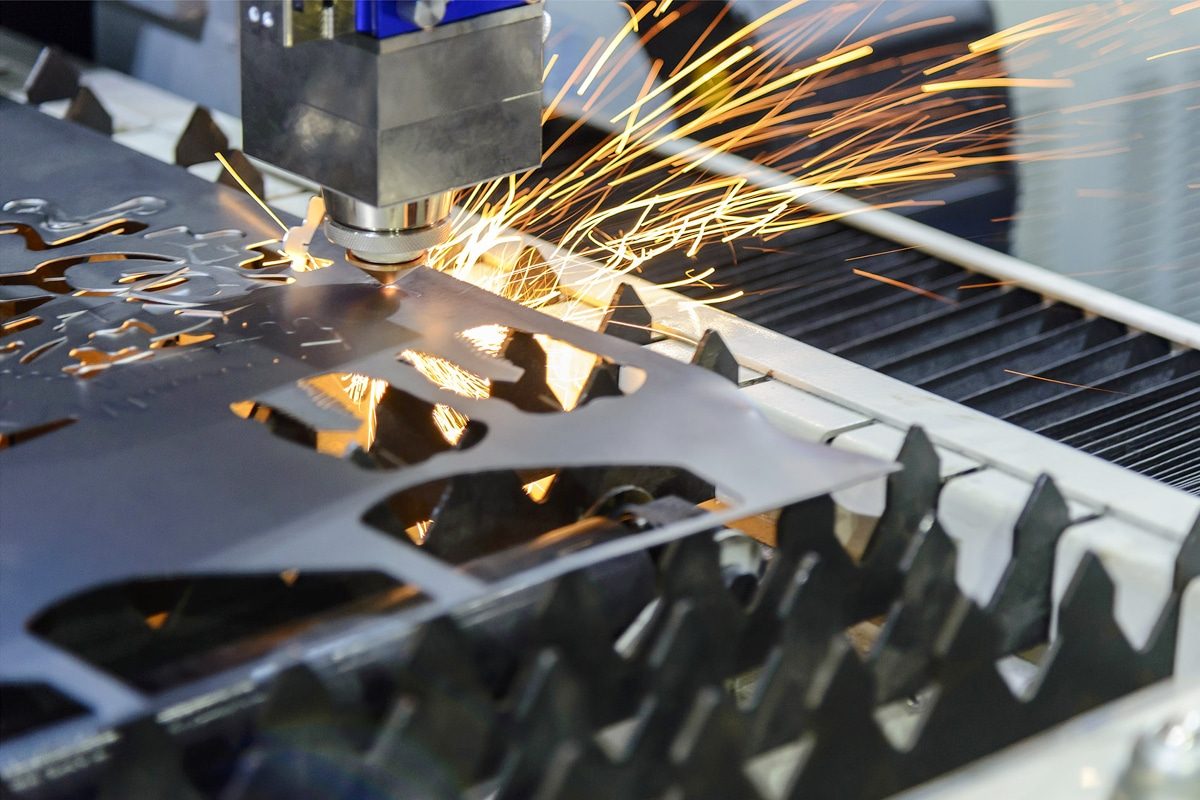
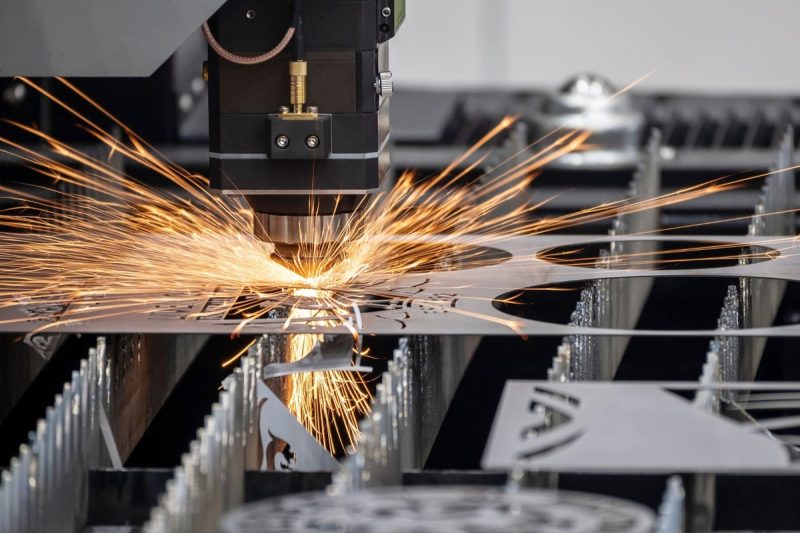
เรียนรู้เกี่ยวกับการตัดด้วยเลเซอร์
คำอธิบายการตัดด้วยเลเซอร์
ประเภทของเลเซอร์ที่ใช้ในการตัด
ไฟเบอร์เลเซอร์
เลเซอร์ CO2
ส่วนประกอบของระบบตัดด้วยเลเซอร์
ทั่วไป ระบบตัดเลเซอร์ ประกอบด้วยส่วนประกอบสำคัญหลายประการที่ทำงานร่วมกันเพื่อให้ประสิทธิภาพการตัดที่แม่นยำและมีประสิทธิภาพ:
- แหล่งกำเนิดเลเซอร์: นี่คือองค์ประกอบหลักที่ผลิตลำแสงเลเซอร์ แหล่งกำเนิดเลเซอร์อาจเป็นเครื่องกำเนิดเลเซอร์ไฟเบอร์ เครื่องกำเนิดเลเซอร์ CO2 หรือเครื่องกำเนิดเลเซอร์ประเภทอื่น ทั้งนี้ขึ้นอยู่กับการใช้งาน
- เลนส์: กระจกและเลนส์ใช้ในการควบคุมและโฟกัสลำแสงเลเซอร์ไปที่วัสดุที่ถูกตัด คุณภาพของเลนส์ส่งผลต่อความแม่นยำและประสิทธิภาพของกระบวนการตัด
- หัวตัด: หัวตัดประกอบด้วยเลนส์โฟกัสและหัวฉีดซึ่งลำแสงเลเซอร์และก๊าซช่วยพุ่งไป มีหน้าที่รับผิดชอบในการรักษาความยาวโฟกัสที่ถูกต้องและรับประกันสภาวะการตัดที่เหมาะสมที่สุด
- โต๊ะทำงาน: รองรับวัสดุที่ถูกตัดและมักจะมีกลไกในการเคลื่อนย้ายวัสดุไว้ใต้หัวตัด
- ตัวควบคุม CNC: ตัวควบคุม CNC จะจัดการการเคลื่อนที่ของหัวตัดด้วยเลเซอร์และชิ้นงาน ตามเส้นทางการตัดที่ตั้งโปรแกรมไว้ เพื่อให้ได้รูปทรงและรูปแบบที่ต้องการ
- Assist Gas Supply: Assist Gas ช่วยเหลือกระบวนการตัดโดยการเป่าวัสดุที่หลอมละลายออกไป ทำให้บริเวณการตัดเย็นลง และป้องกันการเกิดออกซิเดชัน ก๊าซช่วยเหลือทั่วไป ได้แก่ ออกซิเจน ไนโตรเจน และอากาศอัด
- ระบบไอเสีย: กำจัดควันและเศษที่เกิดขึ้นในระหว่างกระบวนการตัดเพื่อรักษาสภาพแวดล้อมการทำงานที่สะอาดและปกป้องเลนส์และส่วนประกอบเลเซอร์
- ระบบทำความเย็น: การตัดด้วยเลเซอร์จะสร้างความร้อนจำนวนมากซึ่งจำเป็นต้องกระจายออกไป เพื่อป้องกันความเสียหายต่อแหล่งกำเนิดเลเซอร์และส่วนประกอบอื่นๆ ระบบทำความเย็น เช่น เครื่องทำน้ำเย็น ถูกนำมาใช้เพื่อรักษาอุณหภูมิในการทำงานให้เหมาะสมที่สุด
พารามิเตอร์หลักที่ส่งผลต่อประสิทธิภาพการตัดด้วยเลเซอร์
พารามิเตอร์หลายตัวอาจส่งผลต่อประสิทธิภาพและคุณภาพของกระบวนการตัดด้วยเลเซอร์ การทำความเข้าใจและปรับพารามิเตอร์เหล่านี้ให้เหมาะสมสามารถช่วยให้บรรลุผลตามที่ต้องการ:
- กำลังเลเซอร์: กำลังเอาท์พุตของแหล่งกำเนิดเลเซอร์จะกำหนดความหนาและประเภทของวัสดุที่สามารถตัดได้ กำลังที่สูงขึ้นทำให้สามารถตัดวัสดุที่มีความหนาได้ แต่อาจจำเป็นต้องปรับพารามิเตอร์อื่นๆ เพื่อรักษาคุณภาพการตัด
- ความเร็วตัด: ความเร็วที่หัวตัดเคลื่อนผ่านชิ้นงาน ความเร็วตัดที่เหมาะสมทำให้มั่นใจได้ถึงความสมดุลระหว่างความสามารถในการผลิตและคุณภาพการตัด ความเร็วที่เร็วเกินไปอาจส่งผลให้การตัดไม่สมบูรณ์ ในขณะที่ความเร็วที่ช้าเกินไปอาจทำให้เกิดความร้อนสะสมมากเกินไปและวัสดุเสียหายได้
- ตำแหน่งโฟกัส: ตำแหน่งของจุดโฟกัสของลำแสงเลเซอร์ที่สัมพันธ์กับพื้นผิวของวัสดุ การโฟกัสที่ถูกต้องทำให้มั่นใจได้ถึงความหนาแน่นของพลังงานสูงสุดที่จุดตัด ส่งผลให้การตัดสะอาดและแม่นยำ การวางแนวที่ไม่ถูกต้องอาจส่งผลให้คุณภาพการตัดไม่ดีและประสิทธิภาพลดลง
