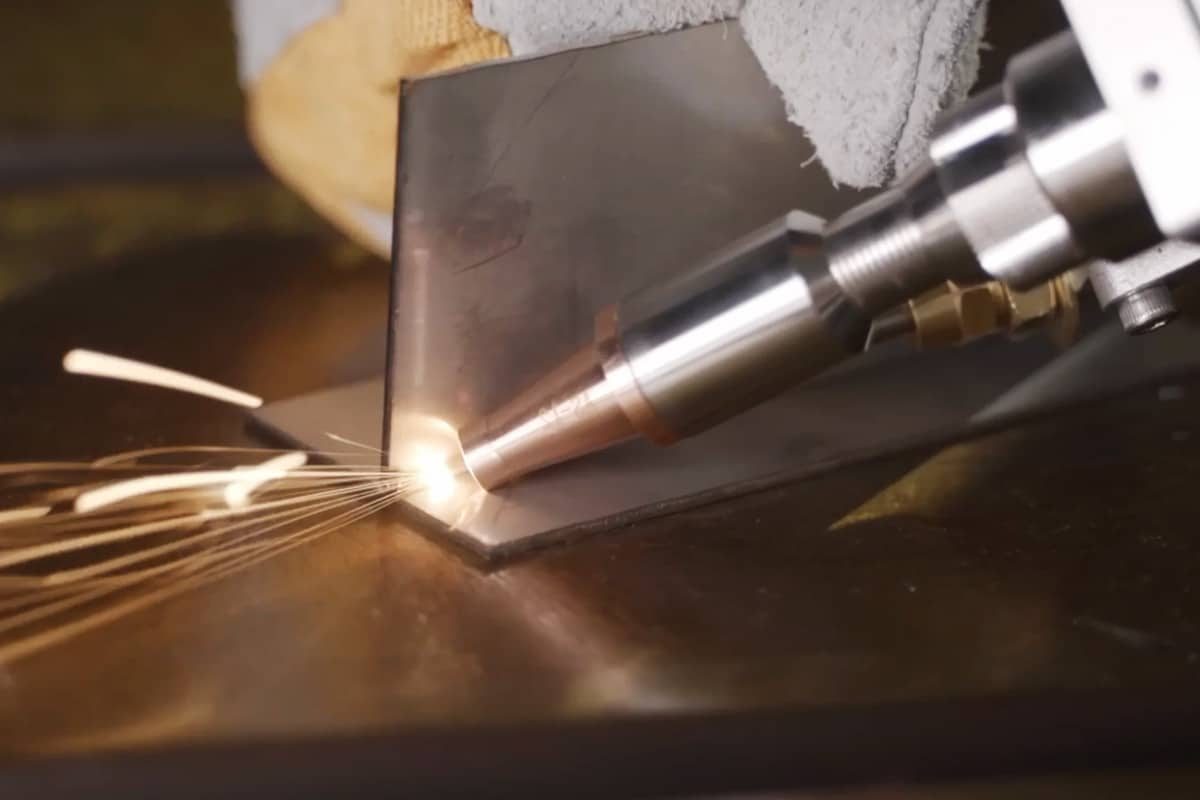
Lazer Kaynaklı Bağlantı Tasarımı
Lazer kaynak, yüksek hassasiyeti, düşük ısı girişi ve yüksek verimliliği nedeniyle havacılık, otomotiv üretimi, elektronik ekipman, tıbbi ekipman ve diğer endüstrilerde yaygın olarak kullanılmaktadır. Geleneksel kaynak yöntemleriyle karşılaştırıldığında, lazer kaynak dar kaynak, hızlı kaynak hızı, küçük ısıdan etkilenen bölge ve düşük deformasyon avantajlarına sahiptir ve bu da onu yüksek talep gören üretim alanları için ideal bir seçim haline getirir. Bununla birlikte, lazer kaynaklamanın birçok avantajına rağmen, kaynak kalitesinin istikrarı ve nihai ürünün güvenilirliği hala büyük ölçüde kaynaklı bağlantının tasarımına bağlıdır. Makul bağlantı tasarımı, kaynağın bütünlüğünü ve mekanik mukavemetini sağlayabilir ve kaynak işlemi sırasında oluşabilecek çatlaklar, gözenekler ve kaynak penetrasyonu gibi kusurları azaltabilir, enerji girişini optimize ederken, üretim verimliliğini artırırken ve yeniden işleme oranını ve üretim maliyetlerini azaltır.
