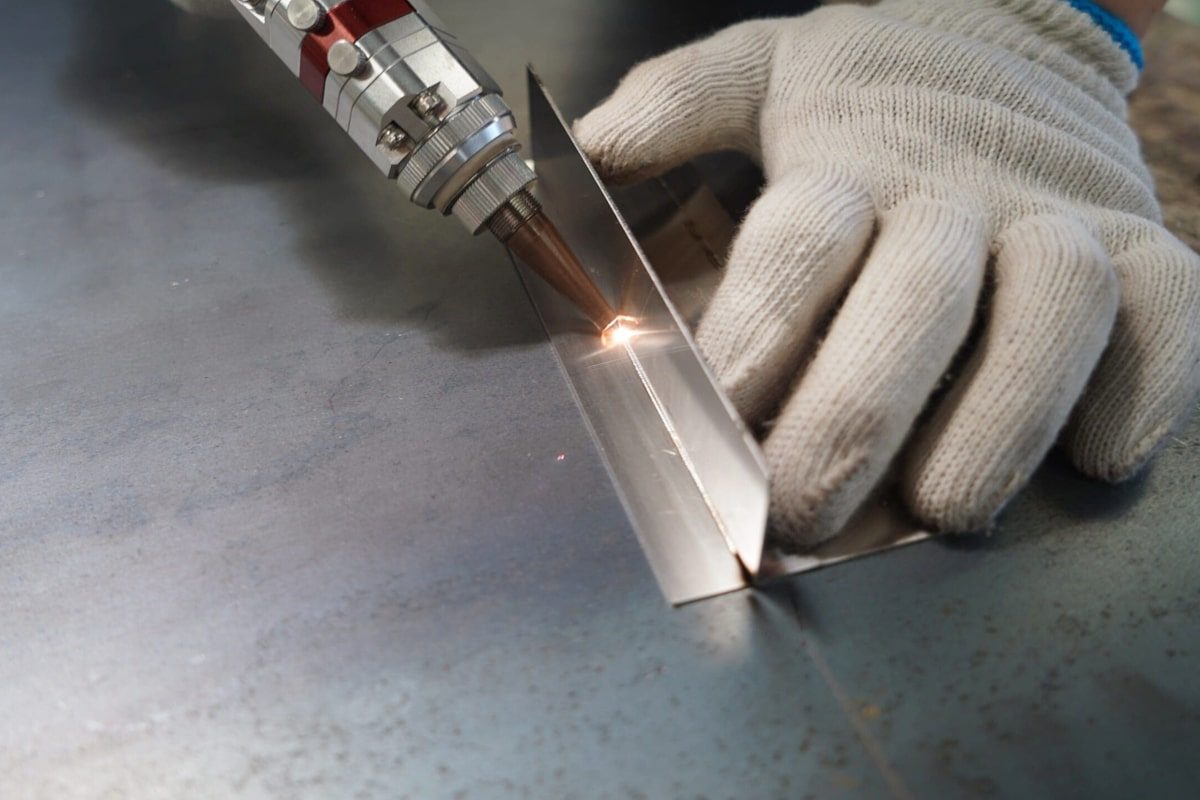
Lazer Kaynağın Kaynaklanabilirliğini Hangi Faktörler Etkiler?
Lazer kaynak, yüksek hassasiyet, minimum ısı bozulması ve geleneksel yöntemlerle kaynaklanması zor olan malzemeleri birleştirme yeteneği sunarak modern üretimde devrim yaratmıştır. Havacılık, otomotiv, tıbbi cihazlar ve elektronik gibi endüstriler, hızı ve minimum kaynak sonrası işlemle yüksek kaliteli, güçlü bağlantılar sağlama yeteneği nedeniyle lazer kaynağına büyük ölçüde güvenmektedir. Lazer kaynağının sayısız avantajına rağmen, optimum kaynaklanabilirliğe ulaşmak her zaman kolay değildir. Bir lazer kaynağının başarısı çeşitli faktörler tarafından belirlenir: malzeme özellikleri, lazer parametreleri, ekipman kurulumu, çevre koşulları ve kaynak sonrası işlemler. Bunların hepsi, güçlü, dayanıklı ve kusursuz bir kaynak üretimi sağlamak için dikkatlice kontrol edilmelidir.
Bu makalede, lazer kaynakta malzemelerin kaynaklanabilirliğini etkileyen çeşitli faktörleri derinlemesine inceleyeceğiz. Bu faktörler arasında temel malzeme bileşimi, eklemin geometrisi, lazer gücü, hızı ve ışın kalitesi ile sıcaklık ve kirleticiler gibi dış çevresel faktörler yer alır. Ayrıca lazer kaynakta karşılaşılan yaygın zorlukları ve bunların mümkün olan en yüksek kaynak kalitesini elde etmek için nasıl hafifletilebileceğini inceleyeceğiz. Bu makalenin sonunda, okuyucular lazer kaynakta yer alan çok sayıda değişken ve bu faktörlerin üstün kaynak sonuçları için nasıl optimize edileceği konusunda kapsamlı bir anlayışa sahip olacaklar.
İçindekiler
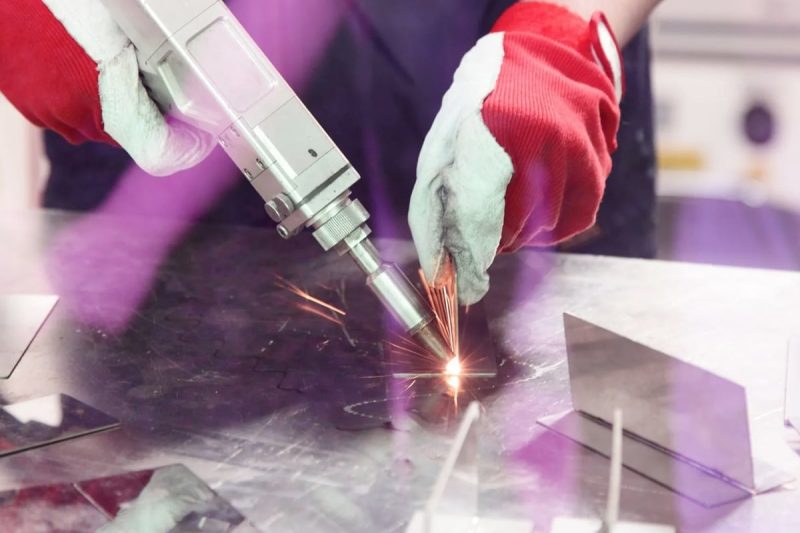
Lazer Kaynakçılığa Giriş
Tanım ve Genel Bakış
Lazer kaynak, genellikle metaller veya termoplastikler olmak üzere malzemeleri eritmek ve kaynaştırmak için oldukça yoğun bir lazer ışını kullanan hassas bir kaynak tekniğidir. Bir lazer kaynağı tarafından üretilen lazer ışını, odaklanmış enerjiyi malzemeye yönlendirerek, birleştirme arayüzünde temel malzemeyi eriten yerel bir ısı bölgesi oluşturur. Erimiş malzeme katılaştıkça bir kaynak oluşturur. Bu işlem, sabit ısı sağlayan sürekli dalga (CW) lazerler veya genellikle aşırı ısınmayı önlemek ve kontrollü penetrasyon sağlamak için kısa patlamalarda enerji veren darbeli lazerler kullanılarak yapılabilir.