- ประเภทและแรงดันของแก๊สช่วย: ประเภทและความดันของแก๊สช่วยที่ใช้ (ออกซิเจน ไนโตรเจน หรืออากาศอัด) มีผลกระทบอย่างมากต่อกระบวนการตัด การเลือกก๊าซและแรงดันที่ถูกต้องช่วยเพิ่มประสิทธิภาพการกำจัดวัสดุที่หลอมเหลว ป้องกันการเกิดออกซิเดชัน และปรับปรุงคุณภาพการตัด
- ประเภทและความหนาของวัสดุ: วัสดุและความหนาที่แตกต่างกันจะทำปฏิกิริยากับการตัดด้วยเลเซอร์แตกต่างกัน เมื่อตั้งค่าพารามิเตอร์การตัด จะต้องพิจารณาคุณสมบัติของวัสดุ เช่น การสะท้อนแสง การนำความร้อน และจุดหลอมเหลว
- คุณภาพลำแสง: คุณภาพของลำแสงเลเซอร์ซึ่งมีจุดเด่นอยู่ที่โครงสร้างโฟกัสและโหมด ส่งผลต่อความแม่นยำและคุณภาพของการตัด ลำแสงคุณภาพสูงที่มีขนาดจุดโฟกัสเล็กทำให้การตัดละเอียดยิ่งขึ้นโดยมีความกว้างในการตัดน้อยที่สุด
- การออกแบบหัวฉีด: การออกแบบหัวฉีด รวมถึงเส้นผ่านศูนย์กลางและรูปร่าง ส่งผลต่อการไหลของแก๊สช่วยเหลือและการกำจัดวัสดุที่หลอมละลาย การออกแบบหัวฉีดที่ได้รับการปรับปรุงจะช่วยเพิ่มประสิทธิภาพและคุณภาพการตัด
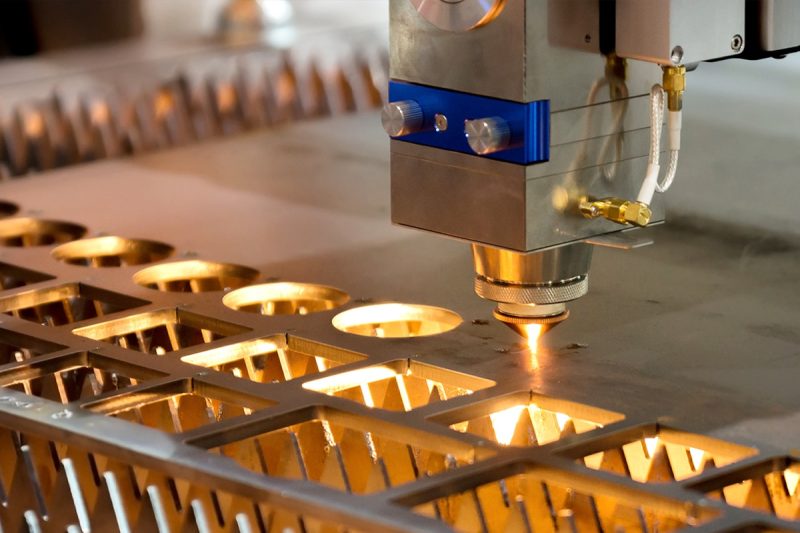
บทบาทของก๊าซช่วยในการตัดด้วยเลเซอร์
การถอดวัสดุที่หลอมเหลว
ในระหว่างกระบวนการตัดด้วยเลเซอร์ ลำแสงเลเซอร์ความเข้มสูงจะละลายวัสดุ ณ จุดที่ตัด ก๊าซช่วยเหลือจะถูกส่งผ่านหัวฉีดไปยังพื้นที่ตัด ซึ่งจะช่วยขจัดวัสดุที่หลอมเหลวออกจากรอยตัด (ช่องว่างที่เกิดจากเลเซอร์) การขจัดวัสดุที่หลอมเหลวออกอย่างมีประสิทธิภาพช่วยรักษาคุณภาพการตัดและป้องกันข้อบกพร่อง
- การฉีดพ่นอย่างมีประสิทธิภาพ: แรงดันสูงของแก๊สช่วยพัดวัสดุที่หลอมละลายออกจากรอยตัด ป้องกันไม่ให้เกิดการแข็งตัวอีกครั้งบนชิ้นงาน และรับประกันการตัดที่สะอาด
- การป้องกันการเกิดตะกรัน: ด้วยการระบายวัสดุที่หลอมละลายอย่างรวดเร็ว ก๊าซช่วยเหลือจะลดการก่อตัวของตะกรัน (วัสดุตกค้างที่เกาะติดกับพื้นผิวด้านล่างของการตัด) ซึ่งช่วยลดความจำเป็นในการประมวลผลภายหลัง
- การรักษาความกว้างของร่อง: การขจัดวัสดุที่หลอมละลายอย่างต่อเนื่องจะช่วยรักษาความกว้างของร่องตามที่ต้องการ ช่วยให้มั่นใจในความแม่นยำของมิติและความแม่นยำของการตัดขั้นสุดท้าย
ระบายความร้อนบริเวณการตัด
ความร้อนที่รุนแรงที่เกิดจากลำแสงเลเซอร์สามารถทำให้เกิดผลกระทบด้านความร้อนอย่างมีนัยสำคัญต่อชิ้นงาน รวมถึงการบิดงอ การเสียรูป และการเปลี่ยนแปลงคุณสมบัติของวัสดุ Assist gas ช่วยควบคุมผลกระทบจากความร้อนเหล่านี้โดยการทำความเย็นบริเวณการตัด
- การกระจายความร้อน: การไหลของแก๊สช่วยดูดซับและกระจายความร้อนส่วนเกินในบริเวณการตัด ช่วยป้องกันความร้อนสูงเกินไปและลดการเปลี่ยนรูปเนื่องจากความร้อนของวัสดุให้เหลือน้อยที่สุด
- การลดโซนที่ได้รับผลกระทบจากความร้อน (HAZ): การระบายความร้อนของโซนการตัดช่วยจำกัดขนาดของ HAZ รักษาคุณสมบัติทางกลของวัสดุ และลดความเสี่ยงของการบิดงอหรือความเสียหายจากความร้อนอื่นๆ
