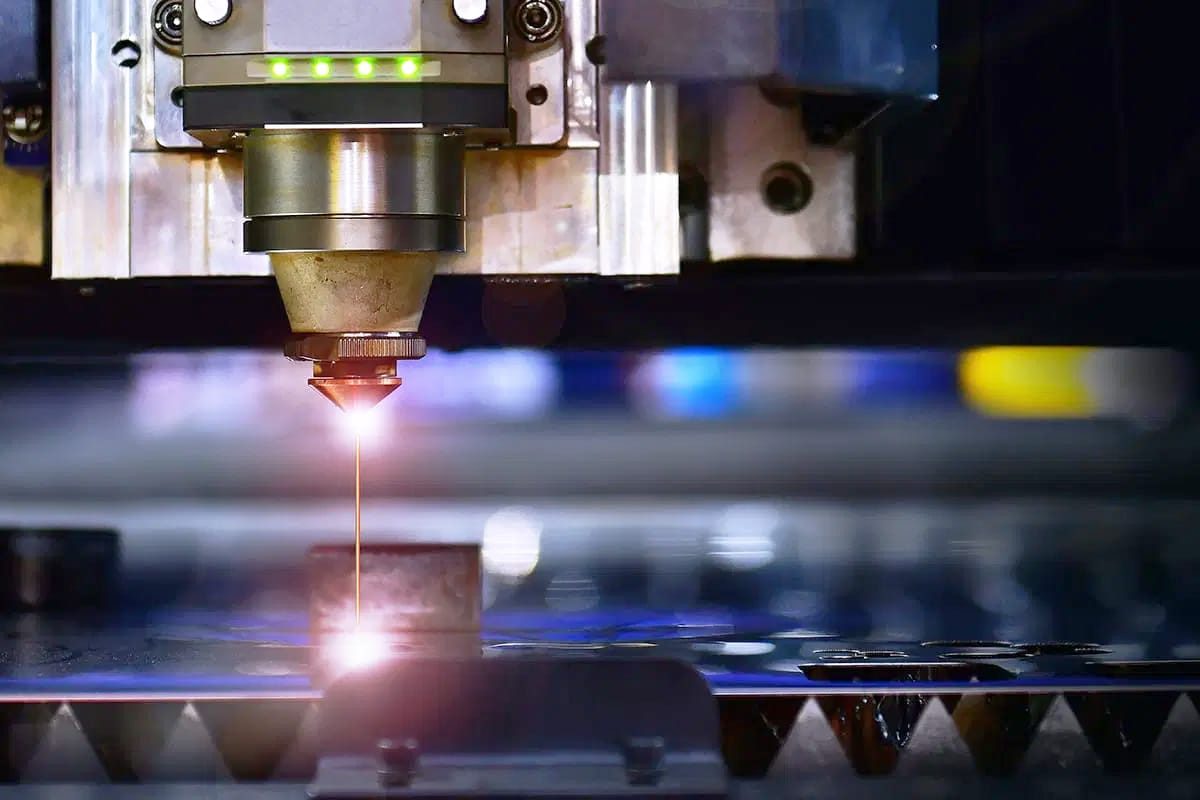
The Influence of Fiber Laser Beam Quality on Cutting Accuracy and Quality
In the field of laser cutting, fiber laser generators are widely used in industrial production such as metal cutting and engraving due to their high efficiency and precise focusing ability. Fiber laser generators can provide concentrated energy in a small cutting area, thereby completing cutting efficiently. However, the laser cutting effect not only depends on the laser power but also the quality of the fiber laser beam is also crucial.
The quality of fiber laser beam directly affects the precision and effect of cutting. High-quality beams can ensure stable focus and uniform energy distribution, thus improving cutting accuracy and surface quality. On the contrary, poor beam quality may lead to inaccurate focus, uneven cutting, and even rough cuts. Therefore, optimizing beam quality is critical to improving cutting performance and production efficiency.
