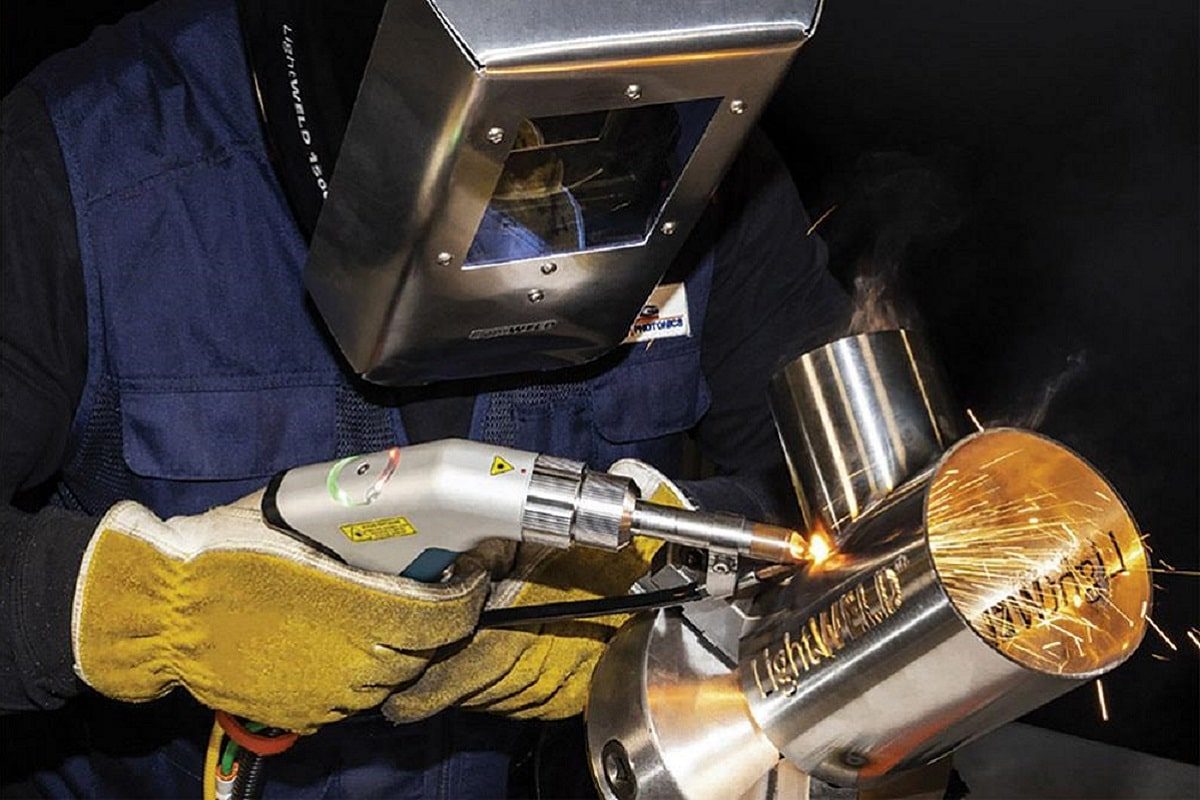
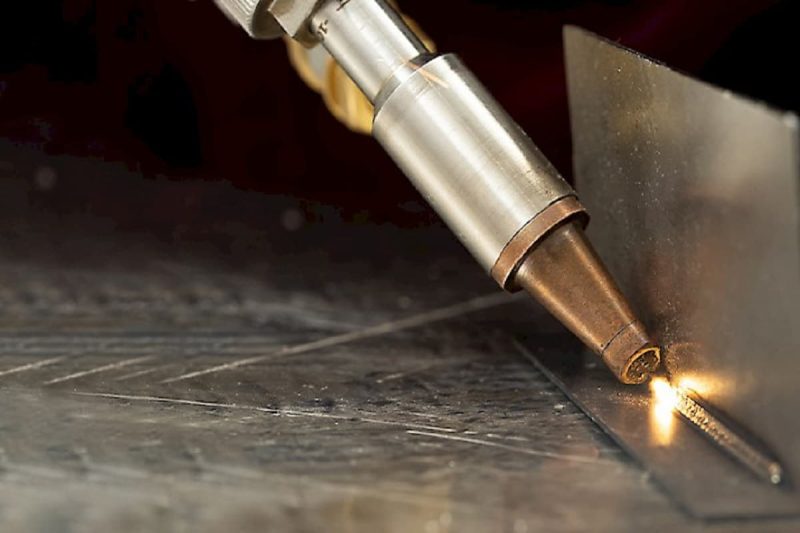
Lazer kaynağı nedir?
