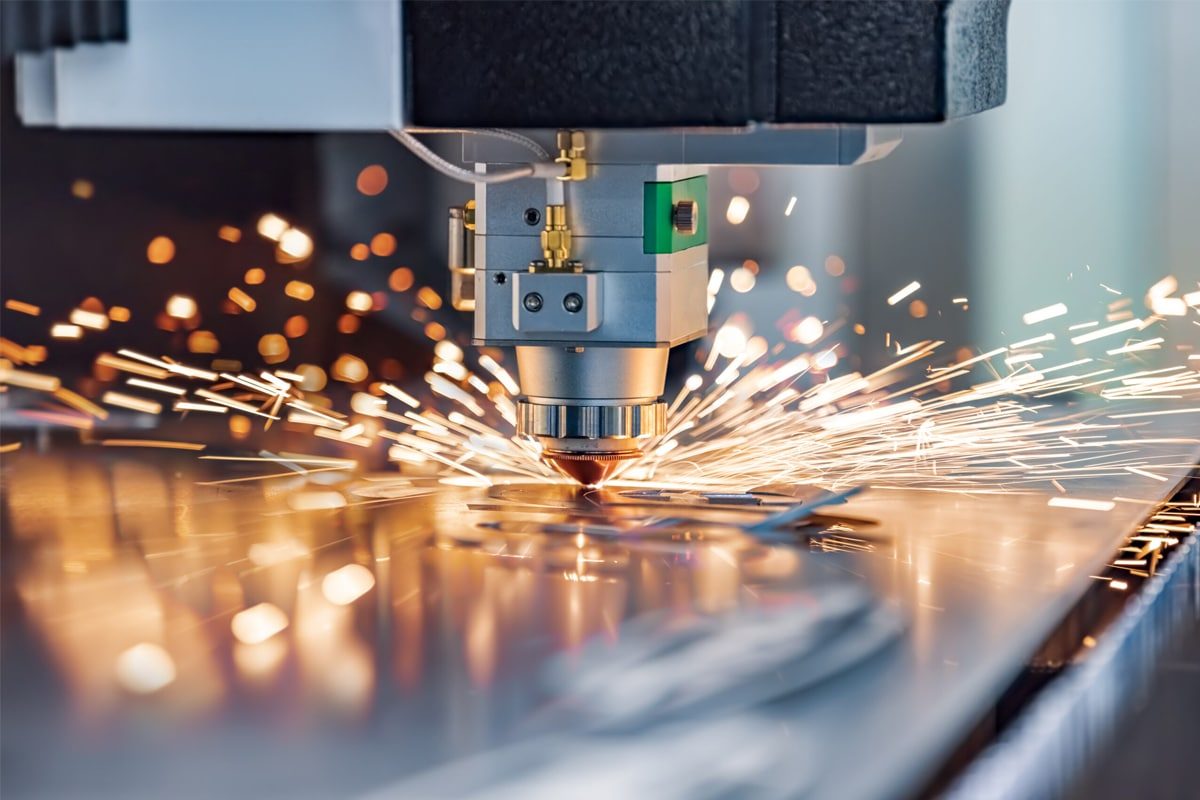
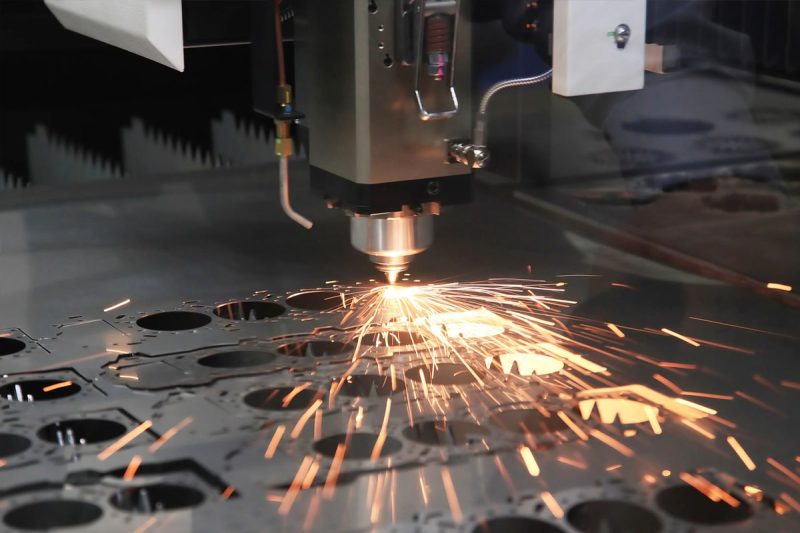
Understanding Fiber Laser Cutting
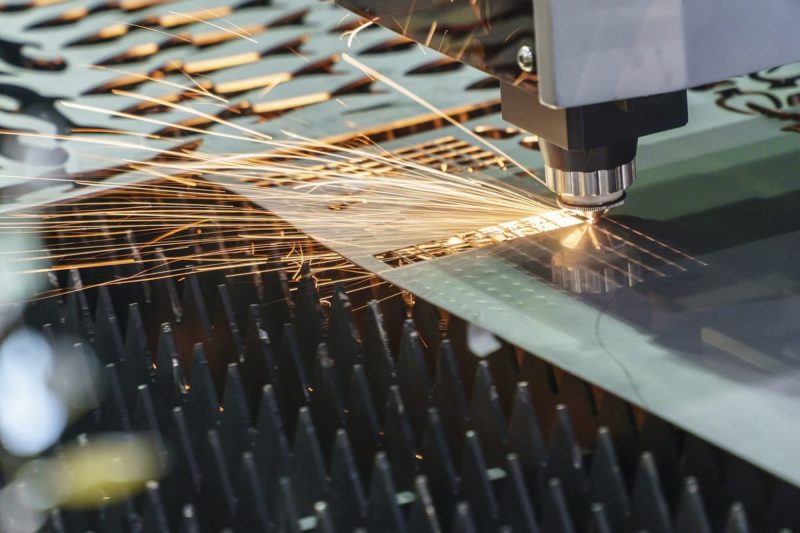
Advantages of Fiber Laser Cutting
High Precision and Accuracy
Speed and Efficiency
Energy Efficiency
Low Maintenance
Versatility
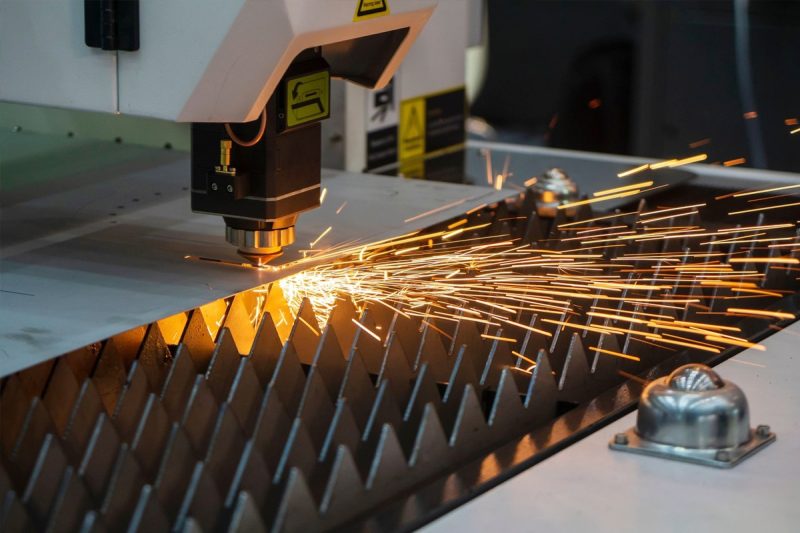
Metals Suitable for Fiber Laser Cutting
Carbon Steel
Carbon steel is one of the most commonly used metals in fiber laser cutting due to its strength, durability, and versatility. It is widely applied in industries requiring robust materials that can withstand high stress and wear, such as automotive and construction.
- Thickness Range: Fiber lasers can cut carbon steel from very thin sheets (0.5 mm) up to thick plates (25 mm or more) based on laser power.
- Cut Quality: Fiber lasers produce smooth, burr-free edges on carbon steel, reducing the need for additional finishing, which makes production more efficient.
- Applications: Carbon steel is essential in the manufacturing of vehicle parts, structural beams, machinery components, and industrial equipment where high tensile strength is critical.
- Advantages: The fiber laser’s precision and minimal heat-affected zone ensure that cuts retain their strength and quality, even on thicker plates. High cutting speeds also make it a cost-effective choice for high-volume applications.
Stainless Steel
Stainless steel’s corrosion resistance and polished finish make it a top choice for industries where durability and appearance are important, including the food and beverage, medical, and architectural sectors.
- Thickness Range: Fiber lasers effectively cut stainless steel from thin foils (0.5 mm) up to thicker plates (up to 20 mm or more).
- Cut Quality: Fiber lasers deliver clean, polished edges on stainless steel, maintaining its aesthetic appeal and integrity. The reduced heat-affected zone helps prevent oxidation along cut edges, which is essential for applications that require a smooth, high-quality finish.
- Applications: Stainless steel is widely used in sanitary equipment, medical instruments, kitchenware, architectural fixtures, and decorative elements.
