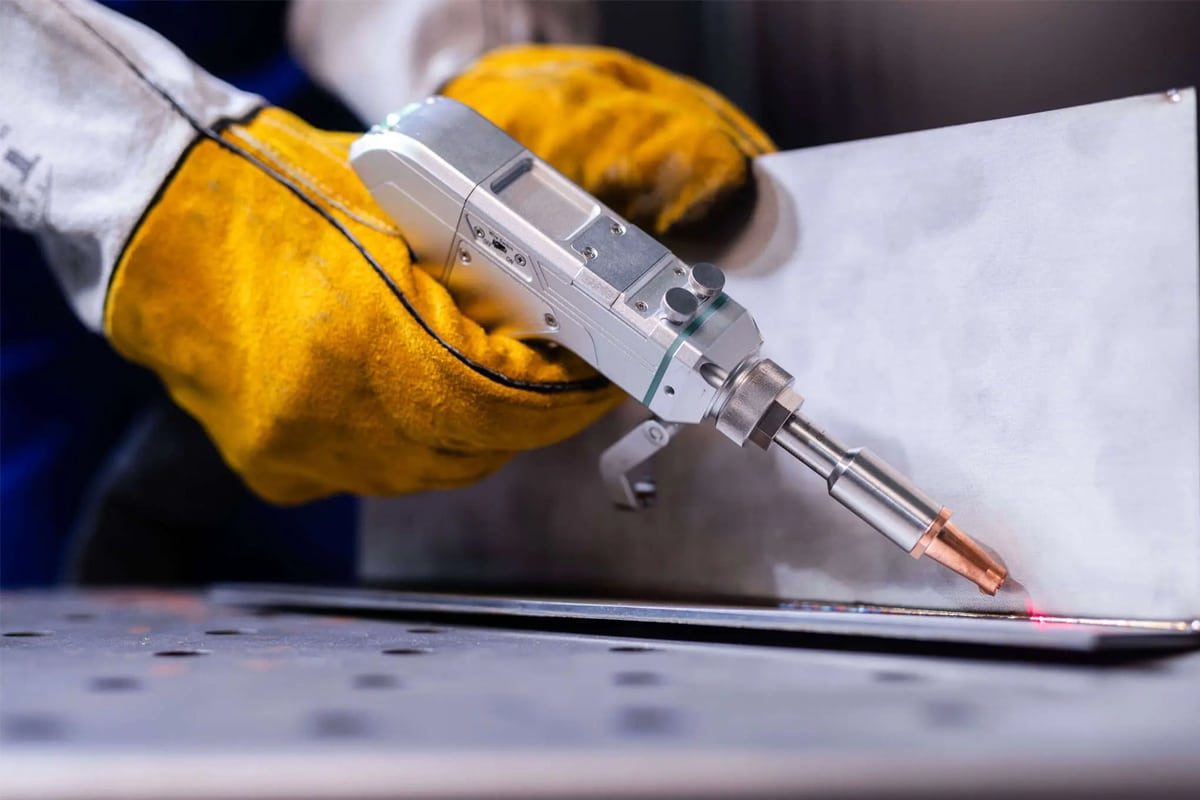
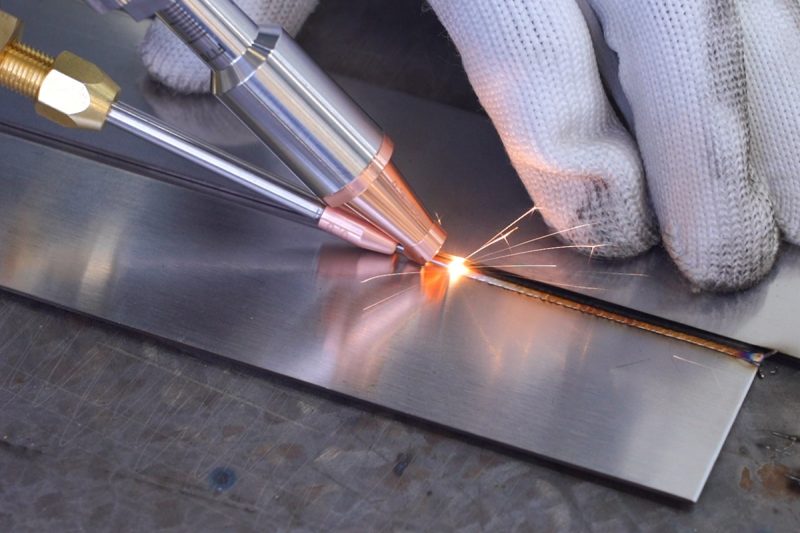
Lazer Kaynağına Genel Bakış
Lazer Kaynak Nedir?
Lazer kaynak, malzemeleri ısıtmak ve birleştirmek için oldukça odaklanmış bir lazer ışını kullanan hassas ve etkili bir birleştirme işlemidir. Lazer ışını, dar, derin kaynaklara izin veren, minimum ısıdan etkilenen bölgelere (HAZ) sahip yoğun bir ısı kaynağı üretir. Lazer kaynak, güç yoğunluğuna ve malzeme özelliklerine bağlı olarak iki ana modda çalışır:
- Anahtar Deliği Modu Kaynak: Bu modda, yüksek güç yoğunluklu bir lazer ışını malzemeyi buharlaştırarak erimiş metal ve buharla dolu dar, derin bir anahtar deliği oluşturur. Anahtar deliği, lazer enerjisi için bir kanal görevi görerek derin penetrasyon ve yüksek en boy oranlı kaynaklar sağlar. Bu mod, otomotiv ve havacılık endüstrileri gibi derin ve dar kaynaklar gerektiren uygulamalar için idealdir.
