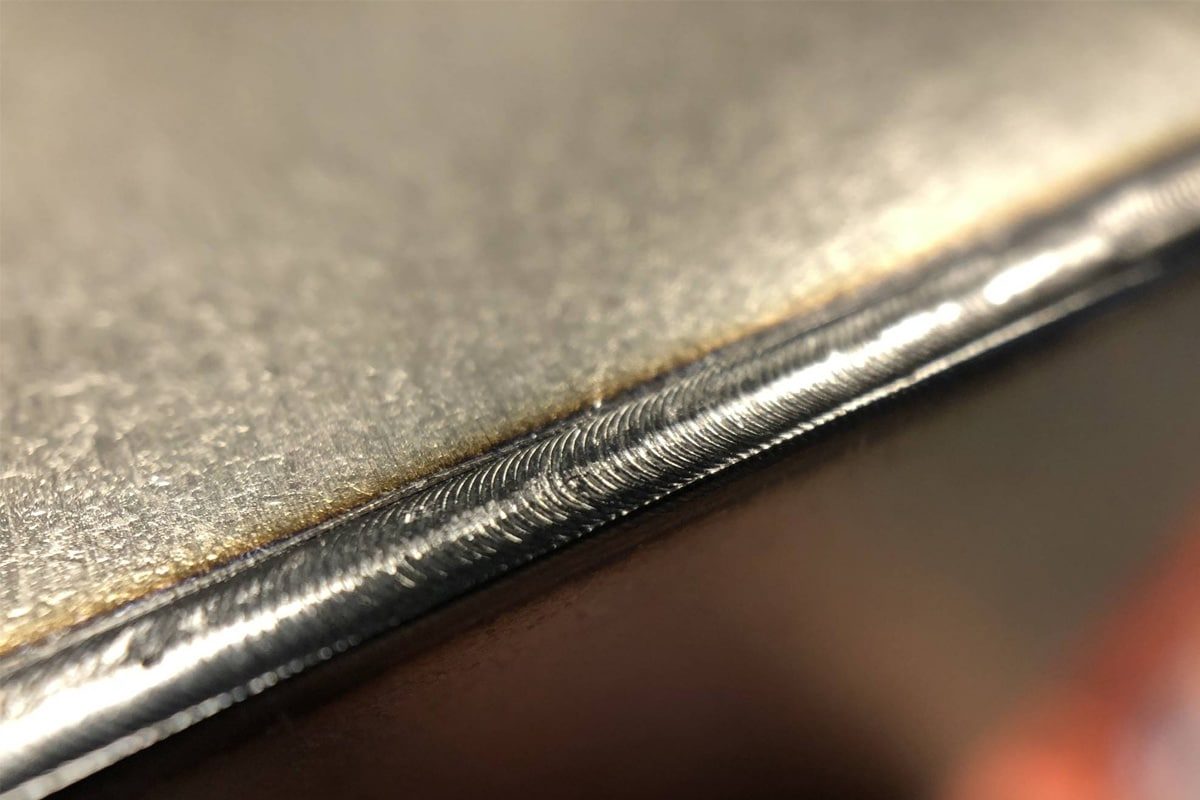
Lazer Kaynakta Minimum Kaynak Genişliğine Nasıl Ulaşılır
Hassas bir kaynak teknolojisi olarak lazer kaynak, yüksek verimliliği, hassasiyeti ve kontrol edilebilirliği nedeniyle havacılık, otomobil üretimi, elektronik bileşenler ve tıbbi ekipmanlarda yaygın olarak kullanılmaktadır. Yerel ısıtma ve eritme için yüksek enerji yoğunluklu bir lazer ışını kullanarak, lazer kaynak, özellikle kaynak boyutu konusunda katı gereksinimlerin olduğu senaryolarda son derece hassas kaynak işlemleri elde edebilir.
Hassas üretim alanında, kaynak genişliğinin kontrolü hayati önem taşır. Kaynak genişliğinin en aza indirilmesi, ısıdan etkilenen bölgenin aralığını azaltabilir, böylece malzeme deformasyonu riskini azaltırken kaynak mukavemetini ve görünüm kalitesini iyileştirir. Ayrıca, daha dar kaynaklar daha az malzeme kaybı ve daha yüksek kaynak verimliliği anlamına gelir, bu da modern endüstrinin yüksek kaliteli ve düşük maliyetli üretim ihtiyaçlarını karşılar.
İçindekiler
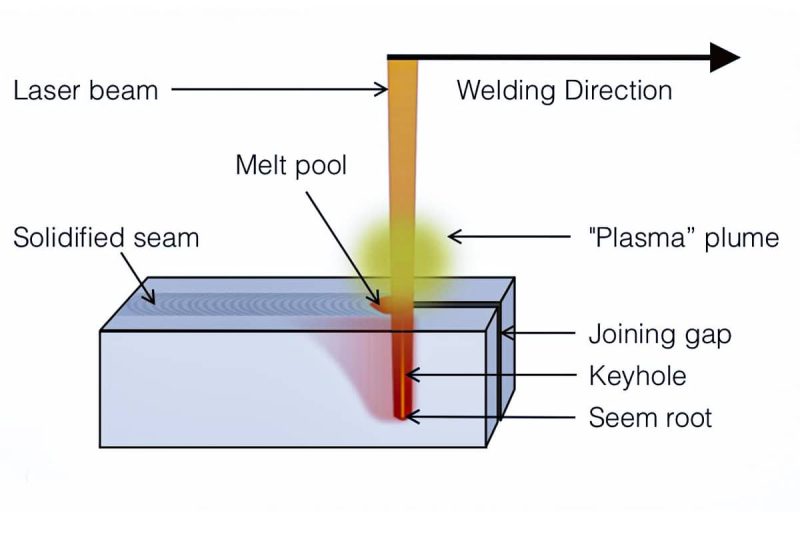
Lazer Kaynağını Anlamak
Lazer Kaynak Temelleri
Lazer kaynak, malzemeyi yerel olarak ısıtmak için yüksek enerji yoğunluklu bir lazer ışını kullanan, malzemenin yüzeyinin erimesine ve bitişik alanlarla hızla birleşmesine neden olan gelişmiş bir kaynak teknolojisidir. Lazer ışınının yüksek güç yoğunluğu ve yüksek hassasiyeti nedeniyle enerji çok küçük bir alanda yoğunlaştırılabilir, böylece hassas ve verimli kaynak elde edilebilir.
