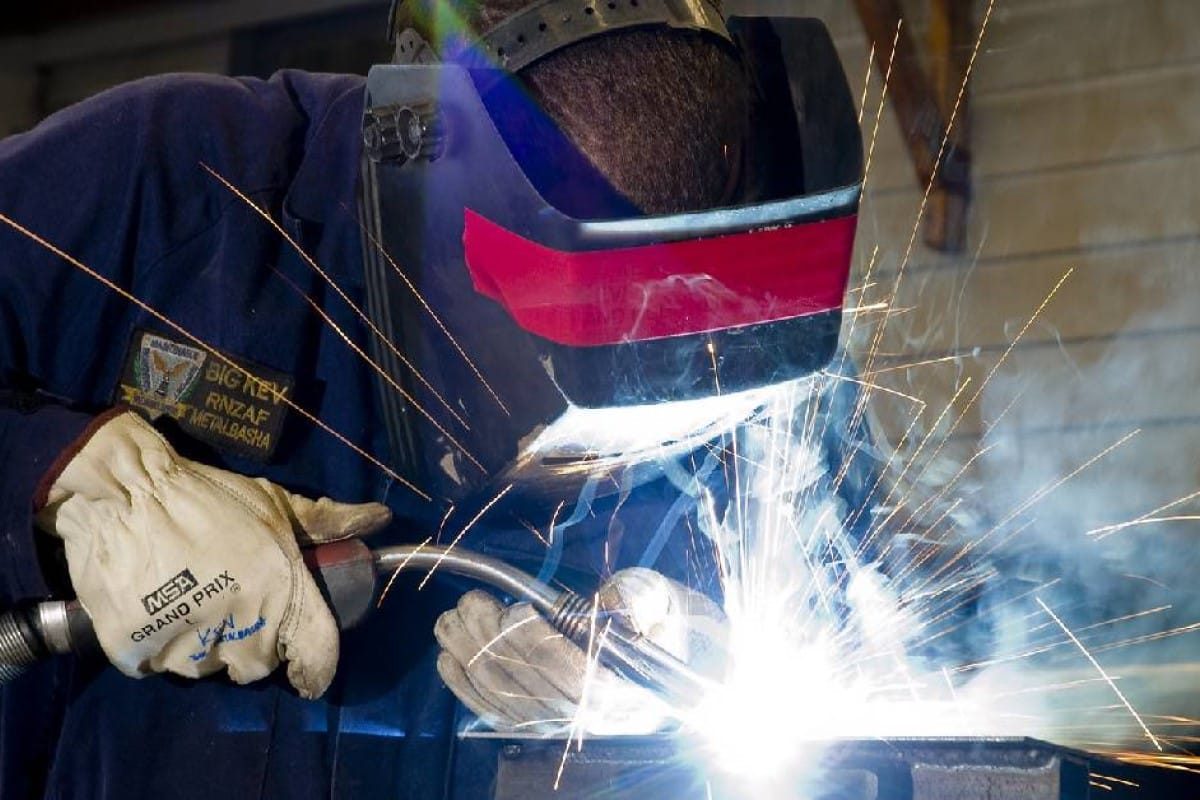
Kaynak Yöntemleri Karşılaştırması: Optimum Performansın Ortaya Çıkarılması
Modern endüstride kaynak, metal parçaları birleştirmek için kullanılan hayati bir işlemdir. Farklı kaynak yöntemleri, çeşitli uygulamalarda önemli bir rol oynar. Kaynak malzemesi, operatör becerisi, kaynak uzunluğu ve boyutu ve kaynak mukavemetini etkileyen diğer faktörlerin yanı sıra kaynak yöntemi de kaynak mukavemetini belirleyen faktörlerden biridir.
Bu makale, lazer kaynağı, tungsten inert gaz kaynağı, metal inert gaz kaynağı, korumalı metal ark kaynağı, tozaltı ark kaynağı ve dirençli nokta kaynağı dahil olmak üzere çeşitli yaygın kaynak yöntemlerini karşılaştıracak, çalışma prensiplerini anlayacak ve hangi kaynak yönteminin en iyi özelliklere sahip olduğunu tartışacaktır. sıradışı performans.
