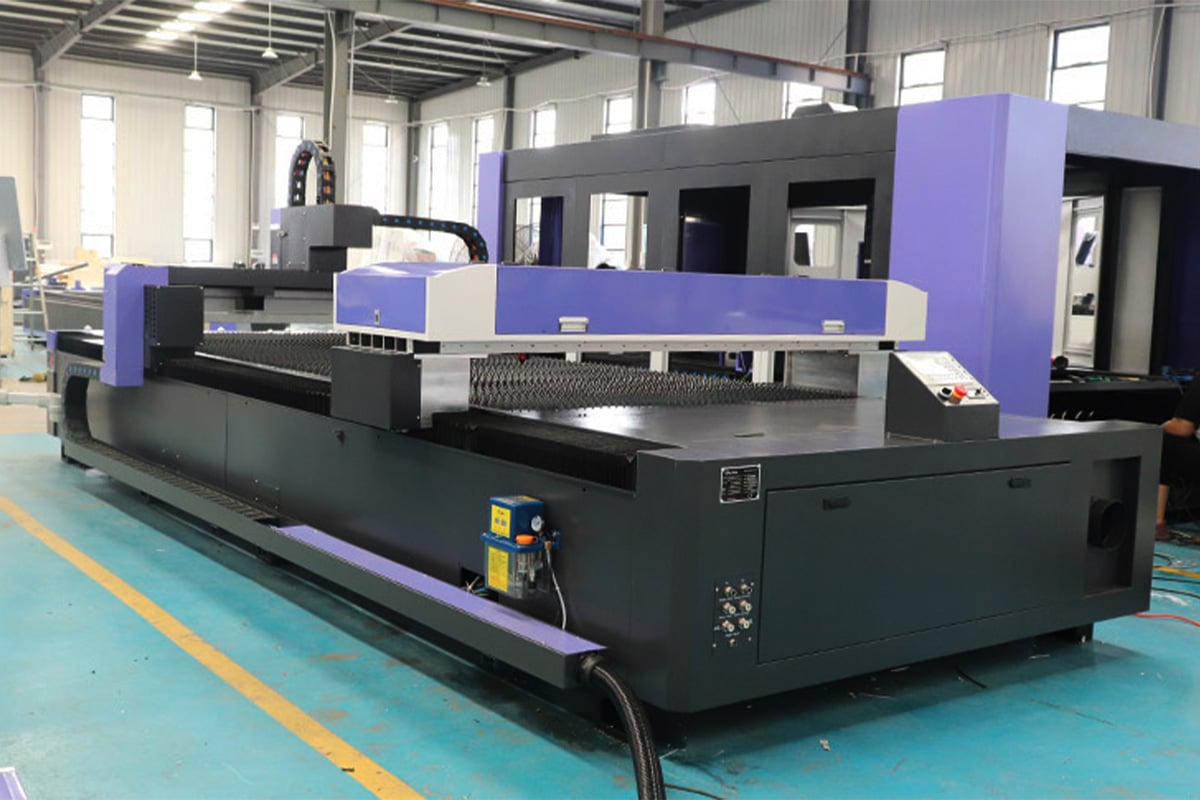
CO2 Lazer Kesimde Minimum Kesi Genişliği Nasıl Elde Edilir?
CO2 lazer kesim teknolojisi, yüksek hassasiyet, yüksek hız ve temassız işleme avantajları nedeniyle metal işleme, plastik, ahşap, kumaş vb. gibi çeşitli malzemelerin kesim sürecinde yaygın olarak kullanılmaktadır. Kerf Genişliği, kesme işlemi sırasında lazer ışınının oluşturduğu kesiğin genişliğini ifade eder. Bu gösterge, doğrudan kesimin hassasiyetini ve kalitesini etkiler. Daha küçük bir kesi genişliği, daha rafine bir işleme etkisi elde edebilir, ürün hassasiyetini iyileştirebilir, malzeme israfını azaltabilir ve üretim maliyetlerini düşürebilir. Bu nedenle, lazer kesim kalitesini ölçmek için önemli bir kriterdir.
