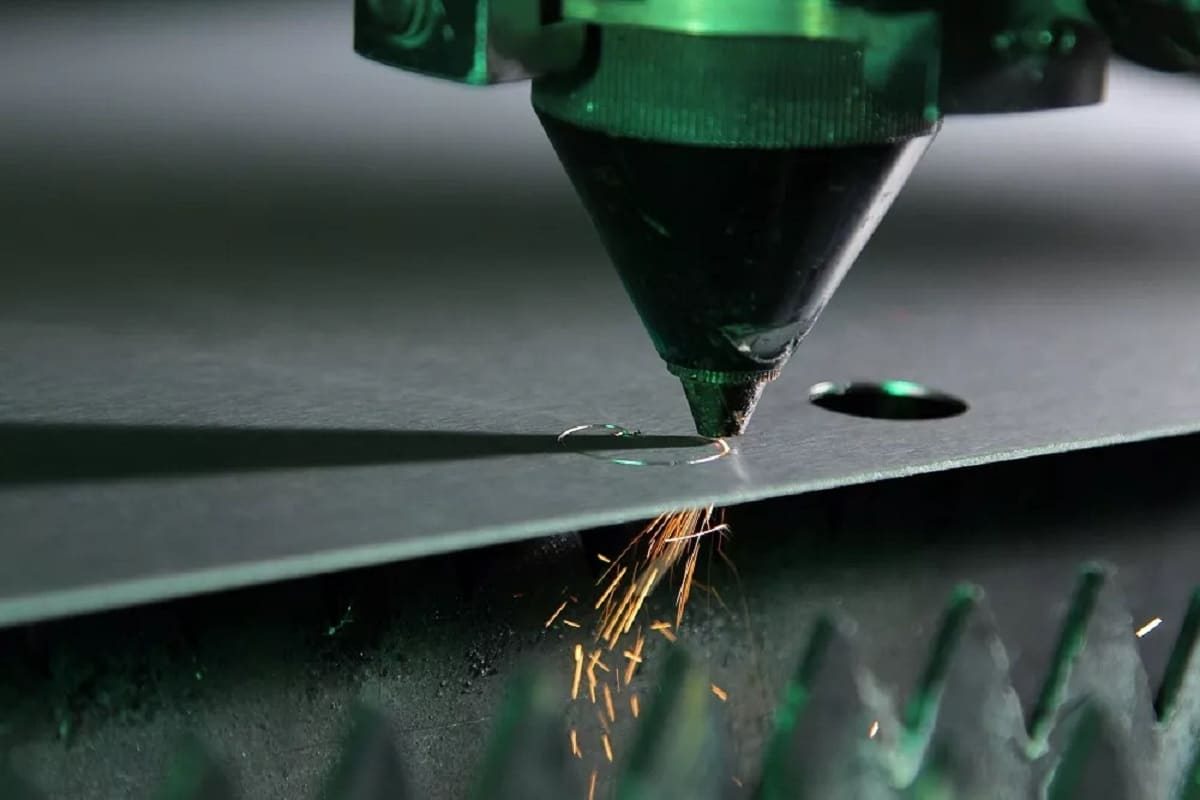
The Impact of CO2 Laser Wavelength on Cutting Capabilities
Laser technology plays a vital role in modern manufacturing, including fiber laser, CO2 laser, UV laser, and other types. As an important type of CO2 laser generator, its wavelength has a profound impact on cutting capabilities.
This article will delve into how the wavelength of the CO2 laser generator affects the cutting ability, covering the basic principles of the CO2 laser generator, the impact of wavelength and material cutting, and how to choose the best laser wavelength. A deeper understanding of the relationship between wavelength and cutting capacity will help improve cutting efficiency and quality.
