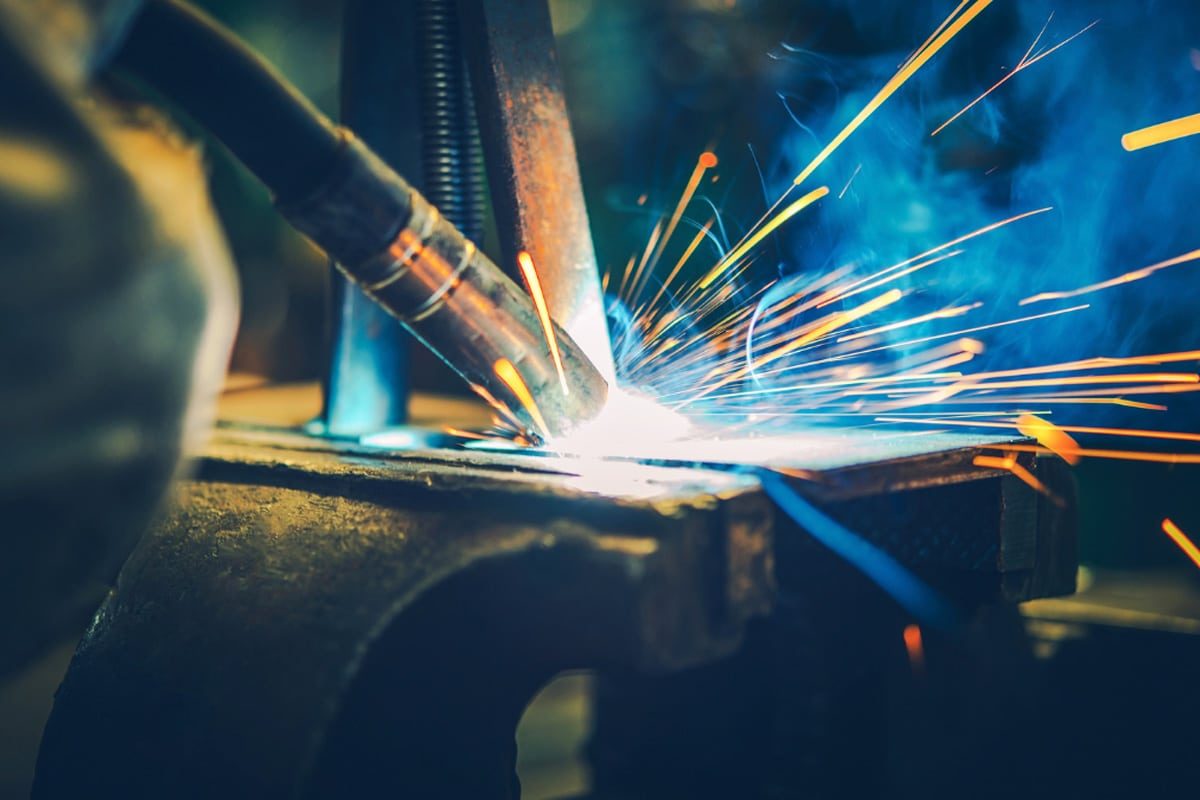
Benzer Olmayan Malzemelerin Lazer Kaynağı Kılavuzu
Modern üretimde, farklı malzemelerin kaynaklanmasına yönelik talep hızla artmaktadır. Malzeme türlerinin çeşitlenmesiyle birlikte, kaynak teknolojisi, özellikle otomobiller, havacılık ve elektronik ekipmanlar gibi yüksek hassasiyetli endüstrilerde benzeri görülmemiş zorluklarla karşı karşıyadır. Farklı malzemelerin kaynaklanması yalnızca yüksek mukavemet ve yüksek dayanıklılık değil, aynı zamanda farklı malzemeler arasında uyumluluk sorunları da gerektirir. Bu sorunlar genellikle malzemelerin fiziksel özellikleri, kimyasal bileşimi, erime sıcaklığı, termal genleşme katsayısı vb. farklılıklarda yansıtılır. Bu nedenle, farklı malzemeleri kaynak yaparken, ısı girişi, kaynak parametreleri ve dolgu malzemelerinin seçimi hassas bir şekilde kontrol edilmelidir.Lazer kaynak makineleriYüksek enerji yoğunluğu ve yüksek hassasiyete sahip bir kaynak teknolojisi olarak, verimli ve doğru ısı girdisi ve dar bir ısıdan etkilenen bölge elde edilebilmesi nedeniyle farklı malzemelerin kaynağı için ideal bir seçim haline gelmiştir.
