช่วยให้ผู้ปฏิบัติงานได้รับประสบการณ์ในการตั้งค่า สอบเทียบ และใช้งานเครื่องจักร ประสบการณ์ตรงจะช่วยสร้างความมั่นใจและความสามารถในโลกแห่งความเป็นจริง
- หลักเกณฑ์ด้านความปลอดภัย: การเชื่อมด้วยเลเซอร์เกี่ยวข้องกับอันตรายที่อาจเกิดขึ้น รวมถึงแสงที่รุนแรง ควัน และความร้อน การฝึกอบรมควรเน้นระเบียบปฏิบัติด้านความปลอดภัยเพื่อปกป้องผู้ปฏิบัติงานและรับรองสภาพแวดล้อมการทำงานที่ปลอดภัย
- โปรแกรมการรับรอง: โปรแกรมการรับรองจะตรวจสอบทักษะและความรู้ของผู้ปฏิบัติงาน โดยยอมรับความเชี่ยวชาญของพวกเขาอย่างเป็นทางการ โดยทั่วไปแล้วผู้ปฏิบัติงานที่ผ่านการรับรองจะสามารถจัดการกับงานเชื่อมที่ซับซ้อนและแก้ไขปัญหาได้อย่างมีประสิทธิภาพ
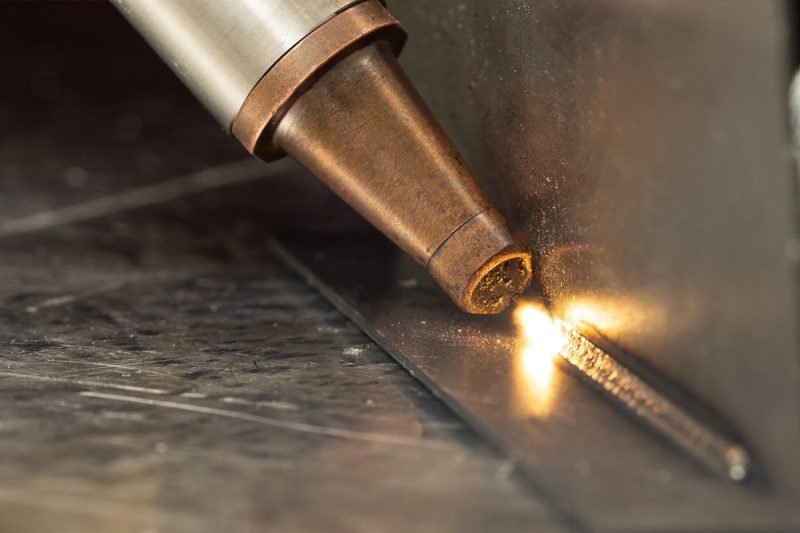
อุปกรณ์และการบำรุงรักษา
แหล่งกำเนิดเลเซอร์
แหล่งกำเนิดเลเซอร์คือหัวใจสำคัญของก ระบบเชื่อมไฟเบอร์เลเซอร์ทำให้เกิดลำแสงความเข้มสูงที่จำเป็นสำหรับการเชื่อม
- เลเซอร์ไฟเบอร์: เป็นที่รู้จักในด้านประสิทธิภาพสูง คุณภาพลำแสงที่ยอดเยี่ยม และความทนทาน เลเซอร์ไฟเบอร์เหมาะอย่างยิ่งสำหรับการเชื่อมวัสดุหลากหลายประเภท รวมถึงโลหะสะท้อนแสง เช่น อลูมิเนียมและทองแดง
- การบำรุงรักษา: ตรวจสอบกำลังขับอย่างสม่ำเสมอเพื่อให้มั่นใจถึงประสิทธิภาพที่สม่ำเสมอ ทำความสะอาดเลนส์เพื่อป้องกันการปนเปื้อน และตรวจสอบการจัดตำแหน่งเพื่อรักษาความแม่นยำของลำแสง
เลนส์
ระบบออพติกส์จะกำหนดทิศทางและโฟกัสลำแสงเลเซอร์ไปยังบริเวณรอยเชื่อม เพื่อให้มั่นใจถึงการส่งพลังงานที่แม่นยำ
- ระบบส่งลำแสง: ประกอบด้วยใยแก้วนำแสงและคอลลิเมเตอร์เพื่อส่งลำแสงเลเซอร์โดยมีการสูญเสียน้อยที่สุด
- เลนส์โฟกัส: เลนส์หรือหัวโฟกัสที่รวมลำแสงเลเซอร์ไปที่จุดขนาดเล็ก จึงเพิ่มความหนาแน่นของพลังงาน