Lazer kaynağı nasıl çalışır?
Lazer kaynağı, metal veya termoplastiği birleştirmek için odaklanmış bir lazer ışını kullanır. Havacılık ve uzay ve tıbbi cihazlardan, mücevher imalatına kadar birçok sektörde kullanılabilir. Lazer kaynağının temel çalışma prensibi aşağıdaki gibidir:
- Lazer kaynağı: Yaygın olarak kullanılan lazer kaynakları arasında karbondioksit lazer jeneratörleri, fiber lazer jeneratörleri ve diyot lazer jeneratörleri bulunur. Bu lazer kaynakları, monokromatik, oldukça tutarlı ve oldukça yönlü lazer ışınları üretme kapasitesine sahiptir.
- Işın odaklama: İş parçasını hızlı bir şekilde ısıtmak için ışının enerjisini kaynak alanına yoğunlaştırmak için lazer ışınının bir mercek veya reflektör aracılığıyla odaklanması gerekir.
- Emilim ve İletim: Lazer ışını iş parçasının yüzeyini ışınladıktan sonra, enerji yansıtılmak yerine iş parçası tarafından emilecektir. Lazer enerjisinin ne ölçüde emildiği malzemenin türüne ve rengine bağlıdır.
- Erime ve füzyon: Lazer ışınının yüksek enerji yoğunluğu, kaynak alanını hızla erime noktasının üzerine çıkararak iş parçası malzemesinin anında erimesine neden olur.
- Soğutma ve katılaşma: Lazer ışını ışınımı durduğunda kaynak alanı hızla soğur ve erimiş metal katılaşır. İş parçaları sıkı bir şekilde bağlanmıştır.
Lazer kaynağının avantajları
Lazer kaynağı çok yönlüdür ve hibrit lazer ark kaynağı oluşturmak için geleneksel ark kaynağıyla birleştirilebilir. Ortaya çıkan kaynak, lazer kaynağının ve ark kaynağının avantajlarını birleştirir. Lazer kaynağının geleneksel kaynak teknolojilerine göre çeşitli avantajları vardır:
- Yüksek hassasiyet: Lazer kaynağı çok yüksek konumlandırma doğruluğuna ve kaynak kalitesine sahiptir ve mikron düzeyinde kaynak doğruluğu elde edebilir. Lazer kaynakla üretilen kaynaklar da genellikle daha yüksek kalitededir; bu da onları mikroelektronik imalatı ve tıbbi cihazlar gibi yüksek hassasiyette kaynak gerektiren uygulamalar için özellikle uygun kılar.
- Temassız: Lazer kaynağı, iş parçası yüzeyine zarar vermeyen ve fiziksel temas gerektirmeyen temassız bir işlemdir. Lazer kaynağında kırılgan malzemelerle veya hassas parçalarla çalışırken çok avantajlıdır.
- Çevrenin korunması: Geleneksel kaynakla karşılaştırıldığında lazer kaynağı genellikle daha az atık ve zararlı gaz emisyonu üretir ve daha çevre dostudur.
- Düşük ısı girişi: Lazer kaynağının ısı girişi düşüktür çünkü kaynak alanı çok küçüktür, bu da deformasyonu ve ısıdan etkilenen bölgenin boyutunu azaltır. İnce sac malzemelerin ve ısıya duyarlı bileşenlerin kaynaklanması sırasında bu çok önemlidir.
- Daha hızlı işlem süresi: Lazer kaynağı hızlıdır ve kaynak görevlerini hızla tamamlayabilir ve üretim verimliliğini artırabilir. Ayrıca lazer kaynağı dolgu malzemesi gerektirmediğinden malzeme israfını azaltır. Ve prosesin geleneksel kaynağa göre daha uygun maliyetli olduğu kanıtlanmıştır.
