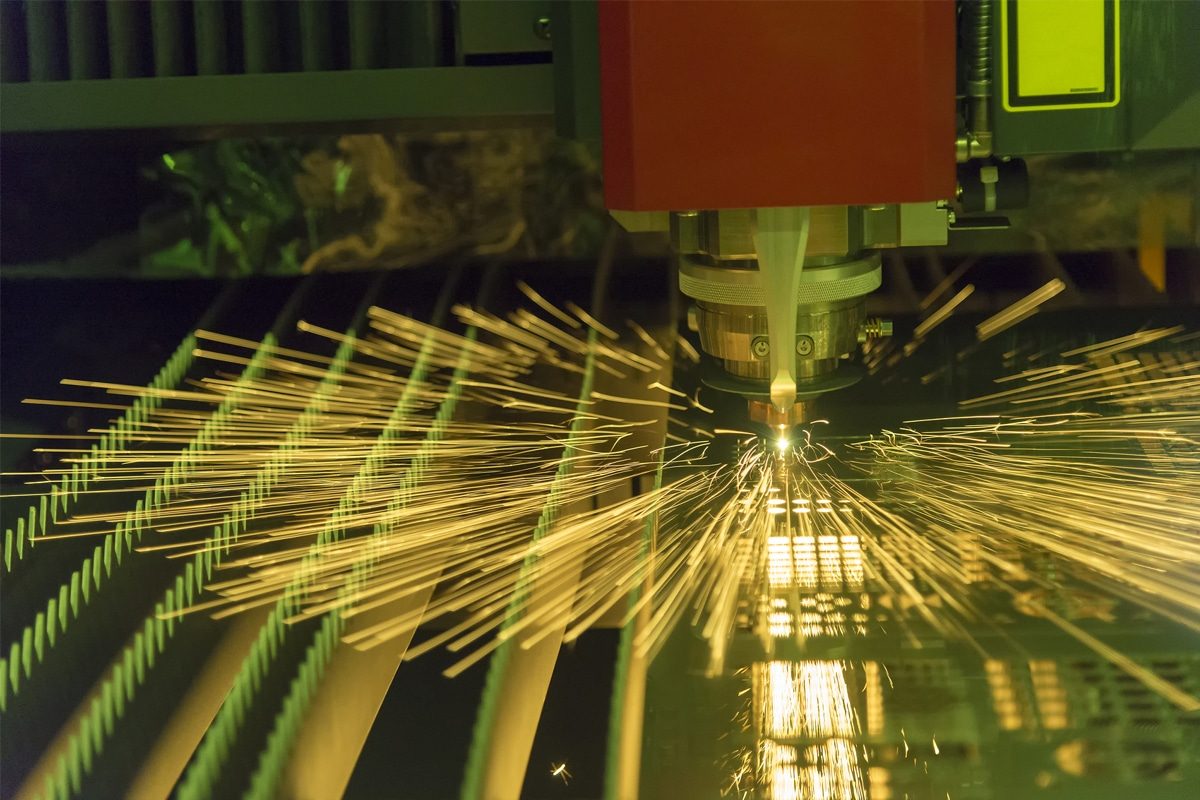
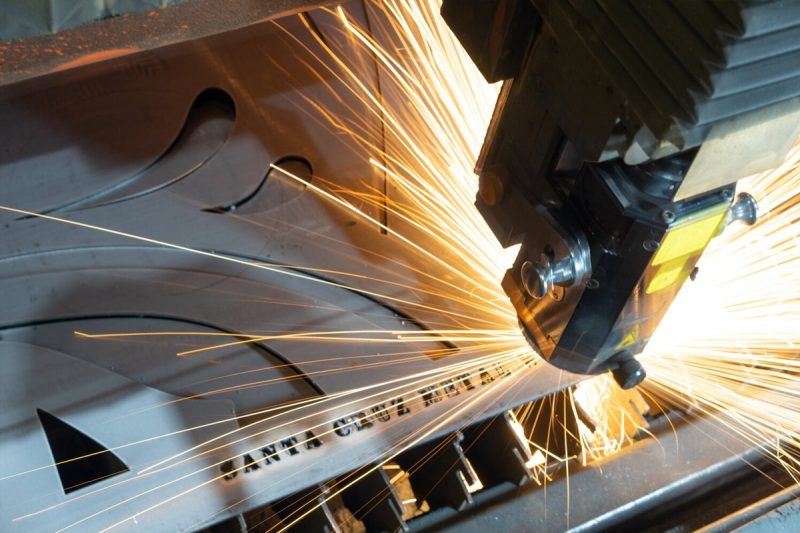
Unparalleled Precision and Accuracy
High Precision Cutting
Laser-cutting machines utilize a focused beam of light that can be as narrow as a fraction of a millimeter. This concentrated energy allows for extremely precise cuts with minimal deviation. The high precision cutting capability of laser technology ensures that each cut adheres closely to the specified design dimensions.