- การเพิ่มความเร็วตัด: การระบายความร้อนที่มีประสิทธิภาพจะเพิ่มความเร็วตัด เนื่องจากวัสดุมีโอกาสน้อยที่จะเกิดข้อบกพร่องที่เกิดจากความร้อน ส่งผลให้การผลิตเร็วขึ้นและมีประสิทธิภาพมากขึ้น
การปกป้องเลนส์
เลนส์ในหัวตัดจะเน้นลำแสงเลเซอร์ไปที่ชิ้นงาน สิ่งปนเปื้อน เช่น ควัน ฝุ่น และเศษต่างๆ ที่เกิดขึ้นระหว่างกระบวนการตัดอาจทำให้เลนส์เสียหายหรือลดประสิทธิภาพลงได้ Assist Gas ช่วยปกป้องเลนส์จากสารปนเปื้อน
- การป้องกันเลนส์: ก๊าซช่วยก่อให้เกิดสิ่งกีดขวางระหว่างเลนส์และพื้นที่ตัด ป้องกันไม่ให้สารปนเปื้อนเข้าถึงและสะสมบนพื้นผิวเลนส์
- การรักษาคุณภาพออพติคอล: ด้วยการรักษาเลนส์ให้สะอาดและปราศจากเศษซาก แก๊สช่วยทำให้มั่นใจได้ว่าการโฟกัสลำแสงที่เหมาะสมที่สุดและประสิทธิภาพการตัดที่สม่ำเสมอ
- การยืดอายุเลนส์: การป้องกันการปนเปื้อนจะช่วยลดการสึกหรอของเลนส์ ยืดอายุการใช้งาน และลดค่าบำรุงรักษา
เพิ่มปฏิกิริยาการตัด
ก๊าซช่วยเหลืออาจส่งผลต่อปฏิกิริยาเคมีที่เกิดขึ้นระหว่างการตัดด้วยเลเซอร์ ซึ่งจะช่วยเพิ่มประสิทธิภาพการตัดของวัสดุที่แตกต่างกัน ประเภทของก๊าซที่ใช้สามารถส่งเสริมหรือยับยั้งปฏิกิริยาบางอย่าง ซึ่งอาจส่งผลต่อคุณภาพและประสิทธิภาพของการตัด
- ออกซิเจน (O₂): ออกซิเจนมักใช้ในการตัดเหล็กกล้าคาร์บอน ส่งเสริมปฏิกิริยาคายความร้อนกับโลหะหลอมเหลว ทำให้เกิดความร้อนเพิ่มเติม ซึ่งจะเพิ่มความเร็วในการตัด ปฏิกิริยานี้ช่วยให้ได้การตัดที่สะอาดและมีขี้เถ้าน้อยลง แต่อาจทำให้เกิดออกซิเดชันที่คมตัดได้
- ไนโตรเจน (N₂): ไนโตรเจนเป็นก๊าซเฉื่อยที่มักใช้ตัดเหล็กสเตนเลส อลูมิเนียม และโลหะนอกกลุ่มเหล็กอื่นๆ ป้องกันการเกิดออกซิเดชันโดยการสร้างบรรยากาศเฉื่อยรอบๆ บริเวณการตัด ทำให้ได้ขอบที่สะอาดและปราศจากออกไซด์ ทำให้เหมาะสำหรับการใช้งานที่ต้องการคุณภาพพื้นผิวคุณภาพสูง
- อากาศอัด: อากาศอัดเป็นทางเลือกที่คุ้มค่าซึ่งสามารถใช้ในการตัดวัสดุได้หลากหลาย โดยผสมผสานคุณสมบัติของออกซิเจนและไนโตรเจนเข้าด้วยกันเพื่อให้มีประสิทธิภาพการตัดที่เพียงพอด้วยต้นทุนที่ต่ำลง อย่างไรก็ตาม อาจก่อให้เกิดสิ่งเจือปนที่ส่งผลต่อคุณภาพการตัดได้
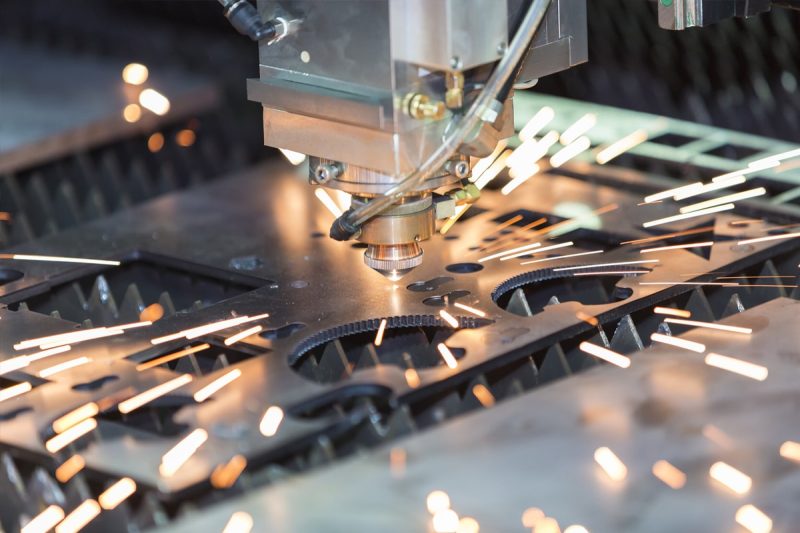
ประเภทของก๊าซช่วย
ออกซิเจน (O₂)
ข้อดี
- ความเร็วตัดที่เพิ่มขึ้น: ออกซิเจนทำปฏิกิริยากับวัสดุในปฏิกิริยาคายความร้อน และปล่อยความร้อนเพิ่มเติม ความร้อนที่เพิ่มขึ้นนี้จะเพิ่มความเร็วในการตัด ทำให้การตัดโดยใช้ออกซิเจนช่วยเร็วขึ้นอย่างมาก โดยเฉพาะกับวัสดุที่หนากว่า
- ปรับปรุงประสิทธิภาพ: ปฏิกิริยาคายความร้อนช่วยลดพลังงานเลเซอร์ที่ต้องใช้ในการตัดวัสดุ ซึ่งช่วยปรับปรุงประสิทธิภาพการใช้พลังงานโดยรวมของกระบวนการตัด
- การตัดที่สะอาดยิ่งขึ้นบนวัสดุที่มีความหนา: ออกซิเจนช่วยสร้างการตัดที่สะอาดยิ่งขึ้นบนวัสดุที่หนาขึ้น ลดขี้เถ้าและตะกรัน ซึ่งช่วยลดความจำเป็นในการประมวลผลภายหลังที่กว้างขวาง
ข้อเสีย
- ออกซิเดชัน: ปฏิกิริยาระหว่างออกซิเจนกับวัสดุอาจทำให้เกิดออกซิเดชันที่คมตัด ส่งผลให้พื้นผิวมีความหยาบมากขึ้นและอาจเกิดปัญหาการกัดกร่อนได้