Lazer kaynaklama son derece çok yönlüdür ve çeşitli malzeme türleri ve kalınlıkları için kullanılabilir. Yüksek kaynak hızları, dar ısıdan etkilenen bölgeler (HAZ), minimum malzeme bozulması ve üretim verimliliğini artıran işlemi otomatikleştirme yeteneği dahil olmak üzere çok sayıda avantaj sunar. Lazer ışınının hassasiyeti, dar alanlarda ve hassas bileşenlerde kaynak yapmaya olanak tanır ve bu da lazer kaynaklamayı havacılık ve elektronik endüstrileri de dahil olmak üzere yüksek hassasiyetli uygulamalar için ideal hale getirir.
Lazer Kaynakta Kaynaklanabilirliğin Önemi
Lazer kaynakta kaynaklanabilirlik, bir malzemenin lazer kaynak işlemine tabi tutulduğunda güçlü, kusursuz bir birleşim oluşturma yeteneğini ifade eder. Kaynaklanabilirliğin elde edilmesi, malzemenin kimyasal bileşimi, termal özellikleri, birleşim tasarımı ve lazer ışınından gelen yerel ısı girişine nasıl tepki verdiği gibi birbiriyle ilişkili birkaç faktöre bağlıdır. Bu faktörler optimize edilmezse, kaynaklı birleşim gözeneklilik, çatlama, bozulma veya zayıf bağlanma gibi kusurlara eğilimli olabilir.
Kaynaklanabilirlik kavramı, lazer kaynakta özellikle önemlidir çünkü lazer ışınının yüksek enerjili konsantrasyonu, malzemenin mikro yapısı ve mekanik özellikleri üzerinde önemli bir etkiye sahip olabilir. Örneğin, hızlı ısıtma ve soğutma döngüleri, belirli malzemelerde kalıntı gerilim, çatlama veya istenmeyen faz dönüşümleri gibi sorunlara yol açabilir. Bu zorlukların üstesinden gelmek için, üreticiler lazer kaynakta yer alan çeşitli parametreleri dikkatlice seçmeli ve kontrol etmelidir.
Geleneksel Kaynak Yöntemleriyle Karşılaştırma
Lazer kaynak, hassasiyeti ve verimliliğiyle bilinse de, MIG (Metal İnert Gaz) kaynak veya TIG (Tungsten İnert Gaz) kaynak gibi geleneksel kaynak yöntemlerinden birkaç önemli açıdan önemli ölçüde farklıdır. Geleneksel kaynak yöntemleri, malzemenin daha geniş bir alanını ısıtan ve genellikle daha geniş ısıdan etkilenen bölgelerle sonuçlanan ısı üretmek için elektrik arkları kullanır. Bu yöntemler ayrıca daha yavaş kaynak hızları ve daha yüksek malzeme bozulması içerir. Öte yandan, lazer kaynak, daha hızlı kaynak hızlarına, daha dar ısıdan etkilenen bölgelere ve minimum bozulmaya olanak tanıyan oldukça yoğun bir enerji demeti ile karakterize edilir.
Ancak lazer kaynak, geleneksel yöntemlere göre malzeme özelliklerindeki, bağlantı tasarımındaki ve lazer ayarlarındaki değişikliklere karşı daha hassastır. Örneğin, geleneksel yöntemler daha kalın malzemeler veya düzensiz geometrilere sahip bağlantıların kaynaklanmasında daha hoşgörülü olabilirken, lazer kaynak, lazer gücü, ışın odağı ve kaynak hızı gibi parametrelerin daha hassas bir şekilde kontrol edilmesini gerektirir. Bu nedenle, lazer kaynak, özellikle işlem için zorlayıcı olan malzemeler veya geometrilerle uğraşırken, tüm uygulamalar için ideal çözüm olmayabilir.
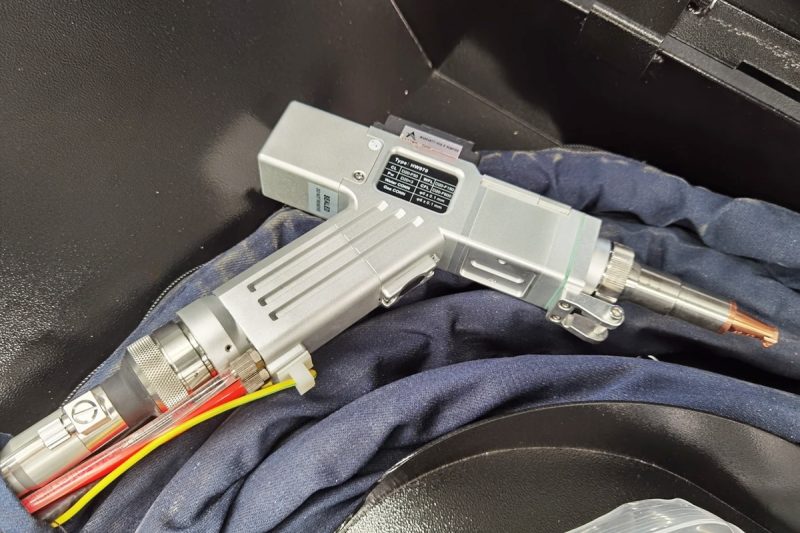
Malzeme özellikleri
Kaynaklanan malzeme, lazer kaynak işleminin başarısında önemli bir rol oynar. Kaynaklanabilirliği etkileyen temel malzeme özellikleri arasında temel malzeme bileşimi, kalınlık ve geometri, erime noktası, ısıl iletkenlik ve alaşım elementlerinin veya katkı maddelerinin varlığı yer alır.
