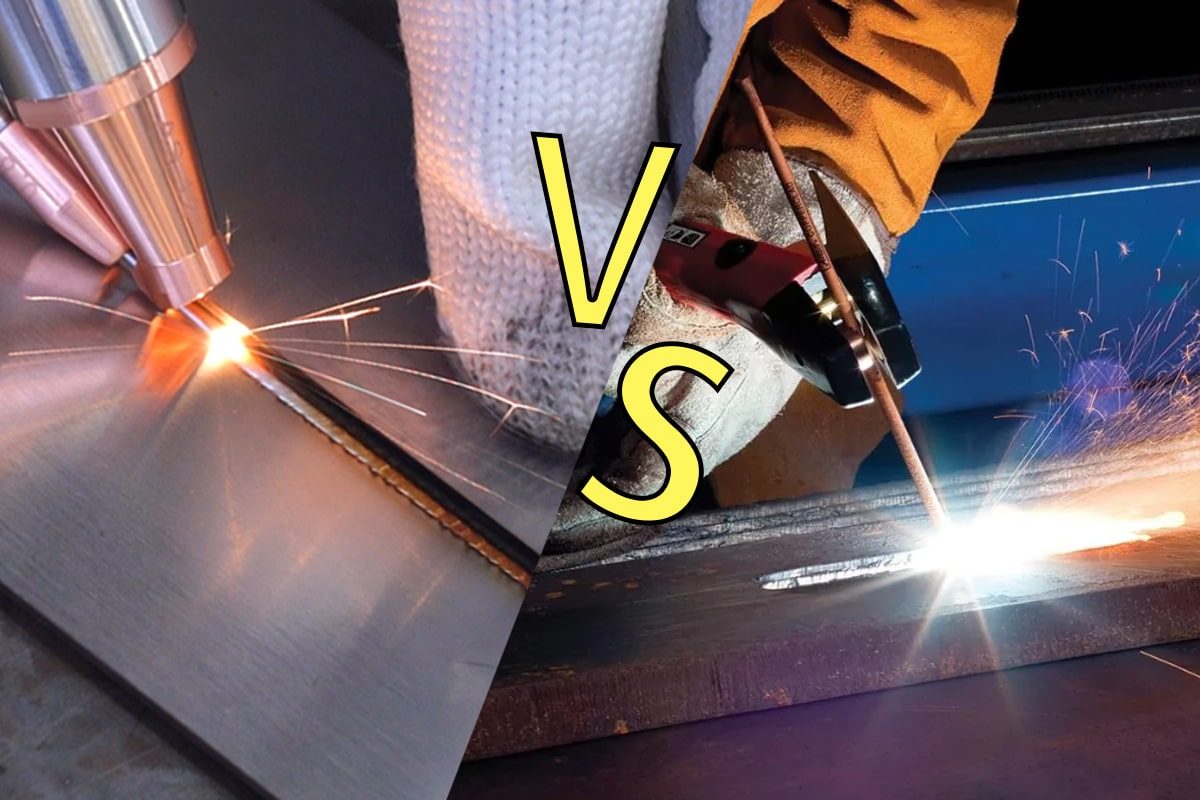
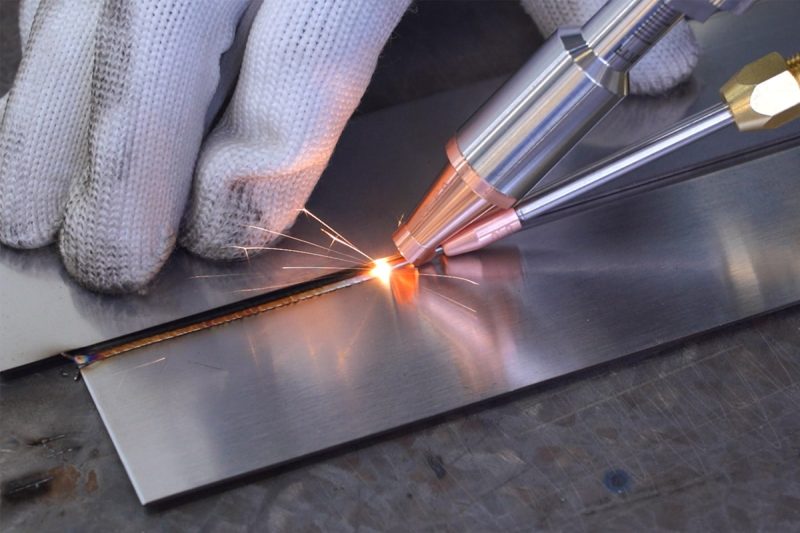
Lazer Kaynak Genel Bakış
Lazer Kaynak Prensibi ve İşlemi
- Malzeme hazırlığı: Kaynak yapılacak malzemenin yüzeyinin temiz olduğundan emin olun ve kaynak kalitesini etkilememek için oksit, yağ ve diğer kirleticileri temizleyin.
- Lazer ışınının odaklanması: Enerji yoğunluğunun yeterince yüksek olduğundan emin olmak için lazer ışınını kaynak alanına odaklamak için bir mercek veya reflektör kullanın.
- Erimiş havuz oluşumu: Lazer ışını malzemenin yüzeyini ışınlar, hızla ısınır ve eriyerek erimiş bir havuz oluşturur ve erimiş havuz lazerin hareketi sırasında giderek genişler.
- Katılaşma ve soğuma: Lazer ışını uzaklaştırıldıktan sonra, erimiş havuz soğur ve sürekli bir kaynak oluşur.
