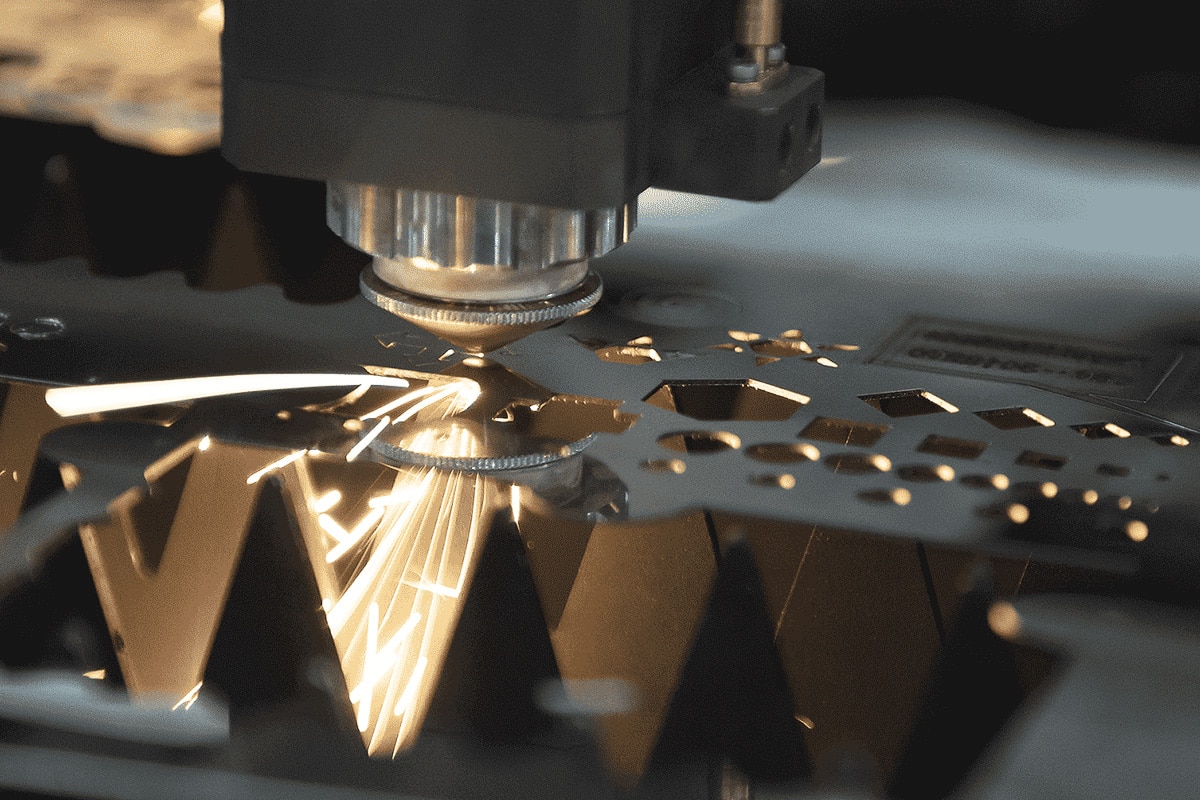
The Influence of Autofocus on the Cutting Accuracy of Fiber Laser Cutting Machine
As an important equipment in the metal processing industry, fiber laser cutting machines are vital in various manufacturing and processing fields. Its cutting accuracy and efficiency not only affect the final quality of the workpiece but are also directly related to production costs and processing efficiency. The focus adjustment of the equipment is crucial to ensure stable and efficient cutting results. The traditional manual focus method is easily affected by human errors and requires frequent adjustments when processing materials of different thicknesses and types, which reduces production efficiency.
The introduction of autofocus technology has greatly optimized the processing capabilities of fiber laser cutting machines. This technology can dynamically adjust the laser focus position in real-time to keep it at the optimal cutting distance from the material surface without manual intervention. This not only improves cutting accuracy but also enhances the adaptability of the equipment to different thicknesses and materials, thereby maintaining stable cutting quality in various complex processing scenarios.
