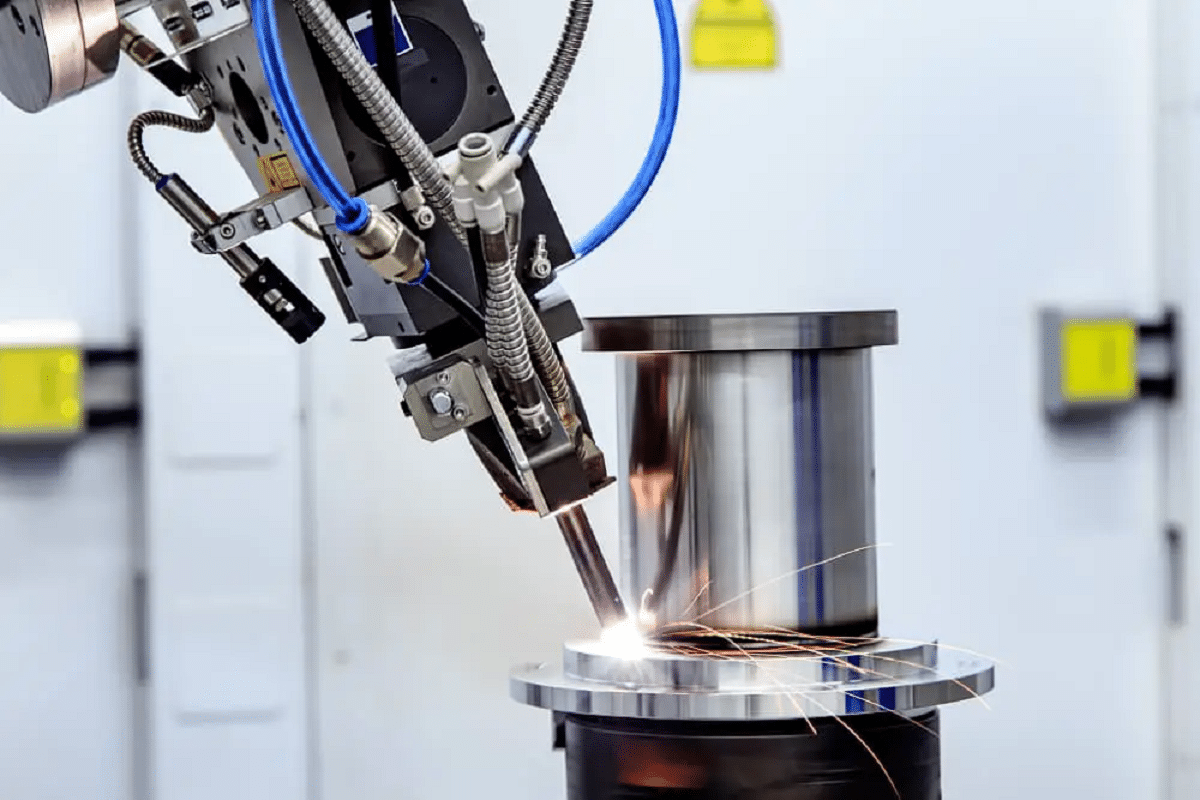
Lazer Kaynakta Hangi Kaynak Kusurları Oluşabilir? Nasıl çözeceksin?
Lazer kaynağı, yüksek verimlilik, yüksek hassasiyet, iyi etki ve kolay otomasyon entegrasyonu avantajlarından dolayı çeşitli endüstrilerde yaygın olarak kullanılmaktadır. Askeri, tıbbi, havacılık, yeni enerji ve diğer endüstriler de dahil olmak üzere endüstriyel üretim ve imalatta önemli bir rol oynar. Ancak herhangi bir işleme yöntemi, ilkeleri ve süreçleri doğru şekilde anlaşılmadığı takdirde kusurlu veya kusurlu ürünler üretebilir ve lazer kaynağı da bir istisna değildir. Lazer kaynağının değerini en üst düzeye çıkarmak ve kusursuz görünüme sahip kaliteli bir ürün üretmek için bu tuzakları anlamak ve bunlardan nasıl kaçınılacağını öğrenmek önemlidir.