- İletim Modu Kaynağı: Bu mod, lazerin malzemeyi buharlaştırmadan ısıttığı anahtar deliği kaynağına kıyasla daha düşük güç yoğunluklarında gerçekleşir. Yüzeyden ısı iletimi sığ, daha geniş bir kaynak havuzu oluşturur. İletim modu kaynağı, ince malzemeler veya minimum penetrasyon ve ısı girişi istendiğinde uygundur.
Lazer Kaynağın Avantajları
Lazer kaynak, geleneksel kaynak yöntemlerine göre onu avantajlı kılan birçok avantaj sunar:
- Hassasiyet ve Doğruluk: Yoğunlaştırılmış lazer ışını, minimum bozulma ile doğru kaynaklar üreterek hassas kontrol sağlar.
- Yüksek Hızlı İşleme: Lazerin yüksek enerji yoğunluğu, hızlı kaynak hızlarını mümkün kılarak verimliliği artırır ve çevrim sürelerini azaltır.
- Minimum Isıdan Etkilenen Bölge: Azaltılmış termal yayılma, bozulmayı en aza indirir ve lazer kaynağını hassas veya ince bileşenler için uygun hale getirir.
- Otomasyon Kabiliyeti: Lazer kaynak, otomasyon sistemlerine ve robotik kollara kolayca entegre edilebilir ve yüksek hacimli üretimde verimliliği artırır.
- Malzeme Çok Yönlülüğü: Titanyum ve paslanmaz çelik gibi kaynaklanması zor malzemeler de dahil olmak üzere çok çeşitli metal ve alaşımları kaynaklama yeteneği.
- Temassız İşlem: Fiziksel temasa gerek duyulmadığından aletlerde aşınma ve yıpranma azalır ve elektrot kontaminasyonu riski ortadan kalkar.
Lazer Kaynak Uygulamaları
Lazer kaynak, benzersiz yetenekleri ve hassasiyeti nedeniyle birçok endüstride kullanılmaktadır:
- Otomotiv Endüstrisi: Yüksek hassasiyet ve hızın kritik olduğu araç gövde panelleri, dişliler, şanzıman parçaları ve egzoz sistemlerinin kaynaklanmasında kullanılır.
- Havacılık ve Uzay Sanayi: Türbin kanatları, yapısal parçalar ve motor bileşenleri gibi hafif, yüksek mukavemetli bileşenlerin kaynaklanması için uygundur.
- Elektronik Endüstrisi: Elektronik cihazlardaki hassas devrelerin, konnektörlerin ve muhafazaların mikro kaynaklanması için idealdir.
- Tıbbi Cihaz Üretimi: Hassasiyet ve temizliğin en önemli olduğu karmaşık tıbbi cihazların, cerrahi aletlerin ve implant bileşenlerinin kaynaklanmasında kullanılır.
- Mücevher ve Sanat: Karmaşık mücevher tasarımlarının ve sanatsal metal işçiliğinin detaylı onarımlarını ve üretimini sağlar.
- Endüstriyel Üretim: Çeşitli endüstriyel sektörlerde metal sacların, boruların ve ağır hizmet tipi yapısal bileşenlerin birleştirilmesinde uygulanır.
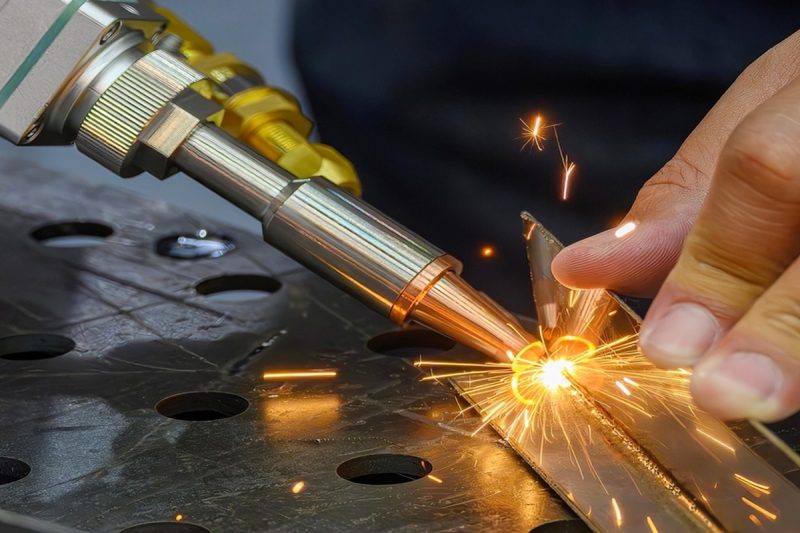
Lazer Kaynakta Yaygın Kaynak Kusurları
Gözeneklilik
Nedenler
- Yüzey Kirliliği: İş parçasının yüzeyindeki yağ, gres, nem ve pas ısıtıldığında gaz üretebilir ve kaynak içerisinde kabarcıkların sıkışmasına neden olabilir.
