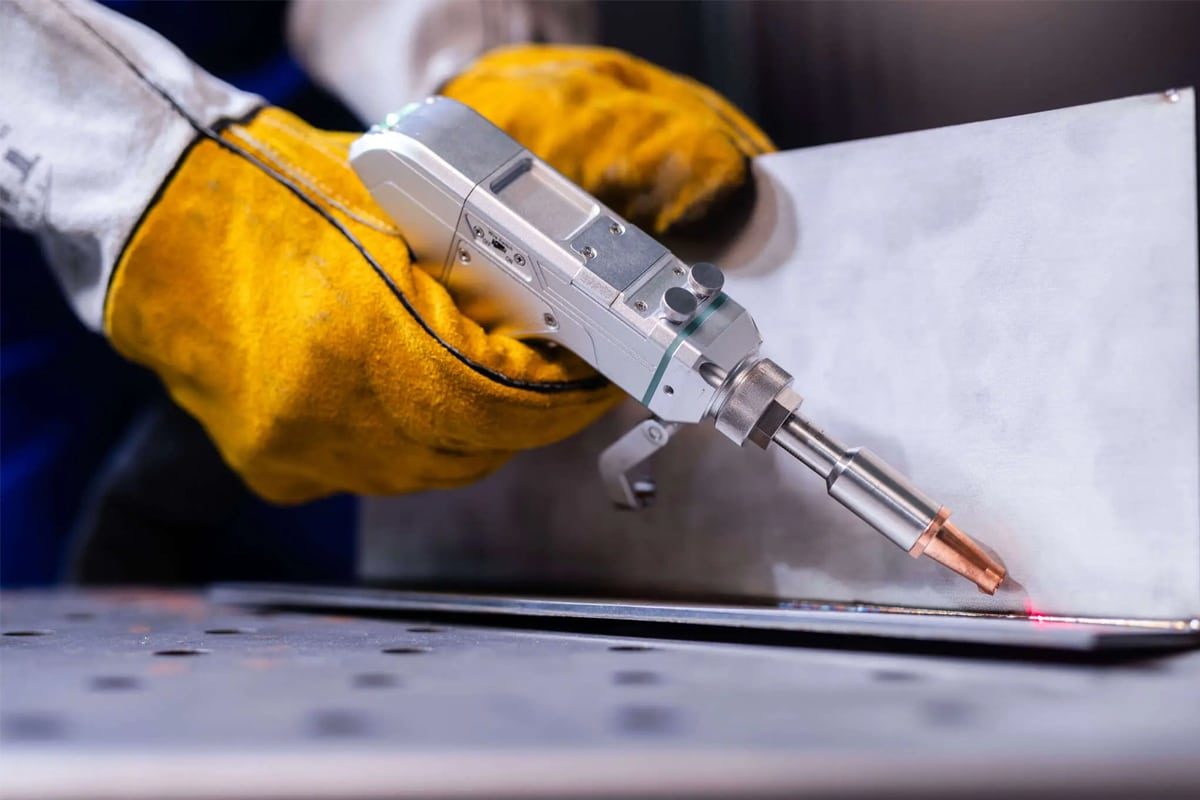
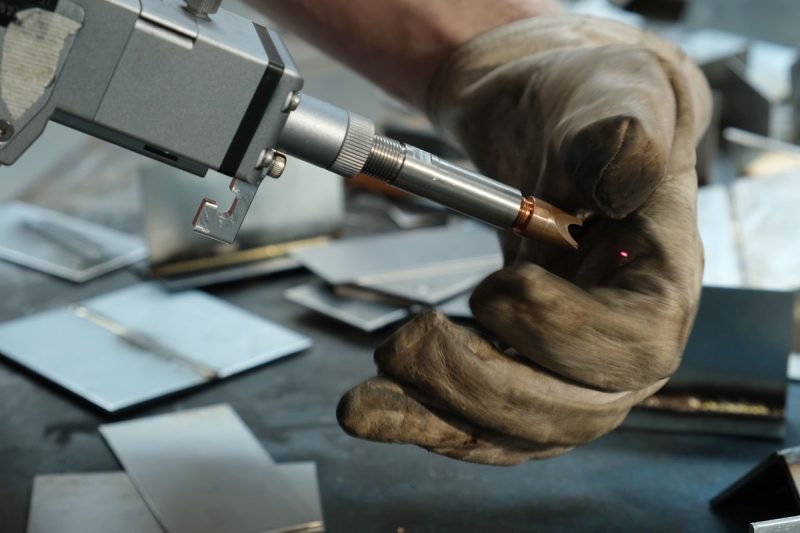
Lazer Kaynak Nasıl Çalışır?
