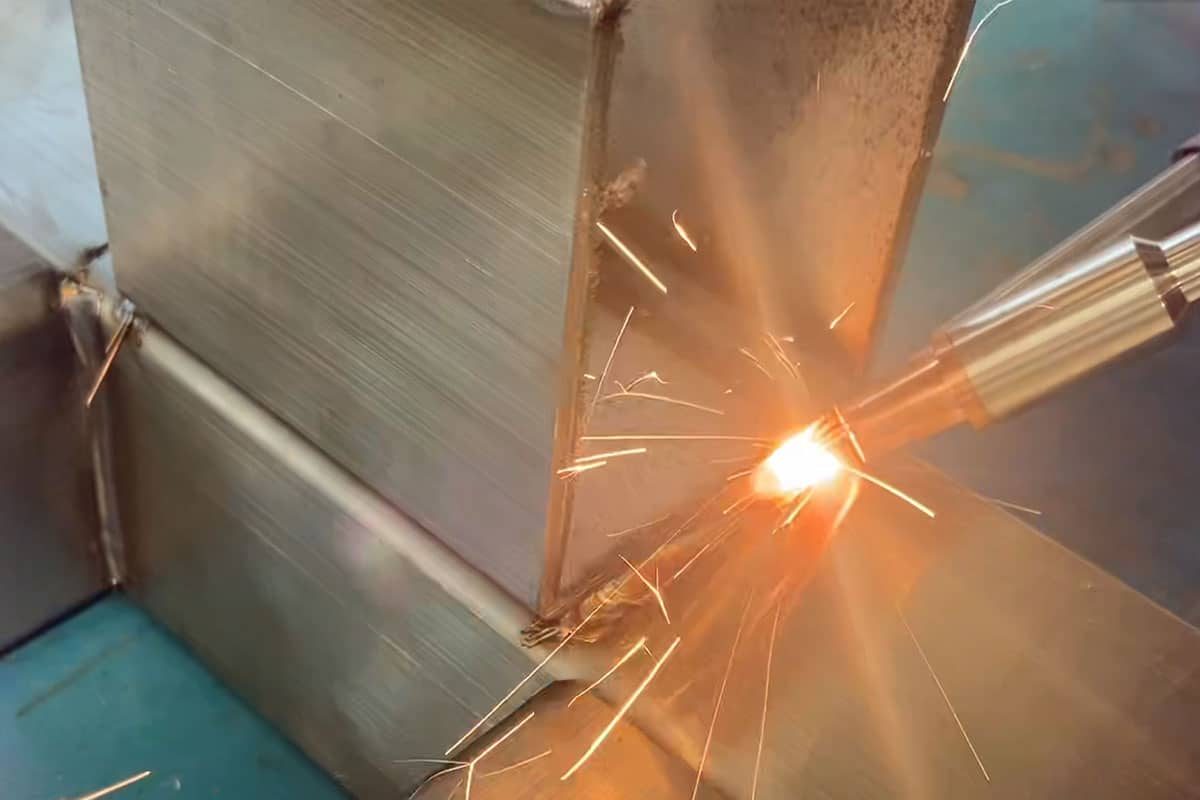
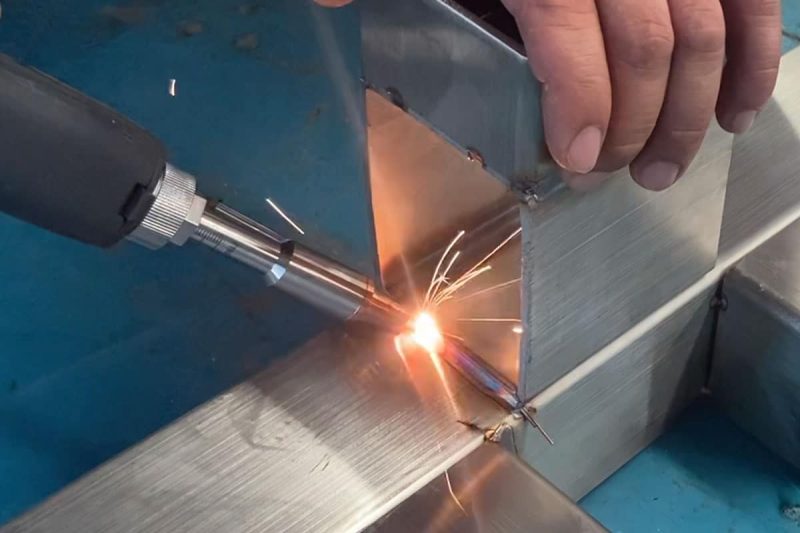
Lazer Kaynak Nedir?