- Koruyucu Gaz Sorunları: Yetersiz koruyucu gaz kapsamı, düşük akış hızları veya uygun olmayan gaz türü, oksijen ve nitrojen girişi gibi atmosferik kirlenmeye ve gaz ceplerinin oluşmasına neden olabilir.
- Malzeme Bileşimi: Ana metalde yüksek konsantrasyonlarda hidrojen, kükürt, karbon veya diğer safsızlıklar kaynak sırasında gaz çıkışına yol açabilir.
- Hızlı Soğutma: Erimiş havuzun hızlı katılaşması, gazın kaçmadan önce hapsolmasını sağlayabilir.
Çözümler
- Yüzey Temizliği: Kaynak yapmadan önce iş parçalarını iyice temizleyin, gres, yağ ve pas gibi kirleticileri giderin.
- Optimize Edilmiş Koruyucu Gaz Akışı: Kaynak havuzunu korumak için doğru akış hızını ve kapsamı sağlayarak argon veya helyum gibi uygun koruyucu gazları kullanın.
- Malzeme Seçimi ve Hazırlanması: Düşük kirlilik oranına sahip malzemeleri seçin ve gaz giderme gibi kaynak öncesi işlemleri gerçekleştirin.
- Parametre Ayarı: Gazların kaçması için zaman tanıyarak kontrollü soğutmaya izin vermek için lazer parametrelerini ayarlayın.
Çatlama
Çatlama Türleri
- Sıcak Çatlama: Katılaşma sırasında yüksek sıcaklıklarda çekme gerilmeleri veya safsızlıkların ayrışması (örneğin kükürt) nedeniyle oluşur.
- Soğuk Çatlama: Soğuduktan sonra oluşur, genellikle hidrojen gevrekliği, kalıntı gerilmeler veya uygunsuz malzeme bileşimi ile ilişkilidir.
Nedenler
- Yüksek Isıl Gradyanlar: Hızlı ısıtma ve soğutma döngüleri, çatlamayı teşvik eden kalıntı gerilimlere neden olabilir.
- Malzeme Bileşimi: Bazı alaşımlar, özellikle kükürt veya karbon oranı yüksek olanlar, çatlamaya karşı daha hassastır.
- Safsızlıklar: Kükürt ve fosfor gibi elementler tane sınırlarında ayrışarak yapıyı zayıflatabilir.
- Hidrojen Emilimi: Nem, kirli koruyucu gaz veya baz metal yoluyla gelen hidrojen, gecikmiş çatlamaya yol açabilir.
Çözümler
- Ön Isıtma ve Kaynak Sonrası Isıl İşlem: Isıl gradyanları azaltmak için iş parçasını önceden ısıtın ve kalan gerilimleri gidermek için kaynak sonrası ısıl işlem uygulayın.
- Malzeme Kontrolü: Çatlak riskini azaltmak için düşük kirlilik seviyelerine sahip malzemeleri seçin ve kimyasal bileşimlerini optimize edin.
- Hidrojen Kontrolü: Malzemeleri kurutun ve kuru koruyucu gazlar kullanmak ve nemden kaçınmak gibi düşük hidrojenli prosesleri kullanın.
- Gerilim Giderme Teknikleri: Gerilim yoğunlaşmasını en aza indirmek için fikstürler ve uygun birleştirme tasarımları kullanın.
Alttan kesilmiş
Nedenler
- Aşırı Isı Girişi: Yüksek lazer gücü veya yavaş hareket hızları, yeterli dolgu metali olmadığında lokal erimeye ve malzeme kaybına neden olabilir.
- Yanlış Işın Açısı: Lazer ışınının birleştirme noktasına göre yanlış hizalanması, füzyon yerine malzemenin çıkarılmasına yol açabilir.
- Uygunsuz Odaklanma: Yanlış lazer odaklaması enerjinin eşit olmayan şekilde yoğunlaşmasına neden olabilir.
Çözümler
- Isı Girişini Optimize Edin: Isı dağıtımını kontrol etmek için lazer gücünü, seyahat hızını ve ışın çapını ayarlayın.
- Işın Hizalaması: Eşit erime ve dolumu sağlamak için lazer ışınını birleştirme yeri ile doğru şekilde hizalayın.
- Kaynak Tekniği: Malzeme kaybını azaltmak için lazerin açısını ve konumunu ayarlayın.
Füzyon eksikliği
Nedenler
- Yetersiz Isı Girişi: Düşük lazer gücü veya aşırı seyahat hızı, temel malzemelerin tam olarak kaynaşmasını önleyebilir.
- Uygunsuz Eklem Hazırlığı: İş parçaları arasındaki yetersiz uyum, boşluklar veya hizalama hataları tam füzyonu engelleyebilir.
- Kirlenme: Yüzey oksitleri, kir veya diğer kirleticiler füzyona engel oluşturabilir.
Çözümler
- Isı Girişini Artırın: Uygun füzyonu elde etmek için yeterli lazer gücü kullanın veya seyahat hızını azaltın.