Lazer Kaynak İlkeleri
Lazer kaynak, yüksek enerjili lazer ışığını malzemenin küçük bir alanına odaklayarak çalışır. Bu yoğunlaştırılmış enerji, malzemeyi hızla ısıtır ve erimesine ve kaynaşmasına neden olur. Genellikle daha geniş ısı bölgelerine dayanan geleneksel kaynaktan farklı olarak, lazer kaynak, minimum ısıdan etkilenen bölgeler oluşturmaya, bozulmayı azaltmaya ve daha temiz, yüksek kaliteli bağlantılar sağlamaya odaklanır. Füzyon, iki temel moddan birinde gerçekleşir: İletim Modu veya Anahtar Deliği Modu.
- Lazer Gücü ve Odaklanma: Lazerin güç yoğunluğu ve nokta boyutu, kaynağın derinliğini ve genişliğini belirler. Daha yüksek güç yoğunlukları daha derin kaynaklar üretirken, daha düşük güç ayarları daha ince, sığ kaynaklar için kullanılır.
- Isı Kontrolü: Lazer kaynak, ısıya duyarlı malzemelerin veya karmaşık parçaların birleştirilmesinde önemli olan ısı girişinin hassas bir şekilde kontrol edilmesini sağlar.
Lazer Kaynak Modlarının Türleri
İletken Mod Kaynak
Özellikler:
- Sığ kaynak penetrasyonu, genellikle 2 mm'den azdır.
- Minimum yüzey deformasyonu ile düzgün, geniş kaynaklar.
- Anahtar deliği oluşma riski minimumdur, gözeneklilik veya boşluk oluşma olasılığı azalır.
Uygulamalar:
- Genellikle ince malzemelerde ve görsel kalitenin önemli olduğu uygulamalarda kullanılır.
- Mücevher, tıbbi cihazlar ve elektronikte temiz yüzey kalitesinin gerekli olduğu uygulamalar için idealdir.
Anahtar Deliği Modu Kaynak
Özellikler:
- Derin kaynak penetrasyonu (birkaç santimetreye kadar) ve dar genişliktedir.
- Yüksek en boy oranı, güçlü ve odaklanmış kaynaklarla sonuçlanır.
- Anahtar deliği içerisinde çoklu yansımalar nedeniyle oluşan verimli enerji emilimi, daha derin kaynak penetrasyonunu destekler.
Uygulamalar:
- Otomotiv ve havacılık bileşenleri gibi güçlü ve dayanıklı bağlantılar gerektiren ağır hizmet uygulamaları için uygundur.
- Derin füzyonun gerektiği kalın malzemeler ve yüksek dayanımlı metaller için etkilidir.
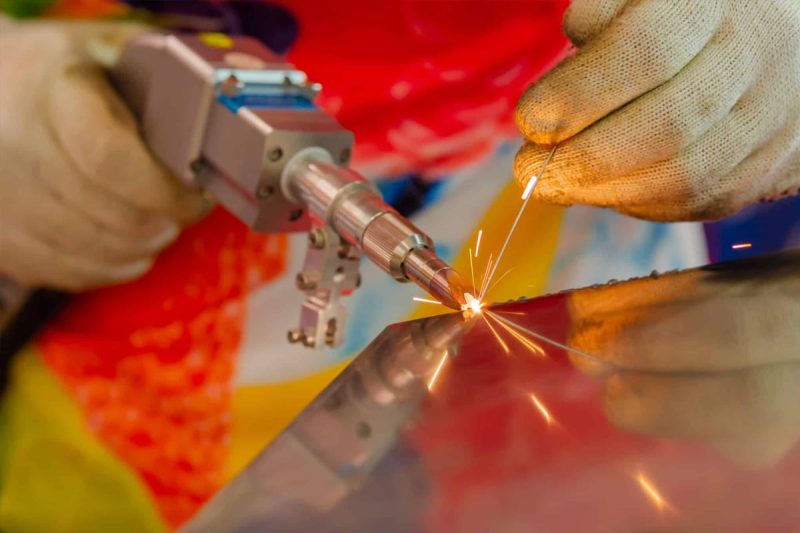
Lazer Kaynağın Avantajları
Hassasiyet ve doğruluk
Yüksek Kaynak Hızı
Temassız İşlem
Derin Penetrasyon ve Dar Kaynaklar
Zor Malzemeleri Kaynaklama Yeteneği
Minimum Bozulma ve Isıdan Etkilenen Bölgeler
Temiz ve Estetik Kaynaklar
Düşük Bakım ve İşletme Maliyetleri
Enerji verimliliği
Otomasyon ve Esneklik
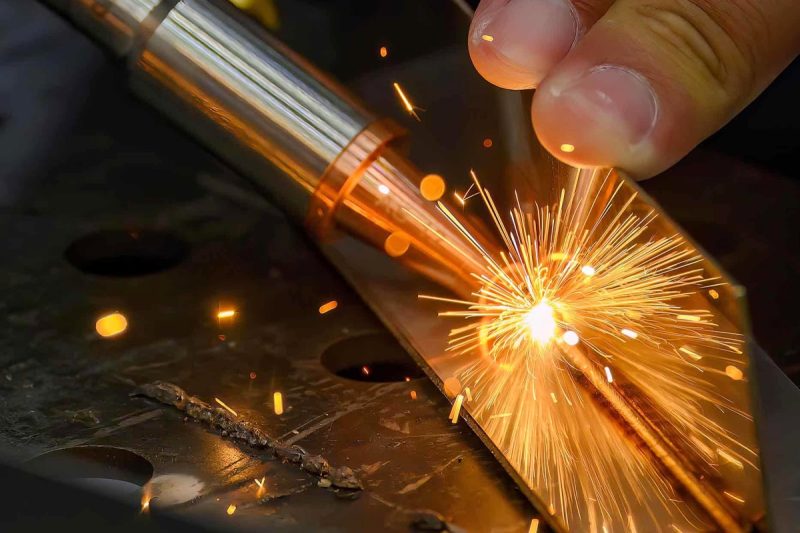
Lazer Kaynağının Dezavantajları
Yüksek İlk Yatırım
Sınırlı Kalınlıkta Kaynak
Eklem Uyumluluğuna Duyarlılık
Güvenlik endişeleri
Yansıtma Sorunları
Teknik Karmaşıklık
Ekipman Hassasiyeti
Sınırlı Alan Kullanımı
Nitelikli Operatörler Gerektirir
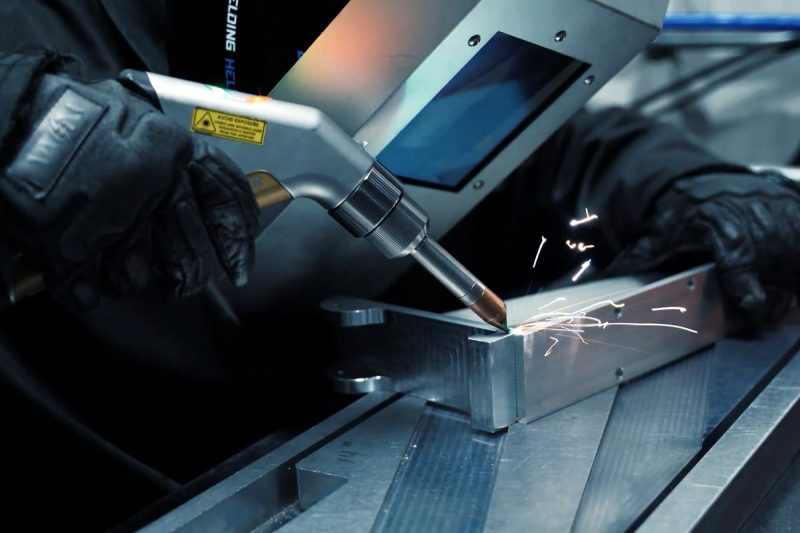
Lazer Kaynak Uygulamaları
Otomotiv endüstrisi
Otomotivdeki Uygulamalar:
- Gövde panelleri ve özel yapım boşluklar.
- Şanzıman parçaları da dahil olmak üzere motor parçaları.
- Hava yastığı kasaları hassasiyet ve güvenilirlik gerektirir.
- Egzoz sistemleri, yüksek sıcaklıklara ve basınçlara dayanıklı kaynaklara ihtiyaç duyar.
Havacılık ve Uzay Endüstrisi
Havacılık ve Uzay Alanındaki Uygulamalar:
- Yakıt sistemleri ve hidrolik hatlarında sızdırmaz kaynak yapılması gerekmektedir.
- Gövde parçaları ve iniş takımları da dahil olmak üzere yapısal bileşenler.
- Dayanıklılığın ve sıcaklık direncinin kritik öneme sahip olduğu türbin kanatları ve diğer motor parçaları.
- Havacılık elektroniği, uzun vadeli güvenilirliği garanti altına almak için hassas ve temiz kaynaklara ihtiyaç duyar.
Tıbbi Cihaz İmalatı
Tıbbi Cihaz Üretimindeki Uygulamalar:
- Korozyon direnci ve temizliğin önemli olduğu cerrahi aletler.