- การบำรุงรักษา: การทำความสะอาดเลนส์ กระจก และหน้าต่างป้องกันเป็นประจำ การตรวจสอบความเสียหาย และการตรวจสอบการจัดตำแหน่งสามารถช่วยรักษาคุณภาพลำแสงให้เหมาะสมที่สุดได้
ระบบการเคลื่อนไหว
ระบบการเคลื่อนที่จะควบคุมการเคลื่อนที่ของลำแสงเลเซอร์และชิ้นงาน ทำให้มั่นใจถึงตำแหน่งที่แม่นยำและการทำงานที่ราบรื่น
- ประเภท: ระบบคาร์ทีเซียนสำหรับการเคลื่อนที่เชิงเส้นแบบสามแกน แขนหุ่นยนต์สำหรับการเคลื่อนที่แบบหลายแกน และระบบโครงสำหรับตั้งสิ่งของสำหรับการใช้งานขนาดใหญ่
- การบำรุงรักษา: การหล่อลื่นชิ้นส่วนที่เคลื่อนไหวเป็นประจำ การสอบเทียบเป็นประจำเพื่อการเคลื่อนไหวที่แม่นยำ และการตรวจสอบการสึกหรอหรือการเยื้องศูนย์ ช่วยให้มั่นใจในการทำงานที่เชื่อถือได้
ระบบทำความเย็น
ระบบระบายความร้อนป้องกันแหล่งกำเนิดเลเซอร์และส่วนประกอบสำคัญอื่นๆ จากความร้อนสูงเกินไป และรักษาการทำงานที่มั่นคง
- การระบายความร้อนด้วยน้ำ: มักใช้ในเครื่องกำเนิดเลเซอร์ไฟเบอร์กำลังสูงเนื่องจากมีการกระจายความร้อนได้ดี
- ส่วนประกอบ: ปั๊ม เครื่องแลกเปลี่ยนความร้อน และถังเก็บน้ำหล่อเย็นเป็นองค์ประกอบสำคัญของระบบทำความเย็น
- การบำรุงรักษา: ตรวจสอบการรั่วไหลและการอุดตัน ตรวจสอบคุณภาพน้ำหล่อเย็น และเปลี่ยนตัวกรองเป็นประจำตามความจำเป็นเพื่อให้มั่นใจในการทำความเย็นที่มีประสิทธิภาพ
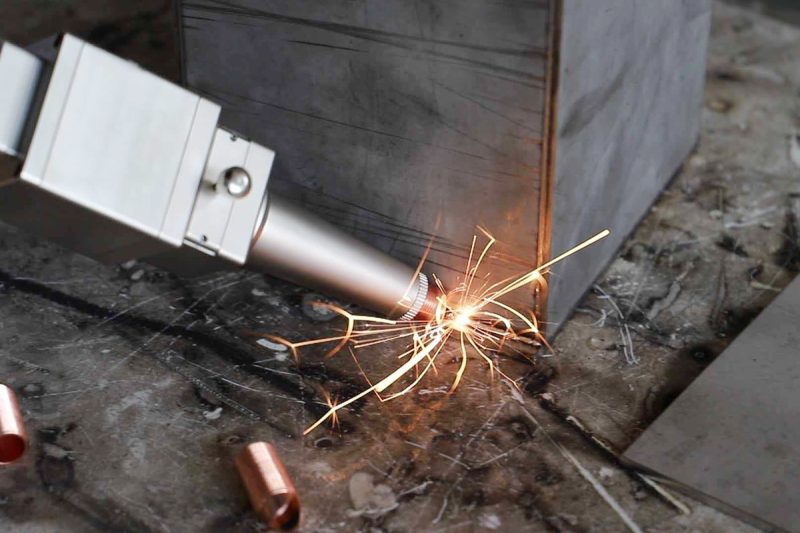
ระบบอัตโนมัติและระบบควบคุม
การตรวจสอบแบบเรียลไทม์
ระบบตรวจสอบแบบเรียลไทม์ให้ข้อเสนอแนะอย่างต่อเนื่องเกี่ยวกับกระบวนการเชื่อม ทำให้สามารถทำการปรับเปลี่ยนได้ทันทีเพื่อให้มั่นใจถึงประสิทธิภาพสูงสุด
- การตรวจสอบคุณภาพการเชื่อม: เซ็นเซอร์และกล้องจะตรวจสอบสระการเชื่อม โดยตรวจจับข้อบกพร่อง เช่น ความพรุน รอยแตก และการเยื้องแนวในแบบเรียลไทม์ ช่วยให้ผู้ปฏิบัติงานสามารถปรับกำลังเลเซอร์ ความเร็ว และโฟกัสได้แบบเรียลไทม์