Table of Contents
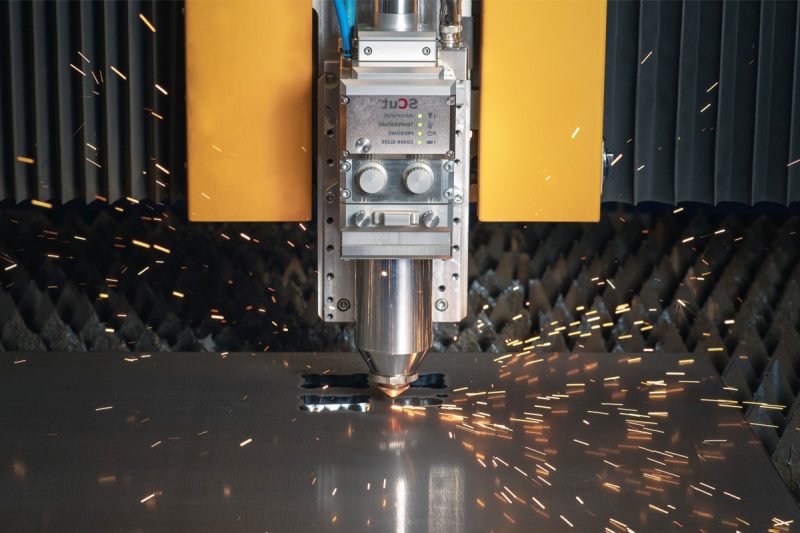
Understanding Autofocus in Fiber Laser Cutting
Definition and function of autofocus
In fiber laser cutting, precise control of focus directly affects cutting quality and efficiency. The traditional manual focusing method is not only time-consuming but also prone to focus deviation due to human error, thus affecting cutting accuracy. The emergence of the autofocus system has greatly improved the intelligence level of laser cutting, enabling the equipment to automatically adjust the laser focus height according to the thickness and surface condition of the material to ensure the best cutting conditions.
The core functions of the autofocus system include:
- Real-time adjustment of focus position: Use sensors and control systems to dynamically detect the material surface height and adjust the focus position in real-time, so that the laser beam is always in the optimal cutting range to ensure high-quality processing.
- Reduce manual adjustment errors: Automated adjustment eliminates the uncertainty of human intervention and improves cutting accuracy and consistency, which is especially important in mass production and complex processing tasks.
- Optimize the processing effect of different materials and thicknesses: When cutting different metal materials or workpieces with large thickness variations, the autofocus system can quickly adjust the focus, avoid errors and efficiency losses caused by manual adjustment, and improve the adaptability and versatility of the equipment.
With the development of intelligent manufacturing, autofocus technology has become a standard feature of high-end fiber laser cutting machines. Its advantages are particularly prominent in application scenarios that require high speed, high precision, and diversified processing.
Types of autofocus systems
At present, the common autofocus systems in fiber laser cutting machines mainly include capacitive autofocus, non-contact autofocus, and autofocus systems based on intelligent control. Different types of systems have their characteristics and are suitable for different processing requirements.
Capacitive autofocus
The capacitive autofocus system uses the change in capacitance between the nozzle and the workpiece surface to detect the focus position and adjust the laser head height in real-time. This technology is based on the principle of electric field induction and can quickly respond to changes in the height of the material surface and maintain a stable focus position during processing.
advantage:
- Applicable to a variety of metal materials, including stainless steel, aluminum alloy, carbon steel, etc., with a wide range of applications;
- Fast response speed, especially suitable for high-speed cutting applications, can accurately adjust the focus position and improve cutting stability;
- The system structure is relatively simple, the maintenance cost is low, and the cost performance is high.
limitation:
- Poor adaptability to non-conductive materials, such as non-metallic materials such as ceramics and plastics, due to the insignificant change in capacitance signals, detection sensitivity decreases;
- May be affected by surface contamination, such as oxidation, dust, or oil, which may affect the accuracy of capacitance measurement and cause focus adjustment errors;
- There are certain limitations in the control of extremely thin or thick materials, and additional optimization of cutting parameters is required.
Capacitive autofocus technology is suitable for metal processing, especially in mass production and standardized processing. However, for special materials or extreme processing environments, its stability and adaptability may need to be further optimized.