- Sub-Millimeter Accuracy: Laser cutting machines can achieve tolerances as tight as ±0.01 mm, making them ideal for applications where exact dimensions are critical.
- Clean Cut Edges: The laser beam melts or vaporizes the material, resulting in smooth and burr-free edges that require little to no post-processing.
- Complex Profiles: Whether it’s straight lines or intricate curves, laser cutting can handle complex profiles without compromising on precision.
Consistent Repeatability
Consistency is key in manufacturing, especially when producing large quantities of identical parts. Laser-cutting machines are equipped with advanced control systems that ensure each part is cut the same way every time.
- Computer Numerical Control (CNC): The integration of CNC systems allows for precise control over the cutting process. Digital designs are followed meticulously, reducing human error.
- Automated Settings: Once the parameters are set for a particular job, the machine can replicate the process repeatedly without variation.
- Quality Assurance: Consistent repeatability enhances quality control, ensuring that every piece meets the required standards and reducing waste due to defects.
Minimal Material Distortion
Traditional cutting methods can introduce stress and heat into the material, leading to distortion and warping. Laser cutting minimizes these issues through its non-contact process and focused energy application.
- Localized Heating: The laser beam heats only a small area, reducing the heat-affected zone (HAZ) and preventing thermal distortion of the surrounding material.
- Non-Contact Cutting: Since there is no physical contact with the material, mechanical stresses that can cause bending or warping are eliminated.
- Material Integrity: The structural and mechanical properties of the metal remain intact, which facilitates components that meet stringent performance standards.
Intricate Designs and Complex Geometries
One of the standout features of laser cutting is its ability to handle intricate designs and complex geometries with ease. This capability opens up new possibilities in design and functionality.
- Fine Detail Work: Laser-cutting machines can produce tiny holes, sharp corners, and intricate patterns that are difficult or impossible with other cutting methods.
- Versatility in Design: Designers have greater freedom to create innovative products without being limited by fabrication constraints.
- Efficient Prototyping: Rapid production of prototypes with complex features accelerates the development process and allows for quick iterations.
Examples of Application
The unparalleled precision and accuracy of laser cutting have transformative effects across various industries:
- Aerospace Industry: Components such as engine parts, brackets, and structural elements require exact dimensions and flawless finishes. Laser cutting ensures that these parts meet rigorous safety and performance standards.
- Medical Devices: Surgical instruments and implants demand the highest level of precision. Laser cutting produces components with the exact specifications needed for medical applications, where errors can have serious consequences.
- Automotive Manufacturing: From body panels to intricate internal components, the automotive industry relies on laser cutting for its ability to produce parts that fit together perfectly, enhancing vehicle performance and safety.
- Electronics and Electrical Equipment: The production of enclosures, connectors, and circuitry components benefits from laser cutting’s ability to create precise and intricate designs necessary for compact and efficient electronic devices.
- Architectural Fabrication: Decorative metalwork and structural components in architecture often feature complex designs. Laser cutting allows architects and builders to realize their creative visions with precision-cut materials.
- Customized Solutions: Companies requiring bespoke metal parts for specialized equipment can utilize laser cutting to produce small batches without the need for expensive tooling or extended lead times.