Table of Contents
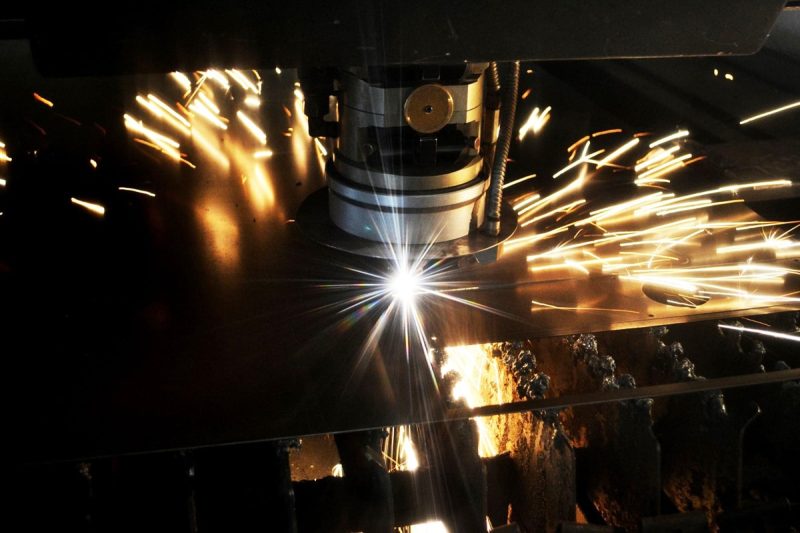
Understanding Fiber Laser Beam Quality
Definition of Beam Quality
Fiber laser beam quality refers to the distribution of the laser beam in space, mainly including its uniformity, directionality, and energy concentration. An ideal fiber laser beam quality should have several characteristics: a small divergence angle, a stable mode structure, and a uniform spatial profile. A small divergence angle means that the laser beam can remain focused during propagation, while a stable mode structure ensures efficient transmission of laser energy and reduces energy dispersion. A uniform spatial profile ensures that the laser beam can provide a balanced heating distribution during the cutting process, avoiding local overheating or uneven cutting. Beam quality is usually measured by the “beam quality factor” (M2 value). The closer the M2 value is to 1, the higher the quality of the laser beam, because an ideal high-quality laser beam has an M2 value close to 1, while a higher M2 value means poor beam quality.
The Importance of Beam Quality in Laser Cutting
In the laser cutting process, the quality of the fiber laser beam directly affects several key parameters in the cutting process, especially the focus accuracy, the incision width, and the edge finish. The higher the beam quality, the more precise the focus, which can achieve more detailed and precise cutting. A high-quality beam can ensure uniform energy distribution in the cutting area, reduce energy loss outside the focus, and avoid excessive heat diffusion so that a narrow incision and a smooth cutting edge can be obtained. In addition, the stability of the high-quality beam also reduces the expansion of the heat-affected zone (HAZ), which helps to improve the surface finish and product quality of the cut. On the contrary, when the beam quality is poor, due to the unfocused focus and uneven energy distribution, it may lead to an unstable cutting effect, rough edges, and even affect the physical properties of the material, increasing the risk of thermal deformation, and thus lead to reduced production efficiency, increased material waste, and even affect the quality of the final product.
Therefore, understanding and optimizing the quality of fiber laser beams will not only help improve cutting accuracy and efficiency, but also help reduce defective products in the production process, improve the quality of the final product, and thus enhance the competitiveness of enterprises in the laser cutting industry.
