
Lazer Kaynak Ne Kadar Sıcaktır?
Lazer kaynak, verimli ve hassas bir kaynak teknolojisidir. Özü, malzemeyi yerel olarak eritmek ve hızlı soğutma yoluyla güçlü bir bağlantı elde etmek için yüksek yoğunluklu bir lazer ışını kullanmaktır. Geleneksel kaynak yöntemlerinden farklı olarak, lazer kaynağının enerjisi yoğunlaştırılır ve kontrol edilebilir ve çalışma sıcaklığı son derece yüksektir, kolayca 6000℃'ye veya daha yükseğe ulaşabilir, bu da çoğu metali ve alaşımı eritmek için yeterlidir. Sıcaklık, lazer kaynak sürecinde kritik bir parametredir. Sadece malzemenin erime hızını ve kaynak derinliğini belirlemekle kalmaz, aynı zamanda kaynaklı eklemin mukavemetini ve yüzey kalitesini de etkiler. Lazer ışınının oldukça yoğun ısı girişi nedeniyle, lazer kaynağı hız, hassasiyet ve ısıdan etkilenen bölge (HAZ) kontrolünde belirgin avantajlara sahiptir ve bu da onu birçok alanda tercih edilen işlem haline getirir.
Lazer kaynakta sıcaklık kontrolü, işlemin uygunluğunu ve nihai performansını da doğrudan etkiler. Kaynak sıcaklığı çok yüksekse, malzeme aşırı yanabilir veya gözenekler ve çatlaklar gibi kaynak kusurları ortaya çıkabilir; sıcaklık çok düşükse, malzeme tamamen erimeyebilir ve bu da eksik kaynak penetrasyonu gibi sorunlara yol açabilir. Ayrıca, kaynak malzemesinin türü, lazer gücü, ışın odağı ve kaynak hızı gibi çeşitli faktörler kaynak sıcaklığı üzerinde önemli bir etkiye sahip olacaktır. Gerçek operasyonlarda, mühendisler genellikle kaynak etkisini, malzemenin erime noktasına ve ısıl iletkenliğine göre işlem parametrelerini ayarlayarak optimize ederler. Tam da bu hassas sıcaklık kontrolü sayesinde lazer kaynak, otomobil üretimi, havacılık ve tıbbi ekipman gibi yüksek talep gören endüstrilerde yaygın olarak kullanılabilir ve üstün performansını ve uyarlanabilirliğini kanıtlamıştır.
İçindekiler
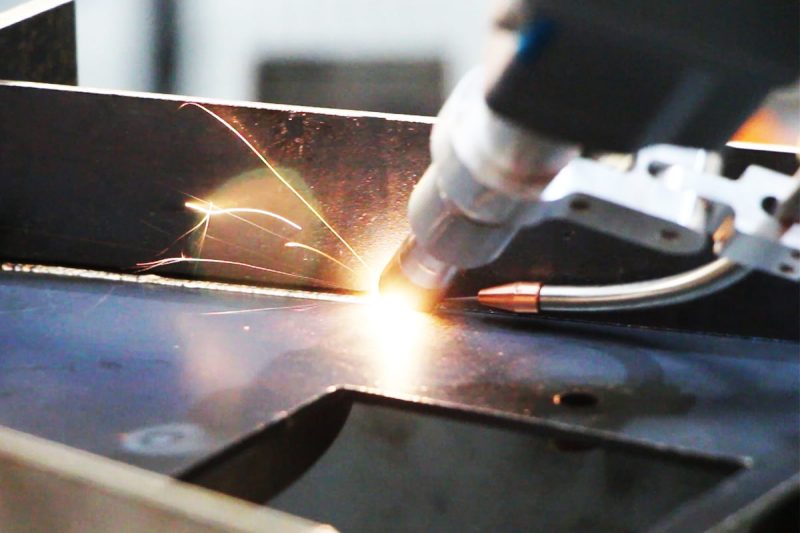
Lazer Kaynak Sıcaklıklarını Anlamak
Lazer Kaynakta Yüksek Sıcaklık Prensibi
odaklanmış lazer ışınının yüksek enerji yoğunluğu sayesinde güçlü bir kaynak bağlantısı oluşturmak için malzeme. Lazer kaynak işlemi sırasında, lazer ışınının odak sıcaklığı çok yüksek olabilir, genellikle 6000℃'yi aşabilir ve hatta bazı durumlarda 10000℃'ye kadar çıkabilir. Bu yüksek sıcaklık, hemen hemen tüm yaygın metal malzemeleri eritmek için yeterlidir, örneğin paslanmaz çelik, alüminyum alaşımı, bakırve titanyum alaşımı. Lazer kaynağının yüksek sıcaklık özellikleri, eritme ve kaynaklama işleminin kısa sürede tamamlanmasını sağlar ve yoğunlaştırılmış ısı girişi nedeniyle ısıdan etkilenen bölge (HAZ) en aza indirilebilir, böylece termal deformasyon ve kalıntı gerilim riski azaltılabilir.
Geleneksel kaynak yöntemleriyle karşılaştırıldığında lazer kaynak yönteminin aşağıdaki benzersiz avantajları vardır:
- Yüksek enerji yoğunluğu: Lazer kaynağının odak alanındaki enerji yoğunlaşmıştır, bu da metali hızla eritebilir ve hassas kaynak için uygundur.
- Yüksek kontrol hassasiyeti: Lazer gücü, ışın odağı ve diğer parametreler, son derece kontrol edilebilir bir sıcaklık dağılımı sağlamak için doğru bir şekilde ayarlanabilir.
- Hızlı ısıtma: Lazer kaynak, metali milisaniyeler içinde hızla eritebilir ve kaynak hızını önemli ölçüde artırabilir.
Lazer Kaynak Sıcaklığının Diğer Kaynak İşlemleriyle Karşılaştırılması
Diğer geleneksel kaynak işlemleriyle karşılaştırıldığında, lazer kaynak farklı sıcaklık özelliklerine ve ısıdan etkilenen modlara sahiptir. Aşağıda lazer kaynak, ark kaynak ve direnç kaynak arasındaki sıcaklık karşılaştırması verilmiştir:
Lazer kaynak
- Sıcaklık aralığı: genellikle 6000℃ ile 10000℃ arasındadır, odak alanındaki sıcaklık çok yüksek olabilir.
- Sıcaklık dağılımı: Lazer kaynakta sıcaklık kaynak bölgesinde yoğunlaşır ve çevredeki malzemelere neredeyse hiç ısı yayılmaz.
- Özellikler: Yüksek yoğunluklu sıcaklık ve hassas kontrol sayesinde lazer kaynak, çok kısa sürede, hızlı kaynak hızı ve küçük bir ısıdan etkilenen bölge ile eritmeyi tamamlayabilir. Kaynak doğruluğu ve kalitesi için son derece yüksek gereksinimlerin olduğu sahneler için uygundur.
Ark Kaynağı
- Sıcaklık aralığı: Ark tipine ve kaynak koşullarına bağlı olarak genellikle 3500℃ ile 6000℃ arasındadır.