İçindekiler
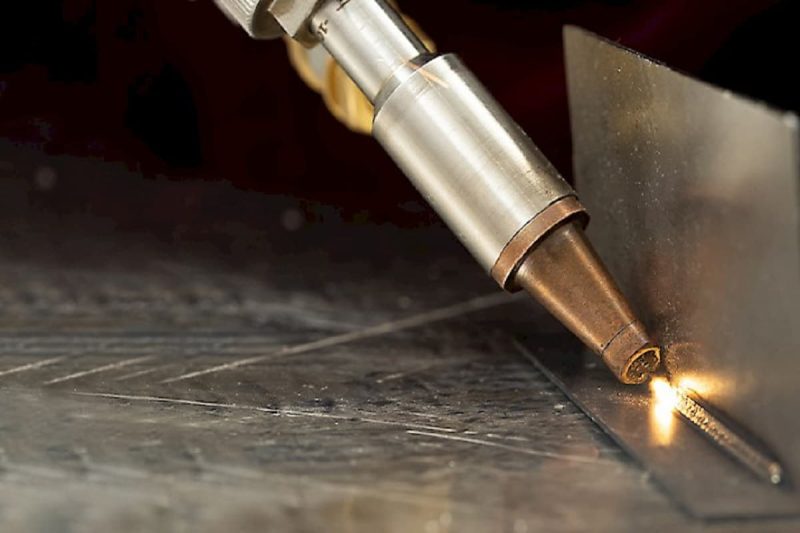
Lazer Kaynak İlkeleri
Lazer kaynağı, lazer malzeme işleme teknolojisinin önemli uygulamalarından biridir. Lazer kaynağı temelde iki farklı modda çalışır: İletim sınırlı kaynak ve derin delik kaynağı. Kaynak işlemi sırasında ısı iletimi gerçekleştirilir, yani lazer radyasyonu yüzeyi ısıtır ve yüzey ısısı, ısı iletimi yoluyla iç kısma yayılır. Lazer darbe genişliği, enerji, tepe gücü ve tekrarlama frekansı, element erimesi ve diğer parametrelerin kontrol edilmesiyle metal yüzey üzerinde özel bir eriyik havuzu oluşturulur. Isı, iki yüzey arasında bir kaynak dikişi oluşturmak için malzemeyi eriterek kaynağı tamamlar.
Lazer kaynak, yüksek kaynak hassasiyetine ve kaynak kalitesine sahiptir. Lazerin kendisi çok az ısı ürettiğinden, lazer kaynağından sonra üretilen kaynak dikişi de nispeten küçüktür, bu da lazer kaynağını özellikle elektronik veya cam/metal contalar gibi daha ince malzemeler için uygun hale getirir. Daha kalın malzemelerin kaynağında ise kare kenarlı parçalar arasında dar ve derin kaynaklar oluşur. Ek olarak, lazer inanılmaz derecede yüksek sıcaklıklara (binlerce Santigrat derece) ulaşabilir, bu nedenle aşırı sıcaklıklara ve zorlu ortamlara dayanabilen çok güçlü ve dayanıklı kaynaklar üretebilir.