- Advantages: Stainless steel’s reflective nature is well-suited to fiber lasers, which minimize reflections and enable precise cuts. With no need for post-processing, manufacturers can streamline production, saving both time and resources.
Aluminum and Aluminum Alloys
Aluminum’s lightweight properties combined with its strength make it indispensable in industries such as aerospace and automotive, where performance and fuel efficiency are top priorities.
- Thickness Range: Fiber lasers can cut aluminum up to 15 mm thick, although higher-power lasers are required for thicker cuts.
- Challenges: Aluminum’s high reflectivity and thermal conductivity pose challenges, as it reflects the laser beam and dissipates heat quickly. However, advanced fiber laser technology can overcome these issues with anti-reflective coatings and optimized cutting parameters.
- Applications: Aluminum is used in aerospace components, automotive body panels, electronic enclosures, and decorative applications.
- Advantages: Fiber lasers allow for precise and detailed cuts on aluminum without causing warping or heat distortion. They also provide a solution for creating intricate designs, essential for lightweight and complex aerospace and automotive components.
Copper and Brass
Copper and brass are prized for their conductivity and appearance, making them ideal for applications in the electrical and decorative sectors. However, these metals are highly reflective and conductive, requiring special handling.
- Thickness Range: Fiber lasers can cut copper and brass up to 10 mm thick, depending on laser power and machine configuration.
- Challenges: Copper and brass reflect laser light, which can damage laser components if not properly managed. Additionally, their high thermal conductivity requires high-power lasers and precise control over parameters.
- Applications: Copper and brass are commonly used in electrical connectors, busbars, plumbing fixtures, and ornamental designs.
- Advantages: Fiber lasers equipped with anti-reflective technology can handle copper and brass effectively. The high accuracy and smooth cuts produced by fiber lasers make them particularly useful for creating precise electrical components and intricate decorative items.
Titanium and Titanium Alloys
Titanium is known for its impressive strength-to-weight ratio and corrosion resistance, qualities that make it highly valued in industries such as aerospace, medical, and sports equipment manufacturing.
- Thickness Range: Fiber lasers can cut titanium and its alloys up to 10 mm thick, though powerful lasers are needed for thicker materials.
- Cut Quality: Fiber lasers produce clean cuts with minimal dross, preserving titanium’s high-quality surface finish. The low heat input ensures that the metal’s structural integrity and properties are not compromised.
- Applications: Titanium is widely used in aerospace components, medical implants, prosthetics, and high-performance sports gear.
- Advantages: Fiber lasers allow manufacturers to cut titanium without causing thermal distortion, ensuring that the metal retains its desirable properties. This makes it an excellent choice for high-stress applications where both durability and weight are critical.
Nickel Alloys (Inconel, Monel)
Nickel-based alloys like Inconel and Monel are used in demanding environments where extreme heat and corrosion resistance are required. These alloys are commonly used in the aerospace, marine, and chemical processing industries.
- Thickness Range: Fiber lasers can cut nickel alloys up to 10 mm thick, although their toughness requires precise laser control.
- Cut Quality: Fiber lasers provide high-precision cuts, essential for components that must perform under high-stress conditions. Nickel alloys’ durability and high melting point are well-matched to fiber laser cutting.
- Applications: Nickel alloys are used in turbine blades, exhaust systems, chemical processing equipment, and marine components.
- Advantages: Fiber lasers enable the efficient processing of these tough alloys, reducing material waste and ensuring clean, accurate cuts that retain the metal’s strength and corrosion resistance.
Galvanized Steel
Galvanized steel has a protective zinc coating, making it resistant to corrosion and well-suited for outdoor and structural applications. However, this coating requires specific considerations during cutting.
- Challenges: The zinc layer can vaporize during laser cutting, creating fumes that may affect cut quality and require appropriate ventilation.
- Applications: Galvanized steel is widely used in HVAC systems, roofing, automotive parts, and construction frameworks.
- Advantages: With proper parameter adjustments and ventilation, fiber lasers can handle galvanized steel effectively, producing cuts that maintain the material’s protective qualities without additional post-processing.
Tool Steel
Tool steel is highly durable and can withstand wear, making it essential in industries that require long-lasting molds, dies, and cutting tools.
- Cut Quality: Fiber lasers deliver clean, precise cuts on tool steel, often eliminating the need for additional machining or finishing.
- Applications: Tool steel is used to create machine parts, dies, molds, and various tools in manufacturing and machining industries.
- Advantages: The accuracy of fiber lasers ensures that tool steel components meet exact specifications, allowing manufacturers to produce high-quality tools and machine parts with minimal waste.