Bu teknoloji, özellikle ince duvarlı yapıların ve hassas parçaların kaynaklanması için uygundur çünkü ısıdan etkilenen bölgesi küçüktür, malzeme deformasyonuna neden olması kolaydır ve ana malzemenin orijinal özelliklerini iyi koruyabilir.
Lazer Kaynak Tipi
Lazer kaynak, sürekli lazer kaynak ve darbeli lazer kaynak olarak ikiye ayrılabilir. Sürekli lazer kaynak daha kalın malzemeler için uygundur, darbeli lazer kaynak ise ince malzemeler ve daha yüksek hassasiyet gerektiren kaynak görevleri için uygundur.
- Sürekli dalga lazer kaynağı: Uzun vadeli, yüksek yoğunluklu kaynak ihtiyaçları için uygundur, kalın metal plakaların bağlantısı ve sızdırmazlığı için yaygın olarak kullanılır.
- Darbeli lazer kaynağı: Kısa süreli yüksek enerjili darbelerle malzemeyi ısıtır, ince levhaların veya mikro bileşenlerin kaynaklanması için daha uygundur ve daha yüksek kontrol hassasiyetine sahiptir.
Ayrıca, lazer parametrelerini (güç, hız, odak konumu vb. gibi) ayarlayarak, kaynak alanının ısı girişi farklı malzeme ve kaynak gereksinimlerini karşılamak için esnek bir şekilde kontrol edilebilir ve böylece kaynak boyutu ve kaynak kalitesi etkilenebilir. Bu yüksek uyarlanabilirlik, lazer kaynağının havacılık, otomotiv üretimi ve elektronik endüstrilerinde yaygın olarak kullanılmasını sağlar.
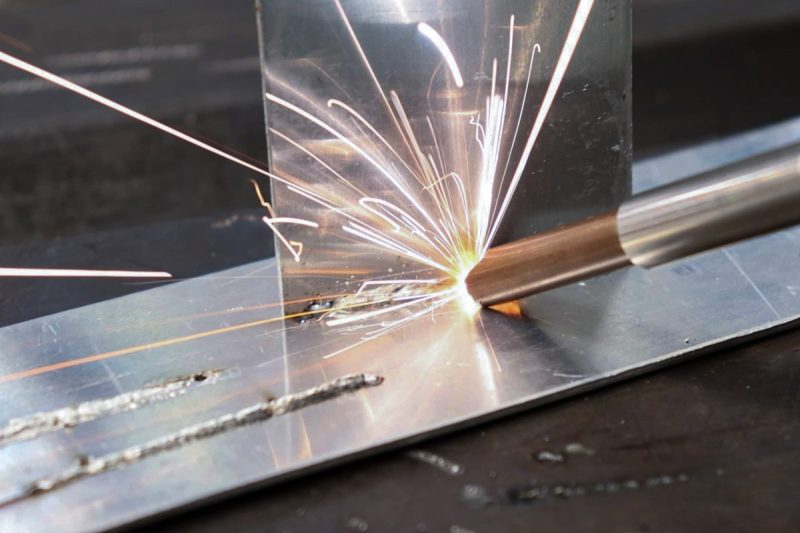
Kaynak Genişliğini Etkileyen Faktörler
Kaynak genişliği, lazer kaynak kalitesinin önemli göstergelerinden biridir ve boyutu doğrudan kaynak doğruluğu, mukavemeti ve görünümüyle ilgilidir. Kaynak genişliğinin kontrolü, esas olarak lazer parametreleri, malzeme özellikleri ve kaynak ortamı dahil olmak üzere birden fazla faktörü içerir. Aşağıda her faktörün kaynak genişliğini nasıl etkilediğine dair ayrıntılı bir analiz verilmiştir:
Lazer Parametreleri
- Lazer gücü: Lazer gücü, kaynak sonuçlarını etkileyen en kritik parametrelerden biridir. Lazer gücü ne kadar büyükse, o kadar fazla ısı üretilir ve ısıdan etkilenen bölgenin ve erimiş havuzun hacmi de artar, bu da kaynak genişliğini artırır. Tersine, güç çok düşükse, malzemeyi eritmek için yeterli enerji sağlayamaz ve kaynak eklemi yetersiz olabilir, bu da dar bir kaynak veya eksik kaynakla sonuçlanabilir. Bu nedenle, kaynağın optimum genişliğini elde etmek için lazer gücünün malzemenin kalınlığına, türüne ve kaynak hızına göre makul bir şekilde seçilmesi gerekir.
- Kaynak hızı: Kaynak hızı, ısı girişi üzerinde önemli bir etkiye sahiptir. Kaynak hızı yavaş olduğunda, lazer kaynak alanında daha uzun süre kalır ve bu da taban malzemesine daha fazla ısı transferi ile sonuçlanarak daha büyük bir erimiş havuz ve ısıdan etkilenen bölge oluşturur ve böylece kaynak genişliği artar. Tersine, çok hızlı bir kaynak hızı ısı girişini azaltarak eksik kaynak, çok dar kaynaklar ve muhtemelen zayıf kaynaklar ile sonuçlanır. Bu nedenle, kaynak hızının makul bir şekilde kontrol edilmesi, uygun kaynak genişliğini sağlamanın anahtarıdır.