Lazer kaynağının çalışma prensibi
Lazer kaynağı hangi malzemeler için kullanılabilir?
Lazer kaynağı, farklı endüstrilerdeki çeşitli malzemeler için kullanılabilen çok yönlü bir kaynak işlemidir. Lazer kaynağının uygunluğu, malzeme özelliklerine ve uygulamanın özel gereksinimlerine bağlıdır. Lazer kaynağında yaygın olarak kullanılan bazı malzemeler şunlardır:
- Çelik: Lazer kaynağı, karbon çeliği ve paslanmaz çelik dahil olmak üzere çeşitli çelik türlerinin kaynaklanmasında yaygın olarak kullanılır.
- Alüminyum: Lazer kaynağı, alüminyum ve alaşımlarının birleştirilmesinde etkilidir.
- Titanyum: Lazer kaynağı, havacılık ve tıp endüstrilerinde titanyum bileşenlerin kaynaklanması için kullanılır.
- Bakır ve Pirinç: Lazer kaynağı bakır ve pirinç gibi demir içermeyen metaller için kullanılabilir.
- Paslanmaz Çelik Alaşımları: Lazer kaynağı, paslanmaz çelikten yapılmış tıbbi cihazların montajında yaygın olarak kullanılır.
- Değerli Metaller: Lazer kaynağı kuyumculuk sektöründe altın ve platin gibi değerli metallerin kaynağında yaygın olarak kullanılmaktadır.
- Çeşitli Metaller ve Alaşımlar: Otomotiv endüstrisinde çeşitli metal bileşenlerin birleştirilmesi için lazer kaynağı kullanılmaktadır.
Ne tür lazer kaynağı vardır?
Her birinin kendine özgü avantajları ve uygulamaları olan çeşitli lazer kaynak yöntemleri vardır. Lazer kaynak tekniğinin seçimi malzeme özellikleri, kalınlık, üretim hızı, istenilen kaynak özellikleri gibi faktörlere bağlıdır. Üreticiler genellikle kendi özel gereksinimlerine ve birleştirilecek malzemelerin özelliklerine göre en uygun yöntemi seçerler. İşte bazı yaygın lazer kaynağı türleri:
- İletim Modlu Kaynak: İletim modlu kaynakta lazer enerjisi öncelikle malzemenin yüzeyinde emilir. Bu mod, ince malzemelerin kaynaklanması için uygundur ve sığ bir nüfuz derinliği ile karakterize edilir. Minimum düzeyde ısıdan etkilenen bölgenin gerekli olduğu uygulamalarda yaygın olarak kullanılır.
- Anahtar Deliği Modu Kaynağı: Anahtar deliği modu kaynağı, malzemede derin bir anahtar deliği oluşturmak için lazerin odaklanmasını içerir. Bu teknik daha kalın malzemelerin kaynaklanması için uygundur ve daha derin nüfuziyet sağlar. Anahtar deliği kaynağı genellikle güçlü, derin bir kaynak gerektiğinde kullanılır.
- Darbeli Lazer Kaynağı: Darbeli lazer kaynağı, lazer enerjisinin darbeler halinde iletilmesini içerir. Bu yöntem, ısı girdisini kontrol etmek, termal bozulmayı en aza indirmek ve ince malzemeleri kaynaklamak için uygundur. Darbeli lazer kaynağı, kaynak işlemi üzerinde hassas kontrolün gerekli olduğu uygulamalarda yaygın olarak kullanılır.
- Sürekli Dalga (CW) Lazer Kaynağı: Sürekli dalga lazer kaynağında darbesiz sabit bir lazer ışını kullanılır. Bu yöntem genellikle yüksek hızlı kaynak uygulamalarında kullanılır ve belirli malzeme ve kalınlıklar için iyi sonuçlar sağlayabilir.