Lazer kaynak uygulamalarında, birleştirme tasarımının alt tabakanın metalurjik özellikleri, kaynak yöntemi, lazer gücü, kaynak şekli, montaj doğruluğu ve sonraki işleme gereksinimleri dahil olmak üzere birden fazla faktörü göz önünde bulundurması gerekir. Mükemmel bir birleştirme tasarımı, yüksek kaliteli, düşük maliyetli kaynak sonuçları elde etmek için lazer kaynak avantajlarından tam olarak yararlanabilir. Bu makale, şirketlerin ve mühendislerin kaynak kalitesini iyileştirmelerine, üretim süreçlerini optimize etmelerine ve pratik uygulamalarda kaynaklı yapıların hizmet ömrünü uzatmalarına yardımcı olmak için lazer kaynak birleştirme tasarımının temel prensiplerini, etkileyen faktörleri ve optimizasyon stratejilerini derinlemesine inceleyecektir.
İçindekiler
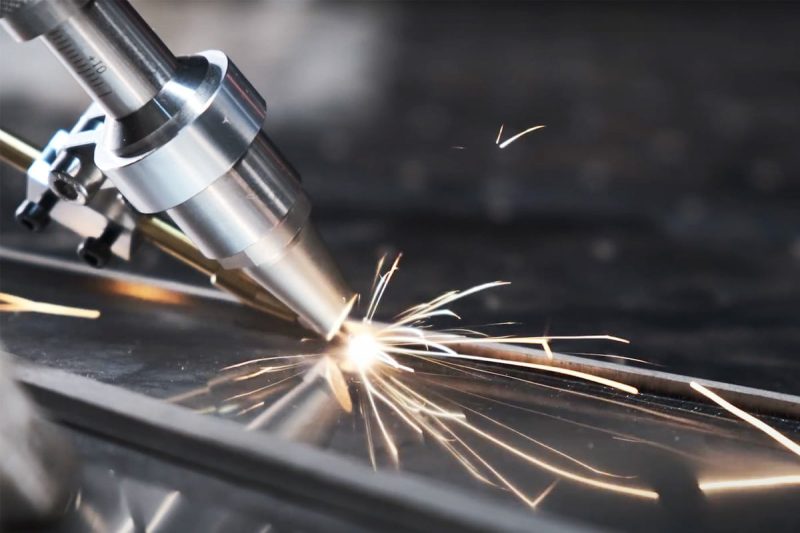
Lazer kaynak birleştirme tasarımının temel prensipleri
Yüksek hassasiyetli ve yüksek verimli bir kaynak işlemi olarak lazer kaynak, otomotiv üretimi, havacılık, elektronik ekipman ve tıbbi cihazlar gibi endüstrilerde yaygın olarak kullanılır. Makul kaynak birleştirme tasarımı, kaynağın bütünlüğü, dayanıklılığı ve üretim verimliliği için çok önemlidir. Optimize edilmiş birleştirme tasarımı yalnızca kaynak kusurlarını azaltmakla ve kaynak kalitesini iyileştirmekle kalmaz, aynı zamanda üretim maliyetlerini düşürebilir ve genel üretim verimliliğini de artırabilir. Bu makale, lazer kaynak birleştirmelerinin temel bileşenlerini ve kaynak kalitesini optimize etmedeki rollerini ele alacak ve bilimsel tasarım yoluyla verimli ve istikrarlı kaynak sonuçlarının nasıl elde edileceğini analiz edecektir.
Lazer kaynaklı bağlantıların temel bileşenleri
Alt tabaka
Temel malzemenin seçimi doğrudan kaynak kalitesini ve nihai ürünün performansını etkiler. Kaynak malzemelerini seçerken dikkate alınması gereken birkaç önemli faktör vardır:
- Mekanik özellikler: Malzemenin mukavemeti, sertliği, sünekliği ve diğer özellikleri kaynaklı bağlantının stabilitesini etkileyecektir.
- Metalurjik özellikler: Kaynağın güvenilirliğini sağlamak için alaşım bileşimi, uyumluluk ve malzemenin kaynak sonrası mikro yapı değişiklikleri dahildir.