- Dalga boyu: Lazerin dalga boyu, lazerin malzemeyle nasıl etkileşime gireceğini belirler. Kısa dalga boylu lazerler (örneğin fiber lazer jeneratörleri tarafından yayılanlar) metal malzemeler tarafından daha iyi emilebilir çünkü daha yüksek bir enerji konsantrasyonuna sahiptirler ve daha küçük bir alanda daha fazla enerji sağlayabilirler, böylece kaynak verimliliğini artırır ve kaynağı daha dar hale getirirler. Nispeten konuşursak, uzun dalga boylu lazerler (örneğin CO2 lazer tüpleri tarafından yayılanlar) metal malzemeleri zayıf bir şekilde emer ve kaynak sırasında enerji dağılımı nispeten geniştir, bu da kolayca daha büyük bir kaynak genişliğine yol açar. Bu nedenle, kısa dalga boylu lazerler yüksek hassasiyetli kaynak için daha uygundur.
- Darbe süresi: Darbeli lazer kaynak, darbe süresini ayarlayarak kaynak işlemini optimize etme konusunda benzersiz bir avantaja sahiptir. Darbe süresi ne kadar kısa olursa, lazerin ısı giriş süresi de o kadar kısalır, bu da ısıdan etkilenen bölgenin genişlemesini azaltmaya ve daha küçük bir kaynak oluşturmaya yardımcı olur. Daha uzun darbe süreleri daha fazla ısı girişi ve daha geniş bir kaynakla sonuçlanır. Darbe şekillendirme teknolojisi sayesinde, lazerin darbe genişliği ve aralığı kaynak sırasında ısı dağılımını ve kaynak morfolojisini optimize etmek için hassas bir şekilde kontrol edilebilir.
- Işın kalitesi: Lazer ışınının kalitesi ve odak kontrolü, kaynak doğruluğu için kritik öneme sahiptir. Daha iyi ışın kalitesine sahip lazerler daha küçük odak boyutlarına ve daha yoğun enerjiye sahiptir, bu da daha yüksek hassasiyette kaynak elde edilmesini sağlar. Daha yüksek ışın kalitesi, ısı yayılımını azaltmaya yardımcı olur, böylece ısı kaynak alanında daha yoğun olur ve kaynak genişliği küçülür. Işın kalitesi düşükse, lazer enerjisinin eşit olmayan bir şekilde dağılmasına neden olur ve böylece kaynak genişliği artar.
Malzeme özellikleri
- Emilim oranı: Malzemenin lazere emilim oranı doğrudan kaynak etkisini etkiler. Metal malzemelerin emilim oranı genellikle yüksektir, özellikle kısa dalga boylu lazer metalle eşleştirildiğinde emilim oranı daha da iyileştirilir. Lazer kaynak işleminde, daha yüksek emilim oranı, lazer enerjisinin etkili bir şekilde ısı enerjisine dönüştürülebileceği ve bunun sonucunda daha küçük bir kaynak elde edilebileceği anlamına gelir. Tersine, malzemenin emilim oranı düşükse, lazer enerjisinin etkili kullanım oranı zayıftır ve bu da kaynağın çok geniş veya eksik olmasına neden olabilir.
- Isıl iletkenlik: Malzemenin ısıl iletkenliği, alt tabakadaki ısının yayılma hızını etkiler. Daha yüksek ısıl iletkenliğe sahip malzemeler (örneğin bakır ve alüminyum) ısıyı hızla dağıtır ve kaynak alanında aşırı ısı dağılımına ve daha geniş kaynaklara neden olur. Bunun aksine, daha düşük ısı iletkenliğine sahip malzemeler (örneğin paslanmaz çelik) kaynak alanında daha fazla ısıyı yoğunlaştırarak daha dar bir kaynak oluşturabilir. Bu nedenle, farklı termal iletkenliklere sahip malzemeleri kaynak yaparken, kaynak genişliğinin uygun olduğundan emin olmak için kaynak parametrelerini termal özelliklerine göre ayarlamak gerekir.
- Yansıtma: Yüksek yansıtma özelliğine sahip malzemeler (alüminyum ve bakır gibi) lazerin daha fazla yansımasını üretecek ve lazer enerjisinin emilim verimliliğini azaltacaktır, bu da kaynak kalitesini etkileyecek ve kaynak genişliğinin artmasına neden olabilir. Bu sorunu aşmak için, yüksek yansıtıcı malzemeler için uygun bir lazer türü seçebilir (kısa dalga boylu bir lazer kullanmak gibi) veya yansıma kaybını telafi etmek için lazer gücünü artırabilirsiniz. Ayrıca, odaklanmış bir ışın ve uygun bir lazer dalga boyu kullanmak da yansıtıcı malzemelerin lazer emilim oranını artırmaya yardımcı olabilir.
Kaynak Ortamı
- Koruyucu gaz: Koruyucu gaz, lazer kaynakta önemli bir rol oynar. Kaynak sırasında oksidasyonu ve kirlenmeyi önlemekle kalmaz, aynı zamanda gaz akışını kontrol ederek ısı iletimini ve kaynak genişliğini de etkiler. Örneğin, argon ve nitrojen genellikle lazer kaynakta koruyucu gaz olarak kullanılır. Isıdan etkilenen bölgenin aralığını etkili bir şekilde azaltabilir ve aşırı kaynak oluşumunu önleyebilirler. Koruyucu gazın seçimi ve kontrolü, belirli malzemelere ve kaynak gereksinimlerine göre ayarlanmalıdır.