Lazer Kaynak Teknolojilerinin Türleri
Lazer Işın Kaynağı
- Bu yöntem esas olarak sığ kaynak için kullanılır. Lazer ışını malzemenin yüzeyini ısıtır ve onu yerel olarak eritir. Isı yavaşça yayıldığı ve erimiş havuz sığ olduğu için genellikle ince malzemeleri birleştirmek veya kaynak görünümüne ilişkin yüksek gereksinimleri olan sahneler için uygundur. Lazer ışını kaynağı hassas elektronik cihazların veya ince duvarlı metal malzemelerin kaynaklanması için uygundur.
Lazer Anahtar Deliği Kaynak
- Yüksek enerjili lazer ışınımı altında, malzeme sadece yüzeyde erimez. Lazerin güçlü enerjisi metali buharlaştırır ve kaynak alanında küçük bir delik (anahtar deliği olarak adlandırılır) oluşturur. Bu küçük delik derin ve dardır, lazerin malzemenin derinliklerine nüfuz etmesini ve çoklu yansımalar yoluyla enerjiyi çevredeki malzemelere aktarmasını sağlar. Bu teknoloji, kalın malzemelerin derin penetrasyonlu kaynaklanması için uygundur ve yüksek kaynak mukavemeti gerektiren otomobil, havacılık ve gemi yapımı gibi endüstrilerde yaygın olarak kullanılır.
Lazer Kaynağının Avantajları ve Sınırlamaları
Lazer Kaynağının Avantajları:
- Yüksek hassasiyet: Lazer kaynak, enerjiyi çok küçük bir alana doğru bir şekilde odaklayabilir, kaynak derinliğini ve aralığını kontrol edebilir ve özellikle karmaşık parçaların işlenmesi için uygun olan son derece yüksek kaynak doğruluğu elde edebilir.
- Küçük ısıdan etkilenen bölge: Lazer kaynakta enerji konsantrasyonunun yüksek olması nedeniyle ısıdan etkilenen bölge küçüktür, bu da malzeme deformasyonunu ve iç gerilimi azaltarak kaynak kalitesini garanti eder.
- Hızlı kaynak hızı: Lazer kaynak, kaynak işlemini çok kısa sürede tamamlayabilir, üretim verimliliğini büyük ölçüde artırabilir ve özellikle büyük ölçekli otomatik üretim hatları için uygundur.
- Temassız işlem: Lazer kaynak, iş parçasıyla doğrudan temas gerektirmediğinden dışarıdan bir kuvvet uygulanmaz veya mekanik hasara neden olmaz.
- Çeşitli malzemelere uygulanabilir: Geleneksel metal malzemelere ek olarak, lazer kaynak, plastik ve seramik gibi metal olmayan malzemelere de uygulanabilir ve geniş bir uygulama yelpazesine sahiptir.
Lazer Kaynağının Sınırlamaları:
- Yüksek ekipman maliyeti: Lazer kaynak ekipmanları karmaşıktır ve lazer jeneratörleri, kontrol sistemleri ve yardımcı ekipmanların maliyeti yüksektir, özellikle yüksek güçlü lazer sistemleri, bu durum küçük ve orta ölçekli işletmeler üzerinde ekonomik baskı yaratabilir.
- Malzeme yüzeyi için yüksek gereksinimler: Lazer kaynak, iş parçası yüzeyinin temizliği konusunda katı gereksinimlere sahiptir. Herhangi bir yağ, oksit veya diğer kirlilikler lazerin emilim verimliliğini ve kaynak kalitesini etkileyecektir.
- İnce malzemeler veya hassas kaynak için uygundur: Lazer kaynak yöntemi çeşitli malzemeleri kaynaklayabilmesine rağmen, kalın yapısal malzemeler üzerindeki geleneksel kaynak işlemleri kadar verimli olmayabilir.
Lazer Kaynağının Çeşitli Endüstrilerde Uygulanması
- Otomobil üretimi: Lazer kaynak, otomobil endüstrisinde, özellikle gövde kaynak, kapı kaynak ve motor parçaları kaynak işlemlerinde yaygın olarak kullanılır. Yüksek hızı ve yüksek hassasiyeti sayesinde üretim hattının otomasyon seviyesini büyük ölçüde iyileştirir. Ayrıca lazer kaynak, alüminyum alaşımı ve çelik gibi karışık metalleri kaynaklamak için de kullanılır.
- Havacılık ve Uzay: Havacılık ve uzay alanında, kaynak malzemeleri genellikle hafiflik ve yüksek mukavemet gerektirir. Yüksek hassasiyeti ve mükemmel kaynak kalitesi nedeniyle lazer kaynak, türbin kanatları, motor kasaları ve diğer bileşenler dahil olmak üzere uçak ve uzay aracı yapıları için yaygın olarak kullanılır.
- Elektronik ve mikroelektronik endüstrisi: Lazer kaynak, küçük alanların hassas bir şekilde kaynaklanmasını sağlayabildiği ve çok küçük bir ısıdan etkilenen bölgeye sahip olduğu için elektronik endüstrisinde, özellikle mikroelektronik üretiminde yaygın olarak kullanılmaktadır. Örneğin, cep telefonları, devre kartları ve pil paketleri gibi küçük hassas parçaların kaynaklanması.
- Tıbbi cihazlar: Lazer kaynak, tıbbi cihazların üretiminde önemli bir rol oynar. Cerrahi aletler, implantlar ve çeşitli paslanmaz çelik ve titanyum alaşımlı cihazlar gibi hassas ve zorlu metal aletleri kaynaklamak için kullanılır.
- Enerji sektörü: Yeni enerji, güneş enerjisi ve pil üretimi alanlarında, temas gerektirmemesi, yüksek verimliliği ve çeşitli malzemelere uyum sağlayabilmesi nedeniyle lazer kaynak yöntemi yaygın olarak kullanılmaktadır, özellikle yeni enerji pillerinin paketlenmesi ve birleştirilmesinde.