- Lazer Mikro Kaynak: Lazer mikro kaynak, küçük ve hassas bileşenlerin kaynaklanması için kullanılan özel bir tekniktir. Hassasiyetin ve minimum ısı girişinin önemli olduğu elektronik ve tıbbi cihazlar gibi endüstrilerde yaygın olarak uygulanır.
- Lazer Hibrit Kaynak: Lazer hibrit kaynak, lazer kaynağını gaz metal ark kaynağı (GMAW) veya tungsten inert gaz (TIG) kaynağı gibi başka bir kaynak işlemiyle birleştirir. Bu yaklaşım, her iki sürecin de faydalarından yararlanır ve genellikle otomotiv ve gemi inşa endüstrilerinde kullanılır.
- Lazer Dikiş Kaynağı: Lazer dikiş kaynağı, üst üste binen malzemelerin uzunluğu boyunca sürekli kaynak dikişleri oluşturmak için kullanılır. Bu teknik ince levhaların birleştirilmesi için uygundur ve otomotiv ve elektronik endüstrilerinde yaygın olarak uygulanır.
- Lazer Nokta Kaynağı: Lazer nokta kaynağı, lazer enerjisinin küçük bir noktaya yoğunlaştırılmasını ve lokalize kaynaklar oluşturulmasını içerir. Bu yöntem genellikle mücevher imalatı ve elektronik bileşen montajı gibi uygulamalarda hassas kaynaklama için kullanılır.
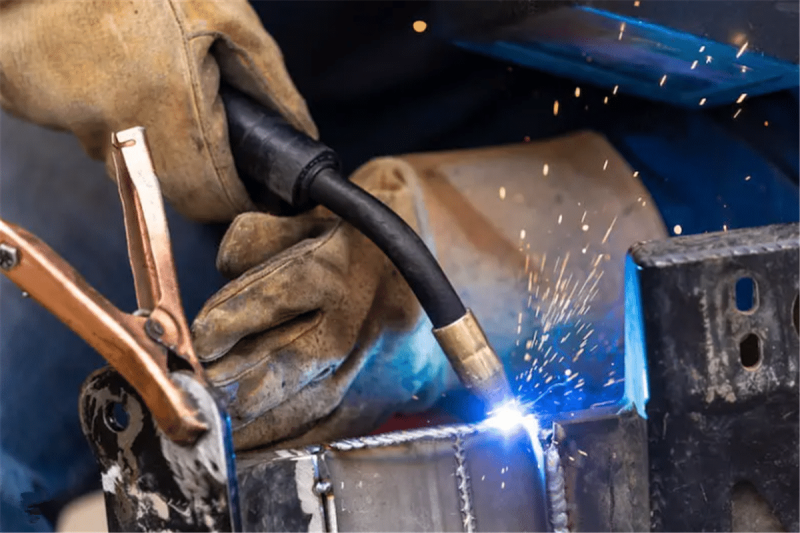
MIG Kaynağı Nedir?
MIG kaynağının çalışma prensibi
MIG kaynağı hangi malzemeler için kullanılabilir?
Gaz Metal Ark Kaynağı (GMAW) olarak da bilinen MIG (Metal İnert Gaz) kaynağı, çeşitli malzemeler için kullanılabilen çok yönlü bir kaynak işlemidir. MIG kaynağı için en yaygın malzemeler şunlardır:
- Karbon Çeliği: MIG kaynağı, karbon çeliğinin kaynağında sıklıkla kullanılır. Hem ince hem de kalın kesitler için geçerlidir.
- Paslanmaz Çelik: MIG kaynağı paslanmaz çelik için uygundur, bu da onu korozyon direncinin gerekli olduğu endüstrilerde yaygın olarak kullanılmasını sağlar.
- Alüminyum: MIG kaynağı alüminyum için kullanılabilir, ancak daha yumuşak alüminyum teli dolaşmadan beslemek için makara tabancası veya itme-çekme sistemi kullanmak gibi özel hususlar gerektirir.
- Nikel Alaşımları: MIG kaynağı, havacılık ve kimyasal işleme gibi endüstrilerde yaygın olarak kullanılan nikel alaşımlarının kaynağında kullanılır.
- Bakır ve Bakır Alaşımları: MIG kaynağı, özel teknik ve ekipman gerektirse de bakır ve bakır alaşımlarının kaynağında kullanılabilir.