- Çevresel koşullar: Sıcaklık ve nem gibi çevresel faktörler de lazer kaynağının etkisi üzerinde belirli bir etkiye sahiptir. Düşük sıcaklıklı ortamlarda, metal malzemelerin termal iletkenliği değişebilir ve bu da kaynak sırasında termal yönetimi etkiler. Ayrıca, yüksek nemli ortamlar lazer enerjisinin dağılmasına neden olabilir ve kaynak kalitesini etkileyebilir. Kararlı çevresel koşullar, lazer ışınının kararlılığını korumaya ve kaynak sırasında kaynak genişliğinin tutarlılığını sağlamaya yardımcı olur.
Lazer kaynakta kaynak genişliğinin kontrolü, lazer parametreleri, malzeme özellikleri ve kaynak ortamı gibi birden fazla faktörün birleşik etkisini içerir. Minimum kaynak genişliğini elde etmek için, bu faktörlerin gerçek uygulamaya göre hassas bir şekilde ayarlanması ve makul bir şekilde seçilmesi gerekir. Lazer gücü, kaynak hızı ve ışın kalitesi gibi parametreleri makul bir şekilde optimize ederek ve malzemenin emiciliğini, termal iletkenliğini ve yansıtıcılığını göz önünde bulundurarak, kaynak doğruluğu, darlığı ve kaynağın kalitesini sağlamak için etkili bir şekilde iyileştirilebilir. Pratik uygulamalarda, yüksek yansıtma ve zor termal yönetim gibi sorunları çözmek, yüksek hassasiyetli kaynak elde etmenin anahtarıdır.
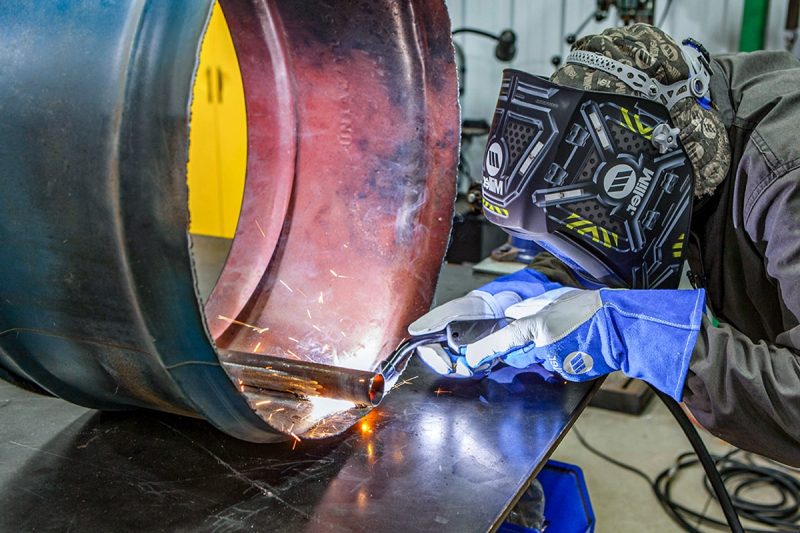
Minimum Kaynak Genişliğine Ulaşma Teknolojisi
Lazer kaynakta minimum kaynak genişliğine ulaşmak için lazer tipi seçimi, lazer parametre optimizasyonu, malzeme hazırlama, ileri kaynak teknolojisi vb. birçok konuda optimizasyon ve ayarlama yapılması gerekir. Bu teknolojiler ısı girişini etkili bir şekilde kontrol edebilir, ısıdan etkilenen bölgeleri azaltabilir ve kaynak doğruluğunu ve darlığını sağlayabilir.
Lazer Tipi Seçimi
Doğru lazer tipini seçmek, minimum kaynak genişliğine ulaşmanın temelidir. Farklı tipteki lazer jeneratörleri, metalleri kaynak yaparken farklı performans gösterir ve farklı kaynak görevleri için uygundur.
- Fiber lazer jeneratörü: Fiber lazer jeneratörü, lazer kaynakta en yaygın kullanılan lazer kaynaklarından biridir. Yüksek güce, yüksek ışın kalitesine ve mükemmel odaklama yeteneğine sahiptir. Fiber lazer jeneratörünün ışını çok küçük bir alana hassas bir şekilde odaklanabilir, böylece kaynak genişliği daha küçük olur ve ince levha malzemeleri verimli bir şekilde işleyebilir. Fiber lazer jeneratörleri, yüksek hassasiyetli ve hızlı kaynak görevleri için çok uygundur ve yüksek kaliteli küçük kaynaklar elde edebilir ve malzemenin ısıdan etkilenen bölgesinin (HAZ) genişlemesini azaltabilir.
- CO2 lazer tüpü: CO2 lazer tüpü, metal kaynaklamada yaygın olarak kullanılan bir diğer lazer kaynağıdır. CO2 lazer tüplerinin ışın kalitesi genellikle fiber lazer jeneratörlerininki kadar iyi olmasa da, daha fazla güç ve daha derin penetrasyon derinliği sağlayabilir, bu da daha kalın malzemelerin kaynaklanması için uygundur. Fiber lazer kadar hassas olmasa da, makul güç düzenlemesi ve optimize edilmiş kaynak hızıyla nispeten küçük kaynak genişlikleri elde edilebilir.