- Sıcaklık dağılımı: Ark kaynağı geniş bir sıcaklık dağılımına sahiptir ve sıcaklık daha geniş bir alana yayılacağından, daha geniş bir ısıdan etkilenen bölge oluşabilir.
- Özellikler: Ark kaynağı genellikle daha kalın malzemelerin kaynaklanmasında kullanılır. Sıcaklık daha yüksek olmasına rağmen, büyük ısı girişi nedeniyle daha fazla termal deformasyona ve strese neden olabilir ve kontrol doğruluğu nispeten zayıftır.
Direnç Kaynağı
- Sıcaklık aralığı: Direnç kaynağının sıcaklığı genellikle 3000℃'nin altındadır ve temas noktasında yoğunlaşır.
- Sıcaklık dağılımı: Direnç kaynağında sıcaklık esas olarak iki elektrodun malzemeye temas ettiği ve lokal ısınmanın oluştuğu bölgede yoğunlaşır.
- Özellikler: Direnç kaynağı ince levha malzemelerinin kaynaklanması için uygundur. Düşük sıcaklık ve yoğun kaynak alanı aşırı ısınmayı önlemeye yardımcı olur, ancak uygulama aralığı dardır.
Lazer kaynak, yüksek sıcaklık ve yoğunlaştırılmış ısı girişi özellikleri nedeniyle kaynak sıcaklığının hassas bir şekilde kontrol edilmesini ve küçük ısıdan etkilenen bölge gerektiren yüksek hassasiyetli kaynak görevleri için uygundur. Geleneksel ark kaynağı ve direnç kaynak işlemleriyle karşılaştırıldığında, lazer kaynak daha yüksek enerji yoğunluğu, daha hızlı bir kaynak işlemi ve daha küçük bir ısıdan etkilenen bölge sağlar ve bu da onu havacılık, otomobil üretimi, elektronik ekipman ve diğer alanlarda yaygın olarak kullanılmasını sağlar. Farklı kaynak işlemlerinin sıcaklık kontrolü ve kaynak kalitesindeki farklılıklar, bunların farklı malzemeler ve endüstriyel ihtiyaçlarda avantajları ve sınırlamaları olmasını sağlar.
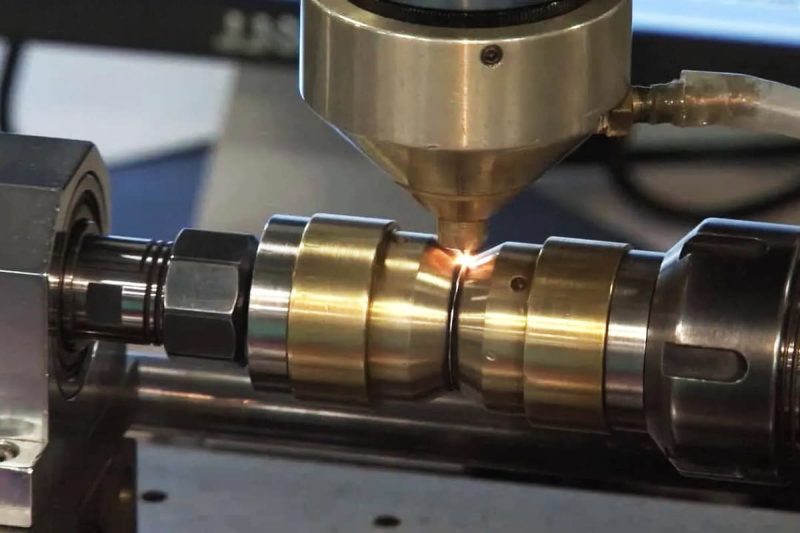
Kaynak Sıcaklığını Etkileyen Faktörler
Lazer kaynak hassas bir kaynak teknolojisidir ve kaynak sıcaklığı birçok faktörden etkilenir. Bu faktörler doğrudan kaynak etkisi, kaynak kalitesi ve nihai ürünün performansıyla ilgilidir. Daha sonra, birkaç önemli faktörün lazer kaynak sıcaklığını nasıl etkilediğini ayrıntılı olarak tartışacağız.
Lazer Gücü
Lazerin çıkış gücü, lazer kaynak sıcaklığını etkileyen en kritik faktörlerden biridir. Güç ne kadar yüksekse, lazer ışını tarafından yayılan enerji o kadar büyük olur ve eritilebilen malzeme o kadar kalın olur, ancak aşırı yanma ve termal hasar gibi sorunlara da neden olabilir.
- Yüksek güçlü lazer: daha kalın malzemeler için kullanılır, malzemeyi eritmek için yeterli enerjiyi hızla sağlayabilir. Endüstriyel sınıfın gücü lazer kaynak makineleri genellikle 500W ile 6000W arasındadır. Farklı ihtiyaçlara göre güç, farklı malzemelerin kalınlığına ve türüne uyum sağlayacak şekilde ayarlanabilir. Daha yüksek güçlü lazer kaynağı kalın malzemeler ve büyük ölçekli üretim için uygundur, ancak aynı zamanda ısı birikimine neden olma olasılığı daha yüksektir ve bu da termal deformasyona veya düzensiz kaynaklamaya neden olur.
- Düşük güçlü lazer: İnce malzemeler için uygundur, kontrollü ısı girişiyle ince kaynak yapabilir. Düşük güçlü lazer kaynağı, malzeme üzerindeki termal etkiyi azaltabilir, ancak güç çok düşükse, malzemeyi tamamen eritemeyebilir ve bu da kaynak bağlantısının yetersiz mukavemetine neden olabilir.
Işın Odaklanması
Işının odağı, lazer kaynağının sıcaklık dağılımını belirleyen temel faktörlerden biridir. Lazer ışınının odaklanma derecesi, enerji yoğunluğunu doğrudan etkiler ve bu da kaynak işlemi sırasında sıcaklığı belirler.
- Hassas odaklama: Lazer ışını ne kadar hassas odaklanırsa, enerji yoğunluğu ve sıcaklık o kadar yüksek olur ve bu da malzemeyi hızla eritebilir ve kaynak işlemini tamamlayabilir. Hassas odaklama, kaynak sırasında düzgün ısı dağılımını ve iyi kaynak sonuçlarını sağlayabilir.
- Odak kayması: Lazer ışınının odağı kaymışsa veya odaklama yeterince hassas değilse, enerji dağılımı eşit olmaz ve kaynak alanının sıcaklığı da eşit olmaz; bu da kaynaklı birleştirmenin düşük mukavemetine veya hatta soğuk kaynak ve çatlaklar gibi kalite sorunlarına yol açabilir.
Malzeme Türü
Farklı malzemelerin termal iletkenlik özellikleri ve erime noktası farklılıkları, gerekli kaynak sıcaklığını belirler. Malzemenin termal iletkenliği, erime noktası ve yansıtıcılığı, lazer kaynak sonuçlarını önemli ölçüde etkileyebilir.
- Isıl iletkenlik: Yüksek ısıl iletkenliğe sahip malzemeler (bakır ve alüminyum gibi) kaynak alanından çevreye hızla ısı yayabilir, bu da bu malzemeleri eritmek için daha yüksek sıcaklıklara ihtiyaç duyulduğu anlamına gelir. Buna karşılık, düşük ısıl iletkenliğe sahip malzemeler (paslanmaz çelik ve titanyum gibi) yerel bir alanda ısı biriktirme olasılığı daha yüksektir, bu nedenle gerekli kaynak sıcaklığına ulaşmak nispeten kolaydır.