- Geniş uygulanabilirlik: Lazer kaynağı, metaller, plastikler, seramikler vb. dahil olmak üzere çeşitli malzemeler üzerinde kullanılabilir ve bu da onu çeşitli endüstriyel alanlarda yaygın olarak kullanılmasını sağlar.
- Lazer kaynağı çok yönlüdür ve hibrit lazer ark kaynağı oluşturmak için geleneksel ark kaynağıyla birleştirilebilir. Ortaya çıkan kaynak, lazer kaynağının ve ark kaynağının avantajlarını birleştirir.
Lazer kaynağının dezavantajları
Lazer kaynağı yüksek hassasiyet ve verimliliğe sahip modern bir kaynak teknolojisidir ancak aynı zamanda bazı eksiklikleri ve sınırlamaları da vardır. Lazer kaynağının ana dezavantajlarından bazıları şunlardır:
- Yüksek maliyet: Lazer jeneratörleri, optik bileşenler, soğutma sistemleri vb. dahil olmak üzere lazer ekipmanının satın alma ve bakım maliyetleri nispeten yüksektir. Bu, lazer kaynağının küçük işletmeler veya sınırlı bütçeli üreticiler tarafından benimsenmesini sınırlayabilir.
- Yüksek malzeme seçimi gereksinimleri: Lazer kaynağının malzeme ve iş parçasının kalitesi konusunda nispeten yüksek gereksinimleri vardır. Metaller gibi yüksek iletkenliğe sahip malzemeler için daha uygun olmakla birlikte bazı iletken olmayan veya şeffaf malzemeler için uygulama aralığı sınırlıdır.
- Yüksek erime noktasına sahip malzemelerin işlenmesindeki zorluk: Tungsten, molibden vb. gibi yüksek erime noktasına sahip malzemelerle karşılaştırıldığında, lazer kaynağı daha yüksek güç ve daha uzun kaynak süresi gerektirir, bu da termal etkilere ve deformasyon sorunlarına yol açabilir.
- Yüksek temizlik gereksinimleri: Lazer kaynağının iş parçası yüzeyinin kalitesi açısından çok yüksek gereksinimleri vardır. Küçük lekeler, oksit tabakaları veya gres bile kaynak kalitesini etkileyebilir. Bu nedenle kaynak öncesinde genellikle dikkatli yüzey hazırlığı ve temizliği gerekir.
- Güvenlik sorunları: Lazer ışınları yüksek enerjiye sahiptir ve insan gözlerine ve cildine zarar verebilir. Bu nedenle operatörlerin uygun koruyucu gözlük ve kıyafet giymek gibi gerekli güvenlik önlemlerini alması gerekir.
- Görünür ışık girişimi: Görünür ışık lazerlerinin, görünür ışık tarafından etkilenmesi muhtemeldir; bu, çalışma alanındaki ışığın uygun şekilde kontrol edilmesini sağlamak için önlemler alınmasını gerektirir.
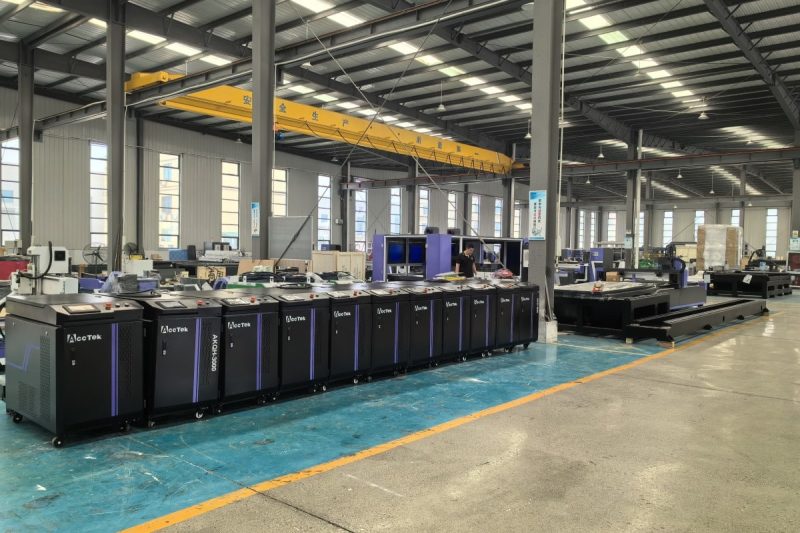
Geleneksel kaynak nedir?