Lazer Dalga Boyu Seçimi
Farklı lazer jeneratör dalga boyları farklı malzemeler için farklı emilim oranlarına sahiptir. CO2 lazerler daha uzun dalga boylarına sahiptir ve genellikle demir dışı metalleri (alüminyum ve bakır gibi) emmede daha az verimlidir. Fiber lazerler daha kısa dalga boylarına sahiptir ve genellikle metal malzemeler tarafından daha iyi emilir, daha yüksek kaynak verimliliği ve daha dar kaynaklar sağlar. Bu nedenle, bir lazer jeneratörü seçerken, güç ve malzeme kalınlığını dikkate almanın yanı sıra, malzemenin optik özellikleri ve lazerin dalga boyu eşleşmesi de dikkate alınmalıdır.
Lazer Parametre Optimizasyonu
- Lazer güç ayarı: Lazer gücü, kaynak ısı girişini etkileyen ana faktördür. Aşırı güç, aşırı ısının çevreye yayılmasına neden olur, böylece kaynak genişler ve hatta kaynak kusurlarına neden olur. Gücü uygun şekilde azaltmak, özellikle ince levha malzemeleri kaynak yaparken ısı girişini azaltmaya ve kaynak genişliğini daraltmaya yardımcı olabilir. Ancak çok düşük güç yetersiz kaynakla sonuçlanabilir. Bu nedenle, lazer gücünün malzeme özellikleri, kaynak hızı ve kaynak gereksinimleriyle eşleşecek şekilde makul bir şekilde ayarlanması, hassas kaynak elde edebilir ve kaynak genişliğini etkili bir şekilde kontrol edebilir.
- Darbe şekillendirme teknolojisi: Darbeli lazer kaynak teknolojisi, lazer darbesinin frekansını, süresini ve enerjisini ayarlayarak kaynak sırasında ısı girişini doğru bir şekilde kontrol edebilir. Darbe genişliği ne kadar kısa olursa, ısı giriş süresi o kadar kısalır ve kaynak alanında daha az ısı birikimi olur, bu da kaynağı daha dar hale getirir. Ayrıca, darbe frekansı ve enerjisi ayarlanarak kaynak hızı ve erimiş havuz morfolojisi kontrol edilebilir ve bu da kaynak genişliğini etkiler. Darbe şekillendirme teknolojisi kullanılarak, özellikle mikro kaynakta, her darbenin ısı dağılımı, minimum kaynak genişliğine etkili bir şekilde ulaşmak için doğru bir şekilde kontrol edilebilir.
- Işın odak kontrolü: Lazer kaynağının doğruluğu ve kaynak genişliği, ışının odak konumuyla yakından ilişkilidir. Lazer ışın odağı ne kadar küçükse, kaynak alanında yoğunlaşabilen enerji yoğunluğu o kadar yüksek olur ve böylece dar ve ince bir kaynak elde edilir. Bu nedenle, lazer odak kontrolü çok önemlidir. Odak konumu ayarlanarak, lazer ışınının enerjisi kaynak alanında daha fazla yoğunlaştırılabilir, böylece çevredeki alana ısı yayılımı önlenebilir ve böylece kaynak genişliği azaltılabilir.
Malzeme hazırlama
- Yüzey temizliği: Kaynak malzemesinin yüzey temizliği, lazer kaynağının etkisini doğrudan etkiler. Yüzeydeki oksitler, yağ, pas ve diğer kirleticiler lazerin emilim oranını etkileyerek ısının kaynak alanında etkili bir şekilde yoğunlaşmasını engeller, böylece kaynak kalitesi etkilenir ve kaynak genişliği artar. Kaynak yüzeyinin temiz ve kirleticilerden arınmış olmasını sağlamak, kaynak kalitesini optimize etmek için ön koşuldur. Yüzey kirleticileri genellikle kimyasal temizleme, mekanik temizleme veya lazer temizleme ile giderilebilir.
- Yüzey kaplaması: Bazı durumlarda, özellikle kaynaklanması zor malzemeler için, yüzey kaplaması lazerin emilim verimliliğini önemli ölçüde artırabilir. Kaplama malzemeleri (bakır kaplama, çinko kaplama vb. gibi) lazer ile malzeme arasındaki etkileşimi iyileştirebilir ve kaynak alanındaki ısı birikimini artırabilir, böylece kaynak işlemi sırasında kaynak genişliğinin doğru bir şekilde kontrol edilmesine yardımcı olabilir. Ek olarak, özel kaplamalar kaynak sırasında erimiş havuzun kararlılığını iyileştirebilir ve kaynak sırasında kusurları azaltabilir.
İleri Kaynak Teknolojisi
- Hibrit lazer kaynak: Hibrit lazer kaynak teknolojisi, lazer ve geleneksel kaynak yöntemlerinin (TIG kaynak veya MIG kaynak gibi) avantajlarını birleştirir ve farklı ısı kaynaklarının avantajlarını birleştirerek ısı girişini ve kaynak doğruluğunu artırır. Lazer ve geleneksel kaynak yöntemlerinin birleşimi, özellikle daha kalın malzemeler kaynaklandığında kaynak genişliğini etkili bir şekilde azaltabilir. Hibrit lazer kaynak teknolojisi, daha yüksek erimiş havuz kararlılığı ve daha küçük ısıdan etkilenen bölgeler sağlayarak daha rafine kaynak efektleri elde edebilir.
- Mikro kaynak teknolojisi: Mikro lazer kaynak, özellikle küçük parçaları birleştirmek için uygun olan ultra küçük kaynakları işlemek için yüksek hassasiyetli bir kaynak teknolojisidir. Mikro kaynak teknolojisi, çok dar kaynakların oluşumunu garanti ederek çok küçük bir kaynak alanında verimli enerji transferi elde etmek için hassas bir şekilde kontrol edilen lazer darbeleri kullanır. Mikro kaynak, elektronik, hassas aletler ve tıbbi cihazlar gibi endüstrilerde yaygın olarak kullanılır ve yüksek kaynak doğruluğu elde edebilir ve kaynak alanının termal etkisini en aza indirebilir.