- Erime noktası: Farklı malzemelerin erime noktalarındaki fark da doğrudan kaynak sıcaklığını etkiler. Örneğin, paslanmaz çeliğin erime noktası 1450℃ iken, alüminyum alaşımının erime noktası daha düşüktür, yaklaşık 660℃. Bu, paslanmaz çeliğin kaynaklanmasının daha yüksek sıcaklıklar ve daha güçlü lazer gücü gerektirdiği, alüminyum alaşımlarının kaynaklanmasının ise daha düşük sıcaklıklar kullanabileceği anlamına gelir.
Kaynak Hızı
Kaynak hızı, sıcaklığı etkileyen bir diğer önemli faktördür. Kaynak hızı, malzemenin birim zaman başına ısı girişini belirler ve bu da kaynak sıcaklığını etkiler.
- Daha yüksek kaynak hızı: Kaynak hızı daha yüksek olduğunda, lazer ışını kaynaktan daha kısa bir süre geçer ve malzemeye ısı girişi azalır. Bu, kaynak bölgesinde daha düşük bir sıcaklık ve daha az ısı birikimiyle sonuçlanacak ve bu da ısıdan etkilenen bölgeyi, deformasyonu ve artık gerilimi azaltmaya yardımcı olacaktır. Ancak, çok hızlı olan kaynak hızları kaynak metalinin yetersiz erimesine neden olarak kaynak kalitesi sorunlarına yol açabilir.
- Düşük kaynak hızı: Daha düşük kaynak hızları, lazer ışınının kaynak bölgesinde daha uzun süre kalmasını sağlayarak ısının birikmesine ve dolayısıyla kaynak bölgesinin sıcaklığının artmasına olanak tanır. Bu, daha kalın malzemelerin kaynaklanmasına yardımcı olur ancak aynı zamanda ısıdan etkilenen bölgenin aşırı ısınmasına, deformasyonuna ve genişlemesine de yol açabilir.
Lazer kaynak sıcaklığı, lazer gücü, ışın odağı, malzeme türü ve kaynak hızı gibi birçok faktörden etkilenir. Her faktör kaynak sıcaklığını farklı derecelerde etkiler ve böylece kaynaklamanın etkisi ve kalitesi belirlenir. Gerçek operasyonda, sorunsuz bir kaynaklama işlemi sağlamak ve yüksek kaliteli kaynaklı bağlantılar elde etmek için kaynak parametrelerinin malzeme türüne, kalınlığa ve işlem gereksinimlerine göre optimize edilmesi gerekir.
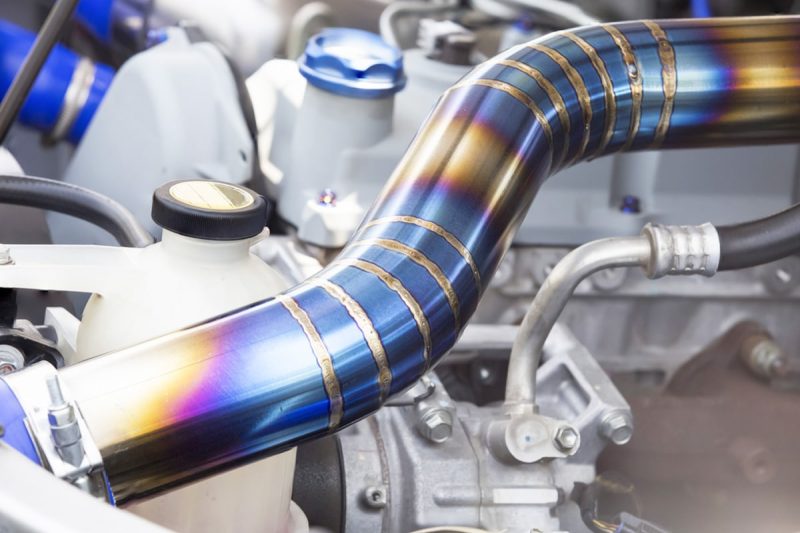
Lazer Kaynak Sıcaklık Aralığı
Lazer kaynak, malzemeyi yoğunlaştırılmış enerjili lazer ışınıyla ısıtan yüksek hassasiyetli bir kaynak işlemidir. Kaynak işlemi sırasında sıcaklık dağılım aralığı, malzemenin erime noktasından kaynak bölgesinin tepe sıcaklığına kadar geniştir. Sıcaklığın kontrolü ve yönetimi, kaynak kalitesi için kritik öneme sahiptir. Aşağıda, malzeme erime noktası, ısıdan etkilenen bölge (HAZ) sıcaklığı ve kaynak havuzunun tepe sıcaklığı dahil olmak üzere lazer kaynaktaki sıcaklığın çeşitli yönleri ayrıntılı olarak ele alınacaktır.
Malzeme Erime Noktası
Lazer kaynak işlemi sırasında, lazer ışını malzemeyi eritmek ve kaynaklı bir bağlantı oluşturmak için malzemeyi erime noktasının üzerine ısıtmalıdır. Farklı malzemelerin farklı erime noktaları vardır ve bu da lazer kaynak için gereken sıcaklığı doğrudan etkiler. Yaygın malzemelerin erime noktası aralıkları şunlardır:
- Çelik: Çeliğin erime noktası genellikle 1200℃ ile 1500℃ arasındadır. Erime noktası, çeliğin türüne (karbon çeliği, alaşımlı çelik vb.) bağlı olarak değişir. Karbon çeliğinin erime noktası nispeten düşüktür, alaşımlı çelik ve paslanmaz çeliğin erime noktaları ise daha yüksek olabilir.
- Alüminyum: Alüminyumun erime noktası nispeten düşüktür, genellikle 600℃ ile 700℃ arasındadır. Daha düşük erime noktası nedeniyle alüminyumun lazerle kaynaklanması daha kolaydır, ancak aynı zamanda aşırı ısınmaya karşı daha hassastır ve bu da termal deformasyona neden olur.
- Titanyum alaşımı: Titanyum alaşımının erime noktası yaklaşık 1660℃'dir ve bu çelik ve alüminyumdan daha yüksektir. Bu nedenle, titanyum alaşımı kaynak yaparken, erime ve kaynak kalitesini sağlamak için lazer sıcaklığının daha yüksek bir aralıkta kontrol edilmesi gerekir.
Bu erime noktası aralıkları, lazer gücünün seçimini ve ayarlanmasını belirler ve ayrıca kaynak işlemi sırasında termal yönetim konusunda gereklilikler getirir.
Isıdan Etkilenen Bölge (HAZ) Sıcaklığı
Isıdan etkilenen bölge (HAZ), kaynak işlemi sırasında lazer ışınının ısınması nedeniyle malzeme sıcaklığının yükseldiği ancak erime noktasına ulaşmadığı alanı ifade eder. Bu alanda erime gerçekleşmese de, sıcaklık artışı nedeniyle malzemenin mikro yapısı değişecektir ve bu da malzemenin mekanik özelliklerini etkileyebilir.