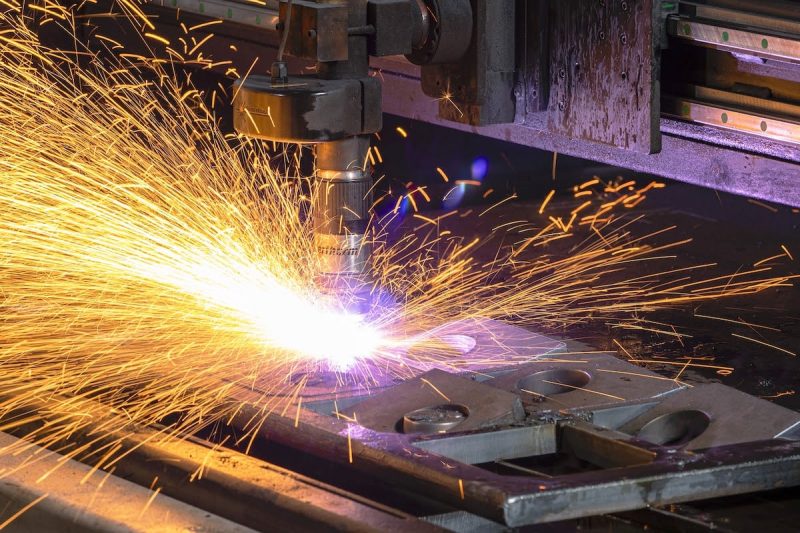
Factors Affecting Fiber Laser Beam Quality
Beam Divergence
The beam divergence angle refers to the degree to which the laser beam gradually expands during propagation, usually expressed as an angle. The divergence angle of the laser beam directly affects its focusing performance and cutting quality. A smaller divergence angle means that the beam can maintain a smaller focal diameter at a longer distance, thereby achieving more precise focusing and higher cutting accuracy during the cutting process. This is particularly important for fine cutting, especially in high-precision processing, to ensure that the laser beam is focused on the cutting point, avoid excessive or scattered focus, and ensure that the material is evenly heated and cut. Conversely, a beam with a divergence angle that is too large will result in a lack of focus, which in turn affects the cutting quality. The incision may be too wide, the edge is rough, the energy distribution during the cutting process is uneven, and it may even cause local overheating, which affects the physical properties of the material and the cutting effect.
Pattern Structure
The mode structure of a laser beam refers to the way the energy of the beam is distributed. Common modes include Gaussian mode and non-Gaussian mode. The energy of a Gaussian mode laser beam is mainly concentrated in the center and has excellent focusing ability, which can ensure that the laser beam has a smaller focal diameter after focusing, making the cutting more precise. This mode of the laser beam can provide a stable and consistent energy distribution, which helps to improve the stability and accuracy of cutting. In contrast, the energy distribution of a non-Gaussian mode laser beam is more dispersed and the focus is not concentrated, so it is difficult to maintain high precision during cutting, which may lead to unstable cutting effects, poor incision quality, and even uneven heating effects, affecting the overall cutting quality.
Space Outline
The spatial profile of a fiber laser beam refers to the shape of the beam and the spatial structure of its energy distribution. A uniform spatial profile means that the energy of the laser beam is evenly distributed throughout the cutting area, which is critical to achieving high-quality cutting. Uniform energy distribution ensures that the laser beam applies uniform heat to the material during the cutting process, thereby avoiding local overheating or energy concentration in a certain part that causes uneven cutting effects. If the spatial profile of the beam is uneven, it may cause excessive concentration of energy in certain areas, resulting in local overheating, and even scorching, melting, or slag, all of which will affect the cutting quality and may increase the workload of subsequent processing. Therefore, keeping the spatial profile of the beam uniform helps improve cutting quality and reduce problems and defective product rates in cutting.
Mode Stability
The mode stability of the laser beam refers to whether the mode of the beam can remain consistent during the cutting process. Changes in the laser beam mode will directly affect the accuracy and efficiency of laser cutting. Ideally, the laser beam should maintain a stable mode to ensure the consistency of the energy and focus of the beam during the cutting process. If the mode of the laser beam changes, it may cause the focus position to shift, so that the focus during the cutting process is no longer concentrated, which in turn leads to a decrease in cutting accuracy. In addition, the instability of the mode may also lead to a decrease in cutting efficiency, because the laser beam may lose energy in an unstable state and cannot be effectively focused, thus affecting the cutting speed and quality. Therefore, maintaining the stability of the laser beam mode is a key factor in ensuring the accuracy, efficiency, and stability of laser cutting.
The quality of fiber laser beams is affected by many factors, including divergence angle, mode structure, spatial profile, and mode stability. These factors jointly determine the focusing performance, energy distribution, and cutting effect of the laser beam during the cutting process. Therefore, optimizing the quality of fiber laser beam, especially by reducing the divergence angle, selecting the appropriate mode structure, maintaining a uniform spatial profile, and ensuring mode stability, can effectively improve the accuracy, quality, and efficiency of laser cutting.