- Isıl iletkenlik ve erime sıcaklığı: lazer enerjisinin emilimini ve transferini etkiler. Yüksek ısıl iletkenliğe sahip malzemeler (bakır gibi) daha yüksek güçte bir lazer jeneratörü gerektirebilirken, düşük ısıl iletkenliğe sahip malzemeler (titanyum gibi) aşırı ısınmadan kaynaklanan yapısal hasardan kaçınmalıdır.
Bağlayıcı Yapılandırması
Farklı kaynak ihtiyaçları için farklı tipte birleştirme yapılandırmaları uygundur. Yaygın birleştirme tipleri şunları içerir:
- Uç Bağlantısı: Yüksek mukavemetli kaynak uygulamaları için uygundur, mükemmel kaynak performansına sahiptir ancak yüksek işleme hassasiyeti gerektirir.
- Bindirme Bağlantısı: İnce sac kaynakları için uygundur, basit bir işlemdir ve hızlı kaynak hızına sahiptir, ancak gerilim yoğunlaşmasının azaltılmasına dikkat edilmelidir.
- T Bağlantı: Genellikle yapısal kaynakta kullanılır, güçlü kaynak taşıma kapasitesine sahiptir, ancak kaynak kusurlarını önlemek için yeterli penetrasyonun sağlanması gerekir.
Ayrıca kaynak işlemi sırasında boşluk boyutu, montaj doğruluğu ve birleştirmenin hizalanması doğrudan kaynak kalitesini etkileyecektir. Bu parametrelerin optimize edilmesi kaynak deformasyonunu azaltabilir ve birleştirme mukavemetini iyileştirebilir.
Dolgu malzemesi
Bazı lazer kaynak uygulamalarında, kaynak kalitesini optimize etmek için dolgu malzemeleri kullanılabilir. Başlıca etkiler şunlardır:
- Kaynak mukavemetini arttırır, kaynak çatlaklarını önler ve kaynağın mekanik özelliklerini iyileştirir.
- Alaşım bileşimini optimize ederek metalurjik özellikleri ayarlayın ve kaynak yapısını iyileştirin.
- Gözenek ve füzyon eksikliği gibi kaynak kusurlarını azaltır ve kaynak stabilitesini artırır.
Dolgu malzemesinin seçimi, ana malzemenin özelliklerine uygun olmalı ve kaynak işlemi ile birlikte makul bir şekilde ayarlanmalıdır.
Lazer kaynaklı bağlantıların temel bileşenleri
Optimize edilmiş kaynak birleştirme tasarımının aşağıdaki hedefleri aynı anda karşılaması gerekir:
- Kaynak bütünlüğünü ve mukavemetini sağlayın: Kaynak bölgesinde iyi bir füzyon ve yeterli mekanik mukavemeti sağlamak için birleştirme yapısını akılcı bir şekilde tasarlayın.
- Kaynak hatalarını azaltın: Malzeme seçimini, birleştirme yapısını ve kaynak sürecini optimize ederek gözenekler, çatlaklar ve füzyon eksikliği gibi yaygın sorunları azaltın.
- Proses verimliliğini ve üretkenliğini optimize edin: Kaynak hızını artırmak, malzeme israfını azaltmak ve işleme maliyetlerini düşürmek için makul birleşim konfigürasyonu tasarlayın, böylece genel üretim verimliliğini iyileştirin.
Lazer kaynak bağlantılarının tasarımı, kaynak kalitesi ve üretim verimliliği açısından hayati önem taşır. Temel malzemeyi rasyonel bir şekilde seçerek, bağlantı yapısını ve dolgu malzemelerini optimize ederek ve kaynak sürecini ince ayarlayarak kaynak kalitesi etkili bir şekilde iyileştirilebilir, kusurlar azaltılabilir ve üretim verimliliği artırılabilir. Bilimsel bağlantı tasarımı yalnızca kaynağın mukavemetini ve kararlılığını sağlamakla kalmaz, aynı zamanda üretim sürecini de optimize ederek şirketlerin yüksek hassasiyetli üretim alanında rekabet güçlerini korumalarına yardımcı olur.