İçindekiler
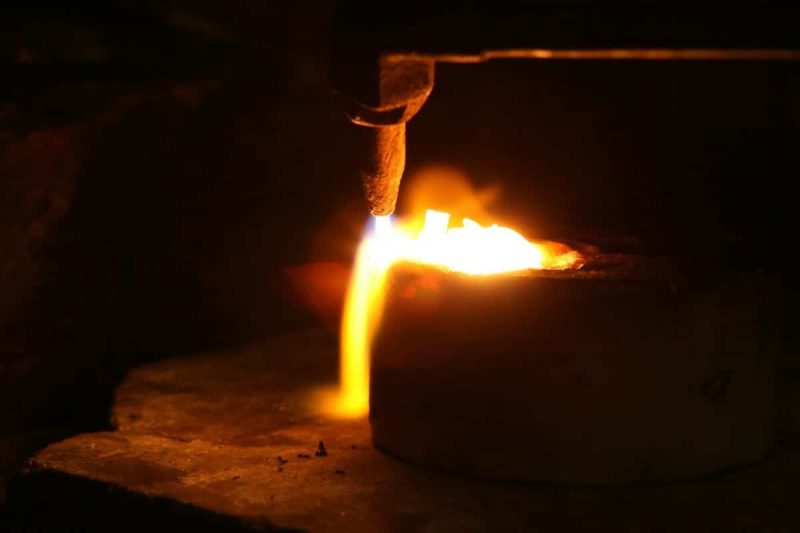
Kaynak uygulamaları nelerdir?
Kaynak, iki veya daha fazla iş parçasının metalinin, soğuduktan sonra güçlü bir bağlantı oluşturacak şekilde ısıtılıp eritildiği bir işlemdir. Bu bağlantı uygulamanın ihtiyaçlarına göre kalıcı veya çıkarılabilir olabilir. Kaynak aşağıdaki şekillerde uygulanabilir:
- Malzemelerin Birleştirilmesi: Kaynak, metalik malzemeleri bir araya getirmenin birincil yöntemidir. Bu tür bağlantı, küçük bileşenlerden büyük endüstriyel bileşenlere kadar çeşitli yapılar oluşturmak için kullanılabilir.
- Güçlendirme ve onarım: Kaynak, malzemeleri güçlendirmek ve hasarlı parçaları veya yapıları onarmak için kullanılabilir. Bu, bakım ve servis ömrünün uzatılması açısından çok önemlidir.
- İmalat: İmalatta kaynak, farklı bileşenlerin eksiksiz bir ürün halinde birleştirilmesinde kritik bir adımdır. Örneğin arabalar, uçaklar, bina yapıları vb. çeşitli parçaların bağlanması için kaynak gerektirir.
- Kişiselleştirme: Kaynak, ürünleri belirli ihtiyaçlara göre uyarlamak için esnek bir yol sunar. Bu, sanat, mimari ve kişiselleştirilmiş üretim dahil olmak üzere çeşitli endüstriler için önemlidir.
- Enerji Endüstrisi: Enerji endüstrisinde, özellikle petrol, gaz ve nükleer enerji sektörlerinde boru, kap ve ekipmanların imalatında ve bakımında kaynak kullanılmaktadır.
- İnovasyon ve Ar-Ge: Yeni kaynak teknolojilerinin araştırılması ve geliştirilmesi aynı zamanda lazer kaynağı, elektron ışın kaynağı vb. gibi yeni ortaya çıkan alanlar için daha gelişmiş ve verimli çözümler sağlar.
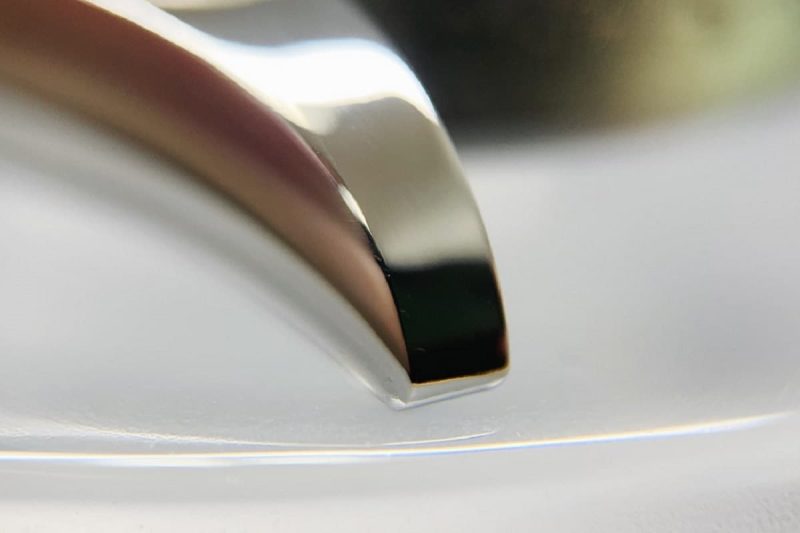
Farklı kaynak türleri nelerdir?