- โซนได้รับผลกระทบจากความร้อน (HAZ): ความร้อนเพิ่มเติมที่เกิดจากปฏิกิริยาคายความร้อนจะเพิ่มขนาดของ HAZ ซึ่งสามารถเปลี่ยนคุณสมบัติทางกลของวัสดุใกล้กับคมตัด และทำให้เกิดปัญหา เช่น การบิดงอหรือความสมบูรณ์ของโครงสร้างลดลง
- ข้อจำกัดสำหรับโลหะที่ไม่ใช่เหล็ก: ออกซิเจนไม่มีประสิทธิผลเท่ากับโลหะที่ไม่ใช่เหล็ก เช่น อลูมิเนียมและทองแดง ซึ่งไม่ทำปฏิกิริยากับออกซิเจนได้ง่าย
ไนโตรเจน (N₂)
ข้อดี
- การตัดแบบไร้ออกซิเดชั่น: ไนโตรเจนเป็นก๊าซเฉื่อยที่ไม่ทำปฏิกิริยากับวัสดุในระหว่างกระบวนการตัด คุณสมบัตินี้ป้องกันการเกิดออกซิเดชัน ส่งผลให้ขอบสะอาด สว่าง ปราศจากออกไซด์ ซึ่งเหมาะสำหรับการใช้งานที่ต้องการคุณภาพพื้นผิวคุณภาพสูง
- การตกแต่งพื้นผิวคุณภาพสูง: การไม่มีออกซิเดชันส่งผลให้ขอบเรียบขึ้นและพื้นผิวเรียบขึ้น ซึ่งช่วยลดหรือขจัดความจำเป็นในการประมวลผลภายหลัง
- โซนที่ได้รับผลกระทบจากความร้อนน้อยที่สุด (HAZ): ไนโตรเจนช่วยรักษาโซนที่ได้รับผลกระทบจากความร้อนขนาดเล็ก โดยคงคุณสมบัติทางกลของวัสดุ และลดการเปลี่ยนรูปเนื่องจากความร้อนให้เหลือน้อยที่สุด สามารถใช้เพื่อให้ได้การตัดที่แม่นยำและการใช้งานที่ต้องการพิกัดความเผื่อต่ำ
ข้อเสีย
- ความเร็วในการตัดช้าลง: หากไม่มีปฏิกิริยาคายความร้อนจากออกซิเจน การตัดโดยใช้ไนโตรเจนช่วยมักจะส่งผลให้ความเร็วในการตัดช้าลง โดยเฉพาะอย่างยิ่งเมื่อใช้กับวัสดุที่หนากว่า ความเร็วที่ช้าลงนี้ส่งผลต่อประสิทธิภาพการผลิตโดยรวม
- ข้อกำหนดด้านพลังงานเลเซอร์ที่สูงขึ้น: เนื่องจากไนโตรเจนไม่ได้ให้ความร้อนเพิ่มเติมแก่กระบวนการตัด เลเซอร์จึงต้องให้พลังงานทั้งหมดที่จำเป็นในการตัดวัสดุ ข้อกำหนดนี้อาจส่งผลให้มีการใช้พลังงานและต้นทุนการดำเนินงานสูงขึ้น
- ข้อควรพิจารณาด้านต้นทุน: ไนโตรเจนอาจมีราคาแพงกว่าก๊าซอื่นๆ และการบริโภคที่เพิ่มขึ้นที่เกิดจากความต้องการพลังงานเลเซอร์ที่สูงขึ้นอาจทำให้ต้นทุนการดำเนินงานเพิ่มขึ้นอีก
อากาศอัด
ข้อดี
- คุ้มต้นทุน: อากาศอัดมีพร้อมใช้มากกว่าและมีราคาถูกกว่าก๊าซบริสุทธิ์ เช่น ไนโตรเจนและออกซิเจน ทำให้เป็นตัวเลือกที่ประหยัดสำหรับการใช้งานตัดด้วยเลเซอร์หลายประเภท โดยเฉพาะอย่างยิ่งงานที่เกี่ยวข้องกับวัสดุที่บางกว่า
- ความหลากหลาย: สามารถใช้ลมอัดเพื่อตัดวัสดุได้หลายประเภท รวมถึงเหล็กเหนียว สแตนเลส และอะลูมิเนียม ความอเนกประสงค์ทำให้เป็นตัวเลือกที่ใช้งานได้จริงสำหรับการตัดอเนกประสงค์
- ต้นทุนการดำเนินงานที่ลดลง: เนื่องจากอากาศอัดมีราคาไม่แพงและมีจำหน่ายกันอย่างแพร่หลาย การใช้อากาศอัดสามารถลดต้นทุนการดำเนินงานโดยรวมได้ ทำให้เหมาะสำหรับการดำเนินงานขนาดเล็กหรือโครงการที่คำนึงถึงงบประมาณ
- ประโยชน์ด้านสิ่งแวดล้อม: การใช้อากาศอัดช่วยลดการพึ่งพาก๊าซบรรจุขวด ซึ่งจะช่วยลดการปล่อยก๊าซคาร์บอนไดออกไซด์ที่เกี่ยวข้องกับการผลิตและการขนส่งก๊าซ ซึ่งเป็นประโยชน์ต่อสิ่งแวดล้อม
ข้อเสีย
- คุณภาพการตัดที่ต่ำกว่า: ออกซิเจนและสิ่งสกปรกในอากาศอัดอาจส่งผลต่อคุณภาพการตัด ส่งผลให้ขอบมีความหยาบมากขึ้น มีขี้เถ้าเพิ่มขึ้น และอาจเกิดการปนเปื้อนของพื้นผิวการตัด ปัญหานี้สังเกตได้ชัดเจนเป็นพิเศษในการใช้งานที่ต้องการคุณภาพพื้นผิวหรือความแม่นยำสูง