Silver and Gold
Silver and gold are precious metals often used in electronics and jewelry, where fine detail and high-quality finishes are essential. These materials require special handling due to their high reflectivity and value.
- Challenges: Silver and gold are reflective, which can reduce laser efficiency and increase the need for precise parameter control to avoid waste.
- Applications: Silver and gold are used in electronics, intricate jewelry, and custom decorative items.
- Advantages: Fiber lasers allow for detailed cutting of these precious metals, making them suitable for high-precision applications in both jewelry making and electronics manufacturing.
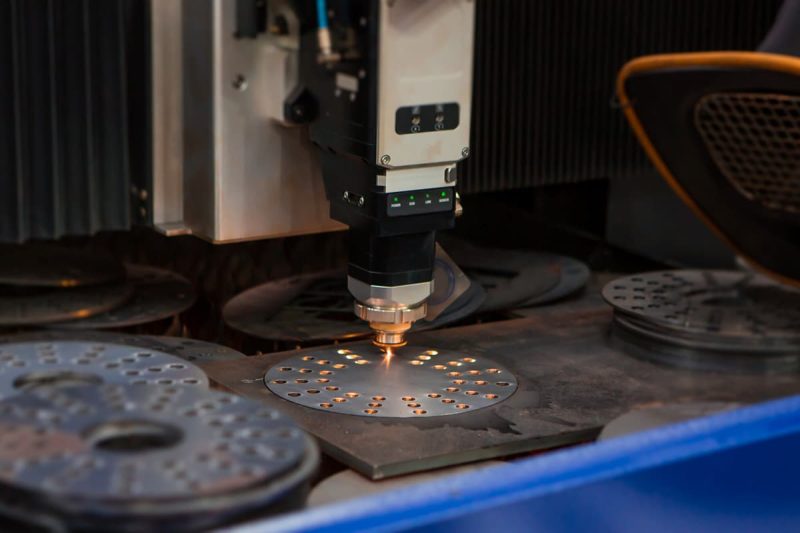
Factors Influencing Cutting Capability
Laser Power
The laser power directly influences a machine’s ability to cut different types of materials and thicknesses. Higher laser power generally allows for faster cuts and the ability to process thicker materials.
- Low Power (1,500W – 3,000W): Suitable for thin materials (up to 15 mm), ideal for precision cutting of intricate designs and fine details.
- Medium Power (3,000W – 6,000W): Handles medium-thickness metals (up to 25 mm) and provides balanced speed and quality for general fabrication.
- High Power (12,000W and Above): Suitable for thicker materials (over 50 mm), including heavy industrial applications and large structural components.
Material Thickness
Material thickness is one of the most influential factors in determining the effectiveness and quality of a fiber laser cut. The thicker the material, the more energy is required to penetrate and cut through it effectively.
- Thin Materials (Below 10 mm): Fiber lasers excel in cutting thin sheets with high precision and minimal heat distortion, making them ideal for applications requiring fine details.
- Medium Thickness (12 mm – 25 mm): Moderate laser power and optimized settings are often necessary to balance speed and cut quality for thicker materials.
- Thick Materials (Above 25 mm): Cutting thick metals requires higher power and slower cutting speeds to ensure a complete cut with smooth edges. Increased focus on dross removal and edge finishing may also be necessary.
Material Reflectivity
The reflectivity of a metal plays a significant role in its compatibility with fiber laser cutting. Highly reflective metals, such as aluminum, copper, brass, silver, and gold, can pose challenges by reflecting the laser beam into the machine, potentially causing damage to the laser source or optics.
- High-Reflectivity Metals: Materials like copper and brass require specialized laser settings or anti-reflective technologies to avoid damaging the laser system. Higher laser power and precise adjustments can improve cutting efficiency and minimize reflection issues.
- Non-Reflective Metals: Carbon steel and stainless steel are less reflective and absorb fiber laser wavelengths more effectively, making them easier to cut with standard settings.
Assist Gases
The choice of assist gas and its pressure play crucial roles in the cutting quality and speed of fiber lasers. Assist gases are used to remove molten material from the cut path, protect the optics, and in some cases, enhance the cutting reaction.
- Oxygen (O2): Oxygen is often used for cutting carbon steel, as it produces an exothermic reaction that increases cutting speed. However, it may cause oxidized edges, which could require additional finishing.
- Nitrogen (N2): Nitrogen is an inert gas that prevents oxidation and is commonly used for cutting stainless steel, aluminum, and other high-quality applications where clean edges are essential. It provides high-quality cuts but may reduce cutting speed compared to oxygen.