Farklı kaynak türleri, farklı deneyim seviyeleri ve uygulamalar için uygundur. Kaynak deneyiminizi ve kaynak yapmak istediğiniz malzemeleri inceleyerek hangi kaynak türünün sizin için uygun olduğunu belirleyebilirsiniz. Bazı yaygın kaynak türlerini, nasıl çalıştıklarını ve artılarını ve eksilerini bir araya getirdik:
Lazer kaynak
Lazer kaynağı, metali eritmek için yüksek enerjili konsantre ışının kullanıldığı bir kaynak yöntemidir. Lazerin özelliklerine dayanır ve kaynak alanında yüksek sıcaklık oluşturmak için konsantre ışık enerjisi kullanır ve iş parçası yüzeyinin anında erimesine neden olur. Kaynak işlemi sırasında lazer ışınının hareketi veya iş parçasının hareketi kontrol edilerek kaynak üzerinde katman katman erime ve katılaşma tamamlanarak güçlü bir kaynaklı bağlantı oluşturulabilir.
Avantajlar
- Hassasiyet: Lazer kaynağı son derece hassastır ve küçük alanlarda kaynak yapılabilir; bu da onu elektronik cihazlar ve tıbbi ekipman gibi son derece yüksek kaynak kalitesi ve görünüm gerektiren uygulamalar için uygun kılar.
- Hız: Geleneksel kaynak yöntemleriyle karşılaştırıldığında lazer kaynak daha hızlıdır. Lazer ışını hızlı hareket ederek yüksek verimli üretime olanak tanır ve büyük ölçekli, yüksek hacimli üretim için uygundur.
- Küçük termal etki: Lazer kaynağının kaynak alanı çok küçük olduğundan, bitişik alanlardaki termal etki nispeten küçüktür ve deformasyonun ve termal hasarın azaltılmasına yardımcı olur.
- Otomasyon: Lazer kaynağının, yüksek düzeyde otomatikleştirilmiş üretim hatları elde etmek ve üretim verimliliğini artırmak için otomasyon sistemleriyle entegrasyonu kolaydır.
Dezavantajları
- Yüksek ekipman maliyeti; lazer kaynak ekipmanının satın alma ve bakım maliyetleri nispeten yüksektir, bu da bazı uygulamalarda lazer kaynağının yatırım maliyetini daha yüksek hale getirir.
- Malzeme seçimine duyarlı: Lazer kaynağı, malzeme seçimine daha duyarlıdır ve bazı malzemeler lazer kaynağına uygun olmayabilir, bu da uygulama kapsamını sınırlandırır.
- Yüksek çalışma becerisi gereksinimleri: Lazer kaynağı, kaynağın doğruluğunu ve kalitesini sağlamak için yüksek eğitimli çalıştırma becerileri gerektirir ve bu da operatörlere belirli gereksinimler getirir.
- Sınırlı kaynak derinliği: Lazer kaynağının kaynak derinliği nispeten küçük olduğundan, derin kaynak gerektiren bazı uygulamalar için uygun olmayabilir.
Gaz tungsten ark kaynağı
Gaz tungsten ark kaynağı, bir tungsten elektrot tarafından üretilen bir elektrik arkını kullanır. TIG kaynağında elektrot olarak saf tungsten veya tungsten alaşımı kullanılır ve elektrot ile iş parçası arasında bir ark oluşturulur. Kaynak işlemi sırasında, kaynağın kalitesini sağlamak amacıyla oksijen ve diğer yabancı maddelerin girişini önlemek için kaynak alanı dışarıdan sağlanan bir inert gazla (genellikle argon) korunur.
Avantajlar
- Yüksek kaliteli kaynaklar: TIG kaynağıyla üretilen kaynaklar yüksek kalitededir. Kaynak işlemi sırasında gaz koruması, oksijen ve diğer yabancı maddelerin kaynakları etkilemesini etkili bir şekilde önleyebilir, böylece gözenekleri ve kalıntıları azaltabilir.