Temel Malzeme Kompozisyonu
Temel malzemenin kimyasal bileşimi kaynaklanabilirliği etkileyen en önemli faktörlerden biridir. Farklı malzemelerin farklı erime noktaları, ısıl iletkenlikleri ve katılaşma davranışları vardır ve bunların hepsi lazer kaynak işlemini etkiler. Örneğin, yüksek karbonlu çelikler soğutma sırasında sert ve kırılgan fazlar oluşturma eğilimindedir ve bu da kaynakta çatlama olasılığını artırır. Benzer şekilde, krom, nikel veya molibden gibi belirli alaşım elementlerinin yüksek seviyelerine sahip malzemeler faz dönüşümlerine daha duyarlı olabilir ve bu da kaynak kusurlarına veya mekanik özelliklerin azalmasına yol açabilir.
Bazı malzemeler, örneğin alüminyum Ve bakır, yüksek termal iletkenlikleri ve düşük erime noktaları nedeniyle lazer kaynak kullanılarak kaynak yapılması özellikle zordur. Bu malzemeler yeterli penetrasyona ulaşmak için daha yüksek lazer gücü gerektirir, ancak yanma riski de çok daha yüksektir. Titanyum alaşımları gibi yüksek genleşme katsayısına sahip malzemeler, kaynak sırasında termal bozulma yaşayabilir ve lazer parametrelerinin hassas bir şekilde kontrol edilmesini gerektirebilir.
Kaynak yapılan malzemenin bileşimini anlamak, optimum lazer parametrelerini belirlemek için önemlidir. Malzemedeki alaşım elementleri ve safsızlıklar, malzemenin ısıya ve kaynak oluşumuna nasıl tepki verdiğini etkileyebilir ve bu da lazer gücü, ışın odağı ve koruyucu gaz gibi parametreleri ayarlamayı gerekli kılar.
Kalınlık ve Geometri
Malzeme kalınlığı ve birleştirme geometrisi, kaynak için gereken enerjiyi ve malzeme içindeki ısı dağılımını doğrudan etkiler. İnce malzemeler için, düşük lazer gücü genellikle yeterlidir, ancak yanmaya neden olabilecek aşırı ısı girişini önlemek için dikkatli kontrol gerekir. Daha kalın malzemeler için, tam penetrasyon ve sağlam bir kaynak sağlamak için daha yüksek lazer gücü ve daha yavaş kaynak hızları gereklidir.
Eklemin geometrisi, lazerin malzemeyle nasıl etkileşime girdiğini de etkiler. Basit uç birleştirmeleri, iki yüzey arasında doğrudan bir bağlantı sağladığı için kaynaklanması nispeten kolaydır. Ancak, T birleştirmeleri, fileto birleştirmeleri veya bindirme birleştirmeleri gibi daha karmaşık birleştirmeler özel ilgi gerektirebilir. Birleştirmenin açısı ve hizalaması, lazerin malzemelere düzgün bir şekilde nüfuz etme ve kaynaştırma yeteneğini etkileyecektir.
Karmaşık geometrilere sahip malzemeler, kirişi birleştirme ile hizalamadaki zorluklar ve birleştirme boyunca kalınlıktaki değişiklikler nedeniyle lazer kaynak için ek zorluklar da getirebilir. Birleştirme tasarımını optimize etmek ve lazer ışınının düzgün hizalanmasını sağlamak, güçlü, yüksek kaliteli kaynaklar elde etmede kritik adımlardır.
Erime Noktası ve Isıl İletkenlik
Bir malzemenin erime noktası, onu eritmek için ne kadar enerji gerektiğini belirler. Tungsten, titanyum veya yüksek alaşımlı çelikler gibi yüksek erime noktalarına sahip malzemeler, erime noktalarına ulaşmak için önemli ölçüde daha fazla enerji gerektirir ve lazer gücünün dikkatli bir şekilde yönetilmesini gerektirir. Öte yandan, alüminyum veya çinko gibi düşük erime noktalarına sahip malzemeler, bir lazer ışını altında çok kolay eriyebilir ve aşırı erimeyi önlemek için hızlı kaynak hızları veya darbeli lazer teknikleri gerektirebilir.
Isı iletkenliği (bir malzemenin ısıyı iletme yeteneği) de kaynaklanabilirliği etkiler. Bakır gibi yüksek ısı iletkenliğine sahip malzemeler ısıyı hızla dağıtır, bu da lazer ışınının bu ısı kaybını aşmak ve uygun penetrasyona ulaşmak için yeterli enerji sağlaması gerektiği anlamına gelir. Tersine, düşük ısı iletkenliğine sahip malzemeler, örneğin paslanmaz çelik, ısıyı daha etkili bir şekilde tutar, bu da düzgün yönetilmezse daha büyük bir ısıdan etkilenen bölgeye (HAZ) ve potansiyel termal bozulmaya yol açabilir.
Alaşım Elementleri ve Katkı Maddeleri
Alaşım elementlerinin ve katkı maddelerinin varlığı bir malzemenin kaynaklanabilirliği üzerinde derin bir etkiye sahip olabilir. Manganez, silikon ve krom gibi yaygın alaşım elementleri bir malzemenin mekanik özelliklerini iyileştirebilir ancak kaynak sırasında zorluklar da çıkarabilir. Örneğin, manganez kaynağı çatlamaya karşı daha hassas hale getirebilirken, aşırı silikon kaynak bölgesinde kırılgan fazların oluşmasına yol açabilir.
Yüzey bağlanmasını artırmak, oksidasyonu önlemek veya kaynak havuzunun davranışını değiştirmek için akı gibi katkı maddeleri kullanılabilir. Akı ve diğer katkı maddelerinin seçimi dikkatli yapılmalıdır, çünkü bunlar kaynağın nihai kalitesini ve mekanik özelliklerini etkileyebilir.
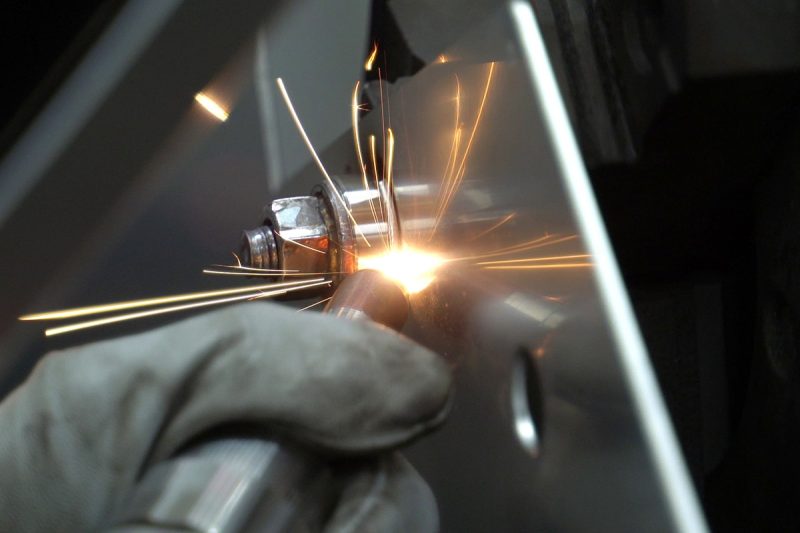
Lazer Parametreleri
Lazer gücü, odak, hız, ışın kalitesi ve diğerleri dahil olmak üzere lazer parametreleri, malzemelerin kaynaklanabilirliği için temeldir. Bu parametreler, lazer ışınının malzemeyle nasıl etkileşime girdiğini, kaynak havuzuna iletilen enerjiyi ve katılaşma oranını kontrol eder.