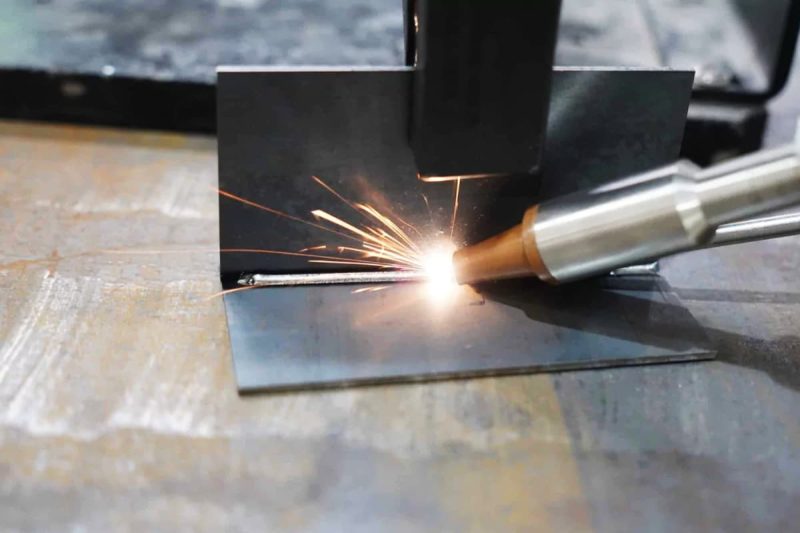
Lazer Kaynak Eklem Tasarımını Etkileyen Faktörler
Lazer kaynak bağlantılarının tasarımı yalnızca temel yapıların seçimini içermez, aynı zamanda malzeme özellikleri, bağlantı konfigürasyonu, kaynak parametreleri ve uygulama gereksinimleri gibi birden fazla faktörden de etkilenir. Bu faktörlerin uygun şekilde dikkate alınması kaynak kalitesinin optimize edilmesine, kaynak mukavemetinin iyileştirilmesine, kusurların azaltılmasına ve üretim verimliliğinin iyileştirilmesine yardımcı olabilir.
Malzeme özellikleri
Alt tabakanın fiziksel ve kimyasal özellikleri, lazer kaynaklı bağlantıların performansında hayati bir rol oynar. Kaynaklı bağlantıları tasarlarken, aşağıdaki temel hususlara odaklanmak önemlidir:
- Alt tabakanın uyumluluğu: Farklı metal malzemelerin kaynak uyumluluğu, kaynak kalitesini belirler. Örneğin, benzer bileşimdeki alaşımlar genellikle iyi füzyon özelliklerine sahipken, farklı termal genleşme katsayıları veya kırılgan intermetalik bileşiklerin oluşumu nedeniyle farklı metal kaynakları çatlaklara veya kaynak kusurlarına neden olabilir.
- Mekanik ve metalurjik özellikler: Mekanik özellikler (sertlik, süneklik ve çekme dayanımı gibi) kaynak güvenilirliğini etkiler. Metalurjik özellikler kaynak sırasında alaşım elementlerindeki değişiklikleri belirler. Örneğin, bazı yüksek karbonlu çelikler kaynak sırasında sertleştirilmiş yapılar üretebilir ve bu da çatlak riskini artırabilir. Bu nedenle, kaynak kalitesini sağlamak için kaynak işlemi parametrelerinin farklı malzeme özelliklerine göre ayarlanması gerekir.
- Isıl iletkenlik ve erime sıcaklığı: Malzemenin ısıl iletkenliği ve erime noktası, lazer enerjisinin iletimini ve emilimini etkiler. Örneğin, yüksek ısıl iletkenliğe sahip metaller (örneğin bakır Ve alüminyum) ısıyı hızla dağıtır ve daha yüksek lazer gücü veya daha yoğun enerji girişi gerektirir. Daha yüksek erime noktalarına sahip malzemeler, yeterli erime ve birleştirme mukavemetini sağlamak için daha fazla kaynak enerjisi gerektirebilir.
Bağlayıcı Yapılandırması
Eklemin türü, montaj doğruluğu ve hizalanması, kaynak işleminin kararlılığını ve kaynak kalitesini doğrudan etkiler. Yaygın eklem türleri şunlardır:
- Uç Bağlantısı: Yüksek mukavemet ve düşük deformasyon gerektiren kaynak senaryoları için uygundur. Uç bağlantı boşluğunun, tam füzyonu sağlamak ve eksik füzyon veya cüruf kapanımı gibi kusurları önlemek için sıkı bir şekilde kontrol edilmesi gerekir.