- ความเร็วในการตัดที่จำกัด: โดยทั่วไปแล้วอากาศอัดจะทำการตัดด้วยความเร็วที่ช้ากว่าการตัดโดยใช้ออกซิเจนช่วย โดยเฉพาะอย่างยิ่งสำหรับวัสดุที่หนากว่า ข้อจำกัดนี้ส่งผลต่อความสามารถในการผลิตและอาจไม่เหมาะสำหรับการผลิตที่มีปริมาณมาก
- ผลลัพธ์ที่ไม่สอดคล้องกัน: คุณภาพและประสิทธิภาพของการตัดด้วยอากาศอัดอาจไม่สอดคล้องกัน เนื่องจากความแตกต่างในองค์ประกอบและความดันของการจ่ายอากาศ ความไม่สอดคล้องกันนี้ทำให้เกิดความท้าทายในการบรรลุผลลัพธ์ที่สม่ำเสมอจากงานตัดชิ้นหนึ่งไปยังอีกชิ้นหนึ่ง
- การเกิดออกซิเดชันและการเกิดขี้เถ้า: อากาศอัดประกอบด้วยก๊าซหลายชนิด รวมถึงออกซิเจน ซึ่งสามารถทำให้เกิดออกซิเดชันและการเกิดขี้เถ้าบนคมตัด ซึ่งจำเป็นต้องมีการประมวลผลเพิ่มเติมในภายหลังเพื่อให้ได้ผลลัพธ์ตามที่ต้องการ
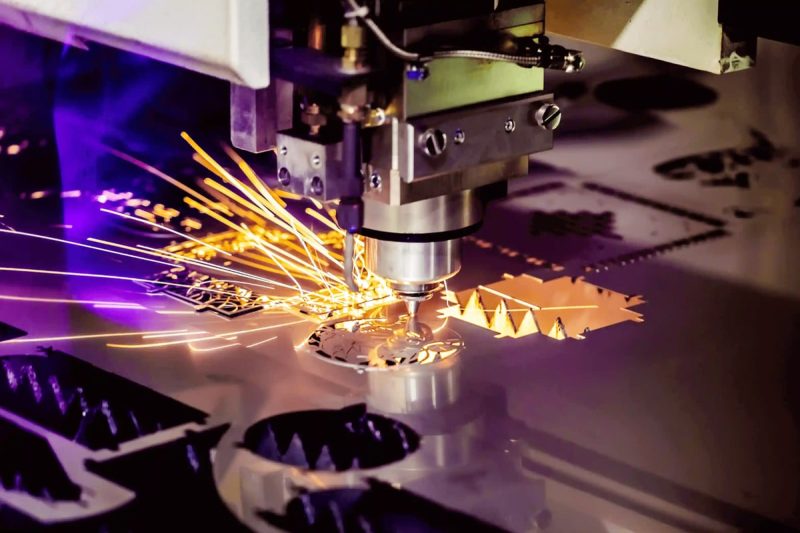
ผลกระทบต่อวัสดุที่แตกต่างกัน
เหล็กกล้าคาร์บอน
ออกซิเจน
- ข้อดี: มักใช้ออกซิเจนในการตัดเหล็กกล้าคาร์บอน เนื่องจากออกซิเจนจะทำปฏิกิริยากับวัสดุแบบคายความร้อน ปฏิกิริยานี้ทำให้เกิดความร้อนเพิ่มขึ้น ซึ่งจะทำให้ความเร็วและประสิทธิภาพการตัดเพิ่มขึ้นอย่างมาก โดยทั่วไปการตัดที่ได้จะสะอาดและมีขี้เถ้าน้อยที่สุด และความร้อนที่เพิ่มขึ้นจะช่วยตัดส่วนเหล็กกล้าคาร์บอนที่หนาขึ้น
- ข้อเสีย: ปฏิกิริยาคายความร้อนกับออกซิเจนทำให้เกิดออกซิเดชัน ซึ่งหากไม่ทำปฏิกิริยา อาจส่งผลให้พื้นผิวมีความหยาบขึ้นและอาจเกิดการกัดกร่อนได้ โซนรับผลกระทบความร้อน (HAZ) ก็มีขนาดใหญ่กว่าเช่นกัน ซึ่งอาจส่งผลต่อคุณสมบัติทางกลของวัสดุใกล้กับคมตัด
ไนโตรเจน
- ข้อดี: ไนโตรเจนไม่ทำปฏิกิริยากับเหล็กกล้าคาร์บอน ป้องกันการเกิดออกซิเดชัน และได้การตัดที่สะอาดปราศจากออกไซด์ ส่งผลให้ได้พื้นผิวคุณภาพสูงและมี HAZ น้อยลง ซึ่งยังคงรักษาคุณสมบัติทางกลของวัสดุไว้
- ข้อเสีย: การขาดปฏิกิริยาคายความร้อนหมายความว่าการตัดโดยใช้ไนโตรเจนช่วยจะช้ากว่าการตัดโดยใช้ออกซิเจนช่วย เพื่อให้ได้ความเร็วตัดเท่ากัน จำเป็นต้องใช้กำลังเลเซอร์ที่สูงขึ้น ซึ่งจะทำให้ต้นทุนการดำเนินงานเพิ่มขึ้น
อากาศอัด
- ข้อดี: อากาศอัดเป็นทางเลือกที่คุ้มค่าสำหรับการตัดเหล็กคาร์บอน มีความสมดุลระหว่างต้นทุนและประสิทธิภาพ และเหมาะสำหรับการตัดส่วนเหล็กกล้าคาร์บอนที่บางลง
- ข้อเสีย: ออกซิเจนในอากาศอัดอาจทำให้เกิดออกซิเดชันและเกิดขี้เลื่อย ซึ่งส่งผลต่อคุณภาพการตัด โดยทั่วไปความเร็วและคุณภาพการตัดจะต่ำกว่าเมื่อใช้ออกซิเจนหรือไนโตรเจนบริสุทธิ์
เหล็กกล้าไร้สนิม
ออกซิเจน
- ข้อดี: สามารถใช้ออกซิเจนในการตัดเหล็กสเตนเลสได้ ซึ่งให้ความเร็วในการตัดที่รวดเร็วเนื่องจากปฏิกิริยาคายความร้อน ปฏิกิริยานี้ยังช่วยให้ได้การตัดที่สะอาดและมีคราบสกปรกน้อยที่สุด
- ข้อเสีย: การใช้ออกซิเจนอาจทำให้เกิดออกซิเดชั่น ซึ่งอาจนำไปสู่การเปลี่ยนสีของขอบและปัญหาการกัดกร่อนที่อาจเกิดขึ้นได้ ชั้นออกไซด์อาจต้องมีการประมวลผลเพิ่มเติมเพื่อให้ได้คุณภาพพื้นผิวที่ต้องการ