Lazer Gücü
Lazer gücü doğrudan penetrasyon derinliğini, kaynak hızını ve işlem sırasında üretilen ısı miktarını etkiler. Daha yüksek lazer gücü daha derin penetrasyona yol açar, ancak aynı zamanda yanma veya aşırı ısıdan etkilenen bölgeler riskini de artırır. Daha düşük güç ayarları daha kalın malzemelerde tam penetrasyona ulaşmak için yeterli enerji sağlamayabilir ve bu da zayıf birleşimlere veya eksik füzyona neden olabilir.
Optimum lazer güç ayarı, kaynak yapılan malzemeye, kalınlığına ve istenen kaynak özelliklerine bağlıdır. Genel olarak, malzemeyi eritmek için yeterli güç ile iş parçasını bozabilecek aşırı ısıdan kaçınmak arasında bir denge sağlanmalıdır.
Lazer Odaklı
Lazer odağı, lazer ışınının boyutunu ve yoğunluğunu kontrol eder. Sıkı bir şekilde odaklanmış bir ışın, malzeme üzerinde küçük, yüksek enerjili bir nokta oluşturur ve bu da daha derin penetrasyona ve daha dar kaynaklara olanak tanır. Ancak, çok sıkı bir odak, özellikle daha ince malzemelerde yanma riskini artırabilir. Buna karşılık, odaklanmamış bir ışın, enerjiyi daha geniş bir alana yayarak yanma riskini azaltır ancak aynı zamanda daha sığ penetrasyona ve daha geniş kaynaklara da yol açar.
Optimum odak, eklemin malzemesine, kalınlığına ve geometrisine bağlıdır. Hassas kontrol için, lazer sistemleri genellikle ayarlanabilir odak özelliğine sahiptir ve operatörlerin ışını belirli kaynak gereksinimlerine göre ince ayarlamasına olanak tanır.
Nabız Süresi
Darbeli lazer kaynakta, lazer ışını kısa, yoğun enerji patlamaları halinde iletilir. Bu darbelerin süresi (darbe süresi) nüfuz derinliğini, soğuma hızını ve kaynağın genel kalitesini önemli ölçüde etkileyebilir. Daha kısa darbeler daha kontrollü enerji girişine izin verir ve aşırı ısınmayı önlemeye yardımcı olabilirken, daha uzun darbeler daha derin nüfuz için daha fazla enerji sağlar.
Darbe süresi, kaynak yapılacak malzeme ve kalınlığa göre dikkatlice ayarlanmalıdır. Daha uzun darbeler genellikle daha kalın malzemeler için kullanılırken, termal bozulmayı önlemek için ince malzemeler için daha kısa darbeler kullanılır.
Işın Kalitesi
Işın kalitesi, lazer ışını içindeki enerji dağılımını ifade eder ve lazerin malzemeye ne kadar etkili odaklanabileceğini belirlemede önemli bir faktördür. Yüksek kaliteli bir ışın, tutarlı enerji iletimi ve daha kararlı bir kaynak sağlayan düzgün bir enerji profiline sahiptir. Öte yandan düşük kaliteli ışınlar, eşit olmayan enerji dağılımına yol açabilir ve bu da düşük kaynak kalitesi ve tutarsız birleşim oluşumuyla sonuçlanır.
Yüksek ışın kalitesine sahip lazer kaynak sistemleri genellikle daha temiz, daha hassas ve daha az kusurlu kaynaklar üretir.
Kaynak Hızı
Kaynak hızı, lazerin malzemeye uygulandığı süreyi etkiler. Daha hızlı kaynak hızları genellikle daha düşük ısı girişiyle sonuçlanır, bu da daha küçük ısıdan etkilenen bölgelere ve daha az bozulmaya yol açar. Ancak, hız çok yüksekse, uygun penetrasyon için yeterli zaman olmayabilir ve bu da zayıf bağlantılara neden olabilir. Daha düşük hızlar ısı girişini artırabilir, bu da daha büyük ısıdan etkilenen bölgelere ve potansiyel olarak daha fazla bozulmaya yol açabilir, ancak daha kalın malzemelerin kaynaklanması için gerekli olabilir.
Optimum kaynak hızı, malzeme türü, kalınlığı ve istenen kaynak özelliklerine göre belirlenir.
Koruyucu gaz
Koruyucu gaz, kaynak havuzunu çevreleyen atmosferin oksidasyona veya diğer kusurlara yol açabilecek kirliliğinden korumak için lazer kaynakta kullanılır. Argon, nitrojen veya gaz karışımı gibi kullanılan koruyucu gaz türü, kaynağın mukavemeti, görünümü ve korozyona karşı direnci dahil olmak üzere kaynağın kalitesini etkileyebilir. Ek olarak, koruyucu gaz kaynak havuzunun ısı dağılımını ve soğuma hızını etkileyebilir ve bu da kaynağın mikro yapısını etkiler.
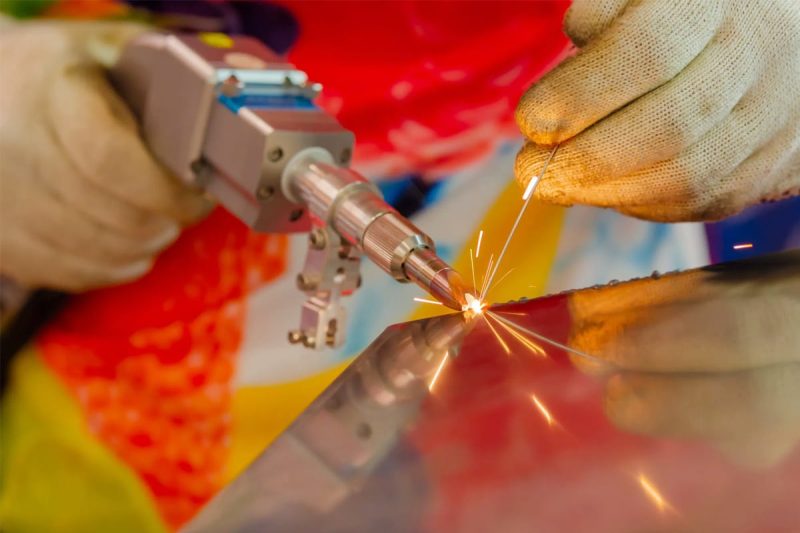
Malzeme Kalınlığı ve Derz Tasarımı
Lazer kaynakta, malzeme kalınlığı ve birleştirme geometrisi kaynak sürecini, gereken enerjiyi ve sonuç olarak kaynak kalitesini önemli ölçüde etkiler. Bu faktörlerin derinlemesine anlaşılması, minimum kusurla optimum kaynaklar elde etmek için kritik öneme sahiptir.