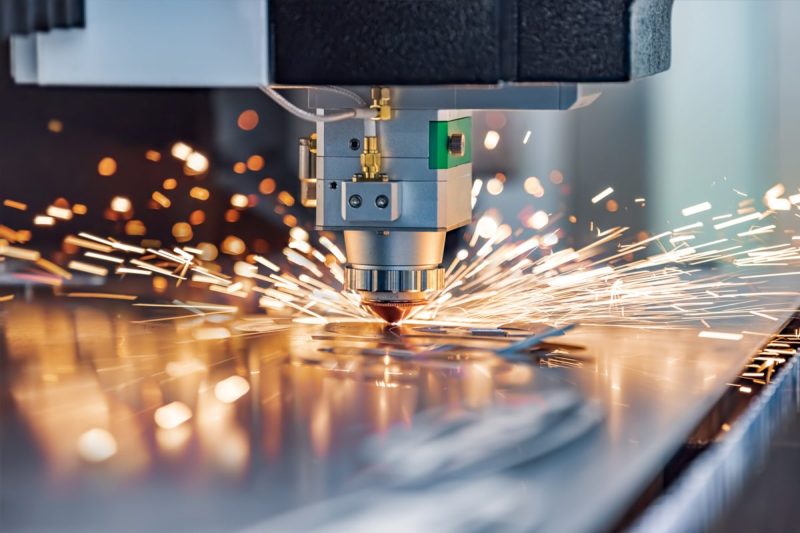
Versatility and Flexibility
Wide Range of Materials
One of the most compelling features of laser cutting is its compatibility with a broad spectrum of materials. Laser-cutting machines are engineered to process a wide range of metals and alloys, allowing manufacturers to meet the needs of different industries.
- Metals and Alloys: Laser cutting is effective on materials such as carbon steel, stainless steel, aluminum, copper, brass, and titanium. This versatility allows for applications across different sectors, from automotive to aerospace.
- Reflective Materials: Advanced laser technology can cut reflective metals like aluminum and copper with high precision, overcoming challenges that traditional methods face with these materials.
- Specialty Metals: For industries requiring exotic or specialized metals, laser cutting provides a solution that maintains material integrity and performance characteristics.
Varied Thickness Capabilities
Laser cutting machines are designed to process materials of various thicknesses, with flexibility that traditional cutting methods cannot match.
- Thin Sheets to Thick Plates: Laser cutting machines can process thin sheets of metal less than 1 mm thick to thick plates up to 30 mm, depending on the material and laser power.
- Adjustable Power Settings: The ability to adjust laser power settings allows for optimal cutting conditions for different thicknesses, ensuring clean cuts regardless of material gauge.
- Consistent Quality: Whether dealing with thin or thick materials, laser cutting delivers consistent edge quality and precision, reducing the need for secondary processing.
Design Flexibility
Laser-cutting technology opens up new horizons in design possibilities, allowing for rapid changes and customization without significant downtime or cost.
- Digital Integration: Designs are created or modified using CAD software and directly transferred to the laser cutting machine. This seamless integration enables quick adjustments and iterations.
- No Tooling Changes: Unlike mechanical cutting methods that require new tools or dies for different designs, laser cutting doesn’t necessitate physical tool changes, saving time and resources.
- Customization: Manufacturers can easily produce custom parts or limited runs without the overhead associated with retooling, catering to specific client needs or market niches.
Complex Shapes and Contours
Laser-cutting machines are highly accurate and can create complex shapes and detailed features that are difficult to achieve with other cutting methods.
- High Precision Beam: The laser’s fine focus point enables the cutting of small radii and sharp angles, facilitating complex geometries.
- Intricate Patterns: Detailed patterns, perforations, and engravings can be executed flawlessly, enhancing both the functionality and aesthetic appeal of components.
- Non-Linear Cutting Paths: The laser cutting machine can follow complex, non-linear paths without mechanical constraints, making it ideal for innovative designs.
Quick Adaptation to Different Projects
The flexibility of laser cutting technology ensures that manufacturers can swiftly adapt to new projects or changes in production requirements.
- Rapid Setup: Minimal setup time is needed when switching between jobs, as adjustments are made digitally rather than physically.
- Efficient Production Switchover: The ability to load different design files quickly allows for efficient transitions between different products or components.
- Scalability: Whether the need is for a single prototype or mass production, laser cutting can scale operations up or down with ease.
Examples of Application
The versatility and flexibility of laser cutting have practical applications across various industries:
- Architecture and Construction: Custom metal panels, decorative elements, and structural components benefit from laser cutting’s ability to produce unique designs with precision.
- Automotive Industry: From prototyping new models to producing complex parts like engine components and intricate bodywork, laser cutting supports innovation and efficiency.
- Aerospace Sector: The need for lightweight yet strong components made from specialized materials is met through laser cutting’s precision and material versatility.