Kesi genişliğinin kontrolü yalnızca ürün kalitesini iyileştirmekle kalmaz, aynı zamanda malzemelerin kullanım oranı, sonraki işleme kolaylığı ve genel üretim verimliliği ile de yakından ilgilidir. Üreticiler için, kesi genişliğinin optimizasyonu doğrudan üretim maliyetlerinin kontrolü ile ilgilidir. Özellikle büyük ölçekli üretimde, çok büyük bir kesi genişliği malzeme israfına yol açabilir ve sonraki süreçlerin sorunsuz ilerlemesini etkileyebilir. Bu nedenle, kesi genişliğinin hassas kontrolü verimli ve düşük maliyetli üretim elde etmek için önemli bir bağlantıdır.
İçindekiler
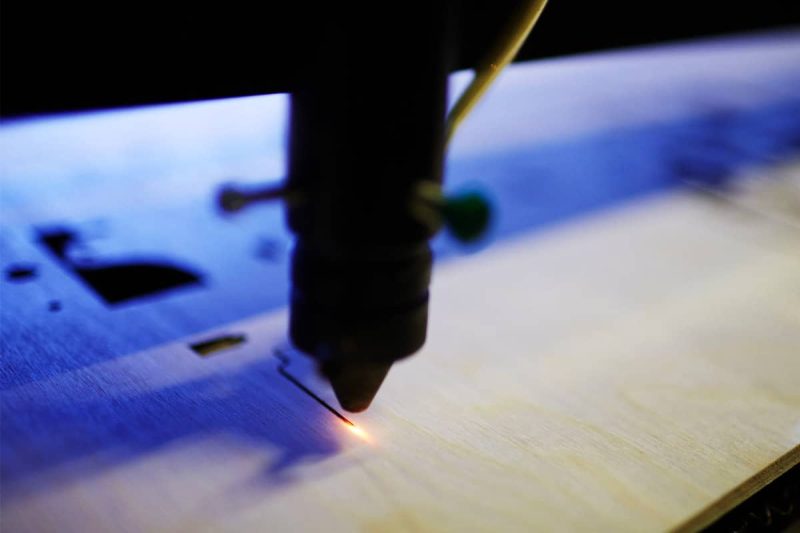
CO2 lazer kesim kerf genişliğini etkileyen temel faktörler
CO2 lazer kesim teknolojisinin kesme etkisi birçok faktörden etkilenir ve kerf genişliği en kritik göstergelerden biridir. Üreticiler bu faktörleri makul bir şekilde ayarlayıp optimize ederek üretim verimliliğini artırabilir ve yüksek hassasiyet sağlarken malzeme kaybını azaltabilirler. Kerf genişliğini ve optimizasyon stratejilerini etkileyen birkaç temel faktör şunlardır:
Lazer odak boyutu: Lazer odak boyutu doğrudan noktanın çapını etkiler ve nokta ne kadar küçükse, kesi genişliği o kadar dar olur. Odak ne kadar hassas olursa, lazer ışını enerjisinin konsantrasyonu o kadar yüksek olur ve böylece kesme doğruluğu artar. Kesik genişliğini optimize etmek için doğru odak uzaklığına sahip lensi seçmek önemlidir. Genellikle, kısa odak uzaklığına sahip bir lens daha küçük bir odak çapı sağlayabilir ve böylece daha rafine bir kesme etkisi elde edilebilir. Farklı malzemeler ve kesme gereksinimleri için, en iyi kesme etkisini sağlamak üzere odak uzaklığı ayarlanarak odak boyutu optimize edilebilir.