Malzeme kalınlığı
Kaynak yapılan malzemenin kalınlığı, lazer kaynak işlemi üzerinde doğrudan bir etkiye sahiptir. Daha kalın malzemeler, tam penetrasyona ulaşmak ve güçlü bir bağ oluşturmak için daha yüksek lazer gücü gerektirir. Daha kalın malzemeleri kaynak yaparken, aşırı ısınmayı ve bozulmayı önlemek için ısı girişini dikkatli bir şekilde yönetmek gerekir. Daha yüksek bir güç ayarı daha derin penetrasyona izin verir ancak aynı zamanda ısıdan etkilenen bölgenin (HAZ) boyutunu artırabilir ve bu da temel malzemenin mekanik özelliklerini etkileyebilir.
İnce malzemeler için, yanmadan kaçınmak için genellikle daha düşük lazer gücü kullanılır, çünkü bu malzemeler erimek için daha az enerji gerektirir. İnce malzemeleri lazerle kaynaklamanın temel zorluğu, aşırı ısı girişini önlemek için lazer gücünü dengelemek ve malzemeye zarar vermeden yeterli penetrasyon sağlamaktır. Lazer kaynağının hızlı soğutma hızı, daha ince malzemeler için ısıdan etkilenen bölgeyi en aza indirmeye yardımcı olur.
Ortak Geometri
Eklem geometrisi (örneğin, uç birleştirme, T birleştirme, bindirme birleştirme ve köşe birleştirme) lazer kaynağının başarısında önemli bir rol oynar. Lazer kaynak genellikle uç birleştirmelerle en iyi şekilde çalışır, çünkü malzeme kenarlarının doğrudan hizalanması tutarlı bir kaynak havuzu sağlar. Ancak, bindirme birleştirme veya T birleştirme gibi daha karmaşık birleştirmeler, lazerin birleştirmenin tüm taraflarına, malzemeler arasında olabilecek boşluklar dahil, nüfuz etmesini sağlaması gerektiğinden dikkatli ışın hizalaması gerektirir.
Eklem geometrisi karmaşık şekiller veya malzeme kalınlığındaki varyasyonları içerdiğinde, kaynak parametrelerinde ayarlamalar gerekir. Örneğin, üst üste bindirme bağlantıları, üst malzemenin alt malzemeyle etkili bir şekilde kaynaşmasını sağlamak için lazer odağının ve ışın açısının hassas bir şekilde kontrol edilmesini gerektirir. Köşe kaynakları ayrıca lazer ışınının bağlantı yüzeyleriyle etkileşiminin dikkatli bir şekilde kontrol edilmesini gerektirir, çünkü açılar ve malzeme yakınlığı ısı dağılımını etkileyebilir.
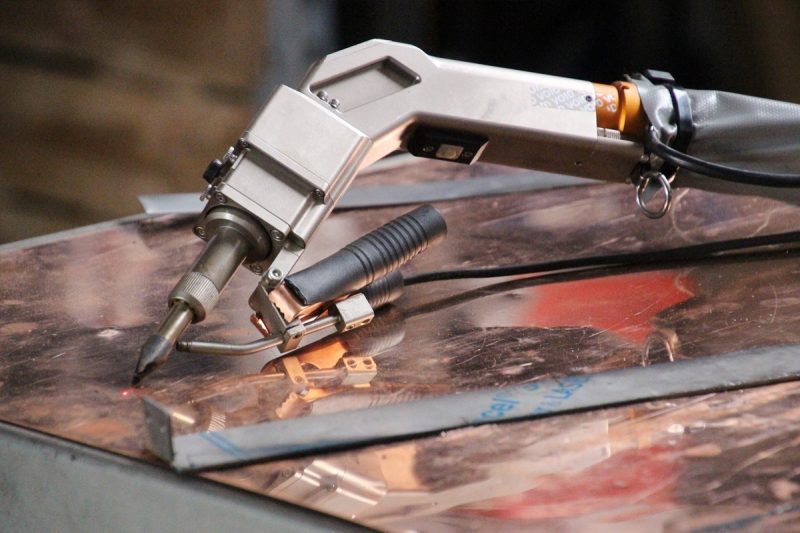
Isı Yönetimi ve Soğutma Oranı
Lazer kaynakta malzeme özelliklerini kontrol etmek, bozulmayı en aza indirmek ve kaynak kusurlarını önlemek için etkili ısı yönetimi çok önemlidir. Isı yönetiminin temel yönleri arasında ısıdan etkilenen bölge (HAZ) ve soğutma hızı yer alır.
Isıdan Etkilenen Bölge (HAZ)
Isıdan etkilenen bölge (HAZ), kaynak sırasında yüksek sıcaklıklar nedeniyle erimeyen ancak mikro yapısında değişiklik yaşayan malzeme bölgesidir. HAZ'ın boyutu ve kapsamı, lazer gücü, kaynak hızı ve malzeme türü tarafından belirlenir. Lazer kaynakta, HAZ, lazer ışınının yoğunlaştırılmış ısısı nedeniyle geleneksel kaynak yöntemlerine kıyasla daha küçük olma eğilimindedir. Ancak, küçük bir HAZ bile, özellikle yüksek dayanımlı çelikler veya termal döngülere duyarlı malzemeler için malzeme özelliklerini etkileyebilir.
Belirli malzemeler için, örneğin yüksek karbonlu çelikler veya titanyum alaşımları, daha büyük bir HAZ, kırılgan davranış veya gerilim korozyon çatlaması gibi mekanik özelliklerin azalmasına yol açabilir. Sonuç olarak, özellikle güç ve hız olmak üzere lazer parametrelerinin dikkatli bir şekilde kontrol edilmesi, eklem arayüzünde yeterli füzyonu sağlarken HAZ'ı en aza indirmek için önemlidir.