- Bağlantı Uyumunu İyileştirin: Tutarlı kaynak penetrasyonu için iş parçaları arasında uygun hizalama ve uyumu sağlayın.
- Yüzey Temizliği: Kaynak yüzeylerinden oksitleri, yağları ve diğer kirleticileri temizleyin.
Eksik Penetrasyon
Nedenler
- Düşük Lazer Gücü: Malzeme kalınlığını tamamen eritmek için yetersiz enerji girişi.
- Yüksek Seyahat Hızı: Lazer, eklemi tam olarak ısıtmak ve eritmek için çok hızlı hareket eder.
- Uygunsuz Işın Odaklanması: Lazerin yanlış odaklanması sığ penetrasyona yol açabilir.
Çözümler
- Lazer Gücünü Artırın: Eklem boyunca tam penetrasyon sağlamak için güç ayarlarını yapın.
- Seyahat Hızını Azaltın: Lazerin malzemeyi ısıtması ve eritmesi için daha fazla zamana izin verin.
- Doğru Işın Odaklanması: Tutarlı penetrasyon derinliğine ulaşmak için lazeri doğru şekilde odaklayın.
sıçramak
Nedenler
- Aşırı Lazer Gücü: Yüksek güç ayarları erimiş havuzun şiddetli kaynamasına neden olabilir.
- Kirleticiler: Yüzeydeki kirleticiler ısıyla reaksiyona girerek hızlı buharlaşmaya neden olabilir.
- Uygunsuz Koruyucu Gaz: Yetersiz koruyucu gaz oksidasyona ve sıçramaya neden olabilir.
Çözümler
- Lazer Parametrelerini Ayarlayın: Lazer gücünü azaltın ve aşırı enerji girişini önlemek için darbe ayarlarını optimize edin.
- Yüzey Temizliği: Kaynak yapmadan önce yüzeylerin kirleticilerden arındırıldığından emin olun.
- Koruyucu Gaz Optimizasyonu: Uygun koruyucu gaz kullanın ve uygun akış hızlarını koruyun.
Kaynak Boncuğu Düzensizlikleri
Nedenler
- Tutarlı Olmayan Seyahat Hızı: Hızdaki dalgalanmalar, eşit olmayan ısı girişine yol açar.
- Lazer Gücü Değişkenliği: Güç çıkışındaki değişiklikler tutarsız eritmeye neden olabilir.
- Yanlış Işın Odaklanması: Yanlış hizalanmış odaklama, enerjinin eşit olmayan şekilde dağılmasına yol açar.
Çözümler
- Tutarlı Seyahat Hızını Koruyun: Kaynak işlemi boyunca tekdüze hızı sağlayın.
- Güç Çıkışını Sabitleyin: Tutarlı lazer çıkışını korumak için sabit bir güç kaynağı kullanın.
- Işın Odaklanmasını Ayarlayın: Eşit enerji dağıtımı için ışın hizalamasını ve odağının doğru olduğundan emin olun.
Yanma
Nedenler
- Aşırı Isı Girişi: Yüksek lazer gücü veya yavaş hareket hızları aşırı erimeye yol açabilir.
- İnce Malzeme: İnce levhalar yanmaya daha yatkındır.
- Yanlış Işın Odaklanması: Enerjiyi küçük bir alanda yoğunlaştırmak erimeyi şiddetlendirebilir.
Çözümler
- Isı Girişini Azaltın: Lazer gücünü azaltın veya seyahat hızını artırın.
- Işın Odağını Genişletin: Lazer enerjisini daha eşit bir şekilde dağıtın.
- Uygun Malzeme Kalınlığını Kullanın: Malzeme kalınlığını kaynak gereksinimlerinize uygun hale getirin.
Deformasyon ve Bozulma
Nedenler
- Isıl Gerilimler: Hızlı ısıtma ve soğutma çevrimleri genleşme ve büzülmeye neden olur.
- İnce Malzemeler: Eğilmeye ve bükülmeye karşı daha hassastır.
- Aşırı Isı Girişi: Yüksek enerji girişi ciddi bozulmalara yol açabilir.
Çözümler
- Isı Girişini Optimize Edin: Aşırı ısıyı en aza indirmek için kontrollü lazer parametrelerini kullanın.
- Fikstür ve Kelepçeleme: Hareketi azaltmak için iş parçalarını fikstürlerle yerinde tutun.
- Dengeli Kaynak: Isınmayı dengeleyen ve stresi en aza indiren teknikleri kullanın.
Oksidasyon ve Renk Bozulması
Nedenler
- Yetersiz Koruyucu Gaz: Düşük gaz akışı veya zayıf kapsama alanı, kaynak havuzunun havaya maruz kalmasına neden olabilir.
- Uygun Olmayan Gaz Bileşimi: Koruyucu gazın yanlış seçilmesi oksidasyonu önlemede başarısızlığa neden olabilir.
- Kirleticiler: Yüzeydeki kirleticiler reaksiyona girerek oksidasyona neden olabilir.
Çözümler
- Uygun Koruma Sağlayın: Kaynak havuzunu korumak için yeterli miktarda koruyucu gaz akışı kullanın.