- Air: Air can be a cost-effective option for cutting thin materials where edge quality is less critical, though it can result in oxidized edges.
Beam Quality
The quality of the laser beam, often measured by its M2 value, significantly affects the precision, efficiency, and smoothness of the cut. A lower M2 value indicates a higher quality beam, which can focus on a smaller spot size and deliver greater power density to the material.
- M2 Value: A high-quality beam (low M2 value) enables smaller, finer cuts with greater accuracy, making it ideal for intricate designs and tight tolerances.
- Focus Control: Dynamic focusing systems allow adjustments to maintain optimal focal distance throughout the cutting process, especially important for thicker materials and complex shapes.
- Auto-Focus Systems: These systems enhance efficiency by automatically adjusting the focus position, reducing setup time, and enabling quicker transitions between different materials and thicknesses.
Cutting Speed
Cutting speed directly impacts the quality, efficiency, and finish of a fiber laser cut. The ideal cutting speed depends on a balance of factors, including material type, thickness, and desired edge quality.
- High Speed: Cutting too quickly may result in incomplete cuts, rough edges, and decreased cut quality, especially on thicker materials.
- Low Speed: Cutting too slowly increases heat input, which can lead to warping or a wider kerf, especially on thin materials.
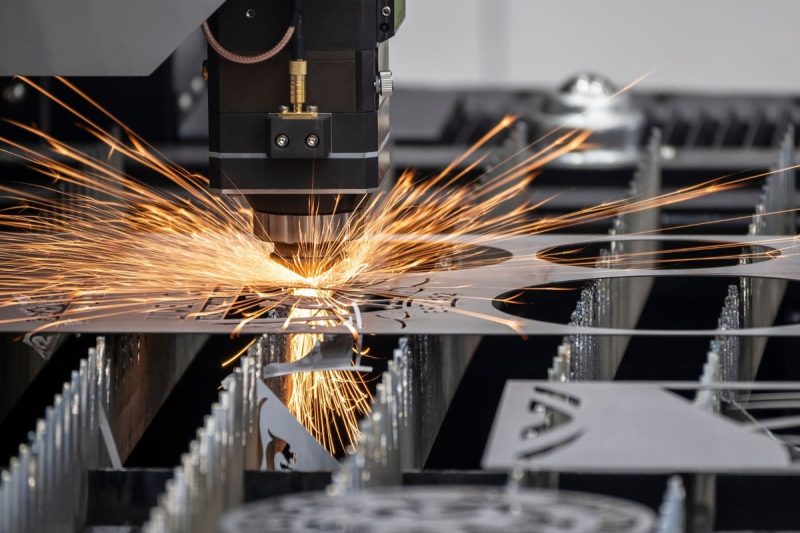
Applications Across Industries
Automotive Industry
Applications
- Body Panels: Precision cutting for external and internal vehicle panels ensures uniformity and clean edges for a smooth fit.
- Chassis Components: Structural parts such as frames and brackets require durable cuts that fiber lasers achieve with minimal material waste.
- Exhaust Systems: The ability to cut stainless steel and titanium enables fiber lasers to produce exhaust components with precision, reducing the need for finishing.
Advantages
- High Throughput: Fiber lasers enhance productivity by reducing cutting time and enabling large-scale production.
- Design Flexibility: Automakers can achieve complex designs and lightweight structures, essential for fuel efficiency.
Aerospace Industry
Applications
- Aircraft Structures: Cutting aluminum, titanium, and high-strength alloys for structural parts ensures durability and precision.
- Engine Components: Fiber lasers can handle the intricate shapes and strict tolerances required for turbine blades and exhaust systems.
- Spacecraft Parts: For satellites and rockets, the ability to cut lightweight metals like aluminum with minimal thermal impact is essential.
Advantages
- Precision and Consistency: Fiber lasers provide the exacting standards necessary for components that face extreme conditions.
- Material Efficiency: Reduced waste of expensive alloys, essential for high-value aerospace components.
Medical Industry
Applications
- Surgical Instruments: The manufacturing of scalpel blades, forceps, and other tools requires exact cuts and polished edges.
- Medical Implants: Fiber lasers enable precision cuts on titanium for implants such as bone plates and joint replacements.
- Equipment Components: Parts for medical devices, such as MRI machines and patient monitors, require high accuracy and reliable performance.
Advantages
- Biocompatibility: The clean, oxidation-free cuts on stainless steel and titanium help maintain material properties essential for medical use.
- Customization: The ability to produce patient-specific implants with exact specifications.
Electronics Industry
Applications
- Circuit Boards: Cutting metal substrates, including copper and aluminum, for printed circuit boards with high accuracy.