- Kalp pili kılıfları ve ortopedik cihazlar gibi tıbbi implantlar biyouyumlu, hava geçirmez kaynaklar gerektirir.
- Kateterler ve endoskoplar küçük parçalarda ince ve hassas kaynaklara ihtiyaç duyar.
- Uzun süreli kullanım için kaynak bütünlüğünün kritik önem taşıdığı tıbbi cihazlar için pil muhafazaları.
Elektronik Sanayi
Elektronikte Uygulamalar:
- Devre kartı bağlantıları, yakındaki bileşenlere zarar vermeden ince ve doğru kaynaklar sağlar.
- Sensör muhafazaları ve pil bağlantıları güçlü, dayanıklı bağlantılara ihtiyaç duyar.
- Hassas elektronik komponentlerin çevresel etkenlerden korunmasını sağlayan muhafazalar.
- Yarı iletken üretiminde hassasiyet ve temizliğin kritik öneme sahip olduğu mikro kaynak.
Mücevher Endüstrisi
Mücevherat Alanındaki Uygulamalar:
- Mevcut mücevherlerde, yüzüklerin boyutunu değiştirme veya kopan zincirleri onarma gibi onarımlar.
- Değerli taşların yakınında ısı hasarına neden olmadan güvenli kaynak yapılmasını sağlayan taş yerleştirme.
- Özel takı tasarımlarında detaylı, hassas kaynakların gerekli olduğu karmaşık metal işçiliği.
- Altın ve platini birleştirerek temiz ve görünmez kaynak dikişleri ile karışık metal tasarımları oluşturmak.
Enerji Sektörü
Enerji Alanındaki Uygulamalar:
- Hücreler ve terminaller arasında dayanıklı bağlantılar oluşturan lazer kaynak yöntemiyle pil üretimi.
- Yakıt hücreleri ve güneş paneli bileşenleri temiz ve hassas kaynaklardan faydalanır.
- Yüksek basınç altında güvenlik açısından yüksek dayanımlı kaynakların önemli olduğu petrol ve gaz borulamaları.
- Rüzgar türbini bileşenleri, yapısal parçalar da dahil olmak üzere, hava koşullarına ve mekanik zorlanmalara dayanıklı olmalıdır.
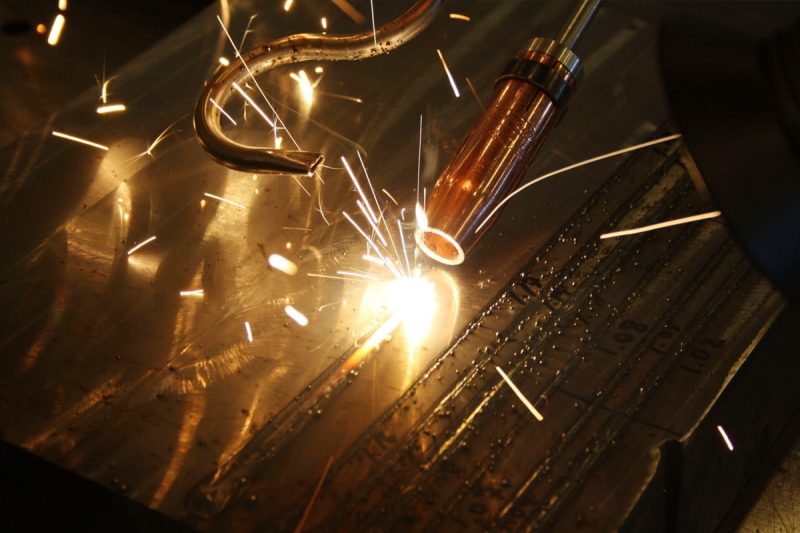
Geleneksel Kaynak Yöntemleriyle Karşılaştırma
Lazer Kaynak ve TIG Kaynak
- Tungsten İnert Gaz (TIG) Kaynağı, alüminyum, paslanmaz çelik ve bakır dahil olmak üzere çok çeşitli metallerde yüksek kaliteli, temiz kaynaklar üretmesiyle bilinir. TIG kaynağı, elektrot ile iş parçası arasında bir ark oluşturmak için bir tungsten elektrot kullanır, metali eritir ve genellikle bir dolgu malzemesi gerektirir.
- Hassasiyet ve Doğruluk: Hem lazer hem de TIG kaynak yüksek hassasiyet sunar, ancak lazer kaynak, minimum ısıdan etkilenen bölgeler (HAZ) ile son derece dar kaynaklar oluşturabilen odaklanmış ışını nedeniyle bir avantaja sahiptir. TIG kaynak daha fazla manuel kontrol gerektirir ve daha yavaştır, bu da onu hassas bileşenlerdeki küçük, karmaşık kaynaklar için daha az uygun hale getirir.