- Çeşitli malzemeler için uygundur: TIG kaynağı, paslanmaz çelik, alüminyum, bakır vb. dahil olmak üzere çeşitli metallerin kaynağı için uygundur ve malzemelere güçlü bir şekilde uyarlanabilirliğe sahiptir.
- Kaynak işlemi son derece kontrol edilebilir: operatörler, yüksek kaynak kalitesi gereksinimleri olan senaryolar için uygun olan akım, voltaj ve kaynak hızı gibi parametreleri ayarlayarak kaynak işlemini doğru bir şekilde kontrol edebilir.
- Daha az termal deformasyon: TIG kaynağının kaynak ısısı nispeten küçük olduğundan, termal deformasyon olasılığı azalır; bu, özellikle iş parçasının şekli için kesin gerekliliklerin olduğu durumlar için uygundur.
Dezavantajları
- Nispeten yavaş kaynak hızı: Diğer bazı kaynak yöntemleriyle karşılaştırıldığında TIG kaynağı yavaştır, bu da onu yüksek hacimli üretimde diğer yöntemlere göre potansiyel olarak daha az verimli hale getirir.
- Yüksek ekipman ve beceri gereksinimleri: TIG kaynağı yüksek eğitimli beceriler gerektirir, operatörlerin yüksek teknik seviyeye sahip olması gerekir ve ekipman maliyeti nispeten yüksektir.
- Kalın levha kaynağına uygun değildir: Daha kalın iş parçaları için TIG kaynağı daha uzun kaynak süresi gerektirebilir.
- Kaynak akımı sınırlaması: Bazı malzemelerde TIG kaynağının akım sınırlaması yetersiz kaynak derinliğine neden olabilir ve kaynağın gücünü etkileyebilir.
Metal inert gaz kaynağı
Metal inert gaz kaynağı, kaynak işlemi sırasında koruma amacıyla inert gaz kullanan bir kaynak yöntemidir. MIG kaynağında, iş parçasıyla bir ark oluşturmak için kaynak alanına bir kaynak tabancası aracılığıyla metal bir elektrot beslenir. Aynı zamanda oksijen gibi yabancı maddelerin girmesini önlemek için kaynak alanı inert gaz (genellikle argon, helyum veya bunların karışımı) enjekte edilerek korunur.
Avantajlar
- Yüksek verimlilik: MIG kaynağı, seri üretime uygun, yüksek verimli bir kaynak yöntemidir.
- Çeşitli metaller için uygundur: MIG kaynağı, çelik, alüminyum, nikel bakır vb. dahil olmak üzere çeşitli metaller için uygundur ve güçlü malzeme uyarlanabilirliğine sahiptir.
- Daha az kaynak deformasyonu: MIG kaynağının kaynak ısısı nispeten küçük olduğundan kaynak sırasındaki termal deformasyon azalır.
- Kaynak çubuklarını sık sık değiştirmeye gerek yok: Diğer manuel kaynak yöntemleriyle karşılaştırıldığında MIG kaynağı, kaynak çubuklarının sık sık değiştirilmesini gerektirmez, arıza süresini azaltır ve üretim verimliliğini artırır.
Dezavantajları
- Yüksek ekipman maliyetleri: MIG kaynak ekipmanının satın alma ve bakım maliyetleri nispeten yüksektir.
- Rüzgara karşı hassasiyet: Açık havada kaynak yaparken rüzgar, kaynak bölgesindeki gaz korumasını etkileyerek kaynak kalitesinin düşmesine neden olabilir.
- Kısıtlı kaynak yerleri: MIG kaynağı güç ve gaz kaynağı gerektirdiğinden belirli ortam veya yerlerde kaynak yapmak sakıncalı hale gelir.
- Çalıştırma becerisi gereksinimleri: MIG kaynağının çalıştırma becerisi gereksinimleri TIG kaynağına göre daha düşük olmasına rağmen, kaynak kalitesini sağlamak için yine de belirli bir eğitim ve deneyim gereklidir.
Korumalı metal ark kaynağı
Korumalı metal ark kaynağının çalışma prensibi, kaynak tabancası elektrodu ile iş parçası arasında oluşan arkın, elektrot üzerindeki metali eriterek iş parçası üzerinde biriktirerek kaynak oluşturması esasına dayanır. SMAW'da kullanılan elektrot, kaynak için koruyucu bir atmosfer oluşturmak üzere kaynak sırasında gaz üreten, havadaki oksijenin ve diğer yabancı maddelerin kaynağı etkilemesini önleyen bir akı tabakası ile kaplıdır.