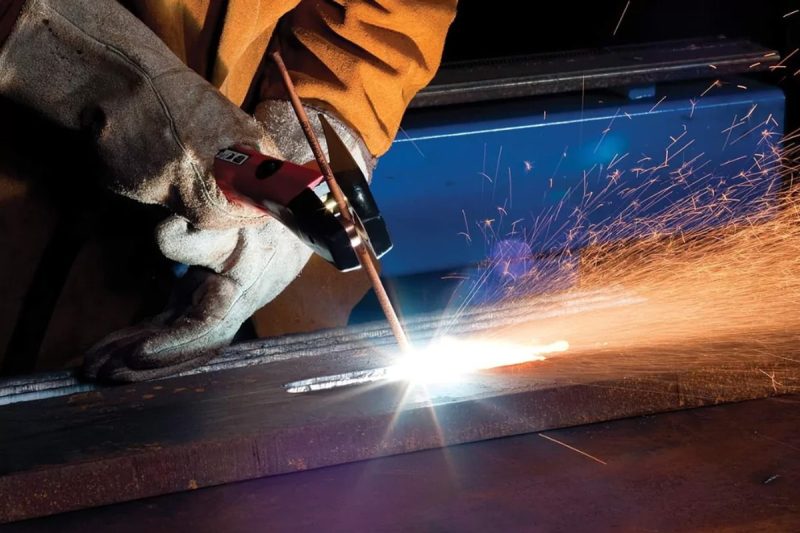
Ark Kaynağı Genel Bakış
Ark Kaynak Prensibi ve İşlemi
- Ark oluşumu: Kaynak elektrodunu iş parçasına yaklaştırarak elektrot ile iş parçası arasında bir ark oluşmasını sağlayın.
- Metal eritme: Arkın oluşturduğu yüksek sıcaklık (5000-6000℃'ye kadar) metali eriterek erimiş bir havuz oluşturur.
- Erimiş havuz dolgusu: Elektrodun malzemesi, iş parçasının yüzeyindeki erimiş metalle karışarak bir dolgu maddesi oluşturur ve bu dolgu, erimiş havuzu yavaş yavaş doldurur.
- Soğuma ve katılaşma: Ark hareket ettikten sonra erimiş havuz hızla soğur ve kaynakta katılaşır.
- Ark kaynak işlemi sırasında kaynak parametrelerinin (akım, gerilim, kaynak hızı gibi) ve kaynak pozisyonunun kontrolü, kaynağın kalitesini ve kaynak etkisini belirler.
Ark Kaynak Tekniklerinin Çeşitleri
Korumalı Metal Ark Kaynağı
MIG/MAG kaynak
Gaz Tungsten Ark Kaynağı
Sualtı Ark Kaynağı
Ark Kaynağının Avantajları ve Sınırlamaları
Ark Kaynağının Avantajları:
- Düşük ekipman maliyeti: Ark kaynak ekipmanları nispeten basittir, ilk yatırım maliyeti düşüktür ve ekonomik bakım maliyetine sahiptir, büyük ölçekli endüstriyel uygulamalar için uygundur.
- Esnek çalışma: Ark kaynağı, çeşitli kaynak pozisyonlarına ve karmaşık yapılara uyum sağlayabilir ve iç mekanlarda, dış mekanlarda veya dar alanlarda çalıştırılabilir.
- Güçlü malzeme uyumluluğu: Ark kaynağı, düşük karbonlu çelik, paslanmaz çelik, alüminyum, bakır vb. dahil olmak üzere çeşitli metalleri kaynaklayabilir ve geniş bir uygulama alanına sahiptir.
- Geniş uygulama alanı: İnce levhalardan ağır yapısal malzemelere kadar ark kaynağı, özellikle ağır ekipman ve inşaat endüstrilerinde kalınlık ve yapısal form açısından güçlü bir adaptasyon kabiliyetine sahiptir.
Ark Kaynağının Sınırlamaları:
- Geniş ısıdan etkilenen bölge: Ark kaynağı, geniş bir ısıdan etkilenen bölgeye kolayca neden olabilen büyük bir ısı girdisine sahiptir ve bu da malzemede deformasyona, çatlaklara veya ısıl işlemle ilgili diğer sorunlara yol açabilir.
- Nispeten düşük kaynak hassasiyeti: Lazer kaynak gibi yüksek hassasiyetli kaynak işlemleriyle karşılaştırıldığında, ark kaynağı kaynak hassasiyetinden yoksundur ve kaynağın inceliği ve estetiği düşüktür.
- Yüksek duman ve gaz emisyonları: Ark kaynağı sırasında operatörlerin ve çevrenin sağlığını etkileyebilecek miktarda duman ve zararlı gazlar ortaya çıkar, bu nedenle iyi havalandırma ve koruyucu ekipman gereklidir.
- Yüksek teknik gereklilikler: Özellikle manuel kaynakta kaynakçının beceri seviyesi kaynak kalitesi üzerinde büyük etkiye sahiptir ve yetersiz teknik yeterlilik kaynak hatalarına yol açacaktır.
Ark Kaynağının Çeşitli Endüstrilerde Uygulanması
- İnşaat sektörü: Ark kaynağı, özellikle çelik yapıların ve köprülerin inşasında olmak üzere, bina yapılarının kaynaklanmasında yaygın olarak kullanılır. Ark kaynağının yüksek mukavemetli kaynakları ve işlerliği, onu çelik yapı kaynaklama için tercih edilen işlemlerden biri yapar.
- Gemi inşa endüstrisi: Gövde imalatında büyük miktarda çelik kaynaklama gereklidir ve ark kaynağı ağır çelik levhaları işleyebilir ve iyi mekanik özellikler sağlayabilir. Özellikle, büyük gövdelerin ve kabukların kaynaklanmasında sualtı ark kaynağı yaygın olarak kullanılır.