Non-contact autofocus
Non-contact autofocus uses optical or laser ranging technology to detect the distance between the nozzle and the material surface through a sensor and dynamically adjust the focus position. Compared with capacitive focus, the non-contact system completely avoids physical contact and is therefore suitable for more types of materials.
advantage:
- Avoid physical contact, reduce sensor wear, increase service life, and reduce failure rate;
- Applicable to more material types, including non-conductive metals, plated materials, and composite materials, expanding the application range of laser cutting;
- Less affected by external pollution, optical or laser ranging technology can work stably in more complex environments, and can maintain high detection accuracy even if there is oil, oxide layer, or dust on the surface of the workpiece;
- Higher accuracy, compared with capacitive focusing, the detection accuracy of non-contact systems is stronger, especially suitable for high-precision micro-machining scenarios.
limitation:
- The system cost is higher. Compared with the capacitive system, the non-contact focus system involves more complex optical or laser sensing technology, which is more expensive;
- Requires higher precision calibration and maintenance. Due to the reliance on optical or laser measurement, the sensor needs to be calibrated regularly to ensure long-term stable focus detection accuracy.
Non-contact autofocus technology is particularly suitable for high-precision and high-requirement processing scenarios, such as microelectronics manufacturing, precision instrument parts cutting, etc., but it may be subject to certain restrictions due to cost factors in general industrial processing.
Autofocus control
Autofocus control is a comprehensive focusing technology that combines software algorithms, sensor feedback, and intelligent control systems. It can not only adjust the focus in real-time but also deeply integrate with the CNC system to achieve more intelligent focus optimization to adapt to different cutting requirements.
advantage:
- It is highly intelligent and can automatically identify different materials and thicknesses, adjust the optimal focus position, and reduce manual intervention;
- It can be seamlessly integrated with the CNC control system to achieve fully automated cutting, improve production efficiency and processing consistency;
- It optimizes cutting parameters through algorithms to maintain the best cutting quality and reduce energy consumption in different processing environments;
- It has strong adaptability and is not only suitable for various metal materials but also can be optimized and adjusted for different surface conditions to improve cutting quality and edge finish.
limitation:
- Depends on the stability of the software and sensors. If the system software or sensor is abnormal, the accuracy of focus control may be affected.
- It is greatly affected by environmental factors. For example, changes in temperature and humidity may affect the accuracy of the sensor, and parameters need to be optimized for different environments.
- It has high technical requirements for operators, and skilled technicians are required to adjust parameters to maximize the performance of the autofocus system.
Autofocus control technology represents the future development direction of fiber laser cutting, especially in the context of intelligent manufacturing and Industry 4.0, its advantages are becoming more and more obvious. Although its cost is high and requires higher skills of operators, its high-precision and intelligent cutting capabilities make it have broad application prospects in the field of high-end manufacturing.
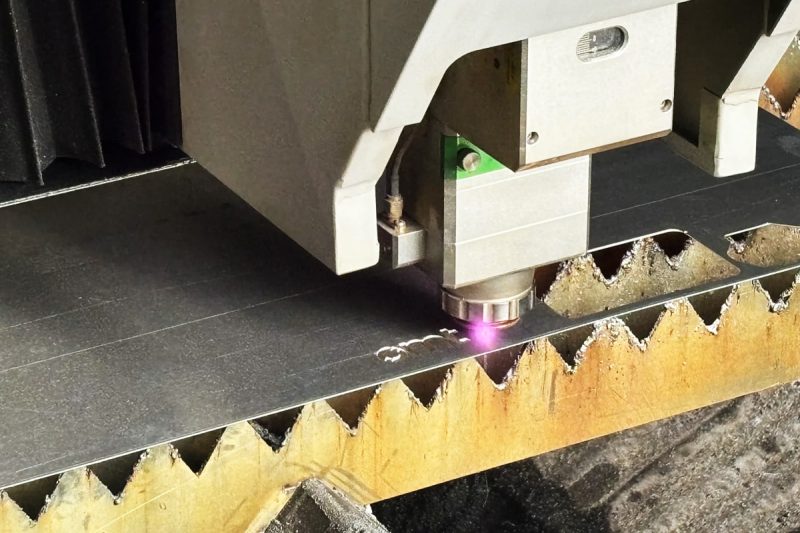
Factors affecting cutting accuracy
The factors that affect the accuracy of fiber laser cutting mainly include material properties, beam quality, nozzle distance, machine stability, and software control.
Material properties: Different materials have a direct impact on cutting accuracy due to their laser absorption rate, thermal conductivity, and melting characteristics. For example, stainless steel, due to its high laser absorption rate, usually produces a smoother cutting edge, while highly reflective materials such as aluminum alloys and copper may reflect the laser, affecting energy absorption and causing unstable cutting. In addition, the thickness of the material will also affect the adjustment of the laser focus. Thicker materials usually require greater laser power and slower cutting speeds to ensure accurate cutting.