- Bindirme Eklemi: İnce levha kaynakları için uygundur, kaynağın üst üste binen kısmı daha iyi mukavemet sağlayabilir. Ancak, istifleme etkisi nedeniyle boşlukta gaz kalabilir ve gözenekliliği azaltmak için kaynak parametrelerinin optimize edilmesi gerekir.
- T-Eklem: Genellikle daha fazla gerilime maruz kalan yapısal parçalar için kullanılır. T-eklemlerinin kaynaklanması, gerilim yoğunlaşmasının neden olduğu çatlamaları önlemek için yeterli penetrasyon sağlamalıdır.
Ayrıca kaynaklı birleştirmelerin tasarımında aşağıdaki hususların da dikkate alınması gerekmektedir:
- Montaj ve boşluk boyutu: Çok büyük bir boşluk yetersiz kaynak dolgusuna neden olabilirken, çok küçük bir boşluk eksik füzyona veya kaynak deformasyonuna neden olabilir. Bu nedenle, doğru montaj ve boşluk kontrolü kaynak kalitesi için kritik öneme sahiptir.
- Lazer ışını iletimi ve parça işleme kanalı: Lazer ışınının kaynak alanına sorunsuz bir şekilde ulaşabildiğinden emin olun, böylece ışın tıkanıklığı veya yansıması nedeniyle kaynak etkisi etkilenmez. Aynı zamanda, otomatik üretim hattında, parça sabitleme yöntemi ve kaynak kanalının tasarımı da kaynak stabilitesi ve tutarlılığını sağlamak için optimize edilmelidir.
Kaynak parametreleri
Kaynak parametrelerinin makul bir şekilde ayarlanması kaynak kalitesini optimize edebilir ve kaynak kusurlarını azaltabilir. Ortak anahtar parametreler şunlardır:
- Lazer gücü: kaynak derinliğini ve erimiş havuz oluşumunu etkiler. Yüksek güç derin penetrasyonlu kaynak için uygundur, düşük güç ise hassas kaynak için uygundur.
- Odak konumu ve ışın çapı: Odaklanmanın doğru kontrolü enerji yoğunluğunu ve kaynak derinliğini etkiler. Daha küçük ışın çapları yüksek hassasiyetli kaynak için uygundur, daha büyük ışınlar ise geniş kaynak gereksinimleri için kullanılabilir.
- Kaynak hızı ve hareket yönü: Çok hızlı kaynak hızı yetersiz penetrasyona yol açabilir ve kaynak mukavemetini etkileyebilirken, çok yavaş kaynak deformasyonuna veya ısıdan etkilenen bölgenin (HAZ) genişlemesine neden olabilir. Bu nedenle, kaynak hızının malzeme ve bağlantı yapısıyla birlikte ayarlanması gerekir.
- Koruyucu gaz ve atmosfer kontrolü: Uygun koruyucu gaz (argon, nitrojen veya karışık gaz gibi) kaynak sırasında oksidasyonu azaltabilir ve kaynak kalitesini optimize edebilir. Farklı malzemelerin gaz için farklı gereksinimleri vardır. Örneğin, titanyum alaşımlarının oksijenden tamamen izole edilmesi gerekirken, paslanmaz çelik Kaynak sırasında renk bozulmasını ve oksidasyonu azaltmak için argonla korunabilir.
Uygulama Gereksinimleri
Malzeme ve proses faktörlerine ek olarak, kaynak bağlantı tasarımı ayrıca aşağıdakiler de dahil olmak üzere belirli uygulama senaryolarının ihtiyaçlarını da karşılamalıdır:
- İşlevsel ve yapısal gereksinimler: Ürünün son kullanımına göre uygun birleştirme tipini ve kaynak yapısını seçin. Örneğin, otomotiv endüstrisindeki lazer kaynak genellikle yüksek mukavemet ve hafiflik gerektirirken, elektronik ekipman kaynak işlemi rafinelik ve ısıdan etkilenen bölge kontrolünü vurgular.
- Yüzey kalitesi ve görünüm: Tüketici elektroniği veya tıbbi cihazlar gibi bazı uygulamalarda, kaynağın estetiği kritik öneme sahiptir. Bu, kaynak parametrelerinin optimize edilmesini, kaynak sıçramasının ve cürufun azaltılmasını ve yüzey kalitesinin iyileştirilmesini gerektirir.