- Isı Girişi ve Bozulma: Lazer kaynaklamanın yoğunlaştırılmış enerji girişi, TIG kaynaklamaya kıyasla çok daha küçük bir HAZ oluşturur. Bu, özellikle ince malzemeler ve ısıya duyarlı uygulamalar için önemli olan termal bozulma riskini azaltır. Kontrollü olsa da TIG kaynaklama, daha geniş bir alana yayılan daha fazla ısı üretir ve bu da daha ince malzemelerde eğrilmeye neden olabilir.
- Hız: Lazer kaynak, TIG kaynaktan önemli ölçüde daha hızlıdır ve bu da onu yüksek hacimli üretim için daha uygun hale getirir. TIG kaynak, yüksek kaliteli sonuçlar üretebilmesine rağmen, manuel işlem ve hassasiyet gerektirdiğinden daha yavaştır ve bu da onu daha küçük projeler veya onarımlar için daha uygun hale getirir.
- Uygulamalar: TIG kaynak genellikle havacılık ve otomotiv parçaları gibi küçük ölçekli ve hassas projelerde kullanılır ancak genellikle hız ve otomasyon uyumluluğu sınırlıdır. Lazer kaynak, elektronik, tıbbi cihazlar ve yüksek hacimli otomotiv bileşenleri gibi hem hız hem de hassasiyet gerektiren uygulamalar için idealdir.
Lazer Kaynak ve MIG Kaynak
- Metal İnert Gaz (MIG) Kaynağı, özellikle hız ve üretim hacminin öncelikli olduğu uygulamalarda daha kalın malzemeleri birleştirmek için kullanılan yaygın bir kaynak yöntemidir. MIG kaynağı, genellikle daha geniş bir kaynak alanı üreten ve sıçramayı gidermek için son işlem gerektiren bir kaynak oluşturmak için eriyen sürekli beslenen bir tel elektrot kullanır.
- Penetrasyon ve Kaynak Genişliği: Lazer kaynak, dolgu malzemesine ihtiyaç duymadan kalın malzemelerde bile dar bir kaynak boncuğu ile derin penetrasyon elde edebilir. MIG kaynak, genellikle ek temizlik ve son işlem gerektiren daha geniş, daha az hassas bir kaynak üretir. Güçlü, dar kaynaklar gerektiren uygulamalar için lazer kaynak daha uygundur.
- Isıdan Etkilenen Bölge: MIG kaynak, lazer kaynaktan daha fazla ısı üretir, daha büyük bir HAZ oluşturur ve termal bozulma riskini artırır. Lazer kaynaklamanın yoğunlaştırılmış ısısı, HAZ'ı azaltarak çevredeki malzemenin mekanik özelliklerini korur ve özellikle ince veya ısıya duyarlı malzemelerde kaynak sonrası bozulmayı en aza indirir.
- Otomasyon ve Üretim Hızı: Lazer kaynak, otomasyonla oldukça uyumludur ve çok daha yüksek hızlarda çalışabilir, bu da onu yüksek hacimli üretim ortamları için ideal hale getirir. MIG kaynak, TIG'den daha hızlı olmasına rağmen, tel besleme ve koruyucu gaz ihtiyacı nedeniyle genellikle manuel veya yarı otomatik işlemler için daha uygundur.
- Malzemeler: MIG kaynak, çelik ve alüminyum gibi daha kalın malzemeler ve yaygın olarak kullanılan metaller için etkilidir, ancak hassasiyet ve düşük ısı girişinin gerektiği farklı malzemeler ve çok ince malzemelerle mücadele eder. Lazer kaynak, hassas enerji kontrolü nedeniyle bakırdan paslanmaz çeliğe kadar hem ince hem de farklı metalleri birleştirmede mükemmeldir.
Lazer Kaynaklama ve Elektron Işını Kaynaklama
- Elektron Işını (EB) Kaynağı, derin ve hassas kaynaklar üretme yeteneği bakımından lazer kaynağına benzer yüksek enerjili bir kaynak işlemidir. EB kaynağı, malzemeleri birleştirmek için vakumda odaklanmış bir elektron ışını kullanır ve bu da onu çok derin penetrasyon ve kontrollü bir ortam gerektiren zorlu uygulamalar için uygun hale getirir.
- Ortam ve Kurulum: Açık havada çalışabilen lazer kaynak yönteminin aksine, EB kaynak yöntemi elektron ışınını korumak için bir vakum odası gerektirir. Bu vakum kurulumu, EB kaynak yöntemini temiz odalar veya yarı otomatik üretim hatları gibi daha geniş bir ortam yelpazesinde kullanılabilen lazer kaynak yönteminden daha karmaşık, maliyetli ve daha az esnek hale getirir.