Avantajlar
- Geniş uygulanabilirlik: SMAW, karbon çeliği, paslanmaz çelik, alüminyum alaşımı vb. dahil olmak üzere birçok metal türünün kaynaklanması için uygundur ve güçlü çok yönlülüğe sahiptir.
- Harici güç kaynağından bağımsız: SMAW, harici güç kaynağına dayanmayan manuel bir kaynak yöntemi olduğundan tamir bakım işleri gibi güç kaynağı olmayan saha ve ortamlarda daha uygundur.
- Nispeten basit ekipman: SMAW için gereken ekipman yalnızca ark kaynak makinelerini ve elektrotları içerir ve karmaşık kontrol sistemleri gerektirmez, bu da ekipman maliyetlerini azaltır.
- Kalın levha kaynağına uygundur: SMAW daha kalın iş parçaları için uygundur, daha derin kaynaklar üretebilir ve yüksek mukavemet gerektiren kaynak işleri için uygundur.
Dezavantajları
- Yavaş kaynak hızı: Bazı otomatik kaynak yöntemleriyle karşılaştırıldığında SMAW'ın kaynak hızı nispeten yavaştır ve seri üretime uygun değildir.
- Yüksek çalışma becerisi gereksinimleri: SMAW, kaynakçılar için ark kontrolü, kaynak konumu seçimi ve kaynak parametresi ayarı dahil olmak üzere yüksek beceriler gerektirir.
- Isıdan etkilenen daha büyük bölge: Büyük kaynak ısısı nedeniyle SMAW, iş parçasının termal deformasyonunu ve gerilimini artırarak daha büyük bir ısıdan etkilenen bölgeye neden olabilir.
- Elektrotların sık sık değiştirilmesini gerektirir: SMAW kaynağı sırasında elektrotlar kullanım sırasında aşınır ve sık sık değiştirilmeleri gerekir, bu da işlemin karmaşıklığını ve aksama süresini artırır.
Tozaltı ark kaynağı
Tozaltı ark kaynağının çalışma prensibi, arkın kaynak tozunun altına "gömülmesi" için kaynak alanına bir tabaka erimiş kaynak tozu sermektir. Teli ısıtan ve eriten harici bir güç kaynağı tarafından bir kaynak havuzu oluşturan bir ark oluşturulur. Kaynak teli, kaynağın kademeli olarak oluşturulması için sürekli olarak beslenir.
Avantajlar
- Yüksek verimlilik: Tozaltı kaynağı, seri üretime uygun, yüksek verimli bir kaynak yöntemidir. Kaynak teli ve tozunun sürekli olarak tedarik edilmesi, kaynağın nispeten hızlı olmasını sağlar.
- Daha kalın iş parçaları için uygundur: Tozaltı ark kaynağı, daha kalın metal iş parçalarının kaynağı için uygundur ve daha büyük kaynak derinliği, onu yüksek mukavemet gerektiren bazı uygulamalar için uygun hale getirir.
- Kararlı kalite: Tozaltı ark kaynağıyla üretilen kaynakların kalitesi nispeten yüksektir ve daha az gözenek ve cüruf kalıntıları vardır.
- Yüksek derecede otomasyon: Tozaltı ark kaynağı genellikle manuel işlemleri azaltan ve üretim verimliliğini artıran otomatik veya yarı otomatik bir kaynak işlemidir.
Dezavantajları
- Ekipman ve enerji tüketimi: Tozaltı ark kaynağı ekipmanı nispeten karmaşıktır ve büyük güç ve besleme sistemleri gerektirir, dolayısıyla ekipman ve enerji tüketimi nispeten yüksektir.
- Küçük yapılar için uygun değildir: Tozaltı kaynağı ile üretilen kaynak dikişleri büyük olduğundan, küçük yapılar veya kaynak dikişlerinin yüksek görünmesini gerektiren durumlar için uygun değildir.
- Dikey veya baş üstü kaynaklara uygun değildir: Kaynak havuzu yerçekiminden etkilendiğinden, tozaltı ark kaynağı dikey veya baş üstü kaynaklara uygun değildir ve uygulama aralığını sınırlar.