- Electronics Manufacturing: Small, precise components, such as enclosures and brackets, are produced efficiently, accommodating the industry’s rapid development cycles.
- Art and Design: Artists and designers leverage laser cutting to create intricate sculptures, installations, and functional art pieces with complex patterns and shapes.
- Medical Equipment: Custom surgical instruments and medical devices require precise cuts and specific materials, which laser cutting provides without compromising sterility or quality.
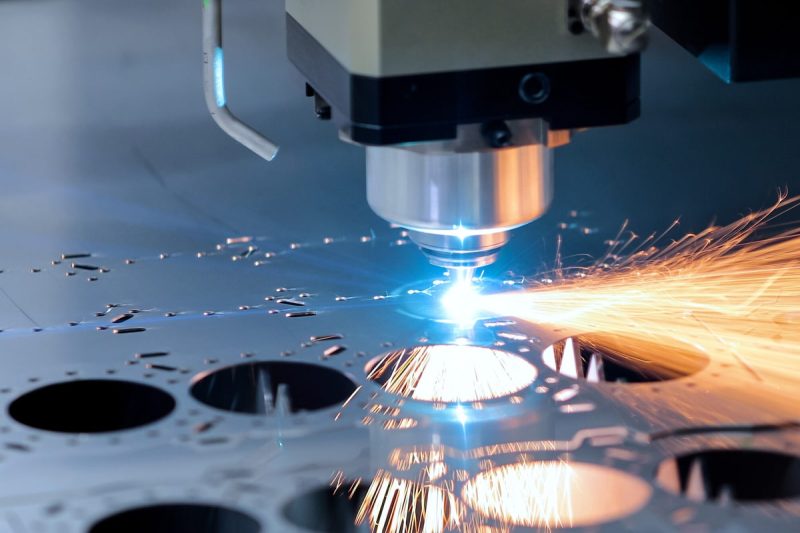
Reduced Material Waste
Minimal Kerf Width
The kerf is the width of material removed during the cutting process. Laser cutting offers an exceptionally narrow kerf width compared to traditional cutting methods.
- Precision Cutting: Laser cutting machines are extremely fine, often less than 0.1 mm in diameter. This precision allows for tight cutting paths, minimizing the amount of material turned into waste.
- Efficient Material Usage: A smaller kerf width means parts can be nested closer together, maximizing the number of pieces cut from a single sheet.
- Reduced Material Loss: Less material is consumed in the kerf, directly translating to lower material costs and waste.
Advanced Nesting Software
Laser-cutting machines come equipped with sophisticated nesting software that optimizes the placement of parts on the metal sheet.
- Optimal Layouts: The software calculates the most efficient arrangement of various shapes and sizes to utilize every possible area of the sheet.
- Automated Efficiency: By automating the nesting process, human error is minimized, and material utilization is maximized.
- Customizable Parameters: Users can adjust settings based on specific project needs, material types, and thicknesses to further enhance efficiency.
Reduced Offcuts and Scraps
Traditional cutting methods often result in significant offcuts and scrap material. Laser cutting minimizes these leftovers.
- Precision Nesting: With advanced software and minimal kerf, parts are closely nested, leaving less unused material.
- Complex Shape Accommodation: Laser cutting can handle intricate designs without increasing waste, unlike methods that struggle with non-standard shapes.
- Efficient Material Reuse: Smaller scraps that are generated can often be reused for smaller parts, further reducing waste.
Cost Savings from Material Efficiency
Reducing material waste leads to direct cost savings for manufacturers.
- Lower Material Costs: Maximizing the number of parts per sheet reduces the total amount of raw material needed.
- Decreased Waste Disposal Expenses: Less scrap means lower costs associated with handling and disposing of waste material.
- Improved Profit Margins: Efficient material use contributes to overall cost reduction, enhancing profitability.
Environmental Benefits
Material efficiency isn’t just good for business—it’s good for the planet.
- Resource Conservation: Using less material conserves natural resources and reduces the environmental impact of mining and processing metals.
- Reduced Carbon Footprint: Efficient fabrication processes consume less energy and produce fewer emissions.
- Sustainable Manufacturing: Companies can promote their commitment to sustainability, appealing to environmentally conscious consumers and partners.
Examples of Application
The advantages of reduced material waste are evident across various industries:
- Aerospace Industry: Expensive materials like titanium and aluminum are commonly used. Minimizing the waste of these costly resources significantly reduces production expenses.