- Petrol ve gaz endüstrisi: Boru hattı kaynakçılığında, ark kaynağının esnekliği ve güçlü malzeme uyumluluğu, onu petrol ve gaz boru hatları için ana kaynak yöntemi haline getirerek, yüksek basınçlı ortamlarda güvenilirliği garanti altına alabilir.
- Ağır ekipman üretimi: Madencilik ekipmanı, inşaat makineleri ve tarım makineleri gibi ağır ekipmanların üretiminde, kovalar, çerçeveler ve bomlar gibi büyük yapısal parçaların kaynaklanmasında ark kaynağı yaygın olarak kullanılır. Bu parçalar yüksek mukavemetli ve dayanıklı kaynak teknolojisi gerektirir.
- Onarım ve bakım: Ark kaynak ekipmanının basit ve rahat çalışması nedeniyle, çeşitli tipteki mekanik ekipmanların onarımı ve bakımında yaygın olarak kullanılır. Otomobil onarımından endüstriyel ekipman onarımına kadar, ark kaynak bakım personeli için yaygın bir araçtır.
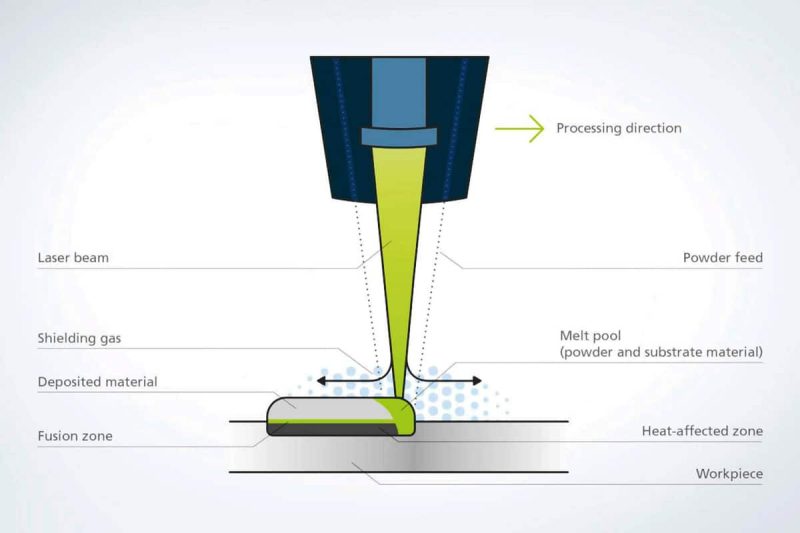
Lazer Kaynak Prensibi
Lazer Kaynak Nasıl Çalışır?
- Lazer ışını üretimi: Yüksek yoğunluklu bir lazer ışını, bir fiber lazer jeneratörü, bir CO₂ lazer jeneratörü veya katı hal lazer jeneratörü olabilen bir lazer jeneratörü tarafından üretilir. Lazer ışını, tek bir dalga boyu, yüksek yönlülük ve yüksek enerji yoğunluğu ile karakterize edilir.
- Lazer ışını odaklama: Lazer ışını, genellikle sadece yaklaşık 0,1 mm çapındaki çok küçük bir noktaya, optik bir sistem (örneğin bir mercek veya reflektör) tarafından odaklanır. Bu, metali hızla eritmek için yeterli olan çok yüksek güç yoğunluklarına (milimetre kare başına yüzlerce ila binlerce watt) olanak tanır.
- Malzeme eritme ve kaynaklama: Lazer ışını malzemenin yüzeyine ışınlandığında, malzeme lazer enerjisini emer ve hızla erime noktasına kadar ısınır ve erimiş bir havuz oluşturur. Lazer ışını kaynak yolu boyunca hareket ettikçe, erimiş havuz kademeli olarak genişler ve soğuduktan sonra katı bir kaynak oluşturur.
- Soğutma ve katılaşma: Lazer ışını hareket ettikten sonra, erimiş havuz alanı soğur ve erimiş metal sürekli bir kaynak oluşturmak üzere katılaşır. Lazer gücünü, kaynak hızını ve odak konumunu kontrol ederek, kaynağın şekli ve kalitesi hassas bir şekilde kontrol edilebilir.
Lazer ve Metal Arasındaki Etkileşim
- Lazer enerjisi emilimi: Lazer ışını metal yüzeyi ışınladığında, metal lazer enerjisinin bir kısmını emer, bu metalin yansıtıcılığına ve lazerin dalga boyuna bağlıdır. Örneğin, alüminyum ve bakır gibi yüksek yansıtıcılığa sahip malzemeler, lazerlerin belirli dalga boyları için düşük emilim oranlarına sahiptir, bu nedenle kaynak için daha yüksek güç veya daha uygun dalga boyları gerekir. Yaygın çelik ve paslanmaz çelik için emilim oranı daha yüksektir ve lazer kaynağı daha verimlidir.
- Isı iletimi ve erime: Metal tarafından emilen lazer enerjisi, ısı iletimi yoluyla malzemeye yayılır, böylece malzeme ısınır ve erime noktasına ulaşır. Daha yüksek güç yoğunluğu, malzemenin yerel ve hızlı bir şekilde erimesine ve erimiş bir havuz oluşmasına neden olur. Lazer ışınının hareketi sırasında, erimiş havuzdaki metal katılaşmaya devam eder ve sonunda bir kaynak oluşturur.
- Anahtar Deliği Etkisi: Yüksek güçlü lazer kaynakta, lazer ışınının enerjisi yalnızca malzemeyi eritmekle kalmaz, aynı zamanda metalin bir kısmını buharlaştırır, yerel basınç oluşturur ve erimiş metali küçük bir delik oluşturacak şekilde iter. Bu anahtar deliği etkisi, lazer ışınının malzemenin derinliklerine nüfuz etmesini, çoklu yansımalar yoluyla enerjiyi daha da iletmesini ve kaynak derinliğini ve verimliliğini artırmasını sağlar. Anahtar deliği kaynağı, kalın malzemeler veya derin penetrasyon kaynakları için çok uygundur.