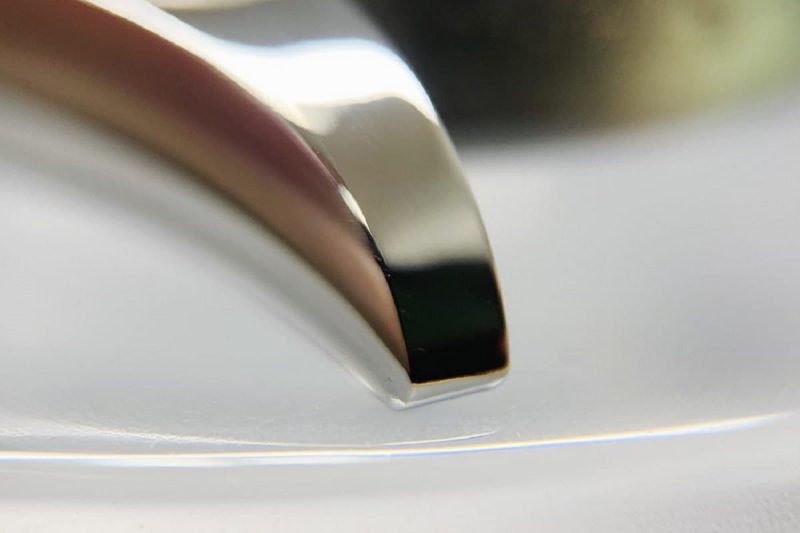
Lazer kaynağındaki yaygın kaynak hataları ve bunların nasıl çözüleceği
Lazer kaynağı, yüksek verimlilik, yüksek hassasiyet, iyi etki, kolay otomasyon, entegrasyon vb. avantajlara sahiptir, ancak yanlış kullanım, ürünlerde ciddi kalite kusurlarına da yol açabilir. Ancak bu kusurları iyi anlayarak lazer kaynağının değeri tam olarak ortaya çıkarılabilir ve güzel görünüme ve yüksek kaliteye sahip ürünler işlenebilir. Aşağıda, lazer kaynağında sıklıkla meydana gelen 8 kaynak hatası bulunmaktadır.
Gözeneklilik
Gözenekler, lazer kaynağında oluşmaya eğilimli kusurlardan biridir. Lazer kaynağındaki gözenekliliğe levha veya yüzey kirlenmesi veya gres, yağ, oksitler, emilen su buharı, kesme sıvısı kalıntıları vb. gibi yetersiz ön temizleme neden olabilir. Lazer kaynak havuzu derin ve dardır ve soğutma hızı hızlı. Sıvı erimiş havuzda üretilen gazın yüzey kirliliği nedeniyle kaçacak zamanı yoktur ve gözenek oluşturmak kolaydır. Bununla birlikte, lazer kaynağı hızla soğur ve üretilen gözenekler genellikle geleneksel füzyon kaynağından daha küçüktür.
Lazer kaynağında gözenekliliği önlemek için:
- uygun koruyucu gaz sağlayın: Atmosferik gazlardan yeterli koruma sağlamak için yüksek kaliteli bir koruyucu gaz (genellikle bir argon veya helyum karışımı) kullanın.
- gaz akışını optimize edin: kaynak alanını büyük ölçüde etkili bir şekilde korumak için uygun koruyucu gaz akışını ve yönünü ayarlayın.
- İş parçasının yüzeyini temizleyin: Kaynak yapılacak yüzeyi, gaz sıkışmasını önlemek için yağ, gres, pas veya kir gibi kirleticileri gidermek üzere iyice temizleyin. Gerektiğinde solventle temizleme, mekanik temizleme veya kimyasal temizleme gibi uygun temizleme yöntemlerini kullanın.
- Uygun derz hazırlığı: Gazın sıkışabileceği boşluklar oluşmasını önlemek için uygun derz uyumu ve hizalamasını sağlayın. Mümkünse, gaz sıkışmasını önlemek için geri temizleme tekniklerini kullanın.
Alttan kesilmiş
Bir alttan kesme, bir kaynağın kenarında oluşan bir oluk veya çöküntüdür. Genellikle aşırı ısı girişi veya kaynak hızından kaynaklanır. Kaynak hızı çok hızlı olduğunda, kaynağın ortasındaki küçük deliğin arkasındaki sıvı metalin yeniden dağıtmak için zamanı yoktur ve kaynağın her iki tarafında katılaşarak bir alt kesim oluşturur.
Lazer kaynağında alttan kesmeleri önlemek için:
- Lazer Parametrelerini Optimize Etme: Uygun ısı girişi elde etmek için lazer gücünü, darbe süresini ve odak konumunu ayarlayın. Aşırı ısınmaya ve alttan kesmeye neden olabileceğinden çok yüksek güç kullanmaktan veya çok hızlı kaynak yapmaktan kaçının.