Direnç kaynağı
Direnç kaynağı tipik olarak metal bir iş parçasını, kapalı bir devre oluşturmak üzere harici bir güç kaynağı tarafından çalıştırılan iki elektrot kullanarak kelepçeler. Kapalı bir devrede, direncin neden olduğu ısı, iki metal iş parçası arasındaki temas noktasının ısınmasına neden olur ve sonunda bir lehim bağlantısı oluşturacak şekilde erime sıcaklığına ulaşır. Kaynak süresi kısadır, genellikle milisaniye ile saniye arasındadır ve kaynak noktasının boyutu ve gücü, akım ve basınç ayarlanarak kontrol edilebilir.
Avantajlar
- Hızlı ve verimli: Direnç kaynağının kaynak süresi kısadır ve lehim bağlantısı hızlıdır, bu da onu yüksek hacimli üretim ortamları için uygun kılar.
- İnce levhalar için uygundur: Direnç kaynağı, kaynak işlemi sırasında oluşan ısının nispeten küçük olması ve kolayca deformasyona neden olmaması nedeniyle ince levhaların kaynağı için uygundur.
- Harici dolgu malzemesi gerekmez: Direnç kaynağı, kaynak metalin kendisinin erimesi ile oluştuğundan ek kaynak malzemesi gerektirmez.
- Kaynak sonrası işleme gerek yoktur: Kısa kaynak süresi ve küçük termal etki nedeniyle genellikle kaynak sonrası işleme gerek kalmaz, bu da üretim sürecini azaltır.
Dezavantajları
- Yalnızca iletken metaller için uygundur: Direnç kaynağı esas olarak metalin iletkenliğine dayanır, dolayısıyla iletken olmayan metaller veya alaşımlar için belirli sınırlamalarla birlikte yalnızca iletken metaller için uygundur.
- Lehim bağlantısının şekli sınırlıdır: Kaynak sırasında metal, elektrotun kelepçeli kısmında ısıtılıp eritildiğinden, lehim bağlantısının şekli nispeten sınırlıdır, genellikle yuvarlak veya ovaldir.
- Karmaşık şekiller için uygun değildir: Direnç kaynağının iş parçasının şekli açısından daha yüksek gereksinimleri vardır ve karmaşık veya düzensiz şekilli iş parçaları için uygun değildir.
- Lehim bağlantılarının mukavemeti malzemelerden etkilenir: Lehim bağlantılarının mukavemeti metal malzemelerin özelliklerinden etkilenir. Bazı yüksek mukavemetli ve yüksek sertlikteki metallerin ideal kaynak sonuçlarına ulaşması zor olabilir.
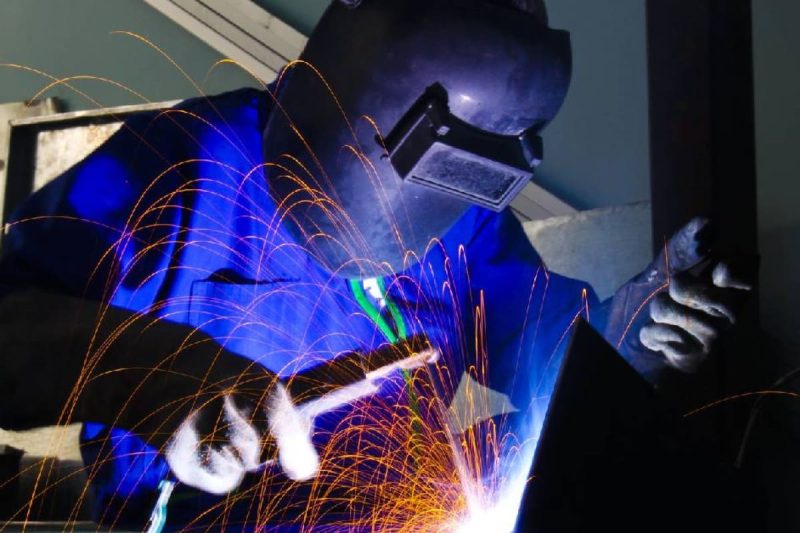
En güçlü kaynak türü hangisidir?