- Enclosures and Casings: Fabricating metal casings for devices like smartphones, laptops, and industrial equipment.
- Heat Sinks: Precision cutting of aluminum and copper materials for components that manage heat dissipation.
Advantages
- High Precision: Essential for creating small, detailed components required in compact electronic devices.
- Increased Productivity: Rapid cutting speeds enable high-volume production to meet the fast-paced demands of the electronics market.
Construction and Architecture
Applications
- Structural Components: Cutting beams, columns, and brackets for steel frameworks in buildings and bridges.
- Decorative Elements: Custom-designed facades, railings, and metal fixtures can be created with intricate patterns.
- HVAC Systems: Manufacturing of metal ductwork and components for heating, ventilation, and air conditioning systems.
Advantages
- Customization and Flexibility: Enables architects and designers to incorporate unique, detailed metalwork into buildings.
- Durability: Fiber laser cutting produces clean, strong edges that withstand structural demands over time.
Renewable Energy
Applications
- Solar Panel Frames: Cutting aluminum frames and mounting systems that provide durability and stability for solar installations.
- Wind Turbine Components: Fabricating parts such as structural supports and turbine blades.
- Battery Enclosures: Production of casings and enclosures for batteries used in electric vehicles and energy storage.
Advantages
- Precision and Strength: Essential for components exposed to outdoor environments and fluctuating temperatures.
- Efficiency: The ability to handle high volumes and complex geometries, making it ideal for renewable energy equipment manufacturing.
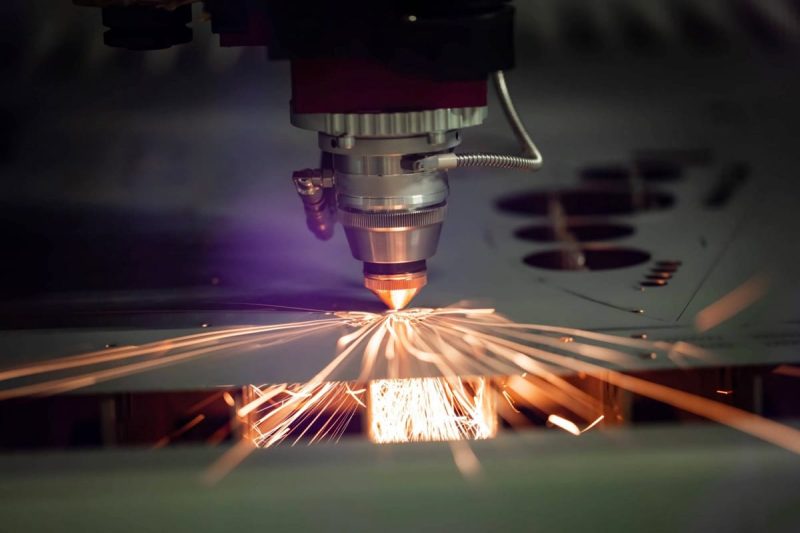
Limitations of Fiber Laser Cutting
Metal Reflectivity
Highly reflective metals, such as aluminum, copper, brass, silver, and gold, can pose challenges in fiber laser cutting. These metals tend to reflect the laser beam into the cutting head, potentially damaging the laser source and optics. This reflection can also reduce cutting efficiency and lead to inconsistent cuts.
- Challenges: Reflective surfaces reduce the absorption of laser energy, which can interfere with cutting depth and quality. Reflection can also cause heat buildup in the machine, which may necessitate additional cooling or protective measures.
- Solutions: Advanced fiber laser systems may include anti-reflective technology and coatings on optics to handle reflective metals more effectively. Additionally, adjusting parameters such as laser power, focal length, and assist gas can improve cutting performance. However, cutting reflective metals still requires careful attention and more frequent maintenance to protect the laser system.
Thickness Limitations
Fiber lasers are highly efficient at cutting thin to medium-thickness metals, but there are practical limitations on the maximum thickness they can cut effectively.
- Thin to Medium Metals (0.5 mm to 25 mm): Fiber lasers excel in cutting thin and medium-thickness metals with high precision and speed.
- Thick Metals (Above 25 mm): While fiber lasers can cut thicker metals, their performance decreases as thickness increases. Cutting very thick materials (over 50 mm) requires higher laser power and slower cutting speeds, which can increase production time and operational costs. Additionally, thick cuts may produce more dross and require post-processing for a clean finish.
Initial Investment
Fiber laser cutting machines represent a significant capital investment. The cost of fiber lasers is generally higher than CO2 lasers and other traditional cutting equipment, primarily due to the advanced technology, high-power lasers, and specialized optics involved.