- Uygun Gaz Bileşimini Seçin: Oksidasyonu etkili bir şekilde önleyen bir koruyucu gaz seçin (örneğin, argon).
- Yüzey Temizliği: Kaynak sırasında oluşabilecek reaksiyonları en aza indirmek için iş parçası yüzeylerini iyice temizleyin.
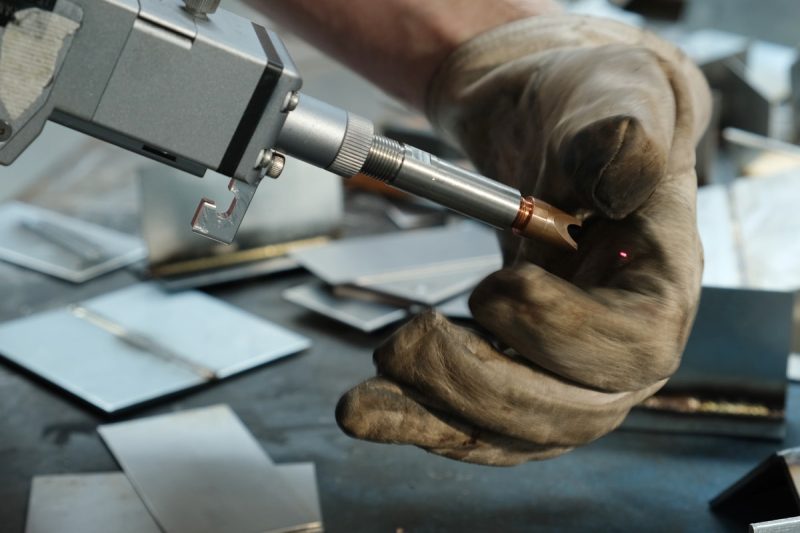
Kaynak Kusurlarını Etkileyen Faktörler
Malzeme özellikleri
Kaynak yapılan malzemelerin özellikleri, kaynağın kalitesini ve hata olasılığını belirlemede önemli rol oynar.
- Isıl İletkenlik: Alüminyum gibi yüksek ısıl iletkenliğe sahip malzemeler ısıyı hızla dağıtma eğilimindedir ve yeterli penetrasyon ve füzyon elde etmek için daha yüksek lazer gücü veya daha yavaş seyahat hızları gerektirir. Yetersiz kontrol, füzyon eksikliği veya eksik penetrasyon gibi kusurlara yol açabilir.
- Erime Noktası: Değişen erime noktalarına sahip malzemeler farklı lazer parametreleri gerektirir. Örneğin, titanyum yüksek bir erime noktasına sahiptir ve daha fazla enerji girişi gerektirirken, çinko gibi düşük erime noktalı malzemeler dikkatli bir şekilde yönetilmezse yanma sorunu yaşayabilir.
- Yansıtma: Bakır ve bazı alüminyum alaşımları gibi yüksek yansıtıcı malzemeler, lazer enerjisinin bir kısmını yansıtarak etkili ısı girişini azaltabilir. Bu, yansıyan enerjinin çevredeki alanları etkileyebilmesi nedeniyle eksik füzyon, tutarsız penetrasyon veya sıçrama ile sonuçlanabilir.
- Malzeme Bileşimi ve Kirlilikler: Malzemedeki kükürt, fosfor ve hidrojen gibi elementler gözeneklilik ve çatlama gibi kusurların olasılığını artırabilir. Örneğin, yüksek hidrojen içeriği gözenekliliğe neden olabilirken, kükürt ve fosfor sıcak çatlama riskini artırır. Düşük kirlilik seviyelerine sahip malzemeler seçmek veya kaynak öncesi işlemler yapmak bu sorunları hafifletmeye yardımcı olabilir.
Kaynak Parametreleri
Lazer kaynak parametrelerinin doğru seçimi ve kontrolü, kusurları önlemede kritik öneme sahiptir. Temel parametreler şunlardır:
- Lazer Gücü: Tam penetrasyon ve füzyon elde etmek için yeterli lazer gücü esastır. Yetersiz güç, füzyon eksikliğine veya eksik penetrasyona yol açabilirken, aşırı güç yanma, sıçrama ve deformasyona neden olabilir.
- Seyahat Hızı: Seyahat hızı, kaynak birim uzunluğu başına ısı girişini etkiler. Çok yüksek bir hız, malzemenin yeterli şekilde ısınmasını önleyebilir ve bu da füzyon eksikliği ve eksik penetrasyon gibi kusurlara yol açabilir. Tersine, çok yavaş bir hız aşırı ısı girişine neden olabilir ve bu da yanma ve bozulmaya yol açabilir.
- Işın Odaklanması: Enerji konsantrasyonu için doğru ışın odaklaması esastır. Yanlış hizalama veya yanlış odak konumu yetersiz penetrasyona, düzensiz boncuk profillerine ve kaynak gözenekliliğine yol açabilir. Derin penetrasyon için küçük nokta boyutuna sahip odaklanmış bir ışın gerekirken, daha geniş, sığ kaynaklar için odaklanmamış bir ışın uygun olabilir.