- Automotive Manufacturing: High-volume production benefits from material efficiency, cutting costs while maintaining quality standards.
- Custom Fabrication Shops: Smaller businesses can offer competitive pricing by reducing material waste, and attracting more clients.
- Electronics Industry: Precise components require minimal material usage; laser cutting ensures efficient production without compromising quality.
- Architectural Projects: Large-scale designs with intricate patterns can be executed with minimal waste, making projects more cost-effective and environmentally friendly.
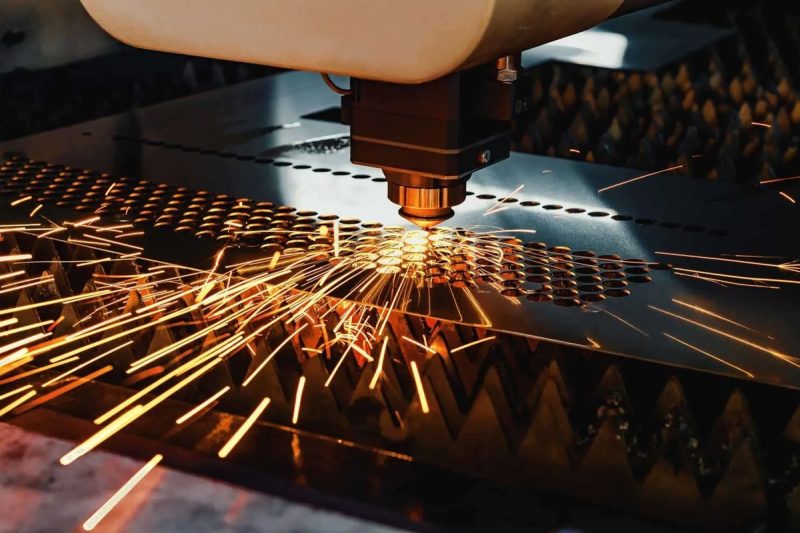
Cost-Effectiveness
Lower Labor Costs
Laser-cutting machines are highly automated, which reduces the reliance on manual labor and associated costs.
- Automation Efficiency: Laser cutting machines feature advanced automation capabilities, allowing for continuous operation with minimal human intervention.
- Reduced Workforce Requirements: Fewer operators are needed to manage laser cutting machines compared to traditional cutting methods, leading to savings on labor expenses.
- Decreased Training Costs: User-friendly interfaces and intuitive controls mean that operators can be trained quickly and effectively, reducing the time and cost associated with extensive training programs.
Reduced Tooling Costs
Traditional cutting methods often require custom tooling for each design, which can be expensive and time-consuming to produce.
- No Need for Physical Tools: Laser cutting utilizes a focused laser beam to cut materials, eliminating the need for physical cutting tools that wear out or need replacement.
- Design Flexibility Without Extra Cost: Changes in product design do not necessitate new tools, updates can be made directly in the software, saving time and money.
- Lower Maintenance Expenses: Without physical tooling, there’s less equipment to maintain or replace, reducing ongoing operational costs.
Energy Efficiency
Energy consumption is a significant operational cost in manufacturing. Machines are designed with energy efficiency in mind.
- Advanced Laser Technology: The fiber laser generator used in the fiber laser cutting machine is more energy-efficient than the CO2 laser tube used in the traditional CO2 laser cutting machine, consuming less electricity while providing excellent performance.
- Reduced Operating Costs: Lower energy consumption translates to reduced electricity bills, contributing to overall cost savings.
- Environmentally Friendly: Energy-efficient machines not only save money but also reduce carbon footprint, supporting sustainable manufacturing practices.
Long-Term Savings
Investing in laser-cutting technology offers substantial long-term financial benefits.
- Durability and Longevity: Laser cutting machines are built with high-quality components, ensuring a long service life with minimal downtime.
- Consistent Quality Reduces Waste: The precision of laser cutting reduces errors and material waste, saving money on rework and discarded materials over time.
- Investment Return: The combination of reduced operational costs and increased productivity results in a quicker return on investment.
Scalability
Laser-cutting technology provides the flexibility to scale operations up or down without significant cost implications.
- Adaptable Production Volumes: Whether fulfilling small custom orders or large production runs, laser cutting machines can adjust to different volume requirements efficiently.