- Cost Factors: High-quality fiber laser cutting machines come with a substantial price tag, which includes the laser source, cutting head, CNC controls, cooling systems, and safety features. While operational costs are low due to energy efficiency and reduced maintenance needs, the initial investment can be a barrier for smaller businesses or those with limited budgets.
- Long-Term ROI: For high-production environments, the cost savings from energy efficiency, low maintenance, and faster processing speeds often justify the investment. However, for low-volume applications, the high upfront cost may make fiber laser cutting less attractive compared to other methods.
Safety Concerns
Fiber lasers emit a high-intensity laser beam at a wavelength that is highly concentrated and can pose safety risks if not properly managed. Additionally, the cutting process can produce fumes and particulates that require careful handling to protect operators and the environment.
- Laser Radiation: The powerful laser beam can cause serious injuries if it comes into direct contact with the skin or eyes. Fiber lasers require safety enclosures and interlock systems to prevent accidental exposure.
- Fume and Particulate Emissions: Cutting certain metals, particularly those with coatings like galvanized steel, can release hazardous fumes and particulates. Proper ventilation and fume extraction systems are essential to maintaining a safe working environment.
- Fire Risk: The high temperatures generated during cutting can ignite flammable materials, posing a fire hazard, especially in poorly ventilated or cluttered spaces. Safety protocols, including regular equipment maintenance and fire suppression systems, are necessary to mitigate these risks.
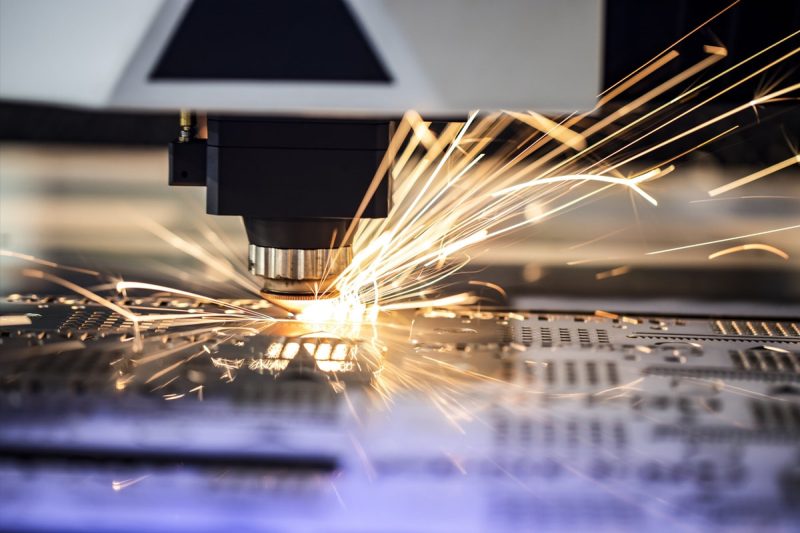
Safety Considerations
Protective Equipment
To protect operators from potential laser hazards, appropriate personal protective equipment (PPE) must be used whenever working near a fiber laser cutting machine.
- Laser Safety Glasses: Operators should wear laser safety glasses specifically rated for the wavelength of the fiber laser (typically around 1.064 micrometers). These glasses prevent eye damage from direct or reflected laser beams.
- Protective Clothing: Fire-resistant clothing and gloves protect operators from sparks, hot metal particles, and burns. This is particularly important when working with thicker or highly conductive metals that generate heat during cutting.
- Hearing Protection: Fiber laser cutting machines can produce noise levels that may require hearing protection, especially in high-power or high-production environments.
Machine Safety Features
Fiber laser cutting machines come equipped with several built-in safety features designed to prevent accidents and protect both operators and the equipment.
- Safety Enclosures: Enclosures shield operators from laser radiation, preventing accidental exposure to the laser beam. These protective barriers contain the laser’s light, ensuring it only impacts the designated cutting area.
- Interlock Systems: Interlock mechanisms automatically shut down the laser when the enclosure is opened or if an unauthorized access point is detected. This feature prevents accidental exposure to the laser beam and provides an extra layer of safety.
- Emergency Stop Buttons: Emergency stop buttons are strategically placed on the machine, allowing operators to halt the laser cutting process instantly in case of a malfunction or emergency.
- Sensors and Alarms: Advanced fiber laser machines are often equipped with sensors and alarms that detect overheating, excess reflectivity, or malfunctions in the system, alerting operators to potential issues before they escalate.
Environmental Controls
Fiber laser cutting can produce fumes, particulates, and even combustible dust, especially when cutting metals with coatings like galvanized steel. Proper environmental controls are essential to maintain air quality, prevent fire hazards, and ensure a safe workspace.