- Tutarlı bir kaynak hızı sağlayın: Sabit bir hareket hızı sağlamak için lazer ışınının veya iş parçasının hareketini kontrol edin. Hızlı hız değişiklikleri, eşit olmayan ısı dağılımına ve alttan kesme oluşumuna neden olabilir.
- Uygun bağlantı tasarımı ve oturması: Doğru bağlantı, uygun şev açısı ve uygun boşluk toleransı dahil olmak üzere uygun bağlantı hazırlığından emin olun. Sıkı oturmanın sürdürülmesi, kenarların aşırı erimesini önlemeye yardımcı olur ve alttan kesmeyi azaltır.
Kaynak çatlakları
Kaynak sıcak çatlakları, kaynak işlemi sırasında kaynak ve ısıdan etkilenen bölgedeki metal katılaşma çizgisinin yakınına kadar soğuduğunda yüksek sıcaklık alanında oluşan çatlakları ifade eder. Genel olarak yüksek sıcaklık çatlakları ve düşük sıcaklık çatlakları olarak ayrılabilir. Lazer kaynak işlemi sırasında, lazerin küçük ısı girişi nedeniyle, kaynak sonrası deformasyon küçüktür ve kaynaktan kaynaklanan stres de küçüktür, bu nedenle genellikle yüksek sıcaklıkta çatlaklar oluşmaz. Bununla birlikte, farklı malzemeler ve yanlış işlem parametreleri seçimi nedeniyle, kusur şeklinde yüksek sıcaklıkta çatlaklar ortaya çıkacaktır.
Kaynak çatlaklarını önlemek için:
- ısı girişini kontrol edin: Isı girişini kontrol etmek ve termal stresi azaltmak için lazer parametrelerini optimize edin. Çatlamaya neden olabilecek aşırı ısı oluşumundan ve hızlı soğuma oranlarından kaçının. Bu, lazer gücünü ve darbe süresini ayarlayarak veya darbe şekillendirme teknikleri kullanılarak elde edilebilir.
- Ön ısıtma ve kaynak sonrası ısıl işlem: İş parçasının kaynaktan önce ön ısıtılması, termal gradyanları ve gerilmeleri azaltmaya ve kaynaklanabilirliği geliştirmeye yardımcı olur. Tavlama veya gerilim giderme gibi kaynak sonrası ısıl işlem teknikleri artık gerilimleri azaltmak, mekanik özellikleri geliştirmek ve çatlama riskini azaltmak için de kullanılabilir.
- Dolgu Malzemesinin Seçimi: Çatlama riskini en aza indirmek için temel malzemeyle uyumlu, uygun bileşime ve sünekliğe sahip bir dolgu malzemesi kullanın.
Eksik füzyon veya penetrasyon eksikliği
Eksik füzyon veya eksik penetrasyon, kaynak metali ahşapla tam olarak kaynaşmadığı veya bağlantının tüm kalınlığına nüfuz etmediği zaman meydana gelir.
Eksik veya nüfuz edilmemiş füzyondan kaçınmak için:
- lazer parametrelerini optimize edin: Uygun malzeme füzyonu ve penetrasyonu elde etmek için lazer gücünü, darbe süresini ve odak konumunu ayarlayın. Daha yüksek bir güç ayarı veya odak konumunun ayarlanması, daha derine nüfuz etmeye yardımcı olabilir.
- Derz hazırlama ve montaj: Uygun derz tasarımı ve montajı sağlayın. Uygun füzyon ve penetrasyonu desteklemek için oluk açıları, boşluk toleransları ve bağlantı hazırlama teknikleri seçilmelidir.
- Kaynak hızını ayarlayın: Kaynak hızını yeterli ısı girişine ve bağlantıya nüfuz etmesine izin verecek şekilde ayarlayın. Kaynak hızının optimize edilmesi, lazer enerjisinin malzeme ile tamamen etkileşime girmesini sağlar.
Sıçrama
Lazer kaynağından kaynaklanan sıçrama, kaynak dikişinin yüzey kalitesini ciddi şekilde etkileyebilir. Kaynak sonrasında iş parçasının veya malzemenin yüzeyinde çok sayıda metal parçacık görünebilir ve bu durum yalnızca görünümü etkilemekle kalmaz, aynı zamanda kullanımı da etkiler. Sıçrama ciddi olduğunda lensi de kirletecek ve zarar verecektir.