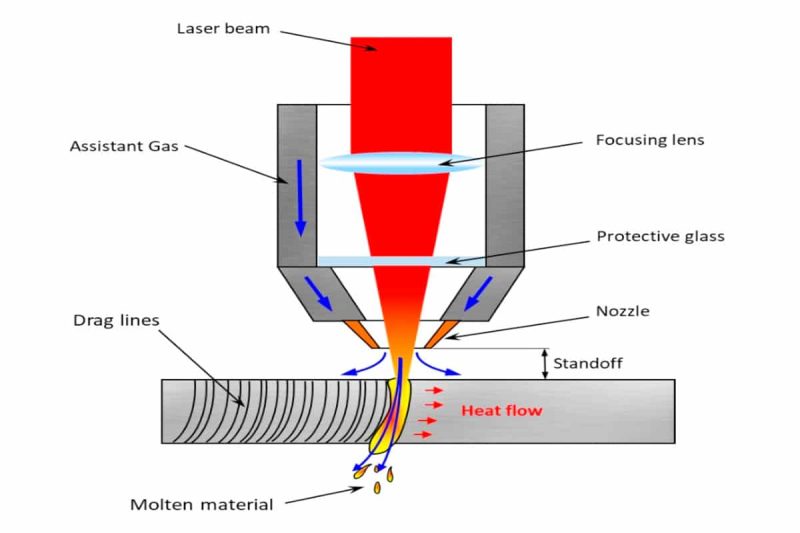
The Influence of Fiber Laser Beam Quality on Cutting Quality
The quality of fiber laser beam plays a vital role in laser cutting and directly affects many aspects of the cutting effect. The quality of cutting not only determines the efficiency of production but also affects the appearance and performance of the final product. The following are several key factors affecting the cutting quality of fiber laser beams:
Kerf Width and Edge Roughness
The incision width and edge roughness are important indicators of laser cutting quality. When the quality of the fiber laser beam is high, the focus can be more concentrated and the energy is evenly distributed in the cutting area, thus achieving finer cutting. A high-quality laser beam can ensure a narrower incision and smoother edges, reducing the workload of post-processing and improving the appearance quality of the product. On the contrary, when the beam quality is poor, due to the unfocused focus, the laser beam may scatter energy during the cutting process, resulting in an increase in the incision width, rough edges, and even scorching or irregular cutting, which affects the overall quality of the product and increases the difficulty and cost of post-processing.
Heat Affected Zone (HAZ)
The heat-affected zone (HAZ) refers to the area where the material undergoes physical or chemical changes due to high temperature during the laser cutting. When the beam quality is high, the laser can release energy in a concentrated area of the focus, reduce heat diffusion outside the focus, and make the heat-affected zone relatively small. This can effectively control the material’s thermal deformation and microstructural changes during the cutting process, thereby ensuring the accuracy and quality of the cutting area. When the beam quality is poor, the focusing ability of the laser beam decreases. The heat energy spreads more widely in the material, causing the heat-affected zone to expand, which may cause overheating, melting, or even deformation of the material, which not only affects the cutting quality but may also damage the physical properties of the material and affect subsequent processing or use.
Cutting Speed and Efficiency
Cutting speed and efficiency are one of the important indicators to measure the performance of laser cutting. A laser generator with good beam quality can provide high-density laser energy so that it can maintain a high power output during the cutting process while avoiding excessive heat accumulation. This high-density energy can effectively cut materials at a higher cutting speed, thereby improving production efficiency. High-quality beams can also effectively improve the accuracy of cutting so that the cutting speed and quality can be improved simultaneously. When the beam quality is poor, due to the problem of unfocused focus, the energy of the laser beam is unevenly distributed on the material, and excessive heat accumulates during the cutting process, resulting in the inability to increase the cutting speed. The speed can only be reduced to avoid uneven cutting, thereby reducing the overall cutting efficiency.