- Quick Changeovers: Rapid setup and minimal downtime between jobs allow manufacturers to respond swiftly to market demands without incurring extra costs.
- Resource Optimization: Scalability ensures optimal use of resources, preventing unnecessary expenditures on labor or materials during fluctuations in production needs.
Examples of Application
The cost-effectiveness of laser-cutting technology benefits various industries and applications:
- Small and Medium Enterprises (SMEs): SMEs can leverage laser cutting to offer competitive pricing by reducing production costs, allowing them to compete with larger companies.
- Automotive Manufacturing: High-volume parts production benefits from lower labor and tooling costs, improving profit margins without sacrificing quality.
- Custom Fabrication Shops: Businesses offering bespoke metalwork can reduce overhead costs, making custom projects more affordable for clients while maintaining profitability.
- Electronics Industry: Energy-efficient laser cutting reduces operational expenses in the mass production of electronic components and enclosures.
- Architecture and Construction: The ability to produce complex designs cost-effectively allows architects and builders to incorporate innovative metal elements into projects without excessive costs.
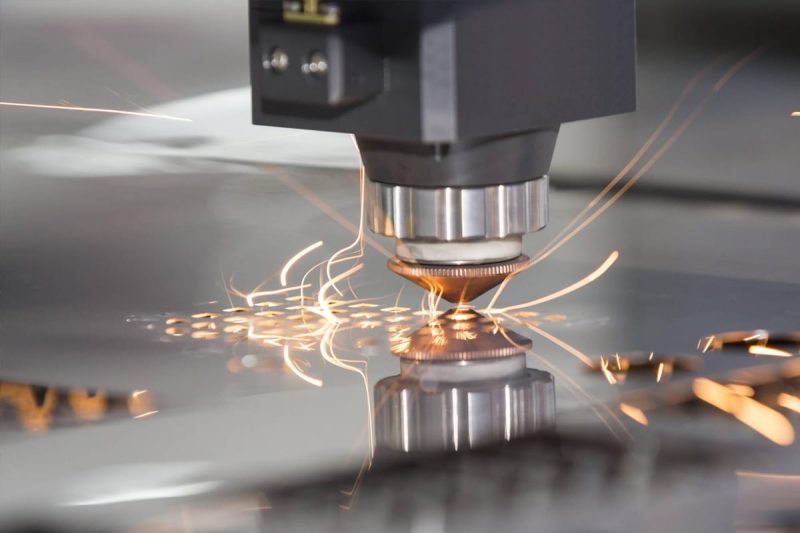
Non-Contact Process Reduces Distortion
Minimization of Mechanical Stress
Laser cutting eliminates the need for physical contact between the cutting tool and the material.
- No Physical Force Applied: The laser beam cuts through the material using concentrated light energy, not mechanical force. This absence of contact means there’s no pressure exerted on the sheet metal.
- Reduced Risk of Deformation: Without mechanical stress, the material maintains its flatness and shape, preventing warping or bending that can occur with traditional cutting methods.
- Ideal for Delicate Materials: Thin or sensitive metals that might be damaged by mechanical cutting tools are safely processed with laser cutting, preserving their structural integrity.
Reduced Heat-Affected Zone
While laser cutting involves high temperatures, the process is highly localized.
- Concentrated Heat Application: The laser focuses heat on a minute area, melting or vaporizing the metal precisely where the cut is needed.
- Minimal Thermal Spread: The surrounding material experiences negligible temperature increase, reducing the heat-affected zone (HAZ) and preventing thermal distortion.
- Preservation of Material Properties: By limiting the HAZ, the mechanical and chemical properties of the metal remain unchanged outside the immediate cutting area, ensuring consistent material performance.
Clean and Smooth Edges
The precision of laser cutting results in superior edge quality.
- Burr-Free Finishes: The laser produces clean cuts with smooth edges, eliminating the need for secondary finishing processes like grinding or sanding.
- Enhanced Aesthetics: For applications where the edge is visible or critical to the design, laser cutting delivers a high-quality finish that enhances the overall appearance.
- Improved Fit and Assembly: Smooth edges ensure parts fit together seamlessly, improving the efficiency of assembly processes and the quality of the final product.
Preservation of Material Integrity
Maintaining the original properties of the metal preserves part performance.
- No Material Contamination: The non-contact nature of laser cutting means there’s no risk of contamination from cutting tools or lubricants, which can compromise material purity.