Table Of Contents
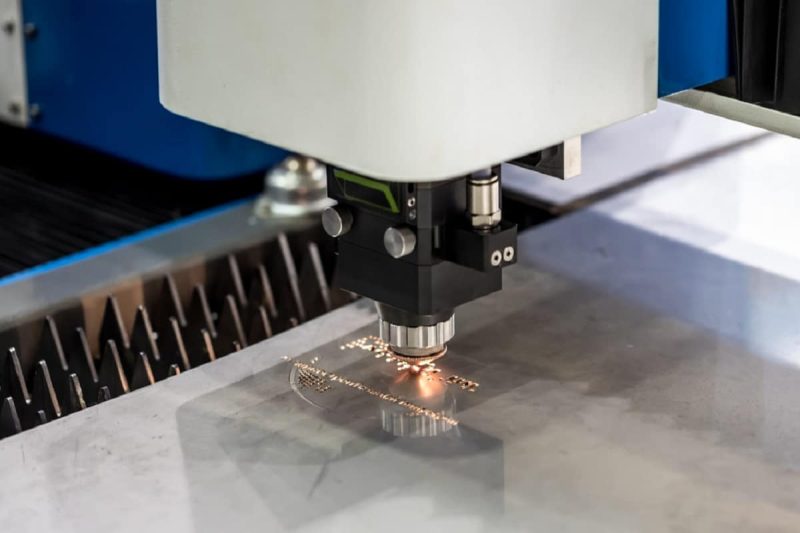
Basic principles of CO2 laser generator
A CO2 laser generator is a device that generates laser light by converting electrical energy into laser radiation. Understanding the generation process of CO2 laser is crucial to the subsequent discussion of how wavelength affects cutting capabilities. The following is the specific working principle of the CO2 laser generator:
- The basic composition of the CO2 laser generator: The CO2 laser generator uses carbon dioxide gas as the excitation medium. It mainly consists of excitation gas, an energy supply system, and an optical chamber.
- Exciting gas energy level transitions: Electrical energy passes through the gas to excite electrons in gas molecules. Make it jump to a high energy level. CO2 laser generator mainly uses the vibration and rotation transition of CO2 molecules.
- Energy level deexcitation process: High energy level molecules deexcite to lower energy levels through collision or radiation. The photons generated by the deexcitation process of carbon dioxide molecules are exactly at 10.6 microns and belong to red light.
- Optical cavity amplification: The optical cavity contains a mirror, which causes the excited light to be reflected multiple times in it, producing a light amplification effect. Through the amplification of the optical cavity, the CO2 laser generator can generate high-intensity, high-energy laser beams.
- Laser output: Finally, through the output mirror, the high-intensity CO2 laser is released. CO2 laser generators usually output laser light in the wavelength range of 10.6 microns, which is their main operating wavelength.
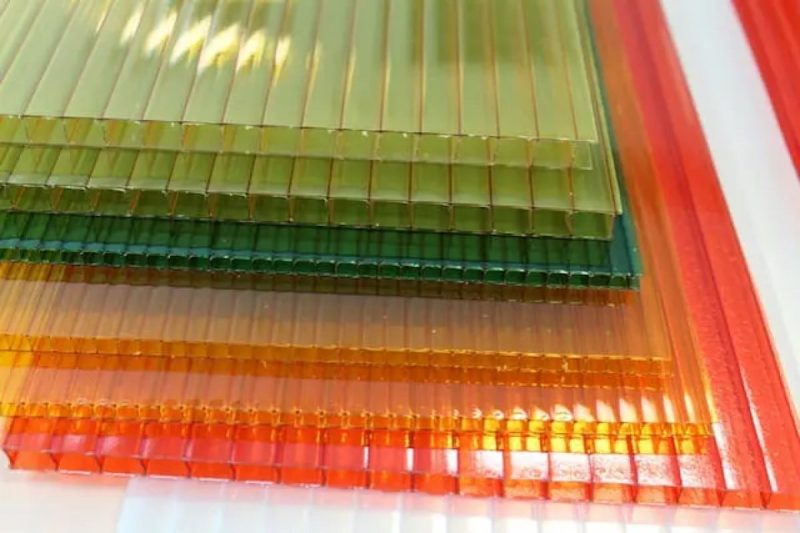
The relationship between wavelength and cutting ability
Laser cutting is a complex and precise processing technology. The wavelength of the laser has a profound impact on cutting ability. By describing the effect of wavelength on material absorption, changes in heat conduction and melting properties, and the relationship between cutting speed and quality, the role of wavelength in laser cutting can be more comprehensively understood.
Effect of wavelength on material absorption
- Material absorption spectrum: Different materials have different absorption characteristics of the laser, which are closely related to the wavelength of the laser. Generally speaking, the absorption peak of the material is related to the laser wavelength, so the choice of wavelength will directly affect the degree of absorption of laser energy in the material.