Ancak, lazer kaynak teknolojisinin birçok avantajına rağmen, özellikle malzemelerin fiziksel ve metalurjik özellikleri oldukça farklı olduğunda, farklı malzemelerin kaynaklanması hala belirli zorluklarla karşı karşıyadır. Farklı malzemeler arasındaki dolgu malzemelerinin termal genleşme davranışı, erime sıcaklığı ve uyumluluğu, kaynak alanında çatlaklara, kırılgan bileşiklerin oluşumuna ve kaynaklı eklemin mukavemetinde azalmaya yol açabilir. Bu sorunları çözmek, lazer kaynak işleminin hassas bir şekilde kontrol edilmesini ve lazer parametrelerinin, dolgu malzemelerinin ve kaynak teknolojisinin makul bir şekilde seçilmesini gerektirir. Bu nedenle, lazer kaynak farklı malzemelerin kaynaklanması için yeni bir çözüm sunsa da, başarılı bir şekilde uygulanması hala birçok önemli faktörü dikkate almalıdır.
İçindekiler
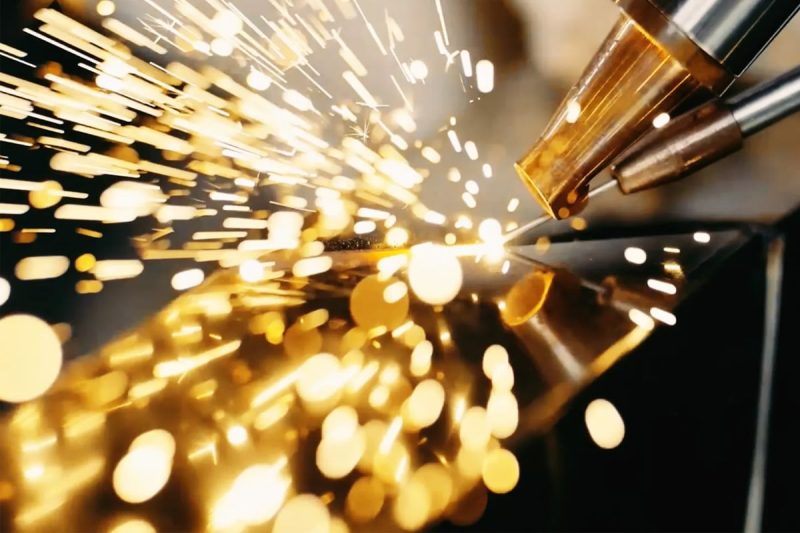
Farklı Malzemeleri Kaynaklamanın Zorlukları
Benzer olmayan malzemelerin kaynaklanması süreci genellikle kendi zorluklarıyla birlikte gelir. Farklı malzemelerin fiziksel özelliklerindeki farklılıklar, metalurjik uyumsuzluklar ve kaynak tasarımlarının karmaşıklığı, kaynak kalitesi ve performansı üzerinde önemli bir etkiye sahip olabilir. İşte benzer olmayan malzemelerin kaynaklanması sırasında karşılaşılan en yaygın zorluklar.
Fiziksel Özelliklerdeki Farklılıklar
- Isıl iletkenlik: Benzer olmayan malzemeleri kaynak yaparken karşılaşılan temel zorluklardan biri ısıl iletkenlikteki farktır. Farklı malzemeler farklı ısıl iletkenlik özelliklerine sahiptir, bu da malzemelerdeki ısı yayılımının hızı ve aralığının farklı olacağı anlamına gelir. Bazı yüksek alaşımlı metaller gibi zayıf ısıl iletkenliğe sahip malzemeler için, kaynak alanının sıcaklığı belirli bir noktada yoğunlaşabilir ve bu da yerel aşırı ısınmaya veya düzensiz erimeye neden olabilir. Bu düzensiz sıcaklık dağılımı yalnızca kaynaklı eklemin kalitesini etkilemekle kalmaz, aynı zamanda gerilim yoğunlaşmasına ve yapısal zayıflamaya da neden olabilir.