Beam quality: The pattern and quality of the laser beam determine the size and energy density of the spot, which in turn affects the precision of the cutting. A high-quality beam usually has a smaller focused spot, which makes the laser energy more concentrated, thereby improving cutting accuracy and reducing the heat-affected zone. If the beam pattern is unstable or the power distribution is uneven, it may cause rough cutting edges or uneven slag residue.
Nozzle distance: The distance between the nozzle and the workpiece surface will affect the flow of auxiliary gas and the stability of cutting. If the nozzle distance is too large, the pressure of the auxiliary gas may be insufficient, resulting in excessive slag residue; if the distance is too small, it may cause turbulent airflow and affect cutting accuracy. Therefore, during the cutting process, it is necessary to ensure the precise adjustment of the nozzle distance to optimize gas flow, reduce cutting defects, and improve the quality of the cutting edge.
Machine stability: The structural stability of the fiber laser cutting machine directly determines the accuracy of the cutting trajectory. High-precision guide rails, lead screws, and servo systems can maintain the smooth operation of the cutting process and reduce the error caused by vibration. If the machine is not rigid enough or the parts are loose after long-term operation, it may cause cutting deviation and affect the final processing effect. Therefore, regular maintenance and inspection of the machine’s stability is essential.
Software control: Advanced software control systems can optimize cutting paths, and adjust laser power and speed to meet the processing needs of different materials and thicknesses. Intelligent software can automatically compensate for errors based on material characteristics to improve cutting consistency. In addition, real-time monitoring and feedback systems can adjust parameters in time to optimize cutting quality. If software control is not accurate or operating parameters are not set properly, it may cause cutting deviations or unnecessary material waste.
In general, to achieve high-precision fiber laser cutting, the above factors must be considered comprehensively, and the stability and consistency of processing quality must be ensured through fine adjustment and optimized control.
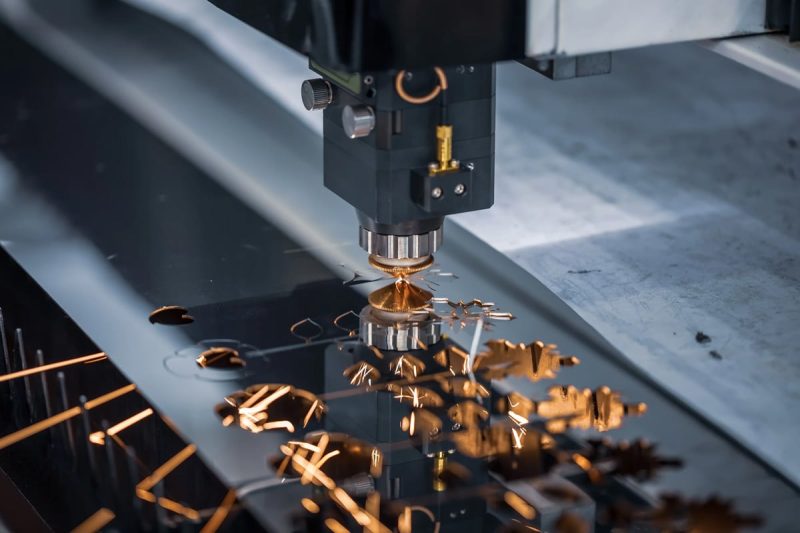
The influence of autofocus on cutting accuracy
Autofocus technology plays a key role in precision and processing efficiency in fiber laser cutting, which is mainly reflected in the following aspects:
Precision and consistency: The autofocus system can adjust the focus position in real-time according to the thickness and surface condition of the material, ensuring that the laser always acts on the optimal focus area. This not only improves the cutting accuracy, but also maintains a stable processing effect in mass production, reduces the error caused by manual adjustment, and improves product consistency.
Reduce preparation time: Traditional manual focus adjustment requires operators to frequently adjust when cutting different thicknesses or materials, which is time-consuming and prone to errors. The autofocus system can quickly complete the focus adjustment, greatly shorten the production preparation time, and improve the overall processing efficiency, especially in the processing scenarios of multiple varieties and small batches.
Adaptability to material changes: Different materials have different laser absorption rates and cutting requirements. The autofocus system can automatically optimize the focus according to the material characteristics, so that the cutting parameters can adapt to various metal materials, from stainless steel to aluminum alloy, to highly reflective materials, ensuring that the cutting quality remains stable at all times and reducing the debugging costs caused by material changes.