- Sıcaklık aralığı: Isıdan etkilenen bölgenin sıcaklığı genellikle malzemenin erime noktasından daha düşüktür, ancak malzemenin kafes yapısında değişikliklere neden olmaya yeterlidir, genellikle 500°C ile 1000°C arasında değişir. Bazı yüksek mukavemetli malzemeler için bu sıcaklıklar sertlik değişikliklerine neden olmak için yeterlidir ve hatta kırılganlığa neden olabilir.
- Etkileyen faktörler: Isıdan etkilenen bölgenin sıcaklığı, lazer gücü, ışın odağı, kaynak hızı ve malzemenin termal iletkenliği gibi birçok faktörden etkilenir. Lazer gücü ne kadar büyük ve kaynak hızı ne kadar yavaşsa, ısıdan etkilenen bölge o kadar büyük ve sıcaklık o kadar yüksek olur.
Kaynaklı eklemin kalitesini sağlamak için HAZ sıcaklığını kontrol etmek çok önemlidir. Aşırı HAZ sıcaklığı, malzeme performansında düşüşe yol açabilir ve hatta genel kaynak mukavemetini ve yorulma ömrünü etkileyebilir.
Tepe Kaynak Havuzu Sıcaklığı
Kaynak havuzu, lazer kaynak işlemi sırasında erimiş metal tarafından oluşturulan sıvı metal alanıdır. Kaynak havuzunun tepe sıcaklığı, kaynak işlemi sırasında en yoğun sıcaklıktır ve genellikle kaynak bölgesinin merkezinde bulunur. Kaynak havuzunun sıcaklığı genellikle 3000℃ ile 6000℃ arasındadır, bu çoğu metali eritmek için yeterlidir ve güçlü bir kaynak bağlantısı oluşturmanın anahtarıdır.
- Kaynak havuzu sıcaklık aralığı: Kaynak havuzunun sıcaklığı, malzeme ve lazer parametrelerine bağlı olarak değişebilir. Yüksek erime noktasına sahip malzemeler (titanyum alaşımları, paslanmaz çelik vb.) için kaynak havuzunun sıcaklığı 3000°C'nin üzerine çıkabilirken, düşük erime noktasına sahip malzemeler (alüminyum alaşımları gibi) için sıcaklık nispeten düşüktür, genellikle 3000°C ile 4500°C arasındadır.
- Sıcaklığın kaynak kalitesi üzerindeki etkisi: Kaynak havuzu sıcaklığı, erimiş havuzun derinliğini ve genişliğini ve ayrıca son kaynak bağlantısının şeklini doğrudan belirler. Çok yüksek bir kaynak havuzu sıcaklığı, erimiş havuzun çok derin olmasına neden olarak termal deformasyon riskini artırabilirken, çok düşük bir sıcaklık yetersiz kaynak ve yetersiz bağlantı mukavemeti ile sonuçlanabilir.
Lazer kaynak sırasında sıcaklık, malzemenin erime noktasından kaynak havuzunun tepe sıcaklığına kadar değişir. Erime noktası, lazerin ulaşması gereken minimum sıcaklığı belirlerken, ısıdan etkilenen bölgenin sıcaklığı ve kaynak havuzunun tepe sıcaklığı, kaynağın derinliğini, eklemin mukavemetini ve malzemenin nihai özelliklerini etkiler. Farklı malzemeler, kaynak parametreleri ve işlem ayarları, kaynak sırasında sıcaklık dağılımını etkileyecektir, bu nedenle gerçek işlemde, kaynağın kalitesini ve kaynaklı eklemin güvenilirliğini sağlamak için sıcaklığın hassas bir şekilde kontrol edilmesi gerekir.
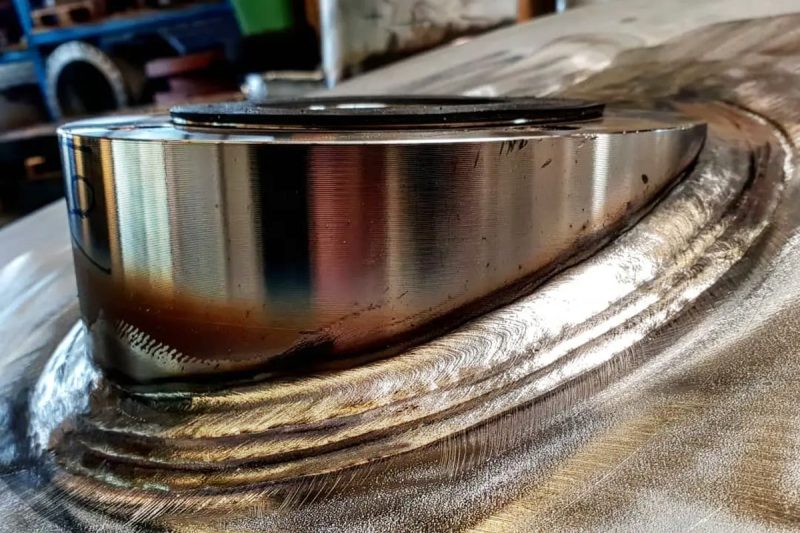
Sıcaklığın Kaynak Kalitesi ve Performansı Üzerindeki Etkisi
Sıcaklık, lazer kaynaklama sürecinde kritik bir faktördür ve kaynak kalitesini, malzeme özelliklerini ve son iş parçasının performansını etkiler. Lazer kaynaklama, malzemenin eriyip birleşecek kadar yeterli bir sıcaklığa ısıtılmasını gerektirir, ancak çok yüksek veya çok düşük sıcaklıklar kaynak kalitesi ve malzeme özellikleri üzerinde olumsuz bir etkiye sahip olacaktır. Aşağıda, sıcaklığın kaynak kalitesi ve performansı üzerindeki belirli etkileri ayrıntılı olarak ele alınmaktadır.
Malzeme özellikleri
Kaynak işlemi sırasında sıcaklık değişimleri malzemenin mikro yapısında değişikliklere neden olacak ve bu durum kaynaklı birleştirmenin mekanik özelliklerini doğrudan etkileyecektir.
- Tanecik incelmesi veya kabalaşması: Lazer kaynaklama sırasında, malzeme hızlı bir şekilde ısıtılır ve soğutulur ve sıcaklık değişiklikleri tanecik incelmesine veya kabalaşmasına yol açabilir. Taneciklerin boyutu, malzemenin mukavemetini ve tokluğunu doğrudan etkiler. Çok yüksek bir sıcaklık tanecik incelmesine yol açarak kaynaklı eklemin mukavemetini azaltabilir. Tersine, daha düşük kaynak sıcaklıkları çok fazla ince taneciğe yol açabilir ve bu da kaynaklı bölgenin tokluğunu zayıflatabilir.
- Faz değişimi: Bazı malzemeler ısıtma sırasında faz değişimlerine uğrar, örneğin çelik yüksek sıcaklıklarda ferritten ostenite dönüşür. Bu faz değişimi, malzemenin mekanik özelliklerinde değişikliklere neden olabilir. Farklı kaynak sıcaklıklarında farklı ısıl işlem süreçleri (tavlama, söndürme gibi) de meydana gelebilir ve bu da malzemenin sertliğini, çekme mukavemetini ve yorulma direncini etkiler.