- Absorption and energy conversion: Laser energy with shorter wavelengths is more easily absorbed by certain materials, while laser energy with longer wavelengths can penetrate deeper into the material. This necessitates careful selection of wavelengths for optimal energy conversion and cutting results for different types of materials.
Changes in heat transfer and melting properties
- Effect of heat conduction: Changes in wavelength have a significant impact on the heat conduction properties of materials. Generally speaking, shorter wavelength lasers are more likely to cause localized high temperatures because their energy is more concentrated. For some materials with poor thermal conductivity, this can concentrate energy more effectively and cause localized melting.
- Differences in melting properties: Lasers of different wavelengths can also cause changes in the melting properties of materials. For example, materials may be more susceptible to melting and vaporization under short-wavelength lasers, while longer-wavelength lasers may be more suitable for causing surface melting of materials. These differences directly affect the way and results of material handling during the cutting process.
The relationship between cutting speed and quality
- Effect of cutting speed: There is a complex relationship between laser cutting speed and wavelength. In general, shorter wavelength lasers are usually able to cut materials faster due to their more dense energy. However, this also depends on the absorption properties and thermal conductivity of the material.
- Cut quality considerations: There is a trade-off between cut quality and cutting speed. Cutting speed that is too fast may cause the material to be incompletely cut, while cutting too slowly may cause too much heat-affected zone, affecting the cutting quality. Therefore, choosing the right wavelength is critical to maintaining cutting speed while maintaining cut quality.
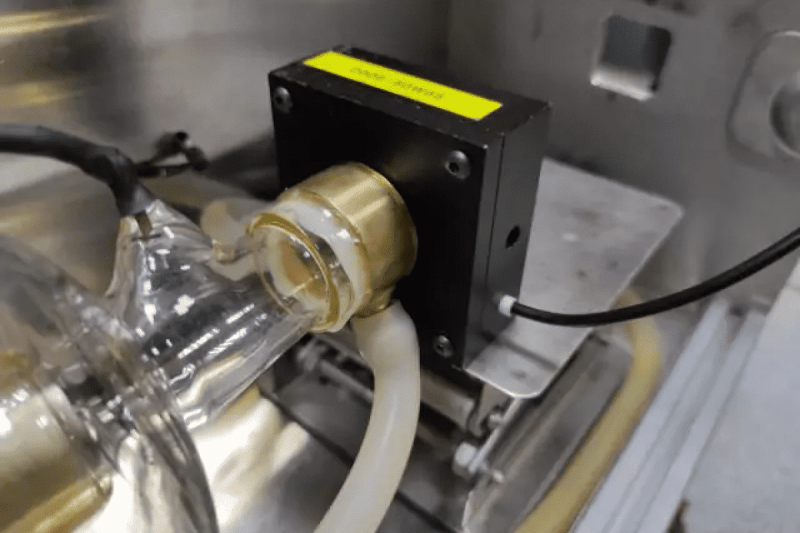
The relationship between material reflectivity and CO2 laser wavelength
The reflectivity of a material refers to the proportion of light that is reflected when it hits the surface of the material. The wavelength of the CO2 laser has a significant impact on the reflectivity of the material. This relationship can be expanded from the following aspects:
Wavelength and material absorption characteristics
- The wavelength of a CO2 laser is usually 10.6 microns, which is in the infrared spectrum.
- The reflectivity of a material is closely related to its absorption properties in this wavelength range. Generally speaking, if a material has high absorptivity in this wavelength range, its reflectivity will be relatively low.
Special reflective properties of metal materials
- For metal materials, the wavelength of the CO2 laser is at the edge of its plasma frequency band, causing the metal to exhibit extremely low reflectivity for lasers of this wavelength.
- This special reflective property makes CO2 laser particularly suitable for metal cutting because more energy is absorbed rather than reflected, improving cutting efficiency.
Considerations for non-metallic materials
- For non-metallic materials, the wavelength of the CO2 laser can also affect its reflectivity. Some non-metallic materials may exhibit high reflectivity at this wavelength, making it difficult for laser energy to effectively penetrate the material surface.
- In this case, you need to consider adjusting the power and other parameters of the laser to achieve better-cutting results.
Applications of multi-wavelength laser systems
- Some modern laser cutting systems use multi-wavelength laser sources to accommodate the needs of different types of materials. Such a system can select the appropriate wavelength based on the characteristics of the material to maximize cutting efficiency.