- Erime sıcaklığı: Farklı malzemelerin farklı erime sıcaklıkları vardır ve bu fark kaynak işlemi sırasında bir etkiye sahip olabilir. Farklı malzemelerin kaynaklanmasında, düşük erime noktasına sahip malzeme erken eriyebilirken, yüksek erime noktasına sahip malzeme kaynak için uygun bir sıcaklığa ulaşmakta zorluk çeker. Bu sırada, düşük erime noktasına sahip malzeme aşırı eriyebilirken, yüksek erime noktasına sahip malzeme uygun bir birleşim oluşturamaz ve bu da kaynağın sağlamlığını ve güvenilirliğini etkiler.
- Termal genleşme katsayısı: Farklı malzemelerin farklı termal genleşme katsayıları vardır, bu da ısıtma veya soğutma sırasında farklı oranlarda genleştikleri veya büzüldükleri anlamına gelir. İki malzeme birbirine kaynaklandığında, termal genleşme katsayılarındaki fark kaynak birleştirme bölgesinde gerilime neden olabilir. Bu gerilim kaynak işlemi sırasında birleştirmede çatlaklara veya deformasyona neden olabilir ve kaynaklı yapının kararlılığını ve dayanıklılığını etkileyebilir.
Metalurjik Uyumsuzluk
- Kırılgan intermetalik bileşiklerin oluşumu: İki metalik malzeme kaynaklandığında, metalurjik uyumsuzluklar genellikle kaynaklanmış eklem bölgesinde kırılgan intermetalik bileşiklerin oluşumuna neden olur. Bu bileşiklerin oluşumu genellikle farklı metallerin atomik yapısı ve kimyasal reaksiyonlarından kaynaklanır ve genellikle ana metalden daha zayıftırlar. Kırılgan intermetalik bileşikler, kaynaklanmış eklemlerin mukavemetini ve tokluğunu önemli ölçüde azaltabilir ve böylece kaynağın genel performansını etkileyebilir.
- Güçlü ve Dayanıklı Kaynaklar Elde Etmenin Zorluğu: Metaller arası bileşiklerin kırılganlığı nedeniyle, farklı malzemeleri kaynak yaparken hem mukavemet hem de tokluk sağlayan bir kaynak elde etmek zordur. Yüksek sıcaklık ve basınçtaki kaynak işlemi sırasında bile, termal stres, aşırı soğuma hızı veya metalurjik uyumsuzluk gibi faktörler nedeniyle kaynak çatlayabilir, düşebilir veya başka kusurlara sahip olabilir ve bu da kaynaklı yapının dayanıklılığını ve kararlılığını etkiler.
Ortak Tasarım Hususları
- Kurulum ve uyumluluk sorunları: Farklı malzemeleri kaynak yaparken, yalnızca uygun kaynak teknolojisi ve malzemelerinin seçimini dikkate almak değil, aynı zamanda malzemelerin kurulumuna ve uyumluluğuna da dikkat etmek gerekir. Farklı malzeme kaynaklı bağlantıların gerilim dağılımı ve termal genleşme davranışındaki farklılıklar, bağlantı bölgesinde eşit olmayan gerilime veya deformasyona neden olarak kaynaklı bağlantının kararlılığını ve bağlantı kalitesini etkileyebilir. Ayrıca, yüzey morfolojisi, malzemelerin boyutu ve montaj işlemi sırasındaki konumsal ilişkileri kaynak etkisi üzerinde önemli bir etkiye sahip olacaktır.
- Doğru dolgu malzemesi ve kaynak teknolojisini seçmek: Farklı malzemeleri kaynak yaparken karşılaşılan zorlukların üstesinden gelmek için doğru dolgu malzemesi ve kaynak teknolojisini seçmek çok önemlidir. Dolgu malzemesinin kimyasal bileşimi, erime sıcaklığı ve termal genleşme katsayısı, kaynaklı eklemin mukavemetini, tokluğunu ve dayanıklılığını sağlamak için ana malzemeyle eşleşmelidir. Farklı malzemeler arasındaki metalurjik uyumsuzluk ve fiziksel farklılıklar, ısı girişini ve kaynak kalitesini daha doğru bir şekilde kontrol etmek için lazer kaynağı, lazer ark hibrit kaynağı vb. gibi özel kaynak yöntemleri gerektirebilir.
Özetle, farklı malzemelerin kaynaklanması daha iyi işlevler ve uygulamalar getirebilse de, aynı zamanda birçok zorlukla da karşı karşıyadır. Bu zorlukları derinlemesine anlayarak ve uygun kaynak tekniklerini ve yöntemlerini benimseyerek, kaynak kalitesi etkili bir şekilde iyileştirilebilir ve kaynaklı eklemin kararlılığı ve dayanıklılığı sağlanabilir.