ไนโตรเจน
- ข้อดี: ไนโตรเจนเป็นก๊าซที่เลือกใช้ตัดเหล็กสแตนเลส เนื่องจากป้องกันการเกิดออกซิเดชัน ส่งผลให้ขอบสะอาด สว่าง ปราศจากออกไซด์ ธรรมชาติเฉื่อยของไนโตรเจนทำให้เกิดการตัดคุณภาพสูงโดยแทบไม่ต้องมีขั้นตอนหลังการประมวลผล ไนโตรเจนยังช่วยรักษาคุณสมบัติทางกลของวัสดุโดยการลดโซนที่ได้รับผลกระทบจากความร้อนให้เหลือน้อยที่สุด
- ข้อเสีย: ไนโตรเจนมีความเร็วในการตัดช้ากว่าและต้องการพลังงานเลเซอร์สูงกว่าออกซิเจน ส่งผลให้มีการใช้พลังงานและต้นทุนการดำเนินงานเพิ่มขึ้น
อากาศอัด
- ข้อดี: สามารถใช้ลมอัดเพื่อตัดส่วนที่บางกว่าของเหล็กสเตนเลสได้ คุ้มต้นทุนมากกว่าก๊าซบริสุทธิ์ และเป็นตัวเลือกที่เหมาะสมสำหรับการใช้งานที่ไม่ต้องการความแม่นยำสูง
- ข้อเสีย: ออกซิเจนในอากาศอัดอาจทำให้เกิดออกซิเดชันและเกิดขี้เถ้า ซึ่งส่งผลต่อคุณภาพการตัด ขอบอาจต้องมีการทำความสะอาดและตกแต่งเพิ่มเติมหลังการตัด
อลูมิเนียมและโลหะนอกกลุ่มเหล็ก
ออกซิเจน
- ข้อดี: โดยทั่วไปไม่แนะนำให้ใช้ออกซิเจนในการตัดอะลูมิเนียมและโลหะที่ไม่ใช่เหล็กอื่นๆ เนื่องจากมีความสามารถในการสะท้อนแสงสูงและการดูดซับลำแสงเลเซอร์ต่ำ อย่างไรก็ตาม ในบางกรณี ออกซิเจนสามารถช่วยลดส่วนที่หนาขึ้นได้โดยการส่งเสริมให้เกิดปฏิกิริยาคายความร้อน
- ข้อเสีย: ออกซิเจนอาจทำให้เกิดออกซิเดชันอย่างรุนแรง ส่งผลให้พื้นผิวการตัดหยาบและมีรูพรุน การเกิดออกซิเดชันนี้อาจส่งผลเสียต่อคุณสมบัติและรูปลักษณ์ของวัสดุ ซึ่งต้องผ่านกระบวนการหลังการประมวลผลอย่างกว้างขวาง
ไนโตรเจน
- ข้อดี: ไนโตรเจนมีประสิทธิภาพมากในการตัดอะลูมิเนียมและโลหะที่ไม่ใช่เหล็กอื่นๆ ป้องกันการเกิดออกซิเดชัน ส่งผลให้ขอบสะอาด สว่าง และมีคุณภาพสูง ไนโตรเจนยังช่วยลดโซนที่ได้รับผลกระทบจากความร้อน โดยรักษาคุณสมบัติทางกลของวัสดุ
- ข้อเสีย: การตัดโดยใช้ไนโตรเจนช่วยจะช้ากว่าการใช้ออกซิเจน และต้องใช้กำลังเลเซอร์สูงกว่าในการตัดวัสดุ ซึ่งจะทำให้ต้นทุนการดำเนินงานเพิ่มขึ้น
อากาศอัด
- ข้อดี: อากาศอัดเป็นตัวเลือกที่คุ้มต้นทุนสำหรับการตัดส่วนที่บางกว่าของอะลูมิเนียมและโลหะนอกกลุ่มเหล็ก สามารถให้ประสิทธิภาพการตัดที่น่าพอใจสำหรับการใช้งานที่ความแม่นยำไม่สำคัญ
- ข้อเสีย: ออกซิเจนในอากาศอัดอาจทำให้เกิดออกซิเดชันและเกิดขี้เถ้า ซึ่งส่งผลต่อคุณภาพการตัด ขอบอาจต้องมีการประมวลผลเพิ่มเติมเพื่อให้ได้ผลลัพธ์ตามที่ต้องการ
วัสดุที่ไม่ใช่โลหะ
ออกซิเจน
- ข้อดี: สามารถใช้ออกซิเจนในการตัดวัสดุที่ไม่ใช่โลหะ เช่น ไม้ อะคริลิค และพลาสติก ปฏิกิริยาคายความร้อนกับออกซิเจนสามารถเพิ่มความเร็วตัดและประสิทธิภาพของวัสดุบางชนิดได้
- ข้อเสีย: การใช้ออกซิเจนอาจทำให้วัสดุ เช่น ไม้และอะคริลิกไหม้เกรียมและไหม้ ซึ่งส่งผลเสียต่อคุณภาพพื้นผิว ซึ่งอาจส่งผลให้ต้องมีกระบวนการตกแต่งเพิ่มเติมเพื่อให้ได้รูปลักษณ์ที่ต้องการ
ไนโตรเจน