- Structural Integrity Maintained: By avoiding mechanical and excessive thermal stress, the metal’s internal structure remains intact, ensuring durability and reliability.
- Suitable for High-Precision Applications: Industries that require exacting standards, such as aerospace and medical devices, benefit from laser cutting’s ability to preserve material properties.
Examples of Application
The advantages of a non-contact process are leveraged across various industries:
- Aerospace Industry: Components like turbine blades and structural elements require precise cuts without altering material properties. Laser cutting ensures these parts meet stringent specifications without distortion.
- Medical Device Manufacturing: Surgical instruments and implants must be produced with exact dimensions and smooth finishes to ensure patient safety. Laser cutting provides the necessary precision and cleanliness.
- Electronics and Microfabrication: Small, delicate components such as circuit boards and microchips benefit from laser cutting’s precision and lack of mechanical stress, preventing damage during fabrication.
- Automotive Sector: High-strength steels and specialized alloys used in automotive parts require cutting methods that don’t compromise material integrity. Laser cutting delivers distortion-free components that enhance vehicle performance.
- Art and Design: Artists and designers utilize laser cutting to create intricate metalwork with clean edges and precise details, all without distorting the material.
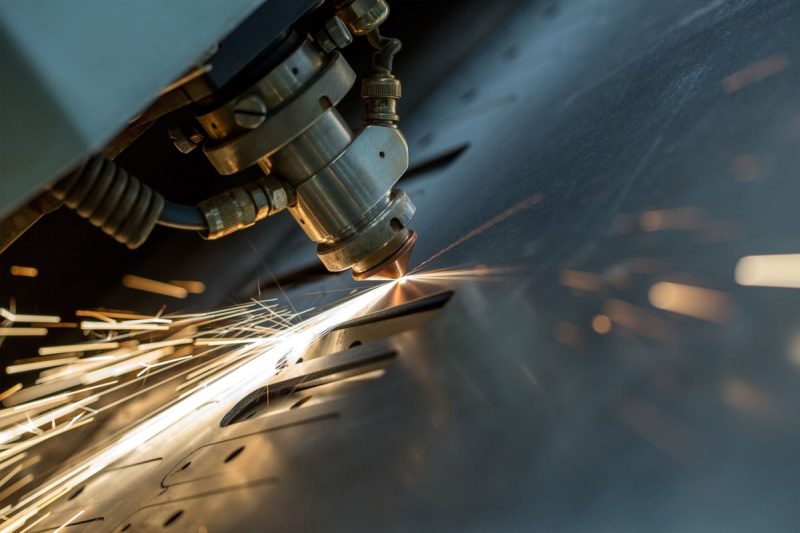
Summary
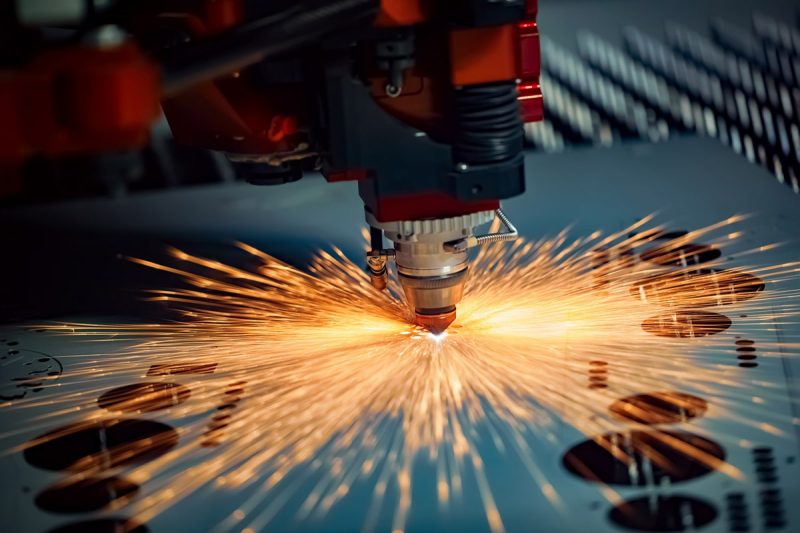
Get Laser Cutting Solutions
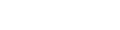
- [email protected]
- [email protected]
- +86-19963414011
- No. 3 Zone A, Lunzhen Industrial Zone,Yucheng City , Shandong Province.