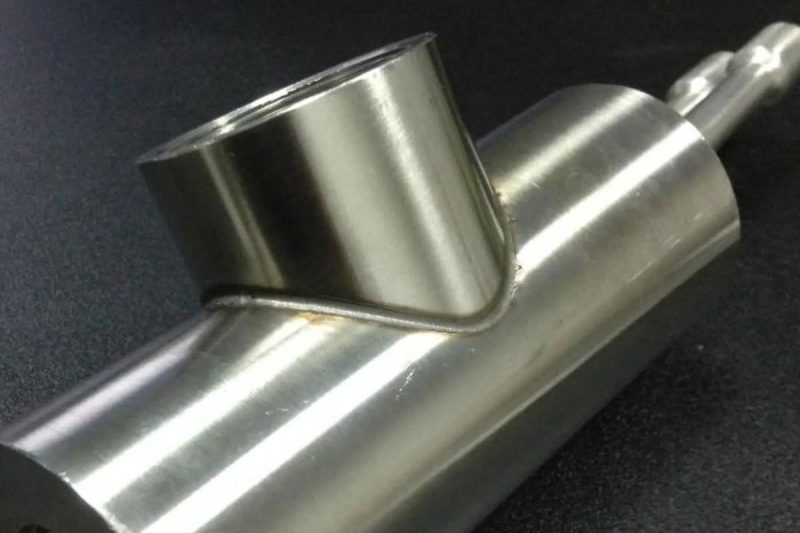
Farklı Malzemelerin Lazer Kaynağının Avantajları
Benzer olmayan malzemelerin kaynaklanmasında bazı zorluklar olsa da, lazer kaynak benzersiz avantajları nedeniyle bu sorunları çözmek için ideal bir teknoloji haline gelmiştir. Aşağıda, modern üretimde geniş uygulama potansiyelini gösteren farklı malzemelerin lazer kaynaklanmasının birkaç temel avantajı verilmiştir.
Yüksek Enerji Yoğunluğu: Lazer kaynağının yüksek enerji yoğunluğu, çok kısa bir sürede büyük miktarda ısı enerjisi salmasına olanak tanır. Bu özellik, çevredeki alanlara aşırı ısı transferini etkili bir şekilde önlediği için özellikle farklı malzemelerin kaynaklanması için uygundur. Yüksek enerji yoğunluğu, malzemeyi hızla erime noktasına kadar ısıtabilir, böylece kaynak alanının aşırı genleşmesi veya aşırı ısınması olgusunu azaltır; bu, ısı girişinin hassas bir şekilde kontrol edilmesini gerektiren uygulamalar için önemlidir. Lazer kaynağı, farklı erime sıcaklıklarına sahip malzemeler arasında etkili bir bağlantı sağlayabilir ve eşit olmayan ısı dağılımından kaynaklanan kaynak kusurlarını önleyebilir.
Hassas Isı Girişi Kontrolü: Lazer kaynak teknolojisi, ısı girişini hassas bir şekilde kontrol edebilir. Lazerin gücünü, odak konumunu ve tarama hızını ayarlayarak, ısı girişi kaynak işlemi boyunca korunabilir. Bu avantaj, farklı malzemelerin kaynak sırasında farklı termal genleşme ve erime davranışlarına sahip olması nedeniyle özellikle farklı malzemelerin kaynaklanması için önemlidir. Isı girişinin hassas bir şekilde kontrol edilmesi, termal stresi ve malzeme deformasyonunu azaltabilir ve termal genleşme farklılıklarının neden olduğu çatlakları veya düzensiz kaynak bağlantılarını önleyebilir.
Dar Isıdan Etkilenen Bölge (HAZ): Lazer kaynağının ısıdan etkilenen bölgesi (HAZ), geleneksel kaynak yöntemlerine göre çok daha küçüktür. Dar ısıdan etkilenen bölge, kaynak sırasında sadece birleştirme yerinin yakınındaki alanın yüksek sıcaklıklardan etkileneceği ve malzemenin geniş bir alanına termal hasar gelmesinin önleneceği anlamına gelir. Birbirine benzemeyen malzemeler için, ısıdan etkilenen bölgenin azaltılması, malzemeler arasındaki termal genleşme farkından kaynaklanan stres sorunlarını azaltmaya yardımcı olur ve çatlak ve deformasyon oluşumunu azaltır. Dar bir HAZ ayrıca, özellikle yüksek mukavemetli veya kırılgan malzemelerin kaynaklanmasında malzemenin orijinal özelliklerinin korunmasına yardımcı olur.