Minimum kaynak genişliğine ulaşmanın anahtarı, lazer tipi, lazer parametreleri, malzeme hazırlamadan gelişmiş kaynak teknolojisine kadar birden fazla faktörün kapsamlı bir şekilde düzenlenmesinde yatar; her bağlantı ince tasarım ve ayarlama gerektirir. Uygun lazer tipini seçerek, lazer gücünü ve darbe şeklini optimize ederek, ışın odak konumunu kontrol ederek ve malzeme hazırlama ve yüzey işlemini iyileştirerek kaynak genişliği önemli ölçüde azaltılabilir. Aynı zamanda, hibrit lazer kaynak ve mikro kaynak teknolojisinin uygulanması, yüksek hassasiyetli ve dar kaynaklar elde etmek için daha fazla olanak sağlar. Bu teknolojilerin birleşimi ve inovasyonu sayesinde lazer kaynak, yüksek hassasiyet gereksinimlerini karşılarken kaynak verimliliğini ve kalitesini iyileştirebilir.
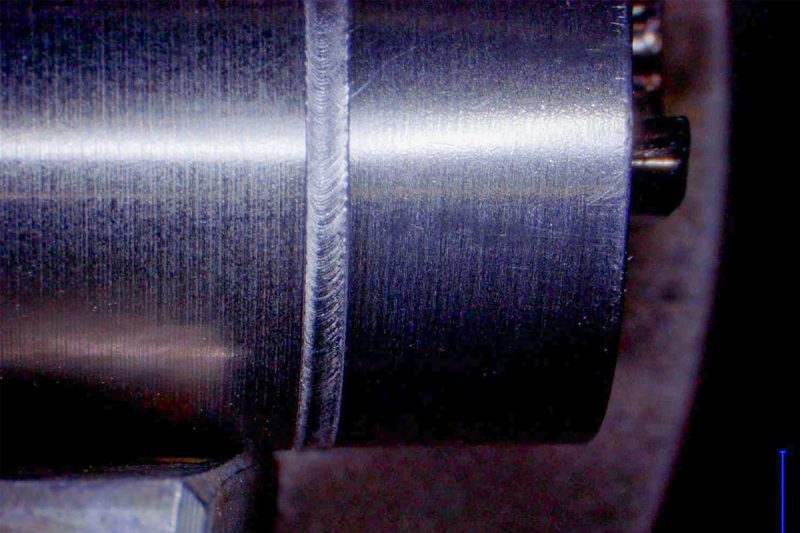
Zorluklar ve Çözümler
Lazer kaynak sürecindeki zorluklar esas olarak termal yönetim, malzeme yansıtıcılığı ve süreç kararlılığında yansıtılır. Bu sorunlar göz önüne alındığında, ilgili çözümleri almak kaynak kalitesini etkili bir şekilde iyileştirebilir, kaynak genişliğini azaltabilir ve kaynak sürecinin kontrol edilebilirliğini ve tutarlılığını sağlayabilir.
Isı Yönetimi
Meydan okumak
Lazer kaynakta, aşırı ısı girişi kaynak alanının aşırı ısınmasına neden olabilir, bu da aşırı kaynak genişliğine yol açabilir ve termal çatlaklar ve deformasyon gibi bir dizi kaynak kusuruna neden olabilir. Ayrıca, büyük bir ısıdan etkilenen bölge (HAZ) malzeme özellikleri üzerinde olumsuz bir etkiye sahip olabilir. Isı girişini makul bir şekilde nasıl kontrol edeceğiniz ve aşırı ısı yayılımını nasıl önleyeceğiniz, hassas kaynak elde etmede önemli bir zorluk haline gelmiştir.
Çözüm
- Yardımcı gaz soğutması kullanın: Uygun koruyucu gaz veya yardımcı gaz (argon, nitrojen veya oksijen gibi) kullanmak, yalnızca kaynak alanının oksidasyonunu önlemekle kalmaz, aynı zamanda kaynak sırasında oluşan aşırı ısıyı etkili bir şekilde giderir ve böylece ısıdan etkilenen bölgenin genişlemesini azaltır. Yardımcı gazın akış hızı ve basıncı, en iyi soğutma etkisini sağlamak için kaynak malzemesine, kaynak hızına ve lazer gücüne göre optimize edilmelidir.
- Kaynak hızı optimizasyonu: Kaynak hızının uygun şekilde artırılması, birim zaman başına ısı girişini azaltabilir ve malzemenin ısınma süresini kısaltabilir, böylece kaynak alanının aşırı ısınmasını etkili bir şekilde önleyebilir. Daha yüksek kaynak hızları, ısının daha geniş bir alana hızla yayılmasına, yerel sıcaklık artışını azaltmaya ve böylece kaynak genişliğini ve ısıdan etkilenen bölgeyi kontrol etmeye neden olabilir.
- Isı kaynağı düzenlemesi: Lazer gücünü ayarlayarak veya darbeli bir lazer kullanarak, kaynak işlemi sırasında ısı girişi hassas bir şekilde kontrol edilebilir. Özellikle darbeli kaynakta, kısa darbeler ve daha yüksek darbe frekansları, ısının hızla odaklanmasını ve kaynak alanına dağıtılmasını sağlayarak ısı yayılımını önleyebilir.
Malzeme Yansıtıcılığı
Meydan okumak
Birçok metal malzeme, özellikle demir dışı metaller (örneğin alüminyum, bakır, vb.), yüksek ışık yansıtma özelliğine sahiptir. Yüksek yansıtma özelliğine sahip malzemeler, büyük miktarda lazer enerjisinin yansıtılmasına neden olur, bu da enerjinin etkili kullanımını azaltır, kaynak verimliliğini sınırlar ve kaynak sırasında eksik kaynak ve artan kaynak genişliğine neden olabilir.