Lazer kaynağında sıçramayı önlemek için:
- lazer ışını odağını ve konumunu optimize edin: İstikrarlı ve hassas kaynak elde etmek için lazer ışını odak konumunu ve şeklini uygun şekilde ayarlayın. Sıçramaya neden olabilecek lazer ışınının yanlış hizalanmasından veya dengesiz odaklanmasından kaçının.
- Uygun koruyucu gaz ve akış hızı kullanın: Yeterli koruma sağlamak için uygun koruyucu gaz bileşimini ve akış hızını seçin. Koruyucu gaz, kaynak havuzunun oksidasyonunu ve kirlenmesini önlemeye yardımcı olur ve sıçramayı azaltır. Gaz akışının kaynak gereksinimlerine göre ayarlanması gerekir.
- İş parçasının yüzeyini temizleyin: İş parçasının yüzeyini iyice temizleyin ve sıçrama oluşumuna neden olabilecek her türlü pisliği temizleyin.
Deformasyon
Deformasyon, kaynak işlemi nedeniyle kaynaklı bir yapının veya iş parçasının deformasyonunu veya bükülmesini ifade eder.
Lazer kaynak deformasyonunu önlemek için:
- Doğru sabitleme ve kenetleme tekniğini kullanın: Kaynak sırasında hareketi veya deformasyonu en aza indirmek için iş parçasını veya yapıyı sabitleyin. İş parçasının yeterli desteği ve hizalanması, boyutsal kararlılığın korunmasına yardımcı olur.
- iş parçasının ön ısıtılması: Termal gradyanları azaltmak ve bozulmayı en aza indirmek için iş parçasını önceden ısıtmayı düşünün.
- Kontrollü Soğutma: Soğutma oranlarını düzenlemek ve termal gradyanları en aza indirmek için ısı emiciler veya armatürlerin kullanımı gibi kontrollü soğutma teknikleri uygulayın.
Isıdan Etkilenen Bölge (HAZ) Sorunları
Lazer kaynağı, kaynak çevresinde oldukça yoğun ısıdan etkilenmiş bir bölge oluşturur. Isıdan etkilenen bölge, malzemenin sertliğinde ve mukavemetinde azalmaya neden olabilecek termal döngüye ve mikroyapısal değişikliklere uğrar.
HAZ sorunlarını önlemek için:
- Lazer Parametrelerini Optimize Etme: Isıdan etkilenen bölgenin boyutunu ve derinliğini en aza indirmek için lazer parametrelerini ayarlayın. Bu, lazer gücünün, darbe süresinin ve ışın odağının kontrol edilmesini içerir.
- Süpürme veya salınım tekniklerinin kullanılması: Süpürme veya salınım tekniklerinin kullanılması, ısının daha eşit dağılımını sağlar ve belirli alanlarda ısı konsantrasyonunu azaltır, böylece ısıdan etkilenen bölgelerle ilgili sorunları en aza indirir.
- kaynak sonrası ısıl işlem gerçekleştirin: Mikro yapıyı iyileştirmek ve ısıdan etkilenen bölge ile ilgili sorunları azaltmak için tavlama veya gerilim giderme gibi uygun kaynak sonrası ısıl işlem işlemlerini uygulayın. Isıl işlem, ısıdan etkilenen bölgedeki malzeme özelliklerinin geri kazanılmasına yardımcı olur.
Kaynak Çöküşü
Lazer kaynağı çökmesi, kaynak işlemi sırasında kaynak dikişinin içe doğru deformasyonunu veya batmasını ifade eder. Bu, çok yüksek lazer gücü, yetersiz eriyik havuzu kontrolü, yetersiz malzeme desteği, yanlış bağlantı montajı, zayıf termal yönetim, malzeme seçimi sorunları ve süreç izleme ve kontrolünün olmaması gibi çeşitli nedenlerle olabilir.