- Diğer Alaşımlar: MIG kaynağı, kullanılan özel kaynak teli ve koruyucu gaza bağlı olarak çeşitli alaşımlara uyarlanabilir.
Ne tür MIG kaynağı vardır?
MIG kaynağı, farklı uygulamalara ve malzemelere uyacak çeşitli teknikleri ve varyasyonları kapsar. MIG kaynak tekniğinin seçimi, malzeme kalınlığı, bağlantı konfigürasyonu, kaynak konumu ve istenen kaynak özellikleri gibi faktörlere bağlıdır. Kaynakçılar genellikle kaynak projesinin özel gereksinimlerine göre uygun modu seçerler. İşte bazı yaygın MIG kaynağı türleri:
- Kısa Devre Transferi: Bu modda kaynak teli kaynak havuzuna temas ederek kısa devreye neden olur. Bu, ark boyunca küçük damlacıkların kontrollü bir şekilde aktarılmasıyla sonuçlanır. Kısa devre transferi ince malzemelerin kaynağına uygundur ve sıklıkla otomotiv ve sac uygulamalarında kullanılır.
- Küresel Transfer: Küresel transferde, erimiş metalin daha büyük damlaları ark boyunca aktarılarak daha belirgin bir ark ve sıçrama meydana gelir. Genellikle daha kalın malzemelerin kaynaklanması için kullanılır ve daha yüksek voltaj ayarları gerektirebilir.
- Püskürtme Transferi: Püskürtme transferi, küçük erimiş damlacıkların ark boyunca bir sprey deseninde sabit bir akışını içerir. Bu mod, daha yüksek amperajlarda daha kalın malzemelerin kaynaklanması için kullanılır, daha iyi nüfuziyet ve daha yüksek birikme oranları sağlar.
- Darbeli MIG Kaynağı: Darbeli MIG kaynağı, sprey aktarımı ve kısa devre aktarımının avantajlarını birleştirir. Isı girişini kontrol etmek ve genel olarak ısıdan etkilenen bölgeyi azaltmak için darbeli bir akım kullanır. Darbeli MIG, ince malzemeler, konum dışı kaynaklar ve hassas kontrol gerektiren uygulamalar için uygundur.
- Yüzey Gerilim Transferi (STT): Yüzey Gerilim Transferi, düşük voltaj ve yüksek akım kullanan kısa devre transferinin bir çeşididir. Özellikle ince malzemelerin kaynaklanması sırasında kaynak işlemi üzerinde daha iyi kontrol sağlamak üzere tasarlanmıştır.
- Soğuk Metal Transferi (CMT): Soğuk Metal Transferi, ısı girişini ve bozulmayı en aza indiren düşük ısılı bir transfer işlemidir. Genellikle ince malzemelerin kaynaklanması için kullanılır ve hassas kontrolün gerekli olduğu uygulamalar için uygundur.
- Değiştirilmiş Kısa Devre Transferi: Değiştirilmiş kısa devre transfer varyasyonları, konum kaynağı veya belirli malzeme kalınlıkları gibi belirli uygulamalar için performansı optimize etmek üzere kaynak parametrelerinde ayarlamalar içerir.
- Eksenel Püskürtme Transferi: Eksenel sprey transferi, arkın eksenel olarak yönlendirildiği, daha iyi penetrasyon ve kontrol sağlayan bir sprey transfer çeşididir.