Çözüm
- Kısa dalga boylu lazerler kullanın: Kısa dalga boylu lazerler (örneğin fiber lazer jeneratörleri tarafından üretilenler) yüksek yansıtıcı malzemeler için daha yüksek bir emilim oranına sahiptir. Kısa dalga boylu lazerler malzemeler tarafından daha iyi emilebilir, yansımaları azaltabilir ve kaynaklama sürecinde daha fazla lazer enerjisinin etkili bir şekilde kullanılmasını sağlayarak kaynak verimliliğini artırabilir ve kaynak genişliğini azaltabilir. Uzun dalga boylu CO2 lazerlerle karşılaştırıldığında, fiber lazer jeneratörleri daha yüksek yansıtıcılığa sahip malzemeleri işlemek için daha uygundur.
- Lazer güç ayarı: Yüksek yansıtıcılığa sahip malzemeler için, lazer gücünü uygun şekilde azaltmak aşırı enerji yansımasını önleyebilir. Daha düşük güç ayarları yansımaları azaltmaya ve enerji israfını önlemeye yardımcı olur, böylece kaynak genişliğini etkili bir şekilde kontrol eder ve kaynak kalitesini optimize eder.
- Kaplamalı malzemeler kullanın: Alüminyum ve bakır gibi bazı yüksek yansıtıcı metal malzemeler, alüminyum kaplama, bakır kaplama ve diğer yüzey işleme yöntemleri gibi kaplama teknolojisini kullanabilir. Bu kaplamalar daha düşük yansıtıcılığa sahiptir, bu da lazerin emilim verimliliğini artırabilir ve kaynak işlemindeki yansımanın müdahalesini azaltabilir, böylece kaynak genişliğini daha iyi kontrol edebilir.
Proses Stabilitesi
Meydan okumak
Lazer kaynaklama sırasında kararlılık önemli bir faktördür. Herhangi bir işlem kararsızlığı kaynak kalitesinde dalgalanmalara, kaynak genişliğinde değişikliklere ve hatta kaynak kusurlarına (gözenekler, kaynak ofseti vb.) yol açabilir. Tutarlı kaynak sonuçları elde etmek için, parametre dalgalanmalarından kaynaklanan kaynak kalitesi sorunlarından kaçınmak için lazer kaynaklama işleminin kararlılığı sağlanmalıdır.
Çözüm
- Gelişmiş lazer kontrol sistemi: Gelişmiş lazer kontrol sistemleri kullanılarak, lazer gücü, kaynak hızı, ışın odağı vb. gibi temel parametreler gerçek zamanlı olarak izlenebilir ve ayarlanabilir, böylece her kaynak işlemi sırasında lazer parametrelerinin tutarlılığı sağlanır. Modern lazer kaynak sistemleri genellikle yüksek hassasiyetli sensörler ve otomatik ayarlama fonksiyonları ile donatılmıştır, bunlar kaynak alanının sıcaklığını, erimiş havuz morfolojisini ve ışın konumunu gerçek zamanlı olarak algılayabilir ve kaynak işleminin kararlılığını korumak için lazer çıkışını otomatik olarak ayarlayabilir.
- Gerçek zamanlı geri bildirim ve kapalı devre kontrolü: Gerçek zamanlı geri bildirim ve kapalı devre kontrol teknolojisinin kullanımı, kaynak işlemi sırasında malzeme özelliklerindeki ve kaynak ortamındaki değişikliklerle başa çıkmak için parametreleri gerçek zamanlı olarak ayarlayabilir. Örneğin, sensörler erimiş havuzun boyutunu, şeklini ve sıcaklığını izleyebilir ve sistem kaynak kalitesinin tutarlılığını korumak için lazer gücünü ve kaynak hızını otomatik olarak ayarlayabilir. Bu teknoloji, kaynak işleminin güvenilirliğini önemli ölçüde artırabilir ve işlem dalgalanmalarından kaynaklanan kaynak sorunlarını önleyebilir.
- Kaynak yolu optimizasyonu: Kaynak işlemi sırasında lazer yolu planlamasını optimize etmek, işlem kararlılığını iyileştirmenin bir diğer önemli yoludur. Kaynak yolunu ve kaynak sırasını doğru bir şekilde kontrol ederek, malzeme deformasyonu ve ısıdan etkilenen bölgedeki değişiklikler azaltılabilir, her kaynak işlemi sırasında tutarlı sıcaklık dağılımı sağlanabilir ve böylece kararlı kaynak sonuçları elde edilebilir.
Termal yönetim, malzeme yansıtıcılığı ve proses kararlılığı, kaynak genişliğini, kaynak kalitesini ve üretim verimliliğini etkileyen lazer kaynaktaki üç büyük zorluktur. Bu zorluklar, uygun soğutma yöntemleri, kısa dalga boylu lazerler, lazer güç düzenlemesi, gelişmiş lazer kontrol sistemleri, optimize edilmiş kaynak yolları ve kaynak sürecinin doğruluğunu ve kararlılığını iyileştirmek için diğer teknolojiler benimsenerek etkili bir şekilde çözülebilir. Bu çözümler yalnızca minimum kaynak genişliğine ulaşmaya yardımcı olmakla kalmaz, aynı zamanda lazer kaynak teknolojisinin yaygın olarak uygulanması için güçlü destek sağlar.