- Ventilation and Fume Extraction: Cutting certain metals can release toxic fumes and fine particulates. Fume extraction systems and adequate ventilation remove harmful substances from the workspace, protecting operators’ respiratory health and ensuring air quality.
- Dust Collection Systems: When cutting metals that generate combustible dust, a dust collection system is crucial to prevent accumulation and reduce the risk of fires or explosions. Regular cleaning and maintenance of these systems are also essential for continuous safe operation.
- Temperature and Humidity Control: Maintaining stable temperature and humidity levels helps prevent condensation, which could interfere with laser performance and increase the risk of electrical hazards.
Training and Procedures
Proper training and strict operational procedures are foundational to ensuring the safe and efficient use of fiber laser cutting machines. All operators should receive comprehensive training on machine handling, safety protocols, and emergency response.
- Operator Training: Every operator should be thoroughly trained in the operation of fiber laser cutting machines, including starting and stopping the machine, adjusting parameters, using assist gases, and handling material. Training should also cover the correct use of protective equipment and the importance of following safety protocols.
- Safety Protocols: Safety guidelines should be established and communicated to all personnel. These protocols include the proper startup and shutdown processes, maintenance schedules, and procedures for handling emergencies or equipment malfunctions.
- Emergency Procedures: Operators should be trained to respond to emergencies, such as laser malfunctions, fires, or fume buildup, and know how to safely evacuate the area if necessary. Regular safety drills and reviews of emergency protocols help reinforce these procedures.
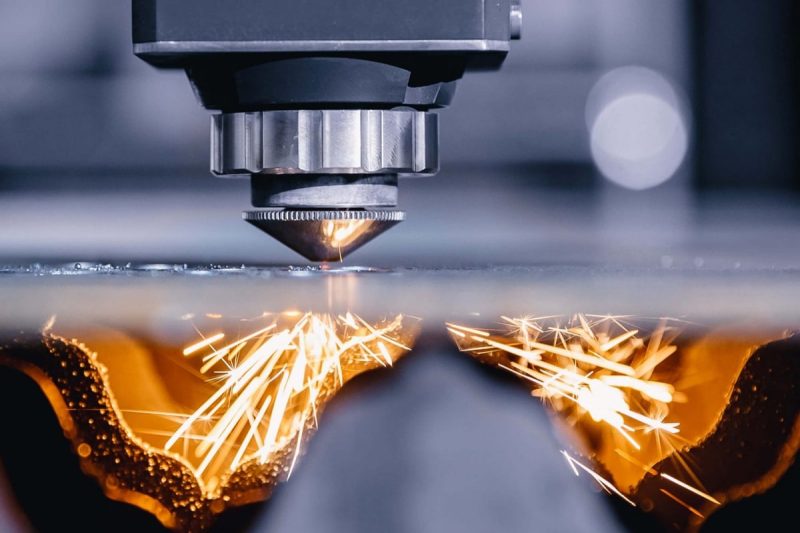
Summary
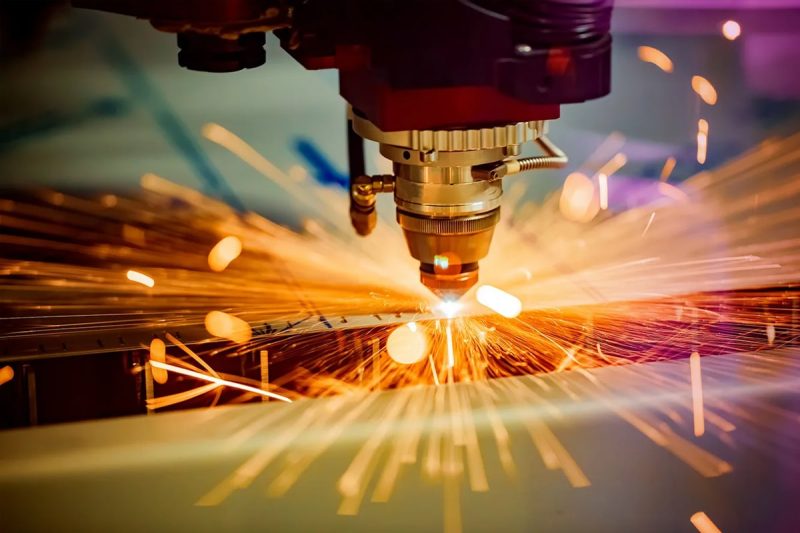
Get Laser Cutting Solutions
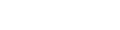
- [email protected]
- [email protected]
- +86-19963414011
- No. 3 Zone A, Lunzhen Industrial Zone,Yucheng City , Shandong Province.