Surface Finish
The surface finish after cutting is one of the important criteria for evaluating cutting quality. Higher beam quality can ensure that the energy of the beam is evenly distributed during the cutting process, making the cut surface smoother and reducing surface defects, cracks, or burnt phenomena. This can not only improve the appearance quality of the product but also reduce the subsequent post-processing processes, such as slag removal, grinding, and polishing. On the other hand, low beam quality may result in a rough cut surface, or even material burnt, slag accumulation, etc., which increases the difficulty and cost of post-processing, and in severe cases, affects the performance and market competitiveness of the final product.
Material Compatibility
Different types of materials have different requirements for laser cutting, and the quality of the fiber laser beam directly affects its adaptability to various materials. Laser generators with high beam quality are usually able to efficiently cut on a wider range of materials, especially for metal materials with higher hardness, such as stainless steel, aluminum alloy, etc. By optimizing the beam quality, higher precision, and better cutting effects can be ensured in the cutting process of these high-demand materials. For some soft materials, such as plastic or wood, the requirements for beam quality are relatively low, but even so, the improvement of beam quality still helps to expand the material compatibility of the equipment, enabling it to handle a wider variety of materials and improve the diversity and flexibility of processing.
The quality of fiber laser beam has a profound impact on many aspects of the laser cutting process, including kerf width, edge roughness, heat-affected zone, cutting speed and efficiency, surface finish, and material compatibility. Improving the quality of laser beams can not only improve cutting accuracy and reduce heat-affected zone but also optimize cutting speed and surface quality, thereby improving production efficiency and reducing the cost of post-processing. Optimizing beam quality is a key factor in improving laser cutting performance, and is of great significance to improving the quality of final products and corporate competitiveness.
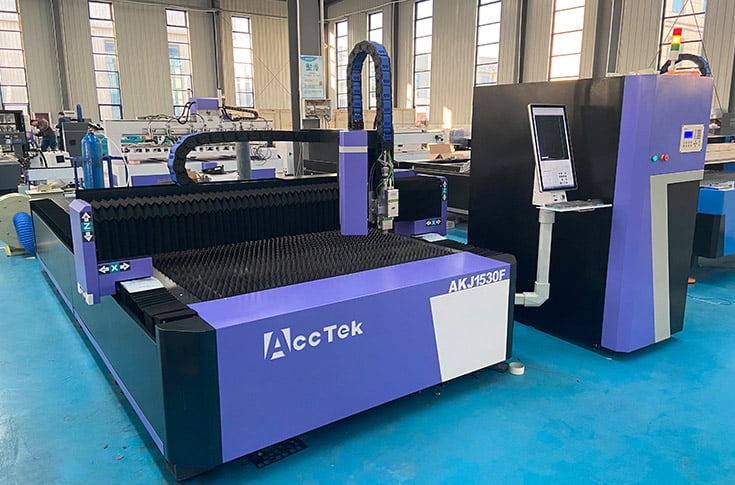
Summarize
The quality of fiber laser beam has a significant impact on cutting accuracy and quality. A high-quality beam can ensure focused focus, high cutting accuracy, smooth cut edges, reduced heat-affected zone, and improved cutting efficiency. Poor beam quality may lead to inaccurate cutting, enlarged heat-affected zone, and reduced cutting speed. By optimizing the optical design, selecting the appropriate laser light source, and regularly calibrating the beam transmission system, the beam quality of fiber laser can be effectively improved, thereby improving the overall performance of laser cutting.
For enterprises, understanding the impact of beam quality on the cutting process and taking corresponding optimization measures will directly improve product quality and production efficiency, reduce waste, and help companies stand out from the competition. I hope this article can help you understand laser cutting technology and help you achieve greater success in the laser industry. If you have any questions about laser cutting equipment or other laser-related technologies, please feel free to contact AccTek Laser. We are committed to providing customers with the most advanced laser solutions.
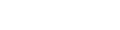
Contact information
- [email protected]
- [email protected]
- +86-19963414011
- No. 3 Zone A, Lunzhen Industrial Zone,Yucheng City , Shandong Province.
Get Laser Solutions