- Darbe Süresi (darbeli lazer kaynakta): Darbe süresi, her darbede iletilen enerji miktarını etkiler. Kısa darbeler ısı girişini azaltır ve deformasyon riskini en aza indirir, bu da onları hassas veya ısıya duyarlı malzemeler için ideal hale getirir. Daha uzun darbeler daha fazla penetrasyona izin verir ancak sıçrama ve gözeneklilik gibi kusur riskini artırabilir.
Ortak Tasarım
Birleştirmenin tasarımı ve hazırlanması, kaynak kalitesini ve hata olasılığını önemli ölçüde etkileyebilir.
- Uyum Toleransı: Tutarlı kaynak kalitesi elde etmek için uygun birleştirme uyumu esastır. İş parçaları arasındaki boşluklar veya hizalama hataları, füzyon eksikliğine, gözenekliliğe veya tutarsız penetrasyona neden olabilir. Sıkı uyumlar, erimiş havuzun daha iyi kontrol edilmesini sağlar ve kusur riskini en aza indirir.
- Bağlantı Tipi: Farklı bağlantı tipleri (örneğin, alın, üst üste bindirme, fileto) farklı lazer kaynak teknikleri ve parametreleri gerektirir. Örneğin, zayıf hizalamaya sahip alın bağlantıları, alt kesimlere veya füzyon eksikliğine yol açabilirken, aşırı örtüşmeye sahip üst üste bindirme bağlantıları sıçramaya ve yetersiz füzyona neden olabilir.
- Erişilebilirlik: Karmaşık yapılarda, birleştirme noktasına sınırlı erişim, lazer ışınının erişimini kısıtlayabilir ve bu da eksik füzyona veya düzensiz boncuk oluşumuna yol açabilir. Sınırlı erişilebilirliğe sahip birleştirme noktaları için uygun sabitleme ve lazer hizalaması gereklidir.
- Hazırlık ve Temizlik: Eklem alanının uygun şekilde hazırlanması ve temizlenmesi kritik öneme sahiptir, çünkü yüzey kirleticileri gözenekliliğe, çatlamaya ve sıçramaya yol açabilir. Temizlik, füzyona müdahale edebilecek ve kusurlara neden olabilecek oksitleri, yağları ve diğer kirleticileri temizler.
Çevresel faktörler
Kaynak yapılan bölgedeki çevresel koşullar kaynak kalitesini ve kaynak hatalarının oluşumunu doğrudan etkileyebilmektedir.
- Ortam Sıcaklığı: Çok soğuk veya çok sıcak aşırı sıcaklıklarda kaynak yapmak, kaynağın soğuma hızını etkileyebilir ve termal strese ve çatlamaya yol açabilir. Örneğin, soğuk ortamlar hızlı soğumaya neden olarak kırılgan kaynaklara ve çatlaklara yol açabilir.
- Nem ve Rutubet: Ortamdaki nem kaynak havuzuna hidrojen sokabilir ve gözeneklilik ve hidrojen kaynaklı çatlama riskini artırabilir. Kuru, kontrollü bir ortamda kaynak yapmak veya rutubete maruz kalmayı önlemek için önlemler almak yüksek kaliteli kaynaklar için önemlidir.
- Koruyucu Gaz Kalitesi ve Akışı: Koruyucu gaz, erimiş kaynak havuzunu atmosferik kirlenmeden korur. Yetersiz koruyucu gaz akışı veya düşük saflıkta gaz kullanımı oksidasyona, gözenekliliğe ve renk bozulmasına yol açabilir. Ek olarak, kirlenmeyi önlemek için malzeme gereksinimlerine göre argon ve helyum gibi koruyucu gazlar kullanılmalıdır.
- Titreşim ve Hareket: Kaynak kurulumundaki çevresel titreşimler veya hareketler tutarsız kaynak boncuklarına ve diğer kusurlara yol açabilir. Tutarlı sonuçlar sağlamak için sabit fikstürleme ve dış hareketi en aza indirmek esastır.
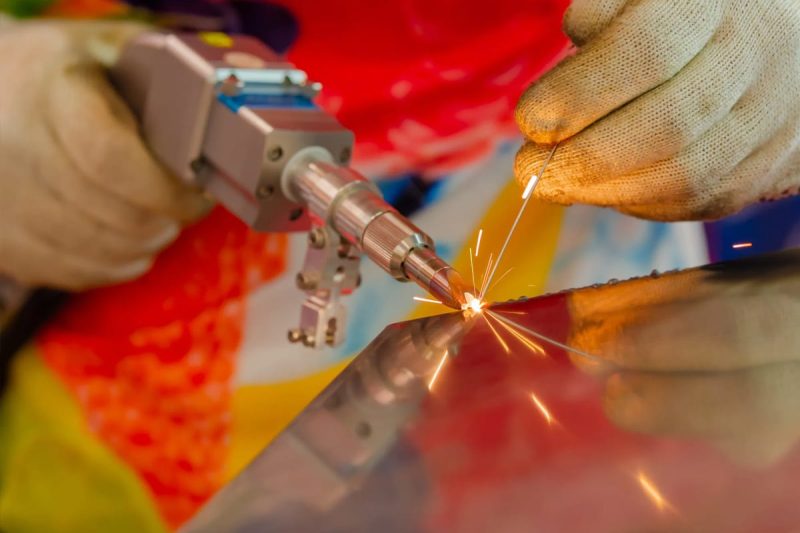
Ek Hususlar ve En İyi Uygulamalar
Uygun Malzeme Seçimi
Lazer kaynakta doğru malzemelerin seçilmesi, yüksek kaliteli kaynaklar elde etmek ve hataları en aza indirmek için çok önemlidir.