- Understanding this relationship is crucial to optimizing the cutting process and improving processing efficiency. In practical applications, the material type and process requirements need to be selected according to the CO2 laser wavelength to achieve the best cutting effect.
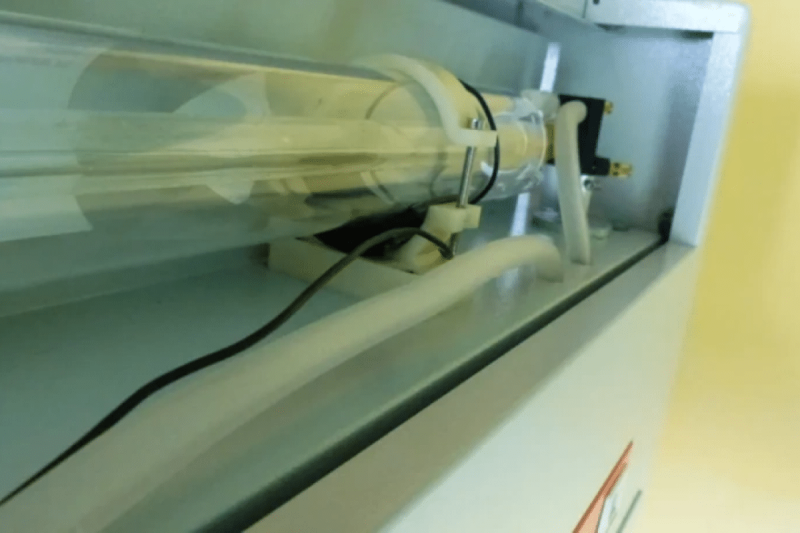
Development Trend of CO2 Laser Technology
Based on estimates of current laser technology and ma rket demand, CO2 laser technology will make new progress in the future. Future development will also be affected by many factors such as technological innovation and changes in market demand.
High power and efficiency
The application demand for CO2 laser technology in cutting, welding, and marking is increasing. One of the future trends is to improve the power and efficiency of CO2 laser generators to meet the needs of larger-scale, higher-speed industrial applications.
Multi-wavelength and hybrid laser systems
Combining lasers of different wavelengths, or combining CO2 lasers with other laser technologies, is expected to create more flexible and versatile laser systems that can adapt to the needs of different materials and applications.
Advanced Optical Design
By adopting advanced optical design and control systems, laser beam quality, focusing accuracy, and cutting quality can be improved. This is key to improving machining accuracy and enabling the cutting of more complex shapes.
Intelligence and automation
With the advancement of industrial intelligence, CO2 laser systems are also developing in the direction of intelligence and automation. Integrating advanced control systems and sensors enables the laser system to achieve a higher degree of automation and intelligent operation.
Application field expansion
CO2 laser technology is not only widely used in traditional cutting and welding fields, but is also expected to make progress in emerging fields such as medical care, communications, and life sciences. For example, in biomedicine, CO2 lasers are used for surgical cutting and tissue repair.
Green environmental protection
In the development of laser technology, more and more attention is paid to energy efficiency and environmental protection. Future CO2 laser systems may focus more on reducing energy consumption and emissions to meet the requirements of sustainable development.
Customization and miniaturization
As technology advances, CO2 laser systems may become more compact, lighter, and more flexible to suit the needs of different sizes and applications.
Summarize
Overall, the wavelength of a CO2 laser generator plays a key role in cutting capabilities. Lasers of different wavelengths are suitable for different types of materials and cutting tasks. By rationally selecting the wavelength, the cutting effect can be optimized and the processing efficiency improved. In future industrial applications, wavelength research on CO2 laser cutting will continue to play an important role in promoting the continuous advancement of cutting technology.
For those ready to embrace the future of CO2 laser technology, AccTek Laser is your trusted partner. If you are interested in purchasing a CO2 laser cutting machine, please feel free to contact us. Our team is here to help you find the perfect solution for your needs. Let’s redefine cutting together.
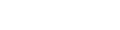
Contact information
- [email protected]
- [email protected]
- +86-19963414011
- No. 3 Zone A, Lunzhen Industrial Zone,Yucheng City , Shandong Province.
Get Laser Solutions