- Kaynak sonrası işleme ve ikincil işleme: Bazı kaynak işlemleri, nihai ürünün kalite standartlarını karşılamak için taşlama, ısıl işlem veya kaplama gibi ek son işlemeler gerektirebilir. Bu nedenle, kaynak bağlantıları tasarlanırken, sonraki işlemlerin uygulanabilirliği ve maliyeti de dikkate alınmalıdır.
Lazer kaynak bağlantılarının tasarımı, alt tabakanın özellikleri, bağlantı konfigürasyonu, kaynak parametreleri ve nihai uygulama gereksinimleri dahil olmak üzere birçok faktörden etkilenir. Malzemeleri rasyonel bir şekilde seçerek, bağlantı yapısını optimize ederek, kaynak işlemi parametrelerini doğru bir şekilde kontrol ederek ve belirli uygulama gereksinimlerine göre ayarlayarak, kaynak kalitesi etkili bir şekilde iyileştirilebilir, kusurlar azaltılabilir ve üretim verimliliği artırılabilir. Bilimsel ve makul bağlantı tasarımı yalnızca kaynağın mukavemetini ve kararlılığını sağlamakla kalmaz, aynı zamanda üretim sürecini de optimize ederek ürün kalitesini garanti ederken üretim rekabet gücünü artırır.
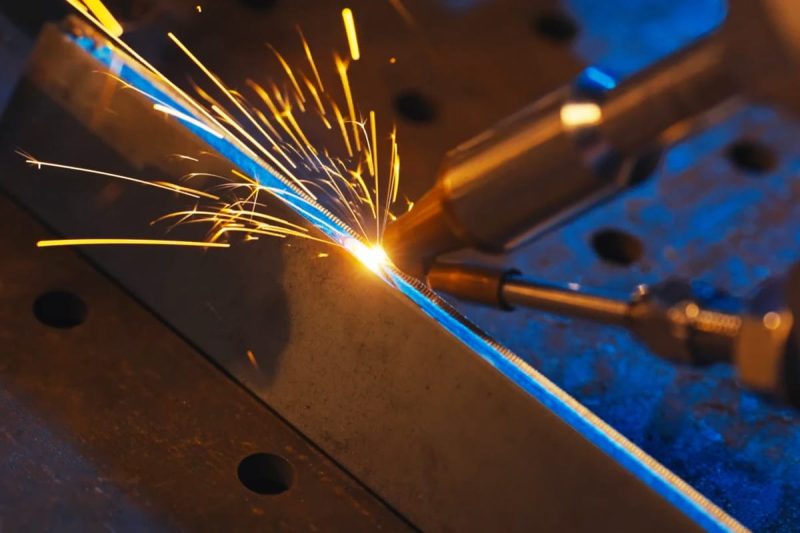
Lazer kaynak birleştirme tasarımı için optimizasyon stratejisi
Lazer kaynak birleştirme tasarımını optimize etmenin amacı kaynak kalitesini iyileştirmek, kaynağın bütünlüğünü ve dayanıklılığını sağlamak, kusurları azaltmak ve üretim verimliliğini artırmaktır. Ana optimizasyon stratejileri aşağıdaki hususları içerir:
Isıdan etkilenen bölgeyi (HAZ) en aza indirin
Büyük bir ısıdan etkilenen bölge (HAZ), malzeme özelliklerini etkileyebilir ve hatta kaynak gevrekliğine neden olabilir. Lazer gücünü, kaynak hızını ve ışın odağını optimize ederek, ısı girişi ısıdan etkilenen bölgeyi azaltmak için etkili bir şekilde kontrol edilebilir. Ayrıca, uç birleştirme veya bindirme birleştirme gibi makul bir birleştirme türü seçimi de ısı birikimini azaltmaya ve kaynak stabilitesini iyileştirmeye yardımcı olabilir.
Kaynak mukavemetini artırın
Kaynaklı bağlantıların mukavemetini sağlamanın anahtarı, ısı dağılımını optimize etmek, boşluk boyutunu kontrol etmek ve iş parçalarını doğru bir şekilde hizalamaktan geçer. Uygun bir kaynak işlemi, gerilim yoğunluğunu azaltabilir ve füzyon eksikliği gibi sorunları önleyebilir. Bazı uygulamalarda, eşleşen dolgu malzemelerinin kullanımı, kaynağın bağını artırabilir ve bağlantının genel mukavemetini ve dayanıklılığını iyileştirebilir.