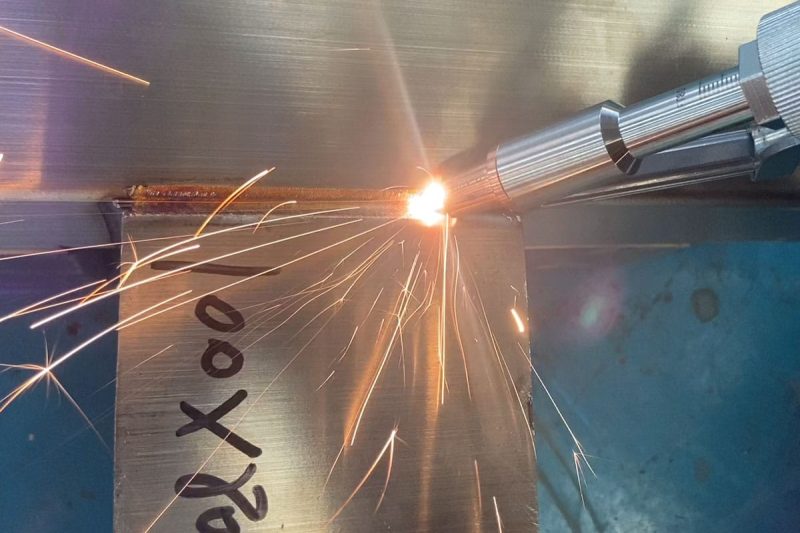
Lazer Kaynağı ve MIG Kaynağı
Kaynak İşlemi
- Lazer kaynağı: Isı kaynağı olarak yüksek düzeyde odaklanmış bir lazer ışınını kullanır. Lazer ışını hassas bir şekilde kontrol edilebilir ve kaynak alanına yönlendirilebilir. Hassas ve konsantre ısı sağlayarak çeşitli malzemelerde ince kaynak yapılmasına olanak tanır.
- MIG kaynağı: Isı kaynağı olarak bir elektrik arkı oluşturmak için sarf malzemesi tel elektrot ve koruyucu gaz kullanır. İyi nüfuz sağlar ve daha kalın malzemeler için uygundur.
Hassasiyet ve doğruluk
- Lazer kaynağı: Yüksek hassasiyet ve doğruluk sunarak hassas ve karmaşık kaynaklara uygun hale getirir. Minimum ısıdan etkilenen bölgeler ve kaynak prosesi üzerinde hassas kontrol gerektiren uygulamalar için çok uygundur.
- MIG kaynağı: Genellikle iyi bir nüfuziyet sunar ancak ısıdan etkilenen bölge daha geniş olabilir. Daha kalın malzemeler için uygundur, yapısal ve ağır hizmet uygulamaları için idealdir.
Kaynak Kalitesi
- Lazer kaynağı: Tipik olarak minimum distorsiyon ve dar ısıdan etkilenen bölge ile yüksek kaliteli kaynaklar üretir. Kaynak kalitesi ve estetiğin önemli olduğu uygulamalar için idealdir.
- MIG kaynağı: Güçlü ve yapısal olarak sağlam kaynaklar üretebilir ancak ısıdan etkilenen bölge, lazer kaynağa kıyasla daha büyük olabilir ve bu da bazı uygulamalarda daha önemli distorsiyona yol açabilir. Yüksek mukavemetli kaynakların gerekli olduğu uygulamalar için uygundur.
Hız Yeteneği
- Lazer kaynağı: Lazer ışınının konsantre ısı kaynağı, özellikle dikiş kaynağı veya punta kaynağı gibi uygulamalarda daha yüksek kaynak hızlarına olanak tanır. Daha hızlı kaynak hızları üretim verimliliğinin artmasına katkıda bulunabilir.
- MIG kaynağı: Bu, özellikle hızın önemli olduğu uygulamalarda nispeten hızlı bir işlem olabilir. Yüksek kaplama oranlarına ve hızlı kaynağa uygundur.
Otomasyon Yeteneği
- Lazer kaynağı: Yüksek hacimli üretim için otomatik sistemlere kolayca entegre edilir. Otomasyon ve hassasiyetin kritik olduğu endüstriyel uygulamalar için çok uygundur.
- MIG kaynağı: Bir dereceye kadar otomatikleştirilebilir ancak lazer kaynağı kadar kolay otomatikleştirilemeyebilir. Hem manuel hem de yarı otomatik işlemler için çok yönlü.
Makine Maliyeti
- Lazer Kaynak Makinesi: Başlangıç maliyeti genellikle MIG kaynak ekipmanından daha pahalıdır ve potansiyel olarak küçük işletmeler veya bireysel kaynakçılar için bir engel oluşturur.
- MIG Kaynak Makinesi: Tipik olarak daha uygun fiyatlı lazer kaynak sistemleridaha geniş bir kullanıcı kitlesinin erişebilmesini sağlıyor.