Hızlı kaynak hızı ve yüksek verimlilik: Lazer kaynak hızlıdır, bu da özellikle çok sayıda farklı malzemenin kaynaklandığı sahnede üretim verimliliğini önemli ölçüde artırabilir. Lazer kaynağının yüksek verimliliği sayesinde, üreticiler daha kısa sürede daha fazla kaynak görevini tamamlayabilir, bu da birim ürün başına üretim maliyetini düşürmeye ve üretim döngüsünü kısaltmaya yardımcı olur. Yüksek hızlı kaynak işlemi yalnızca üretimi artırmakla kalmaz, aynı zamanda özellikle büyük ölçekli üretim veya otomatik üretim hatları için genel iş akışının verimliliğini de artırabilir.
Çok yönlülük ve esneklik: Lazer kaynak son derece yüksek çok yönlülüğe ve esnekliğe sahiptir ve farklı kalınlıklarda, şekillerde ve malzemelerde farklı malzemeleri kaynaklayabilir. Bu, lazer kaynak işleminin çeşitli karmaşık üretim ihtiyaçlarında yaygın olarak kullanılmasını sağlar, ister metal ister alaşım olsun, güvenilir kaynak çözümleri sağlayabilir. Lazer kaynak işlemi malzeme kalınlığı veya şekli ile sınırlı değildir ve küçük hassas bileşenlerin ve büyük karmaşık yapıların kaynak ihtiyaçlarını kolayca karşılayabilir.
Ayrıca, lazer kaynak, metali plastiğe kaynaklamak veya farklı metal alaşımları arasında kaynak yapmak gibi çeşitli farklı malzeme kombinasyonlarını kaynaklama yeteneğine sahiptir. Bu esneklik, yalnızca kaynak uygulama aralığını artırmakla kalmaz, aynı zamanda üreticilerin aynı üretim hattında farklı malzeme kombinasyonlarını işlemesine olanak tanır ve böylece üretim hattının çok yönlülüğünü ve esnekliğini artırır.
Lazer kaynak teknolojisi, yüksek enerji yoğunluğu, hassas ısı kontrolü, dar ısıdan etkilenen bölge, yüksek verimlilik ve çok yönlülük gibi avantajlarıyla farklı malzemelerin kaynaklanması için ideal bir çözüm sunar. Sadece farklı malzemelerin kaynaklanmasındaki fiziksel ve metalurjik zorlukların etkili bir şekilde üstesinden gelmekle kalmaz, aynı zamanda kaynak kalitesini iyileştirebilir, üretim maliyetlerini düşürebilir ve üretim döngülerini kısaltabilir. Lazer teknolojisinin sürekli ilerlemesiyle farklı malzemelerin kaynaklanması artık teknik bir sorun değil, verimli bir şekilde çözülebilen bir zorluktur. Üreticiler için lazer kaynak teknolojisinin kullanımı üretim verimliliğini ve ürün kalitesini büyük ölçüde iyileştirebilir ve modern üretimin hassasiyet ve çeşitlilik ihtiyaçlarını karşılayabilir.