- การตรวจสอบกำลังเลเซอร์: ระบบจะติดตามกำลังแสงเลเซอร์อย่างต่อเนื่องเพื่อให้แน่ใจว่าจะอยู่ในช่วงที่ต้องการ ซึ่งช่วยรักษาการส่งพลังงานที่สม่ำเสมอและการเจาะทะลุของรอยเชื่อม
การควบคุมแบบปรับเปลี่ยนได้
ระบบควบคุมแบบปรับเปลี่ยนได้จะปรับพารามิเตอร์การเชื่อมแบบไดนามิกตามข้อมูลเรียลไทม์เพื่อปรับกระบวนการให้เหมาะสมสำหรับสภาวะที่แตกต่างกัน
- การปรับพารามิเตอร์: ระบบเหล่านี้จะปรับกำลังเลเซอร์ ความเร็วในการเชื่อม และตำแหน่งโฟกัสโดยอัตโนมัติ ตามการเปลี่ยนแปลงคุณสมบัติของวัสดุ ความหนา และการกำหนดค่าข้อต่อ ช่วยให้มั่นใจได้ถึงคุณภาพการเชื่อมที่สม่ำเสมอและสม่ำเสมอทั่วทั้งส่วนต่างๆ ของชิ้นงาน
- ฟีดแบ็กลูป: การรวมฟีดแบ็กลูปช่วยให้ระบบเรียนรู้จากการเชื่อมครั้งก่อน ปรับปรุงความแม่นยำและประสิทธิภาพเมื่อเวลาผ่านไป
บูรณาการกับระบบหุ่นยนต์
การรวมการเชื่อมด้วยไฟเบอร์เลเซอร์เข้ากับระบบหุ่นยนต์ช่วยเพิ่มระบบอัตโนมัติ ความยืดหยุ่น และความสามารถในการทำซ้ำ
- การเคลื่อนที่แบบหลายแกน: แขนหุ่นยนต์ให้การเคลื่อนที่แบบหลายแกนเพื่อการเชื่อมที่แม่นยำของรูปทรงที่ซับซ้อนและพื้นที่ที่เข้าถึงยาก
- คุณภาพคงที่: หุ่นยนต์รับประกันคุณภาพการเชื่อมที่สม่ำเสมอโดยการควบคุมเส้นทางการเชื่อม ความเร็ว และมุมอย่างแม่นยำ ลดความแปรผันที่เกี่ยวข้องกับการเชื่อมด้วยมือ
- เพิ่มปริมาณงาน: ระบบอัตโนมัติของหุ่นยนต์จะเพิ่มปริมาณงานโดยทำให้สามารถดำเนินการได้อย่างต่อเนื่องและลดรอบเวลา ส่งผลให้ได้รับผลผลิตเพิ่มขึ้นอย่างมาก
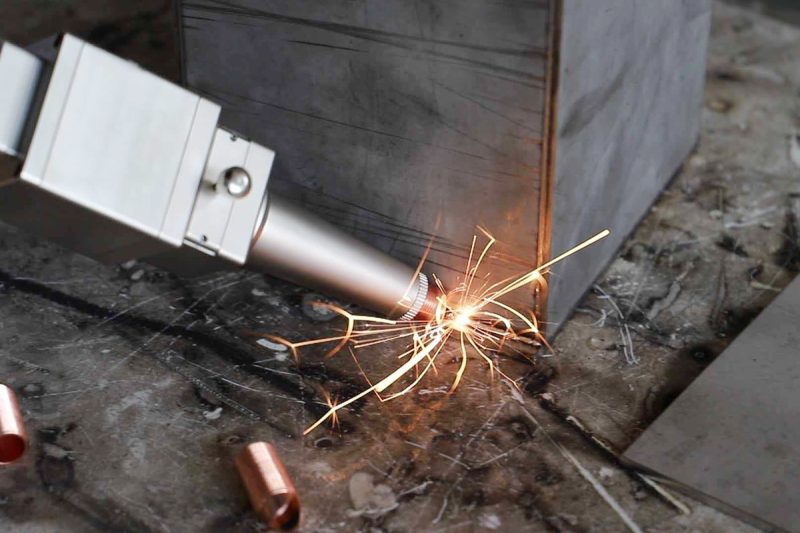
ข้อควรพิจารณาเฉพาะการใช้งาน
การผสมวัสดุ