Kaynak Kalitesi
Sıcaklığın kaynaklı birleştirmelerin kalitesi, özellikle birleştirme bütünlüğü ve stabilitesi üzerinde doğrudan etkisi vardır.
- Çok yüksek sıcaklık: Çok yüksek sıcaklık, gözenekler, çatlaklar, aşırı yanma vb. dahil olmak üzere bir dizi kaynak kusuruna neden olabilir. Yüksek sıcaklıklarda, metal erimiş havuzu çok büyüktür ve gaz kolayca erimiş havuza girebilir ve gözeneklerin oluşmasına neden olabilir. Ek olarak, yüksek sıcaklıklar ayrıca malzemenin yüzeyinde oksidasyon veya kırılgan fazlara neden olarak kaynak çatlakları riskini artırabilir. Çok yüksek sıcaklık ayrıca malzemenin aşırı yanmasına neden olarak kaynak alanının aşırı erimiş hale gelmesine ve sonuçta eklemin mukavemetinin azalmasına neden olabilir.
- Çok düşük sıcaklık: Kaynak sıcaklığı çok düşük olduğunda, metal tamamen eritilemez ve bu da eksik penetrasyona neden olabilir. Eksik penetrasyon, kaynak bağlantısının erimiş kısmının tamamen birleşmemesi ve bunun sonucunda bağlantı mukavemetinde azalma olması anlamına gelir. Ek olarak, daha düşük kaynak sıcaklıkları da kaynaklı bağlantıların düzensiz yüzeylerine, soğuk çatlaklara veya düşük çekme mukavemetine neden olabilir.
Kalıntı Gerilim ve Deformasyon
Lazer kaynakta yüksek sıcaklığın etkisiyle kaynak bölgesinde termal genleşme ve büzülme meydana gelir, bu da kalıntı gerilmelere ve termal deformasyonlara neden olur.
- Kalıntı gerilim: Yüksek sıcaklıkta kaynaklama sırasında, metal genleşme ve büzülme yaşayacak ve kaynaklanmış alanın termal genleşmesi genellikle kaynaklanmamış alandan daha büyük olacak ve bu da kalıntı gerilim üretecektir. Aşırı kalıntı gerilim, malzemenin kullanım sırasında deforme olmasına ve hatta eklemin kopmasına veya yorulma arızasına neden olabilir. Kalıntı gerilimin varlığı ayrıca kaynaklanmış parçada çatlak yayılmasına neden olarak genel yapının güvenilirliğini etkileyebilir.
- Termal deformasyon: Lazer kaynağının yüksek sıcaklığı, özellikle ince malzemelerde malzemenin termal deformasyonuna neden olabilir. Termal deformasyonun derecesi, kaynak sıcaklığı, malzemenin termal genleşme katsayısı ve kaynak hızı gibi faktörlere bağlıdır. Termal deformasyon, parçaların yanlış boyutlarına neden olabilir ve böylece parçaların montajını ve işlevini etkileyebilir. Özellikle havacılık ve elektronik üretimi gibi bazı hassas üretim endüstrilerinde, aşırı termal deformasyon, parçaların tolerans gereksinimlerini karşılayamamasına neden olabilir.
Kaynak Sonrası Isıl İşlem ve Düzeltme
Kaynak sırasında oluşan kalıntı gerilmeyi ve termal deformasyonu kontrol altına almak ve azaltmak için genellikle kaynak sonrasında uygun ısıl işlem veya düzeltme yapılması gerekir.
- Isıl işlem: Kaynaktan sonra, malzemelerin genellikle kalıntı gerilimi ortadan kaldırmak, malzemenin mikro yapısını optimize etmek ve mekanik özelliklerini iyileştirmek için tavlanması, normalleştirilmesi veya söndürülmesi gerekir. Isıtma ve soğutma sürecini kontrol ederek, aşırı yüksek veya düşük sıcaklıkların neden olduğu olumsuz etkiler etkili bir şekilde azaltılabilir.
- Düzeltme: Daha büyük termal deformasyonlar için, iş parçasının şekil ve boyut sapmalarını düzeltmek için genellikle mekanik düzeltme veya lazer tesviye teknolojisinin kullanılması gerekir. Bu, kaynaklı parçanın orijinal şeklini geri kazandırmaya ve kullanım sırasında doğruluğunu ve kararlılığını sağlamaya yardımcı olur.
Sıcaklığın lazer kaynak işleminin kalitesi ve performansı üzerinde derin bir etkisi vardır. Malzemenin mikro yapısal değişikliklerinden kaynaklı eklemin mukavemetine ve kararlılığına, kaynak işlemi sırasında oluşan kalıntı gerilime ve termal deformasyona kadar, sıcaklık kontrolü kaynak kalitesini sağlamanın anahtarıdır. Çok yüksek veya çok düşük sıcaklık kaynak hatalarına neden olabilir ve nihai ürünün performansını ve güvenilirliğini etkileyebilir. Bu nedenle, lazer kaynak işleminde, yüksek kaliteli kaynaklı eklemler elde etmek için hassas sıcaklık kontrolü ve kaynak parametrelerinin makul yönetimi esastır.
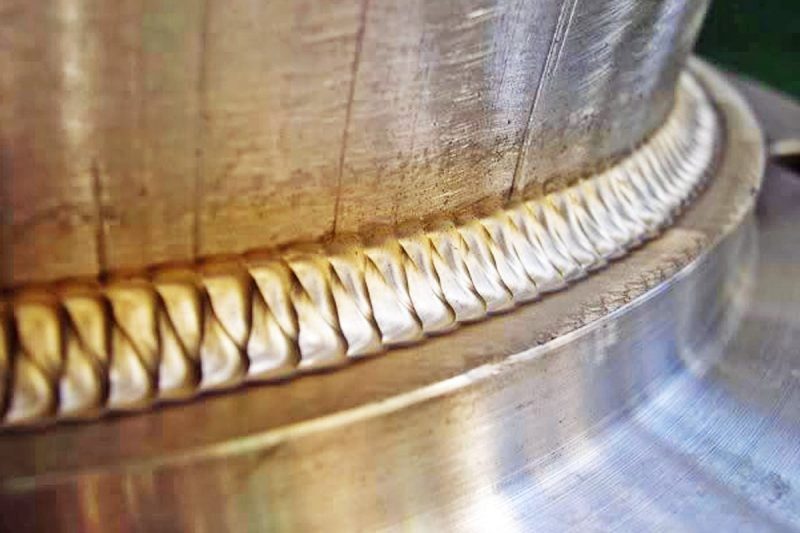
Lazer Kaynak Sıcaklığının Kontrolü
Yüksek kaliteli kaynak sonuçları sağlamak için, lazer kaynak sıcaklığını doğru bir şekilde kontrol etmek esastır. Kaynak sıcaklığı, kaynaklı eklemin mukavemetini, kaynaklı alanın mikro yapısını ve nihai ürünün performansını doğrudan etkiler. Aşağıda, kaynak sürecini optimize etmeye ve kaynak kalitesinin kararlılığını ve tutarlılığını sağlamaya yardımcı olan sıcaklığı kontrol etmek için yaygın olarak kullanılan bazı stratejiler verilmiştir.