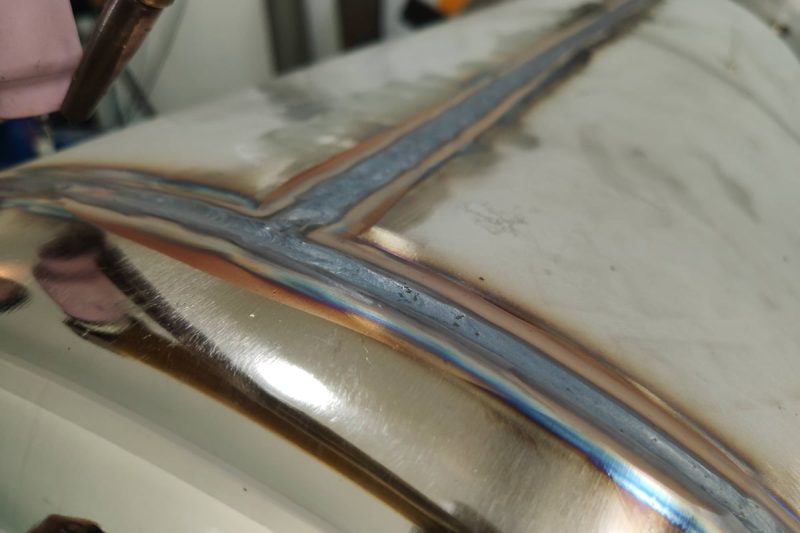
Farklı Malzemelerin Lazer Kaynağı İçin Önemli Hususlar
Lazer kaynağının faydalarını anlamanın yanı sıra, farklı malzemeleri kaynak yaparken dikkate alınması gereken birkaç önemli faktör daha vardır:
Malzeme Eşleşmesi ve Uyumluluğu
Kaynak için farklı malzemeler seçerken, özellikle kimyasal bileşim, erime sıcaklığı ve termal genleşme katsayısı açısından uyumluluk dikkate alınmalıdır. Bu faktörler, kaynağın kararlılığını ve kalitesini doğrudan etkiler.
- Kimyasal bileşim uyumluluğu: Farklı malzemelerin kimyasal bileşimlerindeki farklılıklar, kaynak sırasında istenmeyen bileşiklerin veya oksitlerin oluşmasına yol açabilir ve böylece kaynak kalitesini etkileyebilir. Bu olumsuz reaksiyonlardan kaçınmak için uygun dolgu malzemelerinin seçilmesi gerekir.
- Erime sıcaklığı eşleşmesi: Farklı malzemelerin erime sıcaklıklarındaki farklılıklar, kaynak sırasında eşit olmayan ısı dağılımına yol açabilir ve bu da kaynak etkisini etkiler. Her iki malzemenin de düzgün bir şekilde erimesini sağlamak için kaynak ısı kaynağının sıcaklığını kontrol etmek anahtardır.
- Isıl genleşme katsayısı farkı: Malzemeler arasındaki farklı ısıl genleşme katsayıları kaynak sırasında strese neden olabilir ve çatlak riskini artırabilir. Bu sorun, kaynak tasarımının ve uygun ısıl işlemin optimize edilmesiyle hafifletilebilir.
- Alaşımlı dolgu malzemeleri: Uyumluluğu zor olan malzemeler için alaşımlı dolgu malzemelerinin kullanımı kaynak sonuçlarını iyileştirmeye ve kaynağın mukavemetini ve dayanıklılığını artırmaya yardımcı olabilir.
- Kaynak prosesi seçimi: Lazer kaynak, TIG kaynak vb. gibi uygun bir kaynak prosesi seçmek, malzemeler arasındaki uyumsuzluğu etkili bir şekilde azaltabilir ve istikrarlı bir kaynak prosesi sağlayabilir.
Alaşım dolgu malzemelerinin, kaynak yöntemlerinin rasyonel bir şekilde seçilmesi ve ısı girişinin kontrol edilmesiyle, farklı malzemelerin kaynak stabilitesi ve kalitesi etkili bir şekilde iyileştirilebilir.
Optimum Lazer Parametreleri
Lazer kaynakta, doğru lazer parametrelerini seçmek, özellikle farklı malzemeleri kaynak yaparken kaynak kalitesini garantilemenin anahtarıdır. Aşağıda lazer parametrelerinin kısa bir açılımı verilmiştir:
- Lazer gücü: Lazer gücü, kaynağın derinliğini ve genişliğini doğrudan etkiler. Güç çok düşük olduğunda, yeterli erime derinliği elde edilemeyebilir ve bu da eksik kaynakla sonuçlanabilir; çok yüksek güç ise aşırı ısınmaya, yanmaya veya malzeme deformasyonuna neden olabilir. Farklı malzemelerin farklı termal iletkenliği ve erime sıcaklıkları, kaynak alanında düzgün sıcaklık sağlamak ve kusurları önlemek için lazer gücünün hassas bir şekilde ayarlanmasını gerektirir.
- Darbe frekansı: Darbe frekansı, lazer kaynağının ısıtma ve soğutma oranlarını etkiler. Daha yüksek darbe frekansları daha ince malzemeler için uygunken, daha düşük frekanslar daha kalın malzemeler için uygundur. Birbirine benzemeyen malzemeleri kaynak yaparken, darbe frekansının iki malzemenin ısı iletkenliğindeki farkı dengelemesi gerekir; böylece çok hızlı veya çok yavaş soğutmadan kaynaklanan çatlaklar veya eklem zayıflaması önlenir.