- Erimiş havuzun dinamik davranışı: Kaynak işlemi sırasında, erimiş havuzun akışkanlığı ve yüzey gerilimi, kaynağın kalitesini ve şeklini etkiler. Uygun lazer gücü ve kaynak hızı, erimiş havuzun stabil kalmasını sağlayabilir ve sıçrama ve gözeneklilik gibi kaynak kusurlarını önleyebilir.
Lazer Kaynağını Etkileyen Temel Parametreler
- Lazer gücü: Lazerin gücü, malzemeye uygulanan enerji yoğunluğunu belirler. Daha yüksek güç, kalın levha kaynağı veya derin penetrasyon kaynağı için uygundur, ancak güç çok yüksekse, malzemenin aşırı erimesine veya sıçramasına neden olabilir; daha düşük güç, ısı girişini ve deformasyonu etkili bir şekilde azaltabilen ince levhalar veya hassas kaynak için uygundur.
- Kaynak hızı: Kaynak hızı, lazer ışınının malzeme yüzeyinde hareket ettiği hızı ifade eder. Daha hızlı kaynak hızı, ısıdan etkilenen bölgenin boyutunu ve malzeme deformasyonunu azaltabilir, ancak çok hızlı hız, eksik veya dengesiz kaynaklara neden olabilir; daha düşük hız, derin penetrasyonlu kaynak yapmaya elverişlidir, ancak ısı girişini artırarak çok geniş kaynaklara veya daha büyük bir ısıdan etkilenen bölgeye neden olabilir.
- Odak konumu: Lazer ışınının odak noktasının iş parçası yüzeyine göre konumu, kaynak derinliğini ve kaynak şeklini kontrol etmenin anahtarıdır. İş parçası yüzeyinin altına odaklanmak kaynak derinliğini artırabilir ve kalın levha kaynakları için uygundur; yüzeyin üstüne odaklanmak yüzey hassas kaynakları için uygundur. Odak konumunu doğru bir şekilde kontrol etmek, kaynağın şeklini ve mukavemetini optimize etmeye yardımcı olur.
- Koruyucu gaz: Koruyucu gaz (argon, helyum veya karbondioksit gibi) genellikle lazer kaynakta erimiş havuzun havadaki oksijen ve nitrojenle reaksiyona girmesini önlemek için kullanılır, böylece kaynak oksidasyonu veya gözenek oluşumu önlenir. Farklı gazların kaynak oluşumu ve kalitesi üzerinde farklı etkileri vardır. Argon genellikle kaynak yüzey kalitesini iyileştirmek için kullanılırken, helyum kaynak derinliğini artırmak için kullanılır.
- Lazer dalga boyu: Lazerin dalga boyu, malzemenin emilim verimliliğini etkiler. Farklı malzemeler lazer dalga boylarına karşı farklı hassasiyetlere sahiptir ve doğru dalga boyunu seçmek enerji verimliliğini ve kaynak sonuçlarını iyileştirmeye yardımcı olur. Örneğin, fiber lazer jeneratörleri genellikle çelik, paslanmaz çelik ve diğer malzemelerin kaynaklanması için uygun olan 1μm dalga boyu aralığındadır, CO₂ lazer jeneratörleri ise daha uzun bir dalga boyuna (10,6μm) sahiptir ve metalik olmayan malzemelerin kaynaklanması için daha uygundur.
- Kaynak ortamı: Nem, sıcaklık ve hava akımı gibi çevresel koşullar da özellikle açık havada veya zorlu ortamlarda çalışıldığında lazer kaynağının kararlılığını etkileyebilir ve kaynak kalitesinin sağlanması için gerekli koruyucu önlemlerin alınması gerekir.
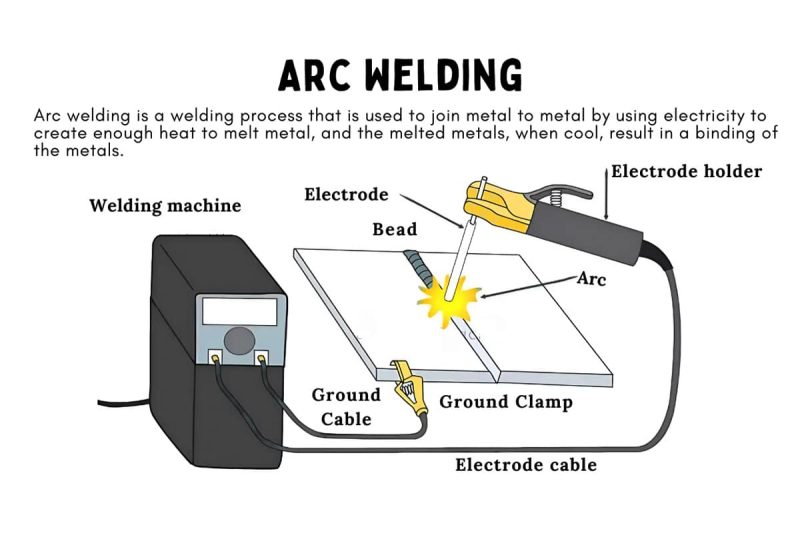
Ark Kaynak Prensibi
Ark Kaynağı Nasıl Çalışır
- Ark oluşumu: Kaynak elektrodu iş parçasına temas ettiğinde devre kapanır ve akım akar. Daha sonra elektrot iş parçasından ayrılır ve oluşan ark, enerjiyi hava veya koruyucu gaz yoluyla iletir ve yerel alandaki metalin hızla erime noktasına ısınmasına neden olur.