- Penetrasyon Derinliği ve Gücü: EB kaynak, lazer kaynaktan daha derin penetrasyona ulaşabilir ve bu da onu kalın malzemeler veya çok güçlü kaynaklar gerektiren yapısal uygulamalar için ideal hale getirir. Ancak, orta kalınlıkta ila ince malzemeler için lazer kaynak genellikle daha verimlidir ve uygulanması daha kolaydır.
- Hız ve Otomasyon: Lazer kaynak daha yüksek hızlara ulaşabilir ve otomatik üretim hatlarına entegre edilmesi daha kolaydır, bu da onu yüksek hacimli üretim için uygun hale getirir. EB kaynak, etkili olmasına rağmen, vakum odası gereksinimleri nedeniyle genellikle daha yavaştır ve otomatik, hızlı tempolu üretim ortamlarına daha az uyarlanabilir.
- Maliyet ve Bakım: EB kaynak sistemleri maliyetlidir ve özellikle vakum sistemi için özel bakım gerektirir. Lazer kaynak daha düşük bakım gereksinimlerine sahiptir, bu da onu düzenli üretim için daha erişilebilir ve uygun maliyetli hale getirir. Ek olarak, EB kaynak için kurulum süresi ve bakım, lazer kaynakla karşılaştırıldığında daha uzun duruş sürelerine yol açabilir.
Karşılaştırmak
- Hassasiyet ve Temiz Kaynaklar: Lazer kaynak, hassasiyet açısından MIG ve TIG kaynak yöntemlerini geride bırakırken, temiz ve hassas sonuçlar konusunda EB kaynak yöntemiyle rekabet etmektedir.
- Hız: Lazer kaynak, hem TIG hem de MIG kaynaktan daha hızlıdır ve özellikle hassasiyetin gerekli olduğu otomatik, yüksek hızlı üretim için genellikle daha uygundur.
- Çevre: Lazer kaynak yönteminin hava tabanlı ortamlardaki esnekliği, vakum gerektiren EB kaynak yöntemine göre onu daha çok yönlü hale getirir.
- Isıdan Etkilenen Bölge: Lazer kaynak yönteminin minimum HAZ değeri, ince ve ısıya duyarlı malzemeler için idealdir ve bu konuda TIG ve MIG kaynak yöntemlerinden daha iyi performans gösterir.
- Maliyet ve Karmaşıklık: Lazer kaynak yönteminin ilk maliyeti yüksektir ancak EB kaynak yöntemine kıyasla daha düşük bakım ve işletme maliyeti sunar; EB kaynak yöntemi daha karmaşık ekipman ve bakım gereksinimlerini içerir.
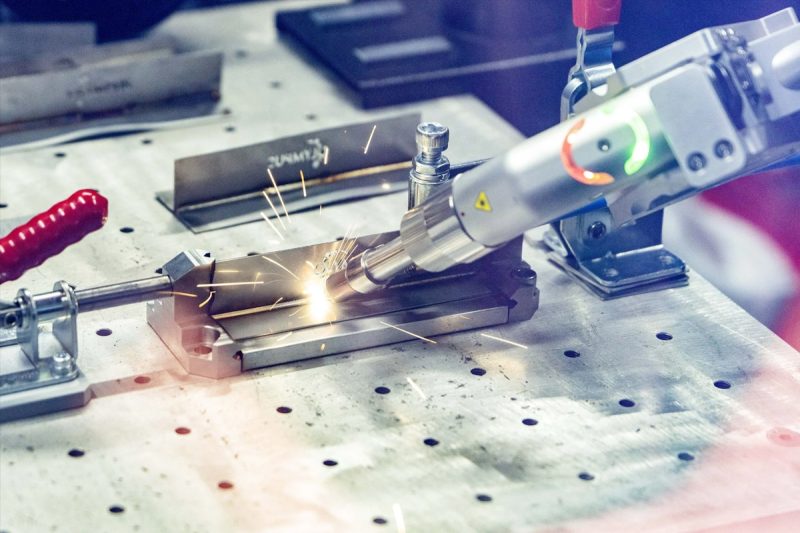
Lazer Kaynak Kalitesini Etkileyen Faktörler
Lazer Parametreleri
Lazerin ayarları ve özellikleri, kaynak kalitesini belirlemede önemli bir rol oynar. Temel lazer parametreleri arasında güç, odak noktası boyutu, kaynak hızı ve darbe frekansı (darbeli lazerler için) bulunur.