- Tarama hızı: Tarama hızı ısı girişini ve kaynak kalitesini etkiler. Çok hızlı tarama hızı, erimiş havuzun tam olarak kaynaşmamasına neden olarak eksik kaynakla sonuçlanabilir; çok yavaş olması aşırı ısınmaya neden olarak birleştirme bölgesinde çatlaklara veya çok büyük bir ısıdan etkilenen bölgeye neden olabilir. Doğru tarama hızını seçmek, ısının kaynak bölgesinde eşit şekilde dağılmasını sağlayabilir.
- Odak konumu ve nokta boyutu: Lazer odağının konumu, ısı kaynağının konsantrasyonunu belirler ve kaynak doğruluğu ve kalitesini etkiler. Çok yüksek veya çok düşük odak konumları kaynak sonuçlarını etkileyebilir ve aşırı ısınmaya veya eksik erimeye neden olabilir. Odak ve nokta boyutunu doğru şekilde ayarlamak, özellikle farklı malzemeleri kaynak yaparken, malzemenin ışık emilimine ve termal iletkenliğine göre ayarlanması gereken ideal ısı girişini elde etmeye yardımcı olur.
- Isı girişi kontrolü: Kaynak sırasındaki ısı girişi, kaynaklı eklemin kalitesini ve performansını belirler. Aşırı ısı girişi, malzemenin aşırı erimesine neden olarak termal çatlaklara veya deformasyona yol açabilir; çok düşük ısı girişi ise yetersiz kaynakla sonuçlanabilir. Lazer gücü, tarama hızı ve darbe frekansı gibi parametreleri hassas bir şekilde kontrol ederek, kaynak kalitesini garantilemek için ısı girişi optimize edilebilir.
- Kaynak yöntemi seçimi: Farklı kaynak yöntemleri (darbeli lazer kaynağı veya sürekli lazer kaynağı gibi) farklı malzemeler ve uygulamalar için uygundur. Darbeli lazer kaynağı ısı girişini daha iyi kontrol edebilir, aşırı ısınmayı azaltabilir ve ısıya duyarlı farklı malzemelerin kaynağı için uygundur.
Kısacası, lazer kaynak parametrelerinin hassas bir şekilde ayarlanması, kaynak alanında düzgün bir sıcaklık dağılımı sağlayabilir ve özellikle farklı malzemeler kaynaklandığında kaynak kusurlarını önleyebilir. Lazer gücü, darbe frekansı, tarama hızı vb. gibi faktörler ayarlanarak kaynak kalitesi büyük ölçüde iyileştirilebilir ve kaynaklı eklemin mukavemeti ve kararlılığı sağlanabilir.
Dolgu Malzemesi Seçimi
Farklı malzemeleri kaynak yaparken dolgu malzemeleri çok önemlidir. Doğru dolgu malzemesi, kaynaklı eklemin mukavemetini, korozyon direncini ve aşınma direncini artırabilir. Seçim, kaynak malzemesinin bileşimi, erime sıcaklığı ve termal genleşme katsayısı gibi faktörlere dayanmalıdır.
- Kaynak mukavemetini artırın: Uygun dolgu malzemeleri, özellikle farklı malzemelerin kaynaklanması durumunda kaynaklı bağlantıların mukavemetini iyileştirebilir, farklı malzemeler arasındaki mukavemet farklılıklarını dengeleyebilir ve kaynaklı bağlantıların çok kırılgan olmasını önleyebilir.
- Korozyon direncini artırın: Korozyona dayanıklı dolgu malzemelerinin (nikel esaslı alaşımlar, krom alaşımları vb.) seçilmesi, özellikle paslanmaz çelik ve alüminyum alaşımları gibi kaynak malzemeleri için, bağlantıların korozyon direncini artırabilir.
- Aşınma direncini artırın: Sürtünmeye dayanması gereken kaynaklı bağlantılar için, aşınmaya dayanıklı dolgu malzemelerinin (sertleştirilmiş alaşımlar gibi) kullanılması bağlantıların hizmet ömrünü uzatabilir.
- Kaynak malzemesinin bileşimi ve sıcaklığının eşleştirilmesi: Kaynak işlemi sırasında stabiliteyi sağlamak ve uyumsuzluktan kaynaklanan kusurları önlemek için dolgu malzemesinin, ana malzemenin bileşimi ve erime sıcaklığıyla eşleşmesi gerekir.