Kaynak çökmesini önlemek için:
- lazer parametrelerini optimize edin: çevreleyen malzemelerin aşırı erimesini önlemek için lazer gücünü veya enerji yoğunluğunu azaltın. Penetrasyon ile çökmeye neden olabilecek aşırı erimeyi önlemek arasında bir denge elde etmek için lazer gücünü, darbe süresini ve ışın şeklini ayarlayın.
- Uygun Malzeme Desteği: İş parçasını yerinde tutmak ve stabilite sağlamak için fikstürler, şablonlar veya kıskaçlar kullanarak kaynak sırasında uygun malzeme desteği sağlayın. Isıyı dağıtmak ve eklemler için ek destek sağlamak için destek çubukları veya ısı emiciler kullanmayı düşünün.
- uygun derz montajı sağlayın: Uygun derz montajı, çökmeyi önlemeye yardımcı olur. Kaynak yapmadan önce eşleşen yüzeylerin uygun şekilde hazırlandığından ve hizalandığından emin olun. Uygun derz tasarımı ve kenar hazırlama teknikleri uygulayarak derz sağlamlığını ve stabilitesini artırın.
- Isı Girişini Yönetin: Isı girişini kontrol edin ve termal döngüleri uygun şekilde yönetin. Isıyı eşit olarak dağıtmak ve bölgesel aşırı ısınmayı önlemek için tarama veya hareket stratejilerini optimize edin. Termal gradyanları en aza indirmek ve çökme riskini azaltmak için ön ısıtma veya kontrollü soğutma teknikleri uygulayın.
- Malzeme Seçimi ve Uyumluluk: Uygun malzemeleri ve birbiriyle uyumlu kaynak parametrelerini seçin. Uygun ısı transferini sağlamak ve aşırı bölgesel erimeyi önlemek için termal iletkenlik ve erime noktası gibi malzeme özelliklerini göz önünde bulundurun.
- Süreci İzleme ve Kontrol Etme: Çökme belirtilerini veya istenen kaynak parametrelerinden sapmaları tespit etmek için gerçek zamanlı bir süreç izleme ve kontrol sistemi uygulayın. Lazer parametrelerini, tarama hızını veya malzeme desteğini ayarlamak için kaynak sırasında geri bildirim mekanizmalarını kullanın. Tutarlı ve istikrarlı kaynak koşulları elde etmek için uyarlanabilir kontrol sistemleri veya kapalı döngü geri bildirim kontrolü gibi gelişmiş teknolojileri benimseyin.
- Uygun eriyik havuzu kontrolünü sağlayın: Lazer parametrelerini ve tarama hızını ayarlayarak eriyik havuzunun boyutunu ve şeklini kontrol edin. Kararlı ve kontrollü bir kaynak havuzu oluşumu sağlamak için anahtar deliği kaynağı veya iletim modu kaynağı gibi uygun kaynak teknikleri kullanın.
özetle
Tabii ki, diğer kusurlar lazer kaynağı ile ilişkilendirilebilir. Teknik işletme problemlerine ek olarak, bazı kusurlar malzemenin özelliklerinde değişikliklere neden olabilir. Ancak lazer kaynak işleminde oluşabilecek kusurları ve farklı kusurların nedenlerini doğru anlayarak anormal kaynak problemini daha hedefli bir şekilde çözebiliriz.
AccTek Lazer geniş bir ürün yelpazesine sahiptir. lazer kaynak makineleritaşınabilir, temizleme ve kaynaklama dahil 3'ü 1 arada lazer kaynak makineleri, sac ve borularınızın kaynağına uygundur. Özel bir uygulama için makine arıyorsanız, AccTek Lazer ayrıca müşterinin gereksinimlerine göre özel bir çözüm gerçekleştirmek için uygun bileşenlerle donatılabilir.
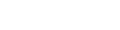
İletişim bilgileri
- [email protected]
- [email protected]
- +86-19963414011
- 3 Bölge A, Lunzhen Sanayi Bölgesi, Yucheng Şehri, Shandong Eyaleti.
Lazer Çözümleri Alın