Soğutma Oranı
Soğutma oranı veya erimiş kaynak havuzunun katılaşma hızı, kaynağın nihai mikro yapısını ve mekanik özelliklerini belirlemede kritik bir faktördür. Lazer kaynak, küçük ısıdan etkilenen bölge ve erimiş havuzun hızlı katılaşması nedeniyle genellikle çok hızlı soğutma oranlarıyla sonuçlanır. Daha hızlı soğutma oranları, kaynağın mukavemetini artırabilecek daha ince bir mikro yapıyla sonuçlanabilir. Ancak, bu hızlı soğutma aynı zamanda kalıntı gerilimler de oluşturabilir ve bu da özellikle yüksek karbonlu çelikler gibi yüksek sertleştirilebilirliğe sahip olan belirli malzemelerde çatlama veya bozulmaya yol açabilir.
Daha yavaş bir soğutma hızı çatlama riskini azaltabilir, ancak daha büyük tanelerin oluşumuna yol açabilir ve bu da kaynağın genel mukavemetini azaltabilir. Soğutma hızını yönetmek bu faktörleri dengelemek için hayati önem taşır. Kaynak sonrası ısıl işlem (örneğin tavlama) gibi teknikler, kalıntı gerilimleri gidermek ve nihai malzeme özelliklerini iyileştirmek için kullanılabilir.
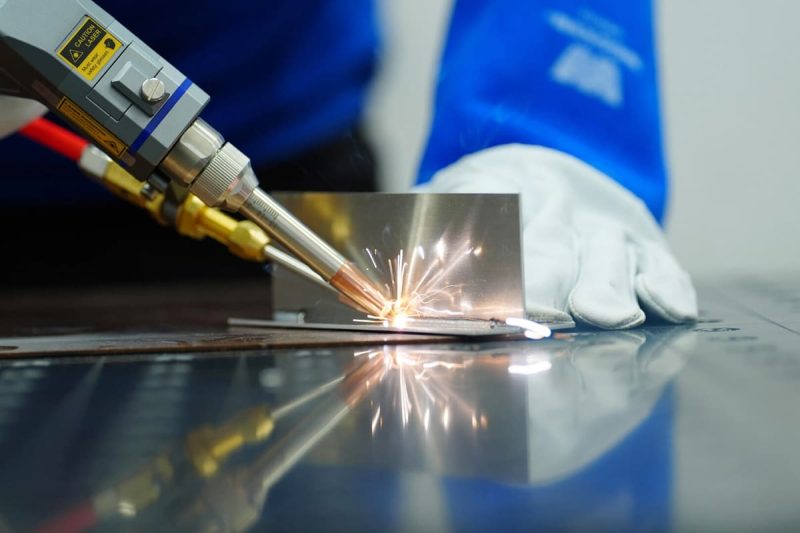
Lazer Kaynak Ekipmanları ve Kurulumu
Lazer kaynağının kalitesi, lazer kaynak ekipmanının türü ve yapılandırmasından büyük ölçüde etkilenir. Ekipmanın temel bileşenleri arasında lazer kaynağı, odaklama merceği, optikler ve kaynak kafası bulunur.
Lazer Kaynak Türü
Kaynaklama sürecinde kullanılan lazer türü, ışın kalitesi, güç ve odaklama dahil olmak üzere işlemin çeşitli yönlerini etkiler. Kaynaklama için yaygın lazer türleri arasında CO2 lazerler, fiber lazerler ve disk lazerler bulunur:
- CO2 lazerler: Yüksek güçleri ve çok yönlülükleri nedeniyle endüstriyel kaynakta en yaygın kullanılan lazerlerdir. CO2 lazerler daha kalın malzemelerin kaynaklanması için idealdir ve sabit bir ışın kalitesi sağlar.
- Fiber lazerler: Bu lazerler yüksek ışın kalitesi ve verimliliğiyle bilinir ve bu da onları ince sac metal kaynaklama için özellikle etkili kılar. Fiber lazerler daha hızlı kaynak hızları sunar ve özellikle düşük termal iletkenliğe sahip malzemelerde CO2 lazerlerden daha yüksek hassasiyete ulaşabilir.
Doğru lazer kaynağının seçimi, malzeme türüne, kalınlığına ve uygulama gereksinimlerine bağlıdır.
Odaklama Merceği ve Optikleri
İstenilen kaynak boyutunu ve penetrasyonu elde etmek için lazer ışını iş parçasına odaklanmalıdır. Odaklama merceğinin ve optiklerin kalitesi ve hizalanması ışın doğruluğu ve kaynak kalitesinde kritik bir rol oynar. Yüksek kaliteli bir optik sistem, lazer ışınının sabit ve odaklanmış kalmasını sağlar; bu özellikle yüksek hassasiyetli uygulamalar için önemlidir.
Merceğin odak uzaklığı, açıklık boyutu ve merceğin konumu, enerjinin malzemenin yüzeyine nasıl dağıtıldığını etkileyebilir. Kötü hizalanmış optikler, odak dışına çıkmaya yol açabilir ve bu da tutarsız enerji iletimi ve potansiyel olarak zayıf veya kusurlu kaynaklarla sonuçlanır.
Kaynak Kafası ve Odaklama Optikleri
Kaynak kafası, lazer ışınını malzemeye yönlendirmekten sorumludur. Kaynak kafasının konumu, eğimi ve hareketi dahil olmak üzere kurulumu, kaynağın düzgünlüğünü ve kalitesini etkiler. Kaynak kafası, lazer ışınının kaynak işlemi boyunca birleştirme noktasına odaklanmasını sağlamak için malzemeyle tam olarak hizalanmalıdır.
Kaynak kafasına ek olarak, ışını şekillendiren ve yönlendiren odaklama optiklerinin düzgün bir şekilde bakımı yapılmalı ve kalibre edilmelidir. Bu optiklerdeki herhangi bir yanlış hizalama veya bozulma, tutarsız ışın iletimine ve düşük kaynak kalitesine yol açabilir.
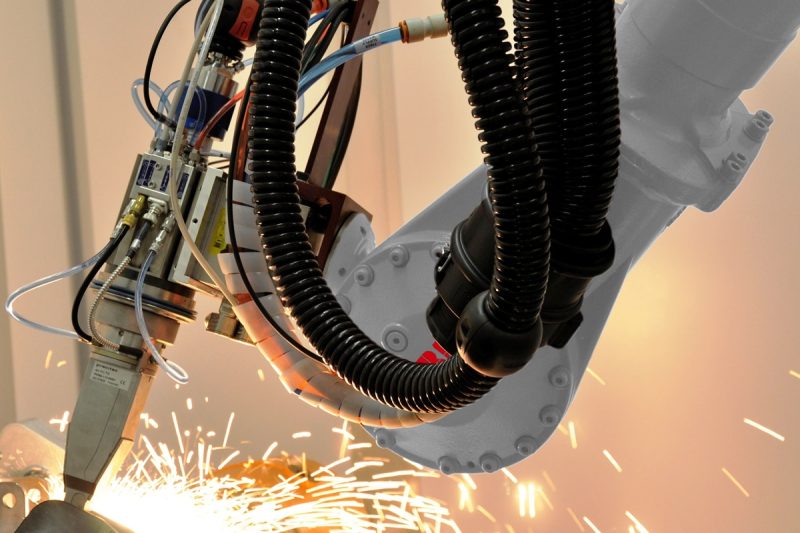
Çevre koşulları
Lazer kaynağının gerçekleştiği çevresel koşullar, kaynağın kalitesi ve tutarlılığı üzerinde önemli bir etkiye sahip olabilir. Dikkate alınması gereken temel çevresel faktörler arasında ortam sıcaklığı ve hava akışı bulunur.