Lazer gücü: Lazer gücü, kesme işlemi sırasında erime, buharlaşma ve kesme etkilerini etkileyen lazer ışınının termal enerji yoğunluğunu doğrudan belirler. Lazer gücü çok yüksekse, kesiğin çok geniş olmasına veya hatta malzemeyi yakmasına neden olmak kolaydır; güç çok düşükse, malzemeye tamamen nüfuz edemeyebilir ve bu da eksik kesme ile sonuçlanabilir. Lazer gücünü, farklı malzemelerin kalınlığına ve özelliklerine göre optimum değere ayarlamak çok önemlidir. Örneğin, daha kalın malzemeler için gücün uygun şekilde artırılması gerekirken, ince malzemeler için kesinin çok geniş olmasını önlemek için güç azaltılabilir. Üreticiler, gücü doğru bir şekilde ayarlayarak hassas ve verimli kesim elde edebilirler.
Kesme hızı: Kesme hızı, lazer kesiminde de önemli bir rol oynar. Kesme hızının uygun şekilde artırılması, yalnızca ısıdan etkilenen bölgeyi ve erimiş malzemenin kesim kenarına olan etkisini azaltmakla kalmaz, aynı zamanda üretim verimliliğini de artırır. Ancak, kesme hızı çok hızlıysa, lazer ışını malzemeye tam olarak nüfuz etmek için yeterli zamana sahip olmayabilir ve bu da eksik kesimle sonuçlanabilir; tersine, çok düşük hız, kesimin çok geniş olmasına ve aşırı erimeye neden olabilir. Kesme etkisini optimize etmek için, kesim genişliğinin en aza indirilmesini sağlamak amacıyla kesme hızının malzemenin türüne ve kalınlığına göre doğru bir şekilde ayarlanması gerekir.
Yardımcı gaz türü ve basıncı: Yardımcı gaz, lazer kesiminde hayati bir rol oynar. Yaygın olarak kullanılan yardımcı gazlar oksijen, nitrojen ve havadır. Oksijen, kesme işlemi sırasında yanma reaksiyonunu artırabilir ve demir ve çelik gibi malzemeleri kesmek için uygundur; nitrojen oksidasyonu azaltabilir ve paslanmaz çelik gibi malzemeler için uygundur; hava, ekonomisi nedeniyle çeşitli malzemelerde yaygın olarak kullanılır. Gaz türüne ek olarak, gaz basıncı da kesme kalitesini etkiler. Uygun gaz basıncı, eriyiği çıkarmaya ve kesiğin kenarına yapışmasını önlemeye yardımcı olabilir, böylece kesi genişliğini azaltabilir. Daha düşük gaz basıncı, eriyiği etkili bir şekilde çıkarma ve kesi genişliğini artırma yetersizliğine neden olabilir, bu nedenle kesme etkisini optimize etmek için uygun gaz basıncı ve türü seçilmelidir.
Malzeme özellikleri: Farklı malzemelerin özellikleri lazer kesiminin doğruluğunu önemli ölçüde etkileyebilir. Malzemenin emilim oranı, ısıl iletkenlik ve erime noktası gibi özellikleri, lazer ışınının iletim verimliliğini ve kesim kalitesini doğrudan etkiler. Yüksek yansıtıcı malzemeler (alüminyum, bakır vb. gibi) lazer ışınının yansımasına ve dağılmasına neden olarak kesme etkisini azaltır. Bu malzemeler için, lazerin malzemeye etkili bir şekilde nüfuz edebilmesini sağlamak için özellikle güç yoğunluğunu artırmak için lazer parametrelerini optimize etmek gerekir. Aksine, çelik gibi düşük yansıtıcı malzemelerin kesilmesi daha kolaydır. Farklı malzemeleri keserken, üreticiler en iyi kesim kalitesini ve en küçük kesi genişliğini sağlamak için kesme parametrelerini malzeme özelliklerine göre ayarlamalıdır.