Geleneksel Kaynak Nasıl Çalışır?
Geleneksel kaynak teknikleri, metalleri veya diğer malzemeleri birleştirmek için uzun yıllardan beri kullanılan ve çok çeşitli imalat ve onarım alanlarında kullanılan bir dizi geleneksel yöntemdir. İşte bazı yaygın geleneksel kaynak teknikleri:
- Ark kaynağı: Ark kaynağı, kaynak malzemelerini ve iş parçalarını eritmek için yüksek sıcaklıklar üretmek ve ardından bunları bir kaynak oluşturmak üzere soğutup katılaştırmak için ark kullanan yaygın bir geleneksel kaynak yöntemidir. Ana ark kaynağı yöntemleri arasında manuel ark kaynağı, gaz korumalı kaynak (MIG), manuel metal ark kaynağı (SMAW/ARC) ve TIG kaynağı (GTAW) bulunur.
- Gaz kaynağı: Kaynak malzemelerini ısıtmak, eritmek ve birleştirmek için alev kullanmak. En yaygın gaz kaynağı yöntemi, iş parçasını ısıtmak için asetilen ve oksijen alevi kullanan ve sac, boru ve metal onarımları için uygun olan asetilen-oksijen kaynağıdır.
- Direnç kaynağı: Isı üretmek için iş parçasının içinden geçecek elektrik akımı kullanılarak iki metal parçanın birleştirilmesi. Ana direnç kaynağı yöntemleri punta kaynağı, dikiş kaynağı ve lehimlemeyi içerir.
- Basınçlı Kaynak: Basınçlı kaynak, iki metal parçasını ısı ve basınç uygulayarak bir araya getirme yöntemidir ve dirençli nokta kaynağı, dirençli dikiş kaynağı ve elektronikleri içerir.
Geleneksel kaynağın avantajları
Bununla birlikte, geleneksel kaynak işlemleri birçok endüstri için dayanıklı bir üretim çözümü olmaya devam etmektedir ve lazer kaynak, geleneksel kaynak yöntemlerine göre çeşitli avantajlar sunmaktadır. Spesifik noktalar aşağıdaki gibidir:
- Düşük maliyet: Geleneksel kaynak ekipmanı genellikle nispeten ucuzdur ve operatörlerin eğitimi daha ucuzdur. Bu, ilk yatırım ve işletme maliyetlerini azaltır ve sınırlı bütçeye sahip işletmeler için uygundur.
- Yaygın olarak uygulanabilir: Geleneksel kaynak teknolojisi, metallerden plastiğe kadar çok çeşitli malzemelerde ve çeşitli kalınlıktaki levhalarda kullanılabilir. Bu çok yönlülük, onu çeşitli uygulamalar için uygun hale getirir.
- Büyük yapıların kaynaklanması: Geleneksel kaynak teknikleri köprüler, binalar ve gemi inşaatı gibi büyük yapıların kaynaklanması için uygundur. Güçlü bağlantı ve uygulanabilirliğe sahiptir.
- Dayanıklılık: Geleneksel kaynak teknikleri genellikle araçlar ve mühendislik yapıları gibi yüksek mukavemetli bağlantılar gerektiren uygulamalar için uygun, güçlü bağlantılar üretir.
- Otomasyon uygulaması: Geleneksel kaynak teknolojisi, özellikle seri üretimde üretim verimliliğini artırmak için otomasyon ve robotik ile birleştirilebilir.
- Alt tabakanın uyarlanabilirliği: Geleneksel kaynak yöntemleri, farklı metalik ve metalik olmayan malzemeler de dahil olmak üzere çeşitli alt tabaka türleri için uygundur.
- Onarım ve Restorasyon: Geleneksel kaynak teknikleri, özellikle güç kaynaklarından uzakta veya karmaşık ortamlarda onarım ve bakımda hala önemli bir role sahiptir.
- Füzyon Derinliği: Geleneksel kaynak genellikle daha büyük bir kaynak derinliğine sahiptir ve daha derin kaynak gerektiren uygulamalar için uygundur.