Ortam sıcaklığı
Aşırı sıcaklıklar malzemenin lazer kaynak işlemine verdiği tepkiyi etkileyebilir. Örneğin, malzemeler düşük sıcaklıklarda kırılgan hale gelebilir ve bu da kaynak sırasında çatlama olasılığını artırabilir. Tersine, yüksek ortam sıcaklıkları aşırı malzeme bozulmasına veya termal genleşmeye yol açabilir ve bu da eklem hizalamasını ve kaynak tutarlılığını etkileyebilir. Malzemenin kaynak işlemine öngörülebilir şekilde tepki vermesini sağlamak için sabit bir ortam sıcaklığının korunması çok önemlidir.
Hava Akışı ve Kirleticiler
Toz, yağ, nem veya duman gibi kirleticilerin varlığı kaynak işlemini çeşitli şekillerde etkileyebilir. Havadaki kirleticiler lazer enerjisinin bir kısmını emerek işlemin verimliliğini azaltabilir. Ayrıca, malzeme yüzeyindeki kirlilikler oksidasyona, korozyona veya kaynak kalitesini tehlikeye atan diğer kusurlara yol açabilir.
Uygun havalandırma, temiz yüzeyler ve kapalı bir kaynak odası aracılığıyla kaynak ortamının kontrol edilmesi, kirlenme riskini azaltmaya ve daha tutarlı kaynaklar sağlamaya yardımcı olabilir.

Kaynak Sonrası İşlem
Lazer kaynak işlemi tamamlandıktan sonra, mekanik özellikleri iyileştirmek, kalıntı gerilimleri gidermek ve kaynağın gerekli özelliklere sahip olmasını sağlamak için kaynak sonrası işlemler gerekebilir.
tavlama
Tavlama, kaynaklanmış malzemenin belirli bir sıcaklığa kadar ısıtıldığı ve ardından yavaşça soğutulduğu bir ısıl işlem sürecidir. Bu süreç, kaynak işleminin hızlı ısıtma ve soğutma aşamaları sırasında ortaya çıkmış olabilecek kalıntı gerilimleri gidermek için kullanılır. Tavlama, malzemenin sünekliğini geri kazandırmaya ve çatlama riskini azaltmaya yardımcı olur.
Lazer kaynakta, hızlı soğuma oranları yaşayan malzemeler, kırılganlığı önlemek ve kaynak tokluğunu iyileştirmek için tavlama gerektirebilir. Tam tavlama sıcaklığı ve süresi, malzeme türüne ve kaynağın özel gereksinimlerine bağlıdır.
Yüzey Kaplama ve Temizlik
Kaynaktan sonra, kaynak yüzeyinde oksidasyon, kireç veya çıkarılması gereken diğer kirleticiler olabilir. Kaynak yüzeyinin temizlenmesi ve bitirilmesi, pürüzsüz, kusursuz bir görünüm sağlamak ve kaynaklanmış bölgenin korozyon direncini artırmak için önemlidir.
Temizlik, mekanik parlatma, kimyasal asitleme veya aşındırıcı püskürtme gibi teknikleri içerebilir. Uygun yüzey kalitesi, tıbbi cihazlar veya tüketici elektroniği gibi kaynak estetiği ve malzeme bütünlüğünün en önemli olduğu endüstrilerde özellikle önemlidir.
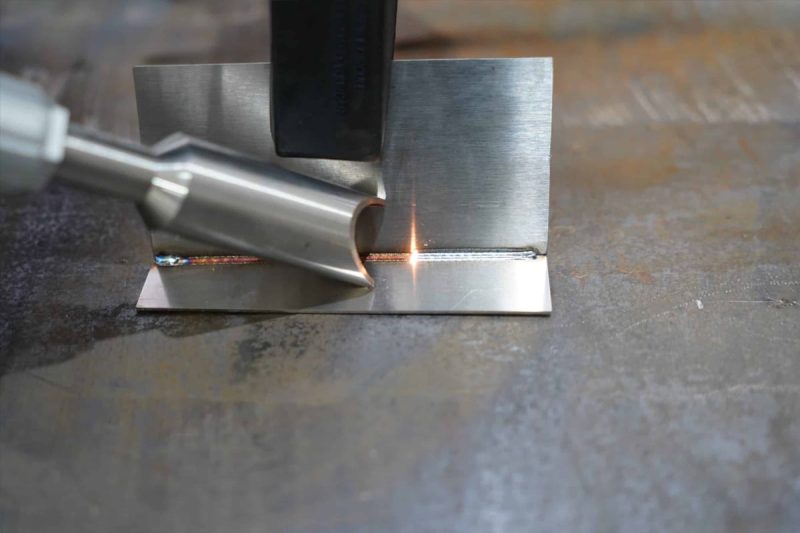
Lazer Kaynakta Karşılaşılan Zorluklar
Lazer kaynak birçok avantaj sunarken, aynı zamanda kendi zorluklarıyla da gelir. Yaygın sorunlar arasında gözeneklilik, çatlama, bozulma ve tutarsız kaynak kalitesi bulunur.
Gözeneklilik
Gözeneklilik, kaynak havuzunda gaz cepleri oluştuğunda ve kaynakta boşluklara yol açtığında oluşur. Bu genellikle katılaşma süreci sırasında sıkışan nitrojen veya oksijen gibi sıkışmış gazlardan kaynaklanır. Gözeneklilik, kaynağı zayıflatabilir ve performansını etkileyebilir. Uygun koruyucu gaz, kaynak parametrelerinin dikkatli kontrolü ve kaynaktan önce temiz yüzeylerin sağlanması gözenekliliği en aza indirmeye yardımcı olabilir.
Çatlama ve Bozulma
Çatlama, özellikle yüksek karbon içeriğine veya düşük sünekliğe sahip malzemelerde lazer kaynakta önemli bir sorundur. Lazer kaynaktaki hızlı soğuma oranları, özellikle ısıdan etkilenen bölgede çatlamaya yol açabilen yüksek kalıntı gerilimler yaratabilir.