Kesme yolu optimizasyonu: Kesme yolunun optimizasyonu, kesi genişliğini kontrol etmek için de önemlidir. Düzgün bir kesme yolu, yön değiştiğinde lazer ışınının hatasını azaltabilir ve düzensiz kesileri önleyebilir. Özellikle karmaşık şekilleri keserken, yolun makul bir şekilde tasarlanması ve dönüşlerin ve acil durdurmaların azaltılması, kesme doğruluğunu önemli ölçüde iyileştirebilir. Ayrıca, besleme ve geri çekme stratejilerinin optimize edilmesi, malzeme aşınmasını azaltmaya ve aşırı ısınmadan kaynaklanan kesi deformasyonunu önlemeye yardımcı olabilir. Yol tasarlanırken, kesme işlemi sırasında enerjinin eşit şekilde dağıtılmasını sağlamak ve böylece kesi genişliğini kontrol etmek için hızlı dönüşlerden ve düzensiz rotalardan mümkün olduğunca kaçınılmalıdır.
Üreticiler, bu temel faktörleri hassas bir şekilde kontrol ederek ve optimize ederek üretim maliyetlerini düşürebilir, malzeme kullanımını iyileştirebilir ve yüksek hassasiyetli kesimi garanti altına alırken üretim verimliliğini artırabilirler.
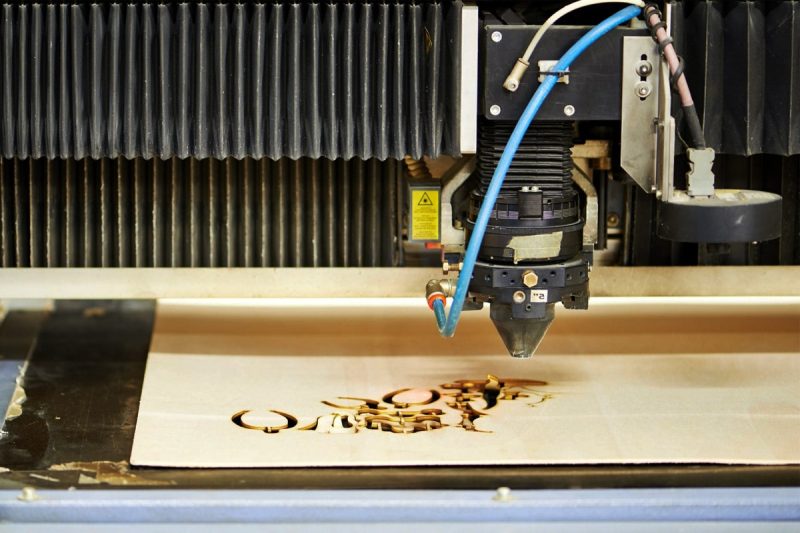
Minimum kerf genişliğine ulaşmak için optimizasyon stratejisi
CO2 lazer kesiminde minimum kerf genişliğine ulaşmak için birden fazla optimizasyon stratejisi dikkate alınmalıdır. Bu stratejiler yalnızca kesme doğruluğunu iyileştirmekle kalmaz, aynı zamanda malzeme israfını etkili bir şekilde azaltabilir ve üretim verimliliğini artırabilir. Minimum kerf genişliğine ulaşmak için temel optimizasyon yöntemleri şunlardır:
Optik sistemi optimize edin: Optik sistemin kalitesi, lazer ışınının odaklama etkisini doğrudan etkiler ve bu da kesiğin inceliğini etkiler. Yüksek kaliteli bir optik lens seçmek, lazer ışınının hedef malzemenin yüzeyine eşit şekilde odaklanmasını sağlayarak kararlı ve hassas bir kesme etkisi elde edilmesini sağlayabilir. Kısa odak uzaklığına sahip bir lens (örneğin 2,5 inç odak uzaklığı) kullanmak, lazer ışınının odaklanmasını optimize etmek için önemli bir stratejidir. Kısa odak uzaklığına sahip bir lens, daha küçük bir nokta çapına odaklanabilir, böylece lazer ışınının difüzyonunu azaltır ve kesi genişliğini büyük ölçüde azaltır. Daha küçük bir nokta yalnızca kesme doğruluğunu iyileştirmekle kalmaz, aynı zamanda malzeme üzerindeki termal etkiyi de azaltabilir ve kesme işlemi sırasında kararlılığı sağlayabilir.