- Lazer Gücü: Daha yüksek güç, nüfuz derinliğini artırır ve daha hızlı kaynak yapılmasını sağlar ancak düzgün bir şekilde kontrol edilmezse aşırı ısıya yol açabilir. Çok fazla güç sıçramaya veya yanmaya neden olabilirken, çok az güç zayıf veya eksik kaynaklara yol açabilir.
- Kaynak Hızı: Lazerin iş parçası üzerinde hareket ettiği hız, kaynak kalitesini etkiler. Yüksek kaynak hızları ısı girişini azaltabilir, ısıdan etkilenen bölgeyi (HAZ) en aza indirebilir ve bozulmayı azaltabilir. Ancak, çok yüksek hızlar malzemelerin tam olarak kaynaşmasını önleyebilir ve zayıf bağlantılara neden olabilir. Daha düşük hızlar daha derin penetrasyona izin verir ancak ısı birikimini artırabilir ve potansiyel olarak termal bozulmaya neden olabilir.
- Odak Noktası Boyutu: Daha küçük bir odak noktası boyutu, enerjiyi küçük bir alana yoğunlaştırarak ince, dar kaynaklara olanak tanır. Odak noktası boyutu, birleştirme genişliğine uymalıdır; çok büyükse, aşırı ısı ve bozulmaya neden olabilir. Çok küçükse, daha kalın malzemeler için yeterince derine nüfuz edemeyebilir.
- Darbe Frekansı (Darbeli Lazerler): Darbeli lazerler gerektiren uygulamalar için, darbe frekansını ayarlamak kaynakta iletilen enerji miktarını kontrol etmeye yardımcı olur. Daha yüksek darbe frekansları daha pürüzsüz, sürekli kaynaklar sağlayabilirken, daha düşük frekanslar aralıklı enerji patlamaları sağlar ve bu da minimum ısı girişi gerektiren uygulamalar için faydalıdır.
Malzeme özellikleri
Kaynak yapılan malzeme, lazerin yüzeyle nasıl etkileşime girdiğini ve metale nasıl nüfuz ettiğini etkiler. Yansıtma, termal iletkenlik ve alaşım bileşimi gibi faktörlerin hepsi kaynak kalitesini etkiler.
- Yansıtma: Alüminyum ve bakır gibi yüksek yansıtma özelliğine sahip malzemeler, lazerin enerjisinin önemli bir kısmını yansıtarak emilimi azaltabilir. Daha düşük lazer dalga boyları veya yansıtıcı malzemelerin ön işlenmesi, emilimi artırmaya ve kaynak kalitesini iyileştirmeye yardımcı olabilir.
- Isıl İletkenlik: Bakır gibi yüksek ısıl iletkenliğe sahip malzemeler ısıyı hızla dağıtır ve uygun penetrasyona ulaşmak için daha yüksek lazer gücü veya ayarlanmış parametreler gerektirir. Titanyum gibi düşük iletkenliğe sahip malzemeler ısıyı tutar ve daha az güçle daha derin kaynaklara olanak tanır.
- Alaşım Bileşimi: Alaşımlar genellikle değişken erime noktalarına sahiptir ve tutarlı kaynaklar elde etmek için farklı lazer ayarları gerektirebilir. Bazı alaşımlar ayrıca daha fazla sıçrama üretir veya çatlamayı önlemek için farklı darbe frekansları gerektirir, özellikle kaynak sıcaklıklarında buharlaşabilen elementlere sahip olanlar.
- Yüzey Durumu: Malzemenin yüzeyinin temizliği ve bitişi, lazer ışınının ne kadar iyi emildiğini etkiler. Oksitler, yağlar veya yüzey kirleticileri kaynak işlemini bozabilir ve daha zayıf bağlantılara yol açabilir. Kaynaktan önce temizlik veya yüzey hazırlığı, kaynak tutarlılığını ve mukavemetini artırmaya yardımcı olabilir.
Ortak Tasarım ve Montaj
Eklemin tasarımı ve uyum kalitesi, nihai kaynak kalitesini önemli ölçüde etkiler. Uygun eklem tasarımı ve sıkı uyum, lazerin malzemeleri boşluklar veya yanlış hizalama olmadan hassas bir şekilde kaynaştırabilmesini sağlar.
- Derz Tasarımı: Farklı derz tipleri (örneğin, uç birleştirme, bindirme birleştirme ve fileto birleştirme) optimum sonuçları garantilemek için belirli lazer ayarları ve odaklama gerektirir. Örneğin, uç birleştirmeler daha derin penetrasyona ihtiyaç duyabilirken, bindirme birleştirmeler daha sığ olabilir ancak aşırı ısı yayılımını önlemek için kontrol gerektirir.