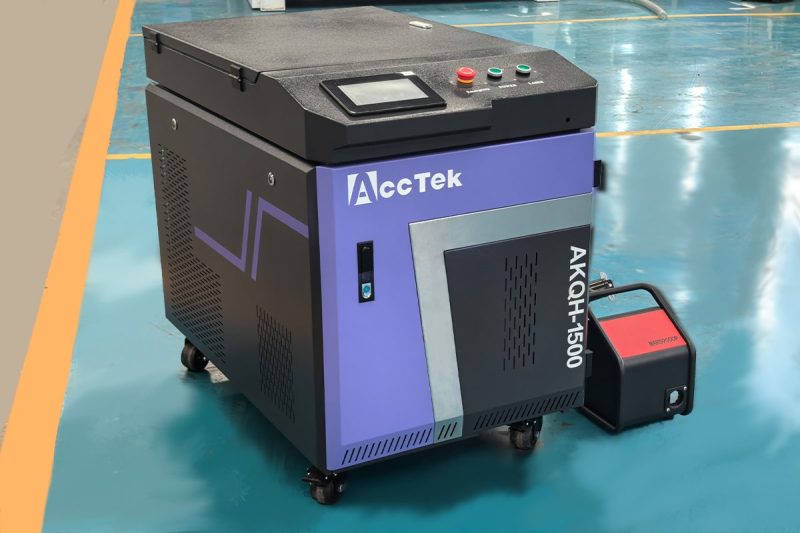
özetle
Lazer kaynakta minimum kaynak genişliğine ulaşmak sadece kaynak kalitesini iyileştirmenin anahtarı değil, aynı zamanda malzeme israfını azaltmak, üretim verimliliğini iyileştirmek ve maliyetleri düşürmek için de önemli bir adımdır. Üretim endüstrisinde hassas kaynak teknolojisine olan talebin artmasıyla birlikte, giderek daha fazla şirket kaynak işlemi sırasında ısı girişini, kaynak genişliğini ve kaynak kalitesini doğru bir şekilde nasıl kontrol edeceklerine dikkat etmeye başlıyor. Lazer kaynakta, lazer parametrelerini (güç, kaynak hızı, darbe şekillendirme ve ışın odağı vb. gibi) doğru bir şekilde kontrol ederek, uygun malzemeleri ve kaynak teknolojisini seçerek, kaynak etkisi etkili bir şekilde optimize edilebilir, ideal kaynak kalitesi elde edilebilir, gereksiz malzeme israfı azaltılabilir ve ürünün tutarlılığı ve güvenilirliği iyileştirilebilir.
Ancak gerçek üretim uygulamalarında, lazer kaynak hala bir dizi teknik zorlukla karşı karşıyadır. Örneğin, aşırı ısı girişi, kaynağın çok geniş olmasına neden olabilir ve malzemenin yansıtıcılığı da lazer enerjisinin etkili iletimini etkileyecektir. Bu zorlukların gelişmiş teknik araçlar ve süreç iyileştirmeleri yoluyla çözülmesi gerekir. Örneğin, uygun soğutma yöntemlerinin kullanılması, kısa dalga boylu lazerlerin seçilmesi, lazer gücünün optimize edilmesi ve verimli lazer kontrol sistemlerinin kullanılması bu sorunları bir dereceye kadar çözebilir. Teknolojinin sürekli ilerlemesiyle, lazer kaynağının doğruluğu ve kararlılığı artmaya devam edecek ve daha geniş ve daha karmaşık endüstriyel uygulamaların ihtiyaçlarını karşılamasını sağlayacaktır.
Bu süreçte, lazer kaynak makineleri Üstün teknolojisi ve yenilikçi tasarımıyla sektörde lider konuma gelmiştir. Firmamızın lazer kaynak makineleri, kaynak işlemi sırasında doğru sıcaklık kontrolünü sağlayarak verimli kaynak elde edebilen en son fiber lazer teknolojisini kullanır, böylece kaynak genişliğini etkili bir şekilde kontrol eder ve ısıdan etkilenen bölgeyi azaltır. Kaynak ekipmanlarımız yalnızca yüksek hassasiyetli lazer ışını ayarlama yeteneklerine sahip olmakla kalmaz, aynı zamanda kaynak işlemi sırasında parametreleri otomatik olarak ayarlayabilen gelişmiş bir sıcaklık kontrol sistemiyle donatılmıştır, böylece kaynak etkisini optimize eder ve her kaynak noktasında istikrarlı ve tutarlı kalite sağlar.
Ek olarak, AccTek Lazer'in Kaynak makineleri çeşitli metal malzemeler ve karmaşık süreçler için yaygın olarak uygulanabilir ve farklı endüstrilerin yüksek hassasiyetli, dar kaynaklara yönelik ihtiyaçlarını karşılayabilir. İster elektronik üretim, ister otomotiv endüstrisi veya hassas alet üretimi olsun, lazer kaynak ekipmanlarımız güvenilir çözümler sağlayabilir. Mükemmel ürün kalitesi ve istikrarıyla, lazer kaynak alanında birçok müşterinin güvenini kazandık. Lazer kaynak teknolojisinin sürekli evrimiyle, AccTek Laser inovasyon ve teknoloji optimizasyonuna bağlı kalmaya, ürün performansını sürekli iyileştirmeye ve müşterilere daha verimli, daha doğru ve daha güvenilir kaynak çözümleri sunmaya devam edecek ve müşterilerin şiddetli pazar rekabetinde avantajlı bir konuma gelmelerine yardımcı olacaktır.
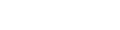
İletişim bilgileri
- [email protected]
- [email protected]
- +86-19963414011
- 3 Bölge A, Lunzhen Sanayi Bölgesi, Yucheng Şehri, Shandong Eyaleti.
Lazer Çözümleri Alın