Impact on edge quality: Accurate focus control helps reduce the heat-affected zone, making the cutting edge smoother and more vertical, reducing burrs and slag residue. Especially in high-precision processing or workpieces that require subsequent welding and coating, autofocus technology can significantly improve cutting quality and reduce the need for secondary processing.
Through the autofocus system, the fiber laser cutting machine can not only achieve higher processing accuracy, but also improve production efficiency, reduce errors caused by human intervention, and make the cutting process more intelligent and efficient.
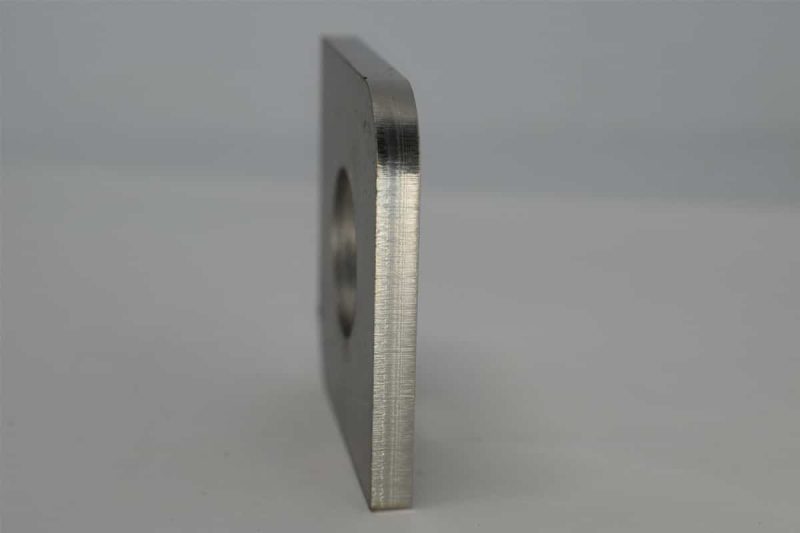
Challenges and Solutions
Although autofocus technology has greatly improved the accuracy and efficiency of fiber laser cutting, it still faces some challenges in practical applications. To ensure the stable operation of the autofocus system, effective solutions need to be taken for the following key issues.
Calibration and maintenance: The autofocus system relies on precision sensors and actuators. If it runs for a long time or lacks maintenance, it may cause focus deviation and affect the cutting quality. Therefore, it is very important to calibrate the autofocus device regularly. Enterprises should establish a strict maintenance plan, including checking sensor sensitivity, cleaning optical components, correcting focus parameters, etc., to ensure that the equipment is always in the best working condition. In addition, the update of the software system should not be ignored. Optimizing algorithms and compensation strategies can further improve the accuracy of autofocus.
Environmental factors: The working environment of the fiber laser cutting machine also has a certain impact on the stability of the autofocus system. For example, factors such as dust, smoke, temperature, and humidity may interfere with the detection accuracy of the sensor. If there is a lot of dust or oil in the cutting environment, it may contaminate the lens and sensor, resulting in abnormal focus detection. Therefore, it is recommended to install a good smoke exhaust and dust removal system around the equipment and clean the sensor and optical components regularly. At the same time, maintaining a constant temperature and humidity working environment can reduce the impact of thermal expansion and contraction on the laser path and focus accuracy.
Operator training and skills: Although autofocus technology reduces manual intervention, operators still need to have certain technical knowledge to quickly adjust and optimize focus parameters when abnormalities occur. Unskilled operation may lead to incorrect focus settings, which will affect the cutting effect. Therefore, companies should conduct systematic training for operators to enable them to master the working principle of the autofocus system, the identification and troubleshooting of common faults, and how to adjust the appropriate focus mode according to different materials. In addition, combined with the intelligent monitoring system, operators can optimize cutting strategies through data feedback and improve overall production efficiency.
Through regular calibration and maintenance, optimizing the working environment, and improving the skills of operators, the challenges of autofocus technology in practical applications can be effectively solved, ensuring that the fiber laser cutting machine always maintains high-precision and high-stability processing capabilities.