Lazer gücünü ve hızını doğru şekilde ayarlayın: Lazer gücü ve kesme hızı, kesi genişliğini etkileyen iki önemli faktördür. En iyi kesme etkisi, lazer gücü ve hızının kombinasyonunun doğru şekilde ayarlanmasıyla elde edilebilir. Darbe modunun kullanılması, sürekli ısıtma süresini azaltabilir, böylece ısıdan etkilenen bölgeyi (HAZ) azaltabilir ve kesi kenarındaki erime fenomenini azaltabilir. Darbe modu, lazer enerjisi dağıtımını daha düzgün hale getirir ve yüksek güçlü sürekli çıkışın neden olduğu aşırı ısınma sorununu önler. Aynı zamanda, lazer gücünü malzemenin kalınlığıyla birlikte ayarlamak, lazer ışınının hem malzemeye tamamen nüfuz etmesini hem de kesi genişliğini kontrol etmesini sağlayabilir. Daha ince malzemeler için, aşırı ısı birikimini önlemek için gücü uygun şekilde azaltın; daha kalın malzemeler için, kesme kalitesini sağlamak için gücü uygun şekilde artırın, ancak yine de kesi genişliğini kontrol etmeye dikkat edin.
Yardımcı gaz parametrelerini ayarlayın: Yardımcı gaz, CO2 lazer kesiminde önemli bir rol oynar. Sadece kesme işlemi sırasında üretilen eriyiği çıkarmaya yardımcı olmakla kalmaz, aynı zamanda gaz basıncını optimize ederek kesme kalitesini de kontrol eder. Gaz basıncını uygun şekilde artırmak, kesme işlemi sırasında üretilen cürufu etkili bir şekilde çıkarabilir ve kesiğin kenarına yapışmasını önleyebilir, böylece dar bir kesi genişliğini koruyabilir. Yardımcı bir gaz seçerken, özellikle oksidasyonu azaltması ve kesme sonucunu iyileştirmesi gereken malzemeler için azot yaygın olarak kullanılan gazlardan biridir. Azot, sadece malzeme yüzeyinin oksidasyonunu etkili bir şekilde azaltmakla kalmaz, aynı zamanda kesme işlemi sırasında kesiğin pürüzsüzlüğünü koruyarak daha kaliteli bir kesme etkisi elde edebilir.
Yazılım ve CNC parametrelerini optimize edin: Yüksek hassasiyetli CNC sistemleri, lazer kesiminin doğruluğunu etkili bir şekilde iyileştirebilir ve mekanik hatalardan kaynaklanan kesim sapmalarını azaltmaya yardımcı olabilir. Gelişmiş CNC sistemlerini kullanarak, kesme yolunu optimize edebilir ve lazer ışınının yönündeki değişikliklerden kaynaklanan hataları azaltabilirsiniz. Doğru yol planlaması, kesme sırasında dönüşler ve düzensiz yollardan kaynaklanan hataları azaltmaya yardımcı olur. Ek olarak, otomatik odaklama sisteminin kullanımı da kesi genişliğini optimize etmek için önemli bir stratejidir. Otomatik odaklama sistemi, lazer ışınının her zaman en iyi konuma odaklanmasını sağlamak için lazer odak konumunu malzemenin kalınlığına, şekline ve kesme gereksinimlerine göre otomatik olarak ayarlayabilir ve böylece yanlış odak konumu nedeniyle düzensiz veya çok geniş kesiler önlenebilir.