İşlem Parametrelerini Ayarla
Kaynak işlemi sırasında lazer gücü, kaynak hızı ve ışın modu gibi işlem parametreleri kaynak sıcaklığını etkileyen temel faktörlerdir. Bu parametrelerin doğru bir şekilde ayarlanması istenilen sıcaklık kontrolünün elde edilmesine yardımcı olur.
- Lazer gücü: Lazer gücü, erimiş havuzun sıcaklığını etkileyen enerji girişinin miktarını doğrudan belirler. Daha yüksek güç, kalın malzemelerin kaynaklanması için uygundur ancak aşırı yanmaya veya termal hasara neden olabilir. Daha düşük güç, ince malzemelerin kaynaklanması için uygundur ancak eksik penetrasyona neden olabilir. Güç, malzemenin kalınlığına ve kaynak gereksinimlerine göre ayarlanmalıdır.
- Kaynak hızı: Kaynak hızı, ısı girdisiyle ters orantılıdır. Daha hızlı kaynak hızları, ısı girdisini azaltabilir ve böylece kaynak sıcaklıklarını düşürebilir; bu, ince malzemeler veya daha az ısının gerektiği durumlar için uygundur. Daha yavaş kaynak hızları, daha fazla ısı girdisi sağlayabilir; bu, kalın malzemeler veya daha güçlü kaynakların gerektiği durumlar için uygundur.
- Işın modu: Lazer ışınının odaklama modu (dairesel, dikdörtgen veya doğrusal mod gibi) ışının enerji yoğunluğunu ve dolayısıyla sıcaklık dağılımını etkiler. Doğru ışın odaklaması lazer enerjisini küçük bir alana yoğunlaştırabilir ve malzemeyi hızla ısıtabilir. Ve genişletilmiş ışın modu ısıyı eşit şekilde dağıtabilir ve yerel aşırı ısınma riskini azaltabilir.
Ön ısıtma ve son ısıtma
Bazı malzemeler ısıya karşı çok hassastır, özellikle alüminyum alaşımları ve yüksek dayanımlı çelik gibi malzemeler. Isı girişini kontrol etme stratejileri arasında çatlakları, termal deformasyonu ve kalıntı gerilimleri azaltmaya yardımcı olabilen ön ısıtma ve son ısıtma bulunur.
- Ön ısıtma: Ön ısıtma, kaynak yapmadan önce malzemeyi belirli bir sıcaklığa ısıtmak anlamına gelir. Alüminyum alaşımları ve magnezyum alaşımları gibi düşük erime noktalı malzemeler için ön ısıtma, kaynak sırasında malzemenin hızla soğumasından kaynaklanan termal stresi ve çatlak riskini azaltabilir. Ön ısıtma ayrıca kaynak sırasında termal şoku azaltabilir ve aşırı sıcaklık farklarından kaynaklanan çatlakları önleyebilir.
- Son ısıtma: Kaynaktan sonra ısıtma (veya tavlama), kaynak alanındaki artık gerilimi azaltmaya, termal deformasyon riskini düşürmeye ve kaynaklı eklemin mekanik özelliklerini iyileştirmeye yardımcı olur. Son ısıtma genellikle kaynaktan sonra soğutma hızını kontrol ederek, özellikle yüksek dayanımlı çelik veya diğer ısıya duyarlı malzemelerin kaynaklanmasında elde edilir.
İzleme ve Geri Bildirim Sistemi
Modern lazer kaynak ekipmanları genellikle kaynak sıcaklığını gerçek zamanlı olarak izleyebilen ve işlem parametrelerini gerçek zamanlı verilere göre ayarlayabilen yüksek hassasiyetli sıcaklık izleme sistemleriyle donatılmıştır. Bu sistemler yalnızca kaynak işleminin doğruluğunu iyileştirmekle kalmaz, aynı zamanda kaynak kalitesinin tutarlılığını da sağlar.
- Sıcaklık sensörü: Sıcaklık sensörü, kaynak alanının sıcaklığını gerçek zamanlı olarak ölçebilir ve sıcaklık değişim bilgilerini kontrol sistemine geri bildirim olarak gönderebilir. Yaygın olarak kullanılan sensörler arasında, kaynak alanının sıcaklığını temas olmadan izleyebilen kızılötesi sıcaklık sensörleri ve lazer spektrum sensörleri bulunur.
- Otomatik geri bildirim ayarlama sistemi: Sıcaklık izleme sistemi, lazer güç kontrol sistemi ve kaynak hızı kontrol sistemi ile bağlantılandırılabilir ve lazer gücü ve kaynak hızı, sıcaklığı gerekli aralıkta tutmak için gerçek kaynak sıcaklığına göre dinamik olarak ayarlanabilir. Böyle bir otomatik geri bildirim sistemi, yalnızca kaynak stabilitesini iyileştirmekle kalmaz, aynı zamanda insan operasyonunun hatasını da azaltır.
Diğer Sıcaklık Kontrol Stratejileri
Yukarıdaki yöntemlere ek olarak, sıcaklığı daha fazla kontrol edebilmek için lazer kaynakta başka teknolojiler de birleştirilebilir.
- Lazer darbe kontrolü: Lazer darbesinin frekansı ve süresi ayarlanarak ısı girişi hassas bir şekilde kontrol edilebilir. Kısa darbeler daha düşük sıcaklık girişi sağlayabilir ve ısıya duyarlı malzemeler için uygundur, uzun darbeler ise daha yüksek sıcaklıklar gerektiren kaynak görevleri için uygundur.
- Çok ışınlı kaynak: Kaynak işlemi sırasında paralel çalışan birden fazla lazer ışınının kullanılması, kaynak bölgesinde ısının eşit şekilde dağılmasına yardımcı olarak, lokal aşırı ısınmayı önleyerek kaynak kalitesini artırır.
Lazer kaynak sıcaklığı, işlem parametrelerinin hassas bir şekilde ayarlanması, ön ısıtma ve son ısıtma, etkili soğutma stratejileri ve gelişmiş sıcaklık izleme ve geri bildirim sistemleri ile etkili bir şekilde kontrol edilebilir. Bu kontroller, kaynak sırasında sıcaklığın optimum aralıkta kalmasını sağlayarak yüksek kaliteli kaynaklı bağlantılar, azaltılmış kusur riski ve nihai ürünün optimize edilmiş performansıyla sonuçlanır.