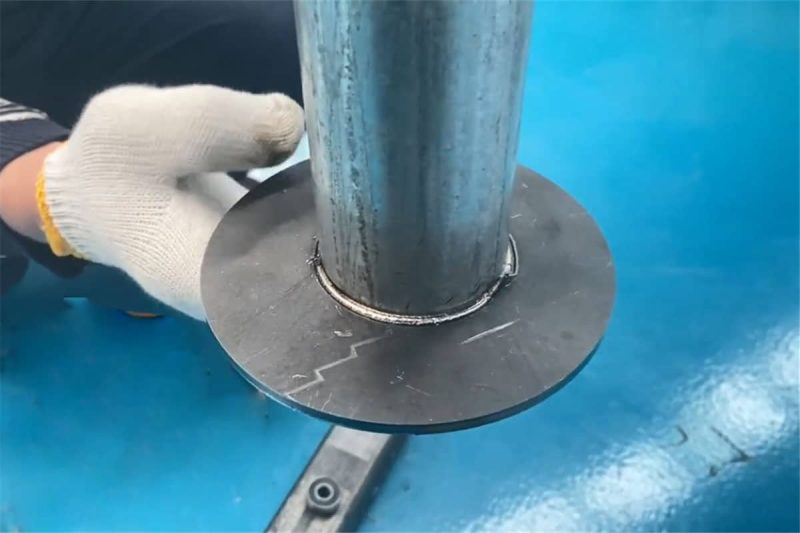
Doğru Kaynak İşlemi Nasıl Seçilir
Malzeme Türü ve Kalınlığı
- İnce malzemeler: Lazer kaynağı, ince malzemelerin yüksek hassasiyetle kaynaklanmasında üstünlük sağlar, bu da onu elektronik gibi uygulamalar için ideal kılar.
- Kalın malzemeler: MIG kaynağı, daha yüksek ısı girdisi nedeniyle inşaat ve ağır sanayide yaygın olarak bulunan daha kalın malzemeler için daha uygundur.
Maliyet Hususları
- İlk yatırım: Lazer kaynak ekipmanının ön maliyeti daha yüksek olma eğilimindedir ve bu da MIG kaynağını belirli kaynak ihtiyaçları için uygun maliyetli bir çözüm haline getirir.
- İşletme maliyetleri: Her kaynak yönteminin uzun vadeli işletme maliyetlerini değerlendirirken sarf malzemesi maliyetleri, enerji verimliliği ve bakım gibi faktörler dikkate alınmalıdır.
Üretim Hızı ve Verimliliği
- Yüksek hacimli üretim: Lazer kaynağının daha yüksek kaynak hızları ve otomasyon yetenekleri, verimliliğin kritik olduğu yüksek hacimli üretim için onu faydalı kılar.
- Özelleştirme ve prototip oluşturma: Çok yönlülüğü ve maliyet etkinliği ile MIG kaynağı, hızdan ziyade esnekliğin odak noktası olabileceği özelleştirme ve prototip oluşturma için çok uygundur.
Endüstriler ve Uygulamalar
- Havacılık: Lazer kaynağının hassasiyeti ve minimum distorsiyonu, onu dar toleransların ve yüksek kaliteli kaynakların hayati önem taşıdığı havacılık ve uzay uygulamaları için uygun kılar.
- Elektronik: Küçük ve hassas bileşenleri kaynaklama yeteneği, lazer kaynağını elektronik endüstrisinde tercih edilen bir seçenek haline getirir.
- Tıbbi cihazlar: Lazer kaynağı, hassasiyeti ve biyouyumlu malzemelerle çalışabilmesi nedeniyle tıbbi cihazların üretiminde yaygın olarak kullanılmaktadır.
- Otomotiv: MIG kaynağı, çok yönlülüğü ve çeşitli malzeme ve kalınlıkları işleme yeteneği nedeniyle otomotiv endüstrisinde yaygın olarak kullanılmaktadır.
- İnşaat: MIG kaynağının maliyet etkinliği ve çok yönlülüğü, onu yapısal çelik içeren inşaat projelerinde tercih edilen bir yöntem haline getirmektedir.
- Genel imalat: MIG kaynağı, kullanım kolaylığı ve geniş bir uygulama yelpazesine uygunluğu nedeniyle genel imalat atölyelerinde yaygın olarak benimsenmektedir.
özetle
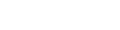
- [email protected]
- [email protected]
- +86-19963414011
- 3 Bölge A, Lunzhen Sanayi Bölgesi, Yucheng Şehri, Shandong Eyaleti.