- Elektrot eritme ve doldurma: Arkın yüksek sıcaklığı sadece iş parçasını eritmekle kalmaz, aynı zamanda kaynak elektrodunu da eritir. Elektrodun erimiş metali erimiş havuza girer ve iş parçasının erimiş metaliyle birleşerek kaynak alanını kademeli olarak doldurur.
- Erimiş havuzun oluşumu ve hareketi: Ark, kaynak yolu boyunca hareket ettikçe, erimiş havuz sürekli olarak oluşur ve hareket eder ve erimiş havuzun arkasındaki alan arktan ayrıldıktan sonra hızla soğur ve kaynakta katılaşır.
- Koruma ve soğutma: Metal ark kaynağı (MIG/MAG kaynağı) gibi bazı ark kaynak tekniklerinde, havadaki oksijen ve azotun yüksek sıcaklıktaki metalle reaksiyona girerek oksit veya gözenek oluşturmasını ve kaynak kalitesini etkilemesini önlemek için erimiş havuzu korumak amacıyla inert gazlar (argon, karbondioksit vb.) kullanılır.
Ark ve Kaynak Havuzu Oluşumu
Yay oluşumu
Erimiş Havuz Oluşumu ve Dinamik Davranış
Kaynak Pozisyonu ve Erimiş Havuz Akışı
Ark Kaynağını Etkileyen Temel Parametreler
- Kaynak akımı: Akım, kaynak işleminin ısı girişini belirleyen temel parametrelerden biridir. Daha yüksek bir akım daha fazla ısı üretebilir, erimiş havuzun boyutunu ve kaynak derinliğini artırabilir ve daha kalın malzemelerin kaynaklanması için uygundur; daha düşük bir akım ise aşırı erime ve deformasyonu önlemek için daha ince malzemeler için uygundur. Çok yüksek bir akım, kaynağın taşmasına ve erimiş havuzun dengesiz olmasına neden olurken, çok düşük bir akım yetersiz erimeye ve yetersiz kaynak mukavemetine neden olur.
- Kaynak voltajı: Voltaj, arkın uzunluğunu ve kararlılığını kontrol eder. Daha yüksek voltaj daha uzun bir ark üretecek ve ısı dağılımını daha eşit hale getirecek, bu da geniş kaynakların oluşumu için uygundur; daha düşük voltaj daha kısa bir ark üretecek ve ısı daha küçük bir alanda yoğunlaşacaktır, bu da derin kaynak için uygundur. Voltajdaki değişiklikler doğrudan arkın şeklini ve kararlılığını etkiler, bu da erimiş havuzun akışkanlığını ve kaynağın şeklini etkiler.
- Kaynak hızı: Kaynak hızı, arkın iş parçası üzerinde hareket ettiği hızı ifade eder ve bu, erimiş havuzun şekli, ısıdan etkilenen bölgenin (HAZ) boyutu ve kaynak kalitesi üzerinde önemli bir etkiye sahiptir. Daha yüksek kaynak hızları, erimiş havuz oluşumu için gereken süreyi kısaltır, ısıdan etkilenen bölgeyi küçültür ve deformasyonu azaltır, ancak kesikli kaynaklara veya zayıf füzyona neden olabilir; daha yavaş kaynak hızları ısı girişini artırır ve derin erimeli kaynak için uygundur, ancak malzemelerin aşırı ısınmasına, çok geniş kaynaklara veya büyük deformasyona neden olabilir.
- Elektrot tipi ve çapı: Elektrot seçimi doğrudan kaynak etkisini etkiler. Farklı tipte elektrotlar (kaynak çubukları, elektrikli kaynak telleri vb.) farklı malzemeler ve kaynak yöntemleri için uygundur. Elektrodun çapı ayrıca arkın kararlılığını ve kaynak genişliğini etkiler. Daha kalın elektrotlar daha kalın malzemelerin kaynaklanması için uygundur ve geniş ve kalın kaynaklar oluşturabilirken, daha ince elektrotlar hassas kaynak veya ince levha kaynak için uygundur.
- Kaynak ortamı: Sıcaklık, nem, rüzgar hızı vb. gibi çevresel faktörler de ark kaynağını etkiler. Aşırı rüzgar hızı, koruyucu gazı uçurarak kaynakta oksidasyona veya gözenek oluşumuna neden olabilir. Kaynak kalitesini sağlamak için, sert dış mekan koşullarında rüzgar bariyerleri ve ısıtılmış iş parçaları gibi uygun koruyucu önlemler gereklidir.
- Koruyucu gaz: Metal ark kaynağında (MIG/MAG kaynağı) ve tungsten ark kaynağında (TIG kaynağı), koruyucu gaz havayı izole etmek ve erimiş havuzun oksijen ve nitrojenle temas etmesini önlemek için kullanılır. Farklı koruyucu gazlar (argon, karbondioksit, helyum vb. gibi) kaynağın morfolojisi, penetrasyon derinliği ve yüzey kalitesi üzerinde farklı etkilere sahiptir. Örneğin, argon daha iyi bir yüzey kalitesi sağlayabilirken, karbondioksit kaynağın derinliğini artırmaya yardımcı olur.