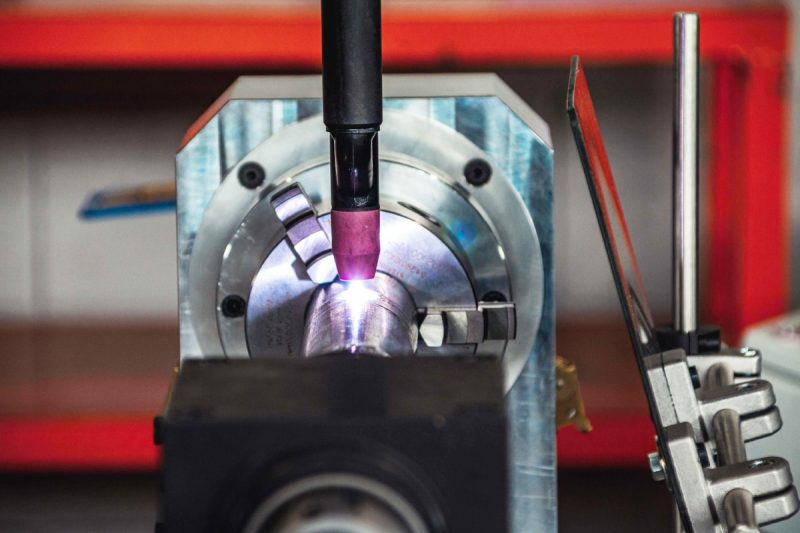
Belirli Uygulamalarda Sıcaklık Hususları
Lazer kaynak teknolojisi birçok endüstride yaygın olarak kullanılır ve farklı alanlardaki kaynak sıcaklığı gereksinimlerinde önemli farklılıklar vardır. Her endüstri lazer kaynak kullandığında, malzeme özelliklerine, kaynak hedeflerine ve kalite gereksinimlerine göre kaynak sıcaklığını doğru bir şekilde kontrol etmek gerekir. İşte başlıca endüstriler için bazı sıcaklık kontrolü hususları.
Otomotiv endüstrisi
Otomotiv sektöründe lazer kaynak, kapı, tavan, şasi vb. gövde yapısal parçalarının kaynaklanmasında yaygın olarak kullanılmaktadır. Bu sektörün kaynak kalitesi ve verimliliği konusunda çok yüksek gereksinimleri vardır, bu nedenle sıcaklık kontrolü özellikle kritik öneme sahiptir.
- Kaynak gücü: Sürüş güvenliğini sağlamak için gövde yapısının yüksek kaynak gücüne sahip olması gerekir. Bu nedenle, kaynak sıcaklığının kaynak alanının iyi bir şekilde kaynaşmasını sağlayacak ve yüksek güç gereksinimlerini karşılayacak kadar yüksek olması gerekir. Ancak, çok yüksek bir sıcaklık kaynaklı eklemin kırılganlığına yol açabilir, bu nedenle ısı girişinin hassas bir şekilde kontrol edilmesi gerekir.
- Verimlilik ve üretim hızı: Otomotiv üretim endüstrisinin üretim hızına ilişkin yüksek gereksinimleri vardır. Kaynak sırasında sıcaklık kontrolü yalnızca kaynak kalitesini sağlamakla kalmamalı, aynı zamanda kaynak verimliliğini de hesaba katmalıdır. Bu nedenle, uygun kaynak sıcaklığını kontrol etmek, yüksek kaliteli kaynaklı bağlantıları korurken üretim hattının hızını artırmaya yardımcı olabilir.
- Isıdan etkilenen bölge (HAZ): Gövde malzemesi çoğunlukla yüksek mukavemetli çelik veya alüminyum alaşımıdır ve ısıdan etkilenen bölgenin kontrolü özellikle önemlidir. Aşırı sıcaklık, ısıdan etkilenen bölgenin yumuşamasına ve malzemenin mekanik özelliklerini etkilemesine neden olur. Bu nedenle, malzeme performansının bozulmasını önlemek için aşırı yüksek kaynak sıcaklıklarından kaçınmak gerekir.
Havacılık ve Uzay Endüstrisi
Havacılık ve uzay endüstrisi, malzemelerin performansı konusunda son derece katı gerekliliklere sahiptir ve kaynak sırasında sıcaklık kontrolü özellikle kritiktir. Özellikle uçak yapısal parçaları ve motor bileşenlerinin üretiminde, çok yüksek veya çok düşük kaynak sıcaklığı, malzemenin performansı üzerinde önemli bir etkiye sahip olacaktır.
- Isıdan etkilenen bölge kontrolü: Titanyum alaşımları ve yüksek sıcaklık alaşımları gibi havacılık endüstrisinde kullanılan malzemeler genellikle yüksek mukavemete ve korozyon direncine sahiptir. Kaynak işlemi sırasında, aşırı büyük bir ısıdan etkilenen bölge (HAZ) oluşmasını önlemek için ısı girişi hassas bir şekilde kontrol edilmelidir. Aşırı ısınma, malzemenin mukavemetinin azalmasına ve hatta çatlaklara neden olarak yapısal parçaların genel performansını etkileyebilir.
- Sıcaklık doğruluğu: Yüksek hassasiyetli sıcaklık kontrolü, havacılık endüstrisinin temel bir gereksinimidir. Malzeme sıcaklık değişimlerine karşı çok hassas olduğundan, kaynak sırasında ısı girişini azaltmak ve kaynaklı eklemin çok fazla etkilenmemesini sağlamak için düşük güçlü lazerlerin kullanılması gerekir.
- Kaynak kalitesi: Havacılık alanında kaynak kalitesi doğrudan uçuş güvenliğiyle ilgilidir. Bu nedenle, eşit olmayan ısınmayı veya aşırı ısınmayı önlemek için kaynak sırasında sıcaklığın her zaman optimum aralıkta tutulmasını sağlamak çok önemlidir.
Elektronik İmalatı
Elektronik üretim alanında, lazer kaynak, mikro devreler, konektörler ve bileşenler gibi küçük hassas parçaları bağlamak için kullanılır. Bu bileşenler küçük ve ısıya karşı çok hassas olduğundan, sıcaklık kontrolü özellikle önemlidir.
- Aşırı ısınma riski: Elektronik montajların bileşenleri ve devreleri termal yükselmeye karşı çok hassastır. Aşırı kaynak sıcaklığı, devre kartının hasar görmesi veya bileşenin kaynak hatası gibi bileşen hasarına veya performans düşüşüne neden olabilir. Bu nedenle, aşırı ısınmayı önlemek için ısı girişini azaltmak amacıyla kaynak sırasında daha düşük lazer gücü kullanılması gerekir.
- Düşük güçlü lazerlerin kullanımı: Bileşenlerdeki termal hasarı azaltmak için, elektronik üretim endüstrisi genellikle düşük güçlü lazerler kullanır ve lazer ışınının odaklanmasını ve kaynak süresini hassas bir şekilde kontrol eder. Bu tür düşük güçlü kaynak yöntemleri, hassas elektronik bileşenlere zarar vermeden yüksek kaliteli bağlantılar elde edebilir.
- Sıcaklık artışı izleme: Kaynak sırasında doğru sıcaklık kontrolünü sağlamak için, elektronik üretim endüstrisi genellikle kaynak sırasında sıcaklık hakkında gerçek zamanlı geri bildirim sağlamak için bir sıcaklık izleme sistemi kullanır. Sıcaklık artışı izlenerek, lazer gücü veya kaynak hızı, kaynak sıcaklığının her zaman güvenli bir aralıkta olduğundan emin olmak için ayarlanır.