Kaynak kalitesini garantileyin
Kaynak kalitesi, lazer gücü, odak konumu, kaynak hızı ve koruyucu gaz kullanımı gibi birçok faktörden etkilenir. Bu parametrelerin makul bir şekilde ayarlanması gözenekler ve çatlaklar gibi kusurları azaltabilir. Ayrıca, kalite denetimi için çevrimiçi izleme teknolojisinin kullanılması, kaynağın tutarlılığını sağlayabilir ve ürün yeterlilik oranını iyileştirebilir.
Lazer kaynak bağlantılarının tasarımının optimize edilmesi, kaynak kalitesini ve üretim verimliliğini artırmanın önemli bir yoludur. Isıdan etkilenen bölgeyi azaltarak, kaynak mukavemetini artırarak ve kaynak kalitesini sıkı bir şekilde kontrol ederek, kaynak etkisi endüstriyel üretimin yüksek standartlarını karşılayacak şekilde etkili bir şekilde iyileştirilebilir.
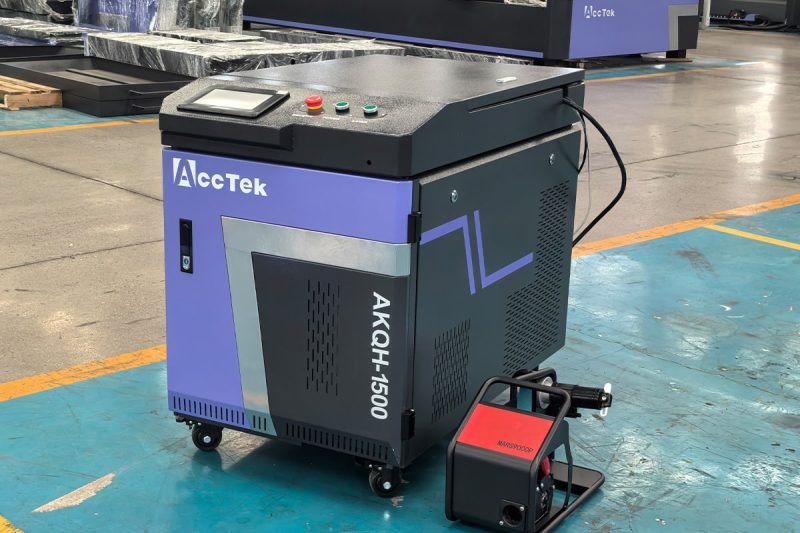
özetle
Lazer kaynak birleştirme tasarımı, kaynak kalitesini ve üretim verimliliğini belirlemede önemli bir faktördür. Birleştirme tasarımının temel prensiplerini, etki eden faktörleri ve optimizasyon stratejilerini derinlemesine anlayarak, üreticiler kaynağın bütünlüğünü sağlayabilir, kusurları azaltabilir ve genel kaynak kalitesini iyileştirebilir. Makul birleştirme tasarımı yalnızca kaynak mukavemetini iyileştirmekle kalmaz, aynı zamanda farklı uygulama senaryolarının ihtiyaçlarını karşılamak için üretim sürecini de optimize edebilir.
Verimli ve hassas lazer kaynak çözümleri arıyorsanız, AccTek Lazer gelişmiş teklifler lazer kaynak makinesiEn yüksek kalite ve verimlilik standartlarını karşılayan ekipmanlar. Ekipmanlarımız, üretim hedeflerinize ulaşmanıza yardımcı olmak için kaynak stabilitesi ve tutarlılığını sağlamak amacıyla gelişmiş lazer teknolojisini kullanır. Bize Ulaşın Ürünlerimizin kaynak sürecinizi optimize etmenize nasıl yardımcı olabileceği hakkında daha fazla bilgi edinmek için!
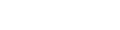
İletişim bilgileri
- [email protected]
- [email protected]
- +86-19963414011
- 3 Bölge A, Lunzhen Sanayi Bölgesi, Yucheng Şehri, Shandong Eyaleti.
Lazer Çözümleri Alın