วัสดุที่แตกต่างกันมีปฏิกิริยาเฉพาะกับการเชื่อมด้วยเลเซอร์ และการผสมผสานของวัสดุเหล่านี้อาจทำให้เกิดความท้าทายเฉพาะได้
- วัสดุที่แตกต่างกัน: การเชื่อมวัสดุที่แตกต่างกัน เช่น อลูมิเนียมกับเหล็ก อาจเป็นเรื่องที่ท้าทายเนื่องจากจุดหลอมเหลว การนำความร้อน และอัตราการดูดซับเลเซอร์ที่แตกต่างกัน ไฟเบอร์เลเซอร์มีประสิทธิภาพในการเชื่อมส่วนผสมเหล่านี้ แต่ต้องมีการควบคุมพารามิเตอร์ที่แม่นยำเพื่อจัดการอินพุตความร้อนและหลีกเลี่ยงข้อบกพร่อง
- วัสดุสะท้อนแสง: วัสดุเช่นทองแดงและอลูมิเนียมสะท้อนส่วนสำคัญของพลังงานเลเซอร์ ซึ่งสามารถลดประสิทธิภาพในการเชื่อมได้ ไฟเบอร์เลเซอร์โดยเฉพาะอย่างยิ่งที่มีความยาวคลื่นสั้นกว่าจะเหมาะสมกว่าสำหรับวัสดุเหล่านี้ แต่การปรับพารามิเตอร์เลเซอร์ให้เหมาะสมเป็นสิ่งสำคัญเพื่อให้แน่ใจว่าการดูดซับพลังงานมีประสิทธิผล
- โลหะผสมและวัสดุคอมโพสิต: โลหะผสมหรือวัสดุคอมโพสิตแต่ละชนิดอาจต้องมีการตั้งค่าเฉพาะเพื่อการเชื่อมที่เหมาะสมที่สุด การทำความเข้าใจคุณสมบัติของวัสดุและการปรับกำลังเลเซอร์ ความเร็ว และโฟกัสให้เหมาะสมเป็นกุญแจสำคัญในการบรรลุการเชื่อมคุณภาพสูง
เรขาคณิตการเชื่อม
รูปทรงของรอยเชื่อมส่งผลต่อกระบวนการเชื่อม และต้องพิจารณาอย่างรอบคอบเพื่อให้มั่นใจถึงประสิทธิภาพ
- รูปทรงที่ซับซ้อน: การเชื่อมรูปทรงที่ซับซ้อน เช่น รูปทรงโค้งหรือซับซ้อน จำเป็นต้องมีการควบคุมลำแสงเลเซอร์และระบบการเคลื่อนที่ที่แม่นยำ ไฟเบอร์เลเซอร์สามารถจัดการกับรูปทรงเหล่านี้ได้อย่างมีประสิทธิภาพเมื่อรวมเข้ากับระบบการเคลื่อนที่ขั้นสูงและแขนหุ่นยนต์
- การเชื่อมส่วนที่บาง VS ส่วนที่หนา: การเชื่อมส่วนที่บางต้องใช้พลังงานที่ต่ำกว่าและความแม่นยำที่สูงกว่าเพื่อหลีกเลี่ยงการไหม้ ในขณะที่ส่วนที่หนาต้องใช้กำลังที่สูงกว่าและความเร็วที่ต่ำกว่าในการเจาะทะลุได้เต็มที่ การปรับพารามิเตอร์เลเซอร์ให้เข้ากับรูปทรงเฉพาะช่วยให้การเชื่อมมีประสิทธิภาพ