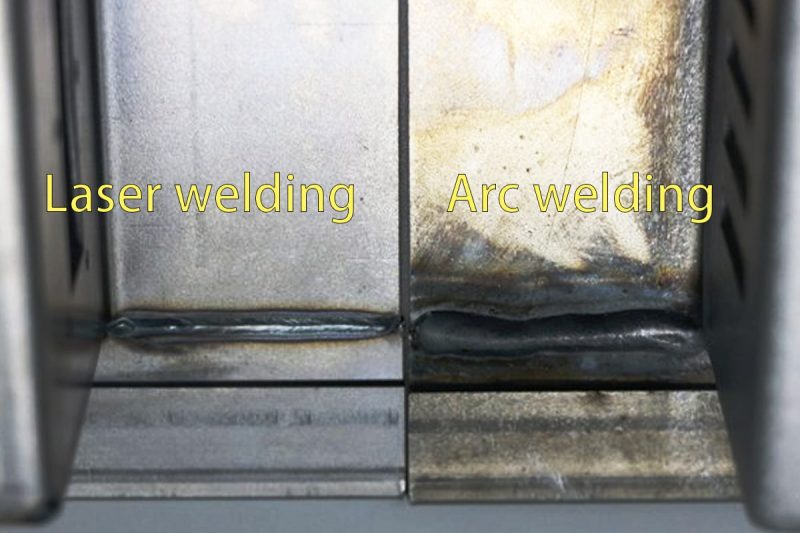
Lazer Kaynağı ve Ark Kaynağı Arasındaki Karşılaştırma
Verimlilik ve Hız
Hassasiyet ve doğruluk
Isıdan Etkilenen Bölge ve Deformasyon
Kaynak Kalitesi ve Mukavemeti
Ekipman ve Kurulum
Lazer kaynak ekipmanlarının tasarımı genellikle karmaşıktır ancak teknolojinin ilerlemesiyle birlikte modern taşınabilir lazer kaynak makineleri kaynak endüstrisinde öne çıkan bir cihaz haline gelmiştir. Bu cihazlar yalnızca lazer jeneratörleri, optik sistemler ve otomatik kontrol ünitelerini entegre etmekle kalmaz, aynı zamanda kaynak sırasında malzemelerin kalitesini ve performansını garanti altına almak için verimli koruyucu gaz cihazlarına da sahiptir. Taşınabilir lazer kaynak makinelerinin kullanıcı dostu işletim arayüzü, operatörlerin hızlı bir şekilde başlamasını ve karmaşık ayarlara olan bağımlılığı azaltmasını sağlar. Aynı zamanda, modern lazer kaynak makinelerinin bakımı nispeten basittir, bu da ekipman arızalarının sıklığını etkili bir şekilde azaltabilir ve sürekli üretim verimliliği sağlayabilir.
Maliyet Hususları
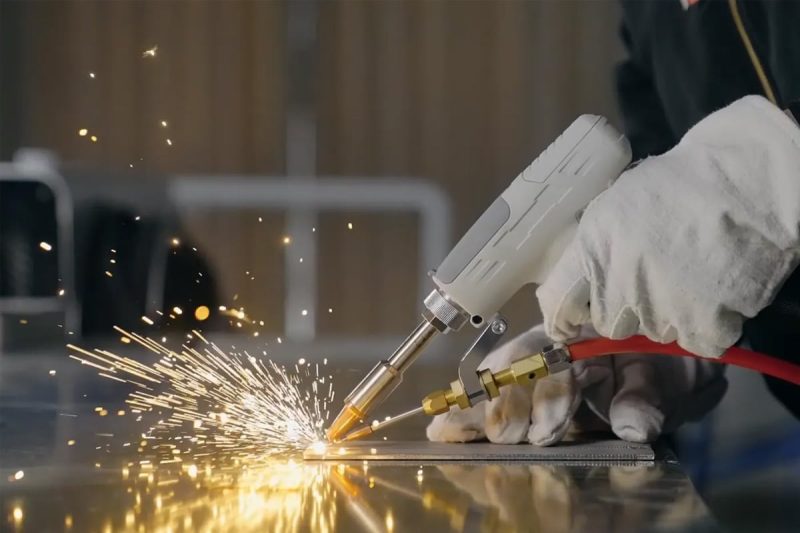
Lazer Kaynak ve Ark Kaynak Uygulamaları
Otomotiv
Havacılık ve Uzay
Elektronik ve Mikroelektronik Sanayi
Tıbbi Cihaz İmalatı
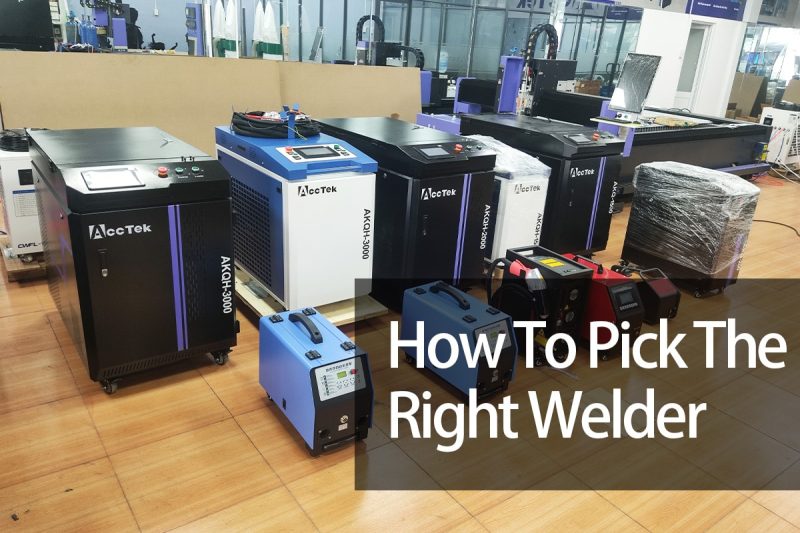
Doğru Kaynak Teknolojisini Seçmek
Kaynak Yöntemi Seçerken Dikkat Edilmesi Gereken Faktörler
- Malzeme türü ve kalınlığı: Farklı malzemeler ve malzeme kalınlıkları farklı kaynak teknikleri gerektirir. Örneğin, ince sac malzemeler lazer kaynak için daha uygundur, kalın levhalar veya yapısal çelikler ise genellikle ark kaynağı ile kaynaklanır.