- Kaynak malzemelerinin mevcudiyeti: Geleneksel kaynak yöntemleri genellikle kolaylıkla bulunabilen ortak dolgu malzemeleri kullanır.
Geleneksel kaynağın dezavantajları
Geleneksel kaynak teknolojileri hala birçok uygulamada değerlidir ancak aynı zamanda bazı dezavantajları ve sınırlamaları da vardır. Geleneksel kaynak teknolojilerinin lazer kaynak teknolojilerine kıyasla temel dezavantajlarından bazıları şunlardır:
- Daha düşük doğruluk: Kaynak işlemi, iş parçası deformasyonuna, boyutsal dengesizliğe veya kaynaklı bağlantıda yanlışlıklara yol açabilecek büyük kaynak genişlikleri ve ısıdan etkilenen bölgeler üretebilir.
- Büyük termal etki: Geleneksel kaynak teknolojisinin ürettiği ısı girdisi nispeten yüksektir; bu, iş parçası üzerinde kolayca büyük ölçekli termal etkiye neden olabilir; bu, özellikle ısıya duyarlı malzemeler söz konusu olduğunda iş parçasının performansını ve kalitesini olumsuz yönde etkileyebilir. .
- Daha düşük üretim verimliliği: Geleneksel kaynak, yavaş kaynak hızı nedeniyle genellikle nispeten uzun bir kaynak süresi gerektirir. Bu, büyük ölçekli üretimin verimliliğini sınırlar ve üretim maliyetlerini artırabilir.
- Daha yüksek atık ve gaz emisyonları: Geleneksel kaynak genellikle daha fazla dolgu malzemesi ve atık malzeme gerektirir ve büyük miktarda atık ve çevreye zarar veren zararlı gaz emisyonları üretir.
- Büyük güvenlik riskleri: Geleneksel kaynaklama sırasında oluşan alevler ve ısı sıçraması, operatörler ve çevre için tehlike yaratabilir.
- Temizleme ve işlem sonrası gereksinimler: Geleneksel kaynak işlemleri, kaynak kalıntılarını gidermek veya kaynak kalitesini artırmak için genellikle sonraki temizleme ve işlem adımlarını gerektirir; bu, üretim süresini ve maliyetini artırır.
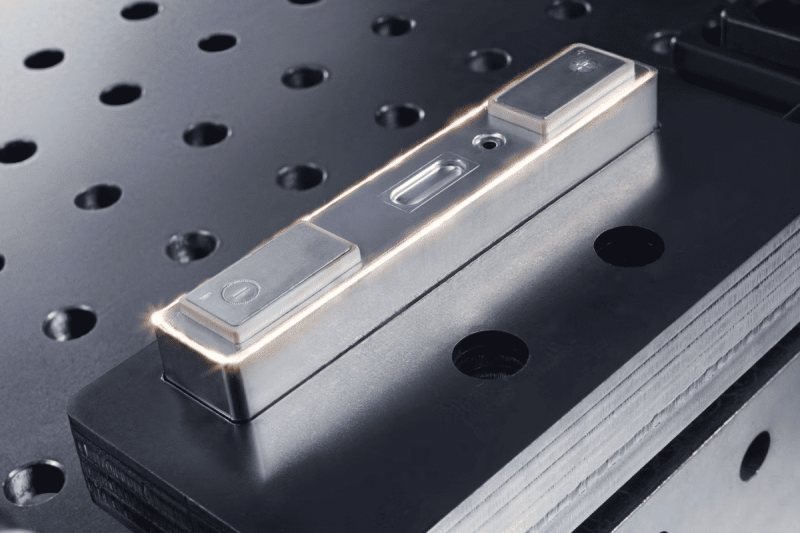
Lazer kaynağı vs geleneksel kaynak: hangi kaynak yöntemini seçmelisiniz?
Malzeme Türü
Doğruluk gereksinimleri
Termal etki
Üretim verimliliği
Maliyet hususları
Malzeme kalınlığı
Çevre ve güvenlik gereksinimleri
özetle
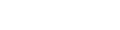
- [email protected]
- [email protected]
- +86-19963414011
- 3 Bölge A, Lunzhen Sanayi Bölgesi, Yucheng Şehri, Shandong Eyaleti.