Isıdan etkilenen bölgeyi (HAZ) azaltın: HAZ'ın boyutu, lazer kesim işlemi sırasında biriken ısı ile yakından ilgilidir. Aşırı ısı, malzeme yüzeyinin aşırı erimesine neden olabilir, böylece kesi genişliğini artırabilir ve kesim kalitesini etkileyebilir. Isıdan etkilenen bölgeyi azaltmak için yüksek hızlı kesim etkili bir stratejidir. Yüksek hızlı kesim, lazer ışınının hareketini hızlandırabilir, böylece malzeme yüzeyindeki ısı birikimini azaltabilir ve kesi kenarının erimesini ve genişlemesini önleyebilir. Ancak, yüksek hızlı kesim kullanılırken, lazer ışınının enerjisinin malzemeye nüfuz etmek için yeterli olduğundan emin olmak gerekir. Kesim kalitesini daha da optimize etmek için, kesme alanının sıcaklığını etkili bir şekilde azaltabilen, aşırı ısınmayı önleyebilen ve daha hassas ve kararlı bir kesim etkisi sağlayabilen sprey soğutma veya çift gaz enjeksiyonu gibi soğutma teknolojisi birleştirilebilir.
Yukarıdaki optimizasyon stratejilerini birleştirerek, üreticiler CO2 lazer kesiminde minimum kerf genişliğine etkili bir şekilde ulaşabilirler. Teknolojinin sürekli ilerlemesi ve ekipmanın sürekli optimizasyonu ile bu stratejiler, kesim hassasiyetini daha da iyileştirmeye, malzeme israfını azaltmaya ve üretim verimliliğini artırmaya yardımcı olacaktır.
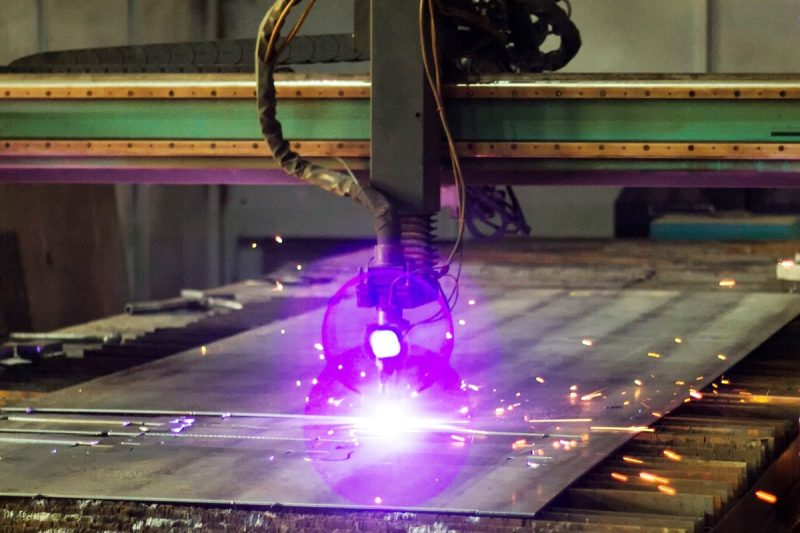
özetle
Minimum kerf genişliğine ulaşmak sadece basit bir parametre ayarlaması değil, aynı zamanda birçok faktörün kapsamlı bir şekilde dikkate alınmasını gerektiren bir süreçtir. Lazer odağını, güç ayarını, kesme hızını, yardımcı gaz türünü ve basıncını ve yazılım kontrolünü doğru bir şekilde optimize ederek, üreticiler üretim verimliliğini en üst düzeye çıkarabilir ve kesim kalitesini garanti ederken malzeme israfını azaltabilirler. Lazer odağının hassas bir şekilde ayarlanması, kesme alanının nokta boyutunu garanti edebilir ve kesme işlemi sırasında aşırı ısıdan etkilenen bölgeleri önleyebilir, böylece ince ve pürüzsüz bir kesim sağlanabilir. Güç ve kesme hızının hassas bir şekilde birleştirilmesi, aşırı ısı birikimini önleyebilir ve eriyiğin kesim genişliği üzerindeki etkisini azaltabilir. Doğru yardımcı gaz yalnızca cürufu gidermekle kalmaz, aynı zamanda oksidasyonu da önleyerek kesim kalitesini daha da iyileştirebilir. Aynı zamanda, gelişmiş CNC yazılımı ve otomatik odaklama teknolojisinin kullanımı, kesme etkisinin kararlılığını ve tutarlılığını sağlamak için kesme yolunu ve lazer ışını odağını sürekli olarak optimize edebilir.