- Kaynak hassasiyeti ve karmaşıklığı: Karmaşık parçalar, ince kaynaklar veya yüksek hassasiyetli kaynak gereksinimleri genellikle lazer kaynak gibi hassas kaynak tekniklerini gerektirir.
- Kaynak hızı: Büyük ölçekli, yüksek hızlı üretime olan talep, genellikle kısa sürede yüksek kaliteli kaynak yapabilen lazer kaynak gibi yüksek otomasyon derecesine sahip kaynak tekniklerini tercih etme eğilimindedir.
- Isı etkisi ve deformasyon kontrolü: Isıya duyarlı malzemeler veya düşük ısıdan etkilenen bölge gerektiren projeler genellikle lazer kaynak için uygundur; duyarsız yapısal çelik veya daha kalın malzemeler için ise ark kaynağı derin penetrasyonlu kaynak sağlayabilir.
Proje Özellikleri ve Hedefleri
Bütçe ve Kaynak Hususları
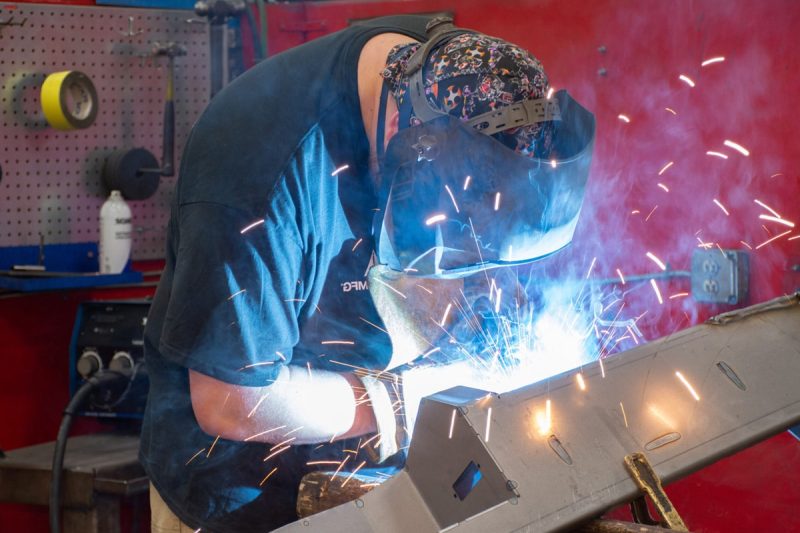
Çevre ve Güvenlik Hususları
Emisyonlar ve Çevresel Etki
Mesleki Sağlık ve Güvenlik Tehlikeleri
Mevzuata Uygunluk ve Standartlar
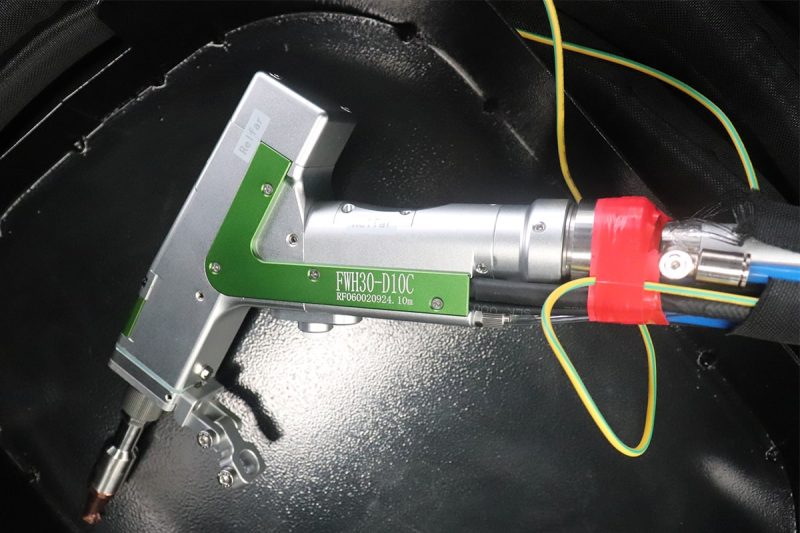
özetle
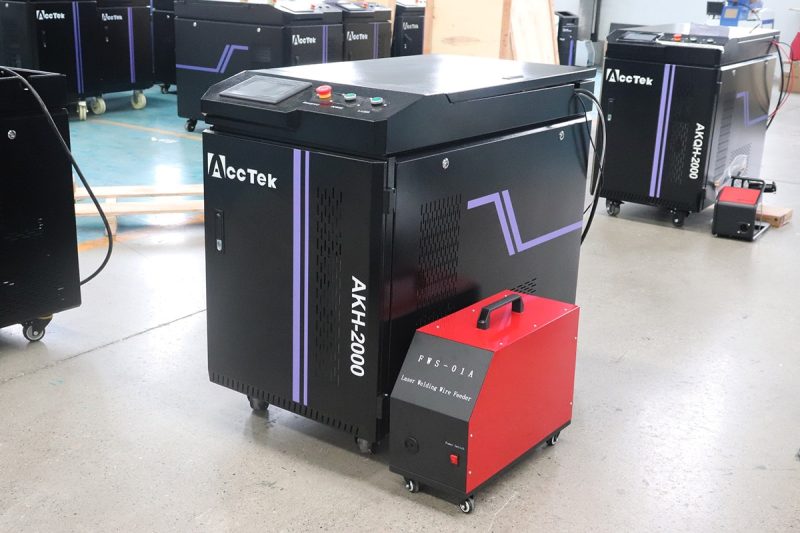
Lazer Çözümleri Alın
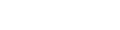
- [email protected]
- [email protected]
- +86-19963414011
- 3 Bölge A, Lunzhen Sanayi Bölgesi, Yucheng Şehri, Shandong Eyaleti.