- ข้อดี: ไนโตรเจนเหมาะอย่างยิ่งสำหรับการตัดวัสดุที่ไม่ใช่โลหะ เช่น พลาสติกและเซรามิก ซึ่งต้องได้รับการปกป้องจากการเกิดออกซิเดชัน ป้องกันการเปลี่ยนสีและสร้างขอบที่สะอาดและมีคุณภาพสูง ในขณะเดียวกันก็ลดความเสียหายจากความร้อนให้เหลือน้อยที่สุด
- ข้อเสีย: การตัดโดยใช้ไนโตรเจนอาจช้ากว่าออกซิเจน ซึ่งต้องใช้กำลังเลเซอร์สูงกว่าเพื่อให้ได้ความเร็วตัดตามที่ต้องการ
อากาศอัด
- ข้อดี: อากาศอัดเป็นโซลูชันที่คุ้มค่าสำหรับการตัดวัสดุที่ไม่ใช่โลหะ และให้ประสิทธิภาพการตัดที่เพียงพอสำหรับการใช้งานที่หลากหลาย เหมาะสำหรับการใช้งานที่ความแม่นยำและคุณภาพไม่สำคัญ
- ข้อเสีย: สิ่งเจือปนในอากาศอัดอาจส่งผลต่อคุณภาพการตัด ส่งผลให้เกิดขอบหยาบและอาจเกิดการปนเปื้อน คุณภาพและความเร็วในการตัดอาจเทียบไม่ได้กับก๊าซบริสุทธิ์ เช่น ออกซิเจนหรือไนโตรเจน
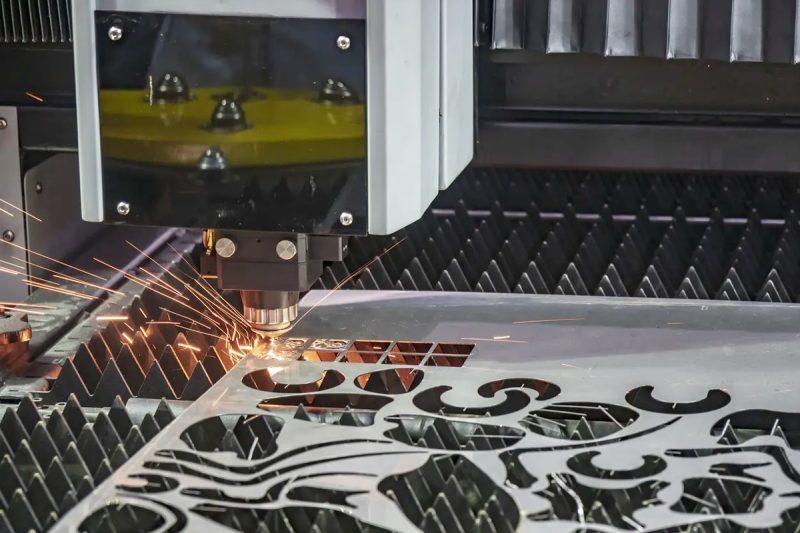
การเพิ่มประสิทธิภาพการเลือกก๊าซช่วย
ประเภทวัสดุและความหนา
ประเภทและความหนาของวัสดุที่ถูกตัดถือเป็นข้อพิจารณาที่สำคัญเมื่อเลือกแก๊สช่วย วัสดุที่แตกต่างกันทำปฏิกิริยากับก๊าซต่างกัน ส่งผลต่อคุณภาพและประสิทธิภาพของการตัด
- เหล็กกล้าคาร์บอน: ออกซิเจนมักเป็นตัวเลือกแรกในการตัดเหล็กกล้าคาร์บอน เนื่องจากมีปฏิกิริยาคายความร้อน ซึ่งจะเพิ่มความเร็วและประสิทธิภาพในการตัด สำหรับเหล็กกล้าคาร์บอนที่หนาขึ้น ออกซิเจนสามารถให้ความร้อนที่จำเป็นในการตัดวัสดุได้อย่างมีประสิทธิภาพ สำหรับเหล็กกล้าคาร์บอนที่บางกว่า สามารถใช้ไนโตรเจนเพื่อให้ได้การตัดที่สะอาดและปราศจากออกซิเดชัน แม้ว่าจะใช้ในอัตราที่ช้ากว่าก็ตาม
- เหล็กกล้าไร้สนิม: ไนโตรเจนเหมาะอย่างยิ่งสำหรับการตัดเหล็กกล้าไร้สนิม เนื่องจากจะป้องกันการเกิดออกซิเดชันและสร้างขอบที่เรียบและมีคุณภาพสูง สำหรับเหล็กสเตนเลสที่มีความหนามาก สามารถใช้ออกซิเจนเพื่อเพิ่มความเร็วในการตัดได้ แต่จะทำให้เกิดออกซิเดชัน ซึ่งต้องผ่านกระบวนการหลังการประมวลผล
- อะลูมิเนียมและโลหะนอกกลุ่มเหล็ก: ไนโตรเจนเป็นตัวเลือกแรกสำหรับการตัดอะลูมิเนียมและโลหะนอกกลุ่มเหล็ก เพื่อหลีกเลี่ยงการเกิดออกซิเดชันและให้การตัดที่สะอาด สำหรับการใช้งานที่มีความสำคัญน้อยกว่า อากาศอัดอาจเป็นทางเลือกที่คุ้มค่า แม้ว่าอาจทำให้เกิดออกซิเดชันบ้างก็ตาม
- วัสดุที่ไม่ใช่โลหะ: สำหรับการตัดวัสดุที่ไม่ใช่โลหะ เช่น พลาสติก เซรามิก และไม้ มักใช้ไนโตรเจนเพื่อป้องกันการเปลี่ยนสีและให้คมตัดคุณภาพสูง ออกซิเจนสามารถใช้เพื่อตัดอโลหะบางชนิดได้เร็วขึ้น แต่อาจทำให้เกิดการไหม้หรือไหม้ได้
คุณภาพการตัดที่ต้องการ
คุณภาพการตัดที่ต้องการเป็นปัจจัยสำคัญในการเลือกก๊าซช่วยเหลือที่เหมาะสม การใช้งานที่มีความแม่นยำมักต้องใช้การตัดคุณภาพสูงโดยมีการเกิดออกซิเดชันน้อยที่สุดและขอบเรียบ
- การตกแต่งพื้นผิวคุณภาพสูง: ไนโตรเจนมักเป็นตัวเลือกที่ดีที่สุดสำหรับการใช้งานที่ต้องการการตัดที่แม่นยำ สะอาด และปราศจากออกซิเดชั่น ป้องกันการเกิดออกซิเดชัน ส่งผลให้ขอบเรียบและคุณภาพผิวสำเร็จสูง
- คุณภาพทั่วไป: ออกซิเจนสามารถให้การตัดคุณภาพสูงโดยมีขี้เถ้าน้อยที่สุด แต่ขอบอาจต้องทำความสะอาดเพิ่มเติมเนื่องจากออกซิเดชั่น อากาศอัดอาจเหมาะสำหรับการใช้งานที่มีความสำคัญน้อยกว่า โดยไม่จำเป็นต้องมีคุณภาพผิวสำเร็จสูงสุด