Bozulma, malzemenin eğilmesine veya deforme olmasına neden olan eşit olmayan ısıtma ve soğutma nedeniyle de meydana gelebilir. Isı girişini optimum lazer parametreleriyle yönetmek ve sıkıştırma tekniklerini kullanmak bozulmayı azaltmaya yardımcı olabilir.
Kaynak Kalitesinde Tutarsızlık
Tutarlı olmayan kaynak kalitesi, malzeme özelliklerindeki, lazer parametrelerindeki veya çevresel faktörlerdeki değişikliklerden kaynaklanabilir. Lazer gücündeki veya odaktaki dalgalanmalar, eklem hizalamasındaki bozukluklar veya koruyucu gaz akışındaki değişiklikler, tutarsız kaynaklara katkıda bulunabilir. Bu tutarsızlıkları en aza indirmek için, kaynak işlemi üzerinde sıkı bir kontrol sağlamak ve tüm kaynaklarda tekdüzeliği sağlamak için ekipmanı düzenli olarak kalibre etmek esastır.
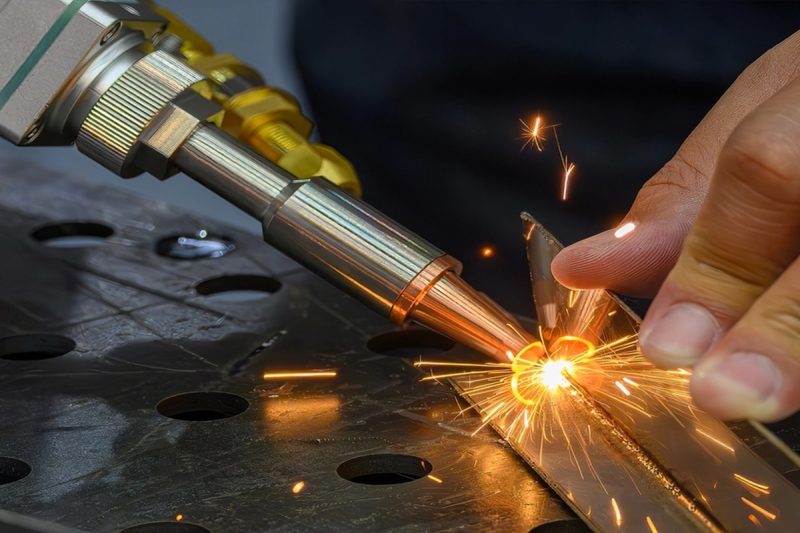
Özet
Lazer kaynakta, malzemelerin kaynaklanabilirliği, malzeme bileşimi ve kalınlığından lazer parametrelerine ve dış çevre koşullarına kadar çok çeşitli faktörlere bağlıdır. Üreticiler, bu faktörleri anlayıp optimize ederek, mukavemet, dayanıklılık ve görünüm için sıkı gereksinimleri karşılayan yüksek kaliteli kaynaklar üretebilirler. Kaynak işlemi sırasında gözeneklilik, çatlama ve bozulma gibi zorluklar ortaya çıkabilse de, kaynak parametrelerinin, ekipmanın ve kaynak sonrası işlemlerin dikkatli bir şekilde kontrol edilmesi ve seçilmesi bu sorunları hafifletebilir ve çeşitli malzemeler ve uygulamalar arasında lazer kaynağının tutarlılığını ve güvenilirliğini artırabilir.
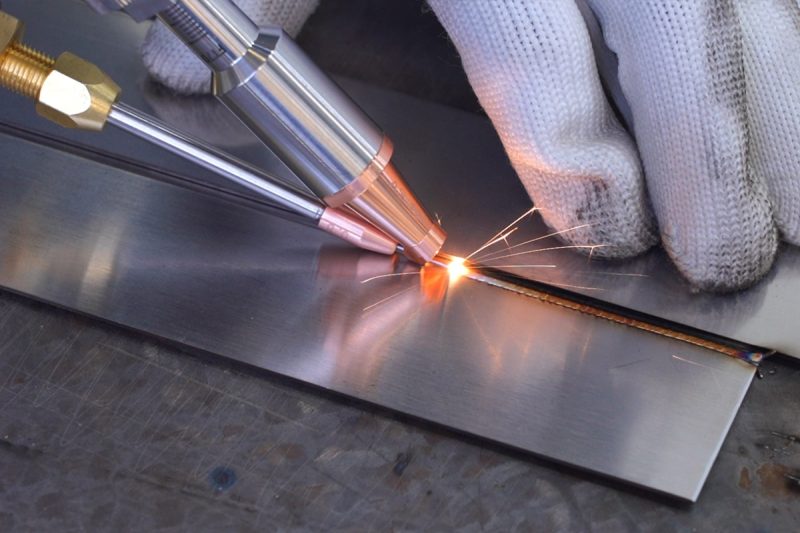
Lazer Kaynak Çözümlerini Alın
Yüksek kaliteli, güvenilir kaynak arayan işletmeler için AccTek Laser, çeşitli endüstriyel ihtiyaçları karşılamak üzere tasarlanmış son teknoloji lazer kaynak çözümleri sunar. Lazer kesim, kaynak, temizleme ve işaretleme makinelerinin profesyonel üreticisi olan AccTek Laser, kaynaklanabilirliği optimize etmek için tasarlanmış son teknoloji ekipmanlar sağlar. İster metallerle, ister plastiklerle veya kompozitlerle çalışın, lazer kaynak makinelerimiz en zorlu uygulamalar için bile hassasiyet, hız ve verimlilik sunar.
AccTek Lazer'in lazer kaynak makineleri lazer gücü, darbe süresi, odak ve kaynak hızı için özelleştirilebilir ayarlarla çeşitli malzemeleri ve kalınlıkları işlemek üzere tasarlanmıştır ve kaynaklarınızın en yüksek standartları karşılamasını sağlar. Uzman ekibimiz doğru ekipmanı seçmenize, sistemi özel ihtiyaçlarınıza göre yapılandırmanıza ve üretim süreci boyunca optimum performansı garantilemek için sürekli destek sunabilir.
AccTek Laser'i seçerek, ileri teknolojiye ve kaynak kalitenizi ve üretkenliğinizi artırmaya kendini adamış bir ortağa erişebilir, böylece her seferinde kusursuz, dayanıklı kaynaklar elde etmenize yardımcı olabilirsiniz.
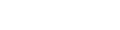
İletişim bilgileri
- [email protected]
- [email protected]
- +86-19963414011
- 3 Bölge A, Lunzhen Sanayi Bölgesi, Yucheng Şehri, Shandong Eyaleti.
Lazer Çözümleri Alın