Teknolojinin sürekli gelişmesiyle birlikte, CO2 lazer kesim makinelerinin performansı ve kontrol doğruluğu da sürekli olarak iyileşiyor. Üreticiler, optik teknolojisinin, otomatik kontrol sistemlerinin ve verimli soğutma teknolojisinin sürekli ilerlemesiyle birlikte yukarıdaki faktörleri sürekli olarak ayarlayıp optimize ederek daha doğru kesim efektleri elde edebilirler. Sonuç olarak, minimum kesi genişliğine ulaşmak yalnızca kesim doğruluğunu iyileştirmekle kalmaz, aynı zamanda daha yüksek üretim verimliliği getirir, malzeme maliyetlerini düşürür ve uzun vadeli kullanımda üretim hattının ekonomik faydalarını önemli ölçüde iyileştirir. Bu nedenle, CO2 lazer kesim makineleriBu optimizasyon stratejilerinin sürekli öğrenilmesi ve ustalaşılması, genel üretim kapasitesinin ve rekabet gücünün artırılmasının anahtarı olacaktır.
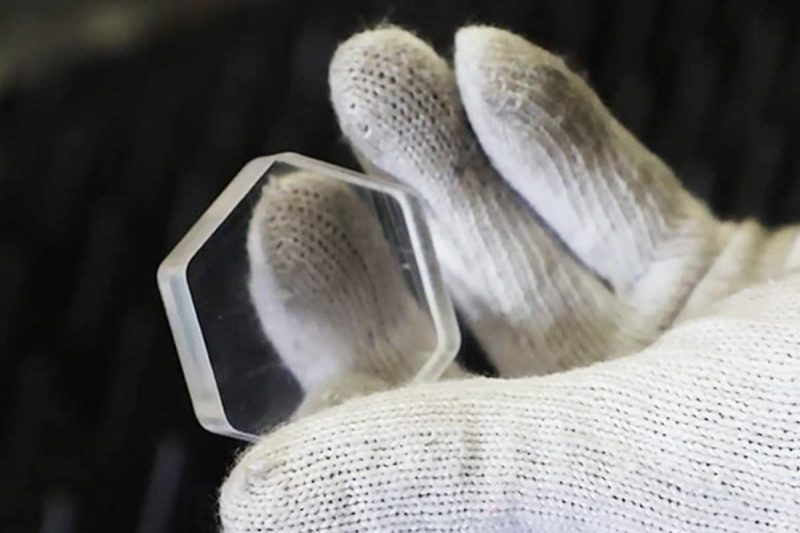
Lazer Çözümleri Alın
AccTek Lazer minimum kesi genişliğini garantilemek ve hassas işleme ulaşmak için akıllı odaklama, otomatik yol optimizasyonu ve verimli yardımcı gaz kontrolünü destekleyen yüksek hassasiyetli CO2 lazer kesim ekipmanı sağlar. Bize Ulaşın Üretim verimliliğinizi ve işleme doğruluğunuzu artırmak için özelleştirilmiş lazer kesim çözümlerine ulaşın!
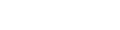
İletişim bilgileri
- [email protected]
- [email protected]
- +86-19963414011
- 3 Bölge A, Lunzhen Sanayi Bölgesi, Yucheng Şehri, Shandong Eyaleti.
Lazer Çözümleri Alın