- การเตรียมขอบ: การเตรียมขอบที่เหมาะสม เช่น การเอียงหรือการทำความสะอาด ช่วยให้มั่นใจได้ถึงความพอดีและการหลอมรวมที่ดีขึ้น การรักษาคุณภาพขอบที่สม่ำเสมอสามารถช่วยให้ได้รอยเชื่อมที่สม่ำเสมอ
ปริมาณการผลิต
ปริมาณการผลิตส่งผลต่อการเลือกอุปกรณ์การเชื่อมด้วยเลเซอร์และพารามิเตอร์กระบวนการ
- การผลิตชุดเล็กหรือแบบกำหนดเอง: สำหรับการผลิตชุดเล็กหรือแบบกำหนดเอง ความยืดหยุ่นและความสามารถในการปรับตัวเป็นสิ่งสำคัญ ไฟเบอร์เลเซอร์ที่มีความอเนกประสงค์ช่วยให้สามารถปรับพารามิเตอร์การเชื่อมและการกำหนดค่าได้อย่างรวดเร็ว ทำให้เหมาะสำหรับงานเชื่อมเฉพาะทางที่หลากหลาย
- การผลิตในปริมาณมาก: การผลิตในปริมาณมากต้องอาศัยความสม่ำเสมอ ความเร็ว และระบบอัตโนมัติ ระบบไฟเบอร์เลเซอร์ที่ผสานรวมกับระบบควบคุมอัตโนมัติและแขนหุ่นยนต์ให้ความแม่นยำและความสามารถในการทำซ้ำตามที่ต้องการ ซึ่งช่วยเพิ่มการผลิตและประสิทธิภาพได้อย่างมาก
- การเพิ่มประสิทธิภาพรอบเวลา: ในสภาพแวดล้อมการผลิต การลดรอบเวลาให้เหลือน้อยที่สุดสามารถปรับปรุงประสิทธิภาพได้ ระบบไฟเบอร์เลเซอร์ที่มาพร้อมกับการตรวจสอบแบบเรียลไทม์และการควบคุมแบบปรับเปลี่ยนสามารถลดเวลาการตั้งค่าและให้ความมั่นใจในความเร็วในการเชื่อมที่เหมาะสมที่สุด ซึ่งจะช่วยเพิ่มประสิทธิภาพการผลิตโดยรวม
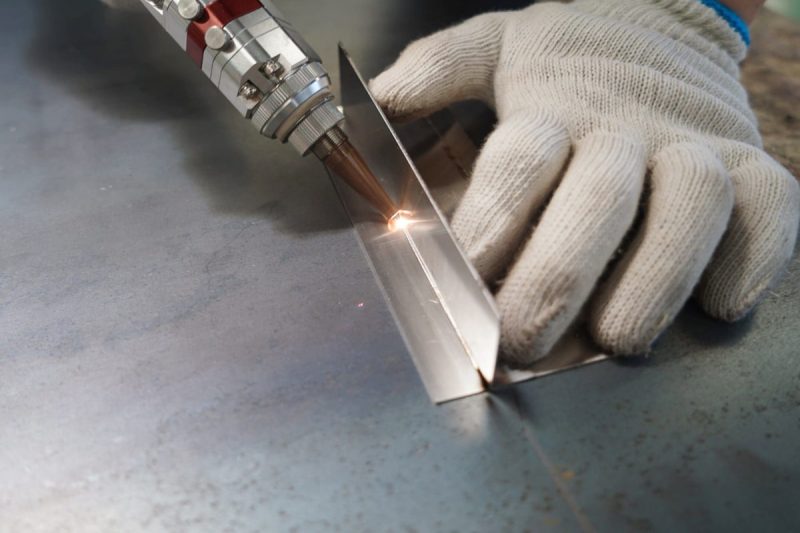
สรุป
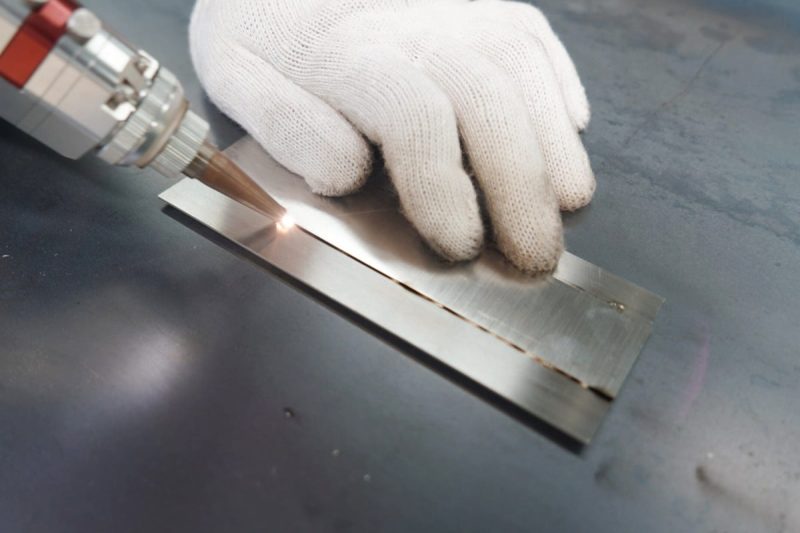
รับโซลูชั่นการเชื่อมด้วยเลเซอร์
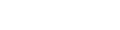
- [email protected]
- [email protected]
- +86-19963414011
- หมายเลข 3 โซน A เขตอุตสาหกรรม Luzhen เมือง Yucheng มณฑลซานตง