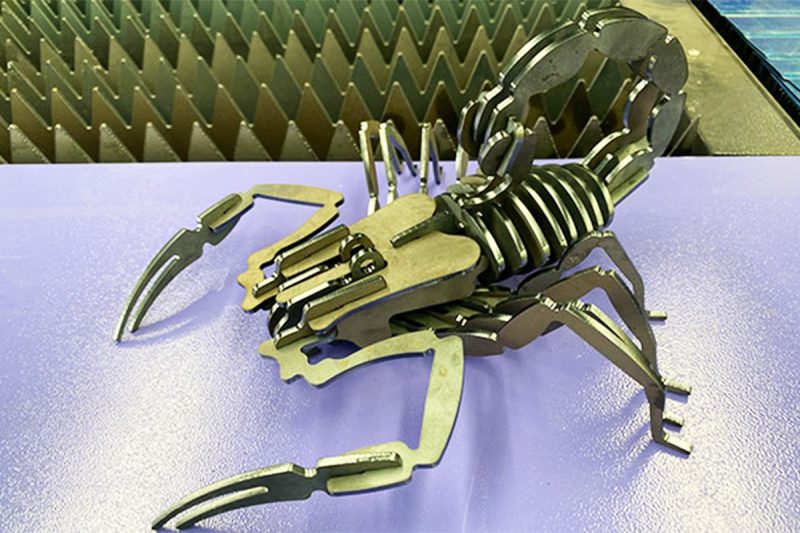
Summarize
The application of autofocus technology in fiber laser cutting machines has greatly improved cutting accuracy and production efficiency. Different types of autofocus systems have their advantages. Through reasonable selection and optimization, they can effectively improve cutting consistency, reduce manual adjustment time, and enhance the adaptability to different materials and thicknesses, ensuring higher-quality processing results. The application of this technology makes laser cutting more intelligent, reduces human errors, and improves production stability and accuracy.
However, the autofocus system still faces certain challenges in actual use, such as calibration maintenance, environmental impact, and operating skill requirements. The accuracy of the sensor, external environmental factors, and the operator’s technical level will affect the stability of the system and the cutting effect. Therefore, companies need to formulate reasonable equipment maintenance plans, optimize the working environment, and strengthen operator training to ensure the best performance of the autofocus system, thereby further improving the overall processing quality and production competitiveness.
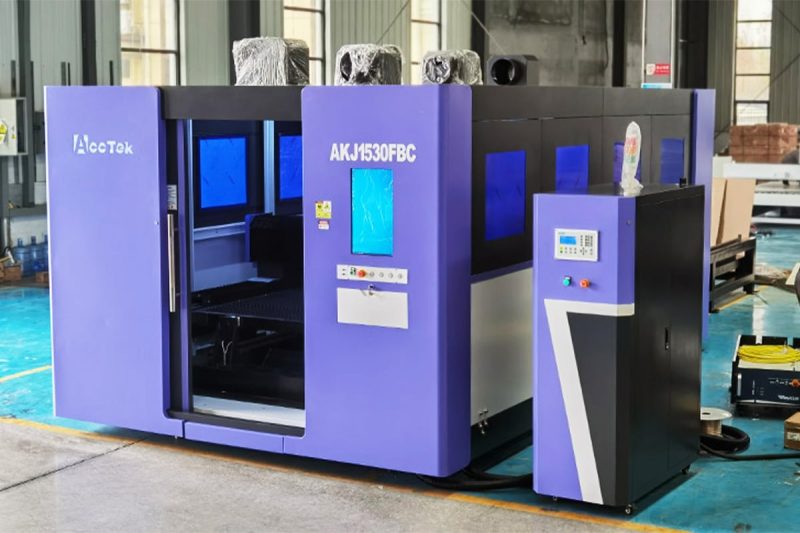
Get Laser Solutions
AccTek Laser is committed to providing advanced fiber laser cutting solutions to users around the world. Our autofocus technology can achieve real-time precise adjustment to ensure that the laser focus is always in the best position, thereby greatly improving cutting accuracy and processing quality. Whether processing metal materials of different thicknesses or coping with complex cutting requirements, our intelligent autofocus system can help users optimize production processes, improve efficiency, and reduce human errors.
Our laser-cutting equipment is widely used in sheet metal processing, automobile manufacturing, aerospace, electronic equipment, and other industries. With its excellent stability and efficient performance, it has won the trust of customers around the world. If you want to learn more about the application of autofocus technology and high-precision laser cutting or find a laser-cutting solution that suits your production needs, please feel free to contact us! Our professional team will provide you with detailed consultation and technical support to help your business move to a higher level.
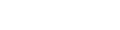
Contact information
- [email protected]
- [email protected]
- +86-19963414011
- No. 3 Zone A, Lunzhen Industrial Zone,Yucheng City , Shandong Province.
Get Laser Solutions