- Malzeme Uyumluluğu: Temel malzemelerin lazer kaynakla uyumlu olduğundan emin olun. Farklı malzemeler, erime noktalarındaki, termal iletkenlikteki ve yansıtıcılıktaki farklılıklar nedeniyle lazer enerjisine farklı tepki verir. Örneğin, alüminyum gibi yansıtıcı malzemeler, yansımayı azaltmak ve ısı emilimini optimize etmek için özel önlemler gerektirebilir.
- Malzeme Saflığı: Gözenekliliğe, çatlamaya ve diğer kusurlara neden olabilen kükürt ve fosfor gibi düşük düzeyde safsızlık içeren malzemeler kullanın.
- Malzeme Kalınlığı: Kaynak yapılacak malzemelerin kalınlığını göz önünde bulundurun; çünkü bu, gerekli lazer gücünü ve ısı girişini etkiler.
Lazer Tipi ve Ayarları
Başarılı lazer kaynak işlemi için uygun lazer tipinin seçilmesi ve ayarlarının hassas bir şekilde yapılması kritik faktörlerdir.
- Lazer Türü: Uygulamaya bağlı olarak sürekli dalga (CW) ve darbeli lazerler arasında seçim yapın. CW lazerler yüksek hızlı kaynak için idealdir, darbeli lazerler ise hassas veya ısıya duyarlı bileşenler için uygundur.
- Güç ve Hız Ayarları: İstenilen penetrasyonu elde etmek, sıçrama veya gözeneklilik gibi kusurları en aza indirmek ve ısı girişini kontrol etmek için lazer gücünü, seyahat hızını ve darbe süresini optimize edin.
- Işın Odaklanması ve Konumlandırılması: Enerjinin eşit dağılımı ve tutarlı kaynaklar için ışının doğru hizalanması ve odaklanması önemlidir.
Ortak Tasarım ve Montaj
Uygun birleştirme tasarımı ve uyumu, tutarlı kaynak kalitesini garanti eder ve füzyon eksikliği, gözeneklilik ve hizalama hatası gibi kusurların olasılığını azaltır.
- Uyum Toleransları: Birleşim yerlerinin sıkı ve tutarlı bir şekilde uyum sağlamasını sağlayarak, düzensiz kaynaşmaya veya gözenekliliğe yol açabilecek boşlukları en aza indirin.
- Derz Erişilebilirliği: Lazer ışınının kolayca erişebileceği şekilde derz tasarımı yapın; böylece tamamlanmamış füzyon veya düzensiz boncuk riski en aza indirilmiş olur.
- Derz Hazırlığı: Yağlar, oksitler ve diğer safsızlıklar gibi kirleticileri gidermek için derz yüzeylerini iyice temizleyin ve hazırlayın.
Koruyucu Gaz Seçimi
Koruyucu gaz, erimiş kaynak havuzunu atmosferik kirlenmeden koruyarak oksidasyonu, gözenekliliği ve diğer kusurları önler.
- Gaz Türü: Temel malzemeye ve istenen kaynak özelliklerine göre argon, helyum veya karışımlar gibi uygun koruyucu gazları seçin. Örneğin, argon genellikle paslanmaz çelik için kullanılırken, helyum daha kalın malzemeler için penetrasyonu iyileştirebilir.
- Akış Hızı: Koruyucu gaz akış hızının, türbülans veya yetersiz kaplama olmadan kaynak havuzunu kaplamaya yetecek kadar olduğundan emin olun.
- Saflık: Kirlenmeyi önlemek için yüksek saflıkta koruyucu gaz kullanın.
Kaynak Öncesi ve Kaynak Sonrası İşlemler
Kaynak öncesi ve kaynak sonrası işlemler, kusur olasılığını önemli ölçüde azaltabilir ve genel kaynak kalitesini artırabilir.
- Kaynak Öncesi Temizlik: Gözenekliliğe, çatlamaya ve diğer kusurlara yol açabilen yağ, pas ve nem gibi kirleticileri gidermek için iş parçalarını iyice temizleyin.
- Ön ısıtma: Özellikle çatlamaya meyilli olan malzemelerin ön ısıtılması, termal gradyanları azaltabilir ve artık gerilmeleri en aza indirebilir.
- Kaynak Sonrası Isıl İşlem: Kaynak sonrası tavlama veya gerilim giderme gibi ısıl işlemler uygulayarak, kalıntı gerilimleri azaltın ve kaynağın mekanik özelliklerini iyileştirin.
Operatör eğitimi
Tutarlı ve yüksek kaliteli lazer kaynaklarının sağlanmasında yetenekli operatörler kritik bir rol oynar.
- Teknik Eğitim: Operatörlere, konumlandırma, hız kontrolü ve parametre ayarlamaları dahil olmak üzere lazer kaynak ekipmanlarının doğru kullanımı konusunda eğitim verin.