Özetle, uygun dolgu malzemesinin seçilmesi kaynak kalitesini önemli ölçüde artırabilir ve mekanik, korozyon direnci ve aşınma direnci açısından birleştirmenin performansını garanti altına alabilir.
Benzer olmayan malzemelerin lazerle kaynaklanmasında, malzeme eşleştirmesi ve uyumluluğu, lazer parametrelerinin optimizasyonu ve dolgu malzemelerinin seçimi, kaynak kalitesini ve etkisini sağlamak için temel faktörlerdir. Uyumlu malzeme kombinasyonlarının makul bir şekilde seçilmesi, kaynak işleminin kararlılığını iyileştirebilir ve kaynak kusurlarını önleyebilir; lazer parametrelerinin hassas bir şekilde ayarlanması, aşırı ısınmayı ve zayıf kaynaklamayı önlemek için düzgün ısı dağılımını sağlar; uygun dolgu malzemeleri, kaynaklı eklemin mekanik özelliklerini ve dayanıklılığını artırabilir. Tüm bu faktörler dikkate alındığında, modern üretimin yüksek standartlarını karşılamak için farklı malzemelerin yüksek kaliteli kaynağı elde edilebilir.
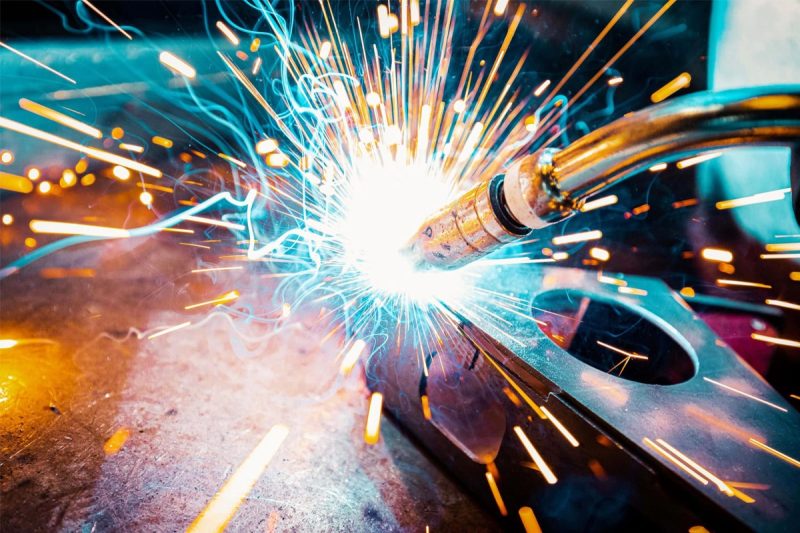
özetle
Benzer olmayan malzemelerin lazerle kaynaklanması, modern üretimdeki kaynak sorunlarını çözmek için etkili bir yoldur. Fiziksel özellik farklılıkları, metalurjik uyumsuzluk ve tasarım sorunları gibi birçok zorluğa rağmen, lazer kaynak, yüksek enerji yoğunluğu, hassas bir şekilde kontrol edilen ısı girişi ve dar ısıdan etkilenen bölge gibi avantajları nedeniyle yüksek kaliteli ve verimli kaynak elde edebilir. Malzemeleri rasyonel bir şekilde seçerek, lazer kaynak parametrelerini optimize ederek ve malzemeleri doldurarak, farklı malzemelerin kaynaklanmasının zorlukları aşılabilir ve kaynaklı yapıların mukavemeti ve güvenilirliği iyileştirilebilir.
Profesyonel lazer kaynak çözümleri arıyorsanız, AccTek Lazer Üretiminizin daha verimli süreç optimizasyonuna ulaşmasına yardımcı olmak için size verimli ve hassas kaynak teknolojisi sağlar. Farklı endüstrilerdeki müşteriler için özelleştirilmiş lazer kaynak ekipmanı sağlıyoruz. Daha fazla ayrıntı için lütfen bizimle iletişime geçin.
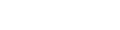
İletişim bilgileri
- [email protected]
- [email protected]
- +86-19963414011
- 3 Bölge A, Lunzhen Sanayi Bölgesi, Yucheng Şehri, Shandong Eyaleti.
Lazer Çözümleri Alın