- Uyum Hassasiyeti: Parçalar arasındaki hassas hizalama, tutarlı kaynak kalitesi için olmazsa olmazdır. Herhangi bir boşluk veya hizalama hatası, kaynakta zayıf noktalar oluşturarak eksik füzyona yol açabilir. Sıkı uyumlar, lazer enerjisinin birleştirme boyunca etkili bir şekilde emilmesini sağlayarak kusur olasılığını en aza indirir. Son derece yakın toleranslar gerektiren uygulamalar için, kaynak sırasında parçaları güvenli bir şekilde tutmak için sıkıştırma ve sabitleme sistemleri kullanılabilir.
- Kalınlık Uyumluluğu: Bağlantı kalınlığı da kaynağın mukavemetini etkiler. Kalın malzemeler kaynaklandığında, lazer parametreleri çevredeki malzemeyi aşırı ısıtmadan tam olarak nüfuz edecek şekilde ayarlanmalıdır. İnce malzemeler ise, eğilmeyi veya yanmayı önlemek için daha düşük güç ayarları gerektirir.
Koruyucu gaz
Koruyucu gaz kullanımı, kaynak alanını kirlenme ve oksidasyondan korumaya yardımcı olur ve bu da kaynak kalitesini ve görünümünü etkileyebilir. Koruyucu gazın seçimi ve akışı, yüksek kaliteli kaynaklar elde etmede önemli bir rol oynar.
- Gaz Türü: Yaygın koruyucu gazlar argon, helyum ve nitrojeni içerir. Argon, kararlı bir atmosfer sağlar ve çeşitli metaller için yaygın olarak kullanılır. Helyum, yüksek termal iletkenliği nedeniyle genellikle derin penetrasyon için kullanılır, ancak daha pahalıdır. Nitrojen bazen paslanmaz çelik gibi belirli malzemeler için kullanılır, ancak bazı metallerde nitrürlere neden olabilir ve bu da potansiyel olarak mukavemeti etkileyebilir.
- Gaz Akış Hızı: Koruyucu gazın akış hızı, malzeme ve kaynak parametrelerine göre ayarlanmalıdır. Çok yüksek bir akış hızı kaynak havuzunu bozabilir ve türbülansa yol açabilirken, çok düşük bir akış hızı kaynağı tam olarak koruyamayabilir, oksidasyona ve renk bozulmasına veya gözenekliliğe yol açabilir.
- Dağıtım Yöntemi: Koruyucu gaz, lazer kafasının yakınındaki bir nozuldan doğrudan veya bazı durumlarda daha fazla kapsama alanı için ikincil bir gaz hattından iletilebilir. Uygun gaz dağıtımı, eşit dağılımı garanti ederek kaynağın havaya maruz kalmasını önler ve temiz, estetik bir kaynak bitişi sağlar.

Özet
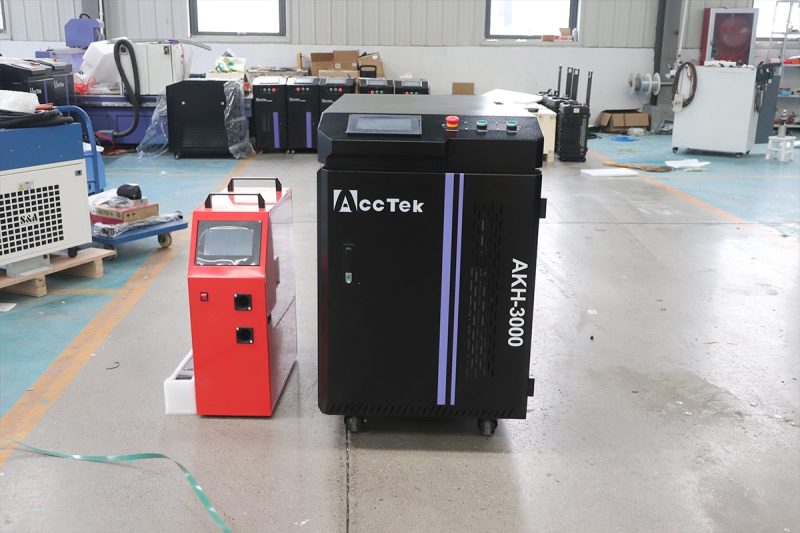
Lazer Kaynak Çözümlerini Alın
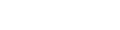
- [email protected]
- [email protected]
- +86-19963414011
- 3 Bölge A, Lunzhen Sanayi Bölgesi, Yucheng Şehri, Shandong Eyaleti.