- Kusur Belirleme: Operatörlere yaygın kusurları, bunların nedenlerini ve tekrarlanmalarını önlemek için gerekli ayarlamaları nasıl yapacaklarını öğretin.
- Güvenlik Protokolleri: Operatörlerin kendilerini ve çalışma ortamını korumak için lazer güvenlik prosedürleri konusunda eğitilmelerini sağlayın.
Ekipman bakımı
Lazer kaynak ekipmanlarının düzenli bakımı, tutarlı performans sağlamak ve arızaları önlemek için önemlidir.
- Optik Temizliği: Işın kalitesini ve doğruluğunu korumak için lensleri, aynaları ve diğer optik bileşenleri düzenli olarak temizleyin.
- Kalibrasyon: Doğru güç çıkışı, ışın hizalaması ve odaklamayı sağlamak için lazer sistemlerini periyodik olarak kalibre edin.
- Bileşen Muayenesi: Kaynak tutarlılığını korumak için nozullar ve mercekler gibi aşınmış veya hasarlı bileşenleri inceleyin ve değiştirin.
Süreç İzleme
Tutarlı ve kusursuz kaynaklar elde etmek için proses izleme ve kontrolü hayati öneme sahiptir.
- Gerçek Zamanlı İzleme: Güç dalgalanmaları, seyahat hızı ve ışın odaklaması gibi kaynak parametrelerindeki sapmaları gerçek zamanlı olarak tespit etmek ve düzeltmek için sensörleri ve izleme sistemlerini kullanın.
- Veri Kaydı: Trendleri analiz etmek, kusurların temel nedenlerini belirlemek ve sürekli iyileştirme önlemlerini uygulamak için kaynak parametrelerini ve sonuçlarını kaydedin.
- Kalite Kontrolleri: Kaynak kalitesini doğrulamak için tahribatsız muayene (NDT) yöntemleri de dahil olmak üzere düzenli kontroller gerçekleştirin.
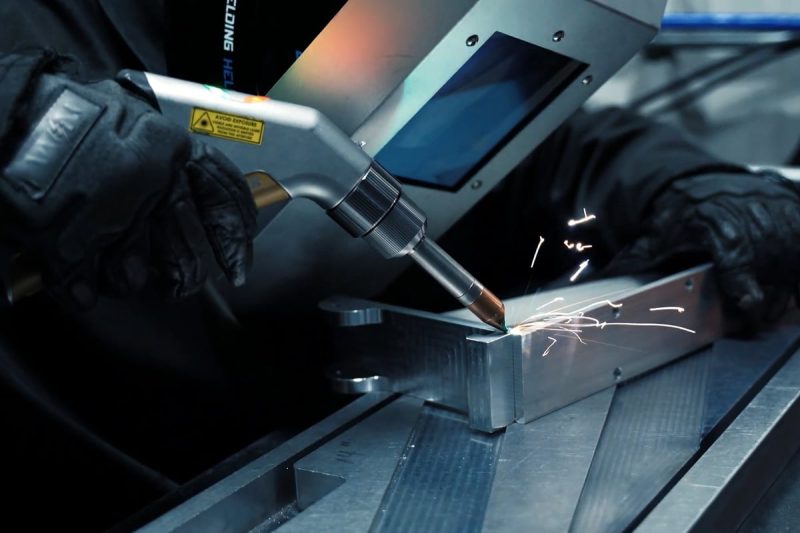
Özet
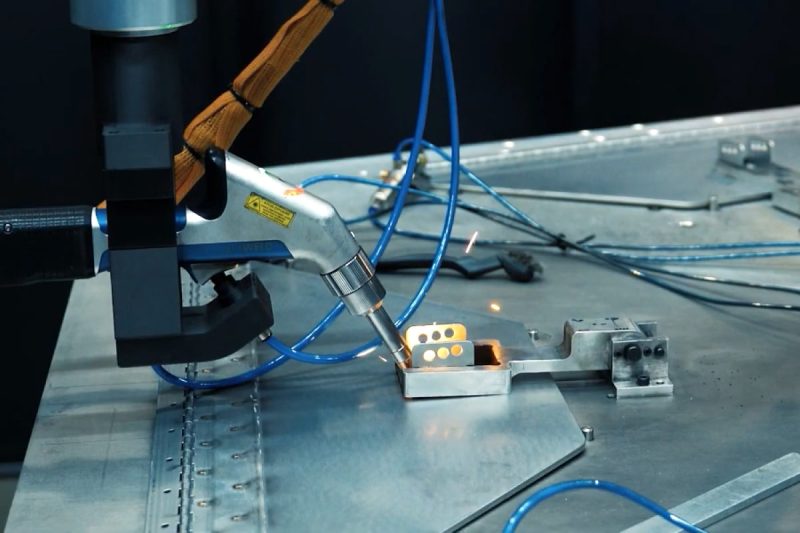
Lazer Kaynak Çözümlerini Alın
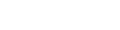
- [email protected]
- [email protected]
- +86-19963414011
- 3 Bölge A, Lunzhen Sanayi Bölgesi, Yucheng Şehri, Shandong Eyaleti.