ความเร็วตัดและประสิทธิภาพ
ความเร็วตัดและประสิทธิภาพจะขึ้นอยู่กับประเภทของแก๊สช่วยที่ใช้ เป้าหมายคือการบรรลุความเร็วสูงสุดที่เป็นไปได้โดยไม่กระทบต่อคุณภาพการตัด
- ความเร็วสูงสุด: ให้ความเร็วตัดที่เร็วที่สุดสำหรับเหล็กกล้าคาร์บอนและวัสดุที่มีความหนามากขึ้น เนื่องจากปฏิกิริยาคายความร้อนของออกซิเจน ซึ่งจะเพิ่มความร้อนเพิ่มเติมให้กับกระบวนการตัด
- ความเร็วและคุณภาพที่สมดุล: ไนโตรเจนสร้างสมดุลระหว่างความเร็วและการตัดคุณภาพสูง แม้ว่าอาจต้องใช้กำลังเลเซอร์สูงกว่าและการตัดด้วยความเร็วที่ช้ากว่าเมื่อเทียบกับออกซิเจนก็ตาม
- ความเร็วที่คุ้มค่า: อากาศอัดมีการประนีประนอมระหว่างความเร็วและต้นทุน เหมาะสำหรับการใช้งานที่ความเร็วตัดปานกลางและคุณภาพสมเหตุสมผลเป็นที่ยอมรับได้
การพิจารณาต้นทุน
ต้นทุนเป็นปัจจัยสำคัญในการช่วยในการเลือกก๊าซ ซึ่งส่งผลต่อค่าใช้จ่ายในการดำเนินงานและความคุ้มทุนโดยรวม
- ต้นทุนการดำเนินงานที่ลดลง: อากาศอัดเป็นทางเลือกที่ประหยัดที่สุด เนื่องจากหาได้ง่ายและราคาถูกกว่าก๊าซบริสุทธิ์ เช่น ออกซิเจนและไนโตรเจน เหมาะอย่างยิ่งสำหรับการตัดวัสดุที่มีความสำคัญน้อยกว่าหรือเมื่อข้อจำกัดด้านงบประมาณเป็นเรื่องสำคัญ
- คุณภาพที่สูงขึ้นและต้นทุนที่สูงขึ้น: ไนโตรเจนแม้จะมีราคาแพงกว่า แต่ก็ให้คุณภาพการตัดที่ดีกว่า ต้นทุนเพิ่มเติมนั้นสมเหตุสมผลด้วยคุณภาพที่ดีขึ้นและความจำเป็นในการประมวลผลภายหลังที่ลดลง
- ต้นทุนและประสิทธิภาพสมดุล: ออกซิเจนเป็นจุดกลาง โดยให้ความเร็วตัดที่รวดเร็วและคุณภาพที่เหมาะสมในราคาปานกลาง เหมาะสำหรับงานอุตสาหกรรมหลายประเภทที่ทั้งความเร็วและคุณภาพมีความสำคัญ
ข้อกำหนดหลังการประมวลผล
ความต้องการหลังการประมวลผลสามารถมีอิทธิพลต่อการเลือกก๊าซได้ เนื่องจากก๊าซบางชนิดทำให้เกิดการตัดที่สะอาดขึ้น ซึ่งสามารถลดงานตกแต่งขั้นสุดท้ายได้
- ขั้นตอนหลังการประมวลผลน้อยที่สุด: ไนโตรเจนสร้างการตัดที่สะอาดและปราศจากออกซิเดชั่น ลดความจำเป็นในขั้นตอนหลังการประมวลผลอย่างกว้างขวาง และประหยัดเวลาและค่าใช้จ่ายในการดำเนินการเก็บผิวละเอียด
- การประมวลผลภายหลังระดับปานกลาง: การตัดด้วยออกซิเจนอาจต้องมีขั้นตอนเพิ่มเติมเพื่อขจัดออกไซด์และทำให้ได้พื้นผิวสำเร็จตามที่ต้องการ อย่างไรก็ตาม ความเร็วในการตัดที่เร็วขึ้นสามารถชดเชยต้นทุนเพิ่มเติมบางส่วนได้
- การประมวลผลภายหลังที่เพิ่มขึ้น: การอัดอากาศอาจทำให้เกิดคราบสกปรกและออกซิเดชั่นมากขึ้น ซึ่งจำเป็นต้องมีการประมวลผลภายหลังอย่างกว้างขวางมากขึ้นเพื่อทำความสะอาดและตกแต่งขอบให้เสร็จ สิ่งนี้สามารถเพิ่มเวลาและต้นทุนการผลิตโดยรวมได้
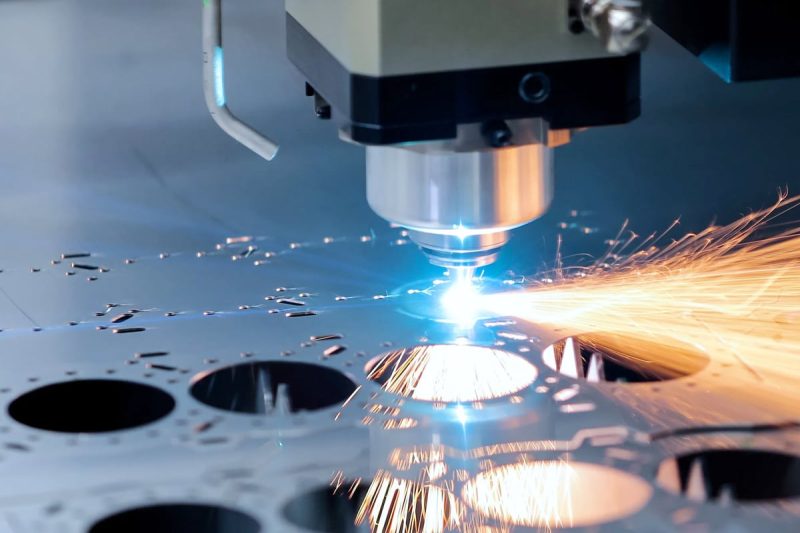
สรุป
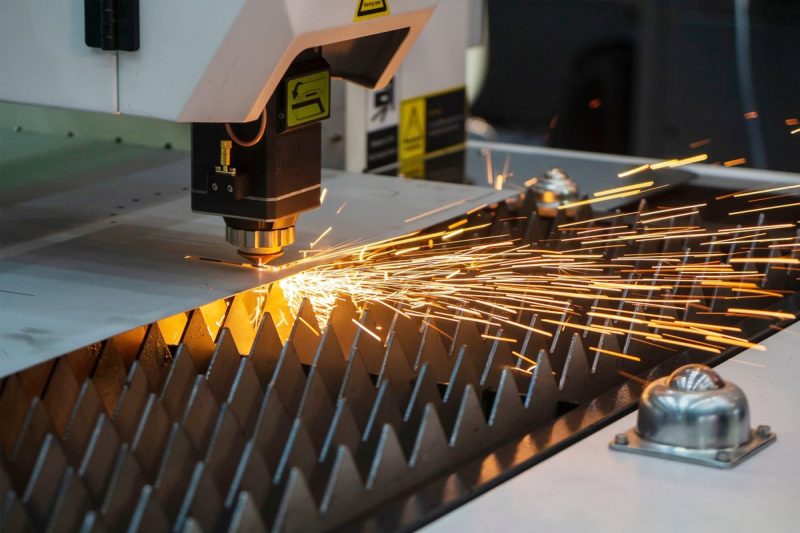
รับโซลูชันการตัดด้วยเลเซอร์
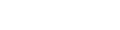
- [email protected]
- [email protected]
- +86-19963414011
- หมายเลข 3 โซน A เขตอุตสาหกรรม Luzhen เมือง Yucheng มณฑลซานตง