Tıbbi Cihaz İmalatı
Tıbbi cihaz üretiminde, hassas kaynak teknolojisi cerrahi aletler, implantlar ve tıbbi cihaz muhafazaları gibi küçük parçaları birleştirmek için yaygın olarak kullanılır. Bu uygulamalar kaynak doğruluğu ve kontaminasyon olmaması için son derece yüksek gereksinimlere sahiptir.
- Hassasiyet gereksinimleri: Tıbbi cihazların kaynak parçaları genellikle çok küçük ve hassastır, bu nedenle hassas sıcaklık kontrolü gerekir. Aşırı sıcaklık, kaynak alanının aşırı ısınmasına neden olabilir, bu da malzemeye zarar verebilir veya eklemin bozulmasına neden olabilir. Bunu önlemek için, lazer kaynak genellikle düşük güç kullanır ve kaynak noktasında düzgün sıcaklık sağlamak için ışın odağını doğru bir şekilde kontrol eder.
- Kirliliksiz gereklilikler: Tıbbi cihazların kaynaklanması, ürün kalitesini etkileyen kirleticilerden kaçınmak için temiz bir ortamda gerçekleştirilmelidir. Kaynak sıcaklığı, son ürünün güvenliğini ve hijyenini etkileyen aşırı sıcaklıktan kaynaklanan metal oksidasyonunu veya zararlı gazları önlemek için sıkı bir şekilde kontrol edilmelidir.
- Orta sıcaklık: Tıbbi cihazların hassas kaynaklanmasında, kaynak sıcaklığının genellikle orta bir aralıkta kontrol edilmesi gerekir; bu, malzemenin tamamen erimesini sağlamalı, ancak malzeme performansında bir düşüşe neden olacak şekilde aşırı ısınmamalıdır. Uygun sıcaklık kontrolü, kaynaklı eklemin mukavemetine ve dayanıklılığına yardımcı olur, nihai ürünün güvenilirliğini ve uzun vadeli performansını garanti eder.
Lazer kaynak, farklı uygulama alanlarında benzersiz sıcaklık kontrol gereksinimlerine sahiptir. Otomotiv endüstrisi kaynak gücüne ve verimliliğine odaklanır, havacılık endüstrisi ısıdan etkilenen bölgelerin kontrolüne vurgu yapar, elektronik üretimi hassas bileşenleri korumak için düşük sıcaklıkta kaynak yapmaya odaklanır ve tıbbi cihaz üretimi hassas kaynak ve kontaminasyon olmamasını gerektirir. Her endüstrinin kaynak sıcaklık kontrol stratejisi, ürünün kalitesini ve performansını garantilemek için belirli malzeme özelliklerine ve kaynak hedeflerine göre hassas bir şekilde ayarlanmalıdır.
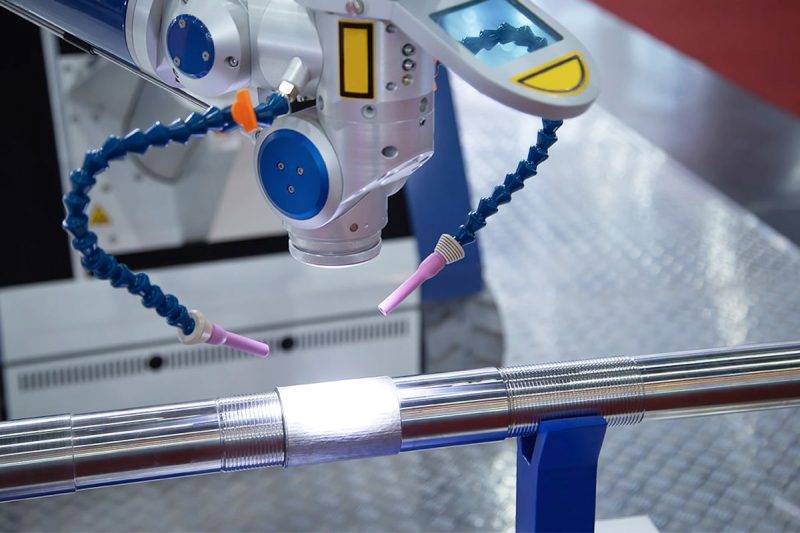
özetle
Lazer kaynak, otomotiv, havacılık, elektronik üretim ve tıbbi cihazlar dahil olmak üzere birçok sektörde yaygın olarak kullanılan yüksek sıcaklıklı, yüksek hassasiyetli gelişmiş bir işlemdir. İşlem, malzemeleri hızlı ve etkili bir şekilde eritmek ve güçlü bir bağlantı oluşturmak için yüksek oranda yoğunlaştırılmış enerjiye sahip bir ısı kaynağı olarak lazer ışını kullanır. Lazer kaynağının başlıca avantajları, kaynak kalitesi konusunda katı gereksinimleri olan birçok sektörde yaygın olarak kullanılmasını sağlayan yüksek hassasiyeti ve yüksek hızıdır. Bununla birlikte, lazer kaynağının başarısı yalnızca lazer ışınının çıkış gücüne ve malzeme özelliklerine değil, aynı zamanda kaynak işlemi sırasında sıcaklığın hassas bir şekilde kontrol edilmesine de bağlıdır. Çok yüksek veya çok düşük bir sıcaklık, kaynaklı bağlantının kalitesini düşürerek gözenekler, çatlaklar, aşırı yanma ve eksik penetrasyon gibi kusurlara neden olabilir. Bu nedenle, sıcaklık kontrolü kaynak kalitesini sağlamanın özüdür. AccTek Laser'in lazer kaynak makinesi, istikrarlı sıcaklık kontrol sistemiyle kullanıcılara daha hassas ve güvenilir bir kaynak deneyimi sunarak sektör rekabetinde öne çıkmalarına yardımcı olur.
Yüksek kaliteli lazer kaynağı elde etmek için, işlem parametrelerini optimize etmek, uygun ekipmanı seçmek ve bir izleme geri bildirim sistemi uygulamak esastır. Lazer gücü, kaynak hızı ve odak konumu gibi parametreleri ayarlayarak, ısı girişi malzemenin özelliklerine ve kaynak gereksinimlerine göre hassas bir şekilde kontrol edilebilir. Ek olarak, modern lazer kaynak ekipmanları genellikle kaynak işlemi sırasında sıcaklık değişikliklerine göre parametreleri zamanında ayarlayabilen ve kaynak kalitesinin her zaman en iyi durumda olmasını sağlayan gerçek zamanlı bir izleme sistemi ile donatılmıştır. Teknolojinin sürekli ilerlemesiyle, lazer kaynağının sıcaklık kontrolü daha hassas hale gelecek ve kaynak kalitesi ve performansı için giderek daha fazla üst düzey endüstrinin ihtiyaçlarını karşılayabilecektir. Gelecekte, lazer kaynak teknolojisi geliştikçe, daha fazla endüstri için daha verimli ve güvenilir kaynak çözümleri sağlayacak ve üretim endüstrisinin ilerlemesini ve yeniliğini teşvik edecektir.
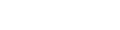
İletişim bilgileri
- [email protected]
- [email protected]
- +86-19963414011
- 3 Bölge A, Lunzhen Sanayi Bölgesi, Yucheng Şehri, Shandong Eyaleti.
Lazer Çözümleri Alın