Lazer kaynağı, tungsten inert gaz kaynağı, metal inert gaz kaynağı, korumalı metal ark kaynağı, tozaltı ark kaynağı ve direnç kaynağı arasında hangi kaynak yöntemi daha güçlüdür? Bu kaynak yöntemleri, özelliklerini ve uygulamalarını daha iyi anlamak için aşağıda karşılaştırılacaktır.
Lazer kaynak
Lazer kaynak Yüksek hassasiyetli ve yüksek verimli bir kaynak yöntemidir. Avantajları arasında küçük kaynaklar, düşük termal etki ve çeşitli malzemelere uygunluk sayılabilir. Lazer kaynağı, elektronik cihazlar, tıbbi ekipman vb. gibi hassas üretim ve zorlu uygulamalar için çok etkilidir.
Tungsten inert gaz kaynağı (TIG kaynağı)
TIG kaynağı, yüksek kaliteli kaynakları ve hassas kontrolüyle bilinir. Özellikle paslanmaz çelik ve alüminyumun kaynaklanması gibi zorlu uygulamalarda, çeşitli metaller için uygundur. TIG kaynağının dezavantajları arasında yüksek operasyonel beceri gereksinimleri ve nispeten yavaş hız yer alır.
Metal İnert Gaz Kaynağı (MIG Kaynağı)
MIG kaynağı seri üretime uygun, verimli bir yöntemdir. Avantajı, hızlı kaynak hızına sahip olması, çeşitli metallere uygun olması ve kaynak çubuklarının sık sık değiştirilmesini gerektirmemesidir. Ancak MIG kaynağının ekipman ve çevre açısından yüksek gereksinimleri vardır ve her çalışma koşuluna uygun değildir.
Korumalı Metal Ark Kaynağı (SMAW)
SMAW, çeşitli metallere uygun ve çok yönlülüğe sahip geleneksel bir manuel kaynak yöntemidir. Avantajı, harici bir güç kaynağına bağımlı olmaması ve saha bakımı ve diğer ortamlar için uygun olmasıdır. Ancak SMAW'ın kaynak hızı daha yavaştır ve yüksek çalışma becerileri gerektirir, bu da onu küçük seri üretim ve onarım çalışmaları için uygun kılar.
Tozaltı ark kaynağı (SAW)
Tozaltı ark kaynağı, seri üretime uygun, yüksek mukavemet gerektiren uygulamalarda öne çıkan otomatik bir kaynak yöntemidir. Ancak ekipman ve enerji tüketimi nispeten yüksektir.
Direnç kaynağı
Direnç kaynağı, kaynak noktalarına odaklanan, ince sacların ve küçük bileşenlerin birleştirilmesi için uygun bir yöntemdir. Avantajı hızlı ve verimli olması, ancak metal iletkenliği açısından yüksek gereksinimlere sahip olması ve lehim bağlantısının şeklinin nispeten sınırlı olmasıdır.
özetle
Yukarıdaki kaynak yöntemlerinin avantaj ve dezavantajları göz önüne alındığında hangi kaynak yönteminin en güçlü olduğunu belirlemek zordur. Farklı uygulama senaryoları farklı kaynak yöntemleri gerektirir. Lazer kaynağı yüksek hassasiyetli ve kaliteli uygulamalara, MIG kaynağı ise yüksek hacimli üretime uygundur. TIG ve SMAW gibi manuel kaynak yöntemleri, küçük ölçekli üretimde ve yüksek derecede teknik kontrol gerektiren alanlarda öne çıkarken, tozaltı ark kaynağının büyük ölçekli yapısal imalatta yeri vardır.
Bir kaynak yöntemi seçerken üretim gereksinimleri, malzeme türü, maliyet ve verimlilik gibi dikkate alınması gereken çeşitli faktörler vardır. Çeşitli kaynak teknolojilerinin kapsamlı kullanımı ve özel ihtiyaçlara göre esnek seçim, farklı projelerin gereksinimlerini daha iyi karşılayabilir ve kaynak prosesinin istikrarlı, verimli ve kalite kontrollü olmasını sağlayabilir. Lazer kaynak yapmayı düşünüyorsanız lütfen iletişime geçiniz. AccTek Lazer ve ihtiyaçlarınız için en iyi seçeneği bulacağız.
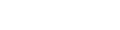
İletişim bilgileri
- [email protected]
- [email protected]
- +86-19963414011
- 3 Bölge A, Lunzhen Sanayi Bölgesi, Yucheng Şehri, Shandong Eyaleti.
Lazer Çözümleri Alın